QA作业流程模板
QA工作流程

公司QA流程及相关事项:一.开发部分:1.接到客人开发要求,整理客人提供的相关资料,包括图稿,纸版,参考鞋,及客人提供的原材料,样品单等,提供给工厂,请工厂安排试版及报价。
2.在公司相关高层确认工厂的报价后,通知工厂进行正式的开发。
工厂根据试版鞋的问题点做相应改善后,用正确的材料,做正式的开发样品给客人确认。
(要求材料,颜色,印刷加工等都要正确。
)所有的材料请工厂先做色卡(包括里面的补强,泡棉。
都需要做色卡)待确认后再做样品3.接收客人对开发样品的修改点,要求工厂进行调整改善,并重做开发样品另,在工厂追踪样品时,需要带上客人的修改点一点一点地检查直到工厂改善为止;4.一般情况下,客人会对新开发的鞋子做一些销样或者展示样品。
收到客人的消息,及时通知工厂调正确的材料,按客人的资讯做销样或者展示样品。
所有的材料请工厂先做色卡(包括里面的补强,泡棉。
都需要做色卡)待确认后再做样品5.客人如要求做试穿样,须请工厂按客人要求做试穿鞋给客人试穿,试穿鞋不记入订单数量;但是客人传的所有的修改点必须改善6.接到正式量产订单后,根据客人原样或者开发样,销样,以及客人修改点,要求工厂制作正确的确认鞋,并请客人确认签名;按照客人签回的确认鞋签回给工厂的留底确认鞋;同时要求工厂在做正确样品品鞋的同时也一起做确认色卡本,一式两份,工厂留底一份,QA留底一份。
客人签名的确认鞋须拿回公司留底。
请记得:每只确认鞋上面需要将客人来的修改点贴上去同时附上图。
7.要求工厂进行全套试做,全套试做的所有材料材质都必须正确,可同材质不同颜色(与确认鞋相同),一般情况全套试做的鞋子左脚贴底,右脚攀帮不贴底。
(全套试做分为纸版手剪试做和斩刀试做两部分,纸版试做OK后,才能进行斩刀试做!)8.召开全套试做会议,分两部分:首先是纸版手剪试做,要求生产相关单位/开发技术/品质等相关部门都必须参加。
会议主要是请大家提出在试做中发现和产生的问题,并提出相应的解决方案。
QA作业指导书

QA作业指导书一、任务背景随着互联网的快速发展,软件质量的要求越来越高,为了保证软件的稳定性和可靠性,质量保证(Quality Assurance,QA)作业成为了软件开辟过程中不可或者缺的一部份。
本文将为您提供一份QA作业指导书,旨在匡助QA团队成员了解并正确执行QA作业。
二、任务目标本次QA作业的目标是确保软件产品的质量和性能,提高用户体验,减少软件缺陷和故障,增强软件的稳定性和可靠性。
通过QA作业,我们将尽可能发现和解决软件中的问题,确保软件产品的顺利交付。
三、QA作业流程1. 需求分析- 与产品经理和开辟团队合作,了解软件产品的需求和功能。
- 确定测试范围和测试目标,制定测试计划和测试用例。
2. 测试设计- 根据需求分析的结果,编写详细的测试用例,包括输入数据、预期输出和执行步骤。
- 设计测试环境和测试数据,确保测试的可重复性和可靠性。
3. 测试执行- 执行测试用例,记录测试结果和问题。
- 进行功能测试、性能测试、安全测试等各类测试,确保软件的完整性和稳定性。
- 使用自动化测试工具进行部份测试,提高测试效率和覆盖率。
4. 缺陷管理- 对测试过程中发现的缺陷进行记录和分类。
- 与开辟团队合作,确认缺陷的修复和验证。
5. 测试报告- 汇总测试结果和问题,编写测试报告。
- 报告中应包括测试执行情况、缺陷统计、风险评估等内容。
6. 验证和确认- 确认缺陷修复后的软件版本是否符合需求和预期。
- 进行用户验收测试,确保软件产品的质量和功能满足用户需求。
四、QA作业要求1. 严格按照测试计划和测试用例进行测试,确保测试的全面性和准确性。
2. 及时记录和报告测试过程中发现的缺陷,确保问题能够及时解决。
3. 与开辟团队和产品经理保持良好的沟通,及时反馈测试结果和问题。
4. 对测试环境和测试数据进行管理,确保测试的可重复性和可靠性。
5. 熟练掌握测试工具和技术,提高测试效率和质量。
6. 持续学习和提升自己的测试能力,关注行业最新的测试方法和技术。
QA作业指导书

QA作业指导书一、项目背景在软件开发过程中,为了保证软件质量和用户满意度,质量保证(Quality Assurance,QA)是必不可少的一环。
QA作业是指对软件项目进行测试、评估和验证,以确保软件的功能、性能和稳定性符合预期要求。
本文将为您提供一份QA作业指导书,以帮助您进行QA作业的规范和有效性。
二、作业目的本次QA作业的目的是确保软件项目的质量,包括功能的正确性、性能的稳定性、用户体验的满意度等方面。
通过QA作业,可以发现和解决软件项目中的问题,提高软件的可靠性和可用性。
三、作业流程1. 确定测试目标和范围:根据软件项目的需求和设计文档,明确测试的目标和范围,包括功能测试、性能测试、安全性测试等。
2. 制定测试计划:根据测试目标和范围,制定详细的测试计划,包括测试的时间安排、测试的资源需求、测试的方法和策略等。
3. 设计测试用例:根据软件项目的功能和需求,设计详细的测试用例,包括正常情况下的功能测试用例、异常情况下的边界测试用例等。
4. 执行测试用例:按照测试计划和测试用例,执行测试用例,记录测试结果和问题。
5. 分析测试结果:根据测试结果,分析软件项目中存在的问题,包括功能缺陷、性能瓶颈、用户体验不佳等。
6. 提出改进建议:根据测试结果和问题分析,提出改进软件项目的建议和措施,以提高软件的质量和用户满意度。
7. 进行回归测试:在软件项目进行修改和改进后,进行回归测试,验证问题是否得到解决。
8. 编写测试报告:根据测试结果和改进建议,编写详细的测试报告,包括测试的目标、范围、方法、结果和建议等。
四、作业工具在进行QA作业时,可以使用一些专业的软件工具来辅助测试和分析,以提高作业的效率和准确性。
常用的QA工具包括:1. 自动化测试工具:如Selenium、JUnit等,可以自动化执行测试用例,减少人工操作的时间和错误。
2. 性能测试工具:如LoadRunner、JMeter等,可以模拟大量用户并发访问,测试软件的性能和稳定性。
qa工作流程
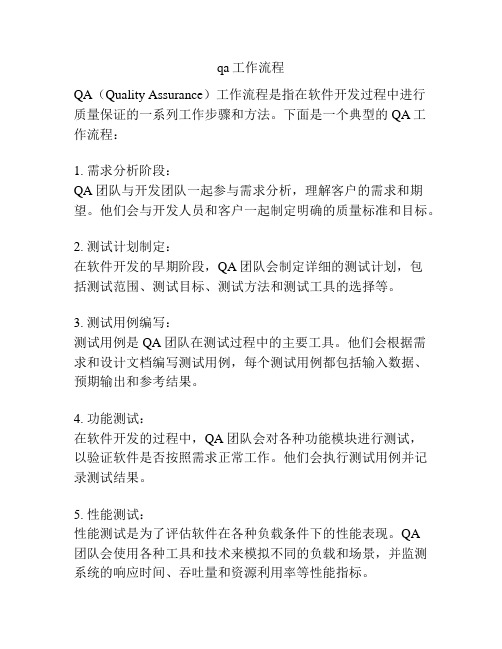
qa工作流程QA(Quality Assurance)工作流程是指在软件开发过程中进行质量保证的一系列工作步骤和方法。
下面是一个典型的QA工作流程:1. 需求分析阶段:QA团队与开发团队一起参与需求分析,理解客户的需求和期望。
他们会与开发人员和客户一起制定明确的质量标准和目标。
