FANUC系统参考点建立
FANUC系统1815

FANUC系统,编码器更换后如何设置回零点我的是fanuc系统,加工中心。
更换了一个新的编码器,绝对的编码器。
就是x轴电机屁股后面的红盖盖就是编码器。
更换后,要重新设置零点,回零点,请问如何设置?要详细的操作步骤!满意回答两种方法:A、对准标记设定参考点在机床上设置对准标记,注意对于磨床使用倾斜轴控制功能的轴上不能使用本功能。
准备工作:a:1005#1设为1——各轴返回参考点不使用挡块方式此时返回参考点就不需要使用减速信号*DEC。
b:1815#5设为1——使用绝对位置编码器1815#4设为0——绝对位置编码器原点位置未确立1006#5设为0——返回参考点方向为正向c:切断NC电源,断开主断路器d:把绝对位置编码器的电池连接到伺服放大器上e:接通电源自动检测编码器基准点(检测编码器的1转信号)(如果未进行此项操作继而进行参考点回零的话出现PS0090号报警)a:用手动或者手轮方式进给,让机床电机转动1转以上b:断开电源再接通电源设定参考点a:JOG方式下对各轴手动移动,将机床移动到10 06#5设定的反方向处,例如上面设的1006#5为0即返回参考点方向为正向,则将机床移至负向,如下图:b:按1006#5设定的返回参考点的方向移动机床,直至机床对准标记与参考点位置重合,当位置快要重合时使用手轮进给进行微调。
c:将1815#4设为1——绝对位置编码器原点位置已确立。
B、无挡块返回参考点不需要安装限位开关和挡块准备工作:a:1005#1设为1——各轴返回参考点不使用挡块方式此时返回参考点就不需要使用减速信号*DEC。
b:181 5#5设为1——使用绝对位置编码器1815#4设为0——绝对位置编码器原点位置未确立1006#5设为0——返回参考点方向为正向c:切断NC电源,断开主断路器d:把绝对位置编码器的电池连接到伺服放大器上e:接通电源自动检测编码器基准点(检测编码器的1转信号)(如果未进行此项操作继而进行参考点回零的话出现PS0 090号报警)a:用手动或者手轮方式进给,让机床电机转动1转以上b:断开电源再接通电源设定参考点a:JOG方式下对各轴手动移动至参考点返回方向的反方向,然后以1006#5设置的方向向参考点移动。
FANUC系统有挡块栅格法返回参考点
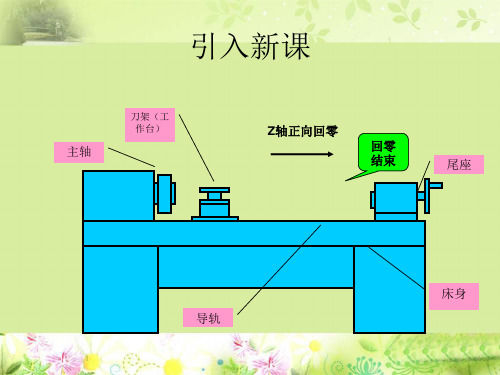
伺服模块
X9.2没有触发
快速接近
减速开关抬起
压下减速开关
超程
负向超程开关
减速开关
正向超程开关
外部接线错误 减速开关损坏
减速开关位置变化
超程
回零 结束
回参考点方向为负向
ZMI
1006
1
回零 结束
负向超程开关
减速开关
正向超程开关负向回零的机床回零 结束X轴负向回零
负向超程开关
减速开关
正向超程开关
(1)工作台快速接近减速开关
快速接近
负向超程开关
减速开关
正向超程开关
(1)工作台快速接近减速开关
• 运动方向设定
参数号
2022
电机旋转方向
• 运动速度设定
参数号
1428
每个轴手动返回参考点的快速移动速度
(2)工作台压下减速开关
• 运动方向
参数号
2022
电机旋转方向
• 运动速度
参数号
1425
每个轴手动返回参考点减速后的速度
• 压下减速开关X9.2(X9.0、X9.1)触发
(X9.0触发X轴减速;X9.1触发Y轴减速;X9.2触发Z轴减速)
(3)减速开关抬起,找到零点
• 运动方向
#7 参数号 #6 #5 ZMI
回零方向设定 #5(ZMI) 0 : 回参考点方向为正向。
#4
#3 #2
#1
#0
1006
• 运动速度
参数号
1 : 回参考点方向为负向。
低速接近
负向超程开关
减速开关
正向超程开关
超程
负向超程开关
减速开关
正向超程开关
FANUC数控系统基本参数的操作与设定
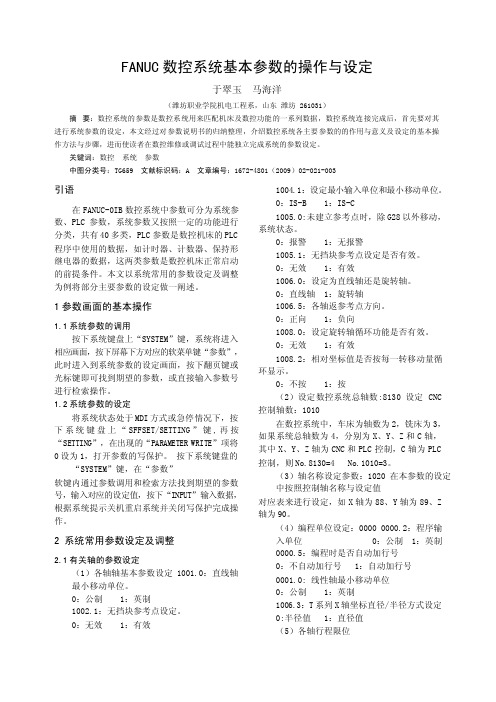
FANUC 数控系统基本参数的操作与设定于翠玉马海洋(潍坊职业学院机电工程系,山东潍坊 261031)摘要:数控系统的参数是数控系统用来匹配机床及数控功能的一系列数据,数控系统连接完成后,首先要对其进行系统参数的设定,本文经过对参数说明书的归纳整理,介绍数控系统各主要参数的的作用与意义及设定的基本操作方法与步骤,进而使读者在数控维修或调试过程中能独立完成系统的参数设定。
关键词:数控系统参数中图分类号:TG659 文献标识码:A 文章编号:1672-4801(2009)02-021-003引语在FANUC-0IB 数控系统中参数可分为系统参数、PLC 参数,系统参数又按照一定的功能进行分类,共有40 多类,PLC 参数是数控机床的PLC 程序中使用的数据,如计时器、计数器、保持形继电器的数据,这两类参数是数控机床正常启动的前提条件。
