乙烯的生产深冷分离
乙烯的生产之深冷分离

(5)三元复迭制冷
用乙烯作制冷剂在正压下操作,不能获得-103℃ 以下的低温。 生产中需要-103℃以下的低温时,可采用沸点更 低的制冷剂,甲烷在常压下沸点是-161.5℃。但 是由于甲烷的临界温度是-82.5℃,若要构成冷 冻循环制冷,需用乙烯作制冷剂为其冷凝器提供 冷量,这样就构成了甲烷-乙烯-丙烯三元复迭 制冷。 在这个系统中,冷水向丙烯供冷,丙烯向乙烯供 冷,乙烯向甲烷供冷,甲烷向低于-100℃冷量用 户供冷。
二、裂解气分离方法简介
裂解气的提浓、提纯工作,是以精馏方法 精馏 完成的。 精馏方法要求将组分冷凝为液态。氢气常 压沸点为-263 ℃、甲烷-161.5℃,很难液化, 碳二以上的馏分相对地比较容易液化(乙烯沸点 -103.68 ℃ )。因此,裂解气在除去甲烷、氢 气以后,其它组分的分离就比较容易。 主要矛盾 所以分离过程的主要矛盾是如何将裂解气 中的甲烷和氢气先行分离。 甲烷和氢气 工业生产上采用的裂解气分离方法,主要 有深冷分离和油吸收精馏分离两种。
深冷分离——在 -100℃左右的低温下,将裂 解气中除了氢和甲烷以外的其它烃类全部冷凝下 来。然后利用裂解气中各种烃类的相对挥发度不 同,在合适的温度和压力下,以精馏的方法将各 组分分离开来。
分离要求
要得到高纯度的单一的烃,如重要的基本有机原料 乙烯、丙烯等,就需要将它们与其它烃类和杂质等 分离开来,并根据工业上的需要,使之达到一定的 纯度,这一操作过程,称为裂解气的分离。 各种有机产品的合成,对于原料纯度的要求是不同的。 所以分离的程度可根据后续产品合成的要求来确定。
一、 裂解气的组成及分离方法
(一)裂解气的组成
组分
H2 CO+CO2+H2S CH4 C2H2 C2H4 C2H6 C3H4 C3H6 C3H8 C4 C5 ≥C6 H2O
乙烯装置深冷分离系统的优化和改进
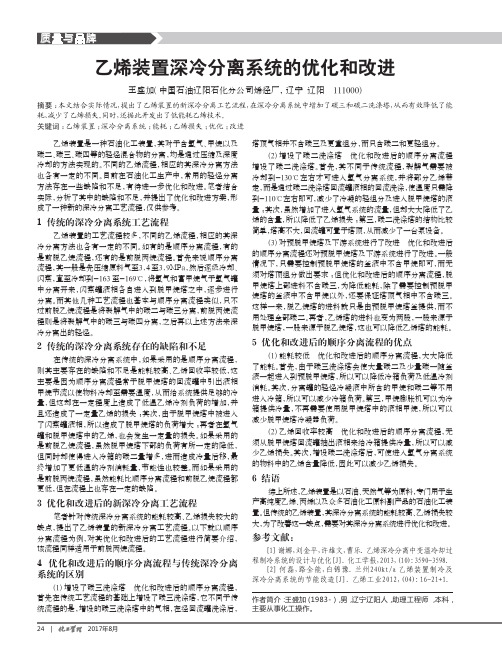
乙烯装置深冷分离系统的优化和改进王盛加(中国石油辽阳石化分公司烯烃厂,辽宁 辽阳 111000)摘要:本文结合实际情况,提出了乙烯装置的新深冷分离工艺流程,在深冷分离系统中增加了碳三和碳二洗涤塔,从而有效降低了能耗、减少了乙烯损失。
同时,还据此开发出了低能耗乙烯技术。
关键词:乙烯装置;深冷分离系统;能耗;乙烯损失;优化;改进乙烯装置是一种石油化工装置,其对于含氢气、甲烷以及碳二、碳三、碳四等的轻烃混合物的分离,均是通过压缩及深度冷却的方法实现的。
不同的乙烯流程,相应的其深冷分离方法也各有一定的不同。
目前在石油化工生产中,常用的轻烃分离方法存在一些缺陷和不足,有待进一步优化和改进。
笔者结合实际,分析了其中的缺陷和不足,并提出了优化和改进方案,形成了一种新的深冷分离工艺流程,仅供参考。
1 传统的深冷分离系统工艺流程乙烯装置的工艺流程较多,不同的乙烯流程,相应的其深冷分离方法也各有一定的不同。
如有的是顺序分离流程,有的是前脱乙烷流程,还有的是前脱丙烷流程。
首先来说顺序分离流程,其一般是先压缩原料气至3.4至3.9MPa,然后逐级冷却、闪蒸,直至冷却到-163至-169℃,将氢气和富甲烷气于氢气罐中分离开来,闪蒸罐液相各自进入到脱甲烷塔之中,逐步进行分离。
而其他几种工艺流程也基本与顺序分离流程类似,只不过前脱乙烷流程是将裂解气中的碳二与碳三分离,前脱丙烷流程则是将裂解气中的碳三与碳四分离,之后再以上述方法来深冷分离出的轻烃。
2 传统的深冷分离系统存在的缺陷和不足在传统的深冷分离系统中,如果采用的是顺序分离流程,则其主要存在的缺陷和不足是能耗较高、乙烯回收率较低,这主要是因为顺序分离流程常于脱甲烷塔的回流罐中引出液相甲烷节流以使物料冷却至需要温度,从而给系统提供足够的冷量,但这却在一定程度上造成了低温乙烯冷剂负荷的增加,并且还造成了一定量乙烯的损失;其次,由于脱甲烷塔中被进入了闪蒸罐液相,所以造成了脱甲烷塔的负荷增大;再者在氢气罐和脱甲烷塔中的乙烯,也会发生一定量的损失。
深冷分离技术在聚乙烯装置的应用及优化措施
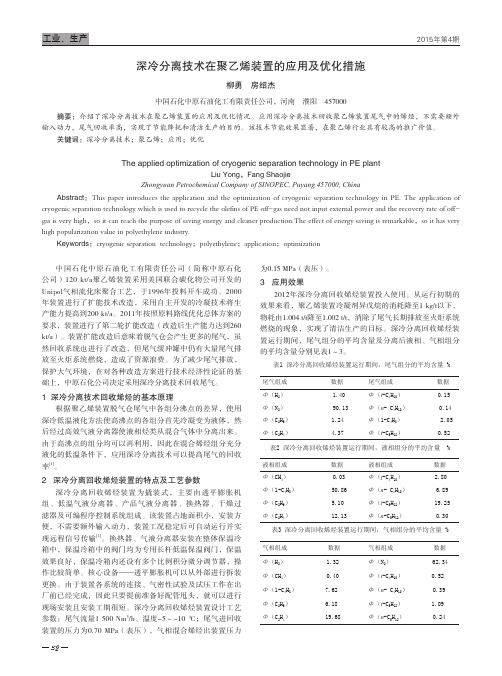
32中国石化中原石油化工有限责任公司(简称中原石化公司)120 kt/a聚乙烯装置采用美国联合碳化物公司开发的Unipol气相流化床聚合工艺,于1996年投料开车成功。
2000年装置进行了扩能技术改造,采用自主开发的冷凝技术将生产能力提高到200 kt/a。
2011年按照原料路线优化总体方案的要求,装置进行了第二轮扩能改造(改造后生产能力达到260 kt/a)。
装置扩能改造后意味着脱气仓会产生更多的尾气,虽然回收系统也进行了改造,但尾气缓冲罐中仍有大量尾气排放至火炬系统燃烧,造成了资源浪费。
为了减少尾气排放,保护大气环境,在对各种改造方案进行技术经济性论证的基础上,中原石化公司决定采用深冷分离技术回收尾气。
1 深冷分离技术回收烯烃的基本原理根据聚乙烯装置脱气仓尾气中各组分沸点的差异,使用深冷低温液化方法使高沸点的各组分首先冷凝变为液体,然后经过高效气液分离器使液相烃类从混合气体中分离出来。
由于高沸点的组分均可以再利用,因此在混合烯烃组分充分液化的低温条件下,应用深冷分离技术可以提高尾气的回收率[1]。