2. 测试计划制定:在软件开发的早期阶段,QA团队会制定详细的测试计划,包括测试范围、测试目标、测试方法和测试工具的选择等。
3. 测试用例编写:测试用例是QA团队在测试过程中的主要工具。
他们会根据需求和设计文档编写测试用例,每个测试用例都包括输入数据、预期输出和参考结果。
4. 功能测试:在软件开发的过程中,QA团队会对各种功能模块进行测试,以验证软件是否按照需求正常工作。
他们会执行测试用例并记录测试结果。
5. 性能测试:性能测试是为了评估软件在各种负载条件下的性能表现。
QA团队会使用各种工具和技术来模拟不同的负载和场景,并监测系统的响应时间、吞吐量和资源利用率等性能指标。
6. 安全测试:安全测试是为了评估软件是否具备一定的安全性能,以保护用户的敏感数据和系统的稳定性。
QA团队会使用各种技术和方法来识别和修复潜在的安全漏洞。
7. 压力测试:压力测试是为了评估软件在高负载条件下的稳定性和可靠性。
QA团队会使用各种工具和技术来模拟大量并发用户和数据,以测试系统的极限承载能力。
8. 自动化测试:自动化测试是为了提高测试效率和覆盖率,QA团队会使用自动化测试工具和脚本来执行重复性和繁琐的测试任务。
他们还会编写自动化测试脚本和工具来保证软件的稳定性和可靠性。
9. 缺陷跟踪和管理:QA团队会记录和跟踪所有发现的缺陷,并向开发团队提供详细的缺陷报告。
他们会与开发人员一起讨论和解决缺陷,并跟踪其修复进度。
10. 验收测试:在软件开发的最后阶段,QA团队会进行验收测试,以确保软件满足客户的需求和质量标准。
他们会执行一系列测试用例,并评估软件的功能、性能、安全性和稳定性等方面。
qa的工作流程

qa的工作流程QA的工作流程。
在软件开发中,质量保证(QA)是一个至关重要的环节,它确保了产品的质量和稳定性。
在这篇文档中,我将介绍QA的工作流程,包括测试计划、测试用例设计、执行测试、缺陷管理和报告等步骤。
首先,测试计划是QA工作的第一步。
在这个阶段,QA团队需要与产品经理和开发团队紧密合作,了解产品的功能和需求。
基于这些信息,QA团队制定测试计划,确定测试范围、测试目标和测试资源。
测试计划需要详细描述测试的目的、测试环境、测试工具和测试时间表,以确保测试工作的顺利进行。
接下来,QA团队开始设计测试用例。
测试用例是QA工作的核心,它描述了针对不同功能和场景的测试步骤和预期结果。
在设计测试用例时,QA团队需要考虑到产品的各种使用场景和边界条件,以确保产品的功能和性能能够得到全面的验证。
同时,测试用例还需要具备可重复性和可扩展性,以适应产品的不断迭代和更新。
随后,QA团队执行测试。
在执行测试过程中,QA工程师需要按照测试计划和测试用例,使用各种测试工具和设备对产品进行全面的验证。
他们需要确保产品的功能和性能符合设计要求,并及时发现和记录缺陷。
同时,他们还需要与开发团队紧密合作,确认和修复缺陷,以确保产品的质量和稳定性。
在测试过程中,QA团队需要进行缺陷管理。
他们需要对发现的缺陷进行分类、分级和跟踪,以确保缺陷能够及时得到解决。
同时,他们还需要对缺陷进行分析,找出缺陷的根本原因,并提出改进建议,以提升产品的质量和稳定性。
最后,QA团队需要编写测试报告。
测试报告是QA工作的总结和反馴,它描述了测试的结果、发现的缺陷和改进建议。
测试报告需要清晰、简洁地呈现测试的情况和产品的质量,以便产品经理和开发团队了解产品的测试状况和存在的问题。
总的来说,QA的工作流程包括测试计划、测试用例设计、执行测试、缺陷管理和报告等步骤。
通过这些步骤,QA团队能够全面、系统地验证产品的功能和性能,确保产品的质量和稳定性。
同时,他们还能够及时发现和解决产品中存在的问题,提升产品的用户体验和市场竞争力。
质量控制(QA)工作流程图
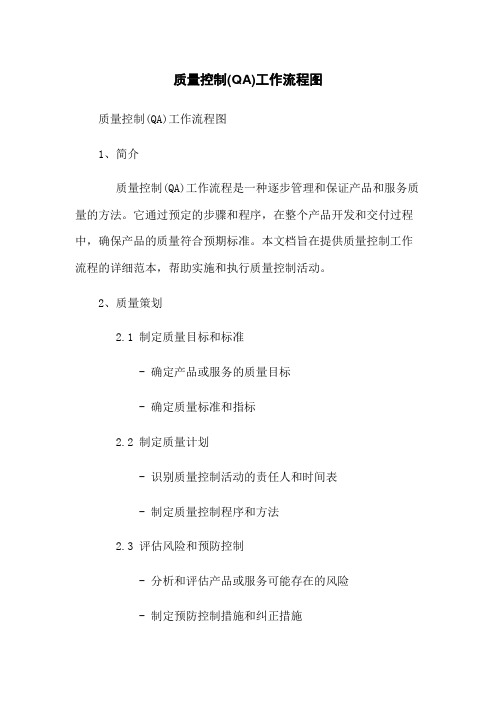
质量控制(QA)工作流程图质量控制(QA)工作流程图1、简介质量控制(QA)工作流程是一种逐步管理和保证产品和服务质量的方法。
它通过预定的步骤和程序,在整个产品开发和交付过程中,确保产品的质量符合预期标准。
本文档旨在提供质量控制工作流程的详细范本,帮助实施和执行质量控制活动。
2、质量策划2.1 制定质量目标和标准- 确定产品或服务的质量目标- 确定质量标准和指标2.2 制定质量计划- 识别质量控制活动的责任人和时间表- 制定质量控制程序和方法2.3 评估风险和预防控制- 分析和评估产品或服务可能存在的风险- 制定预防控制措施和纠正措施3、质量保证3.1 开展质量审核- 进行内部审核,检查质量管理系统的有效性 - 进行外部审核,评估产品或服务的符合性 3.2 实施质量控制计划- 按照质量计划执行各项质量控制活动- 收集和分析质量数据,进行质量改进3.3 管理供应商质量- 评估供应商能力和质量体系- 监督和评估供应商提供的产品或服务质量4、缺陷管理4.1 收集和分析缺陷数据- 建立缺陷管理系统,记录缺陷数据- 分析缺陷数据,找出缺陷的根本原因4.2 实施纠正措施和预防措施- 针对缺陷的根本原因制定纠正措施- 预防类似缺陷再次发生的预防措施4.3 进行缺陷关闭和验证- 确认纠正措施的有效性- 关闭缺陷,并进行验证测试5、文件和记录管理5.1 管理质量相关文件- 确保文件的正确性和及时性- 管理文件的版本控制和变更记录5.2 管理质量相关记录- 确保记录的完整性和准确性- 建立记录的存档和保密措施6、培训和沟通6.1 提供质量培训- 为相关人员提供质量管理和控制的培训- 确保相关人员了解和掌握质量策划和控制方法 6.2 进行质量沟通- 与相关部门和人员进行质量信息的沟通和交流 - 提供质量报告和质量进展更新7、持续改进7.1 分析质量数据- 进行质量数据的统计和分析- 发现潜在问题和改进机会7.2 实施改进措施- 制定改进计划和行动方案- 实施改进措施并进行效果评估7.3 反馈和复审- 根据改进措施的效果进行反馈和复审- 调整和优化质量控制流程附件:2、质量控制记录表3、缺陷管理流程图4、质量培训材料法律名词及注释:1、质量目标和标准:产品或服务的质量要求和期望水平。
QA标准作业流程PPT课件

2021/3/12
19
四、绩效考核部分
• 品质保证人员在月底时,依据生产员工平 时的品质保证表现的累加,对生产员工进 行绩效考核,注意遵守客观、公正、公平 的原则,做出考核表后及时上交生产主管 确认。
2021/3/12
20
感谢您的阅读收藏,谢谢!
