解决窑尾漏料和改善窑系统通风能力的方法
浅谈窑尾漏料的原因与处理
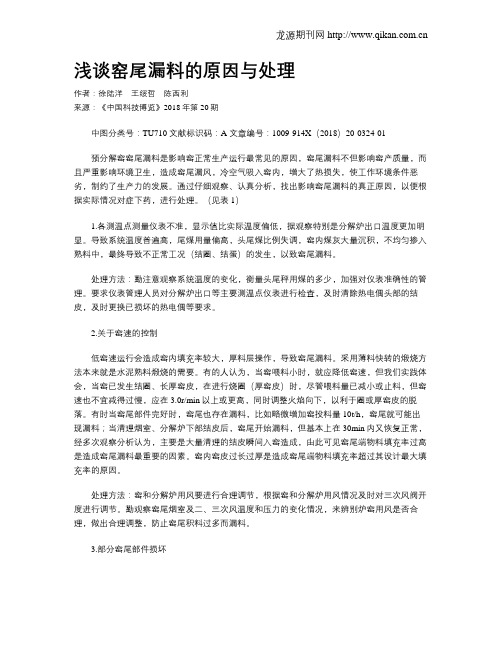
浅谈窑尾漏料的原因与处理作者:徐陆洋王绥哲陈西利来源:《中国科技博览》2018年第20期中图分类号:TU710 文献标识码:A 文章编号:1009-914X(2018)20-0324-01预分解窑窑尾漏料是影响窑正常生产运行最常见的原因,窑尾漏料不但影响窑产质量,而且严重影响环境卫生,造成窑尾漏风,冷空气吸入窑内,增大了热损失,使工作环境条件恶劣,制约了生产力的发展。
通过仔细观察、认真分析,找出影响窑尾漏料的真正原因,以便根据实际情况对症下药,进行处理。
(见表1)1.各测温点测量仪表不准,显示值比实际温度偏低,据观察特别是分解炉出口温度更加明显。
导致系统温度普遍高,尾煤用量偏高,头尾煤比例失调,窑内煤灰大量沉积,不均匀掺入熟料中,最终导致不正常工况(结圈、结蛋)的发生,以致窑尾漏料。
处理方法:勤注意观察系统温度的变化,衡量头尾秤用煤的多少,加强对仪表准确性的管理。
要求仪表管理人员对分解炉出口等主要测温点仪表进行检查,及时清除热电偶头部的结皮,及时更换已损坏的热电偶等要求。
2.关于窑速的控制低窑速运行会造成窑内填充率较大,厚料层操作,导致窑尾漏料。
采用薄料快转的煅烧方法本来就是水泥熟料煅烧的需要。
有的人认为,当窑喂料小时,就应降低窑速,但我们实践体会,当窑已发生结圈、长厚窑皮,在进行烧圈(厚窑皮)时,尽管喂料量已减小或止料,但窑速也不宜减得过慢,应在3.0r/min以上或更高,同时调整火焰向下,以利于圈或厚窑皮的脱落。
有时当窑尾部件完好时,窑尾也存在漏料,比如略微增加窑投料量10t/h,窑尾就可能出现漏料;当清理烟室、分解炉下部结皮后,窑尾开始漏料,但基本上在30min内又恢复正常,经多次观察分析认为,主要是大量清理的结皮瞬间入窑造成,由此可见窑尾端物料填充率过高是造成窑尾漏料最重要的因素。
窑内窑皮过长过厚是造成窑尾端物料填充率超过其设计最大填充率的原因。
处理方法:窑和分解炉用风要进行合理调节,根据窑和分解炉用风情况及时对三次风阀开度进行调节。
技术丨回转窑窑尾漏料的主要原因及解决方法

技术丨回转窑窑尾漏料的主要原因及解决方法回转窑窑尾漏料的主要原因及解决方法活性石灰生产中的回转窑是石灰烧成阶段的主要设备之一,回转窑窑尾漏料是影响窑正常生产运行比较常见的原因。
窑尾漏料造成窑尾漏风,冷空气吸入窑内,增大了热损失,不但影响回转窑的产量和质量,而且严重影响环境卫生,使工作环境条件恶劣,制约了正常的生产。
如何解决和避免窑尾漏料,清洁工作环境,通过生产中仔细观察、认真分析,找出影响窑尾漏料的真正原因,以便根据实际情况对症下药,进行处理,从而达到优质高产和创造一个清洁和谐的工作环境。
通过长期的生产线的设计、现场跟踪观察、分析认为,可能导致窑尾漏料的因素主要有以下几个方面:一、窑内物料填充率过高1、回转窑窑尾设计物料最大填充率计算在回转窑进行设计时,对应于相应的产量,回转窑有一个最大填充率,用以确定回转窑的相关尺寸。
回转窑最大填充率计算时取物料的存在为理想状态,以4×60m回转窑为例进行计算窑的最大填充率计算:图1:回转窑物料的填充状态若窑的缩口尺寸为2650mm,窑内耐火砖厚度为230mm,故R=1770mm,H=445mm,R-H=1325mm,θ=arcos(1325/1770)=41.53o式中:Φ2 ——窑尾缩口允许的填充率(%)θ ——物料填充区最高点与圆心的夹角(o);R ——窑尾部砌砖后的有效半径(m);H ——窑尾填充区弓形截面的高度(m)。
当料面的高度低于缩口时,理论上窑尾不漏料,当料面高度大于等于缩口高度时,就会出现漏料现象。
2、窑实际运转时窑尾物料的填充率首先用下式计算窑实际运转时窑尾物料的填充率:式中:Φ1 ——物料在窑尾的填充率(%)M ——每小时原料石灰石,即成品乘以料耗(t/h);W ——石灰石在窑尾部的运动速度(m/s);Di ——窑尾部砌砖后的有效直径(m);rm ——石灰石的比重(t/m3),一般取1.4(t/m3)。
物料在窑尾部的运动速度可以用下式计算:式中:i ——回转窑的斜度(°);Di ——窑尾部砌砖后的有效直径(m);n ——回转窑的转速(r/min);β ——石灰石的自然休止角,一般取35o。
预分解窑窑尾吐灰问题的解决
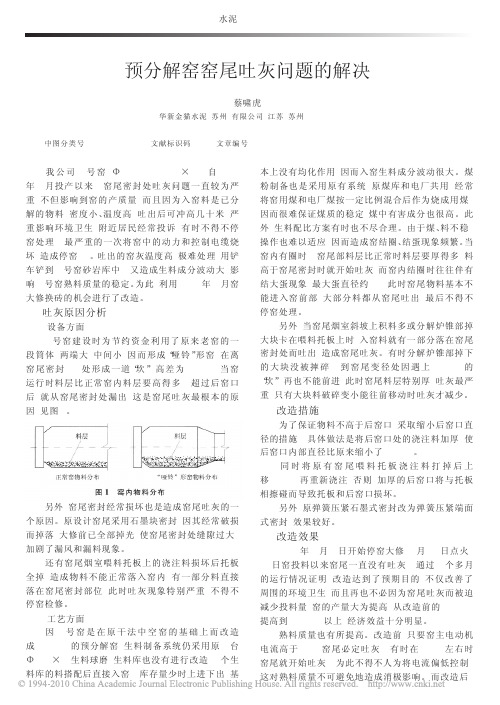
2007 年 2 月 8 日开始停窑大修, 3 月 11 日点火, 12 日窑投料以来窑尾一直没有吐灰, 通过 1 个多月 的运行情况证明, 改造达到了预期目的, 不仅改善了 周围的环境卫生, 而且再也不必因为窑尾吐灰而被迫 减少投料量, 窑的产量大为提高, 从改造前的 2 900t/d 提高到 3 300t/d 以上, 经济效益十分明显。
