齿轮径向跳动测量
《互换性与技术测量》齿轮径向跳动的测量实验
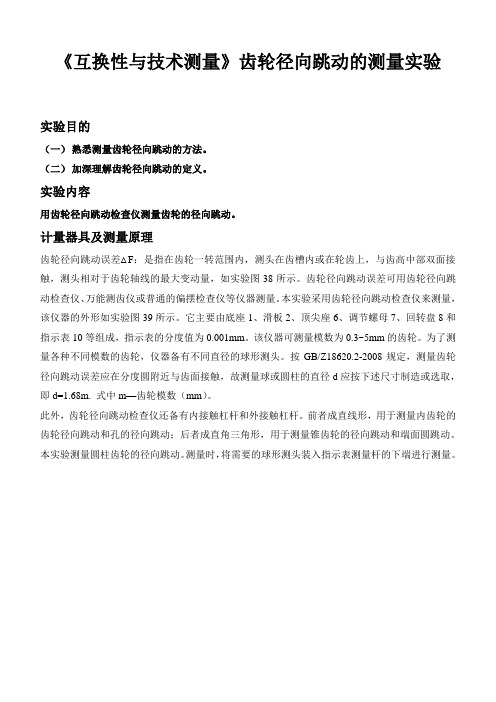
《互换性与技术测量》齿轮径向跳动的测量实验实验目的(一)熟悉测量齿轮径向跳动的方法。
(二)加深理解齿轮径向跳动的定义。
实验内容用齿轮径向跳动检查仪测量齿轮的径向跳动。
计量器具及测量原理齿轮径向跳动误差△F:是指在齿轮一转范围内,测头在齿槽内或在轮齿上,与齿高中部双面接触,测头相对于齿轮轴线的最大变动量,如实验图38所示。
齿轮径向跳动误差可用齿轮径向跳动检查仪、万能测齿仪或普通的偏摆检查仪等仪器测量。
本实验采用齿轮径向跳动检查仪来测量,该仪器的外形如实验图39所示。
它主要由底座1、滑板2、顶尖座6、调节螺母7、回转盘8和指示表10等组成,指示表的分度值为0.001mm。
该仪器可测量模数为0.3~5mm的齿轮。
为了测量各种不同模数的齿轮,仪器备有不同直径的球形测头。
按GB/Z18620.2-2008规定,测量齿轮径向跳动误差应在分度圆附近与齿面接触,故测量球或圆柱的直径d应按下述尺寸制造或选取,即d=1.68m. 式中m—齿轮模数(mm)。
此外,齿轮径向跳动检查仪还备有内接触杠杆和外接触杠杆。
前者成直线形,用于测量内齿轮的齿轮径向跳动和孔的径向跳动;后者成直角三角形,用于测量锥齿轮的径向跳动和端面圆跳动。
本实验测量圆柱齿轮的径向跳动。
测量时,将需要的球形测头装入指示表测量杆的下端进行测量。
实验步骤(一)根据被测齿轮的模数,选择合适的球形测头,装入指示表10测量杆的下端(实验图39)。
(二)将被测齿轮和心轴装在仪器的两顶尖上,拧紧紧固螺钉4和5。
(三)旋转手柄3,调整滑板2的位置,使指示表测头位于齿宽的中部。
通过升降调节螺母7和提升手把9,使测头位于齿槽内。
调整指示表10的零位,并使其指针压缩1~2圈。
.(四)每测一齿,须抬起提升手把9,使指示表的测头离开齿面。
逐齿测量一圈,并记录指示表的读数。
(五)处理测量数据,从GB/T10095.2-2008查出齿轮的径向跳动公差F,判断被测齿轮的适用性。
实验数据记录及处理1、齿轮齿数Z=30,2、根据da=m,得m标准值为:.d=mz=45mm4、:.rmax=2rmin=-45、所以Fr=rmax-rmin=6、查表,得Fr=23um Fr≤Fr检验合格实验结论由实验过程可得,齿轮得最大跳动径向为0.2mm。
径向国跳动和端面圆跳动的测量

实验六径向圆跳动和端面圆跳动的测量
一、实验目的
1、了解跳动误差的测量原理及数据处理方法。
2、掌握齿轮径向跳动测量仪的使用方法。
二、测量器具:
齿轮径向跳动测量仪,百分表或千分表,杠杆百分表
三、测量原理
圆跳动公差是要素饶基准轴线作无轴向移动旋转一周时,在任一测量面内所允许的最大跳动量。
四、测量步骤
1、径向圆跳动的测量:
⑴将零件擦净,置于偏摆仪两顶尖之间固紧顶尖座;
⑵将百分表装在表架上,使表杆通过零件轴心线,并与轴心线大至垂直,测头与零件表面接触,并压约缩1~2圈后紧固表架。
⑶转动被测件一周,记下百分表读数的最大值和最小值,该最大值与最小值之差,为此截面的径向圆跳动误差值。
⑷在轴向的三个截面上进行测量,取三个截面中圆跳动误差的最大值,为该零件的径向圆跳动误差。
2、端面圆跳动的测量:
⑴将杠杆百分表夹持在偏摆检查仪的表架上,缓慢移动表架,使杠杆百分表的测量头与被测端面接触,并予压0.4mm。
⑵转动工件一周,记下百分表读数的最大值和最小值,该最大值与最小值之差,即为直径处的端面跳动误差。
⑶在被测端面上均匀分布的三个直径处测量,取其三个中的最大值为该零件端面圆跳动误差。
3、根据图纸所给定的公差值,判断零件是否合格。
端面圆跳动公差0.12mm,径向圆跳动公差0.06mm
思考题
1 、形位误差的检测原则有哪些?。
齿轮齿圈径向跳动的测量实验报告
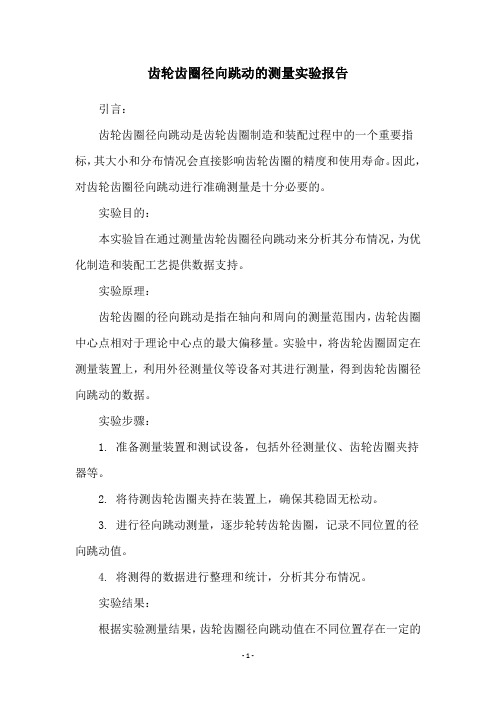
齿轮齿圈径向跳动的测量实验报告
引言:
齿轮齿圈径向跳动是齿轮齿圈制造和装配过程中的一个重要指标,其大小和分布情况会直接影响齿轮齿圈的精度和使用寿命。
因此,对齿轮齿圈径向跳动进行准确测量是十分必要的。
实验目的:
本实验旨在通过测量齿轮齿圈径向跳动来分析其分布情况,为优化制造和装配工艺提供数据支持。
实验原理:
齿轮齿圈的径向跳动是指在轴向和周向的测量范围内,齿轮齿圈中心点相对于理论中心点的最大偏移量。
实验中,将齿轮齿圈固定在测量装置上,利用外径测量仪等设备对其进行测量,得到齿轮齿圈径向跳动的数据。
实验步骤:
1. 准备测量装置和测试设备,包括外径测量仪、齿轮齿圈夹持器等。
2. 将待测齿轮齿圈夹持在装置上,确保其稳固无松动。
3. 进行径向跳动测量,逐步轮转齿轮齿圈,记录不同位置的径向跳动值。
