环氧树脂浇注成型工艺
环氧树脂指标
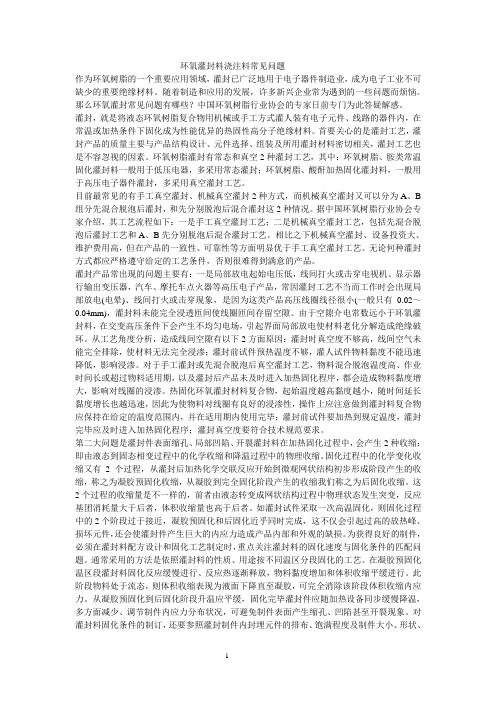
环氧灌封料浇注料常见问题作为环氧树脂的一个重要应用领域,灌封已广泛地用于电子器件制造业,成为电子工业不可缺少的重要绝缘材料。
随着制造和应用的发展,许多新兴企业常为遇到的一些问题而烦恼。
那么环氧灌封常见问题有哪些?中国环氧树脂行业协会的专家日前专门为此答疑解惑。
灌封,就是将液态环氧树脂复合物用机械或手工方式灌人装有电子元件、线路的器件内,在常温或加热条件下固化成为性能优异的热固性高分子绝缘材料。
首要关心的是灌封工艺,灌封产品的质量主要与产品结构设计、元件选择、组装及所用灌封材料密切相关,灌封工艺也是不容忽视的因素。
环氧树脂灌封有常态和真空2种灌封工艺,其中:环氧树脂、胺类常温固化灌封料一般用于低压电器,多采用常态灌封;环氧树脂、酸酐加热固化灌封料,一般用于高压电子器件灌封,多采用真空灌封工艺。
目前最常见的有手工真空灌封、机械真空灌封2种方式,而机械真空灌封又可以分为A、B 组分先混合脱泡后灌封,和先分别脱泡后混合灌封这2种情况。
据中国环氧树脂行业协会专家介绍,其工艺流程如下:一是手工真空灌封工艺;二是机械真空灌封工艺,包括先混合脱泡后灌封工艺和A、B先分别脱泡后混合灌封工艺。
相比之下机械真空灌封、设备投资大、维护费用高,但在产品的一致性、可靠性等方面明显优于手工真空灌封工艺。
无论何种灌封方式都应严格遵守给定的工艺条件,否则很难得到满意的产品。
灌封产品常出现的问题主要有:一是局部放电起始电压低,线间打火或击穿电视机、显示器行输出变压器,汽车、摩托车点火器等高压电子产品,常因灌封工艺不当而工作时会出现局部放电(电晕)、线间打火或击穿现象,是因为这类产品高压线圈线径很小(一般只有0.02~0.04mm),灌封料未能完全浸透匝间使线圈匝间存留空隙。
由于空隙介电常数远小于环氧灌封料,在交变高压条件下会产生不均匀电场,引起界面局部放电使材料老化分解造成绝缘破坏。
从工艺角度分析,造成线间空隙有以下2方面原因:灌封时真空度不够高,线间空气未能完全排除,使材料无法完全浸渗;灌封前试件预热温度不够,灌人试件物料黏度不能迅速降低,影响浸渗。
环氧树脂碳纤维复合材料的成型工艺与应用
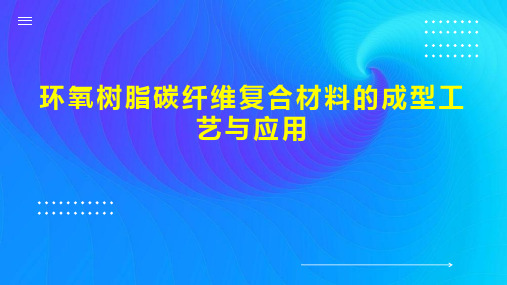
碳纤维缠绕复合材料成型工艺
碳纤维缠绕复合材料的制备过程主要包括纤维铺放、树脂浸润和热处理等环 节。下面分别介绍这些步骤及其对材料性能的影响。
1、纤维铺放:此步骤是碳纤维缠绕复合材料制备的关键环节之一。纤维的 排列方向、密度和厚度等因素都会影响最终产品的性能。铺放过程中需采用专门 的设备和工艺,确保纤维分布的准确性和稳定性。
引言:碳纤维增强环氧树脂复合材料是一种具有优异性能的材料,因其具有 高强度、高韧性、耐腐蚀、轻质等优点而被广泛应用于航空、航天、汽车、体育 器材等领域。随着科技的发展,对于这种复合材料的研究和应用也越来越广泛。 液体成型是一种常见的复合材料制造工艺,具有成本低、效率高等优点,因此, 研究碳纤维增强环氧树脂复合材料的液体成型工艺及其性能具有重要意义。
在航天领域,碳纤维树脂基复合材料被广泛应用于火箭箭体、卫星平台等关 键部位。其轻质、高强度、耐腐蚀等优点使得它在航天领域具有广泛的应用前景。
在汽车领域,碳纤维树脂基复合材料被广泛应用于汽车车身、底盘等部位。 其高强度、耐腐蚀和轻质等优点可以提高汽车的性能和舒适性,同时也可以提高 汽车的安全性。
四、结论
环氧树脂碳纤维复合材料的成型工艺主要包括以下步骤: 1、纤维浸润:将碳纤维或其它纤维浸入环氧树脂中,使其充分浸润。
2、固化:在一定的温度和压力下,环氧树脂发生固化反应,形成固态复合 材料。
3、后处理:对固化后的复合材料进行切割、打磨、钻孔等后处理,以满足 不同应用场景的需求。
3、后处理:对固化后的复合材 料进行切割、打磨、钻孔等后处 理
三、碳纤维树脂基复合材料的应 用研究进展
碳纤维树脂基复合材料在航空、航天、汽车等领域得到了广泛应用。近年来, 随着技术的不断发展,其在这些领域的应用研究也取得了显著的进展。
环氧树脂的生产工艺

对设备 的腐蚀
产品 质量
苯酚 回收量
反应 周期
劳动 强度
硫酸法
旧工艺 新工艺
简单 更简单
间歇 间歇
很严重 较严重
很差 较差
— —
长 一般
高 较高
盐酸法 氯化氢气体法 三氯化硼法 四氯化硅甲苯法 疏基离子交换 树脂法
复杂 复杂 一般 一般 较简单
