冷冲压工艺卡
冲压凸模工艺卡片

机械加工工艺过程卡片产品名称零件名称零件号共6页凸模第1页材料硬度毛坯类型每件毛坯可制造零件数序号工序或工步内容设备45# HRC58~62 棒料010 下料29φ×90(零件图例)020 热处理:调质HRC58~62030 粗车28φ×22,24φ×68C6140 游标卡尺,外圆车刀040 半精车上端面26φC6140 游标卡尺,外圆车刀050 车总长85 C6140 硬质合金车刀060 精车下端面56.20φC6140 硬质合金车刀070 车下端面16.16φC6140 硬质合金车刀080 铣圆角R3X62专用夹具………………学生指导教师:更改标记处数更改依据签名日期机电信息系机械加工工序卡片工序名称下料29×90工序号010(工序简图图例)零件名称凸模零件号零件重量0.56kg 同时加工零件数材料毛坯牌号硬度型号重量HT200 58~62 铸铁件0.72kg 设备夹具名称辅助工具名称型号卧式车床CA6140 专用车夹具安装工步安装及工步说明刀具量具走刀长度走刀次数切削深度进给量主轴转速切削速度基本工时11 车φ29×90硬质合金车刀游标卡90mm 1 2.5mm 0.48mm/r 530r/min1.59m/min25s 设计者指导教师共 6 页第 2 页机电信息系机械加工工序卡片工序名称粗车28φ×22工序号020(工序简图图例)零件名称凸模零件号零件重量0.56kg 同时加工零件数材料毛坯牌号硬度型号重量HT200 58~62 铸铁件0.72kg 设备夹具名称辅助工具名称型号卧式车床CA6140 专用车夹具安装工步安装及工步说明刀具量具走刀长度走刀次数切削深度进给量主轴转速切削速度基本工时212粗车28φ×22粗车24φ×68硬质合金车刀0~250mm游标卡90mm90mm110.8mm0.8mm0.48mm/r0.3mm/r530r/min520r/min1.59m/min1.48m/min22s35s设计者指导教师共6页第 3 页机电信息系机械加工工序卡片工序名称车总长工序号030(工序简图图例)零件名称凸模零件号零件重量0.56kg 同时加工零件数材料毛坯牌号硬度型号重量HT200 170~220 铸铁件0.72kg 设备夹具名称辅助工具名称型号卧式车床CA6140 专用车夹具安装工步安装及工步说明刀具量具走刀长度走刀次数切削深度进给量主轴转速切削速度基本工时31车总长85mm硬质合金车刀0~250mm游标卡85mm 1 2.5mm0.3mm/r530r/min 1.5m/min18s 设计者指导教师共 6 页第 4 页机电信息系机械加工工序卡片工序名称精车上端面工序号040(工序简图图例)零件名称凸模零件号零件重量0.56kg 同时加工零件数材料毛坯牌号硬度型号重量HT200 58~62 铸铁件0.72kg 设备夹具名称辅助工具名称型号卧式车床CA6140 专用车夹具安装工步安装及工步说明刀具量具走刀长度走刀次数切削深度进给量主轴转速切削速度基本工时412精车16.16φ×65精车56.20φ×12车刀直柄麻花钻游标卡尺内径千分尺68mm12mm110.1mm0.1mm0.1mm/r0.05mm/r200r/min200r/min0.45m/min0.08m/min180s60s设计者指导教师共6页第 5 页机电信息系机械加工工序卡片工序名称洗圆角工序号050(工序简图图例)零件名称凸模零件号零件重量0.56kg 同时加工零件数材料毛坯牌号硬度型号重量HT200 58~62 铸铁件0.72kg 设备夹具名称辅助工具名称型号卧式车床数控铣床专用车夹具安装工步安装及工步说明刀具量具走刀长度走刀次数切削深度进给量主轴转速切削速度基本工时51洗圆角硬质合金车刀0~250mm游标卡6mm1 2.5mm 0.48mm/r 530r/min 12.77m/min 40s 设计者指导教师共 6 页第 6 页。
Binder1
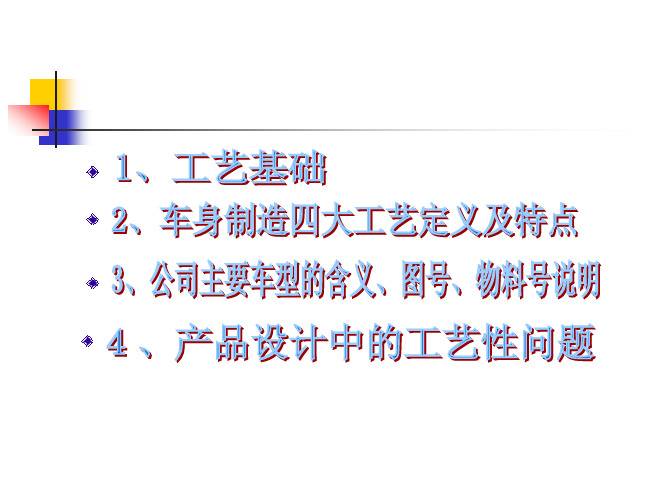
复合模
## 侧整 将上工序件以内形定位,进 形 行侧整形,要求定位准确、 可靠。 定员人数4人,冲压时4人同 时8手操作4只移动按钮台。
或A线其它压力机 MR6370-5401311-5/5
侧整形模
见工艺附图
(40序和50序在同一台压力机 上冲压,为一机双模冲压方 式) J 检验 按检具 入库 按工位器具规定装入专用工 位架
11)材料消耗工艺定额汇总表
将“材料消耗工艺定额明细表”中的各种材料按单台产品汇总填列的 一种工艺文件。
