开题报告---350万吨年常减压蒸馏装置常压加热炉设计
常减压蒸馏装置课程设计

常减压蒸馏装置课程设计一、课程目标知识目标:1. 让学生掌握常减压蒸馏装置的基本原理和结构组成,理解其在石油化工行业中的应用。
2. 使学生了解常减压蒸馏过程中温度、压力等参数对馏分组成的影响,掌握相关计算方法。
3. 帮助学生掌握常减压蒸馏装置的操作步骤和安全注意事项。
技能目标:1. 培养学生运用所学知识分析和解决实际问题的能力,能对常减压蒸馏过程进行模拟计算。
2. 提高学生的实验操作技能,能熟练使用常减压蒸馏装置进行实验。
3. 培养学生的团队协作能力和沟通能力,能在实验过程中进行有效沟通和协作。
情感态度价值观目标:1. 培养学生对化学工程学科的兴趣,激发他们学习化学工程的热情。
2. 培养学生严谨的科学态度,注重实验数据的准确性和实验操作的规范性。
3. 增强学生的环保意识,让他们认识到化学工艺在环境保护中的重要性。
课程性质:本课程为化学工程学科的专业课程,以理论教学和实验操作相结合的方式进行。
学生特点:学生为本科三年级学生,已具备一定的化学基础和实验操作技能。
教学要求:结合学生特点和课程性质,注重理论与实践相结合,提高学生的实际操作能力和解决实际问题的能力。
在教学过程中,关注学生的学习进度,及时调整教学方法和内容,确保学生能够达到预期的学习成果。
二、教学内容1. 基本原理:讲解蒸馏的基本原理,包括相平衡、蒸馏曲线等,结合教材第2章内容,让学生理解常减压蒸馏的原理。
2. 装置结构:介绍常减压蒸馏装置的组成部分,如加热炉、塔体、冷凝器等,参照教材第3章,让学生了解装置结构及其作用。
3. 影响因素:分析温度、压力等参数对馏分组成的影响,结合教材第4章,让学生掌握相关计算方法。
4. 操作步骤:详细讲解常减压蒸馏装置的操作步骤,包括开停车、调节温度、压力等,参照教材第5章,让学生了解实际操作过程。
5. 安全注意事项:强调实验操作过程中的安全事项,如防火、防爆、防中毒等,结合教材第6章,提高学生的安全意识。
6. 实验教学:组织学生进行常减压蒸馏实验,包括实验方案设计、实验操作、数据处理等,参照教材第7章,培养学生的实验操作技能和数据分析能力。
常减压蒸馏装置实习报告

常减压蒸馏装置实习报告一、前言在我国的炼油行业中,常减压蒸馏装置是炼油厂的核心装置之一,主要负责将原油进行初步加工,分离出各种轻、重的中间产品,作为下游装置的加工原料。
我作为一名实习生,有幸参与了某炼油厂的常减压蒸馏装置的实习,通过这次实习,我对常减压蒸馏装置的工艺流程、操作要点以及安全注意事项有了更深入的了解。
二、常减压蒸馏装置概述常减压蒸馏装置主要包括初馏塔、常压塔和减压塔三个部分。
初馏塔主要用来分离原油中的轻组分,如石脑油、汽油等;常压塔则用于分离柴油、润滑油等中间产品;减压塔则负责分离出重柴油、渣油等重质产品。
三、实习过程1. 原油脱盐、脱水在常减压蒸馏装置中,原油首先需要经过电脱盐系统进行脱盐、脱水处理,以减少对设备的腐蚀和影响产品质量。
脱盐后的原油温度约为215-230℃,然后进入初馏塔。
2. 初馏塔操作初馏塔主要用于分离原油中的轻组分。
从初馏塔顶蒸馏出的初馏点-130℃的馏分冷凝冷却后,其中一部分作为塔顶回流,另一部分引出作为重整原料或较重汽油,又称初顶油。
初馏塔底拔头原油经过常压加热炉加热到350-365℃,进入常压分馏塔。
3. 常压塔操作常压塔主要用于分离原油中的柴油、润滑油等中间产品。
塔顶打入冷回流,使塔顶温度控制在90-110℃。
从塔顶到进料段温度逐渐上升,利用馏分沸点范围不同,塔顶蒸出汽油,依次从侧一线、侧二线、侧三线分别蒸出煤油、轻柴油、重柴油。
这些侧线馏分经常压气提塔用过热水蒸气提出轻组分后,经换热回收一部分热量,再分别冷却到一定温度后送出装置。
塔底约为350℃,塔底未汽化的重油经过热水蒸汽提出轻组分后,作减压塔进料油。
4. 减压塔操作减压塔主要负责分离出重柴油、渣油等重质产品。
常压塔底重油用泵送入减压加热炉,加热到390-400℃进入减压分馏塔。
塔顶不出产品,分出的不凝气经冷凝冷却后,通常用二级蒸汽喷射器抽出不凝气,使塔内保持残压1.33-2.66kPa,以利于在减压下使油品充分蒸出。
400万吨年原油蒸馏常压炉工艺设计
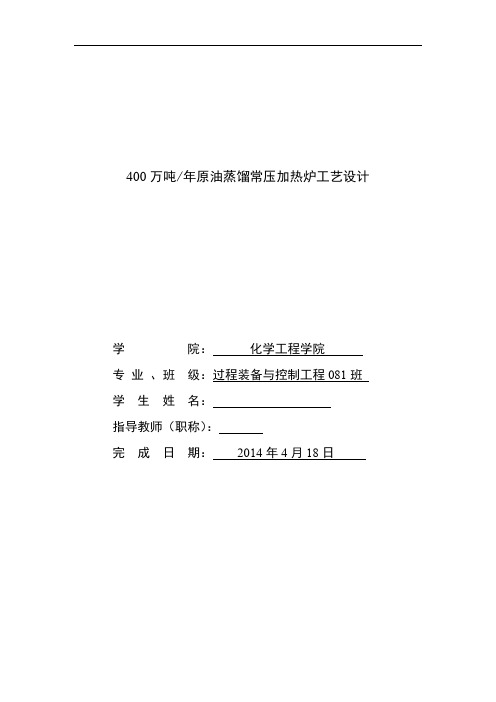
400万吨/年原油蒸馏常压加热炉工艺设计学院:化学工程学院专业、班级:过程装备与控制工程081班学生姓名:指导教师(职称):完成日期:2014年4月18日400万吨/年原油蒸馏常压加热炉工艺设计总计:毕业论文:56页表格:5个插图:9幅指导教师:评阅人:完成日期:2014年4月18日400万吨/年原油蒸馏常压加热炉工艺设计摘要管式加热炉是一种火力加热设备,它利用燃料在炉膛内燃烧时产生的高温火焰与烟气作为热源,加热在炉管中高速流动的介质,使其达到工艺规定的温度,以供给介质在进行分馏、裂解或反应等加工过程中所需要的热量,保证生产正常进行。
本设计为年产350万吨/年原油圆筒加热炉,在本设计中,主要完成对辐射段、对流段以及烟道的工艺尺寸的计算、热量的衡算、钢结构的计算及校核和加热炉各零部件的选用。
其中辐射室工艺尺寸包括辐射室炉管的直径、炉管的壁厚、炉管的长度、炉管的根数、辐射室的外形尺寸等;对流室的工艺尺寸包括对流炉管的形式、炉管的直径、炉管的壁厚、炉管的排数及每排的根数、热量衡算的部分包括计算热负荷、燃料量、燃烧器的规格和根数。
本设计的要点是加热炉高的热效率,提高燃油的利用率。
常采用的措施有降低炉子的排烟温度、减小过热空气系数、减少化学部完全燃烧损失、减少机械不完全燃烧损失、减少炉壁散热等。
也可以设置烟气余热回收系统来提高加热炉的热效率。
关键字:加热炉;炉管;辐射;对流400万吨/年原油蒸馏常压加热炉工艺设计AbstractTubular-furnace heating equipment is a kind of firepower, which the use of fuel combustion in the furnace when the flame and flue gas temperature as a heat source, heating in the furnace tube in the high-speed flow of medium to reach the process temperature requirements, in order to supply medium during fractionation, decomposition or reaction process, such as the heat required to ensure normal production.The design for the annual production capacity of three million fifty tons of crude oil Cylindrical furnace, in the completion of the design of the main paragraph of