间歇 间歇、连续 间歇 间歇、连续 连续
二 环氧树脂的交联固化
固化温度与使用固化剂种类和用量有关,从低温到高温均可。其固化过程一般不放出水或其它低分子,故作胶粘剂、层压制品或浇注灌封的制品均不会有多孔性缺陷。
环氧树脂的固化剂种类繁多,随着科技进步及各部门的需要,新的固化剂还在不断涌现。
双酚A环氧树脂本身很稳定,即使加热到200℃也不变化。由于树脂中含有很多可以反应的活性基团(如环氧基、羟基)所以树脂均能在酸性或碱性固化剂的作用下固化。
弹性模量低、耐温性差、层间剪切强度低、耐老化差
轻质高强
FRP性能特点
性能的 可设计性好
工艺性好
邻苯型、间苯型、双酚A、乙烯基系
FRP生产原料
01
UP
02
树脂
03
生产原料
04
固化剂
EP 填料 助剂
FRP生产工艺
● 手糊成型工艺 ● 喷射成型法 ● 缠绕成型法 ● 注射成型法 ● 模压法 ● 连续挤拉成型法 ● 层压法
NaOH浓度:30%
A 低分子量树脂的生产
配料:双酚A:环氧氯丙烷:NaOH=1:2.75:2.42(摩尔)
除配料比有差别外,操作和温度等基本一致。 中等分子量: 双酚A:环氧氯丙烷:NaOH=1:1.473:1.598(摩尔); NaOH浓度10%。 高分子量: 双酚A:环氧氯丙烷:NaOH=1:1.218:1.185; NaOH浓度10%。
环氧树脂碳纤维复合材料的成型工艺
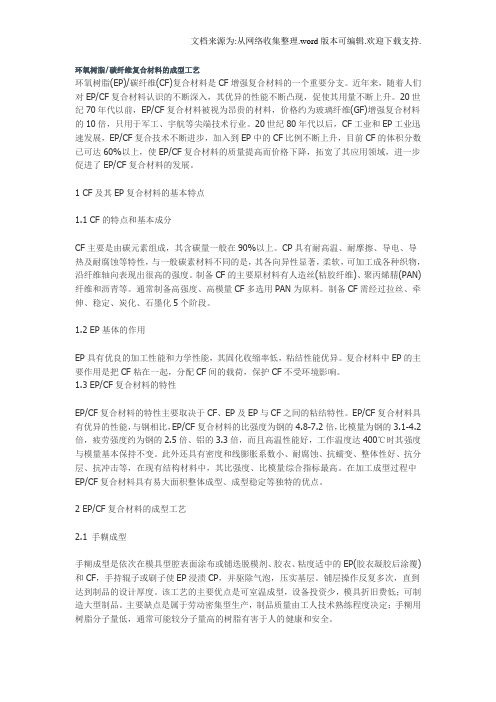
环氧树脂/碳纤维复合材料的成型工艺环氧树脂(EP)/碳纤维(CF)复合材料是CF增强复合材料的一个重要分支。
近年来,随着人们对EP/CF复合材料认识的不断深入,其优异的性能不断凸现,促使其用量不断上升。
20世纪70年代以前,EP/CF复合材料被视为昂贵的材料,价格约为玻璃纤维(GF)增强复合材料的10倍,只用于军工、宇航等尖端技术行业。
20世纪80年代以后,CF工业和EP工业迅速发展,EP/CF复合技术不断进步,加入到EP中的CF比例不断上升,目前CF的体积分数已可达60%以上,使EP/CF复合材料的质量提高而价格下降,拓宽了其应用领域,进一步促进了EP/CF复合材料的发展。
1 CF及其EP复合材料的基本特点1.1 CF的特点和基本成分CF主要是由碳元素组成,其含碳量一般在90%以上。
CP具有耐高温、耐摩擦、导电、导热及耐腐蚀等特性,与一般碳素材料不同的是,其各向异性显著,柔软,可加工成各种织物,沿纤维轴向表现出很高的强度。
制备CF的主要原材料有人造丝(粘胶纤维)、聚丙烯腈(PAN)纤维和沥青等。
通常制备高强度、高模量CF多选用PAN为原料。
制备CF需经过拉丝、牵伸、稳定、炭化、石墨化5个阶段。
1.2 EP基体的作用EP具有优良的加工性能和力学性能,其固化收缩率低,粘结性能优异。
复合材料中EP的主要作用是把CF粘在一起,分配CF间的载荷,保护CF不受环境影响。
1.3 EP/CF复合材料的特性EP/CF复合材料的特性主要取决于CF、EP及EP与CF之间的粘结特性。
EP/CF复合材料具有优异的性能,与钢相比,EP/CF复合材料的比强度为钢的4.8-7.2倍,比模量为钢的3.1-4.2倍,疲劳强度约为钢的2.5倍、铝的3.3倍,而且高温性能好,工作温度达400℃时其强度与模量基本保持不变。
此外还具有密度和线膨胀系数小、耐腐蚀、抗蠕变、整体性好、抗分层、抗冲击等,在现有结构材料中,其比强度、比模量综合指标最高。
环氧树脂浇铸成型工艺流程

环氧树脂浇铸成型工艺流程
环氧树脂浇铸成型工艺是一种常见的制造工艺,用于生产具有高强度、耐磨性和耐腐蚀性的产品。
本文将介绍环氧树脂浇铸成型的工艺流程和关键步骤,帮助读者了解这一制造过程。
首先,环氧树脂浇铸成型工艺的第一步是准备工作。
在开始实际浇铸之前,需要准备好所需的原材料,包括环氧树脂、固化剂、填料等。
确保所有材料的质量符合要求,并按照配方比例准备好。
接下来是模具制备阶段。
选择合适的模具对于最终产品的质量至关重要。
根据产品的形状和尺寸,选择适合的模具,并进行表面处理以确保产品的顺利脱模。
在将模具放置在合适的位置后,可以进行下一步操作。
然后是混合环氧树脂和固化剂。
将事先准备好的环氧树脂和固化剂按照一定的比例混合均匀,通常在一定的时间内搅拌以确保两者充分混合。
在混合过程中可以添加适量的填料以调整产品的性能特性。
随后是浇注和固化环节。
将混合好的环氧树脂倒入准备好的模具中,确保浇注过程中没有气泡产生。
根据产品的大小和复杂程度,选择合适的固化时间和温度,等待环氧树脂完全固化。
