组装二部作业不良分析改善报告
BGA不良分析、改善报告

8
7
6
5 Percentage of Voids
4
3
2
1
0 OSP
Pad Surface Finish
Tin
ENIG
Silver
HASL
OSP板储存、使用注意事项
一、供应及储存条件 1. 供应商在完成OSP制程后, 在受管控的温湿度环境下,
应在12H内完成真空包装. 在不受管控的温湿度环境下, 则必须在4H内完成真空包装. 2.来料外包装箱的识别卡料号后面要有”(OSP)”字样。OSP PCB 来料应采用真空包装. 3.仓库记录进料日期, 按先进先出原则发料. 4.PCB拆封前的储存环境为:温度16 ~ 40 ℃、相对湿度: 10 ~ 65%。 5.符合上述储存条件并未开封的真空包装储存时间最长为 3个月,如超超3个月则必须由IQC协助送回PCB板供应 商重工OSP制程。
OSP工艺焊盘氧化不良图片
ENIG板储存、使用注意事项
ENIG PCB抗氧化能力强,所以储存环境 要求不是很严格。一般储存要求,温度: 20~30℃,湿度:40~60%RH,拆包前 可以保存一年,拆包后可以保存3天。
ENIG工艺PCB出现焊接不良,主要是PCB 板供应商的制程出现问题。如:Ni层涂 覆不均匀,Au层表面裂纹导致焊接不良。
3、TBGA(TAPE BGA)带载BGA 其优点是: ①尽管在芯片连接中局部存在应力,当总体上同环氧
板的热匹配较好。 ②贴装是可以通过封装体边缘对准。 ③是最为经济的封装形式。 其缺点是: ①对湿气敏感。 ②对热敏感。 ③不同材料的多元回合对可靠性产生不利的影响。
2、CBGA(CERAMIC BGA)陶瓷封装BGA 其优点是: ①封装组件的可靠性高。 ②共面性好,焊点形成容易,但焊点不平行度交差。 ③对湿气不敏感。 ④封装密度高。 其缺点是: ①由于热膨胀系数不同,和环氧板的热匹配差,焊点
上锡不良分析改善报告
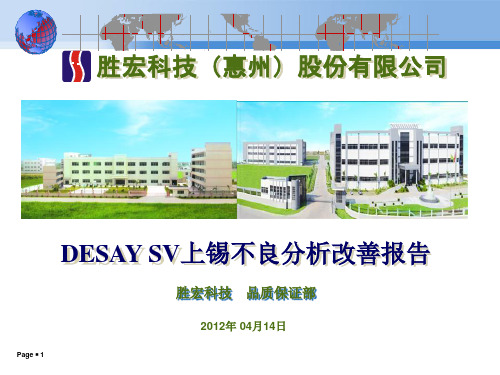
Page 5
改善对策(原因分析 二、原因分析&改善对策 原因分析) 原因分析 改善对策 原因分析)
1. 对其异常位置进行金厚和镍厚,金厚度测试(以1.5*1.5PAD测量)MI要求金厚 1-3u“镍厚100-300U”.结果如下:
序号 1 2 3 4 5 6 7 8 AU 2.05 2.13 2.13 2.34 2.05 2.14 1.31 1.26 NI 132.6 129.0 144.7 148.6 140.4 141.8 247.6 262.6
结果:其上锡不良拒焊主要在金表面,金层未融溶,同时金表面可目视可见水迹 印,在焊盘小孔边缘可见金面异色发红情形。
Page 10
改善对策(原因分析 二、原因分析&改善对策 原因分析) 原因分析 改善对策 原因分析)
5.现场跟进客户端SMT生产,SMT IR炉温设置高温断为275℃,设置温度与实际 炉温差异在1℃以内,实际温度曲线与标准温度曲线相符,过程无掉温的异常情 形,可排除为SMT温度不足导致的上锡不良情形;
固定专人、戴无硫手套检板
保持做桌面清洁干净
全流程戴手套作业
Page 15
四、改善对策
②每日当班早会宣导教育《基板十禁止》提升作业员品质意识,并由当站主管做监 督。 十禁止规范
4.作业方法 作业方法 ①维修刷镀后之板100%进行清洗干净后,增加由OQC抽检OK才可入包装,保障 清洗效果可监控。 清洗后OQC抽检
改善对策(原因分析 二、原因分析&改善对策 原因分析) 原因分析 改善对策 原因分析)
1. 对焊锡不良Pcb焊锡实验,将板子上裸露的焊盘进行全白橡皮擦拭后,结果如 下:
结果:焊锡正常,上锡饱满,排除镍金镀层不良。
