插件元件剪脚成型加工规范标准
DIP插件电子元件切脚作业规范
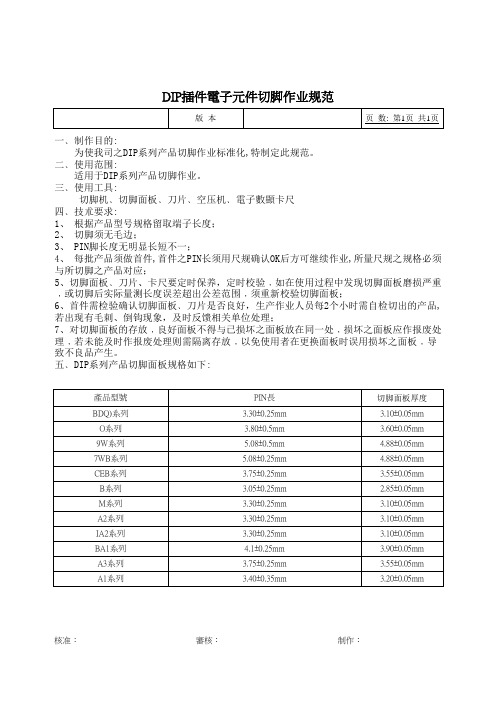
版 本页 数: 第1页 共1页產品型號切脚面板厚度BDQ)系列 3.10±0.05mm O系列 3.60±0.05mm 9W系列 4.88±0.05mm 7WB系列 4.88±0.05mm CEB系列 3.55±0.05mm B系列 2.85±0.05mm M系列 3.10±0.05mm A2系列 3.10±0.05mm IA2系列 3.10±0.05mm BA1系列 3.90±0.05mm A3系列 3.55±0.05mm A1系列3.20±0.05mm4.1±0.25mm 一﹑制作目的:为使我司之DIP系列产品切脚作业标准化,特制定此规范。
二﹑使用范围:适用于DIP系列产品切脚作业。
三﹑使用工具:切脚机﹑切脚面板﹑刀片﹑空压机﹑電子數顯卡尺四﹑技朮要求:1、 根据产品型号规格留取端子长度;2、 切脚须无毛边;3、 PIN脚长度无明显长短不一;4、 每批产品须做首件,首件之PIN长须用尺规确认OK后方可继续作业,所量尺规之规格必须与所切脚之产品对应;5、切脚面板﹑刀片、卡尺要定时保养,定时校验﹐如在使用过程中发现切脚面板磨损严重﹐或切脚后实际量测长度误差超出公差范围﹐须重新校验切脚面板;6、首件需检验确认切脚面板﹑刀片是否良好,生产作业人员每2个小时需自检切出的产品,若出现有毛刺、倒钩现象,及时反馈相关单位处理;7、对切脚面板的存放﹐良好面板不得与已损坏之面板放在同一处﹐损坏之面板应作报废处理﹐若未能及时作报废处理则需隔离存放﹐以免使用者在更换面板时误用损坏之面板﹐导致不良品产生。
五﹑DIP系列产品切脚面板规格如下:3.75±0.25mm 5.08±0.25mm 5.08±0.5mm 3.80±0.5mm 3.75±0.25mm 3.30±0.25mm 3.30±0.25mm DIP插件電子元件切脚作业规范核准: 審核: 制作:3.30±0.25mm 3.30±0.25mm 3.05±0.25mm 3.40±0.35mmPIN長。
插件焊接引脚切割标准
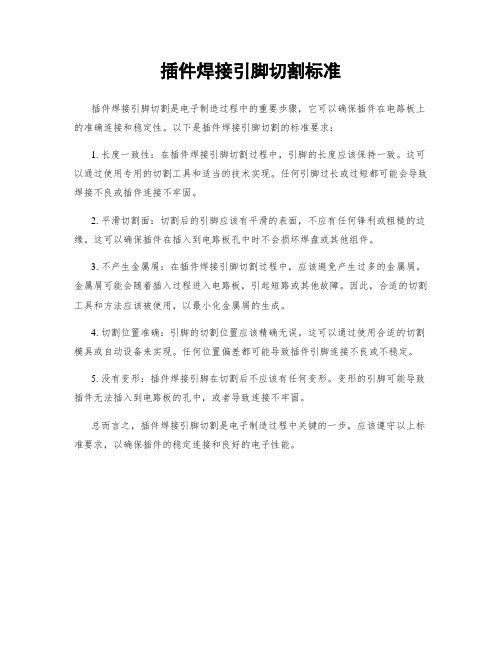
插件焊接引脚切割标准
插件焊接引脚切割是电子制造过程中的重要步骤,它可以确保插件在电路板上的准确连接和稳定性。
以下是插件焊接引脚切割的标准要求:
1. 长度一致性:在插件焊接引脚切割过程中,引脚的长度应该保持一致。
这可以通过使用专用的切割工具和适当的技术实现。
任何引脚过长或过短都可能会导致焊接不良或插件连接不牢固。
2. 平滑切割面:切割后的引脚应该有平滑的表面,不应有任何锋利或粗糙的边缘。
这可以确保插件在插入到电路板孔中时不会损坏焊盘或其他组件。
3. 不产生金属屑:在插件焊接引脚切割过程中,应该避免产生过多的金属屑。
金属屑可能会随着插入过程进入电路板,引起短路或其他故障。
因此,合适的切割工具和方法应该被使用,以最小化金属屑的生成。
4. 切割位置准确:引脚的切割位置应该精确无误。
这可以通过使用合适的切割模具或自动设备来实现。
任何位置偏差都可能导致插件引脚连接不良或不稳定。
5. 没有变形:插件焊接引脚在切割后不应该有任何变形。
变形的引脚可能导致插件无法插入到电路板的孔中,或者导致连接不牢固。
总而言之,插件焊接引脚切割是电子制造过程中关键的一步,应该遵守以上标准要求,以确保插件的稳定连接和良好的电子性能。
元器件引脚成形与切脚工艺、检验规程
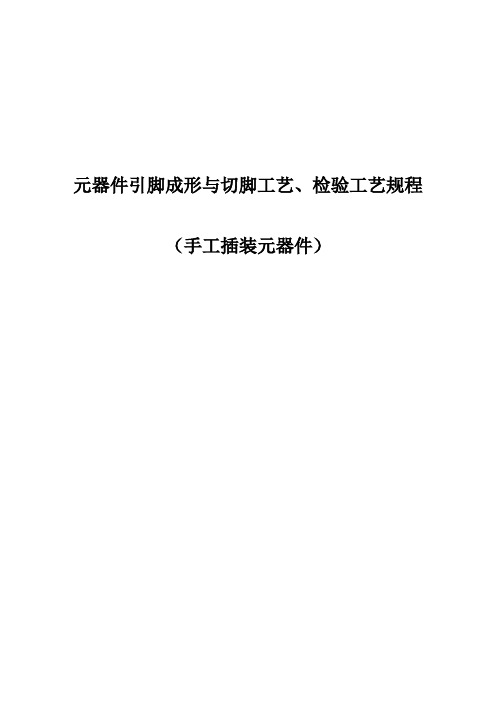
元器件引脚成形与切脚工艺、检验工艺规程(手工插装元器件)1.目的1.1.1.1.本规程规定了手工插装电子元器件引脚成形与切脚应满足的工艺要求,以及引脚成形与切脚过程的检验程序。
2.适用范围2.1.1.1.本规程适用于产品分立电子元器件插装前的引脚成形与切脚,规定了元器件引脚成形与切脚的技术要求和质量保证措施,同时也可作为设计、生产、检验的依据。
3.适用人员3.1.1.1.本规程适用于产品生产的工艺人员、电子装联操作人员、质量检验人员等。
4.参考文件4.1.1.1.IPC-A-610D 《电子组件的可接受性》。
4.1.1.2.IPC J-STD-001D 《焊接的电气和电子组件要求》。
4.1.1.3.QJ 3171—2003 《航天电子电气产品元器件成形技术要求》。
4.1.1.4.QJ 165A—1995 《航天电子电气产品安装通用技术要求》。
4.1.1.5.ANSI/ESD S20.20-2007 《静电放电控制方案》。
5.名词/术语5.1.1.1.功能孔:PCB上用于电气连接的孔。
5.1.1.2.非功能孔:PCB上用于机械安装或固定的孔。
5.1.1.3.支撑孔(Supported Hole):两层及多层PCB上的功能孔,孔壁上镀覆金属,俗称镀通孔。
5.1.1.4.非支撑孔(Unsupported Hole):单层或双层PCB上的功能孔,孔壁上不镀覆金属,俗称非镀通孔。
5.1.1.5.淬火引脚(Tempered lead):元器件的引脚经过淬火处理。
6.工艺元器件成形与切脚是整个PCBA生产的首要工序,成形与切脚的质量直接影响后续的产品生产。
6.1.工艺流程6.1.1.成形与切脚的工艺流程图工艺要求工艺流程说明根据元器件的封装、包装形式、本体以及引脚直径、成形类型、成形间距、印制板厚度、切脚长度以及元器件数量等确定成形与切脚的工具或模具,制定元器件成形与切脚明细表;元器件成形与切脚操作人员应按照设计、工艺文件要求对元器件的名称、型号、规格进行确认;根据明细表中的元器件特性及参数,选择元器件成形与切脚的顺序;依据成形顺序使元器件成形与切脚的尺寸调整更加容易控制;根据元器件首件的成形与切脚试验流程操作;首件成形与切脚检验完成后,将不合格的试样单独存放或处理;成形过程中要不定时的对工具或工装成形面的光滑度进行检查,确保成形质量;当元器件数量超过100个时,操作人员必须对最后成形与切脚的10个元器件按照试验检验项进行检验(7.1.2节);成形与切脚后的一般性元器件密闭保存;静电敏感元器件使用防静电容器存放;湿敏元器件要干燥存储(详见元器件存储工艺规程);图6-1元器件成形与切脚工艺流程6.1.2.首件成形与切脚试验6.1.2.1.成形与切脚试验时,要根据成形与切脚明细表的参数要求调整好工具或工装,按图6-2所示流程进行。
插件元件剪脚成型加工标准

精心整理1、目的:规范元件成型方式与尺寸,使之标准化作业。
2、适用范围:适用于茂硕科技元件成型工艺文件;如果客户有其它或高于此规范的特别要求,一律按客户要求执行。
3、职责:3.1工艺拟制者负责按本规范操作。
4,4.2工艺制作软件统一用EXCEL2000。
4.3工艺规范依据主要参照IPC-A-610C标准,元件两引脚间对应于PCB板两焊盘间(W),在PCB板间焊点免除零件脚长即元件焊接后深处的高度为L(mm),如各项目对于元件管脚伸出长度由特别要求时,以客户的要求为准。
元件成型方式大致分为立式成型和卧式成型两种,元件成型管脚长度分为三种:当设定成型尺寸时,必须要充分考虑上述的成型尺寸要求,避免元件脚变形或是元件本体开裂损伤,对于手工加工或是极其加工安全尺寸要求也不会一致,需要根据实际情况而定。
4.2.2额定功率<1W的普通电阻,要求电阻本体平贴于PCB板面,电阻两引脚间距对应于PCB板两焊间距(L),PCB板厚(T),卧式成型标准。
成型尺寸:手工成型时注意手只能持住元件引脚弯折,而非本体机器成型≥1W的普通电阻,或额定功率<1W的立式成型的普通电阻,要本体底部高于PCB板面1-6mm(h),电阻两引脚间距对应于PCB板两焊盘间距(L),PCB板厚(T)。
成型方式:1、手工整形(如下图)手工成型2、机器成形成型尺寸:4.4.6对于额定功率<1W的稳压二极管,或者是额定电流<1A的其它各种二极管,二极管两引脚对应于PCB板两焊盘间距(L),PCB板厚(T)。
