5W分析法介绍
(1)5W问题分析法
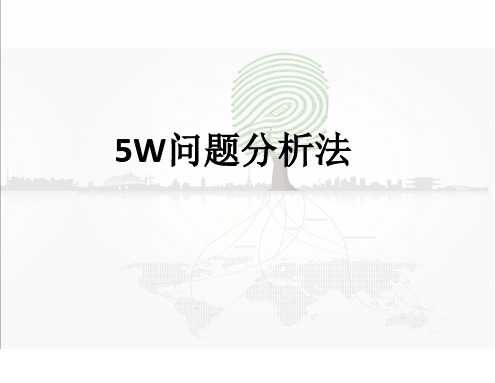
鱼骨图分析法
•鱼骨图使用步骤 •★查找要解决的问题; •★把问题写在鱼骨的头上; •★召集同事共同讨论问题出现的可能原因,尽可能多地找出 问题; •★把相同的问题分组,在鱼骨上标出; •★根据不同问题征求大家的意见,总结出正确的原因; •★拿出任何一个问题,研究为什么会产生这样的问题? •★针对问题的答案再问为什么?这样至少深入五个层次(连 续问五个问题); •★当深入到第五个层次后,认为无法继续进行时,列出这些 问题的原因,而后列出至少20个解决方法。
掌握情况
问题点澄清 原因所在 原因点 原因点 原因点 原因点
原因点
原因点
Why? 1 原因1 Why? 2 原因2 Why? 3 原因3
Why? 1 原因1 Why? 2 原因2 Why? 3 原因3
Why? 1 原因1 Why? 2 原因2 Why? 3 原因3 Why? 4 原因4
原因调查
Why? 4 原因4
“5个Why分析”也是中国人的智慧
• 我们中国古代以来就有“打破沙锅问到底”的
习惯;“打破沙锅问到底”是一句俗语,形象 表达了锲而不舍、不断探索的精神,这是人们 常挂在嘴边的一句口头禅。 • 到了日本人手里就整出一个5why出来了
真理诞生于一百个问号之后
五个为什么
问五次为什么
5
二、5W问题分析法解决方式
• • 这也就是掌握情况的5w2h 在问为什么之前,问这些问题是很重要的。
要把握问题的倾向,问:为什么(Why);做什么
第二部分:原因调查
• 步骤 6: 识别并确认异常现象的直接原因。 • 如果原因是可见的,验证它。如果原因是不可 见的,考虑潜在原因并核实最可能的原因。依 据事实确认直接原因。问: • ♦ 这个问题为什么发生? • ♦ 我能看见问题的直接原因吗? • ♦ 如果不能,我怀疑什么是潜在原因呢? • ♦ 我怎么核实最可能的潜在原因呢? • ♦ 我怎么确认直接原因?
5w分析报告

5W分析报告:解构问题的终极指南引言在解决问题和制定决策时,5W分析法是一个强大而广泛应用的工具。
无论您是解决业务问题、准备市场研究报告,还是审核案例,本文将向您介绍5W分析法的基本概念和步骤,以帮助您更好地分析和解决问题。
什么是5W分析法?5W分析法是一种用于解构问题的方法论。
通过回答以下五个问题,我们可以全面而系统地了解问题的核心要素:1.什么(What):问题的本质是什么?2.为什么(Why):问题发生的原因是什么?3.谁(Who):问题影响的人群是谁?4.何时(When):问题发生的时间和频率是什么?5.如何(How):问题如何解决或处理?接下来,我们将详细介绍每个问题的分析步骤。
什么(What)首先,我们要明确问题的本质。
这是解决问题的第一步,因为只有明确了问题,我们才能正确地定位和解决它。
1.定义问题:明确问题的描述和范围,并确保所有相关方都对问题的定义达成共识。
2.细化问题:将问题进一步细化为具体的子问题或关键要素,以便更好地分析和解决。
为什么(Why)了解问题发生的原因对于制定有效的解决方案至关重要。
通过回答为什么这个问题会发生,我们可以找到问题的根本原因,并采取相应的措施。
1.分析原因:确定导致问题发生的具体原因和背后的因素。
2.寻找关联:寻找问题与其他因素、行为或环境之间的关联性。
3.评估重要性:评估不同原因的重要性和影响程度,以确定解决问题的优先级。
谁(Who)问题通常不会只影响一个人,而是一群人。
因此,了解受影响的人群是解决问题的关键。
1.确定相关方:找出问题的相关方,包括受影响的人员、利益相关者和决策者。
2.需求分析:了解相关方的需求、利益和期望,以便找到解决方案可以满足的共同要求。
何时(When)问题发生的时间和频率对于解决问题的紧迫性和有效性至关重要。
通过了解问题发生的时间和频率,我们可以更好地规划解决方案的时间表和执行策略。
1.时序分析:确定问题发生的时间段、周期或趋势。
5W问题分析法

5W分析法
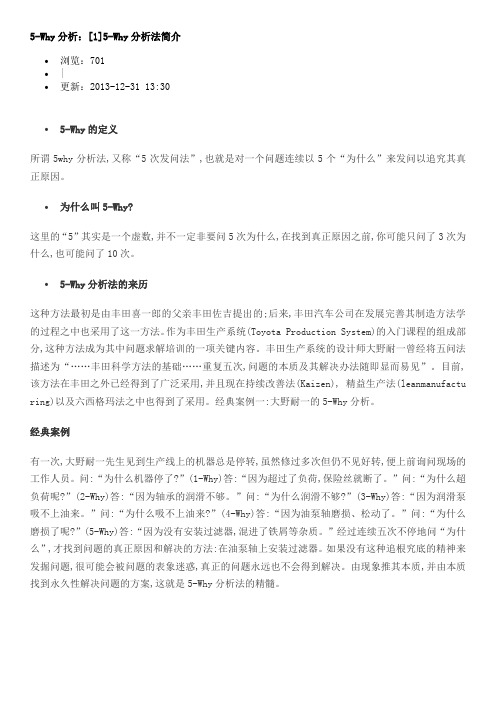
5-Why分析:[1]5-Why分析法简介•浏览:701•|•更新:2013-12-31 13:30•5-Why的定义所谓5why分析法,又称“5次发问法”,也就是对一个问题连续以5个“为什么”来发问以追究其真正原因。
