铜棒型线材缺陷
条痕缺陷产生的原因及解决方法
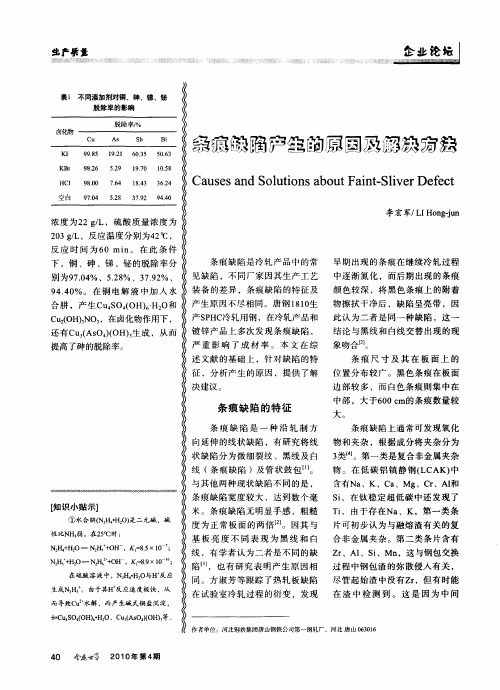
搿 麓 燕 。 ¨ 藏簌 。 嚣 。 糍舞囊 } 誊 ¨
企 业论 坛 I
表 1 不同添加剂对铜 、砷 、锑 、铋 脱除率的影响
疽 陷 壁 翰 属 圆 羼
Ca s sa d S l t n b u i tS i e f c u e n o u i sa o t o Fan . l r v De e t
N + 2 2 Ho— H2O , =.× 0 ; 6+ H 8 1 9
在硫 酸溶液 中,N2 4 0与H 反 应 H・ H2
生成N, 。 由 于其 H 反 应 速 度 极 快 ,从 H
陷 【,也有 研 究表 明产 生原 因相 过 程 中钢包 渣 的弥散侵 入有关 , 3 】
杂是 否来 自同一夹 杂物 ,但 大 的 度 、速 度和 冲击 处液 面深 度 的函
ห้องสมุดไป่ตู้
包 、钢包 渣 、钢包砂 受 到污 染和
侵入式 水 口,中间 包水 口耐 火材 塞 物 的结合 物 。 即使 不 能肯 定夹 钢水 冲击结 晶器 窄边 时 的冲击 角
料 的侵蚀 。第三类条 片 , 在低碳 铝镇静 钢 中 中间包 长水 口附 近仅 含有Al 和Mn钛稳定超低碳钢 中含 ,
条痕 缺陷 是冷轧产 品 中的常 早 期 出现 的条 痕在继 续冷 轧过程 见缺陷 ,不 同厂家 因其生产 工艺 中逐 渐氮化 ,而后 期 出现的条 痕
9 .0 4 4 %。在 铜 电解 液 中加入 水 装 备 的差异 ,条痕缺 陷 的特 征及 颜色 较深 ,将黑 色条痕 上的附 着 80 合肼 ,产生 C O ( )・ 2 uS OH H O和 产 生原 因不 尽相 同。唐钢 1 1 生 物擦拭 干净后 ,缺 陷呈亮带 ,因 C 2 H O3 卤化物作用下 , uO ) ( N ,在
棒线材表面缺陷产生原因及消除方法

棒线材表⾯缺陷产⽣原因及消除⽅法线材⽿⼦产⽣原因及消除⽅法线材表⾯沿轧制⽅向的条状凸起称为⽿⼦,有单边⽿⼦也有双边⽿⼦。
⾼速线材轧机⽣产中由于张⼒原因,产品头尾两端很难避免⽿⼦的产⽣。
有下述情况时容易产⽣⽿⼦:(1)轧槽与导卫板安装不正;(2)轧制温度的波动较⼤或不均匀较严重,影响轧件的宽展量;(3)坯料的缺陷,如缩孔、偏析、分层及外来夹杂物,影响轧件的正常变形;(4)来料尺⼨过⼤。
预防及消除⽅法如下:(1)正确安装和调整⼊⼝导卫;(2)提⾼钢坯加热质量,控制好轧制温度;(3)合理调整张⼒;(4)控制来料尺⼨。
线材表⾯的凸起及压痕(轧疤)形成的原因线材表⾯连续出现周期性的凸起或凹下的印痕,缺陷形状、⼤⼩相似。
凸起及压痕主要是轧槽损坏(掉⾁或结瘤)造成的。
线材产品检验项⽬及影响尺⼨精度的主要因素线材产品检验包括六项内容:外形尺⼨,压扁实验,含碳量⽐较,快速碳分析,⼒学性能试验和⾼倍检验。
影响线材尺⼨精度有以下主要因素:有温度、张⼒,孔型设计、轧辊及⼯艺装备的加⼯精度、孔槽及导卫的磨损、导卫板安装和轧机的机座刚度、调整精度、轧辊轴承的可靠性和电传控制⽔平和精度等。
其中张⼒是影响线材产品尺⼨精度的最主要因数。
在轧制线材的过程中尽可能实现微张⼒或⽆张⼒轧制是⾼速线材轧制的宗旨。
孔型设计与轧件精度也有密切关系,⼀般讲椭圆—⽴椭圆孔型系列消差作⽤⽐较显著;⼩辊径可以减少宽展量,其消差作⽤⽐⼤辊径好。
孔型设计中应特别注意轧件尺⼨变化后的孔型适应性,即变形的稳定性、不扭转不倒钢不改变变形⽅位。
线材裂纹产⽣的原因及预防⽅法裂纹在线材中的分布是不连续的,垂直于线材表⾯或呈⼀⾓度陷⼊线材。
裂纹长短不⼀,通常呈直线形,偶尔也有横向裂纹或龟裂。
由钢坯上的缺陷经轧制后形成的裂纹常伴有氧化质点、脱碳现象,裂纹中间常存在氧化亚铁;由轧后控冷不当形成的裂纹⽆脱碳现象伴⽣,裂缝中⼀般⽆氧化亚铁,多呈横裂或龟裂。
从炼钢到轧钢都有可能产⽣裂纹。
铜线杆质量影响因素浅谈
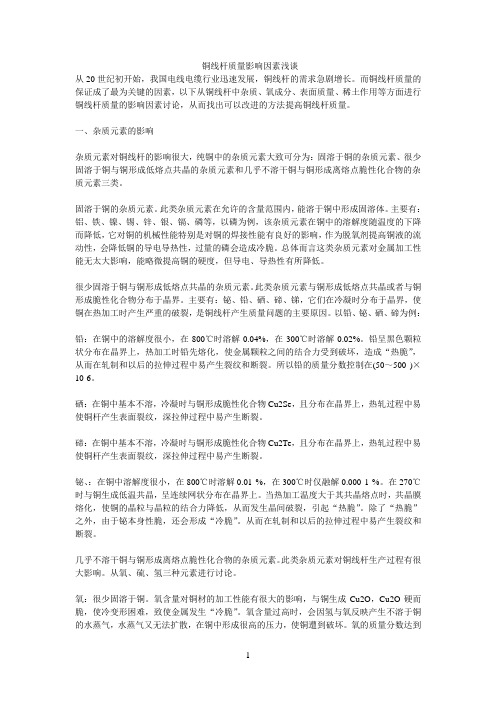
铜线杆质量影响因素浅谈从20世纪初开始,我国电线电缆行业迅速发展,铜线杆的需求急剧增长。
而铜线杆质量的保证成了最为关键的因素,以下从铜线杆中杂质、氧成分、表面质量、稀土作用等方面进行铜线杆质量的影响因素讨论,从而找出可以改进的方法提高铜线杆质量。
一、杂质元素的影响杂质元素对铜线杆的影响很大,纯铜中的杂质元素大致可分为:固溶于铜的杂质元素、很少固溶于铜与铜形成低熔点共晶的杂质元素和几乎不溶干铜与铜形成离熔点脆性化合物的杂质元素三类。
固溶于铜的杂质元素。
此类杂质元素在允许的含量范围内,能溶于铜中形成固溶体。
主要有:铝、铁、镍、锡、锌、银、镉、磷等,以磷为例,该杂质元素在铜中的溶解度随温度的下降而降低,它对铜的机械性能特别是对铜的焊接性能有良好的影响,作为脱氧剂提高铜液的流动性,会降低铜的导电导热性,过量的磷会造成冷脆。
总体而言这类杂质元素对金属加工性能无太大影响,能略微提高铜的硬度,但导电、导热性有所降低。
很少固溶于铜与铜形成低熔点共晶的杂质元素。
此类杂质元素与铜形成低熔点共晶或者与铜形成脆性化合物分布于晶界。
主要有:铋、铅、硒、碲、锑,它们在冷凝时分布于晶界,使铜在热加工时产生严重的破裂,是铜线杆产生质量问题的主要原因。
以铅、铋、硒、碲为例:铅:在铜中的溶解度很小,在800℃时溶解0.04%,在300℃时溶解0.02%。
铅呈黑色颗粒状分布在晶界上,热加工时铅先熔化,使金属颗粒之间的结合力受到破坏,造成“热脆”,从而在轧制和以后的拉伸过程中易产生裂纹和断裂。
所以铅的质量分数控制在(50~500 )×10-6。
硒:在铜中基本不溶,冷凝时与铜形成脆性化合物Cu2Se,且分布在晶界上,热轧过程中易使铜杆产生表面裂纹,深拉伸过程中易产生断裂。
碲:在铜中基本不溶,冷凝时与铜形成脆性化合物Cu2Te,且分布在晶界上,热轧过程中易使铜杆产生表面裂纹,深拉伸过程中易产生断裂。
