工厂设备人员稼动率计算方式说明
设备稼动率如何计算
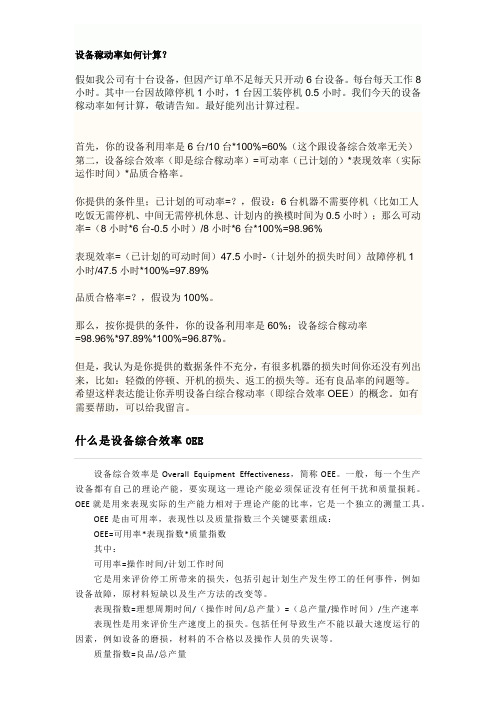
设备稼动率如何计算?假如我公司有十台设备,但因产订单不足每天只开动6台设备。
每台每天工作8小时。
其中一台因故障停机1小时,1台因工装停机0.5小时。
我们今天的设备稼动率如何计算,敬请告知。
最好能列出计算过程。
首先,你的设备利用率是6台/10台*100%=60%(这个跟设备综合效率无关)第二,设备综合效率(即是综合稼动率)=可动率(已计划的)*表现效率(实际运作时间)*品质合格率。
你提供的条件里;已计划的可动率=?,假设:6台机器不需要停机(比如工人吃饭无需停机、中间无需停机休息、计划内的换模时间为0.5小时);那么可动率=(8小时*6台-0.5小时)/8小时*6台*100%=98.96%表现效率=(已计划的可动时间)47.5小时-(计划外的损失时间)故障停机1小时/47.5小时*100%=97.89%品质合格率=?,假设为100%。
那么,按你提供的条件,你的设备利用率是60%;设备综合稼动率=98.96%*97.89%*100%=96.87%。
但是,我认为是你提供的数据条件不充分,有很多机器的损失时间你还没有列出来,比如:轻微的停顿、开机的损失、返工的损失等。
还有良品率的问题等。
希望这样表达能让你弄明设备白综合稼动率(即综合效率OEE)的概念。
如有需要帮助,可以给我留言。
设备综合效率是Overall Equipment Effectiveness,简称OEE。
一般,每一个生产设备都有自己的理论产能,要实现这一理论产能必须保证没有任何干扰和质量损耗。
OEE就是用来表现实际的生产能力相对于理论产能的比率,它是一个独立的测量工具。
OEE是由可用率,表现性以及质量指数三个关键要素组成:OEE=可用率*表现指数*质量指数其中:可用率=操作时间/计划工作时间它是用来评价停工所带来的损失,包括引起计划生产发生停工的任何事件,例如设备故障,原材料短缺以及生产方法的改变等。
表现指数=理想周期时间/(操作时间/总产量)=(总产量/操作时间)/生产速率表现性是用来评价生产速度上的损失。
稼动率的计算方式
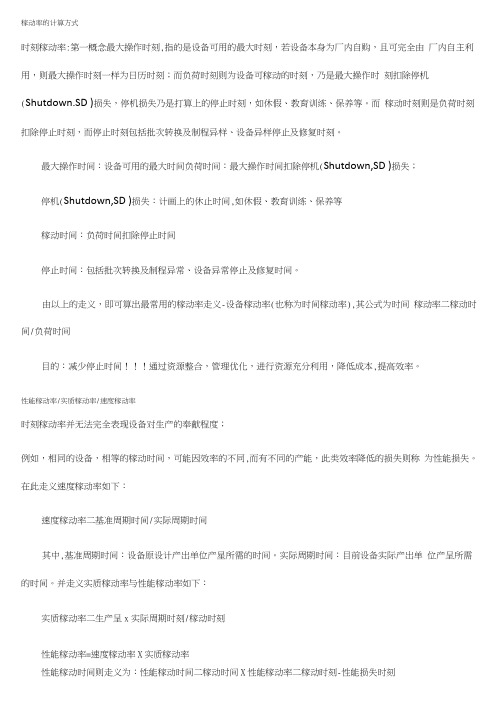
稼动率的计算方式时刻稼动率:第一概念最大操作时刻,指的是设备可用的最大时刻,若设备本身为厂内自购,且可完全由厂内自主利用,则最大操作时刻一样为日历时刻;而负荷时刻则为设备可稼动的时刻,乃是最大操作时刻扣除停机(Shutdown.SD )损失,停机损失乃是打算上的停止时刻,如休假、教育训练、保养等。
而稼动时刻则是负荷时刻扣除停止时刻,而停止时刻包括批次转换及制程异样、设备异样停止及修复时刻。
最大操作时间:设备可用的最大时间负荷时间:最大操作时间扣除停机(Shutdown,SD )损失;停机(Shutdown,SD )损失:计画上的休止时间,如休假、教育训练、保养等稼动时间:负荷时间扣除停止时间停止时间:包括批次转换及制程异常、设备异常停止及修复时间。
由以上的走义,即可算出最常用的稼动率走义-设备稼动率(也称为时间稼动率),其公式为时间稼动率二稼动时间/负荷时间目的:减少停止时间!!!通过资源整合,管理优化,进行资源充分利用,降低成本,提高效率。
性能稼动率/实质稼动率/速度稼动率时刻稼动率并无法完全表现设备对生产的奉献程度;例如,相同的设备,相等的稼动时间,可能因效率的不同,而有不同的产能,此类效率降低的损失则称为性能损失。
在此走义速度稼动率如下:速度稼动率二基准周期时间/实际周期时间其中,基准周期时间:设备原设计产出单位产星所需的时间。
实际周期时间:目前设备实际产出单位产呈所需的时间。
并走义实质稼动率与性能稼动率如下:实质稼动率二生产呈x实际周期时刻/稼动时刻性能稼动率=速度稼动率X实质稼动率性能稼动时间则走义为:性能稼动时间二稼动时间X性能稼动率二稼动时刻-性能损失时刻其中性能损失包括速度低落的损失与短暂停机的损失。
由以上走义可知,若性能稼动率变小,则可判走生产相关设备的效率降低。
价值稼动时间与设备综合效率(OverallEquipmentEffectiveness )性能稼动时间表示设备产出产品的时间,但无法表示设备产出良率的好坏,因此定义「价值稼动时间」来表示真正能产出良品的有价值时间,其走义如下:价值稼动时间二性能稼动时间X良品率而设备的有效使用程度则以「设备总合效率」来判走,其走义如下:设备综合效率(OEE )二时间稼动率X性能稼动率X良品率稼动率与开动率因翻译的不同,有的地址也将稼动率翻译为开动率,于是也有相对应的性能开动率/时刻开动率等辞汇,其实质上为相同内容。
自动化设备的稼动率与可动率

自动化设备的稼动率与可动率一、稼动率的定义和计算方法稼动率是指自动化设备在一定时间内正常运行的时间与总运行时间的比值,用来评估设备的运行效率和稳定性。
稼动率的计算方法如下:稼动率 = (正常运行时间 / 总运行时间)× 100%二、可动率的定义和计算方法可动率是指自动化设备在一定时间内能够正常运行的时间与总时间的比值,用来评估设备的可靠性和可用性。
