现代飞行器制造工艺学复习题简答及答案贾玉红何景武新整理
2015飞行器工艺复习学习资料
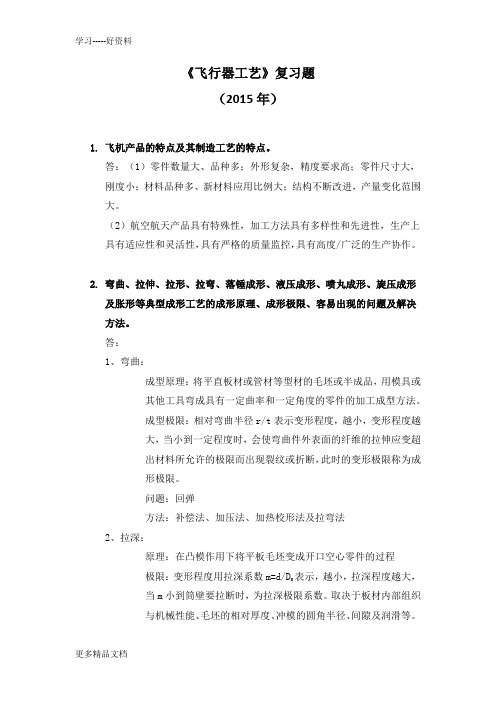
《飞行器工艺》复习题(2015年)1.飞机产品的特点及其制造工艺的特点。
答:(1)零件数量大、品种多;外形复杂,精度要求高;零件尺寸大,刚度小;材料品种多、新材料应用比例大;结构不断改进,产量变化范围大。
(2)航空航天产品具有特殊性,加工方法具有多样性和先进性,生产上具有适应性和灵活性,具有严格的质量监控,具有高度/广泛的生产协作。
2.弯曲、拉伸、拉形、拉弯、落锤成形、液压成形、喷丸成形、旋压成形及胀形等典型成形工艺的成形原理、成形极限、容易出现的问题及解决方法。
答:1、弯曲:成型原理:将平直板材或管材等型材的毛坯或半成品,用模具或其他工具弯成具有一定曲率和一定角度的零件的加工成型方法。
成型极限:相对弯曲半径r/t表示变形程度,越小,变形程度越大,当小到一定程度时,会使弯曲件外表面的纤维的拉伸应变超出材料所允许的极限而出现裂纹或折断,此时的变形极限称为成形极限。
问题:回弹方法:补偿法、加压法、加热校形法及拉弯法2、拉深:原理:在凸模作用下将平板毛坯变成开口空心零件的过程表示,越小,拉深程度越大,极限:变形程度用拉深系数m=d/D当m小到筒壁要拉断时,为拉深极限系数。
取决于板材内部组织与机械性能、毛坯的相对厚度、冲模的圆角半径、间隙及润滑等。
问题:凸缘起皱和筒壁拉裂方法:外皱——压边圈;内皱:带拉深筋的凹模,反向拉伸法和正反向联合拉深法。
多工序拉深,液压机械拉深法。
3、旋压:原理:旋压是借助旋压棒或旋轮、压头对随旋压模转动的板料空心毛坯做进给运动并旋压,使其直径尺寸改变,逐渐成形为空心薄壁回转零件的特殊成型工艺极限:零件锥角越小,材料变形量越大,过大会产生剪切破坏。
4、胀形:原理:在外力作用下使板料的局部材料厚度减薄而表面积增大,或将直径较小的筒形或锥形毛坯,利用由内向外膨胀的方法,使之成为直径较大或曲母线的旋转体零件的加工方法称为胀形。
极限:胀形系数Dmax /D,问题:毛料拉深破裂方法:模具工作表面粗糙度值小、圆滑以及良好的润滑;施加胀形压力的同时施加轴向压力。
现代制造工艺试题及答案

现代制造工艺试题及答案一、选择题(每题2分,共20分)1. 下列哪项不是现代制造工艺的特点?A. 高效率B. 高成本C. 精密化D. 信息化答案:B2. 数控机床与传统机床相比,其最大的优势是什么?A. 价格低廉B. 加工精度高C. 操作简便D. 维护成本高答案:B3. 在现代制造工艺中,CAD/CAM技术的主要作用是:A. 提高材料利用率B. 减少人工成本C. 提高设计和加工效率D. 增加产品多样性答案:C4. 激光加工技术在现代制造中的应用不包括以下哪项?A. 切割B. 焊接C. 铸造D. 打标答案:C5. 快速原型制造技术(RPM)的主要优点是:A. 成本低廉A. 制作周期长B. 制作速度快D. 材料限制多答案:B6. 在制造过程中,六西格玛管理法主要用于:A. 提高产品质量B. 降低生产成本C. 增加产品种类D. 提升员工技能答案:A7. 柔性制造系统(FMS)的核心组成部分是:A. 机器人B. 自动化仓库C. 计算机控制系统D. 传送带系统答案:C8. 超精密加工技术通常可以达到的精度是:A. 微米级B. 毫米级C. 纳米级D. 厘米级答案:C9. 制造业中,ERP系统的主要作用是:A. 提升生产效率B. 优化企业资源配置C. 改善员工福利D. 增强产品竞争力答案:B10. 绿色制造工艺的核心目标是:A. 提高生产速度B. 减少环境污染C. 降低原材料成本D. 提升产品价格答案:B二、填空题(每空2分,共20分)11. 现代制造工艺中的“4M”指的是________、________、________、________。
