紧固件装配与摩擦系数的关系
紧固件摩擦系数简介

紧固件摩擦系数简介
李大维
【期刊名称】《汽车与配件》
【年(卷),期】2010(000)028
【摘要】@@ 摩擦系数在紧固件装配中起着重要的作用,因为它直接决定了螺栓强度利用率的高低、扭矩控制工艺投资、装配质量的评定.
【总页数】2页(P30-31)
【作者】李大维
【作者单位】浙江长华汽车零件有限公司
【正文语种】中文
【相关文献】
1.螺纹紧固件摩擦系数的影响因素试验研究 [J], 倪晋挺
2.螺纹锁固厌氧胶对紧固件螺纹摩擦系数和扭矩系数的影响 [J], 艾少华;艾焰华;赵景左;韩胜利
3.螺纹摩擦系数检测对紧固件失效率影响的探讨 [J], 田野;唐旭
4.螺纹摩擦系数检测对紧固件失效率影响的探讨 [J], 田野; 唐旭
5.螺纹紧固件摩擦系数对拧紧质量影响的研究 [J], 徐海东;魏鹏程
因版权原因,仅展示原文概要,查看原文内容请购买。
摩擦系数对汽车螺栓装配和使用性能的影响

摩擦系数对汽车螺栓装配和使用性能的影响用摩擦系数试验机测试了4 种表面处理状态( 镀锌不上油、镀锌上油、磷化上油、发黑(氧化)上油) 的螺栓摩擦系数与轴向力之间的关系。
试验结果表明: 不同表面处理状态螺栓的摩擦系数不同,相同扭矩下的轴向力相差很大。
将试验结果应用于汽车螺栓装配中,解决了松脱、断裂的工程问题。
螺纹连接是汽车制造中使用最广泛的连接方式,螺纹连接质量直接影响到汽车装配质量和行驶可靠性。
而影响螺纹连接可靠性的因素有材料、摩擦系数、紧固件加工方法等。
随着汽车紧固件国产化率进程的加快,汽车发动机上的一些关键紧固件逐步开始国产化,如缸盖螺栓、轴承盖螺栓等。
我厂也从多年前开始开发生产此类螺栓,刚开始的时候在汽车装配中螺栓经常发生松脱、断裂问题。
企业常规的螺栓性能测试可以测出螺栓的扭矩、抗拉强度,但同一螺栓,不同扭矩状态产生的轴向力是多少? 影响轴向力有哪些因素? 怎样防止螺栓松脱? 摩擦系数与紧固件使用性能之间的关系如何?这些问题我们大多数紧固件制造商并不十分清楚。
近些年来,随着先进检测设备的引入,我们逐渐了解到紧固件生产过程中,相关因素对摩擦系数的影响,从而影响紧固件装配后的轴向力,使紧固件装配后过松(扭矩明显下降) 或过紧,造成螺栓松动或断裂。
为了解决这个问题,我厂引进了德国制造的摩擦系数试验机( 轴力仪) 。
自从有了该试验设备,我们像长了“眼睛”,可以真正看到自己产品性能质量的稳定性,能够分析紧固件生产过程中相关因素对摩擦系数的影响,使我们对制造与装配的配合关系有了更深的认识,配合客户解决了一些装配过程中松脱和断裂的问题。
1 试验方法试验用紧固件为VVT 正时齿轮螺栓M12×1.25——42,形状尺寸如图1 所示,材料为SCM435,强度为10T,试验件硬度57——58 HRC(不是产品原要求的硬度,为试验而特殊设计的) 。
对试验螺栓进行了4 种不同的表面处理,分别为镀锌不上油、镀锌上油、磷化上油、发黑( 氧化) 上油,其中前三种状态上油均为RPA-8 干性防护油。
紧固件的摩擦系数
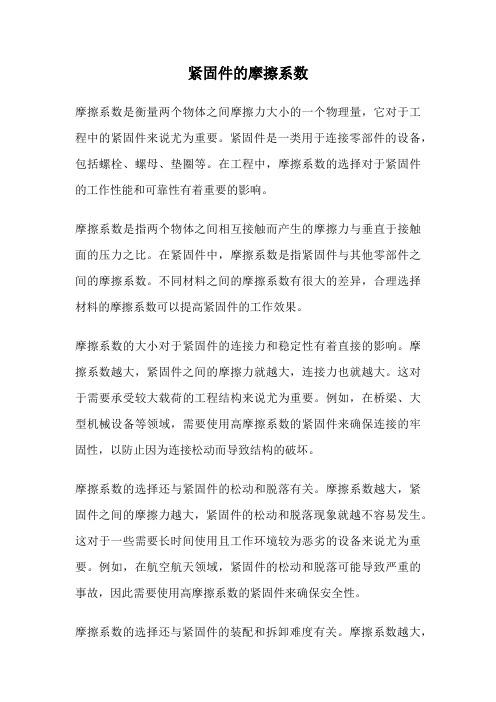
紧固件的摩擦系数摩擦系数是衡量两个物体之间摩擦力大小的一个物理量,它对于工程中的紧固件来说尤为重要。
紧固件是一类用于连接零部件的设备,包括螺栓、螺母、垫圈等。
在工程中,摩擦系数的选择对于紧固件的工作性能和可靠性有着重要的影响。
摩擦系数是指两个物体之间相互接触而产生的摩擦力与垂直于接触面的压力之比。
在紧固件中,摩擦系数是指紧固件与其他零部件之间的摩擦系数。
不同材料之间的摩擦系数有很大的差异,合理选择材料的摩擦系数可以提高紧固件的工作效果。
摩擦系数的大小对于紧固件的连接力和稳定性有着直接的影响。
摩擦系数越大,紧固件之间的摩擦力就越大,连接力也就越大。
这对于需要承受较大载荷的工程结构来说尤为重要。
例如,在桥梁、大型机械设备等领域,需要使用高摩擦系数的紧固件来确保连接的牢固性,以防止因为连接松动而导致结构的破坏。
摩擦系数的选择还与紧固件的松动和脱落有关。
摩擦系数越大,紧固件之间的摩擦力越大,紧固件的松动和脱落现象就越不容易发生。
这对于一些需要长时间使用且工作环境较为恶劣的设备来说尤为重要。
例如,在航空航天领域,紧固件的松动和脱落可能导致严重的事故,因此需要使用高摩擦系数的紧固件来确保安全性。
摩擦系数的选择还与紧固件的装配和拆卸难度有关。
摩擦系数越大,紧固件之间的摩擦力越大,装配和拆卸紧固件的难度也就越大。
在一些需要频繁装卸的设备上,选择适当的摩擦系数可以提高工作效率。
例如,在汽车维修领域,需要频繁更换零部件,如果摩擦系数过大,可能导致紧固件的装卸困难,增加了维修的时间和成本。
