OEE记录表格(设备综合效率)
设备综合效率(OEE)计算表

#D I#VD I#VD I#VD I#VD I#VD IV 0
#D I#VD I#VD I#VD I#VD I#VD IV 0
#D I#VD I#VD I#VD I#VD I#VD IV 0
#D I#VD I#VD I#VD I#VD I#VD IV 0
#D I#VD I#VD I#VD I#VD I#VD IV 0
#D I#VD I#VD I#VD I#VD I#VD IV 0
#D I#VD I#VD I#VD I#VD I#VD IV 0
#D I#VD I#VD I#VD I#VD I#VD IV 0
#D I#VD I#VD I#VD I#VD I#VD IV 0
#D I#VD I#VD I#VD I#VD I#VD IV 0
XXXX 有限
设 备 效 率(OEE) 计 算 表
设备编号: 日期
总工作时间
设备名称:
日 期:
年
月
1
2
3
4
5
6
7
8
9
10
11
12
13
14
15
16
17
18
19
20
21
22
23
24
25
26
27
28
29
30
31
全月总 计
0
点检保养
0
计划 工间休息
0
停止
时间 计划维修
0
停产调整
0
负荷时间
0000000000000000000000000000000 0
实际生产周期
######
时间运行效率
速度运行效率
设备综合效率oee计算表 (1)
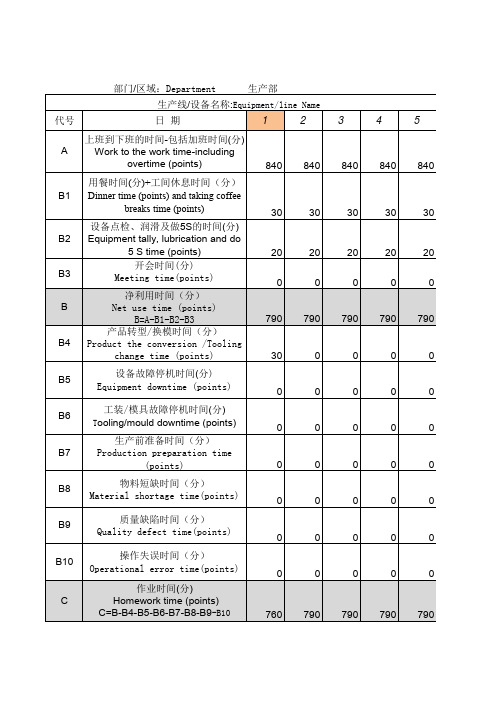
11600 12900
5000
0 14800 18900 7500 17560 16500 17500
0.057 0.045
0.062
0 0.075 0.07 0.097 0.07 0.07 0.07
72.7% 92.1% 96.9% #DIV/0! 86.7% 95.9% 90.9% 96.0% 90.2% 95.7%
320
0 1280 1400 800 1280 1280 1280
0
0
0
0
0
20
0
0
0
0
0
0
0
0
0
0
0
0
0
0
0
0
0
0
0
0
0
0
0
0
0
0
0
0
0
0
0
0
0
0
0
0
0
0
0
0
0
0
0
0
0
0
0
0
0
0
0
0
0
0
0
0
0
0
0
0
0
0
0
0
910 630
320
0 1280 1380 800 1280 1280 1280
100.0% 100.0% 100.0% #DIV/0! 100.0% 98.6% 100.0% 100.0% 100.0% 100.0%
26
27
28
29
30
6月 31 综合
1320 1320 1320 1320 1320
0 30540
设备综合效率OEE统计报表填写指引
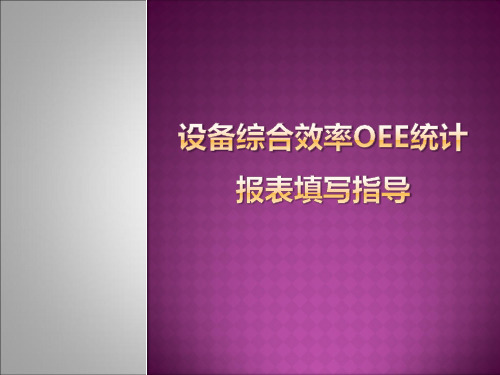
设备开动过程中由于生产不合格品所占用的时间。
几个时间的关系:
日历时间=负荷时间+非设备因素休止时间; 负荷时间=开动时间+停机损失时间; 开动时间=净开动时间+降速损失时间; 净开动时间=价值开动时间+质量损失时间。
几个“率”的概念: 设备利用率:
在整个日历时间中去除休止时间后的可利用时间(即负荷时间)所 占的比例。 设备利用率﹦(日历时间-非设备因素休止时间)÷日历时间
调整点位置关系,如研究标线的设置,调试标准化研究等。
(五)空转造成的时间损失
包括: 1、无输入导致空转; 2、启动、停止缓慢过程导致的空转; 3、调整导致的空转。 应对措施: 1、减少设备短暂停机的频次; 2、通过技术攻关,减少设备空转试运行时间。 3、联动线的匹配设计应充分考虑、输入机构设计要充分考虑,
2、建立设备故障解决预案,通过技术积累、理论指导实践,提 高维修人员的技术水平及解决故障的能力,从而减少故障恢 复时间。
(四)设备调整造成的时间损失
包括: 1、设备模具、规格件的更换; 2、调试; 3、精度、公差调整。 应对措施: 1、操作人员的技能培训; 2、开展技术研究,对设备调整点进行重点攻关,如研究包材与
几个难点讨论:
实际速度能不能大于设计速度? 预防性维修与设备故障、调整如何界定? 空转为什么要用公式推导? 当天没有生产如何记录? 辅Βιβλιοθήκη 记录设施如何设计? 联动线如何计算?
