普通切削加工方法综述
机械加工工艺基础 第二章 传统切削加工方法

砂带
工件
a)砂带无心外圆磨削 (导轮式)
工件
c)砂带定心外圆磨削 (接触轮式)
砂带 接触轮
工件 工件 砂带 工作台 接触轮 支承轮 e )砂带平面磨削 d)砂带内圆磨削 f)砂带平面磨削 (支承板式) (回转式) (支承轮式) 48 图 几种砂带磨削形式
砂带
§2-7 精密加工
精密加工实质是修整砂粒,使其等高,减少磨 削深度,增加行程次数 有:刮削、研磨、珩磨、精密磨削、超精密 磨削等
逆铣和顺铣 的特点:
二、常用铣床
三、主要加工范围(P48图2.40)
40
§2-7 磨削加工
一、磨削工具:主要有砂轮、砂带 1、磨粒形状:
2、砂带构造:
41
精密与超精密砂带磨削
砂带轮
• 砂带在一定工作压力 下与工件接触并作相 对运动,进行磨削或 抛光。 • 有开式(右图)和闭式 两种形式,可磨削平面、 内外圆表面、曲面等。
10
§2-1 车削加工
一、精度范围 二、工艺特点 §2-1-1 车床类型 一、卧式普通车床(P23图2.1) 二、立式车床(P24图2.2) 三、转塔式六角车床(P25图2.3) 四、端面车床(P25图2.4)
11
§2-1-2 车削加工范围
一、车内圆面, 如:通孔、盲孔、台阶孔、内槽 条件:工件上预先有孔; 实质:扩孔 二、车外圆面 三、车平面,如:车端面
5、插削斜面的几种方法 (1)斜放工件垂直插削法
(2)斜垫铁法
35
(3)倾斜滑枕法
36
(4)倾斜工作台垂直插削法
37
§2-5 拉削加工
拉削加工:用定形、定径和多刃的拉刀加工工 件内、外表面的方法
六七普通刀具切削加工方法综述
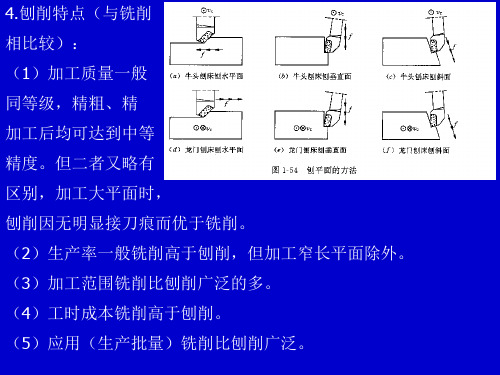
无进给运动,其进给靠拉刀每齿升 高量来实现。 (4)加工范围:内表面(各种型孔)、外表面(平面、半圆弧面、 组合表面等)
六、插削加工
1.定义:用插刀对工件作垂直相对直线往复运动的切削加工方法 称为插削加工。
2.机床:插床(“立式刨床”) 3.加工范围:单件小批量生产中零件的某些内表面及外表面。
4.刨削特点(与铣削 相比较): (1)加工质量一般 同等级,精粗、精 加工后均可达到中等 精度。但二者又略有 区别,加工大平面时, 刨削因无明显接刀痕而优于铣削。 (2)生产率一般铣削高于刨削,但加工窄长平面除外。 (3)加工范围铣削比刨削广泛的多。 (4)工时成本铣削高于刨削。 (5)应用(生产批量)铣削比刨削广泛。
纵磨法:加工精度高,Ra值较小,生产率低, 广泛用于各种类型的 生产中;
横磨法:加工精度低,Ra值较大,生产率高, 只适用于大批量生产中磨削刚度较好、精度较低、长度较 短的轴类零件上的外圆表面和成形面。
2.磨内圆(包括内锥面) (1)机床:内圆磨床、万能外圆磨床 (2)特点: ①由于磨内圆砂轮受孔径限制,切削速度难以达到磨外圆的速度;
工件上精度较高的平面(如导轨面), 以代替刮削和导轨磨削。
三、研磨
(1)定义:利用研磨工具和研磨剂,从 工件上研去一层极薄表面层的精密加工方法。 (2)研磨剂由磨料、研磨液及辅料调配而成。①磨料一般只用微 粉。②研磨液用煤油或煤油加机油,起润滑、冷却以及使磨料能均 匀分布在研具表面的作用。③辅料指油酸、硬脂酸或工业用甘油等 强氧化剂,能使工件表面生成一层极薄的疏松氧化膜,以提高研磨 效率。
多砂轮磨削是宽砂轮磨削的另一种形式。主要用于大批量生产 中外圆和平面的磨削。近年来,内圆磨床也开始采用这种方法,用 来磨削零件上的同轴孔系。
切削加工技术综述

切削加工技术综述切削加工技术是一种通过物理力学原理和工具与工件之间的相对运动来改变工件形状和尺寸的方法。
它是制造业中最常用的一种加工方法,广泛应用于各个领域,如机械、汽车、航空航天等。
切削加工技术的基本原理是利用切削工具对工件进行削除材料的操作,以达到所需的形状和尺寸。
切削工具一般由硬质材料制成,如高速钢、硬质合金等,具有较高的硬度和耐磨性。
在切削加工过程中,切削工具与工件之间的相对运动产生剪切力,使工件表面的材料被削除,从而形成所需的形状。
切削加工技术包括多种方法,常见的有车削、铣削、钻削、刨削等。
车削是利用车床上的主轴和刀具对工件进行旋转切削的方法,常用于加工圆柱形工件。
铣削是通过铣床上的刀具进行旋转切削的方法,常用于加工平面和复杂曲面形状的工件。
钻削是利用钻床上的钻头对工件进行旋转切削的方法,常用于加工孔洞。
刨削是利用刨床上的刀具对工件进行直线切削的方法,常用于加工平面和棱角。
切削加工技术的优点是加工精度高、表面质量好、适用于各种材料和形状的工件。
然而,切削加工也存在一些限制和挑战。
首先,切削加工需要专业的设备和工具,成本较高。