答案:材料(Material)、机器(Machine)、方法(Method)、测量(Measurement)12. 数控编程中的G代码和M代码分别代表________和________。
答案:运动控制指令、辅助功能指令13. 在制造过程中,CAPP代表的是________。
飞行器设计与制造岗位招聘笔试题与参考答案

招聘飞行器设计与制造岗位笔试题与参考答案一、单项选择题(本大题有10小题,每小题2分,共20分)1、在飞行器设计中,为了提高飞行器的升力系数,下列哪项措施是最直接有效的?A. 增加翼展长度B. 提高飞行速度C. 改变机翼剖面形状,增加弯度D. 加大发动机推力【正确答案】C 【解析】升力系数主要由机翼的形状(尤其是翼型)决定,改变机翼的剖面形状使其更加弯曲(即增大弯度)能够更有效地提升升力系数。
虽然增加翼展也可以增加升力总量,但这是通过增加面积实现的,并非对升力系数的直接影响;提高飞行速度能增加升力,但与升力系数无关;加大发动机推力则主要是改善飞行器的动力性能而非升力特性。
2、在考虑飞行器结构材料的选择时,以下哪个因素不是首要考虑的因素?A. 材料的重量B. 材料的成本C. 材料的颜色D. 材料的强度【正确答案】C 【解析】在飞行器的设计与制造过程中,材料的颜色并不是一个关键的设计因素。
相比之下,材料的重量对于控制飞行器的整体质量至关重要;成本则影响到项目的经济可行性;而材料的强度则是保证飞行器结构安全的基础。
因此,颜色通常不会作为结构材料选择的主要考量点。
3、题干:在飞行器设计中,以下哪个部件属于飞行器的推进系统?A. 飞行控制系统B. 起落架C. 发动机D. 机翼答案:C 解析:发动机是飞行器的推进系统核心部件,它通过燃烧燃料产生推力,使飞行器能够飞行。
飞行控制系统(A)负责控制飞行器的飞行方向和姿态,起落架(B)用于飞行器的起飞和着陆,机翼(D)则负责产生升力。
4、题干:在制造飞行器时,以下哪种材料通常用于制造飞行器的机翼?A. 钢铁B. 铝合金C. 玻璃钢D. 不锈钢答案:B 解析:铝合金因其轻质、高强度和良好的耐腐蚀性,是制造飞行器机翼的常用材料。
钢铁(A)虽然强度高,但重量较大,不适合用于需要减轻重量的机翼制造。
玻璃钢(C)通常用于制造一些非承重结构,而不锈钢(D)虽然强度高,但主要用于需要耐腐蚀的部件。
航空器飞行器组装与总装工艺考核试卷

7.飞机总装后必须进行的飞行前测试之一是起落架的______测试。
()
8.航空器飞行器组装中,复合材料部件常用的连接方法是______。
()
9.为了提高飞机总装的效率,可以采用______装配和自动化程度高的设备。
()
10.在飞机总装工艺中,安全生产的措施之一是保持工作场所的______和______。
D.保持工作场所清洁整齐
(以下为试卷其他部分的格式,具体题目根据需要添加)