radiation, convection, as well as the size of the stack process, the heat balance, steel structure and the calculation and checking Selection of the various furnace components. Room size radiation technology, including radiation chamber furnace tube diameter, tube wall thickness, tube length, the root of the number of tube radiation, such as room dimensions; convection process room size, including the form of convection furnace tubes, furnace tube diameter, wall thickness of the tube, the tube row number and the root of the number of each row, the heat balance calculation of the part, including fuel, the specifications of the burner and root number.The gist of the present furnace design with high thermal efficiency and fuel utilization. Measures often used to reduce the furnace flue gas temperature, reducing the over-heated air coefficient, the Department of incomplete combustion to reduce the loss of chemicals to reduce the mechanical loss of incomplete combustion, reduce heat, such as furnace wall. Flue gas can also be set up waste heat recovery system to increase the thermal efficiency of furnace.Keywords: Furnace;Furnace tube;Radiation;Convection400万吨/年原油蒸馏常压加热炉工艺设计目录1. 概述 (1)1.1 课题背景 (1)1.2 本课题发展方向 (1)1.3 管式加热炉的一般结构 (2)1.3.1 辐射室 (2)1.3.2 对流室 (2)1.3.4 燃烧器 (3)1.3.5 通风系统 (8)1.4 管式加热炉的种类 (9)1.5 炉型选用的基本原则 (10)2. 工艺计算 (12)2.1 加热炉热负荷的确定 (12)2.1.1 燃料性质及工艺条件 (12)2.1.2 加热炉热负荷计算 (12)2.2 燃料燃烧过程计算 (13)2.2.1 燃烧的发热量 (13)2.2.2 理论空气量 (13)2.2.3 烟气量及烟气组成 (14)2.3 热效率计算 (15)2.3.1 加热炉的热平衡 (15)2.3.2 燃料用量 (17)2.3.3 加热炉热效率 (18)2.4 辐射段计算 (18)2.4.1 辐射段热负荷 (18)2.4.2 辐射段平均管外壁温度计算 (18)2.4.3 辐射管加热表面积 (19)2.4.4 辐射管管程及管程数 (19)2.4.5 辐射段炉体尺寸 (20)2.4.6 节圆直径和炉管直径 (21)2.4.7 炉膛高度 (21)2.5 对流段尺寸计算 (22)2.5.1 对流室外形长度 (22)2.5.2 对流室宽度 (22)2.6 热平衡计算 (23)2.6.1 当量冷平面 (23)2.6.2 辐射总面积 (23)2.6.3 对辐射段管根数的验算 (24)400万吨/年原油蒸馏常压加热炉工艺设计2.6.4 辐射段烟气计算 (24)3.6.5 辐射段热平衡 (26)2.6.6 辐射段实际排烟温度 (26)2.6.7 辐射段实际热负荷.......................................... 错误!未定义书签。
常减压蒸馏装置实训报告

一、实训目的本次实训旨在通过模拟常减压蒸馏装置的实际操作过程,使学生了解并掌握常减压蒸馏的基本原理、工艺流程、设备构造以及操作规程,提高学生对炼油工艺的认识和实践操作能力。
二、实训时间2023年X月X日至X月X日三、实训地点XX炼油厂常减压蒸馏装置实训室四、实训内容1. 常减压蒸馏装置简介常减压蒸馏装置是炼油厂中最关键的单元操作之一,主要用于将原油通过加热和蒸馏的方式,分离出汽油、煤油、柴油、重油等不同沸点范围的组分。
本次实训主要涉及常压蒸馏和减压蒸馏两部分。
2. 设备构造与操作规程(1)常压蒸馏部分:主要包括加热炉、常压塔、冷凝器、回流罐等。
加热炉用于将原油加热至沸点,常压塔用于分离不同沸点的组分,冷凝器用于冷却蒸气,回流罐用于回收部分蒸气。
(2)减压蒸馏部分:主要包括减压加热炉、减压塔、冷凝器、回流罐等。
减压加热炉用于将重油加热至沸点,减压塔用于分离不同沸点的组分,冷凝器用于冷却蒸气,回流罐用于回收部分蒸气。
3. 操作规程(1)启动装置:先开启加热炉,加热原油至沸点,然后开启常压塔和减压塔的进料阀门,开始蒸馏操作。
(2)调节温度:根据不同组分沸点的差异,调节加热炉温度,使原油在常压塔和减压塔中充分分离。
(3)调节压力:根据不同组分沸点的差异,调节减压塔的压力,使重油在减压条件下充分分离。
(4)收集产品:根据不同组分沸点的差异,收集汽油、煤油、柴油等不同沸点范围的组分。
(5)停止装置:关闭加热炉和进料阀门,关闭常压塔和减压塔的进料阀门,停止蒸馏操作。
五、实训过程1. 设备操作在实训老师的指导下,学生依次进行加热炉、常压塔、减压塔、冷凝器、回流罐等设备的操作,掌握设备的启停、温度调节、压力调节等操作技能。
2. 数据记录学生在实训过程中,记录原油进料量、加热炉温度、常压塔和减压塔压力、产品产量等数据,为后续分析提供依据。
3. 产品分析学生根据收集到的数据,分析不同组分沸点的差异,以及常压蒸馏和减压蒸馏的效果。
350万吨常减压车间工艺设计论文
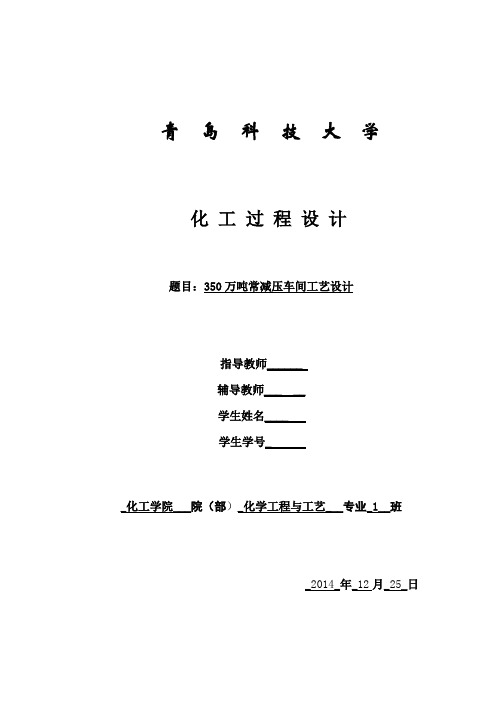
青岛科技大学化工过程设计题目:350万吨常减压车间工艺设计指导教师______辅导教师___ __学生姓名____学生学号__化工学院___院(部)_化学工程与工艺___专业_1__班_2014_年_12月_25_日目录中文摘要在本次设计中,我针对350万吨/年的常减压车间进行工艺设计。
内容主要包括:概述、工艺设计及计算、设备一览表、车间设备布置、非工艺部分设计、自动控制、安全与环境保护及个人的设计体会等。