铋、:在铜中溶解度很小,在800℃时溶解0.01 %,在300℃时仅融解0.000 1 %。
线材表面缺陷发生原因分析及其减少措施
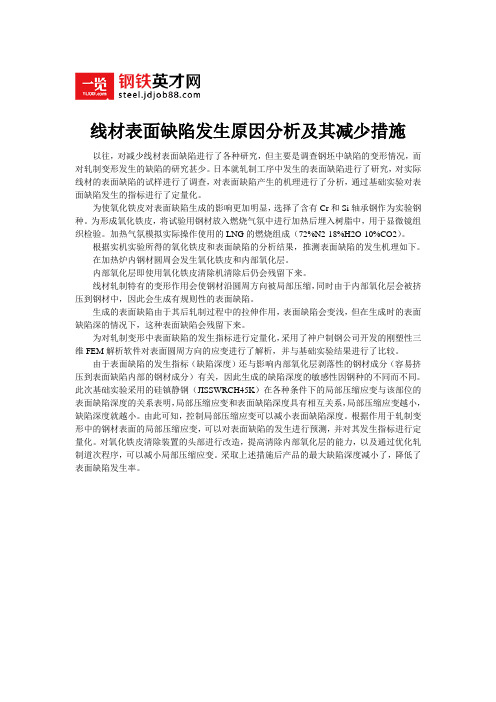
线材表面缺陷发生原因分析及其减少措施以往,对减少线材表面缺陷进行了各种研究,但主要是调查钢坯中缺陷的变形情况,而对轧制变形发生的缺陷的研究甚少。
日本就轧制工序中发生的表面缺陷进行了研究,对实际线材的表面缺陷的试样进行了调查,对表面缺陷产生的机理进行了分析,通过基础实验对表面缺陷发生的指标进行了定量化。
为使氧化铁皮对表面缺陷生成的影响更加明显,选择了含有Cr和Si轴承钢作为实验钢种。
为形成氧化铁皮,将试验用钢材放入燃烧气氛中进行加热后埋入树脂中,用于显微镜组织检验。
加热气氛模拟实际操作使用的LNG的燃烧组成(72%N2-18%H2O-10%CO2)。
根据实机实验所得的氧化铁皮和表面缺陷的分析结果,推测表面缺陷的发生机理如下。
在加热炉内钢材圆周会发生氧化铁皮和内部氧化层。
内部氧化层即使用氧化铁皮清除机清除后仍会残留下来。
线材轧制特有的变形作用会使钢材沿圆周方向被局部压缩,同时由于内部氧化层会被挤压到钢材中,因此会生成有规则性的表面缺陷。
生成的表面缺陷由于其后轧制过程中的拉伸作用,表面缺陷会变浅,但在生成时的表面缺陷深的情况下,这种表面缺陷会残留下来。
为对轧制变形中表面缺陷的发生指标进行定量化,采用了神户制钢公司开发的刚塑性三维FEM解析软件对表面圆周方向的应变进行了解析,并与基础实验结果进行了比较。
由于表面缺陷的发生指标(缺陷深度)还与影响内部氧化层剥落性的钢材成分(容易挤压到表面缺陷内部的钢材成分)有关,因此生成的缺陷深度的敏感性因钢种的不同而不同。
此次基础实验采用的硅镇静钢(JISSWRCH45K)在各种条件下的局部压缩应变与该部位的表面缺陷深度的关系表明,局部压缩应变和表面缺陷深度具有相互关系,局部压缩应变越小,缺陷深度就越小。
由此可知,控制局部压缩应变可以减小表面缺陷深度。
根据作用于轧制变形中的钢材表面的局部压缩应变,可以对表面缺陷的发生进行预测,并对其发生指标进行定量化。
对氧化铁皮清除装置的头部进行改造,提高清除内部氧化层的能力,以及通过优化轧制道次程序,可以减小局部压缩应变。
铜合金铸件铸造缺陷及防止对策ppt课件

○
○
○
○ ○○
○
○○
○
○
○
○
○
○○○ ○
1 1 12
17 7 2
11 3 10
○ 65 3
表3续
2、艺术铸造铜合金的冶金特性
艺术铸造铜合金的独特要求:
①合金应满足艺术铸品的使用要求 ——耐蚀性、色泽、声学特性和机械性能
②合金应满足各种工艺要求 ——铸造成形性能、可焊接性能、可打磨加工 性能和表面着色性能
deabcde图1缩孔缩松缺陷示意图外缩孔内缩孔缩松图2铜合金铸件铸造缺陷分类及其主要原因主要原因铸造缺陷模型装置砂箱装置砂的性质的有机材料造型材料中制芯作业造型作业合箱金属液铸件设计浇冒口系统铸造工艺方案浇注温度浇注技术不注意1错箱2浇不到3冷隔4砂型压崩5胀箱6壁厚尺寸偏差7冲砂8夹砂表3铜合金铸件铸造缺陷分类及其主要原因续主要原因铸造缺陷模型装置砂箱装置砂的性质的有机材料造型材料中制芯作业造型作业合箱金属液铸件设计浇冒口系统铸造工艺方案浇注温度浇注技术不注意9表面气坑10烧结粘砂机械粘砂11内侧面包芯砂12表面不完整13虫眼表面14表面锈迹15锡汗铅汗16表面粗糙表3续铜合金铸件铸造缺陷分类及其主要原因续主要原因铸造缺陷模型装置砂箱装置砂的性质的有机材料造型材料中制芯作业造型作业合箱金属液铸件设计浇冒口系统铸造工艺方案浇注温度浇注技术不注意17表面麻点18褪色a1青铜19固体夹杂20缩孔21热裂22粗晶组织23气孔24铸件清理缺陷1112177211310653表3续2艺术铸造铜合金的冶金特性?艺术铸造铜合金的独特要求
砂 箱 装 置
砂 造的 制
的 性 质
型有 材机 料材 中料
芯 作 业
造 型 作 业
合 箱
铜材断线分析

第一节电弧伤害导致的断线断头的特征是持续的退火电流熔化部分或熔断铜材,导致断线形成的。
局部的熔化是由于持续的退火导致。
原因:1.退火轮表面脏;2.卷筒张力不足导致(也许是收线机张力小或线抖导致);3.退火轮调整不当,跳动。
来源:1.退火导轮;2.卷筒;3.张力控制。
第二节中央爆裂(其他名字:杯状断裂;杯锥状断裂)杯状断裂的断头两端杯状断线的断头在铜材内部的发展过程。
杯状断裂的圆锥体杯状断裂的深洞。
原因:1.高浓度的铜氧化物粒子在线的中央部分集中或沿轴向分布;2.存在一种微观的磁性或非磁性的杂质;3.不适当的模具形状设计、塔轮磨损、进入模具不均匀,模具润滑不足和/或不正确的模具减面率或进线角度,模具定径区过长。
来源:1.铜材含氧量过高(>600万分之一)。
2.在铸造过程中铜氧化物掉入熔融的铜熔池中。
3.簇状的铜的氧化物(铜柱)掉入熔融的铜池中。
4.铸造的铜杆儿的气体空穴的周围有簇状的氧化铜。
5.铜棒不均匀的冷却在成铜氧化物的不均匀的分布。
6.熔融的熔池中有微观的部分磁性非磁性的残留的不溶解的粒子。
7.拉丝过程操作。
第二节A类断头:氧化铜粒子造成的杯状断裂中央爆裂的圆锥状断头高浓度的氧化铜粒子在断头里面断头里的高浓度的氧化铜粒子偏析出的大大小小的氧化铜粒子原因:高浓度的氧化铜粒子或条状物在铜材中心,这些粒子扮演着张力集中点产生微小裂纹,这些裂纹将推广或直接造成铜杆断裂。
来源:1.铜材含有高浓度的氧化物(>600)2.高浓度的铜氧化物掉入熔融铜池中。
3.铜柱掉入熔融铜池中。
4.在轧制过程中铜材上空洞里的气体周围的簇状的铜氧化物被冷轧进铜杆里了。
5.在铜杆的冷却过程中不均匀的冷却导致铜氧化物不均匀的分布。
第二节B类磁性或非磁性物质造成的杯状断裂杯状断裂的圆锥形断头前端的非磁性物质,经过X光分析是硅(可能是二氧化硅)。
高放大倍率的二氧化硅粒子图像。