二、填空题(本题共10小题,每小题2分,共20分)
三、简答题(本题共5小题,每小题10分,共50分)
四、计算题(本题共2小题,每小题15分,共30分)
五、案例分析题(本题共1题,共20分)
二、多选题(本题共20小题,每小题1.5分,共30分,在每小题给出的四个选项中,至少有一项是符合题目要求的)
A.飞行控制系统测试
B.起落架收放测试
C.导航和通信系统测试
D.发动机试车
E.内饰完整性检查
12.以下哪些材料常用于制作飞机机身结构?()
A.铝合金
B.钛合金
C.碳纤维复合材料
D.不锈钢
E.木材
13.在飞机系统安装过程中的调试内容中,以下哪些是正确的?()
A.液压系统的压力测试
B.电气系统的绝缘测试
C.装配工具的准确性
D.环境温度
E.装配工艺的合理性
16.以下哪些情况可能导致飞机系统安装过程中的问题?()
A.管线和电缆布局不合理
B.系统组件安装不牢固
C.调试程序不当
D.系统设计不合理
E.所有部件安装顺序正确
17.在航空器飞行器组装中,以下哪些环节需要进行无损检测?()
A.零件加工完成后
飞行器制造技术基础考点

①交点互换②飞机结构特点③自由弯曲是指、模具弯曲④工艺补偿⑤干涉配合铆接⑥冲裁中的简单模、连续模和复合模⑦部件装配中的装配基准,装配误差产生因素⑧数字化制造中CAD、CAM、CAPP、CAE、DPA的概念,⑨数控加工的刀轨生成方法⑩尺寸传递原则(独立、修配,联系)适用的场合⑪为什么要过定位⑫飞机的先进制造技术,(材料、连接、加工、装配、检测)装配型架一般构成:飞机装配过程中,常使用的装配基准有三种:基准--确定结构件之间位置的一些点、线、面。
设计基准飞机水平基准线、对称轴线、翼弦平面、框轴线、肋轴线梁轴线、长桁轴线。
设计基准一般都是不存在于结构表面上的点、线、面。
因此,在装配过程中要建立装配工艺基准。
工艺基准:⑴定位基准-确定结构件在工装上的相对位置;⑵装配基准-确定结构件之间的相对位置;⑶测量基准-测量结构件装配位置尺寸的起始位置。
两种装配基准:1、以骨架为基准误差积累由内向外骨架零件外形制造误差◆骨架的装配误差◆蒙皮的厚度误差◆蒙皮和骨架贴合误差◆装配后变形2、以蒙皮外形为基准误差积累由外向内◆装配型架卡板外形误差◆蒙皮和骨架贴合误差◆装配后变形装配型架的骨架的形式主要有梁式;单块式;多墙式飞机制造工艺特点1)为保证结构零件的加工精度和各种整体壁板件的应用,广泛使用大量的先进的数控加工设备;2)为保证结构众多的零部件在装配阶段的外形准确度,必须使用大量的夹具、装配型架;3)为了满足使用维护要求,便于拆卸与安装,需要进行合理的确定设计分离面;4)根据不同的结构布局,采用合理的接头连接方式;主要有各种螺栓连接、胶接、铆接、焊接等;5)在保证结构具有足够的刚度、强度及抗疲劳特性的情况下,为了使结构重量最轻,大量采用新材料,如各种合金材料、复合材料等。
制造准确度和协调准确度☐制造准确度:飞机零件、组合件或部件的实际尺寸与图纸上所规定的名义尺寸相符合的程度。
符合程度越高,则制造准确度越高,也就是说制造误差小。
飞机制造工艺学练习题(修改)

飞机制造⼯艺学练习题(修改)《飞机制造⼯艺学》⼀、简释下列概念(每题2分)1、制造准确度:飞机零件,组合件或段部件的制造准确度是指实际⼯件和设计图纸上所确定的理想的⼏何尺⼨和形状相近似的程度,近似程度越⾼,则制造准确度越⾼。