4. 将测得的数据进行整理和统计,分析其分布情况。
实验结果:
根据实验测量结果,齿轮齿圈径向跳动值在不同位置存在一定的
差异,但总体来说,跳动值分布较为均匀,未出现明显的异常情况。
结论:
通过对齿轮齿圈径向跳动的测量和分析,可以得出其分布情况较为均匀的结论。
这对于制造和装配工艺的优化提供了较为实际的参考意义。
同时,实验中使用的测量方法和设备也可为相关领域的研究和开发提供依据。
齿轮径向跳动的测量实验报告
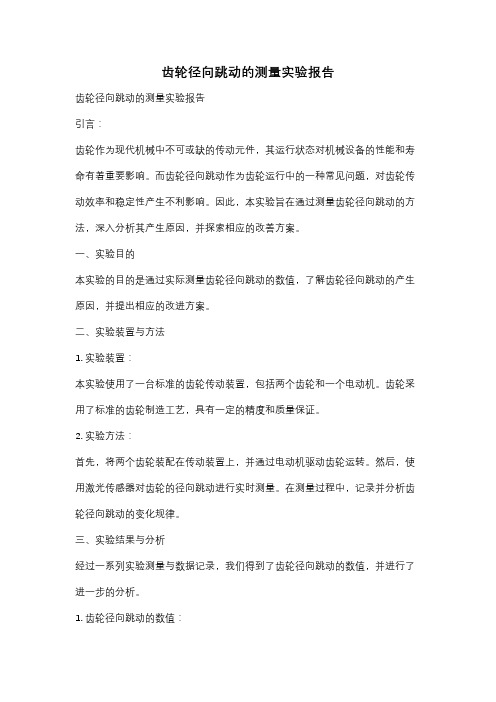
齿轮径向跳动的测量实验报告齿轮径向跳动的测量实验报告引言:齿轮作为现代机械中不可或缺的传动元件,其运行状态对机械设备的性能和寿命有着重要影响。
而齿轮径向跳动作为齿轮运行中的一种常见问题,对齿轮传动效率和稳定性产生不利影响。
因此,本实验旨在通过测量齿轮径向跳动的方法,深入分析其产生原因,并探索相应的改善方案。
一、实验目的本实验的目的是通过实际测量齿轮径向跳动的数值,了解齿轮径向跳动的产生原因,并提出相应的改进方案。
二、实验装置与方法1. 实验装置:本实验使用了一台标准的齿轮传动装置,包括两个齿轮和一个电动机。
齿轮采用了标准的齿轮制造工艺,具有一定的精度和质量保证。
2. 实验方法:首先,将两个齿轮装配在传动装置上,并通过电动机驱动齿轮运转。
然后,使用激光传感器对齿轮的径向跳动进行实时测量。
在测量过程中,记录并分析齿轮径向跳动的变化规律。
三、实验结果与分析经过一系列实验测量与数据记录,我们得到了齿轮径向跳动的数值,并进行了进一步的分析。
1. 齿轮径向跳动的数值:实验结果显示,齿轮径向跳动的数值在不同工况下有所差异。
在正常运行状态下,齿轮径向跳动的数值较小,通常在0.01mm以下。
而在高速运转或负载较大的情况下,齿轮径向跳动的数值会明显增大,甚至超过0.1mm。
2. 齿轮径向跳动的原因:通过对实验结果的分析,我们发现齿轮径向跳动的主要原因是齿轮的制造和装配误差,以及齿轮与轴之间的间隙。
制造误差包括齿轮的几何形状和表面质量等方面的偏差,而装配误差则包括齿轮的安装位置和相对角度等方面的误差。
这些误差会导致齿轮在运转中产生不稳定的径向力,从而引起齿轮径向跳动。
3. 改进方案:为了减小齿轮径向跳动的数值,我们可以采取以下改进方案:(1)提高齿轮的制造精度:通过优化齿轮的制造工艺和加工设备,减小齿轮的制造误差,提高齿轮的几何形状和表面质量,从而减小齿轮径向跳动的数值。
(2)优化齿轮的装配方式:在齿轮的装配过程中,采用精确的定位和调整方法,确保齿轮的安装位置和相对角度的准确性,减小齿轮的装配误差,从而减小齿轮径向跳动的数值。
径向跳动测试方法

径向跳动测试方法1. 嘿,你知道吗?用千分表来进行径向跳动测试就很不错哟!就像医生拿着听诊器给病人检查一样,千分表能精准地检测出工件的跳动情况呢。
比如在检测一个齿轮的时候,把千分表触头轻轻放在齿轮表面,那转动起来就能看到跳动的数据啦!2. 还有哦,使用专门的跳动测量仪也超棒呀!这就好比是给工件做了一次超级全面的体检呢。
就像我们量身高体重一样准确。
比如说在检查一根轴的时候,把它放在测量仪上,那结果不就一目了然了嘛!3. 哇塞,利用光学测量法来进行 radial 跳动测试也很神奇呢!这就跟我们用眼睛去发现美好一样。
比如说检查一个精密零件的表面,通过光学仪器一下就能看清它的跳动细节啦,是不是很厉害!4. 嘿,你想过没有,三坐标测量机也能搞定 radial 跳动测试呀!这就好像是个万能的检测大师。
像检测一个复杂形状的工件时,三坐标测量机就能大显身手啦,轻松找到跳动的问题所在!5. 还有那种比较传统的手动检测法呢,也别小瞧它呀!就像是老手艺一样有它独特的魅力哟。
例如在一些简单的工件检测中,手动检测就能很好地发挥作用呀!6. 激光测量法听说过吗?那可太牛啦!就如同有一双火眼金睛在盯着工件呢。
比如对一个高速旋转的零部件进行检测,激光测量就能快速又准确地给出 radial 跳动的数据咯!7. 干涉测量法也值得一试呀!这就像是给工件拍了一张超级清晰的照片。
就像检测一个很薄的片状工件的跳动时,干涉测量法就能展示它细微的跳动变化呢。
8. 涡流检测法也能用来做 radial 跳动测试哦!就好像是个神奇的探测器。
比如说对一个金属工件进行检测,涡流检测就能敏锐地察觉到跳动情况啦!9. 哎呀呀,这么多种 radial 跳动测试方法,都各有各的厉害之处呀!大家可以根据实际情况选择合适的方法哟,这样才能更好地检测出工件的质量问题呢!。
齿圈径向跳动测量误差分析及处理

图 1 齿坯安装偏心 引起
齿轮加工误差
图 2 齿圈径 向跳动
3 测量 头 的选 择 【3 2】 -
测量齿圈径 向跳动常用 的测量头有 如图 2所示 的球形测