杯状断裂圆锥端中心的的非磁性杂质,经过X光衍射分析确定粒子含有铝,硅和钛(可能为耐火砂混合物)。
线材表面缺陷原因分析及对策

线材表面缺陷原因分析及对策摘要:从设备管理的角度,分析设备问题影响材线表面的各种原因,针对设备存在的问题提出改进措施,表面缺陷得到有效控制。
关键词:线材;表面质量;设备前言线材表面质量是用户对公司实物的第一认知,直接影响到用户对公司产品的满意度。
线材在轧制过程中,设备与线材接触面状况对成品材表面影响极大。
1影响线材表面质量的因素1.1 钢坯表面氧化铁皮影响线材表面质量的原因分析炉温控制不合理,导致钢坯在高温段的停留时间长,钢坯表面氧化严重,经各架轧机轧制后,表面氧化铁皮不能及时脱落,最终嵌入线材表面,形成次材。
空燃配比控制不合理,炉膛为氧化气氛,钢坯表面氧化严重,最终导致线材表面产生缺陷。
高压水除鳞压力不足或是喷嘴安装不正确,不能将钢坯表面的氧化铁皮彻底清除,最终引起成品表面形成麻点、铁皮等缺陷,进而造成次品。
1.2 导卫影响线材表面质量的原因分析由于导卫装配原因,导卫导辊转动不灵活或是导辊对轧件不能起到有效的支撑作用,最终导致轧件表面有划伤、折叠等缺陷。
由于油气润滑以及冷却水系统故障,造成导辊碎裂、粘钢、烧轴承等现象发生,进而导致轧件表面出现划伤。
由于导辊材质原因,在生产过程中有“掉肉”现象发生,进而导致线材表面出现划痕、结疤等缺陷。
由于导卫上线安装原因,导致轧件导入下游轧机时,不能对中相应轧机的孔型,进而导致线材表面出现耳子等缺陷。
1.3 轧辊、辊环影响线材表面质量的原因分析由于轧辊、辊环的质量问题,导致轧辊、辊环在生产过程中有“掉肉”现象发生,进而导致线材表面出现划伤、结疤等缺陷。
由于轧辊、辊环的上线装配原因,各架料型控制不合适,最终导致线材表面出现折叠、耳子等缺陷。
1.4活套轮影响线材表面质量的原因分析活套轮直接与线材表面接触,每条线装机量29个,其运行状态与红钢接触面光洁度对成品线材表面影响非常大。
活套轮高度参数不正确或设定变化范围大,活套轮安装偏离轧制中心线过多,造成辊轮表面磨损不光滑,造成线材表面出现划痕、划伤等问题。
型钢、线材常见缺陷及原因

缺陷名称
缺陷特征
产生原因
结疤
型钢表面上的疤状金属薄块。其大小、深浅不等,外形极不规则,常呈指甲状、鱼鳞状、块状、舌头状无规律地分布在钢材表面上,结疤下常有非金属夹杂物。
由于钢坯未清理,使原有的结疤轧后仍残留在钢材表面上。
表面夹杂
暴露在钢材表面上的非金属物质称为表面夹杂,一般呈点状、块状和条状分布,其颜色有暗红、淡黄、灰白等,机械的粘结在型钢表面上,夹杂脱落后出现一定深度的凹坑,其大小、形状无一定规律。
(1)矫直辊孔型设计不合理。
(2)矫直机调整操作不当。
(3)矫直辊磨损严重。
(4)轧辊磨损或成品孔出口卫板安装不良。
线材常见缺陷
缺陷名称
缺陷特征
产生原因
耳子
盘条表面沿轧制方向的条状凸起称为耳子,有单边耳子,也有双边耳子。在高速线材轧机(连轧)生产中,最终产品头尾两端很难避免耳子的产生。
1)轧槽导卫安装不正及放偏过钢,使轧件产生耳子。
裂纹
顺轧制方向出现在型钢表面上的线形开裂,一般呈直线形,有时呈“Y”形,多为通长出现,有时局部出现。
(1)钢坯有裂缝或皮下气泡、非金属夹杂物,经轧制破裂暴露。
(2)加热温度不均匀,温度过低,轧件在轧制时各部延伸与宽展不一致。
(3)加热速度过快、炉尾温度过高或轧制后冷却不当,易形成裂纹,此种情况多发生在高碳钢和低合金钢上。
(1)孔型设计不良,轧辊车削不正确及轧机调整不当,使轧件进入成品孔时由于金属量不足,造成孔型充填不满。
(2)轧槽错牙或入口导板安装不当,造成轧件某一面缺少金属,再轧时孔型充填不满。
(3)前、后孔磨损程度不一样。
(4)园轧件弯、扭造成进孔不正。
(5)对于工、槽钢,困钢坯不清理,往往出现结疤掉到闭口腿内,在轧制过程中便会出现周期性的腿尖缺肉。
浅谈连续挤压铜母线、异型铜排的各种缺陷

⑤ 挤 压 模 腔 、 具 、 片 设 计 或 组 装 不 合 理 , 成 金 属 流 速 不 模 垫 造
均匀。
③ 合 理控 制挤 压 速 度 ;
④ 上 引铜 杆 时 保 持 合 理 的 引 速 和冷 却 速 度 , 铜 杆 硬 使
度保持在 I 5 - t 2左 右 ; RC
⑤ 更 改 模 具设 计 或 安 装 模 具 时 要认 真 准确 。
序 号 缺 陷 名 称 形 成 原 因 预 防措 施
① 保时 避 免 油 、 存 使
① 铜 杆 表 面 被 油 、 、 土 等 污 染 。 ( 压 驱 动 力 为 挤 压 轮 与 水 尘 挤 水 的污 染 , 现 污 染 时要 及时 清 理 ; 发 ② a挤压 模 具 采 用 不 等 宽 定 径 带 和 偏 心 结 构 。定 径 带 宽度 要 考 虑 其 制 品 的 断 面 积 大 小 、 长 、 挤 压 模 周 在 具 平 面 的位 置 等 。一 般 情 况 定 径 带 宽 2—5 mm, 成 难 型 的 区域 采 用 下 限 。易 成 型 的 区 域 采 用 上 限 ; b对 于 与 铜 杆 直 径 的 比 值 。 比值 愈 大 , 展 比愈 大 , 扩 当扩 展 比大 于 8 . 5时 难 于 成 型 , 尤其 是 形 状 比较 复 杂 的 异 型 ; 压 系 数 是 指 模 挤 前提下, 制 品中心 相对于 模具 中心做 一定 的偏移 , 将 腔 的扩 展 腔 的 断 面 积 与 制 品 的断 面 积 之 比 。 挤 压 系数 愈 大 , 金
充 不 满
慢 , 定 的挤 压 阶 段 ( 度 场 ) 难 建 立 , 易 出 现 充 不 满 现 稳 温 很 极
象 。我 公 司的 复 杂 工 字 型铜 排 就 是 如 此 , 般 大 断 面制 品挤 压 一
铜杆线拉伸质量问题分析及预防对策
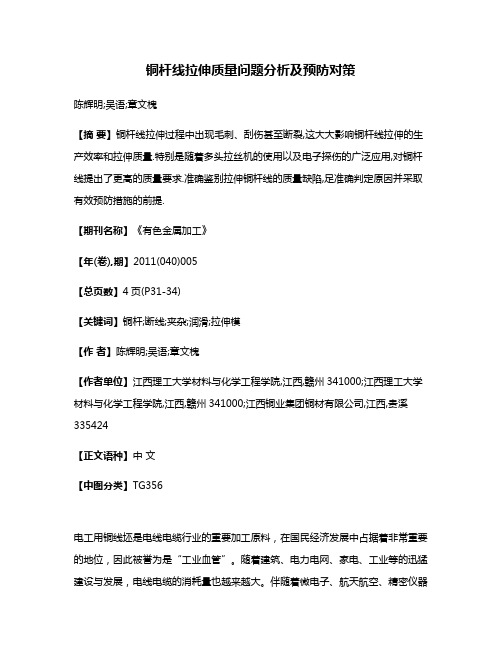
