孔铜制程技术
PCB工艺电镀一次铜工艺介绍

PANEL PLATING PROCESS
1000
WHAT IS PULSE PLATING? Amps 0
-1000
电流以脉冲的方式输出,达到瞬间
-2000
反电解的效果,使电路板上高电流
-3000
Amps
区造成之差异减至最低。
0.5 sec 10 sec
36
PANEL PLATING PROCESS DC 与 PULSE电镀间的差异
Manganate:
Mn6+ + 4 e- Mn2+
Manganese dioxide:
Mn4+ + 2 e- Mn2+
還原劑可以為 Glyoxal, H2O2 or Hydroxylamine sulfate.
insoluble MnO2
Cu
Mn2+ (soluble)
Cu
9
DESMEAR PROCESS Neutralizer / 中和槽 :
DEBURR设备配置图:
风刀 超音波 风刀 刷磨段
水洗 高压水洗 水洗 超音波 中压 水洗
5
除胶渣(DESMEAR)
WHAT IS SMEAR?
钻孔时树脂产生高温超过Tg
值,而形成融熔状,冷却后
凝固形成胶渣。
Cu
功能 :
去除鑽孔後殘留孔內之基材膠渣 形成孔壁微粗糙度
DESMEAR基本流程:
Sweller
H O
+HNH +HNH +HNH +HNH
Positive charged conditioning polymer
10
DESMEAR PROCESS DESMEAR 后以电子显微镜观察之孔壁粗化清洁情形
PCB制程工艺简要介绍
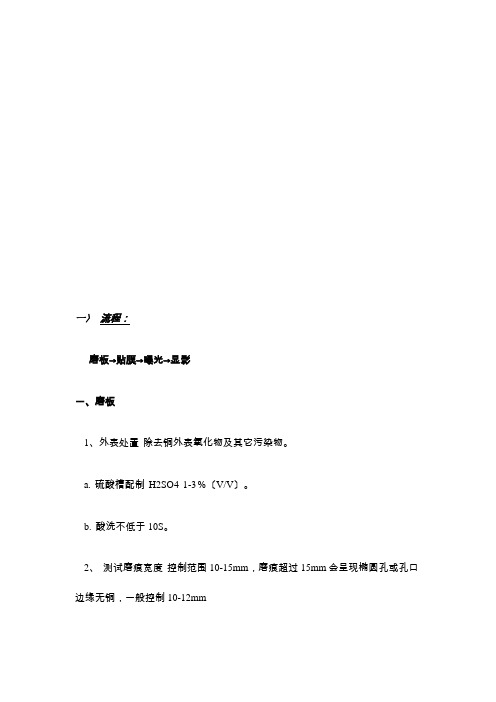
一〉流程:磨板→贴膜→曝光→显影一、磨板1、外表处置除去铜外表氧化物及其它污染物。
a. 硫酸槽配制H2SO4 1-3%〔V/V〕。
b. 酸洗不低于10S。
2、测试磨痕宽度控制范围10-15mm,磨痕超过15mm会呈现椭圆孔或孔口边缘无铜,一般控制10-12mm为宜。
3、水磨试验每日测试水膜破裂时间≥15s,试验说明,在不异条件下磨痕宽度与水膜破裂时间成正比。
4、磨板控制传送速度,间隔1",水压,枯燥温度70-90℃。
二、干膜房1、干膜房洁净度10000级以上。
2、温度控制20-24°C,超出此温度范围容易引起菲林变形。
3、湿度控制60-70%,超出此温度范围也容易引起菲林变形。
4、工作者每次进入干膜房必需穿戴防尘服及防尘靴风淋15-20s。
三、贴膜1、贴膜参数控制a. 温度100-120°C,精细线路控制115-120°C,一般线路控制105-110°C,粗线路控制100-105°C。
b. 速度<3M/min。
c. 压力30-60Psi,一般控制40Psi摆布。
2、本卷须知a. 贴膜时注意板面温度应保持38-40°C,冷板贴膜会影响干膜与板面的粘接性。
b. 贴装前须查抄板面是否有杂物、板边是否光滑等,假设板边毛刺过大会划伤贴膜胶辊,影响使用寿命。
c. 在气压不变情况下,温度较高时可适当加快传送速度,较低时可适当减慢传送速度,否那么会呈现皱膜或贴膜不牢,图形电镀时易发生渗镀。
d. 切削干膜〔手动贴膜机〕时用力均匀,保持切边整齐,否那么显影后呈现菲林碎等缺陷。
e. 贴膜后须冷却至室温前方可进行曝光。
