8连铸原理
连铸原理与工艺
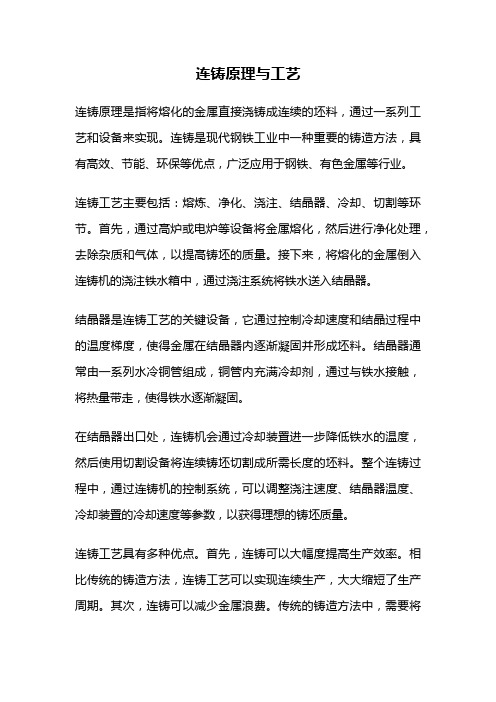
连铸原理与工艺连铸原理是指将熔化的金属直接浇铸成连续的坯料,通过一系列工艺和设备来实现。
连铸是现代钢铁工业中一种重要的铸造方法,具有高效、节能、环保等优点,广泛应用于钢铁、有色金属等行业。
连铸工艺主要包括:熔炼、净化、浇注、结晶器、冷却、切割等环节。
首先,通过高炉或电炉等设备将金属熔化,然后进行净化处理,去除杂质和气体,以提高铸坯的质量。
接下来,将熔化的金属倒入连铸机的浇注铁水箱中,通过浇注系统将铁水送入结晶器。
结晶器是连铸工艺的关键设备,它通过控制冷却速度和结晶过程中的温度梯度,使得金属在结晶器内逐渐凝固并形成坯料。
结晶器通常由一系列水冷铜管组成,铜管内充满冷却剂,通过与铁水接触,将热量带走,使得铁水逐渐凝固。
在结晶器出口处,连铸机会通过冷却装置进一步降低铁水的温度,然后使用切割设备将连续铸坯切割成所需长度的坯料。
整个连铸过程中,通过连铸机的控制系统,可以调整浇注速度、结晶器温度、冷却装置的冷却速度等参数,以获得理想的铸坯质量。
连铸工艺具有多种优点。
首先,连铸可以大幅度提高生产效率。
相比传统的铸造方法,连铸工艺可以实现连续生产,大大缩短了生产周期。
其次,连铸可以减少金属浪费。
传统的铸造方法中,需要将金属熔化后倒入铸型中,过程中会有一定的浪费。
而连铸工艺中,可以直接将熔融金属浇注成坯料,减少了金属的浪费。
此外,连铸还可以提高产品质量。
连铸的结晶过程中,金属凝固速度较快,晶粒细小,可以获得更均匀、致密的铸坯。
最后,连铸工艺对环境友好。
相比传统的铸造方法,连铸工艺中不需要使用砂型和砂芯,减少了对环境的污染。
然而,连铸工艺也存在一些挑战和问题。
首先,连铸过程中会产生较高的温度和压力,对设备和工艺的要求较高。
此外,连铸中还容易产生缺陷,如气孔、夹杂等,需要通过净化和控制工艺参数来解决。
另外,连铸工艺对结晶器的要求较高,结晶器的结构和材料需要经过精心设计和选择,以保证连续铸造的稳定性和质量。
连铸原理与工艺是一种高效、节能、环保的铸造方法,通过熔炼、净化、浇注、结晶器、冷却和切割等环节,将熔化的金属直接浇铸成连续的坯料。
炼钢连铸的作用原理

炼钢连铸的作用原理
炼钢连铸是一种将炼钢和连铸两个工序紧密结合的工艺,其作用原理主要包括以下几个方面:
1. 高效炼钢:连铸炉能够直接从高炉或转炉中接收炼钢过程中的熔化钢液,减少了冷却、搅拌、加热等炼钢工序,有效提高了炼钢的效率和产能。
2. 清洁炼钢:连铸炉内设有多级渣氧复合吹炼设备,可以将钢液中的氧化物、杂质和非金属夹杂物去除,减少了钢液中的气体含量,提高了钢的纯净度。
3. 连续铸造:采用连续浇铸的方式,可以实现钢水的连续供应,并通过连铸机组直接铸造出连续长度的钢坯,提高了炼钢连铸的整体效率和连续性。
4. 精确控制:连铸炉设有多种传感器和自动控制系统,可以对钢水温度、成份、测量等进行实时监测和调整,实现精确控制和自动化操作,提高了产品质量的稳定性。
总之,炼钢连铸工艺通过高效炼钢、清洁炼钢、连续铸造和精确控制等方式,将炼钢和连铸工序有机结合起来,实现了高效、低成本、高质量的钢铁生产。
连铸的原理

连铸的原理
连铸是一种先进的铸造工艺,它通过在同一设备上连续进行浇铸和凝固,实现了铸坯的一次成型,大大提高了生产效率和产品质量。
连铸的原理主要包括连续浇铸、连续凝固和连续切割三个方面。
首先,连续浇铸是指在连铸设备上通过连续浇注熔融金属,使金属液不间断地流入结晶器中。
这样可以避免浇注过程中的温度变化和氧化,保证了金属液的纯净度和温度稳定性。
同时,连续浇铸还可以减少浇注过程中的气体夹杂和金属液的氧化,提高了产品的内部质量。
其次,连续凝固是指在结晶器中,熔融金属通过连续往复的凝固过程,逐渐形成固态铸坯。
在这个过程中,结晶器内部的冷却系统不断地将热量带走,使金属液逐渐凝固成固态金属。
通过控制结晶器的温度和冷却速度,可以实现对铸坯组织和性能的精确控制,从而获得更高质量的产品。
最后,连续切割是指在连铸设备的出口处,通过连续的切割装置将凝固成型的铸坯切割成所需长度的产品。
这样可以避免传统浇铸中的冷却等待时间,提高了生产效率。
同时,连续切割还可以减少铸坯表面的氧化和变形,保证了产品的表面质量和尺寸精度。
总的来说,连铸的原理是通过连续浇铸、连续凝固和连续切割,实现了铸坯的一次成型,大大提高了生产效率和产品质量。
这种先进的铸造工艺在现代工业生产中得到了广泛应用,为各种金属制品的生产提供了可靠的技术保障。
连铸技术的基本原理
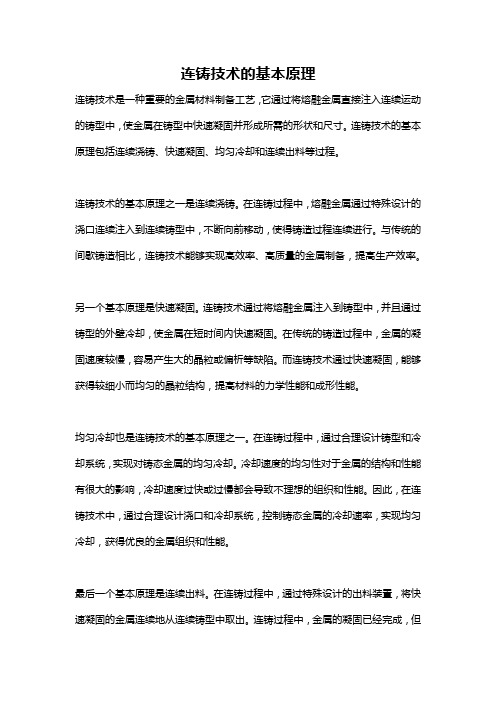
连铸技术的基本原理连铸技术是一种重要的金属材料制备工艺,它通过将熔融金属直接注入连续运动的铸型中,使金属在铸型中快速凝固并形成所需的形状和尺寸。
连铸技术的基本原理包括连续浇铸、快速凝固、均匀冷却和连续出料等过程。
连铸技术的基本原理之一是连续浇铸。
在连铸过程中,熔融金属通过特殊设计的浇口连续注入到连续铸型中,不断向前移动,使得铸造过程连续进行。
与传统的间歇铸造相比,连铸技术能够实现高效率、高质量的金属制备,提高生产效率。
另一个基本原理是快速凝固。
连铸技术通过将熔融金属注入到铸型中,并且通过铸型的外壁冷却,使金属在短时间内快速凝固。
在传统的铸造过程中,金属的凝固速度较慢,容易产生大的晶粒或偏析等缺陷。
而连铸技术通过快速凝固,能够获得较细小而均匀的晶粒结构,提高材料的力学性能和成形性能。
均匀冷却也是连铸技术的基本原理之一。
在连铸过程中,通过合理设计铸型和冷却系统,实现对铸态金属的均匀冷却。
