PCB化学镀铜背光详解
PCB化学镀铜

PCB化学镀铜电镀厂管理软件-懿亮软件--联系电话:137****7345-联系人:罗生一、作用化学镀铜的作用,是在整个印制板上淀积一薄层铜,使之导通孔金属化,以便随后进行孔金属化的电镀时作为导体。
无电镀可能是一种错误的命名,它意指金属沉积时不需要外加电流。
在电镀过程中,电子来自直流电源,使金属离子还原成金属。
化学镀的机理与电镀相类似,但电子来自化学还原剂。
因此可采用化学镀浴,使非导电的表面金属化;因为镀浴内含有其本身的电子源。
电镀浴则不能用于非导电表面,因为电子无法流动。
二、化学镀铜线的工序在许多的工厂生产中,化学镀铜线已实现自动化。
从下列的工序可以看到,化学镀铜线是很容易实现自动化的:1)装板将加工板装好挂具,使浴液能进入孔中。
将加工板斜置或水平放置于挂具上,都能取得较好的效果。
2)清洗(除油),许多专利性的碱性清洗剂可适用于这一操作。
某些含有螯合剂的清洗剂有助于清除氧化物。
必要时可采用电解清洗,则效果更好。
3)冲洗用软化水喷洗或逆流冲洗。
4)铜的蚀刻铜箔制造厂商为防止铜箔表面氧化,在铜箔表面涂有一种防氧化剂。
如果这种防氧化剂未完全清除掉,则在铜箔表面与化学淀积铜之间存在一“可剥层”。
为保证完全清除防氧化剂,应对铜的表面进行轻微的蚀刻。
主要的蚀刻剂是过硫酸铵;虽然用过氧化物--硫酸及氯化铜均可得到满意的结果。
过硫酸铵应配成浓度为2磅/加仑的溶液。
温度控制在70°~100°F 。
温度超过100°F,易造成溶液的化学分解。
浸置时间约2分钟,或浸置足以形成均匀蚀刻。
大量使用时,溶液应每天配制。
蚀刻液的使用寿命为每加仑溶解3~4盎司铜必须记住,具有这种性质的所有蚀刻剂,都含有一定量的重金属;因此,用后必须加以适当的处理。
另一种可以取消蚀刻工序的方法,将在后面加以讨论。
5)冲洗喷洗或逆流冲洗。
6)浸酸—硫酸(按体积计10%)在用过硫酸铵蚀刻后,需要浸酸工序,其目的溶解所有的硫酸铜铵;因为,铜的表面在冲洗槽内形成一层硫酸铜铵薄膜。
PCB化学镀铜背光详解

PCB化学镀铜背光详解线路板 PCB 制作是一个复杂的,多级加工的过程,在生产过程中控制不当 就可能产生很多的报废和品质缺陷。
无论是使用传统的化学铜 PTH 还是新式的 直接电镀 制程,电镀前的通孔和盲孔的金属化是一个复杂的操作过程。
为保证 生产线产量最大化, 使用合理的检测方法和手段来使整个流程良好有效运作是必 要的。
另外,控 制流程中每个处理处理步骤的参数和每个部分处理后的处理效 果的确认评估是一样重要。
这需要对生产线现场有清晰直接的了解:包括对现场 制程难以想象的多次仔 细检查,现场的原材料的不断变化和提供经过确认的各 个制程的控制方法。
对 PTH 制程镀通孔的沉积覆盖率的评估和监控(PTH process)是一个十分 重要的质量控制的检查, 这样可以确保化学铜沉积处理后的镀层可以有效的提供 后续镀通孔的导电和其他性能要求,也可以及时发现生 产线的一些无法预知的 问题及时地在该环节流程进行必要的或者可能返工处理。
定期的进行背光和前光检测来监控化学铜沉积质量和覆盖率,是预防和 有 效减少化学铜制程镀层 不良缺陷的最佳方法。
背光测试可以检查出生产线上化 学铜的沉积不良或者不完整的镀层(背光不良,化学铜沉积不连续),前光测试 可 以看到化学铜沉积覆盖不良区域的位置(如环氧树脂或者玻璃纤维)和化学 铜的沉积状况,亦即环氧树脂,玻璃纤维和内层铜环处的化学铜结合状况。
使用 合理有效 地背光测试方法, 可以有效监控和检测来自PTH生产线的产品的整个 沉铜覆盖率/背光状况的变化,可以使用相对较少检测频率检查出生产线上少量, 不确定的孔 无铜问题,例如可能因为钻孔不良,钻孔毛刺/披锋,钻污等造成的。
取样频率:虽然对生产过程中的每个挂具/挂篮都取样来监控化学铜镀层质量是最好, 但是这也是不太现实的。
每个客户需要根据他们的品质要求来建立一个合理适当 的取样频率,既可以确保生产线在客户的品质要求的制程控制范围,也可以在使 用较少的取样频率和必须的检测成本之间取得平衡。
pcb化学镀铜工艺流程解读(一)
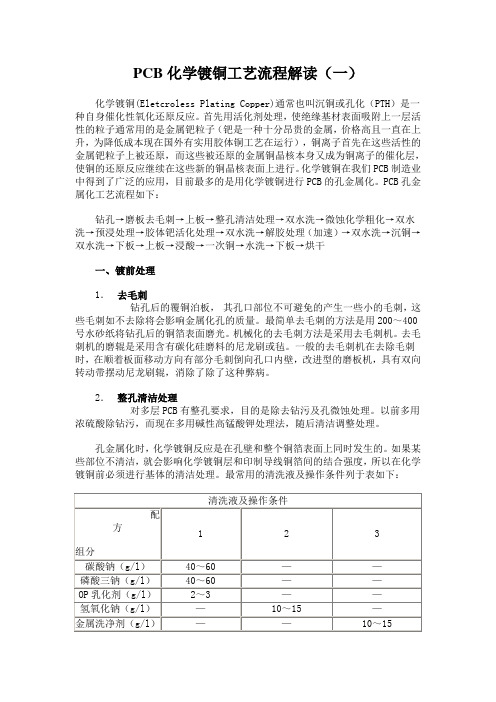
PCB化学镀铜工艺流程解读(一)化学镀铜(Eletcroless Plating Copper)通常也叫沉铜或孔化(PTH)是一种自身催化性氧化还原反应。
首先用活化剂处理,使绝缘基材表面吸附上一层活性的粒子通常用的是金属钯粒子(钯是一种十分昂贵的金属,价格高且一直在上升,为降低成本现在国外有实用胶体铜工艺在运行),铜离子首先在这些活性的金属钯粒子上被还原,而这些被还原的金属铜晶核本身又成为铜离子的催化层,使铜的还原反应继续在这些新的铜晶核表面上进行。
化学镀铜在我们PCB制造业中得到了广泛的应用,目前最多的是用化学镀铜进行PCB的孔金属化。
PCB孔金属化工艺流程如下:钻孔→磨板去毛刺→上板→整孔清洁处理→双水洗→微蚀化学粗化→双水洗→预浸处理→胶体钯活化处理→双水洗→解胶处理(加速)→双水洗→沉铜→双水洗→下板→上板→浸酸→一次铜→水洗→下板→烘干一、镀前处理1.去毛刺钻孔后的覆铜泊板,其孔口部位不可避免的产生一些小的毛刺,这些毛刺如不去除将会影响金属化孔的质量。
最简单去毛刺的方法是用200~400号水砂纸将钻孔后的铜箔表面磨光。
机械化的去毛刺方法是采用去毛刺机。
去毛刺机的磨辊是采用含有碳化硅磨料的尼龙刷或毡。
一般的去毛刺机在去除毛刺时,在顺着板面移动方向有部分毛刺倒向孔口内壁,改进型的磨板机,具有双向转动带摆动尼龙刷辊,消除了除了这种弊病。
2.整孔清洁处理对多层PCB有整孔要求,目的是除去钻污及孔微蚀处理。
以前多用浓硫酸除钻污,而现在多用碱性高锰酸钾处理法,随后清洁调整处理。
孔金属化时,化学镀铜反应是在孔壁和整个铜箔表面上同时发生的。
如果某些部位不清洁,就会影响化学镀铜层和印制导线铜箔间的结合强度,所以在化学镀铜前必须进行基体的清洁处理。
最常用的清洗液及操作条件列于表如下:3.覆铜箔粗化处理利用化学微蚀刻法对铜表面进行浸蚀处理(蚀刻深度为2-3微米),使铜表面产生凹凸不平的微观粗糙带活性的表面,从而保证化学镀铜层和铜箔基体之间有牢固的结合强度。