四、曝光1、光能量a.光能量〔曝光灯管5000W〕上、下灯控制40-100毫焦/平方厘米,用下晒架测试上灯,上晒架测试下灯。
b.曝光级数7-9级覆铜〔Stoffer 21级曝光尺〕,一般控制8级摆布,但此级数须显影后才能反映出来,因此对显影控制要求较严。
通孔镀铜技术详解

通孔镀铜技术详解通孔镀铜技术详解在印制电路板制造技术中,虽关键的就是化深沉铜工序。
它主要的作用就是使双面和多层印制电路板的非金属孔,通过氧化还原反应在孔壁上沉积一层均匀的导电层,再经过电镀加厚镀铜,达到回路的目的.要达到此目的就必须选择性能稳定、可靠的化学沉铜液和制定正确的、可行的和有效的工艺程序。
一.工艺程序要点:1.沉铜前的处理;2.活化处理;3.化学沉铜。
二.沉铜前的处理:1.去毛刺:沉铜前基板经过钻孔工序,此工序虽容易产生毛刺,它是造成劣质孔金属化的最重要的隐患。
必须采用去毛刺工艺方法加以解决。
通常采用机械方式,使孔边和内孔壁无倒刺或堵孔的现象产生.2.除油污:⊙油污的来源:钻头由于手接触造成油污、取基板时的手印及其它。
⊙油污的种类:动植物油脂、矿物等。
前者属于皂化油类;后者属于非皂化油类。
⊙油脂的特性:动植物油类属于皂化油类主要成分高级脂肪酸,它与碱起作用反应生成能溶于水的脂肪酸盐和甘油;矿物油脂化学结构主要是石腊烃类,烯属烃及环烷属烃类和氯化物的混合物,不溶于水也不与碱起反应。
⊙除油处理方法的选择依据:根据油的性质、根据油沾污的程度。
⊙方法:采用有机溶剂和化学及电化学碱性除油。
⊙作用与原理:□可皂化性油类与碱液发生化学反应生成易溶于水的脂肪酸盐和甘油。
反应式如下:(C17H35COO)3十3NAOH3C17H35COON a+C2H5(OH)2□非皂化油类:主要靠表面活性剂如OP乳化剂、十二烷基磺酸钠、硅酸钠等。
这些物质结构中有两种基团,一种是憎水性的;一种是亲水性.首先乳化剂吸附在油与水的分界面上,以憎水基团与基体表面上的油污产生亲和作用,而亲水基团指向去油液,水是非常强的极性分子,致使油污与基体表面引力减少,借者去油液的对流、搅拌,油污离开基体表面,实现了去油的最终目的。
3.粗化处理:⊙粗化的目的:主要保证金属镀层与基体之间良好的结合强度。
⊙粗化的原理:使基体的表面产生微凹型坑,以增大其表面接触面积,与沉铜层形成机械钮扣结合,获得较高的结合强度。
填孔镀铜配方组成,工艺流程及技术研究进展

填孔镀铜配方组成,工艺流程及技术研究进展摘要:文章简述了填孔电镀的概况、工艺以及填孔工艺中的镀铜添加剂关键词:电镀;填孔;镀铜添加剂;1前言从20世纪60年代开始,PCB行业就采用孔金属化和电镀技术来解决层间连接或导通的问题。
实际上过去、现在和将来,在PCB进行电镀铜的最核心问题是解决孔内镀铜连通、镀铜厚度均匀性和填孔镀铜方面等问题。
随着PCB行业产品的高密度化和结构多样化的发展,PCB电镀技术有了飞快的进步,但是电镀铜的核心问题仍然没有得到有效的解决。
到目前为止,PCB行业电镀经历了常规直流电镀—直接电镀—脉冲电镀—新型直流电镀等过程,核心仍然是围绕着PCB层间“孔”导通的问题。
在孔金属化过程中,采用填铜工艺可以提高电路板层间的导通性能,改善产品的导热性,减少孔内孔洞,降低传输信号的损失,这将有效的提高电子产品的可靠性和稳定性。
