红酸果案例答案
案例:蔓越莓(红酸果)
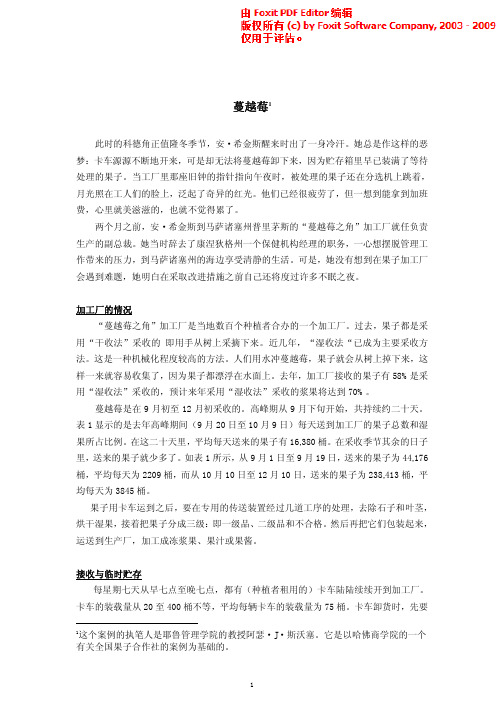
在收获季节(9 月 1 日至 12 月 15 日),加工厂一周七天都开工。在大约二十天的高 峰期,计划使用 53 人,而在其余的非高峰期时间里,只有 27 人上班。工人在每天前八 个小时内拿固定的计时工资,加班则多加 50%的工资。平均的工资水平是每小时 12.50 美元。
按照高峰期工作计划和非高峰期工作计划,负责接收的工人每天都要从早上七点钟 工作到晚上七点钟。如表 2 所示,在非高峰期,其他的工人从下午三点钟开始上班,一 直要工作到晚上 11 点钟。在高峰期,其他的工人被安排从上午 11 点一直工作到晚上 11 点。但是,工作时间超过晚上 11 点钟的情况是司空习惯的。在这种情况下,大约需要 15 名工人操纵贮存箱、通过整套系统来处理果子和进行散装。虽然干果可以在贮存箱内 过夜,但湿果必须在下班前从贮存箱中倒出来。另外,还需要至少两个小时的时间打扫 卫生和维护设备,因此该厂一天开工的时间从没有超过 22 个小时。
接收
去石子
(15 人)
去叶茎
每台倾倒
烘干
机3人
(1 人)
上午 7 点
9点
11 点
下午 1 点
3点
5点
7点
9点
11 点
分选 (15 人) 每条线
5人
装运 (20 人)
控制室 操作员 (任何时候值 班为 1 人)
5
蔓越莓加工的工序流程图
卡车运来
每天 18,000 桶, 70% 是湿的
1500 桶/小时
会有这么长的计划外加班时间?也就是说,实际工作时间为什么会大大超过 12 个小时? 3. 使用烘干机处理完一天内运来的所有湿果需要多长时间?使用分选机处理一天 内运来的所有果子又需要多长时间?根据你对这两个问题的答案,哪个或哪些工 序步骤是瓶颈,也就是说它(它们)会限制物流和生产速度? 4. 我们已经假定了每天运到的果子有 70%是湿的,有 30%是干的。如果湿果的比 例有变化,那又会出现什么情况?比如,如果 30%是湿的、70%是干的,又会怎 样呢?哪个工序步骤是瓶颈是否会有变化呢? 5. 根据此案例表 2,去石子、去叶茎、烘干、分选和装运这几道工序,在高峰期间 是上午 11 点开始运行。这几道工序如果早一点开始运行有什么好处吗?在低峰 期间,这些工序是下午 3 点开始运行,这种做法切合实际吗?为什么最佳开始运 行时间要随着每天所接收的果子数量而变化呢? 6. 奥布里恩打算安装两台新的烘干机(每台 75,000 美元),把 16 个干果贮存箱改 造成干湿兼用贮存箱(每个贮存箱 15,000 美元)。这样做可行吗?增加一台烘 干机有什么收效?再增加一台烘干机又有什么收效?改造一个贮存箱会有什么 效果?再改造其他的贮存箱又会有什么效果? 7. 您建议进行什么改进?尽量扩展思路,您是否还有其他的建议?
红酸果精益分析

红酸果案例分析背景“红酸果之角”加工厂面临经营管理方面的问题。
在酸果成熟期,加工厂外,运送卡车排起了长龙;加工厂里,工人每天轮班超时加班,机器超负荷运转,给工厂带来了额外的成本支出。
但是即便如此,仍然没能改变状况,种植者抱怨不断,加班现象失去控制……分析红酸果加工流程图在高峰期的一天,有18,000桶酸果运来,从早上7点到晚上7点这12个小时内,每小时平均运到的数量就是18,000/12=1,500桶/小时倾倒效率平均每辆车的装载量是75桶,卸一车酸果平均用时7.5分钟,共有5台倾倒机,则每小时可倾倒60/7.5×75×5=3000桶/小时存贮量干贮存箱250×16=4000桶干/湿两用贮存箱250×8=2000桶湿贮存箱400×3=1200桶去石效率1500×3=4500桶/小时去茎效率1500×3=4500桶/小时烘干效率200×3=600桶/小时分选效率400×3=1200桶/小时初步分析可知,整个生产流程中“烘干”工序是最大的一个瓶颈,“分选”工序次之。
问题假定70%的果子是湿的,30%是干的,则运到干果450桶/小时,湿果1050桶/小时;一天内共运到干果5400桶,湿果12600桶。
1、卡车等待问题接受工人每天7:00上班,在高峰时期,处理的工人则11:00上班,即这中间4个小时酸果运到后倾倒入贮存箱中。
干果450×4=1800桶,占7.2个贮存箱;且干果不会积压。
湿果1050×4=4200桶,但最大容量为3200桶,此时卡车需要排队等候。
湿酸果库存图(11:00开工)卡车的等待时间可以从“湿酸果库存图(11:00开工)”中看出,卡车在排队的时间是上午10:00~凌晨2:40。
通过上面的分析可知等待的卡车装载的都是湿果,干果不会堆积。
2、加班问题用分选机处理完一天运来的所有干果需要5,400/1,200=4.5(小时),即干果可以在所有工作时间内处理完。
红酸果案例更正
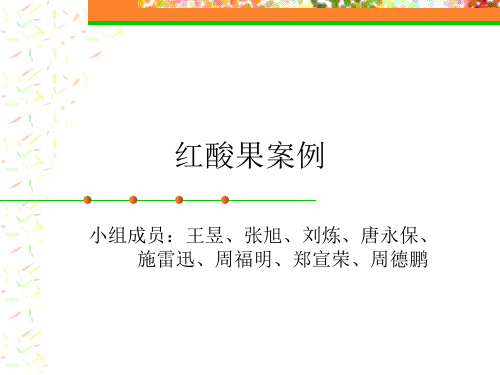
高峰期的总成本
总成本 =5654.25+3131.25+343.75+4031.25+ 4625+362.5 =18148美元
平均等待时间
6.倾倒每一辆车花费的时间是7.5分钟,车辆每隔3分钟一辆,共 有5台倾倒机,若储存箱未满,则卡车无需等待。
7.对于干果车,储存箱容量为4000桶,每小时处理量为600桶, 所以干果车不用等待。
8.对于湿果车,在时间段7点-10点,无车等待; 在时间段10点-11点内,有14辆车等待,总共时间为
14辆,数量为1050桶,干果车6辆,数量为450桶,每3分钟一 辆车(60/20),湿果车先到,干果车后到。 4. 湿果每小时处理量为600桶,干果每小时处理量为600桶。 5. 因为运来湿果的数量大于干果的数量,两者的处理速度相同, 所以用来装湿果的储存箱容量应为3200桶,而装干果的储存箱 容量为4000桶;
案例分析
倾倒机的每小时处理能力为75*5*60/7.5=3000桶(包括湿果和干 果)
储存箱:干果的储存量在4000桶(16*250)和6000桶 ( 4000+250*8 )之间;湿果的储存量在1200桶(3*400)和 3200桶( 1200+250*8 )之间;
去石子设备的每小时处理能力为4500桶(1500*3)(只处理干果) 去叶茎设备的每小时处理能力为4500桶(1500*3)(处理干果和
450
450
分
选
装运
600
ቤተ መጻሕፍቲ ባይዱ
600
平均等待时间
高峰期平均每天运来的酸果18000桶 (见附表二中sheet1、sheet2) 1. 其中湿果为12600桶,占70%;干果为5400桶,占30%: 2. 运输卡车的数量为240台(18000/75),运湿果的卡车数量为