2021/3/12
21
• 若有异常,及时调整,一小时检查调整一 次。
• 2、按要求做好检查调整记录。 • 3、不定期检查加热过渡室的温度状况,防
止温度过高。
2021/3/12
13
(五)、制粒:
• 对相关人员的抽查内容:
• 1.应配合品控员找出不同品种别的生产条件。
• 2.制粒前检查物料颜色、气味、细度。如有异常, 及时汇报并协同现场主管、品保进行处理。
• 对打包人员的抽查内容:
• 1.按生产量领取包装袋,标签。对标签进行打印
时,保证生产日期与检验日期一致,打印清晰无 抹痕。
• 2.检查包装、标签、包装物是否一致,对印刷不 清的包装及残缺的标签,不能使用。
• 3.操作员应检查打包秤的工作是否正常,按包装 要求进行设定并对头尾10包连续抽查,做好抽包
2021/3/12
10
• 6.能否对每一阶段待粉碎仓所存原料都有 标记,合理利用粉碎机并入对相应仓位.
• 7.抽查能否及时主动告知制粒人员不同 待压仓存放粉料的料号.
• 8.主控员应监视控制面板的运行情况, 及时处理或协调有关人员处理各种问题.
• 品保员每个月取样测定混合机的混合均匀 度,保证达到差异较小的效果。
• 2、依据《原料到货报告单》流程,司机从营业处 领得五联单后,及时交与品保人员,品保员接单 后 ,依据原料的品种取样进行感官检查,做出能 否暂卸的判断,合格暂卸,不合格退货。填写五 联单,合格的交与原料库管安排卸货。
QA部门验货人员 ( QC ) 作业标准程序书
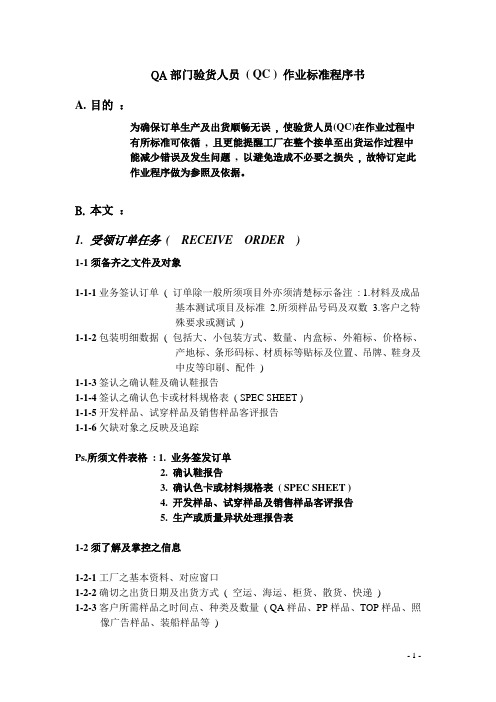
QA部门验货人员( QC ) 作业标准程序书A.目的:为确保订单生产及出货顺畅无误, 使验货人员(QC)在作业过程中有所标准可依循, 且更能提醒工厂在整个接单至出货运作过程中能减少错误及发生问题, 以避免造成不必要之损失, 故特订定此作业程序做为参照及依据。
B.本文:1.受领订单任务( RECEIVE ORDER )1-1须备齐之文件及对象1-1-1业务签认订单( 订单除一般所须项目外亦须清楚标示备注: 1.材料及成品基本测试项目及标准 2.所须样品号码及双数 3.客户之特殊要求或测试)1-1-2包装明细数据( 包括大、小包装方式、数量、内盒标、外箱标、价格标、产地标、条形码标、材质标等贴标及位置、吊牌、鞋身及中皮等印刷、配件)1-1-3签认之确认鞋及确认鞋报告1-1-4签认之确认色卡或材料规格表( SPEC SHEET )1-1-5开发样品、试穿样品及销售样品客评报告1-1-6欠缺对象之反映及追踪Ps.所须文件表格: 1.业务签发订单2. 确认鞋报告3. 确认色卡或材料规格表( SPEC SHEET )4. 开发样品、试穿样品及销售样品客评报告5. 生产或质量异状处理报告表1-2须了解及掌控之信息1-2-1工厂之基本资料、对应窗口1-2-2确切之出货日期及出货方式( 空运、海运、柜货、散货、快递)1-2-3客户所需样品之时间点、种类及数量( QA样品、PP样品、TOP样品、照像广告样品、装船样品等)1-2-4验货之方式、时间及标准( 本公司QC验货、客户QC验货、客户或代表验货、公证单位验货、期中验货、最终验货、包装验货、验货百分比等事项)1-2-5有无特殊或指定供货商( 数据及联系方式)1-2-6有无客户之特殊要求( 材料或成品测试)1-2-7欠缺信息之反映及追踪Ps.所须文件表格: 1. 业务签发订单2. 样品单或E-MAIL3. 测试通知或E-MAIL4. 生产或质量异状处理报告表2.进驻工厂( ENTER INTO FACTORY )2-1须先行核实之数据及文件2-1-1工厂制令与业务原始订单之型体、数量、颜色、SIZE RUN、出货日期等资料是否相符2-1-2核对材料规格表( SPEC SHEET ) 要求与工厂采购订单是否相符2-1-3异常状况反映﹑核实及处理Ps.所须文件表格: 1. 业务原始订单2. 材料规格表( SPEC SHEET )3. 工厂指令表4. 工厂采购单5. 生产或质量异状处理报告表2-2须立即执行及追踪落实之事项2-2-1生产进度( 进度表) 之编排及核实确认2-2-2手剪全套及斩刀试作进度之追踪落实( 含试作报告及报告内容须注意及修改问题点之落实)2-2-3材料进度之追踪( 含材料订单是否已下单给供货商及采购数量是否正确) 2-2-4入库材料之质量、数量查验及测试( 环保测试基础:胶药水不可含苯、五金饰扣不可含镍、猪皮不可含铅、大底喷涂不可含铅、汞、皮面料不可含镉、甲醛、偶氮、五氯酚、六价铬等六大类重金属及毒性毒害物质)2-2-5发外加工物件( 贴合、包跟、组底、三合一、针车、成型) 之进度及质量之查验及讯息反映2-2-6客供材料或指定材料之进度及质量、数量查验( 一般入库材料基本测试包括:面料 1.耐磨擦褪色测试 2.爆破及撕裂强度测试 3.耐黄变测试 4.老化测试, 底料 1.挠折(曲折)测试 2.耐寒测试 3.老化测试, 五金饰物 1.盐水( 抗氧化、褪色) 测试, 包装材料 1. 耐磨擦褪色测试 2.爆破强度测试2-2-7客户特殊要求( 材料或成品测试) 之追踪处理及落实2-2-8异常状况反映及处理Ps.所须文件表格: 1. 工厂生产进度表2. 手剪全套( FULL SIZE ) 试作通知书3. 斩刀( CUTTING TRY ) 试作通知书4. 手剪全套( FULL SIZE )及斩刀( CUTTING TRY )试作报告5. 工厂指令表6. 工厂采购单7. 工厂或供货商材料测试报告( 须送回)8.发外加工进度表9. 认证测试中心测试报告10. 生产或质量异状处理报告表3.进入量产( START PRODUCTION )3-1入库材材料确认3-1-1面﹑内里及副料: 1.一般面、里料可概分为:皮料类、PU及PVC类( 仿皮类)、布料类等三大类别2.须注意颜色与材质是否与确认鞋及确认色卡相match3.抽裁条须加防爆处理4.贴合加工须注意材料方向性及合贴效果5.材料须先经外观检视再依客户须求测试项目进行测试且须合格后始得冲裁6.布类材料须注意每卷颜色之差异性及布头、布尾之色差状况7.材料分批入库特别须注意与先前已入库材料之差异8.入库材料有允收色系时注意务必要求分码配码作业9.尾数及补码材料须特别注意颜色及材质须同量产10. a.耐磨擦褪色测试b.爆破及撕裂强度测试c.耐黄变测试 d.老化测试, 为一般面里材料之基本测试项目3-1-2底料(含跟及中底) : 1.一般跟、底料可概分为:PC跟、ABS跟、PVC跟、HIPS跟、橡胶底、生胶底、TR、TPR、PVC、TPU、PU、EVA、PCU、美耐底、真皮底、皮浆底、竹木大底等2.分段及配码不可错误( 跟、防水台、天皮、半叉)3.三合一及定型中底须视鞋型不同而要求强度4.EV A防水台须注意硬度( 75∘- 80∘) 且须加木桩增加强度‚入库之防水台均须比对楦底版、大底版、侧面版、高度版确认OK后始可准备供应生产5.裁断斩底( CUTTING SOLE ) 须注意斩刀确认及缘边打磨、喷涂之正确性, 模具底( MOLD SOLE )须注意模具确认及首件确认3-1-3五金饰物类:3-1-4包装材料类: 1.