头、 锥形 测头、 V形测头 。
2 齿 圈径 向跳 动 测量
齿 圈径 向跳动测量原理与测量 内外 圆柱 面的径 向跳动 相
A 2s Z ,B:dcs B: ri n A 。 ’ 则 :’ : r ‘ 2t n a
所示 。
测量时 , 以齿 轮内孔 的轴线定位 , 即将被 测齿轮 的内孔 装 在心轴 上 , 心轴支 承在仪器的两顶尖之间 , 百分表测杆 上专 将
(h n ogL iuvc10 , hn ) S ad n aw oai n cnl yc l e L iuS a dn 7 10 C ia o e o oe
A src :repp r nlzsh aue r cp rot i l cr lru iesadte c r f c n esrm n b tat h ae aye e a t mesrs i il f ohcr e i ua mpns n if t et gm aue et p n e ot c c j h ra o a i
当选用球形 测 头 ( 或圆棒 ) , 时 在齿 槽或 轮齿 中部进 行 ,
似 , 同点是测量 头应与 齿面或 齿槽做 双 面接触并 逐齿 测 其不
量, 一般在齿圈径 向跳动检查 仪或 万能测齿 仪上测 量 , 如图 2
因此 测量头 可选择相应 的圆球和 圆棒 在分度圆上或 其附近进 行测量 , 4 示。测头直径 d按下式计算 : 如图 所 。 J
1 引 言
在齿轮 的各种加 工方法 中 , 轮加 工误 差都是来 源于 组 齿
实验齿轮齿圈径向跳动.doc
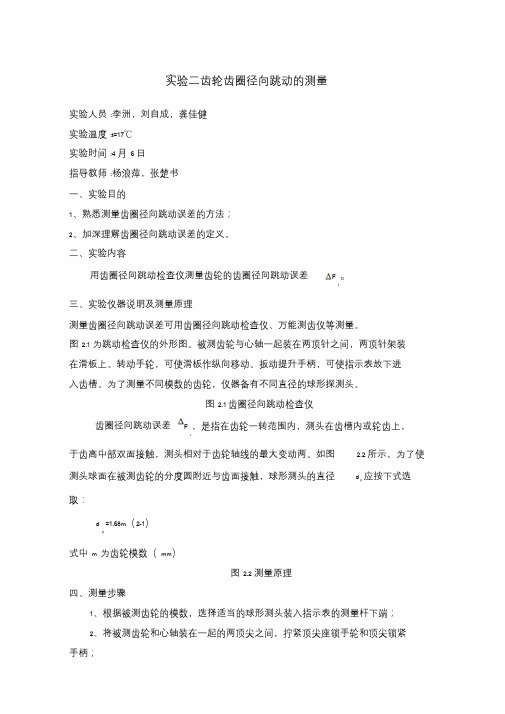
实验二齿轮齿圈径向跳动的测量实验人员:李洲,刘自成,龚佳健实验温度:t=17℃实验时间:4月6日指导教师:杨浪萍,张楚书一、实验目的1、熟悉测量齿圈径向跳动误差的方法;2、加深理解齿圈径向跳动误差的定义。
二、实验内容用齿圈径向跳动检查仪测量齿轮的齿圈径向跳动误差F。
r三、实验仪器说明及测量原理测量齿圈径向跳动误差可用齿圈径向跳动检查仪、万能测齿仪等测量。
图2.1为跳动检查仪的外形图。
被测齿轮与心轴一起装在两顶针之间,两顶针架装在滑板上。
转动手轮,可使滑板作纵向移动。
扳动提升手柄,可使指示表放下进入齿槽。
为了测量不同模数的齿轮,仪器备有不同直径的球形探测头。
图2.1齿圈径向跳动检查仪齿圈径向跳动误差F,是指在齿轮一转范围内,测头在齿槽内或轮齿上,r于齿高中部双面接触,测头相对于齿轮轴线的最大变动两。
如图 2.2所示。
为了使测头球面在被测齿轮的分度圆附近与齿面接触,球形测头的直径d p应按下式选取:d=1.68m(2-1)p式中m为齿轮模数(mm)图2.2测量原理四、测量步骤1、根据被测齿轮的模数,选择适当的球形测头装入指示表的测量杆下端;2、将被测齿轮和心轴装在一起的两顶尖之间,拧紧顶尖座锁手轮和顶尖锁紧3、旋转手轮,调整滑板位置,使球形测量头位于齿宽中部。
借升降螺母和提升手柄。
使是指表下降,直至测头伸入齿槽内且与齿面接触。
调整指示表,使其指针压缩约1-2 圈,拧紧表架后面的紧固旋钮;4、球形测头伸入齿槽最下方即可读数,每测完一齿,抬起提升手柄,使球形测头进入第二个齿槽与齿面接触,以此类推,逐齿测量并记录指示表的读数;5、根据齿轮的技术要求,查出齿圈径向跳动公差F r ,判断被测齿轮的合格性。
五、被测对象图2.3 被测对象齿轮基本参数见表1-1。
表2-1齿轮基本参数六、被模数m 齿数Z 压力角α齿轮精度径向跳动误差测数据记录员:刘3 18 20 12 171μm自成表2-2第一次测量数据序号读数(um)序号读数(um)1 28 10 1352 22 11 1303 61 12 1124 64 13 1035 91 14 866 104 15 617 124 16 208 131 17 99 114 18 3齿圈径跳误差F r (um)135-3=132合格性结论合格,在公差范围内。
齿轮测量方法
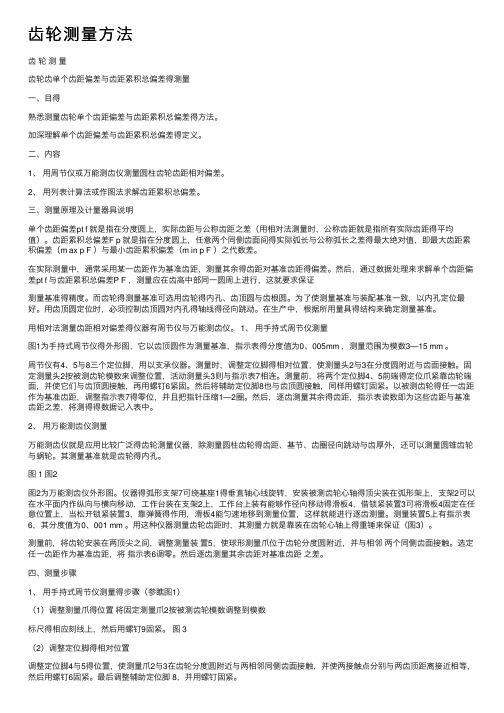
齿轮测量⽅法齿轮测量齿轮齿单个齿距偏差与齿距累积总偏差得测量⼀、⽬得熟悉测量齿轮单个齿距偏差与齿距累积总偏差得⽅法。
加深理解单个齿距偏差与齿距累积总偏差得定义。
⼆、内容1、⽤周节仪或万能测齿仪测量圆柱齿轮齿距相对偏差。
2、⽤列表计算法或作图法求解齿距累积总偏差。
三、测量原理及计量器具说明单个齿距偏差pt f 就是指在分度圆上,实际齿距与公称齿距之差(⽤相对法测量时,公称齿距就是指所有实际齿距得平均值)。
齿距累积总偏差F p 就是指在分度圆上,任意两个同侧齿⾯间得实际弧长与公称弧长之差得最⼤绝对值,即最⼤齿距累积偏差(m ax p F )与最⼩齿距累积偏差(m in p F )之代数差。
