潜在失效模式及后果分析(DFMEA)
汽车内外饰件DFMEA潜在设计失效模式和后果分析
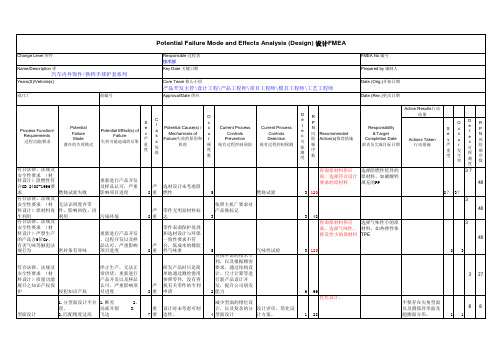
设计时考虑电镀区 域的控制,对有缺 陷或装配点,不再 电镀。或者增加卡 脚长度,来增加卡 局部功能区域去电 6 脚的弹性 镀,增加卡脚长度 设计时考虑弹簧的 4 弹性系数和强度。 设计按钮时考虑按 钮的功能性过盈配 5合
3?
48
3
无法识辨废弃零 件,影响回收、再 利用 污染环境
严 8重
零件无明显材料标 志 零件表面保护处理 和选材设计与环保 一致性要求不符 合,低成本的橡胶 件气味重
48
3
密封条有异味
重新进行产品开发 、过程开发以及样 品认可,严重影响 项目进度
48
严 8重
符合法律、法规及 安全性要求 (材 料设计)质量功能 展开之知识产权保 护 侵犯知识产权
停止生产,无法正 常供货;重新进行 产品开发以及样品 认可,严重影响项 目进度 2. 3.
严 8重
研发产品时只是简 单地通过测绘借用 参照零件,没有查 找有关零件的专利 申请
3
6 96 优化设计, 不要存在尖角型面 以及圆弧异形面及 超擦面分形。
27
型面设计
1.分型面设计不合 1.断差 理。 局部开裂 2.匹配精度过高 飞边
燃烧试验失败
重新进行产品开发 及样品认可,严重 影响项目进度
咨询原材料供应 选择阻燃性优异的 商,选择符合设计 原材料。如碳酸钙 要求的原材料 填充的PP 严 8重 选材设计未考虑阻 燃性 5 依照主机厂要求对 产品做标记 3 3 48 咨询原材料供应 选择气味性小的原 商,选择气味性, 材料。如热弹性体 挥发性小的原材料 TPE 5 查找申请的技术专 利,以及根据顾客 要求,通过结构设 计、尺寸计算等进 行新产品设计开 发,提升公司研发 2 能力 减少型面的错位设 计,以及复杂的分 设计评审,简化设 4 型面设计 计方案。 气味性试验 3 120 8 3 燃烧试验 3 120 8? 3?
电池管理系统BMS潜在失效模式及后果分析(DFMEA)

外部供电低于系统供电最 小电压
系统供电不足无法运行
5 ☆ 电源输入范围不满足指标要求
在指标范围内,选择宽范围输入 的电源模块
3
老化试验
3
45
23 BMS数据存储
数据存储
无法正常存储历史数据
历史数据无法正常保存和 分析
2 ☆ 存储芯片损坏
采用汽车级元器件设计 老化测试
3 老化试验 2 12
24
电源模块 符合技术要求
10
设计验证
1
70
34
绝缘电阻检测 功能
在充电、放电状态下对车 身与电池负极之间的电阻 进行实时检测
在充电、放电状态下,绝 缘采样值跳变
绝缘电阻检测阻值不准,造 成漏电检测误报,影响车 辆行驶
7
☆
平衡桥式绝缘方案设计中绝缘采集 回路滤波电容容值100NF偏小
新电路修改为10UF,功能要充分 进行环境实验验证,包括充电、 放电、高低温实验等
BMS温度采集电路分压电阻损坏或
温度传感器损坏
高低温测试
1 温度采集功能 温度进行实时检测,并且
7☆
精度符合技术要求
温度采集显示温度一直保 持不变,且显示数值与实 际不符
温度采集功能失效,导致 BMS无法检测到温度
BMS与温度传感器接触不良
老化测试 震动测试
2 震动试验 3 42
对电池总电压进行实时检 电池电压采集不到
对接触器失去部分控制, 导致其闭合后不能断开
电源系统一直和负载连 接,使电池一直处于放电 状态
6
高压回路接触器 对接触器实现完全控制, 对接触器失去部分控制导 电源系统和负载失去连
控制功能
包括闭合与断开
DFMEA - 产品设计失效模式及后果分析
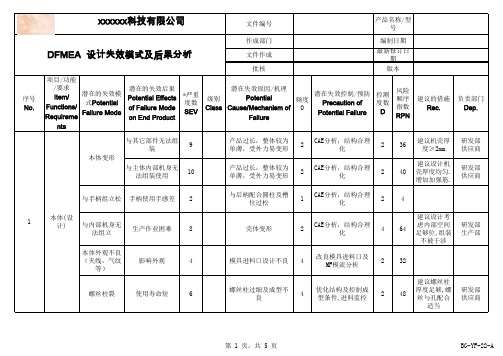
文件编号作成部门文件作成批核序号No.项目/功能/要求Item/Functions/Requirements潜在的失效模式PotentialFailure Mode潜在的失效后果Potential Effectsof Failure Modeon End Product*严重度数SEV级别Class潜在失效原因/机理PotentialCause/Mechanism ofFailure频度O潜在失效控制/预防Precaution ofPotential Failure控测度数D风险顺序指数RPN建议的措施Rec.负责部门Dep.与其它部件无法组装9产品过长,整体较为单薄,受外力易变形2CAE分析,结构合理化236建议机壳厚度≥2mm研发部供应商与主体内部机身无法组装使用10产品过长,整体较为单薄,受外力易变形2CAE分析,结构合理化240建议设计机壳厚度均匀.