其中最主要的部分是工艺设计及计算部分,其主要包含:物料衡算、能量衡算及主要设备的设计选型计算。
该计算主要利用Aspen Plus软件模拟的结果。
另外,我还用Auto CAD软件绘制了带控制点的工艺流程图、设备图和车间的平立面布置图。
关键词:工艺设计及计算;带控制点的工艺流程图;平立面布置图;ASPEN模拟1总论1.1胜利炼油厂简介中国石化集团齐鲁石化公司胜利炼油厂是全国颇具规模的炼油企业之一,于1966年4月动工建设,1967年10月投入生产,现已成为加工能力10500kt/a,占地面积587公顷的现代化石油加工企业。
该厂拥有生产装置和辅助生产装置60余套,拥有相应配套的科学研究、开发设计、计算机应用、环境保护等设施,是全国最具影响力的含硫原油加工以及沥青、硫磺生产和加氢工艺技术应用基地之一,生产的39种石油产品畅销全国27个省市,部分产品已进入国际市场。
胜利炼油厂坚持依靠科技求发展。
该厂VRDS-FCC组合工艺曾获联合国科技创新发明奖;石油苯、-10号军用柴油等产品曾获国家金奖;100号甲级道路沥青、1号喷气燃料、石油甲苯等产品曾获国家银奖;硫磺、90号车用汽油等18种产品曾获省(部)优名牌产品称号;汽油全部实现了高标号无铅系列化生产,其中97号无铅汽油填补了国内空白;1999年开发投产的高等级道路沥青,技术指标达到或超过了国外同类产品水平,从而标志着胜利炼油厂的沥青产品实现了系列化。
按照“质量第一,用户至上”的原则,胜利炼油厂建立了从原材料进厂、生产过程控制、新产品开发、标准化管理、产品出厂控制到售后服务的全过程质量控制保证体系。
优化燃料气管网,确保装置稳定运行

优化燃料气管网,确保装置稳定运行摘要:烯烃运行部供炼油运行部火炬气、轻烃回收装置三顶气脱硫单元干气并入燃料气管网位置不合理,影响350万吨/年常减压装置加热炉稳定运行,通过实施燃料气管网优化项目,调整火炬气、干气并入燃料气管网位置,使其与炼油运行部其他燃料气组分充分混合,实现350万吨/年常减压装置燃料气组成稳定,确保装置稳定运行,产品质量达标。
关键字:燃料气管网、流程优化、信息化石化企业的燃料气主要来自生产过程中副产的小分子“炼厂气”,主要由甲烷、乙烷、氢气、硫化氢等物质组成[1]。
在“高氢气燃料气”的工况下,由于燃料气密度小,提供既定功率的热量时,需要更大的燃料气流量。
在“高丙烷燃料气”的工况下,由于燃料气密度大,提供既定功率的热量时,只需要较小的燃料气流量。
同时企业的应急“补烃”会严重扰乱加热炉的平稳操作[2]。
因此优化公司燃料气管网运行,提升管理能力,确保加热炉稳定运行、环保达标已迫在眉睫。
一、燃料气管网运行现状公司燃料气来源复杂,主要包括催化干气、PSA渗余气、脱硫干气、火炬气、裂解副产燃料气、芳烃尾气、液化气、天然气等。
因燃料气用户较多,管网复杂,除新建油化运行部外,产气及用气装置均就近接入或引自燃料气管网。
目前350万吨/年常减压装置燃料气组成波动较大,严重影响装置的稳定运行及环保达标。
二、燃料气管网问题原因分析为精确分析350万吨/年常减压装置燃料气组成波动原因,对燃料气管网组成进行动态分析,并对分析结果进行统计、分析。
表1 各装置燃料气组成分析(%vol)350万吨/年常减压装置燃料气组成波动较大,主要原因为燃料气中重组分(C4、C5)含量大幅波动,燃料气热值波动大,可能造成加热炉烟气出现NO x等超标、装置生产波动。
图1 350万吨/年常减压装置燃料气组成变化(%vol)通过对350万吨/年常减压装置燃料气来源、组成进行分析,分析其波动原因如下:烯烃运行部火炬气的影响:烯烃运行部不含硫火炬气通过火炬回收压缩机送至350万吨/年常减压装置燃料气缓冲罐前。
5.0Mt·a~(-1)常减压蒸馏装置常压加热炉改造

4 .3 24 MW, 是设 计 热负荷 的 10 3 , 最 终 排 烟温 0.% 但
度高达 2 0 , 效率 只有 8 . 8 。 4℃ 热 7 5%
文章对 常压炉 热效 率低 的原 因进 行 了分析 , 实 施 了 改进 措 施 , 果 表 明 , 热 炉 烟气 排 放 温 度 结 加
第2 7卷
第 9期
甘肃科 技
Ga u S in e a d Te hn l g ns c e c n c oo y
i f2 ,_7 o
Ⅳo 9 .
21 0 1年 5月
Ma . 2 1 r 01
5 O ・ 常减 压蒸 馏 装 置 常压 加 热 炉 改 造 . Mt a
常压炉 平 均 炉 膛 温 度 为 7 1C, 过 后 置 空 气 4 经 o 预 热 器 后 烟 气 的 排 放 温 度 达 到 20C, 设 计 值 4 ̄ 较 10 5 %高 9  ̄ 0C。对流 室传 热条件见 表 1 。
表 1 对流 室传 热 条 件
从表 1看 , 流 室 油 与 烟 气 换 热 时 , 气 温 降 对 烟 19 , 5 ℃ 对数 平 均 温 差 达 到 38 , 面热 热 强 度 为 4℃ 表
的大小 未 变 , 是 4个 进 口位 置 比改 造 前 抬 高 了 2 只 排管位 。改造后 管位 对 照如 图 1所示 。
1 0
甘
肃
科
技
第2 7卷
2 2 炉 墙 内壁做 喷涂 .
本次改造在辐射室炉墙内壁喷涂型隔热材料 , 降低炉墙外表面温度 , 减小散热损失。
3 改造效果及讨论
下 降 5 ℃ , 体 表 面 温 度 下 降 lc , 料 消 耗 下 4 炉 5《 燃 = 降 1 % , 热 炉 效 率 由 8 .8 上 升 到 8 .8 , 3 加 75% 98%
450万吨年原油常减压蒸馏装置工艺设计

1 课题的目的与意义原油是极其复杂的混合物,通过原油的蒸馏可以按所制定的产品方案将其分割成直馏汽油、煤油、轻柴油或重柴油馏分及各种润滑油馏分和渣油等[1]。
原油蒸馏是石油加工中第一道不可少的工序,故通常称原油蒸馏为一次加工,其他加工工序则称为二次加工[2]。
原油的一次加工能力即原油蒸馏装置的处理能力,常被视为一个国家炼油工业发展水平的标志。
截至2008年年底,我国原油加工能力为4.2亿t/a,占世界炼油总能力42.8亿t的10%;我国原油加工量3.42亿t,占世界炼油加工量的7%,居世界第二位(仅次于美国);我国炼厂总数(大中型)为53座,占世界总数655座的8%,其中,镇海炼厂位居世界排名第十七位[3]。
原油常压蒸馏在炼化企业加工过程中占有很重要的地位,其加工的好坏直接关系到后续产品质量和经济效益。
因此,原油常压蒸馏被称为石油加工的“龙头”。
基于以上原因,几乎在所有的炼油厂中,原油的第一个加工装置就是常压蒸馏装置。
尽管近年来常减压蒸馏技术和管理经验不断创新,装置节能降耗和产品质量得到了显著的提高,但与国外先进水平相比,仍存在较大的差距,如装置耗能较大,分馏和减压拔出深度偏低,对含硫原油的适应性较差等。
进一步的提高常减压装置的操作水平和运行水平显得日益重要,对提高炼油企业的经济效益也具有非常重要的意义。
本设计主要是依据国家成品油有关标准和市场供需情况,确定原油加工方案,进行原油常压蒸馏的工艺设计。
它的意义在于,通过常压蒸馏对原油的处理,可以按所指定的产品方案将原油分割得到汽油、煤油、轻柴油、重柴油馏分以重油馏分等。
可以减少渣油量,提高原油总拔出率。
