(完整版)先进制造技术(英文版第三版)唐一平,第五章翻译.doc
(完整版)先进制造技术(第三版)知识点总结
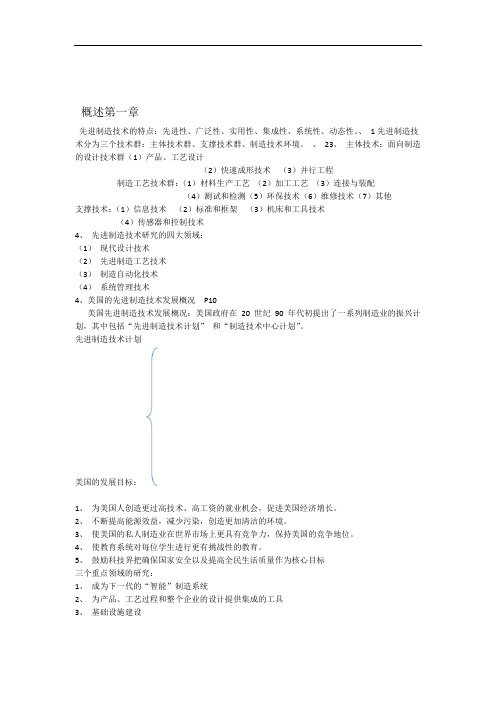
概述第一章先进制造技术的特点:先进性、广泛性、实用性、集成性、系统性、动态性。
、1先进制造技术分为三个技术群:主体技术群、支撑技术群、制造技术环境。
、23、主体技术:面向制造的设计技术群(1)产品、工艺设计(2)快速成形技术(3)并行工程制造工艺技术群:(1)材料生产工艺(2)加工工艺(3)连接与装配(4)测试和检测(5)环保技术(6)维修技术(7)其他支撑技术:(1)信息技术(2)标准和框架(3)机床和工具技术(4)传感器和控制技术4、先进制造技术研究的四大领域:(1)现代设计技术(2)先进制造工艺技术(3)制造自动化技术(4)系统管理技术4、美国的先进制造技术发展概况P10美国先进制造技术发展概况:美国政府在20 世纪90 年代初提出了一系列制造业的振兴计划,其中包括“先进制造技术计划”和“制造技术中心计划”。
先进制造技术计划美国的发展目标:1、为美国人创造更过高技术、高工资的就业机会,促进美国经济增长。
2、不断提高能源效益,减少污染,创造更加清洁的环境。
3、使美国的私人制造业在世界市场上更具有竞争力,保持美国的竞争地位。
4、使教育系统对每位学生进行更有挑战性的教育。
5、鼓励科技界把确保国家安全以及提高全民生活质量作为核心目标三个重点领域的研究:1、成为下一代的“智能”制造系统2、为产品、工艺过程和整个企业的设计提供集成的工具3、基础设施建设第二章柔性制造系统(FMS)技术1、柔性制造系统(FMS)的特点:(1)主要特点:柔性和自动化(2)设备利用率高,占地面积小(3)减少直接劳动工人数(4)产品质量高而稳定(5)减少在制品库存量(6)投资高、风险大,开发周期长,管理水平要求高2、FMS与传统的单一品种自动生产线(即刚性自动生产线,其物流设备和加工工艺是相对固定的,只能加工一个零件,或加工几个相互类似的零件)缺点:改变加工产品的品种,刚性自动线做较大改动,投资和时间方面耗资大,难以男足市场要求。
先进制造技术(英文)

先进制造技术(英文)课程编码:202299 课程英文译名:Advanced Manufacturing Technology 课程类别:学科基础选修课开课对象:机械工程机自动化专业开课学期:5学分:2学分;总学时:32学时;理论课学时:32学时;实践学时:学时;上机学时: 0 学时先修课程:大学英语教材:先进制造技术(英文版),唐一平,机械工业出版社,2004年2月第1版第2次印刷,(ISBN 7-111-10803-5)参考书:【1】21st Century Manufacturing, Paul Kenneth Wright, 清华大学出版社,2002【2】先进制造技术专业英语阅读,屈利刚,化学工业出版社,2006一、课程的性质、目的和任务先进制造技术(AMT)是一门动态的、以传统的机械制造技术为基础,融合包括计算机、信息、自动控制、材料、能源、环保、管理科学等学科成果的,新技术与现代系统管理交叉的新兴课程,并且随着新科技、新理念的不断出现而不断更新、充实和发展。
先进制造技术是机械类本科学生掌握和了解现代制造技术发展情况和技术前沿的基础选修课程,既是基础英语教学的后续英语教学课程,也是一门双语教学的学科基础课程。
通过本课程学习,使学生尽快熟悉机械专业的技术词汇,广泛阅读专业文献,全面了解先进制造技术的最新发展动态,更新制造技术理念。
本课程的任务是:1.了解目前制造业中先进的制造技术和制造工艺;2.了解国内外先进制造技术的发展趋势;3.了解先进制造技术的应用情况和场合;4.初步掌握使用英语进行专业交流能力。
二、课程的基本要求在熟悉机械专业的技术词汇的基础上,培养学生具有查寻最新的技术资料和广泛阅读本专业领域最新文献及使用英语进行专业交流等能力。
三、教学内容及学时分配四、习题及课外教学要求1)结合本科生导师的研究内容,利用因特网查阅相关的文献资料2)选择一个主题,参加课堂上模拟的“21世纪制造业前沿国际论坛”,使用英语进行专业交流,并作为课程考核一部分。
6.5 Environmentally Conscious Design and Manufacturing
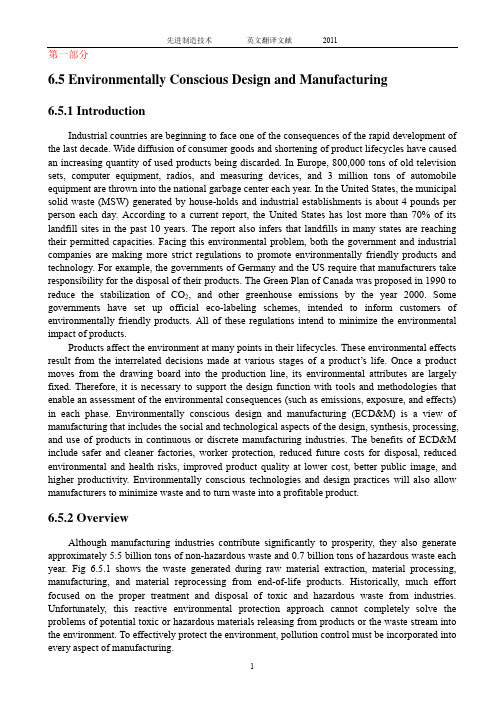
第一部分6.5 Environmentally Conscious Design and Manufacturing6.5.1 IntroductionIndustrial countries are beginning to face one of the consequences of the rapid development of the last decade. Wide diffusion of consumer goods and shortening of product lifecycles have caused an increasing quantity of used products being discarded. In Europe, 800,000 tons of old television sets, computer equipment, radios, and measuring devices, and 3 million tons of automobile equipment are thrown into the national garbage center each year. In the United States, the municipal solid waste (MSW) generated by house-holds and industrial establishments is about 4 pounds per person each day. According to a current report, the United States has lost more than 70% of its landfill sites in the past 10 years. The report also infers that landfills in many states are reaching their permitted capacities. Facing this environmental problem, both the government and industrial companies are making more strict regulations to promote environmentally friendly products and technology. For example, the governments of Germany and the US require that manufacturers take responsibility for the disposal of their products. The Green Plan of Canada was proposed in 1990 to reduce the stabilization of CO2, and other greenhouse emissions by the year 2000. Some governments have set up official eco-labeling schemes, intended to inform customers of environmentally friendly products. All of these regulations intend to minimize the environmental impact of products.Products affect the environment at many points in their lifecycles. These environmental effects result from the interrelated decisions made at various stages of a product’s life. Once a product moves from the drawing board into the production line, its environmental attributes are largely fixed. Therefore, it is necessary to support the design function with tools and methodologies that enable an assessment of the environmental consequences (such as emissions, exposure, and effects) in each phase. Environmentally conscious design and manufacturing (ECD&M) is a view of manufacturing that includes the social and technological aspects of the design, synthesis, processing, and use of products in continuous or discrete manufacturing industries. The benefits of ECD&M include safer and cleaner factories, worker protection, reduced future costs for disposal, reduced environmental and health risks, improved product quality at lower cost, better public image, and higher productivity. Environmentally conscious technologies and design practices will also allow manufacturers to minimize waste and to turn waste into a profitable product.6.5.2 OverviewAlthough manufacturing industries contribute significantly to prosperity, they also generate approximately 5.5 billion tons of non-hazardous waste and 0.7 billion tons of hazardous waste each year. Fig 6.5.1 shows the waste generated during raw material extraction, material processing, manufacturing, and material reprocessing from end-of-life products. Historically, much effort focused on the proper treatment and disposal of toxic and hazardous waste from industries. Unfortunately, this reactive environmental