PCB线路板的电镀铜工艺
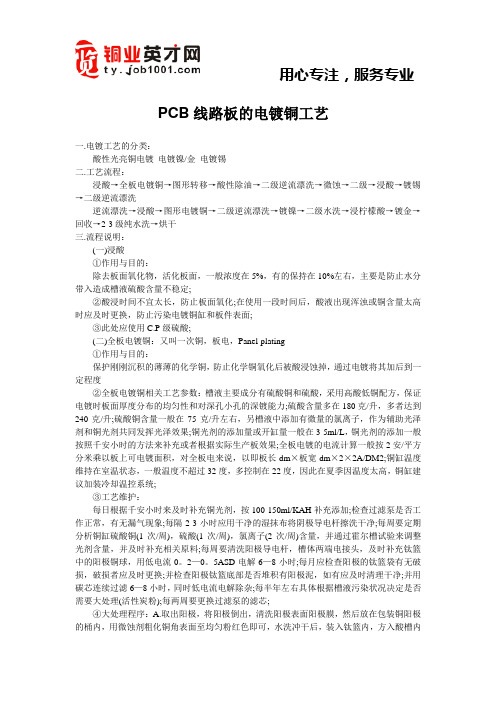
PCB线路板的电镀铜工艺一.电镀工艺的分类:酸性光亮铜电镀电镀镍/金电镀锡二.工艺流程:浸酸→全板电镀铜→图形转移→酸性除油→二级逆流漂洗→微蚀→二级→浸酸→镀锡→二级逆流漂洗逆流漂洗→浸酸→图形电镀铜→二级逆流漂洗→镀镍→二级水洗→浸柠檬酸→镀金→回收→2-3级纯水洗→烘干三.流程说明:(一)浸酸①作用与目的:除去板面氧化物,活化板面,一般浓度在5%,有的保持在10%左右,主要是防止水分带入造成槽液硫酸含量不稳定;②酸浸时间不宜太长,防止板面氧化;在使用一段时间后,酸液出现浑浊或铜含量太高时应及时更换,防止污染电镀铜缸和板件表面;③此处应使用C.P级硫酸;(二)全板电镀铜:又叫一次铜,板电,Panel-plating①作用与目的:保护刚刚沉积的薄薄的化学铜,防止化学铜氧化后被酸浸蚀掉,通过电镀将其加后到一定程度②全板电镀铜相关工艺参数:槽液主要成分有硫酸铜和硫酸,采用高酸低铜配方,保证电镀时板面厚度分布的均匀性和对深孔小孔的深镀能力;硫酸含量多在180克/升,多者达到240克/升;硫酸铜含量一般在75克/升左右,另槽液中添加有微量的氯离子,作为辅助光泽剂和铜光剂共同发挥光泽效果;铜光剂的添加量或开缸量一般在3-5ml/L,铜光剂的添加一般按照千安小时的方法来补充或者根据实际生产板效果;全板电镀的电流计算一般按2安/平方分米乘以板上可电镀面积,对全板电来说,以即板长dm×板宽dm×2×2A/DM2;铜缸温度维持在室温状态,一般温度不超过32度,多控制在22度,因此在夏季因温度太高,铜缸建议加装冷却温控系统;③工艺维护:每日根据千安小时来及时补充铜光剂,按100-150ml/KAH补充添加;检查过滤泵是否工作正常,有无漏气现象;每隔2-3小时应用干净的湿抹布将阴极导电杆擦洗干净;每周要定期分析铜缸硫酸铜(1次/周),硫酸(1次/周),氯离子(2次/周)含量,并通过霍尔槽试验来调整光剂含量,并及时补充相关原料;每周要清洗阳极导电杆,槽体两端电接头,及时补充钛篮中的阳极铜球,用低电流0。
PCB水平电镀技术介绍
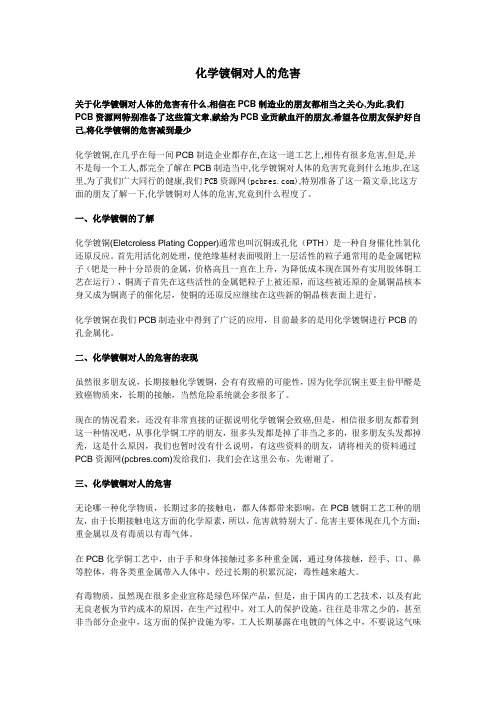
化学镀铜对人的危害关于化学镀铜对人体的危害有什么,相信在PCB制造业的朋友都相当之关心,为此,我们PCB资源网特别准备了这些篇文章,献给为PCB业贡献血汗的朋友,希望各位朋友保护好自己,将化学镀铜的危害减到最少化学镀铜,在几乎在每一间PCB制造企业都存在,在这一道工艺上,相传有很多危害,但是,并不是每一个工人,都完全了解在PCB制造当中,化学镀铜对人体的危害究竟到什么地步,在这里,为了我们广大同行的健康,我们PCB资源网(),特别准备了这一篇文章,比这方面的朋友了解一下,化学镀铜对人体的危害,究竟到什么程度了。
一、化学镀铜的了解化学镀铜(Eletcroless Plating Copper)通常也叫沉铜或孔化(PTH)是一种自身催化性氧化还原反应。
首先用活化剂处理,使绝缘基材表面吸附上一层活性的粒子通常用的是金属钯粒子(钯是一种十分昂贵的金属,价格高且一直在上升,为降低成本现在国外有实用胶体铜工艺在运行),铜离子首先在这些活性的金属钯粒子上被还原,而这些被还原的金属铜晶核本身又成为铜离子的催化层,使铜的还原反应继续在这些新的铜晶核表面上进行。
化学镀铜在我们PCB制造业中得到了广泛的应用,目前最多的是用化学镀铜进行PCB的孔金属化。
二、化学镀铜对人的危害的表现虽然很多朋友说,长期接触化学镀铜,会有有致癌的可能性,因为化学沉铜主要主份甲醛是致癌物质来,长期的接触,当然危险系统就会多很多了。
现在的情况看来,还没有非常直接的证据说明化学镀铜会致癌,但是,相信很多朋友都看到这一种情况吧,从事化学铜工序的朋友,很多头发都是掉了非当之多的,很多朋友头发都掉禿,这是什么原因,我们也暂时没有什么说明,有这些资料的朋友,请将相关的资料通过PCB资源网()发给我们,我们会在这里公布,先谢谢了。
三、化学镀铜对人的危害无论哪一种化学物质,长期过多的接触电,都人体都带来影响,在PCB镀铜工艺工种的朋友,由于长期接触电这方面的化学原素,所以,危害就特别大了。
化学镀铜工艺流程解读
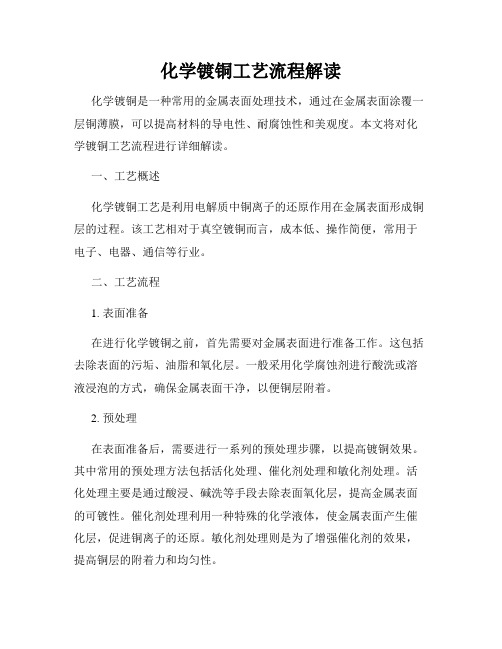
化学镀铜工艺流程解读化学镀铜是一种常用的金属表面处理技术,通过在金属表面涂覆一层铜薄膜,可以提高材料的导电性、耐腐蚀性和美观度。
本文将对化学镀铜工艺流程进行详细解读。
一、工艺概述化学镀铜工艺是利用电解质中铜离子的还原作用在金属表面形成铜层的过程。
该工艺相对于真空镀铜而言,成本低、操作简便,常用于电子、电器、通信等行业。
二、工艺流程1. 表面准备在进行化学镀铜之前,首先需要对金属表面进行准备工作。
这包括去除表面的污垢、油脂和氧化层。
一般采用化学腐蚀剂进行酸洗或溶液浸泡的方式,确保金属表面干净,以便铜层附着。
2. 预处理在表面准备后,需要进行一系列的预处理步骤,以提高镀铜效果。
其中常用的预处理方法包括活化处理、催化剂处理和敏化剂处理。
活化处理主要是通过酸浸、碱洗等手段去除表面氧化层,提高金属表面的可镀性。
催化剂处理利用一种特殊的化学液体,使金属表面产生催化层,促进铜离子的还原。
敏化剂处理则是为了增强催化剂的效果,提高铜层的附着力和均匀性。
3. 镀铜预处理完成后,金属样品进入化学镀铜槽中进行镀铜处理。
镀铜槽中含有铜离子和其他辅助剂,通过电流的作用,铜离子被还原成金属铜,沉积在金属表面形成铜层。
镀铜的过程中需要控制电流密度、温度和镀铜时间等因素,以获得理想的镀层厚度和质量。
4. 后处理镀铜完成后,需要进行一些后处理工作。
通常包括清洗、除漆和抛光。
清洗是为了去除残留的电解质和杂质,确保铜层的纯净度。
除漆则是为了去除镀铜过程中可能产生的涂层或污渍,使铜层表面更加平整。
抛光可以进一步改善铜层的外观,提高光亮度。
三、工艺控制在化学镀铜工艺中,需要进行一定的工艺控制,以保证镀层的质量和一致性。
其中关键的工艺参数包括电流密度、温度、PH值和镀铜时间。