不仅能获得更多的轻质油品,也可为二次加工、三次加工提供更多的原料油。
2 国内外研究现状原油蒸馏作为一次加工在石油加工中占有重要地位。
通常炼厂是依次使用常压和减压的方法,将原油按照沸程切割成不同的馏分。
人们将既采用了常压蒸馏又采用了减压蒸馏的原油蒸馏装置通常称为常减压蒸馏[4]。
常减压蒸馏开题报告-图文
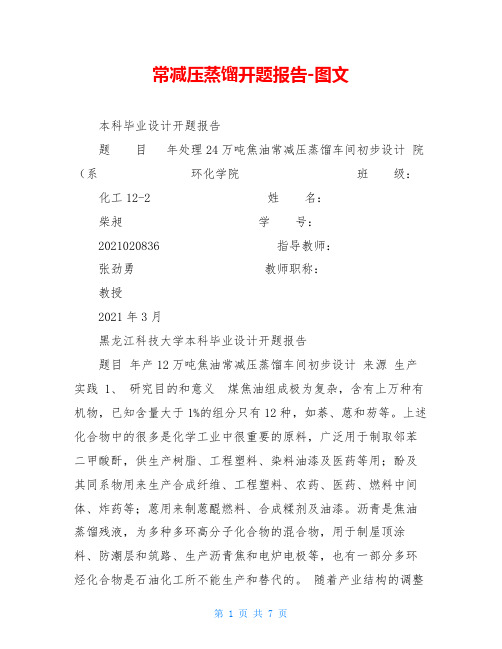
常减压蒸馏开题报告-图文本科毕业设计开题报告题目年处理24万吨焦油常减压蒸馏车间初步设计院(系环化学院班级:化工12-2 姓名:柴昶学号:2021020836 指导教师:张劲勇教师职称:教授2021年3月黑龙江科技大学本科毕业设计开题报告题目年产12万吨焦油常减压蒸馏车间初步设计来源生产实践 1、研究目的和意义煤焦油组成极为复杂,含有上万种有机物,已知含量大于1%的组分只有12种,如萘、蒽和芴等。
上述化合物中的很多是化学工业中很重要的原料,广泛用于制取邻苯二甲酸酐,供生产树脂、工程塑料、染料油漆及医药等用;酚及其同系物用来生产合成纤维、工程塑料、农药、医药、燃料中间体、炸药等;蒽用来制蒽醌燃料、合成糅剂及油漆。
沥青是焦油蒸馏残液,为多种多环高分子化合物的混合物,用于制屋顶涂料、防潮层和筑路、生产沥青焦和电炉电极等,也有一部分多环烃化合物是石油化工所不能生产和替代的。
随着产业结构的调整和企业改制任务的逐步完成,中国经济的发展已开始走上持续发展的轨道。
这对中国基础工业的发展从新的发展层次提出越来越紧迫的更高要求,对煤焦油加工工业的发展在结构和总量上会带来新的发展需求。
进入90年代中期,利用煤焦油加工的萘、蒽、吡啶、酚类等多环或杂环芳香烃产品,以及发展起来的炭素工业对原料的需求不断加大,人们对煤焦油加工业的重要经济地位又有了更新的认识。
中国煤焦油加工工业作为区域经济发展的重要支柱产业已经形成。
煤矿是我国的重要能源,对人民的日常生活起着举足轻重的影响。
而煤焦油蒸馏时焦油加工的龙头,其技术水平影响着焦油馏分的质量,并对焦油馏分的后续加工工艺的选择有着较大影响。
所以对煤焦油蒸馏工段的设计将会对焦油加工业的发展有巨大作用。
2、国内外发展情况(文献综述) 2.1 生产规模德国、法国、俄罗斯等国家的单套焦油蒸馏装置的能力都在10~50万t/a。
国内单套焦油蒸馏装置有0.6万、1.2万、3 万、5万、7.5万、10万和15万t/a各种规模。
常减压操作规程报告

第一章概述1 装置概述本装置是由中国石化总公司北京设计院设计,年加工大庆原油350万吨的润滑油型常减压蒸馏装置。
全装置共有设备232台,占地面积17100m2,1989年4月破土动工,于1991年7月投产,各项主要技术指标均已达到设计要求。
2 装置特点2.1本装置主要设计要求是能生产出优质润滑油料。
减压蒸馏采用了粗转油线(低速段直径2m)、大塔径(汽化段直径10m,精馏段直径8.2m),高效规整全填料(GEMPAK)等多种技术措施来实现减压操作的低炉温、高真空、窄馏份,提高润滑油料的品质。
2.2本装置生产的减压渣又作丙烷脱沥青装置生产150BS光亮润滑油料,装置总拔出率控制在62%左右。
2.3本装置减压渣油直接送到重油催化裂化装置作原料、对渣油的含盐量有一定限制,因此装置设有电脱盐系统。
2.4 本装置生产航空煤油要求符合3号航煤标准,因此设计了航煤脱硫醇系统。
2.5本装置采用集散型控制系统(DCS),以提高装置的管理水平并实现过程的部分优化控制,提高轻质油收率,降低能耗,确保润滑油质量,提高经济效益。
2.6废水排放:为减少含油污水的排放量,减少了含油污水的排放。
因为加工的是大庆原油,硫含量低,排放的污水无需脱硫,只需进行简单隔油,然后直接排放送到含油污水场。
2.7废气排放:本装置正常生产时排放的低压瓦斯,如初顶产品罐排放初顶气送到轻烃回收设施加以回收,常顶气和减顶气分别引到加热炉烧掉,因此本装置正常生产时,不向大气排放有污染性的废气。
塔和容器顶部油气的安全阀放空设有放空总管,引到装置外火炬烧掉;本装置的大气污染源主要是燃料在加热炉燃烧后排放的烟气,从烟气监测数据可知,其中不含SO2,NO X的排放量低于国家排放标准,对环境质量没有太大的影响。
2.8 本装置无废渣产生。
2.9噪声:经调查,该套装置的噪声污染主要来自加热炉火嘴、泵和风机的电机、空冷器风机。
加热炉火嘴在密闭的罩内操作,噪声低于85分贝。
万吨年常减压蒸馏装置工艺设计

万吨年常减压蒸馏装置工艺设计一、引言常减压蒸馏是一种重要的分离工艺,广泛应用于石油化工行业。
本文基于万吨年常减压蒸馏装置的设计要求,对工艺进行详细设计,旨在满足设备的高效运行和产品质量的要求。
二、装置工艺流程常减压蒸馏装置的主要工艺流程包括进料、预热、加热、分馏、冷却和产品收集等步骤。
2.1 进料进料是装置的起始步骤,原料从储罐经过输送管道进入装置。
进料过程需要考虑流量和温度的控制,以确保装置的正常运行。
2.2 预热进料经过加热器进行预热,提高进料的温度至蒸发温度。
预热过程需要控制加热温度和时间,以确保进料在进入分离塔前达到合适的温度。
2.3 加热预热后的进料进入分离塔,在分离塔内进行加热。
加热过程中需要控制加热温度和压力,使得进料能够充分蒸发并分离成不同的组分。
2.4 分馏在分馏塔中进行分离,通过不同组分的沸点差异,实现轻质组分和重质组分的分离。
分馏过程中需要控制塔底的温度和塔顶的压力,以确保合理的分离效果。
2.5 冷却分馏后的产品经过冷却器进行冷却,降低温度至合适的收集温度。
冷却过程中需要控制冷却温度和冷却时间,避免产品的过热或过冷。
2.6 产品收集冷却后的产品通过收集器进行收集,分离出所需的产物。
产品收集过程需要注意收集器的遮挡和密封,以防止产品的污染或泄露。
三、工艺参数设计为了保证装置的高效运行和产品质量的要求,需要对装置的工艺参数进行设计。
3.1 进料流量根据设备的设计要求和生产需求,确定进料的流量范围。
进料流量的选择需要考虑装置的生产能力和运行稳定性。
3.2 加热温度和压力根据进料组分的性质和分离要求,确定加热的温度和压力范围。
加热温度和压力的选择需要兼顾分离效果和能耗的平衡。
3.3 分馏塔底温度和塔顶压力根据产品要求和分离塔的结构特点,确定分馏塔底温度和塔顶压力的要求。
分馏塔底温度和塔顶压力的选择需要满足产品质量和工艺要求。
3.4 冷却温度和冷却时间根据产品的蒸发温度和收集温度,确定冷却的温度和时间范围。
400万吨年常减压蒸馏装置工艺设计

400万吨年常减压蒸馏装置工艺设计常减压蒸馏装置是一种常用的化工设备,用于对原料进行分离和提纯。
本文将介绍一种设计容量为400万吨年的常减压蒸馏装置的工艺设计。
首先,我们需要确定装置的原料和产品。
假设我们的装置用于石油精炼,原料是原油,产品是石油衍生品,如汽油、柴油和液化石油气等。
接下来,我们需要进行原料的预处理。
原油中含有杂质和不同碳链长度的烃类化合物,需要通过脱盐、脱水和脱硫等工艺步骤进行预处理。
这些步骤将有助于提高蒸馏塔的效率和避免设备的腐蚀。
然后,我们需要设计蒸馏塔的结构。
常减压蒸馏装置通常由多个塔组成,包括原料预热塔、主分馏塔和精馏塔等。