•为什么叫5-Why?这里的“5”其实是一个虚数,并不一定非要问5次为什么,在找到真正原因之前,你可能只问了3次为什么,也可能问了10次。
•5-Why分析法的来历这种方法最初是由丰田喜一郎的父亲丰田佐吉提出的;后来,丰田汽车公司在发展完善其制造方法学的过程之中也采用了这一方法。
作为丰田生产系统(Toyota Production System)的入门课程的组成部分,这种方法成为其中问题求解培训的一项关键内容。
丰田生产系统的设计师大野耐一曾经将五问法描述为“……丰田科学方法的基础……重复五次,问题的本质及其解决办法随即显而易见”。
目前,该方法在丰田之外已经得到了广泛采用,并且现在持续改善法(Kaizen), 精益生产法(leanmanufactu ring)以及六西格玛法之中也得到了采用。
经典案例一:大野耐一的5-Why分析。
经典案例有一次,大野耐一先生见到生产线上的机器总是停转,虽然修过多次但仍不见好转,便上前询问现场的工作人员。
问:“为什么机器停了?”(1-Why)答:“因为超过了负荷,保险丝就断了。
”问:“为什么超负荷呢?”(2-Why)答:“因为轴承的润滑不够。
”问:“为什么润滑不够?”(3-Why)答:“因为润滑泵吸不上油来。
”问:“为什么吸不上油来?”(4-Why)答:“因为油泵轴磨损、松动了。
”问:“为什么磨损了呢?”(5-Why)答:“因为没有安装过滤器,混进了铁屑等杂质。
”经过连续五次不停地问“为什么”,才找到问题的真正原因和解决的方法:在油泵轴上安装过滤器。
如果没有这种追根究底的精神来发掘问题,很可能会被问题的表象迷惑,真正的问题永远也不会得到解决。
由现象推其本质,并由本质找到永久性解决问题的方案,这就是5-Why分析法的精髓。
5个为什么分析法
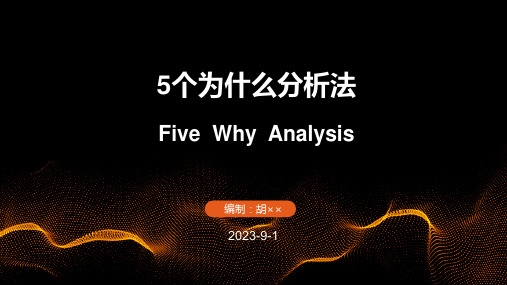
二、5Why 的起源:
5Why首创自日本丰田汽车公司的大野 耐一(丰田生产方式主要创始人之一),源于 一次新闻发布会,有人问:“丰田公司的 汽车质量怎么会这么好?”他回答说: “我碰到问题至少要问5个为什么。”
大野耐一总是爱在车间走来走去,停下 来向工人发问。他反复地就一个问题, “为什么”,直到回答令他满意,被他问 到的人也心里明白为止——这就是著名的 “五个为什么”的起源。 所以,5Why也被称为:丰田5问法。
如上这些原因都应该避免。 2、再发防止对策的一般导出为设备面和管理制度面。
四、5 Why工具注ห้องสมุดไป่ตู้要点:
5Why注意要点:避免围绕问题本身,避免责任推卸
错 误 事 例
产品组装出现质量问题
为什么?
A部品设计不合理,组装到B部品后有裂纹
为什么?
试制阶段的研讨不充分
为什么?
开发阶段设计人员不够
为什么?
设计部门没有增员预算
六、5个Why培训最终总结:
简单来说,就是
多问几次为什么?
通过反复的提问,使解决问题的人避开主观或自负的假设和逻 辑陷阱,从结果着手,沿着因果关系链条,顺藤摸瓜,穿越不 同的抽象层面,直至找出原有问题的根本原因。
Thanks
评估对策成效 流程标准化/吸取教训
基本情况调查 问题发生在哪块?
“去看“问题
5Why 根本原因调查分析
三、5Why的应用~原因调查:
为什么会发生(失效链/技术层)
问题点识别(大的、模糊的、复杂的) 阐明问题 已定位原因区
原因点 原因点 原因点 Why? 1 原因1 Why? 2 原因2 Why? 3 原因3 Why? 4 原因4
五、5个Why运用事例:
5W分析法2篇
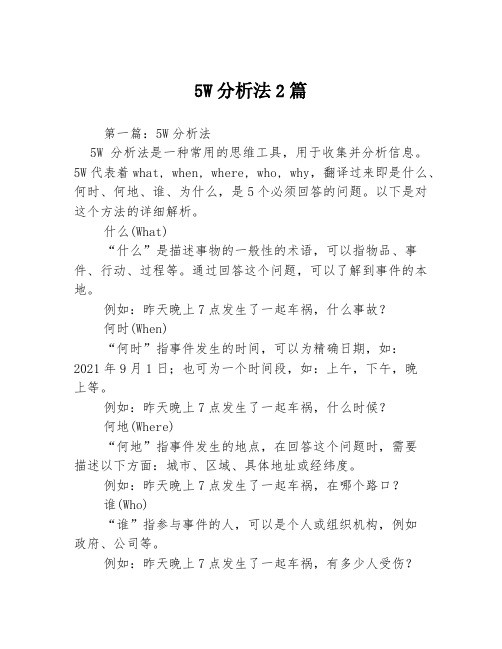
5W分析法2篇第一篇:5W分析法5W分析法是一种常用的思维工具,用于收集并分析信息。
5W代表着what, when, where, who, why,翻译过来即是什么、何时、何地、谁、为什么,是5个必须回答的问题。
以下是对这个方法的详细解析。
什么(What)“什么”是描述事物的一般性的术语,可以指物品、事件、行动、过程等。
通过回答这个问题,可以了解到事件的本地。
例如:昨天晚上7点发生了一起车祸,什么事故?何时(When)“何时”指事件发生的时间,可以为精确日期,如:2021年9月1日;也可为一个时间段,如:上午,下午,晚上等。