protection approach cannot completely solve the problems of potential toxic or hazardous materials releasing from products or the waste stream into the environment. To effectively protect the environment, pollution control must be incorporated into every aspect of manufacturing.Fig 6.5.1 Mineral Waste Material Supply, Utilization, and Disposal System As opposed to the traditional “end-of-pipe” treatment for pollution control, ECD&M is a proactive approach to minimize the product’s environmental impact during its design and manufacturing, and thus to increase the product’s competitiveness in the environmentally conscious market place. There are two general approaches to ECD&M. In the first approach (zero-wasted lifecycle), it is assumed that the environmental impact of a product during its lifecycle can be reduced to zero. The cycle can be absolutely sustainable, and the product may be designed, manufactured, used, and disposed of without affecting the environment. The emphasis in this approach is to create a product cycle that is as sustainable as possible. Sustainable production means that products are designed, produced, distributed, used and disposed of with minimal (or none) environmental and occupational health damages, and with minimal use of resources (material and energy). The sustainability of a system can be considered as the ability of that system to be maintained or prolonged. The second approach (incremental waste control lifecycle) is based on the premise that there is a certain amount of negative impact from the current process cycle. This impact can be reduced or cleaned based on some improvement in technology that is named as incremental waste lifecycle control. This approach is to reduce the negative impact of hazardous materials through clean technology. A “cleaner technology” is a source reduction or recycling method applied to eliminate or significantly reduce hazardous waste generation.Research on ECD&M can be categorized into two areas, namely, environmentally conscious product design and environmentally conscious process design, also called environmentally conscious manufacturing (ECM). Whitmer II, Olson, and Sutherland developed a hierarchy comprised of environmentally conscious products (Fig 6.5.2). At the first level of the hierarchy, theoverall objectives for the system are considered when creating an environmentally conscious product. At the second level, the four groups represent a post-use process that can be employed to achieve the objectives. The third level consists of the five design factors that can facilitate the post-use processes and in turn accomplish the overall goal. This hierarchy shows the method of retiring products, whether the designers intend to have the product discarded in a landfill, or whether they plan to reuse or recycle part or all of the product.Fig 6.5.2 Hierarchy for Designing an Environmentally Conscious ProductThe principle of ECM is to adopt those processes that reduce the harmful environmental impacts of manufacturing, including minimization of hazardous waste and emissions, reduction of energy consumption, improvement of materials utilization efficiency, and enhancement of operational safety. Sandia National Laboratories’ Environmentally Conscious Manufacturing Programs Department describes ECM as “the deliberate attempt to reduce ecological impacts of industrial activity without sacrificing quality, cost, reliability, performance, or energy utilization efficiency.” The activities of ECM emphasize largely extracting the useful product from raw materials, the avoiding of waste generation at the Source, or using waste to create other products. In addition, ECM involves refining operating procedures, replacing existing processes and developing new, waste-free processes, finding innovative ways to redesign products, and increasing recycling.第二部分6.5.3 Recycling and Disassembly ModelingIn the ECD&M literature, many researchers emphasize the importance of recycling end-of-life (EOL) products and the role of product disassembly for effective recycling. Recycling is defined by Jovane et al. as “recovering materials or components of a used product to make them available for new products.” Another definition was given by Bancroft as “the use of product design to facilitate the recovery and reuse of materials in the product.” These definitions infer “closing the loop” of materials and components after usage by reusing them for raw materials or secondary materials at different stages of the product’s lifecycle.