部分常见零件的变形及改进分析
机械零件加工变形的原因分析及其改进

机械零件加工变形的原因分析及其改进摘要:机械零件在加工过程中发生变形难以避免,同时也是机械加工行业中广泛关注的问题。
由于机械零件加工中发生变形容易影响零件质量,因此,应尽可能减少由于变形而引起的质量问题。
文章首先分析了机械零件加工变形的原因,然后寻找相应的改进策略,以期对机械零件加工变形的处理提供参考借鉴。
关键词:机械零件;加工变形;原因;改进机械加工过程中由于受到种种因素的影响,机械零件加工的变形问题一直层出不穷,变形的零件不仅给机械加工业带来了经济损失,而且还影响到了企业在社会上的信誉,产品质量不能得到保证,这样的发展现状不利于机械加工业的正常运营,所以必须找到机械零件加工变形的原因,从而寻求解决问题的办法,推进机械加工业的长期发展。
1 常见机械零件加工中变形的原因1.1 由于内力的作用,零件加工精度改变因为在车床加工的过程中,通常采用四爪卡盘卡紧零件,然后利用其向心内力的作用,对零件进行加工。
并且在零件加工的过程中,也会受到内径向力的作用。
如果没有很好的掌控这两种内力,会导致机械零件松动,进而导致零件加工变形现象的发生。
另外,还应该注意如果机械零件的夹紧力减小,则机械的切削力也要随之而减小,相反机械零件夹紧力变大,机械的切削力也必须加大,只有这样才能保证所加工的零件受力均匀。
但是在实际加工中所面临的问题是,加工后的机械零件的形状与需要形状并不匹配,其精确度已经出现了很大的出入,而出现这种状况的原因是加工不够细腻,导致质量不过关。
1.2 热处理后和加工后机械零件变形问题一些比较薄的机械零件很容易变形,因为他们的长径比例较大,在加工或者热处理后会出现弯曲的状况,这种弯曲被称为草帽弯曲。
这种弯曲会导致其平面变大,而长径比较小的机械零件经过热处理或是加工后也会出现变形,导致零件的直线度相对偏大。
原因是零件本身就具有内应力,而这种内应力是相对平衡的状态,但经过热处理或加工之后,零件自身的内应力发生改变,从而导致零件的外观发生变形。
薄板零件变形原因及解决方法浅析

Internal Combustion Engine&Parts0引言在汽车产品的结构设计中,薄板零件得到广泛应用,本文提到的薄板零件是指厚度在4mm以下,在长方形或圆形的板料中厚度与短边的比值不大于0.2mm的金属薄板[1]。
此类零件薄而宽大,受轧制工艺路线、储运、下料、加工及装配方式等生产过程各因素的影响,成品零件产生的塑性变形变形明显无法满足产品的质量要求。
因此,如何防范、消除零件的变形缺陷,是产品生产厂家亟待解决的问题。
1薄板零件变形的原因在温度变化或力的作用下,薄板零件会产生形状和尺寸大小的改变。
当零件承受的应力在弹性极限以内时,零件产生的变形是弹性变形,外力消除后,零件将恢复原有形状。
如果零件受到应力超过了材料的弹性极限,零件产生弹性变形的同时还产生了塑性变形,此力消除后,弹性变形部分恢复,而塑性变形保留下来,即零件产生了永久变形。
薄板零件主要以收缩变形、角变形、弯曲变形、扭曲变形等大挠度的变形为主[2],也是现实中面临的主要问题。
薄板零件变形的主要原因有以下几方面:①薄板生产过程中,板材受热不均、轧辊弯曲、轧辊间隙不一致等问题,就会使板材在宽度方向的压缩不均匀,有可能失稳而导致变形[3]。
②储存、运输过程不正确的放置方式,使零件受到外力、高温或震动等原因,残余应力会逐渐释放出来或重新分布,造成零件变形。
③材料加工过程产生的变形,材料加工过程中经过火焰切割、剪切、冲裁、切削等某一道或几道工序,每一工序都会引起钢材变形。
④薄板在进行焊接时,容易出现多种类型的变形,距离焊接缝隙较远的位置会产生一定的残余应力,若这些残余应力超过了薄板的变形临界压力时,会导致薄板出现变形。
⑤零件装配过程引起的变形,如零件不当的装配顺序、固定方式、夹具安装位置、零部件间的位置公差过大、紧固和锁紧不当等影响因素。
⑥零件承受超负荷加载或零件受到各种冲击性载荷,使零件产生塑性变形。
位移达0.4mm,远超过标准规定的0.05m,振动数据己降为4.9mm/s,运行恢复正常。
零件装夹变形分析与解决措施

零件装夹变形分析与解决措施零件变形主要表现在装夹变形;切削力、切削热使零件产生变形;加工方法和技巧不当使零件产生变形;材料应力释放零件原因导致的变形等。
如果在生产过程中工件产生变形,那么肯定就会影响工件的形位精度,尺寸精度以及表面粗糙度,所以提高易变形零件加工质量和加工效率的关键就是装夹方法以及车削,铣削时的加工方法和技巧。
标签:装夹方法;刀具选择;切削用量1 为什么会产生零件装夹变形我们在加工生产中会遇到各种各样的问题,譬如在加工薄壁易变型零件时,就必须根据其不同的特点,找出薄弱环节,选用不同的工艺方法和夹紧方法来保证加工要求。
很多时候我们要具体问题具体分析,找到切实可行的办法来应对遇到的实际问题。
1.1 工件装夹不当为什么会产生变形?在我们生产实际操作中,如果我们采用三爪卡盘夹紧薄壁外圆,就会由于夹紧面积过小,夹紧力不均匀分布,那么拆卸以后,被卡爪夹紧部分就可能因弹性变形而涨大,最终导致零件出现多角形变化。
1.2 相对位置调整时候偏差,产生壁厚不均的现象经过多年的工作实践,我发现由于夹具、刀具,工件和机床主轴旋转中心的位置调整相对不准确,导致工件几何形状变化和壁厚不均匀现象。
我们遇见很多薄壁零件对于均匀性要求非常高,但对其尺寸精度要求却不高这种现象。
