压铸件缺陷分析
压铸件的缺陷分析
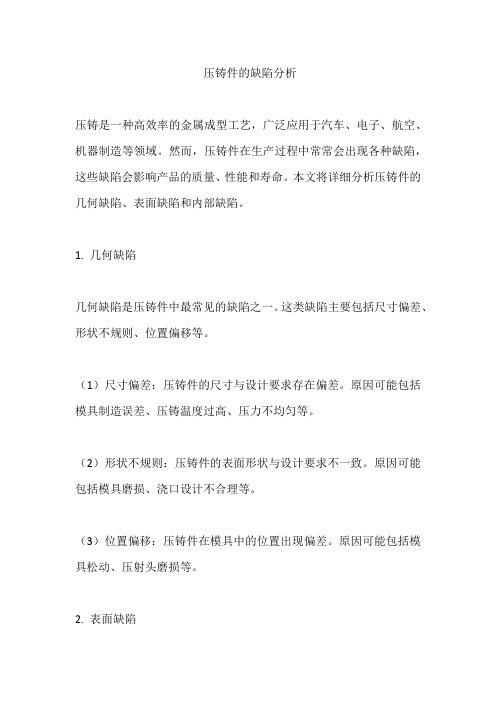
压铸件的缺陷分析压铸是一种高效率的金属成型工艺,广泛应用于汽车、电子、航空、机器制造等领域。
然而,压铸件在生产过程中常常会出现各种缺陷,这些缺陷会影响产品的质量、性能和寿命。
本文将详细分析压铸件的几何缺陷、表面缺陷和内部缺陷。
1. 几何缺陷几何缺陷是压铸件中最常见的缺陷之一。
这类缺陷主要包括尺寸偏差、形状不规则、位置偏移等。
(1)尺寸偏差:压铸件的尺寸与设计要求存在偏差。
原因可能包括模具制造误差、压铸温度过高、压力不均匀等。
(2)形状不规则:压铸件的表面形状与设计要求不一致。
原因可能包括模具磨损、浇口设计不合理等。
(3)位置偏移:压铸件在模具中的位置出现偏差。
原因可能包括模具松动、压射头磨损等。
2. 表面缺陷表面缺陷主要包括气孔、夹杂、裂纹等。
(1)气孔:压铸件表面出现圆形或椭圆形孔洞,直径通常在0.5~1.0mm之间。
原因可能包括模具温度过低、金属原料不纯等。
(2)夹杂:压铸件表面出现黑色或褐色斑点,直径通常在0.1~0.3mm 之间。
原因可能包括原料不纯、模具温度过高、压铸速度过快等。
(3)裂纹:压铸件表面出现垂直于应力方向、宽度在0.1mm左右的微小凹槽或裂纹。
原因可能包括模具温度过高、金属材料脆性大等。
3. 内部缺陷内部缺陷主要包括晶粒间距、偏析、缩松等。
(1)晶粒间距:压铸件晶粒分布不均匀,晶粒大小不一,导致力学性能下降。
原因可能包括冷却速度过慢、浇口设计不合理等。
(2)偏析:压铸件中化学成分分布不均匀,出现局部富集或贫乏的现象。
原因可能包括冷却速度过快、压力不均匀等。
(3)缩松:压铸件内部出现直径在0.3~1.0mm之间的微小孔洞或缝隙。
原因可能包括浇口设计不合理、压力不足等。
针对以上缺陷,可以采取以下解决方案:1. 几何缺陷:通过提高模具制造精度、优化压铸工艺参数(如控制压铸温度和压力)、定期检查和维修模具等方式来减少尺寸偏差、形状不规则和位置偏移等问题。
2. 表面缺陷:通过提高模具温度、选用高质量原料、优化压铸工艺参数(如降低压铸速度)等方式来减少气孔、夹杂和裂纹等问题。
压铸件缺陷原因分析
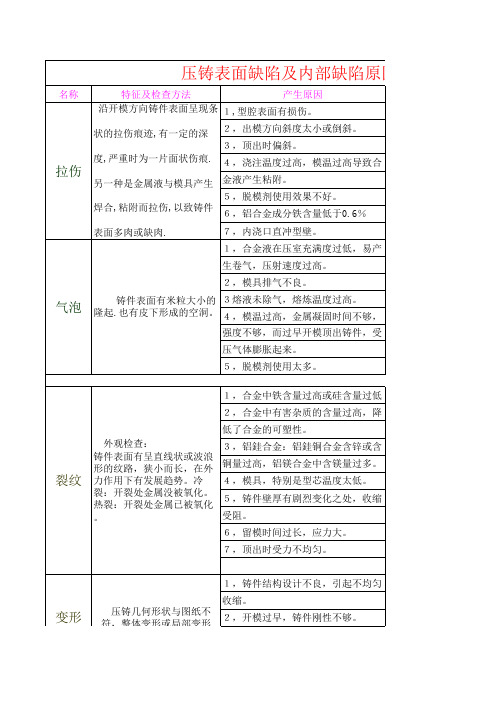
欠铸, 轮廓不 清
毛刺, 飞边
压铸件在分型面边缘上出 3,分型面上杂物未清理干净。 现金属薄片。 4,模具强度不够造成变形。 5,镶块,滑块磨损与分型面不平 齐。 1,不合适的脱模剂。
变色, 斑点
铸件表面上呈现出不同 2,脱模剂用量过多。 于基体金属颜色的斑点。 3,含有石墨的润滑剂中的石墨落入 铸件表层。
d,改善型腔排气条件。
a,提高合金液的质量。 b,提高浇注温度或模具温度。
c,提高比压,充填速度。 d,改善浇注系统金属液的导流方式,在 欠注部位加开溢流槽,排气槽。 e,正确的压铸操作。
a,检查合模力和增压情况,调整压铸工 艺参数。 b,清洁型腔表面及分型面。 c,修整模具。 d,最好是采用闭合压射结束时间控制 系统,可实现无飞边压铸。
1,正确选用压铸模材料及热处理工艺。 2,浇注温度不宜过高,尤其是高熔点 合金。 3,模具预热要充分。 4,压铸模要定期或压铸一定次数后退火 ,消除内应力。 5,打磨成型部分表面,减少表面粗糙度 Ra值。 6,合理选择模具冷却方法。 a,铸件壁厚设计尽量均匀。 b,模具局部冷却调整。 c,提高压射比压。
气孔
缩孔, 缩松
夹渣, 渣孔
1,铝合金中杂质锌,铁超过规定范 围。 铸件基体金属晶体过于粗 大或极小,使铸件易断裂或 碰碎。
脆性
脆性
铸件基体金属晶体过于粗 2,合金液过热或保温时间过长导致 大或极小,使铸件易断裂或 晶粒粗大。 碰碎。 3,激烈过冷,使晶粒粗大。 1,压力不足,基体组织致密度差。 2,内部缺陷引起,如气孔,缩孔, 压铸件经耐压试验,产生 渣孔,裂纹,缩松。 漏气,渗水 3,浇注和排气系统设计不良。 4,压铸冲头磨损,压射不稳定。 1,非金属硬点: ①,混入了合金液表面的氧化物. ②,铝合金与炉衬的反应。 ③,金属料混入异物。 ④,夹杂物。
压铸件常见缺陷及解决办法

压铸件常见缺陷及解决办法
1、尖角缺陷:表现为在压铸件的边缘和表面出现尖利的角,其
原因是模具的固定不牢,模具合模前没有铂精加光等操作,模具和表
面间的空隙较大,导致铸件连续流和溅射的金属物料的冷凝无法完全
填充到模具内。
解决办法是在压铸件的模具制作中要注意模具的固定,还要在合模前进行铂精加光,使模具缝隙尽量控制在最小。
2、翘曲缺陷:表现为铸件胚体过大或模具设计不当,导致部分
孔表面被填充的金属物料过度凝固后发生变形。
解决办法是提高铸件
的成型质量,在模具设计时应注意做到模具中高低正常,同时要增加
相应的引流装置,降低铸件表面在压铸过程中的温度,减少物料凝固
时间。
3、凹槽缺陷:表现为压铸件内壁或内孔出现浅深不均、粗糙凹槽,一般出现在内壁与模穴孔面间,其原因是模具合模时并未完全排
除空气,另外铸件内孔口位、形喉与内壁模穴间距过大,空气中的熔
融物料的细沙子难以充分清除也会导致此缺陷的产生。
解决办法是采
取真空压铸成型,即采用真空室和真空阀将空气真空,以消除空气;
另外应改变合模方式和模具设计,减少内孔口位与形喉与内壁模穴间距。
常见压铸件缺陷及解决方法
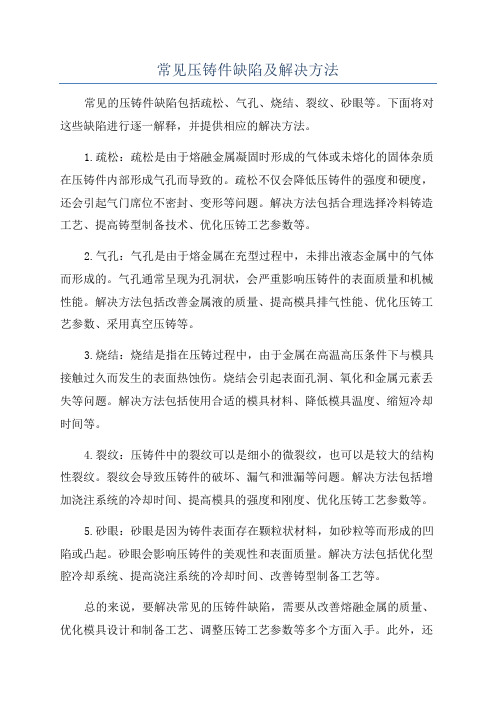
常见压铸件缺陷及解决方法常见的压铸件缺陷包括疏松、气孔、烧结、裂纹、砂眼等。
下面将对这些缺陷进行逐一解释,并提供相应的解决方法。
1.疏松:疏松是由于熔融金属凝固时形成的气体或未熔化的固体杂质在压铸件内部形成气孔而导致的。
疏松不仅会降低压铸件的强度和硬度,还会引起气门席位不密封、变形等问题。
解决方法包括合理选择冷料铸造工艺、提高铸型制备技术、优化压铸工艺参数等。