Page 8
生产工艺改善报告。
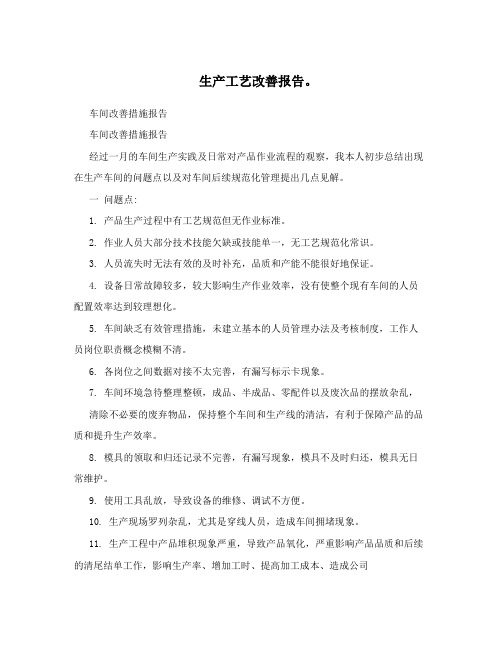
生产工艺改善报告。
车间改善措施报告车间改善措施报告经过一月的车间生产实践及日常对产品作业流程的观察,我本人初步总结出现在生产车间的问题点以及对车间后续规范化管理提出几点见解。
一问题点:1. 产品生产过程中有工艺规范但无作业标准。
2. 作业人员大部分技术技能欠缺或技能单一,无工艺规范化常识。
3. 人员流失时无法有效的及时补充,品质和产能不能很好地保证。
4. 设备日常故障较多,较大影响生产作业效率,没有使整个现有车间的人员配置效率达到较理想化。
5. 车间缺乏有效管理措施,未建立基本的人员管理办法及考核制度,工作人员岗位职责概念模糊不清。
6. 各岗位之间数据对接不太完善,有漏写标示卡现象。
7. 车间环境急待整理整顿,成品、半成品、零配件以及废次品的摆放杂乱,清除不必要的废弃物品,保持整个车间和生产线的清洁,有利于保障产品的品质和提升生产效率。
8. 模具的领取和归还记录不完善,有漏写现象,模具不及时归还,模具无日常维护。
9. 使用工具乱放,导致设备的维修、调试不方便。
10. 生产现场罗列杂乱,尤其是穿线人员,造成车间拥堵现象。
11. 生产工程中产品堆积现象严重,导致产品氧化,严重影响产品品质和后续的清尾结单工作,影响生产率、增加工时、提高加工成本、造成公司经济损失。
二改善计划及措施:1. 制定公司产品生产规范工艺流程,设置关键岗位工艺管控办法。
有利于对产品品质进行管控,以减少产品品质不良现象,并可初步设定生产合格率目标,减少无谓的返工和人力浪费,从而提升产品品质及生产效率。
2. 人员岗位职责的明确化,建立责任机制和追踪机制,有利于岗位人员的责任心的提升,并实施奖罚制度,不能做多做少一个样,做好做坏一个样,做与不做一个样,提升员工的积极性和责任感。
3. 要求员工做到每一道工序的自检和互检,以保证没有漏装、错装及破损和不合格品进入下一道工序。
4. 在早会上,管理人员可总结前日生产时发现的品质、车间及生产过程等发生问题,避免后续生产中再次发生,有利于对员工进行品质和责任教育。
SMT异常分析和改善报告
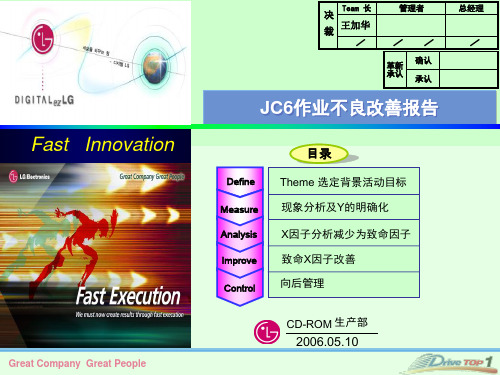
2006.05.10
Great Company Great People
Background Output
D
M
A
I
C
通过4月份工程不良数据分析发现作业不良占比率高,特选定作业不良为活动主题.
4月不良细部分析( PPM )
作业不良改善
TDR改善中
生产规模的迅速扩大,品质控制的
力度相对不足.
1236
修定 叠板 未检SET堆机现象严重
采用JIG放板
未检SET固定车放置 邀请生技,PM进行维修
PCB作业 不良
元件脱落
过桥掉机
修理叠板现象严重
修理不良追加JIG放置 作业者教育数量减少
投入位叠板
线路断
切板JIG不良 作业者修坏
设备重新更换改善 作业者教育数量减少
XS7 XS8
Two-proportions P-Value = 0.038 <0.05
改善前
1,236 1,246 1,123
改善后
作业不良率 改善目标
1,400 1,200 1,000 800 600 400 200 0
1,146
1,023
986 798
1,240
320
4月实绩 5月1日 5月2日 5月3日 5月4日 5月5日 5月6日 5月7日 5月8日
246
5月9日
235
155
13270 1930 2271 4月实际 部品
2435
1498
作业不良给品质,市场不良埋下了
很大的隐患.急需改善.
