多工位模具案例介绍
支架多工位级进模具设计

摘要经过对零件进行仔细的工艺分析,最终确定此套模具采用多工位级进模,此套模具工序复杂,具有冲孔,弯曲,成型等多个工序,难点在于多处弯曲,一处对称弯曲,一处Z型弯曲。
为防止弯曲后回弹,故在Z型弯曲后采用校正工序。
采用多工位级进模不但大大提高生产效率,而且同时避免了多套模具冲裁时多次定位造成的误差,进而提高了零件的精度。
操作起来十分方便,而且大大减少了多个单工序模带来的材料损耗。
使用使得模具的结构更加立体,显而易见。
此套模具为人工手动送料,故安装了导料钉,并且为了提高精度准却定位在每步工位上安装了多个导正销进行定位。
此套模具采用弹性卸料方式,以及浮料装置。
此套模具的设计利用法国Missler 公司开发的三维软件,通过该软件进行对模具的三维实体的设计,再将实体转化为二维图纸,最后再把图纸转入到CAD软件中进行编辑修改。
由于需要以上软件对工件进行设计,因此需要对以上软件进行了解与掌握。
该软件功能强大操作简单方便,在设计中使得模具的结构更加立体,显而易见。
关键词:级进模设计;Z型弯曲;TopSolid’Progress;多工位;AbstractThrough the process of spare parts, carefully finally determined by the mold multi-position pressure, this set of mould process complex, punching, bending, molding multi-process.it is difficult, in a symmetric curved, bending, a Z bending. To prevent bent, after springback using bend in the Z after correction.Using multi-position progressive not only greatly improve the production efficiency, but also avoid the mold cutting position when the error caused by many times, and improve the precision of parts. It is convenient, and operating more than a single procedure greatly reduce the material loss modulus. Using three-dimensional structure of mould makes more, obvious. This set of mould for manually feed installation guide material, and in order to improve the precision positioning in each step but must install a cubicle than guide pin location. This set of mould using elastic and unloading float device. This set of mold design and use of Missler French company development TopSolid 'safely through the 3d software, software for mould design, three-dimensional entity 2d drawings will be converted into the drawing, and finally to edit changes in CAD software. Due to the need for the software design, and therefore need for more understanding and mastering software.This powerful tool for easy operation, in the design of die structure more stereo, obviously.Keywords: progressive die design;Z bending; TopSolid’Progress; Many stations.目录1 绪论 (1)1.1 概述 (1)1.2 冲压技术的进步 (1)1.3冲压的基本工序及模具 (2)1.4 模具的发展与现状 (3)1.5模具CAD/CAE/CAM技术 (3)2冲压工艺方案的确定 (6)2.1工件工艺分析 (6)2.1.1工件外形尺寸 (6)2.1.2工件的材料性能 (7)2.1.3工件的工艺分析 (7)2.1.4 模具类型的确定 (8)2.2排样设计 (10)2.2.1排样搭边的取值 (10)2.2.2条料的利用率 (11)2.2.3排样图设计 (12)2.2.4排样方案的确定 (13)2.2.5模具压力中心的确定 (14)3模具的零件设计及尺寸计算。
多工位级进模设计

4)多工位级进冲裁成型模具
多工位级进模设计
BREAD PPT DESIGN
6
图1 冲压件、展开图和排样图 (a)冲压件;(b)展开图;(c)排样图
2. 按级进模的设计方法分 1)封闭形孔连续式级进模 这种级进模的各个工作形孔(除定距侧
刃形孔外)与被冲零件的各个孔及制件外 形(弯件指展开外形)的形状一致,并把它 们分别设置在一定的工位上,材料沿各工 位经过连续冲压,最后获得所需冲件。用 这种方法设计的级进模称封闭形孔连续式 级进模。如图ຫໍສະໝຸດ 所示为冲制制件及其展开 图和排样图。
BREAD PPT DESIGN
多工位级进模设计
综述
多工位级进模是一种在一副模具内将制件加工成所需工件的冲压 工艺,它将一副模具分成若干个等距离工位,在每个工位上设置—定的冲 压工序,完成零件的某部分冲制工作,经多道工序冲制完成所需要的冲压 件。
多工位级进模设计
BREAD PPT DESIGN
2
目录
冲制厚度较薄(一般不超过2mm)、产量大,形状复杂、 用于:精度要求较高的中、小型零件。
多工位级进模设计
BREAD PPT DESIGN
4
二、多工位级进模的分类
1.按冲压工序性质分 1)多工位级进冲裁模具
2)多工位级进冲裁成型模具
多工位级进模设计
BREAD PPT DESIGN
5
3)多工位级进冲裁拉深模具
(10)在冲裁形状复杂的制件时,可用分段切除方法,以提高凹模强度并 便于模具加工与制造。
多工位级进模设计
BREAD PPT DESIGN
14
3.3含局部成形工序的排样设计原则
(1)有局部成形时,可根据具体情况将其穿插安排在各工位上进行,在 保证产品质量的前提下,利于减少工位数。
角垫多工位级进模模具设计 (初稿)