熟料质量也有所提高。改造前, 只要窑主电动机 电流高于260A 窑尾必定吐灰, 有时在 240A 左右时 窑尾就开始吐灰, 为此不得不人为将电流偏低控制, 这对熟料质量不可避免地造成消极影响。而改造后,
2007.No.9
水泥 CEMENT
- 33 -
一次跑生料事故的原因分析
李金红, 张景峰 ( 中国联合水泥集团有限公司 南阳分公司, 河南 镇平 474250)
中图分类号: TQ172.622.26 文献标识码: B 文章编号: 1002- 9877( 2007) 09- 0033- 01
我 公 司 一 期 3 000t/d 新 型 干 法 生 产 线 为 双 系 列 低压损五级旋风预热器带 N- MFC 分解炉系统, 窑规 格为 Φ4.3m×64m。采用石灰石、砂岩、硫酸渣和粉煤 灰 4 组分配料, 熟料三率值控制在: KH=0.90±0.02, n= 2.65 ±0.1, P =1.45 ±0.1; 入 窑 生 料 80μm 筛 余 要 求 ≤12%。从 2004 年 5 月投料以来窑系统运行一直很 稳定。2007 年 3 月公司组织对立磨及窑系统进行大 修, 大修后前几天生产正常, 但是 3 月 27 日窑出现一 次跑生料的事故。通过对事故的分析及采取有效的措 施, 现在窑运行正常。
2 改ห้องสมุดไป่ตู้措施
窑系统的异常现象及处理
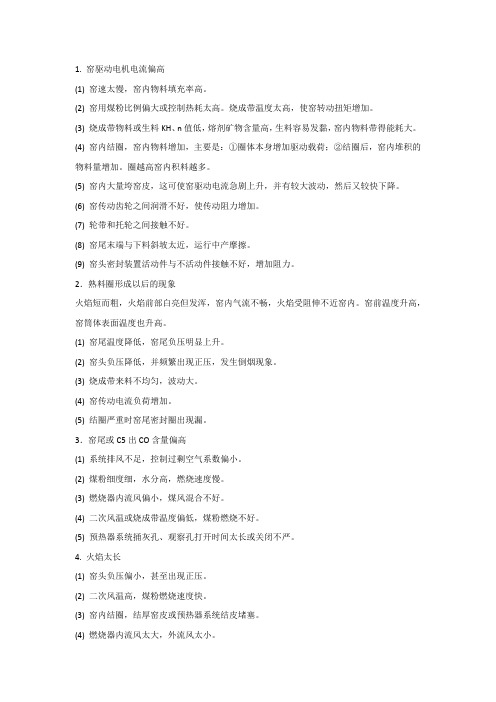
1. 窑驱动电机电流偏高(1) 窑速太慢,窑内物料填充率高。
(2) 窑用煤粉比例偏大或控制热耗太高。
烧成带温度太高,使窑转动扭矩增加。
(3) 烧成带物料或生料KH、n值低,熔剂矿物含量高,生料容易发黏,窑内物料带得能耗大。
(4) 窑内结圈,窑内物料增加,主要是:①圈体本身增加驱动载荷;②结圈后,窑内堆积的物料量增加。
圈越高窑内积料越多。
(5) 窑内大量垮窑皮,这可使窑驱动电流急剧上升,并有较大波动,然后又较快下降。
(6) 窑传动齿轮之间润滑不好,使传动阻力增加。
(7) 轮带和托轮之间接触不好。
(8) 窑尾末端与下料斜坡太近,运行中产摩擦。
(9) 窑头密封装置活动件与不活动件接触不好,增加阻力。
2.熟料圈形成以后的现象火焰短而粗,火焰前部白亮但发浑,窑内气流不畅,火焰受阻伸不近窑内。
窑前温度升高,窑筒体表面温度也升高。
(1) 窑尾温度降低,窑尾负压明显上升。
(2) 窑头负压降低,并频繁出现正压,发生倒烟现象。
(3) 烧成带来料不均匀,波动大。
(4) 窑传动电流负荷增加。
(5) 结圈严重时窑尾密封圈出现漏。
3.窑尾或C5出CO含量偏高(1) 系统排风不足,控制过剩空气系数偏小。
(2) 煤粉细度细,水分高,燃烧速度慢。
(3) 燃烧器内流风偏小,煤风混合不好。
(4) 二次风温或烧成带温度偏低,煤粉燃烧不好。
(5) 预热器系统捅灰孔、观察孔打开时间太长或关闭不严。
4. 火焰太长(1) 窑头负压偏小,甚至出现正压。
(2) 二次风温高,煤粉燃烧速度快。
(3) 窑内结圈,结厚窑皮或预热器系统结皮堵塞。
(4) 燃烧器内流风太大,外流风太小。
(5) 煤粉质量好,着火点低,燃烧速度高。
这种情况下,细度可以适当放宽。
5. 熟料吃火,结粒差(1) 熟料KH和n值太高,熔融相太少。
(2) 生料细度太粗,预烧差。
(3) 火焰太长,高温区集中,烧成温度偏低。
(4) 窑速太快,物料在窑内停留时间太短。
6. 熟料易结大块,立升重偏高(1) 熟料KH和n值低,熔融相尤其是Fe2O3含量大。
造成窑尾漏料的原因详解
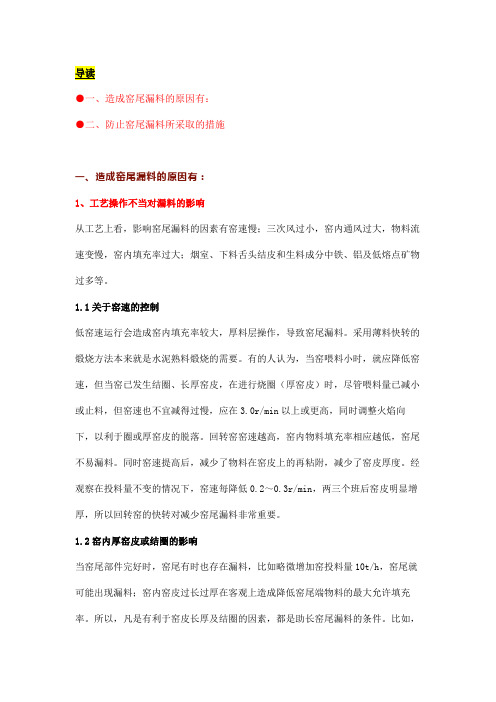
●一、造成窑尾漏料的原因有:●二、防止窑尾漏料所采取的措施一、造成窑尾漏料的原因有:1、工艺操作不当对漏料的影响从工艺上看,影响窑尾漏料的因素有窑速慢;三次风过小,窑内通风过大,物料流速变慢,窑内填充率过大;烟室、下料舌头结皮和生料成分中铁、铝及低熔点矿物过多等。
1.1关于窑速的控制低窑速运行会造成窑内填充率较大,厚料层操作,导致窑尾漏料。
采用薄料快转的煅烧方法本来就是水泥熟料煅烧的需要。
有的人认为,当窑喂料小时,就应降低窑速,但当窑已发生结圈、长厚窑皮,在进行烧圈(厚窑皮)时,尽管喂料量已减小或止料,但窑速也不宜减得过慢,应在3.0r/min以上或更高,同时调整火焰向下,以利于圈或厚窑皮的脱落。
回转窑窑速越高,窑内物料填充率相应越低,窑尾不易漏料。
同时窑速提高后,减少了物料在窑皮上的再粘附,减少了窑皮厚度。
经观察在投料量不变的情况下,窑速每降低0.2~0.3r/min,两三个班后窑皮明显增厚,所以回转窑的快转对减少窑尾漏料非常重要。
1.2窑内厚窑皮或结圈的影响当窑尾部件完好时,窑尾有时也存在漏料,比如略微增加窑投料量10t/h,窑尾就可能出现漏料;窑内窑皮过长过厚在客观上造成降低窑尾端物料的最大允许填充率。
所以,凡是有利于窑皮长厚及结圈的因素,都是助长窑尾漏料的条件。