例如:昨天晚上7点发生了一起车祸,什么时候?何地(Where)“何地”指事件发生的地点,在回答这个问题时,需要描述以下方面:城市、区域、具体地址或经纬度。
例如:昨天晚上7点发生了一起车祸,在哪个路口?谁(Who)“谁”指参与事件的人,可以是个人或组织机构,例如政府、公司等。
例如:昨天晚上7点发生了一起车祸,有多少人受伤?为什么(Why)“为什么”指事件的原因,需要回答的问题包括事件发生的背景、原因及其引起的影响。
例如:昨天晚上7点发生了一起车祸,是因为司机开车时疏忽驾驶所致?总之,5W分析法可以帮助我们更好地了解事件,收集和整合信息,以便更好地解决问题。
这个方法适用于各种领域,例如新闻报道、故事分析、市场调研等。
第二篇:基于5W分析法的市场调研市场调研是指为了了解并满足市场需求,对市场及其相关因素进行系统的认识和探索。
下面以5W分析法为基础,介绍市场调研的具体步骤。
什么(What)首先需要确定调研的内容和目的。
例如,调研的主题是银行理财产品的需求分析,调研目的是了解人们购买理财产品的原因、选择条件、预期收益等。
何时(When)在确定调研目的后,需要设定好调研时间和周期,并计划好具体的调研步骤。
调研周期一般根据调研内容的复杂程度和要求的准确度而定,时间范围通常在1到6个月之间。
5w分析法模板
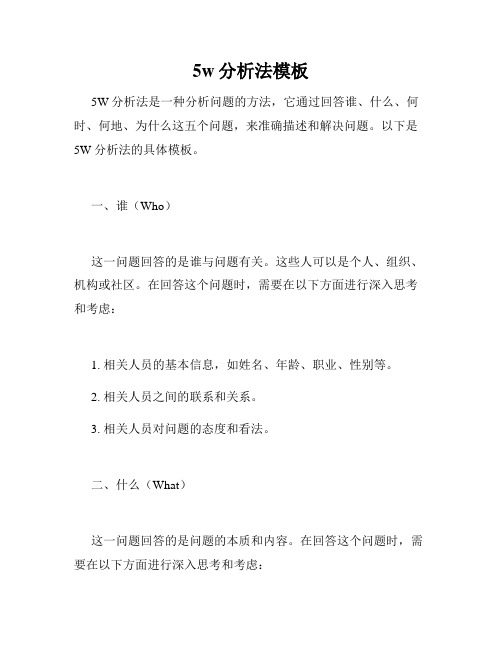
5w分析法模板5W分析法是一种分析问题的方法,它通过回答谁、什么、何时、何地、为什么这五个问题,来准确描述和解决问题。
以下是5W分析法的具体模板。
一、谁(Who)这一问题回答的是谁与问题有关。
这些人可以是个人、组织、机构或社区。
在回答这个问题时,需要在以下方面进行深入思考和考虑:1. 相关人员的基本信息,如姓名、年龄、职业、性别等。
2. 相关人员之间的联系和关系。
3. 相关人员对问题的态度和看法。
二、什么(What)这一问题回答的是问题的本质和内容。
在回答这个问题时,需要在以下方面进行深入思考和考虑:1. 问题的起因和原因。
2. 问题涉及的领域和范围。
3. 问题的影响和后果。
三、何时(When)这一问题回答的是问题发生的时间和时间范围。
在回答这个问题时,需要在以下方面进行深入思考和考虑:1. 问题发生的具体时间点和时期,包括年、月、日、时、分和秒。
2. 问题发生的时间段,包括小时、天、周、月、季度或年。
3. 问题的历史背景和演变过程。
四、何地(Where)这一问题回答的是问题发生的地理位置和范围。
在回答这个问题时,需要在以下方面进行深入思考和考虑:1. 问题发生的具体位置和地址。
2. 问题发生的地理范围,包括市、县、省、国家或全球。
3. 问题发生的环境和场所。
五、为什么(Why)这一问题回答的是导致问题发生的原因和根本原因。
在回答这个问题时,需要在以下方面进行深入思考和考虑:1. 问题发生的原因和动因。
2. 问题发生的背景和条件。
3. 问题发生的根源和深层次因素。
结语5W分析法是一种解决问题的有效方法,通过对问题进行全面、准确的描述和分析,有助于更好地解决问题、优化决策和提高效率。
如果能够正确运用5W分析法模板,相信可以更好地应对挑战和解决问题。
5W分析方法
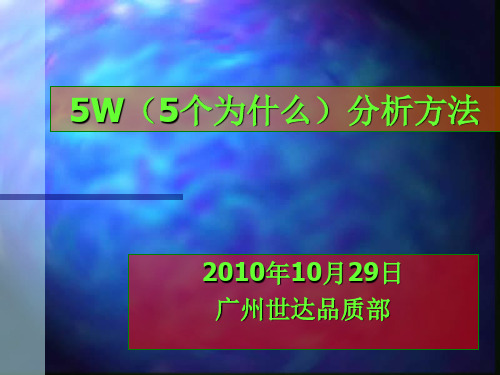
4
没有过滤设备。
安装过滤设备。
5
不使用「○○不好」 「××不明确」等的表 达方式。
分析事例1
为什么 产品开路。 1 2 3 为何结线力度大。 4 为何使用了金属镊 子。 作业要点没有明确。 在作业要点明确使 用胶镊子。 使用了金属镊子。 使用了胶镊子。 为何结线部位线材 断。 结线时拉断线。 培训工人作业方法? 原因 结线部位线材断。 对策
偏差
① 作业或工程与往常不一样时 ・声音、颜色、手感、气味、速度不相同 ・部品过剩/不足、材料使用量过多/过少 ② 货物的完成状态与往常不一致 时 ・比起往常修理得要多/少,完全 沒有不良(减少了) ・管理图的点标示虽在规格內,卻有可疑,初始的不良模型
问题的定义2
所谓偏差即进行过程中发生了某种“变化”而来。要纠正偏 差,必须将变化找出,才能真正解决问题。因此,解决问题 的意义,就是要纠正偏差,能够把发生变化之点找出,才能 真正把问题解决。
做分析之前的必要事項
