生产效率、平衡率、标准产能计算方法
生产线平衡

生产线平衡率的计算方法
平衡率是评价一条产线的重要指标,平衡率高就表示在同等 条件下平衡损失就少,也就是说平衡率高的产线人均产能就 高。
目的:通过平衡生产线提高生产效率同时使生产现场更 加容易理解“一个流”的必要性及对于真正实现“OPF”进 而导入“cell production”的重要意义。
平衡生产线的意义
游戏时间
平衡生产线的意义
通过Line balancing我们可以达到以下几个目的:
有效减少工时损失进而提高作业员及设备工装的工作效率; 减少产品的C/T和pitch time,最终导致Takt time 的减少,提高productivity. 提高OEE & OME. 减少WIP,更容易真正实现“OPF”。 在Line balancing 基础上,实现单元生产,提高了生产对柔性化市场的应变能 力。
Line balance rate = ∑Standard time/(bottleneck time*person qty) = ∑ Standard time/(Pitch time*person qty)
Line imbalance rate =1-Line balance rate
Remark: Pitch time 是指生产线每产出一个batch产品所消耗 的时间,这里我们定义batch size 为1pcs, 所以pitch time=bottleneck time, 理想情况下pitch time=Takt time.
1.不同产品的特性差异
产能分析与计算(本文)

台湾健峰企管集团
八.产能分析
1.同机台不同工作的产能分析 2.同机台不同产品的产能分析 3.生产线的产能分析 (1)加工线产能 (2)装配线产能 4.混合方式组成的生产系统产能分析方法
2016/5/30
21
台湾健峰企管集团
(1)同机台不同工作的产能分析
2016/5/30
22
有效产能=计划产能-因故障及停机所造成标准工时的损失
2016/5/30 13
台湾健峰企管集团
四.产能效用与效率
1.产能利用率(效用)=实际产能÷ 设计产能
产能利用率系衡量全公司产能的依据,这是企业应注意的 产能衡量标准。产能利用率低代表企业机器设备闲置。
2.产能效率 = 实际产能÷ 计划产能
有效产能是企业自行订定,当低估有效产能时,则会高估 产能效率,所以产能效率只能做局部产能衡量的标准。
2016/5/30
25
台湾健峰企管集团
2016/5/30
26
台湾健峰企管集团
2016/5/30
27
28
台湾健峰企管集团
2016/5/30
29
台湾健峰企管集团
台湾健峰企管集团
台湾健峰企管集团
台湾健峰企管集团
台湾健峰企管集团
2016/5/30 9
台湾健峰企管集团
(3)协力厂是厂内生产线的延伸,因此协力厂是厂内产能的 延伸。所以如何建立一个能配合母厂产能的协力体系, 并有效掌握进料的交期与质量,是确保整体生产能力的 基本动作。 (4)生产周期时间 系指从生产订单被下达到工厂那时刻起,一直到完成订 单为止,在工厂实际所花费的时间。生产周期时间是影 响产能计划的因素之一,对现有产能的控制是相当重要 的。所以应对各制程所需的时间予以标准化,并要求各 制程确实遵守。
精益生产各绩效指标计算公式汇总ppt课件
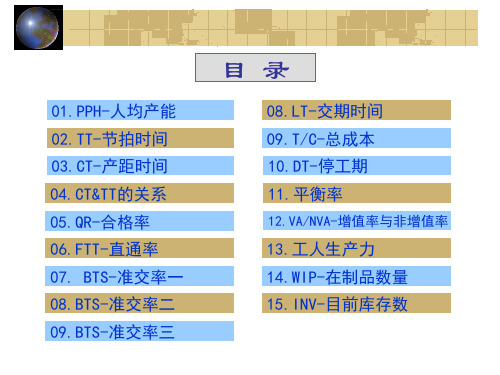
X 100%
制造周期(Manufacturing cycle time)
非增值比率计算方式:
非增值率= 1 - 增值率
在整堂课的教学中,刘教师总是让学 生带着 问题来 学习, 而问题 的设置 具有一 定的梯 度,由 浅入深 ,所提 出的问 题也很 明确
Labor Productivity -- 工人生產力
T/T
&
C/T
的聯系
如果Takt time(节拍時間)不等於Cycle Time (产距时 间),則流程存在不平衡问题。 當T/T 等于C/T 时,表示沒有生产过剩,且員工效率刚好 满足客戶需求
Process Time 流程時間= Cycle time 產距時間 x 操作員人數 Lead Time 流程週期 = Process Time 流程時間 + (在制品數 x 產距時間)
