滚齿机传动链误差测量误差分析及辨识
滚齿机精度检验标准

滚齿机精度检验标准一、齿形精度齿形精度是滚齿机加工质量的关键指标。
为确保齿形精度,需要检查以下几个因素:1. 齿形的对称性:通过观察齿形的左右两侧是否完全对称来判断。
可以使用测量工具进行精确测量。
2. 齿形的完整性:需要检查齿形是否有缺失或不规则部分。
可以通过对比加工出的齿形与理论齿形进行判断。
3. 齿顶圆的圆度:需要保证齿顶圆的圆度公差在允许范围内,以避免齿顶磨损和噪音的产生。
可以使用测量工具进行精确测量。
二、齿向精度齿向精度是指齿轮的螺旋线方向与理论方向之间的偏差。
为确保齿向精度,需要检查以下几个因素:1. 螺旋线的直线度:需要使用测量工具检查齿轮的螺旋线是否平直,无弯曲或扭曲现象。
2. 螺旋线的方向:需要确保齿轮的螺旋线方向与理论方向一致,以避免齿轮运转时的振动和噪音。
3. 齿距的一致性:需要检查同一齿轮上各齿距是否一致,以避免齿轮运转时的冲击和振动。
可以使用测量工具进行精确测量。
三、齿厚精度齿厚精度是指加工出的齿轮厚度与理论厚度之间的偏差。
为确保齿厚精度,需要检查以下几个因素:1. 齿厚的均匀性:需要使用测量工具检查齿轮的各齿厚是否均匀一致,以避免齿轮运转时的冲击和振动。
2. 齿厚的偏差:需要将实际齿厚与理论齿厚进行比较,以判断是否存在偏差。
可以使用测量工具进行精确测量。
3. 齿厚的稳定性:需要检查同一批次的齿轮之间是否存在较大的厚度差异,以确保齿轮运转时的稳定性。
可以使用测量工具进行精确测量。
四、表面粗糙度表面粗糙度是指加工后的齿轮表面微观不平整程度。
为确保表面粗糙度符合要求,需要检查以下几个因素:1. 表面粗糙度的值:需要使用表面粗糙度测量仪检查齿轮表面的粗糙度值是否符合要求。
一般而言,表面粗糙度越小,齿轮的耐磨性和使用寿命越好。
2. 表面缺陷:需要检查齿轮表面是否存在划痕、烧伤、裂纹等缺陷,这些缺陷会影响齿轮的运转性能和使用寿命。
可以使用目视观察或借助放大镜进行检查。
3. 热处理质量:热处理质量对齿轮的表面粗糙度有很大影响。
齿轮传动轴的传动误差与回转间隙分析

齿轮传动轴的传动误差与回转间隙分析引言齿轮传动是常见的一种机械传动形式,广泛应用于工业机械领域。
在齿轮传动中,传动误差和回转间隙是重要的性能指标,对传动系统的精度和运行稳定性有着重要影响。
本文将针对齿轮传动轴的传动误差与回转间隙进行详细分析,探讨它们的原因以及对传动系统性能的影响。
一、传动误差的定义与分类传动误差是指齿轮传动轴在工作过程中由于齿轮的制造、装配等因素,导致输出轴承载方向的误差。
在齿轮传动中,常见的传动误差主要包括齿形误差、齿隙误差和轴向移位误差。
1. 齿形误差:齿形误差是指齿轮齿廓形状与理想齿廓的差异。
齿形误差可以通过齿轮的制造工艺、加工精度以及齿形检测仪器的性能等因素引起。
齿形误差会导致传动系统的噪声和振动增加,降低传动系统的工作效率。
2. 齿隙误差:齿隙误差是指齿轮齿槽之间的间隙大小不一致。
齿隙误差可以由齿轮的制造工艺、装配过程中的间隙控制等因素引起。
齿隙误差会导致传动系统的动态特性变差,降低传动系统的响应速度和稳定性。
3. 轴向移位误差:轴向移位误差是指齿轮轴在工作过程中由于装配不精确或轴向载荷造成的轴向偏移。
轴向移位误差会导致传动系统的运行不平稳,产生冲击和振动,严重时会导致传动轴的断裂。
二、传动误差的影响因素传动误差的产生与多个因素相关,主要包括齿轮的加工工艺、装配精度、使用环境、负载情况等。
1. 加工工艺:齿轮的加工工艺是影响传动误差的重要因素之一。
制造齿轮时,加工精度越高产生的传动误差就越小。
高精度的加工设备和工艺可以减少齿形误差和齿隙误差的产生。
2. 装配精度:齿轮装配过程中的精度控制也会对传动误差产生重要影响。
装配精度越高,齿轮的传动误差就越小。
装配精度主要包括齿轮齿轮间隙的控制、轴向偏移的控制等。
3. 使用环境:齿轮传动系统的使用环境对传动误差有着重要影响。
高温、高湿、高腐蚀等环境会导致齿轮表面的磨损加剧,进而影响传动误差。
4. 负载情况:齿轮传动系统的负载情况也会对传动误差产生影响。
机械传动及其测试实验误差分析
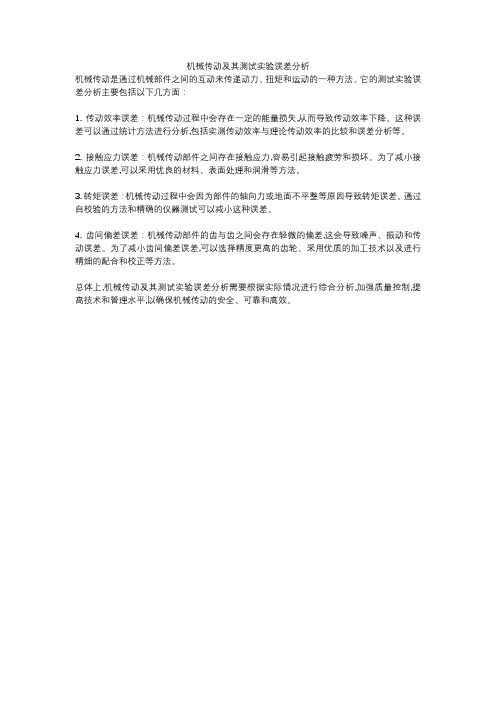
机械传动及其测试实验误差分析
机械传动是通过机械部件之间的互动来传递动力、扭矩和运动的一种方法。
它的测试实验误差分析主要包括以下几方面:
1. 传动效率误差:机械传动过程中会存在一定的能量损失,从而导致传动效率下降。
这种误差可以通过统计方法进行分析,包括实测传动效率与理论传动效率的比较和误差分析等。
2. 接触应力误差:机械传动部件之间存在接触应力,容易引起接触疲劳和损坏。
为了减小接触应力误差,可以采用优良的材料、表面处理和润滑等方法。
3. 转矩误差:机械传动过程中会因为部件的轴向力或地面不平整等原因导致转矩误差。
通过自校验的方法和精确的仪器测试可以减小这种误差。
4. 齿间偏差误差:机械传动部件的齿与齿之间会存在轻微的偏差,这会导致噪声、振动和传动误差。
为了减小齿间偏差误差,可以选择精度更高的齿轮、采用优质的加工技术以及进行精细的配合和校正等方法。