作业
MD
拆装
其他
不良细部分析( PPM )
Pareto Chart of 作业不良 _1
10-72GH60035B背面文字漏印不良分析改善报告--网印

確認人:王榮榮
保存期限:四年
完成日期:2014.06.29
M343-034-05-B
八、标ቤተ መጻሕፍቲ ባይዱ化
执行(文件/系统等) 是否修改文件:■是(□FMEA□QC Plan■SOP)文件编号:M423-033 □否( 原因 ) 1、修訂《網印內部規定作業標準書》,將P.10對策加入SOP, 編號:M423-033。
責任單位:網印
保存期限:四年
負責人:王榮榮
預計完成時間:2014.07.07
M343-034-05-B
謝謝您的聆聽
Thank you
保存期限:四年 M343-034-05-B
四、原因分析
2.作業流程分析: RTR網印---C面文字印刷 RTR網印---S面白色油墨塊印刷
此道文字漏印 網印---S面周期文字印刷
Comment:通過作業流程分析造成不良關鍵站別為:網印--S面文字印刷 .
保存期限:四年 M343-034-05-B
四、原因分析
3.文字漏印的原因查檢:
項 目 類別 內容 確認結果 是否 主因 備注
人 機
違反SOP 機台異常,文字未印下 來
現場巡線及查核,未發現異常 查核生產1063/1064的印刷的機台點檢表(10#印刷 機),未發現異常 經查核1063/1064進料檢驗報表,進料少1PNL,但
X
/
X
文 字
印刷報表、出貨報表上卻記錄100PNL。經確認前 料 進料少板,導致印刷漏 站補板後未印刷,直接補至量產板內(經與當事人
72GH60035B背面文字漏印 不良分析改善報告
Reporter:王榮榮 Approved by:陳禁 Date:2014.06.27
关于缺焊、泄漏不良改善报告 2

健康、舒适环境的引领者
计划 实施
推进计划 改进措施
12月 1月 2月
担当人
甄磊
卫春林
泄 漏 不 良 改 善 计 划
甄磊
胡品贵
张毅 杨坤
六、现场改善
水检区域 烘干区域
健康、舒适环境的引领者
待包装区域
焊接焊台定置
毛细管包装区
成品摆放区
六、现场改善
增加作业流程作业指导书 不良事例展示柜
不良样件展示柜
五、后续计划
制定改善与控制计划
类 别 问题 点 规范焊料、焊膏、喷刷剂使用 料 对供方来料进行委外成分检验,保证部件加工性能符合要求 协助供方品质改善,确保来料品质 法 定期焊工交流焊接手法 统一焊接火焰标准,使火焰温度、形状符合要求 机 焊接焊枪嘴设定专人管理,水检参数、保压时间管理 控制日常焊接件清洁度质量 环 营造精益求精的品质环境,完善激励制度 制造部每月至少一次品质大会宣贯 人 对焊接员工实行上岗资格培训考评 定期组织员工培训,提高人员技能
结论:经调查水检工产值本发现个别水检工产值异常,存在漏检
包装外观检流程再现分析
1、外观检对产品进行检 验(手拿多个存在盲点)
2、对产品中心距的 尺寸进行整形
3、贴追溯标签
4、将合格的产品进 行装箱
结论:外观检在筛选产品时手拿多件产品,导致检测点存在盲点,未有效检出不良品
二、流出原因分析
入库出厂检验流程再现分析:
3、预热后对配合焊 点进行增加焊料
4、取料后未对产品 各焊点进行检验
结论:焊接预热时间不够,焊料未流动到位产生断焊,套管取料人员对产品的焊点未进行 检验
3
二、流出原因分析
水检流程再现分析
健康、舒适环境的引领者
焊接不良专案改善报告

5、建立焊接员工的个人档案 及其监督完成 6、焊接员工岗位的等级重新 评定并颁发对应的上岗证
7、各机型的重点分析
8、对产线的烙铁头种类盘点 并且管控使用 9、定期焊接培训
负责人
钟苗 陈云喜
林伟杰
丁莉平
陈云喜 丁莉平 周元丽 陈云喜 丁莉平 高华
高华 林伟杰
周元丽 林伟杰 林伟杰
改善方案拟定
焊接不良专案改善报告
考核系统化
焊接岗位员工作业记录档案的建立