在填孔镀铜工艺中添加剂组分之间的相互作用直接影响着填铜工艺的顺利进行,因此,了解镀铜添加剂的作用原理对填孔电镀工艺非常重要。
禾川化学是一家专业从事精细化学品以及高分子分析、研发的公司,具有丰富的分析研发经验,经过多年的技术积累,可以运用尖端的科学仪器、完善的标准图谱库、强大原材料库,彻底解决众多化工企业生产研发过程中遇到的难题,利用其八大服务优势,最终实现企业产品性能改进及新产品研发。
样品分析检测流程:样品确认—物理表征前处理—大型仪器分析—工程师解谱—分析结果验证—后续技术服务。
有任何配方技术难题,可即刻联系禾川化学技术团队,我们将为企业提供一站式配方技术解决方案!2填孔电镀的工艺流程2.1填孔镀铜的机理填孔电镀添加剂由三类组份组成:光亮剂(又称加速剂),其作用减小极化,促进铜的沉积、细化晶粒;载运剂(又称抑制剂),增加阴极极化,降低表面张力,协助光亮剂作用;整平剂,抑制高电流密度区域铜的沉积。
微盲孔孔底和孔内沉积速率的差异主要来源于添加剂在孔内不同位置吸附分布,其分布形成过程如下:1、由于整平剂带正电,最易吸附在孔口电位最负的位置,并且其扩散速率较慢因此在孔底位置整平剂浓度较低;2、加速剂最易在低电流密度区域富集,并且其扩散速率快,因此,孔底加速剂浓度较高;3、在孔口电位最负,同时对流最强烈,整平剂将逐渐替代抑制剂加强对孔口的抑制,最终使得微孔底部的铜沉积速率大于表面沉积速率,从而达到填孔的效果。
pcb孔铜厚度标准及成品铜厚构成、由来
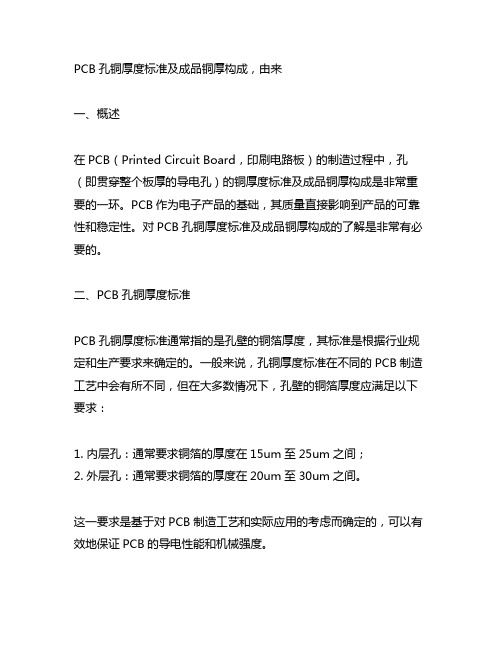
PCB孔铜厚度标准及成品铜厚构成,由来一、概述在PCB(Printed Circuit Board,印刷电路板)的制造过程中,孔(即贯穿整个板厚的导电孔)的铜厚度标准及成品铜厚构成是非常重要的一环。
PCB作为电子产品的基础,其质量直接影响到产品的可靠性和稳定性。
对PCB孔铜厚度标准及成品铜厚构成的了解是非常有必要的。
二、PCB孔铜厚度标准PCB孔铜厚度标准通常指的是孔壁的铜箔厚度,其标准是根据行业规定和生产要求来确定的。
一般来说,孔铜厚度标准在不同的PCB制造工艺中会有所不同,但在大多数情况下,孔壁的铜箔厚度应满足以下要求:1. 内层孔:通常要求铜箔的厚度在15um至25um之间;2. 外层孔:通常要求铜箔的厚度在20um至30um之间。
这一要求是基于对PCB制造工艺和实际应用的考虑而确定的,可以有效地保证PCB的导电性能和机械强度。
三、成品铜厚构成PCB的成品铜厚构成通常包括了板表铜厚度、板内铜厚度和孔壁铜厚度。
这三者的构成对于PCB的性能有着重要的影响。
1. 板表铜厚度:指的是覆盖在PCB表面的铜箔厚度。
一般情况下,板表铜厚度在1oz(35um)至3oz(105um)之间,不同电子产品对板表铜厚度的要求有所不同。
2. 板内铜厚度:指的是PCB板的内层铜箔厚度,在压合制版结束后板材的铜箔厚度即为板内铜厚度。
一般情况下,板内铜厚度在1oz至6oz之间,也根据实际工程应用而定。
3. 孔壁铜厚度:指的是孔的壁内铜箔厚度,是PCB制造中的一个重要指标。
如前所述,按照PCB孔铜厚度标准,通常要求孔壁的铜箔厚度在15um至30um之间。