注: 材料成本:适用的所有材料 非材料成本:勞动力+企业一般管理費用+C品鞋+消費者反饋
在整堂课的教学中,刘教师总是让学 生带着 问题来 学习, 而问题 的设置 具有一 定的梯 度,由 浅入深 ,所提 出的问 题也很 明确
DT --- down time 停工期
停工期指的是任何未计划的生产线或流程停顿。原因包括:材 料短缺,生产 线饱和,机器故障,质量问题。
= 0.62 = 62%
底部(鞋材)FTT: = 合格率(大底)x合格率(PU) x合格率(PH) 例:= 0.98 x 0.89 x 0.90
= 0.78 = 78%
在整堂课的教学中,刘教师总是让学 生带着 问题来 学习, 而问题 的设置 具有一 定的梯 度,由 浅入深 ,所提 出的问 题也很 明确
INV---Inventory 目前库存数
什么是生产效率

1.生产效率的概念
2.生产效率的计算
3. 生产效率的改善
4. 改善分组演练
5. 演练结果点评
2.1:生产效率的计算: 2.1.2:设备稼动率的计算公式:
2.1.2.1:设备稼动率=时间稼动率*性能稼动率*一次良品率;
2.1.2.2:时间稼动率=实际开机时间/计划开机时间;
2.1.2.3:性能稼动率=实际产能/标准产能;
5. 演练结果点评
3.0:生产效率的改善: 3.1:物流规划与平面布具的改善; 3.2:异常工时的降低; 3.3:生产线平衡的改善; 3.4:瓶颈突破与现场改善提案;
1.生产效率的概念
2.生产效率的计算
3. 生产效率的改善
4. 改善分组演练
5. 演练结果点评
1.0:生产效率的概念:
1.4:生产效率的导向性: 1.4.1:生产效率既是一个考核指标,更是一个改善指标,纯粹 追求合理性,会使生产效率改善失去空间和方向; 1.4.2:生产效率的核心是标准工时,标准工时是一个与时俱 进的科学管理工具,并不是约束生产效率改善的镣铐, 需要用运动的概念而不是用静止的概念来看待标准工 时; 1.4.3:生产效率和标准工时是企业管理的基础工作,但不 是单纯由基层人员去做的工作,生产效率是一个综 合指标与企业任何人都有关系;
1.生产效率的概念
2.生产效率的计算
3. 生产效率的改善
4. 改善分组演练
5. 演练结果点评
2.1:生产效率的计算:
2.1.3:生产效率的计算中无效工时的处理:
2.1.3.1:无效动作与无效工时; 2.1.3.2:课级单位异常工时; 2.1.3.3:部级单位异常工时; 2.1.3.4:厂级单位异常工时; 2.1.3.5:公司级单位异常工时;
生产线平衡分析LOB技术

精品课件
生产线平衡分析
IE TEAM
精品课件
课程目录
一﹑生产线平衡定义与目的 二﹑生产线平衡的常见概念 三﹑生产线平衡的分析改善
2
精品课件
一﹑生产线平衡定义与目的
生产线平衡定义: 工程流动间或工序流动间负荷之差
距最小﹐流动顺畅﹐减少因时间差所造成的 等待或滯留現象。
21 25
每生产一个产品就有33秒损失 一个小时就会堆积几十个产品
1、5M方法的改善 2、作业方法的改善
19
三﹑生产线平衡的分精析品课件改善
1、5M方法的改善:
(5M:人员,机器设备,物料,作业方法,环境)
减少耗时最长工序作业时间的方法有: 人员(Man):调换作业者;增加作业者;多能工训练; 新手避免工作负荷过重,利用作业员熟练程度的 差异性,平衡作业流程.
机器设备(Machine):利用或改良工具、机器;人机 比合理配置;人机同步作业;提高自动半自动化水平; 人机工程分析,提高机械效率.
8
精品课件
二﹑生产线平衡的常见概念
3.生产线平衡率
线平衡率:SSRSSrSSR RSrrSR t iirt1i t0i1% 010% 00% 0
t各工站工时之和÷(S瓶颈工站工时×R工站总数)×100%
例:各工站之和:500秒
瓶颈工時*工站总数= 10×55 =550秒
线平衡率: 500÷550×100%=91% 平衡损失:作业人员之间由于作业量的不公平导致的作
21
三﹑生产线平衡的分精析品课件改善
2、作业方法的改善:
取消不必要的动作; 合并微小的动作; 重排作业工序或动作;简化复杂的动作.