冷却速度的均匀性对于金属的结构和性能有很大的影响,冷却速度过快或过慢都会导致不理想的组织和性能。
因此,在连铸技术中,通过合理设计浇口和冷却系统,控制铸态金属的冷却速率,实现均匀冷却,获得优良的金属组织和性能。
最后一个基本原理是连续出料。
在连铸过程中,通过特殊设计的出料装置,将快速凝固的金属连续地从连续铸型中取出。
连铸过程中,金属的凝固已经完成,但温度较高,通过连续出料并进行后续的热处理,可以获得所需的金属材料。
总的来说,连铸技术的基本原理包括连续浇铸、快速凝固、均匀冷却和连续出料。
这些原理相互作用,使得连铸技术成为一种高效、高质量的金属材料制备方法。
连铸技术的广泛应用,不仅能够提高金属材料的生产效率,提高材料的力学性能和成形性能,还能够减少金属材料的能源消耗和环境污染。
随着现代工业的发展,连铸技术在制造业中的地位和作用将越来越重要,对于推动金属材料制造业的发展具有重要的意义。
连铸坯的凝固原理
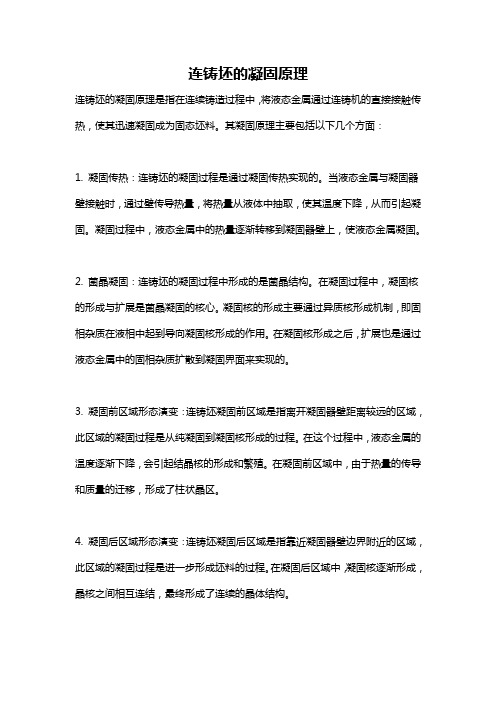
连铸坯的凝固原理
连铸坯的凝固原理是指在连续铸造过程中,将液态金属通过连铸机的直接接触传热,使其迅速凝固成为固态坯料。
其凝固原理主要包括以下几个方面:
1. 凝固传热:连铸坯的凝固过程是通过凝固传热实现的。
当液态金属与凝固器壁接触时,通过壁传导热量,将热量从液体中抽取,使其温度下降,从而引起凝固。
凝固过程中,液态金属中的热量逐渐转移到凝固器壁上,使液态金属凝固。
2. 菌晶凝固:连铸坯的凝固过程中形成的是菌晶结构。
在凝固过程中,凝固核的形成与扩展是菌晶凝固的核心。
凝固核的形成主要通过异质核形成机制,即固相杂质在液相中起到导向凝固核形成的作用。
在凝固核形成之后,扩展也是通过液态金属中的固相杂质扩散到凝固界面来实现的。
3. 凝固前区域形态演变:连铸坯凝固前区域是指离开凝固器壁距离较远的区域,此区域的凝固过程是从纯凝固到凝固核形成的过程。
在这个过程中,液态金属的温度逐渐下降,会引起结晶核的形成和繁殖。
在凝固前区域中,由于热量的传导和质量的迁移,形成了柱状晶区。
4. 凝固后区域形态演变:连铸坯凝固后区域是指靠近凝固器壁边界附近的区域,此区域的凝固过程是进一步形成坯料的过程。
在凝固后区域中,凝固核逐渐形成,晶核之间相互连结,最终形成了连续的晶体结构。
连铸坯的凝固原理是液态金属通过传导传热和纯凝固形成晶核,然后通过晶核的繁殖和晶体的连结形成连续的晶体结构,最终实现连铸坯的凝固。
连铸的基本原理

连铸的基本原理连铸的基本原理?2011-03-19 1.钢水由液体改变固体的条件?2.钢水凝固过程的冶炼金属特点?3.金属凝固时晶体长大方式?4.脱氧方式对于钢水浇铸性能,铸坯质量的影响?5.钢中合金成份和夹杂物对于浇钢操作的影响?6.提高连铸过程中钢水纯净度的措施?谁能帮帮我,我要参加技师考试!没有最佳答案连铸铸铁水平连铸课题为国家"七五"攻关项目,铸铁颠末水平连铸要领出产的型材,无砂型铸造经常出现的夹渣、缩松等缺陷,其表面平整,铸坯尺寸精度高(土L 0mm)无需表面粗加工,即可用于加工各类零件。
特别是铸铁型材组织致密,灰铸铁型材石墨细小强度高,球铁型材石墨球细小园整,机械性能兼有高强度与高韧性结合的优点。
目前国际上铸铁型材已广泛运用到制造液压阀体,高耐压零件,齿轮、轴、柱塞、印刷机辊轴及纺织机零器件。
在汽车、内燃机、液压、机床、纺织、印刷、制冷等行业有广泛用途。
连铸专制造要领1、al-pb合金-钢背轴瓦材料的水平连铸复合要领二、csp薄板坯连铸结晶器保护渣3、把钢连铸成方坯和初轧坯的结晶器4、把液体金属引入金属连铸模具的喷嘴五、板坯连铸电磁搅拌辊6、板坯连铸机的结晶器铜板上电镀镍铁合金的工7、板坯连铸机结晶器铜板上电镀镍-铁合金的要领8、板坯连铸机切割车同步器9、板坯连铸结晶器窄边铜板10、板坯连铸结晶器中的电磁搅拌装置11、板坯连铸浸入式水口在线迅速更换装置1二、板坯连铸拉矫辊13、板坯连铸拉矫机14、半连铸铸态球铁管制造要领1五、包覆连铸产物的出产要领和设备16、包含外表面上的金属镀层的铜或铜合金冷却壁的金属连铸结晶器器件以及镀层的要领17、包晶体钢连铸法18、保持连铸拉速与结晶器振荡频率相匹配的要领19、表面无裂纹连铸坯和用该铸坯的非调质高张力钢材的制法20、表面质量极好的奥氏体不锈钢带的双辊连铸要领以及利用该要领所得到的带材21、薄板还连铸用浸入式水口及其制造要领2二、薄板连铸用结晶器用粉末23、薄板坯、带坯或小方坯连铸装置24、薄板坯连铸保护渣及制造要领2五、薄板坯连铸结晶器26、薄板坯连铸连轧的要领及设备27、薄板坯连铸楔形结晶器28、薄板坯连铸用浸入式水口29、薄板坯连铸用浸渍喷嘴30、薄板坯连铸用特种水口31、薄带连铸要领及装置3二、薄带连铸结晶辊冷却水槽堵头33、薄带连铸用结晶辊34、薄带连铸用异形布流器3五、薄带坯水平连铸机36、薄带铸片连铸要领及装置37、薄钢板连铸机的侧壁38、薄金属产物的连铸要领及实现该要领的设备39、薄型金属产物的连铸要领及设备40、步进槽式连铸机41、采用带坯连铸出产(110)〔001〕晶粒取向电工钢的要领4二、采用两个水口进行板坯连铸的要领及装置43、测定命据以便自动运转连铸机的要领和装置44、长形产物的连铸要领和相应的连铸出产线4五、超薄板坯专用连铸结晶器保护渣及其出产工艺46、超低碳钢用连铸保护渣47、超低头连铸机的矫直辊列布置形状48、垂直连铸装置49、大方坯和板坯连铸机的一种迅速连接更换定位装置50、大管径铜管坯上引连铸机51、大口径铜管连铸工艺5二、带材连铸53、带材连铸设备54、带钢连铸的要领5五、带钢连铸的要领及装置56、带钢