每个焊接岗位员工建立作业记录档案,分别登记该员工当天生产的机型、当 天生产量、不良数量、不良率,处理措施以及最后焊接员工的签名确认等信 息,以便以后进行追查。
每条产线配备一个专人焊接培训讲师 短期考核
员工必须要经过短期考核合格后方可授予点焊上岗证、排焊上岗证、屏焊上 岗证;
焊接不良专案改善报告
焊接不良专案改善报告
汇报人:林伟杰 专案小组成员:周元丽、丁莉平、陈云喜、
钟苗、高华、林伟杰
广州七喜数码科技有限公司
规划纲要
焊接不良专案改善报告
第一部分 调查分析篇 第二部分 改善方案拟定篇 第三部分 改善实施计划篇 第四部分 效果验证篇 第五部分 标准化篇
焊接不良专低
2.1.1员工作业 2.1.1.1没有系统考核体系考
技能不合格
核员工
2.1.1.2烙铁头使用错误(如 点焊使用大刀烙铁)
结果分析: 由上可知,1、缺乏系统的培训与考核;
2、焊接温度标准过低; 3、烙铁头缺乏有效的管控;
调查分析篇
焊接不良专案改善报告
结果汇总
制定系统的培训与考核 ; 重新验证目前的烙铁温度设定的标准是否过低; 重新验证目前的烙铁头的型号是否正确(点焊是否需要尖
10月制程不良分析总结报告
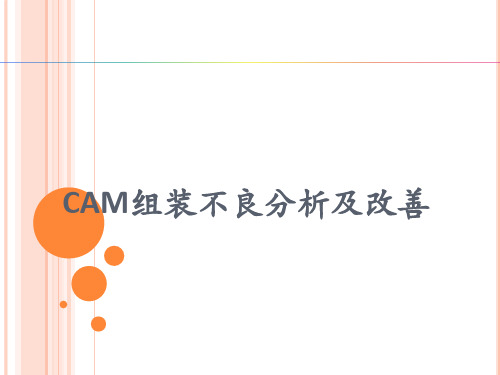
法
使用激光分板、超声波清洗 COB
公司高层
11月10日
棉签擦拭次数,废弃棉签误用 棉签蘸取酒精量多 振动后才能测试,终检前跌落工 序 百级工作台封装—测试洁净度 环
梁江(技术) 梁江(技术) 刘新昌(CAM) 马宏伟(品质)
10月30日 10月30 11月3日 11月1日 透明赃物 IPQC巡查 外校 避免硬板打磨 粉尘
CAM组装不良分析及改善
一.制程不良报表 二.TOP3不良原因分析 三.改善措施及验证计划
一.制程不良前三项
1.脏污 2.功能不良 3.模糊
从10月报表统计出前三大不良项目为:
二.TOP3不良原因分析
1.脏污原因分析:
人
漏检 自身作业水平 人员作业没有休息 棉签蘸取酒精太多
脏 污
测
没有调焦最清晰
说明:OQC退检数据下降,说明产线发现问题的能力提高,流出问题减少
使用的棉签是正牌,
棉签公司网站为 http://www.sa-nyo.co.jp/
脏污棉签防止误用装置 (丢进去后无法从顶部取出)
试验1 使用1280*1024显示屏检测前、后,OQC检出不良数据对比 使用前 10月27日 10月28日 10月29日 10月30日 11月3日 OQC检出不良批数 4 1 5 9 11 使用后 11月6日 11月7日 11月8日 11月9日 11月10日 OQC检出不良批数 6 2 6 3 2
11月5日
11月3日 11月3日
委外做镀层分析
川田 符合使用规定要求
功能不良改善措施
改善对象
措施要点
上料前目视检查FPC洁净度
责任人员
张光水(SMT)
实施时间
11月1日
SMT制程不良原因及改善报告
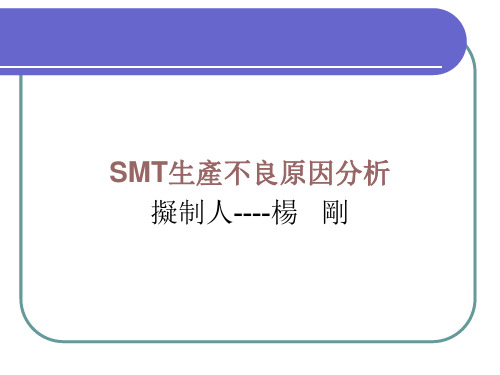
新旧锡膏混用
手放零件方法不当 载板系统不良 元件数据 轨道速度过快 设定不当 吸嘴 规格 吸嘴 弯曲 置件 不稳 坐标 偏移
方法
机器
人
人为跳掉 mark 作业
材料
零件有一边焊盘 吃锡不良 零件过大过重 未及时收板,PCB在回焊 炉中碰撞 人为手抹锡膏 备料时料带过紧 零件厚度不均 零件氧化 异形零件 手推撞板 人为手拨 缺锡 PAD间距与组 件长度不符 零件与PAD不符 手摆料 缺乏质量意识 PAD宽度与组件 宽度不符 零件脚歪 焊盘上有异物 零件脚弯 PAD 离轨道边小 于3mm. PAD氧化
(3) WHERE——何處?在哪裡做?從 哪裡入手? (4) WHEN——何時?什麼時間完成? 什麼時機最適宜? (5) WHO——誰?由誰來承擔?誰來 完成?誰負責?
(6) HOW ——怎麼做?如何提高效率? 如何實施?方法怎樣? (7) HOW MUCH——多少?做到什麼 程度?數量如何?品質水準如何?費用產 出如何?