12)零部件转移卡
填写各装配工序零、部件图号(代号)名称规格等的一种工艺
1、工艺基础-管理
工艺管理内容包括:
产品工艺工作程序、产品结构工艺性审查的方式和程序、工艺方案设计、 工艺规程设计、工艺定额编制、工艺文件标准化审查、工艺文件的修改、 工艺验证、生产现场工艺管理、工艺纪律管理、工艺标准化、工艺装备 编号方法、工艺装备设计与验证管理程序、工装的使用与维护、工艺规 程格式、管理用工艺文件格式、专用工艺装备设计图样及设计文件格式
MR6370-2
共 6页
工 序 内 容
设 备 JS39-630B
闭式四点压力机
或A线其它压力机
工艺装备
MR6370-5401311-3/5
## 修边 将上工序件以内形定位进行 冲孔 修边、冲孔,要求定位准确、 可靠,此序11孔,共11孔。 (毛刺高度<0.1mm) 定员人数4人,冲压时4人同 时8手操作4只移动按钮台。
汽 车 车 身 装 焊 工 艺
焊接设备,由焊接电源、送丝机构、行走机构、焊矩、气路系统、 控制系统等 型号:DNC-200/DNC-250 电源:硅整流电源
冲压过程技术标准
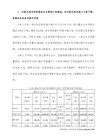
冲压工艺培训教材魏龙2004-5第一章绪论冷冲压是一种先进的金属加工方法,它是建立在金属塑性变形的基础上,利用模具和冲压设备对板料金属进行加工,以获得所需要的零件形状和尺寸。
冲压工艺应用范围十分广泛,在国民经济各个部门中,几乎都有冲压加工产品,如汽车、飞机、拖拉机、电机、电器、仪表、铁道、邮电、化工以及轻工日用产品中均占有相当大的比重。
冷冲压和切削加工比较,具有生产率高、加工成本低、材料利用率高、产品尺寸精度稳定、操作简单、容易实现机械化和自动化等一系列优点,特别适合大批量生产。
一、冲压工序的分类冷冲压工艺按其变形性质可分为分离工序和成形工序两大类。
分离工序又可分为落料、冲孔和切边等,如表1-1所示。
成形工序可分为弯曲、拉深、翻孔、翻边、胀形、扩口、缩口和旋压等,如表1-2所示。
根据产品零件的形状、尺寸精度和其他技术要求,可分别采用各种工序对板料毛坯进行加工,以获得满意的零件。
表1-1分离工序工序名称简图特点及应用范围第二章冲裁冲裁是利用模具使板料产生分离的冲压工序,包括落料、冲孔、切口、剖切、修边等。
用它可以制作零件或为弯曲、拉深、成形等工序准备毛坯。
一、落料从板料上冲下所需形状的零件(或毛坯)叫落料。
如图2-1所示。
图2-1落料图2-2冲孔二、冲孔在工件上冲出所需形状的孔(冲去的为废料)叫冲孔。
如图2-2所示。
三、冲裁的过程冲裁既是分离工序,工件受力时必然从弹、塑性变形开始,以断裂告终。
当凸模下降接触板料,板料即受到凸、凹模压力而产生弹性变形,板料产生弯曲,即从模具表面上翘起(图2-3-1)。
随着凸模下压,模具刃口压入材料,内应力状态满足塑性条件时,产生塑性变形(图2-3-2)。
塑性变形从刃口开始,随着刃口的深入,变形区向板料的深度方向发展、扩大,直到在板料的整个厚度方向上产生塑性变形,板料的一部分相对于另一部分移动。
当切刃附近材料各层中达到极限应变与应力值时,便产生微裂(图2-3-3),裂纹产生后,沿最大剪应变速度方向发展,直至上、下裂纹会合,板料就完全分离。
冲压工艺过程卡的缩写
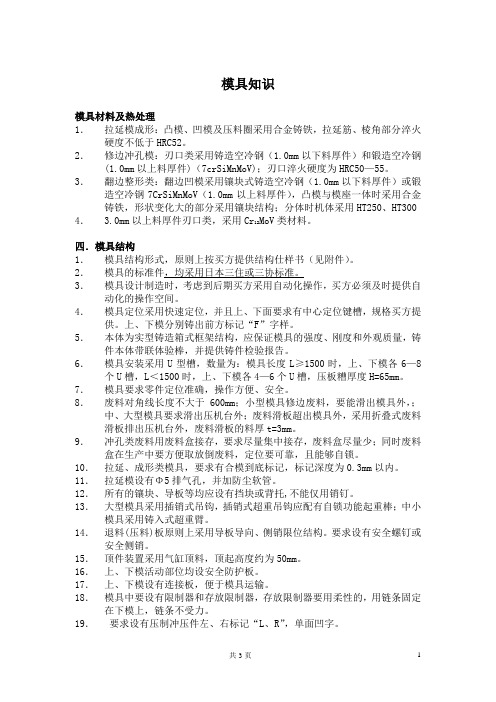
模具知识模具材料及热处理1.拉延模成形:凸模、凹模及压料圈采用合金铸铁,拉延筋、棱角部分淬火硬度不低于HRC52。
2.修边冲孔模:刃口类采用铸造空冷钢(1.0mm以下料厚件)和锻造空冷钢(1.0mm以上料厚件)(7crSiMnMoV);刃口淬火硬度为HRC50—55。
3.翻边整形类:翻边凹模采用镶块式铸造空冷钢(1.0mm以下料厚件)或锻造空冷钢7CrSiMnMoV(1.0mm以上料厚件),凸模与模座一体时采用合金铸铁,形状变化大的部分采用镶块结构;分体时机体采用HT250、HT300 4. 3.0mm以上料厚件刃口类,采用Cr12MoV类材料。
四.模具结构1.模具结构形式,原则上按买方提供结构仕样书(见附件)。
2.模具的标准件,均采用日本三住或三协标准。
3.模具设计制造时,考虑到后期买方采用自动化操作,买方必须及时提供自动化的操作空间。
4.模具定位采用快速定位,并且上、下面要求有中心定位键槽,规格买方提供。
上、下模分别铸出前方标记“F”字样。
