确定成型工艺方法和工艺参数
任务五 确定塑件成型工艺参数

二、相关知识
(二)压力 (2)注射压力 ①定义 注射压力是指注射时柱塞或螺杆顶部对塑料所施加的压 力。 ②作用 克服熔体流动阻力;具有一定的充满型腔的速率;对熔 体进行压实。 ③工作值的确定 注射压力的大小取决于塑料品种、注射机类型、模具结 构、塑料制品的壁厚和流程及其它工艺条件,尤其是浇注系统 的结构和尺寸。
(1)料筒的温度
选择料筒温度注意以下几个方面: 1)高于塑料的粘流温度Tf 或熔点Tm(这两种温度有何区别?)但 低于塑料的热分解温度Td 2)聚合物的分子质量及分子质量分布,同一种塑料,平均分子量 越高、分布越窄,则熔体黏度越大,料筒温度应高些。 3)注射机的类型 螺杆式注射机低于柱塞式的10~20°C。 4)塑料制品及模具结构特点: 料筒的温度分布,一般从料斗一侧(后端)起至喷嘴(前端)止,是 逐步升高的。湿度较高的塑料可适当提高料筒后端温度。螺杆式注 射机料筒中的塑料(摩擦)料筒前段的温度可以略低于中段。
保压压力太高,易产生溢料、溢边增加塑件的应力;保压 压力太低,会造成成型不足。
二、相关知识
(三)时间(成型周期) 完成一次注射模塑过程所需的时间称为成型周期。
在整个成型周期中,注射时间和冷却时间最重要。 一般而言:充模时间3~5s 、保压时间20~25s 、冷却时间30~ 120s
P90表2-24列出常用塑料注射成型工艺参数
三、任务实施
(一)基本训练——编制灯座制件成型工艺卡片
任务四初选螺杆式塑料注射机XS-ZY-500,注射成型工艺条件的选择 可查P90表2-24。成型PC塑件,螺杆转速取20~40r/min,材料预干燥 110℃~120℃,8~12h(任务二结论)
(二)能力强化训练——电池盒盖塑件成型工艺设计P94
成型工艺流程

成型工艺流程成型工艺是制造行业中非常重要的一环,它直接关系到产品的质量和生产效率。
在这篇文档中,我们将重点介绍成型工艺流程的相关内容,希望能对大家有所帮助。
首先,成型工艺的第一步是原料准备。
在进行成型之前,我们需要对原料进行充分的准备工作,包括原料的筛选、配比以及预处理等。
只有做好了原料的准备工作,才能保证后续成型工艺的顺利进行。
接下来是模具设计和制造。
模具的设计和制造直接关系到产品的成型质量。
在进行模具设计时,需要充分考虑产品的结构特点和成型工艺要求,确保模具能够满足产品的成型需求。
而在模具制造过程中,需要严格控制每一个加工环节,确保模具的精度和耐用性。
然后是成型工艺参数的确定。
在进行成型之前,需要确定好成型工艺的各项参数,包括成型温度、压力、速度等。
这些参数的确定需要通过大量的实验和数据分析,以确保产品能够达到设计要求。
接着是成型生产。
在进行成型生产时,需要严格按照之前确定的工艺参数进行操作,确保产品的质量稳定。