2.气孔:气孔是由于熔金属在充型过程中,未排出液态金属中的气体而形成的。
气孔通常呈现为孔洞状,会严重影响压铸件的表面质量和机械性能。
解决方法包括改善金属液的质量、提高模具排气性能、优化压铸工艺参数、采用真空压铸等。
3.烧结:烧结是指在压铸过程中,由于金属在高温高压条件下与模具接触过久而发生的表面热蚀伤。
烧结会引起表面孔洞、氧化和金属元素丢失等问题。
解决方法包括使用合适的模具材料、降低模具温度、缩短冷却时间等。
4.裂纹:压铸件中的裂纹可以是细小的微裂纹,也可以是较大的结构性裂纹。
裂纹会导致压铸件的破坏、漏气和泄漏等问题。
解决方法包括增加浇注系统的冷却时间、提高模具的强度和刚度、优化压铸工艺参数等。
5.砂眼:砂眼是因为铸件表面存在颗粒状材料,如砂粒等而形成的凹陷或凸起。
砂眼会影响压铸件的美观性和表面质量。
解决方法包括优化型腔冷却系统、提高浇注系统的冷却时间、改善铸型制备工艺等。
总的来说,要解决常见的压铸件缺陷,需要从改善熔融金属的质量、优化模具设计和制备工艺、调整压铸工艺参数等多个方面入手。
此外,还需要采用适当的检测手段,如金相分析、X射线检测、超声波检测等,对压铸件进行质量检验,及时排除可能存在的缺陷。
压铸件的缺陷分析及检验要点
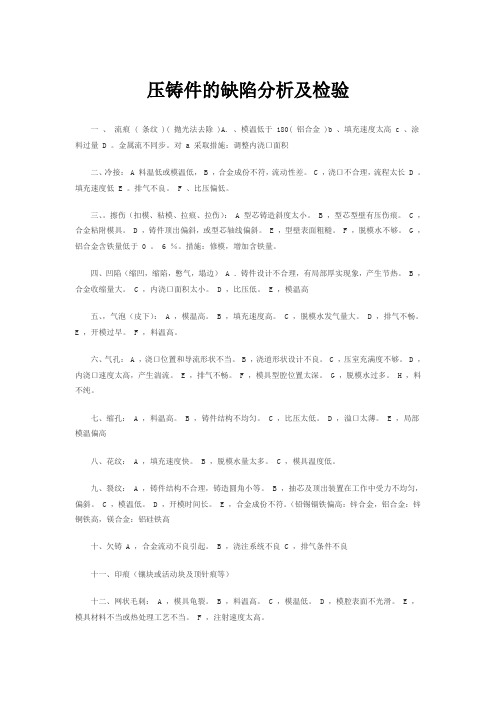
压铸件的缺陷分析及检验一、流痕 ( 条纹 )( 抛光法去除 )A. 、模温低于 180( 铝合金 )b 、填充速度太高 c 、涂料过量 D 。
金属流不同步。
对 a 采取措施:调整内浇口面积二、冷接: A 料温低或模温低, B ,合金成份不符,流动性差。
C ,浇口不合理,流程太长 D 。
填充速度低 E 。
排气不良。
F 、比压偏低。
三、。
擦伤(扣模、粘模、拉痕、拉伤): A 型芯铸造斜度太小。
B ,型芯型壁有压伤痕。
C ,合金粘附模具。
D ,铸件顶出偏斜,或型芯轴线偏斜。
E ,型壁表面粗糙。
F ,脱模水不够。
G ,铝合金含铁量低于 0 。
6 %。
措施:修模,增加含铁量。
四、凹陷(缩凹,缩陷,憋气,塌边) A .铸件设计不合理,有局部厚实现象,产生节热。
B ,合金收缩量大。
C ,内浇口面积太小。
D ,比压低。
E ,模温高五、,气泡(皮下): A ,模温高。
B ,填充速度高。
C ,脱模水发气量大。
D ,排气不畅。
E ,开模过早。
F ,料温高。
六、气孔: A ,浇口位置和导流形状不当。
B ,浇道形状设计不良。
C ,压室充满度不够。
D ,内浇口速度太高,产生湍流。
E ,排气不畅。
F ,模具型腔位置太深。
G ,脱模水过多。
H ,料不纯。
七、缩孔: A ,料温高。
B ,铸件结构不均匀。
C ,比压太低。
D ,溢口太薄。
E ,局部模温偏高八、花纹: A ,填充速度快。
B ,脱模水量太多。
C ,模具温度低。
九、裂纹: A ,铸件结构不合理,铸造圆角小等。
B ,抽芯及顶出装置在工作中受力不均匀,偏斜。
C ,模温低。
D ,开模时间长。
E ,合金成份不符。
(铅锡镉铁偏高:锌合金,铝合金:锌铜铁高,镁合金:铝硅铁高十、欠铸 A ,合金流动不良引起。
B ,浇注系统不良 C ,排气条件不良十一、印痕(镶块或活动块及顶针痕等)十二、网状毛刺: A ,模具龟裂。
B ,料温高。
项目6压铸件缺陷分析与解决方案
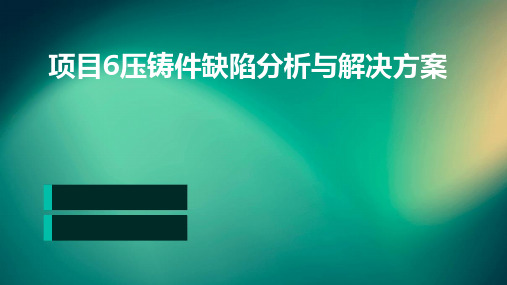
01
使员工能够准确识别压铸件缺陷的类型和原因,提高缺陷预防
意识。
提高员工操作技能
02
通过培训和实践,提高员工在压铸过程中的操作技能和规范意
识。
定期开展意识教育活动
03
通过举办讲座、案例分析等形式,提高员工对压铸件缺陷预防
的重视程度。
定期进行设备维护和检查
制定设备维护计划
根据设备运行状况和生产需求,制定合理设备维护计划。THANKS FOR WATCHING
感谢您的观看
力学试验机
用于对压铸件进行力学性能测试。
04
压铸件缺陷分析流程
收集缺陷数据
通过外观检测、内部检测、力学性能检测和金 相分析等方法收集压铸件缺陷数据。
01
原因分析
根据缺陷特征和检测结果,分析缺陷 产生的原因,如模具设计不合理、浇
注系统不匹配、合金成分不均等。
03
实施解决方案
根据制定的解决方案,采取相应的措施对生 产过程进行改进,以减少或消除缺陷的产生。
总结词
缩孔和缩松是由于金属液在冷却过程中收缩而未能得到足 够的补充所形成的缺陷。
详细描述
缩孔通常表现为铸件内部的空洞,而缩松则表现为细小的 孔洞或疏松结构。缩孔和缩松可能导致铸件性能下降,如 强度降低、疲劳寿命缩短等。
解决方案
优化模具设计,减少金属液的收缩量;控制模具温度和金 属液的冷却速度,促进补缩;调整压铸参数,提高金属液 的流动性。
05
02
分类与整理
对收集到的缺陷数据进行分类整理,以便进 行后续分析。
04
制定解决方案
针对不同缺陷产生的原因,制定相应 的解决方案,如优化模具设计、调整 浇注系统参数、改进合金成分等。
压铸件常见缺陷及解决办法手册 (完整版)
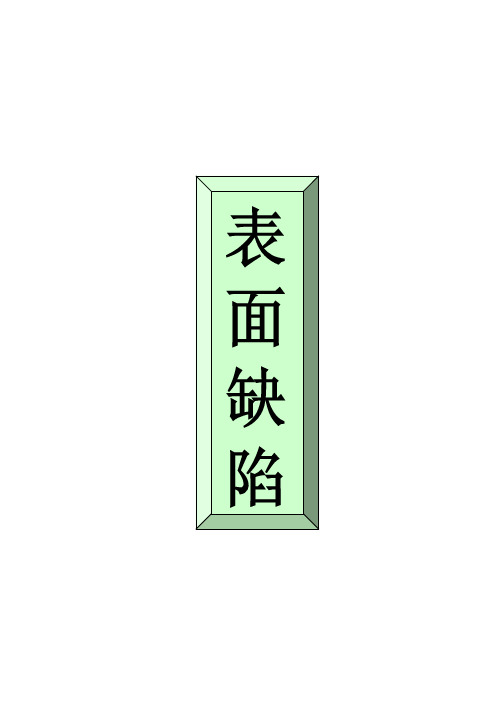
产生原因分析判断及解决办法1、金属液浇注温度低或模具温度低;2、合金成分不符合标准,流动性差;3、金属液分股填充,熔合不良;4、浇口不合理,流程太长;5、填充速度低或排气不良;6、压射比压偏低。
1、产品发黑,伴有流痕。
适当提高浇注温度和模具温度;2、改变合金成分,提高流动性;3、烫模件看铝液流向,金属液碰撞产生冷隔出现一般为涡旋状,伴有流痕。
改进浇注系统,改善内浇口的填充方向。
另外可在铸件边缘开设集渣包以改善填充条件;4、伴有远端压不实。
更改浇口位置和截面积,改善排溢条件,增大溢流量;5、产品发暗,经常伴有表面气泡。
提高压射速度,6、铸件整体压不实。