(1) RecyclingWolf and Ellen reported that the paper industry recycles as much as 50% of its output. However, in the plastics industry, only a small portion is recycled. Wolf and Ellen also reported that there were 58 billion pounds of plastic resin sold in the United States and less than 1% of this was recycled. Ishii, Eubanks and Marco proposed a design for a product retirement model for recycling EOL products. The authors used the concept of “clump,” which is a collection of components and/or subassemblies that share a common characteristic based on the designer’s intent. One intangible benefit arising form recycling is the “green” image. The other significant benefit of recycling EOL products would result form reusing whole parts or subassemblies. For example, electronic materials (such as gallium, germanium, silicon and indium) can be profitably recycled because of their high production cost. Many industrial processes have been proposed for extracting these valuable elements from electronic components.Recycling requires that materials and fastening methods in the clump are compatible with existing technologies. Henstack reviewed recycling practices for various metal-based items, which focuses on steel scrap in automobiles. The study has generated some general principles of design for recyclability, including simplifying mechanical disassembly, avoiding self-contaminating combinations of materials, standardizing materials used, and separating high copper content items from steel items.Two engineering problems associated with design for recyclability are dismantling techniques and recycling costs. Simon pointed out that dismantling required the knowledge of the destination or recycling possibility of the component parts disassembled. However, from the time a product is designed to the time it reaches the end of its life, techniques will have advanced in recycling and reengineering. This phenomenon reveals the difficulties of recycling EOL products. Simon suggested two guidelines for dealing with this problem: 1) remove the most valuable parts first and 2) maximize the “yield” of each dismantling operation.Wittenburg proposed the concept of a recycling path of components and materials, as envisaged by BMW. It entails a “cascade model” of decreasing values, in which attention is first focused on the disassembled parts suitable for reuse that have the highest value. The Decree on Electronic Waste and the Decree on Used Cars forced manufacturers to reclaim waste, to reuse the recyclable fraction, and to dispose of the residue. In the automobile industry, BMW is the leader in design for recycling and disassembly. The Z1 model is a two-seat automobile with an all-plastic skin that can be removed from the metal chassis in 20 minutes. The doors bumpers, and front, rear, and side panels are made of recyclable thermoplastics produced by GE. The BMW 3251 also uses recyclable plastic parts and target-markets to environmental conscious customers. Through these efforts, BMW has identified some guidelines that make disassembly and recycling easier.Material recognition is another interesting approach of recycling. It requires a technology capable of identifying materials including the proportion and type of filler materials used. Ideally, the technology should be cheap, hand-held for use on different components, and significantly durable for use in a workshop-type environment. A number of researchers have been working in this area with varying success. Shergold indicated that the Fourier Transform Infra-Red (FTlR)-based equipment that Rover and Bird developed is good at identifying plastics and some filler materials.It is not possible or economical to recycle a product completely; there-fore, the aim of recycling is to maximize the recycle resources and to minimize the mass and pollution potential of the remaining products. Zussman, Kriwet, and Seliger proposed three objectives that should be considered du-ring the design evaluation: 1) maximization of profit (benefits-costs) over a product's lifespan, 2) maximization of the number of parts reused, and 3) minimization of the amount (weight) of landfill waste.(2) DisassemblyIt has been recognized that disassembly of used products is necessary to make recycling economically viable in the current state of the art of reprocessing technology. Disassembly is defined by Brennan, Gupta, and Taleb as “the process of systematic removal of desirable constitute parts from an assembly while ensuring that there is no impairment of the parts due to the process.” There are both economic and environmental sound reasons for disassembly.Many issues and research need to be addressed in the area of disassembly. The most significant technical challenge is how to design a product for easy disassembly. Designing a product with “easy” disassembly constraints as well as “easy” assembly constraints is likely to be a very difficult task. In the past, products and machines were designed with only the assembly operations considered. Some of the problems to be addressed during design stages are the following: •Ease of separation. Design for ease of separation, handling, and cleaning of all product components.•Fasteners. New fasteners should be developed, and the existing ones should be improved. Screws, glues, and welds should be replaced by other fastening methods. Taking apart a snap-fitted or pop-in, pop-out product is much easier and requires less energy than taking apart a welded product.