一般包材可概分为:外箱、内盒、PE袋、包装纸、贴标、吊牌、干燥剂、结挂绳、撑筷、纸团、工字夹、挂勾、防霉片、结挂配件等3-1-5异常状况反映及处理Ps.所须文件表格:3-2裁断作业3-2-1查验回厂斩刀是否与原始纸版及斩刀试作之斩刀纸版相符3-2-2抽检裁断冲裁材料颜色与材质是否与所签认色卡相符3-2-3抽检裁断之裁片是否配双,有无缺刀、变形3-2-4须注意是否有用错斩刀( 代刀) 或斩错材料( 代用材料) 之情事发生3-2-5须注意是否有裁错号码或漏裁号码之状况3-2-6须注意冲裁时裁刀之裁向( 影响鞋面结帮延伸方向)3-2-7须注意工厂是否有未确认先冲裁( 偷裁) 之情况3-2-8须注意材料贴合与加工方式是否与客户要求及制令相符3-2-9异常状况反映及处理Ps.所须文件表格: 1. 材料规格表( SPEC SHEET )2. 工厂指令表3. 业务原始订单4. 生产或质量异状处理报告表3-3针车作业3-3-1针车首件确认3-3-2生产流程及工序编排确认3-3-3前10双鞋面试攀3-3-4每码抽验3-3-5尾数及补码确认3-3-6异常状况反映及处理Ps.所须文件表格:3-4成型作业3-4-1大货生产前小批量试作3-4-2生产流程、工序及设备确认3-4-3首件( 箱) 成品确认3-4-4停线及区隔处理3-4-5尾数及补码确认3-4-6异常状况反映及处理Ps.所须文件表格:4.验货( INSPECTION ) 4-1生产中抽验4-1-1流水线未封箱成品鞋抽验4-1-2成品仓已封箱成品鞋抽验Ps.所须文件表格:4-2分批验货4-2-1每日量产区隔验货4-2-2重新验货4-2-3开立报告Ps.所须文件表格:4-3满箱验货4-3-14-3-2扩大验货比例4-3-3重新验货4-3-4开立报告Ps.所须文件表格:4-4 客户验货Ps.所须文件表格:4-5公证单位验货Ps.所须文件表格:5.结束订单( FINAL )5-1出货程序及注意事项5-1-1装箱5-1-2装柜(及时照相传回给业务)5-1-3出货5-2出货后结单事项5-2-1文件汇整及送回5-2-2确认鞋及色卡送回Ps.所须文件表格:6.其它( ELSE )6-1材料色卡确认程序6-1-1开发色卡一式三份, 由客户或开发经理确认签认后一份交给客户, 一份转交给工厂, 另一份由公司开发人员保留存档6-1-2确认鞋色卡一式三份, 由客户或开发经理确认签认后一份交给验货员( QC ) 一份转交给工厂, 另一份由公司业务人员保留存档6-1-3大货量产色卡一式五份, 由驻厂QC或QC主管确认签认后一份留给验货员( QC ) 交给工厂三份( 工厂品管、工厂采购、工厂生产单位) , 另一份交由公司业务人员保留存档6-1-4异常状况反映及处理Ps.所须文件表格: 1. 确认色卡或材料规格表( SPEC SHEET )6-2装船样品及QA样品作业程序6-2-1 QA样品6-2-2装船样品Ps.所须文件表格:6-3异状反映及处理程序6-3-1订单及确认数据异常及处理6-3-2生产进度情况异常及处理6-3-3生产质量( 含材料) 情况异常及处理Ps.所须文件表格: 1.生产或质量异状处理报告表6-4 FITTING、手剪全套及斩刀试作要求及注意事项6-4-1 FITTING : 1.须注意不同材质所造成穿着效果不同( 甚至须改不同纸版)2.须注意跟高不同所造成脚前冲之状况不同3.须注意前掌着力点位置所造成穿着之问题4.须注意扣带、松紧带及魔术扣位置、长短所造成穿着之问题5.须注意材料加工方式( 削皮、片皮、贴合材料、上浆上糊等)效果不同所造成穿着之问题6.须注意中底及中皮厚度及柔软度不同所造成穿着之问题7.须注意基本码长度及围度不可有过大差异以免级放后造成生产会产生更大差异8.夹脚凉鞋须特别注意夹脚高及夹脚冲孔位置6-4-2手剪全套: 1.须核对全套纸版级放规格标准是否正确2.不同材质均须纳入全套试作且在全码之中以跳码形式进行3.必须以同量产材质材料进行试作, 不可使用替代材料4.当纸版须进行修改时,须视修改程度及修改部位状况决定跳码或全码重做5.手剪全套是以确认全套纸版为主要目的, 做工问题可于斩刀试作时加以改善6进行手剪全套必须有开发样品及销售样品客评报告和FITTING报告之问题参照及FITTING留底鞋作为参考依据7手剪全套时就必须确认材料加工方式( 削皮、片皮、贴合材料、上浆或上糊等)及效果6-4-3斩刀试作: 1.斩刀试作须设定边距、间距、位置、组合、饰物接合固定、鞋面处理方式、材料质量等标准及做工要求2.进行全套斩刀试作必须有手剪全套报告之问题参照及手剪全套留底鞋作为参考依据3.补充手剪全套未备注之要求重点及客人重点或特殊要求4.须核对全套纸版与斩刀纸版是否相符( 并带回全套斩刀纸版留存)5.如须修改斩刀, 至少须重做大中小码重新确认6.须注意跟、底、五金饰物、LOGO等分段及配码状况7. 斩刀试作须确认全套包装材料正确性( 包括大、小包装方式、数量、贴标、吊牌、印刷、配件)Ps.所须文件表格: 1.手剪全套( FULL SIZE ) 试作通知书2.斩刀( CUTTING TRY ) 试作通知书3.试穿( FITTING ) 报告4.手剪全套( FULL SIZE ) 试作报告5.斩刀( CUTTING TRY ) 试作报告6-5工厂评估及试作、试单程序6-5-1工厂搜寻及初步评估6-5-2评估项目设定6-5-3须备齐填具之文件及数据6-5-4评估报告分析总结及归类6-5-5样品试作6-5-6小张订单试单Ps.所须文件表格:6-6 QA部门工作范畴6-6-1每日工厂生产状况汇总6-6-2每周出货订单汇总更新6-6-3异常状况预判及防范6-6-4生产进度、质量( 含材料) 等各类异常状况处理6-6-5生产技术指导及转移6-6-6出货后资料汇总及转交Ps.所须文件表格:6-7模具作业程序6-7-1模具申请6-7-2模具制作6-7-3模具确认6-7-4生产及请款Ps.所须文件表格:。
QA作业指导书

QA作业指导书一、背景介绍在软件开发过程中,质量保证(Quality Assurance,QA)是非常重要的一环。
QA的目标是确保软件产品的质量,减少缺陷和问题的出现,并提高用户满意度。
为了有效地进行QA工作,需要制定一份详细的QA作业指导书,以确保所有参与者都能清楚地了解任务要求和工作流程。
二、任务目标本次QA作业的目标是对一个电子商务网站进行功能测试和性能测试,以确保网站的正常运行和用户体验。
具体包括以下几个方面:1. 功能测试- 对网站的各个功能模块进行测试,包括登录、注册、商品浏览、购物车、下单等。
- 针对每个功能模块,编写测试用例,包括正常情况下的操作和异常情况下的处理。
- 使用自动化测试工具执行测试用例,并记录测试结果。
- 对测试结果进行分析,发现并报告潜在的缺陷和问题。
2. 性能测试- 使用性能测试工具对网站进行负载测试,模拟多用户同时访问网站的情况。
- 设定不同的负载条件,如同时在线用户数、请求响应时间等。
- 测试网站在不同负载条件下的响应速度和稳定性。