以上三者构成的合理性对于PCB的导电性能、散热性能和机械强度都有着重要的影响,一个合格的PCB必须保证这三者的合理构成。
四、PCB孔铜厚度标准及成品铜厚构成的由来PCB孔铜厚度标准及成品铜厚构成的建立是行业多年经验的总结,并在实际应用中不断验证和完善而来的。
其中,考虑了包括电路板的导电性能、散热性能、机械稳定性等多方面的因素。
电镀(PTH)制程讲解

四、设备的功能作用及要求
1‧阳极移动 阳极移动副度20~25毫米,速度5~45次/分。阴极移动应 与阳极的表面垂直,可提高镀层的均匀性 2‧压缩空气 将液面鼓起3~4cm小于或等于0.08m2/min,空气搅拌不仅 带给镀液的强烈翻动且提供氧气促进溶液中的Cu2+氧化 成Cu+的干扰,避免铜渣的产生、稳定药水的循环及成份 的补给。 3‧过滤:将槽液1~2h/次翻动,净化槽液,使槽液中的有 机杂质及时除去以免污染槽液,影响品质,同时槽液大 量的翻动可调整药水的浓度维持平衡。
F‧速化:作用是剥出铜面及皮膜上的钯胶体一种剥壳剥皮的 作用,使其露出中心钯核来使与下站化铜能进行更好的沉积 反应。 G‧化铜:主要是使孔内金属化,沉上一层薄薄的铜层. 沉铜厚度:15-30U”。
2‧电镀是酸洗、镀铜槽组成
‧酸洗:它的作用是剥除板面氧化层,粗化板面,使镀层牢固 均匀。提供酸性环境进入铜槽,来维持铜槽的稳定性。 ‧ 镀铜:它的作用是:使镀层具有半光泽性、延展性、抗拉 性,增加镀铜厚度最终使线路的导通能力更好。
PI缸 整孔
120L 120L
YC-210 YC-201 SPS
300-500 Ml/l 0.13±0.04N 80±20g/l 1.5-2.5% ≤20 g/l 1.116-1.154 0.6-1.0N 1.116-1.154 0.6-1.0N 80-110% 8-12% 1.5-2.5 g/l 8-12% 4-6% 2-4% 60-90g/l 54-135ml/l 40-60ppm
பைடு நூலகம்1.铜面粗糙
2.铜面发暗
3.板面氧化
1.及时修复设备故障。 2.严格控制板子hold time。
4.铜颗粒
1.钛篮阳极膜生长不良。 2.电镀时超时,长时间低电流电镀。 3.镀铜光泽剂浓度异常。 4.镀铜液异物过多。 5.阳极袋或阳极隔膜破损。
孔隙为100nm多孔铜制备方法

孔隙为100nm多孔铜制备方法
孔隙为100nm多孔铜的制备方法主要包括物理方法和化学方法。
物理方法包括:
1. 电子束熔炼和定向凝固:通过电子束熔炼制备出熔体,然后采用定向凝固技术,在一定的冷却速率下使熔体定向凝固,获得具有特定孔隙结构的铜材料。
2. 3D打印:利用3D打印技术,通过特定的打印路径和工艺参数,将铜粉末逐层堆积并熔化,形成具有特定孔隙结构的铜材料。
化学方法包括:
1. 化学刻蚀:利用化学刻蚀剂对铜表面进行刻蚀,形成具有特定孔隙结构的铜材料。
2. 溶胶凝胶法:利用溶胶凝胶法制备出具有特定孔隙结构的铜凝胶,然后在一定条件下对凝胶进行热处理或还原处理,得到具有特定孔隙结构的铜材料。
具体制备方法应根据所需孔隙结构和性能要求选择,并综合考虑实验条件、成本和可重复性等因素。
黑孔制程简介