红酸果案例
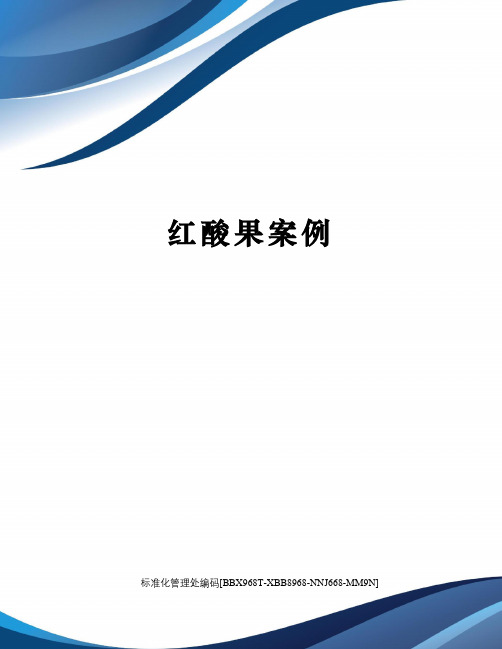
红酸果案例标准化管理处编码[BBX968T-XBB8968-NNJ668-MM9N]红酸果案例分析1、绘制红酸果处理的流程图。
主要设备产能汇总表(等待队列)2、 在高峰期此过程的瓶颈是什么工序按(9月20日~10月9日)高峰期平均每天送来酸果总量16,380桶,那么,按每天12小时工作计算,每小时酸果送达量=16,380 ÷12=1,365桶/小时。
从以上流程图可以看出,红酸果的分选(1200桶/小时),烘干(600桶/小时),都小于每小时送达量(1,365桶/小时),也与其他设备产能相差较大,因此,这两个环节首先有可能是瓶颈环节。
再看看干、湿果送达比例情况:1)由于烘干机和分选机的产能分别为600桶/小时和1200桶/小时,当湿果数在50%以下时,分选机是瓶颈工序,当湿果数量在50%以上时,烘干机是瓶颈工序。
2)在高峰期,假设每天运来酸果总数为T 桶,其中w%是湿果,分选机处理完所有红酸果的时间为S= T / 1200 (小时),烘干机处理完所有湿果的时间为D= T*w% /600 (小时)。
如果S > D,即w% < 50%,那么分选机所用时间就较长,分选机是瓶颈工序,反之,如果S < D,即w% > 50%,那么烘干机所用时间就较长,烘干机是瓶颈工序。
3)如果以高峰期某日(10月1日)为例,酸果数量为18,018桶、湿果比例69%计,则该日烘干机工作时间=18018*69%/600=21(小时),分选机工作时间=18018/1200=15(小时),显然,烘干机是瓶颈工序。
4)按照来年预测,全年湿果的比例将达到70%,那么粗略预计在来年高峰期大多数日子,烘干机是瓶颈工序。
3、计算卡车的平均等待时间截止到晚上七点,600*12=7200桶,12个小时已经处理了7200桶,12600-7200=5400桶,即还有5400桶没处理完,3200桶已装进贮存箱,2200桶还在卡车上。
红酸果案例分析

红酸果加工厂案例分析位于马萨诸塞州的“红酸果之角”加工厂过去都是加工干收法采集的酸果,但是近年来湿收法采集成为主要方式,这就给工厂过去的酸果加工程序带来了挑战。
随着湿收法的推广和普及工厂面临着下面一些问题需要解决红酸果的生产流程如下图所示:从上面图中分析可以看出整个工序的瓶颈工序为烘干,其隐含利用率为175%,所以整个工序湿收法酸果的生产能力为600 桶/小时。
每天从11 点开始不间断地加工红酸果要加工到第二天早上8 点才干彻底满足当天的需求,同时每天还需要2 个小时来清理现场和维护设备。
干果储存能力4000 桶,干果总量5400 桶。
储能能力彻底满足,无需干果卡车等待。
湿果的储存能力3200 桶,每小时到达湿果1050 桶7 点起三小时(3200/1050)以后,十点开始排队,在19 点达到顶峰,此时库存为7800,需要(7800-3200) /600=7.67 小时即最后一辆湿果卡车的卸货时间为凌晨2 点45 摆布。
最后一辆卡车等待时间为从7.67 小时。
建议一:购置两台单价为75000 美元的烘干机建议二:更换十六个单价为15000 美元的干果贮存箱,将其更换为干湿两用的贮存箱。
瓶颈工序处理能力由600 桶每小时提升到1000 桶每小时。
根据分选工序计算,新的完成加工时间为15 个小时,虽然较之前21 个小时减少6 个小时,但工人仍需加班至第二天凌晨2 点才干完成加工工作,加之2 个小时来清理现场和维护设备,凌晨四点才干完工。
近几年湿收法成为主要采收方法,去年58%,估计今年70%。
原流程本身存在问题,需要优化。
由于系统的瓶颈是烘干机,目前的生产能力是600 桶/小时,与需求有较大差距,造成工人长期加班。
从7 点卡车开始卸货,储存箱的容量逐渐被填满,此后造成卡车排队的问题。
满足来年高峰期红酸果加工的需求解决卡车排队问题解决工人的加班问题调整处理设备结构减少干果处理环节设备及人员,增加湿果处理环节设备采用倒班制两班每班工作时间8 小时,共计16 小时时长,解决瓶颈工序产能不足问题。
2014-10月红酸果

红酸果案例分析讨论提纲:1、绘制红酸果处理流程图2、高峰期的瓶颈在哪里?计算每天卡车的总等待时间?3、流程安排是否有问题?4、假设卡车等待成本是10/小时卡车,计算高峰期的总成本是多少?5、对奥布里恩的建议你怎么看?6、你对整个作业系统有什么建议?请尽量扩展思路。
1、绘制红酸果的处理流程图2、高峰期瓶颈分析,每天卡车总等待时间分析:答:因为:已知高峰期每天运来数量:18,000 桶;70% 是湿果即12,600 桶,30%是干果即5400桶。
(1)高峰期,设备的处理速度和能力分析见表-1:表-1通过上表分析得知:高峰期,完成烘干的耗时为21小时,需要在8小时外加班13小时;而完成分选的耗时为15小时需要在8小时外加班7小时,因为耗时最长的是烘干环节,所以烘干是瓶颈。
其次,倾倒机、去石子、去叶茎设备在配置上存在浪费,造成部分产能过剩。
减少部分的启动数量即可满足高峰期的处理需要。
(2)高峰期,每天卡车排队等候时间分析见表-2:表-2通过表-2得知:a)接收工人上班时间为早7:00,下班时间为次日2:40分,工作时间为19.67小时,加班11.67小时。
b)去石子、去叶茎、烘干工人上班时间为早11:00,下班时间为次日8:00分,工作时间为21小时,加班时间为13小时。
c)高峰期,卡车排队等待现象从10:03分开始,次日2:40分结束,排队等候时间持续长达16.6小时。
卡车排队等候时间=40550桶小时=40550 /75=540.67卡车小时。
d)高峰期,卡车总等待时间=卸车时间+排队等候时间=(18000/75*7.5)/60+540.67=570.67小时3、流程安排是否有问题?答:流程在以下方面存在问题:(1)除接收工序外的其他工序工人11:00上班,比接收工序的工人上班时间滞后4小时,造成了卡车等待,各工序工人加班问题严重。
高峰期,接受工人早7:00上班,比去石子、去叶茎、烘干工人上班提前了4小时,湿果的运来速度为:12600/12 = 1050 桶/小时,到11:00时已收到湿果4200桶,其中3200桶进入了贮存箱,贮存箱已满,另有1000桶湿果已经开始在卡车上等待。
生产运作与管理-红酸果案例分析
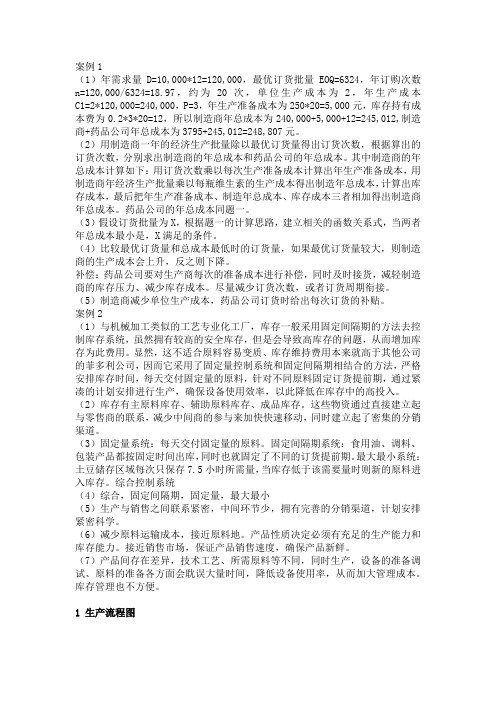