可动率的计算方法如下:可动率 = (可运行时间 / 总时间)× 100%三、稼动率与可动率的关系稼动率和可动率都是评估设备运行情况的指标,但两者有所不同。
稼动率更关注设备的运行效率,即设备在运行过程中的正常运行时间占比;而可动率更关注设备的可靠性和可用性,即设备在一定时间内能够正常运行的时间占比。
稼动率高,表示设备的运行效率高;可动率高,表示设备的可靠性和可用性高。
四、提高稼动率和可动率的方法1. 定期维护保养:定期对设备进行维护保养,包括清洁、润滑、紧固等,以确保设备的正常运行。
2. 预防性维护:采取预防性维护措施,如定期更换易损件、进行设备巡检等,以避免设备故障和停机时间的增加。
3. 增加备件库存:合理增加备件库存,以便在设备故障时能够及时更换,减少停机时间。
4. 培训操作人员:对操作人员进行培训,提高其对设备的操作技能和维护能力,减少设备故障的发生。
5. 引入先进设备:引入先进的自动化设备,提高设备的稳定性和可靠性,减少故障发生的可能性。
6. 数据分析和优化:对设备的运行数据进行分析,找出存在的问题和瓶颈,并进行优化改进,以提高设备的稼动率和可动率。
7. 设备巡检和故障排除:定期进行设备巡检,及时发现并排除设备故障,减少停机时间。
8. 设备更新和升级:及时更新设备,引入新的技术和设备,以提高设备的性能和可靠性。
五、案例分析以某工厂的自动化生产线为例,该生产线包括多台自动化设备,运行时间为24小时。
通过对设备运行情况的监测和数据统计,得到以下数据:- 设备A的正常运行时间为20小时,总运行时间为24小时;- 设备B的正常运行时间为22小时,总运行时间为24小时;- 设备C的正常运行时间为18小时,总运行时间为24小时。
工厂设备人员稼动率计算方式说明
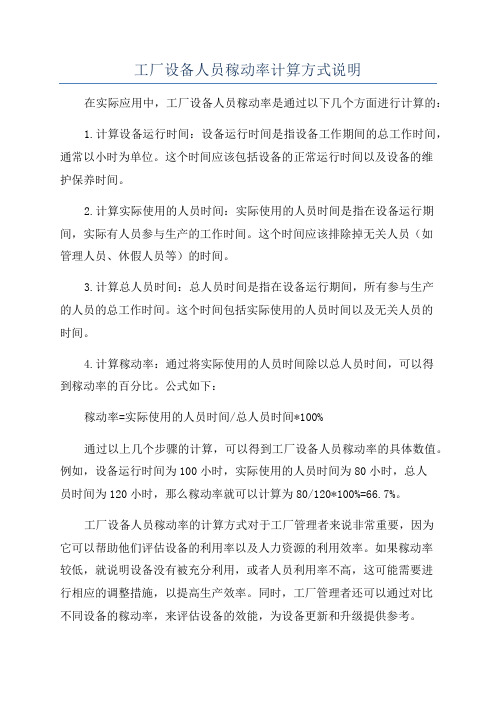
工厂设备人员稼动率计算方式说明在实际应用中,工厂设备人员稼动率是通过以下几个方面进行计算的:1.计算设备运行时间:设备运行时间是指设备工作期间的总工作时间,通常以小时为单位。
这个时间应该包括设备的正常运行时间以及设备的维护保养时间。
2.计算实际使用的人员时间:实际使用的人员时间是指在设备运行期间,实际有人员参与生产的工作时间。
这个时间应该排除掉无关人员(如管理人员、休假人员等)的时间。
3.计算总人员时间:总人员时间是指在设备运行期间,所有参与生产的人员的总工作时间。
这个时间包括实际使用的人员时间以及无关人员的时间。
4.计算稼动率:通过将实际使用的人员时间除以总人员时间,可以得到稼动率的百分比。
公式如下:稼动率=实际使用的人员时间/总人员时间*100%通过以上几个步骤的计算,可以得到工厂设备人员稼动率的具体数值。
例如,设备运行时间为100小时,实际使用的人员时间为80小时,总人员时间为120小时,那么稼动率就可以计算为80/120*100%=66.7%。
工厂设备人员稼动率的计算方式对于工厂管理者来说非常重要,因为它可以帮助他们评估设备的利用率以及人力资源的利用效率。
如果稼动率较低,就说明设备没有被充分利用,或者人员利用率不高,这可能需要进行相应的调整措施,以提高生产效率。
同时,工厂管理者还可以通过对比不同设备的稼动率,来评估设备的效能,为设备更新和升级提供参考。
除了稼动率,还有一些相关指标也可以用于衡量工厂设备的利用率和效率。
例如,设备利用率是指设备运行时间占总时间的比例,它可以帮助评估设备的利用效率;而设备故障率则是指设备在运行期间出现故障的频率,它可以帮助评估设备的可靠性。
这些指标可以综合使用,来更全面地评估工厂设备的运行情况。
总的来说,工厂设备人员稼动率是一个重要的指标,可以帮助工厂管理者评估设备利用率和人力资源利用效率,以便采取相应的措施来提高生产效率。
通过合理计算和分析稼动率,可以有效地提高工厂的综合竞争力。
设备稼动率如何计算

设备稼动率如何计算?悬赏分:0|解决时间:2010-10-28 16:02 |提问者:cyq1119|检举假如我公司有十台设备,但因产订单不足每天只开动6台设备。
每台每天工作8小时。
其中一台因故障停机1小时,1台因工装停机0.5小时。
我们今天的设备稼动率如何计算,敬请告知。
最好能列出计算过程。
首先,你的设备利用率是6台/10台*100%=60%(这个跟设备综合效率无关)第二,设备综合效率(即是综合稼动率)=可动率(已计划的)*表现效率(实际运作时间)*品质合格率。
你提供的条件里;已计划的可动率=?,假设:6台机器不需要停机(比如工人吃饭无需停机、中间无需停机休息、计划内的换模时间为0.5小时);那么可动率=(8小时*6台-0.5小时)/8小时*6台*100%=98.96%表现效率=(已计划的可动时间)47.5小时-(计划外的损失时间)故障停机1小时/47.5小时*100%=97.89%品质合格率=?,假设为100%。
那么,按你提供的条件,你的设备利用率是60%;设备综合稼动率=98.96%*97.89%*100%=96.87%。
但是,我认为是你提供的数据条件不充分,有很多机器的损失时间你还没有列出来,比如:轻微的停顿、开机的损失、返工的损失等。
还有良品率的问题等。