连铸机的引出头57、带坯连铸设备58、带式连铸机的改进的冷却衬垫装置59、带有多功效搅拌器的连铸出产线60、带有钢坯储存和定序的中厚钢坯连铸机和多炉加工功课线61、带有后置炉子、粗轧机和1个精轧机列的连铸机6二、带直通式结晶器和铸坯导辊装置的板坯连铸设备63、电热法矿冶连铸工艺64、调节用于金属且特别是钢材的连铸设备的1个或多个辊道段的要领和装置6五、调整金属连铸模构件的铜或铜合金外表面的要领66、调整连铸机注口位置的要领和设备67、调整连铸坯支承元件位置的调整装置和连铸坯导轨68、断面小于90方连铸机的结晶器69、对于辊连铸胀精密封式结晶辊70、多功效组合式连铸管结晶器71、方坯连铸电磁搅拌器7二、方坯连铸机铸坯导向喷水装置73、方坯连铸结晶器用振荡装置74、防止连铸件的带边缘区的不希望的冷却的要领和装置7五、非均等分瓣体软接触电磁连铸结晶器76、非均等缝隙软接触电磁连铸结晶器77、分瓣式水套电磁软接触连铸结晶器78、关闭金属带材双辊连铸机铸腔的侧壁和配有该侧壁的连铸机79、复合式电磁连铸结晶器80、复合式连铸长水口81、改进的连铸出产无氧铜杆的设备8二、改善连铸板坯表面质量的要领83、钢带的立式连铸的要领84、钢的连铸要领8五、钢的连铸用铸型粉末86、钢的连铸铸件的制造要领87、钢连铸用的铸型保护粉料以及钢的连铸要领88、钢坯、板坯或薄板坯的连铸要领和装置89、钢坯的连铸法和用于该要领的铸模90、钢坯连铸机自适应导向机构91、钢坯连铸中间罐盖9二、高保温、迅速定位连铸钢液容器93、高耐磨连铸结晶器94、高速连铸设备的运行要领及其实施体系9五、高温连铸坯表面缺陷涡流检测装置96、高压水平连铸法及其设备97、铬锆铜质连铸结晶器铜板熔铸成型工艺98、工频有芯感应加热连铸中间包99、管式连铸结晶器100、管式连铸结晶器水套历史上的今天:国家目前的扶持的行业有哪些啦,扶持政策有哪些2011-03-19赛尔号怎么获得火焰推进器在哪2011-03-19谁能帮帮我?2011-03-19。
连铸原理与工艺
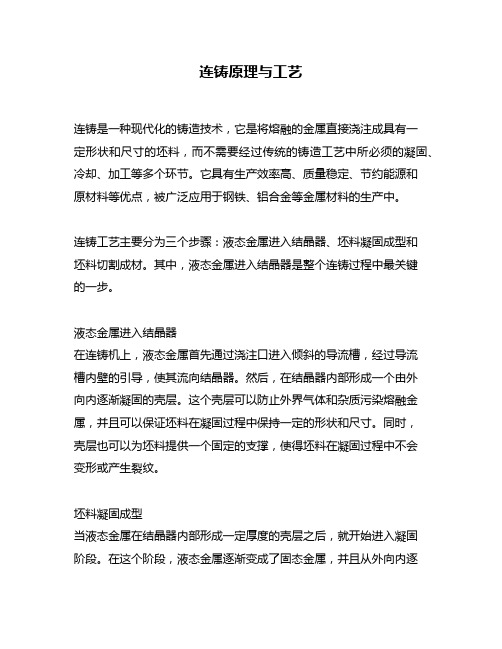
连铸原理与工艺连铸是一种现代化的铸造技术,它是将熔融的金属直接浇注成具有一定形状和尺寸的坯料,而不需要经过传统的铸造工艺中所必须的凝固、冷却、加工等多个环节。
它具有生产效率高、质量稳定、节约能源和原材料等优点,被广泛应用于钢铁、铝合金等金属材料的生产中。
连铸工艺主要分为三个步骤:液态金属进入结晶器、坯料凝固成型和坯料切割成材。
其中,液态金属进入结晶器是整个连铸过程中最关键的一步。
液态金属进入结晶器在连铸机上,液态金属首先通过浇注口进入倾斜的导流槽,经过导流槽内壁的引导,使其流向结晶器。
然后,在结晶器内部形成一个由外向内逐渐凝固的壳层。
这个壳层可以防止外界气体和杂质污染熔融金属,并且可以保证坯料在凝固过程中保持一定的形状和尺寸。
同时,壳层也可以为坯料提供一个固定的支撑,使得坯料在凝固过程中不会变形或产生裂纹。
坯料凝固成型当液态金属在结晶器内部形成一定厚度的壳层之后,就开始进入凝固阶段。
在这个阶段,液态金属逐渐变成了固态金属,并且从外向内逐渐缩小。
同时,由于液态金属的收缩率和晶粒长大率不同,所以在凝固过程中会形成一定数量的热裂纹和气孔。
为了解决这个问题,连铸工艺中采用了多种措施来控制坯料的凝固过程。
例如,在结晶器内部设置冷却水管道来降低壳层温度、使用高效保护气体来防止氧化等。
此外,在连铸工艺中还可以通过调整浇注速度、结晶器倾角、结晶器长度等参数来控制坯料的凝固速度和形状。
坯料切割成材当坯料完全凝固之后,它会被自动切割成一定长度的材料。
在连铸工艺中,切割方式主要分为两种:火焰切割和机械切割。
火焰切割是利用氧炔火焰将坯料加热到一定温度后进行切割,适用于较大尺寸的坯料。
机械切割则是使用钢丝、钢锯等工具将坯料进行切割,适用于较小尺寸的坯料。
总之,连铸工艺是一种高效、节能、环保的现代化铸造技术。
它通过控制液态金属的流动和凝固过程,使得金属材料可以以一种更加稳定和高效的方式生产出来。
同时,在连铸工艺中还可以通过调整参数、优化设备等手段来不断提高产品质量和生产效率,为现代制造业的发展做出了重要贡献。
18—8型不锈钢连铸坯振痕深度的控制及效果
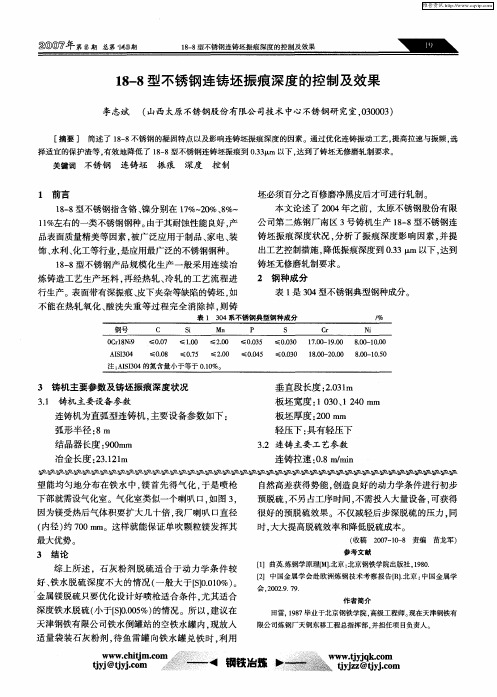
( 内径 ) 70m 约 0 m。这样就 能保证单 吹颗粒镁 发挥其
最大优势 。
3 结论
综上 所述 ,石 灰粉剂 脱硫 适合 于 动力 学条 件较 好、 铁水脱 硫深 度不 大 的情况 ( 般大 于[】.1%) 一 S 00 。 0
… 曲英. 钢学原理 【 】 1 炼 M. : 北京 北京钢铁学院出版社 ,9 o 18 . 【】 中国金属学会 赴欧洲炼 钢技术考 察报告 [) 2 2 R. 北京 : 中国金 属学
维普资讯
⑥ 期 总 别 ⑥ 年第 第母 驷
18 不 钢 铸 振 深 的 制 效 8型锈 连 坯 痕 度 控 及 果 —
1— 8 8型不锈钢连铸坯振痕深度的控制及效果
李志斌 ( 山西太原不锈钢股份有限公司技术中心不锈钢研究室,30 3 000 )
1 前言
1— 型不锈钢指 含铬 、 88 镍分 别在 1%~ 0 8 7 2 %、%~ 1%左右的一类 不锈 钢钢种 。 1 由于其耐蚀性 能 良好 , 产
品表面质量精美等 因素 , 被广泛应 用于制 品、 家电 、 装 饰、 水利 、 化工等行业 , 是应用最广泛 的不锈钢钢种 。
表 1 3 4系不锈钢典型钢种成 分 0
3 铸 机主 要参数 及铸 坯振痕 深 度状 况 31 铸机 主要 设备 参数 .