同时,需要对成型过程进行实时监控,及时发现并解决可能出现的问题。
最后是成型产品的检验和包装。
在成型完成后,需要对产品进行全面的检验,确保产品符合质量标准。
同时,还需要对产品进行包装,以确保产品在运输和使用过程中不受损坏。
总的来说,成型工艺流程是一个复杂而又关键的环节。
只有做好了每一个环节的工作,才能保证产品的质量和生产效率。
希望通过本文的介绍,大家能对成型工艺流程有一个更加深入的了解,从而能够在实际生产中更好地应用。
注塑工艺参数的确定

流动的压力,可以用在射嘴或液压线上的传感器来测量。 它没有固定的数值,而模具填充越困难,所要的注塑压力 也要增大。一般的塑料注射时都需要60Mpa以上的压力, 一些流动性差的塑料要在120Mpa以上,而超精密的注塑 成型一般都会在150Mpa以上。
除了高的锁模压力外,还要对模具进行保护,低压锁 模的压力最好是能调到模具中间没有任何东西时才能合拢, 放一张纸都能够将模具弹开。
成型工艺参数(压力)
脱模系统压力 为了制品的顺利脱模,脱模系统(顶针,抽芯,螺纹,
气辅脱模等)的压力就必须满足动作的需要。但过高的压 力容易损坏设备和产品,所以压力以能安全脱模为准。
注塑工艺参数的确定
注塑成型
注塑成型工艺 注塑成型工艺参数 注射机有关工艺参数的校核 注射充模过程分析 注射成型制品的内应力 工艺参数对制品质量的影响 注射制品力学性能的各向异性 注射制品的熔接强度 注射制品的收缩 模塑工艺规程的编制
注射成型工艺
成型前准备 注射过程
成型工艺参数(压力)
储料压力
储料压力用于提供油马达的动力,便于镙杆旋转速度的调 整,由液压系统压力阀调整大小。
在塑化时,螺杆旋转速度高低将影响塑胶塑化程度。一般 也是多级控制。
成型工艺参数(压力)
塑化压力
又称背压(螺杆头部熔体在螺杆转动后退时所受到的压 力),由液压系统溢流阀调整大小。
在塑化时,螺杆不断旋转将塑胶送到螺杆头部,这些被推 进到螺杆前端的塑胶就会对螺杆产生压力,这就是背压。在 注射成型时,它可以由调整射出油压缸的退油压力来调节, 背压的增加可以取得以下的效果:原料塑化更均匀,利于塑 胶内气体排出,计量更精确;使熔料温度增加,加速分解, 容易造成流涎现象,塑化时间变长等。背压的大小是依塑料 的粘度及其热稳定性来决定,一般为表压0.2-0.6Mpa左右。
注塑成型工艺流程及工艺参数

注塑成型工艺流程及工艺参数塑件的注塑成型工艺过程主要包括填充——保压——冷却——脱模等4个阶段,这4个阶段直接决定着制品的成型质量,而且这4个阶段是一个完整的连续过程。
1、填充阶段填充是整个注塑循环过程中的第一步,时间从模具闭合开始注塑算起,到模具型腔填充到大约95%为止。
理论上,填充时间越短,成型效率越高,但是实际中,成型时间或者注塑速度要受到很多条件的制约。
高速填充。