增加加强筋.研发部供应商与手柄组立松手柄使用手感差2与后柄配合圆柱及槽位过松1CAE分析,结构合理化24与内部机身无法组立生产作业困难8壳体变形2CAE分析,结构合理化464建议设计考虑内部空间足够位,组装不被干涉研发部生产部本体外观不良(夹线,气纹等)影响外观4模具进料口设计不良4改良模具进料口及MF模流分析232螺丝柱裂使用寿命短6螺丝柱过细及成型不良4优化结构及控制成型条件,进料监控248建议螺丝柱厚度足够,螺丝与孔配合适当研发部供应商本体变形xxxxxx科技有限公司产品名称/型号编制日期最新修订日期版本本体(设计)DFMEA 设计失效模式及后果分析1*严重度数SEV高于或等于5的需要填写后面的建议措施。
dfmea潜在失效模式及后果分析案例

7
两侧导向筋强度不 足
CAE分析,导向筋 强度合理化 增加加强筋,提 高强度 连接处配合方式 选择合理
8
撞击导致结构破坏
8
连接处密封性差
密封性
手柄密封性 软管与软管连 不满足客户要 接管的密封性 求,影响手柄吸 差 尘效率 9 连接处密封性不足 增加密封件
裸机通过 重要部位断 需通过球 球击测试, 产品无法再使 裂(尤其是机 击测试 功能正常, 用 壳) 无断裂 电池包2000 电池包松脱或 次插拔寿命 电池使用效率 测试后挂靠 低 不牢 通过整机配 电池包撞墙 测试 机壳配合处断 裂
3
105
排除电池包倒扣位, 各暂定一个插拔力范 围。例3-5 kgf 1.参照样机考虑加弹 簧或弹片式减振结构
尺寸链分析计算保证尺 寸精度 尺寸链分析计算保证尺 寸精度 尺寸链分析计算保证尺 寸精度
检测插拔力 1.单边间隙 0.4mm以上 2.参照园林产 品
保证下盖与进 气口橡胶套翻 边配合无间隙 尘桶和下盖橡 胶密封圈尺寸 保证无间隙 分离管密封圈 翻边与尘桶之 间单边0.2mm过 盈 导流锥与橡胶 圈压装0.3mm过 盈 进气口与风机 橡胶套之间配 合单边过盈 过渡配合,IQC 尺寸全检 气阀密封圈喇 叭口做大,有 段直边配合 进气端两颗螺 丝柱保证高度 方向精度 密封圈与通风 盘内孔有单边 0.2mm过盈,检 测旋转力度 面接触部位开 槽加O型圈
8
A
1.塑件壳体加强筋 1.合理布设筋板 布设不合理 2.连接处强度薄 2.零件连接处强度 弱处加固 过于薄弱 1.机壳未做圆滑过 渡,磨损过大 2.电池包倒扣弹簧 疲劳 1.机壳参照园林 产品做圆滑过渡 2.选用成熟的电 池包 1.参照园林产品 机壳限位筋位强度 设计 2. 不够 配合尺寸计算累 积公差 1.参照园林产品 机壳与电池包卡扣 设计 2. 配合不当有干涉 配合尺寸计算累 积公差 机壳与电池包配合 配合尺寸计算累 间隙不当或无弹性 积公差 减震结构
发动机系列 潜在设计失效模式和后果分析(DFMEA)

全
加强筋布控不合理
产品功能需求;减 少碰穿面,设计时 严 无明显过度增减壁 6 重 厚现象
设计时未充分考虑 严 与其配合安装物的 8 重 安装尺寸公差
卡夹留有的空间余 量不合理,或者设 计时公差标注配合 不好,对配合强度 严 估计不足,设计时 8 重 出现偏差
1.设计时未考虑卡 脚除了配合橡皮胶 套还要与发动机护 严 板配套。2.没有考 7 重 虑后续变形问题,
咨询原材料供应 商,选择符合设计 3 120 要求的原材料
3 72
咨询原材料供应 商,选择气味性, 3 120 挥发性小的原材料
6 96
选择阻燃性优异的 原材料。如碳酸钙 填充的PP
8 3 3 72
选择气味性小的原 材料。
8 3 3 72
结构型面设计 结构型面设计 结构型面设计
1.断差
1.分型面设计不合 2.错位
缺陷积累的经验。
3 108 向主机厂索取与整 车匹配关联尺寸数
4 128 据
3 48
3 126
装配工艺可行性/ 安装工具的运动空 间狭窄
装配困难,客户抱 怨
6
发动及标牌设计
字体高低的控制
字体高低设计不合 理会导致成型时字 体表面熔接痕明显
震动设计
卡脚不单单是装配
强度,同时要考虑 卡脚断裂,从发动
发动机使用过程的 机上剥落等完全失
Approval/Date 供应
Process Function/ Requirements 过程功能/要求
Potential Failure Mode 潜在的失效模式
S
Potential Effect(s) of e
Failure 失效可能造成的后果
DFMEA设计失效模式及后果分析
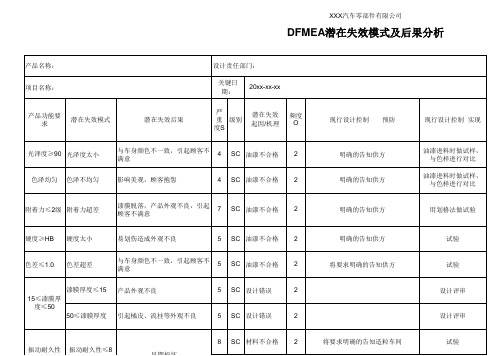
设计评审
3
设计评审
中间开口、 开孔或边沿 无尖角、无