环境
人
材料
露铜 无尘布毛絮堵 塞钢网开口 氧化 沾锡性
焊盘 有杂物 距板边不足3mm 沾油漆 不平整
缺乏质量意识 人为设定E-pass模式 手放散料遗漏/错误 收板不及时炉内撞板 人为设定跳过
PCB
设计 有异物 变形 黏 性 低
印刷后PCB板停留时间过长 手推撞板 手抹锡膏 通风不畅 生产模式被改动 (pass,idle) 未上锡 不正确操机 温度高锡膏变硬 未认真检查 真空不畅 程序缺件 擦钢网方法不正确 元件高度设定太薄 作业标准书不完善 流程错误 新旧锡膏混用 清线时关 闭料站 更改贴片顺序 紧急停止 锡膏印刷缺锡 电磁阀不良 钢网材质 传感器失灵 机器故障 轨道不洁 Z轴不平 机器振动 开口堵塞 MTS振动太大 轨道卡板 气压 Mark点设置 钢网设计不良 钢网未开口 运转速度 开口不正确 贴片 速度 过快 吸嘴 尺寸 不符 吸 嘴 弯 曲 坐 标 误 差 吸 嘴 磨 损 吸嘴 堵塞 跳掉次序数据 收板 零 件 氧 化 外形 尺寸 变形 厚度 不规 损 大小 抛件 差异 则 件 料带过紧 或过松 沾 锡 料带粘性 物质多 性 包裝不良
组件一部破片分析和改善报告(20160603)

5/30 828 1 0 0 1
措施
A班出 现4-1 破片集 中
更换 制定禁止排版 助焊剂喷涂尾部焊死,调整助焊剂长度;每日确认助焊剂喷 增加串 5#机 拍串要求 涂;调整层压参数 长1mm 硅胶板 A班再次出现 4-1破片集中 人员曾群英 发现前 调整5#层压机 前报告 A班再次出现 EL小 压力3KP,出 中硅胶 4-1破片集中 隐裂测 现气泡异常 板影响 人员鲁安波 不出
5/21 965 6 3 3 0
5/22 1015 5 4 0 1
集中人 员鲁安 波调岗
5/23 910 3 0 0 3
5/24 946 2 1 0 1
5/25 913 3 1 2 0
5/26 1031 4 1 2 1
5/27 964 6 1 2 3
5/28 885 1 0 0 1
5/29 956 2 1 0 1
3.每班早中晚点检前EL探针高度及 灵活度
2
控制助焊剂涂敷的电磁阀之间 存在差异,喷涂助焊剂长度难 收尾点焊死 控制,无法做到完全同步,保 养过程造成轨迹歪斜
1.每班早中晚点检助焊剂喷涂轨迹, 清理电池阀,调整助焊剂喷涂时间; 2016--52.日常保养后,试喷涂确认合格后 21 方可复机
吴小龙 /黄宏友
二、原因分析
新排版穿引线破片分析
版型
4-1破片数量
产能
破片比例
组一4月60P新排版
19
7739
0.25%
组一5月72P新排版
22
14570
0.15%
组二5月72P新排版
7
36434
0.02%
结果:1、组一5月72P新排版22块破片,比例为0.15%,通过提前预防培训较5 月新排版4-1破 片比例减少0.10%,但对比组二4-1破片比例仍较多; 2、组一4-1破片集中出现在A班(夜班),占比77.27%。
工厂生产改善报告范文
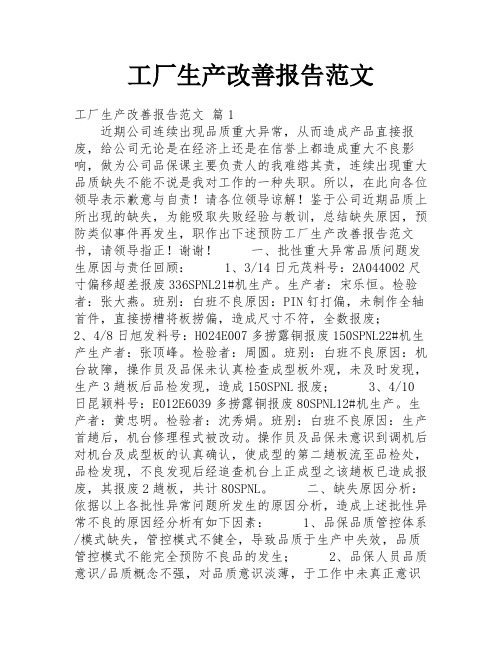
工厂生产改善报告范文工厂生产改善报告范文篇1近期公司连续出现品质重大异常,从而造成产品直接报废,给公司无论是在经济上还是在信誉上都造成重大不良影响,做为公司品保课主要负责人的我难绺其责,连续出现重大品质缺失不能不说是我对工作的一种失职。
所以,在此向各位领导表示歉意与自责!请各位领导谅解!鉴于公司近期品质上所出现的缺失,为能吸取失败经验与教训,总结缺失原因,预防类似事件再发生,职作出下述预防工厂生产改善报告范文书,请领导指正!谢谢!一、批性重大异常品质问题发生原因与责任回顾:1、3/14日元茂料号:2A044002尺寸偏移超差报废336SPNL21#机生产。
生产者:宋乐恒。
检验者:张大燕。
班别:白班不良原因:PIN钉打偏,未制作全轴首件,直接捞槽将板捞偏,造成尺寸不符,全数报废;2、4/8日旭发料号:H024E007多捞露铜报废150SPNL22#机生产生产者:张顶峰。
检验者:周圆。
班别:白班不良原因:机台故障,操作员及品保未认真检查成型板外观,未及时发现,生产3趟板后品检发现,造成150SPNL报废;3、4/10日昆颖料号:E012E6039多捞露铜报废80SPNL12#机生产。
生产者:黄忠明。
检验者:沈秀娟。
班别:白班不良原因:生产首趟后,机台修理程式被改动。