成型尺寸:5、前加工工艺的注意事项要求:5.1应做互检要求,(一般是检查材料有无错料、混料、丝印不符、元件破损不良)。
5.2明确加工先后顺序,首先做什么,最后干什么,逻辑思维强,使操作者能在最短的时间内完成,并且要保证品质要求。
必须注明元件丝印或外观图,注意元件的尺寸范围与误差范围的区别,如0.3-4.0mm与3.5±0.5mm区别。
剪脚工位作业规范
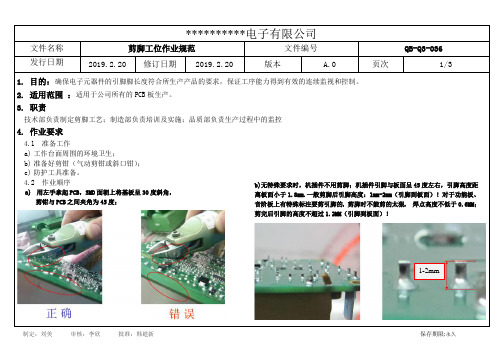
文件名称剪脚工位作业规范文件编号QB-Q3-036 发行日期2019.2.20 修订日期2019.2.20 版本 A.0 页次1/31. 目的:确保电子元器件的引脚脚长度符合所生产产品的要求,保证工序能力得到有效的连续监视和控制。
2. 适用范围:适用于公司所有的PCB板生产。
3. 职责技术部负责制定剪脚工艺;制造部负责培训及实施;品质部负责生产过程中的监控4. 作业要求4.1 准备工作a)工作台面周围的环境卫生;b)准备好剪钳(气动剪钳或斜口钳);c)防护工具准备。
4.2 作业顺序a)用左手拿起PCB,SMD面朝上将基板呈30度斜角,剪钳与PCB之间夹角为45度;b)无特殊要求时,机插件不用剪脚;机插件引脚与板面呈45度左右,引脚高度距离板面小于1.8mm.一般剪脚后引脚高度:1mm-2mm(引脚到板面)!对于功能板、音阶板上有特殊标注要剪引脚的,剪脚时不能剪的太狠,焊点高度不低于0.6MM;剪完后引脚的高度不超过1.2MM(引脚到板面)!1-2mm文件名称 剪脚工位作业规范文件编号 QB-Q3-036发行日期2019.2.20修订日期2019.2.20版本A.0页次2/3E)剪弯脚时,必须顺着弯脚方向剪取;C)避免剪脚时将其周围SMD 料剪破损,需转动PCB 剪脚方向,避免碰触周围元器件; 。
D)有特殊要求时,比如引脚要剪到底,剪脚时把露出的引脚剪掉,剪到焊锡处即可,不能剪的太狠,禁止把焊锡面剪掉。
正确剪脚方错误剪脚方式 F)剪脚顺序:从右至左,从下至上,不能漏剪!文件名称剪脚工位作业规范文件编号QB-Q3-036发行日期2019.2.20 修订日期2019.2.20 版本 A.0 页次3/3 G)零件密集时,剪脚速度放慢,小脚与细脚用适当斜口钳作业;H)剪脚的过程中,剪除的方向对向防护工具。
I)剪脚时,不能把贴片物料,剪掉、剪碎!常见不良现象,见以下附图.。
电子厂手工插件工艺标准
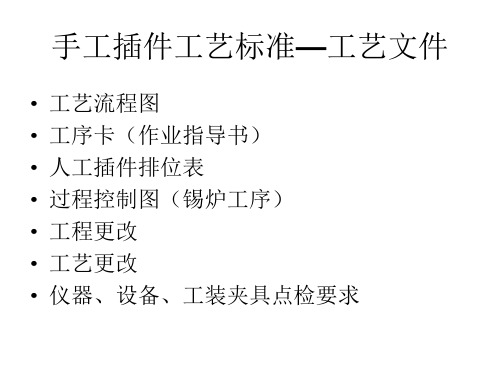
插装标准(4)
手工插件工艺标准—作业标准
• 组件 • 高压包完全插贴PCB,并且使卡扣完全卡入
PCB卡位 • 高频头完全插贴PCB,固定脚对角拧弯紧固,
与PCB相垂直 • 中频板、BBE板、图文板、立体声板等组
件,完全插贴PCB,并且使其与PCB相垂 直;直接插贴板面需点胶加固
插装标准(5)
手工插件工艺标准—工艺文件
• 工艺流程图 • 工序卡(作业指导书) • 人工插件排位表 • 过程控制图(锡炉工序) • 工程更改 • 工艺更改 • 仪器、设备、工装夹具点检要求
手工插件工艺标准—作业标准
• 手指要尽量避免与元件引脚、PCB板焊盘 直接接触
• 大元件(如高压包)或PCB板组件拿取时, 应拿住能支撑整个元件(或组件)重量的 位置,而不能抓住象引线之类的脆弱部位
• 轻拿轻放
元器件拿取要求
手工插件工艺标准—作业准
• 元件成型应尽量使用专用的成型设备或夹 具。
• 元件成型标准:引脚长度相等且与PCB板 孔距一致;元件两端长度约1.5MM,引脚长度 一般为4~6MM
元件成型要求
手工插件工艺标准—作业标准
• 电阻 1/2W及以下功率电阻插平贴板面; 1W及以上功率电阻需预先成型,插件高度 即为成型高度。
手工插件工艺标准—作业标准
• 导线 线头<1MM,将导线和PCB的结合部用热 熔胶覆盖
• 其它如IC、变压器、开关、声表、插座等 元件均需插贴PCB
插装标准(6)
• 二极管 无磁环的二极管平贴PCB板插件 有磁环的二极管由磁环的高度决定 插装时需注意极性
插装标准(1)
手工插件工艺标准—作业标准
• 电容 • 磁介电容、绦纶电容、陶瓷滤波器自插料时
电子元器件插件工艺规范标准
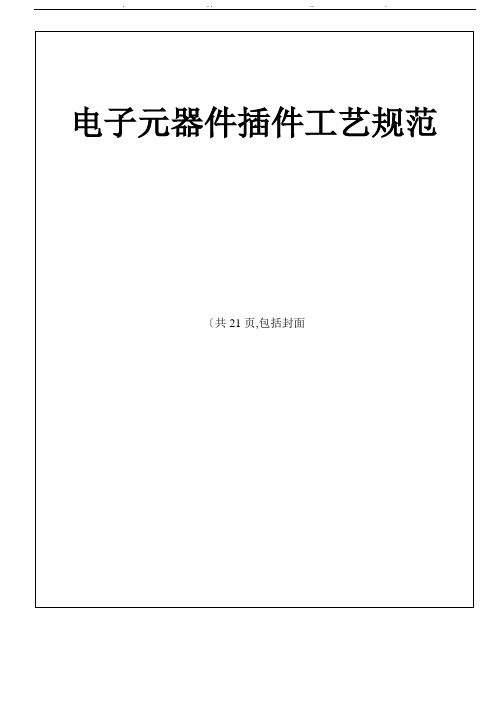
. . . .. .6.2.2立式零件组装的方向与极性6.2.3卧式电子零组件插装高度与倾斜1000μF+++ J233 ●拒收状况<Reject Condition> 1.极性零件组装极性错误 <极性反> 。
2.无法辨识零件文字标示。
3.以上缺陷任何一个都不能接收。
1000μF++10μ 16● 332J允收状况<Accept Condition> 1.极性零件组装于正确位置。
2.可辨识出文字标示与极性。
6.2.4立式电子零组件浮件6.2.5机构零件浮件6.2.6机构零件组装外观〔1 6.2.6机构零件组装外观〔26.2.7零件脚折脚、未入孔、未出孔零件脚与线路间距6.2.9元件本体斜度最佳: 元件本体与其在基板上两插孔位组成的连线或元件体在基板上的边框线完全平行,无斜度,如图: 可接受: 元件体与其在基板上两插孔位组成的连线或元件体在基板上的边框线斜度≤1.0mm,如图: 拒收: 元件体与其在基板上两插孔位组成的连线或元件体在基上的边框线斜度>1.0mm,如图:6.2.10元件引脚的紧张度最佳: 元件引脚与元件体主轴之间夹角为0°<即引脚与元件主轴平行, 垂直于PCB板面>, 如图:可接受: 元件引脚与元件体主轴袒闪角Q<15°,如图:拒收: 元件引脚与元件体主轴之间夹角Q>15°.6.2.11元件引脚的电气保护在PCBA板上有些元件要有特殊的电气保护,则通常使用胶套,管或热缩管来保护电路最佳: 元件引脚弯曲部分有保护套,垂直或水平部分如跨过导体需有保护套且保护套距离插孔之间距离A为1.0mm-2.0mm,如图:可接受: 保护套可起到防止短路作用, 引脚上无保护套时, 引脚所跨过的导体之间的距离B≥0.5mm, 如图:拒收: 保护套损坏或A>2.0mm时, 不能起到防止短路作用或引脚上无保护套时, 或引脚所跨过的导体之间距离B<0.5mm,如图:6.2.12元件间的距离最佳: 在PCBA板上,两个或以上踝露金属元件间的距离要D≥2.0mm,如图:可接受: 在PCBA板上, 两个或以上踝露金属元件的距离最小D≥1.6mm, 如图:拒收: 在PCBA板上, 两个或以上踝露金属元件间的距离D<1.6mm, 如图:6.3元件的损伤6.3.1元件本体损伤最佳: 元件表面无任何损伤,且标记清晰可见,如图:可接受: 元件表面有轻微的抓、擦、刮伤等,但未露出元件基本面或有效面,如图:拒收: 元件面受损并露出元件基本面或有效面积,如图:6.3.2元件引脚的损伤最佳: 元件引脚无任何损伤, 弯脚处光滑完好, 元件表面标记清晰可见, 如图:可接受: 元件引脚不规则弯曲或引脚露铜,但元件或部品引脚损伤程度小于该引脚直径的10%,如图:拒收: < 1 >元件引脚受损大于元件引脚直径的10%,如图:< 2 >严重凹痕锯齿痕,导致元件脚缩小超过元件的10%,如图:6.3.3IC元件的损伤最佳: IC 元件无任何损伤, 如图:可接受: 元件表面受损, 但未露密封的玻璃, 如图:拒收: 元件表面受损并露出密封的玻璃, 如图:6.3.4轴向元件损伤最佳: 元件表面无任何损伤,如图:可接受: 元件表面无明显损伤,元件金属成份无暴露,如图:拒收:< 1 >元件面有明显损伤且绝缘封装破裂露出金属成份或元件严重变形,如图:< 2 > 对于玻璃封装元件,不允许出现小块玻璃脱落或损伤.6.4元件应力评估,进行插件作业时,需参照以下表格对个各元件易产生应力部位进行重点检查和防护。
插件元件剪脚成型加工标准分解

1、目的:规范元件成型方式与尺寸,使之标准化作业。
2、适用范围:适用于茂硕科技元件成型工艺文件;如果客户有其它或高于此规范的特别要求,一律按客户要求执行。
3、职责:3.1 工艺拟制者负责按本规范操作。
3.2 工艺审核人员负责对规范进行对工艺的全面审核。
