玻璃窑炉介绍
光伏玻璃窑炉结构
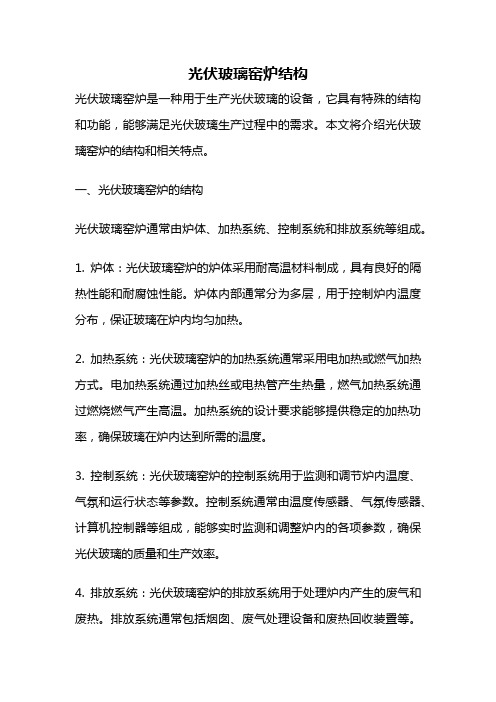
光伏玻璃窑炉结构光伏玻璃窑炉是一种用于生产光伏玻璃的设备,它具有特殊的结构和功能,能够满足光伏玻璃生产过程中的需求。
本文将介绍光伏玻璃窑炉的结构和相关特点。
一、光伏玻璃窑炉的结构光伏玻璃窑炉通常由炉体、加热系统、控制系统和排放系统等组成。
1. 炉体:光伏玻璃窑炉的炉体采用耐高温材料制成,具有良好的隔热性能和耐腐蚀性能。
炉体内部通常分为多层,用于控制炉内温度分布,保证玻璃在炉内均匀加热。
2. 加热系统:光伏玻璃窑炉的加热系统通常采用电加热或燃气加热方式。
电加热系统通过加热丝或电热管产生热量,燃气加热系统通过燃烧燃气产生高温。
加热系统的设计要求能够提供稳定的加热功率,确保玻璃在炉内达到所需的温度。
3. 控制系统:光伏玻璃窑炉的控制系统用于监测和调节炉内温度、气氛和运行状态等参数。
控制系统通常由温度传感器、气氛传感器、计算机控制器等组成,能够实时监测和调整炉内的各项参数,确保光伏玻璃的质量和生产效率。
4. 排放系统:光伏玻璃窑炉的排放系统用于处理炉内产生的废气和废热。
排放系统通常包括烟囱、废气处理设备和废热回收装置等。
烟囱用于排放废气,废气处理设备用于净化废气中的污染物,废热回收装置用于回收炉内产生的废热,提高能源利用效率。
二、光伏玻璃窑炉的特点1. 高温稳定性:光伏玻璃窑炉能够提供高温环境,使玻璃在炉内快速熔化和形成。
同时,光伏玻璃窑炉具有良好的温度控制性能,能够保持炉内温度的稳定性,确保玻璃的质量。
2. 省能高效:光伏玻璃窑炉的加热系统采用高效的电加热或燃气加热方式,能够提供稳定的加热功率,降低能源消耗。
同时,光伏玻璃窑炉的排放系统能够回收废热,提高能源利用效率。
3. 自动化控制:光伏玻璃窑炉的控制系统采用先进的自动化控制技术,能够实时监测和调节炉内的温度、气氛和运行状态等参数。
自动化控制能够提高生产效率,减少人工干预,降低操作难度。
4. 环境友好:光伏玻璃窑炉的排放系统能够处理炉内产生的废气和废热,减少对环境的污染。
玻璃窑炉的发展历史
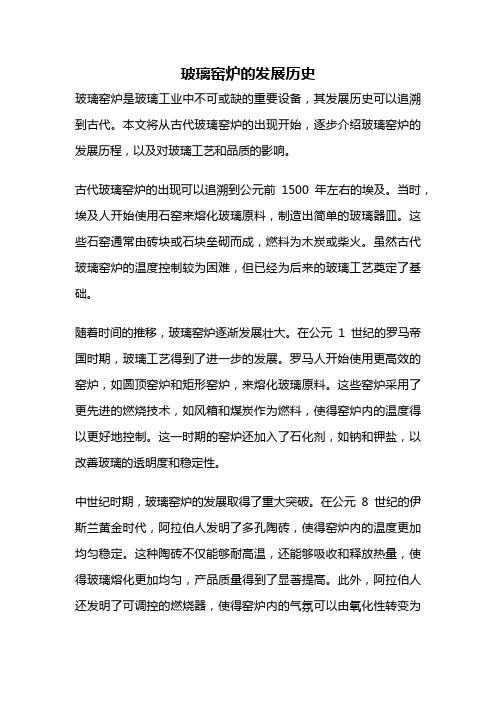
玻璃窑炉的发展历史玻璃窑炉是玻璃工业中不可或缺的重要设备,其发展历史可以追溯到古代。
本文将从古代玻璃窑炉的出现开始,逐步介绍玻璃窑炉的发展历程,以及对玻璃工艺和品质的影响。
古代玻璃窑炉的出现可以追溯到公元前1500年左右的埃及。
当时,埃及人开始使用石窑来熔化玻璃原料,制造出简单的玻璃器皿。
这些石窑通常由砖块或石块垒砌而成,燃料为木炭或柴火。
虽然古代玻璃窑炉的温度控制较为困难,但已经为后来的玻璃工艺奠定了基础。
随着时间的推移,玻璃窑炉逐渐发展壮大。
在公元1世纪的罗马帝国时期,玻璃工艺得到了进一步的发展。
罗马人开始使用更高效的窑炉,如圆顶窑炉和矩形窑炉,来熔化玻璃原料。
这些窑炉采用了更先进的燃烧技术,如风箱和煤炭作为燃料,使得窑炉内的温度得以更好地控制。
这一时期的窑炉还加入了石化剂,如钠和钾盐,以改善玻璃的透明度和稳定性。
中世纪时期,玻璃窑炉的发展取得了重大突破。
在公元8世纪的伊斯兰黄金时代,阿拉伯人发明了多孔陶砖,使得窑炉内的温度更加均匀稳定。
这种陶砖不仅能够耐高温,还能够吸收和释放热量,使得玻璃熔化更加均匀,产品质量得到了显著提高。
此外,阿拉伯人还发明了可调控的燃烧器,使得窑炉内的气氛可以由氧化性转变为还原性,进一步改善了玻璃的质量和色彩。
近代玻璃窑炉的发展主要集中在工业革命以后。
18世纪末,英国工程师与化学家博辛合研发出了用煤炭和空气来加热玻璃的煤气炉。
这种煤气炉不仅效率更高,而且通过调节煤气的流量和氧气的供应来控制炉内的温度,使得玻璃生产更加精确和可控。
19世纪中叶,法国化学家塞尚发明了煤气炉的改进型——瑞利炉,该炉在窑炉顶部加入了预热炉和烟道,提高了炉内的热效率。
20世纪以后,随着科技的不断进步,玻璃窑炉的发展进入了一个新阶段。
燃料的革新、炉膛结构的优化、自动化控制系统的应用等技术的不断推陈出新,使得玻璃窑炉的熔化效率、温度控制精度和产品质量都有了显著提升。
例如,高温燃烧技术的应用使得窑炉内的温度可以达到更高的水平,促进了新型玻璃材料的发展。
玻璃窑炉

窑炉及设计(玻璃)
窑炉及设计(玻璃)
3.3 玻璃电熔原理
将电流通过电极引入玻璃液直接通电加热, 两电极间玻液在交流电作用下产生焦耳热, 达到熔化和调温目的.