比如,生料成分波动的影响,由于生料与原煤灰分含量的无规律变动,会使液相量或大或小,操作无法控制用煤量;更无法使配料方案避免熔剂矿物过多,液相提前出现,造成窑结皮、结圈、结蛋,以致窑尾漏料。
如石灰石中含有一定量的白云石,由于较高的MgO,使熟料最低共熔温度降低,液相提前出现,造成窑皮变长增厚。
1.3后窑口及上升烟道结皮的影响当清理烟室、分解炉下部结皮后,窑尾开始漏料,但在30min内又恢复正常,这主要是大量清理的结皮瞬间入窑,使得本来受窑皮过厚限制的窑尾端物料填充率更容易被突破造成窑尾漏料。
另外,窑尾烟室及下料舌头结皮,同样会导致窑尾漏料,应勤观察、勤发现,及时清理结皮防止窑尾漏料。
中控操作员窑磨试题-附答案

中控窑操作基本知识一、填空题:1、我公司充气梁篦冷机余热回收的主要用途(入窑二次用)、(入分解炉三次用)、(废气余热利用)。
2、分解炉内燃料的燃烧方式为(无焰燃烧)和(辉焰燃烧),传热方式为(对流)为主。
3、篦式冷却机的篦床传动主要由(液压)和(机械)两种方式。
4、熟料中Cao经高温煅烧后一部分不能完全化合,而是以(游离钙)形式存在,这种经高温煅烧后不能完全化合的Cao是熟料(安定性)不良的主要因至素。
5、旋窑生产用煤时,为了控制火焰的形状和高温带长度,要求煤具有较高的(挥发性)和(发热量),以用(烟煤)为宜。
6、熟料急冷主要是防止( C2S )矿物在多晶转变中产生不利的晶体转变。
7、我公司篦冷机一段熟料料层一般控制在( 550-700MM),冷却机热回收效率能够达到(71-75%)。
8、煤灰的掺入,会使熟料的饱和比(降低0.04~0.16 ),硅率(降低0.05~0.2),铝率(提高0.05~0.3 )。
9、与传统的湿法、半干法水泥生产相比,新型干法水泥生产具有(均化)、(节能)、(环保)、(自动控制)、(长期安全运转)和(科学管理)的方大保证体系。
10、旋风筒的作用主要是(气固分离),传热只完成(6~12.5%)。
11、在故障停窑时,降温一定要控制好,一般都采用(关闭各挡板)保温,时间较长时,其降温的速率不要超过(100摄氏度/小时),以免造成耐火材料的爆裂。
12、轮带滑移量是反映(轮带)与(酮体)的相对位移。
13、我公司燃烧器为(四通道)燃烧器,其中中心风的作用为(产生回流)、(保护燃烧器)、(稳定火焰)。
14、篦冷机的规格为( tc-12102 ),篦床面积为( 119.3立方米)。
15、预热器采用高效低压损大锅壳结构的旋风筒,其目的为(最大的损热;最低的阻力;最低的何所亞键为民水泥考试题库投资;最安全的运转.)16、预热器一般分为(旋风式)预热器和(立筒式)预热器。
17、影响物料在预热器旋风筒内预热的因素①(内筒插入的深度)、②( 进风口的结构和类型 )。
试述水泥厂对窑尾废气处理系统的改造方法
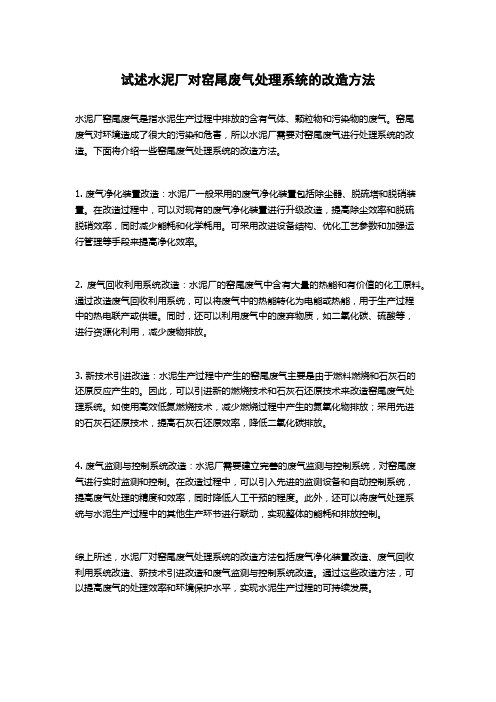
试述水泥厂对窑尾废气处理系统的改造方法水泥厂窑尾废气是指水泥生产过程中排放的含有气体、颗粒物和污染物的废气。
窑尾废气对环境造成了很大的污染和危害,所以水泥厂需要对窑尾废气进行处理系统的改造。
下面将介绍一些窑尾废气处理系统的改造方法。
1. 废气净化装置改造:水泥厂一般采用的废气净化装置包括除尘器、脱硫塔和脱硝装置。
在改造过程中,可以对现有的废气净化装置进行升级改造,提高除尘效率和脱硫脱硝效率,同时减少能耗和化学耗用。
可采用改进设备结构、优化工艺参数和加强运行管理等手段来提高净化效率。
2. 废气回收利用系统改造:水泥厂的窑尾废气中含有大量的热能和有价值的化工原料。
通过改造废气回收利用系统,可以将废气中的热能转化为电能或热能,用于生产过程中的热电联产或供暖。
同时,还可以利用废气中的废弃物质,如二氧化碳、硫酸等,进行资源化利用,减少废物排放。
3. 新技术引进改造:水泥生产过程中产生的窑尾废气主要是由于燃料燃烧和石灰石的还原反应产生的。
因此,可以引进新的燃烧技术和石灰石还原技术来改造窑尾废气处理系统。
如使用高效低氮燃烧技术,减少燃烧过程中产生的氮氧化物排放;采用先进的石灰石还原技术,提高石灰石还原效率,降低二氧化碳排放。
4. 废气监测与控制系统改造:水泥厂需要建立完善的废气监测与控制系统,对窑尾废气进行实时监测和控制。
在改造过程中,可以引入先进的监测设备和自动控制系统,提高废气处理的精度和效率,同时降低人工干预的程度。
此外,还可以将废气处理系统与水泥生产过程中的其他生产环节进行联动,实现整体的能耗和排放控制。
综上所述,水泥厂对窑尾废气处理系统的改造方法包括废气净化装置改造、废气回收利用系统改造、新技术引进改造和废气监测与控制系统改造。
通过这些改造方法,可以提高废气的处理效率和环境保护水平,实现水泥生产过程的可持续发展。
预分解窑窑内通风量的优化
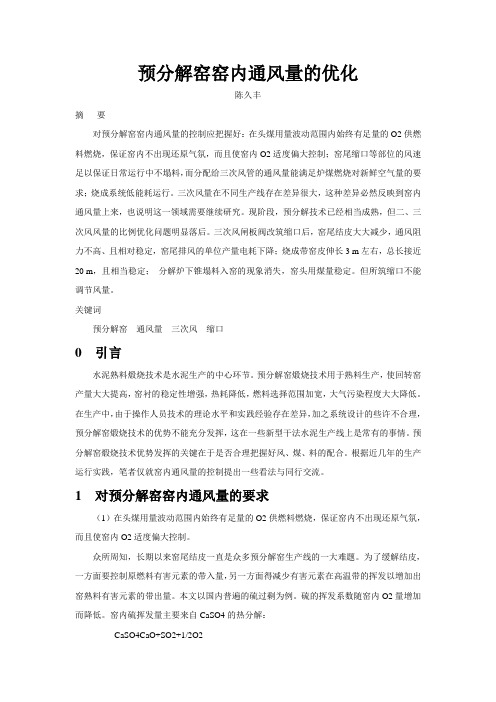