黑孔制程简介一.流程介绍1-1各槽功能1-2原理二.各槽药水名称及各槽操作条件简介及控制及如何配槽2-1药水名称和操作条件2-2药水分析方法三.各槽操作及前后搭配注意事项3-1清洁&整孔槽3-2黑孔槽3-3整孔槽3-4微蚀槽3-5搞氧化槽3-6水洗及烘干3-7黑孔前后搭配注意事项四.问题与解决五.附件5-1微蚀深度测试方法5-2Hrll chain实验方法5-3黑孔线维护保养项目5-4重工流程5-5BlackHole Process药液储存一.流程介绍入料→磨刷→水洗→清洁→水洗→黑孔→吸干→烘干(吹干.烘干)→水洗→整孔→水洗→黑孔→吸干→烘干(吹干.烘干)→微蚀→水洗→抗氧化→水洗→吸干→烘干(吹干.烘干)→出料各槽功能磨刷将板面上之污染物,氧化及钻孔造成之毛头以磨刷之方式去除2.1Clean/Conditioning(清洁/整孔)2.1.1此槽液为微碱性溶液。
主要功能为调整树脂与玻织上的电性(将原有的负电调节为带正电),以利黑孔带负电的碳胶体附着。
2.1.2清洁/整孔剂为界面活性剂的一种,藉由界面活性剂的疏水基深入孔壁,将污物带出,以达清洁之功效;其亲水基则是将树脂与玻织调整为带正电荷。
2.1.3此药剂使用一段时间后,槽液会渐转为蓝色,这是因此种界面活性剂会轻微咬铜所致。
2.1.4此槽液的药剂选择相当重要,因为它将决定碳胶体的附著效力。
2.1.5因为此槽液为界面活性剂,故需注意水刀、水床、阻水滚轮,与水盘的密合度,以降低因机械搅拌所产生的泡沫。
因为泡沫的生成,将会减损整孔功效与槽液的寿命。
2.1.6因为玻织束不易改变电性,故于清洁/整孔程序后,会再经一道整孔处理,以确保孔壁的电性皆为正电荷。
2.2Black Hole(黑孔)2.2.1黑孔槽液是由含碳的悬浮所组成,而碳胶体的大小约为2~5μinch,与其它悬浮液一样,黑孔的碳胶体也会凝聚(aggregation)与羽化(flocculation),故不易沉淀。
PCB填孔电镀制程简介

对于电路板的结构 设计来说,在通盲孔 上直接迭孔的构造 (Via on Via)是获得 最高结构密度可能 性的孔地的平坦性做好,因此填孔就成为必要的技术了
7
总结 填孔的作用:
1.增加PCB的密集度,在最小的面积与体积中,容 纳最大的布线密度与承接最多的主动与被动组件. 2.使镀铜层表面更平滑,避免凹陷产生. 3.避免介电物质及导电物质的不完全填孔. 4.提升微细线路,各项电性及信赖性规范.
A类型
B类型
A类型产生原因
B类型产生原因
24
八.产能统计
電鍍厚度 尺寸(in) 電流密 (mil) 寬 長 度 1.1 21 24 12
電鍍 電鍍時間 線速 保養時 效率 (min) (m/min) 間 90% 109 0.124 1.5
更換料號
時間(min) 次數
40
4
H/DAY 天數 19.8 30
压合 防焊 FQC
雷射 外层 OQC
钻孔 电镀 成仓
5
填孔电镀在电镀制程中的位置
去毛头(DB) 除胶渣(DSM)
水平除胶渣化铜联机 (水平DSM+PTH)
垂直连续电镀线 (VCP)
VCP打底 填孔电镀线
龙门线(PTH+ICu)
后处理
出货
6
三.填孔作用与原理
为什么要用填孔电镀?
在制作传统的印制电路板方面,通孔电镀 一直是业界众所皆知的重要制程,然而随 着时代的进步,电子产品急速往轻薄短小 的趋势发展,印制电路的高密度化要求越 来越高,这时传统制程就无法满足要求了.