本文以系统常用的参数设定及调整为例将部分主要参数的设定做一阐述。
1 参数画面的基本操作1.1 系统参数的调用按下系统键盘上“SYSTEM”键,系统将进入相应画面,按下屏幕下方对应的软菜单键“参数”,此时进入到系统参数的设定画面,按下翻页键或光标键即可找到期望的参数,或直接输入参数号进行检索操作。
1.2 系统参数的设定将系统状态处于MDI 方式或急停情况下,按下系统键盘上“SFFSET/SETTING ”键, 再按“SETTING”,在出现的“PARAMETER WRITE”项将0 设为1,打开参数的写保护。
按下系统键盘的“SYSTEM”键,在“参数”软键内通过参数调用和检索方法找到期望的参数号,输入对应的设定值,按下“INPUT”输入数据,根据系统提示关机重启系统并关闭写保护完成操作。
2 系统常用参数设定及调整2.1 有关轴的参数设定(1)各轴轴基本参数设定 1001.0:直线轴最小移动单位。
0:公制1:英制1002.1:无挡块参考点设定。
0:无效1:有效1004.1:设定最小输入单位和最小移动单位。
FANUC机器人参考位置功能介绍与设定方法
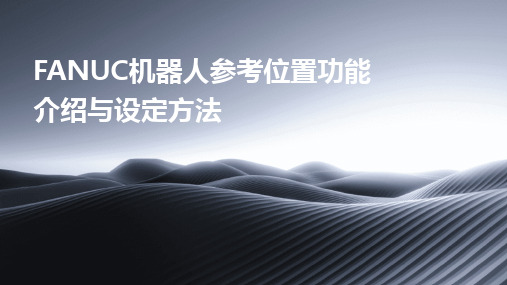
设定过程中出现异常提示
问题原因
可能是由于设定步骤错误、系统参数 设置不当或硬件故障导致。
解决方案
根据异常提示信息,检查设定步骤是 否正确,核对系统参数设置。如果问 题依旧存在,可能需要联系技术支持 进行排查。
应用价值评估
提高生产效率
通过设定合理的参考位置,可以 优化机器人的运动轨迹,减少无 效行程,从而提高生产效率。
降低维护成本
精确的参考位置设定可以减少机 器人的磨损和故障,降低维护成 本和停机时间。
增强产品品质
高精度的位置控制有助于提高产 品的加工精度和一致性,从而提 升产品品质。
未来发展趋势预测
参考位置功能可以帮助机器人快速定位到关键路径点,减少路径规划的
计算量和时间。
03
多机器人协同
在多机器人协同作业的场景中,各个机器人需要共享位置和姿态信息。
通过设定参考位置,可以实现多机器人之间的快速定位和协同运动。
相关术语解析
• 参考位置(Reference Position):在FANUC机器人中,参考位置是指用户设 定的一个或多个特定的机器人位置,用于后续操作中的快速定位或路径规划。
FANUC机器人参考位置功能 介绍与设定方法
目 录
• 参考位置功能概述 • 参考位置类型及特点 • 设定方法与步骤 • 常见问题与解决方案 • 案例分析与应用实例 • 总结与展望
01
参考位置功能概述
定义与作用
定义
参考位置功能是FANUC机器人中的一项重要功能,它允许用户设定一个或多个 特定的机器人位置作为参考点,以便在后续的操作中进行快速定位或路径规划。
FANUC发那科工业机器人系统基本参数设定

维修培训实习教材第二节基本参数设定一实习目的(一)掌握FANUC 数控系统的参数输入方法(二)掌握FANUC 数控系统的参数设定步骤(三)掌握机床运行所需要设定的最基本参数二实习内容学习“参数设定支持画面”中每一项的设定三实习步骤有关参数设定的说明:对于FANUC数控系统,其参数的数目是很大的,想对每一位参数都进行掌握和设定是很困难的。
事实上,对FANUC数控系统参数,并不是需要对其输入某个数值才称之为设定参数。
大部分的位型参数,设为0时反而是有效的,设为0反而是很多机床默认的习惯状态。
这点在进行参数学习时要清楚。
具体步骤:(一)系统通电,将“参数可写入”开关打开。
- 1 -(二)系统断电,重新开机,开机的同时按住[RESET]功能键直到系统进入正常画面,其结果是系统参数被清除,但系统功能参数(也叫保密参数)(NO.9900-9999)不被清除,如果是新版系统,系统功能参数(也叫保密参数)存在于系统软件中,也不会被清除。
所以,此项操作仅会清除系统功能参数(也叫保密参数)之外的普通参数(三)按[SYSTEM] 功能键,然后按扩展软键[+]几次,直到出现参数设定支持画面的软键[PRMTUN] 。
进入参数设定支持画面(按软键[PRMTUN])。
按此键几次,出现下图中的软键[PRMTUN]- 2 -参数设定步骤和内容画面中的项目就是参数的设定调试步骤。
这次着重学习第一项“AXISSETTING(轴设定)”项和最后一项“MISCELLANY (其它)”项,参数设定支持画面里的其他项(伺服参数设定,主轴设定等)将在别的课时里学习。
(四)按照顺序设定这两项参数。
第一项:AXIS SETTING(轴设定)项,轴设定里面有以下几个组,对每一组参数进行设定。