最后是脱模和后处理。
在环氧树脂完全固化后,小心地将产品从模具中取出。
根据产品的要求,进行必要的修整和表面处理工作。
最终得到的产品将具有高强度、耐磨性和耐腐蚀性的特点,可以用于各种工业领域。
总的来说,环氧树脂浇铸成型工艺流程包括准备工作、模具制备、混合环氧树脂和固化剂、浇注和固化、脱模和后处理等关键步骤。
通过掌握这些步骤,可以生产出高质量的环氧树脂制品,满足不同领域的需求。
1。
环氧树脂真空浇注技术

环氧树脂真空浇注技术环氧树脂真空浇注技术环氧树脂真空浇注技术【1】摘要介绍了当前应用较为广泛的环氧树脂真空浇注技术特点。
关键词环氧树脂;真空浇注;绝缘子浇注技术SF6封闭式组合电器的特征是把整个变电站的主要设备(除变压器外)几乎全部封闭在一个接地的金属外壳内,壳体内充以SF6气体,以保证相间和对地绝缘。
它和常规的敞开式变电站相比,具有体积小,运行安全,使用可靠(受环境条件影响小),维修方便,免维护周期长及占地面积少等优点。
为大中城市人口稠密的变电站、山区大型水电站、大型钢厂、矿区以及地下变电站的建设或改造,提供了有利条件。
得益于SF6封闭式组合电器(以下简称GIS)的特点(尤其是小型化特点),20世纪60年代末第一台分相式GIS问世以来,GIS的发展速度突飞猛。
而GIS中的绝缘件,包括盆式绝缘子、绝缘拉杆以及接线座等,也随着GIS设备的广泛应用得到长足的发展。
这些绝缘件通常以环氧树脂为主要原料,浇注成型。
盆式绝缘子是这些绝缘件中极其重要的组件之一,其在GIS设备中具有机械支撑、高压绝缘和隔离两侧气体的综合作用,此外,还承受SF6气体在电弧、电晕和高热量作用下分解出的活性物质的腐蚀。
因此,盆式绝缘子就成为GIS设备中举足轻重、事关成败的关键件了。
国内外研制GIS的厂家、公司,无一例外的对它进行了大量的系统的基础理论和实验研究。
绝缘子浇注技术理所当然的成了生产的关键。
1 现有浇注技术特点目前,使用最广泛的浇注设备均配有环氧树脂熔融、固化剂熔化、填料干燥、材料混合、真空浇注等装置,并配有高真空机组,整个浇注系统由先进的控制系统进行控制,且均具有以下特点:1)各种原料从送料、预热、计量、输送、混合到浇注完成,都在封闭的系统中运行。
从原料加入浇注设备后,就进入与外界隔绝状态,避免二次污染;全过程保持真空状态,在输送过程中减少原料与空气接触;并尽量避免操作人员与生产过程中的原料接触,以减少对操作环境污染。
2)各加热部分采用油循环或电加热,通过控制系统,加温速度快,温度均匀性均保持在相当高的精度。
环氧树脂真空浇注工艺技术
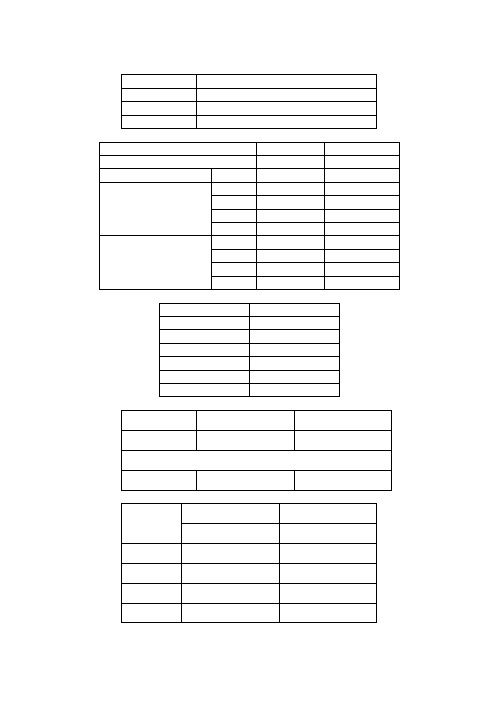
(Static Mixers)一种的高效混合设备通过固定在管内的混合单元内件,使进入二股混合料产生流体的切割、剪切、旋转和重新混合;达到混合料之间良好分散和充分混合的目的,得到均质浇注料。
环氧树脂混合料静态混合的主要技术特点:静态混合罐混料过程精确可控,混料时间短、混合料新鲜,流动性能优越,提高了环氧树脂浇注料对线圈和嵌件的浸润性,能最大程度保证混合材料的低粘度和活性,解决了动态机械搅拌混料因长时间搅拌、抽真空而导致的凝胶时间缩短、粘度增高的问题。
同时,可根据生产量随时混料,缩短周期,提高效率,杜绝动态搅拌混料方式每次浇注都会产生余料的痼疾,节约材料。
对于二组份粘度较大或混合比例差距过大的混合料,上述二种混合器很难在短时间内达到混合的目的,为此,可选择动态混合器进行强制、快速的混合,以增强混合效果。
见图二十一环氧树脂-酸酐配方体系的固化过程——温度-密度变化曲线图二十一图二十一图二十一图二十一六,电工浇注用环氧树脂真空浇注技术工艺链中应加以重视的几个要点环氧树脂浇注料固化成型后,浇注绝缘部件外观光洁无裂缝、无气泡,但是,浇注的绝缘部件(如:电流电压互感器、干式变压器等)却产生了“局部放电”超标现象。
高压电器产生“局部放电”超标现象是与产品结构设计、绝缘材料互配、环氧树脂浇注料和浇注工艺技术有关;在此,我们只对与环氧树脂浇注料和浇注工艺有关的五大要素进行分析探讨:1,微量杂质:主要由配方组分材料(环氧树脂、固化剂、增韧剂、硅微粉)内存在的低分子挥发物,水份和微量金属氧化物等;混料设备及输料管道内有污染物;生产现场粉尘环境污染;操作人为因素和被封装部件表面有油污等;2,微裂纹:这类裂纹发生在浇注件的深层,特别是环氧树脂与部件之间界面上存在的微裂纹;线状”裂纹,是环氧树脂固化物内应力泄放而造成的开裂。