在实际测量中,通常采⽤某⼀齿距作为基准齿距,测量其余得齿距对基准齿距得偏差。
然后,通过数据处理来求解单个齿距偏差pt f 与齿距累积总偏差P F ,测量应在齿⾼中部同⼀圆周上进⾏,这就要求保证测量基准得精度。
⽽齿轮得测量基准可选⽤齿轮得内孔、齿顶圆与齿根圆。
为了使测量基准与装配基准⼀致,以内孔定位最好。
⽤齿顶圆定位时,必须控制齿顶圆对内孔得轴线得径向跳动。
在⽣产中,根据所⽤量具得结构来确定测量基准。
⽤相对法测量齿距相对偏差得仪器有周节仪与万能测齿仪。
1、⽤⼿持式周节仪测量图1为⼿持式周节仪得外形图,它以齿顶圆作为测量基准,指⽰表得分度值为0、005mm ,测量范围为模数3—15 mm 。
周节仪有4、5与8三个定位脚,⽤以⽀承仪器。
测量时,调整定位脚得相对位置,使测量头2与3在分度圆附近与齿⾯接触。
固定测量头2按被测齿轮模数来调整位置,活动测量头3则与指⽰表7相连。
测量前,将两个定位脚4、5前端得定位⽖紧靠齿轮端⾯,并使它们与齿顶圆接触,再⽤螺钉6紧固。
然后将辅助定位脚8也与齿顶圆接触,同样⽤螺钉固紧。
以被测齿轮得任⼀齿距作为基准齿距,调整指⽰表7得零位,并且把指针压缩1—2圈。
然后,逐齿测量其余得齿距,指⽰表读数即为这些齿距与基准齿距之差,将测得得数据记⼊表中。
1.15齿轮径向跳动的测量[11页]
![1.15齿轮径向跳动的测量[11页]](https://img.taocdn.com/s3/m/8bac7302ddccda38376baff7.png)
3.测量 抬起扳手3,使指示表2升高,把被测齿轮13转过一个齿槽。
然后,放下扳手3,使测头进入这个齿槽内,与齿槽双面接 触,并记下指示表的示值,。这样逐齿槽地依次测量所有 的齿槽,并把读数填入表1-35中。
合),然后把心轴安装在两个顶尖5之间。注意调整这两个顶尖之 间的距离,使心轴无轴向窜动,且能转动自如。 松开螺钉11,转动手轮12,使滑台9移动,以便使测头大约位于 齿宽中间。然后,将螺钉11锁紧。
五、实验步骤
2.调整量仪指示表的示值零位 放下扳手3,松开螺钉16,转动螺母15,使指示表测头随表
一、实验目的
(1)了解齿圈径向跳动检查仪的工作原理, (2)掌握齿圈径向跳动的测量方法, (3)加深对齿圈径向跳动定义的理解。
二、实验量仪说明
齿轮径向跳动可以使用齿轮径向跳动测量仪、万能测齿仪来测量。 本实验采用卧式齿轮径向跳动测量仪进行测量。
卧式齿轮径向跳动测量仪的外形如图1-118所示。测量时,把被 测齿轮13用心轴4安装在两个顶尖座7的顶尖5之间(齿轮基准孔与心 轴成无间隙配合,用心轴轴线模拟体现该齿轮的基准轴线)。指示表 2的位置固定后,使安装在指示表测杆上的球形测头或圆锥角等于 (为标准压力角)的锥形测头在齿槽内于接近齿高中部与齿槽的左、 右齿面接触。测头尺寸的大小应与被测齿轮的模数相适应,以保证测 头在接近齿高中部与齿槽双面接触。用测头逐齿槽地测量它相对于齿 轮基准轴线的径向位移,该径向位移由指示表2的示值反映出来。指 示表的最大与最小示值之差即为齿轮径向跳动的数值。
实验五 齿轮齿图径向跳动的测量

实验五齿轮齿图径向跳动的测量
一、测量原理及器具
齿圈径向跳动误差ΔFr是在齿轮一转范围内,将量头依次插入齿槽中,测得量头相对于齿轮旋转轴线径向位置的最大变动量。
可用齿圈径向跳动检查仪(如图3—29)、万能测齿仪或普通偏摆检查仪上带小圆柱和千分表进行测量(如图3-30)。
二、仪器主要技术参数
型号:DD300
被测齿轮模数范围:1~16 m m
测量最大直径:300 m m
顶针最大高度:150 m m
图8=1 用齿圈径向跳动检查仪测量齿圈跳动图8-2 用偏摆检查仪测量齿圈跳动
三、测量步骤
1、安装齿轮:将齿轮套在检验心轴上,用仪器的两顶尖顶在检验心轴的两顶尖孔内,心轴与顶尖之间的松紧应适度,即保证心轴灵活转动而又无轴向窜动。
2、选择测量头:测量头有两种形状,一种是球形测量头,另一种是锥形或V形测量头。
若采用球形测量头时,应根据被测齿轮模数按下表选择适当直径的测量头。
也可用试选法使量头大致在分度圆附近与齿廓接触。
3、零位调整:搬动手柄6放下表架,根据被测零件直径转动螺母4,使测量头插入齿槽内与齿轮的两侧面相接触,并使千分表具有一定的压缩量。
转动表盘,使指针对零。
4、测量:测量头与齿廓相接触后,由千分表进行读数,用手柄6抬起测量头,用手将齿轮转过一齿,再重复放下测量头,进行读数如此进行一周,若千分表指针仍能回到零位,则测量数据有效,千分表示值中的最大值与最小值之差,即为齿圈径向跳动误差ΔFr。
否则应重新测量。
四、填写测量报告单
按步骤完成测量并将被测件的相关信息、测量结果及测量条件填入测量报告单7~12中。
(完整版)端面圆跳动和径向全跳动测量
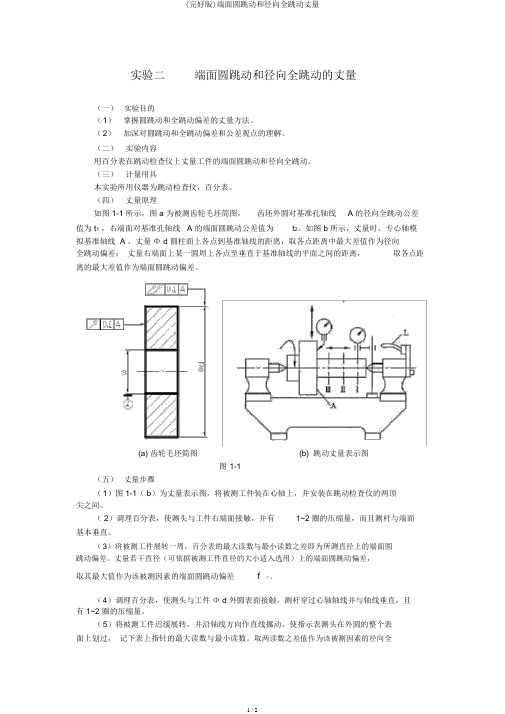