提高比压(尽量不采用)。
缺陷1 ---- 冷隔缺陷现象:温度较低的金属流互相对接但未熔合而出现的缝隙,呈不规则的线形,有穿透的和不穿透的两种,在外力的作用下有发展的趋势。
其他名称:冷接(对接)缺陷2 ---- 擦伤其他名称:拉伤、拉痕、粘模伤痕缺陷现象:顺着脱模方向,由于金属粘附,模具制造斜度太小而造成铸件表面的拉伤痕迹,严重时成为拉伤面甚至产生裂纹。
产生原因 分析判断及解决办法 1、型芯、型壁的铸造斜度太小或出现倒斜度; 2、型芯、型壁有压痕; 3、合金粘附模具;4、铸件顶出偏斜,或型芯轴线偏斜;5、型壁表面粗糙;6、涂料常喷涂不到;7、铝合金中含铁量低于0.6%; 8、合金浇注温度高或模具温度太高;9、浇注系统不正确, 直接冲击型壁或型芯 ; 10、填充速度太高;11、型腔表面未氮化。
1、产品一般拉出亮痕,不起毛。
修正模具,保证制造斜度; 2、产生拉毛甚至拉裂。
打光压痕、更换型芯或焊补型壁; 3、拉伤起毛。
抛光模具; 4、单边大面积拉伤,顶出时有异声修正模具结构; 5、拉伤为细条状,多条。
打磨抛光表面; 6、模具表面过热,均匀粘铝。
涂料用量薄而均匀,不能漏喷涂料; 7、型腔表面粘附铝合金。
适当增加含铁量至0.6~0.8%;8、型腔表面粘附铝合金,尤其是内浇口附近。
压铸件缺陷产生原因及对应措施

1.降低浇注温度,减少收缩量 2.提高压射比压及增压压力,提高致密 性 3.修改内浇口,使压力更好传递,有利 于液态金属补缩作用 4.改变铸件结构,消除金属积聚部位, 壁厚尽可能均匀 5.加快厚大部位冷却 6.加厚料柄,增加补缩的效果
3
夹杂
1.炉料不洁净,回炉料太多 混入压铸件内的金属或非金属 2.合金液未精炼 杂质,加工后可看到形状不规 3.用勺取液浇注时带入熔渣 则,大小、颜色、亮度不同的 4.石墨坩埚或涂料中含有石墨脱落混 点或孔洞 入金属液中 5.保温温度高,持续时间长 1.铝合金中杂质锌、铁超过规定范围 铸件基体金属晶粒过于粗大或 2.合金液过热或保温时间过长,导致 极小,使铸件易断裂或磁碎 晶粒粗大 3.激烈过冷,使晶粒过细 1.压力不足,基体组织致密度差 2. 内部缺陷引起,如气孔、缩孔、渣 压铸件经耐压试验,产生漏气 孔、裂纹、缩松、冷隔、花纹 、渗水 3.浇注和排气系统设计不良 4.压铸冲头磨损,压射不稳定 机械加工过程或加工后外观检 查或金相检查:铸件上有硬度 高于金属基体的细小质点或块 状物使刀具磨损严重,加工后 常常显示出不同的亮度 一、非金属硬点: 1.混入了合金液表面的氧化物 2.合金与炉衬的反应物 3.金属料混入异物 4.夹杂物
铸件缺陷产生原因及应对措施
一、表面缺陷
序号 缺陷名称 特征
沿开模方向铸件表面呈现条状 的拉伤痕迹,有一定深度,严 重时为一面状伤痕;另一种是 金属液与模具产生焊合、粘附 而拉伤,以致铸件表面多肉或 缺肉
产生原因
1.型腔表面有损伤 2.出模方向斜度太小或倒斜 3. 顶出时偏斜 4.浇注温度过高或过低、模温过高 导 致合金液产生粘附 5.脱模剂使用效果不好 6. 铝合金成分铁含量低于 7.冷却时间过长或过短 1.合金液在压室充满度过低,易产生 卷气,压射速度过高 2. 模具排气不良 3. 熔液未除气,熔炼温度过高 4.模温过高,金属凝固时间不够,强 度不够,而过早开模顶出铸件,受压 气体膨胀起来 5.脱模剂太多 6.内浇口开设不良,充填方向不顺
压铸产品的几种常见缺陷和对应分析
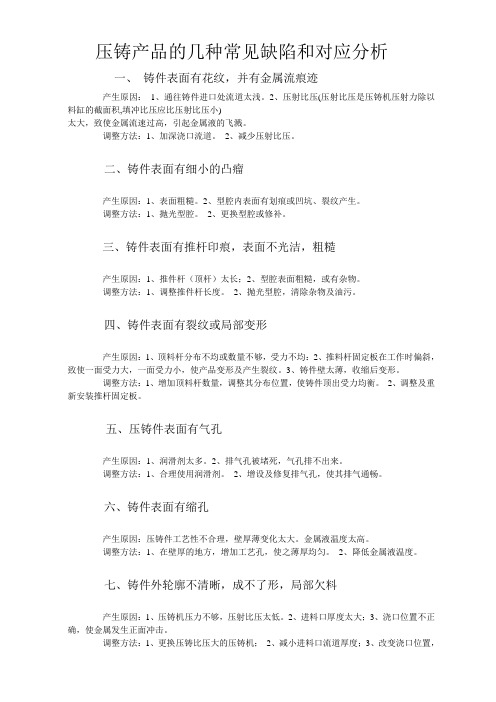
压铸产品的几种常见缺陷和对应分析一、铸件表面有花纹,并有金属流痕迹产生原因:1、通往铸件进口处流道太浅。
2、压射比压(压射比压是压铸机压射力除以料缸的截面积,填冲比压应比压射比压小)太大,致使金属流速过高,引起金属液的飞溅。
调整方法:1、加深浇口流道。
2、减少压射比压。
二、铸件表面有细小的凸瘤产生原因:1、表面粗糙。
2、型腔内表面有划痕或凹坑、裂纹产生。
调整方法:1、抛光型腔。
2、更换型腔或修补。
三、铸件表面有推杆印痕,表面不光洁,粗糙产生原因:1、推件杆(顶杆)太长;2、型腔表面粗糙,或有杂物。
调整方法:1、调整推件杆长度。
2、抛光型腔,清除杂物及油污。
四、铸件表面有裂纹或局部变形产生原因:1、顶料杆分布不均或数量不够,受力不均:2、推料杆固定板在工作时偏斜,致使一面受力大,一面受力小,使产品变形及产生裂纹。
3、铸件壁太薄,收缩后变形。
调整方法:1、增加顶料杆数量,调整其分布位置,使铸件顶出受力均衡。
2、调整及重新安装推杆固定板。
五、压铸件表面有气孔产生原因:1、润滑剂太多。
2、排气孔被堵死,气孔排不出来。
调整方法:1、合理使用润滑剂。
2、增设及修复排气孔,使其排气通畅。
六、铸件表面有缩孔产生原因:压铸件工艺性不合理,壁厚薄变化太大。
金属液温度太高。
调整方法:1、在壁厚的地方,增加工艺孔,使之薄厚均匀。
2、降低金属液温度。
七、铸件外轮廓不清晰,成不了形,局部欠料产生原因:1、压铸机压力不够,压射比压太低。
2、进料口厚度太大;3、浇口位置不正确,使金属发生正面冲击。
调整方法:1、更换压铸比压大的压铸机;2、减小进料口流道厚度;3、改变浇口位置,防止对铸件正面冲击。
八、铸件部分未成形,型腔充不满产生原因:1、压铸模温度太低;2、金属液温度低;3、压机压力太小,4、金属液不足,压射速度太高;5、空气排不出来。
调整方法:1、2、提高压铸模,金属液温度;3、更换大压力压铸机。
4、加足够的金属液,减小压射速度,加大进料口厚度。
压铸件常见的缺陷分析及其改善措施
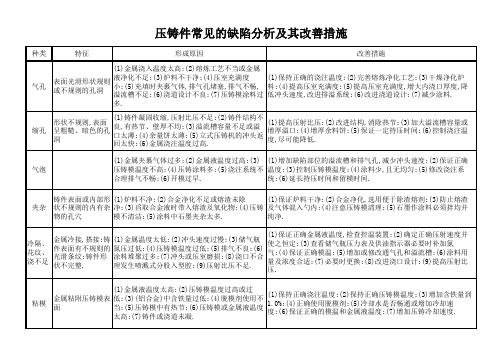
粘模
金属粘附压铸模表 面
(1)金属液温度太高;(2)压铸模温度过高或过 低;(3)(铝合金)中含铁量过低;(4)脱模剂使用不 当;(5)压铸模中有热节;(6)压铸模或金属液温度 太高;(7)铸件或浇道未凝.