每个塔都有不同的功能和操作条件。
例如,原料预热塔用于将原料加热到合适的温度,以便进入主分馏塔进行分离。
在主分馏塔中,原料将经历不同温度的塔板,每个塔板上都有一定的压力和温度。
通过调节供料量、回流比和冷凝器温度等操作参数,可以实现不同组分的分离。
高沸点组分将在底部的液相中收集,而低沸点组分将在顶部的气相中收集。
精馏塔用于进一步提纯分离出的不同组分。
它通常会有更多的塔板和较低的操作压力和温度。
最后,产品将通过冷凝器冷却,并收集在不同的收集装置中。
收集的产品可以进一步处理或直接用作市售产品。
在整个装置的设计过程中,需要进行多次的热力学计算和模拟。
这些计算将帮助我们确定塔板数目、操作参数、回流比和冷凝温度等设计参数。
总之,400万吨年的常减压蒸馏装置的工艺设计需要根据原料和产品的特性进行合理的塔结构和操作参数的选择。
通过热力学计算和模拟,可以优化装置的设计,实现高效的分离和提纯过程。
继续写相关内容,1500字为了确保400万吨年常减压蒸馏装置的高效运行和优化设计,还需要考虑以下几个方面:首先是热能供应和回收利用。
蒸馏过程需要大量的热能来提供蒸汽和加热原料。
为了降低能耗和运行成本,装置需要考虑热能的供应和回收利用。
一种常见的做法是利用余热回收系统和换热器来回收废热,并将其用于加热原料或生成蒸汽。
年处理量420万吨常减压装置常压塔工艺设计

年处理量420万吨常减压装置常压塔工艺设计北京化工大学毕业设计(论文)题目:年处理量420万吨常减压蒸馏装置工艺设计院别:专业:化工工艺班级:学生:指导教师:摘要本设计主要是以某石化公司常减压为设计原型,主要计算数据取自生产实际。
所处理的原料为辽河混合原油,经过初馏塔初步分离后再经过常压塔和减压塔的分离得到不同馏程的馏分油。
在采用新工艺、新设备的同时优化了工艺流程,为了节能常压系统采用4台空冷器,为增加处理量,常压炉四路进料四路出料。
为使相当数量的中间馏分得到合理利用,因为它们是很多的二次加工原料,又能从中生产国民经济所需的各种润滑油、蜡、沥青的原料。
因此本设计采用三段汽化蒸馏,即预汽化—常压蒸馏—减压蒸馏。
关键词:常减压蒸馏;常压塔;工艺;设计目录第1章文献综述 (3)1.1 常减压蒸馏意义 (3)1.2 装置的概况和特点 (3)1.3 工艺流程概况 (4)1.4 主要原料、工艺及能耗指标 (7)第2章设计计算 (12)2.1 基础数据的换算 (12)2.1.1平均沸点 (12)2.1.2 确定各馏分相对分子质量和特性因数K (14)2.1.3 确定临界参数 (14)2.1.4 确定焦点参数 (15)2.1.5 确定平衡汽化温度 (15)2.1.6 确定实沸点温度 (19)2.1.7 原料及产品的有关参数汇总 (22)第三章物料衡算 (19)3.1 初馏塔的物料衡算 (23)3.2 常压塔的物料衡算 (20)第四章确定塔的相关参数和条件 (21)4.1 确定塔板数 (21)4.2 确定塔的操作条件 (21)4.2.1 确定塔的操作压力 (21)4.2.2 确定各侧线及塔底的气提蒸汽量 (23)4.2.3 确定过汽化段温度 (23)4.2.4 估算塔底温度 (27)4.2.5 假定塔顶及各侧线温度 (27)4.3 侧线及塔顶温度的校核 (28)4.4 塔经计算 (34)4.4.1 塔经的初算 (34)4.4.2计算出Wmax后再计算适宜的气速Wa (35)4.4.3计算气相空间截面积 (35)4.4.4 降液管内流体流速Vd (35)4.4.5计算降液管面积 (35)4.4.6塔横截面积Ft的计算 (36)4.5 塔高计算 (36)第五章存在的问题和设想 (37)5.1存在问题 (37)5.2设想 (37)5.3三废的处理情况及噪声的消除 (37)总结 (38)参考文献 (39)致谢 (40)北京工大学继续教育学院论文诚信承诺书本人郑重承诺:我所呈交的毕业设计《年处理量420万吨常减压蒸馏装置工艺设计》是在指导教师的指导下,独立开展研究取得的成果,文中引用他人的观点和材料,均在文后按顺序列出其参考文献,设计使用的数据真实可靠。
常压蒸馏流程模拟与优化及换热网络综合的开题报告
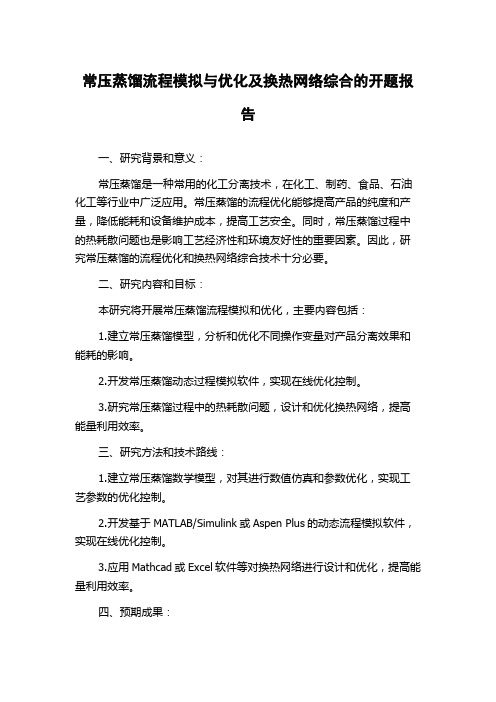
常压蒸馏流程模拟与优化及换热网络综合的开题报
告
一、研究背景和意义:
常压蒸馏是一种常用的化工分离技术,在化工、制药、食品、石油化工等行业中广泛应用。
常压蒸馏的流程优化能够提高产品的纯度和产量,降低能耗和设备维护成本,提高工艺安全。
同时,常压蒸馏过程中的热耗散问题也是影响工艺经济性和环境友好性的重要因素。
因此,研究常压蒸馏的流程优化和换热网络综合技术十分必要。
二、研究内容和目标:
本研究将开展常压蒸馏流程模拟和优化,主要内容包括:
1.建立常压蒸馏模型,分析和优化不同操作变量对产品分离效果和能耗的影响。
2.开发常压蒸馏动态过程模拟软件,实现在线优化控制。
3.研究常压蒸馏过程中的热耗散问题,设计和优化换热网络,提高能量利用效率。
三、研究方法和技术路线:
1.建立常压蒸馏数学模型,对其进行数值仿真和参数优化,实现工艺参数的优化控制。
2.开发基于MATLAB/Simulink或Aspen Plus的动态流程模拟软件,实现在线优化控制。
3.应用Mathcad或Excel软件等对换热网络进行设计和优化,提高能量利用效率。
四、预期成果:
1.建立常压蒸馏流程模型和换热网络模型,实现流程优化和能耗降低。
2.开发常压蒸馏动态过程模拟软件,实现在线优化控制。
3.撰写并发表1-2篇相关研究论文。
总之,本研究将为常压蒸馏行业的技术进步和性能优化提供一定的指导和支持。
常减压蒸馏装置减压深拔加热炉的设计
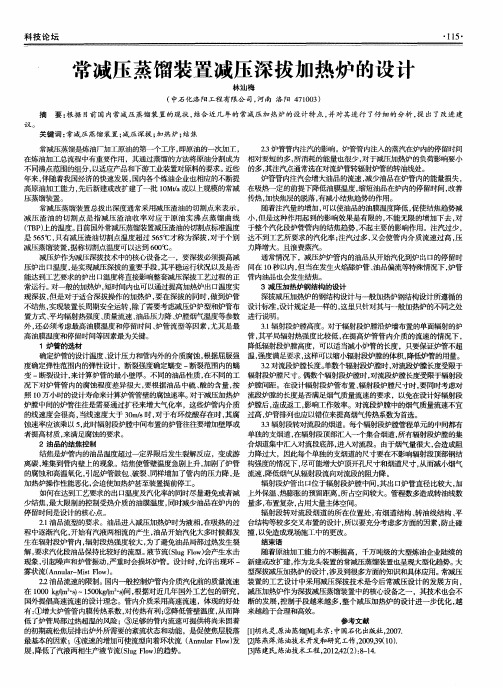
・ 1 l 5 ・
常减压 蒸馏装置 减压深拔 加热炉 的设 计
林 汕 梅 ( 中石 化 洛 阳工 程 有 限公 司 , 河南 洛 阳 4 7 1 0 0 3 )
摘
议 。
ห้องสมุดไป่ตู้
要: 根 据 目前 国内常减压 蒸馏 装置的现状 , 结合近几年的常减压加 热炉的设计特点 , 并对其进行 了仔 细的分析 , 提 出了改进 建
关键 词 : 常减压蒸馏装置; 减 压 深拔 ; 加热炉; 结 焦