操作员及品保未意识到调机后对机台及成型板的认真确认,使成型的第二趟板流至品检处,品检发现,不良发现后经追查机台上正成型之该趟板已造成报废,其报废2趟板,共计80SPNL。
二、缺失原因分析:依据以上各批性异常问题所发生的原因分析,造成上述批性异常不良的原因经分析有如下因素:1、品保品质管控体系/模式缺失,管控模式不健全,导致品质于生产中失效,品质管控模式不能完全预防不良品的发生;2、品保人员品质意识/品质概念不强,对品质意识淡薄,于工作中未真正意识到品质之危机性与突发性,未认真履行品质事前控制之义务性,未事前预防品质,造成生产品质缺失;3、产线操作员/品保员未尽工作义务,工作不认真,不按工作程序步骤作业,导致工作中疏失/漏洞出现;4、干部对组员管理松散,未认真追踪/确认/检查/验收/督导组员工作之成效,造成工作纪律散漫,思想意识/使命感不强,团队战斗力/管理成效不佳导致品质状况下降或缺失发生;三、预防改善方案:经对近期时间所出现的异常缺失原因所作的反思,为预防类似事件再次发生,制定如下预防改善方案。
CNC不良分析及改善报告

CNC不良分析及改善陈说之勘阻及广创作CNC不良分析及改善1.来料抽检是否存在崩角严重划伤或尺寸偏小改善办法:抽检来料根绝不良产物上机既浪费人力物力财力,不良产物退上工序.2. 正确的把持手势和把持流程以免在后续的生产中给本工序或后工序造成良率效率的下滑.改善办法;严格依照作业指导书进行把持或在适当的时间对员工加强培训.3. 崩.改善办法;1法式存在优化2是否是刀具造成,更换刀具3添加适量的切削液4转速在程控且在%1004.划伤改善办法; 1改善现有夹具通气糟的宽度深度限定为1MM(现已贴呵护膜)2检查来料3正确的放料手势防止与夹具相互摩擦(具体见作业指导书)4进行隔行插架防止取放料相互碰撞5呵护膜一个班更换一次6切削液至少一个月完全更换一次5.裂改善办法;1来料为异形超越CNC规定的切削量1改善现有夹具通气糟的宽度深度限定为1MM 2刀具磨损严重,更换刀具6.阴阳边改善办法; 1调机应秉持确认确认再确认的原则在进行生产2生产中进行自检管理者隔2小时巡检一次3每10分钟清理夹具概况4刀具磨损严重,更换刀具7尺寸不良改善办法; 1调完尺寸的机台应进行投影确认再进行生产尺寸为CNC的雷区,因为在后工序没有在检测尺寸的工序,尺寸不良的产物一旦流入客户,后果不胜设想.8.未车到改善办法; 1正确的把持手势2靠角磨损3气压缺乏招致移位目前CNC存在的问题很多,从产物上机到产物下机都没有完整的作业流程.上机前应该做什么(例如:检查刀具是否存在磨损,水泵正常开启,呵护膜是否需要更换).生产中应该注意哪些,防止问题的发生(生产中应当进行自检).下机生产完每架产物进行抽检,防止不良品流入下工序.针对CNC上次生产年夜量不良做出以上分析及改善办法,在以后的生产中将会以基本方针不良对策3原则 1不接收不良品2不制造不良品 3不流出不良品.在后期将会在各方面进行改善及优化:比如加强员工的品质意识.励志提高CNC良率,保证CNC一定能到达预期的目标.建议后期增加产物标示卡,如有问题可以快速的找出对应的机台进行处置.增加产物反馈单使问题呈现严肃化.马甜甜2011-8-27。
焊接不良改进报告
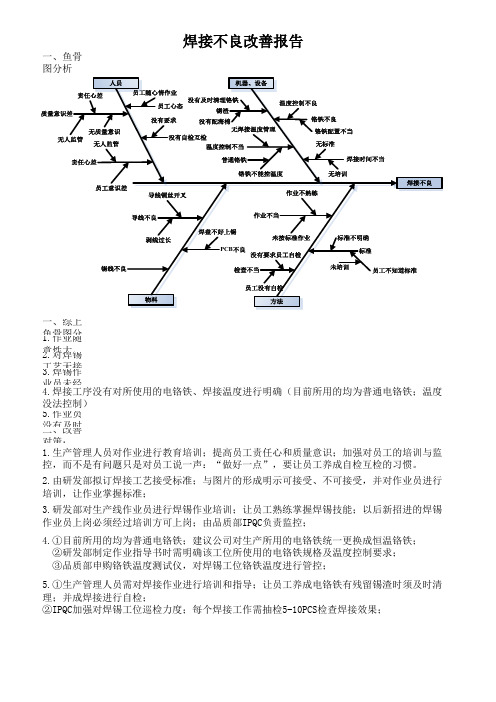
控,而不是有问题只是对员工说一声:“做好一点”,要让员工养成自检互检的习惯。
2.由研发部拟订焊接工艺接受标准;与图片的形成明示可接受、不可接受,并对作业员进行培训,让作业掌握标准;
3.研发部对生产线作业员进行焊锡作业培训;让员工熟练掌握焊锡技能;以后新招进的焊锡作业员上岗必须经过培训方可上岗;由品质部IPQC负责监控;
4.①目前所用的均为普通电铬铁;建议公司对生产所用的电铬铁统一更换成恒温铬铁;
②研发部制定作业指导书时需明确该工位所使用的电铬铁规格及温度控制要求;
③品质部申购铬铁温度测试仪,对焊锡工位铬铁温度进行管控;
5.①生产管理人员需对焊接作业进行培训和指导;让员工养成电铬铁有残留锡渣时须及时清理;并成焊接进行自检;
②IPQC加强对焊锡工位巡检力度;每个焊接工作需抽检5-10PCS检查焊接效果;
拟定:审核:。
【改善报告】宇龙产品包装线UPPH提升报告

点胶机、电脑异常较多 作业台面灯管灯光度不够
订单切换,切线损失较大 物料供应不及时
物料
人员流动性较大,新近作 业员动作不熟练
人为原因,返工不断
人
无
单 需 求 ?