案例1(1)年需求量D=10,000*12=120,000,最优订货批量EOQ=6324,年订购次数n=120,000/6324=18.97,约为20次,单位生产成本为2,年生产成本C1=2*120,000=240,000,P=3,年生产准备成本为250*20=5,000元,库存持有成本费为0.2*3*20=12,所以制造商年总成本为240,000+5,000+12=245,012,制造商+药品公司年总成本为3795+245,012=248,807元。
(2)用制造商一年的经济生产批量除以最优订货量得出订货次数,根据算出的订货次数,分别求出制造商的年总成本和药品公司的年总成本。
其中制造商的年总成本计算如下:用订货次数乘以每次生产准备成本计算出年生产准备成本,用制造商年经济生产批量乘以每瓶维生素的生产成本得出制造年总成本,计算出库存成本,最后把年生产准备成本、制造年总成本、库存成本三者相加得出制造商年总成本。
药品公司的年总成本同题一。
(3)假设订货批量为X,根据题一的计算思路,建立相关的函数关系式,当两者年总成本最小是,X满足的条件。
(4)比较最优订货量和总成本最低时的订货量,如果最优订货量较大,则制造商的生产成本会上升,反之则下降。
补偿:药品公司要对生产商每次的准备成本进行补偿,同时及时接货,减轻制造商的库存压力、减少库存成本。
尽量减少订货次数,或者订货周期衔接。
(5)制造商减少单位生产成本,药品公司订货时给出每次订货的补贴。
案例2(1)与机械加工类似的工艺专业化工厂,库存一般采用固定间隔期的方法去控制库存系统,虽然拥有较高的安全库存,但是会导致高库存的问题,从而增加库存为此费用。
显然,这不适合原料容易变质、库存维持费用本来就高于其他公司的菲多利公司,因而它采用了固定量控制系统和固定间隔期相结合的方法,严格安排库存时间,每天交付固定量的原料,针对不同原料固定订货提前期,通过紧凑的计划安排进行生产,确保设备使用效率,以此降低在库存中的高投入。
红酸果案例分析(2班第五组)
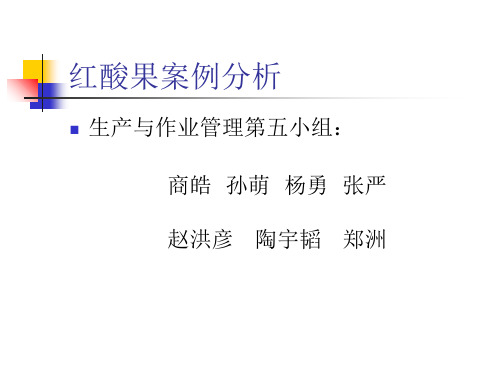
总计节省加班费用:$76125/20天
奥布里恩的建议
总节省费用为 80020+ 76125=$156145/20天
总投资为$150000,因此购置烘干 机方案可行。
奥布里恩的建议
更换储存箱成本太高,因为增加烘赶 机的方案已有效缩短了等待时间,降 低了成本,因此此时再大投入地更换 储存箱的效果(即进一步缩短卡车等 待时间、节省费用)相对较小,不是 个经济的方案,所以可以不予考虑。
每小时酸果流程
每小时流入14车 储存 烘干 每小时流出8车
余量为6车450桶
卡车平均等待时间计算
当天到达的湿果运输车共18000*0.7/75=168辆 3200÷75=42.67车(即卸完第42号车后储存箱容量即
将饱和,第43号湿果运输车于是开始等待)(注:卸 完第42号车时储存箱尚有50桶容量,为简化问题,我 们以车为单位计算等候时间,所以对这部分容量暂不 考虑);
00这12个小时内均匀到达;
卡车的平均等待时间计算
高峰期:
分析:
此时到达酸果数量为1500(18000/12)桶/小时, 即20(1500/75)车/小时,每小时到达干果6车, 计450桶;湿果14车,计1050桶;
倾倒机卸车能力:60/7.5*75*5=3000桶/小时 >1500桶/小时,可见可见该公司的卸车能力是十 分富足的;
红酸果案例分析
生产与作业管理第五小组: 商皓 孙萌 杨勇 张严 赵洪彦 陶宇韬 郑洲
红酸果处理流程图
临时储存 去石子 去叶子
干果 4000 4500
3000
接收
分选
红酸果作业参考答案

红酸果作业参考答案集团档案编码:[YTTR-YTPT28-YTNTL98-UYTYNN08]红酸果案例作业参考答案1、 绘制红酸果处理的流程图。
按(9月20日~10那么,按每天12桶/小时。
从以上流程图可以看出,红酸果的分选(1200桶/小时),烘干(600桶/小时),都小于每小时送达量(1,365桶/小时),也与其他设备产能相差较大,因此,这两个环节首先有可能是瓶颈环节。
再看看干、湿果送达比例情况:1)由于烘干机和分选机的产能分别为600桶/小时和1200桶/小时,当湿果数在50%以下时,分选机是瓶颈工序,当湿果数量在50%以上时,烘干机是瓶颈工序。
2)在高峰期,假设每天运来酸果总数为T 桶,其中w%是湿果,分选机处理完所有红酸果的时间为S= T / 1200 (小时),烘干机处理完所有湿果的时间为D= T*w% /600 (小时)。
如果S > D,即w% < 50%,那么分选机所用时间就较长,分选机是瓶颈工序,反之,如果S < D,即w% > 50%,那么烘干机所用时间就较长,烘干机是瓶颈工序。
3)如果以高峰期某日(10月1日)为例,酸果数量为18,018桶、湿果比例69%计,则该日烘干机工作时间=18018*69%/600=21(小时),分选机工作时间=18018/1200=15(小时),显然,烘干机是瓶颈工序。
4)按照来年预测,全年湿果的比例将达到70%,那么粗略预计在来年高峰期大多数日子,烘干机是瓶颈工序。
3、计算卡车的平均等待时间?截止到晚上七点,600*12=7200桶,12个小时已经处理了7200桶,12600-7200=5400桶,即还有5400桶没处理完,3200桶已装进贮存箱,2200桶还在卡车上。
在卡车上(12600-3200)÷600=15.67小时,湿果运来的速度为12600÷12=1050桶/小时积压情况:1050-600=450桶/小时,存储箱装满为3200÷450=7.11小时装满如图阴影面积即为卡车等待时间,贮存能力线于升降曲线之间。
红酸果案例分析
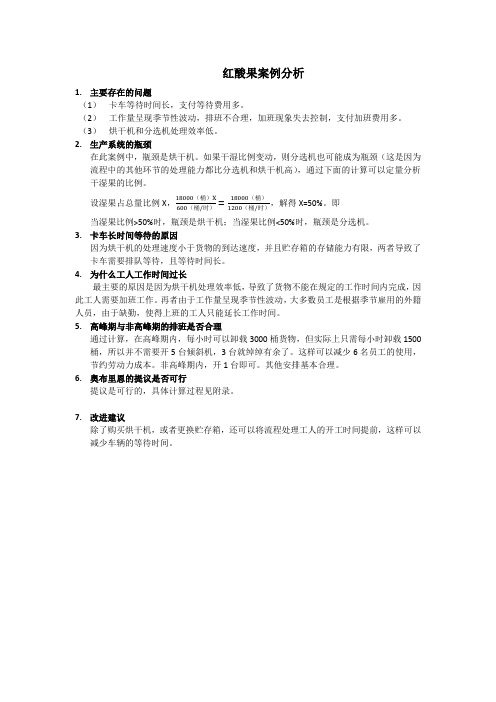
确定瓶颈后,可以将生产流程简化,看作 货车 排队 倾斜机 3000 桶/时 贮 存 3200 桶 箱 烘干机 600 桶/时
根据题目中的各参数做相应计算 一天运来的果子数量:180000 桶; 70%的湿果:126000 桶; 湿果的存储能力:3200 桶; 湿果的处理速度:600 桶/时; 早上七点开始接受,十一点开始处理; 一辆卡车等待的费用$10/时; 员工的平均工资$12.5/时,加班工资$18.75/时
下面,我们增加一台烘干机,则处理能力由 600 桶/时,变为 800 桶/时。
7000 6000 5000 4000 3000 2000 1000 0 7 12 17 22 27 4200 3200 3200 湿果存货 存储能力 6200