5.本体为实型铸造箱式框架结构,应保证模具的强度、刚度和外观质量,铸件本体带联体验棒,并提供铸件检验报告。
6.模具安装采用U型槽,数量为:模具长度L≥1500时,上、下模各6—8个U槽,L<1500时,上、下模各4—6个U槽,压板糟厚度H=65mm。
7.模具要求零件定位准确,操作方便、安全。
8.废料对角线长度不大于600mm;小型模具修边废料,要能滑出模具外,;中、大型模具要求滑出压机台外;废料滑板超出模具外,采用折叠式废料滑板排出压机台外,废料滑板的料厚t=3mm。
9.冲孔类废料用废料盒接存,要求尽量集中接存,废料盒尽量少;同时废料盒在生产中要方便取放倒废料,定位要可靠,且能够自锁。
10.拉延、成形类模具,要求有合模到底标记,标记深度为0.3mm以内。
11.拉延模设有Φ5排气孔,并加防尘软管。
12.所有的镶块、导板等均应设有挡块或背托,不能仅用销钉。
13.大型模具采用插销式吊钩,插销式超重吊钩应配有自锁功能起重棒;中小模具采用铸入式超重臂。
冲压工艺卡片
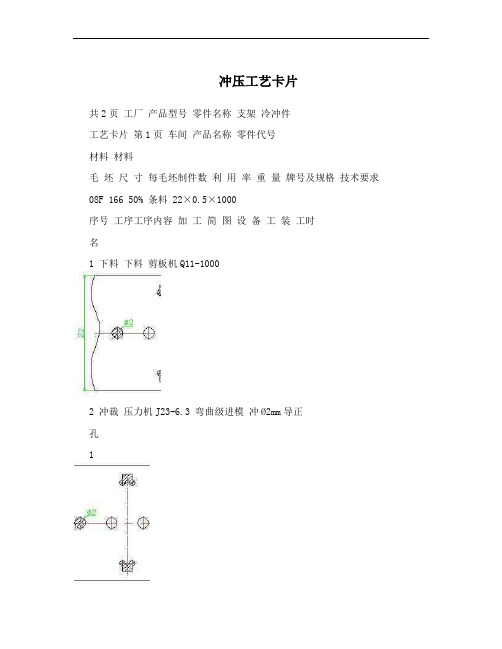
冲压工艺卡片
共2页工厂产品型号零件名称支架冷冲件
工艺卡片第1页车间产品名称零件代号
材料材料
毛坯尺寸每毛坯制件数利用率重量牌号及规格技术要求08F 166 50% 条料22×0.5×1000
序号工序工序内容加工简图设备工装工时
名
1 下料下料剪板机Q11-1000
2 冲裁压力机J23-6.
3 弯曲级进模冲Ø2mm导正
孔
1
3 冲裁冲异型孔压力机J23-6.3 弯曲级进模
4 切边冲出弯曲件压力机J23-6.3 弯曲级进模外形
5 弯曲校正弯曲压力机J23-6.3 弯曲级进模2
6 切断落料压力机J23-6.3 弯曲级进模
7 尺寸根据零件图检
检验验冲压件尺寸
3。
冲压工艺教案
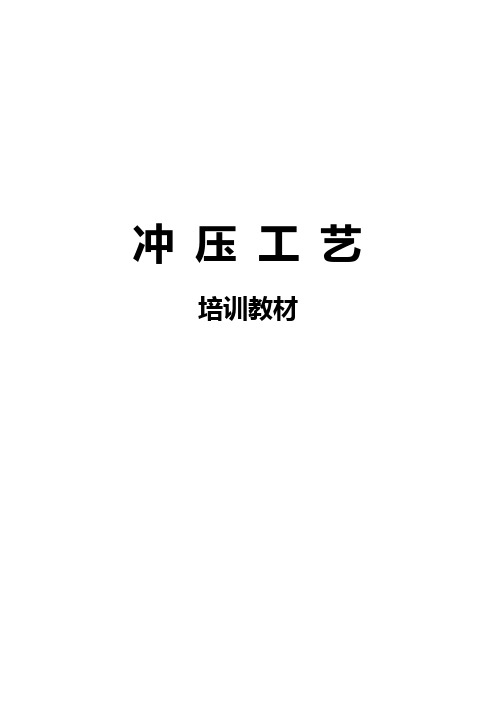
冲压工艺培训教材魏龙2004-5第一章绪论冷冲压是一种先进的金属加工方式,它是成立在金属塑性变形的基础上,利用模具和冲压设备对板料金属进行加工,以取得所需要的零件形状和尺寸。
冲压工艺应用范围十分普遍,在国民经济各个部门中,几乎都有冲压加工产品,如汽车、飞机、拖沓机、电机、电器、仪表、铁道、邮电、化工和轻工日用产品中均占有相当大的比重。
冷冲压和切削加工比较,具有生产率高、加工本钱低、材料利用率高、产品尺寸精度稳固、操作简单、容易实现机械化和自动化等一系列优势,专门适合大量量生产。
一、冲压工序的分类冷冲压工艺按其变形性质可分为分离工序和成形工序两大类。
分离工序又可分为落料、冲孔和切边等,如表1-1所示。
成形工序可分为弯曲、拉深、翻孔、翻边、胀形、扩口、缩口和旋压等,如表1-2所示。
依照产品零件的形状、尺寸精度和其他技术要求,可别离采纳各类工序对板料毛坯进行加工,以取得中意的零件。
表1-1 分离工序表1-2 成形工序第二章冲裁冲裁是利用模具使板料产生分离的冲压工序,包括落料、冲孔、切口、剖切、修边等。
用它能够制作零件或为弯曲、拉深、成形等工序预备毛坯。
一、落料从板料上冲下所需形状的零件(或毛坯)叫落料。
如图2-1所示。
图2-1 落料图2-2 冲孔二、冲孔在工件上冲出所需形状的孔(冲去的为废料)叫冲孔。
如图2-2所示。
三、冲裁的进程冲裁既是分离工序,工件受力时必然从弹、塑性变形开始,以断裂告终。
当凸模下降接触板料,板料即受到凸、凹模压力而产生弹性变形,板料产生弯曲,即从模具表面上翘起(图2-3-1)。
随着凸模下压,模具刃口压入材料,内应力状态知足塑性条件时,产生塑性变形(图2-3-2)。
塑性变形从刃口开始,随着刃口的深切,变形区向板料的深度方向进展、扩大,直到在板料的整个厚度方向上产生塑性变形,板料的一部份相关于另一部份移动。
当切刃周围材料各层中达到极限应变与应力值时,便产生微裂(图2-3-3),裂纹产生后,沿最大剪应变速度方向进展,直至上、下裂纹会合,板料就完全分离。
冲压工艺卡通则(最新修改)
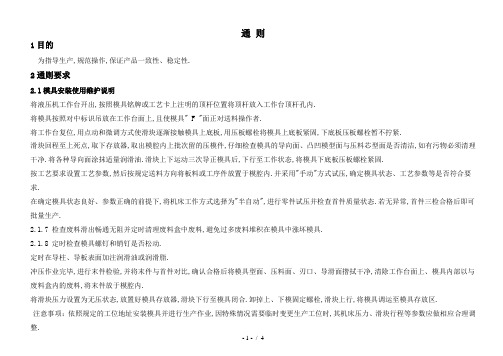