OEE、TEEP统计意义:通过数据分析,指导解 决生产过程中的八大损失!
八大损失:
(一)计划性停机造成的停机损失; (二)外部因素造成的时间损失; (三)设备故障造成的时间损失; (四)设备调整造成的时间损失; (五)空转造成的时间损失; (六)速度降低造成的时间损失; (七)废品造成的时间损失; (八)试产期产品缺陷造成的时间损失;
设备综合效率OEE统计表
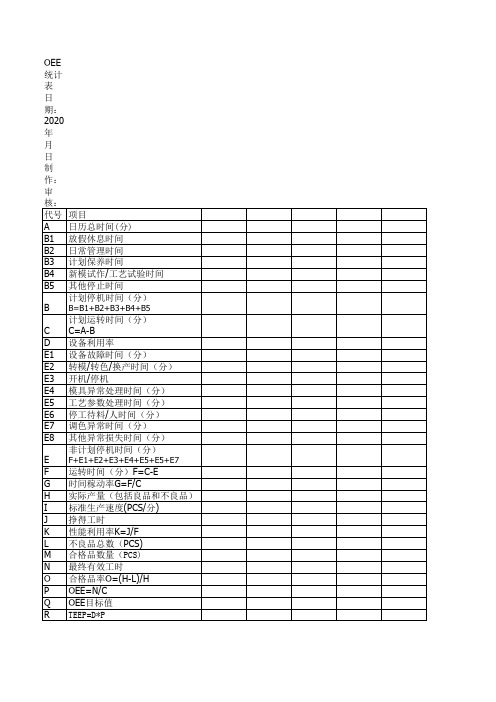
2020 年 月 日 制 作: 审 核: 代号 项目 A 日历总时间(分) B1 放假休息时间 B2 日常管理时间 B3 计划保养时间 B4 新模试作/工艺试验时间 B5 其他停止时间
计划停机时间(分) B B=B1+B2+B3+B4+B5
计划运转时间(分)
C C=A-B D 设备利用率 E1 设备故障时间(分) E2 转模/转色/换产时间(分) E3 开机/停机 E4 模具异常处理时间(分) E5 工艺参数处理时间(分) E6 停工待料/人时间(分) E7 调色异常时间(分) E8 其他异常损失时间(分)
P OEE=N/C Q OEE目标值 R TEEP=D*P
合计
ห้องสมุดไป่ตู้
非计划停机时间(分) E F+E1+E2+E3+E4+E5+E5+E7 F 运转时间(分)F=C-E G 时间稼动率G=F/C H 实际产量(包括良品和不良品) I 标准生产速度(PCS/分) J 挣得工时 K 性能利用率K=J/F L 不良品总数(PCS) M 合格品数量(PCS) N 最终有效工时 O 合格品率O=(H-L)/H
生产综合效率OEE报表

开机时间 (min)
良品数
不良 数
生产数 量
良品率%
早会 定保 其他
小计
换模
机械 故障
模具 故障
异 常
停 工
0 审核:0 0 0 源自 0 0 0 00文件编号/Dc.No.:DG-PD-Form-14 A/1
时间记录(min)
时间运转率 性能运转率 设备综合效
其 他
小计
(%)
(%)
率(%)
备注
00
核准:
部门: 日期 机台
组别:
模具/ 班次 工单号
生产数据 料号
□ 白班
标准工时
总出勤时间
模穴
标准周 期
开机起 完成生 始时间 产时间
小计
制表: 计算 方 时间 运转 性能 运转 设备 综合 良品 率=良
审核
生产综合效率报表
□ 夜班
总出勤时间
产量记录(PCS)
计划停机时间(Min)
无效停机时间记录(min)
oee设备综合效率表格

oee设备综合效率表格篇一:oee设备综合效率二种叫法和计算公式并举例子oee (设备综合效率)是衡量设备综合性时间损失大小的指标,反应设备在负荷时间内有多少时间是有价值的开动时间。
叫法之一:oee=时间开动率x性能开动率x良品率即:(1)〔时间开动率〕:是衡量测定因故障、准备、调整等导致停止损失大小的指标。
时间开动率=(负荷时间一停止时间)/负荷时间*100%(2)〔性能开动率〕:是衡量因空转、小停工及速度降低等导致时间损失大小的指标。
性能开动率=(基准节拍*产量)/开动时间*100%(3)〔良品率〕:是衡量保证充分满足消费者质量要求的指标。
良品率二合格品件数/生产总件数*100%叫法之二:oee=时间利用率*设备性能率*产品合格率=(合格的产品*设计速度)/负荷时间1. 时间利用率=(负荷时间-停机损失)/负荷时间*100%=(有效)利用时间/负荷时间2. 设备性能率=(生产产品数*设计速度)/利用时间*100%3. 质量合格率=(生产产品数-不合格品)/生产产品数*100%其实:设计速度即基本节拍工厂/车间的设备综合效率=(1#设备综合效率*产量+2#设备综合效率*产量+…+n#设备综合效率*产量)+总产量叫法之三:oee=可使用率x工作表现率x品质率1. 可使用率:指实际运转时间与可用时间(负荷时间)之比。