此时工件如果采用常规刚性定位,就会误差非常大,壁的厚度很容易超差。
这样工件在装夹过程中,假设我们没有根据实际特性,也就是工件刚度较低(薄壁件),或者不注意夹紧力的方向和施力点,那么支撑点和压紧点不能够重合就形成力矩效应,最终会引起零件变形。
1.3 为什么要强调零件壁厚差重要性有一部分薄壁零件对均匀性要求非常高,而对其尺寸精度要求却不高。
这种工件和彩刚性定位,就会误差很大,壁厚非常容易超差。
在装夹过程中的工件,假设刚度较低(薄壁件)或者夹紧力方向,施力点选择不恰当,支撑点与压紧点不重合必然形成力矩效应将会引起零件变形。
1.4 选用什么样的刀具至关重要我们选择什么样的刀具,会直接影响零件精度以及表面粗糙度。
薄壁零件变形分析及改进建议

薄壁零件变形分析及改进建议薄壁零件变形分析及改进建议摘要:随着我国社会主义经济的快速发展,各行各业都呈现繁荣景象。
由于薄壁零件具有质量轻、节约材料、结构较为紧密等优良特点,而被广泛应用于机械加工行业。
但是薄壁零件具有口小内大、薄壁、刚性差的缺陷,极易在机械加工过程中发生振动和形变,致使加工过程不能保证加工精度。
通过对薄壁零件进行反复的实验,找出在加工过程中零件发生形变的解决策略。
本文从实际出发,总结和分析了薄壁零件易发生振动和变形的原因,阐述了控制加工过程中薄壁零件发生振动和变形的有效方法,从而保证加工的精度。
关键词:薄壁零件;变形;分析;方法;前言由于薄壁零件具有刚性差、易变形的特点,严重影响了机械加工的精度。
薄壁零件的加工易变形的问题一直是困扰着机械加工行业的主要难题。
为此,许多国内外的专家学者通过反复的实验和验证,建立了多种动态或静态模型,采用先进的有限元技术对加工过程中的刀具和工件进行分析,并依据结论提出了改进加工的有效方法,从而使得薄壁零件的加工工艺有了一些进步。
但在实际生产过程中,我们需要对加工过程中出现的实际变形情况,采用不同的控制措施,以取得较好的生产效率。
影响薄壁零件变形的主要因素在机械加工过程中薄壁零件发生振动和变形的原因多种多样,具有各个方面的影响因素,首先就是在进行零件的设计时,要对零件的结构、工艺性及刚性进行充分的考虑,不断提高薄壁零件的刚性,尽可能的避免加工过程中零件变形,还要保证薄壁零件的对称结构和均一厚度。
在进行零件加工时,选择消除了内应力的毛坯材料。
2.1工件的装夹条件因为薄壁零件具有较差的刚性,在进行加工过程中,如果夹紧力和承受力的作用位置选择不合适,就会增加薄壁零件的内应力;夹、压所产生的弹力极易造成变形,从而影响了零件的表面尺寸、形状和精度,进而导致薄壁零件的变形。
因此,对零件的装夹、定位的合理设计,有助于降低变形的可能性,充分保证加工质量。
2.2加工的残余应力在机械加工过程中,对零件进行加工时会造成刀具与零件的挤压、刀具前刀面和后刀面与已加工表面的挤压、摩擦等作用,从而增加了薄壁零件内部的加工残余应力。
冲压件常见质量缺陷及原因分析,整改对策
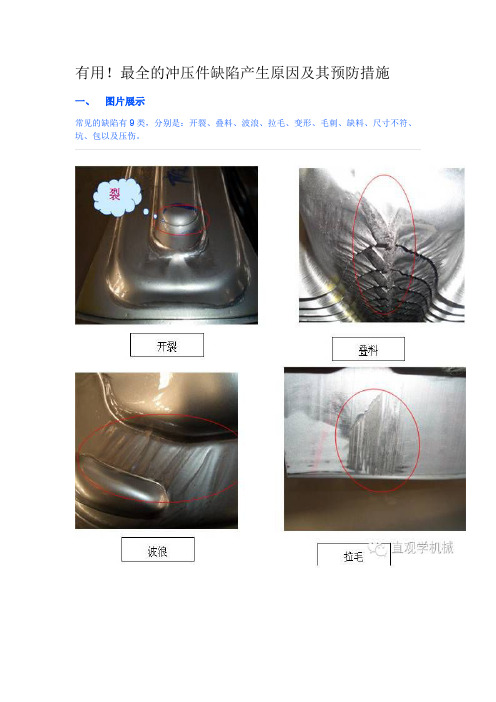
有用!最全的冲压件缺陷产生原因及其预防措施一、图片展示常见的缺陷有9类,分别是:开裂、叠料、波浪、拉毛、变形、毛刺、缺料、尺寸不符、坑、包以及压伤。
二、冲压件缺陷原因及预防1.冲压废品1)原因:原材料质量低劣;冲模的安装调整、使用不当;操作者没有把条料正确的沿着定位送料或者没有保证条料按一定的间隙送料;冲模由于长期使用,发生间隙变化或本身工作零件及导向零件磨损;冲模由于受冲击振动时间过长紧固零件松动使冲模各安装位置发生相对变化;操作者的疏忽,没有按操作规程进行操作。
2)对策:原材料必须与规定的技术条件相符合(严格检查原材料的规格与牌号,在有条件的情况下对尺寸精度和表面质量要求高的工件进行化验检查。
);对于工艺规程中所规定的各个环节应全面的严格的遵守;所使用的压力机和冲模等工装设备,应保证在正常的工作状态下工作;生产过程中建立起严格的检验制度,冲压件首件一定要全面检查,检查合格后才能投入生产,同时加强巡检,当发生意外时要及时处理;>前沿数控技术微信不错,记得关注。
坚持文明生产制度,如工件和坯件的传送一定要用合适的工位器具,否则会压伤和擦伤工件表面影响到工件的表面质量;在冲压过程中要保证模具腔内的清洁,工作场所要整理的有条理加工后的工件要摆放整齐。
2.冲裁件毛刺1)原因:冲裁间隙太大、太小或不均匀;冲模工作部分刃口变钝;凸模和凹模由于长期的受振动冲击而中心线发生变化,轴线不重合,产生单面毛刺。
2)对策:保证凸凹模的加工精度和装配质量,保证凸模的垂直度和承受侧压力及整个冲模要有足够的刚性;在安装凸模时一定要保证凸凹模的正确间隙并使凸凹模在模具固定板上安装牢固,上下模的端面要与压力机的工作台面保持相互平行;要求压力机的刚性要好,弹性变形小,道轨的精度以及垫板与滑块的平行度等要求要高;要求压力机要有足够的冲裁力;冲裁件剪裂断面允许毛刺的高度冲裁板材厚度>0.3>0.3-0.5>0.5-1.0>1.0-1.5>1.5-2.0新试模毛刺高度≤0.015≤0.02≤0.03≤0.04≤0.05生产时允许的毛刺高度≤0.05≤0.08≤0.10≤0.13≤0.153.冲裁件产生翘曲变形1)原因:有间隙作用力和反作用力不在一条线上产生力矩。
薄壁套零件的加工变形分析和工艺改进
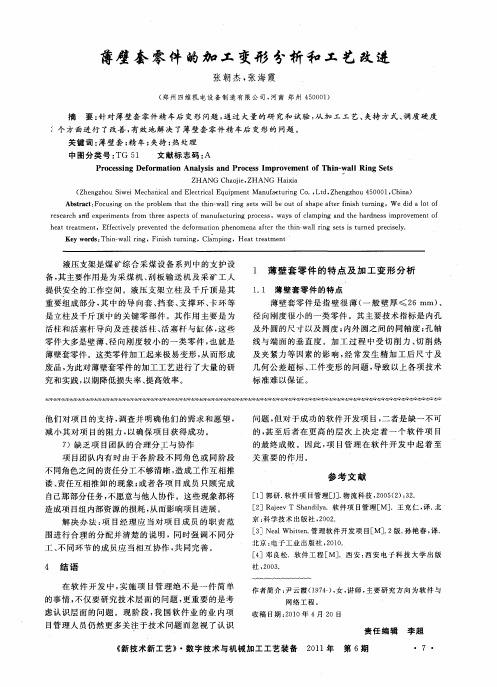