其次,切削加工过程中产生的切屑和废料需要处理和清理,对环境造成一定影响。
此外,切削加工对工件的形状和尺寸有一定限制,无法加工过于复杂和小尺寸的工件。
随着科技的不断进步,切削加工技术也在不断发展。
近年来,随着数控技术的应用,切削加工实现了自动化和智能化,提高了加工效率和精度。
同时,切削工具的材料和结构也得到了改进和创新,提高了切削效果和工具寿命。
切削加工技术的发展为制造业的进步和发展提供了坚实的基础。
切削加工技术是一种重要的制造工艺,具有广泛的应用前景和发展空间。
随着科技的不断进步,切削加工技术将会更加高效、精确和智能化,为制造业的发展做出更大贡献。
同时,我们也需要不断学习和掌握新的切削加工技术,以适应市场需求和技术发展的变化。
常用的金属切削加工方法以及相应设备讲解
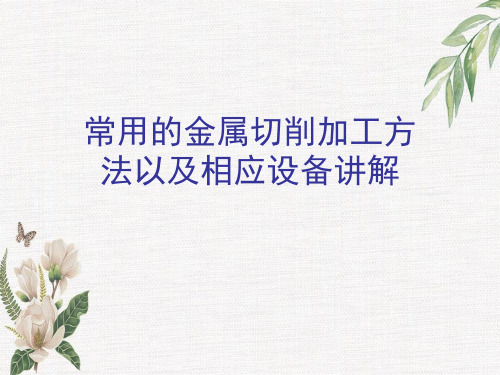
金属切削加工是利用刀具和工件的相对运动,从毛坯或半成品
上去除多余金属已获得需要的几何形状、尺寸精度和表面粗糙度的
加工方法。金属切削加工也称冷加工。
切削加工的方法很多,常用的有车削加工、铣削加工、钻削加
工、刨削加工、磨削加工及特种加工。
1. 车削加工
在车床上进行的切削加工称为车削加工。车削加工是机械加工中应用 最广泛的加工方法之一。
(4)刀架及滑板 刀架装在小滑板上,而小滑板装在中滑板上, 中滑板又装在纵滑板上,纵滑板可沿床身导轨纵向移动,从而带动 刀具纵向移动。
(5)床身及床腿
(6)溜板箱 溜板箱安装在刀架部件底部,溜板箱内装有纵、横 向机动进给的传动换向机构和快速进给机构等。
车床除上述主要组成部分外,还有动力源(如电动机)、液压冷
车削加工时,工件旋转为主运动,车刀移动为进给运动。
(1) 车削加工的特点及应用
1)车削加工的特点
加工范围广;
加工精度较高;
车削生产率较高 ; 车削加工成本较低。
2)车削加工应用
机械制造中精度要求较高的零件多数都要进行切削加工,在车 床上可以车外圆、车端面、车台阶、车槽和车断(切断)、孔加工 、车圆锥面、车螺纹等的加工。
然后拧紧固定螺钉。车 削时,转动小刀架手柄, 切出所需锥面。这种方 法简单易行,可车削短 而锥度大的工件,但不 能自动进给,所车锥面 长度受小滑板行程长度 限制,不能太长。
图14-6小滑板转位法车锥面
※宽刃切削法车锥面
车刀安装时,平直的切
削刃与工件轴线的夹角等于
锥面的半锥角α/2。切削时,
车刀作横向或纵向进给。此
(2) 铣床的组成及运动
铣床是主要用铣刀在工件上加工各种表面的机床。铣床的种类很多, 主要有升降台式铣床、床身式铣床、龙门铣床、工具铣床、仿形铣 床及数孔铣床等。
常用金属切削加工方法综述

车床上工件的常用安装方法有: 1、三爪卡盘安装
特点: 三爪联动,能够实现自动定心。安装工 件时一般不需要找正。定位精度不高,一般为 0.01~0.1mm
应用: 应用广泛,适于安装短轴及盘套类零件 。
正爪的外表面、反爪、 软爪装夹工件。
2 四爪卡盘安装
特点:四个单动卡爪可分别调整,不能自动定 心,安装工件时需细致找正;定位精度可达到 0.005mm;夹紧力较大。 应用: 适于安装铸锻件毛坯、形状不规则工件 或较大的工件
(三)孔加工
在车床上可进行钻孔、扩孔、铰孔、镗孔。
车床钻孔精度IT12~IT11, Ra 25~6.3μm; 钻后扩孔精度IT10~IT9, Ra 6.3~3.2μm;
铰孔精度IT8~IT7, Ra 1.6~0.8μm
镗孔是车床上加工孔 的基本方法。单件小 批生产中,精度等级 IT9~IT7,Ra 3.2 ~ 1.6μm的孔一般用车 床镗出;在成批大量 生产中,镗孔常作为 铰孔、拉孔前的半精 加工工序。对大孔来 说,镗孔常常是唯一 的加工方法。
1)顶尖安装配合附加支承中心架或跟刀架。
2)采用主偏角为90º 的偏刀,以减小径向分力Fy。 3)减小切削深度,增加进给次数,以降低切削力。 4)供足切削液,以降低切削温度,减小热变形产生的 误差,提高刀具的耐用度。
(2)偏心工件的车削
(3)曲轴的车削
(二)车端面及台阶
阶梯轴及盘套类零件上除了存在外圆面以外,还存在 端面及台阶面,也是通过车削来完成的。在车削加工 中利用一次安装可保证零件的端面、台阶面之间的平 行度要求以及它们与外圆、内孔表面的垂直度要求。 车削加工平面主要是指车端面和台阶面。
扩孔质量好,尺寸精度IT10~IT9, Ra6.3~3.2μm。生产率高。 (二)铰孔 铰孔属于孔的精加工过程,尺寸精度IT9~IT6, Ra1.6~0.4μm。 使用的刀具为铰刀。由于铰刀的安装为非刚性 连接,在切削过程中由孔本身定位,不能纠正 原有孔轴线偏斜等位置误差,所以在铰孔前, 位置精度就应该达到图纸要求。
浅谈常见传统金属切削过程