2.设备区别
不同点 前处理 阳极
VCP 化铜 无特殊要求
VCP 无微蚀槽 可溶性阳极
填孔线 VCP线打底 与VCP打底时上下方向相反
PCB成品铜厚和孔铜的由来
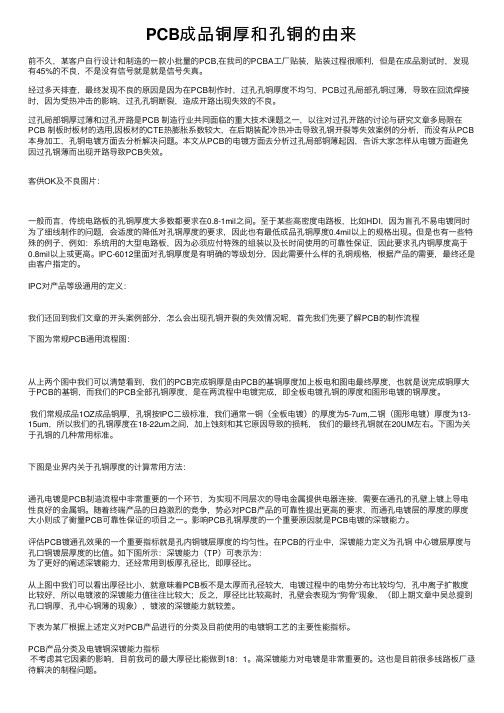
PCB成品铜厚和孔铜的由来前不久,某客户⾃⾏设计和制造的⼀款⼩批量的PCB,在我司的PCBA⼯⼚贴装,贴装过程很顺利,但是在成品测试时,发现有45%的不良,不是没有信号就是就是信号失真。
经过多天排查,最终发现不良的原因是因为在PCB制作时,过孔孔铜厚度不均匀,PCB过孔局部孔铜过薄,导致在回流焊接时,因为受热冲击的影响,过孔孔铜断裂,造成开路出现失效的不良。
过孔局部铜厚过薄和过孔开路是PCB 制造⾏业共同⾯临的重⼤技术课题之⼀,以往对过孔开路的讨论与研究⽂章多局限在PCB 制板时板材的选⽤,因板材的CTE热膨胀系数较⼤,在后期装配冷热冲击导致孔铜开裂等失效案例的分析,⽽没有从PCB 本⾝加⼯,孔铜电镀⽅⾯去分析解决问题。
本⽂从PCB的电镀⽅⾯去分析过孔局部铜薄起因,告诉⼤家怎样从电镀⽅⾯避免因过孔铜薄⽽出现开路导致PCB失效。
客供OK及不良图⽚:⼀般⽽⾔,传统电路板的孔铜厚度⼤多数都要求在0.8-1mil之间。
⾄于某些⾼密度电路板,⽐如HDI,因为盲孔不易电镀同时为了细线制作的问题,会适度的降低对孔铜厚度的要求,因此也有最低成品孔铜厚度0.4mil以上的规格出现。
但是也有⼀些特殊的例⼦,例如:系统⽤的⼤型电路板,因为必须应付特殊的组装以及长时间使⽤的可靠性保证,因此要求孔内铜厚度⾼于0.8mil以上或更⾼。
IPC-6012⾥⾯对孔铜厚度是有明确的等级划分,因此需要什么样的孔铜规格,根据产品的需要,最终还是由客户指定的。
IPC对产品等级通⽤的定义:我们还回到我们⽂章的开头案例部分,怎么会出现孔铜开裂的失效情况呢,⾸先我们先要了解PCB的制作流程下图为常规PCB通⽤流程图:从上两个图中我们可以清楚看到,我们的PCB完成铜厚是由PCB的基铜厚度加上板电和图电最终厚度,也就是说完成铜厚⼤于PCB的基铜,⽽我们的PCB全部孔铜厚度,是在两流程中电镀完成,即全板电镀孔铜的厚度和图形电镀的铜厚度。
我们常规成品1OZ成品铜厚,孔铜按IPC⼆级标准,我们通常⼀铜(全板电镀)的厚度为5-7um,⼆铜(图形电镀)厚度为13-15um,所以我们的孔铜厚度在18-22um之间,加上蚀刻和其它原因导致的损耗,我们的最终孔铜就在20UM左右。
- 1、下载文档前请自行甄别文档内容的完整性,平台不提供额外的编辑、内容补充、找答案等附加服务。
- 2、"仅部分预览"的文档,不可在线预览部分如存在完整性等问题,可反馈申请退款(可完整预览的文档不适用该条件!)。
- 3、如文档侵犯您的权益,请联系客服反馈,我们会尽快为您处理(人工客服工作时间:9:00-18:30)。
900u”
3.2 成果彙總---壓膜、曝光
<1>.第一次曝光 此次與一般流程相同做出線路,故用一般條件作業 <2>.第二次曝光 A. 二次曝光底片所露pad孔大小設計 為得到良好的孔銅一般在二次曝光底片的設計上其露 出的pad需較通孔(0.2mm)大0.1mm, 此種設計的理由:經一次鍍銅後,基材一般會縮3/10000(我 們實際作業中測得數據也驗證了這一點),此次實際設計 pad大小為0.65mm>0.2mm, 故在第二次曝光時雖有偏位, 但導通孔仍在pad內沒 有被蓋住的情形,當然底片 0.65 偏位還可以通過在繪底片時 0.2 先預縮3/10000解決
段差
五、心得
1.大膽假設,小心求證 -----孔破 -----孔邊緣效應 2.抽絲剝繭,找尋根因改善 3.運用資源,達成目標