垂直 段长 度 :.3m 20 l
板坯宽度 : 00 1 4 m 1 3 、 2 0m
板坯 厚度 :0 m 20m
连铸机为直弧型连铸机 , 主要设备参数如下 : 弧形半径 : m 8
1— 8 8型不锈钢 产品规模化 生产 一般采 用连 续冶 炼 铸造工 艺生产 坯料 , 再经 热轧 、 冷轧 的工 艺流程 进
连铸工艺知识点总结

连铸工艺知识点总结一、概述连铸是指在一台设备上同时进行浇铸和凝固过程的一种工艺。
它可以大幅度提高生产效率,减少材料浪费,提高产品质量。
在现代工业中,连铸工艺已经被广泛应用于钢铁、铝、铜等金属的生产中,成为了重要的生产工艺之一。
二、连铸的原理连铸的基本原理是利用连铸机,在一个连续的过程中,将金属液直接浇注至坯料模具中,然后通过顺序凝固、切割、堆垛等工序,最终产生坯料产品。
整个连铸过程中,金属液会先经过结晶器的处理,实现坯料的凝固,在这个过程中,还会进行一系列的拉伸、抽拉和冷却等操作,使得坯料的形状和尺寸得以控制和稳定。
三、连铸的优势1. 提高生产效率:相对于传统浇铸工艺,连铸可以大幅度提高生产效率。
因为它可以在同一个设备上连续进行浇铸和凝固过程,减少了生产过程中的空闲时间,从而实现了生产效率的提升。
2. 减少材料浪费:连铸工艺可以减少金属的二次加工过程,大大减少了金属的浪费,减少了材料的消耗,同时也减少了对环境的污染。
3. 提高产品质量:由于连铸工艺可以控制金属的凝固过程,使得坯料的材料结构更加均匀,从而提高了产品的质量。
4. 节省能源:相对于传统的浇铸工艺,连铸工艺可以在生产过程中更好地利用能源,降低能源的消耗。
四、连铸的工艺流程1. 铸坯模具的准备:连铸的第一步是准备好适用于连铸工艺的铸坯模具,通常采用的是一种特殊的铸坯模具,可以确保坯料的形状和尺寸的准确度。
2. 结晶器处理:在连铸的过程中,金属液会通过结晶器进行处理,实现坯料的凝固。
3. 拉伸、抽拉和冷却:在结晶器处理完后,金属液会经过一系列的拉伸、抽拉和冷却等操作,以控制坯料的形状和尺寸。
4. 切割和堆垛:最后,坯料会被切割为所需的尺寸,然后进行堆垛,完成整个连铸工艺的过程。
五、连铸的应用领域1. 钢铁生产:连铸工艺在钢铁生产中得到了广泛的应用,可以高效地生产出各种规格的钢铁坯料。
2. 铝合金生产:在铝合金生产中,连铸工艺可以提高产品质量,降低生产成本。
连铸机工作原理
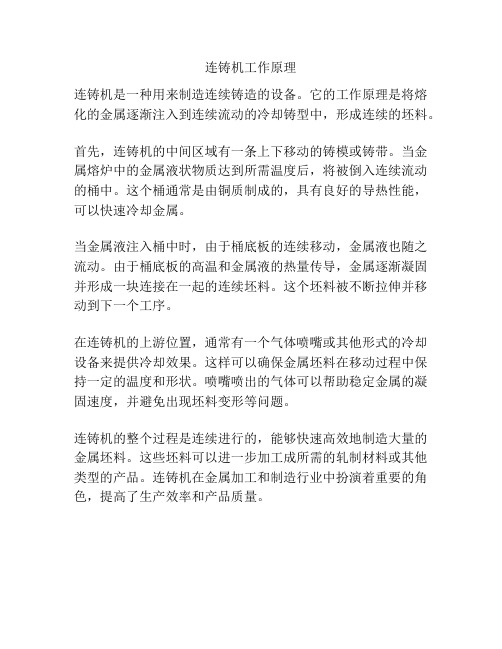
连铸机工作原理
连铸机是一种用来制造连续铸造的设备。
它的工作原理是将熔化的金属逐渐注入到连续流动的冷却铸型中,形成连续的坯料。
首先,连铸机的中间区域有一条上下移动的铸模或铸带。
当金属熔炉中的金属液状物质达到所需温度后,将被倒入连续流动的桶中。
这个桶通常是由铜质制成的,具有良好的导热性能,可以快速冷却金属。
当金属液注入桶中时,由于桶底板的连续移动,金属液也随之流动。
由于桶底板的高温和金属液的热量传导,金属逐渐凝固并形成一块连接在一起的连续坯料。
这个坯料被不断拉伸并移动到下一个工序。
在连铸机的上游位置,通常有一个气体喷嘴或其他形式的冷却设备来提供冷却效果。
这样可以确保金属坯料在移动过程中保持一定的温度和形状。
喷嘴喷出的气体可以帮助稳定金属的凝固速度,并避免出现坯料变形等问题。
连铸机的整个过程是连续进行的,能够快速高效地制造大量的金属坯料。
这些坯料可以进一步加工成所需的轧制材料或其他类型的产品。
连铸机在金属加工和制造行业中扮演着重要的角色,提高了生产效率和产品质量。
连铸连轧知识点

连铸连轧知识点连铸和连轧是金属工业中常见的两个工艺过程。
连铸是指将液态金属连续铸造成坯料的过程,而连轧是指将坯料经过一系列压制和变形操作,连续地轧制成所需尺寸的金属板、带材或线材的过程。
本文将介绍连铸和连轧的基本概念、工艺流程和主要应用。
一、连铸连铸是一种高效的金属铸造技术,具有生产速度快、坯料质量好等优点。
连铸主要应用于钢铁、铜、铝等金属的生产中。
1. 连铸的基本原理连铸的基本原理是将熔融的金属通过连续浇注的方式,直接铸造成连续的坯料。
具体原理如下:首先,将金属熔融至液态,并通过加热设备保持在一定温度范围内;然后,通过连续浇注系统,将熔融金属均匀地注入到连铸结晶器中;在连铸结晶器中,通过冷却剂的作用,使金属迅速凝固,并形成坯料;最后,通过一系列传动装置,将连续产生的坯料送往下游的轧制设备或其他后续处理过程中。
2. 连铸的工艺流程连铸的工艺流程一般包括以下几个关键步骤:(1)冶炼:将矿石等原料经过熔炼处理,得到液态的金属合金;(2)调温:通过加热设备将金属保持在一定的液态温度;(3)连续浇注:通过连续浇注系统,将熔融金属注入到连铸结晶器中;(4)结晶与凝固:在连铸结晶器中,通过冷却剂的作用,使金属迅速凝固,并形成坯料;(5)切割和输送:将连续产生的坯料切割成合适的长度,并送往下游的加工设备。
3. 连铸的应用连铸广泛应用于钢铁、铜、铝等金属的生产中。
在钢铁工业中,连铸可以直接将炼钢铁水铸造成连续坯料,用于后续轧制成钢板和钢材。
在有色金属工业中,连铸可以将液态金属铸造成连续的板材、带材和线材,用于制造电线电缆、汽车零部件等产品。
二、连轧连轧是一种将金属坯料经过多道次的压制和变形操作,连续地轧制成所需尺寸的金属板、带材或线材的工艺过程。
连轧具有高效快速、坯料成形完整等特点,广泛应用于钢铁、有色金属等工业领域。
1. 连轧的基本原理连轧的基本原理是通过一系列的压制和变形操作,使金属坯料逐渐减小厚度、增大长度,并达到所需的尺寸要求。
(技师考试材料连铸课件)08连铸计算题型

B、计算凝固距离:的第一个应用是
• 例3.某厂连铸机浇注断面断面为 210X1250mm2,拉速(Vc)为0.95m/min均 衡不变,比水量是 1L/kg(对K值有影响呈 正比)凝固系数K=27mm/min1/2,求:板坯 需浇铸多少米才能完全凝固?