由于宽 软爪夹 持后 能有 效地 将夹 紧力均 布 于工 件表面, 松开 工件 后 , 件 弹 性 变形 均 匀 , 高 _ 工 提 r工
件 的精 度 。 2 3 控制调 质硬 度 . 零件 的切 削性 能 与材 料 的硬度 、 塑韧 性 密切 相
将 粗加 工 、 精 加 工 、 加 工分 开 进 行 , 避 免 半 精 可
图 1 普通 三爪 定 心 卡盘 夹持 使 工 件 变 形 示 意 图
2 工 艺 改进
通 过反 复 的实践 和分析 , 以增加 半精 车工 序 、 可 定 性处 理 ( 将工 件加 温至 2 0 0 5  ̄3 0℃ , 温 2 ) 保 ~3h
的变形 。缺 点为成 本高 , 只适 合大 批量 、 成规 格 的牛
作 者 简 介 : 云 霞 ( 9 4)女 , 师 , 要 研 究 方 向 为 软 件 与 尹 1 7一 , 讲 主
网络工程 。 收 稿 日期 :0 0年 4月 2 日 21 0
虑认 识层 面 的 问题 。现 阶段 , 国软 件 业 的业 内项 我
目管 理人员 仍 然更 多关 注 于技术 问题 而 忽视 了认 识
自己那 部分任务 , 不愿意与 他人协 作 。这些 现象都将
造成项 目组 内部 资源 的损 耗 , 从而影 响项 目进 展 。 解 决 办法 : 目经 理 应 当对项 目成 员 的职 责范 项 围进 行合 理 的分 配并 清楚 的说 明 ,同时 强调 不 同分
E ]Nel i e. 3 a Wht n 管理软件开发项 目E . t M] 2版. 孙艳 春 , 译.
产。
2 )加 大夹 持面 积 以降低 压强 , 径 向夹 紧 力均 使
布工 件表 面 。常见 的 方式 有 软 爪 夹 持 、 软爪 和 开 口
薄壁零件夹持变形与装夹方法的改进分析
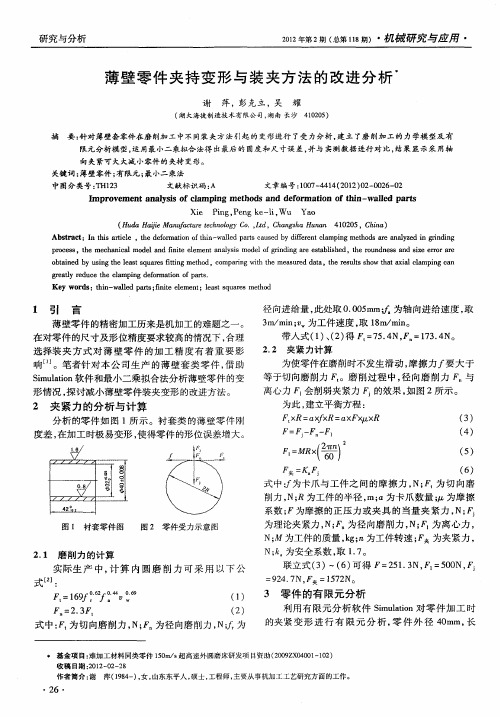
o ti e y u i g t el a t q ae t n t o c mp r gw t h a u e aa, h e u t h w a x a lmp n a b a n d b sn e s u rsf t g meh d, o a i i te me r d d t t e r s lss o t ta i c a i g c n h s i i n h s h l
径 向进 给量 , 此处取 0 O 5 m 为轴 向进 给速 度 , .0 m 取 3 / i ; 为工件 速度 , 1 m m n m mn 口 取 8 / i。 带 入式 ( ) ( ) F = 5 4 F =1 3 4 1 、 2 得 7 . N, 7 . N。 2 2 夹紧 力计算 .
1 引 言
薄 壁零 件 的精 密加 工历 来是 机 加工 的难题 之一 。 在 对 零 件 的尺 寸及 形位 精 度要求 较 高 的情 况 下 , 理 合 度 有 着 重 要 影 响 … 。笔 者 针 对 本 公 司 生 产 的薄 壁 套 类 零 件 , 助 借 Smuai i ltn软 件 和最 d -乘 拟合 法分 析 薄壁 零 件 的变 o x 形 情 况 , 讨减 小 薄壁 零 件装 夹变 形 的改进 方法 。 探
g e t e u e t e c a i g d f r a in o a t . r a y r d c h l mp n eo l m t fp rs o Ke r s h n wa e at ; n t lme t e s q ae t o y wo d :t i - l d p r f i e e n ;l a t u r s meh l si e s d
p o e s h c a i a d la d f i lme ta ay i mo e f r dn r sa l h d,t e ru d e s a d sz ro r r c s ,t e me h n c lmo e n n t ee n n l s d lo i i g a ee tb i e i e s gn s h o n n s n ie er rae
零件凹陷改善对策
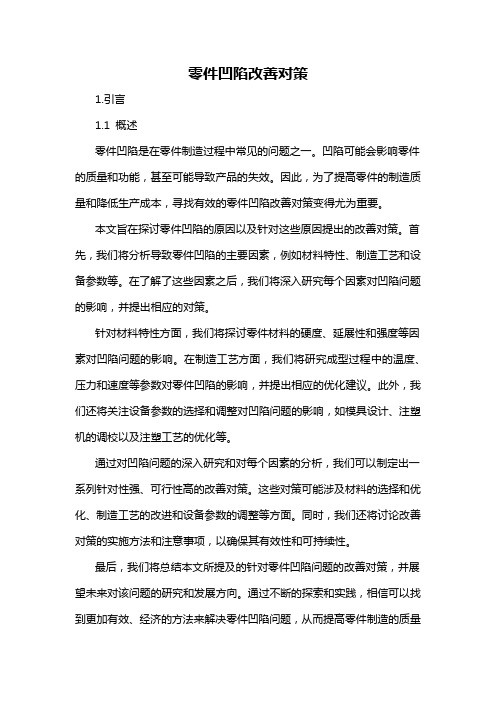
零件凹陷改善对策1.引言1.1 概述零件凹陷是在零件制造过程中常见的问题之一。
凹陷可能会影响零件的质量和功能,甚至可能导致产品的失效。
因此,为了提高零件的制造质量和降低生产成本,寻找有效的零件凹陷改善对策变得尤为重要。
本文旨在探讨零件凹陷的原因以及针对这些原因提出的改善对策。
首先,我们将分析导致零件凹陷的主要因素,例如材料特性、制造工艺和设备参数等。
在了解了这些因素之后,我们将深入研究每个因素对凹陷问题的影响,并提出相应的对策。
针对材料特性方面,我们将探讨零件材料的硬度、延展性和强度等因素对凹陷问题的影响。
在制造工艺方面,我们将研究成型过程中的温度、压力和速度等参数对零件凹陷的影响,并提出相应的优化建议。
此外,我们还将关注设备参数的选择和调整对凹陷问题的影响,如模具设计、注塑机的调校以及注塑工艺的优化等。
通过对凹陷问题的深入研究和对每个因素的分析,我们可以制定出一系列针对性强、可行性高的改善对策。
这些对策可能涉及材料的选择和优化、制造工艺的改进和设备参数的调整等方面。
同时,我们还将讨论改善对策的实施方法和注意事项,以确保其有效性和可持续性。