尖边缘
中间开口、开孔 或边沿有尖角、
尖边缘
外观不良,易产生飞边,并导致 后期修整困难
6
圆柱、卡扣 座、安装筋 等结构强度
足够
圆柱、卡扣座、 安装筋等结构强 加强筋少、矮,壁厚太薄 度不够,易断裂
6
安装方便
安装困难 效率低、拆卸不方便
8 SC 材料不合格 2
耐高温性 不耐高温性 性能下降、强度下降发粘异臭味 8 SC 材料不合格 2
耐热循环性 能良好
耐热循环性能差 易变形、早期失效
耐振动性性 能良好
耐振动性性能差
易变形、断裂、脱落
振动性耐久 振动性耐久性能
性能良好
差
易断裂、早期失效
耐气候老化 耐气候老化性能
性能良好
差
变色、早期失效
试验验证
3
将窄、细、薄等部位加强
设计评审
3
将要求明确的告知造粒车间
试验验证
4
增加定位点
设计评审
3
将要求明确的告知造粒车间
试验验证
4
设计定位面、槽、柱等结构
设计评审
5
图样评审、数模验证
2
设计评审
2
设计评审
2
在三维数模进行面分析
设计评审
壁厚不能超过本体壁厚的1/3,最大不 3 能超过1/2。必须超过时,须对根部进
6
产品易于涂 装
产品难涂装 外观不良
6
尽量避免嵌 件结构 嵌件数量多
效率低、不安全、易损伤模具或 产品
6
嵌件不脱落 、不转动
DFMEA失效模式分析报告

度
O
现行控制
探
测
度
D
RPN
建议
方法
责任
及目
的完
毕日
期
方法成果
防止
探测
采用的方法
S
O
D
RP
N
PCBA
EPON各项
指标合客
户规定
陶瓷电容(C1 C23C24C60源自C46..)影响产品性能、寿命
1
1
1.元器件一致性局限性 2 器件破损
2
1.元件降额使用,最小确保元件使用降额 90%2.规定全部器件严格测试
2
6
无
光模块
(U17)
影响产品性能
3
3
2
零件承认产品试作产品验证
3
54
无
LED灯(LED1-LDE5)
影响产品性能
2
3
1
零件承认产品试作产品验证
3
18
无
PCBA
EPON 各项指标合客户规定
FLASH(U30)
影响产品性能
2
1
1.元器件
一致性局
限性 2.器
件破损
2
1.元件降额使用,最小确保元件使用降额 90%2.规定全部器件严格测试
设计失效模式分析
DESIGNFMEA
产品名称:
NAME:
日期:
DATE:
客户产品型号:
CUSTOMERTYPENO:
批准
Approvedby
审核
Checkedby
拟 制
Madeby
产品EP401M潜在失效模式及后果分析
(设计FMEA)
子系统
功效规定
DFMEA设计潜在失效模式及后果分析范本

4
64
长时间使用,材料摩损严 选择合适的材料,
重
优化踏板结构
2
材料试验,疲劳试 验,设计评审
4
64
迟滞力过大
踏点到旋转中心的距离短
设计符合客户要求 得结构
2
设计计算,评审。
3
54
踏板回位不畅,可 10 Z
能发生驾驶员想减
材料选择不当
选择合适的摩擦材 料
2
材料试验
3 60
速但不能减速
迟滞机构的表面粗糙度大
差
结构和电路
2
EMC试验
3 54
两路信号不同步 ECU报错,车辆不 8 能正常行驶
线性度不符合要求 高低温环境的影响
规定霍尔管在磁 场中的位置
2 初始性能
3 54
选用符合要求的电 子元器件
3
高低温存储试验, 高低温循环试验, 热冲击试验
3
63
配合过紧导致两个霍尔管 设计合理的定位结 安放的高度位置不一致 构
在踏板寿命期 无信号输出 内要保证踏板 旋转角度内需 要输出满足客 户要求的信号
ECU报错,车辆不 8 能正常行驶
☆ 过电压,短接,反接引起 优化电路,增加过
元器件损坏
压保护
2
过压试验,短接试 验,反接试验
3
48
环境潮湿导致短路
采用密封好的结构 3 防水试验
3 72
抗外界电气环境干扰性能 设计抗干扰性好的
有力的感觉,不易
弹簧力偏小
设计合理弹簧力值
2
设计计算,评审。 弹簧检测
2
36
控制车辆速度
内外压簧其中一只失效
选择合适得弹簧参 数及材料
DFMEA设计潜在失效模式和后果分析管理程序

版本修改条款1.目的通过分析、预测设计、设计中潜在的失效,研究失效的原因及其后果,并采取必要的预防措施,避免或减少这些潜在的失效,从而提高产品、过程的可靠性。
2.适用范围适用于公司产品设计DFMEA活动的控制。
3.职责3.1研发中心(PD)负责组织成立DFMEA(设计FMEA)小组,负责DFMEA活动的管理。
工程部(PE)负责组织成立PFMEA(过程FMEA)小组,负责PFMEA活动的管理。