•Modularity design. The importance of using assemblies in a product’s design is to ease dealing with a product after its useful life (that is, designing with a base part).•Material selection. The variety of material types must be minimized to increase the recyclability of the product. Highly recyclable materials such as aluminum and thermoplastics should be encouraged, while the use of thermo sets, which cannot be recycled, should be minimized.Research from the CIM Institute by Rose and Evans focused on disassembly-oriented lifecycle analyses where recyclability of the product was evaluated under possible future trends in recycling technology and economy. At the Swiss Federal Institute of Technology, an evaluation procedure has been proposed to support product design according to conflicting design for disassembly criteria. Each criterion is weighted and the final decision made taken on the basis of scaling all relevant criteria. Leonard reported that two basic methods of disassembly were used: reverse assembly and brute force. For reverse assembly, if a fastener is screwed in, then it is screwed out; if two parts are snap-fit together, then they are snapped apart. For brute force, parts are just pulled or cut.Seliger, Zussman, and Kriwet stated that some obstacles make disassembly difficult for today’s manufactured product. First, it is difficult to gain all the information necessary to plan the disassembly. Parts of the product might have been modified during repair, and wear can make joined elements difficult to remove. In addition, many consumer products are not designed for ease of disassembly. Engineers have done an outstanding job of meeting functional requirements and federal emission regulations. Traditionally, the engineers concentrated on improving productivity and made the product easier to be assembled. Fastening processes, such as welding and adhesive bonding, are permanent-type systems. However, engineers will now have to incorporate recyclability and disassembly into their designs when creating future products.Disassembly sequence is another problem encountered in the design for disassembly. The problems associated with the disassembly sequence are 1) freeing the part of all attachments, 2) finding the succeeding part in the disassembly sequence, and 3) disassembly of the succeeding part. 第三部分6.5.4 Environmental EngineeringAll aspects of environmental problems are considered in environmental engineering, such as water and wastewater, environmental hydrology, environmental hydraulics and pneumatics, air, solid waste, noise, environmental modeling, and hazardous waste. Sincero defined environmental engineering as “the application of engineering principle’s, under constraint, to the protection and enhancement of the quality of the environment and to the enhancement and protection of public health and welfare.” As the US environ-mental policy expanded from clean air to cradle-to-grave solid and hazardous waste management environmental engineering research helped us better understand how pollutants migrate through soils, groundwater, and air, and developed treatment technologies to minimize their impact on natural and human environment.The water resource management system includes water pollution. wastewater disposal, and the measurement of water quality, supply, and treatment. Crook presented guidelines for water reuse. These guidelines were developed to encourage and facilitate the orderly planning, design, and implementation of water reclamation. The air resource management system includes air pollution control and the measurement of air quality. The solid waste management system includes solid waste collection and landfill design. Williams indicated that source reduction, recycling and composting, waste-to-energy facilities, and landfills are the four basic approaches to waste management.(l) Pollution PreventionThe term “pollution prevention” was coined in 1976 by the 3M Co. and is based on the technological and management advances program. The purposes of this program are l) to reduce environmental releases and 2) to lower costs in production from previous methods associated with pollution. The Pollution Prevention Act defined pollution prevention as “source reduction.” Considering this definition, it may infer that the creation of pollutants may be reduced or eliminated through increased efficiency in the use of raw materials, energy, water or other resources, or protection of natural resources by conservation. Pollution prevention is described as a “waste management hierarchy.” There are four preferences in the waste management hierarchy. The highest preference of the hierarchy is to reduce waste at the source of generation through the use of less toxic raw material, equipment changes process redesign, better housekeeping, and materials management. The second preference is reuse and recycling of wastes that cannot be reduced at the source. The third preference is waste treatment, and the least preferred a1ternative is disposal. Two methods of source reduction can be used: product changes and process changes. These two methods reduce the