玻液导电性,主要是电荷通过离子迁移, 网络结构碱金属离子结合最弱,是电流载 体。石英玻璃和硼玻璃含少量碱离子导电 性较差。
窑炉及设计(玻璃)
1986年 德国SORG 6吨铅玻璃炉
1986年 英国KTG 铅玻璃炉
1988年 日本山村硝 50吨钠钙炉 子
1988年 英国KTG 120吨平板炉
窑炉及设计(玻璃)
国内自行研制电熔技术始于七十年代末
贵州灯泡厂 3吨钠钙玻璃炉 1984年8月投产
重庆北碚玻璃 1吨硼硅玻璃电 1984年10月投产
仪器总厂
还原 良好
高 良好 良好
有 中等
中性 不良 >1400℃高
低 不良
无 高
还原 良好 可燃尽 良好 良好
有 低
窑炉及设计(玻璃)
①钼电极:对多种玻璃熔制适用。 由钼粉(钼99.9999%)液压成型,高 温气氛炉烧结,再加热锻打,制成 ¢31、¢50、¢75mm,长1-2m的棒状 电极。有螺纹电极便于推入窑内。
两相系统:多用于横截面为正方形或宽 度是长度整数倍的长方形。斯库特变压 器,三相电源产生。优点:两相负载相 同。要求电极布置须呈正方形。
三相系统:分对称和不对称。不对称型 不论纵、横向功率释放都不均匀。
窑炉及设计(玻璃)
(2)自动控制方案: 保证熔窑各部分玻液温度在范围内。
全电熔窑玻液温 控方式:
熔炉
上海玻璃器皿 0.5吨微晶玻璃电 1984年11月投产
二厂
熔炉
浙江省椒江市 3吨电熔炉
玻璃窑炉结构及窑炉用耐火材料性能.

5、热源供给:蓄热室
1)用途:蓄热室是利用耐火材料做蓄热体 (称为格子体)蓄积从窑内排出烟气的部分 热量,用来加热进入窑内的助燃空气 ---这样不但可以利用烟气余热,而且使得助燃 空气加热到较高温度,有利于提高作业温度; ---同时还起到把窑内废气排出及助燃空气 进入的通道;
2)蓄热室是什么结构和材质? 蓄热室是由前、后墙、隔墙及蓄热室内格子体组成, 使用温度分为上部为1200~1500℃,中部为 800~1200℃,下部为<800℃: a.蓄热室碹(砖厚350mm,外有3*64mm保温砖),其使 用条件为粉料的飞散,高温的温度变化,氧化还原反应, 材质为优质硅砖; b.蓄热室目标墙(砖厚350mm,外有146 的粘土砖及 178mm保温砖)其使用条件同蓄热室碹,材质为 AZS33#锆刚玉砖或高纯电熔镁砖; c.主墙和隔墙:上部(砖厚350mm),使用条件同蓄热室 碹,材质为优质硅砖;中部(砖厚230mm),使用条 件为中温的温度变化,材质为高铝砖或镁质砖;下部 (砖厚350mm),使用条件为低温的温度变化,材质 为低气孔粘土砖。 d.底部炉条碹,使用条件同下部格子砖,材质为低气孔率
卡脖出 口矮碹 卡脖吊 平碹 熔化部 大碹 卡脖入口 J形吊墙
卡脖池底
卡脖大 水包
池壁
2)玻璃液分隔装置有卡脖、冷却水包、窑坎等: ---卡脖是熔化部和冷却部之间的一段缩窄窑池,与 矮碹、吊墙配合使用,对熔化部和冷却部之间的 气体空间及玻璃液起分隔作用,从而降低玻璃液 的温度; ---冷却水管是由一组通过冷却水的圆形或方形钢管 组成,水管高度根据实用确定。冷却水管附近的 玻璃液受冷却后,形成粘度较大的不动层,构成 一道挡墙、降温作用大,不但可以阻挡未熔化的 浮渣进入冷却部,而且通过调节水管的沉入深度, 可以控制进入冷却部玻璃液的质量; ---窑坎,是斜坡式分隔能阻挡玻璃液的对流,窑的 纵向有多个窑坎,如澄清带,进入卡脖及进入工 作部前端均可设置窑坎。
玻璃窑炉-讲稿

二、玻璃的熔制过程
玻璃的熔化是将配合料投入耐火材料砌筑的熔窑中,
经高温加热,得到无固体颗粒、符合成形要求的各种单相
连续体的过程。
传统的方法生产玻璃------是通过加热,经过高温熔制而 得到的。加热的温度是多高哪?-----1580-1590℃ 。 玻璃熔化所用的设备------熔窑。熔窑是一个由多种耐火
进一步的澄清、均化和冷却以满足玻璃液成型的 要求。 玻璃池窑冷却部(Cooling End)的结构与熔化 部的结构基本上相同,也分为下部窑池和上部空 间两部分。 下部窑池由池底和池壁所组成,上部空间由胸 墙和大碹所组成。只是冷却部的窑池深度比熔化 部的窑池深度稍浅,冷却部的胸墙高度略低于熔 化部的胸墙高度。 冷却部冷却时要注意降温要稳定,避免温度较 大的波动,造成二次气泡。
为了提高玻璃液的质量,现代浮法玻璃窑炉的结 构有了演变-----熔化区、澄清区-----微小气泡。
18
(4)熔化部澄清区长度和宽度的确定
为了便于计算和分区,国内外一般以未对小炉中心
线外1.0m处开始到卡脖拐角处为止这一段的距离来 确定为浮法玻璃池窑熔化部澄清区的长度,它和熔化 区的长度一起构成整个熔化部的长度。
9000
600 14695 11250
9375
650 15163 11625
9750
700 15627 12000
10125
21
玻璃池窑熔化部澄清区的宽度BR与玻璃池窑
熔化部熔化区的宽度Bm相同。
(5)窑池的深度
关于窑池的深度,国内外有两种比较通用的结
构形式。
深池结构和浅池结构。