通则1目的为指导生产,规范操作,保证产品一致性、稳定性.2通则要求2.1模具安装使用维护说明将液压机工作台开出,按照模具铭牌或工艺卡上注明的顶杆位置将顶杆放入工作台顶杆孔内.将模具按照对中标识吊放在工作台面上,且使模具" F "面正对送料操作者.将工作台复位,用点动和微调方式使滑块逐渐接触模具上底板,用压板螺栓将模具上底板紧固,下底板压板螺栓暂不拧紧.滑块回程至上死点,取下存放器,取出模腔内上批次留的压模件,仔细检查模具的导向面、凸凹模型面与压料芯型面是否清洁,如有污物必须清理干净.将各种导向面涂抹适量润滑油.滑块上下运动三次导正模具后,下行至工作状态,将模具下底板压板螺栓紧固.按工艺要求设置工艺参数,然后按规定送料方向将板料或工序件放置于模腔内.并采用"手动"方式试压,确定模具状态、工艺参数等是否符合要求.在确定模具状态良好、参数正确的前提下,将机床工作方式选择为"半自动",进行零件试压并检查首件质量状态.若无异常,首件三检合格后即可批量生产.2.1.7 检查废料滑出畅通无阻并定时清理废料盒中废料,避免过多废料堆积在模具中涨坏模具.2.1.8 定时检查模具螺钉和销钉是否松动.定时在导柱、导板表面加注润滑油或润滑脂.冲压作业完毕,进行末件检验,并将末件与首件对比,确认合格后将模具型面、压料面、刃口、导滑面揩拭干净,清除工作台面上、模具内部以与废料盒内的废料,将末件放于模腔内.将滑块压力设置为无压状态,放置好模具存放器,滑块下行至模具闭合.卸掉上、下模固定螺栓,滑块上行,将模具调运至模具存放区.注意事项:依照规定的工位地址安装模具并进行生产作业,因特殊情况需要临时变更生产工位时,其机床压力、滑块行程等参数应做相应合理调整.冲压时注意安全,模具上的红色区域为工作时的危险区域,在冲压时避免身体与之接触,以免发生事故. 2.2 液压机工作过程与参数监测说明 2.2.1 压机行程过程与机床参数说明 1〕压机行程运动过程如下图示:2.2.2 液压机工作方式和工艺动作方式 1〕液压机工作方式本机的控制系统设有工艺动作为手动、调整、半自动三种操作方式,在操纵箱上设置选择开关实现方式转换.在半自动工艺中操作形式又可分为:带顶出、不带顶出、拉伸,并可实现定程、定压两种成形工艺. 2〕液压机工艺动作方式〔按工作方式分〕 a> 调整调整动作又称"点动",操作相应的功能按钮完成相应的动作,每按一次按钮完成相应动作的一次点动.主要用于调整模具时使用.手按压按钮机床上工作台平面机床下工作台平面机床上工作台平面滑块 上 行 运 动 过程慢速下行开始位置模具闭合高度★以下工作台平面为基准〔零点〕快速下行慢速下行★下行停止位置快速回程慢速回程★回程停止位置滑块下行运动过程慢速回程开始位置才有相应的动作,抬手则此动作停.b> 手动手按一次动作按钮后,可完成一个相应动作,按静止按钮或限位开关发讯,该动作结束.c> 半自动采用双手按钮,同时按下两个按钮完成一次工作循环,滑块完成快下—慢下—加压并延时—泄压—快速回程—慢速回程—停止,完成一个单次循环过程.2.2.3 参数监测要求监测范围:对冲压车间现生产的所有车型关键工序零部件参数进行监控并记录.监测内容:所需记录参数内容以工艺卡上所规定参数内容为准.监测频次:正常生产情况下,每批次记录一次.非正常生产情况下,参数每变更一次,便需记录一次.如生产过程中存在因机床、模具或其他原因造成停线,当问题处理完毕后,需对参数重新进行一次监控并记录.当原材料材质、尺寸等更改时,若参数发生变化,也需监控并记录.监测要求:参数记录要求在"首件三检"完成后,并确认零件合格可批量生产后再记录.参数记录要求对车型、零件名称、工序代号等描述清楚、准确,具体可见《冲压车间关键工序工艺参数记录表》.2.3工序间周转注意事项1〕工序零件周转时必须使用专用周转器具或使用传送带进行周转,不得随意挪用其他盛具作为周转器具.2〕各工序件在周转过程中不得码放过高,以免零件变形、滑落;3〕各工序在周转过程中需注意零件保护,零件需码放整齐规范,不得随意丢弃并严禁零件落地.2.4 检查技术条件2.4.1 判定方法1〕目测判定.2〕触摸制件表面,手感判定.3〕油石打磨制件表面后目测判定.2.4.2 缺陷标记检查时,根据判定标准对制件缺陷进行判定,已判定的缺陷要用色笔圈出.根据缺陷对所检零件进行分类〔合格品、返修品、报废品等〕.2.4.3 缺陷零件处理1〕存在缺陷的零件应标识、隔离,标识卡上加盖"不合格"章并放于指定位置.2〕对不合格零件按照流程进行处理〔返修或报废〕.2.4.4 检查1〕首检100%检查,末件100% 检查,生产过程中每25~30件检查一次.2〕对完序产品进行检具检测并准确、规范填写检验记录,首件检查合格后方可批量生产.