过程失效模式及后果分析(PFMEA):制定项目风险管理计划的有效工具
PFMEA过程失效模式及后果分析
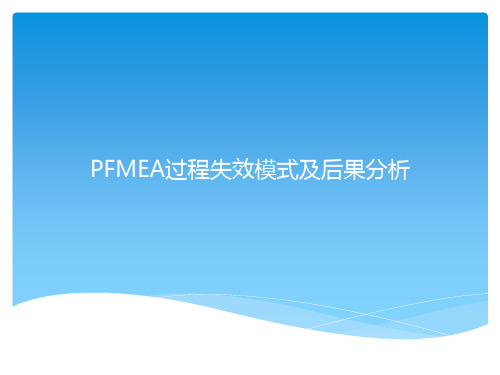
下列可以帮助确定是否将现有的PFMEA纳入最终范围: 新开发的产品和过程; 操作条件的变化; 要求变化(法律/法规,标准规范,客户,最新状态) 制造经验、场内问题,或现场问题/保修; 可能导致危险的过程失效; 人体工程学; 持续改进。
过程FMEA步骤一:规划和准备
PFMEA定义范围的目的---清晰定义过程范围: 识别项目----哪些过程需要分析; 项目计划----培训团队成员、创建项目时间; 定义分析界限---包括什么,不包括什么; 确定能使用的相关经验教训和决策,例如:最佳实践、标准、防错等。
示例:“磨削滑动油封”过程的功能结构
工作坊:步骤三-功能分析(绿色+蓝色笔)
1.过程项目、过程步骤、作业要素具有何种功能和要求? 填入结构树中各项功能和要求: 功能 +要求=绿色字体+蓝色字体 将各项功能填写 在过程项目、过程步骤及作业要素的下面。 备注:“发生什么?”如何从左到右实现产品/过程要求-(过程项目-过程步骤-作业
过程FMEA步骤二:结构分析
结构树按层次排列系统元素,并通过结构连接说明关联关系。这个形象化的结 构考虑了过程项目、过程步骤和过程工作要素之间的关系,在后面,将对他们 分别添加功能模块和失效模块。
对于过程来,查验的最基础层次—变差来源(Sources of Variation),是传统的 “4M(人Man、机Machine、料Material、环Milieu)”,即设备、工装、夹具、 刀/模具的硬件基本参数、动态的控制参数、辅助系统的参数、环境特性、影 响本序的前工序的加工余量、定位点的尺寸及形位公差等。
过程FMEA步骤四:失效分析
PFMEA失效分析的目的是: 1.为过程项目、过程步骤和作业要素的每个功能建立失效(一个或多个失效); 2.识别可能发生的失效/原因,并分配给作业要素和过程步骤; 3.失效关系的可视化(影响-模式-原因,基于功能网的失效网络); 4.通过链接失效链中的失效来创建失效结构; 5.是FMEA表格中记录的失效的基础; 6.失效分析对过程中的每个元素/过程步骤进行了失效描述(结构分析/步骤2和 功能分析/步骤3) 可能的失效从功能/任务推断出来,如设备特定目标状态的不合格、不能充分 完成工作任务、非预期或不必要的活动等; 对失效的描述必须要清晰。不符合、不OK、失效、中断及诸如此类的描述并不 不足以帮助我们去找到失效。 通常,某一功能可以有多种失效。
过程失效模式及后果分析(PFMEA)

XXX汽车技术股份有限公司潜在失效模式及影响分析 PFMEA螺纹孔内无铝屑,机加工面边缘毛刺清理干净;螺纹孔内有铝屑,机加工面边缘未清理干净影响客户装配,客户抱怨61.丝锥损坏2.夹具松动3.切削液未正确喷淋,铝屑未吹掉31.首检记录表2.巡检记录表354None5XΦ0.341±0.01深0.55(英制)尺寸超差 1.毛坯不合格或尺寸变化大4XΦ0.232±0.01深0.5(英制)尺寸超差 2.夹具松动;3.程序错误2XΦ0.232±0.01深0.5(英制)尺寸超差 4.装夹失误2X4.34±0.02(英制)尺寸超差 1.毛坯不合格或尺寸变化大27.19±0.02(英制)尺寸超差 2.夹具松动;3.程序错误2X7.05±0.02(英制)尺寸超差 4.装夹失误2X11.72±0.02(英制)尺寸超差1.毛坯不合格或尺寸变化大1.25±0.02(英制)尺寸超差2.夹具松动;3.程序错误2.38±0.02(英制)尺寸超差 4.装夹失误1.56±0.02(英制)尺寸超差 1.毛坯不合格或尺寸变化大2.44±0.02(英制)尺寸超差 2.夹具松动;3.程序错误8XΦ0.118±0.01(英制)尺寸超差 4.装夹失误尺寸超差1.毛坯不合格或尺寸变化大2X45°±0.5°尺寸超差2.夹具松动;None3影响装配和功能7631.首检记录表2.巡检记录表3★3影响装配和功能7★31.首检记录表2.巡检记录表363NoneNone63影响装配和功能7★31.首检记录表2.巡检记录表3影响装配和功能7★31.首检记录表2.巡检记录表None影响装配和功能7★31.首检记录表2.巡检记录表36363None。
注塑过程PFMEA失效模式及后果分析
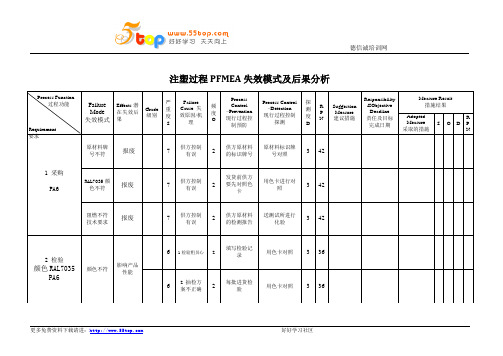
德信诚培训网更多免费资料下载请进: 好好学习社区注塑过程PFMEA 失效模式及后果分析Failure Mode 失效模式 Effects 潜在失效后果Grade 级别严重度SFailure Cause 失效原因/机理频度OProcess Control –Prevention 现行过程控制预防Process Control –Detection 现行过程控制探测探测度DR P N Suggestion Measure 建议措施Responsibility &Objective Deadline 责任及目标 完成日期Measure Result 措施结果Adopted Measure 采取的措施S O D RPN1 采购PA6原材料牌号不符报废 7供方控制有误2供方原材料的标识牌号 原材料标识牌号对照3 42RAL7035颜色不符报废 7供方控制有误2发货前供方要先对照色卡用色卡进行对照3 42阻燃不符技术要求报废 7供方控制有误2供方原材料的检测报告 送测试所进行化验3 422 检验颜色RAL7035PA6颜色不符影响产品性能61检验粗员心 2填写检验记录用色卡对照 3 3662 抽检方案不正确2每批进货检验用色卡对照 3 36Process Function过程功能Requirement 要求。
PFMEA过程失效模式及后果分析

PFMEA过程失效模式及后果分析PFMEA(Process Failure Mode and Effects Analysis)过程失效模式及后果分析是一种常用的质量管理工具,用于评估和改进产品制造过程中的潜在问题和风险。