存档编号华北水利水电学院North China Institute of Water Conservancy andHydroel ectric Power毕业设计题目学院专业姓名学号指导教师完成时间独立完成与诚信声明本人郑重声明:所提交的毕业设计(论文)是本人在指导教师的指导下,独立工作所取得的成果并撰写完成的,郑重确认没有剽窃、抄袭等违反学术道德、学术规范的侵权行为。
文中除已经标注引用的内容外,不包含其他人或集体已经发表或撰写过的研究成果。
对本文的研究做出重要贡献的个人和集体,均已在文中作了明确的说明并表示了谢意。
本人完全意识到本声明的法律后果由本人承担。
毕业设计(论文)作者签名:指导导师签名:签字日期:签字日期:毕业设计(论文)版权使用授权书本人完全了解华北水利水电学院有关保管、使用毕业设计(论文)的规定。
特授权华北水利水电学院可以将毕业设计(论文)的全部或部分内容公开和编入有关数据库提供检索,并采用影印、缩印或扫描等复制手段复制、保存、汇编以供查阅和借阅。
同意学校向国家有关部门或机构送交毕业设计(论文)原件或复印件和电子文档(涉密的成果在解密后应遵守此规定)。
毕业设计(论文)作者签名:导师签名:签字日期:签字日期:随着现代工业的发展,模具行业也得到了长足的发展,模具尤其是冲压模具在国民经济中的地位也更加重要。
经过对角垫的生产批量、零件质量以及零件结构的分析研究,确定用冲压的方法完成生产。
针对角垫的冲裁工艺性和弯曲工艺性,分析比较了单工序模、复合工序模和级进模的优缺点,并最终确定使用级进模完成生产。
进行了压力中心、工艺力及模具工作部分尺寸与公差的计算以及冲压设备的选用。
具体分析了模具的主要零部件的设计与制造,编制了重要零件的加工工艺过程。
列出了模具所需零件的详单,并给出了合理的模具装配图。
总体来说,该模具是一副典型的多工位级进模,包括了冲孔、弯曲、落料等工艺,共用了九个工位完成了全部冲压工艺,其中有三个空工位,保证了凹模板的强度要求。
卡片多工位级进模设计

二、排样设计
为简化模具结构,降低制造成本,提高材料利 用率,保证带料传递的稳定性及降低模具的故障和 返修的几率,拟定了如下两个排样方案。 (1)方案1 采用等宽双侧载体的单排排列方 式。如图2所示,料宽为202mm,步距为23.5mm。 共16个工位:即工位1为冲导正销孔;工位2为空工 位;工位3为冲切两端异形废料;工位4为空工位; 工位5、6为冲切中部异形孔废料;工位7为空工 位;工位8为冲切中部长方形孔废料及设置模内送
60
2013年 第6期
冷加工
D模 具
低,材料利率高(材料利用率为38.88%)。
ie & Mould
图3 方案2排样图
对以上两个方案的分析,考虑到该零件形状简 单,尺寸要求不高,零件装配时对毛刺方向没有特 殊的要求。结合模具制造成本及材料利用率等方 面,最终选用方案2较为合理。
图5 切断凸模
构简单、制造方便、造价低的自动送料装置,其共 同特点是靠送料杆拉动工艺孔,实现自动送料,这 种送料装置大部分使用在有搭边、且搭边具有一定 强度的冲压自动生产中,在拉料杆没有拉住搭边的 工艺孔时,带料需靠手工送进。在多工位级进模冲 压中模内送料通常与导正销配合使用才能保证准确
2013年 第6期
1. 模具结构特点
(1)空工位设计 该模具空工位较多,共有 11个空工位:工位2空工位为带料导正用;工位3~ 8空工位是为了模内送料机构而留;工位9、12、 14、15空工位是为了增加模具的强度。 (2)切断凸模设计 在级进模中最后一工位 切断凸模一般是用来切断载体的废料,但该模具的 切断凸模25是用来切断零件与零件之间的分离作 用。这样一来对切断凸模与卸料板及凹模板的间隙 配合要求较高,该模具在切断凸模的右边安装有挡 板,使切断凸模在其中间滑动,从而提高切断的精 度。通常该切断凸模设计成平刃口,那么会对切断 凸模所产生的侧向力较大,为减少切断时所产生的 侧向力,通常把平刃口切断凸模改为斜刃口,如图 5所示。开始冲压时可以让切断凸模再低点先接触 切断凹模,随着上模继续下行,再慢慢地进行全部 切断工作(如同剪板机的工作原理),同时也减轻 了冲裁力。 (3)模内送料设计 模内送料装置是一种结
衔铁多工位级进模设计