如图1-2所示,高速填充时剪切率较高,塑料由于剪切变稀的作用而存在粘度下降的情形,使整体流动阻力降低;局部的粘滞加热影响也会使固化层厚度变薄。
因此在流动控制阶段,填充行为往往取决于待填充的体积大小。
即在流动控制阶段,由于高速填充,熔体的剪切变稀效果往往很大,而薄壁的冷却作用并不明显,于是速率的效用占了上风。
λ低速填充。
如图1-3所示,热传导控制低速填充时,剪切率较低,局部粘度较高,流动阻力较大。
由于热塑料补充速率较慢,流动较为缓慢,使热传导效应较为明显,热量迅速为冷模壁带走。
加上较少量的粘滞加热现象,固化层厚度较厚,又进一步增加壁部较薄处的流动阻力。
λ由于喷泉流动的原因,在流动波前面的塑料高分子链排向几乎平行流动波前。
因此两股塑料熔胶在交汇时,接触面的高分子链互相平行;加上两股熔胶性质各异(在模腔中滞留时间不同,温度、压力也不同),造成熔胶交汇区域在微观上结构强度较差。
在光线下将零件摆放适当的角度用肉眼观察,可以发现有明显的接合线产生,这就是熔接痕的形成机理。
熔接痕不仅影响塑件外观,同时由于微观结构的松散,易造成应力集中,从而使得该部分的强度降低而发生断裂。
一般而言,在高温区产生熔接的熔接痕强度较佳,因为高温情形下,高分子链活动性较佳,可以互相穿透缠绕,此外高温度区域两股熔体的温度较为接近,熔体的热性质几乎相同,增加了熔接区域的强度;反之在低温区域,熔接强度较差。
2、保压阶段保压阶段的作用是持续施加压力,压实熔体,增加塑料密度(增密),以补偿塑料的收缩行为。
注塑成型工艺流程及工艺参数详解
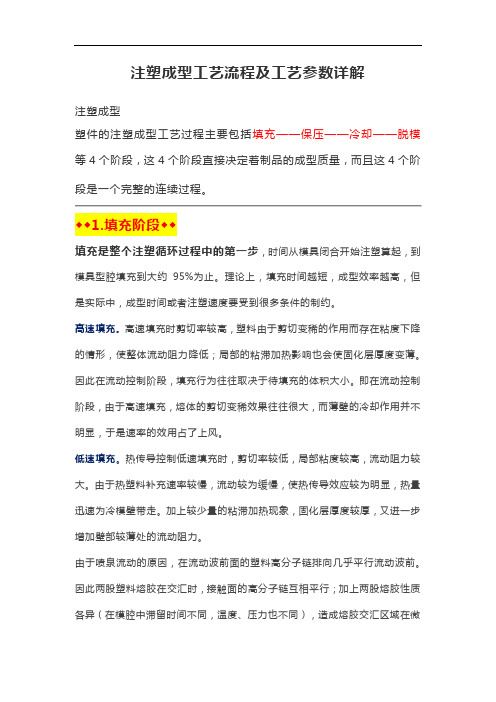
注塑成型工艺流程及工艺参数详解注塑成型塑件的注塑成型工艺过程主要包括填充——保压——冷却——脱模等4个阶段,这4个阶段直接决定着制品的成型质量,而且这4个阶段是一个完整的连续过程。
◆◆1.填充阶段◆◆填充是整个注塑循环过程中的第一步,时间从模具闭合开始注塑算起,到模具型腔填充到大约95%为止。
理论上,填充时间越短,成型效率越高,但是实际中,成型时间或者注塑速度要受到很多条件的制约。
高速填充。
高速填充时剪切率较高,塑料由于剪切变稀的作用而存在粘度下降的情形,使整体流动阻力降低;局部的粘滞加热影响也会使固化层厚度变薄。
因此在流动控制阶段,填充行为往往取决于待填充的体积大小。
即在流动控制阶段,由于高速填充,熔体的剪切变稀效果往往很大,而薄壁的冷却作用并不明显,于是速率的效用占了上风。
低速填充。
热传导控制低速填充时,剪切率较低,局部粘度较高,流动阻力较大。
由于热塑料补充速率较慢,流动较为缓慢,使热传导效应较为明显,热量迅速为冷模壁带走。
加上较少量的粘滞加热现象,固化层厚度较厚,又进一步增加壁部较薄处的流动阻力。
由于喷泉流动的原因,在流动波前面的塑料高分子链排向几乎平行流动波前。