- 分析测试结果,确定网站的性能瓶颈,并提出优化建议。
三、工作流程1. 确定测试范围和测试目标- 与开发团队和产品团队沟通,明确测试的范围和目标。
- 确定需要测试的功能模块和性能指标。
2. 编写测试用例- 针对每个功能模块,编写详细的测试用例,包括输入数据、预期结果和执行步骤。
- 考虑正常情况和异常情况下的测试用例。
3. 执行功能测试- 使用自动化测试工具执行测试用例,记录测试结果。
- 对测试结果进行分析,发现并报告潜在的缺陷和问题。
4. 进行性能测试- 使用性能测试工具设定负载条件,模拟多用户同时访问网站。
- 测试网站在不同负载条件下的响应速度和稳定性。
- 分析测试结果,确定性能瓶颈,并提出优化建议。
5. 编写测试报告- 汇总功能测试和性能测试的结果,编写详细的测试报告。
- 报告中应包括测试的范围、目标、测试用例、执行结果、发现的缺陷和问题等。
QA的工作流程范文

QA的工作流程范文QA(Quality Assurance)是一种质量保证的软件测试工作。
在软件开发过程中,QA是一个非常重要的环节,它帮助确保软件的质量,提高软件的可靠性和稳定性。
以下将介绍QA的工作流程。
1.需求分析:QA从项目开始的第一步就是参与需求分析阶段。
在这个阶段,QA与开发人员一起了解项目的需求,讨论功能和特性,以确定项目的目标和范围。
QA在这个阶段主要的工作是确保需求是明确、准确、可衡量和可追踪的。
他们与开发人员一起评估需求的可行性,并提出任何潜在的问题或疑虑。
2.测试计划制定:在需求分析阶段之后,QA制定测试计划。
测试计划是一个详细的文件,描述了测试的范围、目标、资源、测试方法、测试环境等。
测试计划还包括测试的时间表和时间线,以及测试人员的分工和职责。
3.测试用例设计:在制定完测试计划之后,QA开始设计测试用例。
测试用例是一组详细的步骤,在各种情况下测试软件的功能和特性。
测试用例根据功能和特性进行分类,例如基本功能、边界条件、异常情况等。
QA还可以使用自动化测试工具来设计和执行测试用例。
4.测试环境准备:在进行测试之前,QA需要准备测试环境。
测试环境是一个与生产环境相似的环境,用于测试软件的功能和性能。
测试环境还包括配置管理和测试数据的准备。
5.执行测试:在测试环境准备好后,QA开始执行测试。
测试包括功能测试、性能测试、安全测试等。
功能测试主要是测试软件的功能和特性是否满足需求。
性能测试用于测试软件在不同负载条件下的性能和响应时间。
安全测试用于测试软件的安全性和保密性。
6.缺陷追踪和修复:在执行测试时,QA将记录任何发现的缺陷或错误。
他们将使用缺陷追踪工具来跟踪和管理缺陷。
发现缺陷后,QA与开发人员一起分析、复现和修复缺陷。
7.测试报告和评估:在测试阶段结束时,QA准备测试报告。
测试报告是一个总结和评估测试结果和建议的文档。
报告中包括测试的范围、执行结果、发现的缺陷和建议的改进措施。
QA工作流程图
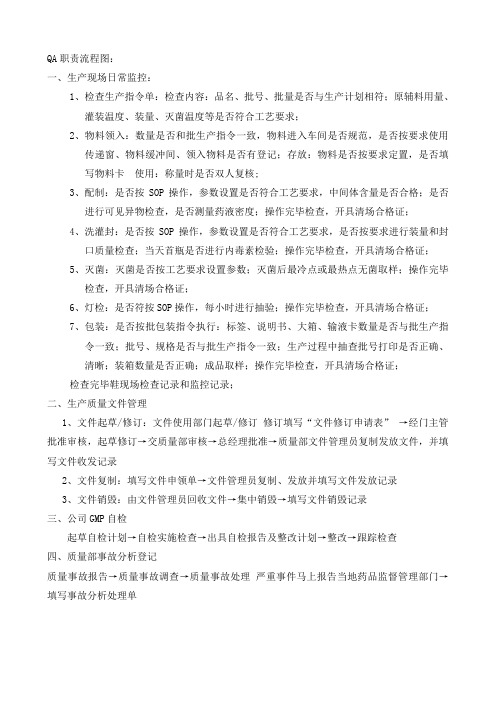
QA职责流程图:一、生产现场日常监控:1、检查生产指令单:检查内容:品名、批号、批量是否与生产计划相符;原辅料用量、灌装温度、装量、灭菌温度等是否符合工艺要求;2、物料领入:数量是否和批生产指令一致,物料进入车间是否规范,是否按要求使用传递窗、物料缓冲间、领入物料是否有登记;存放:物料是否按要求定置,是否填写物料卡使用:称量时是否双人复核;3、配制:是否按SOP操作,参数设置是否符合工艺要求,中间体含量是否合格;是否进行可见异物检查,是否测量药液密度;操作完毕检查,开具清场合格证;4、洗灌封:是否按SOP操作,参数设置是否符合工艺要求,是否按要求进行装量和封口质量检查;当天首瓶是否进行内毒素检验;操作完毕检查,开具清场合格证;5、灭菌:灭菌是否按工艺要求设置参数;灭菌后最冷点或最热点无菌取样;操作完毕检查,开具清场合格证;6、灯检:是否符按SOP操作,每小时进行抽验;操作完毕检查,开具清场合格证;7、包装:是否按批包装指令执行:标签、说明书、大箱、输液卡数量是否与批生产指令一致;批号、规格是否与批生产指令一致;生产过程中抽查批号打印是否正确、清晰;装箱数量是否正确;成品取样;操作完毕检查,开具清场合格证;检查完毕鞋现场检查记录和监控记录;二、生产质量文件管理1、文件起草/修订:文件使用部门起草/修订修订填写“文件修订申请表”→经门主管批准审核,起草修订→交质量部审核→总经理批准→质量部文件管理员复制发放文件,并填写文件收发记录2、文件复制:填写文件申领单→文件管理员复制、发放并填写文件发放记录3、文件销毁:由文件管理员回收文件→集中销毁→填写文件销毁记录三、公司GMP自检起草自检计划→自检实施检查→出具自检报告及整改计划→整改→跟踪检查四、质量部事故分析登记质量事故报告→质量事故调查→质量事故处理严重事件马上报告当地药品监督管理部门→填写事故分析处理单。
QA作业流程模板

QA作业流程模板
QA作业流程
⼀、⽬的:确保客户收到符合要求的产品,防⽌不良品流⼊市场,加强内部沟通,特制定以下内部流程
⼆、范围:所有出货成品包括散件均属之
三、职责:1. 品质部:成品的检验; 2. ⽣产部:产品的⽣产与追踪;
3. 总经办:产品的最终批准;
四、定义:⽆流程图
五、流程程序
签名
2. OK后签收并查找相应的《产品图纸》《检验规
范》《作业指导书》《样板》以及测试⼯具
3. 检查验货单订单号码、数量、箱数、唛头是否
与资料相符,不符时经组长确认与⽣产部门进⾏
确认返⼯
4. 相符后,开始依《检验规范》抽样检验
5. 检验合格后,按箱数填写PASS标签,并贴于外
箱左上⾓,加盖<按客户要求>QA PASS章,并填
写《QA检验报告》
6. 检验NG时,填写《QA检验报告》之NG内容
交品质主管/经理转⽣产主管/经理确认返⼯
7. 返⼯OK后,QA按程序重新抽检,以确认效果
⽕⽜成品检验规范
编
马达成品检验规范
变压器成品检验规范
包装成品检验规范
编号:WI-QC-A06
⽼化⾼低温试验作业指导书
产品落地试验作业指导书
震动试验作业指导书。
QA作业程序

文件名称 QA 作业程序书
****有限公司
文件编号 QP80-009
版本
D
页次
3/3
完成情况,并准备好检测仪器. 6.7.2 验货过程中,出现异常情形(如对某一个品质问题存在争议,验货标准及项目不同时
等),QA 人员需及时通知部门主管,以便与客户验货员及时沟通,取得一致. 6.7.3 验货结束后,QA 人员需把验货客户验货报告交部门主管签名确认,并将验货结果书面通