它旨在预测和预防可能导致产品失效的过程步骤。
1.确定过程步骤:首先,识别和定义产品制造过程中的每个关键步骤,包括原材料采购、加工、装配、测试等。
2.确定失效模式:对于每个过程步骤,识别可能导致失效的模式。
失效模式可以是设备故障、人为错误、材料质量问题等。
3.评估失效后果:对于每个失效模式,评估其可能导致的后果和影响。
后果可以涉及到产品质量问题、安全风险、客户满意度等。
4.定义风险优先级:根据失效模式的严重性、发生频率和检测能力,为每个失效模式分配一个风险优先级。
这可以帮助制定合理的风险控制策略。
5.制定改进计划:对于评估出的高优先级失效模式,制定相应的改进计划和控制措施。
这可能包括优化生产工艺、提供培训和教育、改进设备维护等。
6.实施和监控措施:执行改进计划,并监控其有效性。
定期对PFMEA进行更新,以反映过程改进和新的风险评估。
通过实施PFMEA,可以有效地识别和消除潜在的制造过程问题,并降低产品质量问题的风险。
下面以汽车制造业为例,具体分析PFMEA的应用。
在汽车制造过程中,每个制造步骤都可能存在潜在的失效模式。
例如,原材料采购环节可能存在材料质量问题的风险,加工环节可能存在操作错误或设备故障的风险,装配环节可能存在组装错误或安装不良的风险,测试环节可能存在测试不准确或设备故障的风险。
针对这些潜在问题,可以使用PFMEA来识别并评估其风险。
例如,在加工环节,识别可能的失效模式可能包括不正确的参数设置、设备故障、操作错误等。
然后,评估这些失效模式可能导致的后果和影响,如产品偏差、生产延误、设备故障等。
根据评估结果,确定失效模式的风险优先级,以便制定相应的改进计划和控制措施。
例如,对于评估为高风险的加工失效模式,可以采取以下改进措施:加强对操作员的培训和教育,确保他们正确操作设备和设置参数;增加设备维护和保养频率,以减少设备故障的风险;实施过程监控和自动化控制,以确保稳定的生产环境。
过程失效模式及后果分析管理办法

过程失效模式及后果分析管理办法过程失效模式及后果分析(Process Failure Modes and Effects Analysis,简称PFMEA),是一种常用于管理过程风险和改进的工具。
PFMEA通过对过程中可能发生的失效模式及其后果进行分析,提前识别出潜在问题,并采取相应措施降低风险。
下面将介绍PFMEA的管理办法。
一、PFMEA的管理目标PFMEA的管理目标是识别和分析过程中的失效模式及其潜在后果,评估失效发生的概率和影响程度,并制定相应的预防控制措施,降低风险。
二、PFMEA的管理步骤1.选择适当的团队成员:PFMEA的分析需要跨越多个职能领域,因此需要选择适当的团队成员,包括具有相关专业知识和经验的人员。
2.确定过程:明确要分析的过程范围和目标,包括过程流程、输入和输出等。
3.识别失效模式:团队成员通过头脑风暴和过程分析,识别可能导致过程失效的因素。
失效模式可以是物理性的、功能性的、行为性的等。
4.评估失效影响程度:对每个失效模式,评估其对过程和最终产品或服务的影响程度,包括安全性、质量、交付时间、成本等方面。
5.确定失效发生的概率:评估每个失效模式发生的概率,包括概率的频率、可能性等。
6.评估现有控制措施:评估当前过程中已存在的控制措施,对失效模式的控制程度,包括检验、测试等。
7.制定改进措施:根据评估结果,确定需要改进的控制措施,包括预防措施和检测措施,以降低失效发生的概率和影响程度。
8.实施改进措施:制定实施改进措施的计划,并跟踪监控改进效果。
9.更新PFMEA:根据实施改进措施的结果,修订和更新PFMEA,并确保团队成员了解改进措施的目标和具体要求。
三、PFMEA的管理原则1.整体团队参与:PFMEA需要全员参与,涉及到的问题通常跨越多个职能领域,需要充分调动团队的智慧和经验。
2.系统性分析:PFMEA需要从系统层面进行分析,识别可能的失效模式和其后果,并考虑多种因素对失效的影响。
PFMEA过程潜在失效模式和后果分析

度、温度和压力
9ⅹ.10.01
安装限值控制器。控制图
显示过程已受控制。
CPK=1.85
1
5
35
最小厚度 的蜡,以延 缓腐蚀
损害
7
因 撞 击 使 喷 2 依 预 防 维 护 程 每小时进行目测检 5
头变形
序维修喷头
查,每班检查一次喷
膜厚度(深度计)和
70
无
范围
7
喷蜡时间不 8
按作业说明书进行 7
392 安装喷蜡定时器
潜在过程失效模式应注意的问题
然而,在准备FMEA时,应假定所接收的零 件/材料是正确的。 当历史数据表明进货零件质量有缺陷时, FMEA小组可做例外处理。 根据零组件、子系统、系统或过程特性,对特 定的作业列出每一个潜在的失效模式。前提是 假设这种失效可能发生,但不一定必然发生。
潜在过程失效模式应注意的问题
或可能在无警告的情况下对(机器或组装) 1
作业员造成危害
0
有警 告的 危害 很高
高
严重度定级很高 。当潜在的失效
模式在有警告的情况下影响到车辆 安全运行和/或涉及不符合政府法 规的情况时。
或可能在有警告的情况下对(机器或组装) 操作员造成危害
9
车辆/系统不能工作(丧失基本功 能)
或100%的产品可能需要报废;或者车辆 /系统在修理部门花1个小时以上来修理
FMEA文件完全按照本手册填写,包含 “措施行动”和新的RPN值。
对一个增值的结果而言, FMEA小组尽 可能提早所花费的时间,是时间最有效 和效率的利用。这是假设措施已依需求 被鉴别,其措施都已实施。
过程FMEA中的“顾客”定义
过程FMEA中“顾客”的定义通常是指 “最终使用者”。然而,顾客也可以是随后 或下游的制造或装配工序,维修工序或政府 法规。
过程失效模式及后果分析-教程
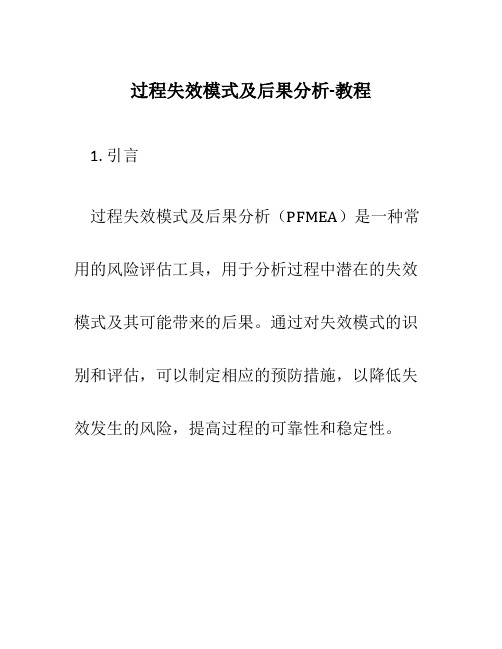