总体上,机械传动及其测试实验误差分析需要根据实际情况进行综合分析,加强质量控制,提高技术和管理水平,以确保机械传动的安全、可靠和高效。
关于齿轮滚齿误差产生的种类及原因分析

角左 右 对称 ,检 测 出的 齿形 图如 图: { 叶 的l 、2 .【 J j 1 是 刀 刃u的
图2
压 力 角 存在 误 差 ;如 果 左 右不 对 称 .检 洲 出 的齿 形 图 像 l 冬 j : { 中 的 1 、2 ,但 齿形 的方 向 是 平 行 的 .9 1 I J 是 刀 县 刀 口的 压 力 角干 ¨ 机I 术
其 检 测 出的 齿 形 图 的 形状 也 不 同 若 是 l 刳s _ 中的 齿 形 } l l l 线 变 成
s 形 ,则 是加 工 中 刀具和 工 件装 夹 部存在 误差
2 . 2形误 差 产 生的 原 因
图2 中1 、2 主 要是 刀具 的压 力角 偏差 较 大
如果 刀具 的压 力
3 4 ;
I 恤
2 O 1 6 年・ 第1 2 期
在 齿轮 制造工 艺 中.保证齿
轮 齿 部 精 度 的 方 法 有 挤 齿 、 滚
齿 、剃 齿 、磨 齿 、珩 齿 、 研齿 等。一般 小模数 齿轮 只能通过滚 齿 的方 法达 到齿 轮精 度要求 在 滚齿过 程 中,由于存在 刀具 、机
刀刃在切削工件时有时有 多切 、有
时有 少 切 .导 致 实 际 齿 形 从 齿 根到
齿顶一段 低于标准渐开线 .一段 高 于标 准渐 开线 ( 见图 3 中3 )。
技 术 创 新
图5 主 要 是 工件 孔 中心 与 工作 台 刚转 中心 不 重合 ,可 通过 齿 形 图 、跳 动 和 双 啮 合 检 测 出 。压 力 角偏 大 的 位 置 是 双啮 合和 齿 跳 的 高 点 、压 力 角偏 小 的 位 置是 双 啮 合 和 齿 跳 的 低 点 ;且 双 啮 合 和齿 跳 的 高 、低 点 误 差 大 ( 垂 直 中心 线 的 上 下位 置 齿 形 ),
滚齿机加工原理及误差分析
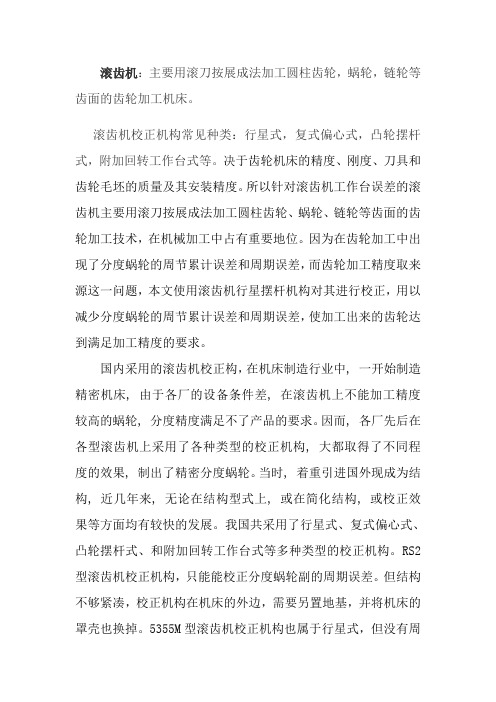
滚齿机:主要用滚刀按展成法加工圆柱齿轮,蜗轮,链轮等齿面的齿轮加工机床。
滚齿机校正机构常见种类:行星式,复式偏心式,凸轮摆杆式,附加回转工作台式等。
决于齿轮机床的精度、刚度、刀具和齿轮毛坯的质量及其安装精度。
所以针对滚齿机工作台误差的滚齿机主要用滚刀按展成法加工圆柱齿轮、蜗轮、链轮等齿面的齿轮加工技术,在机械加工中占有重要地位。
因为在齿轮加工中出现了分度蜗轮的周节累计误差和周期误差,而齿轮加工精度取来源这一问题,本文使用滚齿机行星摆杆机构对其进行校正,用以减少分度蜗轮的周节累计误差和周期误差,使加工出来的齿轮达到满足加工精度的要求。
国内采用的滚齿机校正构,在机床制造行业中, 一开始制造精密机床, 由于各厂的设备条件差, 在滚齿机上不能加工精度较高的蜗轮, 分度精度满足不了产品的要求。
因而, 各厂先后在各型滚齿机上采用了各种类型的校正机构, 大都取得了不同程度的效果, 制出了精密分度蜗轮。
当时, 着重引进国外现成为结构, 近几年来, 无论在结构型式上, 或在简化结构, 或校正效果等方面均有较快的发展。
我国共采用了行星式、复式偏心式、凸轮摆杆式、和附加回转工作台式等多种类型的校正机构。
RS2 型滚齿机校正机构,只能能校正分度蜗轮副的周期误差。
但结构不够紧凑,校正机构在机床的外边,需要另置地基,并将机床的罩壳也换掉。
5355M型滚齿机校正机构也属于行星式,但没有周期误差校正凸轮, 机构是封闭的。
其结构复杂, 构件将近85 种, 使用不方便, 需将机床的双蜗杆传动改成单蜗杆传动, 此时, 必需拆除一根蜗杆。
由于校正机构安装位置不够妥当,使得一部分齿轮外露。
这种结构不太适用于大型滚齿机。
FO-10滚齿机行星式校正机构,该机构有一定的简化, 它省去了四根摆杆和一根长套筒, 结构就比较紧凑一些。
它装在机床分度挂轮箱处, 不需另置地基, 但其构件的种数仍然较多, 达45种, 放大比为0.182毫米每秒。
这种机构的轮廓尺寸较大。
滚齿机加工误差分析

制造 精度 安装 精度 直槽滚刀非 轴向性误差
滚刀齿形 角误差
滚刀轴向 齿距误差
机床蜗杆 副齿距误 差过大 调整 精度 工作台 水平 刀对中 不好 刃磨时 产生导 程误差
滚刀和刀 轴间隙大
滚刀分度圆柱 对内孔轴心线 径向圆跳动误 差
滚刀端面与 孔轴线不垂 直 刀杆径向圆 跳动太大
滚刀和刀轴 间隙大 顶尖 立柱 导轨 制造 精度
滚刀轴向 齿距误差
垫圈两端 面不平行 前面刃磨产生 较大的前角
滚刀容屑槽 槽距误差
安装 精度
滚刀齿形 角误差
滚刀径 向圆跳 动量大
滚刀未 紧而产 生振动 分度蜗轮精 度过低
滚齿加工 误差原因
顶尖 定位
工作台圆形 导轨磨损
中心孔 滚刀磨 损 工作台 蜗杆副 有间隙 滚刀轴 向窜动 分度蜗轮与 工作太圆形 导轨不同轴 调整 技术 夹具定位 面精度 表面粗糙 度差 进给丝杠 有间隙 滚刀轴 径向圆 跳动大 刀架导轨 与刀架间 有间隙 齿坯 偏心 顶尖