电流密度控制决定了铜层的厚度和均匀性,温度控制可以影响镀铜速度和结晶形态,PH值控制可以调节溶液中铜离子的浓度和还原性,而镀铜时间则是决定铜层厚度的重要因素。
四、应用领域化学镀铜工艺广泛应用于电子、电器、通信等领域。
电路板镀铜工艺-解释说明

电路板镀铜工艺-概述说明以及解释1.引言1.1 概述概述:电路板镀铜工艺是电子制造过程中至关重要的一环,它是将铜覆盖在电路板表面的必要步骤。
镀铜工艺能够提高电路板的导电性和耐腐蚀性,保障电路板稳定可靠地工作。
在现代电子行业中,电路板镀铜工艺已经成为了一项常见且不可或缺的工艺环节。
本文将详细介绍电路板镀铜工艺的流程、应用及其重要性,旨在帮助读者更全面地了解这一工艺过程,从而更好地掌握电子制造中的关键技术。
"1.2 文章结构":本文主要分为引言、正文和结论三个部分。
在引言部分中,将概述电路板镀铜工艺的重要性和应用,以及本文的目的和结构。
正文部分将详细介绍电路板镀铜工艺的概述、工艺流程和应用。
结论部分将总结电路板镀铜工艺的重要性,并展望未来的发展方向。
整个文章将围绕电路板镀铜工艺展开阐述,旨在为读者提供全面深入的了解和认识。
1.3 目的:本文旨在探讨电路板镀铜工艺的实际应用及工艺流程,以帮助读者深入理解电路板制造过程中镀铜的重要性和作用。
通过详细介绍镀铜工艺的概述、流程和应用,读者将能够了解电路板镀铜的原理和技术要点,从而更好地掌握电路板制造的技术和方法,促进电子产品制造领域的进步与发展。
同时,本文还旨在引起读者对电路板镀铜工艺的重视,鼓励更多的研究与实践,推动电路板制造行业的持续创新和发展。
2.正文2.1 电路板镀铜工艺概述电路板镀铜工艺是电子制造领域中一项至关重要的工艺技术,它在印刷电路板制造过程中起着至关重要的作用。
在电路板制造中,为了实现电气连接和传导,需要在基板上镀上一层导电性良好的铜层。
这一步骤就是电路板的镀铜工艺。
电路板镀铜工艺通过将左右的电路板浸入含有铜离子的溶液中,利用电化学原理,在电路板表面沉积出均匀的铜层。
这样一来,就能够实现电路板各个电路之间的连通,确保电路板的正常工作。
在实际的制造过程中,电路板镀铜工艺受到许多因素的影响,如温度、电流密度、镀液成分等。
通过合理的控制这些参数,可以保证铜层的质量均匀性和附着力,从而确保电路板的可靠性和稳定性。
PCB水平电镀技术介绍

化学镀铜对人的危害关于化学镀铜对人体的危害有什么,相信在PCB制造业的朋友都相当之关心,为此,我们PCB资源网特别准备了这些篇文章,献给为PCB业奉献血汗的朋友,希望各位朋友保护好自己,将化学镀铜的危害减到最少化学镀铜,在几乎在每一间PCB制造企业都存在,在这一道工艺上,相传有很多危害,但是,并不是每一个工人,都完全了解在PCB制造当中,化学镀铜对人体的危害究竟到什么地步,在这里,为了我们广阔同行的健康,我们PCB资源网〔pcbres 〕,特别准备了这一篇文章,比这方面的朋友了解一下,化学镀铜对人体的危害,究竟到什么程度了。
一、化学镀铜的了解化学镀铜〔Eletcroless Plating Copper〕通常也叫沉铜或孔化〔PTH〕是一种自身催化性氧化复原反响。
首先用活化剂处理,使绝缘基材外表吸附上一层活性的粒子通常用的是金属钯粒子〔钯是一种十分昂贵的金属,价格高且一直在上升,为降低本钱现在国外有实用胶体铜工艺在运行〕,铜离子首先在这些活性的金属钯粒子上被复原,而这些被复原的金属铜晶核本身又成为铜离子的催化层,使铜的复原反响继续在这些新的铜晶核外表上进行。
化学镀铜在我们PCB制造业中得到了广泛的应用,目前最多的是用化学镀铜进行PCB的孔金属化。
二、化学镀铜对人的危害的表现虽然很多朋友说,长期接触化学镀铜,会有有致癌的可能性,因为化学沉铜主要主份甲醛是致癌物质来,长期的接触,当然危险系统就会多很多了。
现在的情况看来,还没有非常直接的证据说明化学镀铜会致癌,但是,相信很多朋友都看到这一种情况吧,从事化学铜工序的朋友,很多头发都是掉了非当之多的,很多朋友头发都掉禿,这是什么原因,我们也暂时没有什么说明,有这些资料的朋友,请将相关的资料通过PCB资源网〔pcbres 〕发给我们,我们会在这里公布,先谢谢了。
三、化学镀铜对人的危害无论哪一种化学物质,长期过多的接触电,都人体都带来影响,在PCB镀铜工艺工种的朋友,由于长期接触电这方面的化学原素,所以,危害就特别大了。
PCB电镀工艺介绍
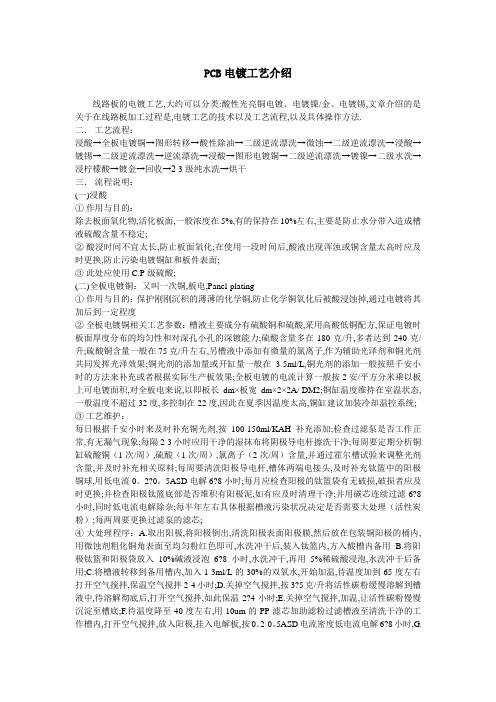
PCB电镀工艺介绍线路板的电镀工艺,大约可以分类:酸性光亮铜电镀、电镀镍/金、电镀锡,文章介绍的是关于在线路板加工过程是,电镀工艺的技术以及工艺流程,以及具体操作方法.二.工艺流程:浸酸→全板电镀铜→图形转移→酸性除油→二级逆流漂洗→微蚀→二级逆流漂洗→浸酸→镀锡→二级逆流漂洗→逆流漂洗→浸酸→图形电镀铜→二级逆流漂洗→镀镍→二级水洗→浸柠檬酸→镀金→回收→2-3级纯水洗→烘干三.流程说明:(一)浸酸①作用与目的:除去板面氧化物,活化板面,一般浓度在5%,有的保持在10%左右,主要是防止水分带入造成槽液硫酸含量不稳定;②酸浸时间不宜太长,防止板面氧化;在使用一段时间后,酸液出现浑浊或铜含量太高时应及时更换,防止污染电镀铜缸和板件表面;③此处应使用C.P级硫酸;(二)全板电镀铜:又叫一次铜,板电,Panel-plating①作用与目的:保护刚刚沉积的薄薄的化学铜,防止化学铜氧化后被酸浸蚀掉,通过电镀将其加后到一定程度②全板电镀铜相关工艺参数:槽液主要成分有硫酸铜和硫酸,采用高酸低铜配方,保证电镀时板面厚度分布的均匀性和对深孔小孔的深镀能力;硫酸含量多在180克/升,多者达到240克/升;硫酸铜含量一般在75克/升左右,另槽液中添加有微量的氯离子,作为辅助光泽剂和铜光剂共同发挥光泽效果;铜光剂的添加量或开缸量一般在3-5ml/L,铜光剂的添加一般按照千安小时的方法来补充或者根据实际生产板效果;全板电镀的电流计算一般按2安/平方分米乘以板上可电镀面积,对全板电来说,以即板长dm×板宽dm×2×2A/ DM2;铜缸温度维持在室温状态,一般温度不超过32度,多控制在22度,因此在夏季因温度太高,铜缸建议加装冷却温控系统;③工艺维护:每日根据千安小时来及时补充铜光剂,按100-150ml/KAH补充添加;检查过滤泵是否工作正常,有无漏气现象;每隔2-3小时应用干净的湿抹布将阴极导电杆擦洗干净;每周要定期分析铜缸硫酸铜(1次/周),硫酸(1次/周),氯离子(2次/周)含量,并通过霍尔槽试验来调整光剂含量,并及时补充相关原料;每周要清洗阳极导电杆,槽体两端电接头,及时补充钛篮中的阳极铜球,用低电流0。