铜杆线拉伸质量问题分析及预防对策陈辉明;吴语;章文槐【摘要】铜杆线拉伸过程中出现毛刺、刮伤甚至断裂,这大大影响铜杆线拉伸的生产效率和拉伸质量.特别是随着多头拉丝机的使用以及电子探伤的广泛应用,对铜杆线提出了更高的质量要求.准确鉴别拉伸铜杆线的质量缺陷,足准确判定原因并采取有效预防措施的前提.【期刊名称】《有色金属加工》【年(卷),期】2011(040)005【总页数】4页(P31-34)【关键词】铜杆;断线;夹杂;润滑;拉伸模【作者】陈辉明;吴语;章文槐【作者单位】江西理工大学材料与化学工程学院,江西,赣州341000;江西理工大学材料与化学工程学院,江西,赣州341000;江西铜业集团铜材有限公司,江西,贵溪335424【正文语种】中文【中图分类】TG356电工用铜线坯是电线电缆行业的重要加工原料,在国民经济发展中占据着非常重要的地位,因此被誉为是“工业血管”。
随着建筑、电力电网、家电、工业等的迅猛建设与发展,电线电缆的消耗量也越来越大。
伴随着微电子、航天航空、精密仪器等尖端科学的不断发展,对电线电缆的规格、性能、质量的要求也越来越高。
同时,随着多头高速拉伸、电子探伤等拉伸设备的广泛运用,对铜杆线拉伸性能也同样提出了更高的要求。
铜杆线在拉伸过程中出现毛刺、刮伤等质量问题,将影响铜线产品质量,随着深层次的拉伸将最终导致断裂。
对漆包线则会产生漆瘤或者在无损探伤检测上出现探伤或电流击穿。
在拉伸过程中出现断裂,将直接影响生产效率,特别是在多头拉伸机上出现断线将增加大量的工作量。
因此,对铜杆线出现的质量问题样品进行分析、确定原因,并对应的采取有效措施,是不断提高铜杆线产品质量及铜杆线可拉性能的前提。
1 质量缺陷及分析1.1 空心断线空心断线在铜杆线拉伸中比较常见,空心断线的断头呈空心状或管状,断口光滑。
空心断线的形成原因主要是由于铸造过程产生的气孔形成的,并且气孔在后序轧制或拉伸中都不能得到完全的消除。
线材产品质量缺陷
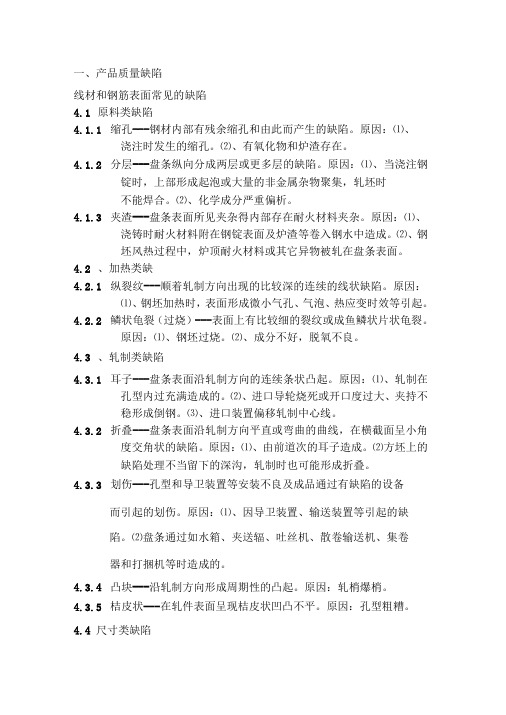
一、产品质量缺陷线材和钢筋表面常见的缺陷4.1原料类缺陷4.1.1缩孔---钢材内部有残余缩孔和由此而产生的缺陷。
原因:⑴、浇注时发生的缩孔。
⑵、有氧化物和炉渣存在。
4.1.2分层---盘条纵向分成两层或更多层的缺陷。
原因:⑴、当浇注钢锭时,上部形成起泡或大量的非金属杂物聚集,轧坯时不能焊合。
⑵、化学成分严重偏析。
4.1.3夹渣---盘条表面所见夹杂得内部存在耐火材料夹杂。
原因:⑴、浇铸时耐火材料附在钢锭表面及炉渣等卷入钢水中造成。
⑵、钢坯风热过程中,炉顶耐火材料或其它异物被轧在盘条表面。
4.2、加热类缺4.2.1纵裂纹---顺着轧制方向出现的比较深的连续的线状缺陷。
原因:⑴、钢坯加热时,表面形成微小气孔、气泡、热应变时效等引起。
4.2.2鳞状龟裂(过烧)---表面上有比较细的裂纹或成鱼鳞状片状龟裂。
原因:⑴、钢坯过烧。
⑵、成分不好,脱氧不良。
4.3、轧制类缺陷4.3.1耳子---盘条表面沿轧制方向的连续条状凸起。
原因:⑴、轧制在孔型内过充满造成的。
⑵、进口导轮烧死或开口度过大、夹持不稳形成倒钢。
⑶、进口装置偏移轧制中心线。
4.3.2折叠---盘条表面沿轧制方向平直或弯曲的曲线,在横截面呈小角度交角状的缺陷。
原因:⑴、由前道次的耳子造成。
⑵方坯上的缺陷处理不当留下的深沟,轧制时也可能形成折叠。
4.3.3划伤---孔型和导卫装置等安装不良及成品通过有缺陷的设备而引起的划伤。
原因:⑴、因导卫装置、输送装置等引起的缺陷。
⑵盘条通过如水箱、夹送辐、吐丝机、散卷输送机、集卷器和打捆机等时造成的。
4.3.4凸块---沿轧制方向形成周期性的凸起。
原因:轧梢爆梢。
4.3.5桔皮状---在轧件表面呈现桔皮状凹凸不平。
原因:孔型粗糟。
4.4尺寸类缺陷4.4.1横肋纵肋偏小---沿轧制方向形成的连续的偏小现象,原因:来料小,孔型充不满。
4.4.2、水平尺寸超标---沿扎制方向形成的连续超标现象。
⑴、来料大。
⑵、进口有倒钢现象。
线材的内部缺陷及其造成原因

线材的内部缺陷及其造成原因线材的内部缺陷是指在线材的内部破坏金属基体完整性的、影响产品质量的各种缺陷,包括局部不连续破裂、成分或结晶不均匀及外来异物等。
内部缺陷需要用取样或探测等手段来确定。
有的缺陷由表面延伸到内部,既是表面缺陷又是内部缺陷。
内部缺陷严重影响线材的性能。
内部缺陷可归纳为两类:一类是宏观的,可以通过酸浸低倍试样或断口时进行观察,或用无损探伤等办法,经肉眼检查和判别,如缩孔、气孔、疏松、分层非金属夹杂和过热、过烧等;另一类是微观缺陷,如晶粒度大小混晶、细小夹杂、组织不均、带状组织和网状组织等。
造成内部缺陷的原因有冶炼、连铸坯浇铸、热轧、控冷或热处理工艺的不合理等。
冶炼时钢液中含有过多的气体,过多的杂质如磷、硫、铅等;加入合金后成分混合不均;炉渣末除净等都影响钢的纯净度,危害产品质量。
浇铸过程是产生内部缺陷的又一来源,炉渣和脱氧产物的卷入,钢液二次氧化,外来异物及耐火材料的混入,浇铸温度过高、过低,冷却速度过快、过慢,热金属回填不够,都会导致出现缩孔、夹杂、裂纹、疏松和气孔等。
热轧时坯料加热温度过高或加热时间过长,会引起过热、过烧、晶粒粗大、表面氧化和脱碳;控温轧制时轧制温度和轧后控冷制度不合理将引起组织不均,或产生不利的组织形态、耳子:盘条表面沿轧制方向的条状凸起称为耳子。
出现在线材一侧的叫单面耳子,两侧的叫双面耳子和上下两个半圆错开的错边耳子。
有的耳子贯穿线材全长,也有的呈局部、断续或呈周期性分布。
产生的原因主要是成品孔轧槽过充满,多余的金属被挤到辊缝里。
在高速轧机生产线材时,线材头尾两端由于失去张力很难避免耳子的产生。