过程失效模式及后果分析-教程1. 引言过程失效模式及后果分析(PFMEA)是一种常用的风险评估工具,用于分析过程中潜在的失效模式及其可能带来的后果。
通过对失效模式的识别和评估,可以制定相应的预防措施,以降低失效发生的风险,提高过程的可靠性和稳定性。
本教程将介绍PFMEA的基本概念、步骤和应用方法,帮助读者了解如何进行过程失效模式及后果分析。
2. PFMEA的基本概念2.1 过程失效模式过程失效模式是指发生在特定过程中的潜在失效形式。
它可以是机械故障、工艺不稳定、材料质量问题等各种各样的问题,可能导致产品或服务无法达到预期的功能要求。
2.2 后果分析后果分析是对失效模式引起的后果进行评估和分析。
它包括两个方面的内容:失效后果的严重性评估和失效后果的概率评估。
严重性评估用于判断失效对产品或服务的影响程度,概率评估用于评估失效产生的频率或概率。
3. PFMEA的步骤PFMEA主要包括以下步骤:3.1 选择分析对象选择需要进行PFMEA分析的过程或系统,确定所要分析的范围和目标。
3.2 建立团队建立一个跨部门的团队,包括相关的设计、生产和质量控制人员。
团队成员应具备相关的知识和经验,以能够准确地分析和评估失效模式及其后果。
3.3 列出过程步骤对所选过程进行详细的步骤分解,将整个过程拆分为多个子过程或操作步骤。
3.4 识别失效模式对每个步骤识别可能存在的失效模式,包括机械失效、材料问题、环境因素等。
3.5 评估失效后果对每个失效模式评估其可能带来的后果,包括严重性和概率评估。
根据经验和数据进行评估,各团队成员提供专业意见。
3.6 优先级排序根据失效后果的严重性和概率进行排序,确定重要性较高的失效模式。
3.7 制定预防措施对于重要性较高的失效模式,制定相应的预防措施,包括改进设计、改变工艺、提高操作规范等。
3.8 实施并跟踪将制定的预防措施实施到实际生产过程中,并定期进行跟踪和评估,以确保措施的有效性和可操作性。
PFMEA过程失效模式与后果分析报告
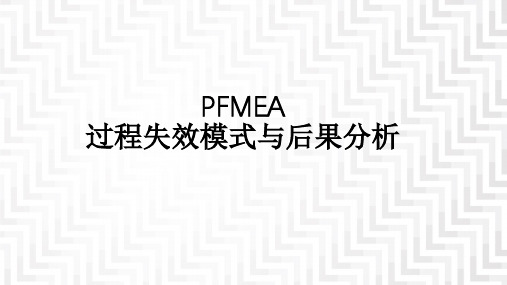
让我们共同进步
知识回顾 Knowledge Review
失效:在规定条件下(环境、操作、时间),不
关键参数
能完成既定功能或产品参数值和不能维持在规定 的上下限之间,以及在工作范围内导致零组件的
失效
规定条件无法达到要求或者规格
ห้องสมุดไป่ตู้
破裂卡死等损坏现象。 严重度(S):指一给定失效模式最严重的影响
严重度(S) 失效模式对后果的影响,越严重越需要通过设计来改善
后果的级别,是单一的FMEA范围内的相对定级 结果。严重度数值的降低只有通过设计更改或重
有些“早知道”是必需的 有些“就不会”是不允许发生的
PFEMA 是对制程中的风险点进行提前识别并预防以致风险降低到最小。 PFEMA 是QCP 的前提之一。 一般PFEMA需要在产品大批量生产前完成, 并在后期逐步更新完善。
PFEMA的用法-关键步骤
确定对象及需 求
识别潜在的失 效模式及后果
S
识别失效原因
探测度(D):指在零部件离开制造工序或装配 之前,利用第二种现行过程控制方法找出失效起 因/机理过程缺陷或后序发生的失效模式的可能性 的评价指标;或者用第三种过程控制方法找出后 序发生的失效模式的可能性的评价指标。 风险优先数(RPN):指严重度数(S)和频度
数(O)及不易探测度数(D)三项数字之乘积。
FMEA的分类
FMEA又根据产品故障可能产生的环节:设计、 制造过程、使用、承包商(供应商)以及服务可 细分为: 1.DFMEA: 设计FMEA
2.PFMFA: 过程FMEA
3.MFMEA:设备FMEA
4.SFMEA: 体系 FEMA
针对系统 及子系统
针对设备和 设备部件
过程失效模式及后果分析PFMEA
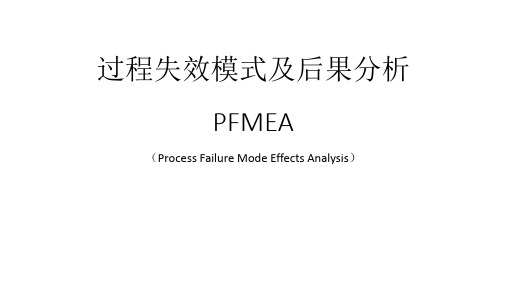
100~500 10~100
1~10
≥1.20
3
≥1.30
2
≥1.67
1
FMEA开发要点
8)当前控制方式
• 当前控制措施包括预防控制(error/mistake proofing or Statistical Process Control)和探测控制(post-process evaluation),“当前措施”应是在本过程或类似过程的中已落实的措施或已证明有效的措施。
Very High: 非常高 Persistent failures 持续失效
High:高 Frequent failures 频繁失效
Suggested PFMEA Occurrence Evaluation Criteria
Likely Failure Rates
以一百万块板里的缺陷计数
Ppk
Ranking
四、FMEA开发要点
下图展示了PFMEA模板。我们今天把理解最容易跑偏的板 块跟大家做一个梳理。
FMEA开发要点
1)功能要求 A 功能要求既包括过程特性和产品特性两大类。 • 过程特性: 过程参数及过程要求,即加工条件和加工参数 • 产品特性:产品规范,如尺寸\性能 B 对于同一个Operation上有多个操作动作的(an operation for a multistation machine or sequential process in one piece of equipment), 不管是人工操作还是极其操作,需要细化到每一个操作,比如:
Criteria: Severity of Effect 标准:后果严重性
This ranking results when a potential failure mode results in a final customer and/or a manufacturing/assembly plant defect. The final customer should always be considered first. If both occur, use the higher of the two severities.