22
三﹑生产线平衡的分精析品课件改善
生产线平衡率
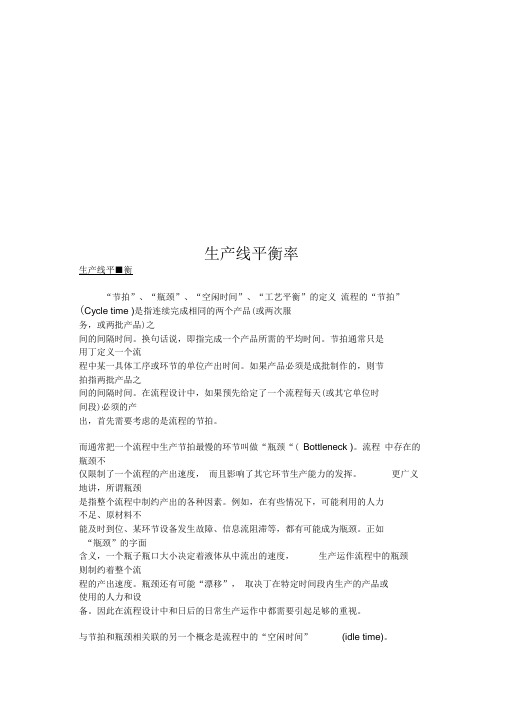
生产线平衡率生产线平■衡“节拍”、“瓶颈”、“空闲时间”、“工艺平衡”的定义流程的“节拍” (Cycle time )是指连续完成相同的两个产品(或两次服务,或两批产品)之间的间隔时间。
换句话说,即指完成一个产品所需的平均时间。
节拍通常只是用丁定义一个流程中某一具体工序或环节的单位产出时间。
如果产品必须是成批制作的,则节拍指两批产品之间的间隔时间。
在流程设计中,如果预先给定了一个流程每天(或其它单位时间段)必须的产出,首先需要考虑的是流程的节拍。
而通常把一个流程中生产节拍最慢的环节叫做“瓶颈“( Bottleneck )。
流程中存在的瓶颈不仅限制了一个流程的产出速度,而且影响了其它环节生产能力的发挥。
更广义地讲,所谓瓶颈是指整个流程中制约产出的各种因素。
例如,在有些情况下,可能利用的人力不足、原材料不能及时到位、某环节设备发生故障、信息流阻滞等,都有可能成为瓶颈。
正如“瓶颈”的字面含义,一个瓶子瓶口大小决定着液体从中流出的速度,生产运作流程中的瓶颈则制约着整个流程的产出速度。
瓶颈还有可能“漂移”,取决丁在特定时间段内生产的产品或使用的人力和设备。
因此在流程设计中和日后的日常生产运作中都需要引起足够的重视。
与节拍和瓶颈相关联的另一个概念是流程中的“空闲时间”(idle time)。
空闲时间是指工作时间内没有执行有效工作任务的那段时间,可以指设备或人的时间。
当一个流程中各个工序的节拍不一致时,瓶颈工序以外的其它工序就会产生空闲时间。
这就需要对生产工艺进行平衡。
制造业的生产线多半是在进行了细分之后的多工序流水化连续作业生产线,此时由丁分工作业,简化了作业难度,使作业熟练度容易提高,从而提高了作业效率。
然而经过了这样的作业细分化之后,各工序的作业时间在理论上,现实上都不能完全相同,这就势必存在工序问节拍不一致出现瓶颈的现象。
除了造成的无谓的工时损失外,还造成大量的工序堆积即存滞品发生,严重的还会造成生产的中止。
生产效率、平衡率、标准产能计算方法
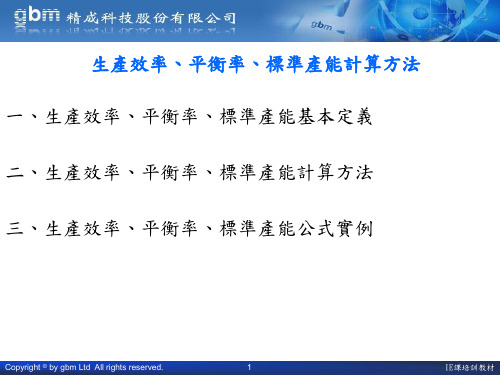
Copyright © by gbm Ltd All rights reserved.
3
IE課培訓Leabharlann 材二、生產效率、平衡率、標準產能計算方法
1.生產效率計算方法: 生產效率=有效工時實際產能/有效工時標準產能*100% 2.平衡率計算方法: 平衡率=各工序作業時間總和/(瓶頸時間*作業總人數)*100%
Copyright © by gbm Ltd All rights reserved.