2 深冷分离回收烯烃装置的特点及工艺参数深冷分离回收烯烃装置为撬装式,主要由透平膨胀机组、低温气液分离器、产品气液分离器、换热器、干燥过滤器及可编程序控制系统组成。
该装置占地面积小,安装方便,不需要额外输入动力,装置工况稳定后可自动运行并实现远程信号传输[1]。
换热器、气液分离器安装在整体保温冷箱中,保温冷箱中的阀门均为专用长杆低温保温阀门,保温效果良好,保温冷箱内还设有多个比例积分微分调节器,操作比较简单。
核心设备——透平膨胀机可以从外部进行拆装更换。
由于装置各系统的连接、气密性试验及试压工作在出厂前已经完成,因此只要提前准备好配管甩头,就可以进行现场安装且安装工期很短。
深冷分离回收烯烃装置设计工艺参数:尾气流量1 500 Nm 3/h、温度-5~-10 ℃;尾气进回收装置的压力为0.70 MPa(表压),气相混合烯烃出装置压力为0.15 MPa(表压)。
乙烯的生产之深冷分离

2.多段压缩
(1)裂解气经压缩后,不仅压力升高,而且温度也会升 高,某些烃类尤其是丁二烯之类的二烯烃,容易在较高 的温度下发生聚合和结焦。这些聚合物和结焦物会堵塞 压缩机阀片和磨损气缸,或沉积在叶轮上。 同时温度升高,还会使压缩机润滑油粘度下降,从而 使压缩机运转不能正常进行。
因此,裂解气压缩后的温度必须要限制,当裂解气中 含有碳四、碳五等重组分时,压缩机出口温度一般不能 超过100℃。 在生产上主要是通过裂解气的多段压缩和冷却相结合 的方法来实现。裂解气段间采用水冷,各段入口38~ 40℃。
(1)氨蒸汽压缩制冷
(1)蒸发
(2)压缩 (3)冷凝 (4)节流膨胀
冷冻剂
冷冻剂本身物理化学性质决定了制冷温度的范围。如液
氨降压到0.098MPa时进行蒸发,其蒸发温度为-33.4℃。 如果降压到0.011MPa,其蒸发温度为-40℃。 要满足深冷分离,获得-100℃的低温,必须用沸点更低 的气体作为冷冻剂。
二、制冷
深冷分离裂解气需要把温度降到-100℃以 下。为此,需向裂解气提供低于环境温度 的冷剂。 获得冷量的过程称为制冷。 深冷分离中常用的制冷方法有两种:冷冻 循环制冷和节流膨胀制冷。
(二)制冷
1、冷冻循环制冷 2、节流膨胀制冷 3、热泵
1、冷冻循环制冷
制冷原理
将物料冷却到低于环境温度的冷冻过程称为冷冻
(5)三元复迭制冷
用乙烯作制冷剂在正压下操作,不能获得-103℃ 以下的低温。 生产中需要-103℃以下的低温时,可采用沸点更 低的制冷剂,甲烷在常压下沸点是-161.5℃。但 是由于甲烷的临界温度是-82.5℃,若要构成冷 冻循环制冷,需用乙烯作制冷剂为其冷凝器提供 冷量,这样就构成了甲烷-乙烯-丙烯三元复迭 制冷。 在这个系统中,冷水向丙烯供冷,丙烯向乙烯供 冷,乙烯向甲烷供冷,甲烷向低于-100℃冷量用 户供冷。
轻油裂解气低压深冷分离制乙烯
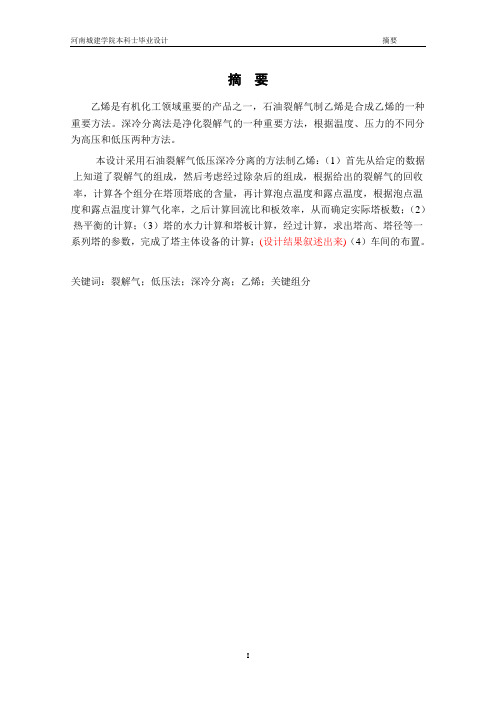
摘要乙烯是有机化工领域重要的产品之一,石油裂解气制乙烯是合成乙烯的一种重要方法。
深冷分离法是净化裂解气的一种重要方法,根据温度、压力的不同分为高压和低压两种方法。
本设计采用石油裂解气低压深冷分离的方法制乙烯:(1)首先从给定的数据上知道了裂解气的组成,然后考虑经过除杂后的组成,根据给出的裂解气的回收率,计算各个组分在塔顶塔底的含量,再计算泡点温度和露点温度,根据泡点温度和露点温度计算气化率,之后计算回流比和板效率,从而确定实际塔板数;(2)热平衡的计算;(3)塔的水力计算和塔板计算,经过计算,求出塔高、塔径等一系列塔的参数,完成了塔主体设备的计算;(设计结果叙述出来)(4)车间的布置。
关键词:裂解气;低压法;深冷分离;乙烯;关键组分AbstractEthylene is an important organic chemical industry one of the products, oil cracked gas ethylene is an important method of synthesis of ethylene. Cryogenic separation of cracked gas purification method is an important method, according to the temperature and pressure were divided into high and low pressure two ways.The design uses low-pressure cryogenic gas oil cracking method of separation of ethylene: (1) First, from the data given that the pyrolysis gas composition, so that later, after considering the composition through the impurity, according to the recovery of pyrolysis gas given rates, the various