预分解窑窑内通风量的优化陈久丰摘要对预分解窑窑内通风量的控制应把握好:在头煤用量波动范围内始终有足量的O2供燃料燃烧,保证窑内不出现还原气氛,而且使窑内O2适度偏大控制;窑尾缩口等部位的风速足以保证日常运行中不塌料,而分配给三次风管的通风量能满足炉煤燃烧对新鲜空气量的要求;烧成系统低能耗运行。
三次风量在不同生产线存在差异很大,这种差异必然反映到窑内通风量上来,也说明这一领域需要继续研究。
现阶段,预分解技术已经相当成熟,但二、三次风风量的比例优化问题明显落后。
三次风闸板阀改筑缩口后,窑尾结皮大大减少,通风阻力不高、且相对稳定,窑尾排风的单位产量电耗下降;烧成带窑皮伸长3 m左右,总长接近20 m,且相当稳定;分解炉下锥塌料入窑的现象消失,窑头用煤量稳定。
但所筑缩口不能调节风量。
关键词预分解窑通风量三次风缩口0 引言水泥熟料煅烧技术是水泥生产的中心环节。
预分解窑煅烧技术用于熟料生产,使回转窑产量大大提高,窑衬的稳定性增强,热耗降低,燃料选择范围加宽,大气污染程度大大降低。
在生产中,由于操作人员技术的理论水平和实践经验存在差异,加之系统设计的些许不合理,预分解窑煅烧技术的优势不能充分发挥,这在一些新型干法水泥生产线上是常有的事情。
预分解窑煅烧技术优势发挥的关键在于是否合理把握好风、煤、料的配合。
根据近几年的生产运行实践,笔者仅就窑内通风量的控制提出一些看法与同行交流。
1 对预分解窑窑内通风量的要求(1)在头煤用量波动范围内始终有足量的O2供燃料燃烧,保证窑内不出现还原气氛,而且使窑内O2适度偏大控制。
众所周知,长期以来窑尾结皮一直是众多预分解窑生产线的一大难题。
为了缓解结皮,一方面要控制原燃料有害元素的带入量,另一方面得减少有害元素在高温带的挥发以增加出窑熟料有害元素的带出量。
本文以国内普遍的硫过剩为例。
硫的挥发系数随窑内O2量增加而降低。
窑内硫挥发量主要来自CaSO4的热分解:CaSO4CaO+SO2+1/2O2这是一个可逆反应。
回转窑的窑头窑尾减少漏风漏料的措施

回转窑的窑头窑尾减少漏睡料的髓目录刖百 (1)1.径向式密封的减漏措施 (1)2.轴向摩擦密封的防漏措施 (2)3.某公司回转窑窑头窑尾密封漏料治理 (3)3.1.存在的问题 (3)3.2.技改方案 (3)3.3.技改效果 (4)结束语 (4)刖百窑头冷风进入窑内,不但破坏了入窑的气体流场,且和二次风混合后,降低了二次风温,在不利于燃烧的同时,也增加了煤耗。
窑尾漏风危害更大,不但降低了尾温,增加了煤耗,还极易造成结皮,影响通风,还影响着产量、质量的发挥,即由于漏风增大了高温风机的负荷,同样条件下高温风机拉废气的量减少,会严重影响系统能力的发挥。
所以危害很大,必须予以重视。
同样窑头、窑尾的漏料危害也不小.首先污染环境,其次危害密封件的寿命。
下面根据笔者的经验谈谈降低窑头、窑尾漏风、漏料的方法与措施,望能起到借鉴作用。
对于窑头尾的密封形式,现在以接触式为主。
一是径向接触式密封,由装在窑上的摩擦圈、弹性薄板(鱼鳞片)及涨紧装置组成。
轴向式密封主要有固定和活动摩擦环及气缸或弹簧装置组成。
1.径向式密封的减漏措施1,保证摩擦圈与窑的连接可靠,保证运转稳定。
在安装摩擦圈时,无论窑的径向跳动如何,要以摩擦圈的径向跳动为准来找正,控制其径向跳动小于12毫米。
2.摩擦圈与鱼鳞板接触的范围内不得有焊瘤、凸台、凹坑凹槽,焊缝需打磨平整,防止运行中挂坏鱼鳞片和鱼鳞的抖动造成漏风漏料。
3.摩擦圈与窑头护铁要扣和严实,防止冷却风进入,也防止热风外串对窑筒体及摩擦圈造成伤害。
4,摩擦圈与鱼鳞片之间可适当润滑,减少磨损。
5.要保证窑的正常串动,避免将摩擦圈磨成凹槽,一旦形成台阶,在窑串动时就会折坏鱼鳞片。
6.必须保证摩擦圈与筒体的冷风冷却,防止摩擦圈变形引起不必要的漏风漏料。
7.鱼鳞片涨紧适当。
以能把鱼鳞片与摩擦圈紧密贴合为准,不要过紧。
不然磨损较快。
8.在窑头尾安装鱼鳞片的喇叭口处要设置排灰装置,保证在摩擦圈与鱼鳞片之间有集灰时能够及时排出,以避免集料对密封的破坏,避免局部密封不良引起漏风漏料。
解决窑尾漏料和改善窑系统通风能力的方法
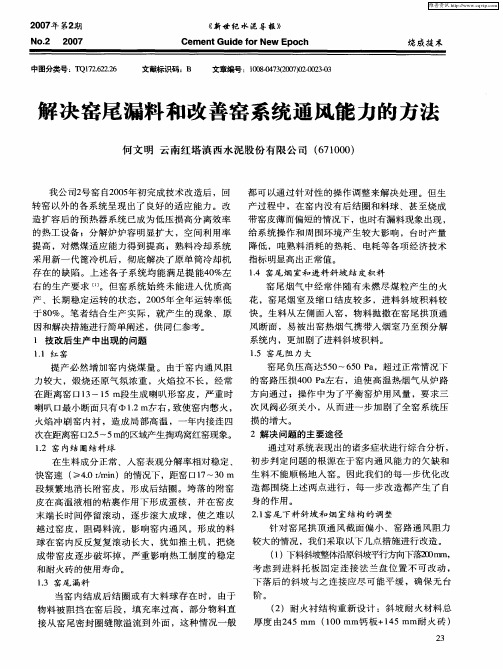
都 可 以通 过 针 对 性 的 操 作调 整 来解 决 处 理 。但 生 产 过 程 中 ,在 窑 内没 有 后结 圈 和 料球 、甚 至烧 成
造扩容 后的预 热器 系统 已成为低压损高分离效率 带 窑 皮薄 而 偏 短 的情 况 下 ,也 时 有漏 料 现象 出现 , 的 热 工设 备 ;分 解 炉 炉容 明显 扩 大 ,空 间 利 用率 给 系 统 操 作 和 周 围环 境 产 生 较 大 影 响 ,台 时 产 量 提 高 ,对 燃 煤 适 应 能 力 得 到提 高 ;熟 料 冷 却 系 统 降低 ,吨 熟料 消 耗 的 热耗 、 电耗 等 各 项 经 济 技 术
15 窑 尾 阻 力 大 .