• 解:L= ( D )2 Vc ( 210 )2 0.95
B、计算凝固距离:的第一个应用是
• 1) 液芯长度的计算:凝固定律有一个特例即 铸坯完全凝固时,坯壳厚度正好于铸坯厚度 的一半,对应的凝固距离就是液芯长度(液相 深度)。这样我们通过对凝固定律公式的的变 形就可以计算出铸坯完全凝固的距离即液芯 长度,其意义在于通过对液芯长度的控制既确 保液芯长度小于铸机的长度防止切割漏钢又 使其不成为拉速提高的限制性环节.
0.6
• =1.5m/min • 答:拉坯速度是1.5米/分。
• (小数点保留一位)
C、计算平均拉坯速度:
• 例4. 小方坯150 X 150mm2,结晶器凝固系数K=19mm/min1/2, 其液面控制在离上口100mm,出结晶器的安全坯壳厚度 δ=12mm,结晶器长度L=700mm,试求其正常拉速V。
• (小数点保留一位)
• 解: V=
(
K
)2
L有效
(19)2 12
2K
2 27
• =14.37m • 答:需浇铸14.37米才能完全凝固。
C、计算平均拉坯速度:
• 例4. 小方坯150 X 150mm2,结晶器凝固系 数K=19mm/min1/2,其液面控制在离上口 100mm,出结晶器的安全坯壳厚度 δ=12mm,结晶器长度L=700mm,试求其 平均拉速V。
连铸计算题型
B、计算凝固距离:
八流连铸中间包控流装置优化的水力学模拟
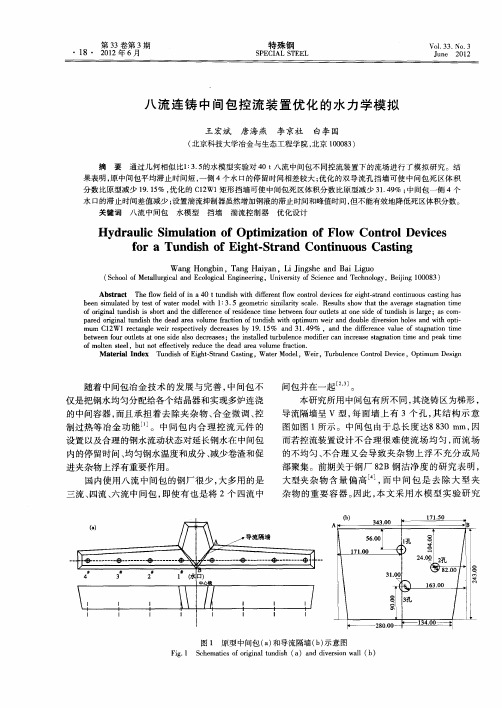
一 ): 粤 』 d
:
一
t
霎( ci t
( 4 )
理 论平 均停 留 时间 : =V/ RQ 以理论 平均 停 留时 间 t作 为 基 准 时 间 , 除停 留
时 间 t可得 出无 因次 停 留 时 间 0 无 因次 最 小 停 留 , ,
老
由此计算 出模 型所 对应 于原 型的体 积流量 和水 口流速 , : 即
包 为 原型 , 结构示 意 图如 图 1b 所示 。浇 铸 的铸 坯 () 断面 尺寸是 10mm×10m 5 5 m。选 取 模 型 与原 型 的 几 何相 似 比 为 =135 / . 。模 型 与 原 型对 应 的 工 艺
参 数 如表 1所示 。
表 1 原 型 和 水 模 型 的主 要 工 艺 参 数
4j. UU
l ’
● - ●
} |/粤 、 f 一 i
. { 0
4
审
3
申
2
审
1 冰 、 口
。
中心缱
审
审 —
.1 _ 。 / . — 1 7 o 0’
孔
3 .0 1O 8 .0J 2 O
5 6 . O 0
果表明 , 中间包平均滞止时 间短 , 原 一侧 4个水 口的停 留时间相差较大 ; 优化 的双 导流孔挡墙 可使 中间包死 区体积 分数比原型减少 1. 5 , 9 1 % 优化 的 C 2 1W1矩形挡墙可使中间包死区体积分数 比原 型减少 3 .9 ; 14 % 中间包一侧 4个 水 口的滞止时间差值减少 ; 设置湍流抑制器虽然增加钢液的滞止时间和峰值时间, 但不能有效地 降低死区体积分数。 关键词 八 流中间包 水模 型 挡墙 湍流控制器 优化设计
连铸连轧原理课件1

连铸机类型
厚板坯 薄板坯
断面形状 大方坯 小方坯 圆坯 异型坯 运行轨迹
立式 立弯式 多点弯曲 弧形
椭圆形
连铸机类型
按铸坯断面分类
连铸机类型
连铸机示意图
机型的特点
(1)立式连铸机:
结晶器、二冷段、拉坯和剪切沿垂直方向排列
优点: - 无弯曲变形、冷却均匀,裂纹少。 - 夹杂物容易上浮。 缺点: ·设备高,建设费用大。 ·钢液静压大,容易产生鼓肚。
1.2 连铸的发展史
世界上第一台工业生产性连铸机是1951年在原苏联 红十月钢厂投产的立式半连续式装置。它是双流机, 断面尺寸180mm×600mm。 作为连续式浇铸的铸机是1952年建在英国巴路钢厂 的双 流立弯式铸机,其生产断面尺寸为 50mm×50mm 和90mm× 90 mm的小方坯。 宽板坯铸机于1959年建在原苏联的新列别茨克厂。 日本住友和罗西为新日铁光厂提供的世界上第一台不 锈钢宽板坯连铸机在1960年12月投产,宽度为 1050mm。 在整个50年代,连续铸钢技术尽管开始步入工业生 产,但产量很少,1960年的产量仅为115万吨,连铸 比仅为0.34﹪。
1.2 连铸的发展史
连续浇铸思想的启蒙阶段 (1840~1930年) 1840年美国 人塞勒斯(Sellers)获得了连续 铸铅的专利。
图1
图2
1856年英国人贝塞麦(Henry Bessemer) 采用双辊连铸机 浇铸出了金属锡箔、铅板和 玻璃板,并获专利。
1.2 连铸的发展史
1.2.1 早期尝试 美国亚瑟(B.Atha)(1866年)和德国工程师戴伦 (R.M.Daelen)(1877年)最早提出以水冷、底部敞口 固定结晶器为特征的常规连铸概念。前者采用一个底 部敞开、垂直固定的厚壁铁结晶器并与中间包相连, 施行间歇式拉坯;后者采用固定式水冷薄壁铜结晶器、 施行连续拉坯、二次冷却,并带飞剪切割、引锭杆垂 直存放装置。 1920~1935年间,连铸过程主要用于有色金属,尤其 是铜和铝的领域。
8#八机八流连铸机新技术在韶钢的应用
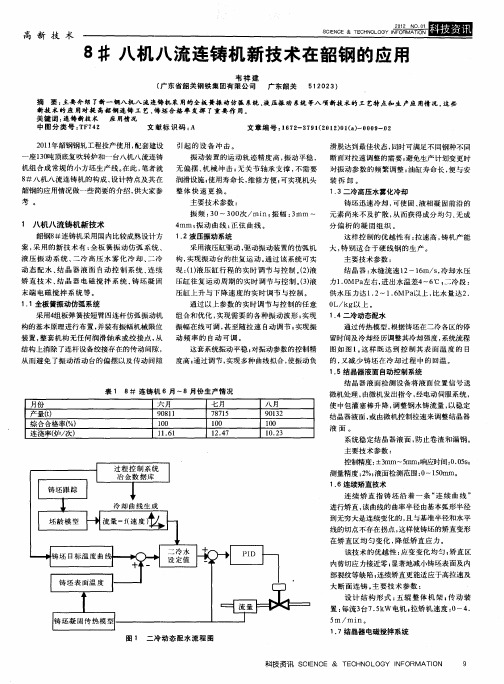
采 用4 组板弹 簧按短 臂四连杆 仿弧 振动机 组 合和优化 , 现需 要 的各种 振 动波形 ; 现 实 实 构 的基本 原理进 行布置 , 装有振幅 机械 限位 振 幅 在线 可调 , 并 甚至 随 拉速 自动 调节 ; 现振 实 装置, 整套 机构 无任 何润 滑轴 承或 绞接 点 , 从 动 频 率 的 自动可 调 。 结 构上消 除 了连 杆设备绞接 存在 的传动 间隙 , 从 而 避免 了振 动活 动 台的偏 摆以 及传 动 间隙 这套 系统振动 平稳 ; 对振 动参 数的控制 精