衔铁多工位级进模设计摘要:多工位级进模是在普通模具的基础上发展起来的一种高精度、高效率、长寿命的模具。
是技术密集型模具的总要代表,是冲模的发展方向之一。
在模具设计前必须对工件进行全面的分析,然后确定工件的冲压成型方案,正确设计模具的结构和模具零件的加工工艺规程,以获得最佳的技术经济效益。
本次设计的零件为板料冲裁弯曲件—衔铁,衔铁采用的材料为电工纯铁DT2,厚度1mm 保证了足够的强度和硬度。
该零件的外形简单,利于合理排样、减小废料。
此材料具有良好的塑性及较高的弹性、较高的冲裁性和良好的弯曲性。
关键词:级进模;冲裁;弯曲;排样;设计D esign of The M ulti-P osition P rogressive D ie ForThe Armature I ronAbstract : Multi-position progressive which is developed on the basis o f the general mold isa mold of high precision, high efficiency,and high durability. Multi-position progressive that is the development of mold is the present of technology-intensive mol. A comprehensive analysis of the workpiece must be made before the mold design. Making a workpiece program and designing the structure correctly after the analysis.The parts of the design is bengding sheet metal parts-the armature iron that is made by electrical iron DT2.The thickness of the iron is 1mm which can ensure the strength and the hardness. The parts is of simple shape that conducive to a layout and reducing waste. The blanking of the material is good and it has good plasticity.Key words: progressive die; punching; bending; layout; design1 前言1.1 概述冷冲压工艺操作简单,便于实现机械化和自动化,适合于较大批量零件的生产,其制品一般都不需要进一步的机械加工,尺寸精度和互换性也都比较好。
基于Pro/E的支撑架多工位级进模设计

22 工步 设计 创 建条 带布 局 .
③ 冲侧 弯边缘废料 ; ④两侧第 1 次向下 9 。 曲; O弯 ⑤一 通过对零件展开钣金件 的分析 , 基本工序 的顺 侧第 2 其 次向下 4 o 5弯曲; ⑥另一侧第 2 向下 4 。 次 5弯曲 ; 序应 为 : 冲裁 弯曲_ 切 断。该零件有 3 ÷ 处两个方 向 ⑦一侧第 3 向下 4 。 曲 ; 次 5弯 ⑧另一侧第 3 向下 4 。 次 5 的不 同弯 曲 , 为简化模 具结构及方便 冲压送料 , 两侧 弯 曲 , 同时切 除 中间弯 曲端废料 ; 中间 向上 z ⑨ 形弯 的 u形弯曲朝下 , 在前面进行 , 一端 的z 弯曲朝上 , 曲; 形 ⑩工件与条料切断。 在后面进行 。两侧 U 形弯 曲的外轮廓形状较复杂 , 应
Ob i u l e Bl c sg fF x d M o d l e S i o k De i n o i e q d l
a d M o e o d Ba e n t e Pr / n v d M l s d o h 0E
【 bt c】 hog nl e esu t e n a c r t s fh a , e r i dt o A s a tT r haa z t rc r adc r t ii e r dt m n em l r u y dh t u h a e sc o t p t e e h d
sr c u e u i g P o E s f r o r d c d l g r p d y a d a c r tl e i n d c r n t t r , s n r / o wa e f rp o u tmo e i , a i l n c u a ey d sg e o e a d u t n
多工位级进模设计实例

多工位级进模设计实例
1.6 计算冲裁各工艺力
6.总的冲裁力 7.卸料力 8.推件力 9.冲裁总工艺力
多工位级进模设计实例
1.7 压力中心的确定
由于冲裁力较小,并且采用对角导柱模架, 受力平稳,同时根据零件的排样图可以看出, 模具压力中心不会超出冲模模柄的投影面积。 故压力中心确定为本模具的凹模对称中心。
冲压工艺与模具设计
多工位级进模设计实例
1.1 零件的工艺性分析
1. 零件尺寸精度
2. 零件结构
形状
3. 确定冲压 工艺方案
多工位级进模设计实例
1.1 零件的工艺性分析
簧片
1.2 排样设计
多工位级进模设计实例
排样图
1.3 模具工作工程
多工位级进模设计实例
模具工作过程
1.4 材料利用率
多工位级进模设计实例
落料凸模
多工位级进模设计实例
1.10 模具主要部件零件图
卸料板
多工位级进模设计实例
1.10 模具主要实例
1.5 凹模轮廓尺寸
1
2
凹模计算尺寸
根据凹模轮廓 尺寸选取标准
凹模
选取模具结构 的典型组合
3
根据典型组合 选取标准模架
4
多工位级进模设计实例
1.6 计算冲裁各工艺力
1.工件外轮廓周边长度 2.孔(φ6 mm)周边长度 3.侧刃冲切长度 4.冲切一个工件的周边长度 5.一个工步内冲切工件的总长度
9、21—
10—防转销;
11—模柄; 13—卸料螺钉;
14—垫板; 15—
16—弹簧; 17—导套;
18—导柱; 20—承料板;
22—下模座
簧片落料冲孔级进模
典型弯曲冲压件多工位级进模设计