线路,制作工艺及外观进行确认;确认无问题后,填好“样品”标贴, 同时将检测结 果及建议记录在“首五件检验报告”上。RoHS 产品需用 RXF 仪器进行检测。 6.2.3 生产样品经主管审核后,交制造部生产班组,作为生产样品使用。 6.3 成品入库检验: 6.3.1QA 人员接到制造部的“成品入库验收单”后(如附件一),首先核对 QA 序时抽检记 录表,制造通知单及 BOM 等相关资料,再根据抽样计划及成品检验规范实施检验; 对于随线包装而未经 QA 序时抽检的机种,抽样数量将提高一个等级进行检验. 6.3.2 根据检验的结果,填写“QA 检验报告”(如附件二),交主管审核,并送经理室核准。 6.3.3 成品检验合格后,QA 人员需在每个外箱侧唛加盖“QA PASS 章”(红色)(如附件 三),并把检验结果填写在“成品入库验收单”上,交制造部物料员。 6.3.4 成品检验不合格则按“MRB 作业程序书”作业。 6.4 成品储存检验: 6.4.1 QA 人员接到资材的复检信息后,根据抽样计划及成品检验规范实施抽样检验。RoHS 产品需用 RXF 仪器进行检测。 6.4.2 根据检验的结果填写好“QA 检验报告”,并将检验结果反馈给资材部与生管部。 6.4.3 成品储存检验不合格则按“不合格品管制程序书”作业。 6.5 样品检验: 6.5.1 接到制造部制作的样品及“成品入库验收单”后,根据样品制造通知单,BOM 及成 品检验规范,对样品实施全检。RoHS 产品需用 RXF 仪器进行检测。 6.5.2 根据检验的结果,填写好“公司样品检验报告”(如附件五)。并把检验结果填写在“成 品入库验收单”上,交制造部物料员。 6.5.3 样品检验不合格时则按“不合格品管制程序书”作业。 6.6 客户抱怨处理: 6.6.1 客户抱怨的处理按“客户抱怨处理程序书”办理。 6.6.2 接到生管部的客户抱怨处理结果,QA 人员需填写好“客户抱怨登记表”(附件四)。 必要时提出修改相应的作业规范,防止问题再发生。 6.7 客户验货: 6.7.1 接到生管部客户验货通知单后,QA 人员需事先检查验货产品品质状况及了解产品的
QA工作流程及职责(推荐)

QA工作流程及职责(推荐)第一篇:QA工作流程及职责(推荐)品质部经理工作职责公司的品质部、技术部、设计部是公司综合实力集中的体现部门。
品质部、技术部、设计部的经理是公司质量的负责人,是生产加工队伍的先行官,是企业质量、技术、设计的管理者,所以经理人在完成产品图纸设计的同时,还需要同步完成产品设计说明书,也可以称:制作加工说明书(清单)。
那么,在确保设计、绘图和质量管理等工作的同时,还需制定和贯彻实施质量方针、质量目标和质量标准的监控工作,从而实现产品和服务质量的持续改进。
所以品质部经理应该根据具以下条款来做好本职工作:一对公司现行质量管理体系进行审核,评估,构建与企业相符的质量管理体系并持续改进:1、建立组织内部协调一致的质量管理目标;2、重视并做好图样、说明及质量的审核,充分利用质量管理体系这个有效的管理手段,促进内部质量体系标准的持续发展;3、建立相应的图样清单程序,制定计划,实施质量管理体系的工作内容;4、确保质量管理体系的工作和持续改进工作进程;5、定期向总经理汇报质量管理体系的业绩,包括改进的需求,以事实为依据,确保企业产品质量的持续改进,使之与客户要求相适应;二内部审核:1、拟定内部质量管理体系审核报告以供总经理批准;2、协助总经理定期召开管理评审会议;3、全面负责内部质量管理体系的审核工作;4、担任审核组长并选定审核员,并制定年度内审计划、每次的审核实施计划和内部质量管理体系审核报告;5、指导编写《年度内审计划》并负责组织人员实现标准的工作.6、组织、协调内审活动的开展;三实现质量计划目标:1.审检生产部门、仓储部门产出收入的质量;2.负责对两个部门的质量策划和实施情况进行监督检查;3.协助生产部门负责人制定相关的质量策划及编制、实施相应的质量计划;四处理好与顾客有关的质量问题:1、识别顾客的需求与期望,组织有关部门对产品需求进行评审,并负责与顾客进行质量方面的沟通;2、评审对新产品质量要求的检测;3、带领技术部评审新产品的设计开发;4、协助生产部评审产品的生产能力及交货日期的跟踪;5、协助采购部负责评审所需物料采购的合格率;6、审查.制图.负责产品要求图样的制作的准确性;五质量标准制定和实施:1、在质量要求方面一定要督导技术部在设计、开发产品、协调、实施、验证、评审、设计、开发的更改,确认等符合质量管理体系的工作;2、为公司生产项目提供建议试产报告、提供质量方面的参考意见;3、协助采购部做好所需物料、采购质量的检查工作;4、协助销售部进行质量方法调研或分析市场信息及新产品动向;5、负责新产品或新原辅材料的试验和检验;6、协助生产部负责新产品的加工试制和生产;7、收集行业质量技术,制定适宜的内控质量标准;六生产和服务动作的质量监控:1、在质量控制方面指导生产部进行生产和过程控制,生产设施的维护保养,编制必要的质量作业指导书,负责产品的防护;2、协助技术部编制相关的完善质量管理的技术规程;3、在质量方面协助生产部对《生产计划》的审检;4、协助行政部对实现产品质量所需的工作环境进行控制;5、负责进行产品质量验证和标识及可追溯性控制;6、协助销售部在质量方面的售后服务工作;七测量和监控装置管理:1、负责对测量、监控设备的校准;根据需要编制内部校准规程;2、负责对偏离校准状态的测量、监控设备的追踪处理;3、负责对测量和监控设备操作人员的培训、考核;八不合格品控制:1、负责对不合格品的识别,并跟踪不合格品的处理结果;2、协助生产部门对不合格品做处理决定并做好采取纠正措施;九数据分析和信息提供:1、协调公司对内、对外相关数据的传递分析、处理;2、指导品质部对相关的数据收集、传递、交流并提供必要的信息;3、协调各部部门统计技术的具体选择与应用;十持续改进:1、负责对质量检验、产品持续改进的策划,当出现存在的或潜在的质量问题时提出相应的纠正和预防措施,并跟踪验证实施效果;2、指导行政部在出现环境问题时发出相应的纠正和预防措施及处理意见,并跟踪验证实施效果;3、协调各部门实施相应的改进、纠正和预防措施的实施;4、负责监督、协调改进、纠正和预防措施的实施;5、协助营销部有效地处理顾客质量方面的意见;十一质量成本控制:用质量管理体系的有效性,对质量成本进行统计、核算、分析、报告和控制,从而找到降低成本的途径,进而提高企业的经济效益。
QA工作流程图

Hale Waihona Puke QA每箱抽检1台功 能及附件
生技/工 程确认
改善后再生产 或要求停产
完工入库出 货
◆注1、计划部PC员根据当日计划制定《工单备料通知单》给QC组,QA组员根据《工单备料通知单》依据BOM核对生产线上每一个 物料的正确性,再做5台首件样机确认并分别给生技(工程师或技术员)、确认;若出现NG 半成品时由QA组员则开制程异常通知 单给生技分析并反馈给相关部门改善或要求停产;若出现NG成品时则开QA组员开出QC退货报告给生技分析并反馈给相关部门改善 或要求停产
每一箱机头抽 检5%功能全测
接工程组
接工程组检验项 目要求 手机成品检验规 范
QA工作流程图
接计划部工单备 料通知单
根据授控BOM对生产 线每个工位的物料
制程异常通 知单
生技/
反馈设计部 改善或要求
反馈给仓库 改善或要求
做五台包括附件 完整的整机首件
生技/工 程确认
改善后再生产或 要求停产
允许量产 生产线送检
QA工作流程

QA工作流程摘要本文档旨在介绍QA(质量保证)工作流程,帮助团队成员了解QA工作的步骤和重要性。