PCB化学镀铜工艺流程

PCB化学镀铜工艺流程产品检验标准2010-02-03 18:26:16 阅读4 评论0 字号:大中小订阅PCB化学镀铜工艺流程解读(一)化学镀铜(Eletcroless Plating Copper)通常也叫沉铜或孔化(PTH)是一种自身催化性氧化还原反应。
首先用活化剂处理,使绝缘基材表面吸附上一层活性的粒子通常用的是金属钯粒子(钯是一种十分昂贵的金属,价格高且一直在上升,为降低成本现在国外有实用胶体铜工艺在运行),铜离子首先在这些活性的金属钯粒子上被还原,而这些被还原的金属铜晶核本身又成为铜离子的催化层,使铜的还原反应继续在这些新的铜晶核表面上进行。
化学镀铜在我们PCB制造业中得到了广泛的应用,目前最多的是用化学镀铜进行PCB的孔金属化。
PCB孔金属化工艺流程如下:钻孔→磨板去毛刺→上板→整孔清洁处理→双水洗→微蚀化学粗化→双水洗→预浸处理→胶体钯活化处理→双水洗→解胶处理(加速)→双水洗→沉铜→双水洗→下板→上板→浸酸→一次铜→水洗→下板→烘干一、镀前处理1.去毛刺钻孔后的覆铜泊板,其孔口部位不可避免的产生一些小的毛刺,这些毛刺如不去除将会影响金属化孔的质量。
最简单去毛刺的方法是用200~400号水砂纸将钻孔后的铜箔表面磨光。
机械化的去毛刺方法是采用去毛刺机。
去毛刺机的磨辊是采用含有碳化硅磨料的尼龙刷或毡。
一般的去毛刺机在去除毛刺时,在顺着板面移动方向有部分毛刺倒向孔口内壁,改进型的磨板机,具有双向转动带摆动尼龙刷辊,消除了除了这种弊病。
2.整孔清洁处理对多层PCB有整孔要求,目的是除去钻污及孔微蚀处理。
以前多用浓硫酸除钻污,而现在多用碱性高锰酸钾处理法,随后清洁调整处理。
孔金属化时,化学镀铜反应是在孔壁和整个铜箔表面上同时发生的。
如果某些部位不清洁,就会影响化学镀铜层和印制导线铜箔间的结合强度,所以在化学镀铜前必须进行基体的清洁处理。
最常用的清洗液及操作条件列于表如下:3.覆铜箔粗化处理利用化学微蚀刻法对铜表面进行浸蚀处理(蚀刻深度为2-3微米),使铜表面产生凹凸不平的微观粗糙带活性的表面,从而保证化学镀铜层和铜箔基体之间有牢固的结合强度。
PCB水平电镀技术介绍

化学镀铜对人的危害关于化学镀铜对人体的危害有什么,相信在PCB制造业的朋友都相当之关心,为此,我们PCB资源网特别准备了这些篇文章,献给为PCB业贡献血汗的朋友,希望各位朋友保护好自己,将化学镀铜的危害减到最少化学镀铜,在几乎在每一间PCB制造企业都存在,在这一道工艺上,相传有很多危害,但是,并不是每一个工人,都完全了解在PCB制造当中,化学镀铜对人体的危害究竟到什么地步,在这里,为了我们广大同行的健康,我们PCB资源网(),特别准备了这一篇文章,比这方面的朋友了解一下,化学镀铜对人体的危害,究竟到什么程度了。
一、化学镀铜的了解化学镀铜(Eletcroless Plating Copper)通常也叫沉铜或孔化(PTH)是一种自身催化性氧化还原反应。
首先用活化剂处理,使绝缘基材表面吸附上一层活性的粒子通常用的是金属钯粒子(钯是一种十分昂贵的金属,价格高且一直在上升,为降低成本现在国外有实用胶体铜工艺在运行),铜离子首先在这些活性的金属钯粒子上被还原,而这些被还原的金属铜晶核本身又成为铜离子的催化层,使铜的还原反应继续在这些新的铜晶核表面上进行。
化学镀铜在我们PCB制造业中得到了广泛的应用,目前最多的是用化学镀铜进行PCB的孔金属化。
二、化学镀铜对人的危害的表现虽然很多朋友说,长期接触化学镀铜,会有有致癌的可能性,因为化学沉铜主要主份甲醛是致癌物质来,长期的接触,当然危险系统就会多很多了。
现在的情况看来,还没有非常直接的证据说明化学镀铜会致癌,但是,相信很多朋友都看到这一种情况吧,从事化学铜工序的朋友,很多头发都是掉了非当之多的,很多朋友头发都掉禿,这是什么原因,我们也暂时没有什么说明,有这些资料的朋友,请将相关的资料通过PCB资源网()发给我们,我们会在这里公布,先谢谢了。
三、化学镀铜对人的危害无论哪一种化学物质,长期过多的接触电,都人体都带来影响,在PCB镀铜工艺工种的朋友,由于长期接触电这方面的化学原素,所以,危害就特别大了。
pcb化学镀铜工艺流程解读

PCB 化学镀铜工艺流程解读〔二〕三、化学镀铜1.化学镀铜液目前应用比较广泛的配方是下表所列举的几种使用不同样络合剂分类的化学镀铜液,配方 1 为洒石酸钾钠络合剂,其优点是化学镀铜液的操作温度低,使用方便,但牢固性差,镀铜层脆性大,镀铜时间要控制合适,不然由于脆性的镀铜层太厚会影响镀层与基材的结合强度。
配方 2 为 EDTA·2Na 络合剂,其使用温度高,聚积速率较高,镀液的牢固性较好,但本钱较高。
配方 3 为双络合剂,介于两者之间。
表中常用的化学镀铜溶液及操作条件组份配方123硫酸铜〔 g/L 〕14108~24酒石酸钾钠〔 g/L 〕40—7~21 EDTA二钠盐〔 g/L 〕—40~27氢氧化钠〔 g/L 〕2012~硫脲〔 g/L 〕//亚铁氰化钾〔 g/L 〕/~aa′-联吡啶〔 g/L 〕/~甲醛〔 ml/L 〕10~151010~15工作温度〔℃〕21~2550~6035~40聚积速率〔μ m/h〕4~51~2PH值;操作条件12~13;空气搅拌12~;空气搅拌连12~13;空气搅拌2连续过滤续过滤连续过滤≤ 1≤1≤ 2工作负荷〔 dm/L 〕2.化学镀铜溶液的牢固性(1〕化学镀铜溶液不牢固的原因在催化剂存在的条件下,化学镀铜的主要反响以下:在化学镀铜溶液中除上式的主反响以外,还存在以下几个副反响。
a.甲醛的歧化反响-在浓碱条件下,甲醛一局部被氧化成为甲酸,另一局部被复原成甲醇,反响式为甲醛的歧视化反响除造成甲醛过分的耗资外,b.在碱性镀铜溶液中,甲醛复原一局部还会使镀液过早的" 老化 " ,使镀液不牢固。