玻璃窑炉工艺(一)
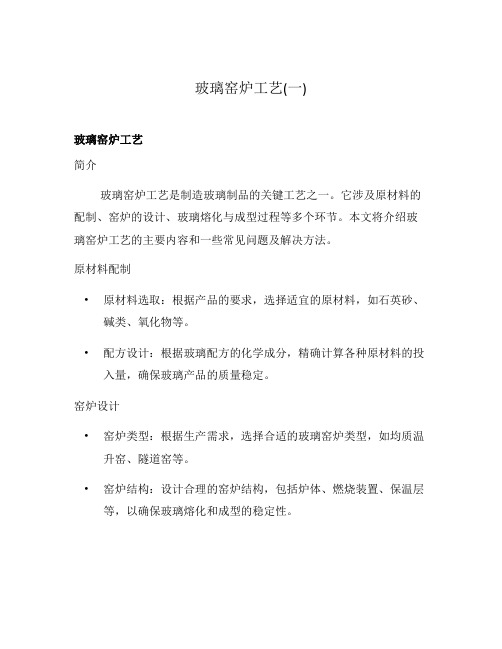
玻璃窑炉工艺(一)玻璃窑炉工艺简介玻璃窑炉工艺是制造玻璃制品的关键工艺之一。
它涉及原材料的配制、窑炉的设计、玻璃熔化与成型过程等多个环节。
本文将介绍玻璃窑炉工艺的主要内容和一些常见问题及解决方法。
原材料配制•原材料选取:根据产品的要求,选择适宜的原材料,如石英砂、碱类、氧化物等。
•配方设计:根据玻璃配方的化学成分,精确计算各种原材料的投入量,确保玻璃产品的质量稳定。
窑炉设计•窑炉类型:根据生产需求,选择合适的玻璃窑炉类型,如均质温升窑、隧道窑等。
•窑炉结构:设计合理的窑炉结构,包括炉体、燃烧装置、保温层等,以确保玻璃熔化和成型的稳定性。
玻璃熔化过程•加料:按照配方要求,将各种原材料逐步加入窑炉中,保持适当的投料速度和顺序。
•燃烧控制:调节燃烧装置,控制燃烧温度和气氛,以实现玻璃原料的熔化。
•熔化调温:通过调节窑炉的温度分布和加热方式,实现熔化温度的控制和调节。
玻璃成型过程•出料:在玻璃熔化达到要求的情况下,逐步将熔融的玻璃从窑炉中取出,保持合适的速度和方法。
•成型方式:根据产品要求,选择合适的成型方式,如浇铸成型、挤压成型、玻璃纤维拉制等。
•冷却处理:经过成型后的玻璃制品需要进行冷却处理,以保证其性能稳定和形状完整。
常见问题及解决方法•玻璃熔化不充分:调整燃烧装置,增加燃料量或提高燃烧温度。
•玻璃成型不良:检查窑炉温度分布,调整加热方式或成型工艺参数。
•玻璃裂纹问题:优化原材料配方,改进冷却处理方式,避免温度快速变化。
以上就是玻璃窑炉工艺的基本内容和常见问题处理方法。
通过合理的配制和设计,以及严格的控制过程参数,可以提高玻璃制品的质量和生产效率。
玻璃窑炉的结构及工作原理

玻璃窑炉的结构及工作原理玻璃窑炉是一种用于玻璃制造的设备,其结构和工作原理对于玻璃生产至关重要。
玻璃窑炉的结构主要包括四个部分:窑体、燃烧系统、温度控制系统和废气处理系统。
首先是窑体部分,它是玻璃窑炉的主体结构,通常由耐火材料构成,以承受高温和化学腐蚀。
窑体通常呈圆筒形,内部分为不同的区域,包括熔化区、保温区和冷却区。
熔化区是玻璃原料在高温下熔化的地方,保温区用于保持玻璃的恒温,冷却区则用于使玻璃逐渐降温。
其次是燃烧系统,它提供燃料和氧气以产生高温,使玻璃原料熔化。
燃烧系统通常由燃料供应系统和燃烧器组成。
燃料供应系统负责供应燃料,常见的燃料包括天然气、液化石油气和重油等。
燃烧器是将燃料和氧气混合并点燃的装置,以产生高温火焰。
温度控制系统是玻璃窑炉的关键部分,它通过监测和调节窑炉内部的温度,使其能够保持在玻璃制造所需的恒定温度范围内。
温度控制系统通常由温度传感器和控制器组成。
温度传感器负责测量窑炉内部的温度,将其信号传输给控制器。
控制器根据接收到的信号,调节燃烧系统的工作状态,以控制窑炉的温度。
最后是废气处理系统,它用于处理窑炉燃烧过程中产生的废气。
废气处理系统通常包括烟气净化器和废气排放装置。
烟气净化器主要用于去除废气中的有害物质,如颗粒物和气态污染物。
废气排放装置则负责将经过净化的废气排放到大气中,以保护环境。
玻璃窑炉的工作原理是利用燃烧系统产生的高温将玻璃原料熔化成液态,然后通过温度控制系统保持玻璃在恒定的温度范围内,最后通过废气处理系统处理废气。
具体工作过程如下:燃烧系统点燃燃料,产生高温火焰。
火焰的温度通常在1500℃至1600℃之间,可以熔化玻璃原料。
火焰通过燃烧器喷射进入窑炉内,形成熔化区。
接着,玻璃原料被投入到窑炉内,与高温火焰接触。
在高温下,玻璃原料逐渐熔化成液态,形成玻璃池。
熔化过程需要一定时间,通常需要几个小时甚至几天。
然后,温度控制系统开始工作。
温度传感器监测玻璃池的温度,并将其信号传输给控制器。
玻璃窑

放电等离子体烧结技术 微波烧结技术 热等静压制备技术 自蔓延高温合成技术
适用于小批量、高 附加值的高技术陶 瓷产品的高温制备
热 工 设 备 的 外 延
无机非金属材料的热工设备工艺过程的特点: 不管使用哪一种烧制方法,从原料(生料)变为产品(熟料),大体上都 要经过预热、烧成和冷却这三个阶段(过程),只是具体的产品在这三个阶 段中的具体细节有所不同。 无机非金属材料热工设备的特点: 热工设备必须在设备结构和烧成制度上满足所烧制产品烧制过程中工艺 过程的要求。
玻璃液的熔制、玻璃产品的成型和玻璃制品的退火都是在高、中温度下进行 的,而要完成这几个热工过程,生产出高质量的玻璃制品,就需要有合理的热工 设备,这就是玻璃熔窑(GlassMeltingFurnace)。玻璃熔窑又称为玻璃窑炉. 它是用来熔制玻璃液的高温热工设备。
2、玻璃生产过程中的热工设备及作用 玻璃熔窑是一个整体的系统,因此,围绕着玻璃窑形成的的系统有:
作用:进一步均化玻璃液,将温度降低到一个合理的范围,分配玻璃液 到各个供料通道。 平板、压延、浮法 为矩形结构 冷却部 结构形式