THE END
415瓶底電鍍法(Bottle Plating) ------之成果報告
部門
: 工程
報告人:汪明
報告大綱
一.瓶底電鍍法之運用 二.瓶底電鍍法之原理 三.415料號瓶底電鍍之成果彙總
四.後續驗證事項
五.心得
一、瓶底電鍍法之運用
1.所謂瓶底電鍍即一種只鍍孔銅而不鍍面銅的新流程電鍍 法(Bottle plating)。 2.隨著客戶對於電鍍導通孔可靠度 的要求,孔銅的厚度即是關鍵(要 求達1000u”),用傳統整板鍍銅而加 厚孔銅的方法在FPC的運用上會 導通孔 PAD 導致如下的一些問題點: A:面銅太厚導致線路過粗,軟板的繞折性大受影響 ; B:因鍍層較厚,鍍層厚薄不均加劇、且銅面凹击易造成的 不良諸多; C:厚銅咬蝕:側蝕過大,在D/S細線上良率變的很差,當然 原物彙總---鍍銅
原因分析: 雖已採行小電流、長時間電鍍做但孔邊緣效應仍比較 明顯,所以面銅雖OK,但孔銅厚度與理論卻相去甚遠! 改善措施: 電流密度不變,將電鍍時間縮減近一半為35min,此時我 們恰好可以選擇程式三。 改善效果: 孔銅厚度符合要求為700~1000u”之間,孔銅外觀較漂亮
三、415瓶底電鍍成果彙總
415料號: 客戶:視達 應用:15“LCD MONITOR 孔銅厚度:1000u” 線路厚度:一般廠內規格 因此在這里必需用到瓶底電鍍法,本次測試選擇流程一:
µ Ø ¶ ¥ 1 2 3 4 5 6 7 8 9 10 11 12 13 14 15 16 17 18 19 20 21 22 23 24 u ¸ ¤ ¯ ¦W º Ù UÆ ¤ ® NC ÂÕ ¶ ¤ á É Á» ®¤ ° ½ n ú Ã¥ ã v ż u Ë ½À k è » ¨ h ¤ ¥ ½ L k · » ®¤ ° ½ n ú Ã¥ ã v ż á É Á» h ¤ ¥ ½ u Ë ½À L k · » K Coverlay ¶ K[ j ù ¶ ¥ ± ¤ A £ À ¦X R Õ ¨ ¤ L k · » Qü ¼¿ pcs/cycle 25 25 25 25 25 25 25 25 25 25 25 25 25 25 25 25 25 25 25 25 25 25 25 25 ÷ Æ Wæ n D u ã s ¹ § ® /³ ® ¨ &¤ ¨ ½ ¸ B40415X1.400 100+30 u"(Á » ) ¡ É
祼露出 的多餘 銅面以 分散孔 邊緣之 電鍍效 應
只鍍孔銅
3.1 成果彙總---鍍銅
B.電流密度 因所鍍銅較厚為減少孔邊緣效應,並得到漂亮孔銅,選 擇長時間、小電流(12ASF)的電鍍方法。 C.電鍍時間 以電流密度計算公式得到理論所需的電鍍時間為67.5 min,故選擇了手動方式去作二次鍍銅 結果:量測面銅厚為700~1000u”,但孔銅厚度卻達到了2200u”,
u S ¥ Å PAD (± ¥ » ¤ µ ½ » ) ø ó P u { T {
TOP&BOT â ü I ± ¤ « KA51 Ö t MN § ³ +¯ ¯
70-700"u
3.1 成果彙總---鍍銅
<1>.為甚麼要分二次鍍銅? 以下流程可否? 下料鑽孔黑孔壓膜曝光(線路&PAD)D.E.S 壓膜曝光(只露PAD)顯影 電鍍銅去膜以下制 程與FPC同 A.問題點: 鍍錫鉛後發現每PCS上皆有 孔破,其不良率達100% B.原因分析: 黑孔後直接壓膜走DES時,顯 影之強鹼會攻擊孔壁之碳黑, 導致碳黑剝落引起孔破 孔破導致手指pad未鍍上 C.改善做法 二次鍍銅:先鍍薄銅(100u”)將孔壁連接以作導通.