Cu2+为 Cu+,其反响式为反响式〔 5-3 〕所生成的Cu2O在碱性溶液中是微溶的:Cu2O+ H2O ===2Cu++2 OH-- (5-4)反响 (5-4)中出现的铜Cu+特别简单发生歧化反响2Cu+=== Cu0↓+ Cu2+ 〔 5-5 〕反响式〔 5- 5〕所生成的铜是极微小的微粒,它们无规那么地分别在化学镀铜液中,这些铜微粒拥有催化性,若是对这些铜微粒不进行控制,那么迅速地以致整个镀液分解,这是造成化学镀铜液不牢固的主要原因。
PCB电镀-化铜

PTH 孔金属化 传统的 PTH
去钻污 – Securiganth P/P500/MV/BLG
工艺流程 – 功能
只有三个工艺步骤:
溶胀 高锰酸盐 蚀刻 还原
溶胀
使树脂易被高锰酸盐蚀刻攻击
高锰酸盐蚀刻
去除钻污和树脂
还原
除去降解产物和清洁/处理表面. (清洁 / 蚀刻玻璃)
去钻污 – Securiganth P/P500/MV/BLG
目的:将可感光的干膜贴附于铜 面上
目的:将设计之影像图形,转移至 基板的干膜上
目的:将没有曝到光之干膜去除
目的:将显影后之线路镀满
目的:将多余的干膜去除
目的:将化铜层蚀刻掉
雷射成孔及全板面式除胶渣
ABF熟化后的膜厚约在30~70μm之间,薄板者以30~40μm较常用一般 双面CO2雷射完工的2~4mil烧孔,其孔形都可呈现良好的倒锥状。无 铜面之全板除胶渣(Desmearing)后,其全板面与孔壁均可形成极为粗糙 的外观,化学铜之后对细线路干膜的附着力将有帮助。
印刷线路板化铜电镀工艺及技术
Contents
1.线路板的结构及技术要求
2.线路板线路形成工艺介绍 3.线路板曝光工艺 4.线路板显影/蚀刻/去膜工艺 5.PCB 化铜工艺介绍 6.PCB 电镀工艺介绍
多层PCB的结构
1.Build-up层线宽 2.Build-up层线距 3.Core层线宽 4.Core层线距 5.盲孔孔径 6.盲孔内层孔环
去钻污 – Securiganth P/P500/MV/BLG
高锰酸盐蚀刻 – 溶胀之后 – 不经过蚀刻
去钻污 – Securiganth P/P500/MV/BLG
PCB化学镀铜工艺
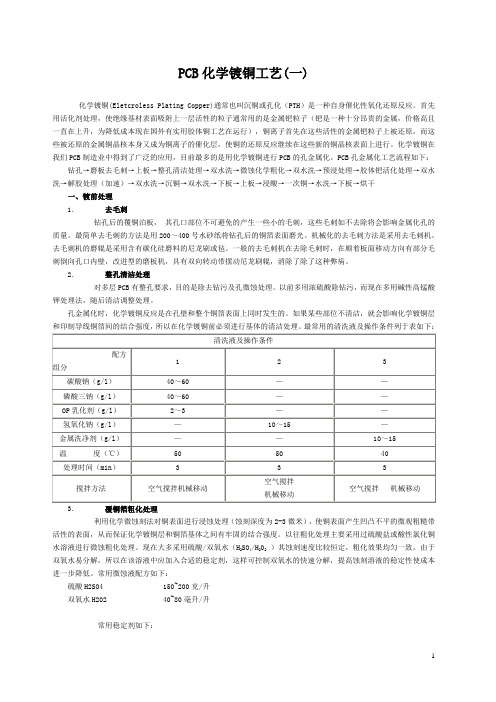
PCB化学镀铜工艺(一)化学镀铜(Eletcroless Plating Copper)通常也叫沉铜或孔化(PTH)是一种自身催化性氧化还原反应。
首先用活化剂处理,使绝缘基材表面吸附上一层活性的粒子通常用的是金属钯粒子(钯是一种十分昂贵的金属,价格高且一直在上升,为降低成本现在国外有实用胶体铜工艺在运行),铜离子首先在这些活性的金属钯粒子上被还原,而这些被还原的金属铜晶核本身又成为铜离子的催化层,使铜的还原反应继续在这些新的铜晶核表面上进行。
化学镀铜在我们PCB制造业中得到了广泛的应用,目前最多的是用化学镀铜进行PCB的孔金属化。
PCB孔金属化工艺流程如下:钻孔→磨板去毛刺→上板→整孔清洁处理→双水洗→微蚀化学粗化→双水洗→预浸处理→胶体钯活化处理→双水洗→解胶处理(加速)→双水洗→沉铜→双水洗→下板→上板→浸酸→一次铜→水洗→下板→烘干一、镀前处理1.去毛刺钻孔后的覆铜泊板,其孔口部位不可避免的产生一些小的毛刺,这些毛刺如不去除将会影响金属化孔的质量。
最简单去毛刺的方法是用200~400号水砂纸将钻孔后的铜箔表面磨光。
机械化的去毛刺方法是采用去毛刺机。
去毛刺机的磨辊是采用含有碳化硅磨料的尼龙刷或毡。
一般的去毛刺机在去除毛刺时,在顺着板面移动方向有部分毛刺倒向孔口内壁,改进型的磨板机,具有双向转动带摆动尼龙刷辊,消除了除了这种弊病。
2.整孔清洁处理对多层PCB有整孔要求,目的是除去钻污及孔微蚀处理。
以前多用浓硫酸除钻污,而现在多用碱性高锰酸钾处理法,随后清洁调整处理。
孔金属化时,化学镀铜反应是在孔壁和整个铜箔表面上同时发生的。
如果某些部位不清洁,就会影响化学镀铜层和印制导线铜箔间的结合强度,所以在化学镀铜前必须进行基体的清洁处理。
最常用的清洗液及操作条件列于表如下:3.覆铜箔粗化处理利用化学微蚀刻法对铜表面进行浸蚀处理(蚀刻深度为2-3微米),使铜表面产生凹凸不平的微观粗糙带活性的表面,从而保证化学镀铜层和铜箔基体之间有牢固的结合强度。
PCB化学镀铜工艺流程解读

PCB化学镀铜工艺流程解读1.准备工作:在进行化学镀铜之前,需要准备一个干燥且无油污的印刷电路板。
一般通过去除油污、清洗、脱脂等步骤来完成准备工作。
2.除锈处理:在准备好的印刷电路板上涂覆一层除锈剂。
除锈剂会溶解表面的氧化铜,使得铜基材表面更容易被导电铜涂层覆盖。
3.化学镀铜处理:将准备好的印刷电路板浸泡在含有化学镀铜液的槽中。
在槽中,有两个极板,一个正极板(被镀件电极)和一个负极板(作为阴极)。
通过施加一定的电流,使得金属离子在正极板上还原并沉积成为金属铜。
4.电解液重置:在化学镀铜处理完成后,需要将电解液中的金属离子浓度恢复到初始状态,以便下一次的处理。
通常是通过电解液的过滤或补充金属离子来实现。
5.清洗与去除阻焊:在化学镀铜处理完成后,需要对印刷电路板进行清洗,以去除可能残留在表面的污垢和化学剂。
同时,如果印刷电路板上有阻焊层,在此步骤也需要去除阻焊层。
6.检测与修复:在完成清洗和去除阻焊后,需要对印刷电路板进行检测,以发现可能存在的缺陷,如导线断路、短路等。
对于发现的问题需要进行修复处理。
7.镀金:在完成检测和修复后,如果需要在印刷电路板的一些区域镀金,可以通过电化学方法将金属离子沉积在该区域上。
8.最终清洗和检测:在完成镀金后,需要对印刷电路板进行最后的清洗,以确保表面干净无油污。
同时还需要进行一次终检,以确保电路板的质量满足要求。
总结:PCB化学镀铜工艺流程是一个多步骤的过程,通过这些步骤,可以在印刷电路板上形成一层铜薄膜,提高导电性和保护电路。
每个步骤都非常重要,需要严格控制工艺参数和操作条件。
只有有效地执行每个步骤,才能得到高质量的印刷电路板。
化学镀铜
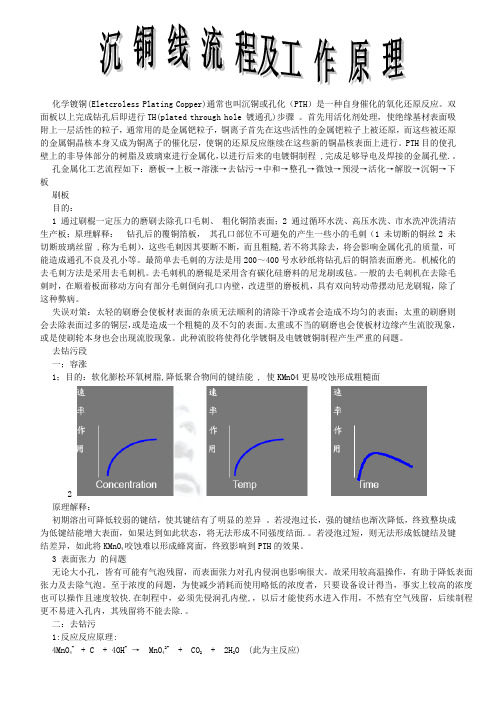