(BASIC(基本))组:有关基本设定的参数。
组参数号简述设定说明- 3 -基本1001#0 直线轴的最小移动单位0:公制(公制机床)公制机床设定为01002#1 无档块参考点设定1004#1 设定最小输入单位和最小移动单位。
FANUC数控系统加工中心工件坐标系建立与操作技巧
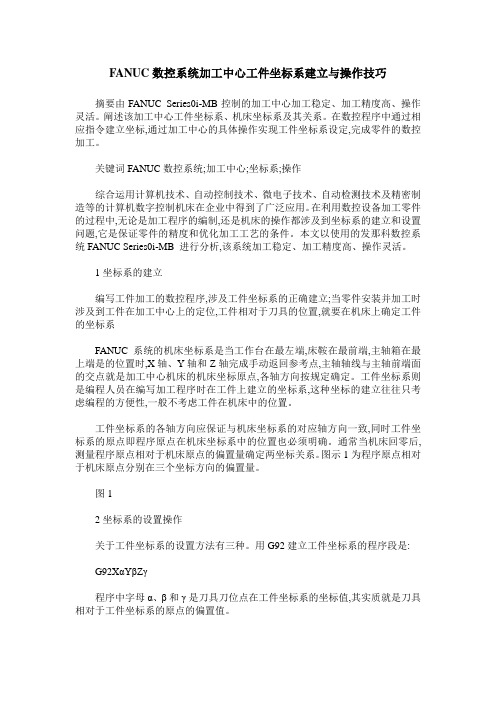
FANUC数控系统加工中心工件坐标系建立与操作技巧摘要由FANUC Series0i-MB控制的加工中心加工稳定、加工精度高、操作灵活。
阐述该加工中心工件坐标系、机床坐标系及其关系。
在数控程序中通过相应指令建立坐标,通过加工中心的具体操作实现工件坐标系设定,完成零件的数控加工。
关键词FANUC数控系统;加工中心;坐标系;操作综合运用计算机技术、自动控制技术、微电子技术、自动检测技术及精密制造等的计算机数字控制机床在企业中得到了广泛应用。
在利用数控设备加工零件的过程中,无论是加工程序的编制,还是机床的操作都涉及到坐标系的建立和设置问题,它是保证零件的精度和优化加工工艺的条件。
本文以使用的发那科数控系统FANUC Series0i-MB 进行分析,该系统加工稳定、加工精度高、操作灵活。
1坐标系的建立编写工件加工的数控程序,涉及工件坐标系的正确建立;当零件安装并加工时涉及到工件在加工中心上的定位,工件相对于刀具的位置,就要在机床上确定工件的坐标系FANUC系统的机床坐标系是当工作台在最左端,床鞍在最前端,主轴箱在最上端是的位置时,X轴、Y轴和Z轴完成手动返回参考点,主轴轴线与主轴前端面的交点就是加工中心机床的机床坐标原点,各轴方向按规定确定。
工件坐标系则是编程人员在编写加工程序时在工件上建立的坐标系,这种坐标的建立往往只考虑编程的方便性,一般不考虑工件在机床中的位置。
工件坐标系的各轴方向应保证与机床坐标系的对应轴方向一致,同时工件坐标系的原点即程序原点在机床坐标系中的位置也必须明确。
通常当机床回零后,测量程序原点相对于机床原点的偏置量确定两坐标关系。
图示1为程序原点相对于机床原点分别在三个坐标方向的偏置量。
图12坐标系的设置操作关于工件坐标系的设置方法有三种。
用G92建立工件坐标系的程序段是: G92XαYβZγ程序中字母α、β和γ是刀具刀位点在工件坐标系的坐标值,其实质就是刀具相对于工件坐标系的原点的偏置值。
FANUC系统培训教案10
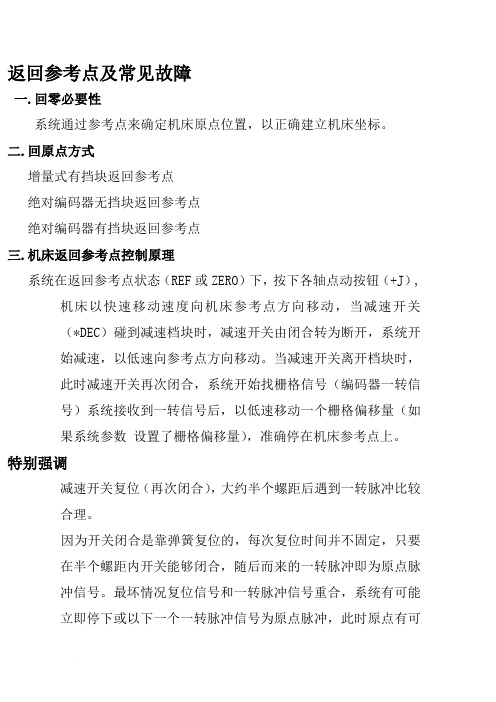
返回参考点及常见故障一.回零必要性系统通过参考点来确定机床原点位置,以正确建立机床坐标。
二.回原点方式增量式有挡块返回参考点绝对编码器无挡块返回参考点绝对编码器有挡块返回参考点三.机床返回参考点控制原理系统在返回参考点状态(REF或ZERO)下,按下各轴点动按钮(+J),机床以快速移动速度向机床参考点方向移动,当减速开关(*DEC)碰到减速档块时,减速开关由闭合转为断开,系统开始减速,以低速向参考点方向移动。
当减速开关离开档块时,此时减速开关再次闭合,系统开始找栅格信号(编码器一转信号)系统接收到一转信号后,以低速移动一个栅格偏移量(如果系统参数设置了栅格偏移量),准确停在机床参考点上。
特别强调减速开关复位(再次闭合),大约半个螺距后遇到一转脉冲比较合理。
因为开关闭合是靠弹簧复位的,每次复位时间并不固定,只要在半个螺距内开关能够闭合,随后而来的一转脉冲即为原点脉冲信号。
最坏情况复位信号和一转脉冲信号重合,系统有可能立即停下或以下一个一转脉冲信号为原点脉冲,此时原点有可能偏移一个螺距的距离,原点返回便不准确了。
基本概念:1.栅格偏移量16/18/21/16i/18i/21i 系统 18500 系统 508-511减速开关由压下断开到复位(由0变为1后)检测到的第1个1转信号后系统的偏移量调整栅格偏移量可调整原点位置2.手动返回参考点方向16/18/21/0i 系统 1006#50系统 3#3设为0,按正方向设为1,按负方向3. 手动返回参考点,同时控制轴数16/18/21/0i 系统 1002#00系统 49#4设为1:3轴设为0:1轴4.第一,第二参考点16/18/21/ 0i 系统 1240 12410 系统 708-711 735-7375.栅格宽度:16/18/21/ 0i 系统 18210 系统 570-573可以在伺服设定画面中参考计数器中直接设定,电机每转进给长度或角度值6.手动返回参考点速度16/18/21/ 0i 系统 14200系统 518 519 520 5217.返回参考点减速速度16/18/21/ 0i 系统 14250 系统 534四.数控系统返回参考点故障1.找不到参考点①机床回零过程无减速动作或一直以减速回零。