因此两股塑料熔胶在交汇时,接触面的高分子链互相平行;加上两股熔胶性质各异(在模腔中滞留时间不同,温度、压力也不同),造成熔胶交汇区域在微观上结构强度较差。
在光线下将零件摆放适当的角度用肉眼观察,可以发现有明显的接合线产生,这就是熔接痕的形成机理。
熔接痕不仅影响塑件外观,同时由于微观结构的松散,易造成应力集中,从而使得该部分的强度降低而发生断裂。
一般而言,在高温区产生熔接的熔接痕强度较佳,因为高温情形下,高分子链活动性较佳,可以互相穿透缠绕,此外高温度区域两股熔体的温度较为接近,熔体的热性质几乎相同,增加了熔接区域的强度;反之在低温区域,熔接强度较差。
◆◆2.保压阶段◆◆保压阶段的作用是持续施加压力,压实熔体,增加塑料密度(增密),以补偿塑料的收缩行为。
塑件成型工艺性分析
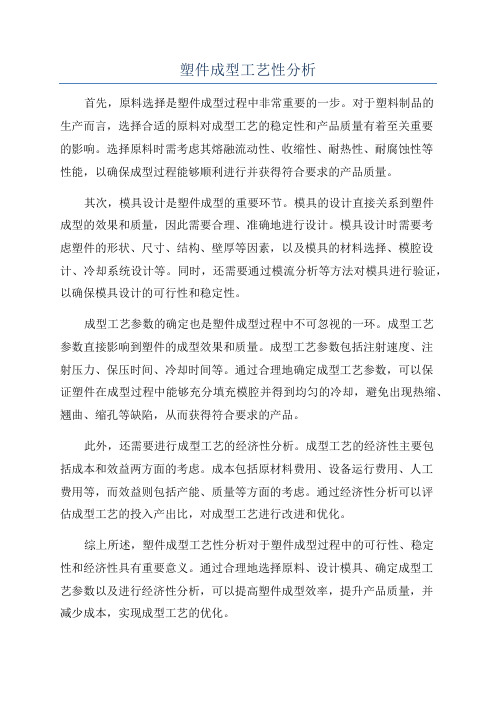
塑件成型工艺性分析首先,原料选择是塑件成型过程中非常重要的一步。
对于塑料制品的生产而言,选择合适的原料对成型工艺的稳定性和产品质量有着至关重要的影响。
选择原料时需考虑其熔融流动性、收缩性、耐热性、耐腐蚀性等性能,以确保成型过程能够顺利进行并获得符合要求的产品质量。
其次,模具设计是塑件成型的重要环节。
模具的设计直接关系到塑件成型的效果和质量,因此需要合理、准确地进行设计。
模具设计时需要考虑塑件的形状、尺寸、结构、壁厚等因素,以及模具的材料选择、模腔设计、冷却系统设计等。
同时,还需要通过模流分析等方法对模具进行验证,以确保模具设计的可行性和稳定性。
成型工艺参数的确定也是塑件成型过程中不可忽视的一环。
成型工艺参数直接影响到塑件的成型效果和质量。
成型工艺参数包括注射速度、注射压力、保压时间、冷却时间等。
通过合理地确定成型工艺参数,可以保证塑件在成型过程中能够充分填充模腔并得到均匀的冷却,避免出现热缩、翘曲、缩孔等缺陷,从而获得符合要求的产品。
此外,还需要进行成型工艺的经济性分析。
成型工艺的经济性主要包括成本和效益两方面的考虑。
成本包括原材料费用、设备运行费用、人工费用等,而效益则包括产能、质量等方面的考虑。
通过经济性分析可以评估成型工艺的投入产出比,对成型工艺进行改进和优化。
综上所述,塑件成型工艺性分析对于塑件成型过程中的可行性、稳定性和经济性具有重要意义。
通过合理地选择原料、设计模具、确定成型工艺参数以及进行经济性分析,可以提高塑件成型效率,提升产品质量,并减少成本,实现成型工艺的优化。
注塑成型工艺参数
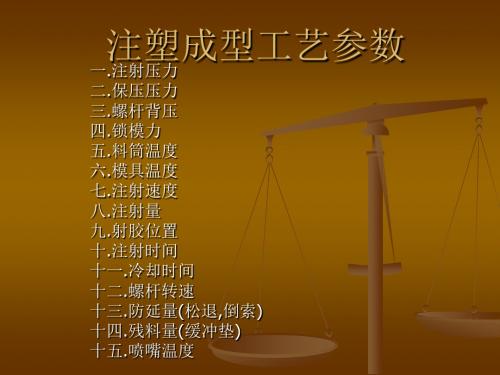
增加流动速率使熔体填充大部分的模穴. 注射压力分二阶段:把熔融物料高速射入模具中的
阶段,此时的压力称为一次注射压力.在材料充满模 具后所加的压力,称为二次注射压力.(保压) 一般二次注射压力约为(80-120MPa)8001200Kg/cm2 在一般正常工艺调试,应从低压力开始并逐渐提高.