日用、医用、化工等成形与冷却合为一体,即供料槽 上部空间:起冷却作用。
结构 下部空间:起供料、分配作用。
分隔装置
作用:将池窑内部分成加热空间和冷却空间。 空气分隔装置的布置形式: 1)矮碹分隔式(flying arch):特点:矮碹处的脑墙比较低,但还有一定空间 。我们把这个称为开度。这种分隔效果较差,如果要想提高 分陋效果,还要配合卡脖。 2)吊矮碹分隔式(suspended flying arch):特点:在矮碹处设U 型吊墙和矮 碹一起构成分隔设施。分隔效果要比矮碹好。但结构复杂。 3)U 型吊墙分隔式(suspended shadow wall):特点:可完全分隔池窑的熔 化部和冷却部。调节开度灵活。平与水平搅拌器相配使用。 4)双J 型吊墙分隔式(double suspended shadow wall):特点:可完全分隔 池窑的熔化部和冷却部.使用在大型、先进的浮法窑上。有利 立式搅拌器的安装,且寿命较长。
玻璃马蹄焰窑炉介绍

玻璃窑炉马蹄焰池窑简介1.熔化池结构窑炉的熔化率主要取决于熔化温度,因为中碱和无碱玻璃球窑的熔制温度比较高,如果进一步提高熔化温度来提高熔化率,会加速对耐火材料的侵蚀,降低球质和影响炉龄。
而采取鼓泡和电助熔技术可以相应提高中下层玻璃温度,促进玻璃的均化,并且提高熔化率。
玻璃原料从熔化到澄清的行程也大,这有利于玻璃质量的控制和提高,而长宽比又受到小炉结构设计、火焰长度及拐弯要求的限制。
池深不仅影响到玻璃液流和池底温度,而且影响玻璃液的物理化学均匀性以及窑炉的熔化率。
一般池底温度在1200—1360℃之间较为合适。
池底温度的提高可使熔化率提高。
但池底温度高于1380℃时,需要提高池底耐火材料的质量及品种,否则会加速池底的侵蚀并降低炉龄,且会增加玻璃球的结石含量,这对后道拉丝生产是不利的,影响池底温度的决定性因素是玻璃的铁含量和玻璃气氛。
当Fe2O3含量在0.25—0.3%范围内时,池深800—1200mm的玻璃球窑,其垂直温降约为15—30℃/100mm。
2.工作池选择半圆形工作池时,其半径R决定于制球机台数与布置方式。
一般工作池半径小于等于熔化池池宽,工作池深度浅于熔化池池深300—400mm。
3.投料池为了获得稳定的玻璃质量,一般在池壁两侧设置一对投料池,随换火操作交替由火根投料。
投料池中心线与窑炉池壁的距离主要决定于小炉喷火口的温度,温度越高距离可缩小。
一般其距离可定在0.8—1.0m。
4.流液洞流液洞的功能是降温和均化。
采用沉式流液洞比采用直通式流液洞温降大。
而均化效果受液洞高度影响较大。
如高度越小则均化效果越好。
所以设计流液洞宽度一般应大于其高度。
在不考虑玻璃回流的情况下,玻璃流经流液洞的平均速度可取5—20m/h。
5.胸墙高度胸墙高度应根据窑炉容积发热强度来确定,目前容积发热强度设计值一般取60—200KW/m3(相当于50—180*103kcal/N.m3),比早期的数据已有明显下降,这说明提高了胸墙高度,而且采用质量改善的耐火材料和较好的保温效果,使窑炉热损失减少,大容积空间更有利于燃料的完全燃烧和增强其容积辐射强度,有利于提高熔制质量和降低能耗。
玻璃行业的三大窑炉

窑炉及设计(玻璃)
电熔玻璃池窑
窑炉及设计(玻璃)
1925年瑞典曾试用纯铁作电极熔制琥珀色和 绿色瓶罐玻璃。
1932年费格森试制水冷钼电极。
1942年康宁公司开始推广钼电极。最大全电 熔玻璃日产240吨,采用自动仪表,微机控 制和工业电视。
基础材料和器件工业.如电熔锆刚玉砖和钼 电极已达较高水平。
窑炉及设计(玻璃)
(2)适合熔制高质量玻璃:火焰池窑须 具备稳定高温和改善均化对流。在电熔 窑中靠窑结构、电极位置,调节电流, 就易取得。熔制玻璃有很高的均一性。 即使配料称量发生大误差,仍可继续作 业。熔制钠钙玻璃可提高合格率(2-4)%, 结石可降至0.3%。熔制乳白硼硅玻璃和 铅玻璃可提高合格率约20%。
浙江省椒江市 3吨电熔炉
1986年投产
窑炉及设计(玻璃)
3.2 电熔窑的优点
(1)热效率高:电熔窑电能在玻璃液内 部变成热能,且玻璃液被配合料覆盖, 周围散热可降到最低限度,且没有废气 热损失。故热效率高,大型电熔窑(7580)%,小型达60%。(火焰池窑效率为 (25-30)%,小型窑10%。)
钠钙玻璃除离子数量外,离子强度和半径 也影响导电性。与Na+相比,K+结合虽弱, 但K+半径较大,迁移阻力大。Li+半径比 Na+小,但Li电性。混合碱玻璃导 电性最差。
窑炉及设计(玻璃)
导电性难易以电阻率ρ(Ω•cm)或电导率σ (1/Ω•cm)来表示。 玻璃室温为电绝缘体σ=10-13~10-15/Ω•cm。 T↑ ρ ↓σ ↑↑ 熔融态σ= 0.1~1/Ω•cm 含其它改良剂离子时,降低离子迁移和ρ 如Ca2+、Ba2+、Pb2+↑玻璃ρ ↑↑。
玻璃窑炉的发展历史

玻璃窑炉的发展历史玻璃窑炉是用于玻璃制造的重要设备,经过长时间的发展,玻璃窑炉在结构、燃料和控制系统等方面都取得了重大的进展。