进行「为什么分析」之前、有些非做好 不可的事项。 这些事项若做得草率的话、「为什么分 析」就无法有効果・有効率的去进行。 以下就介绍、這些必要的事项。
「问题」的明确化
首先、不要用推测・想像、仅就事实做 好掌握问题的现象。 尽可能正确的掌握到问题发生的场所、 时期、发生频度、种类、状态、比例等 等的事实___3现主义。 也可以活用由有关者的面谈中得到的情 报。
两个推进的方法的不同处
如同这个例子、由「应有的形态」来探讨问题、 若是应有的形态的构成条件有遗漏的话、恐怕 无法达成正确的结论。再则、往往发现在做现 场・现物调查时有草率的倾向。 在记述问题的状况时、不是记入「作业者的实 际作业和『作业标准』不同、而要正确的记入 「作业者的某个实际动作和『作业标准』不同、 这样的话错误就可以防止再发生了。
5W 分析方法
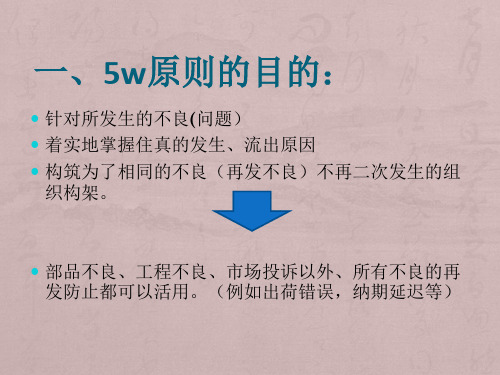
【为什么分析】的使用方法和
顺序
顺序2.追究“为什么”
③确认理论上的重要性
●必须重复确认宗旨是否合理
④要无一疏漏的找出并列关系的原因
【为什么分析】的使用方法和
顺序
顺序2.追究“为什”
⑤使用通俗易懂的语言表达方式 ●避开含糊的语言表达,用心做到通俗易懂 ●用语言难以表现的时候,要来图来表示(特别是方向和位置)
b一条条写出其过程。 c基于说明性、证明性的数据。 ②为什么为什么分析 反复为什么为什么,从而抓住真正的原因。
从各个角度反复为什么为什么,从中明确最有影响 的内容。 (在其它项目中被认为重要的部分,实施对策。)
六、5原则表的作成方法
③对策
对为什么为什么分析的最终项目的对策。 即使为什么为什么分析中无记录,但要因分析判定为NG的内容也要明确 相应对策。 通过硬件面、管理面的对策明确再发防止对策。
4M(Man,Machine,Material,Method)+1M(Measurement)的变化点有无。 明确从2个变化点(使之变化、变化)的批的波及性的。 ※制造指令单、工程检查记录、日常·定期点检表、保养记录、作业日报等。
六、5原则表的作成方法
3、原因的追求。 ①发生过程.再现试验 明确从要因分析结果到发生、流出的过程。 视其必要性,进行再现试验。 ※注意点:a连系要因分析。
六、5原则表的作成方法
1、发生状况
①现象-投诉内容 对于规格来说现品的状况(外观、尺寸、特性、机能、性能)是怎样的状 态呢? ②发生场所,③批号NO. 什么时候,在什么工序,是谁生产的? ④处置内容 处置的方法与结果,以及对处置的识别。
2、事实的把握
5w分析法经典案例

5w分析法经典案例5W分析法,又称为“五个W”,是一种常用于新闻报道、事件分析和问题解决的框架。
它包括五个基本问题:谁(Who)、什么(What)、何时(When)、何地(Where)、为什么(Why)。
通过这五个问题,我们可以全面地理解一个事件或问题。
以下是一个经典的5W分析法案例:谁(Who):在这个案例中,主要涉及的人物是张伟,一位35岁的软件工程师,他在一家知名的科技公司工作。
张伟在业内有着良好的声誉,并且是公司技术团队的核心成员。
什么(What):张伟最近完成了一个重要的项目,这个项目是开发一款新的移动应用程序,用于提高工作效率。
这个应用程序集成了人工智能技术,能够根据用户的工作习惯和偏好自动优化工作流程。
何时(When):这个项目从2023年1月开始,经过六个月的紧张开发,于2023年7月1日正式上线。
张伟和他的团队在这段时间内加班加点,确保项目按时完成。
何地(Where):项目的开发工作主要在张伟所在公司的总部进行,位于市中心的一座现代化办公楼内。
此外,团队成员也通过远程协作的方式参与项目,这使得团队能够充分利用全球资源。
为什么(Why):开发这款应用程序的目的是为了帮助用户更高效地管理他们的工作。
随着技术的发展,人们面临着越来越多的信息和任务,这使得时间管理变得尤为重要。
张伟和他的团队希望通过这款应用程序,帮助用户减少不必要的时间浪费,提高工作效率。
通过5W分析法,我们能够清晰地了解张伟项目的关键要素,包括项目的背景、目标、实施过程以及最终的成果。
这种方法不仅有助于我们理解事件本身,还能够为我们提供解决问题和优化流程的思路。
5w分析法模板
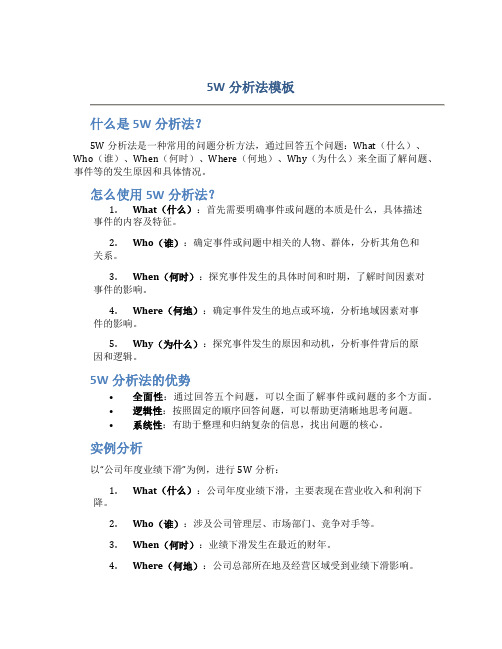