5
IE課培訓教材
2.DIP 、TEST、Packing標準產能的計算實例 • 例如:LT-2AA7機種 1>. 裁板+插件*2:12S 2>. 投板+插件*4:14S 3>. 插件*6:15S 4>. 插件*2+中檢:14S 5>. 取治具+折板邊:13S 6>. 補焊:13.5S 7>. 刷板:12.5S 8>. 鎖鐵片*4:14S
?產線每小時實際生產?為210pcs那此段生產效?21022510093通過以上可以看出此段的站位較多所以要提高生產效?平?通過以上可以看出此段的站位較多所以要提高生產效?平衡?就必須使每個站位負荷較均勻就是?產線要平衡這樣才能使效?發揮到最高
生產效率、平衡率、標準產能計算方法 一、生產效率、平衡率、標準產能基本定義
3.標準產能計算方法: SMT標準產能=3600/瓶頸時間(Sec)*連片數 DIP/TEST/PACKING標準產能=3600/瓶頸時間(Sec)
Copyright © by gbm Ltd All rights reserved. 4 IE課培訓教材
三、生產效率、平衡率、標準產能公式實例
1.SMT標準產能的計算 • 例如:LT-2AA7機種(2連片) 1>.SMT機型:FX1R*3+KE2060RL*1+KE2080RL*1 2>.各機台貼片時間:45S 43S 46S 52S 48S • 瓶頸時間為52S,每小時標準產能為3600/52*2=138PCS
管理培训教材1——标准工时-产能-平衡率篇
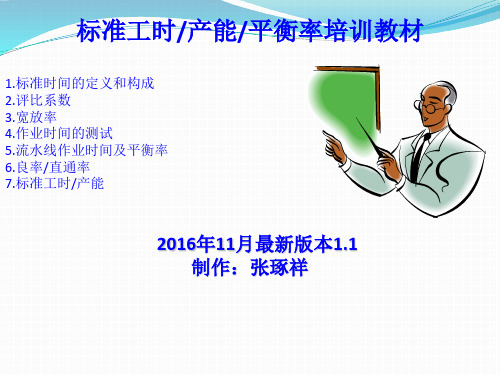
作业时间的测试
观测准备 • 观测次数为最好是可观测10 次 ( 至少 3 次 ); • 备观测板、铅笔、秒表、计算器等。
观测时的要点 • 确认作业者状态及内容是否正常;( 熟练度/努力度 作业条件/一致性) • 测试后要把工序 & 时间记录下来; • 除去异常数据后 ( 去头去尾),取平均值作为改善研 的依据。
标准产能
标准产能= ( 3600 / CT max ) X 标准上班工时 X 直通率 = ( 3600 / 69 ) X 10.5 X 98% = 537 sets
537 台 / 5 人 = 107.4 台
演练题
如何改善工时损失? 提升人均产出
1号工站 CT1=25 s
2 号工站
3号工站 CT3=60 s
1号工站 CT1=25 s
2 号工站
3号工站 CT3=60 s
4号工站 98% CT4=30 s
5号工站 CT5=20 s
CT2=25 s
标准工时= 作业工时 X (1+宽放率 ( 15% )) 28.75 , 28.75 , 69 , 34.5 , 23 瓶颈时间 = Max ( CT1 , CT2 , CT3 , CT4 , CT5 )= 69 sec 作业总时间 = CT1+CT2+…… +CT5 = 184 sec 标准作业工时= CT max X 工站数 = 69 X 5 = 345 sec 平衡率 =作业总时间 / 标准作业工时 = 184 / 345 = 53%
工站 作業時間 寬放率 標準工時 CT 總和 Ctmax X 工站 平衡率 1 12.07 15% 13.88 2 11.86 15% 13.64 3 10.34 15% 11.89 4 12.13 15% 13.95 5 6 13.23 12.56 15% 15% 15.21 14.44 141.63 163.76 86.49% 7 14.24 15% 16.38 8 11.82 15% 13.59 9 13.1 15% 15.07 10 11.81 15% 13.58
生产效率核算

日期: 2010 年 4
經營效率 J=E/E+F 生產效率 K=S/E+F 明
ห้องสมุดไป่ตู้
月 10
日
异常与除外工时内容說 (请填原因及責任单位)
设备,材料 异常造成怠 工,必须有 责任部门签 字并且承担
12 12 12 12 12 12 12 12 12 12 12 12 12 12
没有在标 准工时内, 另外追加 动作
工时管理办法
1.工资计时核算 2.产品必须标准工时制 3.月底考核生产效率
工时测算方法
工时测算表 工位/抽样数 1 2 3 4 5 6 7 8 9 10 累加时间 4〃 7〃 12〃 19〃 23〃 28〃 33〃 36〃 38〃 42〃 传套管 单位时间 4〃 3〃 5〃 7〃 4〃 5〃 5〃 3〃 2〃 4〃 焊接 热缩 扣壳 平均 4.1〃 8〃 12〃 10〃
人
H
人
H
人
H
%
部 长
領 班
月平均效率
举例:
日期 1 2 3 4 5 效率 101 105 110 99 120 日期 16 17 18 19 20 效率 105 107 108 103 94 月平均效率 6 8 9 10 11 12 13 15 平均 98 103 112 109 108 112 104 103 22 23 24 25 26 27 29 30 31 105 95 120 103 105 102 101 102 106 103