(1)保持正确浇注温度;(2)保持正确压铸模温度;(3)增加含铁量到 1.0%;(4)正确使用脱模剂;(5)冷却水是否畅通或增加冷却速 度;(6)保证正确的模温和金属液温度;(7)增加压铸冷却速度.
纯净.
ቤተ መጻሕፍቲ ባይዱ
冷隔、 花纹、 浇不足
金属冷接,搭接;铸 (1)金属温度太低;(2)冲头速度过慢;(3)储气瓶
件表面有不规则的 氮压过低;(4)压铸模温度过低;(5)排气不良;(6)
光滑条纹;铸件形 涂料堆聚过多;(7)冲头或压室磨损;(8)浇口不合
状不完整.
理发生喷溅式分股入型腔;(9)压射比压不足.
(1)保证正确金属液温度,检查控温装置;(2)确定正确压射速度并 使之恒定;(3)查看储气瓶压力表及供油指示器必要时补加氮 气;(4)保证正确模温;(5)增加或修改通气孔和溢流槽;(6)涂料用 量及浓度合适;(7)必要时更换;(8)改进浇口设计;(9)提高压射比 压.
气泡
(1)金属夹裹气体过多;(2)金属液温度过高;(3) (1)增加缺陷部位的溢流槽和排气孔,减少冲头速度;(2)保证正确
压铸模温度不高;(4)压铸涂料多;(5)浇注系统不 温度;(3)控制压铸模温度;(4)涂料少,且无均匀;(5)修改浇注系
合理排气不畅;(6)开模过早.
统;(6)延长持压时间和留模时间.
压铸件常见的缺陷分析及其改善措施
种类
特征
形成原因
改善措施
气孔
(1)金属浇入温度太高;(2)熔炼工艺不当或金属
压铸件常见缺陷分析
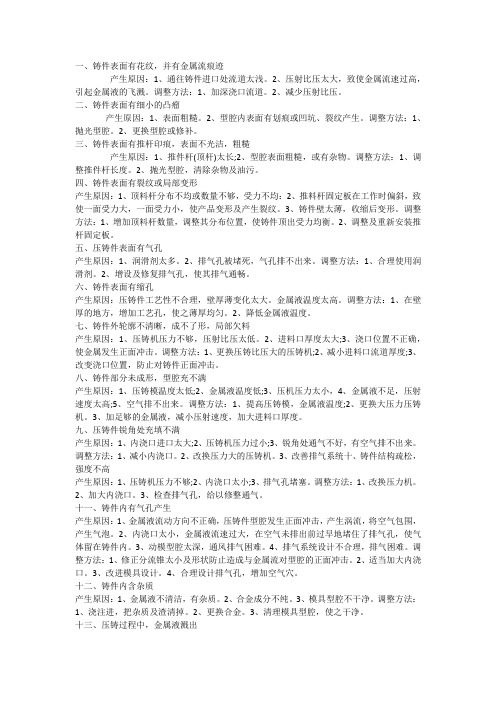
一、铸件表面有花纹,并有金属流痕迹产生原因:1、通往铸件进口处流道太浅。
2、压射比压太大,致使金属流速过高,引起金属液的飞溅。
调整方法:1、加深浇口流道。
2、减少压射比压。
二、铸件表面有细小的凸瘤产生原因:1、表面粗糙。
2、型腔内表面有划痕或凹坑、裂纹产生。
调整方法:1、抛光型腔。
2、更换型腔或修补。
三、铸件表面有推杆印痕,表面不光洁,粗糙产生原因:1、推件杆(顶杆)太长;2、型腔表面粗糙,或有杂物。
调整方法:1、调整推件杆长度。
2、抛光型腔,清除杂物及油污。
四、铸件表面有裂纹或局部变形产生原因:1、顶料杆分布不均或数量不够,受力不均:2、推料杆固定板在工作时偏斜,致使一面受力大,一面受力小,使产品变形及产生裂纹。
3、铸件壁太薄,收缩后变形。
调整方法:1、增加顶料杆数量,调整其分布位置,使铸件顶出受力均衡。
2、调整及重新安装推杆固定板。
五、压铸件表面有气孔产生原因:1、润滑剂太多。
2、排气孔被堵死,气孔排不出来。
调整方法:1、合理使用润滑剂。
2、增设及修复排气孔,使其排气通畅。
六、铸件表面有缩孔产生原因:压铸件工艺性不合理,壁厚薄变化太大。
金属液温度太高。
调整方法:1、在壁厚的地方,增加工艺孔,使之薄厚均匀。
2、降低金属液温度。
七、铸件外轮廓不清晰,成不了形,局部欠料产生原因:1、压铸机压力不够,压射比压太低。
2、进料口厚度太大;3、浇口位置不正确,使金属发生正面冲击。
调整方法:1、更换压铸比压大的压铸机;2、减小进料口流道厚度;3、改变浇口位置,防止对铸件正面冲击。
八、铸件部分未成形,型腔充不满产生原因:1、压铸模温度太低;2、金属液温度低;3、压机压力太小,4、金属液不足,压射速度太高;5、空气排不出来。
调整方法:1、提高压铸模,金属液温度;2、更换大压力压铸机。
3、加足够的金属液,减小压射速度,加大进料口厚度。
九、压铸件锐角处充填不满产生原因:1、内浇口进口太大;2、压铸机压力过小;3、锐角处通气不好,有空气排不出来。
压铸件缺陷原因分析

三、砂孔(有气孔和缩孔之分,为铸件表面或截面上出现不规则的小孔,我们统称为 “砂孔”)
原因分析:
1、进浇口过厚,填充方式不当,造成浇口与铸件断面处形成砂孔。 2、使用原材料质量差,杂质及水口料所占比例过大。 3、浇口位置不当造成金属液流动混乱,在型腔里形成涡流,此种状态形成的气孔在铸件表面看
3、成型时间不够长,即冷却时间过短,铸件没有完全定型硬化,铸件脱模后,留在铸件内的气 体膨胀而形成气泡。
4、脱模剂配比过多,生产时喷的脱模剂配比太浓、太多,造成模具温度过低,析出的气体不易 蒸发排出,形成气泡缺陷原因分析
一、披锋,又称毛刺、飞边,是在铸件的分型面或滑块、镶件、顶针等处凸出过多的 金属薄片。
原因分析:
1、压铸机的安装调整不良,压铸机必须安装在水平的地面上,安装好以后,动模板与定模板要 平行,各种压力调整完成,方能用于生产。
2、模具制造不良,配合不严密,定模与动模闭合后在两者之间不能留有空隙,否则生产时必有 多余合金飞出形成披锋。
四、起泡(在铸件表面有光滑的凸起的鼓包,形成位置不固定,有明泡、暗泡、水纹 泡之分)
原因分析:
1、模具排气不良,排气位置不当,合金溶液充填模腔后,铸件某些部位的排渣包、排气槽等排 溢系统开得不够大、不够深、位置不当而使得留在模腔内的气体不能顺利排出,留在铸件中 形成起泡。
2、进浇口过多,由于有两条以上的液流同时充型,因液流方向、速度等不同,容易使两股液流 产生对撞,在碰撞出形成涡流,产生气泡。
3、浇注系统不合理,如流程长、流道曲折,且流道四周产生大的披锋,所有这些会损耗填充压 力而导致水纹。
4、排气溢流系统不良,渣包位置设置不合理或不够大,模腔里面的空气排出不充分,影响溶液 填充。
压铸件常见缺陷及解决办法

压铸件常见缺陷及解决办法
一、压铸件缺陷
1、压铸凹痕:压铸凹痕是指在压铸后件表面出现的凹痕或沟等处的缺陷。
2、拉伤表面:这种缺陷是指当件拉伸出模后,件毛刺或表面斑点等特
征缺陷。
3、起火晶:起火晶是指压铸件中凝固过程中熔料里存在的大量小气泡
缺陷。
4、压型:这种缺陷是指模具中几个竖向型腔偏移位置,影响压铸件内
部夹紧、定位等缺陷。