volume and toxicity of production wastes and end products during their lifecycles.The pollution prevention techniques used in industry are waste minimization and clean technology. Waste minimization includes source reduction and environmentally sound recycling. Source reduction is defined as many practice that reduces the amount of any hazardous substance, pollutant, or contaminant entering any waste stream or otherwise released into the environment prior to recycling, treatment, or disposal. Fig 6.5.3 shows source reduction methods. Clean technology uses less raw materials, energy, and water, generates less or no waste (gas, liquid, and solid), and recycles waste as useful materials in a closed system. The clean technology used in pollution prevention, can be categorized into five groups: improved plant operations in-process recycling, process modification, materials and product substitutions, and material separations.Fig 6.5.3 source reduction methods(2) Design for EnvironmentDesign for Environment (DFE) is defined by Lenox Jordan, and Ehrenfeld as “the systematic process by which firms design products and processes in an environmentally conscious way.” Another definition provided by Fiksel and Wapman is “the systematic consideration during new production and process development of design issues associated with environmental safety and health over the full product life cycle.” The scope of DEE encompasses many disciplines, including environmental risk management, product safety, occupational health and safety, pollution prevention ecology, re-source conservation, accident prevention, and waste management.Horvath et al. provided three main goals of DFE: 1) minimize the use of nonrenewable resources, 2) effectively manage renewable resources, and 3) minimize toxic release to the environment. The elements of DEE include: metrics, practices, and analysis methods. Mizuki, Sandborn, and Pitts explained that DEE requires the coordination of several design and data-based activities such as environmental impact metrics, data and database management; and design optimization (including cost assessments). The environ-mental metric is defined by Veroutis and Fava as “an algorithmic interpretation of levels of performance within an environmental criterion.” The environmental criterion is the environmental attribute of the product (that is, the energy to heat water for a specific function, grams of CO2 produced to deliver the above energy, chemical oxygen demand generated in the wastewater degree of risk of exposure to a toxic substance, and so on). The New Jersey Department of Environment Protection (NJDEP) conducted a major lifecycle assessment of the environmental impact of producing and disposing of packaging materials. NJDEP analyzed the specific pollutants released form packaging materials. The Hewlett-Packard Co. also provides the tools of DFE for the company's use; DFE guidelines, product assessments, and product stewardship metrics. The product stewardship metrics include material conservation and waste reduction, energy efficiency, and design for environmental and manufacturing process emissions. (3) Lifecycle Engineering and Lifecycle AssessmentLifecycle engineering (LCE) may also be referred to as lifecycle design (LCD). An outstanding analysis of lifecycle design that provides design sup-port from the environmental point of view was provided by Alting. Lifecycle design is based on the early product concept, including product and market research, design phases, manufacturing process, qualification, reliability issues, customerservice, maintainability, and supportability issues. Boothroyd and Alting distinguished six phases in the product lifecycle: need recognition, design development, production, distribution, use, and disposal. Ali of the phases must be considered during the conceptual stage, where it is possible to inexpensively change solutions to accommodate the requirements in each phase and in the total lifecycle.Lifecycle assessment is a family of methods for assessing materials, ser-vices I products processes, and technologies over the entire product life. The definition of product lifecycle assessment, developed by the Society of Environmental Toxicology and Chemistry, is as follows: Lifecycle assessment is an objective process to evaluate the environmental burdens associated with a product or activity by identifying and quantifying energy and materials used and wastes released to the environment, to access the impact of those energy and material uses and releases to the environment, and to evaluate and implement opportunities to affect environmental improvements. The assessment includes the entire lifecycle of the product, process, or activity, encompassing extracting and processing raw materials; manufacturing, transportation and distribution; use, reuse, maintenance; recycling and final disposal.Zust and Wagner explained four phases of the product lifecycle: 1) product definition, 2) product development, 3) product manufacturing and marketing, and 4) product usage. At each of these phases there exists a definition of objectives activities and deliverables for the next phase. Keys described that during the conceptual model phase, various designs and simulation models of the product are generated. From these conceptual models, requirements specifications and analyses will evolve decisions for breadboard and brassbound models. Also, Hewlett-Packard Co. addressed the lifecycle issue by prototyping software, defining development and phases, and standardizing modules and packages.