提高齿坯基 准面精度
齿距累积 误差超差
滚齿机热变形分析与误差检测新方法
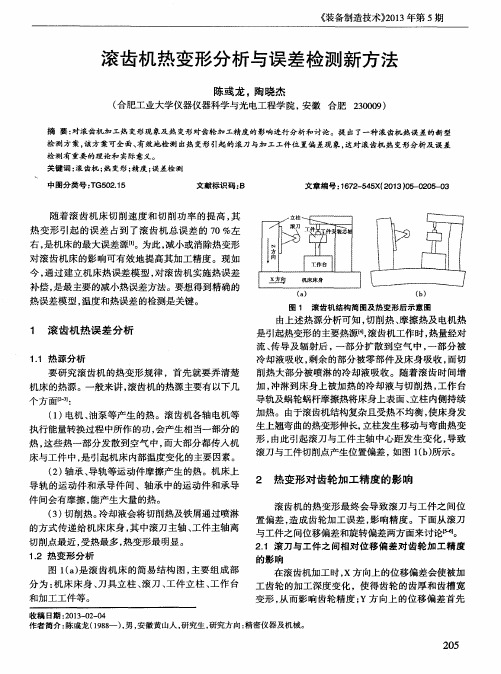
滚齿机热变形分析与误差检测新方法
陈或 龙 , 陶 晓 杰
( 合 肥工 业大 学仪 器仪 器科 学 与光 电工程 学 院 , 安徽 合 肥 2 3 0 0 0 9 )
摘 要: 对滚齿机加 工热变形现 象及热 变形 对齿轮 加工精度的影响进行分析和讨论 。提 出了一种滚齿机 热误 差的新型
刀 对 中 出现 问题 时 , 被 加 工齿 轮会 出现 倒牙 的现象 ,
3 ‘ 、 L 4 ’ 、 L 5 ‘ 、 L 6 t 。 法 向 加工 方 向会 出现偏 差 ,相 当 于刀具 沿 Y方 向有 £
补偿 , 是 最 主要 的 减小热 误 差方 法 。要想 得到 精确 的 热误 差模 型 , 温度 和热误 差 的检测 是关 键 。
( b) ห้องสมุดไป่ตู้
图 1 滚 齿 机 结构 简 图 及热 变 形 后 示 意 图
由上述热源分析可知 , 切削热 、 摩擦热及电机热
1 滚齿机热误 差分析
1 . 1 热 源 分析
可以测量 y 方向上 的位移 , 传感器 6 可 会 使 滚刀 在 Y方 向上 产 生直 线位 移 ,由于这 种 位 置 位移传感器 , 位 于测 试 棒 的正 上 方 , 可测 量 z 方 误 差 的存 在 , 会 影 响 了滚 刀 的对 中 , 如图 2 所 示 。滚 用 固定夹 具 固定 , 向的位移。传感器之间的具体位置分布关 系如 图 3 ( b ) 所示 , 显然在机床未运行之前 , 没有热变形 , £ l = 即 齿 轮 两侧 渐 开 线 齿 形 的对 称 线 不 通 过齿 坯 中心 , : = , , L = L , L 。 在机床运行一段时间后 , 发生热变 影 响齿 轮精 度 ; z方 向的位移 偏 差对 加 工直齿 圆柱 齿 L ’ 、 L ‘ 、 轮 影 响不 大 , 但 当滚 切加 工 斜齿 圆柱 齿轮 时 , 齿 廓沿 形 ,传感器所测得的数据会发生变化 ,变为 。
滚齿机传动链及挂轮误差的精确调整

滚齿机传动链及挂轮误差的精确调整敖小宝(新余高等专科学校工程系,江西新余33803l)摘要:通过分析差动链对挂轮误差的补偿情况,以及存在于两组挂轮上的挂轮误差对工作台计算的位移的影响,说明在用补偿法调整滚齿机时,先设定分齿挂轮,再确定差动挂轮,就能获得较高的调整精度。
关键词:滚齿机;补偿调整;挂轮误差中图分类号:T G6l+2文献标识码:B文章编号:l67l-5276(2005)04-0053-02A precise Ad j ust m ent to t he e rror bet w een t he h an g i n gW heel and t he trans m ission c hai n of t he h obberAO x iao-bao(x i n y u C o lle g e,J x x i n y u33803l,Chi na)Abstract:A nal y zi n g ad j ust m ent to t he error bet w een diff erential chai n and its eff ect on t he dis p lace m ent g au g e caused b y t he error bet w een t w o han g i n g wheels,w e learn t hat a hi g her p recision o f ad j ust m ent can be real-ized,if w e desi g nate first and t hen set t he diff erential han g i n g wheel bef ore m ake an ad j ust m ent o f t he g ear-hobbi n g m achi ne b y com p ensation m et hod.K e y words:g ear-hobbi n g m achi ne;com p ensation and ad j ust m ent;error o f han g i n g wheel按传动比从挂轮表中选择挂轮时,常常存在比位误差,我们把这种误差称为挂轮误差。
滚齿机的加工误差分析与修正
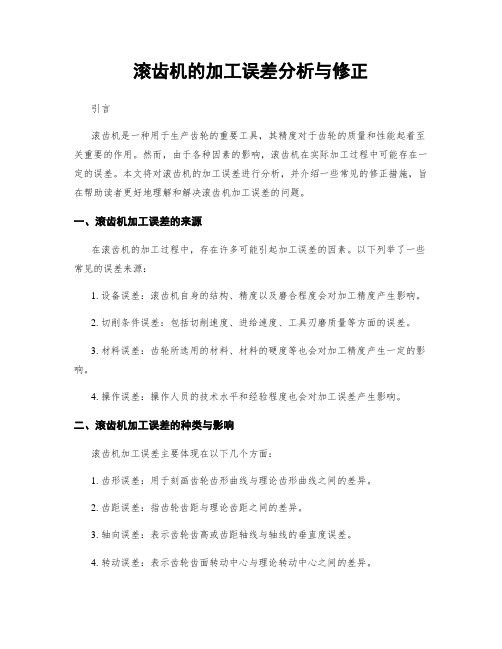
滚齿机的加工误差分析与修正引言滚齿机是一种用于生产齿轮的重要工具,其精度对于齿轮的质量和性能起着至关重要的作用。
然而,由于各种因素的影响,滚齿机在实际加工过程中可能存在一定的误差。
本文将对滚齿机的加工误差进行分析,并介绍一些常见的修正措施,旨在帮助读者更好地理解和解决滚齿机加工误差的问题。
一、滚齿机加工误差的来源在滚齿机的加工过程中,存在许多可能引起加工误差的因素。
以下列举了一些常见的误差来源:1. 设备误差:滚齿机自身的结构、精度以及磨合程度会对加工精度产生影响。