2、协调准确度:指两个相配合的零件,组合件或段部件之间配合的实际尺⼨和形状相近似的程度。
3、设计补偿:在不影响设计使⽤要求的前提下,从结构设计上采取相应措施,保证两个相配合零件中的⼀个可以在⼀定范围内调节相配合尺⼨,满⾜协调要求4、⼯艺补偿:在⼯艺过程中根据实际情况采取的补偿措施5、理论模线:控制飞机各个不见理论外形的模线6、结构模线:飞机部件某个切⾯1:1的结构装配图7、样板:是零件、组合件的制造依据和检验依据,起着图纸和量具的双重作⽤,它是飞机制造中的特种图纸,是⽆刻度的专⽤量具(基本样板、⽣产样板、外形样板、展开样板、切⾯样板、切割钻孔样板)8、弯曲回弹:钣料在塑性变形的同时,存在弹性变形,由于弯曲时钣料剖⾯内同时存在压应⼒和拉应⼒,所以当外载荷卸除后,弯曲件要发⽣⾓度和半径的弹性回跳9、拉深系数:将平板⽑料拉深模压成⼀个空⼼零件,筒形件外径d与⽑料直径D的⽐值,⽤m表⽰10、强⼒旋压:旋轮在机械动⼒作⽤下强⼒挤压材料,使其厚度发⽣预定的变薄量。
(⼯件的成形纯粹是依靠材料有计划的变薄来完成,⽑料的外径在成形过程中始终保持不变)11、胀型⼯艺:胀形是将直径较⼩的筒形或锥形⽑胚利⽤由内往外膨胀的⽅法成形为直径较⼤或有曲形母线的旋转体零件。
可以分为刚性凹模弹性凸模胀形和刚性凸模胀形。
12、蠕变成形:⾦属材料在⼀定温度和载荷作⽤下的缓慢变形,随着时间的增加,变形量增⼤,如果载荷增⼤或温度升⾼则材料变形速度增加13、超塑性成形:当温度升到某以特定温度时,材料在很微⼩的载荷作⽤下就会产⽣很⼤的变形,⽽不发⽣西颈现象和断裂14、整体壁板:整块板加⼯成蒙⽪、桁条与框、肋等整体结构,减少零件和接件的数量15、正挤压法:⾦属流动⽅向与挤压⽅向相同16、⼯艺分离⾯:是由于⽣产上的需要,为了合理的满⾜⼯艺过程的要求,按部件进⾏⼯艺分解⽽划分出来的分离⾯。
国企招聘飞行器设计与制造岗位笔试题及参考答案
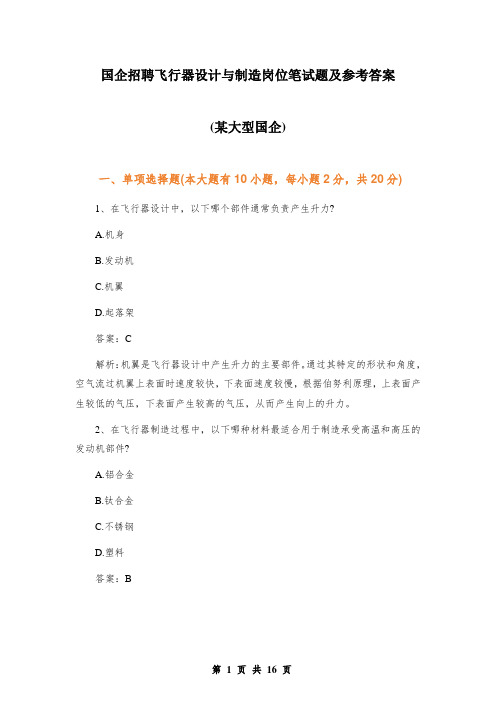
国企招聘飞行器设计与制造岗位笔试题及参考答案(某大型国企)一、单项选择题(本大题有10小题,每小题2分,共20分)1、在飞行器设计中,以下哪个部件通常负责产生升力?A.机身B.发动机C.机翼D.起落架答案:C解析:机翼是飞行器设计中产生升力的主要部件。
通过其特定的形状和角度,空气流过机翼上表面时速度较快,下表面速度较慢,根据伯努利原理,上表面产生较低的气压,下表面产生较高的气压,从而产生向上的升力。
2、在飞行器制造过程中,以下哪种材料最适合用于制造承受高温和高压的发动机部件?A.铝合金B.钛合金C.不锈钢D.塑料答案:B解析:钛合金因其优异的耐高温、耐腐蚀和强度特性,是制造承受高温和高压发动机部件的理想材料。
铝合金虽然轻便,但耐高温性能较差;不锈钢主要用于耐腐蚀环境;塑料则通常不耐高温,不适合用于发动机部件。
3、在飞行器结构设计中,以下哪种材料因其高强度重量比而被广泛使用?A.铝合金B.钢材C.复合材料D.钛合金【答案】C.复合材料【解析】复合材料由于其轻质高强的特点,在现代飞行器的设计中占据重要地位。
相比于铝合金、钢材和钛合金,它们能够提供更好的重量强度比,这对于减少飞行器的自重、提高燃油效率至关重要。