很 难 预 先 估 计 , 问题 只有 在 模 具 加 工 以 后 才 能 暴
空 工位 ;6 )铆 合 ;7 )空 工 位 ;8 )折 弯 ;9 )空
收稿 日期 :2 1 -1- 3 0 1 1 0 作者简介 :苏君 ( 9 7一),女 ,讲 师 ,研究方 向为模具设计 与制造 。 17 [ 0 第3 卷 61 4 第3 期 2 1— 3上 ) 02 0 (
析 , 经 分 析 弯 曲后 能 够 达 到 技 术 要 求 。 零 件 的 网
格划 分 如 图2 所示 。
1 设 计 过 程
11 工 艺分 析及 三维 实 体造 型 .
工 件 为 一 u形 弯 曲 件 ,材 料 为0 钢 板 ,厚 度 8 25 . mm,大 批 量生 产 ,未 注公 差 尺寸 为I 2 。工 T1级
要求。
P DW ( rges eDi Dein P o rsi e s )模 块 是一 个基 v g
于UG的三 维级 进模 C AD系统 ,P DW优 化 了冲 模设
图 1工 件 三 维 模 型
计 过 程 ,极 大 地 提 高 冲 压 级 进 模 设 计 效 率 。利 用 P DW 可 以 进 行 毛 坯 生 成 、坯 料 排 样 、废 料 设 计 、 条 料 排 样 、 模 架 设 计 、冲 孔 设 计 和 让 位 槽 设 计 , 而且 提 供 大 量 的 标 准 部 件 库 和 一 个 钣 金 零 件 的 识 别模 块 ,从 而加 快 了模 具设 计 的速 度 。
S _h 2 ,其 他 系统 默认 设 置 。调 入模 架 如 图9 P =0 所 示 ,还 可 以对此 模架 进行 分割 。
图6 条 料 排 样
图9 模 架 图
多工位级进模设计实例

多工位级进模设计实例在计算机科学领域中,多工位级进模设计是一种用于提高处理器性能的技术。
它通过将处理器划分为多个工位,并在每个工位上同时执行不同的指令,以实现指令级并行处理。
本文将介绍几个多工位级进模设计的实例,以帮助读者更好地理解这一概念。
实例一:乘法器设计乘法运算是计算机中常见的运算之一。
在传统的乘法器设计中,需要进行多次乘法和加法操作,整个运算过程比较耗时。
而采用多工位级进模设计,可以将乘法运算拆分为多个阶段,每个阶段在一个工位上并行执行。
例如,可以将乘法器划分为部分积生成、部分积累加和最终结果生成等多个工位,在每个工位上同时执行不同的操作。
这样可以大大提高乘法器的运算速度。
实例二:浮点数加法器设计浮点数加法是计算机中常见的浮点运算之一。
在传统的浮点数加法器设计中,需要进行多次位运算和规格化等操作,整个运算过程较为复杂。
而采用多工位级进模设计,可以将浮点数加法器划分为多个阶段,每个阶段在一个工位上并行执行。
例如,可以将浮点数加法器划分为对阶段、对尾数相加和规格化等多个工位,在每个工位上同时执行不同的操作。
这样可以显著提高浮点数加法器的运算速度。
实例三:流水线设计流水线是多工位级进模设计中常用的一种技术。
它将处理器的指令执行过程划分为多个阶段,并在每个阶段上同时执行不同的指令。
例如,可以将流水线划分为取指、译码、执行、访存和写回等多个阶段,在每个阶段上并行执行不同的指令。
这样可以大大提高处理器的指令执行效率。
实例四:并行排序算法设计排序算法是计算机中常用的一种算法。
传统的排序算法通常是串行执行的,即每次只处理一个元素。
而采用多工位级进模设计,可以将排序算法划分为多个阶段,每个阶段在一个工位上并行执行。
例如,可以将排序算法划分为分组、局部排序和合并等多个工位,在每个工位上同时处理不同的元素。
这样可以显著提高排序算法的执行速度。
多工位级进模设计是一种提高处理器性能的重要技术。
通过将处理器划分为多个工位,并在每个工位上同时执行不同的指令,可以实现指令级并行处理,从而大大提高处理器的运算速度和指令执行效率。
冲压磨具结构设计的十大经典案例