3.3工程部经理负责本规范在工艺拟制者中有效执行。
4、程序内容:4.1操作规范:4.1.1 收集和确认客户最新资料,文件(如:ENP的ECO,BOM线路图,元件位置图等),产品样板,空PCB板,元器件材料。
4.1.2 对客户资料,文件进行研究,并用通俗易懂的语言将其描述清楚。
4.1.3 对关键性的加工事项和图形示意图,材料加工要求需要进行仔细的研究和确认。
4.1.4 前加工易出错的工序要求特别注意,并加注到生产工艺中。
4.1.5 在成形过程中,除特殊情况下,手工持取元器件一般是持取元器件本体,禁止持取元器件引线,以防止污染元器件引线,从而引起焊接不良。
4.1.6 对于电阻、二极体、电容等非功率半导体元器件,其本体一般没有金属散热器,可以直接持取本体;对于功率半导体元器件如IC,手工持取本体时,禁止触摸其散热面,以免影响散热材料的涂敷或装配。
4.2 工艺制作软件统一用EXCEL2000。
4.3 工艺规范依据主要参照IPC-A-610C标准,元件两引脚间对应于PCB板两焊盘间(W),在PCB板间焊点免除零件脚长即元件焊接后深处的高度为L(mm),如各项目对于元件管脚伸出长度由特别要求时,以客户的要求为准。
元件成型方式大致分为立式成型和卧式成型两种,元件成型管脚长度分为三种:(1).元件成型管脚长度=元件管脚伸出长度(L)+PCB板厚(T)(2).元件成型管脚长度=元件管脚伸出长度(L)+PCB板厚(T)+抬高于PCB板面高度(H)(3).元件成型管脚长度=元件管脚伸出长度(L)+PCB板厚(T)+抬高于PCB板面高度(H)+元件本体高度(b)4.4 元件成型尺寸标注和要求,必须要充分考虑到生产线操作的可行性,另外对于元件本体损伤的可能性也加以充分考虑,确保加工出来的元件符合IPC-A-610C的标准和客户的要求。
元器件成形及标准
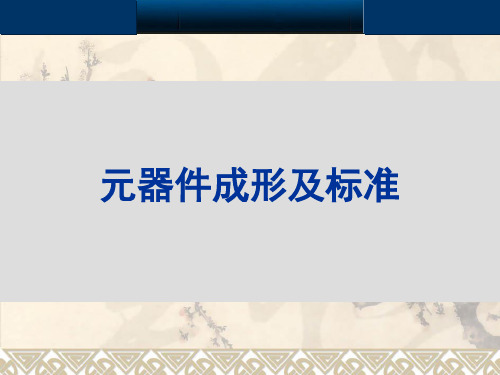
创 新 永 无 止 境
1.严格按照《作业指导书》作业,调整操 作设备. 2.操作时应注意自身及他人的人身安全。 3.元件成形时一定要注意成形的形状和尺 寸,以免造成物料浪费。 4.定时自检,并实装PCB检验,以免批量 浪费。 5.操作时必须戴好静电手环。
成形的注意事项
创 新 永 无 止 境
谢谢
特加工 物料 切脚刀
轨道架 控制面板
成品盒
全自动成形机
成形的治工具、设备
创 新 永 无 止 境
二)机器成形设备
手柄
紧固螺 丝
上成型 模 下成型 模
上成型 模紧固 螺丝 下 成 型 模 紧 固 螺丝
手动啤压机
成形的治工具、设备
创 新 永 无 止 境
三、元器件成形的形状及标准
元器件成形的形状及标准
创 新 永 无 止 境
一)元器件成形的形状 1、U型
2、F型
元器件成形的形状及标准
创 新 永 无 止 境
3、直角型
4、异型
元器件成形的形状及标准
创 新 永 无 止 境
二)元器件成形的标准 1、一般标准 使元件插入PCB板后,漏出PCB的脚长 在1.2~2mm之间。
元件插入PCB板后, 漏出PCB的脚长在 1.2~2mm之间。
加工剪短 元件脚加工成要求的脚长 元件脚来料时过长
成形工艺简介
创 新 永 无 止 境
2.加工成特定形状 因插件的要求,元件有时需要加工成特定的形状 例如:
加工成各种特定形状 元件来料时形状
成形工艺简介
创 新 永 无 止 境
二)成形方式 1.手工成形 指利用剪钳、尖嘴钳等工具以及各种成形治具将元 件进行元件脚剪短及元件成形。手式成形可以加工特殊 元件或加工特殊形状。 2.机器成形 指利用机器设备将元件进行元件脚剪短及元件成形。 机器成形具有快速、准确的特点。
插件元件剪脚成型加工标准分解
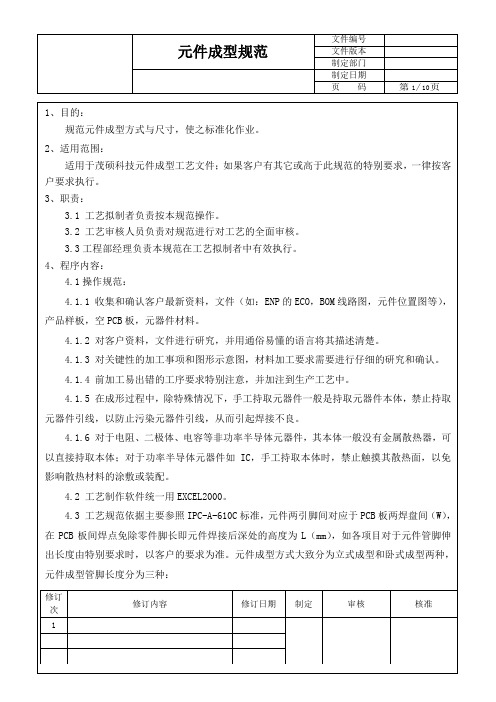
制定日期页码第2/10页(1).元件成型管脚长度=元件管脚伸出长度(L)+PCB板厚(T)(2).元件成型管脚长度=元件管脚伸出长度(L)+PCB板厚(T)+抬高于PCB板面高度(H)(3).元件成型管脚长度=元件管脚伸出长度(L)+PCB板厚(T)+抬高于PCB板面高度(H)+元件本体高度(b)4.4 元件成型尺寸标注和要求,必须要充分考虑到生产线操作的可行性,另外对于元件本体损伤的可能性也加以充分考虑,确保加工出来的元件符合IPC-A-610C的标准和客户的要求。
4.4.1 对于所有引线成型元件(立式和卧式)成型都适用,又哦成型的安全距离和空间:a(图中用L表示)元件直径(D)或厚度(T),注意以下要求:当元件直径(D)或厚度(T)≤0.8mm时,内曲线半径(R)为:R=1D当元件直径(D)或厚度(T)0.8mm< D或T<1.2mm时,内曲线半径(R)为:R=1.5D 当元件直径(D)或厚度(T)≥1.2mm时,内曲线半径(R)为:R=2D当设定成型尺寸时,必须要充分考虑上述的成型尺寸要求,避免元件脚变形或是元件本体开裂损伤,对于手工加工或是极其加工安全尺寸要求也不会一致,需要根据实际情况而定。
4.2.2 额定功率<1W的普通电阻,要求电阻本体平贴于PCB板面,电阻两引脚间距对应于PCB板两焊间距(L),PCB板厚(T),卧式成型标准。
成型尺寸:项目允收范围A 85°< a < 95°L1、L2 L1、L2为1.0mm以上L 依插装位置PCB孔距元件成型管脚长度=元件管脚伸出长度(L)+PCB板厚(T)+抬高于PCB板面高度(H)制定日期页码第3/10页成型方式:手工或机器整形(如下图)手工成型时注意手只能持住元件引脚弯折,而非本体机器成型4.4.3对额定功率≥1W的普通电阻,或额定功率<1W的立式成型的普通电阻,要本体底部高于PCB板面1-6mm(h),电阻两引脚间距对应于PCB板两焊盘间距(L),PCB板厚(T)。
(新人培训)电子元器件插件工艺检验标准
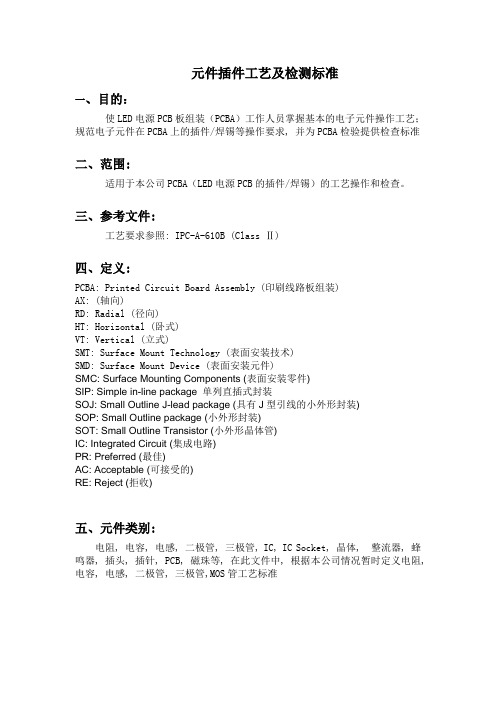
元件插件工艺及检测标准一、目的:使LED电源PCB板组装(PCBA)工作人员掌握基本的电子元件操作工艺;规范电子元件在PCBA上的插件/焊锡等操作要求, 并为PCBA检验提供检查标准二、范围:适用于本公司PCBA(LED电源PCB的插件/焊锡)的工艺操作和检查。
三、参考文件:工艺要求参照: IPC-A-610B (Class Ⅱ)四、定义:PCBA: Printed Circuit Board Assembly (印刷线路板组装)AX: (轴向)RD: Radial (径向) HT: Horizontal (卧式)VT: Vertical (立式) SMT: Surface Mount Technology (表面安装技术)SMD: Surface Mount Device (表面安装元件)SMC: Surface Mounting Components (表面安装零件)SIP: Simple in-line package 单列直插式封装SOJ: Small Outline J-lead package (具有J型引线的小外形封装)SOP: Small Outline package (小外形封装)SOT: Small Outline Transistor (小外形晶体管)IC: Integrated Circuit (集成电路)PR: Preferred (最佳)AC: Acceptable (可接受的)RE: Reject (拒收)五、元件类别:电阻, 电容, 电感, 二极管, 三极管, IC, IC Socket, 晶体, 整流器, 蜂鸣器, 插头, 插针, PCB, 磁珠等, 在此文件中, 根据本公司情况暂时定义电阻,电容, 电感, 二极管, 三极管,MOS管工艺标准六、元件插件工艺及检测标准1. 