如上图,车辆仍然在 10:03 分开始排队等待,但是在 22:45 的时候便结束了等待,而整 个流程在凌晨 2:15 结束。所以接收工少加班 3.92 小时,其它员工少加班 5.75 小时。车辆 等待费用$2947(节省$2453),员工加班费节省$3151,共节省$5604。 由于全年只有 20 天是高峰期,其余时间不会存在等候现象,所以全年节省费用为$112080. 增加一台烘干机的费用为 75000 美元,小于节省费用,购买方案是可行的。 将干果贮存箱更换成湿果贮存箱, 第一可以减少货车等待的时间, 第二可以减少接收工加班 的时间。平均每只箱子减少接收工加班时间为 0.42 小时,节省成本 118 美元。货车等待时 间减少 27.5 辆小时,节省成本 275 美元.
(桶)X 600 (桶/时)
=
18000 (桶)
1200 (桶/时)
,解得 X=50%。即
当湿果比例>50%时,瓶颈是烘干机;当湿果比例<50%时,瓶颈是分选机。 3. 卡车长时间等待的原因 因为烘干机的处理速度小于货物的到达速度,并且贮存箱的存储能力有限,两者导致了 卡车需要排队等待,且等待时间长。 4. 为什么工人工作时间过长 最主要的原因是因为烘干机处理效率低, 导致了货物不能在规定的工作时间内完成, 因 此工人需要加班工作。 再者由于工作量呈现季节性波动, 大多数员工是根据季节雇用的外籍 人员,由于缺勤,使得上班的工人只能延长工作时间。 5. 高峰期与非高峰期的排班是否合理 通过计算,在高峰期内,每小时可以卸载 3000 桶货物,但实际上只需每小时卸载 1500 桶,所以并不需要开 5 台倾斜机,3 台就绰绰有余了。这样可以减少 6 名员工的使用, 节约劳动力成本。非高峰期内,开 1 台即可。其他安排基本合理。 6. 奥布里恩的提议是否可行 提议是可行的,具体计算过程见附录。 7. 改进建议 除了购买烘干机,或者更换贮存箱,还可以将流程处理工人的开工时间提前,这样可以 减少车辆的等待时间。
运营管理-红酸果案例分析报告
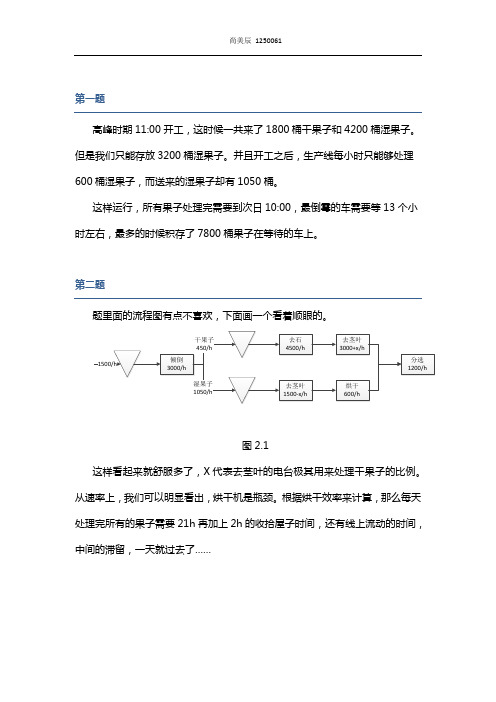
第一题高峰时期11:00开工,这时候一共来了1800桶干果子和4200桶湿果子。
但是我们只能存放3200桶湿果子。
并且开工之后,生产线每小时只能够处理600桶湿果子,而送来的湿果子却有1050桶。
这样运行,所有果子处理完需要到次日10:00,最倒霉的车需要等13个小时左右,最多的时候积存了7800桶果子在等待的车上。
第二题题里面的流程图有点不喜欢,下面画一个看着顺眼的。
图2.1这样看起来就舒服多了,X代表去茎叶的电台极其用来处理干果子的比例。
从速率上,我们可以明显看出,烘干机是瓶颈。
根据烘干效率来计算,那么每天处理完所有的果子需要21h再加上2h的收拾屋子时间,还有线上流动的时间,中间的滞留,一天就过去了……第三题烘干机:21h分选机:15h根据图2.1,烘干和分选是瓶颈第四题图4.1如果干、湿比例变成7:3那么就流程图就会变成图4.1的样子,那么只有分选过程是瓶颈。
、第五题早一点开始运行可能会减少储存箱积满导致的货车等待的可能性,在高峰期可一定程度上提早下班时间,从而少付一些员工工资。
但是挺费电的。
10-12月的低古时段,如果3点运行机器的话,晚上10:00才能完成当天的工作。
不太现实。
9月初的低谷时段,如果三点运行的话,下午7:00左右就完成工作了,还挺合理的最佳时间随接收量变化的原因是:运转机器是要付制造费用的,人工+水电其实挺贵的,所以能少开尽量少开。
于是我们根据每天的接收量计算一下生产线多久能够处理完,尽量晚开一会儿,有利于降低成本。
第六题优先考虑完成工作时间来安排生产,穷举了添加烘干机个数和改造储藏箱个数,形成了如下表格。
可以看出,添加一个烘干机比较优,由于分选机的瓶颈作用,添加第二个并不能够带来巨大的改变。
在增加0、1、2个的情况下,改变14、10、6个箱子最优。
第七题根据第一年高峰期的数据,假设湿果比例的方差和产量不变。
希望60%,80%,95%的高峰期能够在19:00,、21:00能够完成工作,货车最多等4h、2h,给出如下12组合理方案。
红酸果案例分析

红酸果案例分析学号:107119 姓名:袁龙1.解释为什么卡车要等那么长时间。
答:主要是由于湿收的果子需要经过烘干的过程,存放湿果的储存罐最多可以储存3200桶,而对湿果的烘干,三台设备同时进行,每小时也只能完成600桶,倾倒流程可以每小时处理3000桶,其中的湿果每小时有2100桶,虽然可以贮存3200桶,但是两个小时以后运来的果子就没法及时处理了,所以卡车还要等很长时间。
2. 按计划,处理酸果的工人每天工作12 个小时,另外还要加班4 个小时。
为什么会有这么长的计划外加班时间?也就是说,实际工作时间为什么会大大超过12个小时?答:工人之所以要加班还在于处理酸果的烘干过程很慢,而湿酸果又不能储存过夜,必须得当天处理完,所以尽管工人工作时间很长,但是由于烘干流程的耽误工人还会有加班。
3使用烘干机处理完一天内运来的所有湿果需要多长时间?使用分选机处理一天内运来的所有酸果又需要多长时间?根据你对这两个问题的答案,哪个或哪些工序步骤是瓶颈,也就是说它(它们)会限制物流和生产速度?答:烘干机处理完所需要的时间:18000×0.7÷(200×3)=21 小时,分选机处理完所需要的时间:18000÷(400×3)=15 小时,烘干机处理时间> 分选机处理时间,所以说烘干机烘干湿果是瓶颈。
4. 我们已经假定了每天运到的酸果有70%是湿的,有30%是干的。
如果湿果的比例有变化,那又会出现什么情况?比如,如果30%是湿的、70%是干的,又会怎样呢?哪个工序步骤是瓶颈是否会有变化呢?如果湿果的比例有变化,假如30%是湿果、70%是干果,那么去石子这道工序的压力就加大,另外,存放干果的贮藏箱就紧张,而贮藏湿果的贮藏箱就有空闲。
此时,烘干机处理完所需要的时间:18000×0.3÷(200×3)=9 小时,去石子所需要的时间:18000×0.7÷(1500×3)=2.8 小时。
运营管理红酸果案例分析
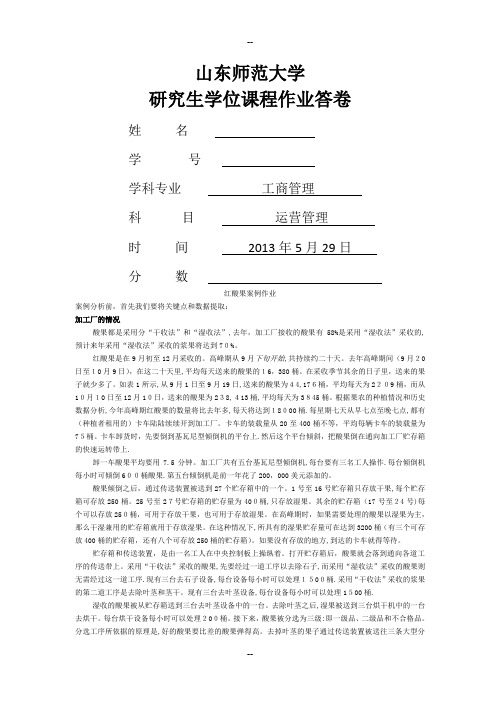
山东师范大学研究生学位课程作业答卷姓名学号学科专业工商管理科目运营管理时间2013年5月29日分数红酸果案例作业案例分析前,首先我们要将关键点和数据提取:加工厂的情况酸果都是采用分“干收法”和“湿收法”,去年,加工厂接收的酸果有58%是采用“湿收法”采收的,预计来年采用“湿收法”采收的浆果将达到70%。
红酸果是在9月初至12月采收的。
高峰期从9月下旬开始,共持续约二十天。