最后,我们将总结本文所提及的针对零件凹陷问题的改善对策,并展望未来对该问题的研究和发展方向。
通过不断的探索和实践,相信可以找到更加有效、经济的方法来解决零件凹陷问题,从而提高零件制造的质量和效率。
在接下来的正文中,我们将详细讨论每个因素及其对策,并探索如何将这些对策应用于实际生产中,以期达到改善零件凹陷问题的目标。
1.2 文章结构文章结构部分的内容可以包括以下几方面的描述:文章结构部分旨在介绍本文的整体组织结构,以引导读者对文章内容的整体把握。
本文分为引言、正文和结论三个主要部分。
引言部分介绍了本文的背景和目的。
接下来是正文部分,主要包括了零件凹陷的原因和零件凹陷改善对策两个部分。
2.1 零件凹陷的原因部分详细阐述了零件凹陷的原因。
可以从以下几个方面进行描述:首先,可以介绍零件凹陷在制造过程中可能出现的一些常见原因,如材料不足、加工不当、工艺参数设置错误等。
薄壁零件的变形

薄壁零件的变形引言:薄壁零件是工程设计中常见的一类零件,它们通常具有较大的长度和宽度,但相对较小的厚度。
由于其特殊的结构,薄壁零件容易发生变形。
本文将探讨薄壁零件变形的原因、影响以及相应的解决方法。
一、薄壁零件变形的原因1.材料特性:薄壁零件通常采用金属材料制造,而金属材料在受力时容易发生塑性变形。
由于薄壁零件的厚度较小,其受力时的应力集中效应较为明显,进而导致材料发生变形。
2.制造工艺:薄壁零件在加工过程中,如切割、折弯、焊接等,容易受到应力的集中,从而引起变形。
此外,制造工艺中的温度变化、冷却过程等也会对薄壁零件的形状产生影响。
3.外部环境:薄壁零件在使用过程中,受到外部力的作用,如振动、冲击、压力等,这些外部环境的变化也会导致零件的变形。
二、薄壁零件变形的影响1.几何形状:薄壁零件变形会导致其几何形状发生改变,不符合设计要求,从而影响零件的功能和装配。
2.尺寸精度:薄壁零件的变形会使其尺寸精度下降,无法满足设计要求,导致装配困难或无法正常工作。
3.强度和刚度:薄壁零件变形后,其强度和刚度可能会下降,从而影响零件的承载能力和稳定性。
三、薄壁零件变形的解决方法1.材料选择:选择具有较高强度和刚度的材料,以减小薄壁零件受力时的塑性变形。
同时,可以考虑使用复合材料等新型材料来提高薄壁零件的性能。
2.结构优化:通过优化薄壁零件的结构,减小应力集中,提高其受力均匀性。
可以采用增加加强筋、加大壁厚等方式来改善零件的结构。
3.制造工艺:合理选择制造工艺,控制加工过程中的变形。
采用适当的预应力、热处理等工艺措施,可以减小薄壁零件的变形。
4.应力分析:通过应力分析,确定薄壁零件的受力情况,找出应力集中的部位,并进行合理的加强设计,以提高零件的抗变形能力。
5.温度控制:在制造和使用薄壁零件时,注意控制温度的变化,避免温度差异引起的热应力导致变形。
结论:薄壁零件的变形是工程设计中常见的问题,其原因主要包括材料特性、制造工艺和外部环境等因素。
薄壁零件加工变形的原因分析及控制方法

薄壁零件加工变形的原因分析及控制方法摘要:在科学技术水平不断提高的今天,越来越多先进的技术和零件被不断的研发出来,并且在实际的应用过程当中能够发挥出良好的作用。
就从目前的情况看来,薄壁零件自身重量比较轻,整体的结构也比较紧凑,该零件在通常的情况下都会应用于航空、船舶等多种产品当中。
不过,薄壁零件在实际的加工过程当中往往会受到很多因素的影响,从而导致零件变形的情况,进而对产品质量造成很大程度的影响。
为此,相关企业需要对薄壁零件加工变形原因进行充分地分析,根据实际的情况来采取措施进行控制。
关键词:薄壁零件;加工变形;原因;控制前言通过实际的调查发现,现阶段我国航天航空和船舶工业随着社会整体经济水平的提高而得到了进一步发展,在这种情况下它们对生产的零件也有着较高的要求。
为了能够进一步提高薄壁零件的各项性能,相关企业在实际加工过程中要对影响其变形的原因予以足够的重视,并且对薄壁零件的加工特点进行充分地分析和了解,这样才可以对其进行有效地控制,为企业带来一定的经济效益。
一、导致薄壁零件加工变形的原因分析就从目前的情况看来,部分企业在对薄壁零件加工过程当中导致其发生变形的因素比较多,这些因素可以分为零件的刚度、工具夹装、走刀路线、切削参数等,对薄壁零件加工变形影响程度最大的三个方面是:切削力、装夹力和残余应力,这就要求加工人员要对这些方面进行充分地分析,在此基础上采取相应的措施来对加工方法进行不断的改进和调整,这样才可以保证薄壁零件在加工过程当中不会发生变形。
(一)加工过程中的切削力在通常的情况下,薄壁零件在加工过程当中切削力主要可以对其实际的尺寸、形状和位置造成一定程度的影响,切削力往往也会受到很多方面的影响,加工人员没有对零件进行充分分析而导致切线参数设置不合理,在实际进行切削的时候就会出现一定的误差还有就是加工人员对切削刀具的磨损程度没有进行充分地分析了解,这样就会导致切削无法达到预期的标准。
这些因素都会对切削力的设定值带来一定程度的影响,薄壁零件受到应力与热量之间的相互影响而最终就会出现变形,其自身的质量也会进一步的降低。
齿轮渗碳淬火热处理变形的分析与改进

齿轮渗碳淬火热处理变形的分析与改进在现代机械组合中齿轮是最常见、应用最多的零件之一,轮船、飞机、汽车、起重机等几乎所有的机械中都有齿轮的存在,足见其作用和用量之大。
在机械使用过程中时有齿轮失效情况的发生,主要包含轮齿疲劳折断与齿面疲劳损伤等问题。