冲压磨具结构设计的十大经典案例案例一:汽车车身冲压件的多工位磨具汽车车身冲压件的磨具设计具有独特的特点和挑战。
为了提高生产效率和质量,设计师通常需要设计多工位磨具。
多工位磨具可以在一次夹紧的情况下完成多个冲压工序,大大提高了冲压生产线的效率。
案例二:飞机翼罩冲压模具飞机翼罩是航空领域中关键的部件之一,其冲压模具设计要求非常高。
翼罩的形状复杂且精度要求高,需要考虑到翼罩的强度、刚度和表面光洁度等因素。
设计师经过精心的磨具结构设计,保证了飞机翼罩的质量和性能。
案例三:家电外壳冲压磨具家电外壳冲压磨具的设计要求外壳的造型美观,同时要满足耐用性和制造成本的要求。
设计师通过合理的冲压工艺和磨具结构设计,实现了家电外壳的高效生产和质量控制。
案例四:电子产品金属外壳冲压模具电子产品金属外壳的冲压模具设计要考虑到外壳的精度、尺寸稳定性和表面处理要求。
设计师通过合理的模具结构设计和冲压工艺,实现了电子产品外壳的高质量和高效生产。
案例五:手机壳冲压模具手机壳的冲压模具设计要考虑到外观要求,如曲面和切割边缘的处理。
设计师通过创新的磨具结构设计和冲压工艺,实现了手机壳的设计复杂性和高质量要求。
案例六:钢铁行业冲压磨具设计钢铁行业的冲压磨具设计要考虑到材料的硬度和可加工性。
设计师通过合理的磨具结构设计和冲压工艺,提高了钢铁行业的生产效率和产品质量。
案例七:航天器零部件冲压模具航天器零部件的冲压模具设计要求非常高,需要考虑到零部件的材料性能、结构复杂度和重量要求等因素。
设计师通过优化的磨具结构设计和精细的制造工艺,实现了航天器零部件的高质量和可靠性。
案例八:新能源汽车零部件冲压模具新能源汽车零部件的冲压模具设计要考虑到其特殊材料和结构要求。
设计师通过创新的磨具结构设计和精细的制造工艺,实现了新能源汽车零部件的高质量和可靠性。
案例九:家具五金件冲压模具家具五金件的冲压模具设计要考虑到五金件的形状复杂度和表面质量要求。
设计师通过合理的磨具结构设计和冲压工艺,实现了家具五金件的高质量和高效生产。
多工位连续模培训资料

资源回收利用
对于多工位连续模生产过程中产 生的废料、废品等,应进行回收 利用或合理处理,以减少对环境
的污染。
环保材料
采用环保材料制作多工位连续模, 如可降解塑料、无毒涂料等,能
够减少对环境的负面影响。
THANKS FOR WATCHING
感谢您的观看
材料选择与加工工艺
总结词
适合的材料和工艺是制造的基础
详细描述
在选择材料时,需要考虑模具的使用条件、成型材料的性质等因素,以确保模具的耐用性和可靠性。 加工工艺的选择应根据模具结构和零件加工要求来确定,包括粗加工构优化
总结词
优化结构可以提高生产效率和产品质量
详细描述
轻量化材料
耐高温材料
对于高温环境下工作的多工位连续模, 需要采用耐高温材料,如耐热钢、镍 基合金等,保证模具在高温下仍能保 持稳定的性能。
为了满足产品轻量化的需求,多工位 连续模开始采用轻量化材料,如铝合 金、钛合金等,降低模具的重量。
智能化与自动化技术的发展
智能化控制
多工位连续模的智能化控制技术 不断发展,通过引入传感器、控 制器等智能元件,实现对模具工 作状态的实时监测和自动控制。
04 多工位连续模的案例分析
案例一:某汽车零件多工位连续模设计
总结词
汽车零件多工位连续模设计
详细描述
该案例介绍了汽车零件多工位连续模的设计 过程,包括模具结构设计、工艺流程制定、 材料选择等方面的内容。通过优化设计,实
现了高效、高精度的汽车零件生产。
案例二:某电子产品多工位连续模制造过程
总结词
通过对模具结构的分析,可以找出存在的问题和优化点,采取相应的措施进行改进。例如,合理布置模具零件的 位置和运动轨迹,优化模具的开合和传送机构,提高模具的刚度和稳定性等。
多工位级进模与冲压自动化

如建筑、铁路、船舶等行业的 金属结构件和零部件的冲压生
产。
03 多工位级进模与冲压自动 化的结合
结合的必要性
提高生产效率
多工位级进模与冲压自动 化结合,可以大幅提高生 产效率,减少人工干预, 降低生产成本。
提升产品质量
通过自动化控制和监测, 可以减少人为因素对产品 质量的影响,提高产品的 一致性和稳定性。
多工位级进模与冲压自动化
目 录
• 多工位级进模介绍 • 冲压自动化技术 • 多工位级进模与冲压自动化的结合 • 多工位级进模与冲压自动化的发展趋势 • 实际应用案例分析
01 多工位级进模介绍
定义与特点
定义
多工位级进模是一种先进的冲压 工艺,通过在多工位上连续完成 一系列冲压操作,实现零件的高 效、高精度制造。
特点
多工位级进模具有高效率、高精 度、高自动化程度等优点,适用 于大批量、小型、复杂零件的冲 压生产。
工作原理
工作流程
多工位级进模在工作时,将原材 料依次送入各个工位,每个工位 完成不同的冲压操作,最终得到
成品零件。
连续加工
多工位级进模采用连续加工的方式, 大大提高了生产效率,减少了人工 干预和生产成本。
02 冲压自动化技术
冲压自动化定义与特点
定义
冲压自动化是指利用自动化设备、机 器人等手段实现冲压生产过程的自动 化,包括材料送料、模具调整、冲压 加工、产品取出等环节。
特点
提高生产效率、降低劳动强度、减少 人工干预、提高产品质量和一致性。
冲压自动化工作原理
基于预设的程序和指令,自动化设备能够独立完成送料、模具调整、加工和取件等 动作。
根据产品需求,进行多工位级进模的 设计与制造,确保模具的精过自动化生产和智能控制,可 以大幅降低生产成本,提高企业
3DQuickPress在电机芯片多工位级进模设计中的应用