产生耳子的具体原因为:(1)孔型设计不合理、轧机调整不当或成品前孔磨损严重,造成成品孔压下量过大,产生双面耳子;(2)成品孔入口导板安装不正、不牢、间隙过大或轧件入孔型不正,易产生单面耳子或双面断续耳子;(3)轧制温度的波动或局部不均匀,影响轧件的宽展量不同,也可能出现耳子;(4)连轧机调整不良,产生堆钢、拉钢现象,堆钢时轧件中间出现耳子,拉钢时轧件头尾出现耳子;(5)成品前孔轧槽掉金属,轧件表面出现凸包,在成品孔中轧制时,将产生周期性耳子;(6)坯料的缺陷,如缩孔、偏析、分层及外来夹杂,影响轧件的正常变形,也是形成耳子的原因。
棒线材常见表面缺陷及成因

棒线材常见表面缺陷及成因线材常见的表面缺陷有裂纹、耳子、折叠、结疤(翘皮或鳞皮)、划痕、麻面、分层、氧化及脱碳等。
表面缺陷最大的危害就是降低线材的断面收缩率等塑性指标,从而影响冷拉加工性能。
1裂纹裂纹是指线材表面沿轧制方向有平直或弯曲、折曲,或以一定角度向线材内部渗透的缺陷。
主要典型缺陷为表面细小裂纹簇、单道长条裂纹、平行裂纹等,如图1[1]。
表面裂纹簇形貌单道线缺陷形貌平行裂纹形貌图1典型裂纹形貌图表面裂纹的形成与钢的化学成分和炼钢、轧制控制均有关系[2]-[4]。
轧制方面的原因:①轧槽表面磨损或损坏;②粗轧前几道导位划伤;③氧化铁皮被轧入轧件;④导位尺寸不合适或偏离轧制线;⑤高压水除鳞的冷却水路堵塞或偏离;⑥错辊;⑦表面保护、吊装方法不当等储运过程中的擦伤。
冶炼方面的原因:钢坯上未消除的裂纹、皮下气泡及非金属夹杂物,它们都会在线材表面造成裂纹。
炼钢时钢液未得到净化,在连铸坯加工中形成皮下夹杂,轧前加热,表层氧化,皮下夹杂逐渐裸露,随后轧制中脱落形成裂纹。
2耳子线材表面沿轧制方向的凸起称为耳子,根据生成的位置可分为:单边耳子、双边耳子及错边耳子[3]-[7]。
图2是实际生产中的耳子[3]。
图2耳子耳子主要是由于轧制方面的原因引起的[2]-[7]。
轧制方面的原因:①过充满,坯料尺寸过大,压下量过大;②入口导卫偏离轧制线、磨损严重或烧坏;③上下辊偏移量不合适引起错辊;④轧件温度不均匀引起变形不均匀;⑤连轧机设置不当引起的堆钢、拉钢。
炼钢方面的原因:冶炼-铸造引起坯料的缩孔、偏析、分层及外来夹杂等,轧制时,影响正常变形,也会导致耳子的出现。
3折叠钢铁表面形成沿轧制方向的各种角度的折线,一般为在横断面与表面呈小角度交角状缺陷,两侧一般伴有脱碳层或部分脱碳层,中间常存在氧化铁夹杂,图3[3]是典型的折叠。
图3折叠轧件折叠的很大一部分原因是前面轧制时形成的各种耳子。
此外,轧辊轴向固定不佳发生窜动;入口导卫磨损严重或烧损时钢坯咬入不稳定;炼钢提供的坯料存在缺陷,未清理等也会导致折叠[2]-[5]、[7]。
线材质量常见五大问题及措施.doc
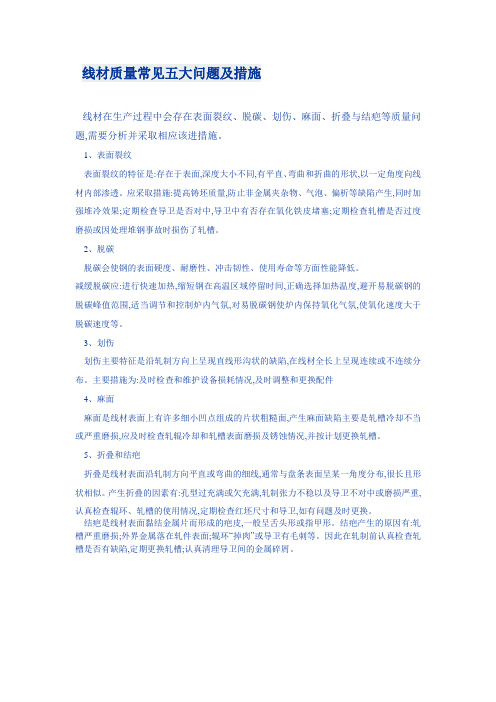
线材质量常见五大问题及措施线材在生产过程中会存在表面裂纹、脱碳、划伤、麻面、折叠与结疤等质量问题,需要分析并采取相应该进措施。
1、表面裂纹表面裂纹的特征是:存在于表面,深度大小不同,有平直、弯曲和折曲的形状,以一定角度向线材内部渗透。
应采取措施:提高铸坯质量,防止非金属夹杂物、气泡、偏析等缺陷产生,同时加强堆冷效果;定期检查导卫是否对中,导卫中有否存在氧化铁皮堵塞;定期检查轧槽是否过度磨损或因处理堆钢事故时损伤了轧槽。
2、脱碳脱碳会使钢的表面硬度、耐磨性、冲击韧性、使用寿命等方面性能降低。
减缓脱碳应:进行快速加热,缩短钢在高温区域停留时间,正确选择加热温度,避开易脱碳钢的脱碳峰值范围,适当调节和控制炉内气氛,对易脱碳钢使炉内保持氧化气氛,使氧化速度大于脱碳速度等。
3、划伤划伤主要特征是沿轧制方向上呈现直线形沟状的缺陷,在线材全长上呈现连续或不连续分布。
主要措施为:及时检查和维护设备损耗情况,及时调整和更换配件4、麻面麻面是线材表面上有许多细小凹点组成的片状粗糙面,产生麻面缺陷主要是轧槽冷却不当或严重磨损,应及时检查轧辊冷却和轧槽表面磨损及锈蚀情况,并按计划更换轧槽。
5、折叠和结疤折叠是线材表面沿轧制方向平直或弯曲的细线,通常与盘条表面呈某一角度分布,很长且形状相似。
产生折叠的因素有:孔型过充满或欠充满,轧制张力不稳以及导卫不对中或磨损严重,认真检查辊环、轧槽的使用情况,定期检查红坯尺寸和导卫,如有问题及时更换。
结疤是线材表面黏结金属片而形成的疤皮,一般呈舌头形或指甲形。
结疤产生的原因有:轧槽严重磨损;外界金属落在轧件表面;辊环“掉肉”或导卫有毛刺等。
因此在轧制前认真检查轧槽是否有缺陷,定期更换轧槽;认真清理导卫间的金属碎屑。
铜棒型线材缺陷
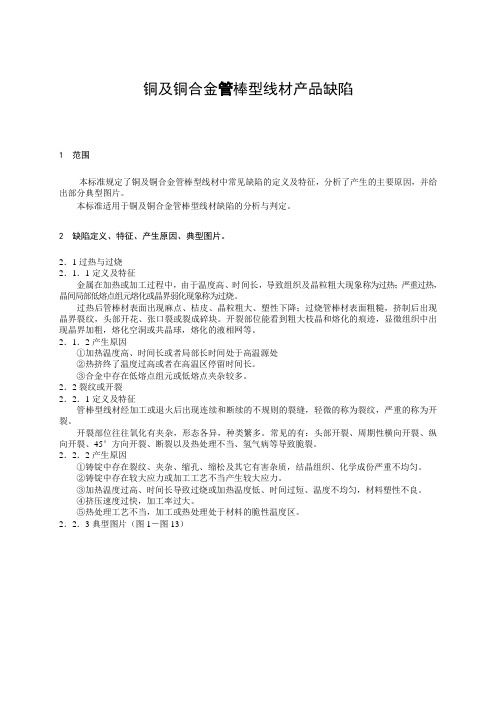
铜及铜合金管棒型线材产品缺陷1 范围本标准规定了铜及铜合金管棒型线材中常见缺陷的定义及特征,分析了产生的主要原因,并给出部分典型图片。
本标准适用于铜及铜合金管棒型线材缺陷的分析与判定。
2 缺陷定义、特征、产生原因、典型图片。
2.1过热与过烧2.1.1定义及特征金属在加热或加工过程中,由于温度高、时间长,导致组织及晶粒粗大现象称为过热;严重过热,晶间局部低熔点组元熔化或晶界弱化现象称为过烧。
过热后管棒材表面出现麻点、桔皮、晶粒粗大、塑性下降;过烧管棒材表面粗糙,挤制后出现晶界裂纹,头部开花、张口裂或裂成碎块。
开裂部位能看到粗大枝晶和熔化的痕迹,显微组织中出现晶界加粗,熔化空洞或共晶球,熔化的液相网等。
2.1.2产生原因①加热温度高、时间长或者局部长时间处于高温源处②热挤终了温度过高或者在高温区停留时间长。
③合金中存在低熔点组元或低熔点夹杂较多。
2.2裂纹或开裂2.2.1定义及特征管棒型线材经加工或退火后出现连续和断续的不规则的裂缝,轻微的称为裂纹,严重的称为开裂。
开裂部位往往氧化有夹杂,形态各异,种类繁多。
常见的有:头部开裂、周期性横向开裂、纵向开裂、45°方向开裂、断裂以及热处理不当、氢气病等导致脆裂。
2.2.2产生原因①铸锭中存在裂纹、夹杂、缩孔、缩松及其它有害杂质,结晶组织、化学成份严重不均匀。
②铸锭中存在较大应力或加工工艺不当产生较大应力。