4、在飞行器的设计过程中,空气动力学分析主要用于解决哪些方面的问题?A.确定最合适的机身形状B.计算飞行器的最大载重量C.分析飞行器在不同飞行阶段的稳定性D.选择最适合的发动机类型【答案】A.确定最合适的机身形状和C.分析飞行器在不同飞行阶段的稳定性【解析】空气动力学分析对于飞行器设计至关重要,它不仅帮助工程师确定最佳的机身外形来减少阻力和提升气动效率,同时也用于评估飞行器在起飞、巡航、降落等不同阶段的稳定性和操控性。
选项B和D虽然也是设计过程中的重要内容,但它们更多地与结构工程和动力系统的选择有关,而不是直接由空气动力学决定。
注意,这里正确答案有两个选项,但按照单项选择题的要求,通常只会有一个最贴切的答案,因此在实际考试中,这道题应当修改为更明确的形式,这里仅为了说明目的而列出两个相关答案。
航空运动飞行器制造工艺与质量控制考核试卷
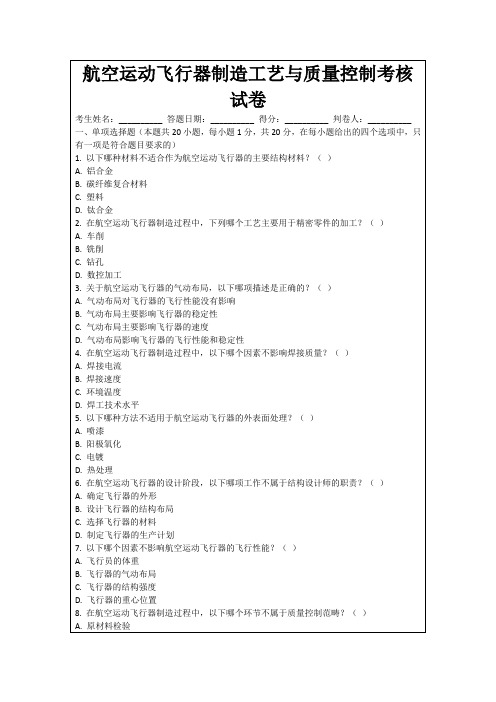
D.生产环境温度变化
(以下为其他题型,请根据实际需求自行设计)
二、多选题(本题共20小题,每小题1.5分,共30分,在每小题给出的四个选项中,至少有一项是符合题目要求的)
1.以下哪些材料常用于航空运动飞行器的制造?()
A.铝合金
B.钢
C.塑料
D.碳纤维复合材料
2.航空运动飞行器制造过程中,以下哪些因素会影响焊接质量?()
C.飞行试验
D.生产线布局
9.以下哪种方法不适用于航空运动飞行器的无损检测?()
A.射线检测
B.超声波检测
C.红外线检测
D.磁粉检测
10.在航空运动飞行器制造过程中,以下哪种设备主要用于金属材料的切割?()
A.车床
B.铣床
C.钻床
D.激光切割机
11.关于航空运动飞行器的质量控制,以下哪项措施是正确的?()
航空运动飞行器制造工艺与质量控制考核试卷
考生姓名:__________答题日期:__________得分:__________判卷人:__________
一、单项选择题(本题共20小题,每小题1分,共20分,在每小题给出的四个选项中,只有一项是符合题目要求的)
1.以下哪种材料不适合作为航空运动飞行器的主要结构材料?()
A.结构完整性
B.飞行控制系统
C.气动布局
D.飞行员的操作技能
9.在航空运动飞行器制造过程中,以下哪些措施有助于提高产品质量?()
A.严格的原材料检验
B.定期的设备校准
C.加工过程的质量控制
D.完善的员工培训
10.以下哪些方法可用于航空运动飞行器的结构优化?()
A.有限元分析
B.模态分析
C.优化设计软件
- 1、下载文档前请自行甄别文档内容的完整性,平台不提供额外的编辑、内容补充、找答案等附加服务。
- 2、"仅部分预览"的文档,不可在线预览部分如存在完整性等问题,可反馈申请退款(可完整预览的文档不适用该条件!)。
- 3、如文档侵犯您的权益,请联系客服反馈,我们会尽快为您处理(人工客服工作时间:9:00-18:30)。
1. 飞机产品的特点及其制造工艺的特点。
飞机产品的特点:1、零件数量大、品种多2、外形复杂、精度要高3、零件尺寸大、刚度小4、材料品种多,新材料应用比例大5、结构不断改进,产量变化范围大制造工艺的特点:1、需采用新的保证互换性的方法-模线样板工作法;2、生产准备工作量大,需采用大量模具、夹具、型架等工艺装备,数字化制造技术;3、批量变化范围大,手工劳动量大,现在用柔性制造技术;4、零件加工方法多种多样,装配劳动量比重大;5、生产协作能力强,推行并行工程。