我们将详细阐述QA流程的主要阶段,并强调每个阶段的重点和注意事项。
背景在软件开发过程中,质量保证(QA)是一个至关重要的环节。
果断迭代、增强产品质量,持续提升用户满意度,都需要一个良好的QA工作流程。
一个完善的QA流程不仅能帮助我们尽早发现和解决潜在的问题,还能提高产品的稳定性和可靠性。
QA工作流程概述QA工作流程通常包括以下几个主要阶段:1. 需求分析和评审阶段- 审查项目需求,确保需求明确和具体- 确定可测量和可验证的需求指标- 与团队成员沟通,并讨论QA工作的相关问题2. 测试计划和用例编写阶段- 制定详细的测试计划,包括测试范围、测试目标和时间计划等- 编写测试用例,覆盖各个功能模块和常见用户操作- 确保测试用例的有效性和可执行性3. 测试环境搭建和配置- 搭建适合测试的环境,包括硬件设备和软件工具的准备- 配置测试环境,确保测试环境的稳定和一致4. 功能测试阶段- 根据测试计划和用例进行功能测试- 在不同的测试环境中执行测试用例,检查软件的功能是否符合需求- 记录和报告发现的缺陷,并跟踪解决进度5. 性能和稳定性测试阶段- 进行性能测试,验证软件在不同负载下的表现- 进行稳定性测试,模拟大量用户同时使用软件的情况- 收集和分析测试结果,并提出优化建议6. 用户验收测试阶段- 邀请用户参与测试,检查软件是否满足用户需求和期望- 收集用户反馈和建议,以完善软件的用户体验7. 缺陷修复和验证阶段- 跟进缺陷修复进度,确保修复的正确性和有效性- 验证缺陷修复,重测相关功能和场景- 确认修复后的软件符合预期要求8. 发布和部署阶段- 完成所有测试工作,准备发布软件- 协调开发团队和部署团队的工作,确保顺利上线QA工作流程最佳实践为了提高QA工作的效率和质量,以下是一些最佳实践建议:- 提早介入:QA团队应当尽早加入项目,并参与需求、设计和开发的过程中,以避免后期的返工和不必要的麻烦。
QA作业流程模板

QA 作业流程一、目的:保证客户收到切合要求的产品,防备不良品流入市场,增强内部交流,特拟订以下内部流程二、范围:全部出货成品包含散件均属之三、职责: 1. 质量部:成品的检验 ; 2. 生产部:产品的生产与追踪 ;3. 总经办:产品的最后同意 ;四、定义:无流程图五、流程程序1. 接到生产部发出《验货通知单》查对有无送检单LQC署名查对确认2. OK 后签收并查找相应的《产品图纸》《检验规返工、返修范》《作业指导书》《样板》以及测试工具签单3.检检验货单订单号码、数目、箱数、唛头能否生产主管 /与资料符合 ,不符时经组长确认与生产部门进行检验经理确认确认返工4. 符合后 ,开始依《检验规范》抽样检验填写报表5. 检验合格后 ,按箱数填写 PASS标签 ,并贴于外OK NG主管 /经理确认箱左上角 ,加盖 <按客户要求 >QA PASS 章,并填填/盖 PASS 章OK写《 QA 检验报告》6. 检验 NG 时,填写《 QA 检验报告》之 NG 内容入库出货交质量主管 /经理转生产主管 /经理确认返工7.返工 OK 后,QA 按程序从头抽检 ,以确认成效火牛成品检验规范编号: WI-QC-A01 项检验方法缺点分类判断基准CRI MAJ MIN目及工具0 0.25 1.51.外观批锋刮手、污渍、损坏、划伤、杂色且30cm 外察看显然目视V2.外观、划伤、污渍、杂色且30cm 外察看不显然目视V3.超音波熔接时面壳有压痕(或发亮), 30cm 察看不显然目视V4.外观刻字,印字不清楚与要求不符目视V5.超音波熔接空隙> 0.5mm 塞规V6.伤针露铜、掉镀层,端子发黑、氧化目视V外7.漏贴铭牌或贴错铭牌;目视V8.漏贴螺丝塞、胶垫目视V9.SR 充胶、伤(烂)线、严重缩水、变形等目视V10.打端子飞铜线,端子变形目视V11.螺丝滑牙、氧化、生锈试打V观12.上、底壳装置错位 >0.3mm 塞规V V13.上、下盖颜色不一致, 30cm 外察看显然V目视14.端子松动零落目视V15.用错物料目视V16.产品内有异物轻摇火牛V V17.线材变形严重影响外观目视V规 1.线材长度偏短> 2% 卷尺V格尺 2.扎线尺寸偏差> 3% 卷尺V 寸 3.PIN 针长度 /距离偏差> 5% 卡尺V1.高压 1000V 测试未经过或达不到客人要求高压仪V功 2.低压 25± 5V 未经过测架V能 3 功能短路、开路、 INT 测架V4.按掣不灵巧,手感不良对样手试V拉1.火牛插针拉力 <15kg 吊重机架V力拉力计2.火牛线位与电线之间的拉力<12kg 吊重机架V吊拉力计重3.产品漏水不防水专用防水测V 试架防水4.参照《老化高低温试验作业指导书》不符要求恒温箱V 老化备注S-2 抽样S-2 抽样PCB 成品检验规范号:WI-QC-A02 项判断基准目1.产品错插、漏插部件2.PCB 板损坏、划伤严重影响外观3.PCB 板稍微损坏、划伤4.电子元件未插到位,插件倾斜>1mm ,影响其余装置及外观5.PCB 型号、线路与“产品图纸”要求不符6.产品出现极性元件极性插反7.PCB 板焊锡面起铜皮、虚焊、包脚、假焊、锡点氧化、发黑等现外象8.PCB 板焊面沙眼、冷焊、锡点不圆滑9.其余部件部位粘锡影响装置、外观10.元件脚高出锡面>2.5mm ,部件脚没有修剪洁净11.PCB 产品表面批峰及锡刺易伤手观 12.PCB 出现绿油不良,稍微影响外观13.SMT 贴片部件未贴到位,倾斜14.PCB 板丝印漏、地点不正确,影响插件15.PCB 板焊锡面连锡影响导通16.电子元件损坏但不影响功能17.电子元件用错18.PCB 板颜色不一致19.PCB 板表面污渍尺 1.尺寸规格与图纸不符,影响装置编检验方法缺点分类CRI MAJ MIN备注及工具0 0.1 1.5目视V目视V目视V目视V目视V目视V目视V V目视V目视V目视 /卡尺V V目视V目视V目视V目视V目视V目视V目视V目视V目视V V卡尺V寸功2.插件高度与图纸不符1.功能测试与资料要求不符卡尺V V机架V能 2.部件开路、短路3.电压与工程资料要求不符老参照《老化高低温试验指导书》不符要求化机架V 机架V 恒温箱V遥控器成品检验规范项判断基准检验方法目及工具1.外观损坏、批锋刮手、划伤、污渍、杂色且30cm 察看显然目视2.外观、划伤、污渍、杂色且30cm 察看不显然目视3.组装冲压时面壳有伤痕,30cm 察看不显然目视4.电线印字模糊不清且与要求不符目视5.面盖贴键、按键丝印模糊印错、漏印目视6.外壳缩水、变形影响装置和外观目视外7.面盖贴键贴歪、按键装错地点目视8.线材变形严重影响外观目视9.PIN 头伤针露铜、掉镀层、氧化、发黑目视10.漏贴铭牌或贴错铭牌及漏装置件目视11.SR 充胶、伤(烂)线、严重缩水、变形目视观12.螺丝滑牙、打花、打不到位、螺丝生锈、氧化目视试打13.上底壳装置错位ф >0.3mm 目视卡尺14.装置空隙ф>0.5mm 塞规15.用错物料目视16.上、底壳颜色偏差, 30cm 察看显然目视对样17.产品内有异物轻摇产品18.贴键、按键不灵巧,手感不良手按对样规 1.长度偏短 >2% 卷尺格 2.扎线尺寸偏差 >3% 卷尺尺 3.PIN 针长度 /距离偏差 >5% 卡尺寸4.