法 满 足 客 户
订
三、生产效率提升改善对策
问题点
1.线平衡率低 2.动作、等待浪费
改善
改善对策
改善瓶颈工站,通过ECRS四大原则对 产线进行优化,使产能提升
组装工位工时图
16.00
标准工时 11.53S
14.00
12.00
10.00
8.00
6.ห้องสมุดไป่ตู้0
4.00
2.00
0.00 1 2 3 4 5 6 7 8 9 10 11 12 13 14 15 16 17 18 19 20 21 22 23 24
系列2 标准工时
二、原因分析---鱼骨图分析法
法
設備
线平衡率低 线平衡率低 作业动作、等待浪费
三、生产效率提升改善对策
目标UPH=420
线平衡率88%
四、改善状况追踪
连续2天平均产出 UPH达420
UPH提升验证线体包装L6在6/24~6/25每天平均产出UPH达到目标420; 最高UPH可达到520。
五、绩效评估
Item 总人力 UPH UPPH
改善前 31 220 8.05
改善后 40 420 10.5
2.因5860E面壳表面为高光面,作业时极易划伤,导致产线作业速 度下降,且外观不良较高
3. 由于客户订单要求较严,且出货时间较紧,产能无法满足 出货需求,需紧急对包装线进行产能提升。
一、现状分析
1、 当前5860E面壳预加工线配置人力28人/线,目标UPH为400, 可实际UPH仅达250(员工熟练度/壳体划伤不良较多影响),经过工 时量测以及UPH评估、线平衡率计算对现状进行详细的分析和评估。
焊接不良改进报告【最新版】

焊接不良改进报告
焊接不良改善报告
一、鱼骨图分析
一、综上鱼骨图分析,产线焊接不良主要原因如下:
1.作业随意性大,无责任心和质量意识;作业不作自检。
2.对焊锡工艺无接受标准:
3.焊锡作业员未经培训就直接上岗,是否可以胜任本岗位工作也监督与考核;
4.焊接工序没有对所使用的电铬铁、焊接温度进行明确(目前所用的均为普通电铬铁;温度没法控制)
5.作业员没有及时清理铬铁上锡渣;焊接造成连锡。
二、改善对策:
1.生产管理人员对作业进行教育培训;提高员工责任心和质量意识;加强对员工的培训与监控,而不是有问题只是对员工说一声:“做好一点”,要让员工养成自检互检的习惯。
2.由研发部拟订焊接工艺接受标准;与图片的形成明示可接受、不可接受,并对作业员进行培训,让作业掌握标准;
3.研发部对生产线作业员进行焊锡作业培训;让员工熟练掌握焊
锡技能;以后新招进的焊锡作业员上岗必须经过培训方可上岗;由品质部IPQC负责监控;
4.①目前所用的均为普通电铬铁;建议公司对生产所用的电铬铁统一更换成恒温铬铁;
②研发部制定作业指导书时需明确该工位所使用的电铬铁规格及温度控制要求;
③品质部申购铬铁温度测试仪,对焊锡工位铬铁温度进行管控;
5.①生产管理人员需对焊接作业进行培训和指导;让员工养成电铬铁有残留锡渣时须及时清理;并成焊接进行自检;
②IPQC加强对焊锡工位巡检力度;每个焊接工作需抽检5-10PCS 检查焊接效果;
拟定:审核:。
IQC批次不合格问题改善报告模板0926

➢问题定位:供应商工序作业的问题
➢处理措施:要求供应商回复8D改善报告,后续对供应商进行稽查确认。
➢影响度:供应商工序作业的问题,严重影响 了公司产品和质量。批量问题影响IQC工作效率。
➢供应商改善措施:
IQC批次问题---耀鑫21011675机柜外检问题
故障现象: 1前门防水密封胶条要求9MM,实际12~13,正常手法无法关门,要手脚并用使很大
➢影响度:供应商工序作业的问题,严重影响 了公司产品和质量。批量问题影响IQC工作效率。
➢供应商改善措施:IQC批次问源自---耀鑫29010316机柜外检问题
故障现象:
1.机柜前门门缝漏水,后门百叶窗漏水 . 分析思路:
以上不良主要是焊接及装配打防水胶操作问题,焊接时有小孔没有焊到,加上后工序打防水 胶不均匀导致试水时有水渗入。
结论:供应商问题 ➢不良数量:批量 ➢问题定位:焊接打胶操作问题 ➢处理措施:现场不良物料已进行返修,要求供应商回复8D改善报告 ➢影响度:防水问题失效,严重影响 了公司质量。批量问题影响IQC工作效率。 ➢供应商改善措施:
➢处理措施:要求供应商回复8D改善报告,后续对供应商进行稽查确认。
➢影响度:供应商工序作业的问题,严重影响 了公司产品和质量。批量问题影响IQC工作效率。
➢供应商改善措施:
IQC批次问题---耀鑫21011675机柜外检问题
故障现象: 1防水测试抽20台漏水2台,前门风扇盖板漏喷涂保护
分析思路: 以上不良是试水操作不规范及防水胶作业不规范的问题,试水作业员没有按照试水流程进行作业, 装配打防水胶没有按SOP规范作业,夜班生产不按首检制度报检作业导致批量漏保护。 结论:供应商问题
力才能关上。 分析思路: 以上不良是泡胶来料检验作业不规范的问题,IQC没有按照进料检验流程进行作业,导致泡胶尺寸 不符合图纸要求没有发现。 结论:供应商问题
组装精益改善报告

组装精益生产改善阶段性总结七月,又是一个骄阳似火的七月!七月的大地,有一种希望在罗美播种!七月的天空,有一种思潮在组装涌动!七月一号,******会议室,由集团**牵头在罗美正式宣告“组装精益改善小组”的成立,经过两个多小时的讨论,会议上提出了实现组装效率提升20%的总方针目标。
俗语云”山雨欲来风满楼“,让我们先回顾一下组装在精益改善之前的样子吧;1.现场物料堆积,半成品占据了车间的“半壁江山“2.计划安排混乱,车间计划和项目计划始终难以吻合3.产品合格率低下,受上几道工序影响严重“穷则变,变则通,通则久”——《易经.系辞下》针对组装目前存在的问题,精益生产执行小组先从中选取一个最具代表性的生产的项目(798项目)进行研究。
首先,我们运用“鱼骨图”主要从人、机、料、法、环五个方面对798项目进行问题分析:1.人通过建立员工技能水平表,我们可以直观反映员工技能水平,发现了部分员工技能经验不足的问题2.机通过精益生产小组成员一个周的观察,发现员工在操作过程中有些工装模具并不适用以及需要新曾一些工装模具3 . 料通过统计每日的完成计划情况,发现组装目前的缺料问题。
通过观察组装798员工的操作以及车间物料布局我们发现物料拿取的不方便。
4.法运用动作打分表,精益生产小组成员分别对员工的操作动作进行打分,然后根据动作打分表的分值找出员工操作中的动作浪费。
对于鱼骨图反映出来的问题,我们进行了如下解决:1.人对于部分员工技能不足,精益生产小组组织工艺工程师对新员工进行了培训并向全体员工讲解了精益生产的知识。
2.机对于员工在操作中反映的工装模具存在的缺陷,我们组织技术部工程师进行了改变。
对于员工频繁需要翻动产品,我们又制作了翻转工装供员工使用3.料对于组装欠料问题,我们组织了生产部、采购部、物流部进行开会讨论,最后决定建立安全库存,若以后再出现缺料则有采购部负责提请采购。
4.法在本次改善中,生产方式方法的改变是我们组装精益改善的最大变化。
- 1、下载文档前请自行甄别文档内容的完整性,平台不提供额外的编辑、内容补充、找答案等附加服务。
- 2、"仅部分预览"的文档,不可在线预览部分如存在完整性等问题,可反馈申请退款(可完整预览的文档不适用该条件!)。
- 3、如文档侵犯您的权益,请联系客服反馈,我们会尽快为您处理(人工客服工作时间:9:00-18:30)。
一、现状调查---数据分析
二、原因分析
作业不良的主要原因 1. 超声波治具与壳料不匹配,导致超声波焊接头与后壳接触面受力 不均匀而压破镜片; 2. 超声波治具与壳料不匹配,导致焊接时焊接头与后壳接触面不平整 而压伤后壳; 3.员工品质意识差 ,新员工岗前培训不够; 4.员工工艺执行力差。
2
生产线重点岗位现场操 作培训计划制定及实施
对重点岗位的员 工进行定期的现 场操作培训
持续
3
护
持续
4
将不良品以图片形式揭 示
定期展示不良品 图片
持续
五、效果确认
三、制定对策
作业不良对策: 1.培训计划的制定及培训方式的改变(原来的普通培训更改为视频培训); 2.对重点岗位实施现场操作培训; 4.超声波供应商进行协助对超声治具进行改善; 5. 将不良品以图片的形式展示在每个岗位上。
四、对策实施 组装二部制程不良改善行动计划
NO 实施项目 目标&要求 普通培训更改成 视频培训 完成时间 责任人 备注 结果 1 培训方式变更 2013.9.4