2. 切削条件误差:包括切削速度、进给速度、工具刃磨质量等方面的误差。
3. 材料误差:齿轮所选用的材料、材料的硬度等也会对加工精度产生一定的影响。
4. 操作误差:操作人员的技术水平和经验程度也会对加工误差产生影响。
二、滚齿机加工误差的种类与影响滚齿机加工误差主要体现在以下几个方面:1. 齿形误差:用于刻画齿轮齿形曲线与理论齿形曲线之间的差异。
2. 齿距误差:指齿轮齿距与理论齿距之间的差异。
3. 轴向误差:表示齿轮齿高或齿距轴线与轴线的垂直度误差。
4. 转动误差:表示齿轮齿面转动中心与理论转动中心之间的差异。
这些加工误差在一定程度上会影响齿轮的传动性能和寿命,因此非常值得我们关注和解决。
三、滚齿机加工误差的修正措施为了确保滚齿机加工出的齿轮达到要求的精度,我们可以采取以下一些修正措施:1. 设备维护:定期检查和维护滚齿机的机械部件,保证其正常工作状态和精度。
2. 切削条件调整:优化切削参数,如切削速度、进给速度等,以减小加工误差。
3. 工具选择与刃磨:选择合适的切削刀具,并定期对刀具进行质量检查和刃磨操作,确保刀具的几何精度和尺寸精度。
4. 材料选择:选择适当的齿轮材料,材料的硬度、耐磨性等特性应符合实际使用要求。
5. 操作培训:加强操作人员的培训和技术指导,提高其对滚齿机操作技术和知识的掌握程度。
这些修正措施可以辅助我们降低滚齿机加工误差,提高齿轮的加工质量和性能。
齿轮传动链误差分析.doc

齿轮传动链误差分析一传动误差的来源与分类机床内联系传动链产生传动误差后, 将引起执行环节的角速度和线位移误差, 就不能保持精确、恒定的传动比, 而影响传动的准确性和均匀性。
对于刀具和工件间要求有准确的传动比关系的机床应减小传动误差,提高传动精度, 如螺丝车床、螺纹磨床、滚齿机床等。
传动误差主要来源于四个方面。
第一是传动件的布置误差。
在设计传动链时, 由于传动件的位置不合理, 而使传动误差逐级扩大。
第二是传动件的制造误差。
如齿轮、蜗轮的齿形误差、周节偏差、切向一齿综合误差, 蜗杆、丝杠的导程误差以及导程累积误差等。
第三是传动件的装配误差。
如齿轮、蜗轮、蜗杆及丝杠因装配而产生的径向跳动和轴向窜动。
第四是机床的热变形及传动件受交变的切削力、摩擦力和惯性力作用产生的传动误差。
传动误差按其性质分为原发性误差和再生性误差两类。
原发性误差是指传动件布置误差、传动件制造误差、传传动件装配误差。
它是常位性误差, 机床一经制造好就存在着, 如果不人为地设置误差抵消或补偿装置, 此误差是不会消除的。
再生性误差是指机床在动态(工作状态)过程中, 受力、受热后产生的误差。
它是偶然性误差, 如果机床停止工作, 此误差逐渐消除。
相比之下,往往原发性传动误差对内联系传动链的传动精度影响更大。
本文着重讨论原发性误差。
二、传动误差的分析方法通常分析传动误差大小的方法有动态多因素综合测试法和单因素分析法两种。
动态多因素综合测试法是在机床动态下, 通过仪器实测出某些选定参数的大小,然后进行综合分析处理, 得到传动误差的定量位。
单因素分析法可以在静态或设计机床传动系统时对传动件布置误差、传动件制造误差, 进行定量的分析, 比较不同传动件如齿轮副、蜗轮副、螺母、丝杠等、传动件处于不同位置或传动件不同精度等级时传动误差的大小, 进而合理、正确的设计传动链, 以减少原发性误差位, 提高内联系传动链的精度。
三、单因素分析法的基本原理(1)分析对象由于在内联系传动链中,其主要传动件为齿轮副, 常选择齿轮副的布置制造误差为分析的对象。
滚齿误差产生原因及其消除方法(精)

4)正确选用切削用量,选用切削性能良好的切削液,充分冷却。
12
啃齿
1)刀架立柱导轨太松或太紧
2)液压不稳定。
3)刀架斜齿轮啮合间隙大。
1)调整立柱导轨塞铁松紧
2)保持油路畅通、油压稳定。
3)刀架斜齿轮若磨损,因立即更换。
13
振纹
1)机床内部某传动环节的间隙过大。
2)工件与刀具的装夹刚性不够。
4)改进齿坯或夹具设计,正确夹紧。
11
撕裂
1)齿坯材质不均匀。
2)齿坯热处理方法不当。
3)滚刀用钝,不锋利。
4)切削用量选择不当,冷却不良。
1)控制齿坯材料质量。
2)建议采用正火处理:45钢、40Cr—179~217HB,20CrMo、20CrMNTi—175~207HB。
调质处理:45钢、40Cr—24~28HRC
3)消除齿坯安装误差。
4
基圆齿距偏差超差
1)滚刀的轴向齿距误差,齿形误差及前刃面非径向性和非轴向性误差。
2)分度蜗轮副的齿距误差。
3)齿坯安装几何偏心。
4)刀架回转角度不正确。
1)提高滚刀铲磨精度和刃磨精度。
2)修复或更换分度蜗轮副。
3)消除几何偏心。
4)调整角度。
5
齿顶部变肥,
左右齿廓对称
滚刀铲磨时齿形角度小或刃磨时产生较大的正前角,使齿形角变小。
3)滚刀主轴系统轴向圆跳动过大或平面轴承损坏。
1)提高分度蜗轮副的制造精度和安装精度。
2)提高工作台定心锥形导轨副的配合精度。
3)提高滚刀主轴系统轴向精度,更换损坏的平面轴承。
3
齿距偏差
超差
1)滚刀的轴向和径向圆跳动过大。
滚齿误差及原因