姓名 基本工(时) 资 5元/H 208H 张三 1040元 加班工(时) 资 6.5元/H 104H 676元 全勤奖 100% 60元 旷工 次数 0 0 质量奖 NC 0 补贴 NC 0 效率奖 110% 200元 其他 水电费 -50元 1926元 合计
标准工时及产能测算表

标准工时及产能测算表
表格编号:XX/QR-SC-014A 说明:本文档主要用于测算某一生产线各工序的标准工时以及标准产能,同时可以用来进行生产线工序平衡分析。
本表格对标准工时、瓶颈工时、产线平衡率、人均产能等关键数据的计算方式进行了详细说明,且在表格中以自动函数形式呈现。
(表格中内含自动计算公式,只需录入部分基本数据即可。
)
3.标准工时=实测时间(即表格中平均工时)×评比系数×(1+宽放率) 4.总标准工时=各工序标准工时之和;
5.瓶颈工时=所有工序中标准工时最大值(工位平衡时间最大值); 6.产线平衡率=总标准工时/(瓶颈工时×直接人力总数);
7.不平衡损失=瓶颈工时×直接人力总数-总标准工时; 8.损失率=(1-产线平衡率)*100%
9. 生产线每小时产能(最大产能)=3600/瓶颈工时; 10.每小时人均产能=3600/(瓶颈工时×直接人力总数)。
提高生产产能的方法--

提高生产产能的方法??转载以下资料供参考如何提高生产效率总体理念1、提高生产,制度先行。
首先,企业必须建立完善的生产制度,以确保生产有章可循。
2、生产状况,定期反馈于相关部门,由相关部门及时了解并快速调整生产计划。
可以通过工作结果定期反馈机制进行保证落实。
3、对人对事,奖罚分明。
俗话说“一分耕耘,一分收获”,生产效率高的员工理应获得应有的奖励。
在一些公司存在这样的现象,业绩好的员工要承担更多的工作,而业绩差的员工反而承担较少工作或较容易的工作,这样肯定会打击优秀员工的工作积极性。
4、工具与技术,双重优化。
为员工提高生产效率提供客观条件:工装夹具。
即便是一流的员工,面对必要的工装夹具,也难以达到高效率。
5、激发员工干劲员工是公司最宝贵的人力资源。
只有这个资源才是取之不尽、用之不竭的。
我们应充分挖掘它、利用它,使之发挥最大的效用。
身为主管,如果你了解了员工的本性,也就知道如何有效激励他们。
只有这样,才能帮助你更快走入他们的心灵,领导他们,开发他们。
6、增强团队凝聚力团队的凝聚力对于团队行为、团队功能有着重要的作用。
有的团队关系融洽,凝聚力强,能顺利完成任务;有的团队成员相互摩擦,关系紧张,凝聚力弱,不利于群体任务的完成。
同时要增强团队成员之间的交往和意见沟通,增进相互了解与友谊,建立良好的工作关系,提高团队的战斗力。
7、建立一支专业化的IE队伍,进行工作研究和方法研究,能提高效率40%左右.计算公式1.1标准工时:指在正常情况下,从零件到成品直接影响成品完成的有效动作时间,其包含直接工时与间接工时。
即加工每件(套)产品的所有工位有效作业时间的总和。
制定方法:对现有各个工位(熟练工人)所有的有效工作时间进行测定,把所有组成产品的加工工位的工时,考虑车间生产的均衡程度、环境对工人的影响、以及工人的疲劳生产信息等因素后,计算得到标准工时。
备注:直接工时:指直接作业的人员作业工时;间接工时:指对现场直接作业工人进行必需的管理和辅助作业的人员,根据现车间管理组织的特点,车间除主任和直接作业人员外产生的工时; 1.2标准人力:指在设定的产量目标前提下,根据标准工时和实际生产状况,生产单位所配置的合理的人力数量。
提升生产效率的有效方法
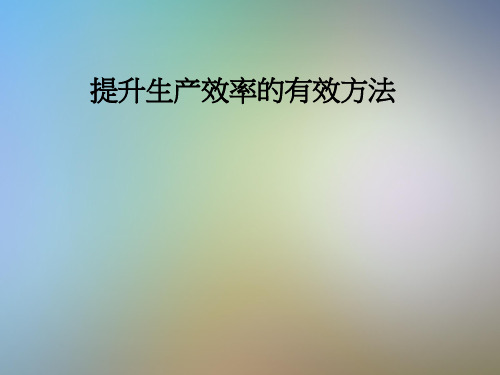
标准不仅要考虑合理性,更要考虑它的导向性.
1.1.2标准工时的两个组成部分:
1.标准工时=正常时间+宽放时间 2.正常时间=平均时间x(1+评比系数) 3.宽放时间=私事宽放+疲劳宽放+程序宽放+
1.1.13标准工时修订的五个时机
1.产品上线的第一个月 2.产品上线后第三个月(三个月之后) 3.产品上线后第九个月(半年之后) 4.产品上线后第二十一个月(一年之后) 5.设备/工艺/材料/治具发生变化时
标准工时不是随意乱改的,也不是固定不变的.
1.1.14标准工时审核发行的四个步骤
1.标准工时测试记录表(IE制作/班组长会签);
如何计算生产线需求人数是管理人员的基本功.
1.2.5生产线人员需求的计算案例
案例:
某生产部门A款产品计划生产数量为1000PCS,该 产品的标准工时为20分钟每个,客户要求2天后交货, 假设每天上班10小时,生产效率60%,该产品需要安排 多少人员作业才能如期交货?
产出工时=? 需求工时=? 需求人数=?
特殊宽放:指因工艺特点或生产计划影响的长短而给予 宽放.
工作环境和管理方法改善后,宽放系数需要重新评估.
1.1.9宽放系数的确认
1.私事(生理)宽放系数的确认;
2.疲劳宽放系数的确认;
3.程序(作业)宽放系数的确认;
4.管理宽放系数的确认;
5.特殊宽放系数的确认.