FANUC系统校基准点步骤

1、 MDI方式下,按功能键[OFFSET] - [SETTING],找到设定界面,将“写参数”改为“1 可以”,此时参数可写;
2、 按[SYSTEM]进入参数界面,找到1815参数,将需要校参考点的那个轴的1815号参数改为0(直接按0,然后按input即可),关开机一次;
3、 确保1240,1320,1321参数还在,此分别为机床基点坐标值和正负软限位值;
②、重复X轴校基点步骤中的3,4两步;
③、也可粗略的设定Z轴基点,用卷尺直接测量刀盘端面到主轴端面的距离,使之达到参数1240中设定的值,然后重复X轴校基点步骤中的3,4两步即可;
6、 为防止误改参数,将第一步中的“写参数”改为“0 不可以”,基点设定完成。
另外一种校X轴参考点的方法:
前提条件:刀具刀补已知,并且刀具没有被拆下来过;
①、跟对刀步骤一样,先取消刀补(用指令Txx00)和坐标偏移;
②、切削零件;
③、记下当前屏幕上的尺寸(X轴)B;
④、测量零件尺寸;
⑤、计算:A=参数1240中设定的值-刀补-零件尺寸+屏幕上显示的尺寸B
⑥、移动坐标到A点上(X轴基点位置);
⑦、重复X轴校基点步骤中的3,4两步。
如有问题请联系
祝好!
4、 X轴校基点步骤:
①、测量刀盘上镗孔刀座孔中心到镗孔刀座在刀盘上安装面的距离A;
②、使用工具使镗孔刀座孔与主轴中心对中,此时将X轴相对坐标U设定为“2*A”,再使用手轮将X轴向正方向移动至参数1240中设定的坐标(X轴基点位置);
③、将对应轴的1815#5(1815参数从右边数第六位)改为“1”, 关开机一次,再将1815#4改为“1”,再关开机一次;
FANUC、SIEMENS数控机床参考点的原理、设置与维修

FANUC、SIEMENS数控机床参考点的原理、设置与维修当数控机床更换、拆卸电机或编码器后,机床会有报警信息:编码器内的机械绝对位置数据丢失了,或者机床回参考点后发现参考点和更换前发生了偏移,这就要求我们重新设定参考点,所以我们对了解参考点的工作原理十分必要。
参考点是指当执行手动参考点回归或加工程序的G28指令时机械所定位的那一点,又名原点或零点。
每台机床有一个参考点,根据需要也可以设置多个参考点,用于自动刀具交换(ATC)、自动拖盘交换(APC)等。
通过G28指令执行快速复归的点称为第一参考点(原点),通过G30指令复归的点称为第二、第三或第四参考点,也称为返回浮动参考点。
由编码器发出的栅点信号或零标志信号所确定的点称为电气原点。
机械原点是基本机械坐标系的基准点,机械零件一旦装配好,机械参考点也就建立了。
为了使电气原点和机械原点重合,将使用一个参数进行设置,这个重合的点就是机床原点。
机床配备的位置检测系统一般有相对位置检测系统和绝对位置检测系统。
相对位置检测系统由于在关机后位置数据丢失,所以在机床每次开机后都要求先回零点才可投入加工运行,一般使用挡块式零点回归。
绝对位置检测系统即使在电源切断时也能检测机械的移动量,所以机床每次开机后不需要进行原点回归。
由于在关机后位置数据不会丢失,并且绝对位置检测功能执行各种数据的核对,如检测器的回馈量相互核对、机械固有点上的绝对位置核对,因此具有很高的可信性。
当更换绝对位置检测器或绝对位置丢失时,应设定参考点,绝对位置检测系统一般使用无挡块式零点回归。
一:使用相对位置检测系统的参考点回归方式:1、FANUC系统:1)、工作原理:当手动或自动回机床参考点时,首先,回归轴以正方向快速移动,当挡块碰上参考点接近开关时,开始减速运行。
当挡块离开参考点接近开关时,继续以FL速度移动。
当走到相对编码器的零位时,回归电机停止,并将此零点作为机床的参考点。
2)、相关参数:参数内容系统0i/16i/18i/21i0所有轴返回参考点的方式: 0. 挡块、 1. 无挡块1002.10076各轴返回参考点的方式: 0. 挡块、 1. 无挡块1005.10391各轴的参考计数器容量18210570~0575 7570 7571每轴的栅格偏移量18500508~0511 0640 0642 7508 7509是否使用绝对脉冲编码器作为位置检测器: 0. 不是、是 1815.50021 7021 绝对脉冲编码器原点位置的设定:0. 没有建立、 1. 建立1815.40022 7022 位置检测使用类型:0.内装式脉冲编码器、1. 分离式编码器、直线尺1815.10037 7037快速进给加减速时间常数16200522快速进给速度14200518~0521FL速度14250534手动快速进给速度14240559~0562伺服回路增益182505173)、设定方法:a、设定参数:所有轴返回参考点的方式=0;各轴返回参考点的方式=0;各轴的参考计数器容量,根据电机每转的回馈脉冲数作为参考计数器容量设定;是否使用绝对脉冲编码器作为位置检测器=0 ;绝对脉冲编码器原点位置的设定=0;位置检测使用类型=0;快速进给加减速时间常数、快速进给速度、FL速度、手动快速进给速度、伺服回路增益依实际情况进行设定。