现阶段制造生产齿轮的过程中,进行渗碳淬火热处理仍然是主流工艺,不过该方式存在一个较大的弊端,即为齿轮渗碳淬火热处理后的变形问题,该弊端大大降低了齿轮的质量。
标签:齿轮;渗碳处理;淬火处理、热处理变形;改进措施加工过程中对齿轮进行合理的热处理有利于增强其承载能力并提升其使用寿命,热处理应用较多的方式为渗碳淬火,该方法能有效提升齿轮的性能,不过该方式工序较为复杂,时常会因某些因素而导致齿轮出现变形等现象。
影响热处理变形的原因有很多,例如齿轮的结构、材料、锻造质量、预备热处理质量等等,而且这些因素还相互影响,很难控制,笔者对齿轮渗碳淬火热处理变形现象做了细致合理的分析,并针对其处理工艺等情况拟定了有效改善措施。
1 齿轮参数及热处理工艺1.1 齿轮参数本文所选齿轮材质:20CrMnTiH,具体参数为:模数=1.191mm、左旋25°、公法线=16.44(-0.05,0)mm、齿顶圆直径Φ=39.831(-0.1,0)mm、内径Φ=16(0,+0.018)mm。
该齿轮是对称中空结构,且内径、外径较大,无腹板支撑,壁厚相对薄,对其进行热处理较易发生变形。
1.2 齿轮热处理工艺该齿轮热处理工艺分别通过长度15米的渗碳淬火炉与长度8米的回火炉进行,具体工艺流程为:将齿轮放入渗碳炉中,经三小时由室温匀速升至(920±5)℃,之后恒温渗碳三小时,渗碳结束后经四十分钟匀速降温至(860±5)℃,之后恒温淬火五十分钟,其中淬火液需为80℃,之后对其进行为期2小时、温度为(160±5)℃的低温回火,原有工艺中齿轮进行渗碳时为四只齿轮分别平放。
模块焊接后变形原因分析
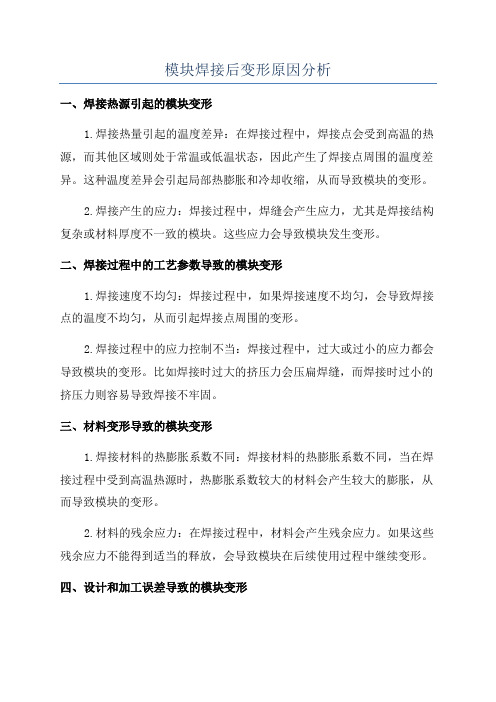
模块焊接后变形原因分析一、焊接热源引起的模块变形1.焊接热量引起的温度差异:在焊接过程中,焊接点会受到高温的热源,而其他区域则处于常温或低温状态,因此产生了焊接点周围的温度差异。
这种温度差异会引起局部热膨胀和冷却收缩,从而导致模块的变形。
2.焊接产生的应力:焊接过程中,焊缝会产生应力,尤其是焊接结构复杂或材料厚度不一致的模块。
这些应力会导致模块发生变形。
二、焊接过程中的工艺参数导致的模块变形1.焊接速度不均匀:焊接过程中,如果焊接速度不均匀,会导致焊接点的温度不均匀,从而引起焊接点周围的变形。
2.焊接过程中的应力控制不当:焊接过程中,过大或过小的应力都会导致模块的变形。
比如焊接时过大的挤压力会压扁焊缝,而焊接时过小的挤压力则容易导致焊接不牢固。
三、材料变形导致的模块变形1.焊接材料的热膨胀系数不同:焊接材料的热膨胀系数不同,当在焊接过程中受到高温热源时,热膨胀系数较大的材料会产生较大的膨胀,从而导致模块的变形。
2.材料的残余应力:在焊接过程中,材料会产生残余应力。
如果这些残余应力不能得到适当的释放,会导致模块在后续使用过程中继续变形。
四、设计和加工误差导致的模块变形1.模块设计不合理:模块的设计不合理,如强度不足、刚度不够等问题,会使模块在焊接过程中更容易发生变形。
2.零件加工精度不高:如果焊接之前的零件加工精度不高,即使焊接过程中没有其他问题,也会导致模块变形。
综上所述,模块焊接后的变形有多种原因,包括焊接热源引起的热膨胀和冷却收缩、焊接产生的应力、焊接过程中的工艺参数、材料的热膨胀系数和残余应力以及设计和加工误差等。
为了减少模块焊接后的变形,可以从控制焊接参数、选用合适的材料、进行适当的热处理、改善设计和加工精度等方面入手,并在焊接前进行充分的分析和优化设计。
机械零件变形成因分析及应对措施

OCCUPATION2013 0984交流E XPERIENCE摘 要:零件变形是机械加工中经常遇到的问题。
明确零件变形的成因,掌握防止零件变形的措施,对于提高零件的加工质量十分重要。
关键词:零件 变形 内应力 加工工艺机械零件变形成因分析及应对措施文/赵学文变形是机械零件在加工过程中普遍存在的现象,它会使零件的加工质量和性能发生改变,从而影响零件的精度和寿命,零件的加工中必须有效防止零件变形。
笔者根据多年实践和体会,就机械加工中零件变形成因及应对措施阐述如下。
一、机械加工中零件变形的成因就变形的成因来讲,零件的变形是各种力作用的结果。
产生变形的作用力可分为两类。
一类是加工过程中产生的外力。
它来源于零件加工过程中的各种夹紧力、切削力、冲击力等,引起零件在刚性较差的方向产生弹性形变,出现让刀现象,加工结束后弹性恢复,使其达不到加工精度。
另一类是零件内部产生的内应力,它来源于零件内部。
因加工条件改变,引起零件材料内部组织变化,产生内应力,如铸造应力、锻造应力、焊接应力、淬火应力等。
在零件加工过程中,零件因所受作用力的性质不同,产生不同的变形效果,并且会在加工的不同阶段产生不同的变形。
外力引起的变形大多发生在零件机械加工的冷加工中。
零件在装夹时,夹持方式不当、夹紧力各要素选择不当会引起夹紧变形,如薄壁零件、悬臂零件的装夹。
在切削加工时,刀具角度不合理、切削要素不合理,会造成切削抗力增大,从而引起零件的弹性变形,如在细长轴车削时产生的腰鼓变形。
内应力引起的变形大多发生在零件的热加工及其后续的切削加工中。
一是在热加工中,零件在加热、受力、冷却等条件改变时内部组织结构发生变化,产生内应力,发生变形。
如在铸造加工中,零件壁厚不均、冷却速度过快等会产生铸造内应力,引起铸造变形;在锻造加工中,产生锻造内应力,引起锻造形变;在焊接加工中,产生焊接应力,引起焊接变形。