希望这样表达能让你弄明设备白综合稼动率(即综合效率OEE)的概念。
如有需要帮助,可以给我留言。
什么是设备综合效率OEE设备综合效率是Overall Equipment Effectiveness,简称OEE。
一般,每一个生产设备都有自己的理论产能,要实现这一理论产能必须保证没有任何干扰和质量损耗。
OEE就是用来表现实际的生产能力相对于理论产能的比率,它是一个独立的测量工具。
OEE是由可用率,表现性以及质量指数三个关键要素组成:OEE=可用率*表现指数*质量指数其中:可用率=操作时间/计划工作时间它是用来评价停工所带来的损失,包括引起计划生产发生停工的任何事件,例如设备故障,原材料短缺以及生产方法的改变等。
设备时间稼动率的计算方法
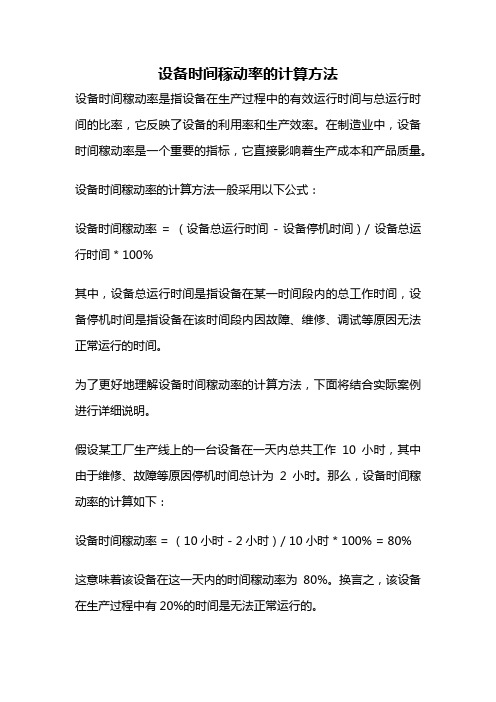
设备时间稼动率的计算方法设备时间稼动率是指设备在生产过程中的有效运行时间与总运行时间的比率,它反映了设备的利用率和生产效率。
在制造业中,设备时间稼动率是一个重要的指标,它直接影响着生产成本和产品质量。
设备时间稼动率的计算方法一般采用以下公式:设备时间稼动率 = (设备总运行时间 - 设备停机时间)/ 设备总运行时间 * 100%其中,设备总运行时间是指设备在某一时间段内的总工作时间,设备停机时间是指设备在该时间段内因故障、维修、调试等原因无法正常运行的时间。
为了更好地理解设备时间稼动率的计算方法,下面将结合实际案例进行详细说明。
假设某工厂生产线上的一台设备在一天内总共工作10小时,其中由于维修、故障等原因停机时间总计为2小时。
那么,设备时间稼动率的计算如下:设备时间稼动率 = (10小时 - 2小时)/ 10小时 * 100% = 80%这意味着该设备在这一天内的时间稼动率为80%。
换言之,该设备在生产过程中有20%的时间是无法正常运行的。
设备时间稼动率的计算方法可以帮助企业评估设备的利用效率和生产效率,从而及时发现设备运行中存在的问题,并采取相应的措施进行改善。
当设备时间稼动率较高时,说明设备的利用率较高,生产效率较好;反之,设备时间稼动率较低时,则需要进一步分析造成设备停机的原因,并采取相应的措施进行改善,以提高设备的时间稼动率。
除了计算设备时间稼动率,企业还可以通过其他方式来提高设备的利用率和生产效率。
首先,定期对设备进行维护保养,及时清理设备故障和故障原因,确保设备正常运行。
其次,加强设备操作员的培训,提高其操作设备的技能水平,减少操作错误和设备故障的发生。
此外,对设备进行合理的调度和排产,避免因为生产计划不合理导致设备运行时间过长或过短。
设备时间稼动率是衡量设备利用率和生产效率的重要指标,通过合理计算和分析设备时间稼动率,企业可以及时发现设备运行中存在的问题,并采取相应的措施进行改善,以提高设备的时间稼动率,从而提高生产效率和降低生产成本。
自动化设备的稼动率与可动率
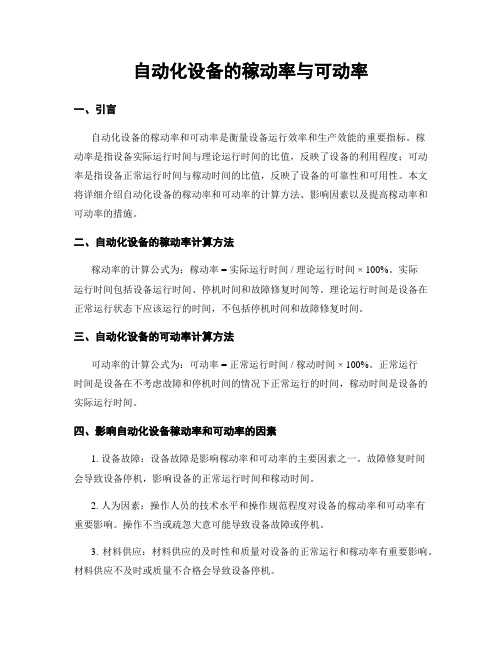
自动化设备的稼动率与可动率一、引言自动化设备的稼动率和可动率是衡量设备运行效率和生产效能的重要指标。
稼动率是指设备实际运行时间与理论运行时间的比值,反映了设备的利用程度;可动率是指设备正常运行时间与稼动时间的比值,反映了设备的可靠性和可用性。
本文将详细介绍自动化设备的稼动率和可动率的计算方法、影响因素以及提高稼动率和可动率的措施。
二、自动化设备的稼动率计算方法稼动率的计算公式为:稼动率 = 实际运行时间 / 理论运行时间 × 100%。
实际运行时间包括设备运行时间、停机时间和故障修复时间等。
理论运行时间是设备在正常运行状态下应该运行的时间,不包括停机时间和故障修复时间。
三、自动化设备的可动率计算方法可动率的计算公式为:可动率 = 正常运行时间 / 稼动时间 × 100%。
正常运行时间是设备在不考虑故障和停机时间的情况下正常运行的时间,稼动时间是设备的实际运行时间。
四、影响自动化设备稼动率和可动率的因素1. 设备故障:设备故障是影响稼动率和可动率的主要因素之一。
故障修复时间会导致设备停机,影响设备的正常运行时间和稼动时间。
2. 人为因素:操作人员的技术水平和操作规范程度对设备的稼动率和可动率有重要影响。
操作不当或疏忽大意可能导致设备故障或停机。
3. 材料供应:材料供应的及时性和质量对设备的正常运行和稼动率有重要影响。
材料供应不及时或质量不合格会导致设备停机。
4. 设备维护:设备的定期维护和保养对设备的稼动率和可动率有重要影响。
定期维护可以预防故障的发生,提高设备的可靠性和可用性。
五、提高自动化设备稼动率和可动率的措施1. 加强设备维护:定期进行设备的维护和保养,及时发现并修复潜在故障,提高设备的可靠性和可用性。
2. 培训操作人员:提高操作人员的技术水平和操作规范程度,减少人为因素对设备稼动率和可动率的影响。
3. 优化材料供应链:与供应商建立良好的合作关系,确保材料供应的及时性和质量,减少设备因材料问题而停机的情况。
稼动率的计算方法