(1)可用时间:指从一天(或一个月)的工作时间中,减去生产计划、计划保养,以及日常管理上必要的的停顿时间后所剩下的时间。
(2)停机时间(停止时间):指因故障、setup、调整、更换模具等所停止的时间。
(3)公式:可使用率=(可用时间-停机时间)/可用时间x100%2. 工作表現率包括速度运转率与纯运转率。
(1)速度运转率系指设备原有这能力(包括周期时间、循环数)对实际速度之比;纯运转率指在单位时间内设备有无以一定速度在运转,由此可以求得日报上无法出现的小故障损失。
(2)工作表现率二速度运转率x有效运转率=理想周期x 加工数量*(负荷时间-停止时间)3. 品质率:品质率系指实际制成之良品数量与加工数量的比率。
设备综合效率教材OEE资料
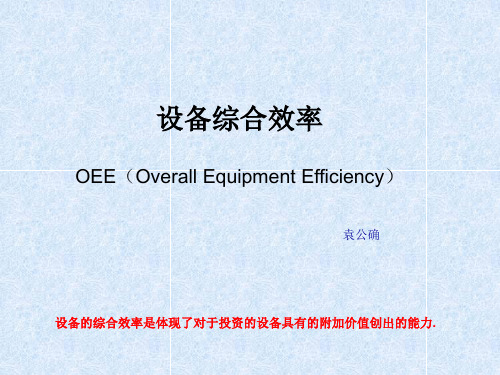
OEE(Overall Equipment Efficiency)
袁公确
设备的综合效率是体现了对于投资的设备具有的附加价值创出的能力.
目录
一、 设备 损失结构
二、 设备 综合效率的算出基准和术语定义
三、 设备综合效率的算出示例
四、 OEE数据表填写
五、 OEE改善步骤(STEP)
一、 设备 损失结构
9
现状 把握
(OEE数 据表填写收集)
A P
标准化 固化措施
8
4
C
7
设定 目标
D
6
5W2H,5W法
④ 性能效率 : 速度运转效率和纯运转率相乘得出的现场部门设备的利用度. 性能效率 = 速度运转效率 × 纯运转率 = 理论C/T × 生产数量 操作时间 × 100 (%)
⑤ 良品率 : 相对于投入的数量良品数量所占的比率. 良品是投入的数量中除去初期开始的不良, 工程内的不良, 不良修理品(再作业)后剩余的. 良 品 率= 良品数量 投入数量 – 不良数量 × 100 = 投入数量 投入数量 × 100 (%)
0 0 XX XX XX XX XX
0 0 XX XX XX XX XX
0 0 XX XX XX XX XX
0 0 XX XX XX XX XX
0 0 XX XX XX XX XX
10:00-12:00 450侧板 12:00-14:00 14:00-16:00 16:00-18:00 18:00-20:00
⑥ 休止时间 : 作业时间中由于设备的非加动而引发的 LOSS时间 (与设备的机能无关 停止的时间) a、会议, 早会 : 作业中因计划或必需的会议及早会而使设备停止的时间 (例 : 月例早会, 参加活动, 故障, 车间, 班长早会, 小组) b、 教育, 训练 : 公司认定的社内 ·外教育和训练必须参加而引起的设备停止时间 (例 : 社外教育, 社内教育, 预备役, 民兵训练等) c、 停电(断水) : 电力供给(断水) 中断引起的设备不能加动的时间 d、 待料 : 生产过程中由于资材的品质问题或资材供应异常引起的生产不能持续进行导致设备停止的时间 (事前预估) ⑦ 停止时间 : 由于以下的原因而引起的设备不能加动的时间 a、 机器故障 : 偶然发生的机器故障引起的设备不能生产的时间 b、 换型 : 资材不良, 品质等偶然发生的因素或依据生产计划 Model 变更时发生的设备停止时间 