3.2研发中心、工艺、品质、生产部、业务部等部门指定人员参加DFMEA小组与PFMEA小组。
必要时,由品质邀请供应商、客户参加。
3.3DFMEA小组负责制定《DFMEA潜在失效后果严重程度(S)评价标准》、《DFMEA潜在失效模式发生频度(O)评价标准》、《DFMEA潜在失效模式发现难度(D)评价标准》。
并负责准备《DFMEA和PFMEA的措施优先级(AP)》。
4.工作程序4.1设计FMEA的开发实施4.1.1DFMEA实施的时机4.1.1.1按APQP的计划进行DFMEA。
4.1.1.2DFMEA在设计之前开始。
DFMEA小组应在提交设计计划批准前就要收集资料,对以往的项目、样品试产时出现的问题、以及客户在检测样品时所反馈的信息进行分析。
4.1.1.3发生设计更改时,应复查DFMEA文件,其应体现最新的设计(或工艺设计水平)及改善,采取最新的相应措施。
4.1.2PFMEA实施前的准备工作4.1.2.1研发中心牵头成立DFMEA(设计FMEA)小组,研发中心(R&D)、品质、生产部、物料部采购等部门指定人员参加DFMEA小组,必要时,由品质邀请供应商、客户参加。
4.1.2.2在DFMEA活动实施前,DFMEA小组应制定出《DFMEA潜在失效后果严重度(S)评价标准》、《DFMEA潜在失效模式频度(O)评价标准》、《DFMEA潜在失效模式探测度(D)评价标准》。
a)DFMEA小组根据FMEA手册参考标准,确定出本公司的实际示例。
硬件设计过程潜在失效模式和后果分析(DFMEA)

重要 收音天线端受瞬时高电 3 压击坏失效。
重要 收音天线接收不好; 3
重要 主机12V输入滤波电路 4 不合格。
重要 12V供电低压检测及高 4 压保护不合格导致。
重要 按键AD检测电路受干扰 3 。
重要 串口数据以11520HZ的 3 速率传输,干扰音频。
重要 DDR走线没达到要求。 3
重要 倒车视频源受整车电源 4 干扰。
选用Molex 连接 器,质量可靠;
高温+70度运行按键 4 测试。
蓝牙模块软件处理 蓝牙音频回声体验 2
3G模块软件处理 3G语音回声体验。 2
TFT5V供电滤波电路 视频信号发生器标 2 准信号输入,TFT显 示测试。
DDR处PCB设计严格 视频老化不间断测 4 按照设计规则走线 试。
FFC厚度与FFC座子间隙不配 面板按键无作用 合
音频背景噪音测试有超标噪 用户体验差 音
7
重要 触摸屏材料耐高,低温 3
选择可靠的触摸屏 触摸屏高温,低温 4
工作范围;生产工艺不
厂家
老化测试。
合格。
7
重要 陶瓷电容受温度影响出 3
选择X7R,X5R型陶瓷 LCR测试仪辅助测 4
现偏差,影响电路性能
接口位置结构设计 GPS天线插拔力拉 4 不干涉;选用合格 力计,压力计测试 GPS座子,接头。 。
PCB天线端阻抗匹配 WINCE下GPS串口数 4
50欧姆。
据检测。
PCB天线端阻抗匹配 3G串口数据检测, 6
50欧姆;3G天线至 界面信号强度显示
于面壳无五金遮挡 检测。
处。
DFMEA设计潜在失效模式及后果分析

7
項目
潛在失 潛在失效
潛在原因/ 8 現行設計控制
建議行動 責任與目標
行動結果
效模式 之效應 功能
失效機制
嚴 重 性
等 級
發 預防性 生 頻 率
探測性
風 難險 檢優 度先
數
完成日期 已採取行動 風
嚴發難險 重生檢優 性度度先
數
9
10
11
12 13
14
15
16
17 18 19
20
21
22
8
FMEA表格
0.010 / 1000
發生度
10 9 8 7 6 5 4 3 2 132
FMEA表格
• 現行設計控制
➢ 現有的設計控制可以預防或驗證出該失效模式 及/或失效原因
➢ 一般可分為下 2 種設計控制
1.
的控制 2.
的控制
預防該失效模式/效 應/原因/機制出現 或減低出現頻次
用分析或測試方式, 可以失效模式/效應 /原因/機制出現前 偵查出來
➢ 是量度失效的風險指數 ➢ 數值愈高,代表風失效風險愈高 ➢ 應在設計發展過程前盡早完成控制
37
FMEA表格
• 建議行動
➢ RPN排序完成後,應該對排序最高的、 極為重要的項目首先採取行動
➢ 建議先處理高於 100分風險度的項目 ➢ 不論RPN指數為多少,應對一些高嚴重
性(S)的項目多加留意,例如S=9, 10
➢ 應根據公司過住的記錄,自行訂立指標 ➢ 設計小組對 評定準則和分級規則應意見
一致,即使因為個別產品分析作了修改也 應一致
31
發生度(O)的提議指標
失效發生的可能性
很高: 持續的ห้องสมุดไป่ตู้效 高: 反複發生的失效 中等: 偶然發生的失效