1 技 改 后 生产 中 出现 的 问题
11 红 窑 .
提 产 必 然增 加 窑 内烧 煤 量 。 由 于 窑 内通 风 阻 力 较大 ,煅烧 还 原气 氛 浓 重 ,火焰 拉 不 长 ,经 常
窑 尾 负压 高 达 5 0 5 a 5 ~6 0P ,超 过 正 常 情 况 下
维普资讯
2 0 年 第2 07 期
No. 2 0 2 07
新世 纪 水 泥导报
Ce n ief r e E o h me t Gu d w p c o N
文献标识码 :B 文章编号 :10 - 7 (37 202 - 08 43 1 ) - 3 3 0 20 0 0 0
烧 威技 术
中图分类号 :T 7 . 2 6 Q12 2 . 6 2
解 决 窑 尾漏 料和 改 善窑 系统 通 风能 力的 方法
何 文明 云 南红塔滇 西水 泥股份 有限公 司 (7 改 造后 , 回 号 05 转 窑 以外 的各 系 统 呈 现 出 了 良好 的适 应 能 力 。 改
新型干法窑常见工艺故障原因分析及应对措施
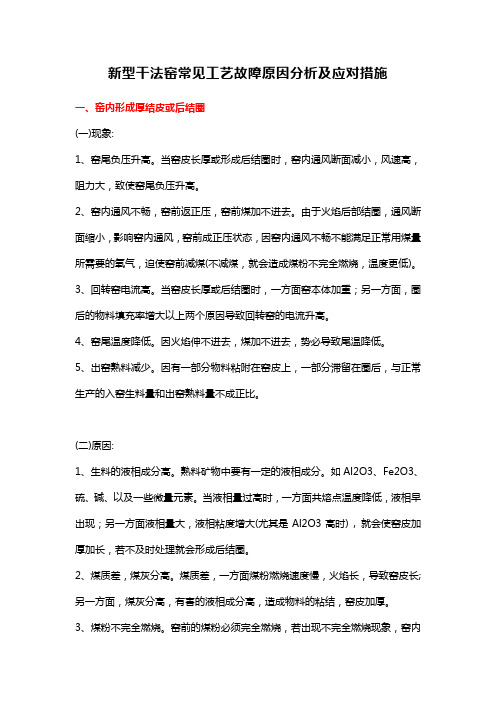
新型干法窑常见工艺故障原因分析及应对措施一、窑内形成厚结皮或后结圈(一)现象:1、窑尾负压升高。
当窑皮长厚或形成后结圈时,窑内通风断面减小,风速高,阻力大,致使窑尾负压升高。
2、窑内通风不畅,窑前返正压,窑前煤加不进去。
由于火焰后部结圈,通风断面缩小,影响窑内通风,窑前成正压状态,因窑内通风不畅不能满足正常用煤量所需要的氧气,迫使窑前减煤(不减煤,就会造成煤粉不完全燃烧,温度更低)。
3、回转窑电流高。
当窑皮长厚或后结圈时,一方面窑本体加重;另一方面,圈后的物料填充率增大以上两个原因导致回转窑的电流升高。
4、窑尾温度降低。
因火焰伸不进去,煤加不进去,势必导致尾温降低。
5、出窑熟料减少。
因有一部分物料粘附在窑皮上,一部分滞留在圈后,与正常生产的入窑生料量和出窑熟料量不成正比。
(二)原因:1、生料的液相成分高。
熟料矿物中要有一定的液相成分。
如Al2O3、Fe2O3、硫、碱、以及一些微量元素。
当液相量过高时,一方面共熔点温度降低,液相早出现;另一方面液相量大,液相粘度增大(尤其是Al2O3高时) , 就会使窑皮加厚加长,若不及时处理就会形成后结圈。
2、煤质差,煤灰分高。
煤质差,一方面煤粉燃烧速度慢,火焰长,导致窑皮长; 另一方面,煤灰分高,有害的液相成分高,造成物料的粘结,窑皮加厚。
3、煤粉不完全燃烧。
窑前的煤粉必须完全燃烧,若出现不完全燃烧现象,窑内就会出现还原气氛,还原气氛会使三价铁还原二价铁,液相粘度增大,窑皮加厚。
4、喷煤管的火焰长而不集中。
火焰长,窑皮就长,窑皮过长就为结圈奠定了基础;一旦生料成分发生变化或操作不当,就会形成后结圈。
(三)应对措施:一旦如前述异常现象出现时,我们就可以判断有形成长厚窑皮或后结圈的可能,有针对性地采取相应的措施,就会转危为安。
具体措施如下:1、调整生料成分。
根据化验室提供的生、熟料全分析结果, 若液相成分或有害成分高,应通知化验室及时调整生料指标,尤其是要提高硅酸率的指标。
回转窑窑尾漏料的主要原因及解决方法
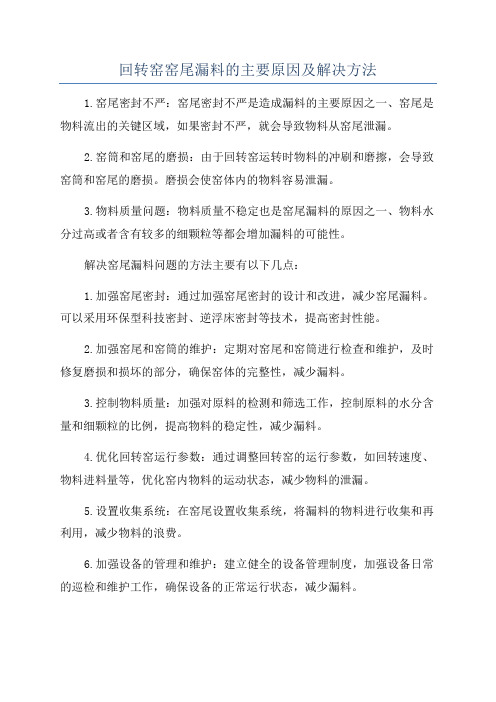
回转窑窑尾漏料的主要原因及解决方法
1.窑尾密封不严:窑尾密封不严是造成漏料的主要原因之一、窑尾是物料流出的关键区域,如果密封不严,就会导致物料从窑尾泄漏。
2.窑筒和窑尾的磨损:由于回转窑运转时物料的冲刷和磨擦,会导致窑筒和窑尾的磨损。
磨损会使窑体内的物料容易泄漏。
3.物料质量问题:物料质量不稳定也是窑尾漏料的原因之一、物料水分过高或者含有较多的细颗粒等都会增加漏料的可能性。
解决窑尾漏料问题的方法主要有以下几点:
1.加强窑尾密封:通过加强窑尾密封的设计和改进,减少窑尾漏料。
可以采用环保型科技密封、逆浮床密封等技术,提高密封性能。
2.加强窑尾和窑筒的维护:定期对窑尾和窑筒进行检查和维护,及时修复磨损和损坏的部分,确保窑体的完整性,减少漏料。
3.控制物料质量:加强对原料的检测和筛选工作,控制原料的水分含量和细颗粒的比例,提高物料的稳定性,减少漏料。