c、 准备, 调整 : 制品生产结束时或开始时工具类的调整, 整理, 清扫等相关的作业引发的停止时间 d、 瞬间停止, 空转 : 运输带上的制品阻塞,或者工作台上的加工品挂住的工程, 或检查装置自动 停止的时间 (故障和导致 问题发生原因 的清除, 插入, 开关 ON等简单操作原状的恢复) e、 资材不良 : 不良资材引起的投入前的选取 ·修理或生产过程中修正导致设备停止的情况 f、 不良再作业 : 品质水准, 式样等没有达成 不合格的制品修理和中间检查后修理作业需要的设备加动时间 g、 工程不均衡 : 前 ·后工程(或者前 ·后设备)中由于别的因素引起的作业停止或者担当设备后工程(设备)的 生产数量或者目标量已达成而停止情况的时间 h、待料:非预估性的物料短缺或物料出现品质不良造成停机。 j、 其 它 : 由以上原因以外的原因引发的设备停止时间 ⑧ 理论 Cycle Time : 设备生产公司提示的或者设备设置后最佳的状态下单位产品的生产所需要的时间. ⑨ 实际 Cycle Time : 作业环境和限制条件等发生影响后实际操作时得到的结果上平均使用的加动速度.
OEE计算表(附实例讲解)
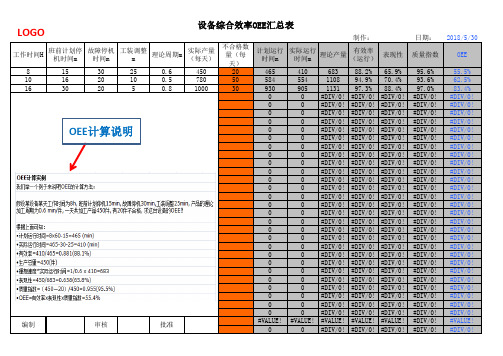
制作:日期:2018/5/30工作时间H 班前计划停机时间m 故障停机时间m 工装调整m 理论周期m实际产量(每天)不合格数量(每天)计划运行时间m 实际运行时间m 理论产量有效率(运行)表现性质量指数OEE 81530250.64502046541068388.2%65.9%95.6%55.5%101620100.578050584554110894.9%70.4%93.6%62.5%16302050.8100030930905113197.3%88.4%97.0%83.4%00#DIV/0!#DIV/0!#DIV/0!#DIV/0!#DIV/0!00#DIV/0!#DIV/0!#DIV/0!#DIV/0!#DIV/0!00#DIV/0!#DIV/0!#DIV/0!#DIV/0!#DIV/0!00#DIV/0!#DIV/0!#DIV/0!#DIV/0!#DIV/0!00#DIV/0!#DIV/0!#DIV/0!#DIV/0!#DIV/0!00#DIV/0!#DIV/0!#DIV/0!#DIV/0!#DIV/0!00#DIV/0!#DIV/0!#DIV/0!#DIV/0!#DIV/0!00#DIV/0!#DIV/0!#DIV/0!#DIV/0!#DIV/0!00#DIV/0!#DIV/0!#DIV/0!#DIV/0!#DIV/0!00#DIV/0!#DIV/0!#DIV/0!#DIV/0!#DIV/0!00#DIV/0!#DIV/0!#DIV/0!#DIV/0!#DIV/0!00#DIV/0!#DIV/0!#DIV/0!#DIV/0!#DIV/0!00#DIV/0!#DIV/0!#DIV/0!#DIV/0!#DIV/0!00#DIV/0!#DIV/0!#DIV/0!#DIV/0!#DIV/0!00#DIV/0!#DIV/0!#DIV/0!#DIV/0!#DIV/0!00#DIV/0!#DIV/0!#DIV/0!#DIV/0!#DIV/0!00#DIV/0!#DIV/0!#DIV/0!#DIV/0!#DIV/0!00#DIV/0!#DIV/0!#DIV/0!#DIV/0!#DIV/0!00#DIV/0!#DIV/0!#DIV/0!#DIV/0!#DIV/0!00#DIV/0!