5W分析法模板什么是5W分析法?5W分析法是一种常用的问题分析方法,通过回答五个问题:What(什么)、Who(谁)、When(何时)、Where(何地)、Why(为什么)来全面了解问题、事件等的发生原因和具体情况。
怎么使用5W分析法?1.What(什么):首先需要明确事件或问题的本质是什么,具体描述事件的内容及特征。
2.Who(谁):确定事件或问题中相关的人物、群体,分析其角色和关系。
3.When(何时):探究事件发生的具体时间和时期,了解时间因素对事件的影响。
4.Where(何地):确定事件发生的地点或环境,分析地域因素对事件的影响。
5.Why(为什么):探究事件发生的原因和动机,分析事件背后的原因和逻辑。
5W分析法的优势•全面性:通过回答五个问题,可以全面了解事件或问题的多个方面。
•逻辑性:按照固定的顺序回答问题,可以帮助更清晰地思考问题。
•系统性:有助于整理和归纳复杂的信息,找出问题的核心。
实例分析以“公司年度业绩下滑”为例,进行5W分析:1.What(什么):公司年度业绩下滑,主要表现在营业收入和利润下降。
2.Who(谁):涉及公司管理层、市场部门、竞争对手等。
3.When(何时):业绩下滑发生在最近的财年。
4.Where(何地):公司总部所在地及经营区域受到业绩下滑影响。
5.Why(为什么):业绩下滑原因可能包括市场竞争加剧、经济环境不景气等。
结论5W分析法是一种简单而有效的问题分析方法,适用于对事件、问题进行深入了解和分析。
通过系统地回答五个问题,可以帮助我们更全面地认识问题的各个方面,找出解决问题的关键因素,为问题的解决提供有效的思路和方法。
在实际应用中,可以根据具体情况灵活运用5W分析法,更好地解决问题和提高工作效率。
以上是5W分析法的模板及实例分析,希望对您有所帮助。
如有任何疑问或需要进一步了解,请随时与我们联系。
感谢阅读!。
5w分析法案例范文大学生
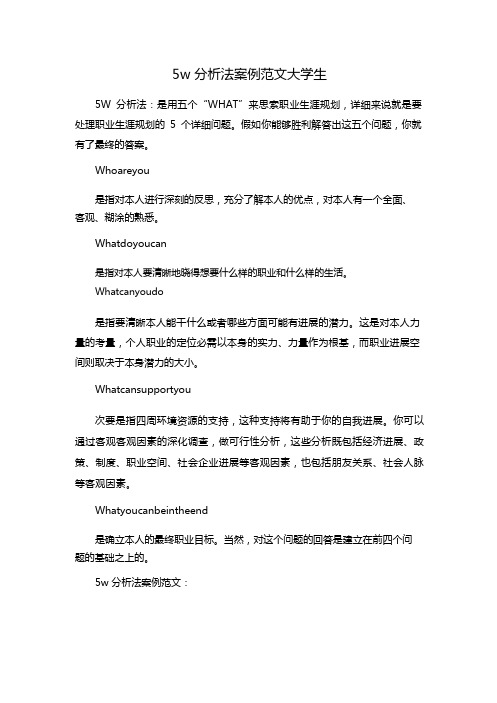
5w 分析法案例范文大学生5W 分析法:是用五个“WHAT”来思索职业生涯规划,详细来说就是要处理职业生涯规划的5 个详细问题。
假如你能够胜利解答出这五个问题,你就有了最终的答案。
Whoareyou是指对本人进行深刻的反思,充分了解本人的优点,对本人有一个全面、客观、糊涂的熟悉。
Whatdoyoucan是指对本人要清晰地晓得想要什么样的职业和什么样的生活。
Whatcanyoudo是指要清晰本人能干什么或者哪些方面可能有进展的潜力。
这是对本人力量的考量,个人职业的定位必需以本身的实力、力量作为根基,而职业进展空间则取决于本身潜力的大小。
Whatcansupportyou次要是指四周环境资源的支持,这种支持将有助于你的自我进展。
你可以通过客观客观因素的深化调查,做可行性分析,这些分析既包括经济进展、政策、制度、职业空间、社会企业进展等客观因素,也包括朋友关系、社会人脉等客观因素。
Whatyoucanbeintheend是确立本人的最终职业目标。
当然,对这个问题的回答是建立在前四个问题的基础之上的。
5w 分析法案例范文:1、Whoareyou我是一个热心、真诚、坦率、乐于助人的人。
在气质类型上属胆汁质和粘液质混合类型。
平常严于律己,经常给本人定一个略微高一点的目标,并朝着这个目标不断地学习和提高。
凡事往好的方面想。
擅长忍耐,不只能接受自我,也能接受他人,擅长发觉别人的闪光点,为人处事会为他人着想,与他人相互沟通和交往,人际关系协调和谐,能和集体融为一体。
能到处敬重、信任他人。
喜爱工作,有上进心,要求本人有进步,通过各种学习途径充实本人。
能调整管理心情,心境良好。
虽然也会有消极的心情,但一般不会长期。
2 、Whatdoyoucan我是学习工程造价专业,英语水平可以,能流利沟通;造价专业扎实,略通经贸学问;具有较强的人际沟通力量;思维灵敏,表达较流畅;在高校期间担当同学干部,有较强的组织协调力量;有很强的学习力量。
5w分析法案例范文
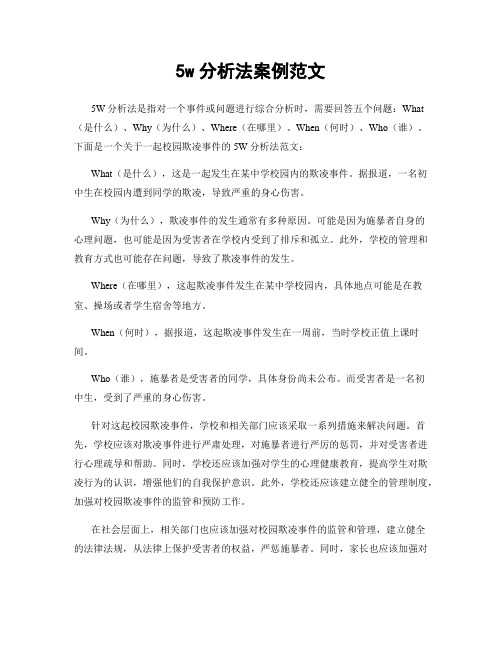
5w分析法案例范文5W分析法是指对一个事件或问题进行综合分析时,需要回答五个问题:What (是什么)、Why(为什么)、Where(在哪里)、When(何时)、Who(谁)。