分析FANUC数控系统返回参考点功能
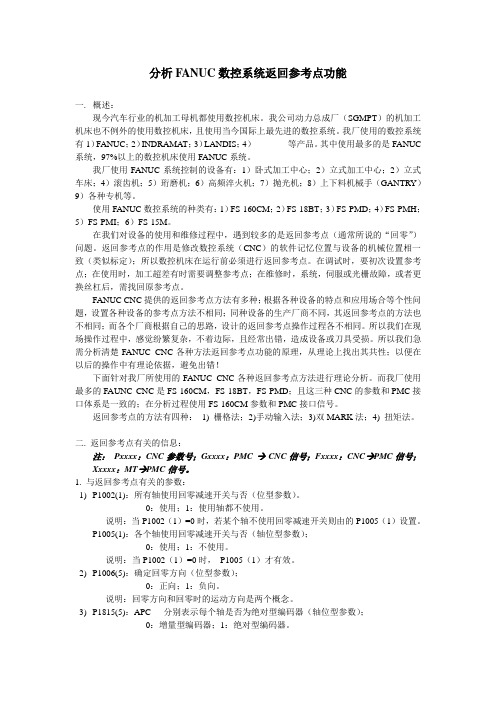
分析FANUC数控系统返回参考点功能一. 概述:现今汽车行业的机加工母机都使用数控机床。
我公司动力总成厂(SGMPT)的机加工机床也不例外的使用数控机床,且使用当今国际上最先进的数控系统。
我厂使用的数控系统有1)FANUC;2)INDRAMA T;3)LANDIS;4)等产品。
其中使用最多的是FANUC 系统,97%以上的数控机床使用FANUC系统。
我厂使用FANUC系统控制的设备有:1)卧式加工中心;2)立式加工中心;2)立式车床;4)滚齿机;5)珩磨机;6)高频淬火机;7)抛光机;8)上下料机械手(GANTRY)9)各种专机等。
使用FANUC数控系统的种类有:1)FS-160CM;2)FS-18BT;3)FS-PMD;4)FS-PMH;5)FS-PMI;6)FS-15M。
在我们对设备的使用和维修过程中,遇到较多的是返回参考点(通常所说的“回零”)问题。
返回参考点的作用是修改数控系统(CNC)的软件记忆位置与设备的机械位置相一致(类似标定);所以数控机床在运行前必须进行返回参考点。
在调试时,要初次设置参考点;在使用时,加工超差有时需要调整参考点;在维修时,系统,伺服或光栅故障,或者更换丝杠后,需找回原参考点。
FANUC CNC提供的返回参考点方法有多种;根据各种设备的特点和应用场合等个性问题,设置各种设备的参考点方法不相同;同种设备的生产厂商不同,其返回参考点的方法也不相同;而各个厂商根据自己的思路,设计的返回参考点操作过程各不相同。
所以我们在现场操作过程中,感觉纷繁复杂,不着边际,且经常出错,造成设备或刀具受损。
所以我们急需分析清楚FANUC CNC各种方法返回参考点功能的原理,从理论上找出其共性;以便在以后的操作中有理论依据,避免出错!下面针对我厂所使用的FANUC CNC各种返回参考点方法进行理论分析。
而我厂使用最多的FAUNC CNC是FS-160CM,FS-18BT,FS-PMD;且这三种CNC的参数和PMC接口体系是一致的;在分析过程使用FS-160CM参数和PMC接口信号。
FANUC 0i-MF数控系统参考点建立与调整
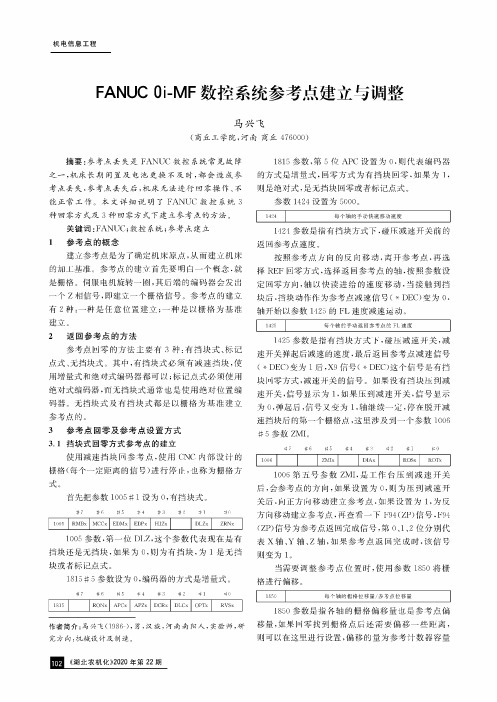
机电信息工程FANUC0i・MF数控系统参考点建立与调整马兴飞(商丘工学院,河南商丘476000)摘要:参考点丢失是FANUC数控系统常见故障之一,机床长期闲置及电池更换不及时,都会造成参考点丢失,参考点丢失后,机床无法进行回零操作、不能正常工作。
本文详细说明了FANUC数控系统3种回零方式及3种回零方式下建立参考点的方法。
关键词:FANUC;数控系统;参考,占、建立1参考点的概念建立参考点是为了确定机床原点,从而建立机床的加工基准。
参考点的建立首先要明白一个概念,就是栅格。
伺服电机旋转一圈,其后端的编码器会发出一个Z相信号,即建立一个栅格信号。
参考点的建立有2种:一种是任意位置建立;一种是以栅格为基准建立。
2返回参考点的方法参考点回零的方法主要有3种:有挡块式、标记点式、无挡块式。
其中,有挡块式必须有减速挡块,使用增量式和绝对式编码器都可以;标记点式必须使用绝对式编码器,而无挡块式通常也是使用绝对位置编码器。
无挡块式及有挡块式都是以栅格为基准建立参考点的。
3 参考点回零及参考点设置方式3.1挡块式回零方式参考点的建立使用减速挡块回参考点,使用CNC内部设计的栅格(每个一定距离的信号)进行停止,也称为栅格方式。
首先把参数1005'1设为0,有挡块式。
'7'6'5'4'3'2'1'0 1005RMBx MCCx EDMx EDPx HJZx DLZx ZRNx 1005参数,第一位DLZ,这个参数代表现在是有挡块还是无挡块,如果为0,则为有挡块,为1是无挡块或者标记点式。
1815'5参数设为0,编码器的方式是增量式。
'7'6'5'4'3'2'1'01815RONx APCx APZx DCRx DLCx OPTx RVSx作者简介:马兴飞(1986-),男,汉族,河南南阳人,实验师,研究方向:机械设计及制造。
FANUC基本参数设定
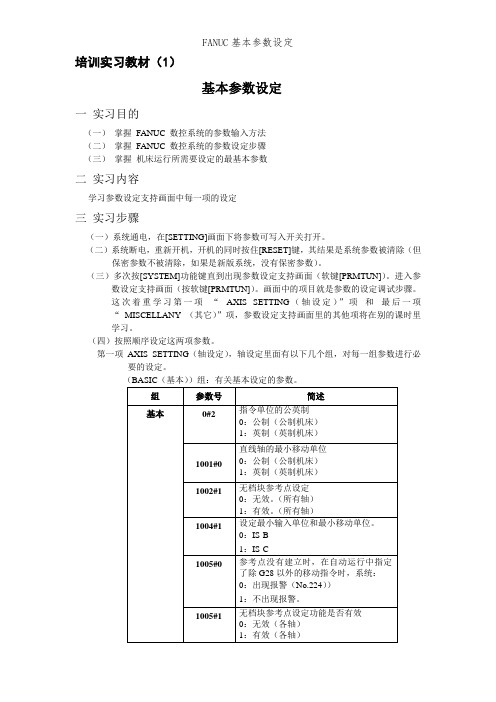