化学镀铜(Eletcroless Plating Copper)通常也叫沉铜或孔化(PTH)是一种自身催化的氧化还原反应。
双面板以上完成钻孔后即进行TH(plated through hole 镀通孔)步骤。
首先用活化剂处理,使绝缘基材表面吸附上一层活性的粒子,通常用的是金属钯粒子,铜离子首先在这些活性的金属钯粒子上被还原,而这些被还原的金属铜晶核本身又成为铜离子的催化层,使铜的还原反应继续在这些新的铜晶核表面上进行。
PTH目的使孔壁上的非导体部分的树脂及玻璃束进行金属化,以进行后来的电镀铜制程 ,完成足够导电及焊接的金属孔壁.。
孔金属化工艺流程如下:磨板→上板→溶涨→去钻污→中和→整孔→微蚀→预浸→活化→解胶→沉铜→下板刷板目的:1 通过刷棍一定压力的磨刷去除孔口毛刺、粗化铜箔表面;2 通过循环水洗、高压水洗、市水洗冲洗清洁生产板;原理解释:钻孔后的覆铜箔板,其孔口部位不可避免的产生一些小的毛刺(1 未切断的铜丝2 未切断玻璃丝留 ,称为毛刺),这些毛刺因其要断不断,而且粗糙,若不将其除去,将会影响金属化孔的质量,可能造成通孔不良及孔小等。
最简单去毛刺的方法是用200~400号水砂纸将钻孔后的铜箔表面磨光。
机械化的去毛刺方法是采用去毛刺机。
去毛刺机的磨辊是采用含有碳化硅磨料的尼龙刷或毡。
一般的去毛刺机在去除毛刺时,在顺着板面移动方向有部分毛刺倒向孔口内壁,改进型的磨板机,具有双向转动带摆动尼龙刷辊,除了这种弊病。
失误对策:太轻的刷磨会使板材表面的杂质无法顺利的清除干净或者会造成不均匀的表面;太重的刷磨则会去除表面过多的铜层,或是造成一个粗糙的及不匀的表面。
太重或不当的刷磨也会使板材边缘产生流胶现象,或是使刷轮本身也会出现流胶现象。
此种流胶将使得化学镀铜及电镀镀铜制程产生严重的问题。
去钻污段一;容涨1;目的:软化膨松环氧树脂,降低聚合物间的键结能 , 使KMnO4更易咬蚀形成粗糙面2原理解释:初期溶出可降低较弱的键结,使其键结有了明显的差异。
PCB化学镀铜的问题与对策

氢氧化钠的来源 也必须使用试药级的氢氧化钠。因为许多工业级的氢氧化钠,其中含有铁离子、氯离子及其 他种类的杂质,这些都会对于槽液造成影响,应该尽量避免使用。
空气搅拌 槽液无论是在操作或是置放之时,均应随时保持在空气搅拌的情形。空气通入的流量不要过 多,否则将会产生过多的泡沫(Foaming),而使槽液的性质发生变化,适当的空气流量已经 足够维持槽液的安定。
甲醛的来源 必须使用试药级的甲醛,因为许多工业级的甲醛中含有铁离子、安定剂或是胶状(Colloidal) 的杂质等,这些杂质都会对槽液与化学铜层造成伤害,所以应尽量避免使用不纯的甲醛。
槽液成份的补充频率 经常以连续及少量的添加方式较佳,因为如果一次大量地进行添加,过量的安定剂会使槽液 产生强烈的冲击。两大部分的补充槽液因该分开进行添加,然后迅速搅拌均匀。任何一次的 添加量勿超过原来槽液体积的 10%以上,因为如此将会导致槽液产生不安定或是过于安定的 现象。如果槽液的浓度低于标准值的 70%以下的时候,则须暂时停止槽液的操作,而来进行 补充添加的工作,待其浓度达到标准数值的 90%以上的时候,即可继续进行槽液的操作。
槽液补充管线的配置 两大部份槽液的管线配置必须正确适当。除了应该分开配置之外,含有铜盐的管线,必须配 在槽体之中间部位,而含有氢氧化钠的管线,必须配在槽体的底部,如此两者才会迅速混合 均匀,而不会发生结块(Clot)与沉积的现象。
清洁剂/整孔剂的使用温度、浓度与时间 正确适当的清洁与整孔处理是必须的。温度过低或是浓度不够的药液,均不适合槽液的操作, 将会使得沉积镀层发生剥离与脱落的现象。再者,槽液当中所积累的铜离子浓度,亦须严格 地加以管制。
PCB沉铜背光判定标准
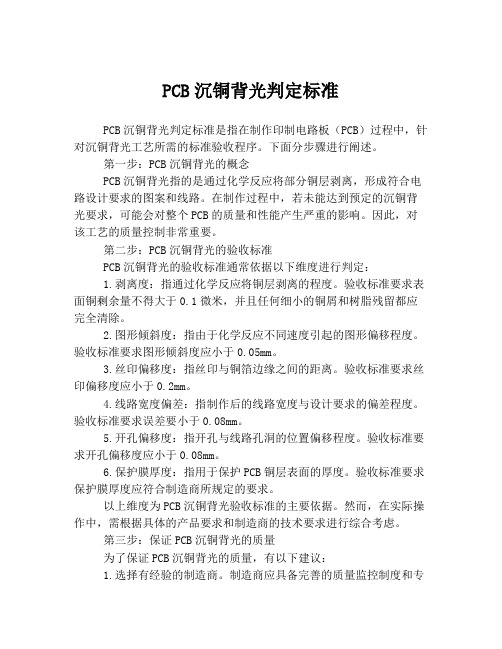
PCB沉铜背光判定标准PCB沉铜背光判定标准是指在制作印制电路板(PCB)过程中,针对沉铜背光工艺所需的标准验收程序。
下面分步骤进行阐述。
第一步:PCB沉铜背光的概念PCB沉铜背光指的是通过化学反应将部分铜层剥离,形成符合电路设计要求的图案和线路。
在制作过程中,若未能达到预定的沉铜背光要求,可能会对整个PCB的质量和性能产生严重的影响。
因此,对该工艺的质量控制非常重要。
第二步:PCB沉铜背光的验收标准PCB沉铜背光的验收标准通常依据以下维度进行判定:1.剥离度:指通过化学反应将铜层剥离的程度。
验收标准要求表面铜剩余量不得大于0.1微米,并且任何细小的铜屑和树脂残留都应完全清除。
2.图形倾斜度:指由于化学反应不同速度引起的图形偏移程度。
验收标准要求图形倾斜度应小于0.05mm。
3.丝印偏移度:指丝印与铜箔边缘之间的距离。
验收标准要求丝印偏移度应小于0.2mm。
4.线路宽度偏差:指制作后的线路宽度与设计要求的偏差程度。
验收标准要求误差要小于0.08mm。
5.开孔偏移度:指开孔与线路孔洞的位置偏移程度。
验收标准要求开孔偏移度应小于0.08mm。
6.保护膜厚度:指用于保护PCB铜层表面的厚度。
验收标准要求保护膜厚度应符合制造商所规定的要求。
以上维度为PCB沉铜背光验收标准的主要依据。
然而,在实际操作中,需根据具体的产品要求和制造商的技术要求进行综合考虑。
第三步:保证PCB沉铜背光的质量为了保证PCB沉铜背光的质量,有以下建议:1.选择有经验的制造商。
制造商应具备完善的质量监控制度和专业的技术团队,确保PCB沉铜背光技术的合理性和稳定性。
2.建立有效的质量控管制流程。
在制造过程中,应当建立科学、标准的质量控管制流程,明确每个环节的质量标准、作业指导、操作流程等。
3.严格实行质量检测。
通过严格的质量检测,及时发现和处理制造环节中存在的问题。
同时,还可以根据检测结果进行质量改进和优化。
总之,PCB沉铜背光技术对于制造高质量的印制电路板至关重要。
PCB背光标准

PCB背光标准背光标准图8.5 9 9.5 105 6 7 81 2 3 4背光级分类及说明:级数分类说明10 3个或5个孔必须完全⿊没有任何亮点或⼩的亮点。
2个孔可以有1个⼩的亮点。