卧式(HT) 插元件卧式插元件主要是小功率, 低容量, 低电压的电阻, 电容, 电感, Jumper(跳线), 二极管, IC等, PCBA上的组装工艺要求和接收标准如下:1.1元件在基板上的高度和斜度1.1.1轴向(AX)元件1.1.1.1功率小于1W的电阻, 电容(低电压, 小容量的陶瓷材料), 电感, 二极管, IC等元件PR: 元件体平行于PCB板面且紧贴PCB板面, 如图示:AC: 元件体与PCB表面之间最大倾斜距离(D)不大于3mm, 元件体与PCB 表面最低距离(d)不大于0.7mm, 如图示:RE: 元件体与PCB板面距离D>3mm, 或d>0.7mm1.1.1.2耗散功率大于或等于1W的元件PR: 元件体平行于PCB板面且与PCB板面之间的距离D≥1.5mm, 如图示:AC: 元件体与PCB板面之间的距离D≥1.5mm, 元件体与PCB板面的平行不作要求RE: 元件体与PCB板面之间的距离D≤1.5mm1.1.1.3 ICPR: 元件体平行于PCB, IC引脚全部插入焊盘中, 引脚突出PCB面1.mm, 倾斜度=0, 如图示:AC: IC引脚全部插入焊盘中, 引脚突出PCB面大于0.5mm, 如图:RE: IC引脚突出PCB面小于0.5mm, 或看不见元件引脚, 如图:1.1.2径向(RD)元件(电容, 晶振)PR: 元件体平贴于PCB板面, 如图示:AC: 元件脚最少有一边贴紧PCB板面, 如图示:RE: 元件体未接触PCB板面, 如图示:1.2元件的方向性与基板对应符号的关系:1.2.1 轴向(AX) 无极性元件(电阻, 电感, 小陶瓷电容等)PR: 元件插在基板中心标记且元件标记清晰可见, 元件标记方向一致(从左到右, 从上到下), 如图:AC: 元件标记要求清晰, 但方向可不一致, 如图:RE: 元件标记不清楚或插错孔位, 如图:1.2.2 轴向(AX) 有极性元件, 如二几管, 电解电容等PR: 元件的引脚插在对应的极性脚位, 元件标记清晰可看见, 如图:AC: 元件的引脚必须插在相应的极性脚位上, 元件标记可看见, 如图:RE: 元件的引脚未按照极性方向插在相应的脚位上, 如图:1.3元件引脚成形与曲脚1.3.1引脚成形PR: 元件体或引脚保护层到弯曲处之间的距离L>0.8mm, 或元件脚直径弯曲处无损伤, 如图:AC: 元件脚弯曲半径( R )符合以下要求:元件脚直径或厚度( D/T ) 半径( R )≤0.8mm 1 X D0.8~1.2mm 1.5 X D≥1.2mm 2 X DRE: ( 1 ) 元件体与引脚保护弯曲处之间L<0.8mm, 且弯曲处有损伤, 如图:( 2 ) 或元件脚弯曲内径R小于元件直径, 如图:1.3.2屈脚PR: 元件屈脚平行于相连接的导体, 如图:AC: 屈脚与相间的裸露导体之间距离(H) 大于两条非共通导体间的最小电气间距, 如图:RE: 屈脚与相间的裸露导体之间距离(H) 大于两条非共通导体间的最小电气间距, 如图:1.4元件损伤程度1.4.1元件引脚的损伤PR: 元件引脚无任何损伤, 弯脚处光滑完好, 元件表面标记清晰可见, 如图:AC: 元件引脚不规则弯曲或引脚露铜,但元件或部品引脚损伤程度小于该引脚直径的10%,如图:RE: ( 1 )元件引脚受损大于元件引脚直径的10%,如图:( 2 )严重凹痕锯齿痕,导致元件脚缩小超过元件的10%,如图:1.4.2 IC元件的损伤PR: IC 元件无任何损伤, 如图:AC: 元件表面受损, 但未露密封的玻璃, 如图:RE: 元件表面受损并露出密封的玻璃, 如图:1.4.3轴向(AX)元件损伤PR: 元件表面无任何损伤,如图:AC: 元件表面无明显损伤,元件金属成份无暴露,如图:RE:( 1 )元件面有明显损伤且绝缘封装破裂露出金属成份或元件严重变形,如图:( 2 ) 对于玻璃封装元件,不允许出现小块玻璃脱落或损伤.1.5元件体斜度PR: 元件体与其在基板上两插孔位组成的连线或元件体在基板上的边框线完全平行,无斜度,如图:AC: 元件体与其在基板上两插孔位组成的连线或元件体在基板上的边框线斜度≤1.0mm,如图:RE: 元件体与其在基板上两插孔位组成的连线或元件体在基上的边框线斜度>1.0mm,如图:2. 立式(VT) 插元件2.1.1 轴向(AX) 元件PR: 元件体与PCB板面之间的高度H在0.4mm-1.5mm之间, 且元件体垂直于PCB板面, 如图:AC: H在0.4-3mm之间, 倾斜Q<15°,如图:RE: 元件体与PCB板面倾斜, 且间距H<0.4mm或H>3mm或Q>15°.2.1.2径向(RD)元件2.1.2.1引脚无封装元件PR: 元件体引脚面平行于PCB板面, 元件引脚垂直于PCB板面, 且元件体与PCB板面间距离为0.25-2.0mm, 如图:AC: 元件体与PCB板面斜倾度Q小于15°, 元件体与PCB板面之间的间隙H在0.20-2.0mm之间, 三极管离板面高度最高大于4.0mm, 如图: RE: 元件与PCB板面斜倾角Q>15°或元件体与PCB板面的间隙H>2.0mm或三极管>4.0mm.2.1.2.2:引脚有封装元件PR: 元件垂直PCB板面, 能明显看到封装与元件面焊点间有距离, 如图: AC: 元件质量小于10g且引脚封装刚好触及焊孔且在焊孔中不受力, 而焊点面的引脚焊锡良好(单面板), 且该元件在电路中的受电压<240VAC或DC, 如图:RE: 引脚封装完全插入焊孔中, 且焊点面焊锡不好, 可看见引脚封装料, 如图:2.2元件的方向性与基板符号的对应关系2.2.1轴向(AX)元件PR: 元件引脚插入基板时,引脚极性与基板符号极性完全吻合一致,且正极一般在元件插入基板时的上部,负极在下部,如图:AC: 元件引脚插入基板时,引脚极性与基板符号极性吻合一致,但元件在插入基板时,正极在上和负极在下不作要求,如图:RE: 元件引脚插入基板时,引脚极性与基板符号极性刚好相反,如图:2.2.2径向(RD)元件AC: 元件引脚极性与基板符号极性一致,如图:RE: 元件体引脚极性与基板符号极性相反,如图:2.3元件引脚的紧张度PR: 元件引脚与元件体主轴之间夹角为0°(即引脚与元件主轴平行, 垂直于PCB板面), 如图:AC: 元件引脚与元件体主轴袒闪角Q<15°,如图:RE: 元件引脚与元件体主轴之间夹角Q>15°.2.4元件引脚的电气保护在PCBA板上有些元件要有特殊的电气保护,则通常使用胶套,管或热缩管来保护电路PR: 元件引脚弯曲部分有保护套,垂直或水平部分如跨过导体需有保护套且保护套距离插孔之间距离A为1.0mm-2.0mm,如图:AC: 保护套可起到防止短路作用, 引脚上无保护套时, 引脚所跨过的导体之间的距离B≥0.5mm, 如图:RE: 保护套损坏或A>2.0mm时, 不能起到防止短路作用或引脚上无保护套时, 或引脚所跨过的导体之间距离B<0.5mm,如图:2.5元件间的距离PR: 在PCBA板上,两个或以上踝露金属元件间的距离要D≥2.0mm,如图:AC: 在PCBA板上, 两个或以上踝露金属元件的距离最小D≥1.6mm, 如图:RE: 在PCBA板上, 两个或以上踝露金属元件间的距离D<1.6mm, 如图:2.6元件的损伤PR: 元件表面无任何损伤,且标记清晰可见,如图:AC: 元件表面有轻微的抓、擦、刮伤等,但未露出元件基本面或有效面,如图:RE: 元件面受损并露出元件基本面或有效面积,如图:3. 插式元件焊锡点工艺及检查标准3.1单面板焊锡点单面板焊锡点对于插式元件有两种情形:a. 元件插入基板后需曲脚的焊锡点b. 元件插入基板后无需曲脚(直脚) 的焊锡点3.1.1标准焊锡点之外观特点A. 焊锡与铜片, 焊接面, 元件引脚完全融洽在一起, 且可明显看见元件脚B. 锡点表面光滑, 细腻, 发亮C. 焊锡将整个铜片焊接面完全覆盖, 焊锡与基板面角度Q<90°, 标准焊锡点如图示:3.1.2可接受标准A. 多锡焊接时由于焊锡量使用太多,使零件脚及铜片焊接面均被焊锡覆盖着,使整个锡点象球型,元件脚不能看到.AC: 焊锡点虽然肥大Q>90°,但焊锡与元件脚,铜片焊接面焊接良好,焊锡与元件脚,铜片焊接面完全融洽在一起,如图:RE: 焊锡与元件引脚, 铜片焊接状况差, 焊锡与元件脚/铜片焊接面不能完全融洽在一起, 且中间有极小的间隙, 元件引脚不能看到, 且Q>90°, 如图:B. 