培训实习教材(1)基本参数设定一实习目的(一)掌握FANUC 数控系统的参数输入方法(二)掌握FANUC 数控系统的参数设定步骤(三)掌握机床运行所需要设定的最基本参数二实习内容学习参数设定支持画面中每一项的设定三实习步骤(一)系统通电,在[SETTING]画面下将参数可写入开关打开。
(二)系统断电,重新开机,开机的同时按住[RESET]键,其结果是系统参数被清除(但保密参数不被清除,如果是新版系统,没有保密参数)。
(三)多次按[SYSTEM]功能键直到出现参数设定支持画面(软键[PRMTUN])。
进入参数设定支持画面(按软键[PRMTUN])。
画面中的项目就是参数的设定调试步骤。
这次着重学习第一项“AXIS SETTING(轴设定)”项和最后一项“MISCELLANY (其它)”项,参数设定支持画面里的其他项将在别的课时里学习。
(四)按照顺序设定这两项参数。
第一项AXIS SETTING(轴设定),轴设定里面有以下几个组,对每一组参数进行必要的设定。
(BASIC(基本))组:有关基本设定的参数。
(COORDINA TE(坐标系))组:有关坐标系的参数。
(ACC./DEC.(加/减速))组:有关加减速的参数。
最后一项“MISCELLANY (其它)”项里面有一个组,对该组的参数进行设(五)设完之后,用手动进给方式尝试轴的进给,同时观察系统诊断画面,看看在梯形图正常的情况下,轴为什么不能实现进给?注意以下几个参数:PRM NO. 1023PRM NO. 1800#1(#404报警的屏蔽)PRM NO. 3003#0 3003#2 3003#3(互锁信号的屏蔽)PRM NO. 3004#5(硬限位信号的屏蔽)查找参数说明书,了解它们的详细意义,然后进行正确的设定。
考虑一下,在实际的机床当中,这些参数的设定!。
fanucMD第二参考点

Fanuc MD第二参考点FANUC MD系统调试资料常用参数说明:修改参数请在“OFF/SET”界面将参数可写树设为“1”参数号设定值002041005#011320100001321-60000014102000014202400014221000014236000185120185220设定绝对值编码器零点1815#5(APCx)设为1,关机,将机械移动到零点位置,1815润滑:间隔时间T2 40min 打油时间T0 12s调试刀库:Z轴第二参考点 1241 主轴定向角度 4077考机程序:刀库(斗笠式)考机程序:G53 G00 X0 Y0 Z0;T2 M6;X-800. Y-500. Z-500.;G54 G00 Z-100.;M03 S1000;M03 S1000 ;M99;G04 X2;整圆切削程序:T16 M6;G54 G01 X0 Y0 Z20. F2000;G54 G00 Z-100.;G01 Z-40.;M03 S1000 ;Z3.;G04 X2;M03 S1500;T8 M6;Z-3. F100;G54 G00 Z-100.;G02 I-40.;M03 S1000;Z-4.95;G04 X2;G02 I-40.;T12 M6;Z-5;G54 G00 Z-100.;G02 I-40.;M03 S1000 ;Z20.F1000;G04 X2;M05;M99;M30;CF卡的DNC操作步骤:将CF卡插到MDI面板的插槽中,将方式选择开关拨到DNC方式,按以下步骤进入DNC [PROGRAM]→[<] → [>] [>] → [DNC CD]选择CF卡上加工程序的编号,按[DNC-ST]键,按循环启动按钮,开始DNC加工。
激光精度检测程序:O0000;O0001;G90;G54 G90 G01 Z0 F4000;M98 P0001 L3;/ / M00;M30;M98 P0002 L24;%G4 X4;M98 P0003 L24;G4 X4;M99;%O0003;G91 G01 X25. F4000;G4 X4;M99;%DNC连线参数设置:0000:000000100020:0 0101: 100010010102:0资料说明CF卡通道未回零可以自动运行正向软限位负向软限位空运行速度最高快移速度最大切削速度手动移动速度反向间隙1反向间隙2,1815#4(APZx)设为1,关机,零点生效。
FANUC数控机床参考点丢失后建立方法

() 5 调节阀门特性 曲线与调节系统静态特性曲线不相符 。 机 组正常状态下 , 动机活塞行程相当于调节汽 门开度 , 油 随着调节
汽门开度增 大,即油动机活塞行程增大 ,汽轮机功率也随之增
大。调节阀门特性 曲线即是油动机行程和汽轮机 功率之问 的关 系曲线 。 在某一功率下 , 根据调节阀门特性曲线可得到对应 的油 动机活塞行 程和调节汽 门开度 ,再根据调速汽门开度得到相对