第四部分(4) Green Product DesignGreen product design is expanded from pollution prevention. Green products-products that can reduce the burden on the environment during use and disposal-have additional marketing appeal. Green product design refers to green engineering design, defined by Navinchandra as “the study of and an approach to product and process evaluation and design for environmental compatibility that dose not compromise products’ quality or function.” This approach is comprised of two parts: l) the evaluation of de-signs to assess their environmental compatibility and 2) the relationship between design decisions and the green indicators. The aim of green engineering design is to develop an understanding of how design decisions affect a product's environmental compatibility. Navinchandra further stressed the need for green design for the following reasons: 1) environmental legislation, 2) corporate image and public reception, 3) demanding consumers, and 4) rising waste disposal costs.The Office of Technology Assessment focused on four objectives of green design in its report:1) Design for pollution prevention: refers to activities by manufacturers and consumers that prevent the generation of waste in the first place (that is, using less material to perform the same function, or designing durable products to extend the product service life).2) Design for better materials management: refers to activities that allow product components or materials to be recovered and reused in their highest value-added application (that is, designing products that can be readily disassembled into constituent materials, or using materials that can be recycled together without the need for separation).3) Design for re-manufacturing and recycling: refers to reducing virgin material extraction rates, waste generated from raw material separation and processing, and energy uses associated with manufacturing. It can also divert residual material from municipal waste| relieving pressure on overburdened landfills..4) Design for composting and incineration: refers to making products entirely out of biodegradable materials. For example, starch-based polymers (which are inherently biodegradable) easily compost, and film can substitute for plastic in a variety of applications.(5) Future TrendsBased on a previous survey, we discuss some suggestions of the future trends in ECD&M. Hopefully, the discussion will be beneficial for guiding other researchers’ topic selections. The ECD&M approach represents a fundamental change in the decision-making processes of most manufacturers. Historically I the selection of waste management methods was based on pure economic analyses of the quantifiable and measurable costs, and economical benefits. This approach ignores the very large number of qualitative factors affecting the selection of the appropriate technologies in decision making. ECD&M, on the other hand, is a complex, multidisciplinary, and multifunctional activity method to determine potentially large numbers of waste minimization technologies available in the industry, for example, changes in the product, changes in the input materials to the production process, changes in operating practices, and recycling. It requires the coordination of several designs and data-based activities, such as environmental impact analysis, data and database management and design optimizations.Many researchers have recognized the importance of ECD&M, and a considerable amount of research in this area has been conducted. While some research issues have been well addressed and the results are being used by the industry, other emerging issues are under initial investigation. These research issues are likely to be the focus in the years to come. This section provides a brief discussion of these issues to stimulate the interest of the research community.Disposition of End-of-Life Discrete Electromechanical ProductsMore research is required for the recycling of EOL discrete electromechanical products, while traditional continuing item products have attracted significant attention for environment impact. Great amounts of discrete electromechanical products have caused urgent concerns of their disposal and recycling problems. So far, there is not a generic method for recycling all different types of the electromechanical products; however, the production rate of such products is rising dramatically year by year. The lifecycle of such products has become shorter in the past decades. For example, the lifespan of personal