这种类型的开裂条纹,容易发生的几个部位:①环氧树脂浇注层厚薄不均匀处,没有过渡区域;②环氧树脂浇注层有尖锐角或直角处(与浇注模具设计有关);③与金属嵌件接触处,特别是金属嵌件有尖锐角或直角而没有倒园角处;④与金属接触处的环氧树脂层较薄等。
环氧树脂的生产工艺课件(共 56张PPT)
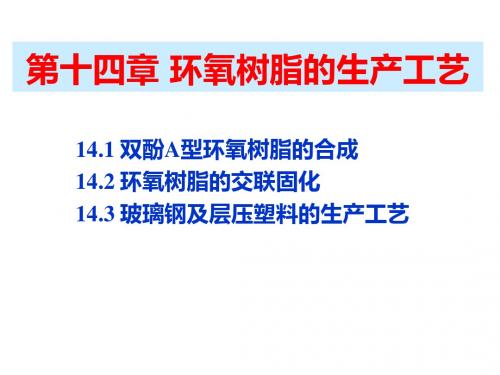
◆聚合:47℃时一次加入环氧氯丙烷;在80-85℃反应 1h,85-90℃ (高分子量树脂为95℃)反应2-3h。 ◆中和:水洗至树脂呈中性。
◆脱水:常压脱水至115℃,减压脱水至135-140℃ 。
二 环氧树脂的交联固化
环氧树脂分子的两端具有环氧基,可以根据环氧基含 量估算环氧树脂的分子量。工业上常以环氧当量、环 氧值来衡量分子量的大小。 环氧值:100克树脂含环氧基的摩尔数。 环氧当量:1摩尔的环氧基所相当的树脂重量。 环氧值=100克/环氧当量 环氧值越小,环氧当量越大,分子量越大。 当n=0,则M=340;一个分子有两个环氧基, 则环氧当量340/2=170, 其环氧值等于100/170分子量树脂的生产 配料:双酚A:环氧氯丙烷:NaOH=1:2.75:2.42(摩尔) NaOH浓度:30% 溶解:溶解温度:70℃,30min。 第一次加碱:4h,50~55℃。 在55-60℃下反应4h,减压回收环氧氯丙烷,温度低 于85℃,真空度>600mmHg,约2h,70℃左右时加苯 溶解,约30min。 第二次加碱:温度55~70℃,约1h。并在此温度下维持3h。 冷却后分出水,使苯溶液透明,再静置4h。然后先常压 脱苯,至液温110℃,再减压脱苯至140~143℃无苯馏出 为止。
O C R C O O C 2R C O O C R C O O + H 2O R O C C O OH OH O+ HO R' OH R O + R' OH R O C C O O C C O OH O HO R' O O C R C O OH OR '
环氧树脂真空浇注工艺探索
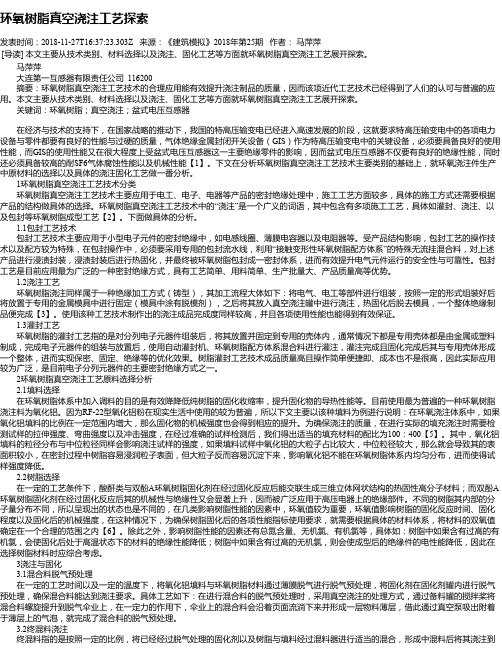
环氧树脂真空浇注工艺探索发表时间:2018-11-27T16:37:23.303Z 来源:《建筑模拟》2018年第25期作者:马萍萍[导读] 本文主要从技术类别、材料选择以及浇注、固化工艺等方面就环氧树脂真空浇注工艺展开探索。
马萍萍大连第一互感器有限责任公司 116200摘要:环氧树脂真空浇注工艺技术的合理应用能有效提升浇注制品的质量,因而该项近代工艺技术已经得到了人们的认可与普遍的应用。
本文主要从技术类别、材料选择以及浇注、固化工艺等方面就环氧树脂真空浇注工艺展开探索。
关键词:环氧树脂;真空浇注;盆式电压互感器在经济与技术的支持下,在国家战略的推动下,我国的特高压输变电已经进入高速发展的阶段,这就要求特高压输变电中的各项电力设备与零件都要有良好的性能与过硬的质量,气体绝缘金属封闭开关设备(GIS)作为特高压输变电中的关键设备,必须要具备良好的使用性能,而GIS的使用性能又在很大程度上受盆式电压互感器这一主要绝缘零件的影响,因而盆式电压互感器不仅要有良好的绝缘性能,同时还必须具备较高的耐SF6气体腐蚀性能以及机械性能【1】。
下文在分析环氧树脂真空浇注工艺技术主要类别的基础上,就环氧浇注件生产中原材料的选择以及具体的浇注固化工艺做一番分析。
1环氧树脂真空浇注工艺技术分类环氧树脂真空浇注工艺技术主要应用于电工、电子、电器等产品的密封绝缘处理中,施工工艺方面较多,具体的施工方式还需要根据产品的结构做具体的选择。
环氧树脂真空浇注工艺技术中的“浇注”是一个广义的词语,其中包含有多项施工工艺,具体如灌封、浇注、以及包封等环氧树脂成型工艺【2】。
下面做具体的分析。
1.1包封工艺技术包封工艺技术主要应用于小型电子元件的密封绝缘中,如电感线圈、薄膜电容器以及电阻器等。
受产品结构影响,包封工艺的操作技术以及配方较为特殊,在包封操作中,必须要采用专用的包封流水线,利用“接触变形性环氧树脂配方体系”的特殊无流挂混合料,对上述产品进行浸渍封装,浸渍封装后进行热固化,并最终被环氧树脂包封成一密封体系,进而有效提升电气元件运行的安全性与可靠性。
环氧树脂灌封料的固化动力学及固化工艺

见,随 升 温 速 率 增 加,Ti,Tp 和 Tf 均 随 之 升 高。 通 过外推法 将 [13] 特征温度外推 至 升 温 速 率 为 0 时 对 应 的特征温 度,作 为 设 计 实 际 固 化 工 艺 条 件 的 固 化 温