去年高峰期间(9月20日至10月9日),在这二十天里,平均每天送来的酸果的16,380桶。
在采收季节其余的日子里,送来的果子就少多了。
如表1所示,从9月1日至9月19日,送来的酸果为44,176桶,平均每天为2209桶,而从10月10日至12月10日,送来的酸果为238,413桶,平均每天为3845桶。
根据果农的种植情况和历史数据分析,今年高峰期红酸果的数量将比去年多,每天将达到18000桶.每星期七天从早七点至晚七点,都有(种植者租用的)卡车陆陆续续开到加工厂。
卡车的装载量从20至400桶不等,平均每辆卡车的装载量为75桶。
卡车卸货时,先要倒到基瓦尼型倾倒机的平台上.然后这个平台倾斜,把酸果倒在通向加工厂贮存箱的快速运转带上.卸一车酸果平均要用7.5分钟。
加工厂共有五台基瓦尼型倾倒机,每台要有三名工人操作.每台倾倒机每小时可倾倒600桶酸果.第五台倾倒机是前一年花了200,000美元添加的。
酸果倾倒之后,通过传送装置被送到27个贮存箱中的一个。
1号至16号贮存箱只存放干果,每个贮存箱可存放250桶。
25号至27号贮存箱的贮存量为400桶,只存放湿果。
其余的贮存箱(17号至24号)每个可以存放250桶,可用于存放干果,也可用于存放湿果。
在高峰期时,如果需要处理的酸果以湿果为主,那么干湿兼用的贮存箱就用于存放湿果。
在这种情况下,所具有的湿果贮存量可在达到3200桶(有三个可存放400桶的贮存箱,还有八个可存放250桶的贮存箱)。
如果没有存放的地方,到达的卡车就得等待。
红酸果作业参考答案

红酸果案例作业参考答案1、绘制红酸果处理的流程图;主要设备产能汇总表等待队列2、 在高峰期此过程的瓶颈是什么工序按9月20日~10月9日高峰期平均每天送来酸果总量16,380桶,那么,按每天12小时工作计算,每小时酸果送达量=16,380 ÷12=1,365桶/小时;从以上流程图可以看出,红酸果的分选1200桶/小时,烘干600桶/小时,都小于每小时送达量1,365桶/小时,也与其他设备产能相差较大,因此,这两个环节首先有可能是瓶颈环节; 再看看干、湿果送达比例情况:1由于烘干机和分选机的产能分别为600桶/小时和1200桶/小时,当湿果数在50%以下时,分选机是瓶颈工序,当湿果数量在50%以上时,烘干机是瓶颈工序;2在高峰期,假设每天运来酸果总数为T 桶,其中w%是湿果,分选机处理完所有红酸果的时间为S= T / 1200 小时,烘干机处理完所有湿果的时间为D= Tw% /600 小时;如果S > D,即w% < 50%,那么分选机所用时间就较长,分选机是瓶颈工序,反之,如果S < D,即w% > 50%,那么烘干机所用时间就较长,烘干机是瓶颈工序;3如果以高峰期某日10月1日为例,酸果数量为18,018桶、湿果比例69%计,则该日烘干机工作时间=1801869%/600=21小时,分选机工作时间=18018/1200=15小时,显然,烘干机是瓶颈工序;4按照来年预测,全年湿果的比例将达到70%,那么粗略预计在来年高峰期大多数日子,烘干机是瓶颈工序;3、计算卡车的平均等待时间截止到晚上七点,60012=7200桶,12个小时已经处理了7200桶,12600-7200=5400桶,即还有5400桶没处理完,3200桶已装进贮存箱,2200桶还在卡车上;在卡车上12600-3200÷600=小时,湿果运来的速度为12600÷12=1050桶/小时积压情况:1050-600=450桶/小时,存储箱装满为3200÷450=小时装满如图阴影面积即为卡车等待时间,贮存能力线于升降曲线之间;S阴影=5400-3200×÷2=9416桶·小时平均每辆卡车等待时间为 9416÷75=126小时;4、过程处理的安排是否有问题根据目前高峰期处理红酸果的工序从卸完货第一小时上午8点开始,到烘干工序完成需要到第二天上午6点;根据目前计划,从上午11点开始处理红酸果,那么整个烘干工序的完成时间是第二天上午8点,这会对第二天的工作进度造成影响;但在非高峰期,平均每天运行的红酸果总量,仅相当于高峰期间2小时左右运达的数量,因此将红酸果的处理工序开始时间延后,有利于充分利用设备生产能力,避免机器空转造成浪费;5、假设卡车等待成本是$10/小时卡车,计算高峰期按18000桶,70%湿果汁的总成本是多少假设卡车是均匀到达如第3题所述,按高峰期一日按18000桶,其中70%湿果计,卡车总的等待时间为126小时,按照US$10/小时计,则高峰期一日卡车等待总成本为US$1260;6、对奥布里恩的建议你怎么看奥布里恩方案针对性提出增加烘干机有助于解决瓶颈问题;1如果增加一台烘干机,产能为 3+1×200=800桶/小时按高峰期1800070%=湿果数12600÷800=小时,即从早上7:00开始工作至晚上10:45可以处理完毕;截止到晚上7:00,能处理12个小时×800=9600桶,剩余12600-9600=3000桶小于贮存容量3200桶,这样即可解决卡车等待问题,而且接收工序可在7点完成;2如果增加两台烘干机,则处理能力为3+2×200=1000桶/小时;12600÷1000=小时即可完成高峰期一天湿果的处理,可满足生产需要;3耗资240,000元改造干果贮存箱,表面上看似乎可以解决卡车长时间等候的问题,但是,由于烘干机作为瓶颈仍然未得到解决,因此生产过程中还是会因为烘干机无法及时加工完所有的湿果而产生积压;7、你对整个作业系统有什么建议1 考虑先优化过程处理时间安排,在高峰期,处理工序调整在早上7时开始;非高峰期,处理工序可调整为下午3时上班,8时前下班;2 建议购置1台烘干机,否则考虑更换1个干/湿果贮存箱;3 减少产能过剩的加工设备,比如目前生产能力盈余较多的是倾倒机、去石机、去叶茎设备,如果能卖掉2台倾倒机、2台去石机和1台去叶茎设备,所得资金可用于购置烘干机或干/湿果贮存箱;4 在高峰期可增加临时用工的投入,尽可能安排工人8小时轮班制,尽量避免加班带来的人力成本增加;5 增加的设备可以购置,也可以采用融资租赁等方式减少资金占用压力;。
MBA经典案例--红酸果的分析解答