过程失效模式及后果分析
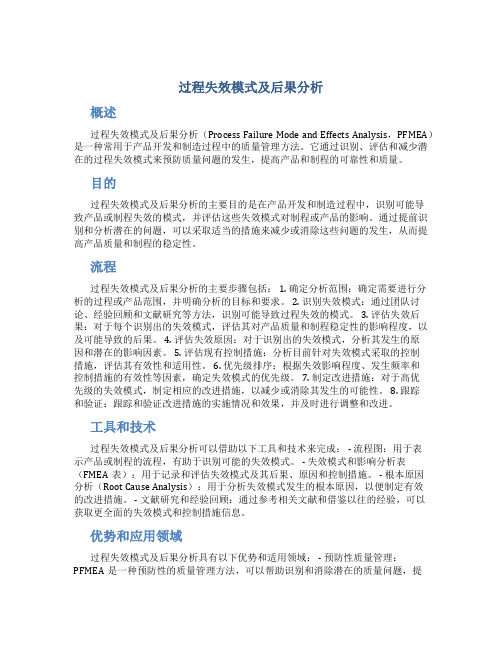
过程失效模式及后果分析概述过程失效模式及后果分析(Process Failure Mode and Effects Analysis,PFMEA)是一种常用于产品开发和制造过程中的质量管理方法。
它通过识别、评估和减少潜在的过程失效模式来预防质量问题的发生,提高产品和制程的可靠性和质量。
目的过程失效模式及后果分析的主要目的是在产品开发和制造过程中,识别可能导致产品或制程失效的模式,并评估这些失效模式对制程或产品的影响。
通过提前识别和分析潜在的问题,可以采取适当的措施来减少或消除这些问题的发生,从而提高产品质量和制程的稳定性。
流程过程失效模式及后果分析的主要步骤包括: 1. 确定分析范围:确定需要进行分析的过程或产品范围,并明确分析的目标和要求。
2. 识别失效模式:通过团队讨论、经验回顾和文献研究等方法,识别可能导致过程失效的模式。
3. 评估失效后果:对于每个识别出的失效模式,评估其对产品质量和制程稳定性的影响程度,以及可能导致的后果。
4. 评估失效原因:对于识别出的失效模式,分析其发生的原因和潜在的影响因素。
5. 评估现有控制措施:分析目前针对失效模式采取的控制措施,评估其有效性和适用性。
6. 优先级排序:根据失效影响程度、发生频率和控制措施的有效性等因素,确定失效模式的优先级。
7. 制定改进措施:对于高优先级的失效模式,制定相应的改进措施,以减少或消除其发生的可能性。
8. 跟踪和验证:跟踪和验证改进措施的实施情况和效果,并及时进行调整和改进。
工具和技术过程失效模式及后果分析可以借助以下工具和技术来完成: - 流程图:用于表示产品或制程的流程,有助于识别可能的失效模式。
- 失效模式和影响分析表(FMEA表):用于记录和评估失效模式及其后果、原因和控制措施。
- 根本原因分析(Root Cause Analysis):用于分析失效模式发生的根本原因,以便制定有效的改进措施。
- 文献研究和经验回顾:通过参考相关文献和借鉴以往的经验,可以获取更全面的失效模式和控制措施信息。
过程失效模式及后果分析(PFMEA)
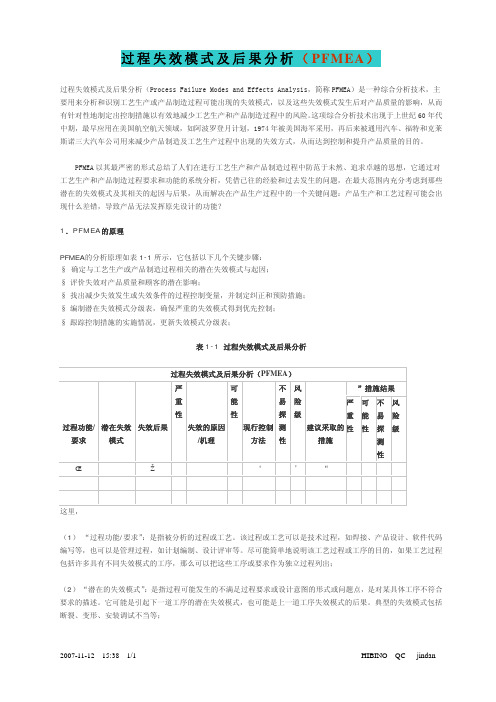
过程失效模式及后果分析(PFMEA)过程失效模式及后果分析(Process Failure Modes and Effects Analysis,简称PFMEA)是一种综合分析技术,主要用来分析和识别工艺生产或产品制造过程可能出现的失效模式,以及这些失效模式发生后对产品质量的影响,从而有针对性地制定出控制措施以有效地减少工艺生产和产品制造过程中的风险。
这项综合分析技术出现于上世纪60年代中期,最早应用在美国航空航天领域,如阿波罗登月计划,1974年被美国海军采用,再后来被通用汽车、福特和克莱斯诺三大汽车公司用来减少产品制造及工艺生产过程中出现的失效方式,从而达到控制和提升产品质量的目的。
PFMEA以其最严密的形式总结了人们在进行工艺生产和产品制造过程中防范于未然、追求卓越的思想,它通过对工艺生产和产品制造过程要求和功能的系统分析,凭借已往的经验和过去发生的问题,在最大范围内充分考虑到那些潜在的失效模式及其相关的起因与后果,从而解决在产品生产过程中的一个关键问题:产品生产和工艺过程可能会出现什么差错,导致产品无法发挥原先设计的功能?1.PFMEA的原理PFMEA的分析原理如表1-1所示,它包括以下几个关键步骤:§确定与工艺生产或产品制造过程相关的潜在失效模式与起因;§评价失效对产品质量和顾客的潜在影响;§找出减少失效发生或失效条件的过程控制变量,并制定纠正和预防措施;§编制潜在失效模式分级表,确保严重的失效模式得到优先控制;§跟踪控制措施的实施情况,更新失效模式分级表;表1-1 过程失效模式及后果分析过程失效模式及后果分析(PFMEA)”措施结果过程功能/要求潜在失效模式失效后果严重性失效的原因/机理可能性现行控制方法不易探测性风险级建议采取的措施严重性可能性不易探测性风险级ŒŽ‘ ’“这里,(1)“过程功能/要求”:是指被分析的过程或工艺。