稼动率的计算方法-CAL-FENGHAI.-(YICAI)-Company One1稼动率的计算方法时间稼动率:首先定义最大操作时间,指的是设备可用的最大时间,若设备本身为厂内自购,且可完全由厂内自主使用,则最大操作时间一般为日历时间;而负荷时间则为设备可稼动的时间,乃是最大操作时间扣除停机(Shutdown,SD)损失,停机损失乃是计划上的休止时间,如休假、教育训练、保养等。
而稼动时间则是负荷时间扣除停止时间,而停止时间包括批次转换及制程异常、设备异常停止及修复时间。
最大操作时间:设备可用的最大时间负荷时间:最大操作时间扣除停机(Shutdown,SD)损失;停机(Shutdown,SD)损失:计画上的休止时间,如休假、教育训练、保养等稼动时间:负荷时间扣除停止时间停止时间:包括批次转换及制程异常、设备异常停止及修复时间。
由以上的定义,即可算出最常用的稼动率定义-设备稼动率(也称为时间稼动率),其公式为时间稼动率=稼动时间/负荷时间目的:减少停止时间!!!通过资源整合,管理优化,进行资源充分利用,降低成本,提高效率。
性能稼动率/实质稼动率/速度稼动率时间稼动率并无法完全表现设备对生产的贡献程度;例如,相同的设备,相等的稼动时间,可能因效率的不同,而有不同的产能,此类效率降低的损失则称为性能损失。
在此定义速度稼动率如下:速度稼动率=基准周期时间/实际周期时间其中,基准周期时间:设备原设计产出单位产量所需的时间。
实际周期时间:目前设备实际产出单位产量所需的时间。
并定义实质稼动率与性能稼动率如下:实质稼动率=生产量×实际周期时间/稼动时间性能稼动率=速度稼动率×实质稼动率性能稼动时间则定义为:性能稼动时间=稼动时间×性能稼动率=稼动时间-性能损失时间其中性能损失包括速度低落的损失与短暂停机的损失。
由以上定义可知,若性能稼动率变小,则可判定生产相关设备的效率降低。
价值稼动时间与设备综合效率(OverallEquipmentEffectiveness)性能稼动时间表示设备产出产品的时间,但无法表示设备产出良率的好坏,因此定义「价值稼动时间」来表示真正能产出良品的有价值时间,其定义如下:价值稼动时间=性能稼动时间×良品率而设备的有效使用程度则以「设备总合效率」来判定,其定义如下:设备综合效率(OEE)=时间稼动率×性能稼动率×良品率稼动率与开动率因翻译的不同,有的地方也将稼动率翻译为开动率,于是也有相对应的性能开动率/时间开动率等词汇,其实质上为相同内容。
人员稼动率的计算公式

人员稼动率是指实际工作的时间与应该工作的时间之比,用于衡量生产效率或工作效能。
它可以帮助企业了解员工的有效工作时间,并识别出生产流程中的瓶颈和浪费。
以下是人员稼动率的计算公式及详细解析。
一、人员稼动率的计算公式人员稼动率= (实际工作小时数/ 计划工作小时数)×100%其中:实际工作小时数= 当天总工时- 损失工时计划工作小时数= 标准工时×生产数量损失工时= 设备故障、品质异常、生产安排等原因导致的停工时间二、详细解析实际工作小时数:这是员工实际用于生产或工作的时间。
为了准确地计算实际工作小时数,需要详细记录每名员工的出勤时间、休息时间和停工时间。
出勤时间是指员工到达工作岗位的时间;休息时间是指员工因用餐、交接班等原因暂时离开工作岗位的时间;停工时间则是指由于设备故障、品质异常、生产安排等原因导致的停工时间。
将员工的出勤时间减去停工时间,即可得到实际工作小时数。
计划工作小时数:这是根据生产计划或工作安排,员工应该用于生产或工作的时间。
计划工作小时数的计算公式中的标准工时是指完成某一生产任务所需的标准时间,生产数量是指计划内的生产任务数量。
将标准工时与生产数量相乘,即可得到计划工作小时数。
损失工时:这是指由于各种原因导致的非计划内停工时间。
这些原因可能包括设备故障、品质异常、生产安排不当等。
损失工时的计算公式中的设备故障是指设备在运行过程中出现的故障,品质异常是指产品不符合质量标准而需要进行返工或调整,生产安排不当是指生产计划不合理或资源配置不均导致的工作效率低下。
通过分析损失工时的原因,可以采取相应的措施来减少非计划内停工时间,提高人员稼动率。
人员稼动率的计算结果是一个百分比值,表示实际工作时间占计划工作时间的比例。
如果人员稼动率较高,说明员工实际用于生产或工作的时间较长,生产效率或工作效率较高;如果人员稼动率较低,说明员工实际用于生产或工作的时间较短,生产效率或工作效率较低。
稼动率计算方法

1.稼动率的计算方法:时间稼动率:首先定义最大操作时间, 指的是设备可用的最大时间,若设备本身为厂内自购,且动的时间,乃是最大操作时间扣除停 机(Shutdown, SD)损失,停机损失乃是计画上的休止时 间,如休假、教育训练、保养等。而稼动时间则是负荷时间 扣除停止时间,而停止时间包括批次转换及制程异常、设备 异常停止及修复时间。
• 2、性能稼动率/实质稼动率/速度稼动率 时间稼动率并 无法完全表现设备对生产的贡献程度; 例如,相同的设 备,相等的稼动时间,可能因效率的不同,而有不同的产 能,此类效率降低的损失则称为性能损失。
• 在此定义速度稼动率如下:
• 速度稼动率= 基准周期时间/ 实际周期时间其中,基准周 期时间:设备原设计产出单位产量所需的时间。