浅谈常见传统金属切削过程金属切削在生产和制造中有多种形式,例如:锯、剪切,冲裁的传统方法,以及激光、超声波、电化学、高压水流等特殊方法。
其中常见的方式为:钻孔、攻丝、车削、铣削和拉削。
各种加工方式各有特点,需要根据实际情况来选取不同的切削液。
金属加工的常见方法有:钻孔、攻丝、车削、铣削和拉削金属切削在生产和制造中有多种形式,例如:锯、剪切,冲裁的传统方法,以及激光、超声波、电化学、高压水流等特殊方法。
这里主要介绍常用的4种方式:1.钻削--钻孔,攻丝2.车削3.铣削4.拉削金属加工的常见方法有:钻孔、攻丝、车削、铣削和拉削金属切削在生产和制造中有多种形式,例如:锯、剪切,冲裁的传统方法,以及激光、超声波、电化学、高压水流等特殊方法。
这里主要介绍常用的4种方式:1.钻削--钻孔,攻丝2.车削3.铣削4.拉削钻削主要分为钻孔和攻丝两个步骤,是通过钻头的旋转运动的加工方式钻孔工艺使用具有螺旋形沟槽的刀具,它带有对称分布的切削刃,切削刃呈锥形,称为钻尖。
钻孔通过钻头的旋转运动去除工件,切屑通过螺旋槽排出。
钻孔的下一步工艺为攻丝,是用刀具--丝锥切削或挤压加工的切削方式,通过除去前道钻孔工序孔壁上的材料,来形成螺纹。
1.切削攻丝切削丝锥通过切除金属形成螺纹,加工过程中会产生切屑。
2.挤压攻丝挤压丝锥通过向旁边挤压金属形成螺纹,加工过程中不产生切屑。
因为该工艺加工过程中摩擦更多,因此需要使用润滑性能更高的切削液。
车削是固定的刀具沿着旋转的工件的轴向运动的加工方式车削加工时,固定的刀具沿着旋转的工件的轴向运动,采用不同的刀具形状、角度和路径,几乎可以加工出任何形状的工件。
车刀可以在轴的外部工作,也可以在管状零件的内部工作。
铣削是铣刀旋转并沿着工件表面移动的加工方式铣削是采用多齿刀具的加工工艺。
与车削不同的是,铣削时,工件不动,铣刀旋转并沿着工件表面移动,用铣刀的端面齿加工平面;或者用铣刀的圆周齿加工型面或沟槽。
切削加工方法总结范文
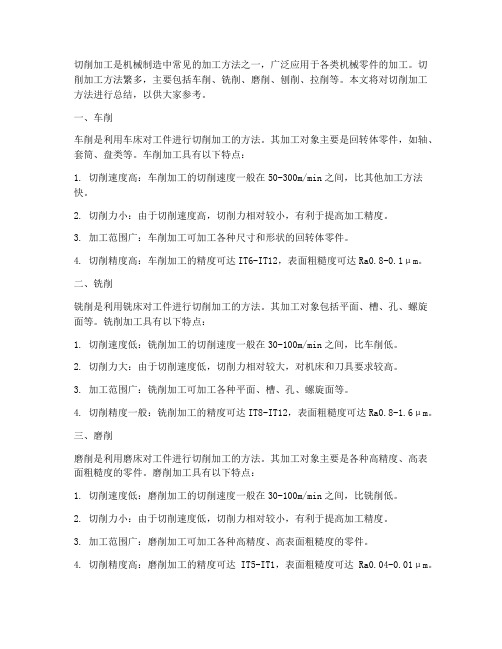
切削加工是机械制造中常见的加工方法之一,广泛应用于各类机械零件的加工。
切削加工方法繁多,主要包括车削、铣削、磨削、刨削、拉削等。
本文将对切削加工方法进行总结,以供大家参考。
一、车削车削是利用车床对工件进行切削加工的方法。
其加工对象主要是回转体零件,如轴、套筒、盘类等。
车削加工具有以下特点:1. 切削速度高:车削加工的切削速度一般在50-300m/min之间,比其他加工方法快。
2. 切削力小:由于切削速度高,切削力相对较小,有利于提高加工精度。
3. 加工范围广:车削加工可加工各种尺寸和形状的回转体零件。
4. 切削精度高:车削加工的精度可达IT6-IT12,表面粗糙度可达Ra0.8-0.1μm。
二、铣削铣削是利用铣床对工件进行切削加工的方法。
其加工对象包括平面、槽、孔、螺旋面等。
铣削加工具有以下特点:1. 切削速度低:铣削加工的切削速度一般在30-100m/min之间,比车削低。
2. 切削力大:由于切削速度低,切削力相对较大,对机床和刀具要求较高。
3. 加工范围广:铣削加工可加工各种平面、槽、孔、螺旋面等。
4. 切削精度一般:铣削加工的精度可达IT8-IT12,表面粗糙度可达Ra0.8-1.6μm。
三、磨削磨削是利用磨床对工件进行切削加工的方法。
其加工对象主要是各种高精度、高表面粗糙度的零件。
磨削加工具有以下特点:1. 切削速度低:磨削加工的切削速度一般在30-100m/min之间,比铣削低。
2. 切削力小:由于切削速度低,切削力相对较小,有利于提高加工精度。
3. 加工范围广:磨削加工可加工各种高精度、高表面粗糙度的零件。
4. 切削精度高:磨削加工的精度可达IT5-IT1,表面粗糙度可达Ra0.04-0.01μm。
四、刨削刨削是利用刨床对工件进行切削加工的方法。
其加工对象主要是平面、斜面、槽等。
刨削加工具有以下特点:1. 切削速度低:刨削加工的切削速度一般在20-50m/min之间,比铣削和磨削低。
5.3常用加工方法综述

端铣法 同时参与切 削的刀齿多 立式安装,悬伸长度 小,刚度好;铣刀可 镶装硬质合金,耐热 好,Vc↑ 切削层厚度变化 小,摩擦情况差 表面粗糙度小 结构单一
铣刀结构:
应用:
种类繁多
铣削各类表面
铣削平面
三、铣削的应用
主要加工:平面、沟槽、成形面… 加工精度:IT8~IT7、Ra 1.6~3.2μm 单件小批生产中、小型工件→→升降台式铣床 中大型工件→→龙门铣床
铣 花 键
铣削的主运动:铣刀的回转运动 进给运动:工件的直线运动
一 . 铣削的工艺特点