下面是一个关于一起校园欺凌事件的5W分析法范文:What(是什么),这是一起发生在某中学校园内的欺凌事件。
据报道,一名初中生在校园内遭到同学的欺凌,导致严重的身心伤害。
Why(为什么),欺凌事件的发生通常有多种原因。
可能是因为施暴者自身的心理问题,也可能是因为受害者在学校内受到了排斥和孤立。
此外,学校的管理和教育方式也可能存在问题,导致了欺凌事件的发生。
Where(在哪里),这起欺凌事件发生在某中学校园内,具体地点可能是在教室、操场或者学生宿舍等地方。
When(何时),据报道,这起欺凌事件发生在一周前,当时学校正值上课时间。
Who(谁),施暴者是受害者的同学,具体身份尚未公布。
而受害者是一名初中生,受到了严重的身心伤害。
针对这起校园欺凌事件,学校和相关部门应该采取一系列措施来解决问题。
首先,学校应该对欺凌事件进行严肃处理,对施暴者进行严厉的惩罚,并对受害者进行心理疏导和帮助。
同时,学校还应该加强对学生的心理健康教育,提高学生对欺凌行为的认识,增强他们的自我保护意识。
此外,学校还应该建立健全的管理制度,加强对校园欺凌事件的监管和预防工作。
在社会层面上,相关部门也应该加强对校园欺凌事件的监管和管理,建立健全的法律法规,从法律上保护受害者的权益,严惩施暴者。
同时,家长也应该加强对孩子的教育,引导他们正确处理人际关系,遇到问题及时向老师或家长求助,而不是采取暴力行为。
总之,校园欺凌事件是一个严重的社会问题,需要学校、家长和社会各界的共同努力来解决。
只有通过多方合作,才能有效地预防和减少校园欺凌事件的发生,为学生营造一个安全、和谐的学习环境。
5Why 为什麼分析法-介绍

為什麼一為什麼分析法為什麼一為什麼分析法(WHY-WHY分析法,Why-Why analysis,5WHY,5W)為什麼-為什麼分析,也被稱作5個為什麼分析,它是一種診斷性技術,被用來識別和說明因果關係鏈,它的根源會引起恰當地定義問題。
不斷提問為什麼前一個事件會發生,直到回答“沒有好的理由”或直到一個新的故障模式被髮現時才停止提問。
解釋根本原因以防止問題重演。
文件中所有帶有“為什麼”的語句都會定義真正的根源(通常需要至少5個“為什麼”,但5個why不是說一定就是5個,可能是1個,也可能是10都沒有抓到根原)。
在一些組織里,一個普通的解決問題方法被用來分析和解決質量問題。
這個方法有4個主要部分:∙把握現狀。
∙原因調查。
∙問題糾正。
∙通過“差錯防止”過程進行預防。
把握現狀在方法的第一部分里,你:∙識別問題∙澄清問題∙查找原因要點 (PoC)原因調查在方法的第二部分里,你可以引導一次5個為什麼的調查來識別根本原因。
∙針對明確的問題。
∙針對為什麼沒有發現問題∙針對為什麼系統允許問題發生問題糾正在方法的第三部分里,你:∙採取明確的措施來糾正問題。
至少要求採取短期臨時措施來保護顧客利益。
通過“差錯防止”過程進行預防在方法的第四部分里,你:∙採取明確的措施來確保問題不會再發生,典型的措施是“差錯防止”過程。
∙銘記吸取到的教訓。
第一部分:把握現狀步驟1: 識別問題在方法的第一步中,你開始瞭解一個可能大、模糊或複雜的問題。
你掌握一些信息,但一定沒有掌握詳細事實。
問:我知道什麼?步驟 2: 澄清問題方法中接下來的步驟是澄清問題。
為得到更清楚的理解,問:∙實際發生了什麼?∙應該發生什麼?步驟 3: 分解問題在這一步,如果必要,將問題分解為小的、獨立的元素。
∙關於這個問題我還知道什麼?∙還有其他子問題嗎?步驟 4: 查找原因要點 (PoC)現在,焦點集中在查找問題原因的實際要點上。
你需要追溯來瞭解第一手的原因要點。
問:∙我需要去哪裡?∙我需要看什麼?∙誰可能掌握有關問題的信息?步驟5: 把握問題的傾向要把握問題的傾向,問:∙誰?∙哪個?∙什麼時間?∙多少頻次?∙多大量?在問為什麼之前,問這些問題是很重要的。
5Why分析
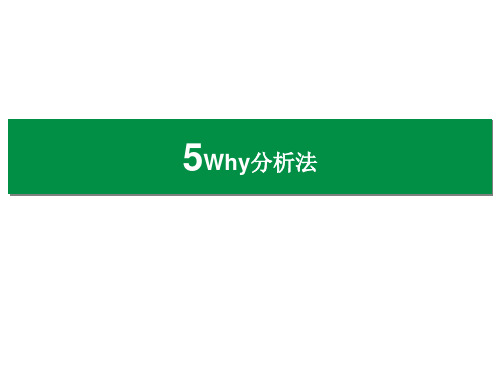
真因
M: 如何发生? O:为何流出?
1W
为什么ma制造?
mb引起
2W
为什么mb? mc引起
3W 为什么mc?
md引起
4W
为什么md?
me引起
5W 为什么me?
Root case 真因引起
1W 为什么oa流出?
ob引起
2W
为什么ob?
oc引起
3W 为什么oc?
od引起
4W
为什么od?
oe引起
5W 为什么oe?