度。从而得 到 1515-3 和 1580EH 的 Ti,Tp 和 Tf 分 别为118 ℃,135 ℃,155 ℃和99 ℃,129 ℃,151 ℃。
106
高分子材料科学与工程
2021 年
料与 B 料质量比100∶28 和100∶90 加 入 B 料,继 续 搅拌10 min,混合均匀,备用。 1.2.2 力 学 性 能 测 试 样 品 制 备:将 混 合 均 匀 的 灌 封 料浇 注 至 聚 四 氟 乙 烯 模 具 中,将 1515-3 和 1580EH 分别以实 际 条 件 85 ℃/6h,105 ℃/2h 和 100 ℃/2 h,125 ℃/5h,理 论 条 件 120 ℃/15 min,140 ℃/40 min,160 ℃/10 min 和 100 ℃/15 min,130 ℃/10 min,160 ℃/10 min进行固化,设计理论见2.2.2节。 1.3 测试与表征 1.3.1 流 变 行 为 分 析:采 用 应 变 控 制 型 旋 转 流 变 仪 (ARES,美国 TAInstruments)对灌封料的流变行为 进行测试。使用直径40 mm 平行板夹具分别对灌封 料进行动态时间 扫 描,频 率 6.28rad/s,应 变 5%,上 下板间距 0.3 mm,分 别 测 试 45 ℃,65 ℃,75 ℃,80 ℃和85 ℃黏度随时间的变化。 1.3.2 固 化 反 应 动 力 学 分 析:采 用 差 示 扫 描 量 热 仪 (DSC Q20,美 国 TAInstruments)测 试 灌 封 料 的 固 化反应动 力 学。 称 取 样 品 约3~5 mg,氮 气 流 量 50 mL/min,升 温 速 率 分 别 为 5 ℃/min,10 ℃/min,15 ℃/min和20 ℃/min,升温范围50~350 ℃。 1.3.3 红 外 光 谱 测 试:采 用 傅 里 叶 变 换 红 外 光 谱 仪 (FT-IR Nicolet6700,美 国 ThermoFisherScientific)对灌封料的分子结构进 行 表 征。采 用 原 位 升 温 红 外透射模式,波数范围650~4000cm-1,扫 描 次 数 32 次,分辨率 4cm-1,测试灌封料在固化反应过程中官 能团随时间的变化。将试样涂在溴化钾窗片并装在 热台上,使 用 透 射 模 式 每 间 隔 10 min 采 集 实 时 红 外 谱图。 1.3.4 力学性 能 测 试:采 用INSTRON 万 能 材 料 实
环氧树脂浇注成型工艺
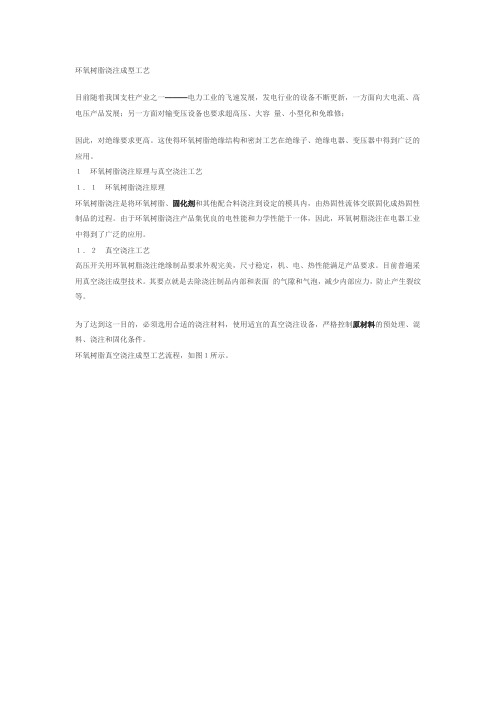
环氧树脂浇注成型工艺目前随着我国支柱产业之一———电力工业的飞速发展,发电行业的设备不断更新,一方面向大电流、高电压产品发展;另一方面对输变压设备也要求超高压、大容量、小型化和免维修;因此,对绝缘要求更高。
这使得环氧树脂绝缘结构和密封工艺在绝缘子、绝缘电器、变压器中得到广泛的应用。
1环氧树脂浇注原理与真空浇注工艺1.1环氧树脂浇注原理环氧树脂浇注是将环氧树脂、固化剂和其他配合料浇注到设定的模具内,由热固性流体交联固化成热固性制品的过程。
由于环氧树脂浇注产品集优良的电性能和力学性能于一体,因此,环氧树脂浇注在电器工业中得到了广泛的应用。
1.2真空浇注工艺高压开关用环氧树脂浇注绝缘制品要求外观完美,尺寸稳定,机、电、热性能满足产品要求。
目前普遍采用真空浇注成型技术。
其要点就是去除浇注制品内部和表面的气隙和气泡,减少内部应力,防止产生裂纹等。
为了达到这一目的,必须选用合适的浇注材料,使用适宜的真空浇注设备,严格控制原材料的预处理、混料、浇注和固化条件。
环氧树脂真空浇注成型工艺流程,如图1所示。
2真空浇注成型工艺关键技术(1)原材料的预处理原材料预处理是在一定温度下加热至一定时间,并经过真空处理以脱除原材料中吸附的水分、气体及低分子挥发物,达到脱气脱水的效果。
(2)混料混料的目的是使环氧树脂、填料、固化剂等混合均匀,便于进行化学反应。
混料分一次和二次混料。
树脂和填料混合称一次混料,在一次混料中加入固化剂成为二次混料。
一次混料是使填料被树脂充分浸润。
因为环氧树脂与酸酐固化剂的反应是放热反应,填料是导热性好的材料,它能将反应释放的热量向外传导而不积集,使浇注物内应力均匀分布而不产生缩痕。
二次混料时间要确保固化剂混合均匀,其温度、真空度的参数也很重要。
温度过高,将使混合料黏度迅速增加,影响脱气浇注工序;真空度用以保证混合料的脱气、脱水,但不能导致固化剂的气化,所以真空度要恰当。