1、生产率较高 主运动利于高速 铣刀是多齿刀具 同时参与切削的刀刃长 2、容易产生振动 每个刀齿均为断续切削,有 切出和切入冲击 参与切削的齿数变化 每齿的切削层厚度随时变化 3、刀齿散热条件较好 每个刀齿均为断续切削,有散热时间
插削实际上是立式刨 削,主要用于加工内表 面,特别适用于加工盲 孔和有障碍的内表面
插削 让刀 退刀
二 、刨削的应用
单件、小批量的窄长平面、沟槽和直线成形面
刨平面
刨垂面
刨斜面
刨直槽
刨V槽
刨T槽
刨燕尾槽
刨成形面
三 、拉削 在拉床上用拉刀进行通孔、成形表面的加工
拉削加工原理
拉削特点
生产率高
精度较高
设备简单
用镗刀对已有的孔进行再加工 主运动:镗刀的回转运动;进给运动:镗刀的直线移动 镗孔可在车床上,也可在镗床上进行
后立柱 主轴 平转盘 主轴箱
工作台
卧式镗床
镗孔精度: IT8~IT7 ; Ra0.8~1.6μm 精镗: IT7~IT6; Ra0.2~0.8 μm 应用: 镗孔多用于箱体类零件上的大孔加工。 大尺寸的孔、内成形表面、内环槽,镗孔是唯一的 加工方法。 孔系则需用镗孔保证位置精度 1、单刃镗刀镗孔 特点:(1)适应性较广,灵活性较大; (2)可以校正原有孔的轴线歪斜或位置偏差; (3)生产率较低。
磨具与磨削过程、普通刀具加工方法

铣削种类 粗铣
半精铣
3.铰孔
用铰刀在工件孔壁上切除微量金属层,以提高尺寸精度和降低 表面粗糙度的方法称为铰孔。铰孔所用机床与钻床相同。铰孔可加 工圆柱孔和圆锥孔,可机铰和手铰,铰孔余量一般为 0.05~0.25mm。
铰孔的精度和表面粗糙度主要不取决于机床的精度,而取决于铰刀 的精度、安装方式以及加工余量、切削用量和切削液等条件。因此, 铰孔时,应采用较低的切速,精铰Vc≤0.083m/s (即5m/min), 避免产生振动、积屑瘤和过多的切削热;宜选用较大的进给量,要 施加合适的切削液;机铰时铰刀与机床最好用浮动连接方式,以避 免因铰刀轴线与被铰孔轴线偏移而使铰出的孔不圆,或使孔径扩大; 铰孔之前最好同材料试铰一下,以确保铰孔质量。
2.扩孔
用扩孔刀具扩大工件孔径的方法称为扩孔。扩孔所用机床与钻
孔相同。可用扩孔钻扩孔,也可用较大直径的麻花钻扩孔。扩孔钻 的直径规格为10~100mm,其中常用的是15~50mm。直径小 于15mm的一般不扩孔。扩孔的余量(D-d)一般为孔径的1/8。 与麻花钻相比,刚度、导向性和切削条件较好,轴向力较小,因此 扩孔的加工精度比钻孔高些,可在一定程度上纠正原孔轴线偏斜, 属于半精加工,其尺寸公差等级为IT10~IT9,表面粗糙度Ra 值 为6.3~3.2 μm 。
切削加工方法

式中:d——钻头直径(mm)
4.钻削加工的工艺特点
1)钻孔是孔的粗加工方法; 2)可加工直径0.05~125mm的孔; 3)孔的尺寸精度在IT10以下; 4)孔的表面粗糙度一般大于Ra12.5μm; 5) 对于精度要求不高的孔,如螺栓的贯穿孔、油孔以 及螺纹底孔,可直接采用钻孔; 6) 一些内螺纹在攻丝前,要先钻孔; 7) 刀具刚性差,容易发生“引偏”; 8) 排屑困难,切削热不易排出 。
CHD
第4章 切削加工方法
基本内容
1 2 2
车削加工 钻、扩、铰、镗加工 刨削、插削和拉削加工
1
3 2 4 5 6 7
铣削加工 磨削加工 光整加工
特种加工
4.1 车削加工
何谓车削加工?用车刀在车床上加工工件的工艺过程称为 车削加工。 主运动:工件随车床主轴旋转 进给运动:刀具沿轴向或径向作进给运动 加工精度: 一般车削加工精度可达IT7~IT8,表面粗糙度 Ra为6.3~1.6μm。 适用范围:各种回转体表面。
常用车床类型
普通卧式车床
普通车床 — 适于各种中、小型轴、盘、套类零件的单件、小批量生产。
常用车床类型 立式车床
适用范围:适于加工直径大,长度短且质量较大的大型盘 套类零件。
(二)
常用车床类型
转塔车床(六角车床)
适用范围:成批加工形状复杂的盘套类零件。适于加工零件尺寸较小、形状 较复杂的中、小型轴、盘、套类零件。 结构特点:没有丝杠和尾座,而在床尾装有一个可纵向移动的转塔刀架,其 上可装多把刀,工作中周期性转位,顺序地对工件进行加工。刀具行程由挡 块控制,易保证精度,提高生产率。
三爪卡盘
四爪卡盘
车削加工的工艺特点
2.加工过程比较平稳
第2章 常规切削加工方法

2、插床:插床其实就是一台将滑枕立起来的刨床。主要用 于加工键槽,也可以用来加工孔内的平面或者成形表面。 其主运动和进给运动与牛头刨床相同。插床的工作台除可 以进行横向、纵向运动外,一般还可以旋转。
插床
3、刨削的加工范围和工艺特点 刨削可加工各类平面和多种沟槽,如图所示。
图2-23 刨削加工范围
4)攻丝和套扣:采用丝锥(如图2-26所示)和板牙(如 图1-27所示)加工内外螺纹的方法。
图2-26 丝锥