若生产中因设备、材料或其他原因停线,恢复生产后,需重新进行首件检验并在确认合格后方可批量生产,同时检验人员应做好相关记录.2.5存放、运输和储存2.5.1存放2.5.1.1 产品应按照要求放置在专用盛具中,且按照设计装箱数量与存放方式进行存放.2.5.1.2盛具上应粘贴产品标示卡,标识卡需标明:1〕产品名称、零件件号、零件配置状态;2〕标明生产班次、生产日期、零件数量、工序数〔必要时填写〕;3〕标明车型状态、产品质量状态;2.5.2 运输1> 成品件在运输过程中切勿碰撞、受压,以免造成产品二次缺陷,影响使用质量.2> 成品件在运输过程中应注意防护,避免因叉车操作不当等其他原因造成的零件损坏.2.5.3 储存1> 成品件应贮存在无腐蚀气体、干燥、通风的库房内,不应与化学药品、酸碱物质等一同存放.2> 成品件应存储在规定区域并在该区域做好标识进行区分,布局合理存放整齐规范.。
冲压过程技术标准

冲压工艺培训教材魏龙2004-5第一章绪论冷冲压是一种先进的金属加工方法,它是建立在金属塑性变形的基础上,利用模具和冲压设备对板料金属进行加工,以获得所需要的零件形状和尺寸。
冲压工艺应用范围十分广泛,在国民经济各个部门中,几乎都有冲压加工产品,如汽车、飞机、拖拉机、电机、电器、仪表、铁道、邮电、化工以及轻工日用产品中均占有相当大的比重。
冷冲压和切削加工比较,具有生产率高、加工成本低、材料利用率高、产品尺寸精度稳定、操作简单、容易实现机械化和自动化等一系列优点,特别适合大批量生产。
一、冲压工序的分类冷冲压工艺按其变形性质可分为分离工序和成形工序两大类。
分离工序又可分为落料、冲孔和切边等,如表1-1所示。
成形工序可分为弯曲、拉深、翻孔、翻边、胀形、扩口、缩口和旋压等,如表1-2所示。
根据产品零件的形状、尺寸精度和其他技术要求,可分别采用各种工序对板料毛坯进行加工,以获得满意的零件。
表1-1分离工序工序名称简图特点及应用范围第二章冲裁冲裁是利用模具使板料产生分离的冲压工序,包括落料、冲孔、切口、剖切、修边等。
用它可以制作零件或为弯曲、拉深、成形等工序准备毛坯。
一、落料从板料上冲下所需形状的零件(或毛坯)叫落料。
如图2-1所示。
图2-1落料图2-2冲孔二、冲孔在工件上冲出所需形状的孔(冲去的为废料)叫冲孔。
如图2-2所示。
三、冲裁的过程冲裁既是分离工序,工件受力时必然从弹、塑性变形开始,以断裂告终。
当凸模下降接触板料,板料即受到凸、凹模压力而产生弹性变形,板料产生弯曲,即从模具表面上翘起(图2-3-1)。
随着凸模下压,模具刃口压入材料,内应力状态满足塑性条件时,产生塑性变形(图2-3-2)。
塑性变形从刃口开始,随着刃口的深入,变形区向板料的深度方向发展、扩大,直到在板料的整个厚度方向上产生塑性变形,板料的一部分相对于另一部分移动。
当切刃附近材料各层中达到极限应变与应力值时,便产生微裂(图2-3-3),裂纹产生后,沿最大剪应变速度方向发展,直至上、下裂纹会合,板料就完全分离。
冷冲压成型工艺

产批量以及各企业设备条件的不同,可能有多种不同的可行工艺方案;
一般情况下,可参照表36-16选定冲压工艺方案与模具类型。
8
主要用于有成型工位的级进 模
卸料装置
采用具有精密导向的弹压 卸料板
弹压卸料板可对小尺寸凸模 起保护作用
出件方式
必要时可采用自动出件装 置
主要用于有成型工序的紧固 件
保护装置 采用自动检测与保护装置 出现故障时自动立即停机
6、紧固件冲压工艺方案与模具类型选定
对于同一种紧固件(垫圈、挡圈、扣紧螺母等),由于尺寸规格、生
1 紧固件冲压生产的原材料与一般工艺流程
采用冲压工艺生产的紧固件仅限于各种垫圈、弹性挡圈与扣紧螺母等, 其原材料厚度为:0.3~8mm的钢板或钢带;厚度≤4mm时为冷轧或 热轧料,>4mm时均为热轧料。
紧固件冲压生产的一般工艺流程为:下料→冲压→热处理与表面处理 →清理→检验。
2 适用于紧固件成型的冲压工艺类型与简要成型原理
5
导板式模具中,导板替代了导柱式模具中的导柱与导套;导板还可以 兼作条料的导料板。由于导板式模具工作时要求凸模不脱离导板孔, 因此应选用行程较小并可调节行程的冲床。
b.可冲切搭边的挡料杆与导正销定位的冲孔落料级进模实例 图3654所示为设置有可冲切搭边的挡料杆的冲孔落料级进模。由于挡料杆 部位的搭边处已冲出缺口,因此条料可平移向前送进。采用这种挡料 装置需设置两个手动始用挡料销6;另外,为了保证条料的送进位置 更为准确,模具上设置了侧压料板4。
7
5、冲压自动模的主要结构特点
标准紧固件,特别是中、小规格标准紧固件,一般均为专业化大量生 产;因此,最适于采用高生产率的冲压自动模。与人工操作的冲压模 具相比较,自动模的主要结构特点见表36-15。