4.优化回转窑运行参数:通过调整回转窑的运行参数,如回转速度、物料进料量等,优化窑内物料的运动状态,减少物料的泄漏。
5.设置收集系统:在窑尾设置收集系统,将漏料的物料进行收集和再利用,减少物料的浪费。
6.加强设备的管理和维护:建立健全的设备管理制度,加强设备日常的巡检和维护工作,确保设备的正常运行状态,减少漏料。
7.加强员工培训:提高员工的操作技能和安全意识,加强对窑尾漏料问题的培训,使员工能够及时发现和处理窑尾漏料问题。
综上所述,解决回转窑窑尾漏料问题需要综合考虑密封技术、设备维护、物料质量控制等因素,通过合理的措施和方法,可以有效减少窑尾漏料,提高生产效率和能源利用率。
窑尾密封装置改进

窑尾密封装置改进【摘要】回转窑窑尾的密封效果,对水泥生产有极为重要的作用。
当密封失效或不良时,窑尾吸入过量的冷空气,会增加窑尾分解炉的燃料损耗、窑尾结皮堵塞;并增大排风机的负荷电耗,同时溢出大量粉尘,严重恶化生产环境。
本文简单阐述我对窑尾密封装置进行的一次技术改造。
【关键词】水泥窑;回转窑;窑尾密封水泥生产中,几乎每一条新型干法窑生产线烧成系统中都存在着程度不等的漏风、漏灰、漏料现象。
上述现象的存在,对系统的热耗、电耗、产质量、生产稳定运行、生产环境等方面均会带来负面影响。
回转窑窑头密封装置及窑尾密封装置设计的不好会直接导致漏风、漏灰、漏料,从而对烧成系统的影响。
以煤粉为燃料的各种规模新型干法窑为例,煤粉燃烧后产生的理论烟气量约为0.8~1.2Nm3/kg.cl,而预热器出口的废气量约为1.5~1.9Nm3/kg.cl,这部分差值除过剩空气、盐类分解、自由水蒸发、高岭土脱水、空气带入湿含量以外,约有0.2~0.5Nm3/kg.cl的废气量来自于漏风,管理不善的企业甚至还远远超出此范围。
这部分的漏风会给系统生产带来较大影响,主要表现在如下方面:(1)能耗提高,产质量下降。
对于回转窑系统,冷风的漏入减少了由冷却机进入窑内的二次风量和回收入窑的总热量;对于三次风管和分解炉系统,冷风的漏入减少了经冷却机、窑头罩进入炉内的三次风量和回收入炉的总热量;对于预热分解系统,冷风的漏入还降低了系统的分离效率和换热效率,提高了热耗,并降低了烧成系统的有效通风能力,导致系统操作不稳定,降低了产量和质量;有效通风能力的降低,还直接导致了单位产品电耗的增加。
我们以某工厂实际的生产数据为计算依据,当窑头、窑尾采用传统形式的密封,总漏风系数达到15%时,热工计算的结果如下:a、窑尾温度降低57℃,不采取措施会影响热工制度、影响入窑分解率,降低窑的产量;b、若采取措施使尾温升高57℃,则需增加热耗109kJ/kg.cl,折标准煤3.73kg/t.cl,对日产2500t熟料生产线,年增加标准煤用量2890吨,以标准煤平均价格600元/t计,年增加采购燃煤的费用为173万元;c、漏风引起的产量降低:8.1%;d、漏风引起的高温风机电耗增加量0.49kWh/t.cl,对日产2500t熟料生产线,年增加电耗38.0万kwh,以工业用电平均价格0.5元/ kWh计,年增加外购电费用19万元;(2)漏风是预热分解系统粘结堵塞的重要原因,进而降低系统运转率,增加了运行成本,而人工处理时还会带来系统热耗的上升,增加劳动强度,带来环境污染。
改善窑系统通风的几点措施
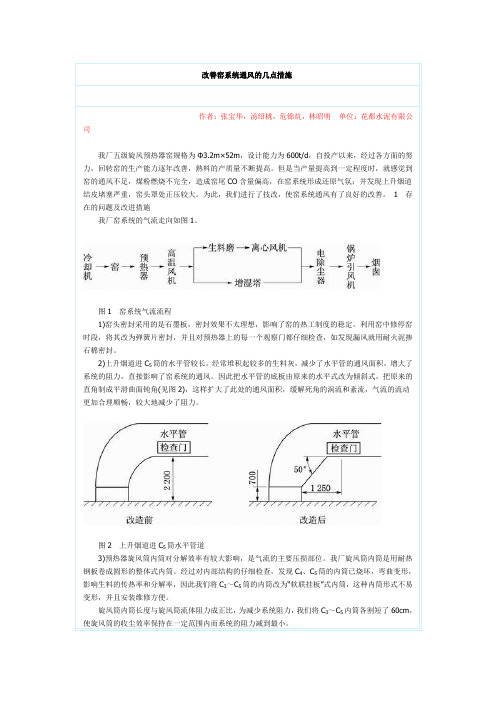
C4
C5
风门开度/%
电流/A
风门开度/%
电流/A
改造前
0.10
56
0.05
138
25.2
2.0
92.0
-6.5
-3.0
-2.3
-0.9
100
25
100
152
改造后
0.06பைடு நூலகம்
59
0.033
136
25.8
2.2
92.99
-6.0
-2.8
-2.1
-0.6
100
24
100
150
搜索更多相关文章:回转窑熟料提高操作预热器
2)上升烟道进C5筒的水平管较长,经常堆积起较多的生料灰,减少了水平管的通风面积,增大了系统的阻力,直接影响了窑系统的通风。因此把水平管的底板由原来的水平式改为倾斜式,把原来的直角制成平滑曲面钝角(见图2),这样扩大了此处的通风面积,缓解死角的涡流和紊流,气流的流动更加合理顺畅,较大地减少了阻力。>Eqr/~__Q
;?