#DIV/0!#DIV/0!#DIV/0!#DIV/0!00#DIV/0!#DIV/0!#DIV/0!#DIV/0!#DIV/0!00#DIV/0!#DIV/0!#DIV/0!#DIV/0!#DIV/0!00#DIV/0!#DIV/0!#DIV/0!#DIV/0!#DIV/0!00#DIV/0!#DIV/0!#DIV/0!#DIV/0!#DIV/0!00#DIV/0!#DIV/0!#DIV/0!#DIV/0!#DIV/0!00#DIV/0!#DIV/0!#DIV/0!#DIV/0!#DIV/0!00#DIV/0!#DIV/0!#DIV/0!#DIV/0!#DIV/0!#VALUE!#VALUE!#VALUE!#VALUE!#VALUE!#DIV/0!#VALUE!0#DIV/0!#DIV/0!#DIV/0!#DIV/0!#DIV/0!设备综合效率OEE汇总表编制审核批准OEE 计算说明LOGO。
oee计算公式 excel
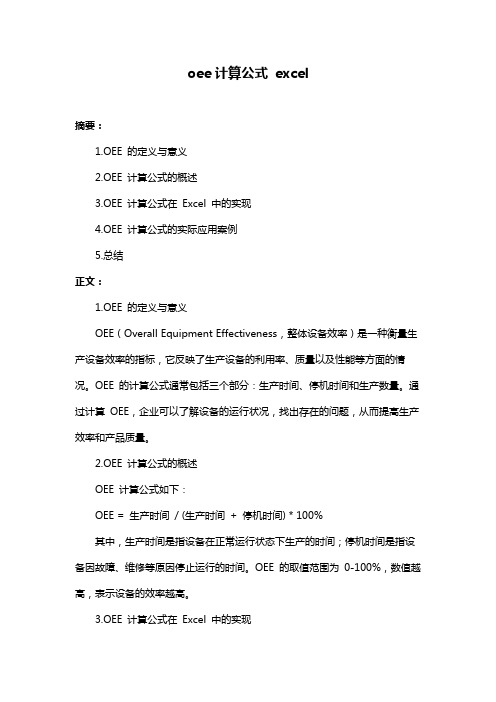
oee计算公式excel摘要:1.OEE 的定义与意义2.OEE 计算公式的概述3.OEE 计算公式在Excel 中的实现4.OEE 计算公式的实际应用案例5.总结正文:1.OEE 的定义与意义OEE(Overall Equipment Effectiveness,整体设备效率)是一种衡量生产设备效率的指标,它反映了生产设备的利用率、质量以及性能等方面的情况。
OEE 的计算公式通常包括三个部分:生产时间、停机时间和生产数量。
通过计算OEE,企业可以了解设备的运行状况,找出存在的问题,从而提高生产效率和产品质量。
2.OEE 计算公式的概述OEE 计算公式如下:OEE = 生产时间/ (生产时间+ 停机时间) * 100%其中,生产时间是指设备在正常运行状态下生产的时间;停机时间是指设备因故障、维修等原因停止运行的时间。
OEE 的取值范围为0-100%,数值越高,表示设备的效率越高。
3.OEE 计算公式在Excel 中的实现在Excel 中,可以使用以下步骤来计算OEE:步骤1:在Excel 表格中,记录每台设备的生产时间和停机时间。
例如,设备A 的生产时间为10 小时,停机时间为2 小时。
步骤2:在Excel 表格中,使用公式`=生产时间/(生产时间+ 停机时间)*100`计算每台设备的OEE。
例如,设备A 的OEE 为10/(10+2)*100=83.33%。
步骤3:根据计算结果,分析设备的运行情况,找出存在的问题,并采取相应措施提高设备效率。
4.OEE 计算公式的实际应用案例假设某企业有10 台生产设备,每天工作8 小时。
在计算OEE 时,发现设备的平均OEE 为60%。
这表明设备的利用率较低,存在很大的改进空间。
企业通过对每台设备的OEE 进行分析,发现问题主要出在设备故障和维修方面。
于是,企业采取了一系列措施,如加强设备维护、提高设备质量等,最终使设备的OEE 提高到了80%。
这使得企业的生产效率得到了显著提升。
(完整版)OEE记录表格(设备综合效率)
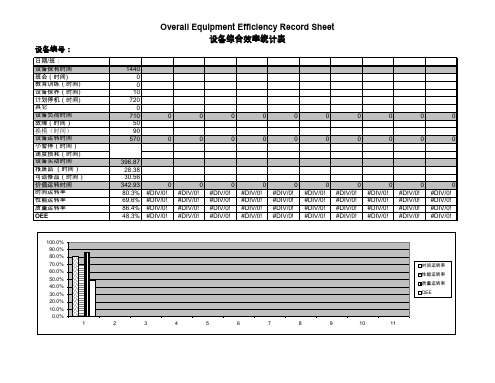
1440
0
0
10
720
0
710
0
0
0
0
0
0
0
0
0
0
50
90
0
0
0
0
0
396.87 28.38 30.56
342.93 80.3% 69.6% 86.4% 48.3%
0 #DIV/0! #DIV/0! #DIV/0! #DIV/0!