该过程或工艺可以是技术过程,如焊接、产品设计、软件代码编写等,也可以是管理过程,如计划编制、设计评审等。
PFMEA过程失效模式及后果分析
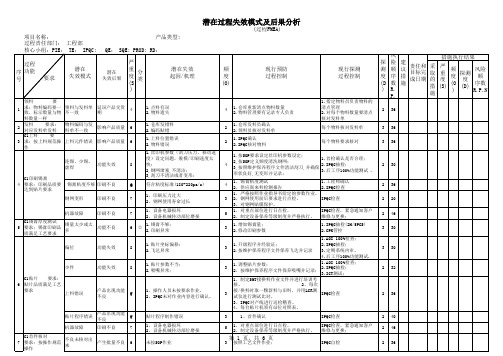
第 1 页,共 6 页
3 按照工艺文件作业;
IPQC检查,紧急通知客户 维修与更换;
IPQC自检
风
措施执行结果
探 测 度 (D )
险 顺 序 数 R. P.
建 议 措 施
责任和 采 目标完 取 成日期 的
措 施
严 重 度 (S)
频 度 (O )
探测 度 (D)
风险 顺 序数 R.P.N
2 36
3 36 3 36
领料
要
1
求:物料编码要一 领料与发料单 致,标示数量与物 不一致
延误产品交货 期
4
料数量一样
2
发料 要求: 对应发料单发料
物料编码与发 料单不一致
影响产品质量
6
C1上料 要
3 求:按上料规范操 上料元件错误 影响产品质量 6
作
连锡、少锡、 虚焊
功能失效
8
C1印刷锡膏
4 要求:印刷品质要 锡膏粘度不够 印刷不良
钢网变形
印刷不良
7
使用前未点检
1.接插件未防护; 2.作业操作失误;
1.摆放不按要求 2.重叠
1.上料位置错误 2.物料错误 1.丝印机参数(刮刀压力,移动速 度)设定问题,脱模/印刷速度太 快; 2,钢网堵塞,不清洁; 3,刮刀不清洁或者变形; 符合粘度标准(180-220pa/s)
1、印刷压力过大 2、钢网使用寿命过长
炉温设定错误
板未放到位 1、板与板叠放产生撞件 2、取放板时板跌落地面引起 3、PCB摆放错误 现场管理不到位 1、现场“5S”未做好 2.物品未标示 未执行工艺要求。 不良位置没有标识。
现场管理不到位 修理技术欠孰练 不按作业规范操作
PFMEA过程失效模式及后果分析
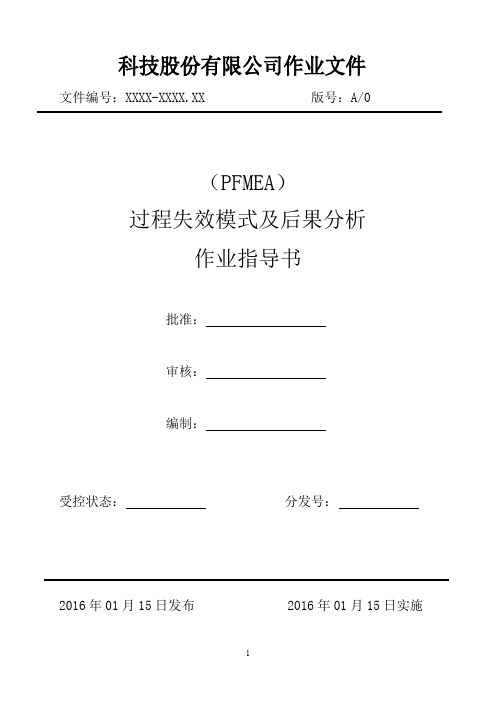
科技股份有限公司作业文件文件编号:XXXX-XXXX.XX 版号:A/0(PFMEA)过程失效模式及后果分析作业指导书批准:审核:编制:受控状态:分发号:2016年01月15日发布2016年01月15日实施过程潜在失效模式及后果分析作业指导书(PFMEA)XXXX-XXXX.XX1目的过程潜在失效模式及后果分析,简称PFMEA。
是一种信赖度分析的工具,可以描述为一组系统化的活动,是对确定产品/过程必须做哪些事情才能使顾客满意这一过程的补充。
其目的是:(a)并评价产品/过程中的潜在失效以及该失效的后果;(b)确定能够消除或减少潜在失效发生机会的措施;(c)将全部过程形成文件。
2范围:适用于公司用于零组件的所有新产品/过程的样品试制和批量生产。
适用于过程设计的风险性及后果的分析;适用于过程重复,周期性永不间断的改进分析。
3术语和定义:1)PFMEA:指Process Failure Mode and Effects Analysis(过程失效模式及后果分析)的英文简称。
由负责制造/装配的工程师/小组主要采用的一种分析技术,用以最大限度地保证各种潜在的失效模式及其相关的起因/机理已得到充分的考虑和论述。
2)失效:在规定条件下(环境、操作、时间),不能完成既定功能或产品参数值和不能维持在规定的上下限之间,以及在工作范围内导致零组件的破裂卡死等损坏现象。
3)严重度(S):指一给定失效模式最严重的影响后果的级别,是单一的PFMEA范围内的相对定级结果。
严重度数值的降低只有通过设计更改或重新设计才能够实现。
4)频度(O):指某一特定的起因/机理发生的可能发生,描述出现的可能性的级别数具有相对意义,但不是绝对的。