图2-27 板牙
第六节 镗床加工
镗床最主要的加工对象是孔,其不但可以加工大型的孔, 而且能够保证孔系的形状、尺寸和位置精度。 1、镗床: 主运动为镗刀回转运动,进给运动为镗杆的轴向运动,主 轴箱的上下运动和工作台的横向、纵向移动。 卧式镗床结构,主轴水平布置﹑主轴箱能沿前立柱导轨垂 直移动的镗床。 可调镗刀
(2)切削力方向的影响。
顺铣时作用于工件上的垂直切削分力始终压下工件 ,这对工件的夹 紧有利。 逆铣时垂直切削分力向上,有将工件抬起的趋势,易引起振动,影 响工件的夹紧。铣薄壁和刚度差工件时影响更大。
逆铣
顺铣
5、铣削工艺特点 1)生产率高。 铣削为多齿切削,没有空行程,可采用较 高的切削速度,故生产率比刨削等方法高得多。 2)切削过程不平稳。 铣削是断续切削过程,刀齿切入切 出时受到的机械冲击很大,易引起振动;铣削时总切削面 积是一个变量,因而铣削力也不断变化,造成机床和刀具 的振动。
2)立式钻床:
主轴竖直布置且中心位置固定的钻床。立钻有方柱立 钻和圆柱立钻两种,还有排式、多轴坐标和转塔等多种变 型。加工中小型工件,一般孔径<50mm,可自动走刀。 立式钻床
3)摇臂钻床:主轴箱可在摇臂上移动,并随摇臂绕立柱 回转的钻床。摇臂还可沿立柱上下移动,以适应加工不同 高度的工件。较小的工件可安装在工作台上,较大的工件 可直接放在机床底座或地面上。摇臂钻床广泛应用于单件 和中小批生产中,加工体积和重量较大的工件的孔。
常用切削加工方法综述

34
第二节 钻、镗削的工艺特点及其应用
扩孔特点及应用
a.刀具刀刃多(3~4个),导向作用好,切削平稳, 加工效率较高 b.加工精度较高 : IT10~ IT9 c.切削用量小, 无横刃,刚性好
d.用于一般精度孔的最终加工,高精度孔的半精加工
35
Ra 3.2-6.3μm
第二节 钻、镗削的工艺特点及其应用
铰 孔
尺寸公差等级IT9~IT7、表面粗糙度Ra值0.4~1.6 μm
铰 孔:是在扩孔或半精镗基础上对孔再进行精加工。
钻削加工-铰孔
36
第二节 钻、镗削的工艺特点及其应用
铰 孔
37
第二节 钻、镗削的工艺特点及其应用 铰孔特点及应用
1.铰刀刀刃多(6~12),导向 性好,刚性好 2.铰刀制造精度高 3.铰刀有修光刃,可校准孔 径和修光孔壁 4.铰孔加工余量小,切削力 小,用高速钢铰刀铰孔时, 切削速度较低,产生切削热 少,排屑,冷却润滑条件好 5.加工精度高 IT9-IT7 , Ra 0.4-1.6μm
切削部分由两个前刀面、两个后刀面、两个 副后刀面、两条主切削刃、两条副切削刃和一条 横刃组成。
(3)副后刀面 副后刀面是与已加工表面(孔壁)相对的 钻头外圆柱面上的窄棱面。 (4)主切削刃 主切削刃是前刀面(螺旋沟表面)与后刀 面的交线,标准麻花钻主切削刃为直线(或近似直线)。 18
第二节 钻、镗削的工艺特点及其应用
①麻花钻刚性差 ②导向作用差 ③横刃的不利影响: 横刀刃产生很大的轴向力 ④两个主切削刃受力不平衡不对称
25
第二节 钻、镗削的工艺特点及其应用
二、钻削的工艺特点 1. 容易产生“引偏” 减少引偏的措施: 预钻锥形定心坑 用钻套为钻头导向 钻头的两个主切削刃尽
普通刀具切削加工方法综述

二、钻削加工
(1)定义:用钻头或铰刀、锪刀在工件上加工孔的方法统称为 钻削加工。
(2)可进行钻削加工的机床:台式钻床、立式钻床、摇臂钻床、 车床、铣床、铣镗床等机床。
1.钻孔
用钻头在实体材料上加工孔的方法称为钻孔。钻孔属于粗加工, 其尺寸公差等级为IT12~IT11,表面粗糙度Ra 值为25~12.5 μm 。
4.车锥面
锥面可看作是内外圆的一种特殊形式。内锥面具有配合紧密、 拆卸方便、多次拆卸后仍能保持准确对中的特点,广泛用于要求对 中准确和需要经常拆卸的配合件上。常用的标准圆锥有莫氏圆锥、 米制圆锥和专用圆锥三种。
种类
规格
说明
应用
莫氏 圆锥
0号尺寸最小(大端直径
0,1,2… 6等7 9.045mm),6号最大(大端直
个号
径63.348mm)其中锥角α /2 在
1°30´ 左右
车床主轴锥孔及 顶尖、钻头、铰
刀的锥柄等
米制 圆锥
4,6,80,100, 120,140,160,
200共8个号
号数系指大端直径尺寸(mm), 各号锥度固定不变,均为1:20
同上
专用 圆锥
1:4,1:12,
1:50,7:24 等
多用于机器零件或某些刀具的特殊部位。例如,1: 50圆锥用于圆锥定位销和锥铰刀,7:24用于铣床
轴向力大(主要因为横刃的存在)
另外,钻头的两条主切削刃手工刃磨难以准确对称,致使钻孔具 有易引偏、孔径易扩大和孔壁质量差等工艺问题。
(3)改进措施: ①修磨横刃,使其为原长的1/5~1/7,增大该处前角,减少横刃的 不利影响。 ②直径大于15mm的钻头,磨分屑槽,切屑变窄便于排出。