computers has shortened from several years to several months. Due to wide diffusion of consumer goods, such as televisions, VCRs, microwaves, and the shortening of product lifecycles, a generic recycling method for electromechanical products is urgently needed.Pitts and Mizuki addressed the disposition problem of electronic products (such as CRTs and printed circuit boards) because these items cannot be recycled easily. Rodi developed a resource recovery model for EOL electronics that includes three parts: assessment, feasibility analysis, and implementation. The assessment allows an organization to efficiently organize the information on the suppliers, materials, quantities,and characteristics of its EOL waste. Feasibility analysis allows the organization to analyze the information gathered in the assessment phase for economic and environmental impacts. Implementation sets the operating parameters for the organization.Zhang and Kuo developed a disassembly model for electromechanical EOL products that is embedded on a graph representation by generating disassembly sequences. Information exchange within the disassembly model is done through four phases: l) disassembly representation and。
(完整)辽宁工程技术大学,先进制造技术,唐一平主编,英文版第三版,题库,翻译,复习资料
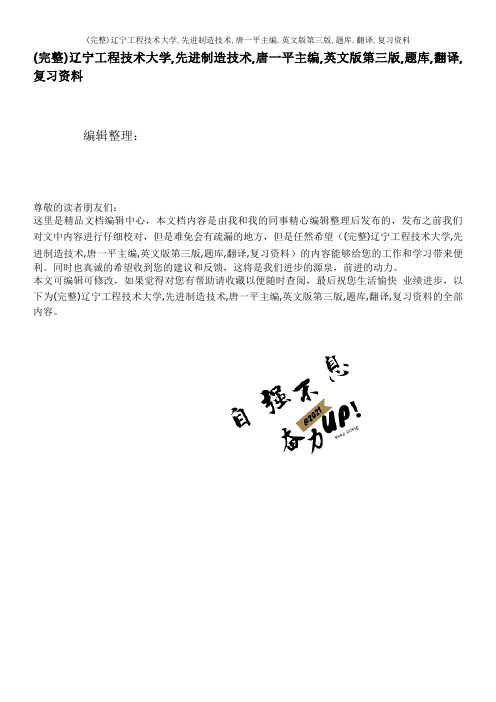
(完整)辽宁工程技术大学,先进制造技术,唐一平主编,英文版第三版,题库,翻译,复习资料编辑整理:尊敬的读者朋友们:这里是精品文档编辑中心,本文档内容是由我和我的同事精心编辑整理后发布的,发布之前我们对文中内容进行仔细校对,但是难免会有疏漏的地方,但是任然希望((完整)辽宁工程技术大学,先进制造技术,唐一平主编,英文版第三版,题库,翻译,复习资料)的内容能够给您的工作和学习带来便利。
同时也真诚的希望收到您的建议和反馈,这将是我们进步的源泉,前进的动力。
本文可编辑可修改,如果觉得对您有帮助请收藏以便随时查阅,最后祝您生活愉快业绩进步,以下为(完整)辽宁工程技术大学,先进制造技术,唐一平主编,英文版第三版,题库,翻译,复习资料的全部内容。
完形填空(1)The spokes of the wheel are made from various kinds of CAPACS involved in the activity .Each CAPACS has a communication link to the controlled database so that it will capture the data to form its own distributed database 。
Values are added the distributed database to meet the needs and requirements of its expected users. The application of CAPACS to the manufacturing process enables the total system to increase productivity,reduce waste, and produce things it would not otherwise be able to make. As a result, new technologies, demands for products of higher quality and lower production costs, and the needs for improved technology in a competitive society have caused extensive use of CAPACS。
先 进 制 造 技 术 Advanced manufacturing technology

(2) 实体造型与仿真
(3) CAD系统的集成化
减速机三维数字化模型
2、CAE技术
计算机辅助工程分析(Computer Aided Engineering ,CAE)技 术,是指在零件或整机的数字化特征建模完成之后,运用有限 元及边界元等数值分析方法,对零件或整机对其未来的工作状 态和运行行为进行结构、动力、运动及各种物理场耦合等一系 列分析、模拟的计算机辅助分析方法,其目的是及早发现设计缺 陷、优化结构并证实未来的产品功能和性能的可用性和可靠性。 它与CAD和CAM技术构成了当今计算机技术在机械设计及制造 领域最重要的三大支撑技术。
在世界经济史上,英国是第一个被称为“世 界制造中心”的国家,从1760年至1830年工业 革命期间,英国制造业在全世界的比重从 1.9%上升到9.5%,后来又达到19.9%,英国以 占世界2%的人口控制了全世界工业生产的 30%~50%和接近五成的制成品贸易。当时, 英国无论在贸易、商业、金融、技术和管理等 方面在世界经济上都是第一位。特别是在1820 年,英国的工业比重占全世界工业的50%,其 进出口占世界贸易总量的27%。
计算机辅助设计(Computer aided design) 计算机辅助工艺规划(Computer aided process planning,CAPP) 计算机辅助工程(Computer aided engineering,CAE) 计算机辅助制造(Computer aided manufacturing,CAM) 现代数控机床、柔性制造系统(Flexible manufacturing system,FMS)等
第二部分 主要现代制造技术
一、CAD/CAE/CAM技术
二、虚拟设计制造技术
三、柔性制造 四、其它先进制造技术
《先进制造技术》翻译作业及报告评阅书-2013

翻译及讲述内容
序号
翻译水平
(50)%
报告组织
(20%)
语言表达
(20%)
时间把握
(10%)
总评成绩
33
4.1 Introduction to Manufacturing System
PartⅠ
34
PartⅡ
35
PartⅢ
36
PartⅣ
37
PartⅤ
38
PartⅥ
39
4.2 Industrial Robots
总评成绩
23
3.4 Precision Manufacturing
PartⅠ
24
PartⅡ
25
PartⅢ
26
PartⅣ
27
PartⅤ
28
PartⅥ
29
3.5 Rapid Prototyping and Manufacturing
PartⅠ
30
PartⅡ
31
PartⅢ
32
PartⅣ
评阅人年月日序号学号PartⅠ65
PartⅡ
66
PartⅢ
67
PartⅣ
评阅人年月日
PartⅣ
15
PartⅤ
16
PartⅥ
17
PartⅦ
18
PartⅧ
19
3.3 Nanotechnology and Micro-machine
PartⅠ
20
PartⅡ
21
PartⅢ
22
PartⅣ
评阅人年月日
序号
学号
姓名
翻译及讲述内容
序号
翻译水平
(完整)先进制造技术(英文版第三版)唐一平,第五章翻译

P655数控数控(NC)是一种控制运动的方法通过直接插入代码指令的机器部件,以数字和字母,进入系统.系统自动解释这些数据并将其转换成输出信号。
这些信号,反过来,控制各种例如机器的部件,通过旋转主轴和关闭,改变工具,移动工件或工具沿着特定路径,或转向切削液的开和关.为了感谢机床数字控制的重要性,让我们简要回顾一个过程如何如工历来是开展。
在研究一部分的工作图纸,操作员设置合适的工艺参数(如切削速度,切削深度进给,切削液,等等),确定加工操作顺序要执行,夹在工件夹具的工件(如卡盘或夹头),并与部分的收益。
根据零件的形状和规定的尺寸精度,这方法需要熟练的操作人员。
后面的加工过程可能依赖于特定的操作;由于人类的可能性错误,甚至部分由同一操作者产生可能不完全相同。
零件的质量,因此,依赖于特定的操作或(甚至同一运营商)在一周或一天的时间一天。
因为增加关注提高产品质量和降低制造成本,这种变异(和对产品质量的影响)不再可接受的。
这种情况可以通过数值控制消除加工操作。
数值控制的重要性可以通过进一步的说明下面的例子。
假设几个孔被钻的一部分图5所示位置。
1.P66在加工这部分传统手工方法,操作者位置钻头相对于工件,使用参考点通过三种方法显示在图中给出。
然后操作员进行钻孔.让我们先假设100个部分,都有形状和尺寸精度的同时,也要钻。
显然,这操作将是乏味的,因为操作者必须经过相同的动作反复。
此外,概率高,各种原因,一些零件加工将与众不同。
现在让我们假设这个生产运行过程中,这些组成部分的顺序是改变了,和十的部分现在需要不同位置的孔.的机械师现在必须重新定位工作台;此操作将时间消费是错误的。
这样的操作可以由数控机床很容易进行能够生产部分多次准确地处理不同的部分(通过加载不同的部分程序,将描述后).在数值控制操作下,有关的所有方面的数据加工操作,如位置,速度,饲料,和切削液,可以存储在磁性介质上,随着时间变化从磁带到硬盘.的数控控制概念,具体信息可以向这些存储设备到机床的控制面板。
先进制造技术(有出处)--中英文翻译

毕业设计(论文)外文资料翻译系别:机械工程学院专业:机械设计制造及其自动化外文出处:Advanced Manufacturing Technology附件:1、外文原文;2、外文资料翻译译文。
1、外文原文(复印件)2、外文资料翻译译文先进制造技术尽管裁断的深度是由材料去除率的总额决定的,增加径向的裁断深度同样能够增加磨损率。
就像增加进给速度一样,工具的使用寿命会随着切削深度的加深而缩短。
因此,工具的使用寿命与磨损率能够像预期那样保持平衡。
每个金属在切削过程中会产生三个力:切向力,即零件运转时产生的力;径向力,由工件材料切削深度的阻隔产生的力;纵向力,利用进给速度产生的力。
这些力比机器运转过程中产生的力强30%到80%。
例如,在洛氏硬度62HRC的强度下,分别经过预热处理和热处理,纵向力会从30%增加到50%,切向力会从30%增加到50%,径向力会从70%增加到100%。
因此,机床必须能够承受不断增加的切削力,尤其是径向的切削力。
切削液能够影响白层的产生,因为白层是物象变化在表面发生的结果,当冷却工件表面时,切削液能够减轻热损坏。