2. 弯曲、拉伸、拉形、拉弯、落锤成形、液压成形、喷丸成形、旋压成形及胀形等典型成形工艺的成形原理、成形极限、容易出现的问题及解决方法。
弯曲:成型原理:弯曲是将平直板材或管材等型材的毛坯或半成品、用磨具或其他的工具弯成具有一定曲率和一定角度的零件的加工成型方法。
材料外层纤维受拉,内层纤维受压,中性层不变。
成形极限:当万区间相对弯曲半径小到一定程度时,会是万区间外表面纤维的拉伸应变超过材料所允许的极限而出现裂纹或折断,此时的变形记先成为成形极限。
相对弯曲半径r/t 达到材料即将破裂的极限是的min r问题:主要问题是回弹。
解决办法:补偿法、加压法,加热校形法及拉弯法。
拉伸原理:拉伸是在凸模作用下将平板毛坯变成开口空心零件的过程。
(凸缘切向收缩为筒壁,筒壁为传力区)成形极限:当壁筒要拉断时的拉伸系数为极限拉伸系数。
在筒壁将要拉断时的最小拉伸系数0/m d D容易出现的问题:凸缘起皱和筒壁拉裂。
解决办法:用压边圈防止外皱。
用带拉伸筋的凹模、反向拉伸法和正反向联合拉伸法防止内皱。
拉形原理:拉形时板料两端在拉形机夹钳夹紧的情况下,随着拉形模的上升,板材与拉形模接触产生不均匀的双向拉伸变形,是板料与拉形模逐渐贴合的成型方法。
成形极限:在拉形时,挡板料濒于出现不允许的缺陷时的拉形系数max 0/l l 。
容易出现的问题:拉裂、起皱。
解决办法:防止拉裂的主要方法是控制一次拉形变量;防止起皱可使夹头钳口取现金量符合模具两端对应曲面的剖面形状,在操作中正确配合夹头拉伸和台面上顶的动作。
拉弯原理:拉弯是将毛料在弯曲的同时加以轴向拉力,改变毛料剖面内的应力分布情况,使之趋于均匀一致,以达到减少回弹,提高零件成形准确度的目的。
成形极限:拉断常见问题:回弹量较大解决办法:先拉后弯,先弯后拉,先拉后弯再补拉。
落压成型原理:利用质量很大的锤头或上模从高处落下时所产生的巨大的冲击力是,使毛料沿着成型模成形。
成形极限:易出现的问题:材料起皱或破裂 解决方法:预成形;采用展开料成形;分区依次成形;采用储料过渡液压成形原理:采用液态的水或油作为传力介质,用软凸模或凹模代替刚性的凸模或凹模,使坯料在传力介质的压力作用下与凹模或凸模贴合的过程成形极限:相对弯曲半径R/t 以及成型压力P易出现的问题:材料的起皱开裂和不贴模解决方法:尽量采用新淬火料进行成形,同时尽可能采用展开料成形,以免除修边工作。
喷丸成形:利用高速弹丸流撞击金属板的表面,使喷丸表面及其下层金属材料受挤压产生塑性变形而向四周延伸,表面面积扩大,从而逐步使板材发生向喷丸面凸起的弯曲变形,从而达到所需变形成形极限:对一定的喷丸设备的弹丸,采用最大覆盖率喷完成形特定材料和厚度的零件时,所获的变形量时一定的,即相应条件下的喷丸成形极限 易出现的问题:受壁板外形和结构特点限制,部分壁板难以成形解决办法:采用预应力喷丸成形技术以提高喷丸变性能力旋压成型:借助旋压棒或旋轮、压头对随旋压模转动的板料或空心毛坯做进给运动并旋压,使其直径尺寸改变,逐渐成形为薄壁空心回转零件成形极限:工件的尺寸形状和厚度问题:表面出现沟槽 解决:在不同的胎膜上进行连续旋压胀形:在外力作用下使板料的局部材料厚度减薄而表面积增大,或将直径较小的筒形或锥形毛坯,利用由内向外膨胀的方法,使之成为直径较大或曲母线的旋转体零件 极限:胀形系数max 0D D ,max D 其中为零件变形最大处的直径;0D 为零件变形最大处的原始直径问题:毛坯拉伸破裂解决:在胀形是施加轴向推力是管坯压缩3. 什么是结构复合材料,什么是功能复合材料,复合材料在性能上有哪些特点。