DFMEA潜在设计失效模式及后果分析
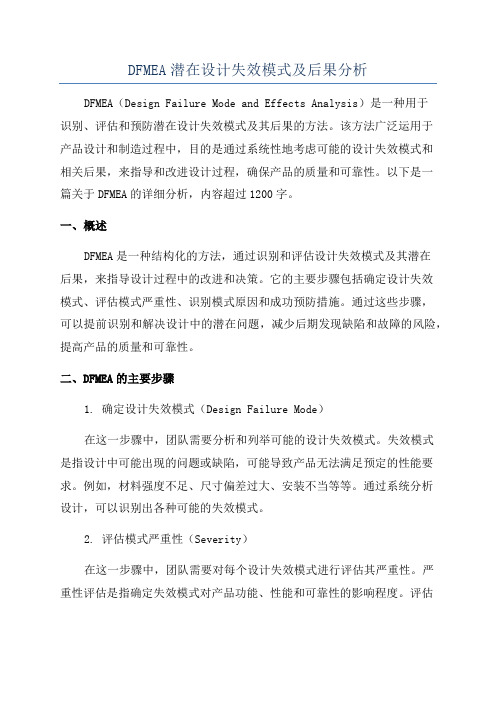
DFMEA潜在设计失效模式及后果分析DFMEA(Design Failure Mode and Effects Analysis)是一种用于识别、评估和预防潜在设计失效模式及其后果的方法。
该方法广泛运用于产品设计和制造过程中,目的是通过系统性地考虑可能的设计失效模式和相关后果,来指导和改进设计过程,确保产品的质量和可靠性。
以下是一篇关于DFMEA的详细分析,内容超过1200字。
一、概述DFMEA是一种结构化的方法,通过识别和评估设计失效模式及其潜在后果,来指导设计过程中的改进和决策。
它的主要步骤包括确定设计失效模式、评估模式严重性、识别模式原因和成功预防措施。
通过这些步骤,可以提前识别和解决设计中的潜在问题,减少后期发现缺陷和故障的风险,提高产品的质量和可靠性。
二、DFMEA的主要步骤1. 确定设计失效模式(Design Failure Mode)在这一步骤中,团队需要分析和列举可能的设计失效模式。
失效模式是指设计中可能出现的问题或缺陷,可能导致产品无法满足预定的性能要求。
例如,材料强度不足、尺寸偏差过大、安装不当等等。
通过系统分析设计,可以识别出各种可能的失效模式。
2. 评估模式严重性(Severity)在这一步骤中,团队需要对每个设计失效模式进行评估其严重性。
严重性评估是指确定失效模式对产品功能、性能和可靠性的影响程度。
评估的标准包括安全性、可用性、性能、可靠性等。
根据评估结果,可以确定哪些失效模式对产品质量和可靠性的影响最大。
3. 识别模式原因(Causes)在这一步骤中,团队需要对每个设计失效模式进行分析,找出导致该失效模式发生的根本原因。
原因可以是设计参数选择不当、材料质量问题、制造过程中的错误等等。
通过识别原因,可以找到解决相应失效模式的关键点,从而提出改进的设计方案。
4. 成功预防措施(Preventive Actions)在这一步骤中,团队根据识别出的失效模式和原因,制定相应的预防措施。
设计过程潜在失效模式和后果分析(修改)(DFMEA)
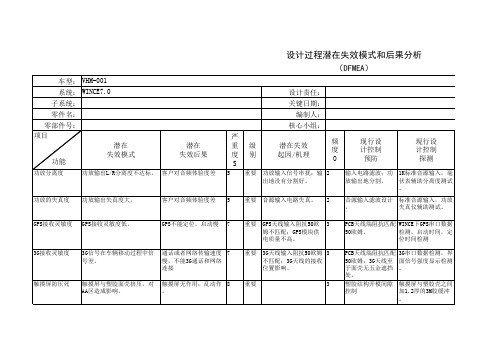
2
把音频解码IC数字 音频指标测试 地和模拟地分割
在LED电回路中串联 暗室灯光测试 电阻,阻值按要求 调节
晶体靠近IC,走线 通过实验室EMC测试 尽量短。
核心板SD1,SD2口 不读取TF卡,不识别卡; 功能不具备
7
容易损坏
载板MCU程序烧录 生产产线不能批量烧录程序 MCU烧录,升级不方便 5
重要 TFT板5V电源滤波不良 3 。
重要 倒车视频源受整车电源 4 干扰。
选用MIC灵敏度较高 MIC语音测试。 的器件,组装到位
选用合格的ALPS编 低温-20度保存启
码器;
动,运行测试。
加强SMT生产工艺 高温+70度运行测试 。
选用Molex 连接 器,质量可靠;
高温+70度运行按键 测试。
增加ESD保护器件 SD端口静电8K放电测 试
载板预留烧录座; 样机MCU烧录时 预留测试点 考虑加屏蔽罩屏蔽 通过实验室EMC测试
考虑加屏蔽罩屏蔽 通过实验室EMC测试
面板加屏蔽罩;KEY 通过实验室EMC测试 处加ESD防护
附件6 0303-034
DFMEA编号: 编制日期:
版本号:
探
测 度
RPN
5 120 收音天线端口加TVS
3 72 选择合适的收音方 案,PCB设计合理
4 96 增加1豪亨的磁芯线 圈,3300UF大电容 滤波
3 72 增加低,高电压检 测电路,保证供电 10.8--14.4V
5 90 按键AD检测上增加 磁珠
3 45 PCB设计GPS串口走 线两边包地
5 120 结构设计合理,一 体化设计
D
建议措施
3 30 RC音源滤波调整
DFMEA设计潜在失效模式及后果分析
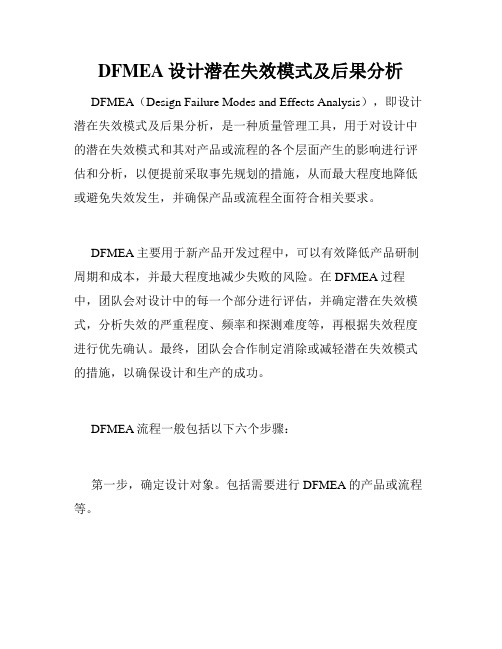
DFMEA设计潜在失效模式及后果分析DFMEA(Design Failure Modes and Effects Analysis),即设计潜在失效模式及后果分析,是一种质量管理工具,用于对设计中的潜在失效模式和其对产品或流程的各个层面产生的影响进行评估和分析,以便提前采取事先规划的措施,从而最大程度地降低或避免失效发生,并确保产品或流程全面符合相关要求。
DFMEA主要用于新产品开发过程中,可以有效降低产品研制周期和成本,并最大程度地减少失败的风险。