实验二端面圆跳动和径向全跳动的丈量(一)实验目的(1)掌握圆跳动和全跳动偏差的丈量方法。
(2)加深对圆跳动和全跳动偏差和公差观点的理解。
(二)实验内容用百分表在跳动检查仪上丈量工件的端面圆跳动和径向全跳动。
(三)计量用具本实验所用仪器为跳动检查仪,百分表。
(四)丈量原理如图 1-1 所示,图 a 为被测齿轮毛坯简图,齿坯外圆对基准孔轴线 A 的径向全跳动公差值为 t1,右端面对基准孔轴线 A 的端面圆跳动公差值为t2。
如图 b 所示,丈量时,专心轴模拟基准轴线 A ,丈量Φ d 圆柱面上各点到基准轴线的距离,取各点距离中最大差值作为径向全跳动偏差;丈量右端面上某一圆周上各点至垂直于基准轴线的平面之间的距离,取各点距离的最大差值作为端面圆跳动偏差。
(a) 齿轮毛坯简图(b) 跳动丈量表示图图1-1(五)丈量步骤(1)图 1-1( b)为丈量表示图,将被测工件装在心轴上,并安装在跳动检查仪的两顶尖之间。
( 2)调理百分表,使测头与工件右端面接触,并有1~2 圈的压缩量,而且测杆与端面基本垂直。
(3)将被测工件展转一周,百分表的最大读数与最小读数之差即为所测直径上的端面圆跳动偏差。
丈量若干直径(可依据被测工件直径的大小适入选用)上的端面圆跳动偏差,取其最大值作为该被测因素的端面圆跳动偏差 f ↗。
(4)调理百分表,使测头与工件Φ d 外圆表面接触,测杆穿过心轴轴线并与轴线垂直,且有 1~2 圈的压缩量。
(5)将被测工件迟缓展转,并沿轴线方向作直线挪动,使指示表测头在外圆的整个表面上划过,记下表上指针的最大读数与最小读数。
取两读数之差值作为该被测因素的径向全跳动偏差 f ↗↗。
( 6)依据丈量结果,判断合格性。
若 f ↗≤t2, f ↗↗≤t1,则部件合格。
(六)思虑题(1)心轴插入基准孔内起什么作用?(2)圆跳动、全跳动丈量与圆度、圆柱度偏差丈量有何异同?实验一端面圆跳动和径向全跳动丈量一、丈量对象和要求:1.被测试件编号——2.部件的端面圆跳动公差 t2=______________mm 。
1.8径向和轴向圆跳动测量[12页]
![1.8径向和轴向圆跳动测量[12页]](https://img.taocdn.com/s3/m/e1a94b45941ea76e59fa0408.png)
二、实验仪器设备说明
三、实验原理
调整卧式齿轮径向跳动仪或偏摆仪两端顶尖同轴,以两顶尖的
轴线模拟公共基准,被测工件对顶尖无轴向移动且转动自如, 采用跳动原则,看指示表读数,确定跳动量。 如图1-95所示,为径向和轴向圆跳动的测量示意图。被测零件2 以基准孔安装在心轴3上(被测零件与心轴成无间隙配合),
四、实验步骤
1.径向圆跳动测量
(1)准备要求 在量仪上安装工件并调整指示表的测头与工件的相对
位置,把工件13 安装在心轴4 上(工件基准孔与心轴成无间隙配合)。
然后,把心轴4 安装在量仪的两个顶尖座7 的顶尖5 之间,使心轴无
轴向窜动,且能转动自如。
(2)调整指示表的测头与工件的相对位置 松开螺钉11,转动手轮12, 使滑台9 移动,以便使指示表2 的测头大约位于工件宽度中间。然 后,将螺钉11锁紧,使滑台9的位置固定。
四、实验步骤
(4)测量 把工件缓慢转动一周,读取指示表2 的最大与最小示值, 它们的差值即为单个测量截面上的径向圆跳动数值,如图1-96所示。 按上述方法在3个正截面上测量,将所测数据记录在表1-21中。 2.轴向圆跳动测量 (1)调整指示表的测头与工件的相对位置 松开螺钉17,转动表架14, 使指示表2测杆的轴线平行于心轴4的轴线。然后,将螺钉17锁紧。松 开螺钉16,转动螺母15,使表架14沿立柱1下降到指示表2的测头位于 工件被测端面范围内的位置。再将螺钉16锁紧,使表架14的位置固定。 (2)调整量仪的指示表示值零位 松开螺钉11,转动手轮12,使滑台9 移动到工件被测端面与指示表2的测头接触,注意指示表指针指示不 得超过指示表量程的1/3,然后,旋紧螺钉11,使滑台9的位置固定。 转动指示表2的表盘,把表盘的零刻线对准指示表的长指针,确定指 示表的示值零位。
齿轮径向跳动测量

齿轮径向跳动检测一、实验目的、1、了解卧式径向检查仪工作原理及使用方法。
2、学会使用卧式径向检查仪检测齿轮径向跳动。
二、实验原理图2-11-底座;2-工作台固紧螺丝;3-顶针固紧螺丝;4-被测齿轮;5-升降螺母6-指示表抬起手柄;7-指示表;8-测量头;9-中心顶针;图2-2齿圈径向跳动误差ΔF r是在齿轮一转范围内,处于齿槽内或轮齿上、与齿高中部双面接触的测头在齿槽内或齿轮上,于齿高中部双面接触,测头相对于齿轮轴心线的最大变动量。
见图2-2a,以齿轮基准孔的轴线o为中心,转动齿轮,使齿槽在正上方,再将球形测头(或用圆柱)插入齿槽与左右齿面接触,从千分表上读数,依次测量所有齿。