—— 大野耐一
(丰田生产方式主要创始人之一)
5Why的关键:
鼓励解决问题的人要努力避开主观或自负的假设和逻辑 陷阱,从结果着手,沿着因果关系链条,顺藤摸瓜,穿越不 同的抽象层面,直至找出原有问题的根本原因。
5Why简介:
用中国古代的成语来说就是:“打破沙锅问到底”的习 惯,包含了锲而不舍、不断探索、追本溯源的精神。
5Why的应用:
5Why分析有助于解决零星的品质缺陷引发的问题。 5Why分析被用作一个解决实际问题过程的一部分,即根本 原因分析和调查。
5Why的应用原则和要点
5Why的指导原则:
1、总的指导方针: 用创新性思维思考,可以天真、可以异想天开的去分析; 要绝对的客观,确认所描述的状态为事实,而非推断、猜 测,可以的话,使用数据进行说明; 不要认为答案是显而易见的; 如果你自己不完全熟悉过程,就组建一个相关部门组成的 小组来完成分析;
□ 原因调查 ____识别/确认直接原因 ____问 5 个为什么以识别根本原因 ____问 5 个为什么以查找为什么问题没有发现并流出到顾客处 ____问 5 个为什么以想找为什么系统会允许问题发生
□ 问题纠正 ____实施纠正措施,至少,实施临时措施
五个为什么分析法

句都会定义真正的根源(通常需要至少5个“为什么”)。
5个为什么问题解决方法•♦握现状。
•♦原因调查。
•♦问题纠正。
•♦通过“差错防止”过程进行预防。
把握现状在方法的第一部分里,你:•♦识别问题•♦澄清问题•♦查找原因要点 (PoC)原因调查在方法的第二部分里,你可以引导一次5个为什么的调查来识别根本原因。
•♦针对明确的问题。
•♦针对为什么没有发现问题•♦针对为什么系统允许问题发生问题纠正在方法的第三部分里,你:•♦采取明确的措施来纠正问题。
至少要求采取短期临时措施来保护顾客利益。
通过“差错防止”过程进行预防在方法的第四部分里,你:•♦采取明确的措施来确保问题不会再发生,典型的措施是“差错防止”过程。
•♦铭记吸取到的教训。
“5个为什么”漏斗5个为什么分析法问题解决方法的基本步骤第一部分:把握现状步骤1: 识别问题在方法的第一步中,你开始了解一个可能大、模糊或复杂的问题。
你掌握一些信息,但一定没有掌握详细事实。
问:我知道什么?步骤 2: 澄清问题方法中接下来的步骤是澄清问题。
为得到更清楚的理解,问:•♦实际发生了什么?•♦应该发生什么?步骤 3: 分解问题在这一步,如果必要,将问题分解为小的、独立的元素。
•♦关于这个问题我还知道什么?•♦还有其他子问题吗?步骤 4: 查找原因要点 (PoC)现在,焦点集中在查找问题原因的实际要点上。
你需要追溯来了解第一手的原因要点。
问:•♦我需要去哪里?•♦我需要看什么?•♦谁可能掌握有关问题的信息?步骤5: 把握问题的倾向要把握问题的倾向,问:•♦谁?•♦哪个?•♦什么时间?•♦多少频次?•♦多大量?在问为什么之前,问这些问题是很重要的。
第二部分: 原因调查步骤 6: 识别并确认异常现象的直接原因。
如果原因是可见的,验证它。
如果原因是不可见的,考虑潜在原因并核实最可能的原因。
依据事实确认直接原因。
问:•♦这个问题为什么发生?•♦我能看见问题的直接原因吗?•♦如果不能,我怀疑什么是潜在原因呢?•♦我怎么核实最可能的潜在原因呢?•♦我怎么确认直接原因?步骤 7: 使用“5个为什么”调查方法来建立一个通向根本原因的原因/效果关系链。
- 1、下载文档前请自行甄别文档内容的完整性,平台不提供额外的编辑、内容补充、找答案等附加服务。
- 2、"仅部分预览"的文档,不可在线预览部分如存在完整性等问题,可反馈申请退款(可完整预览的文档不适用该条件!)。
- 3、如文档侵犯您的权益,请联系客服反馈,我们会尽快为您处理(人工客服工作时间:9:00-18:30)。
附件-1
3现主义的定义
3现主义是指重视现场、现物、现实的思考方式。 不重视「3现」を的话,很难抓住事情的本质。 在工厂的生产现场,发现了不良品,仅仅问当事人一些情况,就下判断, 很容易向操作人员下达错误的指示。 ・需要看产生不良品的工序 即 (现场)、 ・需要看不良品本身 即 (现物)、 ・产生不良品的情况 即 (现实) 重视以上3现主义的话,可以做出更正确的判断。 3现主义不仅适用于工厂产生不良品的场合,也适用于犯罪调查、 销售不佳等问题的解决。
5W(=追究根本原因)是思考战略(※)之一。将5W作为大家共通一项思考 程序可以达到相互学习促进、提高员工协作能力。 ※思考战略=构建能产生价值的系统方法论
5. 5W分析概要
“为什么”栏的写法 ①「与现象栏的写法」相同。 ②必须写事实。 ③用过去式写。 ④不用辩解之词。 ⑤也写别人的错误。
<现 象 > < 1W >
7. 5W分析的实施
2)“为什么”栏(<为什么1>・・・<为什么n>)的写法 (=为什么?」的回答的写法)
①使用像「哪里不行」的简洁词汇。 ② 避免使用2个动词。 ③ 以写“事实”为原则。 必须填写事实。事先不充分调查的话就不能了解事实,往往会写上推测的 内容。这样就不能找到真正的原因。 如果不明白不清楚的话就要做调查,必须填写“事实”。
5 W 分析指南
5W(问5次为什么)分析有效实施法
中天日立光缆有限公司 小仓 光一
目
录
1. 品质保证/品质管理的重要性 2.产品开发、品质管理主要技巧
3. 4. 5. 6. 7. 8. 5W分析引言 什么是5W分析 5W分析概要 5W分析事先准备 5W分析法的实施 事例介绍 1)事例-1 2)事例-2 3)事例-3 9. 5W分析Excel表 10.结束语
9.5W分析表
标题:
原因分 类 发生原因 现 象 为什么 1W 2W
5W分析成员:
3W 4W
制作者
5W
分析实施日: 20
6W
年
月
日
对策
出厂原因
(分析时的事前准备) ①在现场确认现场、现实和实物,牢牢掌握事实。 ②前提是对有问题部分的结构、功能的正确理解。
制作要 领
(分析 时的注意事项) ① 5W分析重要的是以简洁、具体的表达方法来进行事实的 积累。 (没有什么 辩解,不管是 对自己部门还是 对其它部门都能坦率地提出并能 坦率地接受 ) ②避免使用两个 动词的表现。 过去的分析以 过去式来记述。 ③在 5W分析中, 1个“为什么”的原因不一定只有一个。有数个原因 时,将它们分开来考 虑。 ④不 应边考 虑对策, 边实施5W分析。(边考 虑对策 边进行5W分析的 话,分析会向所考 虑对策的方向 发展,就有可能找不到真正的原因。) ⑤人 为失 误不是原因,而是结果。防范于未然的对策、应注意的 对策(防止不良品的出厂 ),肯定是有的。 ⑥ 对于“没有遵守・・・”和“没能遵守・・・”的对策是不相同的。此外,必须明确是“只有这次”, 还是“ 总是”。
<为什么1 > 螺丝与板之间的 阻力比螺丝转矩 大
5W分析完成后,必须从最后的 “为什么”到“现象”为止倒过 来读一遍,以确认在逻辑上是否 正确。
臂力不够 涂有涂料 螺丝与板间生锈 了
螺丝进入了螺 丝帽部分
螺丝斜的
最后的为什么
螺丝斜的
所以
螺丝进入了螺 丝帽部分
所以
螺丝与板之间的 阻力太大
所以
螺丝与板之间的 阻力比螺丝转矩 大
品 成 交 安 士 环
质 本 期 全 气 境
企业/工厂的6大任务及管理・改进
控制、保持活动的重要性(决定→保持→改进→保持)
1)管理就是定下目标后,努力使目标实现
维持活动 管 理 水 平
保持活动 改进活动
改进活动 时间
2)改进/改革就是提高平均值(管理水平)
企业/工厂6大任务及管理・改进
抛物线型改进活动
(对策方面的注意事项) ①基本上以 5W1H来 记述 ② How以 4M+测量·管理来分解设定 ③考 虑对策成本 ④人 为因素 对策, ・ 应该为不依 赖于人的本 质性 对策 ・不可 为"彻底了解○○”等 必 须系 统化和 规则化
10.不良改进情况汇报单
【用户投诉】改进汇报()
不良品情况 不良现象 原因
改进效果确认 方法及内容确认 判定(年月日)
完结 审核
良
・ 否
要
・ 否
11.结束语
1.在日常工作中我们常常要面对公司内部的质量缺陷和外部的用户投诉。 所以可以说「我们的工作就是解决问题」。
2.因此、发现问题后需要寻求根本原因,解决问题。
3.好不容易找到的根本原因,可以相信能从根本上解决问题。
4.运用「5W分析法」可以顺利找到根本原因并采取行之有效的对策, 该工作会成为我们品质管理方法之一。 5.运用「5W分析法」在降低材料、工资等制造成本的同时,还可以提高客户满 意度。
7. 5W分析的实施
3)一个为什么的原因往往不止一个
有2个以上时,我们将其并列写在分析表上,并各自反复追问为什么。
4)为什么、为什么持续几次?