MBA经典案例--红酸果的分析解答瓶颈分析每天运来18000桶的红酸果(1)70%的湿果,12600桶,30%的干果,有5400桶去石子的时间(干):5400桶÷4500桶/小时=1.2小时<12小时去叶茎的时间(干湿):18000桶÷4500桶/小时=4小时<12小时烘干的时间(湿):12600桶÷600桶/小时=21小时>12小时分选的时间(干湿):18000桶÷1200桶/小时=15小时>12小时此情况下烘干的过程是瓶颈(2)30%的湿果,5400桶,70%的干果,12600桶石子的时间(干):12600桶÷4500桶/小时=2.8小时<12小时去叶茎的时间(干湿):18000桶÷4500桶/小时=4小时<12小时烘干的时间(湿):5400桶÷600桶/小时=9小时<12小时分选的时间(干湿):18000桶÷1200桶/小时=15小时>12小时此情况下分选的过程是瓶颈(3)干湿果的比例为多少的时候,瓶颈分别为烘干和分选烘干机的产能效率最低,假设烘干机完全工作一天,能处理的湿果为600桶/小时×12小时=7200桶,湿果占总的比例为7200桶÷18000桶=40%所以当湿果的比例小于等于40%时,瓶颈是分选机;当比例大于40%时,瓶颈是烘干机。
讨论题1.卡车为何要等待。
要等待的原因是,当贮存箱是满的的时候,卡车就无法卸货,就要等待。
高峰期,70%的湿果,所以贮存箱用8个干/湿果贮存箱,3个湿果贮存箱,总量为3200桶。
而且,烘干机为瓶颈工序,600桶/小时,而接收湿果的速度为1050桶/小时,所以积压的WIP为1050桶/小时-600桶/小时=450桶/小时,所以卡车开始等待的时间为3200桶÷450桶/小时=7.11小时。
上午7点开始,则下午2点左右,卡车就开始等待了。
2.实际工作时间当全部的湿果接收完毕时,为(18000桶×70%-3200桶)÷600桶/小时=15.67小时。
红酸果案例分析

所以70%湿果的前提下,处理时间用的最长的是烘干工 序;
1、卡车等待的时间问题?
◦ 理论上总共接收需要的时间:
接收工作从早7点到晚7点,共12小时,从7点开始处理的话,处理 湿果共600*12=7200桶 则剩余12600-7200=5400桶湿果没有处理,这个时候储存箱中 有3200桶,那么还有2200桶仍在卡车中; 2 2200桶接收需要的时间为 2200 / 600 3 3 小时 即:需要接收到10点40分才能接收完所有的湿果;
◦ 增加一台烘干机,减少接受工序人员成本为:(3.67+2) *1.5*15*12.5=1595美元;减少的倾倒工序成本为: 3.67*1.5*3*12.5=206.4美元;另还有卡车等待成本,假设为10美 元/小时,则共(2200/75)*(12+3.67-7.11)/2=126车,1年节省 20*(1595+206.4+1260)=61228美元; ◦ 烘干机成本为75000美元,收回成本需要0.82年;
综上所述,我们建议: 1. 处理工序提前到7点开始;
2.
增加1台烘干机; 增加烘干机后,分选过程为整个工艺的瓶颈,如果成 本不是很高的情况下,增加分选线为提高产能的关键, 同时需要评估烘干机的效率,持续改进;
3.
在职一班 2013组 周承 李维娜 秦萌 岳从敏 陈海慈 陈琦 杨志豪 刘斌
问题及分析 解决方案 结论
1.
2.
3.
4.
卡车等待的问题 处理工序计划外加班 时间长的问题 处理工序开始时间太 晚(11点)是否可以 提前 工序中有没有影响效 率的瓶颈
1、以高峰期每天工作12小时不加班为标准; 2、以在12小时内处理完所有的红酸果为目标;
红酸果案例
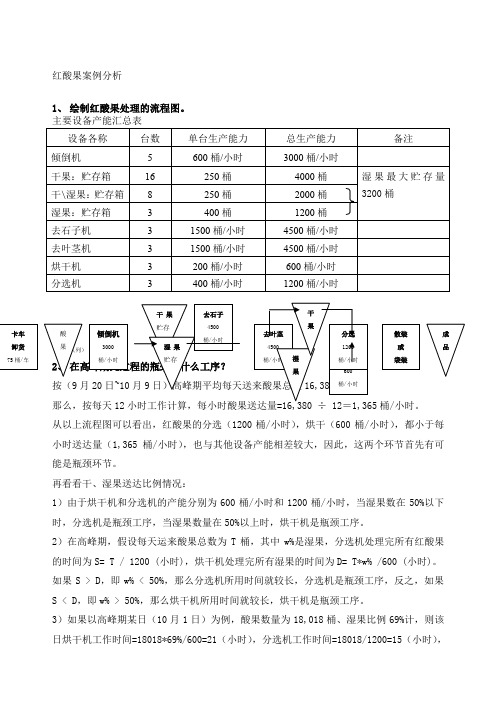
红酸果案例分析1、 绘制红酸果处理的流程图。
按(9月20日~10那么,按每天12桶/小时。
从以上流程图可以看出,红酸果的分选(1200桶/小时),烘干(600桶/小时),都小于每小时送达量(1,365桶/小时),也与其他设备产能相差较大,因此,这两个环节首先有可能是瓶颈环节。
再看看干、湿果送达比例情况:1)由于烘干机和分选机的产能分别为600桶/小时和1200桶/小时,当湿果数在50%以下时,分选机是瓶颈工序,当湿果数量在50%以上时,烘干机是瓶颈工序。
2)在高峰期,假设每天运来酸果总数为T 桶,其中w%是湿果,分选机处理完所有红酸果的时间为S= T / 1200 (小时),烘干机处理完所有湿果的时间为D= T*w% /600 (小时)。
如果S > D ,即w% < 50%,那么分选机所用时间就较长,分选机是瓶颈工序,反之,如果S < D ,即w% > 50%,那么烘干机所用时间就较长,烘干机是瓶颈工序。
3)如果以高峰期某日(10月1日)为例,酸果数量为18,018桶、湿果比例69%计,则该日烘干机工作时间=18018*69%/600=21(小时),分选机工作时间=18018/1200=15(小时),显然,烘干机是瓶颈工序。
4)按照来年预测,全年湿果的比例将达到70%,那么粗略预计在来年高峰期大多数日子,烘干机是瓶颈工序。
3、计算卡车的平均等待时间?截止到晚上七点,600*12=7200桶,12个小时已经处理了7200桶,12600-7200=5400桶,即还有5400桶没处理完,3200桶已装进贮存箱,2200桶还在卡车上。
在卡车上(12600-3200)÷600=15.67小时,湿果运来的速度为12600÷12=1050桶/小时积压情况:1050-600=450桶/小时,存储箱装满为3200÷450=7.11小时装满如图阴影面积即为卡车等待时间,贮存能力线于升降曲线之间。
红酸果案例讨论分析A1

红酸果案例讨论分析针对《运营管理》中提到的“红酸果案例”,我们小组通过认真、仔细的讨论,就该案例的相关问题进行了如下分析:数据分析:A、根据案例中提供的去年高峰期间每天送到工厂的红酸果数量计算,高峰期平均每天的总量为16380桶,其中湿果占48.43%,干果占51.57%,单日总量最多为18879桶(9月24日),单日湿果数量最多为12432桶(占69%,10月1日)。
如表一所示:B、以案例中提到的今年高峰期情况,运达数量18000桶,其中70%为湿果,30%为干果,则平均每小时运达的数量为1500桶,其中,湿果1050桶,干果450桶。
C、该厂目前的加工能力为(参见第3页流程图):接收3000桶/小时,去石子4500桶/小时,去叶茎4500桶/小时(其中干果3000桶/小时,湿果1500桶/小时),湿果烘干600桶/小时(占每小时运达湿果数量的57%),分选1200桶/小时(占每小时运达红酸果数量的80%)。
高峰期数据表一:去年高峰期数据问题1、绘制红酸果处理的流程图:3000桶/小时问题2、在高峰期此过程的瓶颈是什么工序?从上述流程图上不难发现,工厂大部分配置的生产能力高于实际工作的需求,但是存在两个环节严重延缓了工序的进展:一是湿果烘干每小时仅600桶,根据表一数据显示,去年高峰期内,平均每天运达的湿果数量为:7969桶,每天必须工作13.3小时才能完成全部工作;二是分选每小时1200桶,根据表一数据显示,去年高峰期内,平均每天运达的红酸果总数量为:16380桶,每天必须工作13.7小时才能完成全部工作。