0 #DIV/0! #DIV/0! #DIV/0! #DIV/0!
4
符号:
P 设备保养 D 无生产计划
C 换模 T 模具或设备故障(需注明故障名称)
R 休息 W 待料
A 调试新模具 O 其它
维修和处理结果及验证 最终解决方案和验证
0 #DIV/0! #DIV/0! #DIV/0! #DIV/0!
0 #DIV/0! #DIV/0! #DIV/0! #DIV/0!
0 #DIV/0! #DIV/0! #DIV/0! #DIV/0!
0 #DIV/0! #DIV/0! #DIV/0! #DIV/0!
0 #DIV/0! #DIV/0! #DIV/0! #DIV/0!
0 #DIV/0! #DIV/0! #DIV/0! #DIV/0!
0 #DIV/0! #DIV/0! #DIV/0! #DIV/0!
0 #DIV/0! #DIV/0! #DIV/0! #DIV/0!
100.0%
90.0%
80.0%
70.0% 60.0% 50.0% 40.0% 30.0%
时间运转率 性能运转率 质量运转率 OEE
20.0%
10.0%
0.0%
设备综合效率OEE计算(附计算表格)

OEE(设备综合效率)
OEE计算(文末附计算表格)
1、OEE=时间开动率x性能开动率x合格率
2、时间开动率=实际操作时间/计划工作时间
计划工作时间=总可用时间-计划停机时间
(计划停机时间为员工休息、吃饭时间,计划保养时间)
实际操作时间=计划工作时间-计划外停机时间
(计划外停机时间为计划工作时间中设备故障、设备调整、设备紧急换型等非计划性时间)
3、性能开动率=实际产量/(实际操作时间/理想节拍时间)
4、合格率=良品数量/实际总产量
例如:某设备1天工作时间为24h,员工用餐、休息时间90min,班中计划保养停机60min,故障停机20min,生产中工艺调整30min,产品的理论加工周期为1.2min/件,一天加工产品1000件,有100件废品,求这台设备的设备综合效率OEE
备注:浅绿色为需要输入数据。
OEE统计表
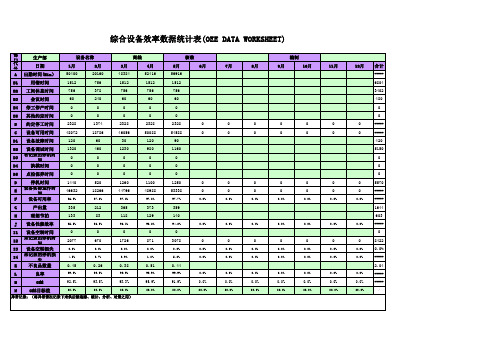
0.0%
5.8%
0.0%
0.44
99.9%
0.0%
91.9%
0.0%
80.0%
80.0%
7月
0 0
0 0
0.0%
0.0%
0
0.0% 0.0% 0.0% 0.0% 80.0%
8月
0 0
0 0
0.0%
0.0%
0
0.0% 0.0% 0.0% 0.0% 80.0%
编制
9月
10月
0
0
0
0
0
0
0
0
0.0%
0.0%
未记录的停机时 间
I3 设备空转损失
I4
未记录的停机损 失
K
不良品数量
0 2077
0.0% 4.5%
0.45
0 670
0.0% 3.7%
0.26
0 1726
0.0% 3.9%
0.38
0 871
0.0% 1.8%
0.51
L
良率
99.9%
99.9%
99.9%
99.9%
M
OEE
92.5%
93.5%
93.3%
0.0% 7
良率
0.0%
0.0%
5
6
7
8
0.0% 8
0.0% 8
9
0.0% 9
0.0% 9
10
0.0% 10
0.0% 10
11
0.0% 11
0.0% 11
12
0.0% 12