③在两个主切削刃上磨出对称凹圆弧面,改善定心性能。
第2章 常规切削加工方法20111013
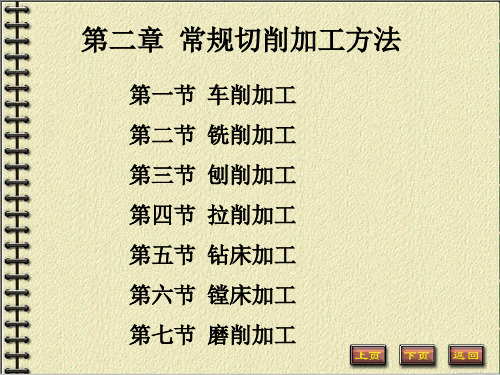
2)龙门刨床:如图所示,用于加工大型、重型工件上的各 龙门刨床:如图所示,用于加工大型、 所示 种平面和沟槽,亦可多工件同时加工。 种平面和沟槽,亦可多工件同时加工。主运动为工作台带 着工件的往复运动,进给运动通过刀具运动实现。 着工件的往复运动,进给运动通过刀具运动实现。
2、插床:插床其实就是一台将滑枕立起来的刨床。主要用 、插床:插床其实就是一台将滑枕立起来的刨床。 于加工键槽,也可以用来加工孔内的平面或者成形表面。 于加工键槽,也可以用来加工孔内的平面或者成形表面。 其主运动和进给运动与牛头刨床相同。 其主运动和进给运动与牛头刨床相同。插床的工作台除可 以进行横向、纵向运动外,一般还可以旋转。 以进行横向、纵向运动外,一般还可以旋转。 插床
当用卡盘扳手转动小锥齿轮时,大锥齿轮也随之转动, 当用卡盘扳手转动小锥齿轮时 , 大锥齿轮也随之转动 , 在大 锥齿轮背面平面螺纹的作用下,使三个卡爪同时向心移动或退出, 锥齿轮背面平面螺纹的作用下,使三个卡爪同时向心移动或退出, 以夹紧或松开工件。当工件直径较小时,可用正爪夹紧外圆, 以夹紧或松开工件。当工件直径较小时,可用正爪夹紧外圆,对于 内孔较大的盘套类工件,可用正爪反撑,当外圆直径较大时, 内孔较大的盘套类工件,可用正爪反撑,当外圆直径较大时,可用 反爪夹紧,如图所示。 反爪夹紧,如图所示。
四爪卡盘:四个爪不关联,各通过丝杆调整。 2)四爪卡盘:四个爪不关联,各通过丝杆调整。夹紧力较 不能自动定心,安装工件时需要进行找正。 大,不能自动定心,安装工件时需要进行找正。用于装夹外 形不规则工件或较大工件。 形不规则工件或较大工件。 四爪卡盘装夹
3)顶尖:长轴类工件使用。定位精度高,多次安装与调头, 顶尖:长轴类工件使用。定位精度高,多次安装与调头, 仍能保持轴线位置。 仍能保持轴线位置。 顶尖装夹
切削加工

莫氏 圆锥
米制 圆锥 专用 圆锥
1:4,1:12, 多用于机器零件或某些刀具的特殊部位。例如,1: 1:50,7:24 50圆锥用于圆锥定位销和锥铰刀,7:24用于铣床 等 主轴锥孔及铣刀杆的锥柄。
车锥面的方法: (1)小滑板转位法:主要用于单件小批生产中精度较低和长度 较短(≤ 100mm)的内锥面。 (2)尾座偏移法:用于单件或成批生产中轴类零件上较长的外 锥面。 (3)靠模法: 用于成批和大量 生产中较长的内 外锥面。 (4)宽刀法: 用于成批和大量 生产中较短 (≤ 20mm)的 内外锥面。
IT8~IT7 (精车) IT7~IT6 (精磨)
1.6~0.8 0.8~0.2
精密加工
在精加工基础上进一步提高精度 和降低表面粗糙度(其中不提高 精度,只降低表面粗糙度的加工 又称光整加工) 比精加工更高级的亚微米加工和 纳米加工,用于加工极个别的超 精密零件
IT5~IT3
0.1~ 0.008
研磨、珩磨、超 精加工、抛光等
几种典型机床的切削运动见表1.1。 表1.1 几种典型机床的切削运动
2、切削用量三要素
在切削运动的作用下,工件上有三个不断变 化的表面,见图1.3。 待加工表面:工件上将被切除切削层的表面。 已加工表面:工件上切除切屑后留下的表面。 加工表面 (过渡表面):工件上正在切削的表面。 它由切削刃形成,在下一切削行程,刀具或工 件的下一转里被切除,或由下一切削刃切除。 图1.3 工件表面
切削用量三要素:切削速度、进给量、吃刀量(背吃刀量、侧吃刀 量、进给吃刀量) (1)切削速度 ①主运动为回转运动: c v
(切削刃选定点相对于工件的主运动的瞬时速度)
(m s) v c dn (m min ) 1000 60 1000
常用的切削加工方法

常用的切削加工方法
常用的切削加工方法包括:
1. 铣削:使用铣床和铣刀将工件表面上的材料切削掉,形成所需的轮廓和表面质量。
2. 钻削:使用钻床和钻头在工件上进行钻孔加工,形成所需的孔径和孔深。
3. 车削:使用车床和车刀将工件固定在主轴上,通过旋转工件进行切削。
4. 磨削:使用磨床和磨料进行工件表面的修整和加工,以获得更高的精度和光洁度。
5. 刨削:使用刨床和刨刀将工件表面的材料切削掉,用于修整大型平面和表面。
6. 镗削:使用镗床和刀具将工件上的孔加工成所需的精度和尺寸。
7. 拉削:使用拉床和刀具对工件进行拉伸或拉压加工,以改变其形状和尺寸。
8. 搓削:使用搓床和滚轮对工件进行搓削加工,以形成齿轮、花键等零件。
9. 锯削:使用锯床和锯片对工件进行切割和分离,常用于金属材料和木材的加