这两个环节完成的时间均超过其他工序每天正常完成的时间,因此,我们认为案例中加工过程存在的瓶颈工序是:烘干和分选。
问题3、计算卡车的平均等待时间是多少?表二去年红酸果平均送达数据根据案例中给出的信息,去年高峰期时,工厂各环节的处理数据如下: A 由于卡车早上7点开始运达,除接收工序以外的工人中午11点开始上班,因此在除接收工序以外的工人上班以前的4个小时内,一共运达的红酸果数量为:16380/12 *4=5460桶,其中湿果数量为:5460*48.56%=2651桶.工厂的接收储存能力为:总数量7200桶,其中湿果的最大接收储存能力为:3200桶.因此,该阶段,卡车不存在等候情况.B 去年高峰期, 除接收工序以外的工人开始上班后,生产的瓶颈在于烘干和分选,其中分选完成全天工作的时间长于烘干工序,是现有状态下最大的瓶颈,因此,以分选工序的处理能力进行卡车等候时间的分析,从中午11点到下午7点之间,接收环节每小时新增储存的红酸果数量为:16380/12-1200=165桶.一共165*8=1320桶.连同中午11点以前,接收环节储存的红酸果5460桶,一共为6780桶,小于接收环节的最大储存能力7200桶,因此,在此阶段,卡车也不存在等候现象.同样,以烘干环节处理能力进行分析, 从中午11点到下午7点之间,接收环节每小时新增储存的湿果数量为:7969/12-600=64桶,一共64*8=512桶, 连同中午11点以前,接收环节储存的湿果2651桶,一共为3163桶,小于接收环节湿果的最大储存能力3200桶, 卡车也不存在等候现象.C 工厂卡瓦基型倾倒机的处理能力为3000桶/小时,远大于高峰期每小时运达的红酸果数量16380/12=1365桶.综上,去年高峰期,卡车并不存在排队等待现象.问题4、处理过程中的安排是符有问题?在去年高峰期时段,烘干工序每天需要13.3小时才能完成工作,分选工序每天需要13.7小时才能完成工作,这主要是由于这两个工序中,设备能力的限制造成的.在去年非高峰期间,如表二所示: 9月1日—9月19日,平均每天运来2209桶,其中湿果1193桶.平均每小时接收红酸果184桶,其中湿果100桶。
- 1、下载文档前请自行甄别文档内容的完整性,平台不提供额外的编辑、内容补充、找答案等附加服务。
- 2、"仅部分预览"的文档,不可在线预览部分如存在完整性等问题,可反馈申请退款(可完整预览的文档不适用该条件!)。
- 3、如文档侵犯您的权益,请联系客服反馈,我们会尽快为您处理(人工客服工作时间:9:00-18:30)。
数据分析根据案例中提供的去年高峰期间每天送到工厂的红酸果数量计算,高峰期平均每天的总量为16380桶,其中湿果占48.43%,干果占51.57,单日总量最多为18879桶(9月24日),单日湿果数量最多为12432桶(占69%,10月1日)。
案例中假定的数字:每天运达数量18000桶,其中70%为湿果,30%为干果,则平均每小时运达的数量为1500桶,其中湿果1050桶,干果450桶。
该厂目前的加工能力为(参见第4页流程图):接收3000桶/小时,去石子4500桶/小时,去叶茎4500桶/小时(其中干果3000桶/小时,湿果1500桶/小时),湿果烘干600桶/小时(占每小时运达湿果数量的57%),分选1200桶/小时(占每小时运达红酸果数量的80%)。
问题1不难发现,工厂大部分配置的生产能力高于实际工作的需求,但是存在两个环节严重延缓了工序的进展:一是湿果烘干每小时仅600桶,即每天必须工作21小时才能完成全部工作;二是分选每小时1200桶,即每天必须工作15小时才能完成全部工作。
这两个环节中以烘干对整个工序的制约最大,也正是这个环节导致前面工序产生红酸果的积压,从而使卡车长时间等待。
问题2与上题相联系,由于整个工序中湿果烘干的步骤构成了瓶颈,必须用21个小时才能处理完所有的湿果,所以使得实际工作时间远远超过12小时。
问题3使用烘干机处理完一天内运来的所有湿果需要21小时,使用分选机理完一天内运来的所有红酸果需要15小时,我认为这两个步骤构成了整个工序的瓶颈,其中烘干机对整个流程的阻碍作用要大于分选机,只有使烘干机达到每小时1050桶(即6台机器)的生产能力,分选机达到每小时1500桶(即4台机器)的生产能力,才能保证工作流程不产生积压。
问题4假如湿果比例为30%(即450桶),干果比例为70%(即1050桶),则烘干机能跟上工作流程,而分选机依然无法满足需要,此时,构成瓶颈的就是分选机。
按照目前工厂的设备配置情况,只有当湿果比例不高于40%的情况下,烘干机才能满足生产的需要,不构成瓶颈。
问题5时间安排上,假如高峰时期处理红酸果的工序从上午8点(即卸完第一个小时的货)开始,则整个烘干工序的完成时间是第二天上午6点;根据目前的工作计划,从上午11点开始处理红酸果,则整个烘干工序的完成时间是第二天上午8点,这将影响到第二天的工作开展。
从目前的情况来看,在高峰期,即使红酸果的处理工序从上午8点开始,等到一天的工作完成,也已经要到第二天上午8点之后,再加上打扫卫生维护设备的两个小时,第二天的工作也必定受到影响。
非高峰期平均每天运达的红酸果总量,仅相当于高峰期间2小时左右运达的数量,因此将红酸果的处理工序开始时间延后,有利于充分利用设备生产能力,避免机器空转造成浪费。
问题6奥布里恩提出的方案,看到了烘干机对整个生产过程的阻碍作用,因此提出增加烘干机,有助于问题的解决。
增加一个烘干机,可以使每小时的生产能力提高到800桶,占每小时运达湿果数量的76%,即用15.75小时就可以完成一天中所有湿果的加工。
假如增加两个烘干机,可以使每小时的生产能力提高到1000桶,占每小时运达湿果数量的95%,即用12.6小时就可以完成一天中所有湿果的加工,基本可以满足生产的需求。
而耗资240000元改造干果贮存箱,表面上看似乎可以解决卡车长时间等候的问题,但是,由于烘干机作为瓶颈仍然未得到解决,因此生产过程中还是会因为烘干机无法及时加工完所有的湿果而产生积压。
问题7由于农产品的产量在一定时期是相对稳定的,因此,我们制订整个生产流程和计划的时候,从目前的最大数量进行考虑,就能够满足一定时期内的生产需要了。
要解决工厂面临的问题,我认为需要从以下四个方面着手:1、减少产能过剩的加工设备。
目前生产能力盈余较多的有倾倒机、去石子设备、去叶茎设备,可以卖掉两台倾倒机、两套去石子设备和一套去叶茎设备,所得的资金可用于购置烘干机、分选机等设备或作他用。