(3)浇注浇注是将组装好并预热到一定温度的模具放入真空浇注罐中或在真空浇注罐内预热,模具温度略高于混合料的温度,浇注罐抽真空度到1330Pa以下,维持一定温度[1],最后将混合均匀的物料浇入模具内;浇注完成后要继续抽真空一段时间,以去除浇注件内所形成的气泡,即可关闭真空,打开浇注罐,将模具送入固化炉进行固化。
细说环氧树脂浇注工艺方法
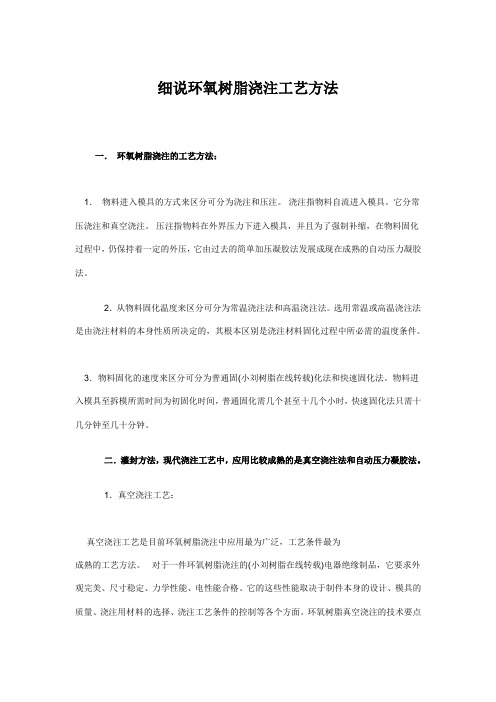
细说环氧树脂浇注工艺方法一.环氧树脂浇注的工艺方法:1.物料进入模具的方式来区分可分为浇注和压注。
浇注指物料自流进入模具。
它分常压浇注和真空浇注。
压注指物料在外界压力下进入模具,并且为了强制补缩,在物料固化过程中,仍保持着一定的外压,它由过去的简单加压凝胶法发展成现在成熟的自动压力凝胶法。
2.从物料固化温度来区分可分为常温浇注法和高温浇注法。
选用常温或高温浇注法是由浇注材料的本身性质所决定的,其根本区别是浇注材料固化过程中所必需的温度条件。
3.物料固化的速度来区分可分为普通固(小刘树脂在线转载)化法和快速固化法。
物料进入模具至拆模所需时间为初固化时间,普通固化需几个甚至十几个小时,快速固化法只需十几分钟至几十分钟。
二.灌封方法,现代浇注工艺中,应用比较成熟的是真空浇注法和自动压力凝胶法。
1.真空浇注工艺:真空浇注工艺是目前环氧树脂浇注中应用最为广泛,工艺条件最为成熟的工艺方法。
对于一件环氧树脂浇注的(小刘树脂在线转载)电器绝缘制品,它要求外观完美、尺寸稳定、力学性能、电性能合格。
它的这些性能取决于制件本身的设计、模具的质量、浇注用材料的选择、浇注工艺条件的控制等各个方面。
环氧树脂真空浇注的技术要点就是尽可能减少浇注制品中的气隙和气泡。
为了达到这一目的,在原料的预处理、混料、浇注等各个工序都需要控制好真空度、温度及工序时间。
2.自动压力凝胶工艺自动压力凝胶工艺是20世纪70年代初由瑞士CIBA-Geigy公司开发的技术。
因为这种工艺类似于热塑性塑料注射成型的(小刘树脂在线转载)工艺方法,因此也称其为压力注射工艺。
它的最为显著的优点是大大提高了浇注工效。
可以说自动压力凝胶技术的开发成功及在工业上的大量应用,是真空浇注由间歇、手工操作向自动化生产发展的一场革命,它和真空浇注的主要区别在于:⑴浇注材料是在外界压力下通过管道由注入口注入模具。
⑵物料的混料处理温度低,模具温度高。
⑶物料进入模具后,固化速度快,通常为十几分钟至几十分钟。
环氧板的工艺
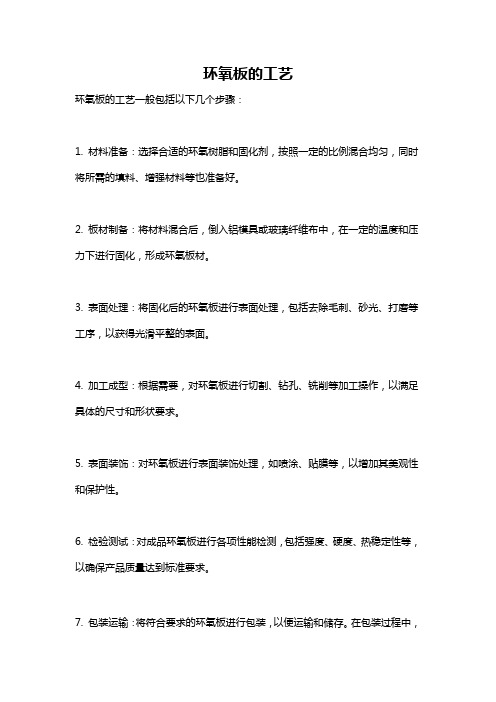
环氧板的工艺
环氧板的工艺一般包括以下几个步骤:
1. 材料准备:选择合适的环氧树脂和固化剂,按照一定的比例混合均匀,同时将所需的填料、增强材料等也准备好。
2. 板材制备:将材料混合后,倒入铝模具或玻璃纤维布中,在一定的温度和压力下进行固化,形成环氧板材。
3. 表面处理:将固化后的环氧板进行表面处理,包括去除毛刺、砂光、打磨等工序,以获得光滑平整的表面。
4. 加工成型:根据需要,对环氧板进行切割、钻孔、铣削等加工操作,以满足具体的尺寸和形状要求。
5. 表面装饰:对环氧板进行表面装饰处理,如喷涂、贴膜等,以增加其美观性和保护性。
6. 检验测试:对成品环氧板进行各项性能检测,包括强度、硬度、热稳定性等,以确保产品质量达到标准要求。
7. 包装运输:将符合要求的环氧板进行包装,以便运输和储存。
在包装过程中,
还需注意保护环氧板的表面免受损坏。
环氧树脂的固化
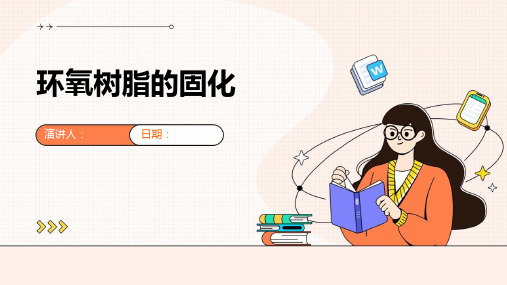
绝缘性
固化后的环氧树脂是一种优良的绝缘 材料,可用于电气工程中。
固化产物的化学性能
耐化学药品性
固化产物对多种化学药品具有稳定性,不易发生化学反应。
热稳定性
固化产物在高温下能保持较好的稳定性,不易分解或变形。
耐候性
固化产物在户外环境中能长期保持性能稳定,不易受紫外线、氧 化等因素影响。
环氧树脂结构
环氧树脂的分子结构中含有环氧基、 羟基等极性基团和脂肪族、芳香族等 非极性基团,因此具有许多优异的性 能。
环氧树脂的性质
物理性质
环氧树脂通常是黏稠液体或低熔点固体,无色或淡黄色,透明或半透明,有良 好的黏附力和浸润性。
化学性质
环氧树脂在固化过程中,环氧基会与固化剂中的活性基团发生化学反应,形成 三维网状结构,从而赋予固化物优异的力学性能、耐化学药品性能和电性能等 。
高固化质量。
固化工艺的优化与改进
固化温度与时间的控制