常减压蒸馏是炼油厂加工原油的第—个工序 , 即原油的一次加工 , 2 . 3 炉管管内注汽的影响。炉管管内注入的蒸汽在炉内的停留时间 在炼油加工总流程中有重要作用 ,其通过蒸馏的方法将原油分割成为 相对要短的多, 所消耗的能量也很少 , 对于减压加热炉的负荷影响要小 不 同沸点范 围的组分 , 以适应产品和下游工业装置对原料的要求 。 近些 的多 , 其注汽点通常选在对流炉管转辐射炉管的转油线处。 年来 , 伴随着我国经济的快速发展 , 国内各个炼油企业也相应 的不断提 炉管管 内注汽会增大油品的流速 , 减少油品在炉管 内的能量损失 , 高原油加工能力 , 先后新建或改扩建了一批 1 0 Mt / a 或以上规模的常减 在吸热一定的前提下降低油膜温度 , 缩短油品在炉内的停 留时间 , 改善 压蒸馏 装置 。 传热 , 加快焦层 的脱落, 有减小结焦趋势的作用。 常减压蒸馏装置总拔 出深度通常采用减压渣油的切割点来表示 , 随着注汽量的增加 , 可以使油品的油膜温度降低 , 促使结焦趋势减 减压 渣油 的切 割点 是指减压渣油收率对应 于原油 实沸点蒸馏 曲线 小 , 但是这种作用起到的影响效果是有限的, 不能无限的增加下去 , 对 ( T B P ) 上的温度。 目前国外常减压蒸馏装置减压渣油的切割点标准温度 于整个汽化段炉管管内的 结焦趋势 , 不起主要的影响作用。注汽过少 , 是5 6 5 ℃, 只有减压渣油切割点温度超过 5 6 5  ̄ C 才称为深拔 , 对 于个别 达不到工艺所要求的汽化率 ; 注汽过多, 又会使管 内介质流速过高 , 压 减 压蒸 馏装 置 , 据称 切割 点 温度可 以达 到 6 0 0 ℃。 力降增大。且浪费蒸汽。 通常 隋况下 ,减压炉炉管内的油品从开始汽化到炉出口的停留时 减压炉作为减压深拔技术中的杨 设备之一,要深拔必须提高减 压炉出口温度 , 是实现减压深拔的重要手段 , 其平稳运行状况以及是否 间在 1 O 秒以内, 但当在发生火焰舔炉管 、 油品偏流等特殊情况下 , 炉管 能达到工艺要求的炉出口温度将直接影响整套减压深拔工艺过程的正 管内油品也会 发生结焦。 常运行。 对一般的加热炉 , 短时间内也可以通过提高加热炉出口温度实 3 减压 加热炉 钢结 构的设 计 现深拔 , 但是对于适合深拔操作的加热炉, 要在深拔 的同时 , 做 到炉管 深拔减压力 1 1 热炉的钢结构 十 与一般加热炉钢结构设计所遵循 的 设计规定是一样的 , 这里只针对其与一般加热炉的不同之处 不结焦 , 实现装置长周期安全运转 , 除了需要考虑减压炉炉型和炉管布 设计标准 , 置方式、 平均辐射热强度 、 质量流速、 油品压力降 、 炉膛烟气温度等参数 进行 说明 。 外, 还必须考虑最高油膜温度和停留时间、 炉管流型等 因素 , 尤其是最 3 . 1 辐射段炉膛高度。对于辐射段炉膛沿炉墙布置的单面辐射的炉 高油膜温度和停 留时间等因素最为关键 。 管, 其平局辐射热强度 比较低 , 在提高炉管管内介质的流速的情况下 , 1炉管 的选 材 降低辐射段炉膛高度 ,可以适当减小炉管的长度,只要保证炉管不超 确定炉管的设计温度、 设计压力和管内外的介质腐蚀 , 根据屈服强 温, 强度满足要求, 这样可以缩小辐射段炉膛的体积 , 降低炉管的用量。 度确定弹性范围内的弹性设计 ,断裂强度确定蠕变 一断裂范围内的蠕 3 . 2 对流段炉膛长度。 单数 个辐射段炉膛时 , 对流段炉膛长度受限于 偶数个辐射段炉膛时, 对流段炉膛长度受限于辐射段 变 一断裂设计, 来计算炉管的最小壁厚。不同的油品性质 , 在不同的工 辐射段炉膛尺寸。 况下对炉管管内的腐蚀程度差异很大 , 要根据油品中硫 、 酸的含量 , 按 炉膛间距。在设计辐射段炉管布置 、 辐射段炉膛尺寸时 , 要同时考虑对 照1 0万小时的设计寿命来计算炉管管壁的腐蚀速率。 对于减压加热炉 流段炉膛的长度是否满足烟气质量流速的要求 ,以免在设计好辐射段 炉膛中间的炉管往往是需要通过扩径来增大气化率,这些炉管内介质 炉膛后 , 造成返工 , 影响工作效率。对流段炉膛中的烟气质量流速不宜 的线速度会很高 , 当线速度大于 3 0 m / s 时, 对于有环烷酸存在时 , 其腐 过高 , 炉管排列也应以错位来提高烟气传热系数为首选。 蚀速率应该乘以 5 , 此时辐射段炉膛中间布置的炉管往往要增加壁厚或 3 . 3 辐射段转对流段的烟道。每个辐射段炉膛管程单元的中间都有 者提高材质 , 来满足腐蚀 的要求。 单独的支烟道 , 在辐射段顶部汇入— 个集合烟道 , 所有辐射段炉膛的集 2 油 品的结 焦控 制 合烟道集中汇 人对流段底部 , 进 入对流段。由于烟气量很大 , 会造成阻 结焦是炉管 内的油品温度超过—定界限后发生裂解反应 ,变成游 力降过大,因此每个单独的支烟道的尺寸要在不影响辐射段顶部钢结 离碳 , 堆集到管内壁上的现象。结焦使管壁温度急剧上升 , 加剧了炉管 构强度的情况下 , 尽可能增大炉顶开孔尺寸和烟道尺寸 , 从而减小烟气 的腐蚀和高温氧化, 引起炉管鼓包 、 破裂、 同样增加了管内的压力降 , 是 流速 , 降低烟气从辐射段流向对流段的阻力降。 加热炉操作f 生 能恶化 , 会迫使加热炉甚至装置提前停工。 辐射段炉管 出口位于辐射段炉膛中间 , 其出 口炉管直径 比较大, 加 如何在达到工艺要求的出口温度及汽化率的同时尽量避免或者减 上外保温、 热膨胀的预留距离 , 所 占空间较大。管程数多造成转油线数 少结焦, 最大限制的控制受热介质的油膜温度, 同时减少油品在炉内的 量多 , 布置复杂, 占用大量主体空间。 停留时间是谢 十 的核心点。 辐射段转对流段烟道的所在位置处 , 有烟道结构 、 转油线结构 、 平 2 . 1 油 品流 型 的要 求 。油 品进入 减压 加 热炉 时为 液相 , 在 吸 热 的过 台结构等较多交叉布置的设计 , 所以要充分考虑多方面的因素, 防止碰 程中逐渐汽化 , 开始有汽液两相流的产生 , 油品开始汽化大多时候都发 撞 , 以免 造成 现场施 工 中的更改 。 生在辐射段炉管 内, 辐射段热强度较大 , 为了避免油品局部过热发生裂 结束语 解, 要求汽化段油品保持 比较好的流型。 液节流( S l u g F l o w ) 会产生水击 随着原油加工能力的不断提高 ,千万吨级的大型炼油企业陆续 的 作为龙头装置的常减压蒸馏装置也呈现大型化趋势。 大 现象 , 引起噪声和炉管振动, 严重时会损坏炉管。设计时, 允许 出现环 一 新建或改扩建, 雾状流( A n n u l a r - Mi s t F l o w) 。 型深拔减压力 1 1 热炉的设计, 涉及到很多方面的知识和具体应用。 常减压 2 . 2 油品流速的限制。 国内—般控制炉管内介质汽化前的质量流速 装置的工艺设计中采用减压深拔技术是今后常减压设计的发展方向, 在1 0 0 0 k g / ( m ・ s 1 ~1 5 0 0 k  ̄ ( m ・ s 1 间, 根据对近几年国外工艺包的研究 , 减压加热炉作为深拔减压蒸馏装置中的核心设备之一,其技术也会不 国外提倡高速流速的设计理念。管内介质采用高速流速 ,体现的好处 断的发展 , 控制手段越来越多 , 整个减压加热炉的设计进一步优化 , 越 有: ①增大炉管管内膜传热系数 , 对传热有利 ; ②降低管壁温度 , 从而降 来越趋于合理和高效。 低 了炉管局部过热超温的风险;③足够的管内流速可提供将尚未固着 参考 文献 的初期疏松焦层排出炉外所需要 的紊流状态和动能,是促使焦层脱落 『 1 瑚 兆灵原 油蒸馏 . 北京: 中国石化 出版社 , 2 0 0 7 . 最基本的因素;④流速的增加可使流型向着环状流 ( A n n u l a r F l n W ) 发 f 2 1 陈燕萍. 炼油技术开发和研 究工作 , 2 0 0 9 ' 3 9 ( 1 0 ) . 展, 降低了汽液两相生产液节流( S l u g F l o w) 的趋势。 『 3 1 陈建民. 炼油技术工程, 2 0 1 2 , 4 2 ( 2 ) : 8 - 1 4 .