C01-TTRA-00415 Rev:X1 C01-BTRA-00415 Rev:X1 10ª ¬ GF-1040 9.75" ø K 4+-0.5mil
C01-TMAS-00415 Rev:X1 C01-BMAS-00415 Rev:X1
600-900u" (° ¥ ¶ ´ ¤ « « ) È ² q ú Õ p ×
導通孔 PAD
3.2 成果彙總---壓膜、曝光
B. 二次曝光底片板邊設計 因在曝光、顯影完成後即進行二次鍍銅,此時需要在曝光 時將鍍銅所需夾板的兩邊緣留出
鍍須銅須夾板, 故板邊緣不應 有乾膜附蓋
此處需預留出來 (板兩邊各留10mm 遮光區域
3.3 成果彙總---DES、AOI
<1>.第一次線路 此次與一般流程相同做出線路,故用一般條件作業 <2>.第二次顯影及去膜 測試時我們采行一般條件,因是先鍍銅再去膜,如量產 此去膜條件再study <3>.AOI 因在DES完成後還需再鍍孔銅,流程上我們就沒有再加線 檢,而是在第二次去膜完成後再一次做AOI,此次415共20 PNL,AOI良率在99.3%,所以在整體上是非常成功的。
二、瓶底電鍍法之原理
瓶底電鍍法是通過兩次曝光,在完成線路後用乾膜將線路保 護住,而只露出予鍍的通孔再進行電鍍的做法以達成要求,其 一般的流程如下: 1.流程一: 下料→NC→黑孔→鍍薄銅(100u”)→壓膜、曝光→D.E.S (線路)→ 壓膜、曝光→顯影→鍍孔銅(600~1000u”)→ 去膜 →以下同一般流程 該法缺點: 獨立點through hold 需拉導線. 2.流程二: 下料→NC→黑孔→鍍薄銅(100u”)→壓膜、曝光(只露 PAD)→顯影→鍍孔銅(600~1000u“)→去膜→壓膜、曝 光 → D.E.S (線路) →以下同 一般流程 該法缺點: PAD與線路有落差易造成斷路
四、後續待驗證事項
<1>.流程二 流程二為先鍍導通孔再做線路的製程, 因PAD孔設計比通孔大,在孔邊緣銅面 上會鍍上銅,去膜後孔邊情形如右圖,會 成約1mil高的段差,如干膜的填復性不佳 即會造成在蝕刻線路時藥水從此段差處 攻入,導致pad與線路斷開-----驗證干膜 之填復性是否能克服此段差 <2>.PAD孔大小設計 現PAD孔設計比通孔大會有段差情形產,反之 段差就不會產生,但此時through power變差,孔 內鍍層可能變差,如再有偏 位發生可導致孔變形,故此 PAD孔設計待再驗證
3.1 成果彙總---鍍銅
<2>.第一次鍍薄銅條件(100u”) 電流密度(ASF)=1080×鍍銅厚度(mil)/時間(min) 鍍銅程式二:15min,得電流密度為7.2ASF SHIPLEY光澤劑應用範圍為10~40ASF,故 選擇手動鍍銅,鍍銅條件為12ASF、11min <3>.第二次鍍銅條件(750+150u”) A.電鍍面積: 因第二次只鍍孔銅,鍍銅面積太小邊緣效應明顯,故我們 在曝光時留出祼露的銅面以分散電流,減少邊緣效應,總 鍍銅面積須從底片上計算出(工程提供)