工。
10. 焊削:使用焊接设备对工件进行切割和加工,常用于金属材料的切割和焊接。
以上方法仅为常见的切削加工方法,实际的切削加工方法还会根据具体的工件材料、形状和尺寸等要求进行选择和组合使用。
- 1、下载文档前请自行甄别文档内容的完整性,平台不提供额外的编辑、内容补充、找答案等附加服务。
- 2、"仅部分预览"的文档,不可在线预览部分如存在完整性等问题,可反馈申请退款(可完整预览的文档不适用该条件!)。
- 3、如文档侵犯您的权益,请联系客服反馈,我们会尽快为您处理(人工客服工作时间:9:00-18:30)。
•按车刀的
结构分类
整体式
焊接式 机夹式
焊接装配式
可转位车刀
• 成形车刀
切向成形车刀
二、铣削加工及铣刀
1. 铣削工艺
• 铣削加工是指铣刀旋转作主运动、工
件移动作进给运动的切削加工方法。
• 在卧式铣床、立式铣床、龙门铣床、
工具铣床以及各种专用铣床上进行。
• 可加工平面、沟槽和成形面等,还可
进行孔加工和分度工作。
钻床上加工时,工件不动,刀具作旋转 主运动,同时沿轴向移动作进给运动
钻孔
钻削加工
用钻头在实体材料上加工孔的方法称为钻孔
钻孔属于粗加工,其精度为IT13~IT11, Ra为50~12.5μm
扩孔
用扩孔刀具对工件上已经钻出、铸出或锻出的 孔作进一步加工的方法称为扩孔。
所用机床与钻孔相同。
钻床扩孔可用扩孔钻扩孔,也可用直径较大的 麻花钻扩孔。扩孔钻直径规格为10~100mm, 直径小于15mm者不扩孔。
拉刀
拉削是一种高生产率、高精度的 加工方法,拉削质量和拉削精度 主要依靠拉刀的结构和制造精度
拉刀由头部、颈部、过渡锥、前导 部、切削部、校准部和后导部组成
拉刀
刨刀
• 平面刨刀、偏刀、角度刀和成形刀等
常用 刨刀 及其 应用
• 刨削与铣削加工的比较
加工质量大致相当,经粗、精 加工之后均可达到中等精度 生产率一般刨削低于铣削 加工范围刨削不如铣削广泛 工时成本刨削低于铣削
刨削不如铣削应用广泛
插削 工艺
2. 插削加工及插刀
插削加工指用插刀对工件作铅直相 对直线往复运动的切削加工方法
可以在牛头刨床和龙门刨床上进行
可以加工平面、沟槽和直线型成形面等
刨削加工
• 刨削分为粗刨、半精刨和精刨。
粗刨后的精度为 IT13~IT11,Ra为25~12.5μm;
半精刨的精度为 IT10~IT9,Ra为6.3~3.2μm;
精刨的精度为 IT8~IT7,Ra为3.2~1.6μm ; 直线度可达0.04~0.08mm/m。
粗车
中小型锻件和铸件可直接粗车。粗车 精度为IT13~IT11,Ra为25~12.5μm。
半精车
尺寸精度要求不高的工件或精加工工 序之前可安排半精车。精度为 IT10~IT8,Ra为6.3~3.2μm。
精车
一般指最终加工,也可作为光 整加工的预加工工序。精度为 IT8~IT7,Ra为1.6~0.8μm。
扩孔加工精度比钻孔高,属于半精加工,其精 度为IT10~IT9;Ra为6.3~3.2μm。
铰孔
用铰刀在工件孔壁上切除微量金属层,以 提高尺寸精度和降低表面粗糙度的方法。
所用机床与钻孔相同。
可加工圆柱孔和圆锥孔。既可 进行机铰,也可进行手铰。
铰孔余量一般为0.05~0.25mm。 铰孔是在半精加工基础上进行的一种精加工。可分 为粗铰和精铰。粗铰精度为IT8~IT7,Ra为 1.6~0.8μm;精铰精度为IT7~IT6,Ra为0.8~0.4μm。
铣只适宜端铣刀或立铣刀加工平面
逆铣 和
顺铣
当铣刀和工件接触部分的旋转方向 与工件的进给方向相反时称为逆铣
当铣刀和工件接触部分的旋转方向 与工件的进给方向相同时称为顺铣
对称铣和不对称铣
当工件铣削宽度偏于端铣刀回转 中心一侧时,称为不对称铣削
当工件与铣刀处于对称位置时,称为对称铣
3. 铣刀
•多齿、多刃
抛物线型深孔钻
3. 镗削工艺
镗刀旋转作主运动、工件或镗刀作进给 运动的切削加工方法称为镗削加工
镗削加工主要在铣镗床、镗床上进行
在普通铣镗床上镗孔,粗镗的精度为ITl2~IT11, Ra为25~12.5μm;半精镗为IT10~IT9,Ra为 6.3~3.2μm;精镗为IT8~IT7,Ra为1.6~0.8μm
锪孔和 锪凸台
用锪钻(或代用刀具)加工平底 和锥面沉孔的方法称为锪孔、加 工孔端凸台的方法称为锪凸台。
锪孔一般在钻床上进行。
2. 钻削刀具
麻花钻
可在实心 材料上钻 孔,也可 用来扩孔
铰刀
分为圆柱手动铰刀和锥度铰刀
锥度铰刀常见的有1∶50锥度铰 刀和莫氏锥度铰刀两种
铰刀也属于定径刀具,适宜加工中批或大 批大量生产中不宜拉削的孔;适宜加工单 件小批生产中的小孔(0<10~15mm)、 细长孔(L/D>5)和定位销孔。
精细车