最大操作时间:设备可用的最大时间负荷时间:最大操 作时间扣除停机(Shutdown, SD) 损失;停机 (Shutdown, SD)损失:计画上的休止时间,如休假、教 育训练、保养等稼动时间:负荷时间扣除停止时间停止时间: 包括批次转换及制程异常、设备异常停止及修复时间。由以 上的定义,
即可算出最常用的稼动率定义-设备稼动率(也称为时 间稼动率),其公式为时间稼动率= 稼动时间 / 负荷时间 目的:减少停止时间!!!通过资源整合,管理优化,进行 资源充分利用,降低成本,提高效率。
设备稼动率简单算法表格
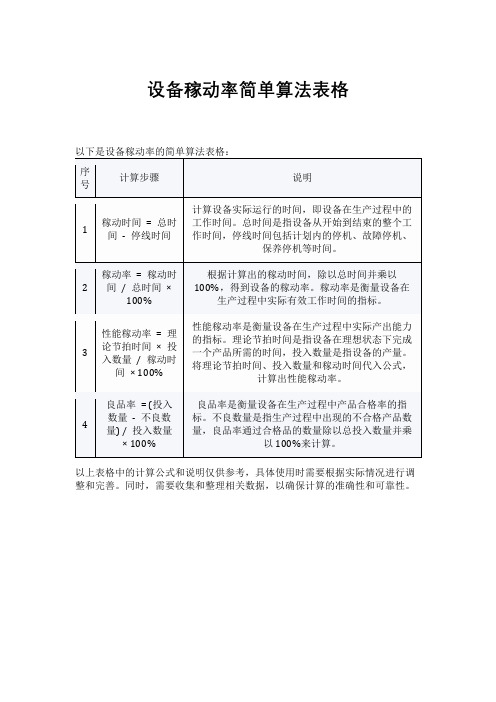
以下是设备稼动率的简单算法表格:
序号
计算步骤
说明
1
稼动时间=总时间-停线时间
计算设备实际运行的时间,即设备在生产过程中的工作时间。总时间是指设备从开始到结束的整个工作时间,停线时间包括计划内的停、故障停机、保养停机等时间。
2
稼动率=稼动时间/总时间× 100%
根据计算出的稼动时间,除以总时间并乘以100%,得到设备的稼动率。稼动率是衡量设备在生产过程中实际有效工作时间的指标。
3
性能稼动率=理论节拍时间×投入数量/稼动时间× 100%
性能稼动率是衡量设备在生产过程中实际产出能力的指标。理论节拍时间是指设备在理想状态下完成一个产品所需的时间,投入数量是指设备的产量。将理论节拍时间、投入数量和稼动时间代入公式,计算出性能稼动率。
4
良品率= (投入数量-不良数量) /投入数量× 100%
良品率是衡量设备在生产过程中产品合格率的指标。不良数量是指生产过程中出现的不合格产品数量,良品率通过合格品的数量除以总投入数量并乘以100%来计算。
以上表格中的计算公式和说明仅供参考,具体使用时需要根据实际情况进行调整和完善。同时,需要收集和整理相关数据,以确保计算的准确性和可靠性。
自动化设备的稼动率与可动率

自动化设备的稼动率与可动率一、引言自动化设备的稼动率与可动率是衡量设备运行效率和生产能力的重要指标。
稼动率指设备实际运行时间与总运行时间的比值,反映了设备的利用率;可动率指设备实际运行时间与设备可运行时间的比值,反映了设备的可靠性和可用性。
本文将详细介绍自动化设备的稼动率与可动率的计算方法、影响因素以及提高稼动率与可动率的措施。
二、自动化设备的稼动率计算方法稼动率的计算方法为:稼动率 = (设备实际运行时间 / 总运行时间) × 100%。
设备实际运行时间指设备在生产过程中真正运行的时间,不包括停机、维修、调试等非运行时间;总运行时间指设备应该运行的总时间,包括设备实际运行时间和非运行时间。
三、自动化设备的可动率计算方法可动率的计算方法为:可动率 = (设备实际运行时间 / 设备可运行时间) × 100%。
设备可运行时间指设备在一定时间内应该可靠运行的时间,不包括计划停机、计划维修等预定非运行时间。
四、影响自动化设备稼动率与可动率的因素1. 设备故障率:设备故障率高会导致设备停机时间增加,降低稼动率与可动率。
2. 维修时间:维修时间长会导致设备停机时间增加,降低稼动率与可动率。
3. 操作人员技能:操作人员技能水平高低直接影响设备的运行效率和故障率。
4. 原材料供应:原材料供应不稳定会导致设备停机等待原材料,降低稼动率与可动率。
5. 设备设计与制造质量:设备设计与制造质量好坏直接影响设备的可靠性和稳定性。
五、提高自动化设备稼动率与可动率的措施1. 加强设备维护:定期进行设备维护保养,减少设备故障率和维修时间,提高稼动率与可动率。
2. 培训操作人员:加强操作人员的培训和技能提升,提高设备的运行效率和故障排除能力。
3. 优化生产计划:合理安排生产计划,减少设备的停机等待时间,提高稼动率与可动率。
4. 优化原材料供应链:与供应商建立稳定的合作关系,确保原材料供应的及时性和稳定性。
5. 选择优质设备供应商:选择具有良好声誉和高品质设备的供应商,提高设备的可靠性和稳定性。
设备稼动率
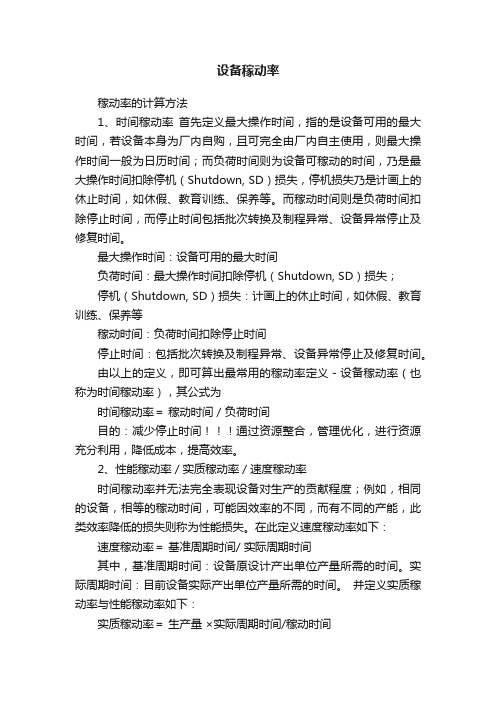
设备稼动率稼动率的计算方法1、时间稼动率首先定义最大操作时间,指的是设备可用的最大时间,若设备本身为厂内自购,且可完全由厂内自主使用,则最大操作时间一般为日历时间;而负荷时间则为设备可稼动的时间,乃是最大操作时间扣除停机(Shutdown, SD)损失,停机损失乃是计画上的休止时间,如休假、教育训练、保养等。
而稼动时间则是负荷时间扣除停止时间,而停止时间包括批次转换及制程异常、设备异常停止及修复时间。
最大操作时间:设备可用的最大时间负荷时间:最大操作时间扣除停机(Shutdown, SD)损失;停机(Shutdown, SD)损失:计画上的休止时间,如休假、教育训练、保养等稼动时间:负荷时间扣除停止时间停止时间:包括批次转换及制程异常、设备异常停止及修复时间。
由以上的定义,即可算出最常用的稼动率定义-设备稼动率(也称为时间稼动率),其公式为时间稼动率=稼动时间 / 负荷时间目的:减少停止时间通过资源整合,管理优化,进行资源充分利用,降低成本,提高效率。
2、性能稼动率/实质稼动率/速度稼动率时间稼动率并无法完全表现设备对生产的贡献程度;例如,相同的设备,相等的稼动时间,可能因效率的不同,而有不同的产能,此类效率降低的损失则称为性能损失。