二是零件经热加工后,其内应力得不到充分的释放和消除,仍然留在零件内部形成残余应力。
板式家具板类部件的变形及解决方法

板式家具板类部件的变形及解决方法制造板式家具时,大都采用中密度纤维板、细木工板、刨花板以及胶合板等作为板式家具的基材,这些基材具有幅面大、表面平整、易于加工、便于涂饰等优点,但也有吸湿、弹性变形等缺点。
有些刚刚加工好的家具的部件过不了几天就发生了变形,如原先平整的柜门发生了翘曲,而且基本上没有办法恢复。
如何解决这些令人头痛的问题呢?实际上,可以从产生变形的原因来进行探讨。
众所周知,构成板式家具的主要零部件有旁板,搁板、门板、顶板或面板以及背板等,板件所存在的主要变形有板件的弹性弯曲、翘曲、蠕变等,其中,翘曲和蠕变在很大程度上取决于基材本身的内在质量,而零部件的弹性弯曲,除了板件本身的质量之外,主要还取决于生产过程的管理和工艺的处理。
对于基材本身的问题,可以选用内应力较小,强度较大的品牌产品。
而对于在外力作用下的弹性变形,则是一个比较复杂的问题,下面就以搁板和高柜的长门为例来加以分析。
1 搁板的弯曲变形1.1 搁板的受力情况板式家具的搁板重要承受到以下几种应力:1)压应力是承载物件的压力及搁板自重形成的应力。
是造成搁板变形的主要原因。
2)弯曲压力是承载弯距形成的应力,能使搁板弯曲和蠕变。
3)剪切应力由承载搁板支撑或连接件接口处压力与支撑力产生的剪切作用而形成。
4)涂料固化应力由于搁板表面涂料固化的内表收缩不一致而产生的内应力,使得搁板弯曲变形。
以上4种应力造成板式家具搁板弯曲变形。
1.2搁板的受力分析:在上述应力中,对搁板的弯曲影响最大的是压应力,其弯曲程度取决于负荷的大小,配置的情况以及材料的尺寸和本身的特性。
搁板在负荷下产生的弯曲变形可以用下列公式来计算:1)负荷集中于搁板中心时(图1)Y=PL3/4Ebh32)当负荷均匀分布时(图2)Y=5QL4/32Ebh3式中:y——弯曲变形量(m)p——负荷(N)L——支点间的距离(m)b——搁板断面的宽度(m)H——搁板的厚度(m)E——材料的弹性模量(Pa)Q——均布负荷(N/m)在对上述的公式进行分析时就会发现,搁板材料的弹性模量最能体现出抗弯强度的主要特征,材料的弹性模量是由材料本身的材质决定的,弹性模量越大,材料的抗变形能力越强。
薄壁零件车削加工中热变形分析及对策

薄壁零件车削加工中热变形分析及对策薄壁零件在车削加工过程中容易受到热变形的影响,影响产品的加工精度和表面质量。
对薄壁零件车削加工中的热变形进行分析并提出对策是非常必要的。
本文将从热变形的原因、分析方法以及对策措施等方面进行深入探讨,以期为相关行业提供一些有益的参考。
一、热变形的原因1.1 刀具和工件之间的摩擦在车削加工中,刀具和工件之间的摩擦会产生大量的热量,导致工件局部升温。
当工件表面发生热变形时,其形状和尺寸都会发生变化,从而影响产品的加工精度。
1.2 切削温度的影响1.3 切削速度和进给速度对热变形的影响切削速度和进给速度的选择直接影响着切削过程中的热变形情况。
如果选择不当,容易引起工件的热变形,进而影响产品的加工质量。
二、热变形的分析方法2.1 数值模拟分析通过数值模拟分析的方法,可以对车削过程中的热变形情况进行较为准确的预测。
数值模拟分析可以方便地获取刀具和工件间的摩擦热源以及切削温度等信息,从而为热变形的分析和对策提供科学依据。
2.2 实验测量分析三、对策措施3.1 采用合适的刀具材料为了减少车削过程中的热变形,可以选择较高的热导率和热稳定性较好的刀具材料,如硬质合金等,以提高刀具的散热性能,从而减少切削时的热量积累。
3.2 优化切削参数针对薄壁零件的车削加工,可以通过优化切削速度、进给速度和切削深度等参数,以减少切削时的热量积累,从而减少热变形的产生。
3.3 冷却液的应用在车削加工过程中,适当地应用冷却液可以有效地降低工件的表面温度,从而减少热变形的产生。
冷却液还可以有效地冷却刀具,减少刀具的磨损和延长使用寿命。
3.4 加强工件的支撑在薄壁零件的车削加工过程中,应加强对工件的支撑,以减少工件的挠曲和变形,从而降低热变形的影响。
零件弯曲变形的分析研究与改进措施

零件弯曲变形的分析研究与改进措施摘要:一些机械零件在长期受到外加环境载荷和内部环境的共同作用下后,就可能会逐渐损失自身零件原有的力学机械性能及物理、化学或其他特殊性能,直至不能完全恢复到继续正常运行服役的特殊现象,我们称之为零件弯曲变形所导致的零件失效现象。
根据零件弯曲变形的特点、所受载荷的类型及所处条件的不同,零件弯曲变形的原因可归纳为受力引起的弯曲变形,热处理过程中引起的弯曲变形以及弹性及塑性变形几类。
在实际操作中,由于不同客观因素的影响,机械零件会发生变形,这不仅影响了企业的经济效益而且缩短了产品的使用寿命。
激烈的市场竞争中企业要提高竞争力,就必须研究机械零件变形的原因和改进措施。
关键词:机械零件、弯曲变形、原因分析、方法措施1零件弯曲变形研究意义机械加工的性能不仅仅关系着企业的切身利益,而且关系到机械加工过程中的安全。
好的机械加工设备在为企业发展带来最大经济效益基础的同时还有效地降低了机械零件安全事故发生的最大可能性。
因此,在机械加工零件的使用过程中,避免加工零件发生变形尤为重要,零件变形加工时机械操作技术人员自身应充分考虑到各种因素和环境条件,在加工过程中及时采取适当防护措施以防止零件变形,使一件成品零件能正常加工使用。