主要用于有色金属加工或要求很高的 钢制工件的最终加工。精度为 IT7~IT6,Ra为0.4~0.025μm。
• 车外圆 • 车床镗孔
• 车平面
• 车锥面 锥面有内锥面和外锥面之分 常用标准圆锥有莫氏、米制和专用圆锥 车锥面的方法有小刀架转位法、 尾座偏移法、靠模法和宽刀法等
• 车回转成形面
• 常用方法
靠模法
双手控制法
成形刀法
• 车螺纹
几个值得注 意的共同点
保证牙型 保证螺距P或导程L
保证中径D2(d2)
保证线数
保证旋向
2. 车削加工的特点
适用范围广泛 容易保证零件加工表面的位置精度 适宜有色金属零件的精加工 生产效率较高 生产成本较低
3. 车刀
• 车刀的种类
•按加工
表面特 征分类
铣镗床镗孔主要用于机座、箱体、支架 等大型零件上孔和孔系的加工。
铣镗床还可以加工外圆和平面
镗削除了加工孔之外,还可进行铣削和车削加工
在镗床上镗孔,按其进给形式可分为 主轴进给和工作台进给两种方式
镗削箱体孔系通常采用坐标法和镗模法
坐标法:将被加工各孔间的孔距尺寸换 算成两个相互垂直的坐标尺寸,再按坐 标尺寸调整机床主轴与工件在水平方向
复合铰刀 可调铰刀
钻 铰 刀
深孔钻
深孔加工时,由于孔的深径比较大,钻 杆细而长,刚性差,切削时很容易走偏 和产生振动,加工精度和表面粗糙度难 以保证,加之刀具在近似封闭的状态下 工作,因此必须特别注意导向、断屑和
排屑、冷却和润滑等问题
单刃外排屑深孔钻,又称枪钻
高效、高质量加工的内排屑深孔钻,又称 喷吸钻
铣削 加工 的 典型 表面
铣削
粗 铣
精度为IT13~IT11,Ra为25~12.5μm
半
粗 铣
精度为IT10~IT9,Ra为6.3~3.2μm
粗 精度为IT13~IT11,Ra为25~12.5μm 铣
• 工件在铣床上常用的装夹方法
平口虎钳装夹
压板螺栓装夹
V型铁装夹
分度头装夹 分度头装夹
铣平面
拉削加工的典型表面
拉削工件
拉削工件
拉削可分为粗拉和精拉 粗拉精度为IT8~IT7,Ra为1.6~0.8μm 精拉精度为IT7~IT6,Ra为0.8~0.4μm 拉圆孔:孔径为8~125mm,孔的深径比L/D≤5
拉圆 孔的 方法
拉孔内单键槽 拉平面 拉削平面是采用平面拉刀一次性成形
拉键槽的方法
插削加工指用插刀对工件作铅直相 对直线往复运动的切削加工方法 插削的加工精度比刨削的差, 插削加工的Ra为6.3~1.6μm
常用 插刀
3. 拉削加工及拉刀
拉削 工艺
拉削加工是指用拉刀加工工件 内、外表面的加工方法
拉削在拉床上进行 拉削一般在低速下工作
拉削可以加工内表面和外表面
拉刀的直线运动为主运动,拉削无进给运 动,其进给靠拉刀的每齿升高量来实现的
和铅直方向的相互位置来保证孔间距
镗模法:利用专用夹具——镗模镗孔
镗刀杆浮动接头
镗模法 镗孔
4. 镗刀
• 镗刀分为单刃镗刀与多刃镗刀两大类
单刃镗刀
微调镗刀
高速
高精度
ZMAC
多
镗刀
刃
镗
刀
微调镗刀
双刃 浮动 镗刀
四、刨削、插削和拉削加工 及其刀具
刨削 工艺
1. 刨削加工及刨刀
刨削加工是指用刨刀对工件作水平 相对直线往复运动的切削加工方法
圆柱平面铣刀 两面刃铣刀
面铣刀
三面刃铣刀
错齿刃铣刀
立铣刀 角度铣刀
键槽铣刀
成形铣刀
槽铣刀
• 模具铣刀
用于加工模具型腔或凸模成形表面
圆锥形 立铣刀
圆柱形球 头立铣刀
圆锥形球 头立铣刀
三、钻镗加工及钻头、镗刀
1. 钻削工艺
用钻头或铰刀、锪钻在工件上加 工孔的加工方法统称为钻削加工
可在台式钻床、立式钻床、摇臂钻床上进行, 也可以在车床、铣床、铣镗床等机床上进行
铣弧形槽时,可采用立铣刀, 并使用附件圆形工作台
铣花键
花键轴加工批量小时, 可在铣床上加工
2. 铣削方式
端铣和周铣
利用铣刀端部齿切削者称为端铣; 利用铣刀圆周齿切削者称为周铣
端铣加工的工件表面粗糙度值比周 铣的小,端铣的生产率也高于周铣
周铣的适应性比端铣好,周铣能用多种铣刀, 能铣削平面、沟槽、齿形和成形面等,而端
材料冷成形工艺基础(Ⅱ)
普通切削加工方法综述
普通切削加工方法综述
• 一、车削加工及车刀 • 二、铣削加工及铣刀 • 三、钻镗加工及钻头、镗刀 • 四、刨削、插削和拉削加工及其刀具
一、车ห้องสมุดไป่ตู้加工及车刀
1. 车削加工
• 指工件旋转作主运动、刀具移动作进给
运动的切削加工方法。
• 可在卧式车床、立式车床、转塔车床、
有端铣、 周铣和二 者兼有三
种方式
刀具有镶齿端 铣刀、套式立 铣刀、圆柱铣 刀、三面刃铣 刀和立铣刀等
铣沟槽
铣沟槽通常采用立铣刀加工
直角槽可直接用立铣刀铣出
V型槽则用角度铣刀直接铣出
T型槽和燕尾槽则应先用立铣刀切出 直角槽,然后再用角度铣刀铣出
铣螺旋槽时,则需要工件在作等速 移动的同时还要作等速旋转