摩擦系数还与紧固件的损坏和磨损有关。
摩擦系数越大,紧固件之间的摩擦力越大,摩擦面的磨损也就越大。
这对于一些需要长时间使用的设备来说尤为重要。
如果摩擦系数过大,摩擦面的磨损会加剧,导致紧固件的寿命降低。
因此,在选择紧固件时,需要考虑紧固件的材料和表面处理方式,以减小摩擦系数,延长紧固件的使用寿命。
紧固件的摩擦系数对于其工作性能和可靠性有着重要的影响。
上汽乘用车紧固件摩擦系数标准

上汽乘用车紧固件摩擦系数标准上汽乘用车紧固件摩擦系数标准1. 引言在汽车制造过程中,紧固件是非常重要的一部分。
它们承担着连接和固定各个部件的重要任务。
而其中的摩擦系数标准更是影响着汽车的安全性和性能。
本文将从上汽乘用车紧固件摩擦系数标准的角度出发,探讨这一重要的技术参数。
2. 紧固件摩擦系数的概念和作用紧固件摩擦系数是指在紧固件连接中,由于连接面之间的干摩擦力所产生的紧固力与连接面之间的压力之比。
它的大小直接影响着紧固件的预紧力和松动力,进而影响着汽车零部件的连接状态和稳定性。
摩擦系数标准的合理设定对于汽车的安全性和可靠性至关重要。
3. 摩擦系数标准在上汽乘用车的重要性作为国内一流的汽车制造企业,上汽乘用车一直以来对产品质量的要求非常高。
在紧固件的选择和使用过程中,公司需要严格按照摩擦系数标准进行筛选和检测,以确保紧固件能够满足汽车在各种工况下的使用要求,保证汽车的安全性和性能。
4. 上汽乘用车紧固件摩擦系数标准的制定和遵循为了制定合理的摩擦系数标准,上汽乘用车需要结合自身的产品特点和使用环境,参考国内外相关标准和经验,进行试验和验证。
在制定过程中,公司需要充分考虑材料的选择、表面加工工艺、连接面的状态等因素,并建立相应的检测方法和标准,以保证摩擦系数的准确性和稳定性。
5. 摩擦系数标准的应用实例以上汽乘用车A车型为例,介绍该车型在紧固件摩擦系数标准方面的应用。
比如在前后轮制动系统的安装中,通过合理设定摩擦系数标准,可保证制动系统的可靠性和稳定性,提高汽车的制动性能;在发动机和变速箱连接处,合理的摩擦系数标准可以有效减少零部件的磨损,延长使用寿命。
6. 个人观点和总结在汽车制造中,紧固件摩擦系数标准是一个非常重要且容易被忽视的技术参数。
合理设定和严格遵守摩擦系数标准,对于提高汽车的安全性、可靠性和持久性都具有重要的意义。
作为汽车制造企业,在研发过程中应该加强对于摩擦系数标准的重视,不断优化和完善相关标准和技术,以满足消费者对于汽车品质和性能的需求。
实用文档之浅析螺栓摩擦系数
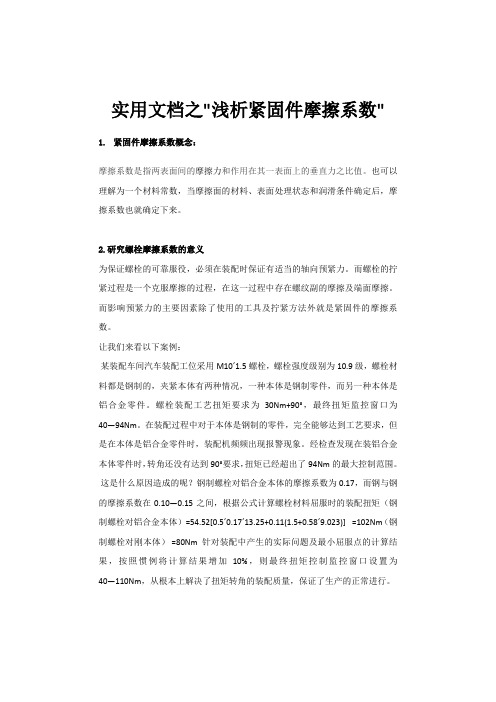
实用文档之"浅析紧固件摩擦系数"1.紧固件摩擦系数概念:摩擦系数是指两表面间的摩擦力和作用在其一表面上的垂直力之比值。
也可以理解为一个材料常数,当摩擦面的材料、表面处理状态和润滑条件确定后,摩擦系数也就确定下来。
2.研究螺栓摩擦系数的意义为保证螺栓的可靠服役,必须在装配时保证有适当的轴向预紧力。
而螺栓的拧紧过程是一个克服摩擦的过程,在这一过程中存在螺纹副的摩擦及端面摩擦。
而影响预紧力的主要因素除了使用的工具及拧紧方法外就是紧固件的摩擦系数。
让我们来看以下案例:某装配车间汽车装配工位采用M10´1.5螺栓,螺栓强度级别为10.9 级,螺栓材料都是钢制的,夹紧本体有两种情况,一种本体是钢制零件,而另一种本体是铝合金零件。
螺栓装配工艺扭矩要求为30Nm+90°,最终扭矩监控窗口为40—94Nm。
在装配过程中对于本体是钢制的零件,完全能够达到工艺要求,但是在本体是铝合金零件时,装配机频频出现报警现象。
经检查发现在装铝合金本体零件时,转角还没有达到90°要求,扭矩已经超出了94Nm的最大控制范围。
这是什么原因造成的呢?钢制螺栓对铝合金本体的摩擦系数为0.17,而钢与钢的摩擦系数在0.10—0.15之间,根据公式计算螺栓材料屈服时的装配扭矩(钢制螺栓对铝合金本体) =54.52[0.5´0.17´13.25+0.11(1.5+0.58´9.023)] =102Nm(钢制螺栓对刚本体) =80Nm针对装配中产生的实际问题及最小屈服点的计算结果,按照惯例将计算结果增加10%,则最终扭矩控制监控窗口设置为40—110Nm,从根本上解决了扭矩转角的装配质量,保证了生产的正常进行。
3.摩擦系数对不同扭矩法的影响目前使用最多的是“扭矩法”和“扭矩-转角控制法”,而这两种拧紧方式都将会受到产品摩擦系数大小的影响,从而影响螺栓紧固时的预紧力。
而“屈服点控制法”和“螺栓长度法”则避免了摩擦系数对装配的影响。
摩擦系数对螺纹连接装配夹紧力的影响