冲压工序卡-模板
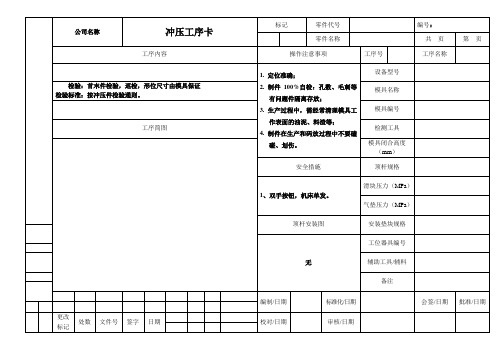
模具编号
工序简图
检测工具
模具闭合高度(mm)
安全措施
顶杆规格
1、双手按钮,机床单发。
滑块压力(MPa)
气垫压力(MPa)
顶杆安装图
安装垫块规格
无
工位器具编号
辅助工具/辅料
备注
编制/日期
ห้องสมุดไป่ตู้标准化/日期
会签/日期
批准/日期
更改标记
处数
文件号
签字
日期
校对/日期
审核/日期
公司名称
冲压工序卡
标记
零件代号
编号:
零件名称
共页
第页
工序内容
操作注意事项
工序号
工序名称
1.定位准确;
2.制件100%自检:孔数、毛刺等有问题件隔离存放;
3.生产过程中,需经常清理模具工作表面的油泥、料渣等;
4.制件在生产和码放过程中不要磕碰、划伤。
设备型号
检验:首末件检验,巡检,形位尺寸由模具保证
检验标准:按冲压件检验通则。
冷加工工艺过程卡片
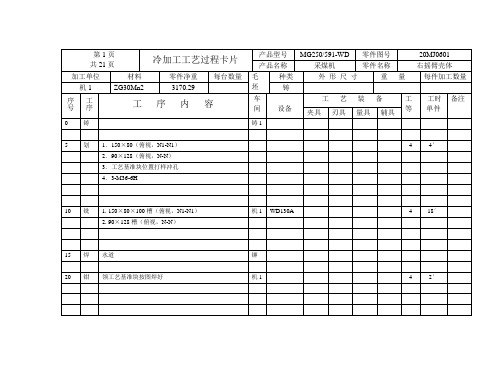
共21页
冷加工工艺过程卡片
产品型号
MG250/591-WD
零件图号
20MJ0601
产品名称
采煤机
零件名称
右摇臂壳体
序号
工序
工序内容
车间
设备
工艺装备
工等
工时
单件
备注
夹具
刃具
量具
辅具
(2) 120H7镗成
(3)90H7镗成
(4) 100镗好
(5) 320刀检镗好
(6) 130及5 镗好
(7)各止口台面镗留余量1
4
4′
2.90×128(俯视,N-N)
3.工艺基准块位置打样冲孔
4.3-M36-6H
10
铣
1. 150×80×100槽(俯视,N1-N1)
机1
WD130A
4
18′
2. 90×128槽(俯视,N-N)
15
焊
水道
铆
20
钳
领工艺基准块按图焊好
机1
4
2′
第2页
共21页
冷加工工艺过程卡片
产品型号
MG250/591-WD
4. 215H7行孔
(1) 275镗好
(2) 215H7镗成
(3) 296镗好
(4) 320刀检镗好
(5)行孔各尺寸面镗留余量1
5. 240H7行孔
(1) 304刀检镗好
(2) 240H7镗成
(3) 170H7镗成
(4) 230镗好
(5)行孔各尺寸面镗留余量1
第13页
共21页
冷加工工艺过程卡片
产品型号
二、工件调个,主视图示向床头,按870 0.2上面拉
冲床工艺流程卡

材料技术要求 胚料尺
加
工
简
图
工序内容
工艺装备 工时
序号 1 2 3 4 5 6 7 标记
检验项目
技术要求
误差范围 检验手段 自检频次
专检频次
检验操作 要求
处数
更改文件号
签字
日期
绘制
审核
会签
材料牌号及规格材料技术要求胚料尺寸每个胚料可制零件数毛胚重量辅助材料工序号工序名称工序内容工艺装备工时序号检验项目技术要求误差范围检验手段自检频次专检频次更改文件号签字日期绘制审核会签检验操作要
冲压工艺流程卡
深圳市华兴盛五金朔胶有限公司 冲床编号: 模具编号: 材料牌号及规格 产品型号: 产品名称: 零部件名称: 零部件型号:
冷冲压成形钣金件的简易模具制作工艺
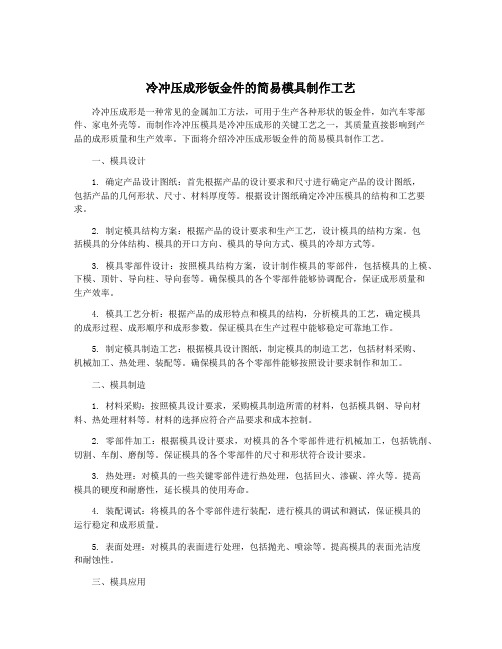
冷冲压成形钣金件的简易模具制作工艺冷冲压成形是一种常见的金属加工方法,可用于生产各种形状的钣金件,如汽车零部件、家电外壳等。
而制作冷冲压模具是冷冲压成形的关键工艺之一,其质量直接影响到产品的成形质量和生产效率。
下面将介绍冷冲压成形钣金件的简易模具制作工艺。
一、模具设计1. 确定产品设计图纸:首先根据产品的设计要求和尺寸进行确定产品的设计图纸,包括产品的几何形状、尺寸、材料厚度等。
根据设计图纸确定冷冲压模具的结构和工艺要求。
2. 制定模具结构方案:根据产品的设计要求和生产工艺,设计模具的结构方案。
包括模具的分体结构、模具的开口方向、模具的导向方式、模具的冷却方式等。
3. 模具零部件设计:按照模具结构方案,设计制作模具的零部件,包括模具的上模、下模、顶针、导向柱、导向套等。
确保模具的各个零部件能够协调配合,保证成形质量和生产效率。
4. 模具工艺分析:根据产品的成形特点和模具的结构,分析模具的工艺,确定模具的成形过程、成形顺序和成形参数。
保证模具在生产过程中能够稳定可靠地工作。
5. 制定模具制造工艺:根据模具设计图纸,制定模具的制造工艺,包括材料采购、机械加工、热处理、装配等。
确保模具的各个零部件能够按照设计要求制作和加工。