components of the content in the top of the tower bottom of the column, followed by calculation of bubble point temperature and dew point temperature, according to the temperature and dew point temperature, bubble point calculation gasification efficiency, followed by calculation of the efficiency of reflux ratio and the board to determine the actual plate number; (2) the heat balance calculation; (3) tower tray hydraulic calculations and calculation, after calculation, find the tower, tower diameter and other parameters of a series of towers, the tower of the main equipment to complete the calculation (4) workshop layout ( 5) Show the design process used in the proprietary symbol (6) summarizes the work on the design Many of the design process with reference to literature, to a large number of look-up table and calculation. Part of the chart extract to the design, reference is also cited in the design。
乙烯的生产深冷分离PPT课件
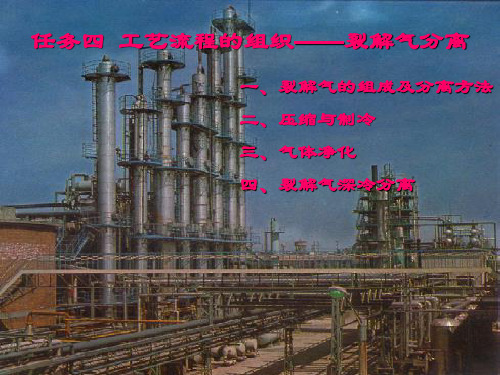
2.多段压缩
(1)裂解气经压缩后,不仅压力升高,而且温度也会升 高,某些烃类尤其是丁二烯之类的二烯烃,容易在较高 的温度下发生聚合和结焦。这些聚合物和结焦物会堵塞 压缩机阀片和磨损气缸,或沉积在叶轮上。 同时温度升高,还会使压缩机润滑油粘度下降, 从而使压缩机运转不能正常进行。
因此,裂解气压缩后的温度必须要限制,当裂 解气中含有碳四、碳五等重组分时,压缩机出口温度一 般不能超过100℃。 在生产上主要是通过裂解气的多段压缩和冷却 相结合的方法来实现。裂解气段间采用水冷,各段入口 38~40℃。
深冷分离——在 -100℃左右的低温下, 将裂解气中除了氢和甲烷以外的其它烃类全部冷 凝下来。然后利用裂解气中各种烃类的相对挥发 度不同,在合适的温度和压力下,以精馏的方法 将各组分分离开来。
深冷操作的系统组成
1、压缩 冷冻系统
该系统的任务是加压、降温,以保 证分离过程顺利进行。 为了排除对后继操作的干扰,提高 产品的纯度,通常设置有脱酸性气 体、脱水、脱炔和脱一氧化碳等操 作过程。 将各组分进行分离并将乙烯、丙烯产 品精制提纯,这是深冷分离的核心。
(2)丙烯制冷系统
丙烯常压下沸点为 - 47.72 ℃,用 丙烯作冷冻剂可以得到-40℃以上温度级的冷 量。 把丙烯压缩到 l.864MPa 的条件下, 丙烯的冷凝点为45℃,很容易用冷水冷却使之 液化。
(3)乙烯制冷系统
常压下乙烯的沸点为- 104℃,即用乙烯作制冷 剂可以获-100℃的低温。 乙烯的临界温度为9.9℃,临界压力为5.15MPa, 在此温度之上,不论压力多大,也不能使其液化, 所以不能用普通冷水使之液化。为此,乙烯循环 制冷中的冷凝器需要使用制冷剂冷却。 工业生产中常采用丙烯作制冷剂来冷却乙烯,这 样丙烯的冷冻循环和乙烯冷冻循环制冷组合在一 起,构成乙烯-丙烯复迭制冷。
乙烯深冷分离工艺中LNG冷能的利用

传统乙烯分离装置热负荷分析
文中以某30万t/a乙烯的深冷分离系统为研
究背景,分析裂解气深冷系统、分馏系统和三机压缩 制冷系统中需要甲烷冷剂、乙烯冷剂和丙烯冷剂提 供的冷负荷大小.以裂解气分离流程为例,质量流量
73.31 3.45
t/h的裂解气(其组成如表1所示)在15℃、
MPa的工艺条件下,冷却至一定温度后经预切
c2比
C3比
C4Hs
1,3-C4比4.99
N・C4Hio C5H12 0.07 0.08
C3114
C6H12
0.003
C6H6
流程模拟分析结果表明,该乙烯深冷分离工艺 中的开式甲烷制冷系统需将甲烷冷剂(部分塔顶甲 烷气)从0.61 MPa加压至3.9MPa(消耗压缩功耗约 614kW),经水冷后进入冷箱,压缩后的脱甲烷塔顶 气在一111.8℃全部冷凝,然后再通过节流阀节流 膨胀降压降温,在一128.3℃、1.01 MPa下进闪蒸 罐.经闪蒸罐后,液相返塔回流,气相进深冷系统为 裂解气提供冷量.而乙烯制冷系统提供的冷量 55.5%用于脱甲烷塔进料的深冷;丙烯制冷系统提 供的冷量除了55.4%用于乙烯精馏塔塔顶尾气冷 凝,还有约17%用于乙烯冷剂的冷却和冷凝.两系 统的冷量分配如表2、表3所示. 根据表2、表3所示乙烯制冷系统和丙烯制冷 系统提供的冷量分配,利用化工流程模拟软件