③加热温度过高、时间长导致过烧或加热温度低、时间过短、温度不均匀,材料塑性不良。
④挤压速度过快,加工率过大。
⑤热处理工艺不当,加工或热处理处于材料的脆性温度区。
2.2.3典型图片(图1-图13)图1 QSn7-0.2 1×图2 QSi1-3 1×过烧引起头部开裂热挤头部开裂图3 QAl10-3-1.5 2/3×图4 BAl10-2 1×周期性横裂周期性横裂图5 QAl10-3-1.5 1/2×图6 QSn7-0.2 1/2×45°方向开裂 45°方向开裂图7 HSn70-1 1×图8 QSn7-0.2 1×周期性横裂周期性横裂图9 Cu-Ni合金 1×图10 H62 1×塑性不良引起周期性裂口 45°方向开裂图11 H62 1/2×图12 HSn70-1 1/2×纵向、45°方向交错开裂纵向开裂图13 QAl10-4-4 1/3×加热工艺不当引起纵向开裂2.3应力腐蚀开裂2.3.1定义及特征铜制品(黄铜或白铜)在拉应力和特定腐蚀环境共同作用下发生脆性开裂现象称为应力腐蚀开裂。
高速线材表面质量缺陷的产生原因及排除方法
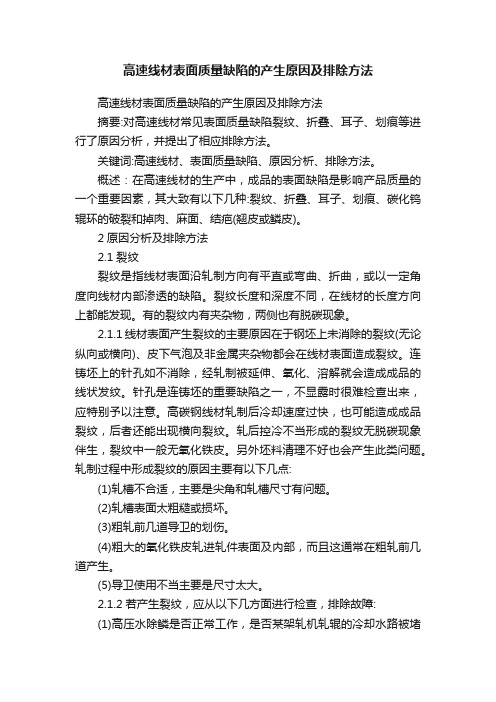
高速线材表面质量缺陷的产生原因及排除方法高速线材表面质量缺陷的产生原因及排除方法摘要:对高速线材常见表面质量缺陷裂纹、折叠、耳子、划痕等进行了原因分析,并提出了相应排除方法。
关键词:高速线材、表面质量缺陷、原因分析、排除方法。
概述:在高速线材的生产中,成品的表面缺陷是影响产品质量的一个重要因素,其大致有以下几种:裂纹、折叠、耳子、划痕、碳化钨辊环的破裂和掉肉、麻面、结疤(翘皮或鳞皮)。
2原因分析及排除方法2.1裂纹裂纹是指线材表面沿轧制方向有平直或弯曲、折曲,或以一定角度向线材内部渗透的缺陷。
裂纹长度和深度不同,在线材的长度方向上都能发现。
有的裂纹内有夹杂物,两侧也有脱碳现象。
2.1.1线材表面产生裂纹的主要原因在于钢坯上未消除的裂纹(无论纵向或横向)、皮下气泡及非金属夹杂物都会在线材表面造成裂纹。
连铸坯上的针孔如不消除,经轧制被延伸、氧化、溶解就会造成成品的线状发纹。
针孔是连铸坯的重要缺陷之一,不显露时很难检查出来,应特别予以注意。
高碳钢线材轧制后冷却速度过快,也可能造成成品裂纹,后者还能出现横向裂纹。
轧后控冷不当形成的裂纹无脱碳现象伴生,裂纹中一般无氧化铁皮。
另外坯料清理不好也会产生此类问题。
轧制过程中形成裂纹的原因主要有以下几点:(1)轧槽不合适,主要是尖角和轧槽尺寸有问题。
(2)轧槽表面太粗糙或损坏。
(3)粗轧前几道导卫的划伤。
(4)粗大的氧化铁皮轧进轧件表面及内部,而且这通常在粗轧前几道产生。
(5)导卫使用不当主要是尺寸太大。
2.1.2若产生裂纹,应从以下几方面进行检查,排除故障:(1)高压水除鳞是否正常工作,是否某架轧机轧辊的冷却水路被堵塞或偏离轧槽。
(2)导卫是否偏离轧制线,有无氧化铁皮堵塞在某个导卫中。
(3)轧槽是否过度磨损或因处理堆钢事故时损伤了轧槽。
(4)精轧机是否有错辊,导卫是否对中及尺寸是否对应于所轧的规格。
2.2折叠线材表面沿轧制方向平直或弯曲的细线,以任意角度渗入线材的表面内,在横断面上与表面呈小角度交角状的缺陷多为折叠,通常折叠较长,但亦有间断的不连续的,并在线材的长度方向上都有分布,折处的两侧伴有脱碳层或部分脱碳层,折叠中间常存在氧化铁夹杂。
铜合金管棒型材常见缺陷分析

铜合金管棒型材常见缺陷分析1、过热、过烧:定义:金属在加热或加工过程,由于温度高、时间长岛之组织及晶粒出大现象称为过热,严重过热时晶间决不低熔点组元熔化或晶界弱化现象称为过烧。
产生原因:a、加热温度高、时间长或局部长时间处于高温源处;b、热挤压终了温度过高或者在高温区停留时间长;c、合金中存在低熔点组元或低熔点杂质较多。
2、裂纹或开裂:定义:管棒型材表面出现连续或间断不规则裂纹,轻微的称为裂纹,严重的称为开裂。
产生原因:a、铸造锭中存在裂纹、夹杂、缩孔、疏松、冷隔或其他有害杂质或结晶组织、化学成分严重不均匀;b、铸锭中存在较大应力或加工工艺不当产生较大应力;c、挤压速度过快,加工率过大;d、热处理工艺不当,加工或热处理处于材料的脆性温度区。
3、缩尾:定义:缩尾是挤制品尾部的一种特殊缺陷。
在挤压末期,由于金属紊流,铸锭表面的氧化皮,润滑剂等污物往往流入其中,而导致金属之间的分层。
产生原因:a、挤压尾部金属流动紊乱;b、铸锭表面、次表面有缺陷,挤压筒有润滑剂等污染物。
4、鼓泡定义:经挤制、拉制、退货后的产品表面沿着加工方向拉长的条状鼓起,解剖开后为一空腔,这种鼓起称为鼓泡。
鼓泡多呈长条形,表面光滑,剖开内部有金属光泽,个别伴生氧化物或其他夹杂。
产生原因:a、铸锭中有气孔、缩孔、夹杂等缺陷,经挤压、拉伸、冷轧后沿加工方向形成分层;b、挤压筒润滑剂过量;c、挤制品缩尾未切除干净,经进一步拉伸后形成分层。
5、脱锌定义:含锌铜合金管棒型线材退火或酸洗后,表面出现灰白或泛红色斑现象称为脱锌。
轻微出现上述色斑,严重脱锌发生显微组织变化。
产生原因:a、退火温度过高,火焰直接喷到制品表面,使标卖弄锌熔化、挥发或氧化;b、挤压温度太高;c、酸洗时,酸液浓度过高,酸洗时间过长引起表面脱锌;d、在环境介质作用下,发生化学或电化学反应形成脱锌。
6、麻面(俗称麻点、沙眼)定义:管棒型线材表面出现微小的点状凹陷不平的粗糙面称为麻面。
棒线材产品质量缺陷及轧制事故及浅析1

棒线材产品质量缺陷及轧制事故浅析摘要:通过对棒线材中频繁出现的产品质量问题,轧制事故现象的分析,查找原因。
针对性采取措施,促进生产顺行,以提高产品质量及经济指标。
前言:我国是个钢铁生产大国,棒线材占总钢产量很大的比例,具有举足轻重的地位。
棒材线生产线形式仍就多样化,有先进的全连续高速轧制线,有半连续轧制线,甚至还有少量的经改造过的较为落后的生产线。
由于棒线材总产量很大,所以即使达到较高的成材率,其废品的绝对数量还是相当大的。
略钢有两条棒材线生产线,现就这两条生产线中常见的问题做以分析,探讨。