生产部门自我确认,IE部门审核确认,上级主管核准确认, 独立部门单独确认,独立产线单独确认,独立工站确认.
产线平衡与产能计算-IE-工业工程
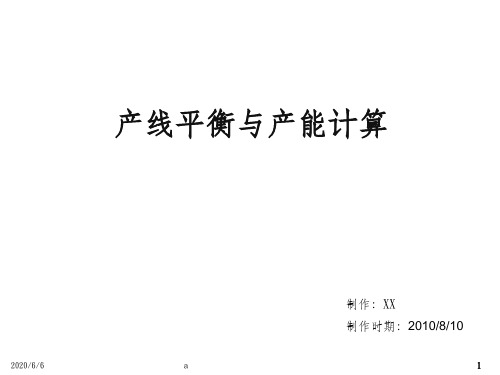
2020/6/6
a
16
标准工时﹕在适宜的操作条件下,一名培训合 格的作业员以正常速度完成特定 作业内容的时间﹔
1.马表法
标准工时=量测工时*宽放率*评比系数
量测工时是用马表直接测出的时间 宽放率和评比系数详见附档
正常速度相当于在不负重的条件下,以68cm左右 的步长和每小时4.8公里的速度,在平坦的道路上 行走的情况;或者相当于用30秒钟把一付52张扑 克牌,逐张摆在一个正方形的四个角上.
产线平衡与产能计算
2020/6/6
a
制作:XX 制作时期:2010/8/10
1
目录
一.何为线平衡(Line Balancing) 二.线 平 衡 名 词 解 释 三.线 平 衡 率 计 算 四.线 平 衡 方 法 五.产能计算
2020/6/6
a
2
一.何为线平衡(Line Balancing)
Line balancing即是对生产的全部工序进 行平均化,调整作业负荷,以使各作业时 间尽可能相近的技术手段与方法,是生产 流程设计及作业标准化中最重要的方法。
a
6
二.线 平 衡 名 词 解 释
瓶颈时间Cycle Time:一条线成品产出的循环时 间,也即整条线所有工站中标准工时最大值。
2020/6/6
a
7
三. 线平衡率的计算
PS:每站的工时加总是指每个工站的标准工时加总. (标准工时解释见第9、10 、11页) 节拍:整条线标准工时最长的那个工时.
2020/6/6
2.另一种标准工时的计算方法是预定标准工时法(模特法),此处不 再详细介绍
2020/6/6
a
5
二.线 平 衡 名 词 解 释
产 能

产能当一个企业决定了要提供什么产品,决定了竞争策略和生产运作组织方式等问题之后,他们的注意力就会集中到生产能力上来:在给定的生产运作组织方式下,现有的生产能力能否满足生产要求?如果不能,如何扩大生产能力等等。
生产运作管理人员必须考虑提供足够的能力,以满足目前及将来的市场需求,否则就会遭受机会损失。
但反过来,生产能力过大,又会导致设施闲置,资源浪费,在考虑这一问题时,需要有一定的原则和方法,这就是以下要介绍的内容。
第一节基本概念一.产能的定义所谓产能,是指一个设施的最大产出率。
这里的设施,可以是一个工序,一台设备,也可以是整个企业组织。
这里的产能,主要是指一个企业的生产能力。
企业的生产能力从广义上说,是指人员能力,设备能力和管理能力的总和。
人员能力是指人员的数量,实际工作时间,出勤率,技术水平等诸因素的组合;设备能力是指设备和生产运作面积的数量,水平,开动率和完好率等诸因素的组合;管理能力包括管理人员经验的熟练程度与应用管理理论,方法的水平和工作态度。
从狭义上说,主要是指人员能力和设备能力,在资本集约度较高的制造企业中,尤其是指设备能力。
在实际的企业管理中,由于管理能力一般来说只能作定性分析,而人员能力和设备能力是可以定量计算的。
故生产运作能力主要是指狭义的能力,即指一个企业在一定的生产运作组织条件下,企业内部各个生产运作环节综合平衡以后能够产出一定种类产品的最大数量,它是反应企业产出可能性的一种指标。
二.产能的度量(一)基本度量没有一种度量适用于所有类型的组织。
不同的组织,根据其具体的情况,需要考虑用不同的度量。
一般来说,度量可分为两种基本形式:投入度量和产出度量。
一个汽车厂,其生产能力可用产出来简单的度量,例如,年产30万辆;但在一个机械配件厂,因其生产的品种很多,用可利用的设备数,即投入度量更方便。
一个医院,可以用它的投入来度量,如它所拥有的床位,也可以用产出来度量,如平均每天可看的病人数;航空客运业,可用它所拥有的飞机数量(投入)度量,也可以用它每月所提供的座位数(投入)度量,还可以用每月的飞行距离*顾客人数(产出)度量;一个餐馆,可用所拥有的座位(投入)度量,也可用每天可接待的顾客数(产出)来度量。
生产线平衡和计算精品资料

时间(Mins) 任务描述 2 装配外框 1 安装开关
3.25 装配马达架 1.2 将马达架装入外框 0.5 安装扇叶 1 安装格栅 1 安装电缆 1.4 测试
紧前务 无 A 无 A, C D E B F, G
1、确定TT
假定我们每天要装配100台风扇。周期时间 应是多少?