5)探测度(D):指在零部件离开制造工序或装配之前,利用第二种现行过程控制方法找出失效起因/机理过程缺陷或后序发生的失效模式的可能性的评价指标;或者用第三种过程控制方法找出后序发生的失效模式的可能性的评价指标。
如何完成过程失效模式及后果分析

如何完成过程失效模式及后果分析过程失效模式及后果分析(PFMEA)是一种常用的质量管理工具,用于识别过程中可能出现的失效模式及其潜在后果,并采取相应的预防措施,以避免失效对产品、顾客以及组织造成的负面影响。
本文将介绍如何完成过程失效模式及后果分析。
一、确定分析范围在进行PFMEA之前,首先需要明确分析的范围。
确定需要分析的过程,可以是制造过程、产品设计过程或供应链中的特定环节。
同时,还需要确定分析所涉及的产品或零部件。
二、组建分析团队为了保证PFMEA的有效性,需要组建一个具有多学科背景和经验的分析团队。
团队成员可以包括工程师、生产人员、质量专家、供应商代表等。
分析团队的多样性将为PFMEA提供不同的视角和丰富的经验,从而提高分析的准确性和全面性。
三、识别失效模式在进行PFMEA分析时,需要首先识别潜在的失效模式。
这些失效模式指的是导致过程产生非预期结果的根本原因。
例如,制造过程中的设备故障、材料质量问题、操作员误操作等都可能引发失效模式。
四、定义失效后果失效后果是指造成产品、顾客或组织经济损失、安全风险或声誉损害等不良影响的结果。
在PFMEA分析中,需要准确定义和描述每个失效模式可能引发的后果,包括其严重性、频率和可检测性等方面的考量。
五、确定风险优先级风险优先级是指失效模式的严重性、频率和可检测性三个因素的综合评估结果。
通过对每个失效模式进行定量或定性评估,并对其进行排序,有助于确定应优先处理的失效模式和制定相应的预防措施。
六、制定预防措施根据确定的风险优先级,制定相应的预防措施以减小失效发生的概率和影响。
预防措施可以包括改进设计、优化制程参数、加强质量控制和培训操作员等。
确保预防措施可行性的同时,还需要确保其有效性和可持续性。
七、跟踪和改进一个完整且持续的PFMEA过程应包括跟踪和改进措施的实施情况,并及时反馈和修正分析结果。
跟踪后续过程中是否出现了已识别的失效模式,并评估预防措施的有效性。
PFMEA 过程失效和结果分析

13
PFMEA 表格模版举例 表格模版举例
14
过程失效的潜在原因
• 漏操作 • 误加工 • 错误的安装 • 遗失零备件 • 备件错用 • 错误的处理半成品 • 错误的操作 • 错误的调整 •设备润滑不当 设备润滑不当 •使用错误的工具
• 差的控制程序 • 不正确的设备维护 • 错误的配方 • 老化 • 缺乏安全 • 错误的机器设置 • 执行错误的程序 • 环境 • 连接错误 差的FMEA系统 • 差的 系统
6
PFMEA 流程
实施行动计划降低 4 RPN
3 确定 S/O/D 的分级表
CI
D
5 检查并促进行
计算RPN并制
定优先计划
动计划的实施
只要一个流程没有从生产 线上退出, 线上退出,PFMEA 将永远 不会结束 6 执行可控的
C
2 绘制流程
图
1
标准程序
组队
7 改进后再次评
P
估 RPNs
A
识别失效模式: 识别失效模式 产品未能符合设计的意图或过程的要求 识别潜在要因 : 应按失效为何发生的迹象来确定,按照可纠正或可控制的情形来描述 识别潜在后果: 识别潜在后果:如果失效模式没有预防或纠正而导致顾客察觉的失效模式后果来定义
19
PFMEA 是 ISO9001 的一部分
Process Failure Mode and Effects Analysis
Statistical Process Control Quality System Analysis
Measurement System Analysis
ISO-9001 QS-9000
•操作步骤是否重复还是无顺序? •这些步骤是否频繁产生失误? •是否有循环的返工?