5W分析的“5”是反复追问为什么“5次”的意思。 并非完全“5次“的意思。有时追问3次便可,有时却要反复追问10次以上。 反复追问到能采取具体的对策防止问题的再度发生。 再追问下去就成了重复或概念性的东西,采取不了具体对策了,这时候就 停止追问为什么。
7. 5W分析的实施
1)”现象”栏的写法
①「哪里不行」,像这样用简洁的词汇来表达。 例:螺丝拧不动。 镀层的厚度超过了规格要求。 ②避免使用2个动词。 不好的例子:电流过大,镀层变厚了。 (是要分析电流过大,还是要分析镀层变厚? 要点不明确。) ③不用抽象、含糊的词汇。 不好的例子:在△△工序中,零部件的组装缺陷很多。 (未明确具体缺陷,不清楚到底要分析什么。) 原材料不好。 (材料方面有什么不好,其解释会因人而异。)
QFD(Quality Function Deployment):品质技能展开 TRIZ(俄罗斯人构思) TM(Taguchi Method/田口理论) :发明问题解决理论 :新品开发方法
○
○
○ ○ ○ ○
3.引言 1.日立电线开展着被称为提高品质运动的活动,2006年开始的 三年规划中一直展开着NewQF21 运动。 “5W分析”作为该运动的具体活动项目,被采用并普及至今。 2.「5W分析」不是机械性的分析方法。 通过该指南,坚持运用5W分析,才会寻求到合适的分析方法。 充分理解这一点很重要。不希望大家实施了1次、2次后感觉不 顺,便立即作出「5W分析」没有用的结论。 多多坚持实践并积累经验很重要。
④ 采用分析产生原因与流出原因两个方面比较好。 ⑤ 采用过去时态来分析。 「做过」 「当时怎么样」 ⑥ 不使用像「太忙了」等辩解、借口。 ⑦ 不使用「太乐观了」等缺乏具体内容的词汇。 例:想法太乐观了。 ⇒ 我原认为是△△△也可以。 ⑧ 不仅仅写有关自己、本部门的事情,也可写上上一级或其他部门的情况。 根据需要,我们还可以按照部门分析。
一个为什么未必 只有一个原因
反复问为什么,知道不 能采取具体对策为止, 不一定问5次。
事先准备
< 2W >
< 3W >
<nW >
原 因
“现象”栏的写法 ①用简介的语句表达。 ②避免用2个动词。 ③不用抽象和含糊的词汇。
最后从根本原因至现象进行逻 辑性的追究。
6. 5W分析的事先准备
1)整理问题,详细了解事实情况。
4. 什么是5W分析
1) 5W分析是指不能凭随便想象来考虑现象所产生的主要原因 而是要有规则、有顺序、毫无遗漏地来分析 用原理和原则核实的同时,从理论上来查明。 2) 最后的「为什么」是现象所产生的根本原因。 对此、必须能切实有效地阻止,(采取防止再度发生的对策。)
3) 生产现场的根本原因一般不是夹具、设备的零部件, 而多为这些的设计构思、制造安装、操作方法、保养程序和方法 (包括清扫、加油、拧紧和检查)等想法、做法、管理方法。 4) 在达到这样的状态之前不以多问「为什么」的形式来查明的话, 就不能得到持续性的效果。
8.事例介绍
(事例-2) <1W> <2W> <3W>
追究设备停止原因
< 现 象>
生产设备停止
润滑油不足
循环泵的转轴磨损
金属屑进入到轴部
<4W>
<5W> <6W>
过滤器破损,产生小的空隙
过滤器已经超过其使用寿命
缺乏跟换过滤器的相关制度
<对
策 >
将跟换过滤器制度化
8.事例介绍
(事例-3) <1W> <2W> <3W> <4W> <5W>
「现象」
螺丝拧不动
所以
8.事例介绍
(事例-1) <1W>
追究未能赶上公车原因
< 现 象>
错过班车
睡过头了
<2W> <3W>
3点才睡觉,很晚了。(一般为11点睡觉)
回家晚了(一般是7点回家)
<4W>
工作没来得及做完。
<5W>
新的任务,工作安排时,时间预估过少。
< 对 策>
为了提高工作安排精确率,需要向有经验人员请教。
5)最后从“根本原因”向“现象”追溯验证。
倒过来重新读一遍,来验证逻辑上是否存在不自然的地方。 如有不自然的地方,说明分析不当,对此部分必须重新分析。
7. 5W分析的实施
< 现 象> 螺丝拧不 动