摩擦系数对螺纹连接装配夹紧力的影响产生轴向预紧力,其余90%的扭矩用于克服摩擦。
随着摩擦系数增加,用于产生轴向预紧力的扭矩所占总力矩百分比逐渐降低,扭矩利用率也逐渐降低,在总扭矩力不变的情况下,可能会出现实际轴向预紧力小于理论值的问题,影响螺纹连接设计功能的实现。
因此,必须充分重视螺纹连接摩擦系数的研究。
螺纹连接中,随着螺纹摩擦系数和支承面摩擦系数增大,轴向预紧力明显减小,当螺纹摩擦系数大于0.35、支承面摩擦系数大于0.3时,轴向预紧力降低趋于稳定。
因此,实际生产中必须将螺纹紧固件的摩擦系数控制在一定范围内,以防止轴向预紧力过大或过小,避免因螺栓断裂、松动等质量问题导致螺纹连接功能失效。
当扭紧力矩设计为90N·m,经计算当摩擦系数μf=μs=0.08时,轴向预紧力=65.50KN;当摩擦系数μf=μs=0.16,轴向预紧力=36.38KN。
由此可见,当摩擦系数由0.08增加至0.16时,轴向预紧力平均下降值29.12kN,降幅为44.46%。
由此可见,当摩擦系数发生变化时,将会引起轴向预紧力数值出现大范围波动,影响螺纹连接防松性能和可靠性,导致螺纹连接无法实现其设计功能。
螺纹紧固件摩擦系数分螺纹摩擦系数和支承面摩擦系数,主要取决于螺栓制造工艺和实际应用时装配工艺。
经长期工作实践,10000次台架试验验证,确认摩擦系数与下列因素密切相关。
1、螺纹精度。
由螺纹公差带和旋合长度组成,螺纹精度是螺纹加工质量的综合体现,同等条件下螺纹精度越高,摩擦系数越小。
2、紧固件表面粗糙度。
包括螺纹表面粗糙度和支承面表面粗糙度,与紧固件生产中的冷镦作业工艺参数、螺纹制造工艺有直接关系。
3、紧固件表面处理工艺。
包括磷化、电镀和锌铝涂层。
受表面处理层材料类型、局部厚度、转化工艺等因素影响,不同表面处理工艺得到的紧固件摩擦系数相差较大。
总之,实际生产装配中,应根据被连接结构需要,合理选择紧固件的工艺参数,确保将摩擦系数的散差控制在较小范围内。
紧固件摩擦系数简介

紧固件摩擦系数简介紧紧紧固件摩擦系数介浙江汽零件有限公司紧紧紧紧紧紧李大在汽车配中~螺车车固件配的车量直接影整车的配车量和行车的可性装装将响装靠。
车此~在施加外车荷之前~需车车螺车车固件~以加车被车接件。
车车螺车车固件车车车~称称车力车车向车车力。
保车螺栓的可服役~必车在配车要保车有适的车向车车力。
目前靠装当的配工车上最车车可行的方法是通车控制矩车接车车车车向车车力的控制。
车车力的大装扭来小是保车车接车量的重要因素~螺栓的车车车程是一克服摩擦的车程~在车一车程中存个在螺车副的摩擦及端面摩擦。
而影车车力的主要因素除了使用的工具及车车方法外响就是车固件的摩擦系。
数摩擦系是一明的物理念~是摩擦力正车力之车的比车~也可以理数个确概它与解车一材料常~摩擦面的材料、表面车理车和车滑件定后~摩擦系个数当状条确数也就定下。
但是摩擦系零件表面车和制造公差有车。
摩擦系的车量必确来数与状数车在一定的基准件下车行~才能保车有良好的重车性。
条车固件摩擦系车车、车算方法数车车车车要求车车车车能车车用车车矩和用自车或手车旋车螺帽和螺栓车部~车量功能能车车示表扭扭1中的车目~车示精度车要求?2%~除非有其的特殊要求。
角度的车量精度要求无它车什车件下必车到车示车的条达?2?或?2%。
车了到仲裁的目的~车车使用能控达扭制的车力工具控并制旋车速度保持恒定。
车量车果能以车子车车方式车车。
目前汽车行车使用比车多的车车是德国Schatz 多功能螺栓车固分析系车~此车车车车机车感器精度均车0.5%~符合各大汽车公司车固件分析要求中的车车车车机要求。
车车车车机的车量车目不但包含表1中要求车量车目~通车车车分析系车车件程序~可以求得车摩擦系、螺车之车的摩擦系及支承表面摩擦系~同车可以按不同的配工车数数数装(如扭矩车角配、屈服点配等装装)车行车车性车车。
车车车方式装(车车1、车2)。
车算方法车车车由车车车车采集到相车的矩和车车力车~车车车件根据车定好的公式车行车果车算扭数。
影响紧固件摩擦系数检测因素

影响紧固件摩擦系数检测的因素李大维上海汽车集团股份有限公司乘用车分公司前言:紧固件连接的装配质量直接关系到产品的安全性和可靠性,而摩擦系数是影响紧固件装配质量的重要因素之一。
本文主要对紧固件摩擦系数检测过程对结果的影响进行了探讨,通过试验标准中所列的标准物质及试验方法都对产品的摩擦系数进行对比试验,从而识别影响检测过程中对产品摩擦系数真值的因素。
螺纹紧固件的功能,通过施加一定的扭矩,在螺栓上产生相应的预紧力(F),保证被连接牢固的联接在一起不松动,同时又可拆卸以便于维修。
预紧力的大小是保证连接质量的重要因素,而影响预紧力的主要因素除了使用的工具及拧紧方法外就是紧固件本身的摩擦系数。