滚齿误差及原因分析对策图表王津盛齿距误差 (2)相邻齿距误差大单个齿距误差大整个齿距误差大齿形误差 (5)各齿齿形误差形式一致窜刀后齿形变化左右侧上齿形形状不一致但同侧齿形形状一致差各齿齿形形状不同齿向误差 (12)单侧齿向多切锥度齿向两侧齿廓多切螺线角误差各齿齿向不一致两侧齿向中凹齿向波动齿面单个凹坑走刀纹不均匀台阶齿向四、径向跳动 (24)工件一圈有一次峰值工件一圈有二次峰值五、齿面粗糙度 (26)撕裂振纹单齿面粗糙六、齿厚 (27)每个齿轮之间变化周期变化随时间变化合制加工上下件不一致齿距误差当产生齿距误差时应该如何去分析相邻齿距变动量大时C只是单个齿距存在大的误差D 一圈上所有齿距都存在大的误差齿距误差的类型A、两相邻齿距误差大(采用多头滚刀)两相邻齿距间产生变动量大的原因见表1。
当被加工齿轮的齿数与多头滚刀的头数成倍数时或用多头滚刀进行高速滚削加工时,在用多头滚刀滚齿时会产生这类误差;B、两相邻齿距间变动量大(采用单头滚刀)C、单个齿距变动量大单头滚刀滚削下齿距变动量大的原因见表2。
若是齿廓的两侧左右齿面齿距变动量均大,则有可能是工作台主轴回转精度差。
表2D、全部齿距变动量大图2 齿形误差的形式齿形误差产生齿形误差的缘由如下:a滚刀的齿形误差b、滚刀一转螺旋线齿距累积误差c、滚刀安装偏心d、齿形棱度作为误差出现每个齿上的齿形误差不同D每个齿的齿形不同(当滚削的齿数是多头滚刀头数的倍数关系时)E每个齿的齿形不同(当滚削的齿数与多头滚刀头数不成倍数关系时)A每个齿的齿形相同(a)齿顶抬高(b)齿顶低头B、滚刀窜刀后齿形改变(每个齿的齿形均相同)A、B、C和D具有同样的齿形67777/77%] v窜刀后齿形发生变化表5分类原因说明优先级滚刀精度低a、滚刀精度低b、滚刀切削刃刃磨不正确1滚刀定心精度差a、滚刀定心精度低b、滚刀没有可靠锁紧1滚刀心轴精度低a、滚刀心轴外径磨损b、滚刀心轴径向跳动过大1滚刀主轴回转精度差a、滚刀主轴径跳过大;b、滚刀主轴轴向跳动过大;C、滚刀小支架侧轴承跳动过大2C、每个齿的左右齿廓上的齿形不同(同一齿侧方向上的齿形一致)通常把这种误差考虑为A类,已在前面叙述过。
滚齿误差原因及消除方法
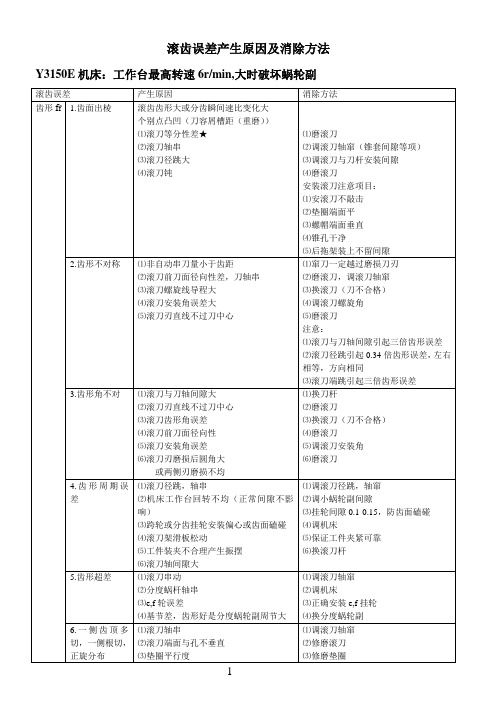
滚齿误差产生原因及消除方法Y3150E机床:工作台最高转速6r/min,大时破坏蜗轮副
2.滚刀杆安装精度:7(8)级,m1-6:里0.01(0.02)外0.015(0.025)端跳0.01(0.02)
滚刀轴肩跳动:里0.01(0.02)端跳0.015(0.025)外0.018(0.03)轴窜0.01(0.015)
⑴滚刀与刀轴间隙引起三倍齿形误差
⑵滚刀径跳引起0.34倍齿形误差,左右相等,方向相同 ⑶滚刀端跳引起三倍齿形误差 刀主轴锥孔跳动0.005
3. 夹具精度7级:端跳0.005-0.01心轴下面0.01-0.015 上部0.015-0.025 顶尖0.015
实际夹具跳动引起误差:△1<
工件
分圆
βB d F 5* △2=Fr/4
齿坯端跳引起偏心e =
工
△D B
*1 D 工为工件定位面直径 4. 滚刀安装角修正:选用滚刀设计分圆偏离(>2°明显),修正安装角△=arcsin
刀顶高
刀h 2a mn
-D
h 刀顶高=α
△△刀sin 2h h W
-±
滚刀螺旋线误差:m2 α20 1°57′扳至1°40′,△ff =0.006 滚刀前刀面等分0.1引起△ff =0.006 滚刀安装偏心0.03引起△ff =0.01 滚刀杆轴窜1:1引起△ff 滚刀杆径跳1:0.33引起△ff
所以⑴滚刀与刀杆间隙0.02-0.03 ff 难达8级 ⑵综合检验不反映滚刀歪斜引起ff (中凹),故加检Fw ⑶刀磨损0.25-0.3窜刀一 个齿距。
齿轮传动误差报告

齿轮传动误差报告1. 引言在机械工程中,齿轮传动广泛应用于各种机械设备中。
然而,由于制造、安装等因素的影响,齿轮传动可能会产生一定的误差。
本报告旨在对齿轮传动误差进行分析和评估,并提出相关的解决方法。
2. 齿轮传动误差的定义和分类齿轮传动误差是指实际传动速比与理论传动速比之间的差异。
根据误差的来源,齿轮传动误差可分为制造误差、安装误差和运行误差。
2.1 制造误差制造误差主要是由于齿轮制造过程中的精度限制导致的误差。
制造误差包括齿轮的模数误差、齿数误差、齿面形状误差等。
2.2 安装误差安装误差主要是由于齿轮安装时的不精确或不恰当导致的误差。
安装误差包括齿轮的定心误差、齿轮轴线误差等。
2.3 运行误差运行误差主要是由于齿轮传动在运行过程中受到外界因素的影响导致的误差。
运行误差包括齿轮的磨损误差、齿轮轴向移动误差等。
3. 齿轮传动误差的影响齿轮传动误差会对机械设备的工作性能和寿命产生一定的影响。
3.1 工作性能影响齿轮传动误差会引起传动系统的振动和噪声,降低传动效率,影响传动的精度和稳定性。
3.2 寿命影响齿轮传动误差会加速齿面磨损,导致齿轮传动的寿命缩短。
4. 齿轮传动误差的测试和评估方法为了准确评估齿轮传动误差,可以采用以下测试和评估方法:4.1 测试方法常用的测试方法包括齿轮测量仪、滚动轴承测力仪、干涉法等。