二、模具制造1. 材料采购:按照模具设计要求,采购模具制造所需的材料,包括模具钢、导向材料、热处理材料等。
材料的选择应符合产品要求和成本控制。
2. 零部件加工:根据模具设计要求,对模具的各个零部件进行机械加工,包括铣削、切割、车削、磨削等。
保证模具的各个零部件的尺寸和形状符合设计要求。
3. 热处理:对模具的一些关键零部件进行热处理,包括回火、渗碳、淬火等。
提高模具的硬度和耐磨性,延长模具的使用寿命。
4. 装配调试:将模具的各个零部件进行装配,进行模具的调试和测试,保证模具的运行稳定和成形质量。
5. 表面处理:对模具的表面进行处理,包括抛光、喷涂等。
提高模具的表面光洁度和耐蚀性。
三、模具应用1. 成形试验:对制作完成的模具进行成形试验,检查产品的成形质量和模具的运行稳定性。
垫板冷冲压模具设计及主要零件加工工艺过程卡的编制

目录摘要 1绪论 3第1章工件分析 4第2章零件的工艺分析 52.1 结构与尺寸 52.2 精度 52.3 材料 5第3章确定冲裁工艺方案 6第4章确定模具总体结构方案 74.1 模具类型 74.2 操作与定位方式 74.3 卸料与出件方式 74.4 模架类型及精度 74.5 凸模设计 7第5章工艺设计计算 85.1 排样设计与计算 85.2 计算冲压力与压力中心,初选压力机 95.3 计算凸、凹模刃口尺寸及公差 11第6章设计选用零件、部件,绘制模具总装草图 13 6.1 凹模设计 136.2 凸模设计 146.3 凸凹模的设计 166.4 定位零件 186.5 卸料与出件装置 186.6 模架及其它零件的选用 21第7章压力机的校核 257.1 公称压力 257.2 滑块行程 257.3 行程次数 257.4 工作台面的尺寸 257.5 滑块模柄孔尺寸 257.6 闭合高度 25第8章模具主要零件加工工艺规程的编制 268.1 冲压模具制造技术要求 268.2 总装工艺 268.3 加工要求 28总结 29致谢 30参考文献 31摘要该垫板形状简单,结构对称。
设计内容从零件工艺性分析开始。
首先,确定该模具类型为倒装式落料、冲孔复合模;接着,做工艺计算,计算出冲压力、压力中心、选择压力机。
然后,根据计算出确定模具的凸、凹模尺寸和形状。
最后,设计其他零部件并对压力进行校核,无问题后绘图,完成设计。
经过分析,只需2道工序落料和冲孔,通过挡料钉进行2次加工将零件生产出来。
当中使用导正销可以确保孔位精度和生产率。
关键词:垫板;凸模;凹模,倒装复合冲裁模ABSTRACTThe plate shape is simple, the structure is symmetrical. Design content part manufacturability analysis from the beginning. First, we determine the mould for flip chip type blanking, punching compound die;Then, do process calculation, calculate the impact pressure, the pressure center, choose to press. Then, according to calculate the mould of convex and concave die size and shape. Finally, the design of other parts and the stress checking, no problem after drawing, complete the design.Through the analysis, just 2 steps blanking and punching,through keep-off nail for processing the parts produced twice. Use of guide pin can ensure a hole accuracy and productivity.Keywords: plate; Punch; Die, inversion compound blanking die绪论冲压是靠压力机和模具对板材、带材、管材和型材等施加外力,使之产生塑性变形或分离,从而获得所需形状和尺寸的工件(冲压件)的成形加工方法。
《冷冲压工艺及模具设计》课程设计任务书
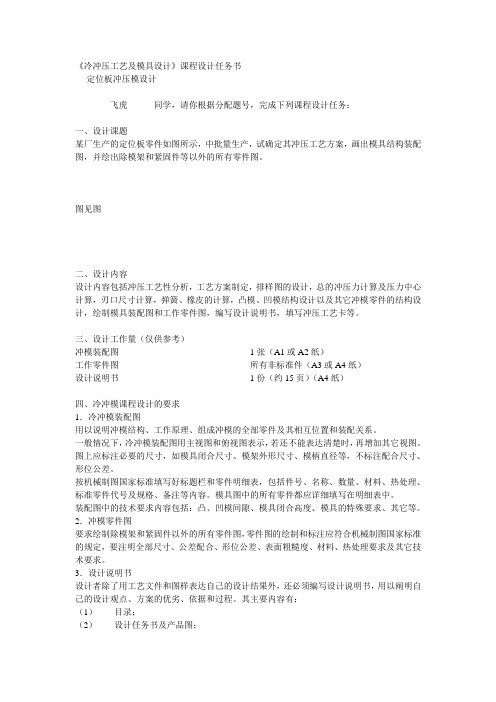