上锡不足(少锡)焊锡、元件引脚、铜片焊接面在上锡过程中,由于焊锡量太少,或焊锡温度及其它方面原因等造成的少锡.AC: 整个焊锡点, 焊锡覆盖铜片焊接面≥75%, 元件脚四周完全上锡,且上锡良好, 如图:RE: 整个焊锡点, 焊锡不能完全覆盖铜片焊接面<75%, 元件四周亦不能完全上锡, 锡与元件脚接面有极小的间隙, 如图:C. 锡尖AC: 焊锡点锡尖, 只要该锡尖的高度或长度h<1.0mm, 而焊锡本身与元件脚、铜片焊接面焊接良好, 如图:RE: 焊锡点锡尖高度或长度h≥1.0mm, 且焊锡与元件脚、铜片焊接面焊接不好, 如图:D. 气孔AC: 焊锡与元件脚、铜片焊接面焊接良好, 锡点面仅有一个气孔且气孔要小于该元件脚的一半, 或孔深<0.2mm, 且不是通孔, 只是焊锡点面上有气孔, 该气孔没有通到焊接面上, 如图:RE: 焊锡点有两个或以上气孔, 或气孔是通孔, 或气孔大于该元件脚半径, 如图:D. 起铜皮AC: 焊锡与元件脚、铜片焊接面焊接良好, 但铜皮有翻起h<0.1mm,且铜皮翻起小于整个Pad位的30%, 如图:RE: 焊锡与元件脚、铜片焊接面焊接一般, 但铜皮翻起h>0.1mm, 且翻起面占整个Pad位的的30%以上, 如图:E. 焊锡点高度对焊锡点元件脚在基板上的高度要求以保证焊接点有足够的机械强度AC: 元件脚在基板上高度0.5<h≤2.0mm, 焊锡与元件脚, 铜片焊接面焊接良好, 元件脚在焊点中可明显看见, 如图:RE: 元件脚在基板上的高度h<0.5mm或h>2.0mm, 造成整个锡点为少锡, 不露元件脚, 多锡或大锡点等不良现象, 如图:注:对用于固定零件之插脚如变压器或接线端子之插脚高度可接受2.5mm为限.3.1.3不可接受的缺陷焊锡点在基板焊锡点中有些不良锡点绝对不可接收, 现列举部分如下RE: ( 1 ) 冷焊(假焊/虚焊)如图:( 2 ) 焊桥(短路),锡桥,连焊,如图:( 3 ) 溅锡, 如图:( 4 ) 锡球, 锡渣, 脚碎, 如图:( 5 ) 豆腐渣, 焊锡点粗糙, 如图:( 6 ) 多层锡, 如图:( 7 )开孔(针孔),如图:3.2双面板焊锡点双面板焊锡点同单面板焊锡点相比有许多的不同点:a. 双面板之PAD位面积较小(即外露铜片焊接面积)b. 双面板每一个焊点PAD位都是镀铜通孔鉴于此两点, 双面板焊锡点在插元件焊接过程及维修过程就会有更高要求, 其焊锡点工艺检查标准就更高, 下面将分别详细讨论双面板之焊锡点收货标准3.2.1标准焊锡点之外观特点A. 焊锡与元件脚, 通孔铜片焊接面完全融洽在一起, 且焊点面元件脚明显可见.B. 元件面和焊点面的焊锡点表面光滑, 细腻, 发亮.C. 焊锡将两面的Pad位及通孔内面100%覆盖, 且锡点与板面角度Q<90°, 如图:3.2.2可接收标准A.多锡焊接时由于焊锡量过多, 使元件脚, 通孔, 铜片焊接面完全覆盖,不是使焊接时的两面元件脚焊点肥大, 焊锡过高AC: 焊锡点元件面引脚焊锡虽然过多, 但焊锡与元件脚, 通孔铜片焊接面两面均焊接良好, 且Q<90°, 如图:RE: 焊锡点元件面引脚肥大, 锡点面引脚锡点肥大, 不能看见元件脚且焊锡与元件脚, 铜片焊接面焊接不良, 如图:B. 上锡不良AC: 焊锡与元件脚, 通孔铜片焊接面焊接良好, 且焊接锡在通孔铜片内的上锡量高度h>75%·T (T: 基板厚度), 从焊点面看上锡程度大于覆盖元件脚四周(360°)铜片的270°, 或从元件面能清楚的看到通孔铜片中的焊锡, 如图:RE: 从焊点面看, 不能清晰的看到元件引脚和通孔铜片焊接面中的焊锡或在通孔铜片焊接面完全无焊锡或元件引脚到Pad位无焊锡或h<75%·T或上锡角度Q<270°(针对Solder Pad 360°而言), 如左图:C. 锡尖在焊接过程中由于焊锡温度过低或焊接时间过长等原因造成的锡尖AC: 焊锡点的锡尖高度或长度h<1.0mm, 而焊锡本身与元件引脚及通孔铜片焊接面焊接良好, Q<90°, 如图:RE: 焊锡点锡尖高度或长度h≥1.0mm, 且焊锡与元件引脚, 通孔铜片焊接面焊接不良, 如图:D. 气孔AC: 焊锡与元件脚, 铜片焊接面焊接良好, 锡点面仅有一个气孔且气孔要小于该元件脚的1/2, 且不是通孔(只是焊锡点表面有气孔, 未通到焊接面上), 如图:RE: 焊锡点上有两个或以上气孔, 或气孔是通孔, 或气孔大于该元件脚直径的1/2, 焊点面亦粗糙, 如图:E. 起铜皮AC: 焊锡点与元件脚, 通孔铜片焊接面焊接良好, 但铜皮翘起高度h<0.1mm, 翘起面积S<30%·F (F为整个焊盘的面积)RE: 焊锡与元件脚, 通孔铜片焊接面焊接质量一般, 但铜皮翘起h>0.1mm, 且翘起面积S>30%·F (F为整个焊盘的面积), 如图:F. 焊接点高度PR: 元件脚在焊锡点中明显可见, 引脚露出高度h=0.1mm, 且焊锡与元件脚, 通孔铜片焊接面焊接良好, 如图:AC: 元件脚露出基板的高度0.5mm<h≤2.0mm, 元件脚在焊锡点中可明显看见, 且焊锡与元件脚, 通孔铜片焊接面焊接良好. (但对于通孔铜片焊接面的双面PCB板, 基板厚度T>2.3mm, 则元件脚露出基板高度可接收0<h≤0.5mm), 如图:RE: 元件脚露出基板高度h<0.5mm或h>2.0mm (仅对于厚度T≤2.3mm 的双面板), 造成整个锡点为少锡, 不露元件脚, 多锡或大锡点等不良现象, 且焊接不良, 如图:3.2.3 不可接收的缺陷焊锡点:在双面板(镀铜通孔铜片焊接面)焊锡点中, 有些不良焊点绝对不可接收, 其不可接收程度完全同于单面板, 详细请参考3.1.3。
元器件成型工艺规范
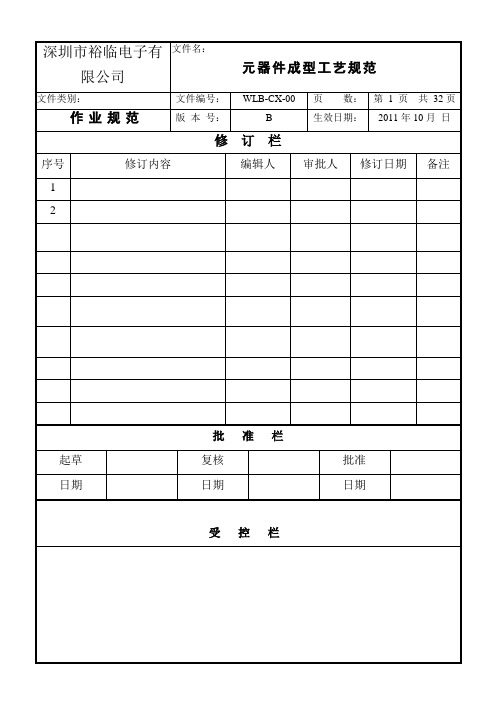
5.1.3.3 折弯角度ω折弯类型折弯角度ω(公差+3度),优选值变向折弯90度非变向折弯120度、135度或150度5.1.3.4 偏心距V偏心距是针对非变向折弯而言的参数,对偏心距不规定具体数值。
但必须要保证元器件在其丝印框内,且符合电气间隙与安规要求,同进引脚上无应力存在。
如果偏心距过小(主要针对功率管的引脚成型),我司的模具无法保证成型的偏心距。
给出一个通用的参考值:不小于1.5mm。
5.1.3.5 K值引脚的直径(D)或厚度(T)K值(优选值)D( T )≤0.8mm 2.5 mm0.8mm<D( T )<1.2mm 3.5 mmD( T )≥1.2mm 4.0 mm5.1.4 元器件的成型(主要根据公司的实际情况)5.1.4.1 元件的出脚(指插装后的元件伸出PCB部分的长度)控制在0.5 – 2.5 mm间。
因考虑到模具公差和波峰时的焊锡堆积和拉尖,同时为方便控制加工,将成型元件的出脚长度统一规定为2.0mm。
注意:如果客户对元件出脚有特殊要求,必须按客户要求进行元件成型加工。
如要求出脚为1.0mm,则贴板元件按:板厚+1.0mm控制,抬高元件按:H(抬高高度)+板厚+1.0mm控制;如要求出脚为1.5mm,则贴板元件按:板厚+1.5mm控制,抬高元件按:H(抬高高度)+板厚+1.5mm 控制。
5.1.4.2 具体元器件的成型要求5.1.4.2.1 对1W以下卧式插装的非功率电阻,要求贴板成型,成型尺寸如下图所示:L:电阻所对应的焊盘之孔距;H为电阻的本体的半径;X-Y≤±0.5mm;其它尺寸需满足5.1.3引脚折弯的要求。
5.1.4.2.2 对1W以下立式插装的非功率电阻,要求贴板插装,成型尺寸如下图所示:L:电阻所对应的焊盘之孔距;其它尺寸需满足5.1.3引脚折弯的要求。
5.1.4.2.3 对1W 及1W 以上卧式成型的功率电阻,我司均有要求供应商来料成型,有打K 和扁脚两种抬高方式。
电子元器件插件工艺标准规范标准

电子元器件插件工艺规范
(共 21 页,包括封面)
-*
文件修订记录
No. 修正后版本 修正人
修正内容概要
修正日期
1. 目的:
使手插件工作人员掌握基本的电子元件插件操作工艺;规范了手工插件工艺设计的基本原则、作业质量标准以及
作业者的基本操作方法、要求等内容。使符合手工插件工序的基本作业要求和质量要求.