在DFMEA过程中,团队会对设计中的每一个部分进行评估,并确定潜在失效模式,分析失效的严重程度、频率和探测难度等,再根据失效程度进行优先确认。
最终,团队会合作制定消除或减轻潜在失效模式的措施,以确保设计和生产的成功。
DFMEA流程一般包括以下六个步骤:第一步,确定设计对象。
包括需要进行DFMEA的产品或流程等。
第二步,构建流程选择。
在这一步中,团队将制定具体的流程,以便能够在DFMEA中对每个过程进行评估和分析。
第三步,确定失效模式。
通过对设计的产品或流程的每一个部分进行审查和评估,识别出可能存在的失效模式。
第四步,分析失效效果。
在这一步中,团队考虑每个潜在失效模式的可能造成的实际效果,分析失效对顾客、公司、维护等方面的影响。
第五步,确定严重程度、频率和探测难度。
通过对每个潜在失效模式的影响进行评估,以便确定其对顾客、公司和维护方面的影响程度、发生的频率和探测难度。
第六步,确定纠正和预防措施。
通过对失效模式的分析和评估,确定有效的改进方案,以预防或消除潜在的失效模式。
DFMEA对于企业来说,具有很多的好处。
首先,它可以提前发现设计中的问题,降低产品故障率,提高产品的可靠性,减少客户抱怨和售后服务次数;其次,它可以帮助企业降低产品开发和生产成本,减少成本浪费;还可以帮助企业提高品质和声誉,提升客户满意度。
总之,DFMEA是一种非常有用的工具,可以有效地降低新产品开发过程中的风险,提高产品的质量和信誉,为企业的成功创造坚实的基础。
DFMEA 座椅泡绵 潜在失效与后果分析

xxx-xx-xx 汽车 座椅面料 系统 座椅 泡绵 核心小组: 项目 子系统 零组件:坐垫、靠背 xxx车 设计责任: 关键日期: xx部 -xx-xx 编制: FMEA日期(编制): 探 风险 建议 测 顺序 数 措施 度 R.P.N D 每批次首 3 90 改善工艺 件检查 现行探测 设计控制 自测 5 180 甲醛含 量要求≤ 300mm/k g 供应商改 善工艺 供应商改 善工艺 供应商改 善工艺 生产管控 责任和 目标完 采取的 成日期 措施 质保部 措施执行结果 严 发 探 R.P.N 重 生 测 度 率 度 同建议 2 5 2 20 措施 依照检 测报告 变更标 准 同建议 措施 同建议 措施 同建议 措施 同建议 措施 依照检 测报告 变更材 质 9 2 3 54 FMEA编号: 001 污染 燃烧性 (mm/min)
大多数顾客感 觉有缺陷 50%顾客感觉 有缺陷 50%顾客感觉 有缺陷 大多数顾客感 觉有缺陷 不符合政府的 法规
4 3 3 4 9
○ 影响外观,乘坐体 验不舒服 ○ 影响外观,乘坐体 验不舒服 ○ 影响外观,乘坐体 验不舒服 ○ 影响外观,乘坐体 验不舒服 ● 泡沫阻燃未能达标
车型年度/车辆类型:
严 重 潜在失效模 潜在失 效后果 式 度 S 功能
色泽/色差
顾客不满意
6
气味 1.增加乘 坐舒适 感; 2.保护车 内零部 件; 3.保护乘 客免受划 伤等。
不符合政府的 9 法规
发 生 潜在失效起因/机理 现行预防设计控制 率 O ☆ 制作工艺管控,材 5 首次供货提供第三方 料色牢度要求低(染 检验 料的热稳定性差) ● 甲醛标准偏低 4 首次供货提供第三方 检验
6 6 5 5 4
设计潜在失效模式及影响(DFMEA)的分析理解与应用
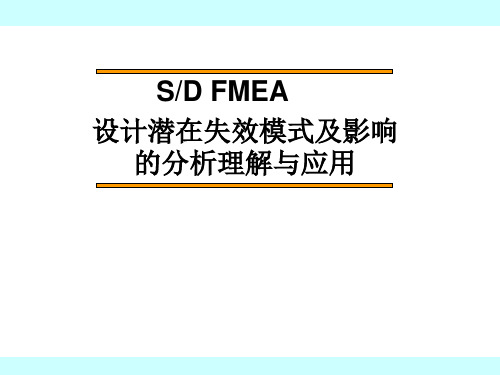
课程回顾
一.FMEA背景知识 二.实施FMEA的原因 三.实施FMEA的步骤
谢 谢!
1.FMEA基本知识—常规的设计思路
当前是怎么设计的 ? 可能会发生哪些问题 ? 这些问题会导致什么后果 ? 当前采用什么办法控制 ?
效果如何 ? 还需要做什么 ?
过去发生过 什么问题? 还会发生什 么问题? 经验积累
设计实准际则上 这设就计是经F验MEA !
冗余设计 工程计算 试验确认
进一步分 析试验确 认设计修 改
E D
B A
G
C
H
F
实施实例——活塞DFMEA
• 活塞组的边界图
3)接 口 矩 阵
• 接口矩阵是用适当的方法表示系统接口相关 性的工具。用以显示接口所表示的组件、零 部件之间的关系是正相关的还是负相关的。
实施实例——活塞DFMEA
• 活塞组的接口矩阵
4)P 图
• P图是用于确定和描述噪声控制因素和错误状 态的健壮性工具。
干扰因子
输入信号
系统描述 控制因子
理想功能 错误状态
实施实例——活塞组DFMEA
2.FMEA 实施流程
确定分析对象
鉴别故障模式
故障影响
鉴别故障原因
严重度
频度
风险顺序数 接下页
预先控制措施 探测度
2.FMEA 实施流程
接上页
是否要 纠正?