在此定义速度稼动率如下:速度稼动率=基准周期时间/ 实际周期时间其中,基准周期时间:设备原设计产出单位产量所需的时间。
实际周期时间:目前设备实际产出单位产量所需的时间。
并定义实质稼动率与性能稼动率如下:实质稼动率=生产量×实际周期时间/稼动时间性能稼动率=速度稼动率×实质稼动率性能稼动时间则定义为:性能稼动时间=稼动时间×性能稼动率=稼动时间-性能损失时间其中性能损失包括速度低落的损失与短暂停机的损失。
由以上定义可知,若性能稼动率变小,则可判定生产相关设备的效率降低。
3、价值稼动时间与设备总合效率性能稼动时间表示设备产出产品的时间,但无法表示设备产出良率的好坏,因此定义「价值稼动时间」来表示真正能产出良品的有价值时间,其定义如下:价值稼动时间=性能稼动时间×良品率而设备的有效使用程度则以「设备总合效率」来判定,其定义如下:设备总合效率=时间稼动率×性能稼动率×良品率。
设备稼动率的计算方法
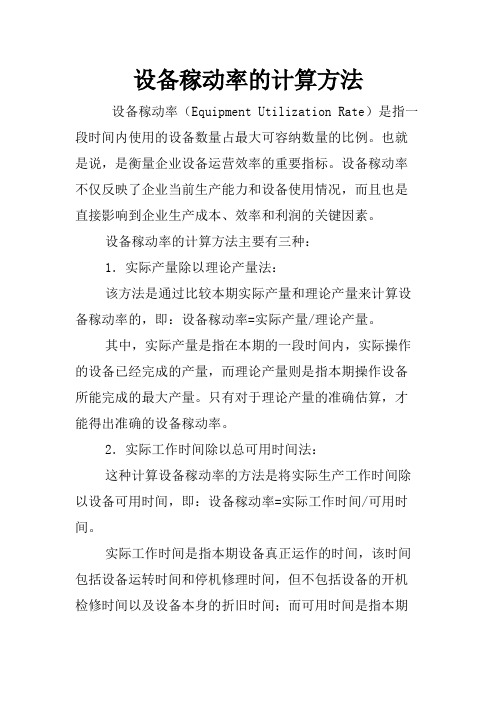
设备稼动率的计算方法设备稼动率(Equipment Utilization Rate)是指一段时间内使用的设备数量占最大可容纳数量的比例。
也就是说,是衡量企业设备运营效率的重要指标。
设备稼动率不仅反映了企业当前生产能力和设备使用情况,而且也是直接影响到企业生产成本、效率和利润的关键因素。
设备稼动率的计算方法主要有三种:1.实际产量除以理论产量法:该方法是通过比较本期实际产量和理论产量来计算设备稼动率的,即:设备稼动率=实际产量/理论产量。
其中,实际产量是指在本期的一段时间内,实际操作的设备已经完成的产量,而理论产量则是指本期操作设备所能完成的最大产量。
只有对于理论产量的准确估算,才能得出准确的设备稼动率。
2.实际工作时间除以总可用时间法:这种计算设备稼动率的方法是将实际生产工作时间除以设备可用时间,即:设备稼动率=实际工作时间/可用时间。
实际工作时间是指本期设备真正运作的时间,该时间包括设备运转时间和停机修理时间,但不包括设备的开机检修时间以及设备本身的折旧时间;而可用时间是指本期设备可用时间,该时间包括设备开机检修时间以及设备本身的折旧时间。
3.实际产出价值除以最大产出价值法:该方法是通过比较本期实际产出价值和最大产出价值来计算设备稼动率的,即:设备稼动率=实际产出价值/最大产出价值。
其中,实际产出价值是指在本期的一段时间内,实际操作的设备所产生的产出价值,而最大产出价值则是指本期操作设备所能完成的最大产出价值。
以上是设备稼动率的计算方法,正确合理的计算设备稼动率,对企业来说具有重大意义,可以有效提高企业的效率和利润。
因此,企业应依据不同的情况进行合理的设备稼动率计算,以更好地提高企业的生产效率和利润水平。
稼动率的计算方法

稼动率的计算方法稼动率(Utilization Rate)是指生产设备、工作人员、生产线或整个生产系统在一段时间内实际运行的时间与可运行的时间之比,也就是工作时间的利用率。
在生产管理中,稼动率是一个重要的指标,反映了生产资源的有效利用程度。
稼动率计算方法主要根据不同的生产对象和时间粒度有所差异,以下是几种常见的计算方法:1.设备稼动率的计算方法:设备稼动率是指一台或多台设备实际运行时间与可运行时间之比。
设备稼动率可以按照设备运行情况分为两种:- 总稼动率(Overall Equipment Effectiveness,OEE):OEE是指设备在一定时间内实际生产数量与理论最大生产能力之比。
计算公式为:OEE=设备实际运行时间/(设备理论运行时间×设备设计生产能力)设备实际运行时间是指设备在一定时间内真正处于生产状态的时间,不包括设备运行中的停机、换模、维修等非生产时间。
设备理论运行时间是指设备在一定时间内能够连续运行的最长时间,通常以24小时为基准。
设备设计生产能力是指设备在理论运行状态下能够达到的最大产能。
- 开动率(Running Rate):开动率是指设备实际运行时间与可运行时间之比。
计算公式为:开动率=设备实际运行时间/可运行时间可运行时间是指设备在一定时间内应该处于运行状态的时间,包括除停机、换模、维修外的所有时间。
2.人工稼动率的计算方法:人工稼动率是指生产线上工人实际工作时间与可工作时间之比。
计算公式为:人工稼动率=工人实际工作时间/可工作时间工人实际工作时间是指工人在一定时间内实际从事生产工作的时间,不包括工人的休息、用餐、集合、培训等非工作时间。
可工作时间是指工人在一定时间内应该从事生产工作的时间,包括除非工人休息、用餐、集合、培训等以外的所有时间。
3.生产线稼动率的计算方法:生产线稼动率是指生产线实际运行时间与可运行时间之比。
生产线稼动率可以按照不同的计算方法分为两种:-连续开动率:连续开动率是指生产线在一定时间内连续运行的时间与可运行时间之比。
设备稼动率的计算公式举例
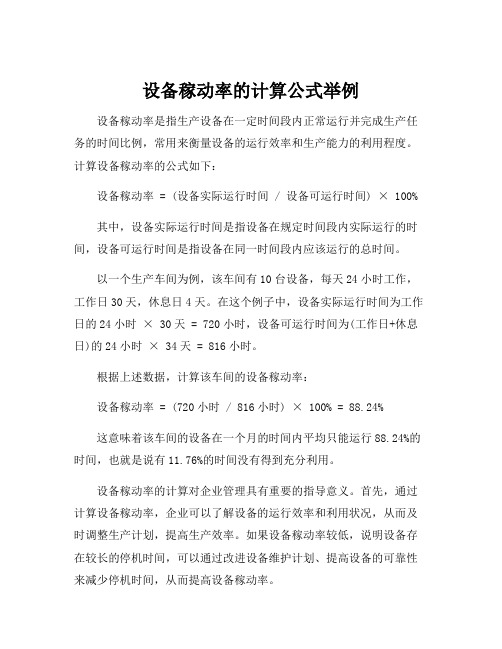
设备稼动率的计算公式举例设备稼动率是指生产设备在一定时间段内正常运行并完成生产任务的时间比例,常用来衡量设备的运行效率和生产能力的利用程度。