本文将从玻璃窑炉的起源开始,逐步介绍其发展历史。
一、起源与早期发展玻璃的历史可以追溯到公元前3000多年,而玻璃制品的制造被认为起源于古埃及。
最早的玻璃制造是通过在沙漠中熔炼沙子和碱制成的玻璃块,但这种方法并不高效。
随着时间的推移,人们开始尝试改进玻璃制造的方法,并发展出了玻璃窑炉。
早期的玻璃窑炉多采用土建筑,以石头和黏土为主要材料。
这些窑炉通常为圆形或方形,顶部有一个出气孔,用于排除窑炉内的烟尘和废气。
燃料主要使用木材或煤炭,通过火焰加热窑炉内的玻璃原料,使其熔化并成型。
这种早期的窑炉虽然简单,但已经为后来的发展奠定了基础。
二、中世纪的改进与创新在中世纪,玻璃制造业得到了较大的发展,窑炉的设计和技术也有了一定的改进。
其中最重要的创新是引入了化学反应炉,即将燃烧炉与玻璃制造炉相结合。
这种窑炉可以通过控制燃烧过程中的氧气供应,使得玻璃原料在不同的化学环境下熔化,从而实现对玻璃质量和颜色的控制。
中世纪的玻璃窑炉还采用了间歇式操作,即在熔化和成型过程之间有一定的停顿时间。
这种操作方式可以使玻璃原料充分熔化,并排除其中的气泡和杂质。
同时,窑炉的结构也得到了改进,采用了更耐高温的材料,如石灰石和石英砂。
三、现代玻璃窑炉的发展随着工业化的进程,玻璃窑炉得到了进一步的改进和创新。
现代玻璃窑炉主要分为平板玻璃窑炉、浮法玻璃窑炉和玻璃纤维窑炉等几种类型。
这些窑炉在结构、燃料和控制系统等方面都有了重大的进展。
现代玻璃窑炉的结构多采用金属材料,如钢铁和铬铁合金,具有较高的耐高温性能。
窑炉内部通常采用隔热材料进行衬里,以减少热量损失。
此外,现代窑炉还配备了先进的燃烧系统和排放控制设备,以提高燃烧效率和降低环境污染。
对于平板玻璃窑炉和浮法玻璃窑炉来说,其主要的改进是在玻璃成型和冷却过程中。
通过引入先进的玻璃成型技术和冷却系统,可以实现对玻璃板材的尺寸和质量的更精确控制。
玻璃工业窑炉 第一章窑炉概述 第一节玻璃的熔制过程

1.1 玻璃的熔制过程 1.2 玻璃窑炉现状和发展方向 1.3 玻璃熔窑的分类、构造和窑型 1.4 玻璃池窑的工作原理及作业制度 1.5 坩埚窑 1.6 玻璃熔窑的数值模拟 1.7 耐火材料概述
1
1 玻璃工业窑炉
定义:玻璃工业生产专用热工设备统称为玻璃窑炉。
玻璃熔窑 玻璃退火窑 玻璃加工用的窑炉 玻璃熔窑作用:熔化玻璃。玻璃工厂“心脏”。 退火窑作用:消除制品热应力,影响成品率和使用。 热加工作用:复杂形状和特殊要求的制品,如烧口、 火抛光、钢化等。
温度范围
硅酸盐形成
玻璃形成 玻璃液澄清 玻璃液均化 玻璃液冷却
配合料粉料受热、水 分蒸发、盐类分解、 多晶转变、组分熔化 例如SiO2+Na2CO3→ Na2SiO3+CO2↑ 硅酸盐开始熔融
除去玻璃液中肉眼可 见的气体夹杂物
依靠扩散和对流作用 均化
时间空间
不透明烧结物 800~1000℃
不够均匀的透明 1200℃ 的玻璃液。 透明的玻璃液 1400~1500℃ 均匀透明玻璃液 1400~1300℃ 均匀透明玻璃液 1300~1100℃
2
玻璃生产模型及工艺流程图
配料
熔制
成型
3
退火
深加工
窑炉设计基础知识:材料热工基础、 玻璃工艺学、玻璃机械、耐火材料、 热工仪表和自控、工业炉施工等。
设计要点:采用先进经验和数据时, 必须结合工厂实际,仔细分析,因时 因地而异,不可生制过程阶段
主要反应过程
形成物质
5
玻璃熔制过程各阶段关系图
6
玻璃池窑结构示意图
7
我国玻璃窑炉的节能
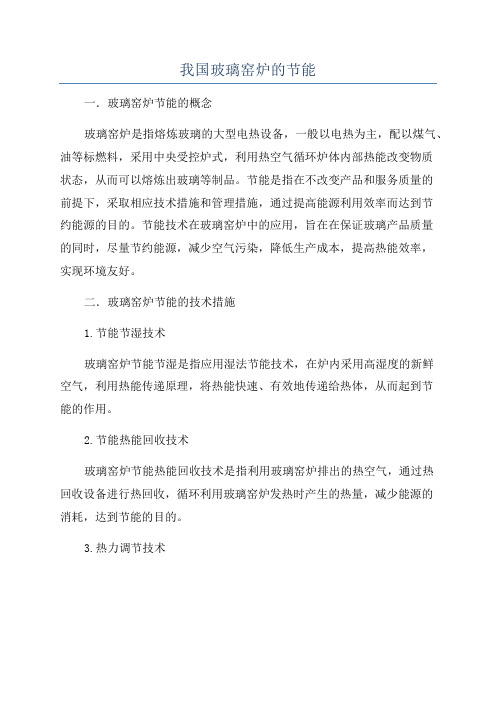
我国玻璃窑炉的节能
一.玻璃窑炉节能的概念
玻璃窑炉是指熔炼玻璃的大型电热设备,一般以电热为主,配以煤气、油等标燃料,采用中央受控炉式,利用热空气循环炉体内部热能改变物质
状态,从而可以熔炼出玻璃等制品。
节能是指在不改变产品和服务质量的
前提下,采取相应技术措施和管理措施,通过提高能源利用效率而达到节
约能源的目的。
节能技术在玻璃窑炉中的应用,旨在在保证玻璃产品质量
的同时,尽量节约能源,减少空气污染,降低生产成本,提高热能效率,
实现环境友好。
二.玻璃窑炉节能的技术措施
1.节能节湿技术
玻璃窑炉节能节湿是指应用湿法节能技术,在炉内采用高湿度的新鲜
空气,利用热能传递原理,将热能快速、有效地传递给热体,从而起到节
能的作用。
2.节能热能回收技术
玻璃窑炉节能热能回收技术是指利用玻璃窑炉排出的热空气,通过热
回收设备进行热回收,循环利用玻璃窑炉发热时产生的热量,减少能源的
消耗,达到节能的目的。
3.热力调节技术。
光伏玻璃窑炉结构

光伏玻璃窑炉结构光伏玻璃窑炉是用于制造光伏玻璃的重要设备,其结构主要包括炉体、炉腔、加热系统、控制系统等。
下面将详细介绍光伏玻璃窑炉的结构。
一、炉体光伏玻璃窑炉的炉体通常由钢结构和保温材料组成。
钢结构为炉体提供了强度和稳定性,保温材料则用于降低热量损失。
常用的保温材料有耐高温陶瓷纤维、硅酸铝纤维等。
炉体的设计应考虑到结构的稳定性和热量传递的效果,以确保炉腔内温度的稳定和均匀。