一、两条生产线介绍:1、二轧生产线建成于2008年7月,工艺平面布置如图(1).图(1)1)加热炉——全高炉煤气蓄热式连续推钢加热炉2)粗轧机组——600x3和500x3.3)中轧机组——420x6 4)精轧机组为:320x6 5)冷床为87.6mX12.5m.全线共18架短应力线轧机,均采用平-立交替布置,其中第14、16、、18架为平立可转换轧机,采用连续、无扭、高速轧制的先进生产工艺,设计最大轧制速度为17(18)m/s。
轧机以断面为150*150连铸坯为原料。
中轧机组后有预穿水装置,精轧机组后有穿水冷却装置。
设计年产量60万吨。
2、一轧生产线:这是一条由两火成材改成一火成材的较为落后的生产线。
其工艺布置见图(2)。
1)加热炉——全高炉煤气蓄热式加热炉2)粗轧——500穿梭轧制。
3)中轧——400x4连轧,350x2活套轧制4)精轧——310X6活套轧制5)冷床——60mx6m二、生产现状介绍略钢年产钢材约80万吨,其中二轧68万吨,品种规格为φ12到φ32的螺纹钢,生产制度是四班三运转,满负荷生产;一轧年产量12万吨,以φ12到φ16的圆钢和螺纹钢作为补充,未达到满负荷。
2009年产品合格率99%,轧废约7800吨,验废1240吨。
在生产中常见的产品缺陷有:耳子、折叠、成品尺寸不合格、脱圆、刮伤、力学性能不合等。
- 1、下载文档前请自行甄别文档内容的完整性,平台不提供额外的编辑、内容补充、找答案等附加服务。
- 2、"仅部分预览"的文档,不可在线预览部分如存在完整性等问题,可反馈申请退款(可完整预览的文档不适用该条件!)。
- 3、如文档侵犯您的权益,请联系客服反馈,我们会尽快为您处理(人工客服工作时间:9:00-18:30)。
铜及铜合金管棒型线材产品缺陷1 范围本标准规定了铜及铜合金管棒型线材中常见缺陷的定义及特征,分析了产生的主要原因,并给出部分典型图片。
本标准适用于铜及铜合金管棒型线材缺陷的分析与判定。
2 缺陷定义、特征、产生原因、典型图片。
2.1过热与过烧2.1.1定义及特征金属在加热或加工过程中,由于温度高、时间长,导致组织及晶粒粗大现象称为过热;严重过热,晶间局部低熔点组元熔化或晶界弱化现象称为过烧。
过热后管棒材表面出现麻点、桔皮、晶粒粗大、塑性下降;过烧管棒材表面粗糙,挤制后出现晶界裂纹,头部开花、张口裂或裂成碎块。
开裂部位能看到粗大枝晶和熔化的痕迹,显微组织中出现晶界加粗,熔化空洞或共晶球,熔化的液相网等。
2.1.2产生原因①加热温度高、时间长或者局部长时间处于高温源处②热挤终了温度过高或者在高温区停留时间长。
③合金中存在低熔点组元或低熔点夹杂较多。
2.2裂纹或开裂2.2.1定义及特征管棒型线材经加工或退火后出现连续和断续的不规则的裂缝,轻微的称为裂纹,严重的称为开裂。
开裂部位往往氧化有夹杂,形态各异,种类繁多。
常见的有:头部开裂、周期性横向开裂、纵向开裂、45°方向开裂、断裂以及热处理不当、氢气病等导致脆裂。
2.2.2产生原因①铸锭中存在裂纹、夹杂、缩孔、缩松及其它有害杂质,结晶组织、化学成份严重不均匀。
②铸锭中存在较大应力或加工工艺不当产生较大应力。
③加热温度过高、时间长导致过烧或加热温度低、时间过短、温度不均匀,材料塑性不良。
④挤压速度过快,加工率过大。
⑤热处理工艺不当,加工或热处理处于材料的脆性温度区。
2.2.3典型图片(图1-图13)图1 QSn7-0.2 1×图2 QSi1-3 1×过烧引起头部开裂热挤头部开裂图3 QAl10-3-1.5 2/3×图4 BAl10-2 1×周期性横裂周期性横裂图5 QAl10-3-1.5 1/2×图6 QSn7-0.2 1/2×45°方向开裂 45°方向开裂图7 HSn70-1 1×图8 QSn7-0.2 1×周期性横裂周期性横裂图9 Cu-Ni合金 1×图10 H62 1×塑性不良引起周期性裂口 45°方向开裂图11 H62 1/2×图12 HSn70-1 1/2×纵向、45°方向交错开裂纵向开裂图13 QAl10-4-4 1/3×加热工艺不当引起纵向开裂2.3应力腐蚀开裂2.3.1定义及特征铜制品(黄铜或白铜)在拉应力和特定腐蚀环境共同作用下发生脆性开裂现象称为应力腐蚀开裂。
裂纹垂直于应力方向,断口呈脆性,多为突发性。
2.3.2产生原因材料存在拉应力并对应力腐蚀敏感,存在能引发腐蚀的介质,如硝酸盐、氨蒸气及溶液、汞盐溶液、二氧化硫大气、硫酸蒸汽、水蒸汽等。
2.3.3典型图片(图14-图17)图14 QSn7-0.2 2/3×图15 H65 1/2×应力腐蚀开裂应力腐蚀开裂图16 H65 1/2×图17 HSn70-1A 1/2×应力腐蚀开裂应力腐蚀开裂2.4缩尾2.4.1定义及特征缩尾是挤制品尾部的一种特殊缺陷。
在挤压末期,由于金属紊流,铸锭表面的氧化皮,润滑剂等污物往往流入其中,而导致金属之间的分层。
缩尾一般在制品横截面上呈环形、弧形或月牙形,个别多孔挤压缩尾呈条状,从中心向边缘延伸。
位于制品中心横断面上长度小而严重的称为中心缩尾,位于稍外层呈环状或弧形的称为环状缩尾,位于制品表面的称为皮下缩尾,多孔挤压还出现各种形状的缩尾。
2.4.2产生原因①挤压尾部金属流动紊乱。
②铸锭表面、次表面有缺陷,挤压筒有润滑剂等污染物。
2.4.3典型图片(图18-图23)图18 T2 1/3×图19 HAl59-3-6 2/3×皮下缩尾环状缩尾图20 TU1 1/3×图21 TU1 1/3×中心缩尾中心缩尾图22 HPb59-1 1×图23 HPb58-2.5 1/2×多孔挤压特殊缩尾多孔挤压特殊缩尾2.5断口缺陷2.5.1定义及特征挤制品折断后,断口上出现针孔、夹杂、分层、撕裂、缩尾、层状断口及黄色组织,或者由于组织不均匀导致的其它缺陷统称为断口缺陷。
2.5.2产生原因①铸锭中存在气孔、缩孔、缩松、夹杂、分层、组织不均匀等缺陷。
②加热或挤压工艺不当。