3DQuickPress在电机芯片多工位级进模设计中的应用I. 前言-介绍电机芯片多工位级进模设计的背景-阐明3DQuickPress在模具设计中的作用II. 电机芯片多工位级进模设计的概述-电机芯片多工位级进模设计的基本原理-多工位级进模设计的优点和应用领域III. 3DQuickPress的应用-3DQuickPress在电机芯片多工位级进模设计中的基本功能-使用3DQuickPress进行模具设计的流程和注意事项IV. 案例应用-实际案例的设计流程、模型建立和模具加工-讨论该设计中3DQuickPress的应用,分析其优势和实际成效V. 结论-总结3DQuickPress在电机芯片多工位级进模设计中的应用-探讨今后该技术的发展和应用前景言简意赅、实例丰富的相关案例和数据的引用将使本论文更具说服力和可读性。
第一章前言电机芯片多工位级进模设计是一种先进的模具设计技术,已广泛应用于各类电机和电子元器件的生产制造中。
这一技术的关键在于利用模具的多工位设计,使得在一次压力下即可完成一块芯片的多个工序,从而大幅提高了芯片生产的效率和质量。
3DQuickPress是一款专门为模具设计而开发的软件,能够提供全面的模具设计解决方案,支持芯片多工位级进模设计。
本文将重点介绍3DQuickPress在电机芯片多工位级进模设计中的应用,为模具设计工程师提供一些有用的经验和思路。
第二章电机芯片多工位级进模设计的概述1. 电机芯片多工位级进模设计的基本原理电机芯片多工位级进模设计是一种高效的生产方式,能够利用多工位模具,在单次模具操作中完成多个工序。
具体来说,该技术常用于电机芯片制造中。
在传统的制造流程中,要完成加工和成型、沟槽和焊接等多个工序,需要多个工作单元才能完成,这样不仅造成了浪费,而且还会影响电机芯片的质量。
而采用多工位模具,制造工艺可以大大简化,并能够提高制造效率,降低成本。
2. 多工位级进模设计的优点和应用领域使用多工位级进模设计可以获得多个优势。
多工位级进模设计