将各次读数记在坐标图上,如图2-2b所示,取最大读数与最小读数之差作为齿圈径向跳动误差。
三、实验步骤1、查阅仪器附件盒表格,根据被测齿轮选取球形测头,并将测头装入表的测杆下端。
2、 把擦净的被测齿轮装在仪器的中心顶尖上,安装后齿轮不应有轴向窜动!借助升降螺母5与抬起手柄6调整指示表,使指示表有一到二圈的压缩量; 3、 球形测头伸入齿槽最下方即可读数,读完数,向后扳拨杆,抬起千分表转过一齿,再放下,开始测第二齿。
如此依次测量各个齿面,把指示表的读数记下,并绘制出齿圈径向跳动图,取最大读数与最小读数之差,算出齿圈径向跳动误差ΔFr (r F ∆=max r -min r )。
4、 根据齿轮的技术要求,查出齿圈径向跳动公差Fr ,判断合格性:合格条件:r F ∆≤r F 为合格四、 实验数据记录及处理1、齿轮齿数Z=30,齿顶圆da=48.02mm2、根据da=(2h a *+z )m ,得m 标准值为1.5mm ∴d=mz=45mm4、∴ r max =4.2um r min =-3.2um5、所以 r F ∆=max r -min r =7.4um6、查表,得F r=23um ∴ r F ∆≤r F 检验合格。
齿轮径向跳动测量实验报告

齿轮径向跳动测量实验报告齿轮径向跳动测量实验报告引言:齿轮作为机械传动中常见的元件之一,其精度和稳定性对于整个机械系统的运行至关重要。
而齿轮径向跳动作为评估齿轮传动性能的重要指标之一,对于齿轮的设计和制造具有重要意义。
本实验旨在通过测量齿轮径向跳动的方法,分析其对齿轮传动性能的影响,为齿轮的优化设计提供参考依据。
实验原理:齿轮径向跳动是指齿轮在运动过程中齿距方向的振动幅度。
齿轮径向跳动的大小直接影响到齿轮传动的平稳性和噪声水平。
常见的齿轮径向跳动测量方法有两种:接触法和非接触法。
接触法是通过在齿轮齿距上放置传感器,测量齿轮齿距的振动情况来间接评估齿轮径向跳动。
这种方法的优点是简单易行,但由于传感器的存在会对齿轮传动产生一定的干扰,测量结果可能存在一定的误差。
非接触法是通过光学或激光传感器等设备,直接测量齿轮齿距的振动情况,从而准确评估齿轮径向跳动。
这种方法的优点是测量结果准确可靠,但设备复杂,操作难度较大。
实验步骤:1. 准备实验设备:齿轮传动实验台、传感器、数据采集系统等。
2. 将齿轮传动实验台调整至工作状态,并确保齿轮传动装置的稳定性。
3. 根据实验要求选择合适的径向跳动测量方法,接触法或非接触法。
4. 进行齿轮径向跳动测量。
如果采用接触法,将传感器放置在齿轮齿距上,并连接至数据采集系统;如果采用非接触法,根据设备要求进行操作。
5. 启动齿轮传动装置,进行实验测量。
记录下齿轮径向跳动的振动幅度和频率等数据。
6. 重复实验多次,取多组数据并进行平均,以提高测量结果的准确性。
7. 分析实验数据,评估齿轮径向跳动对齿轮传动性能的影响。
实验结果与讨论:根据实验测量得到的数据,可以对齿轮径向跳动的大小和频率进行分析。
通过比较不同齿轮传动装置的径向跳动数据,可以评估不同装置的传动性能。
同时,还可以通过改变齿轮的设计参数,如齿轮模数、齿数等,来优化齿轮传动装置的性能。
根据实验结果分析,我们可以得出以下结论:1. 齿轮径向跳动的大小与齿轮传动装置的稳定性密切相关。
齿轮径向跳动公差表

齿轮径向跳动公差表介绍齿轮是机械传动中常见的元件,用于传递动力和转速。
在齿轮的制造过程中,为了确保齿轮的准确性和可靠性,需要进行公差控制。
其中,齿轮径向跳动公差是齿轮制造中的一个重要参数。
本文将详细介绍齿轮径向跳动公差表的相关内容。
齿轮径向跳动公差的定义齿轮径向跳动公差是指齿轮齿面与基准轴线之间的距离差,也可以理解为齿轮齿面的偏心量。
齿轮径向跳动公差的大小直接影响到齿轮的运转精度和噪音水平。
通常情况下,齿轮径向跳动公差应控制在一定范围内,以确保齿轮的正常运行。
齿轮径向跳动公差的测量方法齿轮径向跳动公差的测量是通过测量齿轮齿面与基准轴线之间的距离差来完成的。
常用的测量方法包括以下几种:1. 直接测量法直接测量法是通过测量齿轮齿面的偏心量来确定齿轮径向跳动公差的大小。
这种方法需要使用专用的测量工具,如齿轮齿距测量仪、齿轮齿距测量仪等。
通过将测量仪放置在齿轮齿面上,可以直接读取齿轮齿面与基准轴线之间的距离差。
2. 间接测量法间接测量法是通过测量齿轮齿面的其他参数来推算齿轮径向跳动公差的大小。
常用的间接测量方法包括齿距测量法、齿厚测量法等。
这些方法通过测量齿轮齿面的几何参数,然后根据几何关系计算出齿轮径向跳动公差。
齿轮径向跳动公差的控制齿轮径向跳动公差的控制是齿轮制造中的重要环节。
合理的公差控制可以确保齿轮的运转精度和噪音水平,提高齿轮的使用寿命和可靠性。