1.极性零件组装极性错误(MA)。
1000
(极性反)
μF
6.3F
2.无法辨识零件文字标示(MA)。
+ 3.以上缺陷任何一个都不能接 收。
-*
6.2.4 立式电子零组件浮件
-*
6.2.5 机构零件浮件
-*
6.2.6 机构零件组装外观(1)
-*
6.2.6 机构零件组装外观(2)
6.2.7 零件脚折脚、未入孔、未出孔
列方向统一。(由左至右,或 由上至下)
允收状况(Accept Condition) 1.极性零件与多脚零件组装正确。 2.组装后,能辨识出零件的极性符 号。 3.所有零件按规格标准组装于正确
位置。 4.非极性零件组装位置正确,但文
字印刷的辨示排列方向未统一 (R1,R2)。
拒收状况(Reject Condition) 1.使用错误零件规格(错件)(MA)。 2.零件插错孔(MA)。 3. 极 性 零 件 组 装 极 性 错 误 (MA)( 极
-*
可接受: 保护套可起到防止短路作用, 引脚上无保护套时, 引脚所跨过的导体之间的距离 B≥0.5mm, 如图:
拒收: 保护套损坏或 A>2.0mm 时, 不能起到防止短路作用或引脚上无保护套时, 或引脚所跨过的导体之间 距离 B<0.5mm,如图:
剪脚操作规范
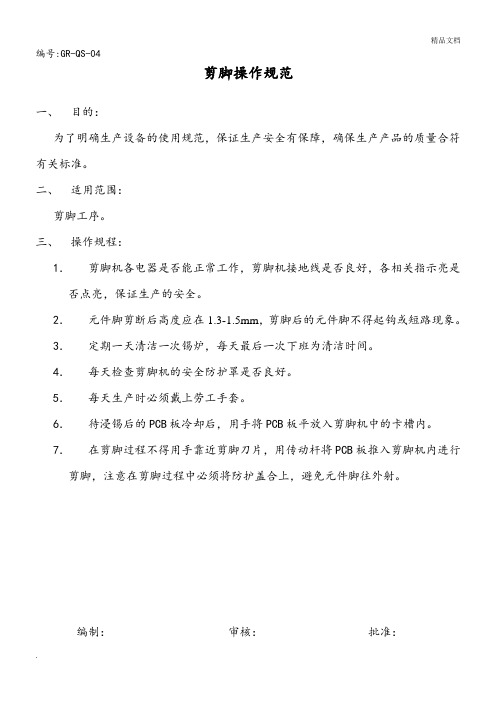
精品文档编号:GR-QS-04
剪脚操作规范
一、目的:
为了明确生产设备的使用规范,保证生产安全有保障,确保生产产品的质量合符有关标准。
二、适用范围:
剪脚工序。
三、操作规程:
1.剪脚机各电器是否能正常工作,剪脚机接地线是否良好,各相关指示亮是否点亮,保证生产的安全。
2.元件脚剪断后高度应在1.3-1.5mm,剪脚后的元件脚不得起钩或短路现象。
3.定期一天清洁一次锡炉,每天最后一次下班为清洁时间。
4.每天检查剪脚机的安全防护罩是否良好。
5.每天生产时必须戴上劳工手套。
6.待浸锡后的PCB板冷却后,用手将PCB板平放入剪脚机中的卡槽内。
7.在剪脚过程不得用手靠近剪脚刀片,用传动杆将PCB板推入剪脚机内进行剪脚,注意在剪脚过程中必须将防护盖合上,避免元件脚往外射。
编制:审核:批准:
.。
插件手工焊接剪脚
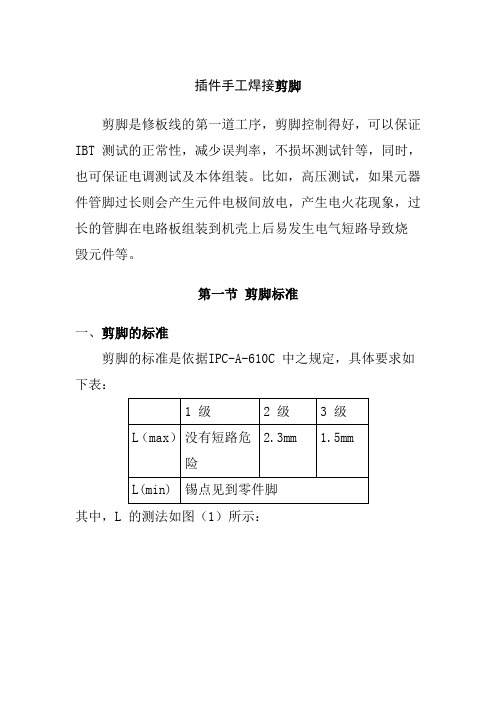
插件手工焊接剪脚剪脚是修板线的第一道工序,剪脚控制得好,可以保证IBT 测试的正常性,减少误判率,不损坏测试针等,同时,也可保证电调测试及本体组装。
比如,高压测试,如果元器件管脚过长则会产生元件电极间放电,产生电火花现象,过长的管脚在电路板组装到机壳上后易发生电气短路导致烧毁元件等。
第一节剪脚标准一、剪脚的标准剪脚的标准是依据IPC-A-610C 中之规定,具体要求如下表:1 级2 级3 级2.3mm 1.5mmL(max)没有短路危险L(min) 锡点见到零件脚其中,L 的测法如图(1)所示:图(1) L 的测量方法IPC 中将电子产品分成三个级别,分别为1 级、2 级、3 级。
级别越高,相应的要求也越高。
目前,我们部门遵循2 级标准,所以工艺中要求元件的管脚最长不得超过2.3mm,否则就要剪去多余的管脚。
二、剪脚元件举例在实际生产中,插排、IC 及机器整形的元件脚长一般不超过2.3mm,故不剪脚,经常要剪的主要是手工整形的异形元件,如竖插电阻,竖插二极管,部分三极管等。
因为这些元件从插件线流入波峰焊后会有所倾斜,导致过完波峰焊后,一边脚符合要求,而另一边经常达到3~5mm,超出2.3mm 有0.7~2.7mm 不等。
这种情况经常在多功能一体机 DAA 板、主板及DH9093 主板上出现,因为这些板竖插件较多,另外一种情况就是尺寸整得刚好的三极管插入基板,过完波峰焊后亦有所倾斜,造成其中某个管脚超过2.3mm。
这种情况在马兰士功放PM7000、PM8000 的M01 板上会经常出现。
所以对这些元件就必须剪脚,否则就影响到IBT的测试及本体组装。
★练习题1、试举例说明剪脚的好处。
2、剪脚标准的依据是什么?试叙述其关于剪脚长度的具体内容。
3、目前,我们工艺上要求剪脚的长度是多少?4、试举例哪些元件脚长可以不剪,而哪些元件的脚长要剪。
第二节剪脚工具剪脚的主要工具是斜口钳,当然,剪完管脚之后还要将剪断的残余管脚扫出印制板,因为刚过完波峰焊的印制板还有助焊剂的粘性,易将剪断的残余管脚吸附住,造成焊点之间不必要的短路,为了克服这一点,必须使用毛刷清除。
电子元器件插件工艺规范标准[详]
![电子元器件插件工艺规范标准[详]](https://img.taocdn.com/s3/m/546a9417a8956bec0975e3ec.png)
6.2元器件的插件检验标准6.2.1卧式零件插件的方向与极性+R1 C1Q R2D2 理想状况(Target Condition)1.零件正确组装于两锡垫中央;2.零件的文字印刷标示可辨识;3.非极性零件文字印刷的辨识排列方向统一。
(由左至右,或由上至下)+R1 C1Q R2D2 允收状况(Accept Condition)1.极性零件与多脚零件组装正确。
2.组装后,能辨识出零件的极性符号。
3.所有零件按规格标准组装于正确位置。
4.非极性零件组装位置正确,但文+C1 R2 拒收状况(Reject Condition)1.使用错误零件规格(错件)(MA)。
2.零件插错孔(MA)。
6.2.2立式零件组装的方向与极性6.2.3卧式电子零组件插装高度与倾斜1000μF + + + J233 ● 拒收状况(Reject Condition) 1.极性零件组装极性错误(MA)。
(极性反) 2.无法辨识零件文字标示(MA)。
3.以上缺陷任何一个都不能接收。
1000μF + + 10μ 16 ● 332J 允收状况(Accept Condition) 1.极性零件组装于正确位置。
2.可辨识出文字标示与极性。
6.2.4立式电子零组件浮件6.2.5机构零件浮件6.2.6机构零件组装外观(1)6.2.6机构零件组装外观(2)6.2.7零件脚折脚、未入孔、未出孔6.2.8零件脚与线路间距6.2.9元件本体斜度最佳: 元件本体与其在基板上两插孔位组成的连线或元件体在基板上的边框线完全平行,无斜度,如图: 可接受: 元件体与其在基板上两插孔位组成的连线或元件体在基板上的边框线斜度≤1.0mm,如图: 拒收: 元件体与其在基板上两插孔位组成的连线或元件体在基上的边框线斜度>1.0mm,如图:6.2.10元件引脚的紧度最佳: 元件引脚与元件体主轴之间夹角为0°(即引脚与元件主轴平行, 垂直于PCB板面), 如图:可接受: 元件引脚与元件体主轴袒闪角Q<15°,如图:拒收: 元件引脚与元件体主轴之间夹角Q>15°.6.2.11元件引脚的电气保护在PCBA板上有些元件要有特殊的电气保护,则通常使用胶套,管或热缩管来保护电路最佳: 元件引脚弯曲部分有保护套,垂直或水平部分如跨过导体需有保护套且保护套距离插孔之间距离A为1.0mm-2.0mm,如图:可接受: 保护套可起到防止短路作用, 引脚上无保护套时, 引脚所跨过的导体之间的距离B≥0.5mm, 如图:拒收: 保护套损坏或A>2.0mm时, 不能起到防止短路作用或引脚上无保护套时, 或引脚所跨过的导体之间距离B<0.5mm,如图:6.2.12元件间的距离最佳: 在PCBA板上,两个或以上踝露金属元件间的距离要D≥2.0mm,如图:可接受: 在PCBA板上, 两个或以上踝露金属元件的距离最小D≥1.6mm, 如图:拒收: 在PCBA板上, 两个或以上踝露金属元件间的距离D<1.6mm, 如图:6.3元件的损伤6.3.1元件本体损伤最佳: 元件表面无任何损伤,且标记清晰可见,如图:可接受: 元件表面有轻微的抓、擦、刮伤等,但未露出元件基本面或有效面,如图:拒收: 元件面受损并露出元件基本面或有效面积,如图:6.3.2元件引脚的损伤最佳: 元件引脚无任何损伤, 弯脚处光滑完好, 元件表面标记清晰可见, 如图:可接受: 元件引脚不规则弯曲或引脚露铜,但元件或部品引脚损伤程度小于该引脚直径的10%,如图:拒收: ( 1 )元件引脚受损大于元件引脚直径的10%,如图:( 2 )严重凹痕锯齿痕,导致元件脚缩小超过元件的10%,如图:6.3.3IC元件的损伤最佳: IC 元件无任何损伤, 如图:可接受: 元件表面受损, 但未露密封的玻璃, 如图:拒收: 元件表面受损并露出密封的玻璃, 如图:6.3.4轴向元件损伤最佳: 元件表面无任何损伤,如图:可接受: 元件表面无明显损伤,元件金属成份无暴露,如图:拒收:( 1 )元件面有明显损伤且绝缘封装破裂露出金属成份或元件严重变形,如图:( 2 ) 对于玻璃封装元件,不允许出现小块玻璃脱落或损伤.6.4元件应力评估,进行插件作业时,需参照以下表格对个各元件易产生应力部位进行重点检查和防护。