工序排样过程
复杂零件弯曲
送进高度
带局部成形时的工序排样
2.8 工序排样示例
3 多工位级进模实例
冲孔落料弯曲级进模
1-垫板;2-凹模镶块;3-导柱; 4-导正销;5-弹压导板;6-导套; 7-切断凸模;8-弯曲凸模; 9-凸模固定板;10-模柄; 11-上模座;12-分离凸模; 13-冲槽凸模;14-限为柱; 15-导板镶块;16-侧刃; 17-导料板;18-凹模;19-下模座
电位器外壳带料连续拉深多工位级进模
1-浮动导料销;2-小导套;3-小导柱;4-翻边凸模;5-切边凸模;6-导向套;7-冲小方孔凸 模;8-凸模护套;9-冲缺口凸模;10-凸模固定板;11-卸料板;12-侧面导板;13-冲缺口凹 模镶块;14-定位圈;15-冲孔凹模;16-顶件块;17-检测导正销;18-导线
多工位级进模设计
1
概
述
多工位精密级进模
1
概
述
多工位级进模是在普通级进模的基础上发展起来的一种 高精度、高效率、高寿命的模具,是技术密集型模具的重要 代表,是冲模发展方向之一。
1.1 多工位级进模特点
1.可以完成多道冲压工序,局部分离与连续成形结合。 2.具有高精度的导向和准确的定距系统。 3.配备有自动送料、自动出件、安全检测等装置。 4.模具结构复杂,镶块较多,模具制造精度要求很高,制造 和装调难度大。
T∑=CT
=1.2×(1/2)×0.004×
=0.012 mm
3.工序件定位方式:挡料销、侧刃、自动送料装置对工序 件送 进时定距,设置导正销则可以对工序件精确定位。
2.6 导正
导正原理
1-导料板;2-顶料销;3-侧刃挡块;4-导正销
2.7 工序排样原则与要点
冲压模具设计和制造实例
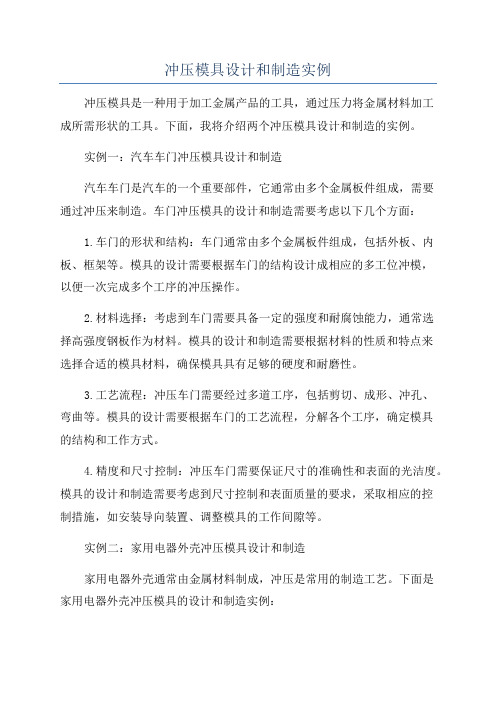
冲压模具设计和制造实例冲压模具是一种用于加工金属产品的工具,通过压力将金属材料加工成所需形状的工具。
下面,我将介绍两个冲压模具设计和制造的实例。
实例一:汽车车门冲压模具设计和制造汽车车门是汽车的一个重要部件,它通常由多个金属板件组成,需要通过冲压来制造。
车门冲压模具的设计和制造需要考虑以下几个方面:1.车门的形状和结构:车门通常由多个金属板件组成,包括外板、内板、框架等。
模具的设计需要根据车门的结构设计成相应的多工位冲模,以便一次完成多个工序的冲压操作。
2.材料选择:考虑到车门需要具备一定的强度和耐腐蚀能力,通常选择高强度钢板作为材料。
模具的设计和制造需要根据材料的性质和特点来选择合适的模具材料,确保模具具有足够的硬度和耐磨性。
3.工艺流程:冲压车门需要经过多道工序,包括剪切、成形、冲孔、弯曲等。
模具的设计需要根据车门的工艺流程,分解各个工序,确定模具的结构和工作方式。
4.精度和尺寸控制:冲压车门需要保证尺寸的准确性和表面的光洁度。
模具的设计和制造需要考虑到尺寸控制和表面质量的要求,采取相应的控制措施,如安装导向装置、调整模具的工作间隙等。
实例二:家用电器外壳冲压模具设计和制造家用电器外壳通常由金属材料制成,冲压是常用的制造工艺。
下面是家用电器外壳冲压模具的设计和制造实例:1.外壳结构和形状:家用电器外壳通常具有盒状结构,需要通过冲压来成形。
模具的设计需要根据外壳的尺寸和形状,设计成相应的单工位或多工位冲模。
2.材料选择:外壳通常采用不锈钢或者冷轧钢板作为材料,以保证外壳的强度和耐腐蚀能力。
模具的设计和制造需要选用适当的模具材料,以确保模具具有足够的硬度和耐磨性。
3.工艺流程:外壳冲压通常包括剪切、成形、冲孔、折弯等工序。
模具的设计需要分解各个工序,确定模具的结构和工作方式,以便一次完成所有工序。
4.精度和表面质量:外壳冲压需要保证尺寸的准确性和表面的光洁度。
模具的设计和制造需要考虑到尺寸控制和表面质量的要求,采取相应的控制措施,如安装导向装置、选用合适的冲头等。
冲压工艺与模具设计第6章多工位级进模设计
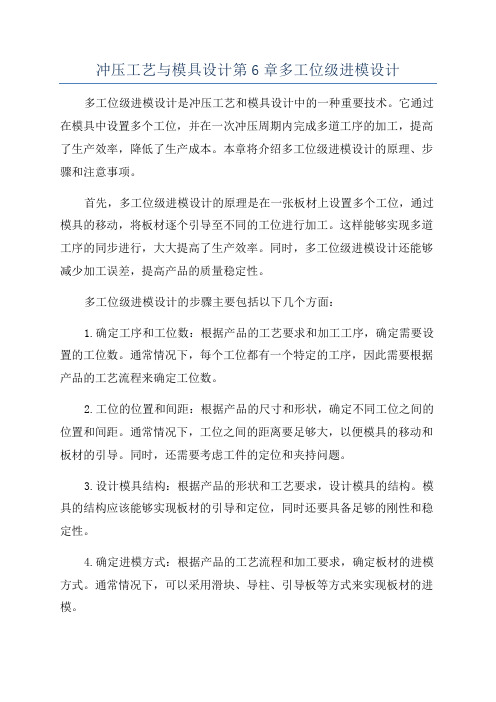
冲压工艺与模具设计第6章多工位级进模设计多工位级进模设计是冲压工艺和模具设计中的一种重要技术。
它通过在模具中设置多个工位,并在一次冲压周期内完成多道工序的加工,提高了生产效率,降低了生产成本。
本章将介绍多工位级进模设计的原理、步骤和注意事项。
首先,多工位级进模设计的原理是在一张板材上设置多个工位,通过模具的移动,将板材逐个引导至不同的工位进行加工。
这样能够实现多道工序的同步进行,大大提高了生产效率。
同时,多工位级进模设计还能够减少加工误差,提高产品的质量稳定性。
多工位级进模设计的步骤主要包括以下几个方面:1.确定工序和工位数:根据产品的工艺要求和加工工序,确定需要设置的工位数。
通常情况下,每个工位都有一个特定的工序,因此需要根据产品的工艺流程来确定工位数。
2.工位的位置和间距:根据产品的尺寸和形状,确定不同工位之间的位置和间距。
通常情况下,工位之间的距离要足够大,以便模具的移动和板材的引导。
同时,还需要考虑工件的定位和夹持问题。
3.设计模具结构:根据产品的形状和工艺要求,设计模具的结构。
模具的结构应该能够实现板材的引导和定位,同时还要具备足够的刚性和稳定性。
4.确定进模方式:根据产品的工艺流程和加工要求,确定板材的进模方式。
通常情况下,可以采用滑块、导柱、引导板等方式来实现板材的进模。
5.考虑模具的适应性:在设计模具的同时,还要考虑模具的适应性。
模具应该能够适应不同尺寸和形状的板材,以应对不同的生产需求。
在进行多工位级进模设计时,还需要注意以下几点:1.合理安排工位的顺序:根据产品的工艺要求和加工工序,合理安排工位的顺序。
通常情况下,先进行简单工序,再进行复杂工序,以确保生产的连续性和高效性。
2.考虑工位的平衡性:在设置多个工位时,要考虑工位之间的平衡性。
工位之间的加工时间应该尽量一致,以避免生产的瓶颈。
3.加工误差的控制:在多工位级进模设计中,由于板材的引导和移动,容易产生加工误差。
因此,需要在设计模具时,采取相应的措施来控制加工误差,提高产品的精度和一致性。
单机多工位模具结构设计