结构复合材料:主要作为承力结构使用的材料,由能够承受载荷的增强体组元与能联结增强体成为整体材料同时又起传力例作用的基体组元构成的复合材料。
功能复合材料:指除力学性能意外还能够提供其他物理、化学、生物等性能的复合材料。
复合材料性能上的特点:1、材料具有可设计性2、比强度高及比刚度大3、抗疲劳性能好4、高温性能好5、制造工艺简单6、结构可实现功能智能化4.试说明聚合物基复合材料预成形件/树脂转移成形工艺方法(RTM方法)的特点与适用范围。
RTM特点:整体性好,减少机械连接,近无余量加工,与手工铺放比工时少,可采用低成本的纤维/树脂体系;有效的改善了劳动强度和环境条件;可提高复合材料的设计需用应变。
适用范围:适用于各种铺放形式与毛坯构型的复杂构件。
5.什么是设计分离面和工艺分离面?设计分离面:飞机的零件根据使用功能、维护修理、方便运输等方面的需要、设计人员对整架飞机的结构要划分为许多部件,这些部件之间所形成的可拆卸的分离面称为设计分离面。
工艺分离面:在装配过程中,为了生产需要,将飞机结构进一步划分称为组合件和板件,这些板件、段件或组件之间一般采用不可拆卸的连接,这种为了满足工艺过程要求而划分的称为工艺分离面。
6.提高装配准确度的补偿方法有哪些。
1、装配时相互修配2、装配后精加工3、垫片补偿4、连接补偿件5、可调补偿件7.飞机装配基准的选择方法及误差积累特点。
1、以骨架外形为基准:将骨架在型架上装配好,然后再蒙皮上施加外力,使蒙皮贴紧在骨架上并连接在一起。
误差累计特点:骨架零件制造的外形误差骨架的装配误差蒙皮的厚度误差蒙皮与骨架由于贴合不紧而产生的误差装配连接的变形误差2、以蒙皮为基准:是将部分骨架零件分别装在蒙皮上,然后在型架上施加外力,使蒙皮外形贴紧在卡板上,最后将骨架连接起来。
误差:装配型架卡板的外形误差蒙皮和卡板外形之间由于贴合不紧而产生误差装配连接的变形误差8.互换与协调的概念及相互关系,三种协调原则及其特点。
互换:指的是独立制造的零件(组合件、部件),装配时无需补充加工,就能满足产品使用要求;亦指一般互换的零件(组合件、部件)能与另一同样的零件(组合件、部件)互相代替,装配时不经任何修配,即可保证产品性能。
协调:指两个相互配合的零件(组合件、部件)之间,其配合部位的几何形状和尺寸的相符合程度。
互换是指同一种工件之间的一致性,它通过控制制造误差来达到。
协调是指相配合工件之间配合尺寸、形状的一致性,它可以通过控制制造误差来达到,也可以通过修配来达到。
互换的一定是协调的,协调的不一定是互换的。
独立制造原则:为保证互换性所需的协调准确度,就必须对零件制造的准确度提出很高的要求。
这与飞机制造的具体情况正好相反,因为在飞机制造总,对协调准确度比制造准确度要求更高;尤其是表明情况复杂的零件,技术上难度大,经济效果差。
因此,独立制造原则比较适用于那些形状简单的零件,例如起落架、操纵系统等机械加工类零件。
有利一面:生产过程中能够平行地制造飞机零件、组合件和部件,以及各种工艺装备。