电子元器件插件工艺规范标准
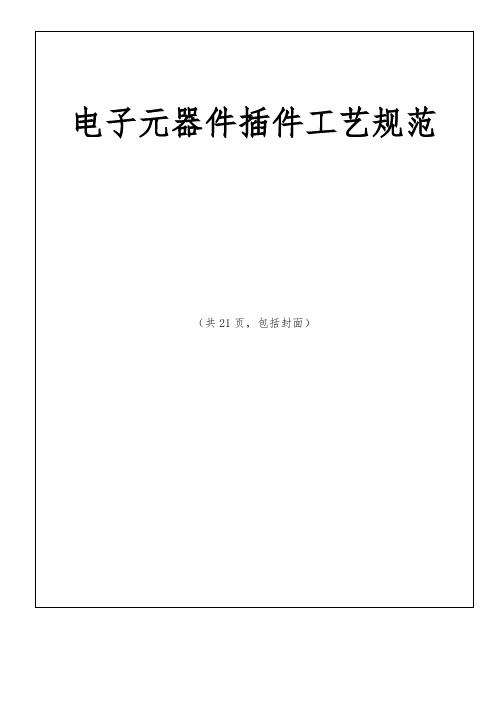
6.2.2立式零件组装的方向与极性6.2.3卧式电子零组件插装高度与倾斜 1000μF + + + J233 ● 拒收状况(Reject Condition) 1.极性零件组装极性错误 (极性反) 。
2.无法辨识零件文字标示。
3.以上缺陷任何一个都不能接收。
1000μF + + 10μ 16 ● 332J 允收状况(Accept Condition) 1.极性零件组装于正确位置。
2.可辨识出文字标示与极性。
6.2.4立式电子零组件浮件6.2.5机构零件浮件6.2.6机构零件组装外观(1)6.2.6机构零件组装外观(2)6.2.7零件脚折脚、未入孔、未出孔6.2.8零件脚与线路间距6.2.9元件本体斜度最佳: 元件本体与其在基板上两插孔位组成的连线或元件体在基板上的边框线完全平行,无斜度,如图: 可接受: 元件体与其在基板上两插孔位组成的连线或元件体在基板上的边框线斜度≤1.0mm,如图: 拒收: 元件体与其在基板上两插孔位组成的连线或元件体在基上的边框线斜度>1.0mm,如图:6.2.10元件引脚的紧张度最佳: 元件引脚与元件体主轴之间夹角为0°(即引脚与元件主轴平行, 垂直于PCB板面), 如图:可接受: 元件引脚与元件体主轴袒闪角Q<15°,如图:拒收: 元件引脚与元件体主轴之间夹角Q>15°.6.2.11元件引脚的电气保护在PCBA板上有些元件要有特殊的电气保护,则通常使用胶套,管或热缩管来保护电路最佳: 元件引脚弯曲部分有保护套,垂直或水平部分如跨过导体需有保护套且保护套距离插孔之间距离A为1.0mm-2.0mm,如图:可接受: 保护套可起到防止短路作用, 引脚上无保护套时, 引脚所跨过的导体之间的距离B≥0.5mm, 如图:拒收: 保护套损坏或A>2.0mm时, 不能起到防止短路作用或引脚上无保护套时, 或引脚所跨过的导体之间距离B<0.5mm,如图:6.2.12元件间的距离最佳: 在PCBA板上,两个或以上踝露金属元件间的距离要D≥2.0mm,如图:可接受: 在PCBA板上, 两个或以上踝露金属元件的距离最小D≥1.6mm, 如图:拒收: 在PCBA板上, 两个或以上踝露金属元件间的距离D<1.6mm, 如图:6.3元件的损伤6.3.1元件本体损伤最佳: 元件表面无任何损伤,且标记清晰可见,如图:可接受: 元件表面有轻微的抓、擦、刮伤等,但未露出元件基本面或有效面,如图:拒收: 元件面受损并露出元件基本面或有效面积,如图:6.3.2元件引脚的损伤最佳: 元件引脚无任何损伤, 弯脚处光滑完好, 元件表面标记清晰可见, 如图:可接受: 元件引脚不规则弯曲或引脚露铜,但元件或部品引脚损伤程度小于该引脚直径的10%,如图:拒收: ( 1 )元件引脚受损大于元件引脚直径的10%,如图:( 2 )严重凹痕锯齿痕,导致元件脚缩小超过元件的10%,如图:6.3.3 IC元件的损伤最佳: IC 元件无任何损伤, 如图:可接受: 元件表面受损, 但未露密封的玻璃, 如图:拒收: 元件表面受损并露出密封的玻璃, 如图:6.3.4轴向元件损伤最佳: 元件表面无任何损伤,如图:可接受: 元件表面无明显损伤,元件金属成份无暴露,如图:拒收:( 1 )元件面有明显损伤且绝缘封装破裂露出金属成份或元件严重变形,如图:( 2 ) 对于玻璃封装元件,不允许出现小块玻璃脱落或损伤.6.4元件应力评估,进行插件作业时,需参照以下表格对个各元件易产生应力部位进行重点检查和防护。
元件成型的规范要求
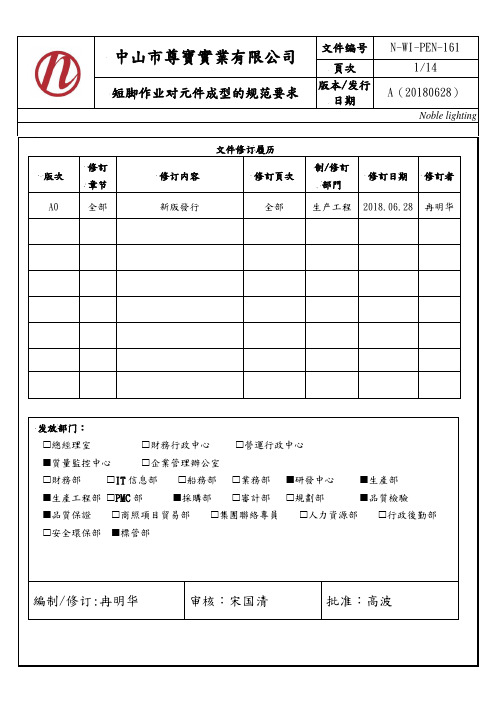
5.4未注公差均按±0.5mm。
5.5成型时不允许从元器件引线的根部直接弯折。规定弯折处距离元器件主体≥1.0mm。
5.6成型后的引线
5.6.1不得有扭曲现象,引线上不得有明显压坏和其他伤痕。
5.6.2折弯处的痕迹规定不超过0.25d的凹陷(d为引线直径)。
文件修订履历
版次
修訂章节
修订内容
修訂頁次
制/修訂部門
修訂日期
修訂者
A0
全部
新版發行
全部
生产工程
2018.06.28
冉明华
发放部门:
總經理室財務行政中心營運行政中心
質量監控中心企業管理辦公室
財務部IT信息部船務部業務部研發中心生產部
生產工程部PMC部採購部審計部規劃部品質檢驗
品質保證商照項目貿易部集團聯絡專員人力資源部行政後勤部安全環保部標管部
适用元器件
径向型(电容、发光二极管、三极管、红外接收器)
应用环境
元器件表面温升≤40℃
元器件的外形尺寸
备注
*为成型三极管类、无极性电容字符面或红外接收器类的工作面定向
6.6 ZR型
ZR型
成型代号
电容类CZR-s×h
径向二极管类VZR-s×h
三极管类VZR-s×h
电感类LZR-s×h
标定成型跨距/参数(s)
編制/修订:冉明华
审核:宋国清
批准:高波
1.0目的
规范元器件来料成型操作的方法和流程,消除元器件成型时应力造成的损伤,提高产品可靠性,提高产品质量,防止出现批次质量事故。
2.0适用范围
本规范规定了元器件引线成型生产中人、机、料、法、环的工艺要求和质量检测中的管理要求、质量控制方法、元器件引线成型方式和技术要求。本规范适用于印制板厚度为1.0~1.6mm,用手工插件的元器件(包括电阻器、电容器、电感器、二极管、三极管、集成电路、振荡器、保险丝管保险管)引线成型。适用于本公司所有产品,包括内、外发产品。
剪腿通用工艺精选全文

可编辑修改精选全文完整版
1. 元器件管脚剪腿标准
对于焊接面的元器件管脚较高的,需要用剪线钳剪腿。
1.1 如果元器件的管脚直径φ≤0.8 mm,则剪腿后,其管脚露出焊点的高度为
0.5~1.5mm;
1.2 如果元器件的管脚直径1mm≥φ﹥0.8mm,,则剪腿后,其管脚露出焊点的高度为0.5mm~
2.0 mm。
1.3 如果元器件的管脚直径φ≥1mm, 则剪腿后,其管脚露出焊点的高度为1.5mm~
2.5 mm。
1.4 集成电路、接插座的管脚一般不需要剪腿。
图1
注意:1、在剪腿时,应注意不能破坏焊点;
2、在剪腿时,剪线钳应基本平行于PCB板进行剪腿,避免剪线钳倾
斜使用,造成剪线钳尖划伤板子。
3、在剪腿时,如果一次没能剪断,应用剪线钳再剪一次,严禁用剪
线钳拽拉元件腿,以免损伤焊盘。
图2
破裂的痕迹。
- 1、下载文档前请自行甄别文档内容的完整性,平台不提供额外的编辑、内容补充、找答案等附加服务。
- 2、"仅部分预览"的文档,不可在线预览部分如存在完整性等问题,可反馈申请退款(可完整预览的文档不适用该条件!)。
- 3、如文档侵犯您的权益,请联系客服反馈,我们会尽快为您处理(人工客服工作时间:9:00-18:30)。
1、目的:规范元件成型方式与尺寸,使之标准化作业。
2、适用范围:适用于茂硕科技元件成型工艺文件;如果客户有其它或高于此规范的特别要求,一律按客户要求执行。
3、职责:3.1 工艺拟制者负责按本规范操作。
3.2 工艺审核人员负责对规范进行对工艺的全面审核。
3.3工程部经理负责本规范在工艺拟制者中有效执行。
4、程序内容:4.1操作规范:4.1.1 收集和确认客户最新资料,文件(如:ENP的ECO,BOM线路图,元件位置图等),产品样板,空PCB板,元器件材料。
4.1.2 对客户资料,文件进行研究,并用通俗易懂的语言将其描述清楚。
4.1.3 对关键性的加工事项和图形示意图,材料加工要求需要进行仔细的研究和确认。
4.1.4 前加工易出错的工序要求特别注意,并加注到生产工艺中。
4.1.5 在成形过程中,除特殊情况下,手工持取元器件一般是持取元器件本体,禁止持取元器件引线,以防止污染元器件引线,从而引起焊接不良。