一些报道认为切削液会消除白层,但却有研究表明切削液没有这样的作用。
刀具状态也是一个很重要的因素,然而白层的增加同样伴随着刀具的磨损。
如果硬态切削能够代替精磨操作,硬态切削的产品表面光洁度能够与精磨操作相媲美。
与精磨操作不同的是,表面光洁度是由大小,形状,强度和在磨削砂轮中磨粒的作用决定的。
硬车削表面通常是由切削过程中形成的几何图形决定的,其中主要是由切削工具的进给和刀尖半径决定的。
对于磨削圆柱的应用,其砂轮和工件必须能够顺利的旋转。
其次,砂轮飞快旋转的同时工件要缓慢的旋转。
如果旋转的构件不完全同心,组合的缺陷和旋转速度的细微差别会引起圆柱的凸角。
当生产的几何图形不够圆时,这会影响最终的生产。
另一方面,对于硬切削来说,工件或者切削工具不能同时旋转。
因此,机器加工表面将会与机床主轴和紧挨机床的中心线的机床纵向的方向一样精准。
- 1、下载文档前请自行甄别文档内容的完整性,平台不提供额外的编辑、内容补充、找答案等附加服务。
- 2、"仅部分预览"的文档,不可在线预览部分如存在完整性等问题,可反馈申请退款(可完整预览的文档不适用该条件!)。
- 3、如文档侵犯您的权益,请联系客服反馈,我们会尽快为您处理(人工客服工作时间:9:00-18:30)。
P65 对输入信息的基础上,继电备5 数控器和其他设备(硬程序员,它可能包含了制图数控( NC)是一种控制运动P67 信息的方法控制)可以采用以获得所需软件包和加工模拟,为了确通过直接插入代码指令的机的机器设置。
复杂操作(如保器部件,以数字和字母,进将有不同的轮廓,在一部分部分程序的 bug。
机器操作员入系统。
系统自动解释这些或开模铣床)可以很容易地可以,但是,容易和手动程数据并将其转换成输出信进行。
序计算机。
操作员可以修改号。
这些信号,反过来,控数控已经对制造业各方面的程序直接,准备不同的零件制各种重大影响操作。
数控机床是程序,并将程序。
由于利用例如机器的部件,通过旋转现在广泛使用的小中量生产小型计算机有一个大的内主轴和关闭,改变工具,移(通常是 500 件或更少)的存,动工件或工具沿着特定路各种各样的部分,在小商店P69径,或转向切削液的开和关。
和大型制造设施。
老的机器微处理器( S),和程序的编为了感谢机床数字控制的重通常可以加装数控。
辑功能,数控系统广泛今天要性, 5.1 历史使用的。
低成本可编程控制让我们简要回顾一个过程如在数值控制的基本概念,显器的可用性也起到了在数控何如工历来是开展。
在研究然是实现制造厂成功实施的重要作一部分的工作图纸,操作员在 19 世纪早期,当穿孔金属用。
设置合适的工艺参数(如切板卡被用来自动控制织机的在传统的数控系统数控机床削速度,切削深度进给,动作。
针由感应卡中孔的存的一些优点如下:切削液,等等),确定加工操在或不存在的活性。
这发明( 1)增加刀灵活性的机器可作顺序后自动钢琴(钢琴),其中钥以产生一个特定的部分,然要执行,夹在工件夹具的工匙是由流动的空气通过孔活后件(如性在穿孔辊穿孔纸。
其他不同形状的零件,以降卡盘或夹头),并与部分的收对数控机床的运动原理最初低成本。
益。
设想是在 40 年代由美国人在( 2)高精度电脑具有较高的根据零件的形状和规定的尺他企图机复杂的直升机桨采样率和更快的寸精度,这方法需要熟练的叶。
第一个原型数控机床建操作。
操作人员。
后面的加工过程于 1952 在麻省理工学院。
这( 3)多样化的编辑和调试程可能依赖于特定的操作;由是一个垂直轴,两轴仿形铣序,编程,于人类的可能性错误,甚至床加装伺服电机,和加工执策划和印刷部分的形状是简部分由同一操作者产生可能行的操作包括端铣和面铣上单的。
不完全相同。
厚厚的一层铝合金板数值数数控机床的 5.3 项原则的基零件的质量,因此,依赖于据被输入进纸带生成的数字本元素,一个典型的数控机特定的操作或(甚至同一运计算机,另一种是在相同的床操作显示图。
在数值控制营商)在一周或一天的时间开发时间在麻省理工学院。
功能元件和组件一天。
因为增加关注提高产在实验中,部分被加工成功,包括以下。
品质量和降低制造成本,这准确,并多次在没有操作员( 1)数据输入:数字信息的种变异(和对产品质量的影干预。
此成功的基础上,对读取和存储在磁带响)不再可接受的。
这种情机床工具行业开始设计,建读者或在计算机内存。
况可以通过数值控制消除设,销售数控机床工具。
后( 2)数据处理:程序读入机加工操作。
来,这些机器都配备了计算控制单元数值控制的重要性可以通过机数值控制( CNC)产生了更处理。
进一步的说明下面的例子。
大的灵活性,准确性,通用P70假设几个孔被钻的一部分图性强,易于操作。
( 3)数据欧印 UT:这个信5 所示位置。
1。
P68 息翻译成命令(通常P66 5.2 计算机数字控制脉冲命令)给伺服电机在加工这部分传统手工方在数控发展的下一个步骤,( fig.5.3 )。
然后移动的伺服法,操作者控制电机位置钻头相对于工件,使用硬件(安装在数控机床上)表(即工件安装)的特定位参考点转换到本地计算机用软件控置,通过线性或旋转运动,通过三种方法显示在图中给制。
两种类型的计算机系统由步进电机,丝杠,等类似出。
然后操作员进行钻孔。
被开发出来:直接数值控制,的装置。
让我们先假设 100 个部分,和计算机数值控制。
DNC),最控制电路的类型。
数控机床都有形状和尺寸精度的同在直接数字控制(可以控制通过两类型:开环时,也要钻。
显然,这操作初的设想和在上世纪60 年和闭环电路。
在开环系统将是乏味的,因为操作者必代,几台机器的直接控制,( fig.5.3(一)),信号通过控须经过相同的动作反复。
此一步一步,由一个中央计算制器发送给伺服电机,但运外,概率高,各种原因,一机主机。
在这个系统中,运动和工作台的最终位置不检些零件加工将与众不同。
营商已经进入中央计算机通查的准确性。
现在让我们假设这个生产运过远程终端。
这样,录音带闭环系统( fig.5.3( B))配备行过程中,这些组成部分的的处理在每台机器上的一个各种传感器,传感器和计数顺序是改变了,和十的部分单独的计算机需要被淘汰。
器,精确测量工作台的位置。
现在需要不同位置的孔。
的随着通过反馈控制,工作台的位机械师现在必须重新定位工DNC,所有机器在制造设备的置比较信号。
表运动终止时,作台;此操作将时间消费是状态监测从中央计算机评适当的坐标达到。
闭环系统错误的。
估。
然而,有一个关键的 DNC 是更复杂和更昂贵开环系这样的操作可以由数控机床缺点:如果计算机关闭时,统。
数控机床中的位置测量很容易进行能够生产部分多所有的机器都不起作用。
可以通过直接或间接的方次准确地处理DNC 最近的定义(现在意义法。
直接测量系统,传感装不同的部分(通过加载不同的分布式计算控制)包括中置读取的部分程序,将描述后)。
央计算机作为控制系统中的刻度尺在机台或滑直线运动在数值控制操作下,有关的应用在一些个人电脑数值控( fig.5.4(一))。
本系统是更所有方面的数据加工操作,制机器车载微机。
该系统提准确,因为规模建成如位置,速度,饲料,和切供了大量的内存和计算能机,和间隙(相邻两啮合齿削液,可以存储在磁性介质力,提供了灵活性,同时克轮齿之间的游戏)上,随着时间变化从磁带到服直接的缺点数值控制。
机制不显著硬盘。
的计算机数控( CNC)是一个系P71数控控制概念,具体信息可统的控制微型计算机是一台在间接测量系统,旋转编码以向这些机器或设备的一个组成部分器或解析器(图 5.4 ( b)。
存储设备到机床的控制面(车载电脑)。
该项目的一部中( C))转换成旋转运动的板。
分,可以通过远程站点的准平移运动。
在这个系统中,侧隙可显著影响测量精度。
位置反馈机制,利用各种传感器,主要是根据磁光电原理。
5.4 种类型的控制系统有数控控制系统的两个基本类型:点对点和轮廓。
(1)在一个点对点的系统,也被称为定位,对各轴机分别被丝杠驱动,一个氏取决于类型的以不同的速度运行。
该机最初在最大速度以减少非生产时间,但在刀具方法数据定义的位置。
因此,在一个操作钻床等(或打孔),定位和切割发生顺序(fig.5.5(一))。
在钻或冲孔缩回,工具上迅速移动到另一个位置,并重复上述操作。
路径从一个位置到另一个是重要的只有一点:它必须是选择减少旅行时间,提高效率。
点对点系统P72主要用于钻孔,冲孔,直铣操作。
(2)在一个轮廓系统(也被称为连续路径系统),其定位和操作都沿着指定的路径,但在进行不同的速度。
因为这个工具是它沿着规定的路径(fig.5.5 (B)),运动和速度的精确控制和同步是重要的。
轮廓系统通常用于车床,铣床机,研磨机,焊接机械,加工中心。
插值。
沿路径运动(插值)发生一个增量的几种基本方法(fig.5.6)。
实际的例子路径钻,镗,铣操作示于图5.7 冲压。
在所有的插值,路径控制,刀具的旋转中心。
对于不同类型的刀具补偿,对不同直径的工具,或在加工过程中,可以在数控程序的刀具磨损。
P73(一)线性插值,从开始到结束在一条直线上移动的工具( fig.5.6(一)),在两或三轴。
理论上,所有类型的配置文件,可以用这种方法生产的,做点小的增量(fig.5.6 (B))。
然而,大量的数据必须经过处理才能。
(b )在圆弧插补( fig.5.6(C)),为路径所需要的输入是结束点的坐标,对圆心和半径的坐标,并沿圆弧方向的工具。
(c)在抛物线插值法和三次插值,路径近似曲线的数学方程,利用高阶。
这种方法是有效的,是特别有用的五轴机床开模操作板汽车体形成。
这些方法也可用于工业机器人的运动。
5.5 精度的数值控制数控机床中的定位准确度被定义为机器可以定位到某一坐标系统。
数控机床通常有至少3±| 微米定位精度(0.0001。
)。
重复性(重复动作的位置一手工编程可以通过人的知识高生产力和多样性是加工中差的精确和一致的。
致性geable 关于特定的制造工艺心的主要优点。
能力进行钻主轴头的改进先进的容纳五P74 和能够理解,阅读,并改变孔,车削,铣削,钻孔,扩分之一轴(及以上)的运动,该机在相同的操作条件下)部分项目。
因为他们熟悉机孔,轮廓,和线程操作一台大大提高了加工中心的通用通常在± 8nm(0.0003。
)。
分床和工艺能力,熟练的机械机器上消除多个机床的需性。
重点对新设计的俯仰和辨率(机器的各部件运动的师能(有一些培训规划)也要,从而降低资本设备和劳横滚运动的主轴头的权利。
最小增量)通常是 2.5(。
IM 做手工编程。
然而,涉及的动力需求。
一个相对不熟练运动的附加轴是有必要的,( 0.0001。
)。
工作是乏味的,的操作员可以经常参加两个特别是在较大的加工中心,机床的刚度及其在齿轮和丝P76 加工中心,有时更。
大多数在工件不易移动,工具必须杠的间隙尺寸精度的重要。
费时,又不经济;因此,手工件可在一个单一的加工中倾斜和转向机固定阻尼部虽然在旧机器,反弹已与特工编程大多采用简单的点对心完成,往往与一个安装程分。
但主轴头移动超过三个殊化妆电路消除间隙(即工点应用。
序。
主轴也是小的工件越来越受具总是接近工件上的特定位计算机辅助编程涉及特殊符额外的储蓄导致减少物料搬欢迎。
部分以前加工几个设置,从同一方向),在现代机号编程语言,确定角点的坐运成本,夹具,和空间需求。
置 RAM 型万能铣床移动超过械间隙采用预加载滚珠丝杠标,边缘,和表面的部分。
大量的时间花在机器移动工小型加工中心可以完成一部消除。
同时,指挥信号的快编程语言是与计算机进行通作机保存,和吞吐量是多分设置。
速响应要求,摩擦和惯性被信的一种手段;它涉及到使faster.131 也,在制品库存,一些机床厂商现在提供水平最小化,例如,通过减少机用象征性符号。
程序员描述由通常出现在几台机器工件垂直轴。
这些在外观上右角器的运动部件的质量。
这种语言被加工的零件,和打滑表示,在只有一个机器的主轴附件一直都可以通过5.6 数控的优点和局限性计算机化的描述命令为数控工作取代。
90 度改变主轴定位相似。