根据环氧树脂的性质和工件要 求,合理调整固化温度和时间 ,以获得最佳的固化效果。
新型固化技术的探索
研究新型固化技术,如微波固 化、超声波固化等,以进一步 缩短固化时间、降低能耗和提 高产品质量。
固化设备的改进
针对现有固化设备的不足之处 进行改进,如提高加热效率、 优化温度控制系统等,以提高 固化质量和效率。
催化剂
催化剂可以加速固化反应,提高生产效率。常用的催化剂 包括有机胺、有机酸、金属盐等。
固化剂种类和用量
不同种类的固化剂具有不同的反应活性和机理,对固化产 物的性能也有显著影响。同时,固化剂的用量也直接影响 固化反应的进行程度和产物的性能。
湿度和氧气
环氧树脂的固化

甲基四氢 邻苯二甲 酸酐
C9H10O3
166.17
淡黄色透明油状液体
沸点 115~155℃
溶解性 溶于丙酮、 乙醇、 甲苯等
毒性 低毒
(3)胺类固化剂经过数代发展,型号繁多,种类庞杂,各有所长,在此不作赘述。
四、实验仪器
烧杯,牛皮纸,电子天平,果冻盒模具
五、实验步骤及现象
实验操作 用电子天平称取 8g 环氧树脂 E51,置于小果冻盒中。直接 在果冻盒中称取约 3.2g 酚醛 胺。剧烈搅拌混匀后静置。 实验现象 起初是黄色透明粘稠液体。 静 置后有少量气泡生成, 放出少 量热。 手触碰时有暖感。 无进 一步现象。 邻组刘政阳的发生明显的爆 聚, 体积增大, 有大量气泡嵌 在内部。 其表面呈现多孔泡沫 状。 现象解释 爆聚现象是由于固化过程传 热不均,局部过热使传热过 快, 而过热又加速了反应, 从 而造成了爆聚现象。 在本实验 中,小果冻盒的散热面积不 大, 而且投料时特意让固化剂 量偏多, 静置后就有可能会发 生爆聚。 当然这也于操作条件 有关, 并不能保证爆聚现象的 发生。 一个是因为卡安太大了, 把中 间的环氧卡住了。 而且它的背 面有一个别针, 使它无法在体 系中平衡存在。 如果让它在粘 度适当的时候摆正,再固化, 真是基本不可能做到。 丑点就 丑点吧。
三、实验药品
3
高分子化学实验
环氧树脂
化工系 毕啸天 2010011811
环氧 E51,改性胺,聚醚胺,酚醛胺,MeTHPA (1)环氧 E51 技术指标及简介: 外观无明显机械杂质; 环氧值 (eq/ 100g) 0.48~0.54; 无机氯值 (eq/ 100g) ≤ 1 × 10 -3; -2 有机氯值( eq/ 100g )≤ 2 × 10 ;挥发物 %≤ 2;色泽号≤ 2;粘度 40 ℃ (mPaS) ≤ 2500 E51 环氧值高、粘度低、色泽浅,广泛用作粘接剂、无溶剂涂料、自流平地平料、浇注 料。制备的涂料色彩艳丽、抗剥性好、施工方便。制备的浇注料工艺性好、流动性好、机械 强度高、绝缘性能好、收缩率小、吸水率低。 (2)MeTHPA 性质 物质 英文名 Methyl Tetrahydroph thalic Anhydride 熔点 -20℃ 分子式 分子量 外观性状 密度 1.20~1. 22 用量 25.5g
- 1、下载文档前请自行甄别文档内容的完整性,平台不提供额外的编辑、内容补充、找答案等附加服务。
- 2、"仅部分预览"的文档,不可在线预览部分如存在完整性等问题,可反馈申请退款(可完整预览的文档不适用该条件!)。
- 3、如文档侵犯您的权益,请联系客服反馈,我们会尽快为您处理(人工客服工作时间:9:00-18:30)。
环氧树脂浇注成型工艺
目前随着我国支柱产业之一———电力工业的飞速发展,发电行业的设备不断更新,一方面向大电流、高电压产品发展;另一方面对输变压设备也要求超高压、大容量、小型化和免维修;
因此,对绝缘要求更高。
这使得环氧树脂绝缘结构和密封工艺在绝缘子、绝缘电器、变压器中得到广泛的应用。
1环氧树脂浇注原理与真空浇注工艺
1.1环氧树脂浇注原理
环氧树脂浇注是将环氧树脂、固化剂和其他配合料浇注到设定的模具内,由热固性流体交联固化成热固性制品的过程。
由于环氧树脂浇注产品集优良的电性能和力学性能于一体,因此,环氧树脂浇注在电器工业中得到了广泛的应用。
1.2真空浇注工艺
高压开关用环氧树脂浇注绝缘制品要求外观完美,尺寸稳定,机、电、热性能满足产品要求。
目前普遍采用真空浇注成型技术。
其要点就是去除浇注制品内部和表面的气隙和气泡,减少内部应力,防止产生裂纹等。
为了达到这一目的,必须选用合适的浇注材料,使用适宜的真空浇注设备,严格控制原材料的预处理、混料、浇注和固化条件。
环氧树脂真空浇注成型工艺流程,如图1所示。
2真空浇注成型工艺关键技术
(1)原材料的预处理