.w!|6
g=L80$_1_
]mT2a8`c.r
图3异型汇风箱结构:hFKmo_y#_
U__Wo*_%&J
2改造效果H?_cJ'Q, 5
经过对窑系统的这些改造,结合配料方案及操作参数的优化,窑系统的通风、结皮情况有很大的改善,减少了以往由于结皮堵塞而停窑的次数,熟料的产质量也有一定的提高。改造后效果见表1。_ K_GJ *h
改善窑系统通风的几点措施])_$Rw $`w
作者:张宝华,汤绍桃,危锦炕,林昭明 单位:花都水泥有限公司#'oGtF_Cd`
&bT \4__
窑系统漏风处理方法
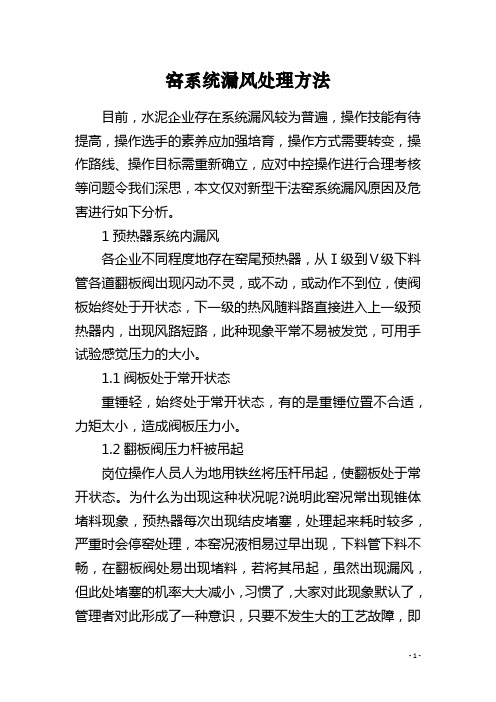
窑系统漏风处理方法目前,水泥企业存在系统漏风较为普遍,操作技能有待提高,操作选手的素养应加强培育,操作方式需要转变,操作路线、操作目标需重新确立,应对中控操作进行合理考核等问题令我们深思,本文仅对新型干法窑系统漏风原因及危害进行如下分析。
1预热器系统内漏风各企业不同程度地存在窑尾预热器,从Ⅰ级到Ⅴ级下料管各道翻板阀出现闪动不灵,或不动,或动作不到位,使阀板始终处于开状态,下一级的热风随料路直接进入上一级预热器内,出现风路短路,此种现象平常不易被发觉,可用手试验感觉压力的大小。
1.1阀板处于常开状态重锤轻,始终处于常开状态,有的是重锤位置不合适,力矩太小,造成阀板压力小。
1.2翻板阀压力杆被吊起岗位操作人员人为地用铁丝将压杆吊起,使翻板处于常开状态。
为什么为出现这种状况呢?说明此窑况常出现锥体堵料现象,预热器每次出现结皮堵塞,处理起来耗时较多,严重时会停窑处理,本窑况液相易过早出现,下料管下料不畅,在翻板阀处易出现堵料,若将其吊起,虽然出现漏风,但此处堵塞的机率大大减小,习惯了,大家对此现象默认了,管理者对此形成了一种意识,只要不发生大的工艺故障,即便是存在一点内漏风,热耗高一点,不会出现大的工艺故障,对系统没有大阻碍,总比出事好,久而久之形成习惯。
另一种原因是预热器系统常出下掉落浇注料块,耐火砖,磨损的内挂片,脱落的大块结皮,被卡在翻板阀处,出现块状物料的卡堵,为防止大块物料堵塞下料管,采取用铁丝吊起翻板阀杆,使翻板阀处于常开状态。
这种将翻板阀杆吊起使阀板处于常开状态的做法是不符合新型干法水泥熟料煅烧工艺要求的。
必需树立正确的理念,杜绝内漏风的出现,其它方面有问题,要想方法去解决。
比如是配料方面的原因,要从配料上找原因进行分析解决,若是浇料量砌筑方面上的问题,如材料问题,浇注施工工艺问题,养护问题,耐火砖质量,砌筑问题等,从各个方面去找,但不能采用吊起翻板阀来缓解这种问题,甚至掩盖问题,其后果使系统恶性循环。
窑尾废气系统异常的原因分析及解决措施

-38-
ce^ snr
2021.N0.6
时间电流波动,通知现场岗位查看,发现入库斗式提 因。鉴于熟料库位高,决定烧空煤粉仓,停窑进行详
升 机 尾 冒 烟 ,增 湿 塔 下 0 6 回 灰 拉 链 机 、窑尾大布袋 细检查。主要排查项目如下:
收尘丨〇拉链机、余 热 发 电 PH炉 拉 链 机 现 场 回 灰 量 增
窑尾袋收尘器回灰0 6 型号FU4 1 0 X 28680 mm,功 率 15 kW,额定
拉链机(生料) 输 送 能 力 110 m3/h ,额 定 电 流 31.37 A
窑尾袋收尘器回灰0 7 型号FU500X 43 150 mm,功 率 37 kW,额定
拉链机(生料) 输 送 能 力 160 m3/h ,额定电 流 71.1 A
(1) 重点检查预热器(:,、(:2 内 筒及锥体是否异常。
(2) 检查增湿塔底部锥体及出风管道是否积料。
(3) 检查生料立磨出磨旋风筒内部是否异常。
(4)
全 面 检 查 窑 尾 大 布 袋 箱 体 内 部 、滤 袋 、喷吹
系统是否异常。 (5) 检查PH锅炉进口管道和旁路管道是否异常。
(6) 检查其他工艺管道及细节问题。
窑 尾 袋 收 尘 器 回 灰 1 0 型 号 FU4 1 0 X 31 415 mm,功 率 18.5 kW ,额
拉链机(生料及窑灰) 定 输 送 能 力 110 m3/h ,额定电流44.8 A
2 出现的问题 在 2018年 7 月8~13日生产过程中发生多次窑废
气 系 统 不 正 常 现 象 ,造 成 生 产 困 难 ,具 体 表 现 在 : (1)窑 尾 袋 收 尘 器 压 差 变 大 或 入 口 正 压 。
φ4m×43m短窑窑尾漏料原因的探讨
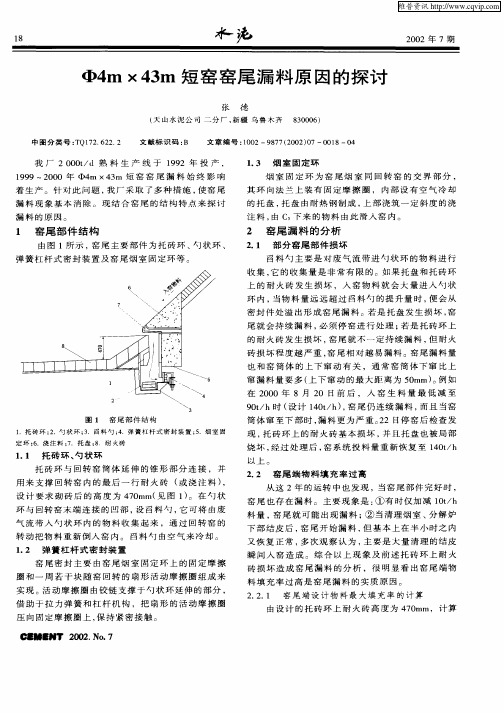
也 和 窑 简 体 的 上 下 窜 动 有 关 ,通 常 窑简 体 下 窜 比上 窜 漏 料 量 要 多 ( 下 窜 动 的 最 大 距 离 为 5 rm) 例 如 上 0 a 。 在 20 0 0年 8月 2 日前 后 ,人 窑 生 料 量 最 低 减 至 0 9 t h时 ( 计 1 0 / ) 窑 尾 仍 连 续 漏 料 , 且 当 窑 0/ 设 4 th , 而
料填充率过 高是窑尾漏料 的实质原 因。
实 现 。活 动摩 擦 圈 由铰 链 支撑 于 勺 状 环 延 伸 的 部 分 ,
借 助 于 拉 力 弹 簧 和 杠 杆 机 构 ,把 扇 形 的活 动 摩 擦 圈
压 向固 定 摩 擦 圈 上 , 持 紧 密 接 触 。 保
C硼 暑町 ‘2 0 . o 7 02 N .