这些测试方法可以获取齿轮传动的实际传动速比、齿面形状、轴向位移等数据。
4.2 评估方法基于测试数据,可以采用误差分析法、统计分析法等方法对齿轮传动误差进行评估。
这些方法可以对误差进行定量分析和定性分析,评估误差的大小和对传动性能的影响程度。
5. 解决齿轮传动误差的方法为了降低齿轮传动误差,可以采取以下方法:5.1 制造控制通过优化齿轮制造过程,控制齿轮的模数、齿数等参数,减小制造误差。
5.2 安装调整在齿轮安装过程中,加强定心和校正,减小安装误差。
5.3 优化润滑合理选择润滑剂,并定期添加和更换,减小运行误差。
机床传动误差测量方法

机床传动误差测量方法1.引言机床的传动误差是指在机床传动链的输入轴驱动完全准确且为刚性的条件下,其输出轴的实际位移与理论位移之差。
机床上实现工件表面成形所需复合运动的传动链——“内联系”传动链的两末端执行元件之间必须始终严格保持符合给定要求的运动关系。
传动链的传动精度是指其传递运动的准确程度,可用传动误差来衡量。
由于机床实际存在传动链误差,导致工件表面成形运动轨迹存在误差,最终反映到被加工工件上即引起成形表面的形状误差等。
由于机床传动链主要由齿轮副、蜗轮蜗杆副、螺纹副等组成,因此传动链误差主要来源于这些传动元件的加工精度及安装精度。
从运动学角度来讲,一切引起瞬时传动比偏离给定传动要求的因素均是传动链误差的来源。
对机床传动误差的测量是对传动误差进行有效补偿的前提,因此机床传动误差的精密测量一直是机械传动技术的一项重要研究课题。
机床传动误差的基本测量方法是在机床的相关部位安装传感器,借助于采用机、光、电原理的测量仪器并应用误差评定理论对机床传动系统各环节的误差进行测量、分析及调整,从而找出误差产生的原因及变化规律。
2.传感器的选用根据传动链末端元件的运动性质正确、合理地选用、安装传感器是准确测量传动链运动精度的必要条件。
根据工作原理,机床传动误差测量常用传感器可分为以下几类:(1)光栅传感器光栅传感器的最大优点是信号处理方式简单,使用方便,测量精度高(国外著名厂家如德国Heidenhain、西班牙Fagor等公司制造的光栅传感器精度可达1μm/m);缺点是光栅尺价格较昂贵,对工作环境要求较高,玻璃光栅尺的线胀系数与机床不一致,易造成测量误差。
(2)激光传感器激光传感器(包括单频和双频激光)具有较高的测量精度,但测量成本也较高,对环境条件变化(如温度、气流、振动等)较敏感,在生产现场使用时必须采取措施保证测量的稳定性和可靠性。
(3)磁栅传感器磁栅尺可分为线状(有效测量长度3m)和带状(有效测量长度可达30m)两种型式,其优点是制造成本较低,安装使用方便,线胀系数与机床相同;缺点是测量精度低于光栅尺,由于磁信号强度随使用时间而不断减弱,因此需要重新录磁,给使用带来不便。
齿形齿向误差分析
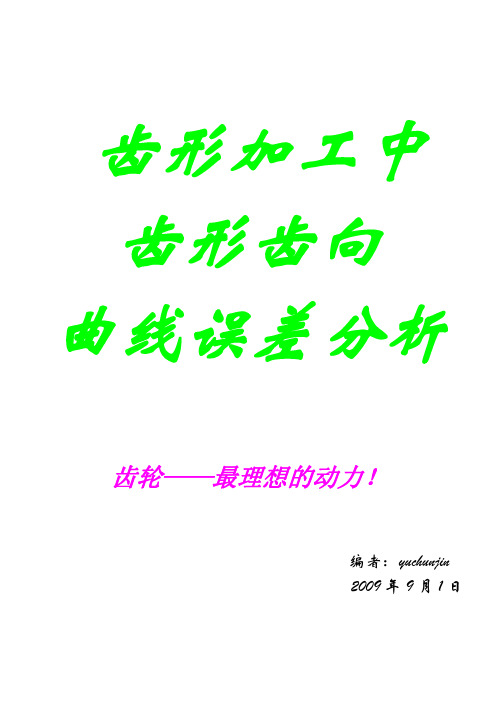
齿形误差曲线分析
一、齿形误差曲线的形状 当齿形为理论渐开线时,仪器所记录的曲线为一条直线。 1、无齿形误差的曲线为理论渐开线曲,为一条直线,如《图 一》所示,当设计齿形为鼓形齿时,而无齿形误差的曲线为中 凸,如《图二》所示。
《图一》
《图二》
2、有压力角误差的齿形误差曲线:曲线倾斜,齿顶比齿
根高,压力角误差为负,基圆误差为负,见《图三》所示目视
《图七》
7、齿向形状误差是由滚齿机分度蜗轮副的周期误差和进
给丝杆的轴向窜动产生的。
第八页
a
b
《图五》
5、由径向和切向误差同时影响的曲线:两种误差同时出
现时,而且大小相等,则会在一侧齿面上两种误差相互抵消,
而在另一侧齿面上两种误差互相加强,因而就出现如《图六》
所示一齿面正确,一齿面有齿齿向误差。如《图七》所示。是由于齿坯基准 端面的端面圆跳动引起的,是由齿坯轴线对齿轮机床的歪斜而 产生的,这一误差对齿的纵向接触具有很大的影响。当一组齿 向曲线同时存在锥度有正有负时,全齿范围内同时存在一端齿 有厚有薄,也称齿向有正“八”字或倒“八”字,造成此现象 的主要原因是刀架导轨镶条有松动、磨损或调整不对称造成 的。
《图二》
2、同一侧四根曲线向同一方向倾斜,而另一侧四根曲线 也向同一方向倾斜,且倾斜程度大约一至,如《图三》所示。 这种形状是存在螺旋线斜率误差,即螺旋线误差,主要有以下 两个方面引起的:a、滚斜齿时,差动挂轮精度不够;b、刀架 导轨相对于工作台回转轴线在切向的平行度误差的影响。【即 刀架导轨与工件轴线的切向不平行】
窜动和径向跳动,也同样会使滚刀的刀齿产生“空切”或“过
切”引起齿轮的齿面出棱。
第三页
《图八》
4、同一侧四根曲线一至,但曲线弯弯曲曲,走向与基准 线平行,如《图九》所示。这种曲线我们称之为齿形形状误差 曲线。齿形形状误差又分两种:一种为周期误差,如《图九》 所示,其特点为齿面凸凹不平,一般齿形形状误差在 0.01~0.05mm 之间,甚至可达到 0.08mm,产生周期误差的主要 原因有:滚刀安装后,滚刀径向跳动和端面跳动过大,机床传 动链短周期误差的影响,如机床分齿挂轮的运动误差和分度蜗 杆的径向、轴向跳动引起分度蜗轮的小周期转角误差,这些误 差最终在齿形上形成周期性的波形误差。