二、解决办法
1、压铸凹痕:首先要检查有没有流淌痕或模具内应有的空气渗入,来
找出原因,同时要及时修整和修复模具。
2、拉伤表面:要检查压铸模具表面的震动是否合理,如果表面粗糙可
以适当采用打磨,以降低拉伤表面。
3、起火晶:保证熔料温度合适,及时移动和改变拳头垫针,使熔料流
动均匀;改进圠充,减少浪涌现象;改变压力以降低小气泡形成的机会;合理的检查温度之间的差异。
4、压型:检查模具的型腔,确保它们定位准确,消除产品的分离现象;合理更换冷却介质等以降低成型环境的温度差异。
压铸件缺陷分析

缺陷名称特征形成原因防止方法及修补气孔1、气孔主要呈梨形,圆形或椭圆形2、孔壁表面光滑,带在金属光泽3、大多存在于铸件皮下,大气孔单独存在,小气孔成群出现4、油烟气孔呈油黄色1、液体金属浇注时被卷入的气体 在合金液凝固后以气孔的形式存在于铸件中2、金属与铸形反应后在铸件表皮下生成皮下气孔3、合金液中的夹渣或氧化皮上附着的气体被混入合金液后形成气孔1、浇注时防止空气卷入2、合金液在进入形腔前先经过过滤网以去除合金中的夹渣、氧化皮和气泡3、更换铸形材料或加涂料层防止合金液与铸形发生反应4、在允许焊补部位将缺陷清理干净后进行焊补针孔1、均匀的分布在铸件的整个断面上的析出性小孔(直径小于1mm)2、凝固快的部位孔小数量少,凝固慢的部位孔大数量多3、在共晶合金中呈圆形孔洞,在凝固间隔宽的合金中呈长形孔洞4、在X射线底片上呈小黑点,在断口上呈互不连接的乳白色小凹点合金在液体状态下溶解的气体(主要是氢),在合金凝固过程中自合金中析出而形成的均布形式的孔洞1、合金液体状态下彻底精炼除气2、在凝固过程中加大凝固速度,防止溶解的气体自合金中析出3、铸件在压力下凝固,防止合金溶解的气体析出4、炉料、辅助材料及工具应干燥缩孔和缩松1、铸件凝固过程由于补缩不良形成的孔洞2、缩孔相对集中,形状极不规则,孔壁粗糙并带有枝晶状,常出现在铸件最后凝固部位3、缩松细小而分散地出现在铸件的断面上4、铸件缩孔和缩松引起气密性试验的渗漏1、铸件冒口位置和尺寸与热节不配套,不能有效补缩引起缩孔2、同时凝固的铸件厚大部位不能有效获得补缩引起缩松合理设计铸件浇冒系统和浇注位置,尽量保证铸件顺序和冒口充分补缩,可以减轻缩孔和缩松产生疏松(显微缩松)1、呈海绵状的不紧密组织,严重时呈缩孔2、孔的表面呈粗糙的凹坑,晶状粗大3、断口呈灰色或浅黄色,热处理后为灰白、浅黄或灰黑色4、多在热节等铸件缓慢凝固部位产生,分布在枝晶间或枝晶内5、X射线底片上呈云雾状,荧光检查时呈密集的小亮点1、合金液除气不干净形成气体性疏松2、最后凝固部位补缩不足3、铸型局部过热、水分过多、排气不良1、保证合理凝固顺序和补缩2、炉料洁净3、在疏松部位放置冷铁4、在允许焊补的部位可将缺陷部位清理干净后焊补夹杂由涂料、造型材料、耐火材料等混入合金液中而形成的铸件表面或内部的与基体金属成分不同的质点1、外来物混入液体合金并浇注入铸型2、精炼效果不良3、铸型的内腔表面的外来物或造型材料剥落1、仔细精炼并注意扒渣2、熔炼工具涂层附着牢固3、浇注系统及型腔应清理干净4、炉料应保持干净5、表面夹杂可打磨去除,必要时可进行焊补冷隔1、铸件上穿透或不穿透性的,边缘呈圆角状的裂缝2、多出现在远离浇口的宽大薄壁部位,金属汇合部位以及冷铁和芯撑等激冷部位1、金属液浇注温度太低2、金属液充型流程太长3、壁厚太薄4、冷铁或芯撑冷却能力太大1、适当提高浇注温度2、调整浇冒系统位置,减小金属液流程3、适当加大薄壁铸件的壁厚4、减少冷铁或芯撑尺寸夹渣1、氧化夹渣以团絮状存在于铸件内部,断口呈黄色或灰白色,无光泽2、熔剂夹渣呈暗褐色点状,夹渣清除后呈光滑表面的孔洞,在空气中暴露一段时间后,有时出现腐蚀特征3、一般存在于铸件上部或浇注死角部位1、精炼变质处理后除渣不干净2、精炼变质后静置时间不够3、浇注系统不合理,二次氧化皮卷入合金液中4、精炼后合金液搅动或被污染1、严格按精炼变质浇注工艺操作2、浇注时应使金属液流平衡地注入铸型,采用过滤技术3、炉料应保持洁净,回炉料处理及使用量应严格遵守工艺规程裂纹1、铸件凝固后在较低的温度下产生的裂纹称冷裂。
压铸缺陷图文详解

1 ,压铸部分
3,粘模: 压铸件表面缺料,且没有
金属光泽。
产生的可能原因: 1,模具局部温度过高; 2,模具表面粗糙; 3,开模时间不当。
预防及改善方法: 1,注意喷水,保持模温平衡; 2,抛光模具; 3,调整开模时间,不可过长也不可过短。
1 ,压铸部分
4,拉模: 压铸件表面顺着开模(或
滑块)方向留有擦伤的痕迹。
产生的可能原因: 1,材料杂质含量过高,降低了可塑性; 2,模温太低; 3,铸件壁厚过薄或壁厚剧烈变化; 4,铸件收缩产生应力而开裂 5,顶出时受力不均匀; 6,填充不良,铸件凝固未融合。
预防及改善方法: 1,控制铝料成分; 2,提高模温; 3,改善产品结构,如加大R角; 4,适当增加顶杆。
1 ,压铸部分
产生的可能原因: 1,铸件顶出有偏斜; 2,喷水过少,冷却不够; 3,成型表面光洁度不够,脱模方向上平整度较差。
预防及改善方法: 1,加大拔模(脱模)斜度; 2,拉伤位置多喷水(但不可出现冷隔); 3,调整顶杆,使顶出力平衡。
1 ,压铸部分
5,开裂: 压铸件本体被破坏裂开,
呈不规则线形,在外力作用下 有延展趋势。
要求公差。
产生的可能原因: 1,铸件收缩不均匀; 2,顶出过程受力不均匀; 3,铸件刚性不足,堆放不合理或去浇口不当。
预防及改善方法: 1,改善产品结构,使壁厚均匀; 2,对于大而薄的产品,不要堆叠,更不可随意丢、仍; 3,调整开模时间、顶出时间和顶出速度; 4, 适当矫形。
1 ,压铸部分
10,级位(段差/台阶): 压铸件表面出现阶梯痕迹。
7,气泡: 压铸件表面有气体聚集,
甚至在铸件表面鼓泡。
产生的可能原因: 1,有卷入性气体; 2,铝料中气体较多; 3,局部模温过高,料温过高。