0.0% 12
0.0%
0
0.0% 0.0%
0.0% 0.0% 80.0%
表格模板-设备综合利用率统计表 精品
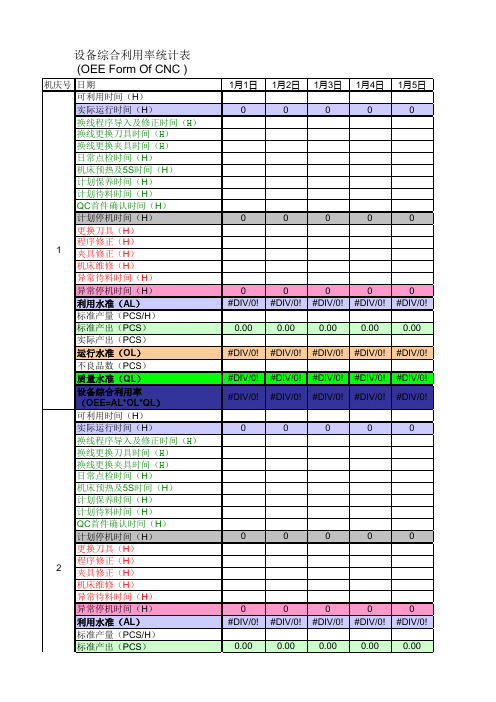
(OEE Form Of CNC )
机庆号 日期 可利用时间(H) 实际运行时间(H) 换线程序导入及修正时间(H) 换线更换刀具时间(H) 换线更换夹具时间(H) 日常点检时间(H) 机床预热及5S时间(H) 计划保养时间(H) 计划待料时间(H) QC首件确认时间(H) 计划停机时间(H) 更换刀具(H) 程序修正(H)
0.00
0.00
0.00
0.00
0.00
#DIV/0! #DIV/0! #DIV/0! #DIV/0! #DIV/0!
#DIV/0! #DIV/0! #DIV/0! #DIV/0! #DIV/0! #DIV/0! #DIV/0! #DIV/0! #DIV/0! #DIV/0!
0
0
0
0
0
0
0
0
0
0
0
0
0
0
0
0
0
0
0
0
0
0
0
0
0
0
0
#DIV/0! #DIV/0! #DIV/0! #DIV/0! #DIV/0!
0.00
0.00
0.00
0.00
0.00
实际产出(PCS) 运行水准(OL) 不良品数(PCS) 质量水准(QL)
设备综合利用率 (OEE=AL*OL*QL) 可利用时间(H) 实际运行时间(H) 换线程序导入及修正时间(H) 换线更换刀具时间(H) 换线更换夹具时间(H) 日常点检时间(H) 机床预热及5S时间(H) 计划保养时间(H) 计划待料时间(H) QC首件确认时间(H) 计划停机时间(H) 更换刀具(H) 程序修正(H) 3 夹具修正(H) 机床维修(H) 异常待料时间(H) 异常停机时间(H) 利用水准(AL) 标准产量(PCS/H) 标准产出(PCS) 实际产出(PCS) 运行水准(OL) 不良品数(PCS) 质量水准(QL)
设备综合效率OEE统计表(使用)
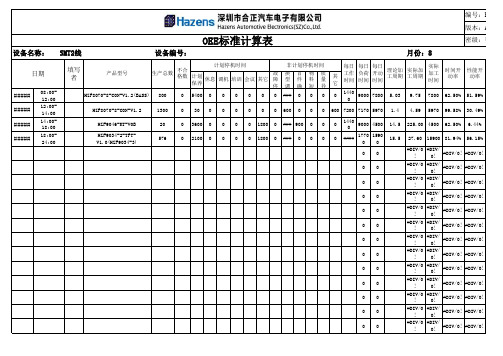
HZF8070-8-CON-V1.2(BASS) 800
0 5400 0 0 0 0 0 0 ### 0 0 0
其 它
每日 工作 时间
每日 每日 负荷 开动 时间 时间
理论加 工周期
实际加 工周期
实际 加工 时间
0
1440 0
9000
7800
5.03
#DIV/0! #DIV/0! #DIV/0! #DIV/0! #DIV/0! #DIV/0! #DIV/0! #DIV/0! #DIV/0! #DIV/0! #DIV/0! #DIV/0! #DIV/0! #DIV/0! #DIV/0! #DIV/0! #DIV/0! #DIV/0!
00
#DIV/0 !
#DIV/ 0!
#DIV/0!
#DIV/0!
00
#DIV/0 !
#DIV/ 0!
#DIV/0!
#DIV/0!
00
#DIV/0 !
#DIV/ 0!
#DIV/0!
#DIV/0!
00
#DIV/0 !
#DIV/ 0!
#DIV/0!
#DIV/0!
00
#DIV/0 !
#DIV/ 0!
#DIV/0!
#DIV/ 0!
#DIV/0!
#DIV/0!
00
#DIV/0 !