要求T的 ak.Ttim,T e T=每 每期 期的 要生 求产 的时 产间 出
这不仅仅是在单位时间内没有创造任何价值,更重要是每个 工序按一人计算,就损失了11个人工资费用以及影响交货, 不能快速响应市场,甚至失去市场。
改进方法:
运用工业工程(IE)中的八个字:“排除”、“组 合”、“替换”、“简化”。 “排除” →消除一些不必要作业及搬运动作; “组合” →两个或两个以上工序或工位组合成一个 ,或重新划分工序,以平衡各工序工作量; “替换” →用另一种方法或工艺代替,如工具、及 搬运手段的替代; “简化” →将作业动作简化,或将某工序一部分作 业内容分解出去。
生产线平衡改善
1、缩短瓶颈时间,提高产能
作 业 时 间
工序 1 2 3 4 5
1、分割作业
作 业 时 间
工序 1 2 3 4 5
2、缩短时间
1人
作
2人
业
时
间
工序 1 2 3 4 5
3、增加人员
生产线平衡改善
2、减少人员
作 业 时 间
工序 1 2 3 4 5
1、分割作业 省略工序
作 业 时 间
工序 1 2 3 4 5
(第四工序),而最长的达22.4秒(第六 工序),是最短工序的6倍多,也就是说6 工序干一件活的时间,4工序可以干6件。 这样必然导致工序间在制品积压,设备和
标准工时及产能计算表

部门主管:
现场工序调整填写IE现场改善
标准工时 (s)
73.28 82.52 40.94 93.74 49.30 121.90 80.10 58.10 123.00 58.98 160.84 194.72 79.44 67.12 58.76 125.86 89.78 155.78 56.12 1338.28 .94
121 127 119 115
28
33
25
30
1195
1183 194.72
1189 1201 工序最小工时 (s):
不平衡损失
44.80 10% 53.20 10% 15.40 10% 63.40 10% 23.00 10% 89.00 10% 51.00 10% 31.00 10% 90.00 10% 31.80 10% 124.40 10% 155.20 10% 50.40 10% 39.20 10% 31.60 10% 92.60 10% 59.80 10% 119.80 10% 29.20 10% 1194.80 10%
7、人均产能=每小时产能/总人数
8、不平衡损失=瓶颈工时×总人数-各工序(每人)时间之和;
9、最大产能=单位标准时间/瓶颈工序标准时间。
线长/物料员
备注:维修员Fra bibliotek当生产均衡率<90%时,需对生产平衡率进行现场改善, 改善步骤:工位摄影 填写IE工序工时分析表 改善瓶颈工位的工序作业 效果表
制表人:
班组长:
产品名 称
工序 (No.)
工序名称
标准工时及产能计算表
型号/模块
线别
文件编号:
测试日期
实测作业时间(s) 实测1 实测2 实测3 实测4 实测5
生产产能产测法

如何制定标准产能1.产能的定义产能:1小时之产出数量.标准产能=3600÷标准时间.标准时间=观测时间×(1+宽放率)=观测时间+宽放时间2.标准时间的定义:使用既定的方法及时间—在既定的作业条件之下—对于该工作,具有十分熟练度的作业者—对于该职务已接受过完整的训练,被期待能圆满完成该职务的作业者—在不受到外在之影响下,每天对其职务,能够维持最高作业之绩效时—完成一单位作业量的所必要时间。
3.宽放的定义:宽放时间一般宽放作业宽放进行作业时不规则的发生小事(如清扫铁屑,不良品混入等)身边宽放上厕所喝水擦汗等方面必要的宽放时间疲劳宽放恢复疲劳所必须的休息时间特殊宽放管理宽放上班时间到医务室因而延迟工作时间小组宽放在小组工作中,每位作业员往往会碰到一时没有工作的情况,此即小组宽放机械干扰的宽放一人负责多机台操作时,当操作其中一部机械时,另外的机械由于加工完毕在空转或停下来其它宽放数量单位太小,往往在尚未热身之前作业就结束了,额外增加的时间可称为小数量单位宽放4.标准时间的用途:用来决定最适当的作业方法(两种以上作业方法的比较)。
以小组作业来说,可使作业者的工作时间保持平衡,并使作业效率化。
决定每名作业者负责的机械台数。
为生产计划制订基础数值。
为标准成本制订基础数值。
为效率制订基础数值。
决定外包单价的基础数值。
制订衡量生产力、作业效率的基础数值。
制订生产计划、日程计划的基础数值。
制订安排主要人员的基础数值(为了决定公平的一天的作业量)。
制订标准成本与实际成本差异分析的基础数值决定劳务管理费的基础数值。
5.瓶颈工序:流水线中消耗时间最长且非手工作业之工序。
6.时间的测订:观察作业有无过多浪费之处,布置是否合理,有无动作浪费及搬运浪费等观察作业有无等待现象观察作业者动作是否熟练观察作业者是否有按作业标准书作业(即动作是否标准)观察使用之机台及辅助工具是否合理使用秒表测得每个产品之作业时间(去除停顿、等待时间)每次测得的时间一般以一次产品之加工周期为单位测试(个别加工时间较短的产品除外),即正常测得的时间包含:开始→拿产品(治具)→其它动作(定位、正常检查等)→加工作业→放产品(治具)→回到准备产品的位置→停。
- 1、下载文档前请自行甄别文档内容的完整性,平台不提供额外的编辑、内容补充、找答案等附加服务。
- 2、"仅部分预览"的文档,不可在线预览部分如存在完整性等问题,可反馈申请退款(可完整预览的文档不适用该条件!)。
- 3、如文档侵犯您的权益,请联系客服反馈,我们会尽快为您处理(人工客服工作时间:9:00-18:30)。
Copyright © by gbm Ltd All rights reserved.