压铸件缺陷分析

施。
渗漏
孔、渣孔、裂纹、缩松、冷 隔、花纹。
3. 改进浇注系统和排气系统。 4. 进行浸渗处理,弥补缺陷。
3. 浇注和排气系统设计不良。
5. 更换压室、冲头。
4. 压铸冲头磨损, 压射不稳定。
机械加工过程 A、 非金属硬点
1. 铸造时不要把合金液表面的
或加工后外观检
1. 混入了合金液表面的氧化
阻力大而引起顶出时变形。
铸件表面有与
1. 首先进入型腔的金属液形成
1. 提高金属液温度。
金属液流动方向
一个极薄的而又不完全的金
2. 提高模温。
一致的条纹, 有明
属层后,被后来的金属液所
3. 调整内浇道截பைடு நூலகம்积或位置。
显可见的与金属 流痕
基体颜色不一样 花纹
的无方向性的纹
弥补而留下的痕迹。 2. 模温过低,模温不均匀。 3. 内浇道截面积过小及位置不
压铸件缺陷分析
一、 缺陷分类及影响因素 1.缺陷分类 1) 几何缺陷:压铸件形状、尺寸与技术要求有偏离;尺寸超差、挠曲、变形等。 2) 表面缺陷:压铸件外观不良,出现花纹、流痕、冷隔、斑点、缺肉、毛刺、飞边、缩痕、 拉伤等。 3) 内部缺陷:气孔、缩孔、缩松、裂纹、夹杂等,内部组织、机械性能不符合要求。 2.影响因素 1) 压铸机引起
脆性 极小,使铸件易
2. 合金液过热或保温时间过
3. 降低浇注温度。
断裂或碰碎。
长,导致晶粒粗大。
4. 提高模具温度。
3. 激烈过冷,使晶粒过小。
压铸件经耐压 1. 压力不足,基体组织致密度
1. 提高比压。
试验,产生漏气,
差。
压铸件的缺陷及产生的原因
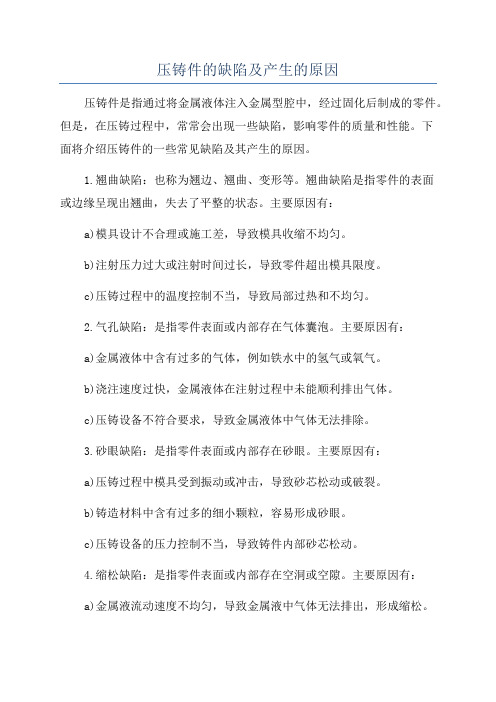
压铸件的缺陷及产生的原因压铸件是指通过将金属液体注入金属型腔中,经过固化后制成的零件。
但是,在压铸过程中,常常会出现一些缺陷,影响零件的质量和性能。
下面将介绍压铸件的一些常见缺陷及其产生的原因。
1.翘曲缺陷:也称为翘边、翘曲、变形等。
翘曲缺陷是指零件的表面或边缘呈现出翘曲,失去了平整的状态。
主要原因有:a)模具设计不合理或施工差,导致模具收缩不均匀。
b)注射压力过大或注射时间过长,导致零件超出模具限度。
c)压铸过程中的温度控制不当,导致局部过热和不均匀。
2.气孔缺陷:是指零件表面或内部存在气体囊泡。
主要原因有:a)金属液体中含有过多的气体,例如铁水中的氢气或氧气。
b)浇注速度过快,金属液体在注射过程中未能顺利排出气体。
c)压铸设备不符合要求,导致金属液体中气体无法排除。
3.砂眼缺陷:是指零件表面或内部存在砂眼。
主要原因有:a)压铸过程中模具受到振动或冲击,导致砂芯松动或破裂。
b)铸造材料中含有过多的细小颗粒,容易形成砂眼。
c)压铸设备的压力控制不当,导致铸件内部砂芯松动。
4.缩松缺陷:是指零件表面或内部存在空洞或空隙。
主要原因有:a)金属液流动速度不均匀,导致金属液中气体无法排出,形成缩松。
b)金属液温度过低或过高,凝固速度过快或过慢,容易形成缩松。
c)压铸设备的注射压力和速度不匹配,导致金属液无法充分填充模腔。
5.热裂缺陷:是指零件在冷却过程中出现裂纹。
主要原因有:a)压铸件的凝固收缩不均匀,产生内部应力,导致零件热裂。
b)零件的壁厚不均匀,导致凝固速度不同,产生应力集中。
c)零件冷却速度过快,导致表面和内部温度差异大,产生应力热裂。
除了以上列举的缺陷外,还有一些其他常见的缺陷,如砂眼、金属氧化、皮肤等。
这些缺陷的产生原因也是多种多样的,包括模具的设计、注射过程的控制、金属材料的选择等等。
因此,为了减少和避免压铸件的缺陷,需要从以下几个方面进行改进和控制:1)模具设计和制造的精准度和稳定性。
2)铸件的金属液配方和处理技术。
压铸件缺陷汇总(图文)

解决方法
适当提高浇注温度/模具温度
改变合金成分,提高流动性
改进浇注系统,加大内浇口速度,改善填充条件合理使用脱模剂
解决方法
改进制件结构,减少壁厚差,增大铸造圆角
缺陷名称流痕
缺陷名称
缺陷等级
缺陷释义合金液未充满型腔,制件上出现填
解决方法降低浇注温度
解决方法适当降低模温
解决方法增加脱模角度
缺陷名称缩痕
解决方法
解决方法模具进行表面氮化或氧化处理合理选用脱模剂
合理使用脱模剂
解决方法提高注射压力
解决方法
解决方法
解决方法增加锁模力
解决方法见“铸造毛刺”的解决方法。
压铸件不良及原因分析
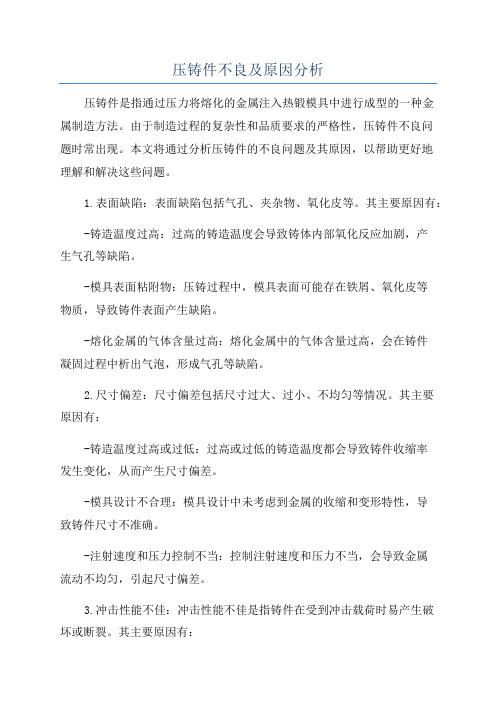
压铸件不良及原因分析压铸件是指通过压力将熔化的金属注入热锻模具中进行成型的一种金属制造方法。
由于制造过程的复杂性和品质要求的严格性,压铸件不良问题时常出现。
本文将通过分析压铸件的不良问题及其原因,以帮助更好地理解和解决这些问题。
1.表面缺陷:表面缺陷包括气孔、夹杂物、氧化皮等。
其主要原因有:-铸造温度过高:过高的铸造温度会导致铸体内部氧化反应加剧,产生气孔等缺陷。
-模具表面粘附物:压铸过程中,模具表面可能存在铁屑、氧化皮等物质,导致铸件表面产生缺陷。
-熔化金属的气体含量过高:熔化金属中的气体含量过高,会在铸件凝固过程中析出气泡,形成气孔等缺陷。
2.尺寸偏差:尺寸偏差包括尺寸过大、过小、不均匀等情况。
其主要原因有:-铸造温度过高或过低:过高或过低的铸造温度都会导致铸件收缩率发生变化,从而产生尺寸偏差。
-模具设计不合理:模具设计中未考虑到金属的收缩和变形特性,导致铸件尺寸不准确。
-注射速度和压力控制不当:控制注射速度和压力不当,会导致金属流动不均匀,引起尺寸偏差。
3.冲击性能不佳:冲击性能不佳是指铸件在受到冲击载荷时易产生破坏或断裂。
其主要原因有:-金属组织不均匀:熔化金属在快速冷却过程中,易产生晶粒过大、晶界异常等问题,导致冲击性能下降。
-含气量过高:熔化金属中的气体含量过高,会在铸件凝固过程中析出气泡,降低冲击性能。
-金属材料的不合理选择:选择不合适的金属材料,其化学成分和机械性能可能不满足冲击性能要求。