滚齿误差原因及消除方法
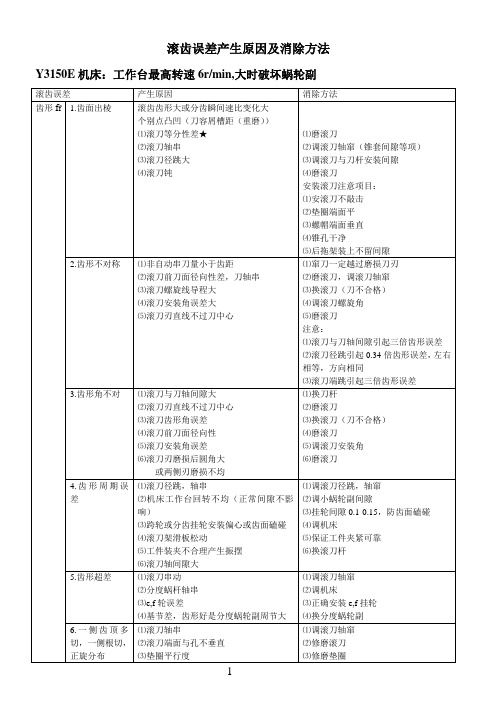
滚齿误差产生原因及消除方法Y3150E机床:工作台最高转速6r/min,大时破坏蜗轮副
2.滚刀杆安装精度:7(8)级,m1-6:里0.01(0.02)外0.015(0.025)端跳0.01(0.02)
滚刀轴肩跳动:里0.01(0.02)端跳0.015(0.025)外0.018(0.03)轴窜0.01(0.015)
⑴滚刀与刀轴间隙引起三倍齿形误差
⑵滚刀径跳引起0.34倍齿形误差,左右相等,方向相同 ⑶滚刀端跳引起三倍齿形误差 刀主轴锥孔跳动0.005
3. 夹具精度7级:端跳0.005-0.01心轴下面0.01-0.015 上部0.015-0.025 顶尖0.015
实际夹具跳动引起误差:△1<
工件
分圆
βB d F 5* △2=Fr/4
齿坯端跳引起偏心e =
工
△D B
*1 D 工为工件定位面直径 4. 滚刀安装角修正:选用滚刀设计分圆偏离(>2°明显),修正安装角△=arcsin
刀顶高
刀h 2a mn
-D
h 刀顶高=α
△△刀sin 2h h W
-±
滚刀螺旋线误差:m2 α20 1°57′扳至1°40′,△ff =0.006 滚刀前刀面等分0.1引起△ff =0.006 滚刀安装偏心0.03引起△ff =0.01 滚刀杆轴窜1:1引起△ff 滚刀杆径跳1:0.33引起△ff
所以⑴滚刀与刀杆间隙0.02-0.03 ff 难达8级 ⑵综合检验不反映滚刀歪斜引起ff (中凹),故加检Fw ⑶刀磨损0.25-0.3窜刀一 个齿距。
齿轮的误差和分析报告

齿轮误差及其分析第一节:渐开线圆柱齿轮精度和检测对于齿轮精度,主要建立了下列几个方面的评定指标:一.运动精度:评定齿轮的运动精度,可采用下列指标:1.切向综合总偏差F i′:定义:被测齿轮与理想精确的测量齿轮单面啮合时在被测齿轮一转,(实际转角与公称转角之差的总幅度值)被测齿轮的实际转角与理论转角的最大差值。
切向综合总偏差F i′。
(它反映了齿轮的几何偏心、运动偏心和基节偏差、齿形误差等综合结果。
)Δ2.齿距累积总偏差F p,齿距累积偏差F pk。
定义:齿轮同侧齿面任意弧段(k=1或k=z)的最大齿距累积偏差。
它表现为齿距累积偏差曲线的总幅值。
——齿距累积总偏差。
在分度圆上,k个齿距的实际弧长与公称弧长之差的最大绝对值,称k个齿距累积误差ΔF pk。
k为2到小于Z/2的正数。
这两个误差定义虽然都是在分度圆上,但实际测量可在齿高中部进行。
这项指标主要反映齿轮的几何偏心、运动偏心。
用ΔF p 评定不如ΔF i′全面。
因为ΔF i是在连续切向综合误差曲线上取得的,而ΔF p不是连续的,它是折线。
ΔF i′= ΔF p + Δf f测量方法:一般用相对法,在齿轮测量机上测量。
3.齿圈径向跳动ΔF r与公法线长度变动ΔF w:ΔF r定义:在齿轮一转围,测头在齿槽,于齿高中部双面接触,测头相对于齿轮轴线的最大变动量。
它只反映齿轮的几何偏心,不能反映其运动偏心。
(用径跳仪测量检测。
)由于齿圈径跳ΔF r 只反映齿轮的几何偏心,不能反映其运动偏心。
因此要增加另一项指标。
公法线长度变动ΔF w。
ΔF w定义:在齿轮一周围,实际公法线长度最大值与最小值之差。
ΔF w=W max-W min测量公法线长度实际是测量基圆弧长,它反映齿轮的运动偏心。
测量方法:用公法线千分尺测量。
4.径向综合误差ΔF i″和公法线长度变动ΔF w:齿轮的几何偏心还可以用径向综合误差这一指标来评定。
ΔF i″定义:被测齿轮与理想精确的测量齿轮双面啮合时,在被测齿轮一转,双啮中心距的最大变动量。
- 1、下载文档前请自行甄别文档内容的完整性,平台不提供额外的编辑、内容补充、找答案等附加服务。
- 2、"仅部分预览"的文档,不可在线预览部分如存在完整性等问题,可反馈申请退款(可完整预览的文档不适用该条件!)。
- 3、如文档侵犯您的权益,请联系客服反馈,我们会尽快为您处理(人工客服工作时间:9:00-18:30)。
数程序曰计数程序以圆光栅-C 产生的 TTL 信号的下
降沿为触发信号袁 将 2 路编码信号的计数值写入
FIFO 结构袁主程序读取 FIFO 中的计数值计算再该点
处的传动链误差遥
1.2 测量误差分析
圆光栅的刻线在制造过程中无法保证完全均
匀袁 且在安装过程中刻线与读数头之间存在相对位
姿误差遥 因此袁圆光栅测量角位移时存在与读数头位
置相关的测量误差误差遥 圆光栅误差对传动误差的
作用为院
吟越
em i
渊 2冤
式中吟为圆光栅测量误差对传动链误差测量值
的贡献量曰i 为圆光栅与工作台转速比曰em 为圆光栅 误差遥
滚刀轴的圆光栅与工作台转速比通常较高袁而
工作台的圆光栅与工作台转速比为 1遥 因此袁传动链 误差测量系统的误差主要由工作台编码器引起袁而 滚刀轴的圆光栅的误差的影响可忽略不计遥
滚刀轴转角曰琢 为工作台与滚刀转速比遥
如图 1 所示袁 工作台与滚刀轴末端分别安装高