POM PBT PP HPVC FPVC HIPS TPR PC+PBT 山都平 HDPE LDPE
160-200 230-260 180-220 150-190 140-180 180-240 150-220 220-270 180-210 180-230 160-220
如何检测熔体的实际温度
料管温度是通过加热圈来控制,加热温度的 升降是通过感温线探测,所以在设定温度时, 要考虑设定值,探测温度,熔料温度三者的差 异.
常用的材料的模具温度介绍
定义
注射速度
不同速度的熔体填充的比较
注射速度与模具结构的关系
注射速度与 产品结构的关系
定义
注射量
注射量与产品/机台的匹配
如何计算注射量
射胶位置
射胶位置设定的依据
射胶位置的构成
定义
注射时间
设定注射时间的方法
设定的依据
保压
一.定义 二.保压与注射压力的关系和位置(切换点) 三.保压过程的控制 四.保压时间的控制
二、保压
在注射过程将近结束时,注射压力切换为保压压 力后,就会进入保压阶段。保压过程中注塑机由 喷嘴不断向型腔补料,以填充由于制件收缩而空 出的容积;如果型腔充满后不进行保压,制件大 约会收缩25%左右,特别是筋处由于收缩过大而 形成收缩痕迹。保压压力一般为充填最大压力的 85%左右,当然要根据实际情况来确定。如下图 所示,图a表示填充开始,图b表示型腔充满到 90%左右,图c表示保压开始,螺杆缓慢向前推进, 图d表示保压结束,型腔完全充满。
实际注塑成型工艺在MOLDFLOW中的设定方法

实际注塑成型工艺在MOLDFLOW中的设定方法常听到做MOLDFLOW的同行提到MOLDFLOW分析成型工艺与实际注塑成型不符,不知怎样在MOLDFLOW中设定实际成型工艺,进而无法与实际生产进行比较。
做过注塑成型的朋友都知道,一个产品的质量好坏跟工艺设定有很大关系,所以用MOLDFLOW分析时,分析结果的准确性跟工艺的设定也有很大关系。
本人从使用MOLDFLOW的经验总结一下,帮助大家对工艺设定有更清楚的了解。
目前大多数注塑成型机器注塑阶段控制方式主要有1、注射时间-注射速度2、螺杆位置-注射速度,而第二种方式用得最多,对于大型制品来说经常采用多段速度来控制以获得更好的质量。
不论哪种方式,其注射的速度都是由注塑机的性能决定的,因此必须要对注塑机的性能有所了解,下面以图例对注塑机的工作原理及注塑工艺做简单介绍。
1.注塑机的简明结构图1(注塑成型机示意图)图2(注塑系统示意图)2.注塑成型工艺接下来用我本人做的一个案例来介绍的是怎样在MOLDFLOW 中设定注塑工艺参数(螺杆位置-注射速度即stroke vs % maximun ram speed ).1. 注塑机选择或定义由于moldflow 数据库中的注塑机大多是国外品牌,如雅宝(Auburg )、赫斯基(Husky )、徳马格(Demag )等,很多牌子是没有的,需要自定义,定义方法如下(以我公司的东芝EC350为例,其它品牌可参照)1) 点toosl-new personal database,出现如下对话框:产品模型和网格统计,分析材料选的是pc+abs (GE C6600)在category(类别)拦中选择process condition(工艺条件)下面的 injection molding machine (注塑机),点OK,进入下一步,点new(新建),出现新对话框如下第1栏为description(描述),trade name中输入名称EC350,manufacturer输入厂家toshiba, data