那么为了能够使这些零件材料变形的加工事故尽可能不发生或少量的发生,就需要我们去详细分析这些零件材料加工发生变形的主要原因,确定这些零件加工变形的可靠解决措施,以此为实现现代企业战略目标提供坚实的基础。
2变形原因分析2.1受力引起的弯曲变形(1)内力作用引起的变形当车床机械加工重要零件时,可用机械夹具固定整个工件。
为了能够保证零件在加工过程中不至于出现松动损坏情况,必须要特别注意对切削力的自动控制,灵活地改变切削力以便于保证松动工件始终低于规定夹紧切削力。
同时,为了能够保证整个零件材料加工的正常有序进行,还需要及时调整整个工件上下受力平衡情况,以此来保证整个工件上下的受力平衡。
机械零件加工常见的变形原因与应对措施分析
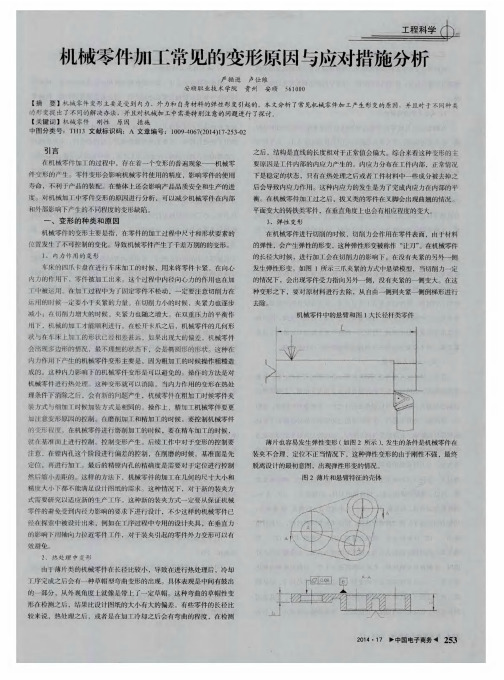
面对零件变形中多种 多样的情况 ,处理途径只有一种那就是增加机 械零件的刚性程度。这种 刚性的控制一定要早控制在预先发生的变形之
前。 1 、减 小 夹 紧力 的 措 施
热 变形情况减少 ;因此 ,充分 的切削 液可 以减少零件 的变形 。
3 、减 小 内 应 力 的 措 施
机械零件在加 工中 ,要注 意各种 参数和工艺方法 的运用 。机 械零
件 的浇 口和 冒口袋 地让 要在冷却之后 , 终止煅造温度 的升高 ,机械零 件 也要注意保温 和缓慢冷却 。 在进行 对称焊接 的工序 时候 , 冷 却的速 度 要在焊接之后缓 慢降低 。 在机械零件 出现热 处理之后的 变形时候 ,
是一项技术性和综合性 的课题 ,只有在实践的基础 上多加总结 ,才能
的 、细的加丁分开 来进行 , 控 制好切削力 和切削时候 的温 度对 于整体 机械零件 的影响 。在薄壁零件 的车削 中,合理的刀具对 车削时切削力
的大小产 生的热变形 、工件表 面的微观都 是至关重要 的。控制刀具前
角大小 ,与刀具前角 的锋利 程度 。前角大 , 变形 和摩擦力减小 。 但前 角过 大 , 会 使刀具的楔 角变小 ,强度减弱 , 散热情 况差 ,磨损速度加 快。 所以, 薄壁零 件加工 时 , 用高速 的刀具 , 前角 取 6 。~ 3 0 。大小 , 用硬 质合金刀具 , 前角取 5 。~ 2 O 。大小 的角度 。 后 角大 , 摩擦变 小 , 切削 力也变减小 。使 刀具 强度减弱 。用高速 钢车刀的时候 ,刀具后 角
于机械零件 中的铸件处理 中,要消除 内部 的残余 的应力 。加工 的时间
的零件 的加工 的 时候要 注意 不能采用 一端 悬空 一端进行 夹 紧的方 式 对机 械零 件进行夹 紧 , 要 采用两端一起 夹紧的方式从零 件顶端进行夹 紧 ,主要采用前 端的驱动力进 行夹紧控制 , 这样 的情况下 就控制 了受 力 中简支梁横性 的大小 , 零件 的刚性就会 大大提高 , 减 小 了切削力 引 起 的变形 。当加 工小 的薄片类 工件 的时候 , 为 了减 少夹 紧变形在 电磁 吸盘 对其作用 时候产生 , 要在对零件 进行第一次加 工的时候在工作 台 之 间垫衬基层厚 布 , 这种 垫衬可 以减少变形 情况 的产生 , 在铸铁类工 件加 工的时候 , 要在创新 夹具上下足 功夫 。 在央具 设计的时候要 充分 考 虑对于工件 刚性的影 响 , 这种悬臂 部分增加 了浮 动的支撑 ,同时通
焊接壳体组成内孔加工变形分析及工艺改进

1 序言图1所示焊接壳体组成(以下简称壳体组成)是钩缓装置缓冲系统的重要部件之一。
其内孔车削加工完成后,受结构焊接应力时效释放和加工工艺性等因素影响,出现了较大的内孔变形,导致尺寸超差的惯性质量问题。
经过对各型号壳体组成的内孔变形原因的分析[1],采用不同的工艺改进措施进行试验验证,基本查明了内孔产生变形的主要原因。
通过改进壳体组成加工工艺过程,完善加工操作细节,最终解决了加工后变形造成尺寸超差的惯性质量问题。
图1 焊接壳体组成2 壳体组成结构公司已有30余种不同型号的壳体组成,每年生产数量达4000多件。
壳体组成主要由拉环(见图2)和壳体(见图3)两大零件经焊接组成。
壳体外圆分布许多焊接金属子件,整体结构属于薄壁深孔类工件[2]。
图2 拉环图3 壳体3 原加工工艺分析3.1 原加工工艺壳体组成原加工工艺为:焊接→探伤→精车外圆工艺面→粗车内孔→放置72h释放应力→精车内孔各尺寸和内螺纹→铣、镗等加工壳体外形孔和槽。
3.2 存在的问题图4为T997壳体组成结构尺寸。
对按原工艺加工的7个零件(用于装配1列高铁)进行尺寸测量,结果见表1。
从表1中的测量结果看,凡外圆尺寸偏差大者,对应的内孔尺寸偏差也大,特别是尺寸偏差超过0.1mm的3个内孔超差的零件,均存在这个规律。
壳体内孔尺寸设计公差带为0.1mm,加工完成后内孔尺寸偏差均在0.07~0.33mm,超差现象明显,且数量占比近半,可以定性为惯性质量问题。
图4 T997壳体组成结构尺寸表1 T997壳体组成尺寸测量结果(单位:mm)3.3 超差对产品的影响壳体内孔超差后,会造成装配间隙超标,引发内部零件定位失效,从而导致装配不合格。
经调查,因组装间隙不合格而返修的部件占比20%,造成大量工时浪费。
此外,壳体组成孔口端为M205×3-6H内螺纹,车削螺纹前内径变形大会造成与端螺母装配后,因间隙过大导致螺母有脱出的风险,是生产工艺中严格控制的关键项点。