精度圆光栅袁同步采集滚刀轴和工作台的角位置袁计
算传动链误差遥 主要设备详细参数如表 1 所示遥
滚刀轴
圆光栅-B
滚
齿机Βιβλιοθήκη 圆光栅-C工作台细分盒-B 细分盒-C
计算机 数字信号 渊 PXIe-1071冤 采集卡 渊 PXI-7842R冤
基于编码器和圆光栅广泛用于滚齿机床传动链 误差的测量[3-6]袁离散角度采样的方法适合于使用编 码器测量旋转机械中多路信号的情况[7]曰Palermo 等 人[8]讨论了使用低成本数字编码器来测量高速传动 系统的方法曰Zhou 等人[9]和 Zhao 等人[10-11]利用机床内 置编码器采集机床传动链的传动误差信号袁 用于确 定传动链中的故障源曰Brecher 等人[12]测量齿轮组传 动误差和噪声情况以研究齿轮组的传动误差与齿轮 箱在其应用中的噪声特性之间的相关性曰彭等人[13]和 李等人[14]利用 FMT 系统对滚齿机进行传动误差测 量袁并通过修正传动齿轮遥 通过传动链误差准确分析 机床传动链性能以及传动链误差精确补偿的前提为 传动链误差的精确测量遥
本文考虑圆光栅的制造误差和装配误差袁 分析 传动链误差测量平台的测量误差曰 基于测量误差相 位特性提出了一种新的修正测量系统误差的方法袁 通过两次不同安装位置下的测量数据计算并消除测 量误差曰基于 YDA1132 型滚齿机的实验表明该方法 能准确计算并消除测量误差袁同时流程简单成本低遥
1 测量误差分析及辨识原理
刻线沿圆光栅钢毂周向分布袁 读数头检测扫过
中图分类号:TG61.2
文献标识码:A
文章编号:1672-545X(2019)04-0001-05
0 引言
滚齿加工是一种生产效率高尧 应用广的齿形加 工方法[1]遥 滚刀轴尧电子齿轮箱和工作台构成滚齿机 传动链袁是滚齿机的关键核心部件遥 滚齿机传动链误 差不仅会引起工件齿轮的螺距误差尧 齿廓误差和工 件螺旋误差袁还会诱导滚齿机的振动和噪声[2]遥 准确 测量传动链误差袁 对通过传动链误差准确分析机床 传动链性能以及传动链误差精确补偿具有十分重要 的意义遥
为保证测量的精确性袁Du 等人 研 [15] 究了包含齿 轮的驱动系统的编码器测量误差袁 并提出一种减少 编码器误差的方法曰Li 等[16]基于阿贝原则分析了转台 倾斜运动误差和径向运动误差引起的圆光栅角位移 测量误差及其对转台定位精度的影响规律曰Lopez 等 人[17]分析了振动对和读数头的摆动引起的编码器测 量误差袁 并基于对恶化的测量信号的利萨如图的拟 合技术提高传感器精度遥 除上述方法外袁雷尼绍海德 汉等厂商推出了多读数头的圆光栅以消除测量误 差袁但成本高昂且安装不便遥 针对基于单读数头圆光 栅的传动链误差测量系统的测量误差分析及消除技 术亟待研究遥
1.1 传动链误差测量方案 滚齿机传动链包括滚刀轴电机尧滚刀箱尧电子齿
收稿日期:2019-01-29 基金项目:国家自然科学基金资助项目渊 51635003冤 曰重点产业共性关键技术创新专项项目渊 cstc2017zdcy-zdzxX0005冤 曰重庆市博士
后科研项目特别资助项目渊 Xm2017044冤 作者简介:龙 谭渊 1994-冤 袁男袁湖南人袁硕士研究生袁主要从事滚齿机床精度研究遥 通讯作者:王时龙渊 1966-冤 袁男袁湖南人袁教授袁博士生导师袁研究方向院机电一体化遥
主程序 计数 程序
图 1 传动链误差测量平台
表 1 主要实验设备参数表
设备 圆光栅-C 细分盒-C 圆光栅-B 细分盒-B
参数 23600 线 细分 50 倍 20000 线 细分 25 倍
为明确传动链误差沿工作台的空间分布情况袁
首先测量圆光栅参考点相对机床工作台原点的相位
差袁 并从第一次检测到圆光栅的参考点开始进入计
1
Equipment Manufacturing Technology No.04袁2019
轮箱尧工作台电机以及工作台传动装置遥 传动链误差
即为由传动副传动误差和伺服控制误差引起的工作
台和滚刀轴间的相对运动误差袁如式渊 1冤 所示遥
eT = 渍C - 琢渍B
渊 1冤
式中袁eT 为传动链误差曰渍C 为工作台转角曰渍B 为
叶 装备制造技术曳 2019 年第 04 期
检测与测试
滚齿机传动链误差测量误差分析及辨识
龙 谭 1,王时龙 1,任 磊 1,杨 勇 2
渊 1.重庆大学袁机械传动国家重点实验室袁重庆 400044曰2.重庆机床集团有限责任公司袁重庆 400055冤
摘 要:滚齿机传动链误差检测平台的测量误差直接影响滚齿机传动链误差的测量结果袁导致难以精确补偿滚齿机传动 链误差和准确诊断滚齿机传动链故障遥为提高滚齿机传动链误差测量准确性袁消除圆光栅的制造和安装误差对测量结果 的干扰袁首先分析了由圆光栅制造及装配误差引起的测量误差对滚齿机传动链误差测量的影响袁然后基于不同安装位置 下的测量误差相位特征和离散傅里叶逆变换方法辨识测量误差袁该方法在 Y D A 31 32 型滚齿机上进行了实验验证遥 结果 表明袁该方法能准确辨识检测平台的测量误差袁消除了对传动链误差测量结果的干扰袁提高了测量准确性袁具有低成本尧 高可行性的优点遥 关键词:滚齿机曰传动链曰传动链误差曰测量误差曰误差补偿