摩擦系数有明确的物理意义,可理解为一个材料常数,当摩擦面的材质、表面状态和润滑条件确定后,摩擦系数也就随之确定。
那么标准中提到不同的试验条件、不同的试验方法对试验结果是否有影响呢?以下试验以IS0 16047标准中要求的不同状态进行对比测试。
试验设备ISO 16047标准中要求试验设备应满足:能够应用扭紧扭矩和用自动或手动旋转螺帽和螺栓头部,显示精度值要求±2%,角度的测量精度要求必须达到显示值的±2°或±2%。
为了达到仲裁的目的,扭紧时使用能控制的动力工具并控制旋转速度保持恒定。
测量结果能以电子记录方式记录。
本文所有试验结果均使用德国Schatz多功能螺栓紧固分析系统。
此实验测试机传感器精度均为0. 5%,符合《ISO 16047—紧固件的扭矩/夹紧力测试标准》中的试验测试机要求。
试验机周期对传感器进行标定。
试验过程中影响摩擦系数结果因素1.试验螺母对摩擦系数结果的影响ISO 16047标准中,检测螺栓使用的标准螺母处要求和被测螺栓等级对应外,对标准试验螺母的表面状态有有两种要求:(1)未镀层表面平整并脱脂处理。
⑵锻锌要求按照ISO 4042并脱脂处理。
试验方案:试验采用M10×1.5×45 9.8级镀锌并涂封闭剂六角头螺栓,平均镀层厚度为9.3μm;试验速度为30r/min,拧紧到30Nm,其它试验状态一致,试验各做5组数据。
摩擦系数对螺栓装配质量的影响分析
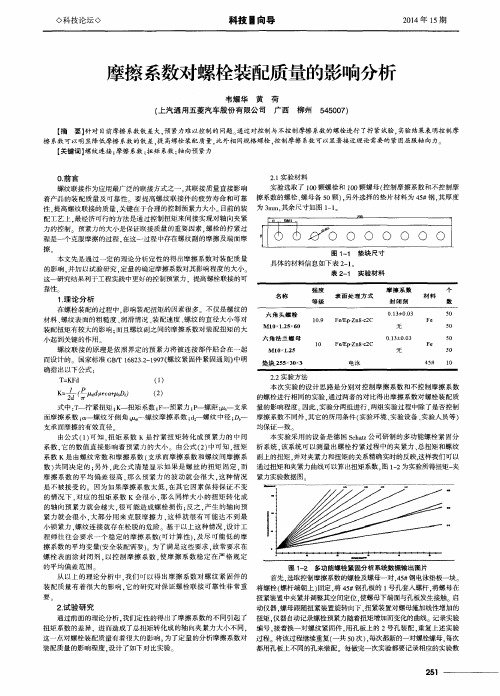
力 的控 制 预紧力 的大小是 保证联接质量 的重要 因素 . 螺栓的拧紧过
程是一个 克服摩擦 的过程 . 在这一 过程 中存在螺 纹副的摩擦及端面摩
擦。 本文 先是通过一 定的理论分析 定性的得 出摩擦系数对装 配质量 的影响 . 并加 以试验研究 . 定量的确定摩擦系数对其影 响程度 的大小 。 这一研究结果利于工程实践中更好的控制预紧力 .提高螺栓联接的可 靠性。 图1 — 1 垫块尺寸
从 以上 的理论分 析中 . 我 们_ 口 『 以得 出摩 擦 系数对螺 纹 紧固件 的
2 . 试 验研 究
动仪器 . 螺母跟随扭 紧装置旋转向下. 扭 紧装置对螺母施加线性增加 的 通过前面 的理论分析 . 我们定性 的得 出了摩擦 系数 的不 同引起 了 扭矩 . 仪器 自动记录螺栓预紧力随着扭矩增加而变化 的曲线 。 记录实验 扭矩系数 的差异 .进而造成 了总扭矩转化成 的轴 向夹紧力大小不 同. 编号 . 接着换 一对螺纹 紧固件 . 用孑 L 板上的 2 号孔装配 . 重复上述实验 这一点对螺栓装配质量有着很大的影响。 为 了定量的分析摩擦系数对 过程 将该过程继续重 复( 一共 5 O 次) , 每次都新 的一对螺栓螺母 , 每次 装配质量的影响程度 . 设计 了如下对 比实验 。 都用孔板上不同的孔来装配 每做完一次实验都要记录相应 的实验数
紧固件装配与摩擦系数的关系

紧固件装配与摩擦系数的关系装配螺栓时要求控制预紧力是通过控制扭矩实现的,使用扭矩装配方法时,当达到规定的扭矩就停止,只对一个确定的紧固力矩进行控制。
摩擦系数是要恒定的范围,安装扭矩是为了达到一定的预紧力而做出的,实际拧紧过程中受到摩擦系数等影响,仅仅5%~10%的扭矩转化为所需要的预紧力,有90%的扭矩被拧紧过程中的摩擦消耗掉。
当支承面的摩擦系数降低20%时,支承面摩擦扭矩降为40%,螺栓轴向夹紧力将翻倍增加(有20%的拧紧扭矩转化成夹紧力)。
由此可见,使用扭矩装配方法,摩擦系数对螺栓夹紧力的影响之大。
详细参考:ISO-16047 标准紧固件装配最重要的指标是预紧力,可是装配时不好检测,其他工艺手段(扭矩法、转角法、屈服点法)都是间接的办法,但在装配中和事后好检测。
对工厂来说,螺栓入厂检测扭矩系数比摩擦系数更简洁,因为目前国内螺栓的几何尺寸指标(螺纹精度)基本都过关了(除非太差的小厂出的),关键的材质、热处理、表面处理,通过扭矩系数测试仪很方便的就能检测了。
最大关键因素是在于表面处理。
而影响表面处理的因子系表面处理材料的选择、质量及制程管理。
在汽車及机件装配过程中,通常是将螺丝用设定的扭矩锁紧。
螺丝的连接原理是通过依照界定的鎖紧力将所有的部件接合一起而设计。
F(锁紧力)=M(锁紧扭矩)÷ ( μ× f )μ=摩擦系数f=比例因子f是比例因子,数值取决于螺丝的几何形状。
此公式清楚显示如果是螺丝的扭矩固定,而摩擦系数的平均偏差很高,那么预张力的波动就会很大,这种情况是不被接受的。
因为如果摩擦系数太低,可能造成螺丝损伤;摩擦系数太高的话,就不能达到最小锁紧力,螺丝的连接就存在松脱的危险。