1. 公差设计在齿轮的设计阶段,需要根据齿轮的使用要求和传动系统的要求,确定合适的齿轮径向跳动公差。
公差设计应考虑到齿轮的制造工艺、材料特性和运行环境等因素,以确保齿轮的性能和可靠性。
2. 制造工艺控制齿轮的制造工艺对齿轮径向跳动公差的控制具有重要影响。
制造工艺中的加工精度、热处理工艺等因素都会对齿轮的公差产生影响。
因此,在齿轮的制造过程中,需要严格控制各个工艺环节,以确保齿轮的公差符合设计要求。
3. 检测和筛选在齿轮的制造过程中,需要对齿轮的径向跳动公差进行检测和筛选。
齿轮齿圈径向跳动的测量

齿轮齿圈径向跳动的测量
齿轮齿圈径向跳动的测量
⼀、实验⽬的
1. 熟悉测量齿轮径向跳动的⽅法。
2. 加深理解齿轮径向跳动的定义。
⼆、实验内容
⽤齿圈径向跳动检查仪测量齿轮齿圈径向跳动。
三、测量原理及计量器具说明
齿轮径向跳动F r 为计量器测头(圆形、圆柱形等)相继置于每个齿槽内时,从它到齿轮轴线的最⼤和最⼩径向距离之差。
检查中,测头在齿⾼中部附近与左右齿⾯接触。
即min max r r F r -=。
四、测量步骤
1. 根据被测齿轮的模数,选择合适的球形测量头装⼊指⽰表测量杆的下端。
2. 将被测齿轮和⼼轴装在仪器的两顶尖上,拧紧固紧螺钉。
3.调整指⽰表测量头位于齿宽的中部,使测量头位于齿槽内。
调整指⽰表10的零位,并使其指针压缩1—2圈。
4. 每测⼀齿,须抬起提升⼿把,使指⽰表的测量头离开齿⾯。
逐齿测量⼀圈,并记录指⽰表的读数。
5. 处理测量数据,从GB/T10095.2-2001查出齿轮径向跳动公差Fr ,判断被测齿轮的适⽤性。
思考题
1. 齿轮径向跳动产⽣的主要原因是什么?它对齿轮传动有什么影响?
2. 为什么测量齿轮径向跳动时,要根据齿轮的模数不同,选⽤不同直径的球形测头?
齿轮齿圈径向跳动测量实验报告。
齿轮径向跳动公差表

齿轮径向跳动公差表
摘要:
1.齿轮径向跳动公差的概念
2.齿轮径向跳动公差的测量方法
3.齿轮径向跳动公差的影响因素
4.齿轮径向跳动公差的标准和控制
5.齿轮径向跳动测量仪的使用
正文:
一、齿轮径向跳动公差的概念
齿轮径向跳动公差是指在齿轮转动过程中,齿圈在径向方向上产生的偏移量。
它是齿轮制造和装配误差的一种表现形式,对齿轮传动的精度和平稳性具有重要影响。
二、齿轮径向跳动公差的测量方法
齿轮径向跳动公差的测量通常采用齿轮径向跳动测量仪进行。
这种测量仪具有测量力可调、测量方向可调的特点,能够适应不同类型的齿轮测量。
通过测量仪的检测,可以对齿轮的径向跳动公差进行准确的评估。
三、齿轮径向跳动公差的影响因素
齿轮径向跳动公差的大小受到多种因素的影响,包括齿轮材料、加工工艺、装配方式等。
为了保证齿轮传动的精度和平稳性,必须对这些因素进行严格的控制。
四、齿轮径向跳动公差的标准和控制
我国对齿轮径向跳动公差的标准有严格的规定。
根据《公差和配合》标
准,齿轮齿圈径向跳动公差应控制在0.015mm 以内。
在实际生产过程中,通过严格的质量控制和检验,可以有效地保证齿轮径向跳动公差的符合标准。
五、齿轮径向跳动测量仪的使用
齿轮径向跳动测量仪的使用方法如下:首先,根据被测齿轮的类型和尺寸选择合适的测头;其次,调整测量仪的测量力和测量方向;最后,将齿轮放置在测量仪上进行测量。
通过测量结果,可以对齿轮的径向跳动公差进行分析和评估,以确保齿轮传动的精度和平稳性。
总之,齿轮径向跳动公差是评价齿轮制造和装配质量的重要指标。
圆柱齿轮齿面径向跳动允许值

圆柱齿轮齿面径向跳动允许值E.1 目的本附录提供径向跳动的公差公式和应用范围。
E.2 任一径向测量距离(Individual radial measurement),为测头(球形、圆柱形或砧形)相继置于每个齿槽内时,齿轮轴线到测头的中心或其他指定位置的径向距离。
测量中,测头在近似齿高中部与左右齿面接触。
径向跳动也可以由齿距测量中获得的点确定(见E.5 和图E.2)。
注1:的个数与齿槽数相同。
注2:实际测量的结果与用齿距测量计算的结果有细微的不同。
当径向跳动测量指定量球直径时,如果用齿距的测量数据来计算径向跳动,则齿距测量需在量球的接触圆上进行,否则在测量圆上进行。
E.3 径向跳动(Runout),r齿轮的径向跳动值为任一径向测量距离最大值与最小值的差。
图 E.1 给出了径向跳动的示例,图中,偏心量是径向跳动的一部分(见GB/Z 18620.2)。
标引序号说明:1偏心量n 齿槽编号图E.1 16齿齿轮的径向跳动E.4 径向跳动公差rT推荐公式可用公式(E.1)计算:0. pT0. (0.002d0.55√d0.7m n12)(√2)()................ (E.1)rT应用范围如下:公差等级从1 到11 级5≤z≤1 0005 mm≤d≤15 000 mm0.5 mm≤m n≤70 mmE.5 由齿距测量计算径向跳动通过测量圆上的测量数据,可以知道左右齿面的位置。