—
莫 I l 具l ll 网
/
一
I
l
;
。
.
下垫 板 件
1 . 柱 1. 0导 脱料 板 1
1. 3上模
板 1 . 垫板 1. 4上 5上模 座 1. 凸包 凸模 6冲 1. 7冲孔 凸模 I 1. 8 抽牙 凸模 图6 第一工位模具结构 1. 9等高套筒
图7 第二工位模具结构
l 1 门 l l 户 l l 网 l l 站
/
l
l i
I 。
ll
/ 震 一
\ \
÷
l
零件 Ⅱ 6定位销 7下垫板 8 . . . 下模 座 9导 套 1 . . 0下模板 l. 导柱 1 脱料板 1 背板 l. 1 2 3 4上模板 1. 5上垫板 1. 6上
/
模座 1. 7上模折弯零件 I 1 上 模 折弯零件 Ⅱ 1. 8 9上模折 弯零件 Ⅲ 2 . 0冲孔凸模 I 2 . 1 冲孔凸模 Ⅱ 2 . 2等高套筒
出一个 工位来放置机 械手 的翻转 机构 , 来实现制件在 第 四工 步的制件放置要求 。故此制件 的单 机多工位 模 具 实 际上 需 要 四工 位 。预 计 生 产 节拍 为 1 次/ 5 a 。最终单机多工位模具的动作顺序为 : rn i
图 4 折 弯成形 、 在凸包上冲孔工步
机械手到料筒取制件 ( 一工步的制件 ) 第一 第 一 工位 ( 图 6 第二 工步 ) 第二 工位 ( 图7 第 三工 见 , 见 ,
ll ≤ 乏 ≤l
l l j
l l - o
霪
、 、 \
\
ll ∽l
l I 国
、
- 1、下载文档前请自行甄别文档内容的完整性,平台不提供额外的编辑、内容补充、找答案等附加服务。
- 2、"仅部分预览"的文档,不可在线预览部分如存在完整性等问题,可反馈申请退款(可完整预览的文档不适用该条件!)。
- 3、如文档侵犯您的权益,请联系客服反馈,我们会尽快为您处理(人工客服工作时间:9:00-18:30)。
已批产项目介绍
APAC
序号 图片
2PX项目
冲压工艺 OP10 DR OP20 TR+PI OP30 FL+BU+RST OP40 PI+C-PI OP10 DR OP20 TR OP30 FL+RST OP40 PI+C-PI OP10 DR OP20 TR+PI OP30 RST OP40 CUT+C-PI OP50 C-PI+SEP 压机
1
1500 TRF
2
1500 TRF
3
1500 TRF
APAC
2PX项目 DL图
APAC
2PX项目 工序安排
APAC
2PX项目 机械手设计
在制MODELL-Z项目介绍
在制MODELLБайду номын сангаасZ项目介绍
正在制造的多工位模具为大众 MODELL-Z(B、C)项目,共6组零件26 套模具。现已制造完毕准备在多工位压机 上调试。
多工位模具案例介绍
多工位模具设计注意问题总结
1、根据压机干涉曲线考虑机械手、零件与模具三者之间的干涉问题; 2、模具需设计提升器保证机械手夹件方便及保证送料高度一致; 3、设计时需考虑零件定位的稳定性及机械手夹持零件时的稳定性; 4、保证废料排除顺畅;(冲压工艺制定时考虑全面) 5、零件前后工序冲压方向改变需设计空工位来调整冲压方向; 6、为方便模具装夹可考虑采用2套模具共用垫板结构;