原材料预处理是在一定温度下加热至一定时间,并经过真空处理以脱除原材料中吸附的水分、气体及低分子挥发物,达到脱气脱水的效果。
(2)混料
混料的目的是使环氧树脂、填料、固化剂等混合均匀,便于进行化学反应。
混料分一次和二次混料。
树脂和填料混合称一次混料,在一次混料中加入固化剂成为二次混料。
一次混料是使填料被树脂充分浸润。
因为环氧树脂与酸酐固化剂的反应是放热反应,填料是导热性好的材料,它能将反应释放的热量向外传导而不积集,使浇注物内应力均匀分布而不产生缩痕。
二次混料时间要确保固化剂混合均匀,其温度、真空度的参数也很重要。
温度过高,将使混合料黏度迅速增加,影响脱气浇注工序;真空度用以保证混合料的脱气、脱水,但不能导致固化剂的气化,所以真空度要恰当。
(3)浇注
浇注是将组装好并预热到一定温度的模具放入真空浇注罐中或在真空浇注罐内预热,模具温度略高于混合
料的温度,浇注罐抽真空度到1330Pa以下,维持一定温度[1],最后将混合均匀的物料浇入模具内;浇注完成后要继续抽真空一段时间,以去除浇注件内所形成的气泡,即可关闭真空,打开浇注罐,将模具送入固化炉进行固化。
浇注过程中应注意浇注速率和模具放置的位置,应有利于排气和使物料充满模具。
(4)固化
选择合适的温度和固化时间。
环氧树脂浇注件的性能与交联密度密切相关。
一般来说,浇注件的力学性能随交联密度的提高而上升,但到某一程度随交联密度的提高,其机械强度反而下降。
这个转折点的标志就是玻璃化转变温度Tg。
所以固化温度太高,常使固化物性能下降,因此,必须选择合适的固化温度。
固化采用两阶段进行:一阶段是初固化成型;二阶段是在一次固化温度稍高的情况下进行后固化,保证完全固化,达到最佳性能状态。
有时为了减少缩痕,可以在加压下凝胶来消除。
(5)脱模
脱模过程主要控制脱模温度和浇注件的冷却速率,减少浇注件的内应力,一般控制低于80℃。
真空浇注工艺是目前环氧树脂浇注中应用最为广泛、工艺条件最为成熟的工艺。
3真空浇注模具设计关键技术
3.1模具总体设计原则
浇注模型腔表面应力求光滑,不得有砂眼。
在设计浇注模时应浇注方便,避免产生气泡。
为减少内应力和容易脱模,型腔各处都应圆滑过渡,在所有拐角及转弯处都应使气体逸出方便。
3.2收缩率
根据填料的不同,浇注材料的收缩率也不同。
对于SiO2+环氧树脂,取收缩率为0.4%;而Al2O3+环氧树脂的收缩率为0.4%~0.5%(以上均为实验数据)。
在设计中一般取收缩率0.4%[2]。
3.3支撑结构
从浇注工艺方面入手。
因真空浇注的技术要点就是尽可能减少浇注制品中的气隙和气泡,提高零件质量,所以为利用浇口补缩的方式消除浇注成型缺陷,在模具下模板上增加了支脚,以确保浇口始终处于高点位置(倾斜约15~20°),达到更好的补缩效果。
3.4冷却装置
零件浇注时的冷却主要采用水冷却方式。
因为零件在固化过程中的第一阶段为热固化,冷却装置中的水可使浇口处与模腔有约20℃的温差,这样可以延迟浇口处的固化,起到补缩的效果,避免了浇不满缺陷。
水箱的设置分内外两种,根据模具特点可选用不同的形式。
3.5密封元件
由于环氧树脂液态时流动性良好,对密封的要求高,故应加密封元件。
根据零件特点,设计中采用大小密封圈同时密封的形式。
在嵌件颈部位置采用环形小密封圈,在型腔周围采用大密封圈。
3.6模具选材及表面处理
因为环氧树脂与铝合金的热膨胀系数基本一致,又由于该类模具主要用于真空浇注过程中,更多采用手工操作,所以选择铝合金材料,以便于搬运。
但因材料硬度低,故对材料进行表面硬质阳极氧化处理,氧化层深度达50μm,表面维氏硬度提高到400~500,这样提高了模具的耐磨性和抗腐蚀性能。
而对于在开、合模时经常拆卸的零件采用了钢件或铜件,模具在装卸过程中损伤程度低,模具使用寿命长。
4真空浇注模具设计实例
互感器浇注模具是互感器制造必需的工装设备。
浇注成型模具必须保证互感器的绕组、铁心、出线端子及其它零件的位置正确,使浇注体的尺寸和性能符合要求;注意浇注体外形美观,并考虑装模、拆模方便及封模要求和浇注时空气容易排出,同时尽可能减轻模具的质量。
本文主要介绍钢制模的设计及加工。
图3为互感器浇注模具装配图。
模具使用注意事项:
(1)模具装配完成后,先在浇注罐内均匀加热6~8h后,使模具温度达到80~85℃,再抽真空,进行浇注。
如果模具内部温度达不到,会出现固化后缺料现象。
(2)环氧树脂浇注时,若真空度达不到,没有把浇注体内的空气全部抽出,则会造成固化后浇注体内有气泡。
有气泡的浇注体的绝缘强度将大大降低[3]。