14二冷动态 配水 .
通过传 热模型 , 根据铸坯 在二冷各 区的停 留时间及 冷却经 历调整其 冷却强度 , 系统流程 图如 图 l 这 样 既 达 到 控 制 其 表面 温 度 的 目 。 的, 又减 少 铸坯 在 冷却 过 程 中的 回温 。 1 5结 晶器液 面 自动 控制 系统 .
座 10 3 吨顶 底复吹转 炉和一 台八机八 流连铸
韶钢 的应用情 况做一些 简要 的介绍 , 大家参 整 体 快 速 更换 。 供 考 。
主 要技 术参数 : 振 频 : 0 0 次 / i 振 幅 : mm ~ 3 ~3 0 a r n; 3 4 m ; 动 曲 线 : 弦 曲线 。 a r 振 正
力1 0 .MPa 右 , 出水温 差4~6 二冷 段 : 左 进 ℃l 供水 压 力达 1 2~1 6 . . MPa 以上 , 比水量 达2.
1 八机 八流铸机新 技术
案 , 用的 新技 术有 : 板 簧振 动 仿 弧 系统 、 采 全
韶钢8 #连铸 机采用 国内 比较成熟 设计方 1 2 . 液压 振动系统 液 压振 动 系统 、 二冷 高 压 水 雾 化 冷 却 、 冷 构 , 二 实现振 动 台的往 复运 动 。 通过 该 系统 可实 动 态 配 水 、 晶 器液 面 自动 控 制 系 统 、 续 现 :1液 压 缸 行程 的 实 时调 节 与 控 制 。2 液 结 连 () () 矫 直 技 术 、 晶 器 电磁 搅 拌 系 统 、 坯 凝 固 结 铸 压缸 往 复运 动周 期 的实 时 调节 与控 制 。3 液 ()
连铸原理

3、中间包的设计
③角度的确定 ❖ 原则:保证耐火材料的稳定性;残钢易于脱
除;操作人员易于观察结晶器液面。一般为 9~13° ④宽度的确定 ❖ 宽度依照容量进行确定。一般应尽量提高深 度,减小宽度,以降低浇余、减少热损失。
3、中间包的设计
⑷中间包水口流量的控制 ①定径水口控制 ❖ 对水口的要求:孔径在整个浇注过程基本不变,以
加工; ❖ 较好的耐磨性能及抵抗热应力的性能;器主要尺寸计算 ①结晶器断面尺寸的确定 ❖ 圆坯结晶器
❖ 方坯结晶器
4、结晶器的设计
❖ 矩坯结晶器
C—调整值,断面小于160mm2时,C为1; 断面大于160mm2时,C为1.5
4、结晶器的设计
❖ 板坯结晶器 结晶器宽边
2、连铸机的基本参数计算
❖ ⑶拉速设计 当液芯长度等于冶金长度时的拉速为连铸机 的最大拉速,最大拉速一般为工作拉速的 1.15~1.2倍。
限制拉速提高的因素:
❖ 钢种的影响。碳素高凝固系数大,拉速高; 合金钢凝固系数小,拉速应适当小一点;一 般同断面的合金钢拉速比碳素钢低20~30%。
❖ 铸坯断面的影响。随着断面增加,拉速应减 小。
三、连铸工艺参数的设计原理
⑶连铸机流数 ⑷连铸机作业率 ⑸金属收得率
三、连铸工艺参数的设计原理
⑹浇注时间 ⑺准备时间
三、连铸工艺参数的设计原理
附:连铸钢水金属平衡图
2、连铸机的基本参数计算
⑴弧形半径的确定 ①按照经验确定 ❖ 按照断面确定
小方坯连铸机R=(30~40)铸坯厚度 大方坯连铸机R=(30~50)铸坯厚度 板坯连铸机 R=(40~50)铸坯厚度 ❖ 按照钢种确定 普碳钢和低合金钢R=(30~40)铸坯厚度 优质钢和高合金钢R=(40~50)铸坯厚度
连铸铸造原理

连铸铸造原理连铸铸造原理是一种现代金属铸造工艺,它通过连续铸造的方式将熔融金属直接注入连铸机中,经过冷却和凝固后,得到所需形状和尺寸的金属坯料。
连铸铸造原理的实现依赖于多种技术和设备,包括连铸机、结晶器、冷却系统和浇注系统等。
下面将从铸造过程、设备原理和优点等方面介绍连铸铸造原理。
连铸铸造的整个过程可以分为几个步骤:熔炼和净化、浇注和冷却、结晶器和坯料的形成。
在熔炼和净化阶段,金属材料被加热到熔点以上,并通过一系列的处理方法去除杂质和气体,以提高金属的纯度和质量。
在浇注和冷却阶段,熔融金属被注入连铸机的浇注系统中,通过一系列的冷却措施,使金属迅速凝固成坯料。
在结晶器和坯料形成阶段,通过一系列的结晶器和冷却系统,使金属坯料在连铸机内逐渐形成并冷却。
连铸铸造原理的实现离不开各种设备的配合。
连铸机是实现连铸铸造的核心设备,它包括浇注系统、结晶器、坯料切割系统等。
浇注系统用于将熔融金属注入连铸机内,结晶器则用于控制金属凝固的速度和结晶方式,从而得到所需的金属坯料。
坯料切割系统用于将连续铸造得到的金属坯料切割成所需的长度。
此外,冷却系统用于控制金属的冷却速度,以确保坯料的质量和性能。
连铸铸造原理相比传统的铸造方法具有许多优点。
首先,连铸铸造可以实现大规模、高效率的生产,可以连续铸造大量的金属坯料。
其次,连铸铸造的产品尺寸和形状可以根据需求进行调整,具有较高的灵活性。
此外,连铸铸造可以通过控制金属的冷却速度和结晶方式,改善金属的组织和性能,提高产品的质量。
最后,连铸铸造还可以减少金属材料的浪费,提高资源利用率。
连铸铸造原理是一种现代金属铸造工艺,通过连续铸造的方式将熔融金属直接注入连铸机中,经过冷却和凝固后,得到所需形状和尺寸的金属坯料。
连铸铸造原理的实现依赖于多种技术和设备,包括连铸机、结晶器、冷却系统和浇注系统等。
连铸铸造具有高效率、灵活性和产品质量优良等优点,是现代工业生产中重要的一种铸造方法。
随着科技的进步和工艺的不断改进,连铸铸造原理将在未来的金属铸造领域发挥更加重要的作用。
三炼钢8 #高效连铸机铸坯夹渣分析与改进

( ) 晶器 渣 样 中含 有 较 高 的 ( a 、 1 结 c 0)