PFMEA过程失效模式及后果分析

PFMEA过程失效模式及后果分析PFMEA(Process Failure Mode and Effects Analysis)是一种通过系统地识别和评估潜在的失效模式及其后果来预防产品和过程问题的方法。
它有助于组织在设计和开发阶段就发现并解决潜在的问题,从而提高产品质量和生产效率。
在这篇文章中,我们将重点讨论PFMEA过程中的失效模式及其后果分析。
失效模式是指导致产品或过程失效的特定原因或机制。
它可以是由于设计缺陷、材料问题、加工误差、操作失误等引起的。
失效模式常常以不同的方式出现,在不同的环境下可能会有不同的后果。
在进行PFMEA过程中,首先需要识别潜在的失效模式。
这可能涉及到对产品、过程和相关文档的仔细研究,以了解可能存在的问题。
接下来,需要对每个失效模式的影响进行评估,这也就是后果分析。
后果分析可以帮助确定失效对产品质量、生产效率和安全性等方面造成的影响,从而决定需要采取的预防措施。
在进行PFMEA过程失效模式及后果分析时,以下是一些常见的失效模式和其可能的后果:1.设计缺陷:-可能的后果:产品性能不达标、产品寿命缩短、安全隐患、产品被召回等-预防措施:加强设计评审、使用可靠的设计工具、进行模拟测试等2.材料问题:-可能的后果:产品强度不足、耐腐蚀性差、产品寿命缩短等-预防措施:严格选择、测试和审查材料供应商、加强入库检查等3.加工误差:-可能的后果:产品尺寸偏差、表面质量不良、装配困难等-预防措施:加强生产工艺控制、使用先进的制造设备、严格执行质量标准等4.操作失误:-可能的后果:生产过程中出现错误、设备损坏、人员伤亡等-预防措施:提供员工培训、实施作业规程、设立安全警示标志等除了上述提到的失效模式和后果,还有许多其他可能的情况需要被考虑和分析。
在进行PFMEA过程中,团队成员需要全面了解产品和过程,积极参与讨论和决策,以确保有效识别和评估潜在的问题。
此外,通过对失效模式及后果进行分析,团队还可以确定应对措施的优先级和实施计划。
- 1、下载文档前请自行甄别文档内容的完整性,平台不提供额外的编辑、内容补充、找答案等附加服务。
- 2、"仅部分预览"的文档,不可在线预览部分如存在完整性等问题,可反馈申请退款(可完整预览的文档不适用该条件!)。
- 3、如文档侵犯您的权益,请联系客服反馈,我们会尽快为您处理(人工客服工作时间:9:00-18:30)。
过程失效模式及后果分析(PFMEA):制定项目风险管理计划的有效工具2003年2月1日,美国东部时间上午9时(北京时间1日22时),即将返航的哥伦比亚号航天飞机在大约63 k m高空处与地面控制中心失去联系,在得克萨斯州中部地区上空爆炸解体,机上7名航天员全部遇难。
项目的失败,使人类付出了生命的代价!那么,怎样去减少项目失败的风险呢?项目风险是一种不确定的事件或条件,这种事件或条件一旦发生,就会对项目目标产生某种程度的影响,或者导致项目进度拖期、成本超支,或者引起质量事故、客户投诉,甚至引发项目执行不下去、系统瘫痪、机毁人亡的灾难。
项目的风险事件或条件往往具有不确定性,但它发生后对项目的范围、成本、进度、质量性能等方面的影响却是肯定的。
因此,项目管理人员必须具备“生于忧患,死于安乐”的意识,在执行项目之前就尽可能识别出项目的各种风险,并由此制定出周密的风险管理计划,以便能够在项目执行期间有效地监控和响应,从而消除风险事件对项目的影响或者将其影响降至最小,做到化险为夷。
过程失效模式及后果分析(Process Failure Modes and Effects Analysis,简称PFMEA)是一种综合分析技术,主要用来分析和识别工艺生产或产品制造过程可能出现的失效模式,以及这些失效模式发生后对产品质量的影响,从而有针对性地制定出控制措施以有效地减少工艺生产和产品制造过程中的风险。
这项综合分析技术出现于上世纪60年代中期,最早应用在美国航空航天领域,如阿波罗登月计划,1974年被美国海军采用,再后来被通用汽车、福特和克莱斯诺三大汽车公司用来减少产品制造及工艺生产过程中出现的失效方式,从而达到控制和提升产品质量的目的。
PFMEA以其最严密的形式总结了人们在进行工艺生产和产品制造过程中防范于未然、追求卓越的思想,它通过对工艺生产和产品制造过程要求和功能的系统分析,凭借已往的经验和过去发生的问题,在最大范围内充分考虑到那些潜在的失效模式及其相关的起因与后果,从而解决在产品生产过程中的一个关键问题:产品生产和工艺过程可能会出现什么差错,导致产品无法发挥原先设计的功能?1.PFMEA的原理PFMEA的分析原理如表1-1所示,它包括以下几个关键步骤:§ 确定与工艺生产或产品制造过程相关的潜在失效模式与起因;§评价失效对产品质量和顾客的潜在影响;§找出减少失效发生或失效条件的过程控制变量,并制定纠正和预防措施;§编制潜在失效模式分级表,确保严重的失效模式得到优先控制;§跟踪控制措施的实施情况,更新失效模式分级表;表1-1 过程失效模式及后果分析这里,(1)“过程功能/要求”:是指被分析的过程或工艺。
该过程或工艺可以是技术过程,如焊接、产品设计、软件代码编写等,也可以是管理过程,如计划编制、设计评审等。
尽可能简单地说明该工艺过程或工序的目的,如果工艺过程包括许多具有不同失效模式的工序,那么可以把这些工序或要求作为独立过程列出;(2)“潜在的失效模式”:是指过程可能发生的不满足过程要求或设计意图的形式或问题点,是对某具体工序不符合要求的描述。
它可能是引起下一道工序的潜在失效模式,也可能是上一道工序失效模式的后果。
典型的失效模式包括断裂、变形、安装调试不当等;(3)“失效后果”:是指失效模式对产品质量和顾客可能引发的不良影响,根据顾客可能注意到或经历的情况来描述失效后果,对最终使用者来说,失效的后果应一律用产品或系统的性能来阐述,如噪声、异味、不起作用等;(4)“严重性”:是潜在失效模式对顾客影响后果的严重程度,为了准确定义失效模式的不良影响,通常需要对每种失效模式的潜在影响进行评价并赋予分值,用1-10分表示,分值愈高则影响愈严重。
“可能性”:是指具体的失效起因发生的概率,可能性的分级数着重在其含义而不是数值,通常也用1—10分来评估可能性的大小,分值愈高则出现机会愈大。
“不易探测度”:是指在零部件离开制造工序或装备工位之前,发现失效起因过程缺陷的难易程度,评价指标也分为1—10级,得分愈高则愈难以被发现和检查出;(5)“失效的原因/机理”:是指失效是怎么发生的,并依据可以纠正或控制的原则来描述,针对每一个潜在的失效模式在尽可能广的范围内,列出每个可以想到的失效起因,如果起因对失效模式来说是唯一的,那么考虑过程就完成了。