MPa
压缩至1.05 MPa,替代原流程中将甲烷冷剂压缩至 3.9MPa的工艺,这样甲烷制冷系统所需压缩功耗 仅为161 kW,相比原流程的压缩机功耗614kW,减 少了453 kW.故以122×104
t/a
名称丽矿丽厂丽丽彰品
物流进、出换热网络的运行条件 度/。C(kg・h‘1)度/。C(kW・K一)。
乙烯的生产工艺介绍

乙烯的生产工艺介绍生产乙烯的重要核心过程就是分离过程,目前世界乙烯装置分离技术主要分为3大类,即顺序分离技术、前脱乙烷前加氢技术和前脱丙烷前加氢技术。
经过几十年的发展乙烯装置的分离流程,通过不断改进,已发展出几种不同的分离路线[3]。
1顺序分离技术深冷分离技术中,顺序分离技术应用的最早也最广泛。
在顺序分离技术中,是把关键组分的相对挥发度最接近1的乙烯和乙烷、丙烯和丙烷的分离放到流程的最后,首先按照从轻到重的顺序,将裂解气中的各个组分进行分离。
其典型流程主要包括:裂解气急冷、裂解气压缩、裂解气分离及制冷系统等几个主要部分[3],见图1-2。
图1-2典型的顺序分离流程示意(1)裂解气急冷重裂解汽油组分分离出来后,一部分作为急冷油塔的回流,一部分送至汽油汽提塔。
急冷油塔底部采出裂解燃料油,经燃料油汽提塔汽提,来控制闪点,并且冷却。
裂解气急冷部分还包括稀释蒸汽发生系统,它的作用是为裂解炉提供稀释蒸汽。
(2)裂解气压缩裂解气从急冷水塔中出来后进入裂解气压缩机一段吸入罐,压缩后经一段后冷器冷却进入压缩机二段吸入罐,然后分别进入压缩机三、四、五段吸入罐(3)裂解气分离裂解气经过干燥后依次经过脱乙烷塔进料、乙烯精馏塔、中间再沸器和丙烯冷剂冷却,进入脱甲烷塔,塔顶要控制乙烯损失在0.3%一下。
塔釜再沸器用丙烯冷剂回收冷量作为热源,塔釜液送进脱乙烷塔,塔釜控制乙烷含量在0.04%以下,塔顶控制丙烯含量在0.25%以下,乙炔选择加氢生成乙烯和乙烷,塔顶气相经乙烯干燥器后进乙烯精馏塔。
世界上乙烯装置采用最为广泛的一种乙烯分离技术就是顺序分离技术,随着技术进步以及节能减排的要求不断提高,各个行业也在传统的顺序流程的基础上开发了不少新的分离技术,为乙烯分离技术做了很大的改进。
2前脱乙烷分离技术图1-3前脱乙烷前加氢技术前脱乙烷技术的主要特点就是指分离流程的第一个塔为脱乙烷塔[4]。
见图1-3裂解气经急冷、压缩后预冷,首先进人脱乙烷塔系统,C2组分和C3以上组分先分开。
乙烯装置深冷分离系统能耗脱瓶颈技术研究的开题报告

乙烯装置深冷分离系统能耗脱瓶颈技术研究的开题报告一、研究背景乙烯是化工产品中的重要原料,其生产需要通过乙烯装置进行。
在乙烯装置中,深冷分离系统是关键部分之一,其主要功能是将乙烯气体从混合气体中分离出来,并对乙烯进行冷却和液化。
目前,深冷分离系统的能耗问题已经成为乙烯生产中的瓶颈问题。
传统的深冷分离系统存在能耗较高、回收率低等问题,难以满足工业化生产的要求。
因此,针对深冷分离系统能耗问题,开展脱瓶颈技术研究,既有利于提高产业竞争力,也符合新能源、节能环保的社会发展需求。
二、研究目的本研究旨在探究乙烯装置深冷分离系统能耗脱瓶颈技术,寻求能够优化深冷分离系统的方案,降低能耗、提高乙烯回收率的途径。
三、研究方法(一)理论分析通过对深冷分离系统的原理进行理论探讨,分析深冷分离系统中能耗产生的原因,找出能够降低能耗的技术途径。
(二)实验研究采用实验方法,建立深冷分离系统性能测试和分析的实验平台,分析不同操作条件下深冷分离系统的能耗特性。
(三)数学建模基于理论分析和实验数据,构建深冷分离系统能耗数学模型,并采用优化算法进行优化,得出深冷分离系统的优化方案。
四、研究内容(一)深入研究乙烯装置深冷分离系统的工作原理,鉴别其能耗产生的主要原因。
(二)建立深冷分离系统性能测试和分析的实验平台,对不同操作条件下深冷分离系统的能耗特性进行分析。
(三)通过对实验数据的分析,构建深冷分离系统能耗数学模型,采用优化算法进行优化,得出深冷分离系统的优化方案。
(四)利用得出的优化方案,对实验总体性能进行评价,并验证深冷分离系统能耗降低、乙烯回收率提高的效果。
五、研究意义(一)通过深入研究乙烯装置深冷分离系统的工作原理,找出能够降低能耗的技术途径,为提高乙烯生产的效率和降低生产成本提供技术支持。
(二)结合实验研究和数学建模,建立深冷分离系统优化方法,为乙烯工业提供深冷分离系统能耗优化方案的参考。
(三)研究结果可为其他相关领域提供参考和依据,促进节能减排,并贡献环境保护事业。
项目一、乙烯的生产

(一)反应原理
CO2 +2NaOH→Na2CO3 + H2O
H2S +2NaOH→Na2S+2H2O
NaOH吸收剂不可再生
(二)碱洗工艺流程
塔分三段:I段水洗塔为泡罩塔板
Ⅱ段和Ⅲ段为碱洗段填料层
碱液浓度由上而下降低:新鲜碱液含量为18%~20%,Ⅱ段循环碱液NaOH含量约为5~7%Ⅲ段循环碱液NaOH含量为2%~3%.流程图(略)
1.原料油供给和预热系统