栅点法 回机床原点根据采用 的编码器不 同有 :挡块 式回参
考 点 、 块 式 回参考 点 及 无 挡 块 或撞 块 时 回参 考 点 。 照 检 测 元 撞 按
测反馈元件所发 出的栅点信号或零标志信号确立的参考点 。为
了使电气原点与机械原点重合 ,必须将 电气原点到机械原点 的
件测量方式的不 同分为绝对脉冲编码器和增量脉冲编码器方式
应的汽轮机转速 。汽轮机功率和汽轮机转速之间的关 系曲线即
是 调节 系统静态特性 曲线 。 机 组负荷在 2 MW 以下运行时 , 组加减 负荷时均平稳正 2 机
圈 设 管 与 修 22 5 置 理 维 0 № 1
运行正常 。
() 2 汽轮机调节系统故障。进行调节系统静态试验 , 输入模
拟信号调节油动机行程 , 对应汽轮 机调速汽 门开度符合要求 。
() 3 电液 转 换 器 故 障 或 控 制油 压 力 问题 。 换 1台新 电 液 转 更
换器 , 调整 电控供油系统 中的溢 流阀 , 保持 系统 油压 , 机组甩 负 荷现象没有改善 。 () 4 调节阀故 障。测量调节阀操纵座连杆滚轮与凸轮 间隙 ,
在 2 MW 以上 运 行 时 , 节 阀 门特 性 曲线 与 调 节 系统 静 态 特 性 2 调 曲线 不 相符 是 造 成 发 电机 组 甩 负 荷 的 主 要 原 因 。
参考点的设置(Fanuc

1、发那克系统:
1)、工作原理:
当手动或自动回机床参考点时,首先,回归轴以正方向快速移动,当挡块碰上参考点接近开关时,开始减速运行。当挡块离开参考点接近开关时,继续以FL速度移动。当走到相对编码器的零位时,回归电机停止,并将此零点作为机床的参考点。
b、选择“手动”模式,将控制轴移动到参考点附近;
c、输入参数:MD34100,机床坐标位置;
d、激活绝对编码器的调整功能:MD34210=1.绝对编码器调整状态;
e、按机床复位键,使机床参数生效;
f、机床回归参考点;
g、机床不移动,系统自动设置参数:34090. 参考点偏移量;34210. 绝对编码器设定完毕状态,屏幕上显示位置是MD34100设定位置。
b、重启电源,回参考点。
C、在|报警/诊断|→|伺服|→|伺服监视(2)|,计下栅间隔和栅格量的值。
d、计算栅罩量:
当栅间隔/2<栅格量时,栅罩量=栅格量-栅间隔/2
当栅间隔/2>栅格量时,栅罩量=栅格量+栅间隔/2
e、把计算值设定到栅罩量参数中。
f、重启电源,再次回参考点。
g、重启电源。
2)、无挡块参考点方式调整:
a、设定参数: #2049 = 2 无挡块参考点调整方式;
#2050 = 0 正方向、 = 1 负方向;
b、选择“绝对位置设定”画面,选择手轮或寸动模式;
c、在“绝对位置设定”画面,选择“无碰压”方式;
d、#0绝对位置设定=1 , #2原点设定:以基本机械坐标为准,设定参考点的坐标值;
是否使用绝对脉冲编码器作为位置检测器: 0. 不是 、1. 是 1815. 50021 7021
fanuc系统数控车床设置工件零点常用方法

fanuc系统数控车床设置工件零点常用方法1.直接用刀具试切对刀1.用外园车刀先试车一外园,记住当前X坐标,测量外园直径后,用X坐标减外园直径,所的值输入offset界面的几何形状X值里。
2.用外园车刀先试车一外园端面,记住当前Z坐标,输入offset界面的几何形状Z值里。
2.用G50设置工件零点1.用外园车刀先试车一外园,测量外园直径后,把刀沿Z轴正方向退点,切端面到中心。
2.选择MDI方式,输入G50 X0 Z0,启动START键,把当前点设为零点。
3.选择MDI方式,输入G0 X150 Z150 ,使刀具离开工件进刀加工。
4.这时程序开头:G50 X150 Z150 …….。
5.注意:用G50 X150 Z150,你起点与终点务必一致即X150 Z150,这样才能保证重复加工不乱刀。
6.如用第二参考点G30,即能保证重复加工不乱刀,这时程序开头G30 U0 W0 G50 X150 Z1507.在FANUC系统里,第二参考点的位置在参数里设置,在Yhcnc软件里,按鼠标右键出现对话框,按鼠标左键确认即可。
3.用工件移设置工件零点1.在FANUC0-TD系统的Offset里,有一工件移界面,可输入零点偏移值。
2.用外园车刀先试切工件端面,这时Z坐标的位置如:Z200,直接输入到偏移值里。
3.选择“Ref”回参考点方式,按X、Z轴回参考点,这时工件零点坐标系即建立。
4.注意:这个零点一直保持,只有从新设置偏移值Z0,才清除。