是
确定纠正措施
确定责任人和完 成日期
纠正措施效果判 定
是否满
S/D FMEA
设计潜在失效模式及影响 的分析理解与应用
主要内容
一.FMEA背景知识 二.为什么要实施FMEA? 三.如何实施FMEA?
DFMEA失效模式分析报告-范例

电感(L21
L3 L151)
影响产品性能
4
1
2
零件认可
产品试作
产品验证
2
16
无
电源按键
(S3)
影响产品性能
3
1
1
零件认可
产品试作
产品验证
2
6
无
光模块
(U17)
影响产品性能
3
3
2
零件认可
产品试作
产品验证
3
54
无
LED灯
(LED1-LDE
5)
影响产品性能
2
3
1
零件认可
产品试作
产品验证
3
18
无
PCBA
EPON各项
产品试作
产品验证
3
12
无
电源接口
(J5)
影响产品组装
2
1
1
零件认可
产品试作
产品验证
3
6
无
变压器
(T2)
影响产品性能
3
1
2
零件认可
产品试结构器件
满足外观
及结构要
求
下壳
影响外观及安装
2
1
安装及搬
运过程中
划伤
1
注意操作规
范
零件认可
产品试作
产品验证
3
6
无
上盖
影响外观及安装
2
1
1
零件认可
产品试作
产品验证
3
6
无
产品EP401M潜在失效模式及后果分析
(设计
子系统
功能要求
潜在失效 模式
- 1、下载文档前请自行甄别文档内容的完整性,平台不提供额外的编辑、内容补充、找答案等附加服务。
- 2、"仅部分预览"的文档,不可在线预览部分如存在完整性等问题,可反馈申请退款(可完整预览的文档不适用该条件!)。
- 3、如文档侵犯您的权益,请联系客服反馈,我们会尽快为您处理(人工客服工作时间:9:00-18:30)。
FMEA编号: 共 5页 , 第 1~5 页 编制人: FMEA日期(编制)2015.3.14 FMEA日期(修订) 2016.5.15 措施结果 责任及目标 建议措施 采取的措施 S O D 完成日期
RPN
胶带宽度不足 胶带宽度符合产品 要求,不可露铜线 。 绕线胶带
1、露铜线 2、造成耐压不良, 产品功能丧失 3、绕组之间安规距 离不足。
FMEA编号: 共 5页 , 第 1~5 页 编制人: FMEA日期(编制)2015.3.14 FMEA日期(修订) 2016.5.15 措施结果 责任及目标 建议措施 采取的措施 S O D 完成日期
RPN
含浸/烘烤
产品外观凡立水不 产品外观凡立水不能烘 烘干,不能粘手 干,粘手
1、磁芯、线圈松动 2、产品整机使用会 产生异音 3、绝缘度不足易产 生耐压不良或短路
1
20
含浸/烘烤
潜在失效模式及后果分析
(DFMEA)
项目名称:变压器类 核心小组: 过程 要求 功能 组长: 潜在 失效模式 潜在 失效后果 严 重 度 S 级 别 潜在失效 起因/机理 发 生 度 O 现行过程 控制预防 现行过程 控制探测 探 测 RPN 度 D 过程责任部门 :APQP小组 关键日期 : 2015.3.14
2
40
1、造成铜线上挡墙 2、安规距离不足 3、对功能无影响 5
1:选择挡墙厚度不合理 2:定义挡墙圈数不合理
2
50
理线
1、产品外观不符, 理线缠线不能超出 理线缠线超出线架凸点高 量产难度大,客户 线架凸点高度 度 装板浮高。
5
1:引出线股数太多; 2:引出线线径太大; 3:骨架凸点太低.
1:重新选择引出线股数; 5 2:重新选择引出线线径; 3:重新选择高凸点骨架.
绕线挡墙
挡墙高度与绕组铜 线同高 1、挡墙圈数少 2、挡墙厚度太薄
1、计算绕组铜线高度,选择 合适的挡墙的圈数,使挡墙高 制样组长及 度与铜线同高; 5 工程师首件 2、计算绕组铜线高度,选择 确认 合适的挡墙厚度,使挡墙高度 与铜线同高。 1、计算绕组铜线高度,选择 合适的挡墙的圈数,使挡墙高 制样组长及 度与铜线同高; 5 工程师首件 2、计算绕组铜线高度,选择 确认 合适的挡墙厚度,使挡墙高度 与铜线同高。
潜在失效模式及后果分析
(DFMEA)
项目名称:变压器类 核心小组: 过程 要求 功能 组长: 潜在 失效模式 潜在 失效后果 严 重 度 S 级 别 潜在失效 起因/机理 发 生 度 O 现行过程 控制预防 现行过程 控制探测 探 测 RPN 度 D 过程责任部门 :APQP小组 关键日期 : 2015.3.14
1:选择与骨架幅宽同宽胶带; 2:将张力评估过大. 4 5
1、设计选择胶带宽度比骨架 制样组长及 幅宽略宽0.5mm~1.0mm; 工程师首件 2、依据产品结构,考量作业 确认 过程张力对胶带宽度的影响。
2
40
1、挡墙圈数多 2、挡墙厚度太厚
1、线包大 2、造成下站作业困 难 3、对功能无影响。
1:选择挡墙厚度不合理 2:定义挡墙圈数不合理 4
FMEA编号: 共 5页 , 第 1~5 页 编制人: FMEA日期(编制)2015.3.14 FMEA日期(修订) 2016.5.15 措施结果 责任及目标 建议措施 采取的措施 S O D 完成日期
RPN
尺寸符合SPEC
尺寸达不到SPEC要求
1、产品外观不符安 规要求,产品外观 不良客户抱怨 2、对功能无影响。
温度低,时间短
6
1、设计烘烤温度及时间不合 理
2
48
1、磁芯、线圈松动 2、产品整机使用会 凡立水渗透线圈最 凡立水没有渗透线圈最里 产生异音 里层 层 3、绝缘度不足易产 生耐压不良或短路
5
1:原料凡立水不良 2:凡立水比重,烘烤温度,时间, 真空时间操作不符SOP要求
1:请原料厂家回复改善报告 2、制样时由制样组长及 制样组长及 对应工程师确认OK后方可作 4 工程师首件 业; 确认 3、制作首件由制样组长及 对应工程师确认.