( O) ( 2 ) 三 者 比 例 分 别 为 8.4% 、 Mg 、 Al O3 , 6 1 7 % 、 . 5 ; 间 包 渣 样 中 也 含 有 较 高 的 .6 58 % 中 ( a 、 Mg 、 Al ) 三 者 比 例 分 别 高 达 C O) ( O) ( 2 o3 + 1 .0 、 . 5 、 3 0 % 。 在 浇 铸 过 程 中 , 5 0 % 3 O % 1 .4 钢 液 内 部 不 可 能 产 生 大 量 ( a 、( O ) C O) Mg 、
中 间 包 4 . 9 4.4 1 ; 4 1 O 3. 5 9 6 1 3 0 5.O O 结 晶 器 3 .8 1 .7 5 8 94 4 9 .5 8 6 .4 17 .6
0.4 7
5 7 7.6 .3 6
4 7 1 .O O 1 2 4 .O 4 O .2 4. 1
昆 钢 科 技 \ 成 分
20 0 2年 1期
渣榨\ sc i h
F Ah 3 C O e O a Mg O MF e
_
0 F 2 3 ∑F o Po Mn eo e 25 O
3.2 4 10 .6 48 .5 0 3 l .2 .6 16
开 浇 注 , 间 包 和 结 晶 器 钢 液 面 都 裸 露 在 空 气 中 中 , 进 一 步 加 大 空 气 进 ^ 钢 水 的机 会 . 而 使 会 从
钢 水二 次氧化 加剧 , 坯 夹渣增 加 。 铸
2 2 渣 样 分 析 ・
8 铸 机 高 效 化 改 造 投 产 初 期 , 坯 出 现 大 铸
一
量夹 渣缺 陷 . 重 影 响 了铸 坯 的质 量 。 为 了进 严 步 搞 清 铸 坯 产 生 夹 渣 的 原 因 ,0 0年 3月 我 20
- 1、下载文档前请自行甄别文档内容的完整性,平台不提供额外的编辑、内容补充、找答案等附加服务。
- 2、"仅部分预览"的文档,不可在线预览部分如存在完整性等问题,可反馈申请退款(可完整预览的文档不适用该条件!)。
- 3、如文档侵犯您的权益,请联系客服反馈,我们会尽快为您处理(人工客服工作时间:9:00-18:30)。
一、连续铸钢的发展
1、连续铸钢发展概况: ⑴1933年德国人Junghans(容汉斯)建设 第一台连铸机; ⑵1951年前苏联建设了第一台不锈钢板坯连 铸机; ⑶1952年英国建设了第一台小方坯连铸机; ⑷1954年德国建设了第一台圆坯连铸机。
2、我国连续铸钢技术发展:
⑴1957年进行试验研究; ⑵1958年在重钢建成双流连铸机,浇注 175×200mm铸坯; ⑶1960年在唐钢建成立式方坯连铸机; ⑷1964年在重钢建成弧形板坯连铸机(世界最 早弧形连铸机)。
⑵板坯连铸机的特点
钢包支撑(回转台、升降、称量、长水 口、钢包加盖) 中间包和中间包车(大容量、内设挡墙、 侵入式水口、塞棒控制、滑动水口、升 降、横移) 结晶器(在线调宽、液面自控、漏钢预 警) 二次冷却(上半部分强水冷、中部和下 部气-水冷却;支撑装置为小辊距密排辊)
⑵板坯连铸机的特点
轧机规格 高速线材 420/250轧机 铸坯断面,mm 方坯:100× 100~150× 150 方坯:90× 90~140× 140 矩坯:<100×150 方坯:100× 100~180× 180 矩坯:<150×180 方坯:140× 140~180× 180 矩坯:<140×260 板坯:(120~180)×(700~1000) 板坯:(120~180)×(700~1000) 板坯:(150~250)×(900~2100) 板坯:(150~350)×(1200~2100) 板坯:(150~350)×(1200~1600) 板坯:(100~200)×(700~1350) 板坯:(120~350)×(700~1600) 板坯:(120~350)×(900~1900)
三、连铸工艺参数的设计原理
1、连铸机生产能力
⑵断面选择原则 合适的压缩比; 碳素钢和低合金钢压缩比为6;不锈钢和耐热钢压缩 比为8;高速钢和工具钢压缩比为10 连铸机的生产能力和炼钢能力相匹配; 根据轧机组成、轧材品种和规格确定; 要适合连铸工艺要求。
三、连铸工艺参数的设计原理
附:断面与轧机配合
⑶圆坯连铸机特点
结晶器锥度(φ≤200mm锥度为1%;φ> 200mm锥度为1.2%;含C量低铸坯收缩明 显,应选用较大锥度;含C量高铸坯收缩不 明显,应选用较小锥度) 二冷区(弱冷,比水量0.3~0.8L/kg钢;矫 直温度≤1000℃) 拉矫机(多点矫直) 切割机(火焰切割) 冷床(步进式)
对于小方坯坯壳厚度应大于8~10mm;板坯为 15~20mm
4、结晶器的设计
⑴结晶器主要尺寸计算
③方坯结晶器的圆角半径 原则:圆角半径越大,纵向裂纹倾向越严重。一 般为4~8mm ④结晶器的倒锥度 定义:钢水在结晶器内冷却后生成坯壳,进而收 缩脱离了结晶器内壁形成气隙,影响了结晶器的传 热,为了减少气隙,提高洁净的传热能力,加速坯 壳生长,通常将结晶器设计成上大下小的形式,成 为结晶器的倒锥度。
3、连续铸钢的优越性
⑴节省工序缩短流程;省掉了模铸的脱模、 整模、均热和开坯工序 ⑵提高了金属收得率;可提高金属收得率 10~14%(开坯工艺切头、切尾损失大约 为10~20%,而连铸的切头、切尾损失为 1~2%) ⑶降低能量消耗; ⑷生产过程机械化和自动化程度高; ⑸品种多、质量高。
二、连铸机机型和结构特征
2、连铸机的基本参数计算
②按照凝固计算确定 按照全凝固矫直计算
(K为综合凝固系数,板坯为26~29;方坯为28~32) 为保证铸坯在凝固前完全凝固,有下列关系:
2、连铸机的基本参数计算
⑵冶金长度 液芯长度:又称液相穴深度,是指从结晶器 液面到铸坯中心液相完全凝固点的长度。
冶金长度:根据最大拉速计算的液芯长度就 是连铸机的冶金长度。