9.5 每5个孔最多可以有5个亮点9.0 每5个孔最多可以有20个⼩亮点8举例1:每5个孔最多可以有40个⼩亮点举例2:每5个孔内有1个亮点与5个亮点举例3:每5个孔内有2个横向纤维横向纤维点,没有⼩亮点。
7举例1:每个孔可以有100个⼩亮点举例2:每个孔内有2个亮点,且有20个⼩亮点举例3:在每个孔中有3个横向纤维点,并伴有10个⼩亮点。
6.0举例1:在每个孔有很多⼩亮点。
(⼤约300个)举例2:在每个孔内有2个亮点,每个⽩点中有50⼩亮点。
举例3:每个孔内有4个横向纤维点,每个孔内有50个⼩亮点。
5.0举例1:在椭圆的图形中有许多⼩亮点。
这些圆形图形是玻璃团的终端。
并不是所有的玻璃团被看清淅的。
举例2:每个孔内有5个横向纤维点,并有⽆数⼩亮点和5个亮点。
举例3:每个孔内20个⼩亮点和1个粗亮点(⾁眼可见)4.0举例1:每个孔有90%的玻璃团可见,和5个横向纤维点。
举例2:每个孔最多10个亮点每个孔有5个亮点和1个粗亮点3.0举例1:所有的玻璃团可以清淅看见并⾮常明亮。
在同⼀个孔内还有⼀些横向纤维点。
举例2:在每个孔内有⼀些亮点和2个粗亮点。
2.5举例1:所有的玻璃团可以清淅看见并⾮常明亮。
在同⼀个孔内还有⼀些横向纤维点。
举例2:在每个孔内有⼀些亮点并最多有3个粗亮点2.0 有⼤量的⼤的玻璃和环氧亮点1.5 表⾯残铜1.0 表⾯薄铜0 表⾯⽆铜例⼦取样B —包括5个孔5个孔的背光级数— 9.5,9.5,9.0,8.5,9.05个孔的背光级平均值 = 9亮点的⼤⼩分类⼩亮点(针孔) 1-5µm(4-20µ")⼀般亮点 5-80µm(200µ"-0.0032")粗亮点 80-200µm(0.0032-0.008")。
- 1、下载文档前请自行甄别文档内容的完整性,平台不提供额外的编辑、内容补充、找答案等附加服务。
- 2、"仅部分预览"的文档,不可在线预览部分如存在完整性等问题,可反馈申请退款(可完整预览的文档不适用该条件!)。
- 3、如文档侵犯您的权益,请联系客服反馈,我们会尽快为您处理(人工客服工作时间:9:00-18:30)。
PCB化学镀铜背光详解线路板 PCB 制作是一个复杂的,多级加工的过程,在生产过程中控制不当 就可能产生很多的报废和品质缺陷。
无论是使用传统的化学铜 PTH 还是新式的 直接电镀 制程,电镀前的通孔和盲孔的金属化是一个复杂的操作过程。
为保证 生产线产量最大化, 使用合理的检测方法和手段来使整个流程良好有效运作是必 要的。
另外,控 制流程中每个处理处理步骤的参数和每个部分处理后的处理效 果的确认评估是一样重要。
这需要对生产线现场有清晰直接的了解:包括对现场 制程难以想象的多次仔 细检查,现场的原材料的不断变化和提供经过确认的各 个制程的控制方法。
对 PTH 制程镀通孔的沉积覆盖率的评估和监控(PTH process)是一个十分 重要的质量控制的检查, 这样可以确保化学铜沉积处理后的镀层可以有效的提供 后续镀通孔的导电和其他性能要求,也可以及时发现生 产线的一些无法预知的 问题及时地在该环节流程进行必要的或者可能返工处理。
定期的进行背光和前光检测来监控化学铜沉积质量和覆盖率,是预防和 有 效减少化学铜制程镀层 不良缺陷的最佳方法。
背光测试可以检查出生产线上化 学铜的沉积不良或者不完整的镀层(背光不良,化学铜沉积不连续),前光测试 可 以看到化学铜沉积覆盖不良区域的位置(如环氧树脂或者玻璃纤维)和化学 铜的沉积状况,亦即环氧树脂,玻璃纤维和内层铜环处的化学铜结合状况。
使用 合理有效 地背光测试方法, 可以有效监控和检测来自PTH生产线的产品的整个 沉铜覆盖率/背光状况的变化,可以使用相对较少检测频率检查出生产线上少量, 不确定的孔 无铜问题,例如可能因为钻孔不良,钻孔毛刺/披锋,钻污等造成的。
取样频率:虽然对生产过程中的每个挂具/挂篮都取样来监控化学铜镀层质量是最好, 但是这也是不太现实的。
每个客户需要根据他们的品质要求来建立一个合理适当 的取样频率,既可以确保生产线在客户的品质要求的制程控制范围,也可以在使 用较少的取样频率和必须的检测成本之间取得平衡。
一种常见方法是从生产线上沉铜后的每个挂具或者挂篮上抽取一块板进行 取样检查,但是一般每四个样品检查一次背光和前光。
如果发现问题,再检查取 样挂篮/ 挂具的其他生产板。
另外,如果发现在同一挂具或者挂篮不同位置的生 产板背光出现差异,最好从从挂具或者挂篮不同位置进行取样检测。
背光或前光 测试一般使用生产板板边科邦孔(样品孔,样孔列)作为检测。
一般是不同孔径,孔中心在同一轴线上的 510 个孔。
根据生产板类型选择不同 孔径的孔进行检测 评估。
生产上,我们一般多倾向于选择孔径在0.016 "0.043 之间的孔(0.4 mm1.1mm)。
一般小于0.016 "(0.4 mm)的孔一般比较难于取样, 相对较少;孔径大于 0.043(1.1mm)的孔一般作为插件装配孔,很少要求电气 互连功能。
背光测试孔最好选择生产板上下 板边位置至少有0.5 "(6.0毫米), 这样, 测试孔上下位置的其他孔才可能保证在背光检测过程与测试样孔背光的稳 定均一性。
下面有几种常用的背光检测样品取样方法:首选方法: 一般把背光测试样孔合并设计到生产板的空白区域或者板边边缘区域,多数在板边外缘。
可以从挂具/挂篮的生产板上取一些板边科邦孔,而不 需损坏成 品线路图形。
这种方法同时也受一些相关的生产批量和其他具体参数, 譬如钻孔或者基板材料等因素影响。
其他两种方法也许会用到:1.从生产线最常见的板料取样,最好从一个生产板件上取样时可以或者尽可 能抽取不同孔径的孔;2.使用钻孔报废板作为检测板;使用上述两种取样方法,沉铜挂板方式是一个外来重要影响;因为它们可 能会和生产板一起在槽液中经过槽液流动搅拌, 空气搅拌和机械摇摆过程暴露在 液位上;然 而上述两种方法的缺陷是会有很多特定因素影响,如试验板板材类 型,钻孔参数等一些不能检测的因素。
把背光测试样品直接拼到生产线的生产板 上是唯一可以实际 监控现场生产状况的直接方法。
取样方法:取样板一旦经过PTH处理后,可以使用铣床,锯子,冲床等工具取样。
为 方便后续处理,取样时最好冲切边缘和测试孔保持足够距离(一般是35mm)。