基于这种情况,设计工程师和品保经理都要求一个稳定的摩擦系数(可计算性),及尽可能低的摩擦系数的平均变量(安全装配需要)。
为了满足这些要求,故常要求在螺丝表面涂覆摩擦系数稳定,使摩擦系数稳定在严格规定的平均偏差范围内。
紧固件摩擦系数-概述说明以及解释

紧固件摩擦系数-概述说明以及解释1.引言1.1 概述概述部分的内容可以按照以下方式编写:在紧固件设计和应用中,摩擦系数是一个十分重要的参数。
摩擦系数是指在两个表面接触并相对滑动时所产生的摩擦力与正压力之比。
它不仅会影响到紧固件的性能和可靠性,也会对装配过程和使用寿命产生重要的影响。
在工程实践中,选择合适的摩擦系数对于确保紧固件的工作正常以及减少因松动或脱落而引起的潜在危险十分重要。
低摩擦系数可确保紧固件在正常工作条件下保持稳定,而高摩擦系数则可以提高紧固件的保持力。
然而,摩擦系数的确定并不是一个简单的过程。
它受到多种因素的影响,包括材料的选择、表面处理、润滑条件等。
因此,在设计和选择紧固件时,需要综合考虑各种因素以确定最合适的摩擦系数。
本文将从紧固件的定义和分类开始,介绍摩擦系数的概念和作用,深入探讨影响紧固件摩擦系数的因素,并介绍常用的测试方法。
最后,我们将总结摩擦系数对紧固件性能的影响,探讨摩擦系数的优化方法,以及紧固件摩擦系数在不同应用领域中的具体应用。
通过对紧固件摩擦系数的研究,我们可以更好地理解该参数的重要性和潜在价值,为紧固件的设计和选择提供科学依据。
综上所述,本文旨在全面介绍紧固件摩擦系数及其相关内容,希望能够对读者在紧固件设计和选择方面提供有益的参考和指导。
文章结构部分的内容为:1.2 文章结构本文共分为三个部分:引言、正文和结论。
(1)引言部分主要包括概述、文章结构、目的和总结四个方面。
概述部分对紧固件摩擦系数的重要性进行了简要介绍,并引出了摩擦系数对紧固件性能的影响。
文章结构部分向读者介绍了文章的整体结构,包括引言、正文和结论三个部分,并简要描述了每个部分的内容。
目的部分明确了本文的研究目标,即探讨紧固件摩擦系数的定义、影响因素、测试方法,以及摩擦系数对紧固件性能的影响和优化方法。
总结部分提前总结了文章的主要内容和结论。
(2)正文部分是本文的核心内容,主要包括紧固件的定义和分类、摩擦系数的概念和作用、影响紧固件摩擦系数的因素,以及紧固件摩擦系数的测试方法。
螺纹紧固件摩擦系数的影响因素试验研究
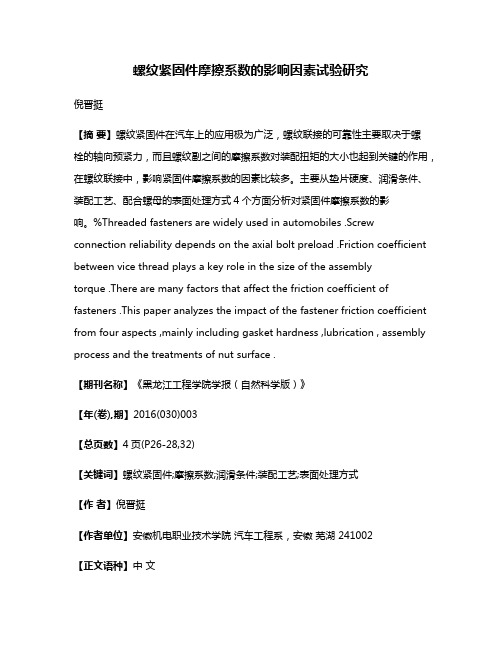
螺纹紧固件摩擦系数的影响因素试验研究倪晋挺【摘要】螺纹紧固件在汽车上的应用极为广泛,螺纹联接的可靠性主要取决于螺栓的轴向预紧力,而且螺纹副之间的摩擦系数对装配扭矩的大小也起到关键的作用,在螺纹联接中,影响紧固件摩擦系数的因素比较多。
主要从垫片硬度、润滑条件、装配工艺、配合螺母的表面处理方式4个方面分析对紧固件摩擦系数的影响。
%Threaded fasteners are widely used in automobiles .Screw connection reliability depends on the axial bolt preload .Friction coefficient between vice thread plays a key role in the size of the assemblytorque .There are many factors that affect the friction coefficient of fasteners .This paper analyzes the impact of the fastener friction coefficient from four aspects ,mainly including gasket hardness ,lubrication , assembly process and the treatments of nut surface .【期刊名称】《黑龙江工程学院学报(自然科学版)》【年(卷),期】2016(030)003【总页数】4页(P26-28,32)【关键词】螺纹紧固件;摩擦系数;润滑条件;装配工艺;表面处理方式【作者】倪晋挺【作者单位】安徽机电职业技术学院汽车工程系,安徽芜湖 241002【正文语种】中文【中图分类】TH131.3紧固件是机械行业不可缺少的通用零件,主要包括螺纹紧固件、垫圈、销和铆钉等。
020测量螺纹紧固件的摩擦系数

8螺纹紧固件摩擦系数的测量及应用神龙汽车有限公司 刘建文 佘东晓摘要 本文主要对螺纹紧固件的摩擦系数的概念和测量方法作了重点介绍,并结合实际经验对试验过程中应注意的问题作了说明;然后阐述了在使用扭矩拧紧法时,摩擦系数值在拧紧工艺设计中的应用。