2.裂解和高压蒸汽系统
3.急冷油和燃料油系统
4.急冷水和稀释水蒸汽系统
第二节裂解气的净化与分离技术
一、裂解气的组成与分离方法
1、组成
烃类:CH4、C2H2、C2H4、C2H6、C3H4、C3H6、C3H8、C4、C5、C6~204℃馏分
非烃类:H2、H2O、CO、CO2、H2S
所以从动力学分析得出:降低压力可增大一次反应对于二次反应的相对速度。
故无论从热力学还是动力学分析,降低裂解压力对增产乙烯的一次反应有利,可抑制二次反应,从而减轻结焦的程度。
(3).稀释剂的降压作用
如果在生产中直接采用减压操作,因为裂解是在高温下进行的,当某些管件连接不严密时,有可能漏入空气,不仅会使裂解原料和产物部分氧化而造成损失,更严重的是空气与裂解气能形成爆炸性混合物而导致爆炸。另外如果在此处采用减压操作,而对后继分离部分的裂解气压缩操作就会增加负荷,即增加了能耗。工业上常用的办法是在裂解原料气中添加稀释剂以降低烃分压,而不是降低系统总压。
另外从以上讨论,可以归纳各族烃类的热裂解反应的大致规律:
烷烃—正构烷烃最利于生成乙烯、丙烯,是生产乙烯的最理想原料。
环烷烃—在通常裂解条件下,环烷烃脱氢生成芳烃的反应优于断链(开环)生成单烯烃的反应。含环烷烃多的原料,其丁二烯、芳烃的收率较高,乙烯的收率较低。
深冷分离技术在聚乙烯装置中的应用

深冷分离技术在聚乙烯装置中的应用介绍了深冷分离技术回收烯烃的基本原理以及在聚乙烯装置的应用情况。
将深冷分离技术应用于气相法聚乙烯装置回收烯烃,烯烃总回收率达80%以上,不仅减少了尾气排放,还增加了企业的经济效益。
该技术回收率高、能耗低,具有广阔的应用前景。
标签:聚乙烯装置;烯烃回收;深冷分离技术气相法聚合工艺在我国聚乙烯(PE)装置中占有重要的地位。
在PE生产过程中,从反应器排放的惰性气体中含有许多未反应的单体,如乙烯、乙烷、1-丁烯、异戊烷和甲烷等,这些烯烃组分进入膜分离回收系统经过压缩冷凝后,部分1-丁烯和异戊烷被回收,但受压缩能力和冷凝温度的制约,仍有部分气体无法回收利用。
这部分排放气除一部分返回排料系统做输送气循环使用外,其余部分则直接排放到火炬系统燃烧。
气体排放量随着反应负荷的提高和排料频次的增加而增大,造成了资源浪费还增加了装置的能耗。
采用气相法聚合工艺的PE装置其物料消耗主要存在于尾气回收系统的排放损失,如果将膜分离尾气中的乙烯和N2进一步深冷分离,将会取得可观的经济效益。
1深冷分离技术的基本原理深冷分离技术广泛应用于工农业生产、国防建设和科学研究领域。
该技术主要是以气体或气体混合物为工质,经绝热膨胀制取低温,通过换热器返流回收低温冷量或者使气体液化。
透平膨胀机是压力能转化为冷能的核心部件,它的高速平稳运转能够提高制冷效率并为液化、分离系统提供持续足够的低温和冷能。
深冷分离技术回收烯烃的基本原理:根据PE装置尾气中各组分沸点的差异,通过深冷低温液化方法使高沸点的组分首先冷凝变为液体,然后经过高效气液分离器使液相烯烃从混合气体中分离出来。
高沸点的组分都可以再利用,在混合烯烃组分充分液化的低温条件下,利用该技术可以提高膜分离尾气的回收率。
2深冷分离技术的应用针对PE装置尾气处理中存在的问题,邯郸市深冷气体分离设备有限公司开展了大量调研和模拟计算工作,在此基础上设计并制造了深冷分离回收烯烃成套装置。
乙烯装置操作工乙烯深冷分离精馏试卷(练习题库)

乙烯装置操作工乙烯深冷分离精微试卷(练习题库)1、冷箱是由许多O组成的。
2、冷箱一般是由O板翅式换热器串联或并联而成。
3、冷箱内部所装珠光砂的作用是()。
4、外部管道与冷箱的联接一般采用()。
5、冷箱内部所有受压部件采用O相连。
6、冷箱壳体充氮气是为了防止O进入。
7、冷箱系统热交换物流达十余种,物流的流向形式有()。
8、冷箱系统所用的冷剂有()。
9、O运用的不是焦耳一汤姆逊效应。
10、冷箱系统氢气开工线是指()。
11、冷箱系统控制的主要指标为()。
12、控制粗氢中乙烯含量的目的是()。
13、深冷顺序分离流程中,氢气经冷箱回收冷量后送往()。
14、粗氢中乙烯含量主要通过O来保证的。
15、冷箱系统分离出来的氢气纯度主要取决于()。
16、深冷顺序分离流程中,脱甲烷塔第三进料分离罐顶部气相物料氢气含量大约为()。
18、与传统的顺序分离法相比较,KTI与布朗路特公司合作开发的KTI/AET 先进乙烯工艺,其主要的优点在于19、同传统乙烯装置深冷分离与脱甲烷系统相比较,采用先进的分凝分离器技术的脱甲烷系统的优点有()。
20、ARS技术的核心是采用了高效、节能的()。
21、关于分凝分离器的分离过程叙述正确的是()。
22、下列情况中不适合应用分凝分离器技术的是()。
23、冷箱系统的冷量来源是()。
24、冷箱系统操作要求()。
25、为使冷箱尾气中乙烯损失量减小,应该使操作压力和操作温度向()的方向变化。
26、冷箱系统的操作压力正常情况下是通过O来控制的。
27、冷箱系统压力波动会造成()。
28、对于冷箱系统压差过大的处理方法,下列选项不正确的是()。
29、冷箱系统压差过大、温度分布异常,处理方法不正确的是()。
30、正常操作时,关于冷箱温度的控制,下列选项不正确的是()。