否则,还要在众多的起因中分析出根本原因,以便针对那些相关的因素采取纠正措施,典型的失效起因包括:焊接不正确、润滑不当、零件装错等;(6)“现行控制方法”:是对当前使用的、尽可能阻止失效模式的发生或是探测出将发生的失效模式的控制方法的描述。
这些控制方法可以是物理过程控制方法,如使用防错卡具,或者管理过程控制方法,如采用统计过程控制(SPC)技术;(7)“风险级(RPN)”:是严重性、可能性和不易探测性三者的乘积。
该数值愈大则表明这一潜在问题愈严重,愈应及时采取纠正措施,以便努力减少该值。
在一般情况下,不管风险级的数值如何,当严重性高时,应予以特别注意;(8)“建议采取的措施”:是为了减少风险发生的严重性、可能性或不易探测性数值而制定的应对方案,包括行动计划或措施、责任人、可能需要的资源和完成日期等。
当失效模式排出先后次序后应首先对排在最前面的风险事件或严重性高的事件采取纠正措施,任何建议措施的目的都是为了阻止其发生,或减少发生后的影响和损失;(9)“措施结果”:是对上述“建议采取的措施”计划方案之实施状况的跟踪和确认。
在明确了纠正措施后,重新估计并记录采取纠正措施后的严重性、可能性和不易探测性数值,计算并记录纠正后的新的风险级值,该数值应当比措施结果之前的风险级值低得多,从而表明采取措施后能够充分降低失效带来的风险。
2.运用PFMEA制定项目风险管理计划由表1-1可以发现,PFMEA事实上就是一套严密的识别、控制、改善失效模式的管理过程,通过对过程失效模式及其后果的系统分析,制定出相应地预防措施和行动方案,从而大大降低失败的机会。
这种系统分析工具不仅可在工艺过程的管理中,也可应用于任何期望能严格控制潜在问题出现的管理过程,尤其是产品或服务质量的好坏可能会极大影响到顾客利益的领域。
当然在具体应用的时候,不一定完全按照PFMEA给定的“严重性”、“可能性”及“不易探测性”之评价标准进行评分,完全可以视本行业或管理过程的实际情况来设定一系列类似的评价标准,并且在具体操作手法上也可根据实情采用适合于自身的方式,只要能达到更有效地识别、控制潜在问题的发生、提高管理过程质量的目的即可。
项目管理本身就是一种过程管理,目的就是要在规定的时间、在批准的预算、完成事先确定的任务并达到质量性能标准要求,风险事件或条件就是项目过程中潜在的失效模式,它们的发生可能导致项目的上述目标无法实现。
只要对上述PFMEA的原理稍加改造,就可以成为一种有效地制定项目风险管理计划的工具,如表1-2所示。
表1-2 项目风险管理计划这里,a) “项目管理过程”:是指项目管理生命期的启动、计划、执行、控制和收尾五个过程。
在不同的行业,项目管理过程的叫法可能不一样,如软件开发项目通常分为需求分析、系统设计、编码、测试、上线安装和系统维护几个过程,而工程建设项目则分为项目评估、设计准备、设计、施工、验收与移交等几个过程;b) “风险识别”:风险识别包括确定那些潜在的、可能对项目造成影响的风险事件,只有事先识别出了这些风险事件并且知道了它们对项目可能带来怎样的影响,才谈得上对其进行应对和处理。
因此,风险识别是制定项目风险管理计划的第一步。
由于项目管理处于一个动态的环境中,随着项目的进展原先可能导致项目风险的机会和条件或许已经不复存在,而新的机会和条件可能发生,因此风险识别并不是一僦而就的事情,往往需要贯穿项目执行的始终。
项目小组通常使用头脑风暴法、故障树分析、系统分解法、检查表法、德尔菲法、SWOT分析技术等方法来识别项目的风险事件。
风险发生的后果可能导致项目进度拖期,成本超支,利润降低,质量或安全事故,人员士气低落或流失,客户不满意或投诉、项目取消等;c) “风险评估”:是在风险识别的基础上对每种风险事件对项目的影响进行定性或定量的分析,并根据风险对项目目标的影响程度对项目风险由大到小分级排序的过程。
定性评估是从类别上评价出已识别出的项目风险的影响和可能性大小,一般分为高、中、低三档。
低风险是指发生的可能性相当低,发生后对项目的影响也无关紧要,又很容易被项目小组控制的风险,这类风险不需要采取其它的专门措施来处理;中等风险是指发生的可能性比较高,对项目的技术性能、成本或进度将产生较大影响,并且控制起来又有一定难度的风险,这类风险,需要对其进行有效的监控和评审,并应采取适当的手段或行动来降低风险;高风险是指发生的可能性很高,其后果将对项目产生极大影响,并且运用现有的技术条件和手段又很难控制的风险。
表1-3是借助风险识别检查单,运用定性的方法评估出的项目的风险情况。
该项目有哪些风险,其中哪些风险低,哪些中等,哪些高,从表中一目了然。
表1-3 风险识别清单及定性评估结果定量分析是量化分析每一风险的概率及其对项目目标造成后果的严重程度,并得出每种风险大小及其严重程度的一种方法。
一般来讲,风险定量评估是在定性评估的基础上进行的,通常采用从若干方面逐项评分的方法来量化风险的大小,即事先确定评分的标准,然后由项目小组一起,对预先识别出的项目风险一一打分,然后得出不同风险之大小,按照PFMEA的思想,可以从风险时间发生的可能性、风险发生对项目影响的严重性和项目小组能否有效控制风险发生三方面来定量分析。
如图1-4所示。
例如,可以从1到10分的等级来评估风险,如果项目小组在评估发生资金短缺的风险时,认为它非常不可能发生,得3分,但是一旦发生后果则非常严重,得9分;而且,资金短缺项目小组很难控制,得8分,然后把这三个数字相乘,即得到该风险的风险级别(RPN)。
风险级别越高,表示风险越大,需要项目小组制定相应的措施认真对待。
表1-4 风险定量评估标准d) “风险应对措施”:包括紧急措施和预防措施,紧急措施是风险发生后采取的应对措施,而预防措施则是为了防止同样的问题再次出现所采取的防患措施。
常用的风险应对措施包括:a) 回避风险回避有两种含义,一是指风险发生的可能性极大,后果极其严重,又不能控制,感到无计可施,于是主动放弃项目或改变项目目标的策略;二是通过变更项目计划,消除风险事件本身或风险产生的条件,从而保护项目目标免受影响的方法。
虽然项目团队永远不可能消除所有的风险,但某些特定的风险还是可能回避的。
例如,保险公司认为某项目的风险太大,拒绝承保;采用一种熟悉的、而不是创新的方法;避免使用一个不熟悉的分承包商;建筑工程上尽量避开梅雨季节施工等,这些都都是风险回避的例子。