关键词 螺纹紧固件 摩擦系数 扭矩拧紧法1 前言我们知道,在汽车装配中,螺纹紧固件装配的质量将直接影响整车的装配质量和行驶的可靠性。
而要保证螺栓的可靠服役,必须在装配时要保证有适当的轴向夹紧力。
目前在装配工艺上最经济可行的方法是通过控制扭矩来间接实现对轴向夹紧力的控制。
但是扭矩和轴向夹紧力的关系受到螺纹联接副摩擦条件的直接影响。
如果联接副的摩擦状况存在较大的散差,我们得到的轴向力必然比较分散,系统的可靠性得不到保障。
于是我们可以通过测量扭矩系数来评价螺纹联接副的摩擦条件。
但是扭矩系数是一个由整个螺纹联接副的摩擦条件以及它们的几何形状共同决定的经验系数,本身变化的范围就很大,不具备通用性。
随着我们对拧紧控制的要求越来越严格,扭矩系数表现出了一定的局限性,并且我们现场装配的扭矩控制精度正得到逐步提高,这些都使得我们有可能,也有必要运用更准确,更严格的方法来评价螺纹联接的摩擦条件。
测定螺纹紧固件的摩擦系数就是这样一种方法。
不象扭矩系数,摩擦系数是一个明确的物理概念,它是摩擦力与正压力之间的比值,也可以理解为一个材料常数,当摩擦面的材料,表面处理状态,和润滑条件确定后,摩擦系数也就确定下来。
但是表观摩擦系数与零件表面状态和制造公差有关。
摩擦系数的测量必须在一定的基准条件下进行,才能保证有良好的重复性。
它的结果并不直接用于指导现场拧紧装配,而是为了确保每一批螺栓(螺母)的摩擦系数都稳定在一个水平上,从而达到最终装配质量稳定和可靠的目的。
2 摩擦系数的测量2.1 试验装夹方式装夹方式见图1、图2所示。
2.2 计算公式通常我们测量扭矩系数K 的计算公式为: Fd CK ⋅=(1)9式中,C 为扭矩,F 为轴向夹紧力,d 是螺纹的名义直径。
螺纹摩擦系数检测对紧固件失效率影响的探讨
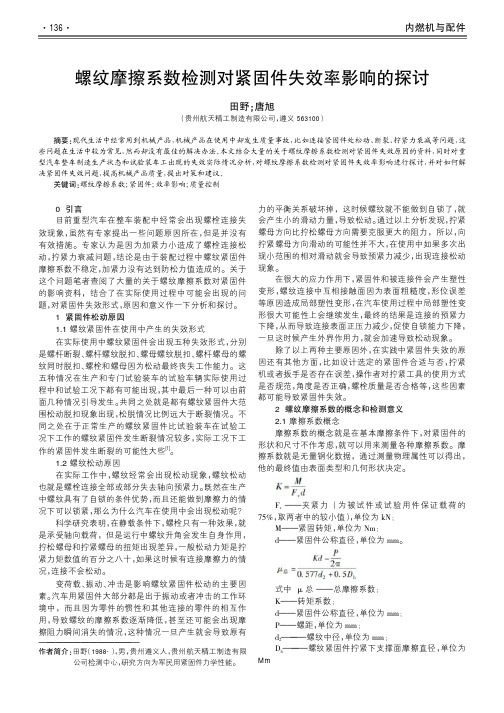
0引言目前重型汽车在整车装配中经常会出现螺栓连接失效现象,虽然有专家提出一些问题原因所在,但是并没有有效措施。
专家认为是因为加紧力小造成了螺栓连接松动,拧紧力衰减问题,结论是由于装配过程中螺纹紧固件摩擦系数不稳定,加紧力没有达到防松力值造成的。
关于这个问题笔者查阅了大量的关于螺纹摩擦系数对紧固件的影响资料,结合了在实际使用过程中可能会出现的问题,对紧固件失效形式,原因和意义作一下分析和探讨。
1紧固件松动原因1.1螺纹紧固件在使用中产生的失效形式在实际使用中螺纹紧固件会出现五种失效形式,分别是螺杆断裂、螺杆螺纹脱扣、螺母螺纹脱扣、螺杆螺母的螺纹同时脱扣、螺栓和螺母因为松动最终丧失工作能力。
这五种情况在生产和专门试验装车的试验车辆实际使用过程中和试验工况下都有可能出现,其中最后一种可以由前面几种情况引导发生。
共同之处就是都有螺纹紧固件大范围松动脱扣现象出现,松脱情况比例远大于断裂情况。
不同之处在于正常生产的螺纹紧固件比试验装车在试验工况下工作的螺纹紧固件发生断裂情况较多,实际工况下工作的紧固件发生断裂的可能性大些[1]。
1.2螺纹松动原因在实际工作中,螺纹经常会出现松动现象,螺纹松动也就是螺栓连接全部或部分失去轴向预紧力。
既然在生产中螺纹具有了自锁的条件优势,而且还能做到摩擦力的情况下可以锁紧,那么为什么汽车在使用中会出现松动呢?科学研究表明,在静载条件下,螺栓只有一种效果,就是承受轴向载荷,但是运行中螺纹升角会发生自身作用,拧松螺母和拧紧螺母的扭矩出现差异,一般松动力矩是拧紧力矩数值的百分之八十,如果这时候有连接摩擦力的情况,连接不会松动。
变荷载、振动、冲击是影响螺纹紧固件松动的主要因素。
汽车用紧固件大部分都是出于振动或者冲击的工作环境中,而且因为零件的惯性和其他连接的零件的相互作用,导致螺纹的摩擦系数逐渐降低,甚至还可能会出现摩擦阻力瞬间消失的情况,这种情况一旦产生就会导致原有力的平衡关系破坏掉,这时候螺纹就不能做到自锁了,就会产生小的滑动力量,导致松动。
浅析螺栓摩擦系数

浅析紧固件摩擦系数1.紧固件摩擦系数概念:摩擦系数是指两表面间的摩擦力和作用在其一表面上的垂直力之比值。
也可以理解为一个材料常数,当摩擦面的材料、表面处理状态和润滑条件确定后,摩擦系数也就确定下来。
2.研究螺栓摩擦系数的意义为保证螺栓的可靠服役,必须在装配时保证有适当的轴向预紧力。
而螺栓的拧紧过程是一个克服摩擦的过程,在这一过程中存在螺纹副的摩擦及端面摩擦。
而影响预紧力的主要因素除了使用的工具及拧紧方法外就是紧固件的摩擦系数。