#DIV/ 0!
#DIV/0!
#DIV/0!
00
#DIV/0 !
#DIV/ 0!
#DIV/0!
#DIV/0!
00
#DIV/0 !
#DIV/ 0!
#DIV/0!
#DIV/0!
00
#DIV/0 !
设备综合效率(OEE)
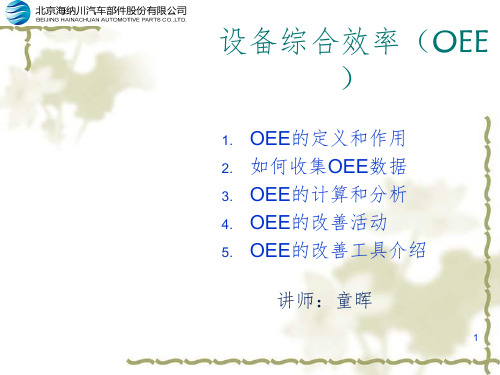
【实行OEE的意义】
OEE的解决方案能够使得制造商在世界占有一席之地。另外. 可以获得以下几方面效益。
企业规划: A、可以为企业规划提供客观科学的决策依据。
B、可以为企业提供很多的增值意见和建议。
生产管理:
1、能收集到生产线的实时数据,以便建立车间监控管理系 统。
2、能分析/跟踪生产设备的有效利用情况,以便最大化挖掘 设备生产潜力。
设备loss的构造和指标计划维持开动时停止loss纯开动时间速度loss加动时间不良loss故障设备1台当故障频度10分以上准备调整准备调整时间10分以下空转瞬间停止空转瞬间停止频度10分以下速度理论cycletime实现回转数10以上up工程不良工程别不良率修理包含初期收率初期收率lotsize90以上时间开动率100性能开动率100合格品率100设备综合效率合格品率10085以上开动时间负荷时间90以上工程物量99以上95以上理论c生产量加动时间良品数量投入数量目标手段分类实施活动防止劣化测知劣化防止劣化操作员点检员正常运行正常操作复位调整清扫找出潜在缺陷处理加油紧固低技术要求的日常点检小检修定期点检定期诊断分析定期修理监测诊断不定期检修状况早期发现准确及时报告突发修理减轻负荷提高强度提高可靠性按故障后果决定适当的维修策略技术改造以改善设备性能与精度适当技术措施提高可维修性故障根源诊断改变设计永久消灭故障日常维护定期维修状态维修事后维修改善维修可靠性可维修性主动维修设备综合效率level评价表level故障loss有多大没有统计发生故障loss1以上故障loss1以下对信赖性保修性关心程度高状态保修体制的确立促进信赖性保修性的开展准备作业loss对作业者的工作无控制状态时间的不规则性大调整机制和与其对应的要素充分考虑到达极点状态singl依据调整排除速度loss设备性能不明确性状态10没有按品种别机械别设定速度11速度的不规则性大针对速度loss集约问题点设备
- 1、下载文档前请自行甄别文档内容的完整性,平台不提供额外的编辑、内容补充、找答案等附加服务。
- 2、"仅部分预览"的文档,不可在线预览部分如存在完整性等问题,可反馈申请退款(可完整预览的文档不适用该条件!)。
- 3、如文档侵犯您的权益,请联系客服反馈,我们会尽快为您处理(人工客服工作时间:9:00-18:30)。
可疑品处理
冲针断,换下模具维修
筛选
新模不稳定
筛选,返工
13:00
操 作
18:00
注: 每格为5分钟 维修和处理结果及验证
最终解决方案和验证
3 4
设 备 保 P养 符号:
无 生 产 计 D划
架 模 ( 需 注 明 下 一 产 品 号 C) 模 具 或 设 备 故 障 ( 需 注 明 故 障 名 称 T)
可返工产品数量:
0
质量问题描述:
1
KA:孔未冲出
2
KC:毛刺大
10:00 15:00
组 长 确 认 :
11:00
16:00
班 长 确 认 :
12:00
17:00
产品 #2 KC0154 400次/min 420次/min 67125
0 12225
产品 #3
模具或设备故障描述
1 2 3 4 5 6 问题原因初步判定和措施
设备运行状况统计表
设备编 号:
生产日 期/班:
8:00
9:00
时间
(10分钟/ 格)
原因
时间
(10分钟/ 格)
13:00
14:00
原因
产品 #1
零件号/名称: 理论节拍时间: 实际节拍时间: 合格产品数量:
KA 0051 400次/min 320次/min 70048pcs
报废产品数量:
11352pcs
设备运行状况统计表
休 R息
调 试 新 模 A具
待 W料
其 O它
设备运行状况统计表
19'40