4.1.6 对于电阻、二极体、电容等非功率半导体元器件,其本体一般没有金属散热器,可以直接持取本体;对于功率半导体元器件如IC,手工持取本体时,禁止触摸其散热面,以免影响散热材料的涂敷或装配。
4.2 工艺制作软件统一用EXCEL2000。
4.3 工艺规范依据主要参照IPC-A-610C标准,元件两引脚间对应于PCB板两焊盘间(W),在PCB板间焊点免除零件脚长即元件焊接后深处的高度为L(mm),如各项目对于元件管脚伸出长度由特别要求时,以客户的要求为准。
元件成型方式大致分为立式成型和卧式成型两种,元件成型管脚长度分为三种:(1).元件成型管脚长度=元件管脚伸出长度(L)+PCB板厚(T)(2).元件成型管脚长度=元件管脚伸出长度(L)+PCB板厚(T)+抬高于PCB板面高度(H)(3).元件成型管脚长度=元件管脚伸出长度(L)+PCB板厚(T)+抬高于PCB板面高度(H)+元件本体高度(b)4.4 元件成型尺寸标注和要求,必须要充分考虑到生产线操作的可行性,另外对于元件本体损伤的可能性也加以充分考虑,确保加工出来的元件符合IPC-A-610C的标准和客户的要求。
4.4.1 对于所有引线成型元件(立式和卧式)成型都适用,又哦成型的安全距离和空间:a(图中用L表示)元件直径(D)或厚度(T),注意以下要求:当元件直径(D)或厚度(T)≤0.8mm时,内曲线半径(R)为:R=1D当元件直径(D)或厚度(T)0.8mm< D或T<1.2mm时,内曲线半径(R)为:R=1.5D 当元件直径(D)或厚度(T)≥1.2mm时,内曲线半径(R)为:R=2D当设定成型尺寸时,必须要充分考虑上述的成型尺寸要求,避免元件脚变形或是元件本体开裂损伤,对于手工加工或是极其加工安全尺寸要求也不会一致,需要根据实际情况而定。
4.2.2 额定功率<1W的普通电阻,要求电阻本体平贴于PCB板面,电阻两引脚间距对应于PCB板两焊间距(L),PCB板厚(T),卧式成型标准。
成型尺寸:项目允收范围A 85°< a < 95°L1、L2 L1、L2为1.0mm以上L 依插装位置PCB孔距元件成型管脚长度=元件管脚伸出长度(L)+PCB板厚(T)+抬高于PCB板面高度(H)成型方式:手工或机器整形(如下图)手工成型时注意手只能持住元件引脚弯折,而非本体机器成型4.4.3对额定功率≥1W的普通电阻,或额定功率<1W的立式成型的普通电阻,要本体底部高于PCB板面1-6mm(h),电阻两引脚间距对应于PCB板两焊盘间距(L),PCB板厚(T)。
成型尺寸:项目允收范围X 1.0mm < x<3.0mm(手工)4.0mm <x<5.0mm(机器)A 25°< a <35°L 依插装位置PCB孔距元件成型管脚长度=元件管脚伸出长度(L)+PCB板厚(T)+抬高于PCB板面高度(H)成型方式:1、手工整形(如下图)手工成型2、机器成形机器成型4.4.4 对于水泥电阻,要求电阻本体的底部抬高于PCB板面2.55~3.5mm,电阻两引脚间对应于PCB板两焊盘间距(L),PCB板厚(T)。
成型尺寸:项目允收范围X X>2mmL 依插装位置PCB孔距元件成型管脚长度=元件管脚伸出长度(L)+PCB板厚(T)+抬高于PCB板面高度(H)4.4.5 对于压敏电阻、热敏电阻,对于类似瓷介电容外形的电阻元件,要求成型从距离管脚包皮处1-2MM开始成型,电阻和电容两引脚间距对应于PCB板焊盘间距(L),PCB板厚(T)。
成型尺寸:项目允收范围X 1mm < x <2mmL 依插装位置PCB孔距元件成型管脚长度=元件管脚伸出长度(L)+PCB板厚(T)+抬高于PCB板面高度(H)4.4.6 对于额定功率<1W的稳压二极管,或者是额定电流<1A的其它各种二极管,二极管两引脚对应于PCB板两焊盘间距(L),PCB板厚(T)。
成型尺寸:项目允收范围A 85°< a < 95°L1、L2 1.0mm < L1、L2< 3mmL 依插装位置PCB孔距元件成型管脚长度=元件管脚伸出长度(L)+PCB板厚(T)+抬高于PCB板面高度(H)4.4.7 对于额定功率≥W的稳压二极管,或者是额定电流≥A的其它各种二极管,或者额定功率<1W的稳压二极管和额定电流<1A的其它各种二极管,要求立式成型,要求二极管本体的底部抬高于PCB板面1-4mm,二极管两引脚间距对应于PCB板两焊盘间距(L),PCB板厚(T)。
成型尺寸:项目允收范围X 2.0mm < x < 3.0mm(手工) 4.0mm < x < 5.0mmL 依插装位置PCB孔距元件成型管脚长度=元件管脚伸出长度(L)+PCB板厚(T)+抬高于PCB板面高度(H)4.4.8 发光二极管需根据产品类型,LED封装形式来定,详细内容见抬高和特殊要求汇总表LED两引脚间距对应于PCB板两焊盘间距。
4.4.9 独石电容、瓷片电容、金膜电容、钽电容、铝电解电容均要求插装到底,平贴PCB 板,(卧式安装例外),元件两引脚间距对应于PCB板两焊盘间距。
4.4.10 小功率三机关成型时要求三极管本体底部抬高于PCB板元件面3-4mm,三极管引脚间距对应于PCB板两焊盘间距。
4.4.11 自带散热器的大功率三极管、电压调整器为立式安装时,要求将元件引脚细的一段完全插入焊盘通孔内。
4.4.12 晶体为立式安装时,要求晶体外壳不能触及PCB板上非接地的铜箔、走线等,否则需加绝缘垫片隔离。
晶体为卧式安装时,需加镀铜线进行固定(补焊工段将晶体外壳同镀锡线焊接在一起,补焊时应避开晶体外壳上的字符)。
4.4.13 散热器上固定大功率元件时,要求元件同散热器之间有薄薄的一层导热胶,用螺钉+弹垫+螺母将元件和散热器进行紧固。
元件同散热器装配要求端正,不许有歪斜现象。
4.4.14 插件式的保险管、保险管座需要在插件前进行组装。
将一保险套在两保险管座中,两保险管座尽量保持在同一方向、同一平面上,保险管上有字符的一面朝上。
4.4.15 对于其它需要对引脚长度进行成型加工的元件,元件两引脚间距对应于PCB板间两焊距。
前加工元件成型抬高和特殊要求汇总表:元件大类型元件小类型及规格描述元件本体抬高于PCB板尺寸或其它要求(mm)备注电阻额定功率<1W的普通电阻平贴于PCB板面1-6mm 额定功率≥1W的普通电阻抬高于PCB板面1-6mm水泥电阻抬高于PCB板面2.5-3.5mm压敏电阻、热敏电阻等外形类似瓷介电容的电阻元件有安全距离,要求从距离管脚皮处1-2mm处开始成5、前加工工艺的注意事项要求:5.1 应做互检要求,(一般是检查材料有无错料、混料、丝印不符、元件破损不良)。
5.2 明确加工先后顺序,首先做什么,最后干什么,逻辑思维强,使操作者能在最短的时间内完成,并且要保证品质要求。
必须注明元件丝印或外观图,注意元件的尺寸范围与误差范围的区别,如0.3-4.0mm与3.5±0.5mm区别。
必须使用后者中心值加误差范围的方式来表述元件的尺寸工艺品,用±来表示(如3.5±0.5mm),保证加工的一致性。
5.3 对于同一种元件多个配量且有不同种成型方式,加工要求必须在一个工位中完成,并且注明不同成形示意图和零件位置。
5.4 元件外观相同而型号不同的元件要分开加工,并自检材料型号与丝印是否正确;对无极性元件,要按照(IPC-A-610标准)字符朝上,或按PCB板丝印方向加工。
5.5 元件成型必须考虑PCB板的厚度,例要求插机后的管脚长为1.5±0.5mm,如果工艺的剪脚尺寸要求为3.5±0.5mm,而实际的PCB板厚度为1.5mm插机后的管脚长就可能为2.5mm。
生产线需重新剪脚。
元件加工要一步到位,尽可能不再有加工工位(如:剪脚工位)。
5.6 在制作工艺过程中,如有材料的两管脚间距与PCB插件位置孔的间距不一致,必须找工程师确认,是否对此材料进行加工。
无特殊说明的电解电容、IC、变压器等零件脚标准件,其他的零件在前加工工段都有跨距要求。
5.7 IC管脚易损坏变形的,加工后应使用原包装或防护包装。
5.8 保险管座在前加工和插机工艺中方向性都写有,但对于保险管或是保险管与保险管座组件则方向性为无。
5.9 首次使用的成形工具,需工艺与品保确认后方可使用;已经使用的成形工具,再次使用前需校验或调校,满足成形尺寸参数后方可使用;成形工具在使用一定时间或成形一定数量后,必须按照工装使用说明需校验或调校,满足成形尺寸参数后方可使用。