上引锭装置(引锭杆卷取桁heng架 式、引锭杆卷取导向式) 切割机(火焰切割) 去毛刺装置((刀具刮除、火焰去 除) 拉矫机(多点矫直)
⑵板坯连铸机的特点
板坯连铸机的自动监测和自动控制 系统 钢包、中间包钢水重量测量、结晶 器液面自动控制、漏钢预警、铸坯 表面温度检测、二冷水动态监控、 辊缝检测、电磁搅拌。
1、连铸机机型
2、各种连铸机的特点
⑴立式连铸机 主要设备垂直分布,厂房高度要求高; 利于钢水中夹杂物上浮排出; 坯壳冷却均匀;不受弯曲、矫直作用,裂纹敏感 性低。 ⑵立弯式连铸机 在垂直方向进行浇注,有利于夹杂物上浮排出; 只适应于浇注小断面铸坯。
⑶弧形连铸机
单点矫直弧形连铸机 高度低、投资少;钢水静压力小,可以减少因鼓肚 而造成的内裂和偏析;夹杂物易向内弧聚集,造成 内部夹杂物分布不均匀。 多点矫直弧形连铸机 带液芯矫直过程中,分散了固液界面变形,不易产 生中心裂纹。 直结晶器弧形连铸机 有利于夹杂物上浮排出及夹杂物均匀分布;两相区 已造成裂纹缺陷。
4、结晶器的设计
⑵结晶器冷却水量 结晶器冷却水量通过下式计算
F—结晶器水缝总面积,mm2;v—结晶器水流速, m/s,方坯一般为6~9m/s,板坯一般为3.5~5m/s。 注:结晶器水量与钢水C含量有关,对于低碳钢, 凹坑敏感性强,应采用弱冷,结晶器水量取下限; 高碳钢采取强冷,结晶器水量取上限。
(h为耐火材料厚度,H为最大液面深度,h’为 最大液面到包口距离)
3、中间包的设计
②长度的确定 基准:中间包水口的位置
(n为流数;为流间距;)
(H为中间包深度,α为中间包内墙倾角,一般为 9~13°)
3、中间包的设计
③角度的确定 原则:保证耐火材料的稳定性;残钢易于脱 除;操作人员易于观察结晶器液面。一般为 9~13° ④宽度的确定 宽度依照容量进行确定。一般应尽量提高深 度,减小宽度,以降低浇余、减少热损失。
⑶圆坯连铸机特点
对钢水要求 无渣出钢技术、[Al]=0.005~0.020%之 间,[O]≤0.005%,[S]≤0.020%;真 空处理、吹Ar、喂Ca-Si丝; 钢包(长水口、Ar封) 中间包(大容量、内设挡墙、侵入式水口、 保护渣) 连铸机弧形半径(φ≤200mmR为8.0~10m; φ>200mmR为12m以上)
5、二冷区设计
⑴二冷区比水量的确定 ①钢种对比水量的要求 随着比水量的减少和二冷区的延长,钢坯内部裂 纹减少,即二冷区采取弱冷有利于减少内部裂纹的 产生。 普碳钢、低合金钢比水量为1.0~1.2L/kg;中高碳 钢、合金钢比水量为0.6~0.8L/kg;高速钢比水量 为0.1~0.3L/kg;裂纹敏感性强的钢种比水量为 0.4~0.6L/kg。
4、结晶器的设计
结晶器应具有的性能: 良好的导热性能; 较好的结构刚性,便于拆装、调整,容易 加工; 较好的耐磨性能及抵抗热应力的性能; 重量轻,振动时惯性小。
4、结晶器的设计
⑴结晶器主要尺寸计算 ①结晶器断面尺寸的确定 圆坯结晶器
方坯结晶器
4、结晶器的设计
矩坯结晶器
C—调整值,断面小于160mm2时,C为1; 断面大于160mm2时,C为1.5
500/350轧机
650轧机 2300轧机 2450轧机 中厚板轧机 2800轧机 3300轧机 4200轧机 1450轧机 热轧带钢 1700轧机 2030轧机
三、连铸工艺参数的设计原理
⑶连铸机流数 ⑷连铸机作业率
⑸金属收得率
Байду номын сангаас
三、连铸工艺参数的设计原理
⑹浇注时间 ⑺准备时间
三、连铸工艺参数的设计原理
2、连铸机的基本参数计算
⑶拉速设计 当液芯长度等于冶金长度时的拉速为连铸机 的最大拉速,最大拉速一般为工作拉速的 1.15~1.2倍。
限制拉速提高的因素: 钢种的影响。碳素高凝固系数大,拉速高; 合金钢凝固系数小,拉速应适当小一点;一 般同断面的合金钢拉速比碳素钢低20~30%。 铸坯断面的影响。随着断面增加,拉速应减 小。 坯壳厚度的影响。 钢坯质量的影响。 (K为结晶器内钢的凝固系数,一般为20)
附:连铸钢水金属平衡图
2、连铸机的基本参数计算
⑴弧形半径的确定 ①按照经验确定 按照断面确定 小方坯连铸机R=(30~40)铸坯厚度 大方坯连铸机R=(30~50)铸坯厚度 板坯连铸机 R=(40~50)铸坯厚度 按照钢种确定 普碳钢和低合金钢R=(30~40)铸坯厚度 优质钢和高合金钢R=(40~50)铸坯厚度
倒锥度的计算:
或
注:结晶器锥度过小,导致铸坯出现脱方、纵裂及纵向凹陷 缺陷;倒锥度过大,增大拉坯阻力,就会导致横裂、拉断等 缺陷或事故。 倒锥度大小取决于拉速、断面和含C量: 80~110mm方坯,倒锥度为0.4%/m;110~140mm方坯, 倒锥度为0.6%/m;140~200mm方坯,倒锥度为0.9%/m; 低碳钢(C<0.08%)小方坯倒锥度为0.5%/m;高碳钢(C >0.40%)小方坯倒锥度为0.8~0.9%/m;圆坯结晶器倒锥 度为1.20%/m.
3、中间包的设计
⑵中间包形状 中间包外形 条件:能均匀的把钢水分配到每个水口、利 于钢渣分离、减少热损失、利于操作、维修 方便。一般设计成T型。 中间包内型 条件:钢液流动方式、防止卷渣。一般水口 中心线距离内衬大于400~600mm。
3、中间包的设计
⑶中间包内腔主要尺寸 高度的确定 原则:保证夹杂物充分上浮,钢液在包中停 留时间8~10min。
4、连铸机机型选择原则
• 满足钢种和断面规格的要求; • 满足铸坯质量的要求; ←内裂危险性增大 立式→直结晶器弧形→弧形→多点矫直弧 形→超低头弧形→水平 →内弧侧夹杂物富集增强 • 节省建设投资。
三、连铸工艺参数的设计原理
1、连铸机生产能力 ⑴产量 台时产量=60×断面×拉速×7.6×流数 日产量=1440÷浇注周期×连浇炉数×出钢 量×收得率 年产量=365×日产量×连铸机作业率