不受工艺装备制造次序的约束,可以扩大制造工作面,有利于缩短生产周期,开展广泛的协作相互联系制造原则:在尺寸专递过程中,共同环数量越多,协调准确度就越高,所以适用于制造形状复杂的零件。
在制造过程中,可以将技术难度大的、制造准确度不高的环节作为尺寸传递的共同环,这样就能大大提高零件之间的协调准确度,对于结构复杂的飞机产品,采用这种原则就行协调具有特别重要的现实意义。
但是,为了保证零件互换性所需的工艺装备必须依次制造,工作面受限制,使生产周期拖长,对保证厂际协作不力。
相互修配原则:可以保证很高的协调准确度,但难以满足零件互换的要求,而且修配劳动量大,装配周期长,只有当其他协调原则在经济上、技术上都不合理,又不要求零件互换性时,才选用这种原则,一般在飞机的试制中应用较多,而成批生产中应用较少。
9.铆接、螺接、胶接、焊接、胶焊等各种连接方法的特点。
铆接:连接强度比较稳定可靠,铆接方法与工艺参数容易掌握和控制,铆接质量检验方便,故障比较容易排除,使用工具比较简单、价廉,适用于较复杂结构的连接。
虽然存在一些缺点,增加了结构质量,降低了结构强度,容易引起变形,仍是飞机装配中主要的连接方式螺接:螺栓的受力形式有拉、剪、拉剪三种,应根据受力形式选用不同形式的螺栓。
在飞机装配中数量不断增加。
除标准螺栓,还有高锁螺栓和锥型螺栓,质量轻,体积小,耐振动,夹紧力大,耐疲劳性高,密封性好,安装简单,但结构复杂,成本高。
胶接:不削弱基体材料,形成的连接缝是连续的,受力均匀,能改善板材支持情况,提高临界应力,减轻结构重量,提高结构的疲劳强度和破损安全性;胶接结构表面平滑,有良好的气动力性能;胶缝本身有良好的密封性,适用于气密舱和整体油箱等要求密封的结构;劳动量显着低于铆接,成批生产时成本也低于铆接;胶层对金属有防腐保护作用,可以绝缘,防止电化学腐蚀;使用材料范围广,金属材料之间、非金属材料之间、金属与非金属材料之间;对材料、工艺条件的环境应力极为敏感,剥离强度低,不易检查,无损检测方法不完善,环境温度有限制。
焊接:生产效率高,成本低,比铆接结构质量轻,表面光滑,改善了劳动条件,疲劳强度比铆接低20%。
胶焊:焊接头质量轻,静强度高,可靠性好,胶接头良好的疲劳特性和密封性,力学性能十分优良10.铆接、胶接的工艺过程。
铆接:确定钉孔位置,制铆钉孔及制埋头窝,放铆钉,铆接胶接:预装配,胶接表面制备,涂胶和晾置(或烘干),装配,固化,胶缝清理和密封,试验和检验11.飞机总装包括哪些内容。
飞机机体各部件的对接及水平测量;安装调整发动机、燃油和滑油系统,安装和调整发动机操纵系统;液压和冷气系统的设备、附件和导管的安装、敷设和实验;起落架极其收放机构、信号系统的安装、调整和实验;飞机操纵系统的安装和调整;电器、无线电、仪表设备与电缆的安装、敷设和实验;高空救生设备的安装和实验;特种设备的安装和实验。
12.什么是CAD/CAE/CAPP/CAM/PDM,并简述它们之间的关系。
CAD/CAE/CAPP/CAM分别是计算机辅助设计,计算机辅助工程分析,计算机辅助工艺过程设计,计算机辅助制造的英文缩写。
他们是制造业信息化中数字化设计与制造技术的基础,是实现计算机辅助产品开发的主要工具。
PDM是产品数据管理的缩写,是某一类软件的总称。
PDM技术集成并管理与产品相关的信息、过程及人与组织,实现分布环境中的数据共享,为异构计算机环境提供了集成应用平台,从而支持CAD/CAE/CAPP/CAM系统过程的实现。