4.用G54-G59设置工件零点1.用外园车刀先试车一外园,测量外园直径后,把刀沿Z轴正方向退点,切端面到中心。
2.把当前的X与Z轴坐标直接输入到G54----G59里,程序直接调用如:G54X50Z50……。
3.注意:可用G53指令清除G54-----G59工件坐标系。
Fanuc系统数控车床常用固定循环G70-G80祥解1.外园粗车固定循环(G71)假如在下图用程序决定A至A’至B的精加工形状,用△d(切削深度)车掉指定的区域,留精加工预留量△u/2及△w。
FANUC教学回参考点及对刀
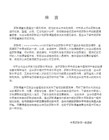
3、编写好程序内容后,按“RESET”复位按钮;
4、进入机床的“自动运行”状态,并选中下方的“单段”,在小倍率状态下按“循环启动”执行程序。
二、数控车床一把刀的对刀过程:
1、工件安装及刀具安装好后,在“手动”状态下,使刀具靠近工件;
2、进入“手轮”状态,选择好方向及手轮速率后,切工件端面,沿原路(X轴)离开工件;
3、选择对刀界面“工具/形状”,在指定的刀位后的“Z”轴输入“Z0.0”后按下方“测量”按钮,产生刀具的Z编程坐标;
4、利用手轮使刀具切工件外圆,沿原路(Z轴)离开工件,利用主菜单中测量功能,量出所切工件直径,并记下***;
5选择对刀界面“工具/形状”,在指定的刀位后的“X”轴输入“X***”后按下方“测量”按钮,产生刀具的X编程坐标。
最终建立该刀具的编程坐标系在工件右端面的中心点,正Z轴指向尾座,正X轴与Z轴垂直指向刀架。
三、如何编写程序并首次执行:
1、进入机床的“编辑”状态,再点“PROG”程序界面,进入“程式”编程界面;
一、数控车床回参考点的步骤(法那克OI系统):
答:注:使用数控车床前必须先回参考点。2、进入“回原点”状态,选中“X”轴,再点一下“+”,回轴,X轴回原点灯亮;
3、选中“Z”轴,再点一下“+”,回轴,Z轴回原点灯亮;
4、进入“手动”状态,选中“Z”轴,点一个快速按钮,按住“-”方向,使刀架离开尾座靠近卡盘;
- 1、下载文档前请自行甄别文档内容的完整性,平台不提供额外的编辑、内容补充、找答案等附加服务。
- 2、"仅部分预览"的文档,不可在线预览部分如存在完整性等问题,可反馈申请退款(可完整预览的文档不适用该条件!)。
- 3、如文档侵犯您的权益,请联系客服反馈,我们会尽快为您处理(人工客服工作时间:9:00-18:30)。
第一步,判断位置检测器类型:增量式编码器和绝对式编码器。
判断方法:查看系统参数1815第五位APCx的值 0:增量式编码器,
1:绝对式脉冲编码器
注:(当系统指定此轴使用绝对式脉冲编码器时,伺服模块上必须安装电池来记忆参考点)
第二步,设定参考点:A、增量式(1815.5=0):1、手动将机床移动到指定的参考点位置(挡块式的必须使会参考点减速信号(*DEC)由0变1回到原状。
)2、MDI模式将参数写保护打开。
3、1815的第四位APZx,先改成1,再改成0。
4、关机重启,参数写保护恢复。
5、手动回零检查参考点位置是否正确。
B、绝对式(1815.5=1):
1、手动将机床移动到指定的参考点位置。
(挡块式的必须使会参考点减速信号(*DEC)由0变1回到原状。
)
2、MDI模式将参数写保护打开。
3、1815的第四位APZx,先改成0,再改成1。
4、关机重启,参数写保护恢复。
5、手动回零检查参考点位置是否正确。
FANUC 1815号的参数:
一。
增量方式的编码器伺服电机:(机床每次上电都要进行回零的操作)
1. 1815#5设0,使用增量方式的编码器伺服电机;1815#4设0当前位置不是参考点。
2. 关机重启,移动轴到参考点附近(要保证电机至少转一转以上的距离)
3. 选择回零方式,并按轴正向移动,该轴就会找下一个栅格信号,该点即为参考点,然后将1815#5、#4设为1 。
(在加工前需要重新进行对刀。
)
二。
绝对方式的编码器伺服电机:(机床首次调好零点后,不再需要机床每次上电都进行回零的操作)
FANUC 0I MATE TD系统无撞块回零点的设定步骤:分别把X轴,Z轴放大器上的电池安装上。
把参数1815#5设为1 ,无撞块回零点方式有效。
把参数1815#4 设为零。
在手摇方式下分别把X轴,Y轴,Z轴摇到要设定为零点的地方,再把参数1815#4设为1.
把机床下电,再重新上电。
在手摇方式下分别把X轴和Z轴摇回100多MM ,
再把方式选择放到回零方式,分别进行手动回零操作。
回零完成后,相应轴的回零指示灯会亮。
(手动回零操作完后,X和Z轴的回零灯会亮。
表示零点位置设定完毕。
然后设定软限位的值:参数1320号和参数1321号。
在加工前需要重新进行对刀。
)。