计算设备稼动率的公式如下:设备稼动率 = (设备实际运行时间 / 设备可运行时间) × 100%其中,设备实际运行时间是指设备在规定时间段内实际运行的时间,设备可运行时间是指设备在同一时间段内应该运行的总时间。
以一个生产车间为例,该车间有10台设备,每天24小时工作,工作日30天,休息日4天。
在这个例子中,设备实际运行时间为工作日的24小时× 30天 = 720小时,设备可运行时间为(工作日+休息日)的24小时× 34天 = 816小时。
根据上述数据,计算该车间的设备稼动率:设备稼动率 = (720小时 / 816小时) × 100% = 88.24%这意味着该车间的设备在一个月的时间内平均只能运行88.24%的时间,也就是说有11.76%的时间没有得到充分利用。
设备稼动率的计算对企业管理具有重要的指导意义。
首先,通过计算设备稼动率,企业可以了解设备的运行效率和利用状况,从而及时调整生产计划,提高生产效率。
如果设备稼动率较低,说明设备存在较长的停机时间,可以通过改进设备维护计划、提高设备的可靠性来减少停机时间,从而提高设备稼动率。
其次,设备稼动率的计算也有助于企业进行设备投资决策。
通过分析不同设备的稼动率,企业可以了解到哪些设备利用率较高、收益较大,进而合理规划设备更新和购置计划,提升企业的竞争力。
此外,设备稼动率还可以作为员工激励的依据。
对于企业来说,稼动率高意味着生产效率高,员工完成任务的数量也会相应增加,这可以作为绩效考核的评价标准之一,同时也可以激励员工积极参与设备的运行和维护工作,提高整体生产效率。
综上所述,设备稼动率的计算公式简单明了,通过计算设备稼动率可以全面了解设备的运行效率和利用状况,为企业的生产管理和设备投资决策提供重要的参考依据,同时也可以作为员工激励的一种手段。
设备稼动率如何计算
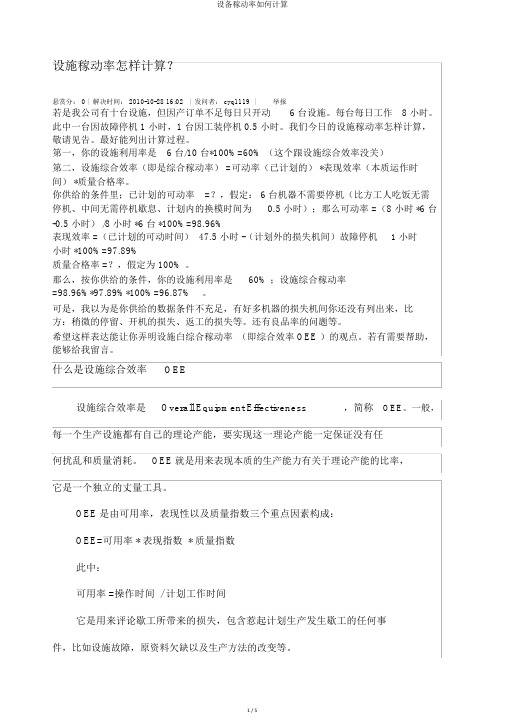
设施稼动率怎样计算?悬赏分: 0 | 解决时间: 2010-10-28 16:02 | 发问者: cyq1119 | 举报若是我公司有十台设施,但因产订单不足每日只开动 6 台设施。
每台每日工作8 小时。
此中一台因故障停机 1 小时,1 台因工装停机 0.5 小时。
我们今日的设施稼动率怎样计算,敬请见告。
最好能列出计算过程。
第一,你的设施利用率是 6 台/10 台*100%=60% (这个跟设施综合效率没关)第二,设施综合效率(即是综合稼动率) =可动率(已计划的) *表现效率(本质运作时间) *质量合格率。
你供给的条件里;已计划的可动率=?,假定: 6 台机器不需要停机(比方工人吃饭无需停机、中间无需停机歇息、计划内的换模时间为0.5 小时);那么可动率 =(8 小时 *6 台-0.5 小时) /8 小时 *6 台 *100%=98.96%表现效率 =(已计划的可动时间) 47.5 小时 -(计划外的损失机间)故障停机 1 小时小时 *100%=97.89%质量合格率 =?,假定为 100% 。
那么,按你供给的条件,你的设施利用率是60% ;设施综合稼动率=98.96%*97.89%*100%=96.87%。
可是,我以为是你供给的数据条件不充足,有好多机器的损失机间你还没有列出来,比方:稍微的停留、开机的损失、返工的损失等。
还有良品率的问题等。
希望这样表达能让你弄明设施白综合稼动率(即综合效率 OEE )的观点。
若有需要帮助,能够给我留言。
什么是设施综合效率OEE设施综合效率是Overall Equipment Effectiveness,简称OEE。
一般,每一个生产设施都有自己的理论产能,要实现这一理论产能一定保证没有任何扰乱和质量消耗。
OEE就是用来表现本质的生产能力有关于理论产能的比率,它是一个独立的丈量工具。
OEE是由可用率,表现性以及质量指数三个重点因素构成:OEE=可用率 * 表现指数 * 质量指数此中:可用率 =操作时间 / 计划工作时间它是用来评论歇工所带来的损失,包含惹起计划生产发生歇工的任何事件,比如设施故障,原资料欠缺以及生产方法的改变等。
SMT稼动率定义和案例,什么叫稼动率,
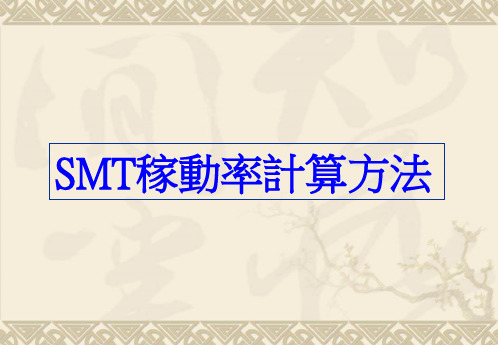
519*(3600/20*1)
150
148
* * 3600/0.044+3600/0.044+3600/0.094=201933
3600/20*1
150
37.98% (稼動率)
519*(3600/20*1)
3600/0.044+3600/0.044+3600/0.094=201933
*
150 3600/20*1
38.5% (稼動率)
SMT稼動率計算方法(2) (無轉嫁)
稼動率
= (每小時)
÷ Upload 料站表導入總點數
*AOI站實際產出掃描片數 (每小時)
(3600S/第1台機貼裝1顆點的理論時間 +3600S/第2臺機貼裝1顆點的理論時間 +3600S/第3台機貼裝1顆點的理論時間
SMT稼動率計算方法
一.稼動率的定義
SMT效率表達方式說明﹕