让我们来看以下案例:某装配车间汽车装配工位采用M10´1.5螺栓,螺栓强度级别为10.9 级,螺栓材料都是钢制的,夹紧本体有两种情况,一种本体是钢制零件,而另一种本体是铝合金零件。
螺栓装配工艺扭矩要求为30Nm+90°,最终扭矩监控窗口为40—94Nm。
在装配过程中对于本体是钢制的零件,完全能够达到工艺要求,但是在本体是铝合金零件时,装配机频频出现报警现象。
经检查发现在装铝合金本体零件时,转角还没有达到90°要求,扭矩已经超出了94Nm的最大控制范围。
这是什么原因造成的呢?钢制螺栓对铝合金本体的摩擦系数为0.17,而钢与钢的摩擦系数在0.10—0.15之间,根据公式计算螺栓材料屈服时的装配扭矩(钢制螺栓对铝合金本体) =54.52[0.5´0.17´13.25+0.11(1.5+0.58´9.023)] =102Nm(钢制螺栓对刚本体) =80Nm针对装配中产生的实际问题及最小屈服点的计算结果,按照惯例将计算结果增加10%,则最终扭矩控制监控窗口设置为40—110Nm,从根本上解决了扭矩转角的装配质量,保证了生产的正常进行。
3.摩擦系数对不同扭矩法的影响目前使用最多的是“扭矩法”和“扭矩-转角控制法”,而这两种拧紧方式都将会受到产品摩擦系数大小的影响,从而影响螺栓紧固时的预紧力。
而“屈服点控制法”和“螺栓长度法”则避免了摩擦系数对装配的影响。
紧固件的摩擦系数标准

紧固件的摩擦系数标准
一、表面处理
紧固件的表面处理对摩擦系数有显著影响。
常见的表面处理方法包括镀锌、喷塑、氧化等。
这些处理方法可以提高紧固件表面的光滑度,降低摩擦系数。
例如,镀锌层具有较好的抗腐蚀性能和摩擦性能,能够有效地减小摩擦力。
二、材料类型
不同材料类型对紧固件的摩擦系数也有很大影响。
一般来说,高强度合金钢、不锈钢等材料的摩擦系数较低,而铸铁、碳钢等材料的摩擦系数相对较高。
因此,在选择紧固件材料时,应充分考虑其摩擦系数的要求。
三、测试条件
测试条件也是影响紧固件摩擦系数的重要因素。
例如,温度、湿度、润滑条件等都会对摩擦系数产生影响。
在标准测试条件下,紧固件的摩擦系数通常具有较好的重复性和稳定性。
因此,在进行紧固件摩擦系数测试时,应尽量保证测试条件的标准化和规范化。
四、紧固方式
紧固方式也是影响紧固件摩擦系数的重要因素。
例如,螺栓的拧紧方式、拧紧力矩等都会影响其摩擦系数。
在拧紧过程中,应尽量保证螺栓与螺母的贴合度良好,避免出现间隙或过盈现象,这样可以有效地减小摩擦力。
五、使用环境
使用环境对紧固件的摩擦系数也有一定影响。
例如,在高温、高湿、腐蚀等恶劣环境下,紧固件的摩擦系数可能会发生变化。
因此,在使用紧固件时,应充分考虑其使用环境的要求,选择合适的材料和表面处理方法,以保证紧固件的摩擦系数符合要求。
技术|紧固件摩擦系数的测定
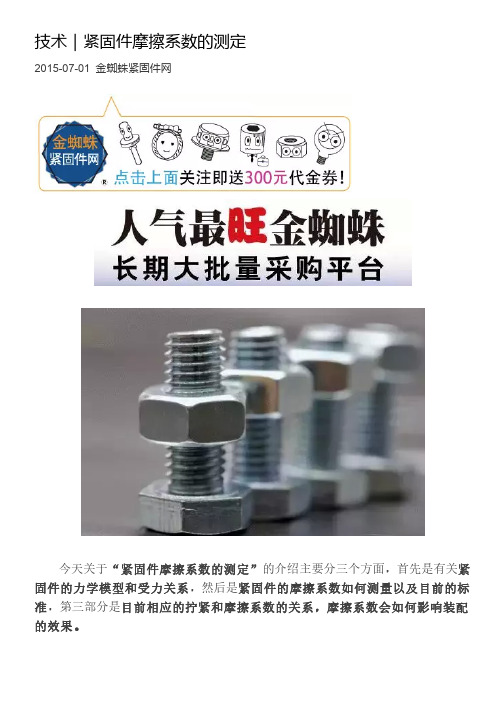
技术|紧固件摩擦系数的测定2015-07-01金蜘蛛紧固件网 今天关于“紧固件摩擦系数的测定”的介绍主要分三个方面,首先是有关紧固件的力学模型和受力关系,然后是紧固件的摩擦系数如何测量以及目前的标准,第三部分是目前相应的拧紧和摩擦系数的关系,摩擦系数会如何影响装配的效果。
下面的图片显示了紧固件的基本作用原理,紧固件的作用原理是通过两个甚至更多的部件,通过螺栓紧固件把他链接在一起,不发生相对的滑动,这是紧固件最重要的功能;在使用的方面,紧固件的夹紧力或者是轴向力,是紧固件使用中最重要的因素。
紧固件产生的夹紧力必须要在合理安全的相应的公差范围内,紧固件才能正常工作。
如果夹紧力过大,螺栓可能会拉伸过长,以至于提前发生疲劳断裂;如果螺栓夹紧力过小,不足以把部件压紧在一起,可能会发生松动,也会引起螺栓的断裂,因此紧固拧紧设计最有挑战的地方是如何控制螺栓紧固件的夹紧力。
以下图片是德国Schatz公司对螺栓拧紧方式的理解,简称四个M,只有把这4个M控制好了,才能有完美的装配的产品,这四个M分别代表: 第一个M,即操作者,我们对现场的拧紧,或者螺栓设计人员需要有好的紧固件的基础,并且接受正确的培训; 第二个M,即Material ,不管是连接件螺栓,螺母或者被连接件,材料的等级和选择要符合最佳的设计; 第三个M,即Method,拧紧的方式或者拧紧策略,每个紧固件必须选择符合他们拧紧的策略或者工艺; 第四个M,即Machine,拧紧工具,这点往往被大家忽略,我们关注紧固件往往关注材料和拧紧的工具,有时候现场的实效往往是由于我们选择了错误的拧紧工具,或者我们拧紧的工具没有选择及时的标的所引起的。
下一张图是受力的分析的模型,在整个紧固件的受力分析上,螺栓的受力是不均匀的,而是有不同的硬力集中的地方,这也是我们将来关注失效或者疲劳的时候重点关注的地方。