以上 。
1 1 托 砖 环 、 状 环 . 勺 托砖 环 与 回 转 窑 简 体 延 伸 的 锥 形 部 分 连 接 ,并
用 来 支 撑 回转 窑 内 的 最 后 一 行 耐 火 砖 ( 浇 注 料 ) 或 , 设 计要求砌 砖后 的高 度为 40 7 mm( 图 1 。 在 勺 状 见 )
图 1 窑 尾 部 件 结 构 1 .托 砖 环 ; .勺 状 环 ; .舀 料 勺 ;.弹 簧 杠 杆 式 密 封 装 置 ; .烟 室 固 2 3 4 5 定 环 ;.浇 注 料 ;.托 盘 ; .耐 火 砖 6 7 8
简 体 窜 至下 部 时 , 料 更 为 严 重 。 2日停 窑 后 检 查 发 漏 2 现 , 砖 环 上 的耐 火 砖 基 本 损 坏 , 且 托盘 也 被 局 部 托 并 烧 坏 , 过 处 理 后 , 系 统 投 料 量 重 新 恢 复 至 10/ 经 窑 4th
- 1、下载文档前请自行甄别文档内容的完整性,平台不提供额外的编辑、内容补充、找答案等附加服务。
- 2、"仅部分预览"的文档,不可在线预览部分如存在完整性等问题,可反馈申请退款(可完整预览的文档不适用该条件!)。
- 3、如文档侵犯您的权益,请联系客服反馈,我们会尽快为您处理(人工客服工作时间:9:00-18:30)。
解决窑尾漏料和改善窑系统通风能力的方法
1.1红窑
提产必然增加窑内烧煤量。
由于窑内通风阻力较大,煅烧还原气氛浓重,火焰拉不长,经常在距离窑口13~15m段生成喇叭形窑皮,严重时喇叭口最小断面只有①1.2 m左右,致使窑内憋火,火焰冲刷窑内衬,造成局部高温,一年内接连四次在距离窑口2.5~5 m的区域产生掏鸡窝红窑现象。
1.2窑内结圈结料球
在生料成分正常、人窑表观分解率相对稳定、快窑速(≥4.O r/min)的情况下,距窑口1 7~30m段频繁地消长附窑皮,形成后结圈。
垮落的附窑皮在高温液相的粘裹作用下形成蛋核,并在窑皮末端长时间停留滚动,逐步滚大成球,使之难以越过窑皮,阻碍料流,影响窑内通风。
形成的料球在窑内反反复复滚动长大,犹如推土机,把烧成带窑皮逐步破坏掉,严重影响热工制度的稳定和耐火砖的使用寿命。
1.3窑尾漏料
当窑内结成后结圈或有大料球存在时,由于物料被阻挡在窑后段,填充率过高,部分物料直接从窑尾密封圈缝隙溢流到外面,这种情况一般都可以通过针对性的操作调整来解决处理。
但生产过程中,在窑内没有后结圈和料球、甚至烧成带窑皮薄而偏短的情况下,也时有漏料现象出现,给系统操作和周围环境产生较大影响,台时产量降低,吨熟料消耗的热耗、电耗等各项经济技术指标明显高出正常值。
1.4窑尾烟室和进料斜坡结皮积料
窑尾烟气中经常伴随有未燃尽煤粒产生的火花,窑尾烟室及缩口结皮较多,进料斜坡积料较快。
生料从左侧面入窑,物料抛撒在窑尾拱顶通风断面,易被出窑热烟气携带人烟室乃至预分解系统内,更加剧了进料斜坡积料。
1.5窑尾阻力大
窑尾负压高达550~650Pa,超过正常情况下的窑路压损400Pa左右,迫使高温热烟气从炉路方向通过;操作中为了平衡窑炉用风量,要求三次风阀必须关小,从而进一步加剧了全窑系统压损的增大。
2、解决问题的主要途径
通过对系统表现出的诸多症状进行综合分析,初步判定问题的根源在于窑内通风能力的欠缺和生料不能顺畅地入窑。
因此我们的每一步优化改造都围绕上述两点进行,每一步改造都产生了自身的作用。
2.1窑尾下料斜坡和烟室结构的调整
针对窑尾拱顶通风截面偏小、窑路通风阻力较大的情况,我们采取以下几点措施进行改造。
(1)下料斜坡整体沿原斜坡平行方向下落200mm,考虑到进料托板固定连接法兰盘位置不可改动,下落后的斜坡与之连接应尽可能平缓,确保无台阶。
(2)耐火衬结构重新设计:斜坡耐火材料总厚度由245mm(100mm钙板+145 mm耐火砖)调整为150mm,取消100mm厚的硅酸钙板,全部采用高强高铝质耐火浇注料。
(3)在斜坡及其进料舌头浇注料整体设计上,为确保拱顶到斜坡垂直距离尽可能增大,斜坡分三个倾斜角度平缓过渡人窑。
上段50。
维持不变;中段以两头保证150 mm衬厚为控制基准,实际倾斜角度大约42.5。
;下段即1000mm左右长的入料舌头约以33。
的倾斜角度人窑,相应地把入料舌头端面总衬厚由300 mm减为200mm,以增大倾斜度,取消了人料舌头端面原有约150mm长的水平过渡段。
(4)斜坡上段和中段各设置2个空气炮,进料舌头段设置3个。
7个空气炮设为自动循环控制。
(5)窑尾拱顶长度被缩短,拱顶与烟室之间的连接设计成50。
左右的倒角,基本同斜坡平行,减薄耐火衬厚度,以进一步加大拱顶断面。
(6)调整窑尾烟室耐火材料总厚度,硅酸钙板由100 mm改为80mm,浇注料由200mm 减薄为150mm,即烟室断面长度和宽度都比原来扩大了140-mm。
窑尾下料斜坡和烟室改造前后见图1。
这次改造基本杜绝了窑尾斜坡积料问题,烟室断面风速有所降低,边壁结皮大幅度减少;系统阻力略有降低,但没有根本性改观,窑尾负压仍然高达400Pa左右,窑内依旧憋火;窑尾漏料现象还是较为突出。
2.2回转窑和烟室连接结构优化
回转窑为亚快速转动设备,烟室处于静止状态,两者连接既要考虑紧凑性,又要考虑窑的上下窜动、转动变形等方面的影响,如入料舌头与窑筒体缩口之间的动态间隙较大或不均匀时,窑回转过程中必然有一部分生料从间隙漏入窑封圈。
因此,我们对回转窑和烟室连接结构进行了优化,优化改进前后情况见图2,具体优化改进内容包括:
入料舌头托板由整体式改进为分块组合型,便于装卸和浇注。
入料舌头两侧增设400 mm 高的挡料板,长度与人料托板相当,防止生料从入料舌头两侧冲出掉人密封圈内,进而漏到窑外。
密封圈回料勺重新修复,回料勺倾角和形状大小适当调整,确保抛落的生料落在入料舌头上。
回转窑尾部浇注料取消了水平过渡段,从耐火砖末端到后窑口端面整体倾斜浇注,并将后窑口末端浇注料厚度由120mm提高为270 mm,同时也将人料舌头与窑筒体缩口之间的间隙由200mm减为50mm。
窑尾部浇注料材质由高铝质耐火型改为高档次的窑口专用浇注料,以提高耐磨性能。
优化效果:窑尾漏料现象未再出现,但窑内憋火依旧厉害,窑尾负压仍然高达400Pa 左右,窑尾废气含尘浓度仍然较高,窑系统运行情况还是不理想。
2.3生料入窑方式改造
原设计的生料人窑方式为左侧面人窑,入口底部距离斜坡200mm左右。
经过对斜坡进行平行下落改造之后,人口底部距离斜坡达到460mm左右,致使经预热分解后的生料流人烟室时不能沿入料舌头顺利进窑,生料颗粒犹如瀑布撒落在窑尾拱顶通风断面,既不利于窑内废气的排出,又增加了废气携带的生料粉粒。
因此,虽然通风断面积提高了,但是系统阻力仍然较大。
改进途径:取消生料侧面入窑方式,将C5下料管以锥体底部为支点,向右方偏移大约10。
,使生料从窑尾正背面顺着斜坡流人窑内。
上述改进过程中的关键点,首先是C5锥体底部与下料管连接部位耐火浇注料施工一定要细心,尽可能地平滑过渡,确保无台阶;其次是烟室进料口开口不能过大,以防止窑尾废气短路窜人下料管;再次是进料口底部耐火衬要和斜坡耐火衬整体设计,形成一个平面。
3、改进后的效果
通过对窑尾各个部位的优化改进,窑系统平均产量基本可稳定在1 3 50 t/d以上,系统阻力(即高温风机进口负压)由改前的一5400 Pa左右降低至一4800~一5000 Pa,窑综合运转率超过了85%,熟料质量合格率稳步提高,系统生产状况日趋良好。