31、冷箱系统压差过大、温度分布异常可能的原因有()。
32、冷箱系统压差过大、温度分布异常的可能原因是()。
33、冷箱系统压力、温度波动,下列说法不正确的是()。
乙烯的生产—裂解气的分离流程的组织

炔<1μg/g,产品回收率达98%。
项目二 乙烯的生产 石油化工产品生产技术
流裂 任程解 务的气 五组分
织离
知识点3:裂解气的压缩
1.压缩的原因
需要大量冷量和耐低温设备 常压下,冷凝精馏分离温度低
裂解气常压下沸点很低
常压下沸点
解决办法
1.压缩的原因
为什么要多段压缩? 压缩后的气体温度必须要限制
✓ 原因:裂解气压缩是绝热过程,压力升高,温度升高。 ✓避免压缩过程温升过大造成裂解气中双烯烃尤其是 丁二烯之类的二烯烃在较高的温度下发生大量的聚 合,以至形成聚合物堵塞叶轮流道和密封件。 ✓生产上通过裂解气的多段压缩和段间冷却结合的方 法实现。(压缩机出口温度一般不超过100 ℃,各段 入口温度一般为38 ~40 ℃。)
有水生成
影响加氢效果
水分带入低温 系统造成冻堵
二、脱水
危害
低温下,水冻结成冰,而且与轻质烃形成白色结晶水合物(高 压低温下稳定) ,如CH4·6H20、C2H6·7H20、C3H8·7H20等。 这些固体附着在管壁上,既增加动能消耗,又堵塞管道。
脱水方法
固体吸附法(分子筛、硅胶、活性氧化铝),目前广泛采用 效果较好的是分子筛吸附剂。
顺利进行。
四、脱炔
乙炔的脱除方法主要有溶剂吸收法和催化加氢法。
催化加氢脱炔
特点:不会带入任何新杂质;工艺操作简单;将炔烃变成产品烯烃
1、原理:
主反应: 副反应:
CH≡CH十H2→CH2=CH2 CH≡CH十2H2→CH3—CH3 CH2=CH2十H2→CH3—CH3
mC2H2+nH2→低聚物(绿油)
乙烯装置深冷分离系统的优化和改进_吴兴松
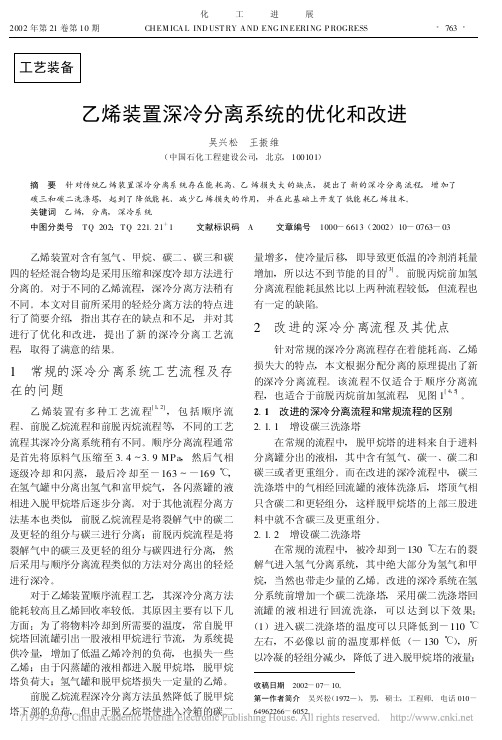
工艺装备乙烯装置深冷分离系统的优化和改进吴兴松 王振维(中国石化工程建设公司,北京,100101)摘 要 针对传统乙烯装置深冷分离系统存在能耗高、乙烯损失大的缺点,提出了新的深冷分离流程,增加了碳三和碳二洗涤塔,起到了降低能耗、减少乙烯损失的作用,并在此基础上开发了低能耗乙烯技术。
关键词 乙烯,分离,深冷系统中图分类号 T Q 202;T Q 221.21+1 文献标识码 A 文章编号 1000-6613(2002)10-0763-03 乙烯装置对含有氢气、甲烷、碳二、碳三和碳四的轻烃混合物均是采用压缩和深度冷却方法进行分离的。
对于不同的乙烯流程,深冷分离方法稍有不同。
本文对目前所采用的轻烃分离方法的特点进行了简要介绍,指出其存在的缺点和不足,并对其进行了优化和改进,提出了新的深冷分离工艺流程,取得了满意的结果。
1 常规的深冷分离系统工艺流程及存在的问题 乙烯装置有多种工艺流程[1,2],包括顺序流程、前脱乙烷流程和前脱丙烷流程等,不同的工艺流程其深冷分离系统稍有不同。
顺序分离流程通常是首先将原料气压缩至3.4~3.9MPa ,然后气相逐级冷却和闪蒸,最后冷却至-163~-169℃,在氢气罐中分离出氢气和富甲烷气,各闪蒸罐的液相进入脱甲烷塔后逐步分离。
对于其他流程分离方法基本也类似,前脱乙烷流程是将裂解气中的碳二及更轻的组分与碳三进行分离;前脱丙烷流程是将裂解气中的碳三及更轻的组分与碳四进行分离,然后采用与顺序分离流程类似的方法对分离出的轻烃进行深冷。
对于乙烯装置顺序流程工艺,其深冷分离方法能耗较高且乙烯回收率较低。
其原因主要有以下几方面:为了将物料冷却到所需要的温度,常自脱甲烷塔回流罐引出一股液相甲烷进行节流,为系统提供冷量,增加了低温乙烯冷剂的负荷,也损失一些乙烯;由于闪蒸罐的液相都进入脱甲烷塔,脱甲烷塔负荷大;氢气罐和脱甲烷塔损失一定量的乙烯。
前脱乙烷流程深冷分离方法虽然降低了脱甲烷塔下部的负荷,但由于脱乙烷塔使进入冷箱的碳二量增多,使冷量后移,即导致更低温的冷剂消耗量增加,所以达不到节能的目的[3]。
乙烯生产-深冷分离

(1)氨蒸汽压缩制冷 (2)丙烯制冷系统 (3)乙烯制冷系统 (4)乙烯—丙烯复迭制冷 (5)三元复迭制冷
(1)氨蒸汽压缩制冷
(1)蒸发 (2)压缩 (3)冷凝 (4)节流膨胀
冷冻剂
冷冻剂本身物理化学性质决定了制冷温度的范 围。如液氨降压到0.098MPa时进行蒸发,其蒸发 温度为-33.4℃。 要满足深冷分离,获得-100℃的低温,必须用 沸点更低的气体作为冷冻剂。
在这个系统中,冷水向丙烯供冷,丙烯向乙烯供 冷,乙烯向甲烷供冷,甲烷向低于-100℃冷量用 户供冷。
2、节流膨胀制冷
所谓节流膨胀制冷,就是气体由较高的压 力通过一个节流阀迅速膨胀到较低的压力,由 于过程进行得非常快,来不及与外界发生热交 换,膨胀所需的热量,必须由自身供给,从而 引起温度降低。
0.76
0.18 0.09
4.36
原料来源
石脑油裂解 轻柴油裂解
14.09 0.32 26.78 0.41 26.10 5.78 0.48 10.30 0.34 4.85 1.04 4.53 4.98
13.18 0.27 21.24 0.37 29.34 7.58 0.54 11.42 0.36 5.21 0.51 4.58 5.40