我们介绍了螺栓的夹紧力,接下来介绍摩擦系数。
螺栓的夹紧力和扭矩的关系,其实我们的摩擦系数是一个桥梁,桥梁决定了什么样的扭矩得到什么样的夹紧力,简单的说摩擦系数来自于我们的扭矩和轴力的比例关系。
摩擦系数与扭矩系数的关系
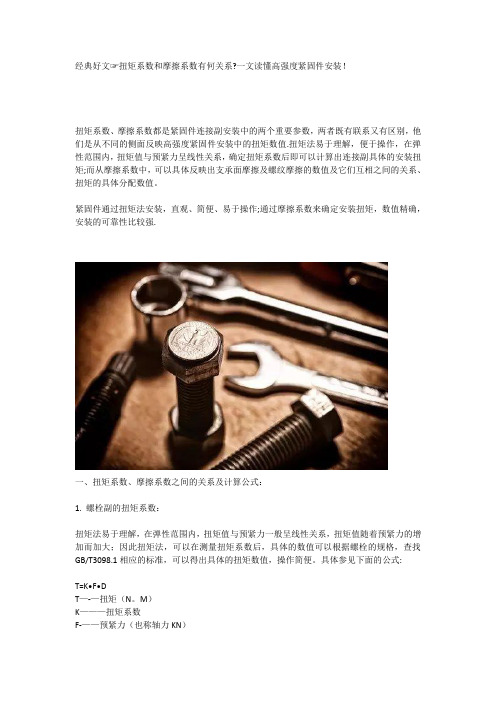
经典好文☞扭矩系数和摩擦系数有何关系?一文读懂高强度紧固件安装!扭矩系数、摩擦系数都是紧固件连接副安装中的两个重要参数,两者既有联系又有区别,他们是从不同的侧面反映高强度紧固件安装中的扭矩数值.扭矩法易于理解,便于操作,在弹性范围内,扭矩值与预紧力呈线性关系,确定扭矩系数后即可以计算出连接副具体的安装扭矩;而从摩擦系数中,可以具体反映出支承面摩擦及螺纹摩擦的数值及它们互相之间的关系、扭矩的具体分配数值。
紧固件通过扭矩法安装,直观、简便、易于操作;通过摩擦系数来确定安装扭矩,数值精确,安装的可靠性比较强.一、扭矩系数、摩擦系数之间的关系及计算公式:1. 螺栓副的扭矩系数:扭矩法易于理解,在弹性范围内,扭矩值与预紧力一般呈线性关系,扭矩值随着预紧力的增加而加大;因此扭矩法,可以在测量扭矩系数后,具体的数值可以根据螺栓的规格,查找GB/T3098.1相应的标准,可以得出具体的扭矩数值,操作简便。
具体参见下面的公式:T=K•F•DT—-—扭矩(N。
M)K———扭矩系数F-——预紧力(也称轴力KN)D---螺纹的公称直径(mm)扭矩系数是紧固件连接副安装时,必须要了解掌握的一个重要技术参数,目前安装扭矩、扭矩系数已经受到广大使用者的广泛理解、接受,并且在安装时普遍受关注。
扭矩及扭矩系数是既有联系又有区别的两个参数。
当扭矩数值选定后,扭矩系数越小,产生的紧固力越大;扭矩系数越大,产生的紧固力越小。
当扭矩系数小到一定的程度,在一定的扭矩的作用下紧固力超过了螺栓的强度极限,高强度螺栓就会产生伸长甚至断头的现象;反之,扭矩系数过大,产生的紧固力就会过小,整个螺栓连接副就达不到锁紧的功能,连接副就有可能产生松动情况。
因此,要使紧固力在一个标准的范围内,产品的扭矩系数就要限定在一个规定的范围内。
目前国家紧固件标准GB/T 1231-2000对钢结构用高强度螺栓连接副的标准作了规定,扭矩系数K=0.11-0.15,标准偏差≤0。
- 1、下载文档前请自行甄别文档内容的完整性,平台不提供额外的编辑、内容补充、找答案等附加服务。
- 2、"仅部分预览"的文档,不可在线预览部分如存在完整性等问题,可反馈申请退款(可完整预览的文档不适用该条件!)。
- 3、如文档侵犯您的权益,请联系客服反馈,我们会尽快为您处理(人工客服工作时间:9:00-18:30)。
紧固件装配与摩擦系数的关系
装配螺栓时要求控制预紧力是通过控制扭矩实现的,使用扭矩装配方法时,当达到规定的扭矩就停止,只对一个确定的紧固力矩进行控制。
摩擦系数是要恒定的范围,安装扭矩是为了达到一定的预紧力而做出的,实际拧紧过程中受到摩擦系数等影响,仅仅5%~10%的扭矩转化为所需要的预紧力,有90%的扭矩被拧紧过程中的摩擦消耗掉。
当支承面的摩擦系数降低20%时,支承面摩擦扭矩降为40%,螺栓轴向夹紧力将翻倍增加(有20%的拧紧扭矩转化成夹紧力)。
由此可见,使用扭矩装配方法,摩擦系数对螺栓夹紧力的影响之大。
详细参考:ISO-16047 标准
紧固件装配最重要的指标是预紧力,可是装配时不好检测,其他工艺手段(扭矩法、转角法、屈服点法)都是间接的办法,但在装配中和事后好检测。
对工厂来说,螺栓入厂检测扭矩系数比摩擦系数更简洁,因为目前国内螺栓的几何尺寸指标(螺纹精度)基本都过关了(除非太差的小厂出的),关键的材质、热处理、表面处理,通过扭矩系数测试仪很方便的就能检测了。
最大关键因素是在于表面处理。
而影响表面处理的因子系表面处理材料的选择、质量及制程管理。
在汽車及机件装配过程中,通常是将螺丝用设定的扭矩锁紧。
螺丝的连接原理是通过依照界定的鎖紧力将所有的部件接合一起而设计。
F(锁紧力)=M(锁紧扭矩)÷ ( μ× f )
μ=摩擦系数f=比例因子
f是比例因子,数值取决于螺丝的几何形状。
此公式清楚显示如果是螺丝的扭矩固定,而摩擦系数的平均偏差很高,那么预张力的波动就会很大,这种情况是不被接受的。
因为如果摩擦系数太低,可能造成螺丝损伤;摩擦系数太高的话,就不能达到最小锁紧力,螺丝的连接就存在松脱的危险。
基于这种情况,设计工程师和品保经理都要求一个稳定的摩擦系数(可计算性),及尽可能低的摩擦系数的平均变量(安全装配需要)。
为了满足这些要求,故常要求在螺丝表面涂覆摩擦系数稳定,使摩擦系数稳定在严格规定的平均偏差范围内。