《冷冲压工艺及模具设计》课程设计任务书----定位板冲压模设计飞虎同学,请你根据分配题号,完成下列课程设计任务:一、设计课题某厂生产的定位板零件如图所示,中批量生产,试确定其冲压工艺方案,画出模具结构装配图,并绘出除模架和紧固件等以外的所有零件图。
图见图二、设计内容设计内容包括冲压工艺性分析,工艺方案制定,排样图的设计,总的冲压力计算及压力中心计算,刃口尺寸计算,弹簧、橡皮的计算,凸模、凹模结构设计以及其它冲模零件的结构设计,绘制模具装配图和工作零件图,编写设计说明书,填写冲压工艺卡等。
三、设计工作量(仅供参考)冲模装配图1张(A1或A2纸)工作零件图所有非标准件(A3或A4纸)设计说明书1份(约15页)(A4纸)四、冷冲模课程设计的要求1.冷冲模装配图用以说明冲模结构、工作原理、组成冲模的全部零件及其相互位置和装配关系。
一般情况下,冷冲模装配图用主视图和俯视图表示,若还不能表达清楚时,再增加其它视图。
图上应标注必要的尺寸,如模具闭合尺寸、模架外形尺寸、模柄直径等,不标注配合尺寸、形位公差。
按机械制图国家标准填写好标题栏和零件明细表,包括件号、名称、数量、材料、热处理、标准零件代号及规格、备注等内容。
模具图中的所有零件都应详细填写在明细表中。
装配图中的技术要求内容包括:凸、凹模间隙、模具闭合高度、模具的特殊要求、其它等。
2.冲模零件图要求绘制除模架和紧固件以外的所有零件图,零件图的绘制和标注应符合机械制图国家标准的规定,要注明全部尺寸、公差配合、形位公差、表面粗糙度、材料、热处理要求及其它技术要求。
3.设计说明书设计者除了用工艺文件和图样表达自己的设计结果外,还必须编写设计说明书,用以阐明自己的设计观点、方案的优劣、依据和过程。
其主要内容有:(1)目录;(2)设计任务书及产品图;(3)序言;(4)制件的工艺性分析;(5)冲压工艺方案的制定及分析比较;;(6)模具结构形式的论证及确定;(7)排样图设计及材料利用率计算;(8)工序压力计算及压力中心确定;(9)冲压设备的选择及校核;(10)模具零件的选用、设计及必要的计算;(11)模具工作零件刃口尺寸及公差的计算;(12)其它需要说明的问题;(13)主要参考文献目录。
冲压工艺卡细化检查表

落冲
521.3
24
成型
10MPa
25 第一横梁下板
成型
10MPa
26
修边冲孔 499.4
27 第四横梁上板
落料冲孔 604.7
28
成型
10MPa
29
侧冲
550
30 第四横梁下板
落料冲孔 597.6
31
成型
12MPa
32 纵梁中断内板
修边冲孔 597.4
33
成型、翻孔 558.9
34 纵梁中断外板
落冲
K2车架冲压工艺卡细化检查表
序号 制件名称
工序
闭合高度 主缸压力 液压垫压力 液压垫上升距离
1 纵梁前段左内板 落冲
696.6
2
成型
55%
3 纵梁前段右内板 落冲
696.6
4
70%
5 纵梁前段左外板 落冲
701
6
成型
85%
7
侧翻侧冲孔 848.4
8 纵梁前段右内板 落冲
701
9
成型
85%
10
侧翻侧冲孔 844.5
11 第四横梁左支架上板落料冲孔 430
12
一次成型 400
13
二次成型
10MPa
14
侧冲孔侧整 660
15 第四横梁右支架上板落料冲孔 430
16
一次成型 400
17
二次成型
10MPa
18
侧冲孔侧整 660
19 第四横梁支架下板 落冲
485.5
20
拉延
12MPa
21
冲孔
373
22
翻遍切断 675
【最新文档题库】冲压工艺过程卡

附录冲压工艺过程卡
表 1 冲压工艺过程卡
产品型号零(部)件名称固定片共 1 页集美大学
冲压工艺卡片
产品名称零(部)件型号第 1 页
材料牌号及规格
材料
技术要求
毛坯尺寸
每毛坯可
制件数
毛坯重量辅助材料
板料
08 钢板 1.5mm×1400mm×75
1220mm
工序号工序工序内容加工简图设备工艺工时名称装备
0 排样按交叉双排
排样将板料煅成
1 备料 1.5mm×1220mm
×279mm
2 热处理退火
冲φ148mm的圆
3 落料拉深
复合
并拉深φ80外
圆、R1.5mm、
R5mm、
R3.5mm
倒角
4 热处理调质
5 胀形胀形
6 冲孔冲中间孔
7 翻边翻中间孔边
8 冲孔冲凸缘孔
9 冲孔冲边孔
10 切边整形切边整形
11 检验按零件图检验
会签
日期
编制日期审核日期
更改更改
签日标记处数文件签字日期标记处数文件
字期号号。