但不能任意加压,若压力增高: 对设备材料强度要求增高; 动力消耗增大; 使低温分离系统精馏塔釜温升高,易引起一些
不饱和烃的聚合 使烃类相对挥发度降低,增加了分离的困难。
因此,在深冷分离中要采用经济上合理而技 术上可行的压力,一般为3.54~3.95MPa。
2.多段压缩
(1)裂解气经压缩后,不仅压力升高,而且温度也会升 高,某些烃类尤其是丁二烯之类的二烯烃,容易在较高 的温度下发生聚合和结焦。这些聚合物和结焦物会堵塞 压缩机阀片和磨损气缸,或沉积在叶轮上。
乙烯深冷分离中变温冷却过程制冷系统的设计与优化

e x c h a n g e t e mp e r a t u r e d i f f e r e n c e b e t we e n c o l d a n d h o t s t r e a ms i s ma s s i v e i n p r e c o o l i n g p r o c e s s o f c r a c k i n g
Xi o n g we n , CAO Le XI E Na, LI U J i n p i n g, XU
Te c hn o l o gy , Guan gz ho u 51 06 4 0, Gu an gdo ng, Chi na) ( S c h o o l o f E l e c t r i c P o we r ,S o u t h C h i n a U n i v e r s i t y o f
( 华 南 理 工 大 学 电力 学 院 ,广 东 广 州 5 1 0 6 4 0 )
摘 要 :根 据 乙烯 装 置 中 的用 冷 需 求 ,将 乙烯 装 置 的 深 冷 分 离 过 程 分 为 变 温 冷 却 过 程 和 定 温 冷 凝 过 程 ,变 温 冷 却 过 程 指 的 是 裂 解 气 的预 冷 过 程 ,定 温冷 凝 过 程 指 的 是 乙 烯 装 置 中 各 塔 塔 顶 冷 凝 器 中 的换 热 ;分 析 了 乙烯 一 丙 烯 复 叠 制 冷 系 统 的换 热 集 成 曲线 ,可知 在 裂解 气 的 预 冷 阶 段 ,冷 热 物 流 换 热 温 差 大 。 提 出 一 种 组 合 制 冷 系 统 ,它 集 成 了纯 工 质 复 叠 制 冷 和混 合 冷 剂 制 冷 ,其 中 的 多 元 混 合 冷 剂 制 冷 系 统 为 乙烯 深 冷 分 离 的 变 温 换 热 过 程 提 供 冷 量 。 并 用 As p e n P l u s 软 件 对 混 合 冷 剂 系 统 进 行 建 模 ,使 用 遗 传 算 法 优 化 ,优 化 结 果 表 明 在 替 代 原 制 冷 系 统 6 8 9 5 . 5 k w 冷 量 负 荷 的情 况 下 ,功 耗 降低 5 2 1 . 6 k W ,节 能 l 4 . 7 。 关 键 词 :混 合 制 冷 系 统 ; 乙烯 装 置 ;分 离 ;计 算 机 模 拟 ;优 化 设 计
乙烯的生产之深冷分离共74页文档

60、生活的道路一旦选定,就要勇敢地 走到底 ,决不 回头。 ——左
乙烯的生产之深冷分离
41、实际上,我们想要的不是针对犯 罪的法 律,而 是针对 疯狂的 法律。 ——马 克·吐温 42、法律的力量应当跟随着公民,就 像影子 跟随着 身体一 样。— —贝卡 利亚 43、法律和制度必须跟上人类思想进 步。— —杰弗 逊 44、人类受制于法律,法律受制于情 理。— —托·富 勒
45、法律的制定是为了保证每一个人 自由发 挥自己 的才能 ,而不 是为了 束缚他 的才能 。—— 罗伯斯 庇尔
56、书不仅是生活,而且是现在、过 去和未 来文化 生活的 源泉。 ——库 法耶夫 57、生命不可能有两次,但许多人连一 次也不 善于度 过。— —吕凯 特 58、问渠哪得清如许,为有源头活水来 。—— 朱熹 59、我的努力求学没有得到别的好处, 只不过 是愈来 愈发觉 自己的 无知。 ——笛 卡儿
- 1、下载文档前请自行甄别文档内容的完整性,平台不提供额外的编辑、内容补充、找答案等附加服务。
- 2、"仅部分预览"的文档,不可在线预览部分如存在完整性等问题,可反馈申请退款(可完整预览的文档不适用该条件!)。
- 3、如文档侵犯您的权益,请联系客服反馈,我们会尽快为您处理(人工客服工作时间:9:00-18:30)。
2、节流膨胀制冷
所谓节流膨胀制冷,就是气体由较高的压 力通过一个节流阀迅速膨胀到较低的压力,由 于过程进行得非常快,来不及与外界发生热交 换,膨胀所需的热量,必须由自身供给,从而 引起温度降低。
但不能任意加压,若压力增高: 对设备材料强度要求增高; 动力消耗增大; 使低温分离系统精馏塔釜温升高,易引起一些
不饱和烃的聚合 使烃类相对挥发度降低,增加了分离的困难。
因此,在深冷分离中要采用经济上合理而技 术上可行的压力,一般为3.54~3.95MPa。
2.多段压缩
(1)裂解气经压缩后,不仅压力升高,而且温度也会升 高,某些烃类尤其是丁二烯之类的二烯烃,容易在较高 的温度下发生聚合和结焦。这些聚合物和结焦物会堵塞 压缩机阀片和磨损气缸,或沉积在叶轮上。
(3)乙烯制冷系统
常压下乙烯的沸点为- 104℃,即用乙烯作制冷 剂可以获-100℃的低温。