二、炉腔光伏玻璃窑炉的炉腔是光伏玻璃制造过程中玻璃材料的加热和熔化区域。
炉腔通常由炉底、炉墙和炉顶组成。
炉底是玻璃材料放置和加热的基础,通常使用耐高温的耐火材料制成。
炉墙是围绕炉底的墙壁,用于隔离炉腔内外的温度和环境。
炉顶则是覆盖在炉腔上方,用于保护炉内温度和防止热量散失。
三、加热系统光伏玻璃窑炉的加热系统是实现玻璃材料加热的关键设备。
常用的加热方式包括电阻加热、电弧加热和燃气加热等。
电阻加热是通过电阻丝产生热量,将热量传递给玻璃材料,使其加热和熔化。
电弧加热则是通过电弧产生高温,使玻璃材料迅速加热。
燃气加热是利用燃气燃烧产生高温,将热量传递给玻璃材料。
加热系统的设计应考虑到温度的控制和能源的利用效率。
四、控制系统光伏玻璃窑炉的控制系统负责控制加热系统的运行和炉腔温度的调节。
控制系统通常包括温度传感器、温度控制器和执行器等。
温度传感器用于监测炉腔内的温度变化,将温度信号传递给温度控制器。
温度控制器根据设定的温度范围,控制加热系统的运行,使炉腔内的温度保持在设定的范围内。
执行器则根据控制信号,控制加热系统的运行和炉腔温度的调节。
光伏玻璃窑炉的结构对于光伏玻璃的制造至关重要。
合理的炉体结构和加热系统设计可以提高生产效率和产品质量,而稳定的控制系统可以保证制造过程的稳定性和可控性。
因此,在光伏玻璃窑炉的设计和制造过程中,需要综合考虑结构的稳定性、加热系统的效果以及控制系统的可靠性,以实现光伏玻璃制造的高效、稳定和可控。
玻璃窑炉的分类及工作原理
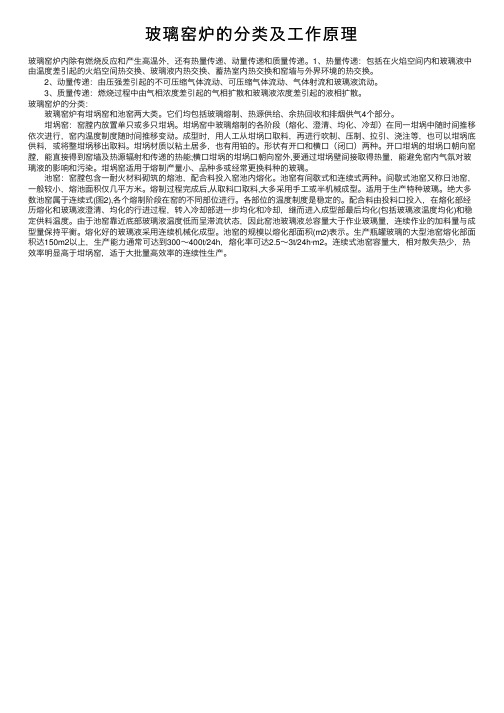
玻璃窑炉的分类及⼯作原理玻璃窑炉内除有燃烧反应和产⽣⾼温外,还有热量传递、动量传递和质量传递。
1、热量传递:包括在⽕焰空间内和玻璃液中由温度差引起的⽕焰空间热交换、玻璃液内热交换、蓄热室内热交换和窑墙与外界环境的热交换。
2、动量传递:由压强差引起的不可压缩⽓体流动、可压缩⽓体流动、⽓体射流和玻璃液流动。
3、质量传递:燃烧过程中由⽓相浓度差引起的⽓相扩散和玻璃液浓度差引起的液相扩散。
玻璃窑炉的分类: 玻璃窑炉有坩埚窑和池窑两⼤类。
它们均包括玻璃熔制、热源供给、余热回收和排烟供⽓4个部分。
坩埚窑:窑膛内放置单只或多只坩埚。
坩埚窑中玻璃熔制的各阶段(熔化、澄清、均化、冷却)在同⼀坩埚中随时间推移依次进⾏,窑内温度制度随时间推移变动。
成型时,⽤⼈⼯从坩埚⼝取料,再进⾏吹制、压制、拉引、浇注等,也可以坩埚底供料,或将整坩埚移出取料。
坩埚材质以粘⼟居多,也有⽤铂的。
形状有开⼝和横⼝(闭⼝)两种。
开⼝坩埚的坩埚⼝朝向窑膛,能直接得到窑墙及热源辐射和传递的热能;横⼝坩埚的坩埚⼝朝向窑外,要通过坩埚壁间接取得热量,能避免窑内⽓氛对玻璃液的影响和污染。
坩埚窑适⽤于熔制产量⼩、品种多或经常更换料种的玻璃。
池窑:窑膛包含⼀耐⽕材料砌筑的熔池,配合料投⼊窑池内熔化。
池窑有间歇式和连续式两种。
间歇式池窑⼜称⽇池窑,⼀般较⼩,熔池⾯积仅⼏平⽅⽶。
熔制过程完成后,从取料⼝取料,⼤多采⽤⼿⼯或半机械成型。
适⽤于⽣产特种玻璃。
绝⼤多数池窑属于连续式(图2),各个熔制阶段在窑的不同部位进⾏。
各部位的温度制度是稳定的。
配合料由投料⼝投⼊,在熔化部经历熔化和玻璃液澄清、均化的⾏进过程,转⼊冷却部进⼀步均化和冷却,继⽽进⼊成型部最后均化(包括玻璃液温度均化)和稳定供料温度。
由于池窑靠近底部玻璃液温度低⽽呈滞流状态,因此窑池玻璃液总容量⼤于作业玻璃量,连续作业的加料量与成型量保持平衡。
熔化好的玻璃液采⽤连续机械化成型。
池窑的规模以熔化部⾯积(m2)表⽰。
玻璃窑炉

玻璃熔窑编辑本段回目录正文编辑本段回目录玻璃制造中用于熔制玻璃配合料的热工设备。
将按玻璃成分配好的粉料和掺加的熟料(碎玻璃)在窑内高温熔化、澄清并形成符合成型要求的玻璃液。
玻璃制造有5000年历史。
以木柴为燃料、在泥罐中熔融玻璃配合料的制造方法延续了很长时间。
1867年德国西门子兄弟建造了连续式燃煤池窑。
1945年后,玻璃熔窑迅速发展。
热工过程玻璃熔窑内除有燃烧反应和产生高温外,还有热量传递、动量传递和质量传递。
①热量传递:包括在火焰空间内和玻璃液中由温度差引起的火焰空间热交换、玻璃液内热交换、蓄热室内热交换和窑墙与外界环境的热交换。
②动量传递:由压强差引起的不可压缩气体流动、可压缩气体流动、气体射流和玻璃液流动。
③质量传递:燃烧过程中由气相浓度差引起的气相扩散和玻璃液浓度差引起的液相扩散。
类型玻璃熔窑有坩埚窑和池窑两大类。
它们均包括玻璃熔制、热源供给、余热回收和排烟供气4个部分。
坩埚窑窑膛内放置单只或多只坩埚。
坩埚窑(图1)中玻璃熔制的各阶段(熔化、澄清、均化、冷却)在同一坩埚中随时间推移依次进行,窑内温度制度随时间推移变动。
成型时,用人工从坩埚口取料,再进行吹制、压制、拉引、浇注等,也可以坩埚底供料,或将整坩埚移出取料。
坩埚材质以粘土居多,也有用铂的。
形状有开口和横口(闭口)两种。