4.裂纹:裂纹是指铸件表面或内部出现的细小或明显的裂缝。
其主要原因有:-材料内部应力过大:熔化金属在凝固过程中,由于收缩等原因会产生内部应力,过大的应力会导致铸件出现裂纹。
-注射速度和压力控制不当:控制注射速度和压力不当,使得金属充实不充分或过量,都会导致铸件的裂纹。
-模具温度不均匀:模具温度不均匀会导致铸件冷却速率不均匀,产生应力过大而发生裂纹。
5.金属疲劳:金属疲劳是指铸件在循环载荷下产生的微裂纹最终引起断裂。
- 1、下载文档前请自行甄别文档内容的完整性,平台不提供额外的编辑、内容补充、找答案等附加服务。
- 2、"仅部分预览"的文档,不可在线预览部分如存在完整性等问题,可反馈申请退款(可完整预览的文档不适用该条件!)。
- 3、如文档侵犯您的权益,请联系客服反馈,我们会尽快为您处理(人工客服工作时间:9:00-18:30)。
压铸件缺陷分析:压铸件缺陷中,出现最多的是气孔。
气孔特征。
有光滑的表面,表现形式可以在铸件表面、或皮下针孔、也可能在铸件内部。
(铸件壁内气孔)一般呈圆形或椭圆形,具有光滑的表面,一般是发亮的氧化皮,有时呈油黄色。
(表面气孔)气泡可通过喷砂发现,内部气孔气泡可通过X光透视或机械加工发现气孔气泡在X 光底片上呈黑色.<A>气体来源(1)合金液析出气体:a与原材料有关;b与熔炼工艺有关(2)压铸过程中卷入气体:a与压铸工艺参数有关b与模具结构有关(3)脱模剂分解产生气体:a与涂料本身特性有关b与喷涂工艺有关<B>原材料及熔炼过程产生气体分析铝液中的气体主要是氢,约占了气体总量的85%。
熔炼温度越高,氢在铝液中溶解度越高,但在固态铝中溶解度非常低,因此在凝固过程中,氢析出形成气孔。
氢的来源:(1)大气中水蒸气,金属液从潮湿空气中吸氢。
(2)原材料本身含氢量,合金锭表面潮湿,回炉料脏,油污。
(3)工具、熔剂潮湿。
<C>压铸过程产生气体分析由于压室、浇注系统、型腔均与大气相通,而金属液是以高压、高速充填,如果不能实现有序、平稳的流动状态,金属液产生涡流,会把气体卷进去。
压铸工艺制定需考虑以下问题:(1)金属液在浇注系统内能否干净、平稳地流动,不会产生分离和涡流。
(2)有没有尖角区或死亡区存在?(3)浇注系统是否有截面积的变化?(4)排气槽、溢流槽位置是否正确?是否够大?是否会被堵住?气体能否有效、顺畅排出?应用计算机模拟充填过程,就是为了分析以上现象,以作判断来选择合理的工艺参数。
<D>涂料产生气体分析涂料性能:如发气量大对铸件气孔率有直接影响。
喷涂工艺:使用量过多,造成气体挥发量大,冲头润滑剂太多,或被烧焦,都是气体的来源。
<E>解决压铸件气孔的办法先分析出是什么原因导致的气孔,再来取相应的措施。
(1)干燥、干净的合金料。
(2)控制熔炼温度,避免过热,进行除气处理。
(3)合理选择压铸工艺参数,特别是压射速度。
调整高速切换起点。
(4)顺序填充有利于型腔气体排出,直浇道和横浇道有足够的长度(>50mm),以利于合金液平稳流动和气体有机会排出。
可改变浇口厚度、浇口方向、在形成气孔的位置设置溢流槽、排气槽。
溢流品截面积总和不能小于内浇口截面积总和的60%,否则排渣效果差。
(5)选择性能好的涂料及控制喷涂量。
铸造铝合金的缺陷及防止方法:铸件之缺陷种类繁多其原因亦甚复杂,如:铸造温度,铸造前之除气,除渣处理不完全而形成存气量过高或非金属介在物之混入以及回炉料添加比例再精炼,辅料配方,模具设计及压铸工艺等等。
有关温度、辅料及常见的铸缺件陷及改善建议如下:浇注温度:指铝液浇入压室至填充型腔时的平均温度。
铝合金压铸时的各合金浇注温度见下表:铝合金浇注温度(°C)铸件壁厚< 3 mm 铸件壁厚> 3 mm简单件复杂件简单件复杂件铝硅合金610 ~ 650 640 ~ 700 590 ~ 630 610 ~ 650铝铜合金620 ~ 650 640 ~ 720 600 ~ 640 620 ~ 650铝镁合金640 ~ 650 660 ~ 700 620 ~ 660 640 ~ 680压铸模温度:压铸模既是换热器又是蓄热器在生产前预热以避免金属液激冷;减少压铸模的疲劳应力,故在压铸过程中需保持一定温度。
铝合金压铸件的压铸模工作温度见下表:压铸铝合金压铸模工作温度(°C)铸件壁厚< 3 mm 铸件壁厚> 3 mm简单件复杂件简单件复杂件压铸模工作温度预热温度150~180 200 ~ 230 120 ~ 150 150 ~ 180 连续工作持续温度180 ~ 240 250 ~ 280 150 ~ 180 180 ~ 220压铸用涂料:1.涂料的作用:预防粘膜,减少压铸模的导热,改善铝液的成型性,避免铝液对压铸模的直接冲刷,改善压铸模的填充条件,对压铸模起润滑作用。
2.铝合金压铸件的常用涂料(1) 5% 氧化锌+ 1.2%水玻璃+ 水(2) 胶体石墨(3) (3%~5%)聚乙烯+ 煤油压铸件缺陷及防止方法:铝合金在压铸过程中,除因铝液处理不当(包括除气,变质,合金成分)而造成产品的化学成分及力学性能不合格外,还因压铸工艺选择不当或成型模,装配,涂料使用不当等多种原因引起铸件出现缺陷。
常见的缺陷如下表:缺陷类型产生原因防止方法胀砂,变形压射力过大减小压射力冷隔,气泡,缩孔,疏松,欠铸压射力过小增大压射力流痕及花纹,网状毛边,粘浇注温度过高降低浇注温度膜拉伤,气孔,缩孔,疏松冷隔,欠铸浇注温度过低升高浇注温度缩陷,粘膜拉伤模温过高降低模温流痕及花纹,网状毛边,冷模温过低升高模温隔,裂纹粘膜拉伤,气孔压射速度过大减小压射速度缩陷,冷隔,气孔,欠铸,排气不畅开排气槽等流痕及花纹化学成分不合格,夹渣,铝液除气等处理不当严格铝液处理规程硬点印痕,分层,机械拉伤,设计,装配不当改进设计,注意装配粘膜拉伤,裂纹缺陷名称特征产生原因防止方法拉伤沿开模方向铸件表面呈现条状的拉伤痕迹,有一定深度,严重时为一面状伤痕。