常减压蒸馏装置改造设计的开题报告

常减压蒸馏装置改造设计的开题报告一、选题背景及意义常减压蒸馏是一种适用于石油化工、精细化工、医药等行业的蒸馏技术,具有节能、加工效率高、产品品质优良等特点。
然而,传统的常减压蒸馏装置存在很多问题,如能效低、设备体积大、占地面积大、操作复杂等。
因此,对常减压蒸馏装置进行改造设计,提高其性能和效率,对于推进相关行业的发展具有重要的意义和价值。
二、研究内容和目标本次常减压蒸馏装置改造设计的研究内容主要包括以下方面:1. 设计一种能够有效提高装置能效的供料系统和回流系统。
2. 设计一种合理的控制系统,能够实现装置的自动化运行和监控。
3. 设计一种较小体积的常减压蒸馏装置,以降低设备成本和占地面积。
4. 通过实验测试,验证装置改造后的性能和效率是否得到提升。
本次研究的目标是通过装置的改造和优化设计,提高其能效和效率,降低设备成本和占地面积,实现常减压蒸馏装置的自动化控制和运行。
三、研究方法和技术路线本次研究将采取多种方法和技术手段进行,包括理论分析、数值模拟、实验研究、数据分析等。
具体技术路线如下:1. 分析传统常减压蒸馏装置的运行特点和存在的问题,确定改造设计的目标和方案。
2. 采用数值模拟技术,对装置的供料系统、回流系统以及分离塔进行优化设计。
3. 设计一种合理的自动控制系统,实现装置的自动化控制和监控。
4. 进行实验验证装置改造后的性能和效率是否有所提升,通过数据分析和对比来验证改造效果。
四、预期成果通过本次常减压蒸馏装置改造设计,预期可以获得以下成果:1. 设计出一种能够有效提高装置能效和效率的常减压蒸馏装置。
2. 开发出一种操作方便、自动化程度较高的控制系统。
3. 实现装置较小体积化,降低设备成本和占地面积。
4. 提高装置的分馏效率和产品品质,使其在相关领域得到广泛应用。
五、进度计划1. 研究背景和文献调研:1个月。
2. 设计装置改造的方案:2个月。
3. 进行数值模拟和实验研究:4个月。
4. 改造装置并实现自动化控制:3个月。
常减压蒸馏装置实习报告(2篇)
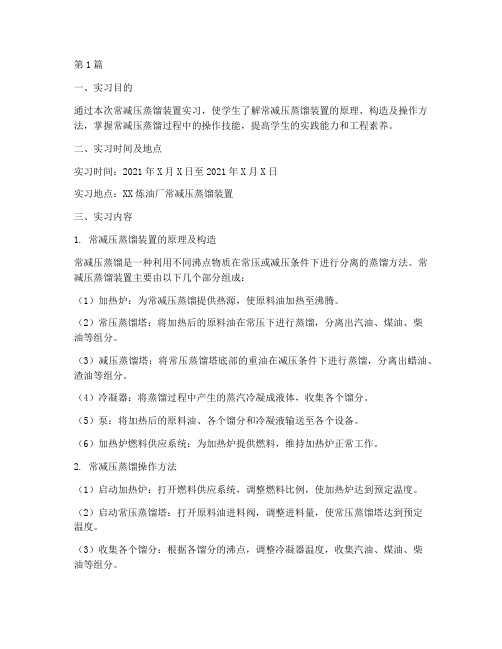
第1篇一、实习目的通过本次常减压蒸馏装置实习,使学生了解常减压蒸馏装置的原理、构造及操作方法,掌握常减压蒸馏过程中的操作技能,提高学生的实践能力和工程素养。
二、实习时间及地点实习时间:2021年X月X日至2021年X月X日实习地点:XX炼油厂常减压蒸馏装置三、实习内容1. 常减压蒸馏装置的原理及构造常减压蒸馏是一种利用不同沸点物质在常压或减压条件下进行分离的蒸馏方法。
常减压蒸馏装置主要由以下几个部分组成:(1)加热炉:为常减压蒸馏提供热源,使原料油加热至沸腾。
(2)常压蒸馏塔:将加热后的原料油在常压下进行蒸馏,分离出汽油、煤油、柴油等组分。
(3)减压蒸馏塔:将常压蒸馏塔底部的重油在减压条件下进行蒸馏,分离出蜡油、渣油等组分。
(4)冷凝器:将蒸馏过程中产生的蒸汽冷凝成液体,收集各个馏分。
(5)泵:将加热后的原料油、各个馏分和冷凝液输送至各个设备。
(6)加热炉燃料供应系统:为加热炉提供燃料,维持加热炉正常工作。
2. 常减压蒸馏操作方法(1)启动加热炉:打开燃料供应系统,调整燃料比例,使加热炉达到预定温度。
(2)启动常压蒸馏塔:打开原料油进料阀,调整进料量,使常压蒸馏塔达到预定温度。
(3)收集各个馏分:根据各馏分的沸点,调整冷凝器温度,收集汽油、煤油、柴油等组分。
(4)启动减压蒸馏塔:调整减压系统,使减压蒸馏塔达到预定温度。
(5)收集重油组分:根据重油组分的沸点,调整冷凝器温度,收集蜡油、渣油等组分。
(6)停机操作:关闭各个设备,切断燃料供应,使设备恢复正常状态。
3. 常减压蒸馏装置的运行维护(1)定期检查设备:检查加热炉、常压蒸馏塔、减压蒸馏塔、冷凝器等设备的运行情况,确保设备正常运行。
(2)调整操作参数:根据原料油性质、设备运行情况,调整加热炉、冷凝器等设备的操作参数。
(3)处理故障:发现设备故障,及时进行处理,确保设备正常运行。
四、实习心得体会通过本次实习,我对常减压蒸馏装置有了更深入的了解,掌握了常减压蒸馏的操作方法,提高了自己的实践能力和工程素养。
- 1、下载文档前请自行甄别文档内容的完整性,平台不提供额外的编辑、内容补充、找答案等附加服务。
- 2、"仅部分预览"的文档,不可在线预览部分如存在完整性等问题,可反馈申请退款(可完整预览的文档不适用该条件!)。
- 3、如文档侵犯您的权益,请联系客服反馈,我们会尽快为您处理(人工客服工作时间:9:00-18:30)。
大连大学本科毕业论文(设计)开题报告论文题目:350万吨/年常减压蒸馏装置常压加热炉设计学院:环境与化学工程学院专业、班级:过程装备与控制工程081 班学生姓名:指导教师(职称):赵启成(副教授)2012年03月6 日填毕业论文(设计)开题报告要求开题报告既是规范本科生毕业论文工作的重要环节,又是完成高质量毕业论文(设计)的有效保证。
为了使这项工作规范化和制度化,特制定本要求。
一、选题依据1.论文(设计)题目及研究领域;2.论文(设计)工作的理论意义和应用价值;3.目前研究的概况和发展趋势。
二、论文(设计)研究的内容1.重点解决的问题;2.拟开展研究的几个主要方面(论文写作大纲或设计思路);3.本论文(设计)预期取得的成果。
三、论文(设计)工作安排1.拟采用的主要研究方法(技术路线或设计参数);2.论文(设计)进度计划。
四、文献查阅及文献综述学生应根据所在学院及指导教师的要求阅读一定量的文献资料,并在此基础上通过分析、研究、综合,形成文献综述。
必要时应在调研、实验或实习的基础上递交相关的报告。
综述或报告作为开题报告的一部分附在后面,要求思路清晰,文理通顺,较全面地反映出本课题的研究背景或前期工作基础。
五、其他要求1.开题报告应在毕业论文(设计)工作开始后的前四周内完成;2.开题报告必须经学院教学指导委员会审查通过;3.开题报告不合格或没有做开题报告的学生,须重做或补做合格后,方能继续论文(设计)工作,否则不允许参加答辩;4.开题报告通过后,原则上不允许更换论文题目或指导教师;5.开题报告的内容,要求打印并装订成册(部分专业可根据需要手写在统一纸张上,但封面需按统一格式打印)。
一、选题依据1.论文(设计)题目350万吨/年常减压蒸馏装置常压加热炉设计2.研究领域石油化工工艺管式加热炉设计3.论文(设计)工作的理论意义和应用价值近年来,随着石油化学工业的迅速发展,管式加热炉技术越来越引起人们的重视。
管式加热炉消耗着大量的能量,而在制造乙烯、氢气和合成氨的工艺过程中,它已成为进行裂解和转化反应的心脏设备,支配着整个工厂或装置的产品质量、收率、能耗和操作周期。
因此对管式加热炉的设计和余热回收系统的设计就非常必要了。
管式炉在石油化厂具有举足轻重的作用,管式炉的能耗很高。
管式炉的能量消耗在生产装置中约占80%~90%[3]。
它的投资一般占15%左右,高的可达30%[3]。
此外,由于加热炉在燃料燃烧时的噪声和烟气排放也对环境污染造成相当严重的影响。
这些因素都必须在加热炉设计时加以考虑。
4.目前研究的概况和发展趋势在炼油工程上,采用管式加热炉开始于1910年至1911年间,在没有采用管式加热炉之前原油加工方式均为釜式蒸馏,小处理量、且为间歇生产。
管式加热炉的使用是炼油工业由小处理量、间歇生产转向大处理量、连续生产的标志。
常减压蒸馏装置是原油初加工装置,其的处理能力决定了整个炼油厂加工能力或规模。
在常减压蒸馏装置中,常压炉的处理能力决定了常减压蒸馏装置处理能力,如果常压炉的处理能力不够,整个装置将无法完成预定的任务。