8
IE課培訓教材
Copyright © by gbm Ltd All rights reserved.
2
IE課培訓教材
2.平衡率基本定義: 平衡率就是對這條線的全部工序(工位)進行平均化,調整
各工序(工位)作業負荷,以使各工序(工位)作業時間盡可 能相近。
3.標準產能基本定義:
標準產能是指在标准的环境下,设备正常、人员安排合理、 时间一定情况下的产量,它与理论产能的区别在于一个是 停留在设计图上,一种是经过实践证明。
Copyright © by gbm Ltd All rights reserved.
7
IE課培訓教材
3.平衡率、生產效率的計算實例 • 依以上例子計算: 1>.平衡率為(219.5/(16*16))*100%=86% 2>.若產線每小時實際生產量為210PCS 那此段生產效率(210/225)*100%=93% • 通過以上可以看出此段的站位較多,所以要提高生產效率平 衡率就必須使每個站位負荷較均勻,就是說產線要平衡這樣 才能使效率發揮到最高.
生產效率是指生產活動中產出和投入的比值,管理和改善 的目的就是將必要的投入量控制在最小,而取得最大的產 出,換句話說,管理和改善活動的目的是盡一切所能降低 生產成本,提高生產活動的附加價值。所有的產出不外乎 包括兩方面的內容,一方面是數量意義上的成果,如生產 量、 成本等;另一方面是產品和技術質量意義上的成果, 如品質等,因此為了提高生產效率就必須從開展品質和數 量兩方面的管理改善活動著手。
3.標準產能計算方法: SMT標準產能=3600/瓶頸時間(Sec)*連片數 DIP/TEST/PACKING標準產能=3600/瓶頸時間(Sec)
Copyright © by gbm Ltd All rights reserved. 4 IE課培訓教材
三、生產效率、平衡率、標準產能公式實例
1.SMT標準產能的計算 • 例如:LT-2AA7機種(2連片) 1>.SMT機型:FX1R*3+KE2060RL*1+KE2080RL*1 2>.各機台貼片時間:45S 43S 46S 52S 48S • 瓶頸時間為52S,每小時標準產能為3600/52*2=138PCS
Copyright © by gbm Ltd All rights reserved.
3
IE課培訓教材
Байду номын сангаас、生產效率、平衡率、標準產能計算方法
1.生產效率計算方法: 生產效率=有效工時實際產能/有效工時標準產能*100% 2.平衡率計算方法: 平衡率=各工序作業時間總和/(瓶頸時間*作業總人數)*100%
生產效率、平衡率、標準產能計算方法 一、生產效率、平衡率、標準產能基本定義
二、生產效率、平衡率、標準產能計算方法
三、生產效率、平衡率、標準產能公式實例
Copyright © by gbm Ltd All rights reserved.
1
IE課培訓教材
一、生產效率、平衡率、標準產能基本定義 1.生產效率基本定義:
9>. 貼腳墊*4:13S 10>. 貼黑色塑膠墊片*4:12S
Copyright © by gbm Ltd All rights reserved. 6 IE課培訓教材
11>. 裝鎖風扇*8:32S 12>. 目檢錫面+撕高溫膠:14.5S 13>. 總檢+擦拭金手指:15S 14>. 阻抗量測+貼機種貼紙:13S 15>. 貼貼紙+掃描+裝箱:12S • 瓶頸站是第11站裝鎖風扇,排兩站一個人也要16S • 每小時標準產能為3600/16S=225PCS
Copyright © by gbm Ltd All rights reserved.
5
IE課培訓教材
2.DIP 、TEST、Packing標準產能的計算實例 • 例如:LT-2AA7機種 1>. 裁板+插件*2:12S 2>. 投板+插件*4:14S 3>. 插件*6:15S 4>. 插件*2+中檢:14S 5>. 取治具+折板邊:13S 6>. 補焊:13.5S 7>. 刷板:12.5S 8>. 鎖鐵片*4:14S