2、增加产能不足的瓶颈部位加工设备。
需增加三台烘干机和一台分选机,这样使产能相对于目前要求的最大值稍大。
增加的设备可以购置,也可以采用租赁等方式。
通过对设备的增减,可以优化工作流程,提高设备的使用率,请参见第5页的流程图。
3、加强对工人的培训,努力提高其工作效率。
每年高峰期到来之前,应至少培训一个星期,使其熟悉操作规程和设备的运用。
4、改进临时用工的措施,尽量与临时雇工形成较为长期的合作关系;制订严格的制度,减少缺勤率,使临时用工对生产的负面影响尽量降低。
红酸果之角”加工厂是当地数百个种植者合办的一个加工厂。
红酸果采收的高峰期从每年的9月下旬开始,持续大约二十天。
红酸果的采收方法有“干收法”和“湿收法”两种。
根据果农的种植情况和历史数据分析,今年高峰期红酸果的数量将比去年多,每天将达到18000桶。
红酸果“湿收法”所占的比例今年将达到总量的70%。
“湿果”的加工工序有:装卸-- 临时储存--去茎叶--烘干--分选--包装。
“干果”的加工工序有装卸--临时储存--去石子--去茎叶--分选--包装。
卸一车酸果的平均时间是7.5分钟。
工厂共有27个储存箱,1号至16号只存放干果,的容量是250桶;25号至27号只存放湿果,容量是400桶;17号至24号可存放干果也可存放湿果。
可存湿果3200桶。
共有5台装卸机,总处理能力为3000桶/每小时。
去石子机只处理干果,共3台,总处理能力为4500桶/小时。
去叶茎设备同时处理干果和湿果,共3台,总处理能力为1500桶/小时。
烘干机只处理湿果,共3台,总处理能力为600桶/小时。
分选机同时处理干果和湿果,共3台,总处理能力为1200桶/小时。
工人平均工资是12.50美圆/小时,8小时之外工厂要多付50%。
雇佣工人数量可根据季节调整雇佣去年的情况是:旺季时由于设备的生产能力有限,造成种植者的卡车等候的时间过久,加班时间过长。
红酸果案例作业参考答案21、绘制红酸果处理的流程图。
2、在高峰期此过程的瓶颈是什么工序?按(9月20日~10月9日)高峰期平均每天送来酸果总量16,380桶,那么,按每天12小时工作计算,每小时酸果送达量=16,380 ÷12=1,365桶/小时。
从以上流程图可以看出,红酸果的分选(1200桶/小时),烘干(600桶/小时),都小于每小时送达量(1,365桶/小时),也与其他设备产能相差较大,因此,这两个环节首先有可能是瓶颈环节。
再看看干、湿果送达比例情况:1)由于烘干机和分选机的产能分别为600桶/小时和1200桶/小时,当湿果数在50%以下时,分选机是瓶颈工序,当湿果数量在50%以上时,烘干机是瓶颈工序。
2)在高峰期,假设每天运来酸果总数为T桶,其中w%是湿果,分选机处理完所有红酸果的时间为S= T / 1200 (小时),烘干机处理完所有湿果的时间为D= T*w% /600 (小时)。
如果S > D,即w% < 50%,那么分选机所用时间就较长,分选机是瓶颈工序,反之,如果S < D,即w% > 50%,那么烘干机所用时间就较长,烘干机是瓶颈工序。
3)如果以高峰期某日(10月1日)为例,酸果数量为18,018桶、湿果比例69%计,则该日烘干机工作时间=18018*69%/600=21(小时),分选机工作时间=18018/1200=15(小时),显然,烘干机是瓶颈工序。
4)按照来年预测,全年湿果的比例将达到70%,那么粗略预计在来年高峰期大多数日子,烘干机是瓶颈工序。
3、计算卡车的平均等待时间?截止到晚上七点,600*12=7200桶,12个小时已经处理了7200桶,12600-7200=5400桶,即还有5400桶没处理完,3200桶已装进贮存箱,2200桶还在卡车上。
在卡车上(12600-3200)÷600=15.67小时,湿果运来的速度为12600÷12=1050桶/小时积压情况:1050-600=450桶/小时,存储箱装满为3200÷450=7.11小时装满如图阴影面积即为卡车等待时间,贮存能力线于升降曲线之间。
S阴影=(5400-3200)×(15.67-7.11)÷2=9416桶·小时平均每辆卡车等待时间为9416÷75=126小时。
4、过程处理的安排是否有问题?根据目前高峰期处理红酸果的工序从卸完货第一小时(上午8点)开始,到烘干工序完成需要到第二天上午6点。
根据目前计划,从上午11点开始处理红酸果,那么整个烘干工序的完成时间是第二天上午8点,这会对第二天的工作进度造成影响。
但在非高峰期,平均每天运行的红酸果总量,仅相当于高峰期间2小时左右运达的数量,因此将红酸果的处理工序开始时间延后,有利于充分利用设备生产能力,避免机器空转造成浪费。
5、假设卡车等待成本是$10/小时卡车,计算高峰期(按18000桶,70%湿果汁)的总成本是多少?(假设卡车是均匀到达)如第3题所述,按高峰期一日按18000桶,其中70%湿果计,卡车总的等待时间为126小时,按照US$10/小时计,则高峰期一日卡车等待总成本为US$1260。
6、对奥布里恩的建议你怎么看?奥布里恩方案针对性提出增加烘干机有助于解决瓶颈问题。
1)如果增加一台烘干机,产能为(3+1)×200=800桶/小时按高峰期(18000*70%=)湿果数12600÷800=15.75小时,即从早上7:00开始工作至晚上10:45可以处理完毕。
截止到晚上7:00,能处理12个小时×800=9600桶,剩余12600-9600=3000桶小于贮存容量3200桶,这样即可解决卡车等待问题,而且接收工序可在7点完成。
2)如果增加两台烘干机,则处理能力为(3+2)×200=1000桶/小时。
12600÷1000=12.6小时即可完成高峰期一天湿果的处理,可满足生产需要。
3)耗资240,000元改造干果贮存箱,表面上看似乎可以解决卡车长时间等候的问题,但是,由于烘干机作为瓶颈仍然未得到解决,因此生产过程中还是会因为烘干机无法及时加工完所有的湿果而产生积压。
7、你对整个作业系统有什么建议?1) 考虑先优化过程处理时间安排,在高峰期,处理工序调整在早上7时开始;非高峰期,处理工序可调整为下午3时上班,8时前下班;2) 建议购置1台烘干机,否则考虑更换1个干/湿果贮存箱;3) 减少产能过剩的加工设备,比如目前生产能力盈余较多的是倾倒机、去石机、去叶茎设备,如果能卖掉2台倾倒机、2台去石机和1台去叶茎设备,所得资金可用于购置烘干机或干/湿果贮存箱;4) 在高峰期可增加临时用工的投入,尽可能安排工人8小时轮班制,尽量避免加班带来的人力成本增加;5) 增加的设备可以购置,也可以采用融资租赁等方式减少资金占用压力。