面盖贴键尺寸偏差 >1% 卡尺投影仪功1.开路、短路、插头 INT 机架2.功能测试与资料要求不符机架能3.电压与要求不符机架拉1.冲压之产品 SR 扣压拉力 <5kg 吊重机架力拉力计吊重机架吊 2.打螺丝之产品 SR 扣压拉力 <12kg 拉力计重老 3.参照《老化高低温试验作业指导书》不符要求恒温箱化防水测试防 4.防水套破碎、未装到位、漏打硅胶或未打到位,致使漏水仪器水编号 :WI-QC-A03缺点分类CRI MAJ MIN备注00.65 2.5VVV VVVVVVVVVVVVVVV VVVVVVVVVVVV按客户V要求进行试验马完成品检验规范项判断基准目1.外壳缩水、变形影响装置、批锋刮手2.外壳损坏、杂色、胶花、污渍30cm 察看显然3.外壳损坏、胶花、污渍仅影响外观,30cm 外察看不显然4.螺丝打花、滑牙、打不到位外 5.缺胶严重影响外观6.前后壳装置错位> 0.3mm7.啤头伤线、充胶、严重缩水观8.前后壳装置空隙>0.5mm9.漏贴或贴错铭牌及漏装置件10.2PIN 针电镀不良、伤针露铜、掉镀层、发黑、氧化11.用错物料12.产品内有异物声响规1.针长偏短> 3%格尺寸2.总长扎线尺寸偏短> 3%1.开路、短路、 INT功 2.启动不正常,有卡死现象3.工作噪声大、冒烟及异味能4.工作电压> 24V ± 25.工作电流> 150MA老参照《老化高低温试验作业指导书》不符要求化编号 :WI-QC-A04缺点分类检验方法CRI MAJ MIN备注及工具0 0.65 2.5目视VV目视V目视试打V目视V塞规卡尺V目视V塞规V目视V目视V目视V轻摇外壳V卡尺V卷尺钢尺V机架V机架V样板V 对样机架V机架V恒温箱V变压器成品检验规范编号: WI-QC-A05项目判断基准检验方法及工具1、引线颜色与要求不符目视2、引线破皮 (露铜丝 ) 目视3、端子 (PIN 针 )发黑、氧化目视4、端子( PIN 针)松动、零落目视外5、边沿批锋大于 0.1mm 目视6、外观污渍、杂色、划伤30mm 内不显然目视7、产品型号表记与要求不符目视8、贴纸地点不正确、打折、撕破目视观9、丝印不请、残破不行辩认目视10、硅钢片穿出铁架 0.3mm 目视11、铁架由镀层超层、零落目视12、烤漆后表面皱皮、脏物、漆瘤(大于 2X3mm ,高度小于 1mm),目视13、油漆自动脱漆、粘手目视1、引线长度与要求偏差大于 2 mm 钢尺规格2、引线间距与要求偏差大于 3 mm 钢尺尺3、变压器的整体尺寸与要求偏差大于 3 mm,但不影响实质装寸钢尺、卡尺配1、线圈电阻不符实质要求万用表2、空载电流高出规定最大值综合测试仪功3、空载消耗高出规定最大值能综合测试仪4、空载电压、负载电压偏差大于±5% 综合测试仪5、高压测试示经过、达不到客户要求高压测试仪缺点分类CRI MAJ MIN备注0 0.25 1.5VVVVVVVVVVVVVVVVVVVVV包装成品检验规范项判断基准检验方法目及工具1.包装箱损坏> 10 mm 目视2.包装箱规格、箱唛内容与资料要求不符目视3.包装纸箱坑数不符目视4.包装箱及胶袋无环保标记目视外5.箱唛印字内容模糊不清,难以辨识或易造成误会目视6.包装方法与要求不符目视7.产品堆放凌乱,不齐整目视8.油墨污渍但不影响整体外观目视9.箱顶、箱底封箱后空隙 >10mm 钢尺观10.整批纸箱颜色不一目视11.超出 7 英寸胶袋,气泡袋未打孔目视12.打带封装带颜色、松紧不一目视试《包装箱落地摔产品破碎、破坏、功能不良试验指导书》编号 :WI-QC-A06缺点分类CRI MAJ MIN备注00.65 2.5VVVVVVVVVV VV VVVV作业名称:老化高低温试验文件编号: WI –QC –A07版次/订正:A2一、试验目的:保证产品在不一样的环境天气下能正常使用工作,不会因环境天气的不一样而影响产品正常使用工作造成质量异样。
QA工作流程

试);
6.工艺难点评审,督促研管课进行工艺评审, 结合ES设备、质量水准识别加工难度工件,提 前策划合适的工艺方法(邀请研发工程师参 加)
7、输出功能样点检问题汇总表,召集相关人 员检讨,形成记录报批。
1、制定模具样阶段质量控制计划,根据实际 <<模具样阶段质量控制计划
需要是否成立质量控制团队
>>
2、根据项目提供的客装部位信息,确认工艺 (尤其关注正面外观工艺要求)及检具规划;
四
产 阶 段
5、试生产点检问题改善对策评价,确认并结 案,改善不彻底的课题列入量产遗留问题跟踪
5、根据需要是否抽样做包装验证。试生产包 装更改项目的工艺、包装确认,如有变动需抽 样测试,原则上量产分阶段QA不抽样测试;
6、组织出货评审。准备好各阶段要求输出的 相关评审资料和测试报告、客人样机(如有)
《XX产品XX部件质量控制要 求》;
试 生
5、客装部位需安排非专业人员组装评价(需 专业人员组装的产品除外);
《非专业人员组装评价表》
三
产
阶
《包装强度跌落测试报告》
段 6、落实并查核各实验项目,模具样阶段强度
《耐久测试报告》
结构件有作更改的均需重新测试验证;
《关键部件耐久测试报告》《
短时零部件人工测试报告》
7、包装确认和验证,包装预防式查检表查检 包装防护的合理性,包装实验FQ、国内市场 按3A、其他客户按2D,测试样品最少2SETS, 注意有保护罩类产品低温测试)
《包装预防式查检表》
8、汇总试生产点检问题,召集相关人员检 讨,形成记录报批;
《试生产质量问题汇总》
9、大单重要产品编制PQC、制造培训资料并 培训,重点关注关键工序、相似工件特征区分
- 1、下载文档前请自行甄别文档内容的完整性,平台不提供额外的编辑、内容补充、找答案等附加服务。
- 2、"仅部分预览"的文档,不可在线预览部分如存在完整性等问题,可反馈申请退款(可完整预览的文档不适用该条件!)。
- 3、如文档侵犯您的权益,请联系客服反馈,我们会尽快为您处理(人工客服工作时间:9:00-18:30)。
QA作业流程
一、目的:确保客户收到符合要求的产品,防止不良品流入市场,加强内部沟通,特制定以下内部
流程
二、范围:所有出货成品包括散件均属之
三、职责:1. 品质部:成品的检验; 2. 生产部:产品的生产与追踪;
3. 总经办:产品的最终批准;
四、定义:无流程图
五、流程程序
签名
2. OK后签收并查找相应的《产品图纸》《检验规
范》《作业指导书》《样板》以及测试工具
3. 检查验货单订单号码、数量、箱数、唛头是否
与资料相符,不符时经组长确认与生产部门进行
确认返工
4. 相符后,开始依《检验规范》抽样检验
5. 检验合格后,按箱数填写PASS标签,并贴于外
箱左上角,加盖<按客户要求>QA PASS章,并填
写《QA检验报告》
6. 检验NG时,填写《QA检验报告》之NG内容
交品质主管/经理转生产主管/经理确认返工
7. 返工OK后,QA按程序重新抽检,以确认效果
火牛成品检验规范
编
马达成品检验规范
变压器成品检验规范
包装成品检验规范
编号:WI-QC-A06
老化高低温试验作业指导书
产品落地试验作业指导书
震动试验作业指导书。