开口坩埚的坩埚口朝向窑膛,能直接得到窑墙及热源辐射和传递的热能;横口坩埚的坩埚口朝向窑外,要通过坩埚壁间接取得热量,能避免窑内气氛对玻璃液的影响和污染。
坩埚窑适用于熔制产量小、品种多或经常更换料种的玻璃。
玻璃熔窑池窑窑膛包含一耐火材料砌筑的熔池,配合料投入窑池内熔化。
池窑有间歇式和连续式两种。
间歇式池窑又称日池窑,一般较小,熔池面积仅几平方米。
熔制过程完成后,从取料口取料,大多采用手工或半机械成型。
适用于生产特种玻璃。
绝大多数池窑属于连续式(图2),各个熔制阶段在窑的不同部位进行。
各部位的温度制度是稳定的。
配合料由投料口投入,在熔化部经历熔化和玻璃液澄清、均化的行进过程,转入冷却部进一步均化和冷却,继而进入成型部最后均化(包括玻璃液温度均化)和稳定供料温度。
玻璃窑炉
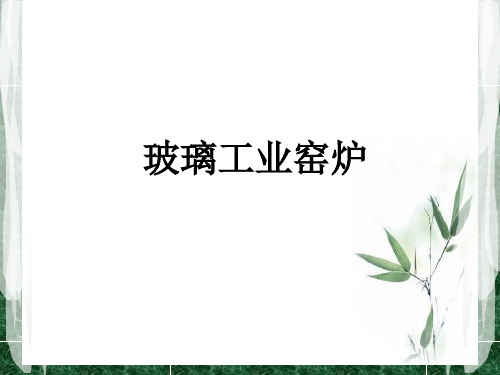
冷却部
④分隔装置
将玻璃池窑的熔化部和冷却部之间分隔。 包括玻璃液的分隔装置和气体空间的分隔装置
分隔装置的类型
浅层分隔装置:卡脖和冷却水管 卡脖:使玻璃液通过卡脖后能用较小的冷却 面积就使其冷却下来。 冷却水管 :挡浮渣作用良好 深层分隔装置:流液洞和窑坎 流液洞:可明显减少回流. 窑坎:可以延长玻璃液在熔化部的时间
小型:300以下吨/天
玻璃熔制部分
玻璃熔化时的重要部位,其作用是将玻璃 配合料加热熔化使之成为玻璃液。 ①熔化部 ②投料口 ③冷却部 ④分隔装置
①熔化部
作用是进行配合料熔化和玻璃液澄清、均化
胸墙: 上空间 (火焰空间) 大碹: 池壁
提供熔化玻璃所需要的热量供给空间
熔化空间
下空间 (窑池)
构成配合料熔化成玻璃液并进行 澄清的空间
池底
②投料口
作用:将玻璃配合料送入窑内并接受来自窑内的 部分热量 将表面部分物料熔融。
正面式:特点: 可使配合料在熔化区池 表面上均匀布,但易造成跑料现象。 侧面式:特点 :克服正面式的缺点,但会 造成③冷却部
作用:进一步均化玻璃液,将温度降低到 一个合理的范围 分配玻璃液到各个供料通道。
燃烧室——小炉
小炉是玻璃窑系统中一个重要的组成部分, 它的好坏直接影响着池窑的工作性能和玻 璃液的质量。结构特征:象一个鸭头或鹅 头。有以下四个部分: ①气道 ②舌头 ③预燃室 ④喷火口
余热回收部分
目的作用: 回收余热、减少热量的损耗,提高热量利用率 提高窑内燃料燃烧温度 加速煤气充分燃烧,节约燃料 余热回收设备: 蓄热室 热交换器 余热锅炉
玻璃工业窑炉
玻璃窑的分类
玻璃窑炉结构

玻璃窑炉结构玻璃窑炉是用于制造玻璃的重要设备,它的结构由多个部分组成。
本文将介绍玻璃窑炉的结构及其功能。
一、炉体结构玻璃窑炉的炉体是整个设备的主要部分,它由炉壳、炉底和炉顶三部分组成。
炉壳是由耐火材料制成的外壳,用于隔离高温炉膛与外界环境。
炉底是玻璃窑炉的底部,用于承载玻璃原料和燃料,并通过燃烧产生高温。
炉顶则用于封闭炉膛,防止热量散失。
二、燃烧系统燃烧系统是玻璃窑炉的关键部分,它由燃烧室、燃烧器和燃气供应系统组成。
燃烧室是将燃料和空气混合并燃烧的空间,通常采用多级燃烧室以提高燃烧效率。
燃烧器则是将燃料和空气混合并喷射到燃烧室中的设备,它的设计和调节能够影响到玻璃窑炉的热效率和燃烧稳定性。
燃气供应系统则负责将燃气输送到燃烧器中,通常包括气体调节阀、气体管道和气体计量装置等。
三、冷却系统冷却系统用于控制玻璃窑炉的温度,避免过热和热量损失。
它由冷却管道、风机和水冷却装置组成。
冷却管道贯穿整个炉体,通过循环水来吸收炉膛的热量。
风机则用于增加冷却效果,将热空气排出,保持炉膛内的温度稳定。
水冷却装置则通过水循环来冷却冷却管道和风机,以保证其正常运行。
四、玻璃产出系统玻璃产出系统是将熔融的玻璃从炉膛中取出并形成所需产品的部分。
它由玻璃收料装置、玻璃流动控制系统和玻璃成型设备等组成。
玻璃收料装置用于接收从炉膛中流出的玻璃,并将其输送到下一道工序。
玻璃流动控制系统则通过控制玻璃的流动速度和方向,以确保玻璃在成型设备中得到适当的形状。
玻璃成型设备则根据产品的要求,将玻璃进行成型、淬火等处理。
五、控制系统控制系统是玻璃窑炉的核心,它用于监测和控制炉膛内的温度、压力、流量等参数。
控制系统通常由传感器、控制器和执行器等组成。
传感器用于采集炉膛内各种参数的信号,并将其传输给控制器。
控制器则根据预设的参数和算法,对炉膛内的温度、压力等进行控制和调节。
执行器则根据控制器的指令,对燃烧器、风机、冷却系统等进行调节和控制。
玻璃窑炉的结构是一个复杂而严密的系统,各个部分相互配合,共同完成玻璃制造过程。
玻璃窑炉国标 耗水量
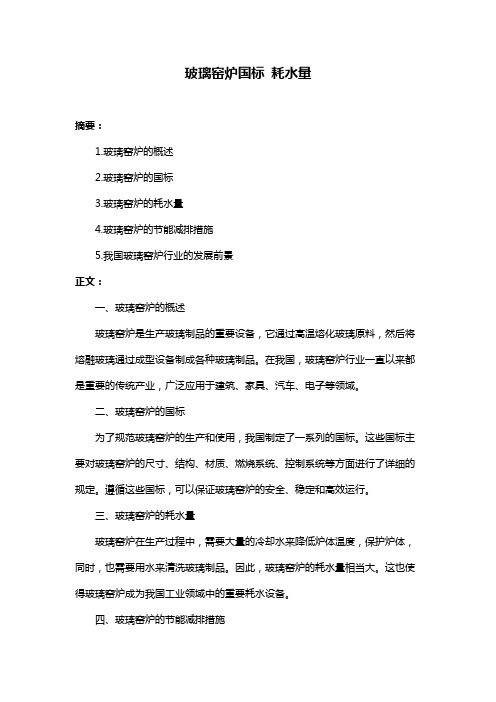
玻璃窑炉国标耗水量
摘要:
1.玻璃窑炉的概述
2.玻璃窑炉的国标
3.玻璃窑炉的耗水量
4.玻璃窑炉的节能减排措施
5.我国玻璃窑炉行业的发展前景
正文:
一、玻璃窑炉的概述
玻璃窑炉是生产玻璃制品的重要设备,它通过高温熔化玻璃原料,然后将熔融玻璃通过成型设备制成各种玻璃制品。