另一种是金属液与模具产生焊合、粘附而拉伤,以致铸件表面多肉或缺肉。
1、型腔表面有损伤2、出模方向斜度太小或倒斜3、顶出时偏斜4、浇注温度过高或过低,模温过高导致合金液产生粘附5、脱模剂使用效果不好6、铝合金成分含铁量低于0.6%7、冷却时间过长或过短1、修理模具表面损伤处,修正斜度,600细油石顺磨提高光洁度2、调整或更换顶杆,使顶出力平衡3、更换离型剂4、调整合金含铁量5、控制合适的浇注温度,控制模具温度6、修改内浇口,避免直冲型芯型壁或对型芯表面进行特殊处理气泡铸件表面有米粒大小的隆起表皮下形成的空洞1、合金液在压室充满度过低,易产生卷气,压射速度过高2、模具排气不良3、溶液未除气,熔炼温度过高4、模温过高,金属凝固时间不够,强度不够,而过早开模顶出铸件,受压气体膨胀起来5、脱模剂太多6、内浇口开设不良,充填方向不顺1、提高金属液充满度2、降低第一阶段压射速度,改变低速与高速压射切换点3、降低模温4、增设排气槽、溢流槽、充分排气5、调整熔炼工艺,进行除气处理6、留模时间延长7、减少脱模剂用量裂纹 1. 铸件表面有呈直线状或波浪形的纹路,狭小而长,在外力作用下有发展趋势2. 冷裂-开裂处金属没有被氧化3. 热裂-开裂处金属已经被氧化 1. 合金中含铁量过高或硅含量过低2. 合金中有害杂质的含量过高,降低了合金的可塑性3. 铝硅合金:铝硅铜合金含锌或含铜量过高;铝镁合金中含镁量过多4. 模具:特别是型芯温度太低5. 铸件壁存有剧烈变之处,收缩受阻,尖角位形成应力6. 留模时间过长,应力大7. 顶出时受力不均匀 1. 正确控制合金成分,在某种情况下可在合金中加纯铝锭以降低合金中含镁量;或在合金中加铝硅中间合金以提高硅含量2. 改变铸件结构,加大圆角,加大出模斜度,减少壁厚差3. 变更或增加顶出位置,使顶出受力均匀4. 缩短开模及抽芯时间5. 提高模温,保持模温稳定变形 1. 铸件几何形状与图纸不符2. 整体变形或局部变形 1. 铸件结构设计不良,引起不均匀收缩2. 开模过早,铸件刚性不够3. 顶杆设置不当,顶出时受力不均匀4. 切除浇口方法不当5. 由于模具表面粗糙造成举报阻力大而引起顶出时变形 1. 改进铸件结构2. 调整开模时间3. 合理设置顶杆位置及数量4. 选择合适的切除浇口方法5. 加强模具型腔表面抛光,减少托模阻力流痕、花纹 1. 铸件表面上有与金属液流动方向一致的条纹,有明显可见的与金属体颜色不一样的无方向性的纹路,无发展趋势 1. 首先进入型腔的金属液形成一个极薄的而又不完全的金属层后,被后来的金属液所弥补而留下的痕迹2. 模温过低,模温不均匀3. 内浇道截面积过小及位置不当产生喷溅4. 作用于金属液的压力不足5. 花纹:涂料用量过多 1. 提高金属液温度2. 提高模温3. 调整内浇道截面积或位置4. 调整充填速度及压力5. 选用合适的涂料及调整用量冷隔 1. 铸件表面有明显的、不规则的、下陷线性纹路(有穿透与不穿透两种)形状细小而狭长,有的交接边缘光滑,在外力作用下有发展的可能 1. 两股金属流相互对接,但未完全熔合而又无夹杂存在其间,两股金属流结合力很薄弱2. 浇注温度或压铸模温度偏低3. 选择合金不当,流动性差4. 浇道位置不对或流路过长5. 充填速度低6. 压射比压低 1. 适当提高浇注温度和模具温度2. 提高压射比压,缩短充填时间3. 提高压射速度,同时加大内浇口截面积4. 改善排气、充填条件5. 正确选用合金,提高合金流动性变色、斑点 1. 铸件表面呈现出不同的颜色及斑点 1. 不合适的脱模剂2. 脱模剂用量过多,局部堆积3. 含有石墨的润滑剂中的石墨落入铸件表层4. 模温过低,金属液温度过低导致不规则的凝固引起 1. 更换优质脱模剂2. 严格喷涂量及喷涂操作3. 控制模温4. 控制金属液温度网状毛翅 1. 压铸件表面上有网状发丝一样凸起或凹陷的痕迹,随压铸次数增加而不断扩大和延伸 1. 压铸模型腔表面龟裂2. 压铸模材质不当或热处理工艺不正确3. 压铸模冷热温差变化大4. 浇注温度过高5. 压铸模预热不足6. 型腔表面粗糙 1. 正确选用压铸模材料及热处理工艺2. 浇注温度不易过高,尤其是高熔点合金3. 模具预热要充分4. 压铸模要定期或压铸一定次数后退火,消除内应力5. 打磨成型部分表面,减少表面粗糙度6. 合理选择模具冷却方法凹陷1、铸件平滑表面上出现凹陷部位 1. 铸件壁厚相差太大,凹陷多产生在厚壁处2. 模具局部过热,过热部分凝固慢3. 压射比压低4. 由憋气引起型腔气体排不出,被压缩在型腔表面与金属液界面之间2. 铸件壁厚设计尽量3. 模具局部领却调整4. 提高压射比压5. 改善型腔排气条件欠铸(缺料)1、铸件表面有浇不足部位1、流动性差原因:1) 合金液吸气、氧化夹杂物,含铁量高,使其质量差而降低流动性2) 浇注温度低或模温低2、充填条件不良:1) 比压过低2) 卷入气体过多,型腔的背压变高,充型受阻3、操作不良,喷涂料过度,涂料堆积,气体挥发不掉1、提高合金液质量2、提高浇注温度或模具温度3、提高比压、充填速度4、改善浇注系统金属液的导流方式,在欠铸部位加开溢流槽、排气槽5、检查压铸机能力是否足够毛刺飞边 1. 压铸件在分型面边缘上出现金属薄片 1. 锁模力不够2. 压射速度过高,形成压力冲击峰过高3. 分型面上杂物未清理干净4. 模具强度不够造成变形5. 镶块、滑块磨损与分型面不平齐 1. 检查合模力和增压情况,调整压铸工艺参数2. 清洁型腔及分型面3. 修理模具4. 最好是采用闭合压射结束时间控制系统,可实现无飞边压铸气孔(内部缺陷) 1. 解剖后外观检测或探伤检查,气孔具有光滑的表面、形状为圆形 1. 合金液导入方向不合理或金属液流动速度太高,产生喷射;过早堵住排气道或正面冲击壁而形成漩涡包住空气,这种气孔多产生排气不良或深腔处2. 由于炉料不干净或熔炼温度过高,使金属液中较多的气体没除净,在凝固时析出没能充分排出。