乙烯的临界温度为9.9℃,临界压力为5.15MPa, 在此温度之上,不论压力多大,也不能使其液化, 所以不能用普通冷水使之液化。为此,乙烯循环 制冷中的冷凝器需要使用制冷剂冷却。
工业生产中常采用丙烯作制冷剂来冷却乙烯,这 样丙烯的冷冻循环和乙烯冷冻循环制冷组合在一 起,构成乙烯-丙烯复迭制冷。
二、 压缩与制冷
(一)裂解气的压缩
1.压力与温度的关系
根据物质的冷凝温度随压力增加而升高的规律,对 裂解气加压,从而使各组分的冷凝点升高,这既有利于 分离,又可节约冷冻量和低温材料。
ѹ Á¦ /Mpa Π¶È £¬ ¡æ
0.15«¡ 0.3 -140
0.6«¡ 1 -130
3«¡ 4
-96
此外,对裂解气压缩冷却,还能除掉相当量的水份 和重质烃,以减少后继干燥及低温分离的负担。
0.76
0.18 0.09
4.36
原料来源
石脑油裂解 轻柴油裂解
14.09 0.32 26.78 0.41 26.10 5.78 0.48 10.30 0.34 4.85 1.04 4.53 4.98
13.18 0.27 21.24 0.37 29.34 7.58 0.54 11.42 0.36 5.21 0.51 4.58 5.40
(4)乙烯—丙烯复迭制冷循环
(5)三元复迭制冷
用乙烯作制冷剂在正压下操作,不能获得-103℃ 以下的低温。
生产中需要-103℃以下的低温时,可采用沸点更 低的制冷剂,甲烷在常压下沸点是-161.5℃。但 是由于甲烷的临界温度是-82.5℃,若要构成冷 冻循环制冷,需用乙烯作制冷剂为其冷凝器提供 冷量,这样就构成了甲烷-乙烯-丙烯三元复迭 制冷。
任务四 工艺流程的组织——裂解气分离
一、裂解气的组成及分离方法 二、压缩与制冷 三、气体净化 四、裂解气深冷分离
一、 裂解气的组成及分离方法
(一)裂解气的组成
组分ห้องสมุดไป่ตู้
H2 CO+CO2+H2S
CH4 C2H2 C2H4 C2H6 C3H4 C3H6 C3H8
C4 C5 ≥C6 H2O
乙烷裂解
34.0 0.19 4.39 0.19 31.51 24.35
(二)裂解气分离方法
不同压力下某些组分的沸点℃
压力 1.103 10.13 15.19 20.26 25.23 30.39 组分 ×105Pa ×105Pa ×105Pa ×105Pa ×105Pa ×105Pa
H2
-263 -244 -239 -238 -237 -235
CH4 -162 -129 -114 -107 -101 -95
C2H4 -104 -55 -39 -29 -20 -13
C2H6
-86 -33 -18
-7
3
11
C3H6 -47.7
9
29
37
44
47
深冷分离——在 -100℃左右的低温下,将裂 解气中除了氢和甲烷以外的其它烃类全部冷凝下 来。然后利用裂解气中各种烃类的相对挥发度不 同,在合适的温度和压力下,以精馏的方法将各 组分分离开来。
液体的汽化温度(即沸点)是随压力的变化而改 变的,压力越低,相应的汽化温度也越低。
(1)氨蒸汽压缩制冷 (2)丙烯制冷系统 (3)乙烯制冷系统 (4)乙烯—丙烯复迭制冷 (5)三元复迭制冷
(1)氨蒸汽压缩制冷
(1)蒸发 (2)压缩 (3)冷凝 (4)节流膨胀
冷冻剂
冷冻剂本身物理化学性质决定了制冷温度的范 围。如液氨降压到0.098MPa时进行蒸发,其蒸发 温度为-33.4℃。 要满足深冷分离,获得-100℃的低温,必须用 沸点更低的气体作为冷冻剂。
(3)同时,压缩机采用多段压缩也便于在压缩段之 间进行净化与分离。
目前工业上对裂解气大多采用三至五段压缩。 由于裂解炉的废热锅炉副产高压蒸汽,因此多 用蒸汽透平驱动的离心式压缩机。
(二)制冷
1、冷冻循环制冷 2、节流膨胀制冷 3、热泵
1、冷冻循环制冷
制冷原理
冷冻剂自液态汽化时,要从物料中吸收热量, 使物料温度降低。所吸收的热量,在热值上等于 它的汽化潜热。
在石油化工深冷分离中使用最广泛的是氨、丙 烯和乙烯等。对乙烯装置而言,乙烯和丙烯为本 装置产品,已有贮存设施,且乙烯和丙烯已具有 良好的热力学特性,因而均选用乙烯和丙烯作为 制冷剂。
(2)丙烯制冷系统
丙烯常压下沸点为 - 47.72 ℃,用丙烯作 冷冻剂可以得到-40℃以上温度级的冷量。
把丙烯压缩到 l.864MPa 的条件下,丙烯的 冷凝点为45℃,很容易用冷水冷却使之液化。
同时温度升高,还会使压缩机润滑油粘度下降,从而 使压缩机运转不能正常进行。
因此,裂解气压缩后的温度必须要限制,当裂解气中 含有碳四、碳五等重组分时,压缩机出口温度一般不能 超过100℃。
在生产上主要是通过裂解气的多段压缩和冷却相结合 的方法来实现。裂解气段间采用水冷,各段入口38~ 40℃。
(2)采用多段压缩可节省能量,提高效率,减小压 缩比。
深冷操作的系统组成
1、压缩 冷冻系统
2、气体净 化系统
该系统的任务是加压、降温,以保 证分离过程顺利进行。
为了排除对后继操作的干扰,提高 产品的纯度,通常设置有脱酸性气 体、脱水、脱炔和脱一氧化碳等操 作过程。
3、低温精 馏分离系 统
将各组分进行分离并将乙烯、丙烯产 品精制提纯,这是深冷分离的核心。