2
60
焊锡 焊锡后PIN要光亮 焊锡后PIN不光亮 1、产品外观不符 SOP要求,客户装 机与PCB焊接虚焊 2、音箱不响 6 1:锡使用时间太久无定期进行 更换 2:原材料厂家锡铅比例超标
1
30
潜在失效模式及后果分析
(DFMEA)
项目名称:变压器类 核心小组: 过程 要求 功能 组长: 潜在 失效模式 潜在 失效后果 严 重 度 S 级 别 潜在失效 起因/机理 发 生 度 O 现行过程 控制预防 现行过程 控制探测 探 测 RPN 度 D 过程责任部门 :APQP小组 关键日期 : 2015.3.14
2
48
包装
包装材料正确
1、产品在客户端无 1、包装材料导致产品运 法正常使用 输破损 2、产品在客户端无 2、包装材料导致产品运 法正常插件 输过程造成PIN脚歪斜
6
1.包装材料选择不正确 2、包装方式不正确
3
1、制样时由制样组长及 制样组长及 对应工程师确认OK后方可作 工程师首件 业; 确认 2、制作首件由制样组长及 对应工程师确认.
4
1:原料凡立水不良 2:凡立水比重,烘烤温度,时间, 真空时间操作不符SOP要求
1:请原料厂家回复改善报告 2、制样时由制样组长及 制样组长及 对应工程师确认OK后方可作 4 工程师首件 业; 确认 3、制作首件由制样组长及 对应工程师确认. 1、制样时由制样组长及 对应工程师确认OK后方可作 制样组长及 4 业; 工程师首件 确认 2、制作首件由制样组长及 对应工程师确认. 1、制样时由制样组长及 对应工程师确认OK后方可作 制样组长及 4 业; 工程师首件 2、制作首件由制样组长及 确认 对应工程师确认.
1:选择与骨架幅宽同宽胶带; 2:未考量到作业过程胶带在张 力作用下轻微收缩; 6
1、设计选择胶带宽度比骨架 幅宽略宽0.5mm~1.0mm; 制样组长及 4 2、依据产品结构,考量作业 工程师首件 过程张力对胶带宽度的影响。 确认
2
48
胶带宽度偏宽 胶带宽度符合产品 要求,不可皱褶。
1、沿骨架壁皱褶 2、造成线包大 3、造成下站作业困 难 4、对功能无影响。
5
1:背胶治具无法管控尺寸
1、制样时由制样组长及 对应工程师确认OK后方可作 制样组长及 5 业; 工程师首件 2、制作首件由制样组长及 确认 对应工程师确认. 1、向客人建议更合理之方式 2、制样时由制样组长及 制样组长及 对应工程师确认OK后方可作 5 工程师首件 业; 确认 3、制作首件由制样组长及 对应工程师确认.
2
36
胶带宽度超过磁芯厚度
5
1:胶带宽度选择不合理
2
50
温度太高,时间太长
1、产品丧失功能
6
1、设计烘烤温度及时间不合 理
1、参考类似机种设计温度及 制样组长及 4 时间; 工程师首件 2、首样拆解确认 确认
2
48
烘烤
胶烤干 1、胶未烤干 2、磁芯松动 3、在客户端使用产 生异音 4、噪音太大。 1、参考类似机种设计温度及 制样组长及 4 时间; 工程师首件 2、首样拆解确认 确认
2
采用治具 50 辅助
生技人员
制作治具 辅助,固 定胶带长 度
5
1
2
10
包CORE反折胶带 包胶带方式符合 SPEC 1、产品外观不符安 规要求,产品外观 不良客户抱怨 2、对功能无影响。 1、依据SPEC方式不适合量产 作业 2、选择节省工时之方式
按照SPEC方式无法作业
5
2
50
胶带宽度不足磁芯厚度
2
32
焊锡正确
焊锡虚焊,假焊,包焊
1、产品功能可能丧 失,客户抱怨
6
1:焊锡温度 2:助焊剂比重和时间不符SOP 3:铜线异常不吃锡
2
48
二次焊锡 焊锡后PIN要光亮 焊锡后PIN不光亮 1、产品外观不符 SOP要求,客户装 机与PCB焊接虚焊 2、对功能无影响。 6 1:锡使用时间太久无定期进行 更换 2:原材料厂家锡铅比例超标
1、磁芯外露 2、与周边零件安规 距离不足
6
1:胶带宽度选择不合理 2:未考量产品与周边零件之 安规距离
1、选择与磁芯厚度同宽胶带 制样组长及 5 2、向客户了解与周边零件之 工程师首件 安规距离 确认
2
60
包CORE固定胶带
胶带与磁芯厚度相 等 1、胶带外沿皱褶 2、外观不良 3、浪费材料成本 4、对功能无影响。 制样组长及 5 1、选择与磁芯厚度同宽胶带 工程师首件 确认
制样组长及 工程师首件 确认
2
50
焊锡正确
焊锡虚焊,假焊,包焊
1、产品功能可能丧 失,客户抱怨来自61:焊锡温度 2:助焊剂比重和时间不符SOP 3:铜线异常不吃锡
1、制样时由制样组长及 对应工程师确认OK后方可作 制样组长及 5 业; 工程师首件 确认 2、制作首件由制样组长及 对应工程师确认. 1、制样时由制样组长及 对应工程师确认OK后方可作 制样组长及 5 业; 工程师首件 2、制作首件由制样组长及 确认 对应工程师确认.