2.5.3典型图片(图24-图37)图24 QBe2.0 1×图25 QAl10-3-1.5 2/3×断口针孔断口夹杂图26 QAl10-3-1.5 1/2×图27 HPb59-1 1/2×断口分层断口撕裂图28 HPb59-1 1/2×图29 T2 1/2×断口缩尾多孔挤压缩尾拉伸断口图30 HPb59-1 1×图31 QTi6.0 2/3×多孔挤压断口缩尾特殊缩尾折断实物图32 QAl10-3-1.5 1/2×图33 QAl10-3-1.5 1×层状断口图32的局部图34 QAl10-3-1.5 1/2×图35 HPb59-1 1/2×层状断口黄色组织图37 HPb59-1 1×黄色组织图37 HPb59-1 1×黄色组织2.6鼓泡2.6.1定义及特征挤制品或经拉伸、退火后的制品表面沿加工方向拉长的条状鼓起,剖开后为一空腔,这种鼓起称为鼓泡。
鼓泡多呈长条形,表面光滑,剖开内部有金属光泽,个别伴生氧化物或其它夹杂。
2.6.2产生原因①铸锭存在气孔、缩孔、缩松等缺陷。
②挤压筒、穿孔针润滑过量,挤压筒清理不干净,穿孔针有裂纹。
③坯料退火炉内气氛控制不当,炉温过高。
④铸锭与挤压筒、挤压垫配合不良。
2.7分层2.7.1定义及特征管棒型线材沿加工方向剖开后呈现缝隙称为分层。
层与层之间接触平整,有些有氧化色或夹杂;断口检查,出现断口分层现象。
2.7.2产生原因①铸锭中有气孔、缩孔、夹杂等缺陷,经挤压、拉伸、冷轧后沿加工方向形成分层。
②挤压筒或穿孔针润滑过量,穿孔针有裂纹。
③挤制品缩尾未切净,经进一步拉伸、轧制形成分层。
2.7.3典型图片(图38)图38 QAl10-3-1.5 2/5×分层2.8成份不均2.8.1定义及特征管棒型线材经退火加工后,不同部位化学成份存在较大差异现象称为成份不均,成份不均能引起颜色或变形特性差异,宏观检验往往能看到成份偏析区或偏析点,显微组织和性能有差异。
2.8.2产生原因①铸锭成份偏析、反偏析合金表面车铣不彻底。
②退火导致的脱锌。
2.8.3典型图片(图39-图40)图39 QAl9-2 1/4×图40 QAl9-2 70×成份不均中心低铝区图39交界处高倍组织2.9机械损伤外力作用于管棒型线材表面和管材内壁,而引起内外表面呈条状、束状、凹坑状尖锐沟槽状及其它形状的伤痕,统称为机械损伤。
常见的有:擦伤、划伤、碰伤、压伤等。
2.9.1擦伤2.9.1.1定义及特征物体之间接触后相对滑动或错动而引起管棒型线材内外表面成束状分布的伤痕称为擦伤。
2.9.1.2产生原因①工模具清理不当,润滑不良,磨损有变形或有裂纹,出料台导板等不光滑。
②金属表面粘附有异物或金属粘附在挤压模、穿孔针、或拉伸模工作带上。
2.9.2划伤2.9.2.1定义及特征尖锐物体与管棒型线材表面接触后产生相对滑动而引起条状、尖锐沟槽状伤痕称为划伤。
2.9.2.2产生原因①加工工具有棱角,冷加工工具表面脱铬,润滑剂中有硬颗粒异物,润滑不良。
②管棒材表面的棱角,相互划伤。
③金属表面或工模具上粘附有硬的异物。
2.9.3碰伤、压伤2.9.3.1定义及特征物体碰撞管棒型线材表面而引起碰伤,硬物压在管棒型线材表面引起压伤。
2.9.3.2产生原因①装料、捆绑、运输过程中碰撞、压靠。
②管棒材之间及外来硬物的碰撞、压靠。
2.10偏心、破肚2.10.1定义及特征管材挤压后,断面上厚度不均匀现象称为偏心。
若挤压偏心管或管材偏心严重,从侧面挤穿或者管材严重偏心经进一步拉伸造成破肚。
2.10.2偏心产生原因①铸锭加热温度不均匀,或铸坯端部不平整。
②铸坯未充填就挤压或穿孔针前头秃或弯曲。
③设备中心线不一致,挤压轴根部、端面斜或安装不正。
④挤压筒、模座、垫片、磨损配合不好,尺寸不合适。
2.10.3破肚产生原因①锭坯温度过高,不均匀。
②挤压速度过快,挤压系数太小。
③挤压模孔设计不合理或变形,穿孔针弯曲。
2.10.4典型图片(图41-图42)图41 BFe10-1-1 1/2×图42 BAl13-3 1/2×偏心破肚2.11型材扭拧2.11.1定义及特征型材挤压后出现扭拧现象称为型材扭拧,俗称麻花。
2.11.2产生原因①铸锭加热温度不均匀,挤压工具设计安装不合理、润滑不均匀等原因导致金属流动不均匀。
2.12撕裂2.12.1定义及特征管棒材挤压或扒皮后,表面出现沿加工方向分布的片状、条状伤痕现象称为撕裂。
撕裂部位有金属色泽,个别有夹杂等缺陷。
2.12.2产生原因①铸锭表面不平,有夹杂、裂纹等缺陷。
②挤压模具设计安装不合理,润滑不良,金属流动不均。
③扒皮模不锋利,设计安装不合理。
④扒皮工艺不合理。
2.12.3典型图片(图43-图44)图43 QAl9-4 1/4×撕裂图44 TP2 1/2×撕裂(扒皮)2.13夹杂2.13.1定义及特征管棒型线材表面和内部出现的与基体有明显分界面,性能相差悬殊的金属或非金属物称为夹杂。
夹杂一般呈颗粒状、长条状沿加工方向分布,有一定颜色和形态,界面明显。
常见有金属夹杂和非金属夹杂。
2.13.2产生原因①铸锭中未熔化完的纯金属颗粒、大块初晶或异金属进入。
②金属氧化物、硫化物及其它金属化合物。
③硅酸盐,覆盖剂等非金属化合物。
2.13.3典型图片(图45-图46)图45 H85 1/3×图46 H85 1×硼砂夹杂图45的局部2.14异物压入2.14.1定义及特征金属或非金属压入管棒型线材表面称为异物压入。
金属压入物与基体有明显分界面,轮廓清晰,有不同的金属光泽,呈点状、块状,剥离后形成凹坑;非金属压入物形态不一,颜色各异,多呈脆性,无金属光泽,呈点状、长条状沿加工方向分布,不易剥离。
2.14.2产生原因①加热温度过高形成的氧化皮、润滑剂粘附在工模具和制品表面。
②工模具的碎片及粘附物。
③金属屑及毛刺,热处理炉的炉屑油污。
④轨道及导板上的异物。
2.14.3典型图片(图47)图47 BFe30-1-1 1×铁块压入2.15表面起皮、起刺2.15.1定义及特征制品表面局部破裂翻起称为起皮。