进行 背光或者前光测试,样品一般通过剪切或者研磨到测试排孔的中央轴线, 要保证孔内没有毛刺和脏物粉尘等,然后从测试孔背后研磨到孔边(一般是 13mm), 这样可以保证背光测试的光线可以顺利穿过测试样。
另外,样品制 作过程不可以人为损坏测试孔表面。
取样后,不管使用金刚石刀片切开测试孔或 者通过抛光盘研磨 抛光到孔中部附近,先用120或者240砂纸去除样品切片板 边或孔边毛刺,然后再用 400 或者 600 号砂纸进行研磨抛光。
抛光研磨时,最 好使用小镊子夹紧 测试样进行研磨。
如图一所示。
首先从测试样孔后面研磨 12mm,然后翻转,用镊子夹紧这12mm区域研磨正面。
研磨后水洗烘干即可。
注意镊子不可以损 伤测试孔。
备注:取样后,样品要保持干燥,减少试样周围空气流通,特别是对于这样 一些测试样情况:在除胶渣过程中难于除胶和调整的板料,化学铜和基材之间结 合程度不好,在外层铜箔和非导电基材之间的化学铜容易发生部分氧化。
图1:样品制作图2:样品外观测试样检查:样品可以使用 50200 倍放大镜或者金相显微镜观察。
先使用上光聚焦, 然后使用下光观察背光状况。
透光区域则是化学铜沉积覆盖不良区域。
要检测样 品的每 一个测试孔。
评估标准有很多,我们喜欢使用 0,55.0 的测试标准级数 (实际上大陆更多的是使用原希普列 10 级标准级数表)。
5.0 代表完全的化学 铜覆 盖率。
我们使用一系列的标准图,可以有效保证在不同员工之间进行背光 操作的一致性和稳定性,这些图片通常作为背光检查评估标准和操作指南。
图3:背光级数表背光检测的验收标准不同客户要求不同, 通常要求生产线沉铜背光在4.25级 (或 者8级)以上,这样就可以保证后续电镀孔铜覆盖率和均匀性,满足客户品质要 求。
结果说明:通过下光检查背光效果,通过前光,检查确定孔无铜区域的位置(树脂或 者玻璃纤维),孔内微空洞类型,化学铜沉积状况和沉积镀层质量。
为了保证沉 铜评估检 测的客观性,减少人为因素,我们使用下面一些术语来更加准确的判 定通过背光和前光测试检测到的沉铜覆盖率,沉铜层沉积状况。
1.TOG玻璃纤 维沉铜层偏薄(Thin Plating on Glass):玻璃纤维处特别是纵向纤维处,沉铜层太薄,背光观察时,部分光线穿过出现轻 微透光现象。
主要是化学铜制程沉积速率过慢造成。
出现这种问题的 主要原因 化学铜拖缸时间不够,活性不足或者槽液活性尚未起来,化学铜槽液管控不当, 前处理碱性除油调整不足或者活化不良,除油后或者活化后水洗过度,除油 后 微蚀处理时间过长等;2.TOE环氧树脂沉铜过薄(Thin Plating on Epoxy):孔内环氧树脂处出现这种问题原因类似上述玻璃纤维处。
一些高Tg树脂或者填 充材料或者复合材料的基材是比较难于调整和活化,也经常会发生上述情况。
3.ROP 珍珠环(Ring of Pearls):这种缺陷一般发生在非导电基材和铜层之间,最常见树脂或者内层铜层和 B 阶 树脂之间。
严重情况下,C 阶树脂也会发生。
(译者注:在孔内出现 圈状圆环 状透光)珍珠环出现时,可能在上述区域是不连续透光,有时也可能会出现轻微 连续的圆环状透光。
当这种孔无铜区域发生在外层铜箔和树脂结合处,称之 为 外缘空隙。
这种缺陷主要是因为钻孔不良或者钻孔工艺参数不应当,造成基材2 种不同基材受损;B阶树脂和内层铜箔之间出现撕裂;这种情况,在后续除胶渣 过 程中造成撕裂加大,造成后续沉铜困难;化学铜沉积速率越慢,珍珠环出现 的几率越大;钉头(孔内毛刺)的产生:内层铜层被挤压变形成钉头形状,延伸到孔内非导电 基材内。
经过微蚀粗化处理后,一圈环状未经过除油调整的基材暴露出来,因为 未经过除油调整处理,所以后续活化不良,造成沉铜不良,偏薄,甚至沉铜不上;4.GTV: 玻璃纤维尖端空洞(Glass Tip Voids):主要发生在纵向玻璃纤维束垂直于孔壁的玻璃纤维断面处,外形看起来像眼睛, 主要是因为此处沉铜覆盖不良造成;这种缺陷一般主要原因是碱除油 调整不良 或者活化不良造成, 也可能因为一些工艺步骤过程如碱除油和化学铜后水洗过度 造成。
微蚀时间过长,微蚀过度,也可能造成环氧树脂或者玻璃纤维表面的 碱 性调整剂损失,造成后续活化不良或者无活化。
本来玻璃纤维处就是难于调整, 过微蚀粗化首先会造成玻纤尖端空洞。
5.TGV: 横向玻璃纤维区域空洞 Transverse Glass Voids:横向玻璃纤维束是和孔壁平行。
玻璃纤维束的尺寸会因为半固化片(pp 材料) 和或者所用芯材的不同而不同。
再次,这个问题主要是因为沉铜覆盖不 良造成。
典型的形成原因类似于GTVGlass Tip Voids玻璃纤维尖端空洞。
另外,孔内微 空洞发生在横向纤维束处也可能因为玻纤处化学桶结合力不良造成。
化学铜在玻 璃纤维束处沉积时或者在后续生产过程 中会出现裂开,甚至爆裂现象,造成孔 内微空洞(详细信息请参考 popoff 玻璃纤维表面孔铜爆裂和镀层褶皱 wrinkles 的讨论)。
这种情况在玻璃纤 维布较厚的基材中较易发生图4:显示ROP, GTV, TGV.的背光和前光图片6.PO: 横向玻璃纤维束化学铜爆裂 Pop Off:当化学铜在玻璃纤维处沉积结合不良, 最终会出现化学铜镀层剥离起泡分层等现 象,最终导致 TGV 横向玻璃纤维束区域的玻璃纤维尖端空洞现象。
引起 GTV 的原因有以下几个不同的主要原因,通过分析评估化学铜镀层结合不良(镀层剥 离)可以提供关于品质缺陷的其他信息。
图5:化学铜在横向玻璃纤维束表面发生镀层剥离(PO)的SEM照片发生化学铜镀层爆裂的主要原因是因为调整过度或者活化过度,但是,化学铜的 沉积厚度和玻璃纤维的厚度也可能是造成这个缺陷的主要原因。
化学铜越厚,在玻璃 纤维处发生镀层剥离的现象的机会越大,因为化学铜的沉积造成的镀层应 力原因。
另外,较厚的玻璃纤维布较薄的玻璃纤维布对于化学铜来说,更容易发 生镀层玻璃 现象,因为厚的玻璃纤维布的表面积较大,相对应力加大。
在有些 情况下可能发生如下现象,当使用前光观察玻璃纤维时,发现化学铜镀层结合不 良或者镀层皱褶, 但是背光试验是 OK 的。
化学铜和玻璃纤维束之间的较差的 结合力是这块生产板的其他区域发生纵向玻璃纤维束尖端空洞的潜在显示。