1.作業生產效率=實際生產片數/(3600S/最慢一台機cycletime)*工作時間 2.制造效率=實際生產片數/(3600S/最慢一台機cycletime)*(總工作時間-非制造損耗時間) 3.程式利用率=機器利用率=3600/程式優化cycletime*點數/每小時所有機器理論點數總合 4.設備點數稼動率(無轉嫁)=實際生產點數/(每小時所有機器理論點數總合*所有工作時間) 5.設備點數稼動率(有轉稼)=實際生產點數/〔每小時理論點數總合*(所有工作時間-不可控損失時間)〕 6.設備時間稼動率=(總工作時間-損失時間)/總工作時間 7.機台平衡率=每台機cycletime總合/(最慢一台機cycletime*機台數) 8.機台故障率=機台故障時間總合/所有線工作時間總合
工厂设备人员稼动率计算方式说明
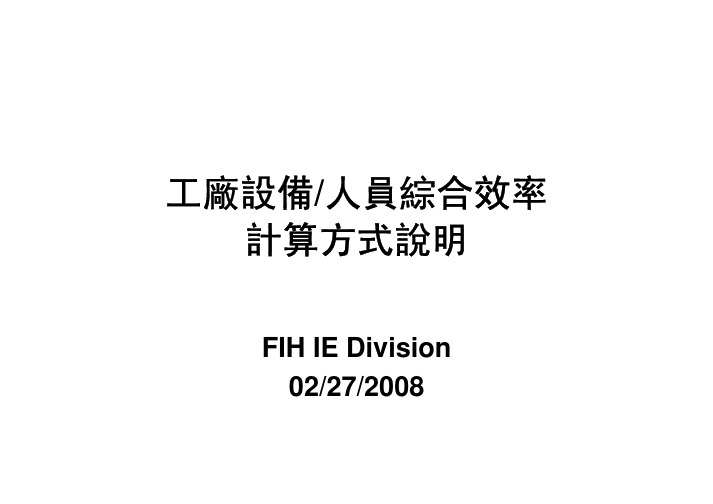
工廠設備/人員綜合效率計算方式說明FIH IE Division02/27/2008Content ¾設備綜合效率定義OEE¾人員綜合效率定義OEE設備時間稼動率統計範圍: FIH所有生產廠部統計內容: 各廠部上周設備時間稼動率以及未來8周統計預估時間稼動率;統計之時間稼動率需區分開量試&量產各自稼動比例.統計頻率: 每周統計更新一次.備註:1. 設備數: 所有主體生產設備, 包含量產,量試,閑置,待移轉以及借用的設備.設備數= ( 周初設備數+周末設備數) / 22. 製程單一的廠部僅統計製程內主體設備的時間稼動率,例如成型製程則只需統計成型機的稼動率.3. 以線體方式進行生產的廠部僅統計整個線體的設備時間稼動率,例如SMT和烤漆製程.4. 製程多且長的廠部僅統計瓶頸工站設備設備稼動率,例如表面處理以及特殊加工製程.預估設備性能稼動率和產品良率•預估設備性能稼動率和產品良率數據一般與現狀水平保持一致.•若針對上述指標有做針對性的改善, 則預估值填寫上述指標的改善目標值.人員時間稼動率統計範圍: FIH所有組裝製程廠部統計內容: 各廠部上周人員時間稼動率以及未來8周統計預估時間稼動率;統計之時間稼動率需區分開量試&量產各自稼動比例.統計頻率: 每周統計更新一次.備註:DL人數: 廠部所有DL人數, 包含在冊和借入人數,不包含借出人數.DL人數= ( 周初DL人數+周末DL數) / 2預估人員綜合效率•預估人員綜合效率各項指標數據一般與現狀水平保持一致.•若針對上述指標有做針對性的改善, 則預估值填寫上述指標的改善目標值.Thanks。
【e百科】可动率稼动率
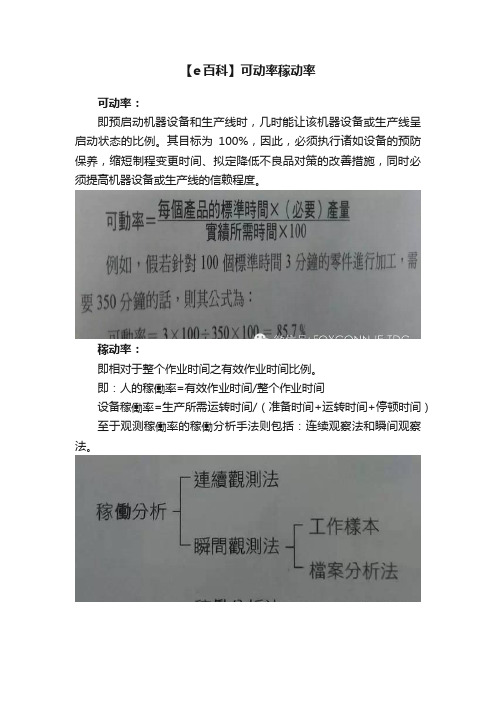
【e百科】可动率稼动率
可动率:
即预启动机器设备和生产线时,几时能让该机器设备或生产线呈启动状态的比例。
其目标为100%,因此,必须执行诸如设备的预防保养,缩短制程变更时间、拟定降低不良品对策的改善措施,同时必须提高机器设备或生产线的信赖程度。
稼动率:
即相对于整个作业时间之有效作业时间比例。
即:人的稼働率=有效作业时间/整个作业时间
设备稼働率=生产所需运转时间/(准备时间+运转时间+停顿时间)至于观测稼働率的稼働分析手法则包括:连续观察法和瞬间观察法。
来源:《图解工厂管理暨现场用语事典》。
- 1、下载文档前请自行甄别文档内容的完整性,平台不提供额外的编辑、内容补充、找答案等附加服务。
- 2、"仅部分预览"的文档,不可在线预览部分如存在完整性等问题,可反馈申请退款(可完整预览的文档不适用该条件!)。
- 3、如文档侵犯您的权益,请联系客服反馈,我们会尽快为您处理(人工客服工作时间:9:00-18:30)。
工廠設備/人員綜合效率計算方式說明
FIH IE Division
02/27/2008
Content ¾設備綜合效率定義OEE
¾人員綜合效率定義OEE
設備時間稼動率
統計範圍: FIH所有生產廠部
統計內容: 各廠部上周設備時間稼動率以及未來8周統計預估時間稼動率;
統計之時間稼動率需區分開量試&量產各自稼動比例.
統計頻率: 每周統計更新一次.
備註:
1. 設備數: 所有主體生產設備, 包含量產,量試,閑置,待移轉以及借用的設備.
設備數= ( 周初設備數+周末設備數) / 2
2. 製程單一的廠部僅統計製程內主體設備的時間稼動率,例如成型製程則只需統計成
型機的稼動率.
3. 以線體方式進行生產的廠部僅統計整個線體的設備時間稼動率,例如SMT和烤漆製程.
4. 製程多且長的廠部僅統計瓶頸工站設備設備稼動率,例如表面處理以及特殊加工製程.
預估設備性能稼動率和產品良率
•預估設備性能稼動率和產品良率數據一般與現狀水平保持一致.
•若針對上述指標有做針對性的改善, 則預估值填寫上述指標的改善目標值.
人員時間稼動率
統計範圍: FIH所有組裝製程廠部
統計內容: 各廠部上周人員時間稼動率以及未來8周統計預估時間稼動率;
統計之時間稼動率需區分開量試&量產各自稼動比例.
統計頻率: 每周統計更新一次.
備註:
DL人數: 廠部所有DL人數, 包含在冊和借入人數,不包含借出人數.
DL人數= ( 周初DL人數+周末DL數) / 2
預估人員綜合效率
•預估人員綜合效率各項指標數據一般與現狀水平保持一致.
•若針對上述指標有做針對性的改善, 則預估值填寫上述指標的改善目標值.
Thanks。