石化工艺加热炉的能耗约占整个生产装置能耗的50%~60%,其热效率的高低直接决定着整个生产装置能耗大小,直接影响着生产成本[2][3]。
由于石油化工工艺管式加热炉的被加热工艺介质为易燃、易爆的液体或气体,且压力较高,一旦发生重大事故,后果不堪设想。
因此,石油化工工艺管式加热炉能否长周期安全、稳定运行对整个装置或全厂实现“长周期安全、稳定运转”有着直接的影响。
几乎每一套炼油和石油化工装置中都有管式加热炉,也就是说:管式加热炉几乎参与了炼油和石油化工的整个生产过程。
管式加热炉是炼油装置中的三大主力设备之一(塔器、换热器和管式加热炉),是乙烯和化肥等石油化工生产装置的“心脏”设备,没有石油化工工艺管式加热炉,就没有现代化的炼油和石油化工工业。
石油化工工艺管式加热炉排放的烟气中NO x、SO x、CO2等有害成分含量是否达到国家标准规定,对操作工人和周边居民的生活或身体健康都有着直接影响。
上述充分说明了管式加热炉在炼油和石油化工生产中占有十分重要的地位,搞好石油化工工艺管式加热炉操作、管理工作对炼油和石油化工生产装置实现高处理量、高质量、高效率、低能耗和长期安全、稳定运转及减轻对环境的污染有着重大意义。
1.重点解决的问题决定加热条件及设计需要考虑的各种标准和法规。
完成350万吨/年常减压蒸馏装置常压加热炉设计,其中包括:加热炉的工艺设计及机械设计,设计一览表,CAD图(350万吨/加热炉的总装配图、钢结构图、盘管图)。
2.拟开展研究的几个主要方面(论文写作大纲或设计思路)设计前期,了解管式加热炉的特点及类型,查阅各类期刊文献和专利资料,得到设计所需参数和要求。
然后是加热炉的设计,首先做出工艺设计,其中有工艺计算(物料热量衡算),根据工艺技术决定加热炉辐射室、对流室的直径、高度以及相关的部件的结构。
用CAD绘出具体的装配图。
2.本论文(设计)预期取得的成果设计年产350万吨/年常减压蒸馏装置常压加热炉的所有内容,其中包括:工艺计算、炉管系统设计、加热炉结构设计、钢结构计算、机械设计及CAD图纸等。
设计的目的:提高加热炉的热效率、减少燃料消耗量,加热产品的质量满足下一个工序的要求。
1.拟采用的主要研究方法(技术路线或设计参数);加热炉设计:原油工艺条件入炉温度℃出炉温度℃出炉压力(MPa)比重d420粘度(cp)309 365 1.0 0.8615 50℃80℃23 11.47原油量(吨/年)350一般条件炉工作时间(h/年)8000 环境温度℃20排烟温度℃160 蒸气压力/MPa 1.02.论文(设计)进度计划1~2周完成资料的整理和英文论文的翻译;第3周结合资料的整理,完成开题报告,完成论文概述部分;4~7周根据设计参数,完成工艺设计和机械设计等内容;8~11周完成CAD图的绘制;12周以后整理和修改论文和CAD图纸,完成中英文摘要;13周论文装订、评阅、准备答辩;14周答辩。
四、需要阅读的参考文献[1] 中国石油化工总公司石油化工规划院编.炼油厂设备加热炉设计手册(上)[D].中国石油化工总公司石油化工规划院,1986.[2] 化工部工业炉设计中心站编.化学工业炉设计手册[D].北京:化学工业出版社,1988.[3] 上海炼油厂编.石油化工管式加热炉[M].上海:上海科学技术出版社,1978.[4] 钱家麟.管式加热炉[M].北京:中国石化出版社,2002.[5] 大庆石化炼油厂编写组.炼油厂设备加热炉(下) [D].大庆:大庆石化炼油厂,1996.[6] 闫康平.工程材料(第二版) [M].北京:化学工业出版社,2008.[7] 李志义,俞建良,刘志军.过程容器及设备[M].北京:化学工业出版社,2008.[8] 大连理工大学编.化工原理(上、下)[M].北京:高等教育出版社,2002.[9] 郑津洋.过程设备设计[M].北京:化学工业出版社,2001:29-50.[10] HG 20581-2011.钢制化工容器材料选用规定[S].中国人民共和国行业标准,2011.[11] Wimpress.R.N.Rting Fired heater.Petro[J].1963,42(10):23~46.[12] L. Shen, Oxygen corrosion of low pressures,hot-water boiler and its protective measure [J].Qualityworld No 7, 2003:63-64.[13] Huang Zhuqi,Y ang, Guangjiong and Zhang, Zhongxian. Simulation and Calculation of TubularFurnaces in Petroleum Chemistry [J].Beijing:Chemical Industry Press,1993.[14] Wang Y ingshi,Fan Weicheng; and Xu Xuchang. Numerical Calculation of Combustion Process[J].Beijing :Science Press,1986.[15] J.S.Zheng and Z.P.LV..A study of mechanism and influencing factors of carbon dioxide corrosion.[J].Journal of Petroleum, V o 16 No3,1995:4-138.附:文献综述或报告审核意见指导教师评阅意见(对选题情况、研究内容、工作安排、文献综述等方面进行评阅)签字:2012 年 3 月16 日教研室主任意见签字:2012 年 3 月20 日学院教学指导委员会意见签字:年月日公章:附:文献综述或报告文献综述1、概述近年来,随着石油化学工业的迅速发展,管式加热炉技术越来越引起人们的重视。
管式加热炉消耗着大量的能量,而在制造乙烯、氢气和合成氨的工艺过程中,它已成为进行裂解和转化反应的心脏设备,支配着整个工厂或装置的产品质量、收率、能耗和操作周期。
因此对管式加热炉的设计和余热回收系统的设计就非常必要了。
管式炉在石油化厂具有举足轻重的作用,管式炉的能耗很高。
管式炉的能量消耗在生产装置中约占80%~90%[3]。
它的投资一般占15%左右,高的可达30%[3]。
此外,由于加热炉在燃料燃烧时的噪声和烟气排放也对环境污染造成相当严重的影响。
这些因素都必须在加热炉设计时加以考虑。
在炼油工程上,采用管式加热炉开始于1910年至1911年间,在没有采用管式加热炉之前原油加工方式均为釜式蒸馏,小处理量、且为间歇生产。
管式加热炉的使用是炼油工业由小处理量、间歇生产转向大处理量、连续生产的标志。
常减压蒸馏装置是原油初加工装置,其的处理能力决定了整个炼油厂加工能力或规模。
在常减压蒸馏装置中,常压炉的处理能力决定了常减压蒸馏装置处理能力,如果常压炉的处理能力不够,整个装置将无法完成预定的任务。
石化工艺加热炉的能耗约占整个生产装置能耗的50%~60%,其热效率的高低直接决定着整个生产装置能耗大小,直接影响着生产成本[2][3]。
石化工艺加热炉的基建投资费用,约占一般炼油装置总投资的10%~20%,总设备费用的30%左右;在重整、制氢等装置中则占装置总投资的25%左右;乙烯裂解炉和化肥转化炉的基建投资费用约占装置总投资的35%左右[3]。
石化管式加热炉的基建投资费用大小直接影响着整个生产装置或炼油厂、石油化工厂的基建投资。
由于石油化工工艺管式加热炉的被加热工艺介质为易燃、易爆的液体或气体,且压力较高,一旦发生重大事故,后果不堪设想。