风电产品主要零部件加工变形的原因及应对方法

风电产品主要零部件加工变形的原因及应对方法发布时间:2023-04-21T03:11:47.272Z 来源:《当代电力文化》2023年第1期作者:马赛[导读] 随着国家对风电的支持,我国风力发电市场快速发展,风力发电技术也不断改善,风电生产商对于产品的质量要求也越来越高。
马赛润阳能源技术有限公司 300000摘要:随着国家对风电的支持,我国风力发电市场快速发展,风力发电技术也不断改善,风电生产商对于产品的质量要求也越来越高。
风电的主要零部件转子、定子、主轴、底座、塔筒等都是铸造而成,这些零部件的共同特征是壁厚相对薄,体积大,加工过程容易变形。
在加工过程中,工件变形一直是难以解决的问题。
工件变形成为机械加工行业工艺设计人员重要的研究课题之一。
本文针对风电主要零部件转子、定子、主轴、底座、塔筒等在加工过程中变形、变形的原因以及应对措施进行分析并加以阐述。
关键词:零部件;工件;风电;变形引言在实际的工业生产加工中,机械零件和设备生产是非常重要的环节,能够对加工工艺的精度产生关键性影响。
由于加工工艺对零件加工精度的影响会受到很多因素的制约,所以不同的加工工艺会对不同的零件加工精度产生不同的影响。
为了提升加工精度,提升机械加工的整体水平,需要不断对机械加工工艺进行探索和创新。
加工精度是指工件加工后的实际几何参数(尺寸、形状和位置)与设计几何参数的符合程度。
为了提升机械零件的可操作性,必须加强对精度的要求,降低或避免各种因素对加工产生的影响。
因此,在实践中要想有效地解决机械加工工艺对零件加工精度的影响,就必须对各种影响因素进行深入分析和探讨。
1机械加工工艺技术概述机械加工工艺技术是指利用传统的机械加工方法进行机械制造,并在制造中结合机械产品尺寸、形状及性质等方面设计的图纸和相关生产技术,形成完整的机械产品的零部件加工。
机械加工工艺技术水平决定了机械加工产品的质量,所以需要机械产业技术人员做好全面的加工工作,减少加工误差的出现,降低机械产业的成本。
- 1、下载文档前请自行甄别文档内容的完整性,平台不提供额外的编辑、内容补充、找答案等附加服务。
- 2、"仅部分预览"的文档,不可在线预览部分如存在完整性等问题,可反馈申请退款(可完整预览的文档不适用该条件!)。
- 3、如文档侵犯您的权益,请联系客服反馈,我们会尽快为您处理(人工客服工作时间:9:00-18:30)。
剪切扭曲变形
木鎯头整形
3
用扁钢(4mm,6mm,8mm,10mm,等)焊接成的各种支承格栅
格栅平面拱起、扭曲 经过几道满焊,焊接收缩引起,尤其是有齿条的格栅 1:原坯料一般都存在内紧外松的状况、厚度越薄越严重 2:焊接热变形(有影响,但不是主要因素) 1:原材料质量(厚度、厚薄均匀度、应力等) 2:焊接热变形 1:冲烟囱方孔引起的变形 2:冲叠边引起的 变形 3:焊接热变形 焊接热变形
压力机或铁鎯头整形 可尝试设计专用的整形工具
4
分布器分槽折弯、焊接后
上边产生波浪
木鎯头整形
除提高坯料质量(或板材厚度)外,暂无太好的办法
5
VKG/VKGF装配焊接后
不规则变形
木鎯头整形
需要深入分析 1:增添一副折弯叠边模(同昆阳路)或由昆阳路折弯。 2:将工艺改为冲烟囱孔---矫平(用薄板矫平机)---折叠边 需要深入分析,但在序6工作做好后可能回有所改善 1:严格控制外协单位的剪板质量(对角线误差<1mm) 2:压弯 厂模具需要改进和增添,不得压弯3mm与6mm通用
6
SK烟囱式塔盘的底板数冲后
底板不平
木鎯头整形
7
SK烟囱式塔盘的底板焊接烟囱后
底板不平
木鎯头整形
8
气体分布器叶片
形状不到位
外协加工未达到图纸要求
铁鎯头整形
9
气体分布器焊接叶片后
整体弯曲、扭曲
不对称连续焊接引起的严重热变形
压力机或铁鎯头整形 用压力机或火焰整形(荷兰采用火焰整形) 1:将工艺改为冲孔---矫平(用薄板矫平机)---折叠边 2:由 工程部确定系列数据,增加几副非整数的冲模,以减小间隙3: 不垂直问题可用夹具适当改善,但不能完全消除 连接板一律采用3mm制作
10
管式分布器焊接后
1:底板不平 1:数冲后引起底板变形确 2:管子与底板不垂直 2:管子与孔的配合间隙不好(太大) 引起焊接热变形 连接板变形 焊接热变形
火焰整形
11
集液器焊接后
木鎯头整形
12
GIS支承格栅数冲后
板波浪形
数冲量大引起板波浪形
木鎯头整形
用序号2设备矫平 但可以考虑将现有的三辊卷板机换成适合于我公司产品的小型 四轴卷板机,这对制作需卷板的圆形零件是可以提高精度的。 上口增加连接板、支撑板尝试改焊接为铆接
部分常见工件变形及改进分析
序号
1 各种外协剪切的扁钢
工件类型
变形状态
弯曲、扭曲 外协未工艺要求整平
原因
目前整形方法
铁鎯头整形
改进方法
1:重新评定外协单位(协作厂必须有机械矫直机) 2:加强外协 检验 本公司增添一台薄板矫平机(GIS支承格栅等通用)
2
TS SUPPORT GRID齿条剪切后
弯曲、扭曲
13
EMS支承格栅的制造
零件成型
制作过程所必须
铁鎯头制作
14
闪蒸盒焊接后
上口面波浪形弯曲
U字形开口,焊接主要在下端,造成弯曲严重
木鎯头整形
15
预分布器焊接后
口面波浪形弯曲及整体 焊接热变形 不平整
木鎯头整形
尝试将填料角铁、围板的焊接改为碰焊或铆接(可能铆接更好)