在我国,玻璃窑炉行业一直以来都是重要的传统产业,广泛应用于建筑、家具、汽车、电子等领域。
二、玻璃窑炉的国标
为了规范玻璃窑炉的生产和使用,我国制定了一系列的国标。
这些国标主要对玻璃窑炉的尺寸、结构、材质、燃烧系统、控制系统等方面进行了详细的规定。
遵循这些国标,可以保证玻璃窑炉的安全、稳定和高效运行。
三、玻璃窑炉的耗水量
玻璃窑炉在生产过程中,需要大量的冷却水来降低炉体温度,保护炉体,同时,也需要用水来清洗玻璃制品。
因此,玻璃窑炉的耗水量相当大。
这也使得玻璃窑炉成为我国工业领域中的重要耗水设备。
四、玻璃窑炉的节能减排措施
针对玻璃窑炉的高耗能、高耗水问题,我国积极推动玻璃窑炉的节能减排工作。
这些措施包括提高燃料的利用率、改进燃烧技术、降低烟气排放、减少窑炉散热等。
这些措施的实施,不仅可以降低玻璃窑炉的能耗和水耗,同时也有助于保护环境。
五、我国玻璃窑炉行业的发展前景
随着科技的进步和社会的发展,我国玻璃窑炉行业正面临着新的发展机遇。
未来的玻璃窑炉将更加节能、环保、高效。
玻璃窑简介

Ⅳ
小炉
熔 化池
火焰 空间 花格 墙 工 作池
供料 道
油喷 嘴
流液 洞
蓄热式池窑立剖面图
玻璃窑炉
(4)换热式双碹池窑: F<20m2,也有>30m2,纵焰。烧煤、重油、
天然气等。 优点:与单碹池窑相比,窑顶散热小,炉温
较高,窑内温度分布均匀且稳定。 缺点:砌筑费时,内碹易被高温和粉料蚀损,
与蓄热式比热效率低,换热室易堵,易漏 气。
缓慢 煤炭 飞跃 高热值 持续 高热值
1920~1945年池窑 1945~1960年池窑 1960~至今池窑
窑龄
几个月
0.5年~1.0 年 1~2年 3~4年 7~8年
玻璃窑炉
1.1.2 池窑的几项主要技术指标 (1)熔化率k 窑池每平方米面积上每天熔制的玻璃液量。 t /(m2 ·24h)。 (2)燃料单位消耗量 熔化一吨玻璃液消耗的燃料重量(或体积)。
kg燃料/ t玻璃或m3 / t玻璃液。
玻璃窑炉
(3)有效热效率 (用于玻璃熔制的耗热量 / 单位耗热量)% (4)窑龄和周期熔化率 连续生产的时间。以年为单位。 周期熔化率=窑龄×熔化率(t/ m2 )
玻璃窑炉
1.1.3 玻璃窑炉现状
截止2008年我国玻璃行业约拥有玻璃窑 炉4000~5000座,生产各种玻璃 2800~3500万吨,耗用能源(主要燃料为 煤炭、重油、天然气及电等)折合标准 煤1700~2800万吨。
焰空间分隔
墙等.
形式
全分隔 完全分隔
玻璃窑炉
1.2.1 熔窑分类(3)
玻璃液分 流液洞 流液洞 隔形式 无流液洞
窑产量 大型>150t;中型: 50~100t;小型
窑的规模
- 1、下载文档前请自行甄别文档内容的完整性,平台不提供额外的编辑、内容补充、找答案等附加服务。
- 2、"仅部分预览"的文档,不可在线预览部分如存在完整性等问题,可反馈申请退款(可完整预览的文档不适用该条件!)。
- 3、如文档侵犯您的权益,请联系客服反馈,我们会尽快为您处理(人工客服工作时间:9:00-18:30)。
玻璃窑炉介绍
成都东方凯特瑞环保催化剂有限责任公司(以下简称东方凯特瑞,英文缩写DKC)坐落于四川省成都市武侯工业园,是国内首家集SCR脱硝催化剂研究、开发、设计、制造、检验、销售及服务为一体的国家级高新技术企业。
公司成立于2004年,系中外合资企业,由东方锅炉股份有限公司(其控股公司是中国东方电气集团有限公司)、成都汇联住房经营管理股份有限公司、德国环保热力有限公司(Envirotherm GmbH)合资组建。
公司引进了德国环保热力有限公司(ENV)成熟的烟气脱硝催化剂设计、制造、检验技术及整条生产线,出产的蜂窝式脱硝催化剂具有国际先进水平,广泛应用于火力发电厂、化工厂、垃圾焚烧炉(脱除二恶英)、玻璃制造厂、钢铁厂、水泥厂等的烟气净化,也可为轮船、重型卡车等脱除氮氧化物(NOx)。
公司拥有催化剂性能分析系统、X射线荧光分析仪、X射线衍射分析仪、万能强度实验机、BET比表面积、气相色谱仪等先进的实验、试验设备,并从德国引进了移动式催化剂再生设备专业从事失效催化剂的评估和再生,从而最大程度地提升用户价值。
公司是质量管理体系(GB/T19001-2008)、环境管理体系(GB/T24001-2004)和职业健康与安全管理体系(GB/T28001-2001)"三标合一"管理的规范化企业。
我公司于2011年10月在福建漳州旗滨玻璃窑炉3#炉,成功运行第一条日产600 t浮法玻璃生产线SCR脱硝工程,其后2012年3月又在旗滨4#炉,日产800 t浮法玻璃生产线SCR 脱硝工程中顺利运行。
2012年4月,我公司与江苏亿金环保、浙江大学合作签订江苏华尔润集团浮法七线玻璃窑炉烟气脱硝工程技术协议。
“保护地球环境,建设和谐社会”是东方凯特瑞责无旁贷的历史使命。
东方凯特瑞将秉承“励精图治,和谐发展”的企业理念,立足脱硝市场,面向环保产业,不断产出高质量的环保催化剂,不断“催化”出更为清洁的绿色能源,造福人类社会。