在端平面内,在齿槽中可构建出两条渐开线,这两条渐开线与对应齿面上被测点间的距离等于量球半径除以基圆螺旋角的余弦。
该距离沿着基圆切线方向。
每个齿槽中这两条构建的渐开线的交点给出了径向测量中量球中心的近似径向位置。
由于接触位置不同和存在表面误差,由此获得的结果可能与实际使用量球与两齿面接触的测量结果有细微的差距。
图 E.2 所示为一个直齿轮的简化示例。
E.6 应用指南径向跳动的测量不是强制性的,除非另有规定。
因此,本附录有关的参数信息没有包含在本文件的正文中。
齿轮径向跳动测量实验报告

齿轮径向跳动测量实验报告一、实验目的本实验的主要目的是掌握齿轮径向跳动测量方法,了解齿轮在运动中的变形情况,并通过实验数据分析其原因。
二、实验原理齿轮径向跳动是指齿轮在旋转过程中,齿顶和齿谷之间的距离变化。
这种变化会导致齿轮的变形和振动。
为了测量齿轮径向跳动,可以使用厚度测量仪或激光干涉仪等工具。
三、实验器材与试件1. 高精度激光干涉仪2. 齿轮测试台3. 直角尺、卡尺等测量工具四、实验步骤1. 将待测齿轮安装在测试台上,并调整好测试台的位置和方向。
2. 使用直角尺等工具将激光干涉仪安装在测试台上,并根据需要进行调整。
3. 打开激光干涉仪,并进行预热和校准。
4. 将激光束对准待测齿轮表面,开始进行测量。
5. 根据测量结果,分析齿轮径向跳动的原因,并进行记录和整理。
五、实验结果与分析通过实验测量,我们得到了待测齿轮的径向跳动数据。
根据这些数据,我们可以分析出齿轮在运动中产生径向跳动的原因。
首先,齿轮材料的质量和加工精度对径向跳动有很大影响。
如果材料质量不好或者加工精度不高,就容易导致齿轮表面出现凸起或凹陷,从而产生径向跳动。
其次,齿轮在运动过程中受到的载荷也会影响径向跳动。
如果载荷不均匀或者过大,就会导致齿轮表面变形和振动,从而产生径向跳动。
最后,安装和调整不当也会导致齿轮径向跳动。
如果测试台位置或方向不正确,或者激光干涉仪安装不稳定等问题都可能导致测试结果不准确。
六、实验结论通过本次实验,我们掌握了齿轮径向跳动测量方法,并且了解了齿轮在运动中产生变形和振动的原因。
同时,在实验过程中我们也发现了一些问题,例如测试台位置和方向的调整、激光干涉仪的安装等,这些问题都需要我们在以后的实验中加以注意和改善。
- 1、下载文档前请自行甄别文档内容的完整性,平台不提供额外的编辑、内容补充、找答案等附加服务。
- 2、"仅部分预览"的文档,不可在线预览部分如存在完整性等问题,可反馈申请退款(可完整预览的文档不适用该条件!)。
- 3、如文档侵犯您的权益,请联系客服反馈,我们会尽快为您处理(人工客服工作时间:9:00-18:30)。
齿轮径向跳动检测
一、实验目的、
1、了解卧式径向检查仪工作原理及使用方法。
2、学会使用卧式径向检查仪检测齿轮径向跳动。
二、实验原理
图2-1
1-底座;2-工作台固紧螺丝;3-顶针固紧螺丝; 4-被测齿轮;5-升降螺母
6-指示表抬起手柄;7-指示表;8-测量头;9-中心顶针;
图2-2
齿圈径向跳动误差ΔFr是在齿轮一转范围内,处于齿槽内或轮齿上、与齿高中部双面接触的测头在齿槽内或齿轮上,于齿高中部双面接触,测头相对于齿轮轴心线的最大变动量。
见图2-2a,以齿轮基准孔的轴线o为中心,转动齿轮,使齿槽在正上方,再将球形测头(或用圆柱)插入齿槽与左右齿面接触,从千分表上读数,依次测量所有齿。
将各次读数记在坐标图上,如图2-2b所示,取最大读数与最小读数之差作为齿圈径向跳动误差。
三、实验步骤
1、查阅仪器附件盒表格,根据被测齿轮选取球形测头,并将测头装入表的
测杆下端。
2、 把擦净的被测齿轮装在仪器的中心顶尖上,安装后齿轮不应有轴向窜动!
借助升降螺母5与抬起手柄6调整指示表,使指示表有一到二圈的压缩量; 3、 球形测头伸入齿槽最下方即可读数,读完数,向后扳拨杆,抬起千分表转过一齿,再放下,开始测第二齿。
如此依次测量各个齿面,把指示表的读数记下,并绘制出齿圈径向跳动图,取最大读数与最小读数之差,算出齿圈
径向跳动误差ΔFr(r F ∆=m ax r -min r )。
4、 根据齿轮的技术要求,查出齿圈径向跳动公差F r,判断合格性:
合格条件:r F ∆≤r F 为合格
四、 实验数据记录及处理
1、齿轮齿数Z=30,齿顶圆da=48.02mm
2、根据da=(2h a
*
+z )m,得m标准值为1.5mm
∴d=mz=45mm
4、∴ r ma x=4.2um
r min =-3.2um
5、所以 r F ∆=m ax r -min r =7.4u m 6、查表,得F r=23um ∴ r F ∆≤r F 检验合格。