source 输入toshiba,data last modified输入sep 10 ,2002, data status默认,这一页的内容主要是注塑机的一些信息,无关紧要的东西,输入结果如下:第2栏为注射部分(重点),maximum machine injection stroke中输入最大计量行程300mm, maximum machine injection rate中输入最大注射率314cm^3/s,machine screw diameter输入螺杆直径50mm,fill control默认stroke vs ram speed)。
- 1、下载文档前请自行甄别文档内容的完整性,平台不提供额外的编辑、内容补充、找答案等附加服务。
- 2、"仅部分预览"的文档,不可在线预览部分如存在完整性等问题,可反馈申请退款(可完整预览的文档不适用该条件!)。
- 3、如文档侵犯您的权益,请联系客服反馈,我们会尽快为您处理(人工客服工作时间:9:00-18:30)。
塑料成型工艺 与模具设计
二、相关知识
(一) 注射成型 2.注射成型工艺过程
包括成型前的准备、注射过程、制品的后处理。
(1) 注射成型前的准备
1) 原料的检验和预处理 对于吸水性强的塑料(PC、PA、PSU、PMMA):干燥处理 干燥处理的方法 2) 塑料着色: 3) 嵌件的预热:减少内应力 4) 料筒的清洗 塑料不同或颜色不一致时,要进行清洗。 5) 脱模剂的选用
塑料成型工艺 与模具设计
确定成型工艺方法和工艺参数
一、项目导入 二、相关知识 三、项目实施
塑料成型工艺 与模具设计
一、 项目引入
本任务以食品盒盖(如图1-1所示)为载体,训练学生合理选 择分型面的能力。
图1-1 食品盒盖二维图形
图1-2 食品盒盖三维图形
塑料成型工艺 与模具设计
二、相关知识
(一) 注射成型 1.注射成型原理
塑料成型工艺 与模具设计
二、相关知识
(二) 压缩成型 2.压缩成型工艺过程
包括压缩成型前的准备、压缩成型和压后处理 。
图2-7 压缩成型工艺过程
塑料成型工艺 与模具设计
二、相关知识
(二) 压缩成型
2.压缩成型工艺过程
包括压缩成型前的准备、压缩成型和压后处理 。
(1) 压缩成型前的准备
① 预热与干燥
二、相关知识
(一) 注射成型
2.注射成型工艺过程
5)冷却 塑件在模内的冷却过程是指从浇口处的塑 料熔体完全冻结时起到塑件将从模腔内推出为止的全部 过程。实际上冷却过程从塑料注入型腔起就开始了,它 包括从充模完成、保压开始到脱模前的这一段时间。
6)脱模 塑件冷却到一定的温度即可开模,在推出机 构的作用下将塑件推出模外。
首先将粒状或粉状的塑 料原料加入到注射机的料筒 中,经过加热熔融成粘流态, 然后在螺杆或柱塞的推动下, 熔融塑料以一定的流速通过 料筒前端的喷嘴射入闭合的 模具型腔中,经过一定的保 压,塑料在模内冷却、硬化 定型,接着打开模具,从模 内脱出成型的塑件。
1—合模液压缸 2—锁模机构 3—推出液压缸 4—移动模板 5—模具 6—喷嘴 7—固定模板 8—加热器 9—料筒 10—料斗 11—电机 12—注
具有良好的可塑性,这一过程称为塑化。 3)充模 塑化好的熔体在注射压力作用下,被柱塞或螺杆推挤至料筒
前端,经过喷嘴、模具浇注系统进入并充满型腔,这一阶段称为充模。 4)保压 在模具中熔体冷却收缩时,柱塞或螺杆迫使料筒中的熔料不
断补充到模具中,从而成型出形状完整、质地致密的塑件,这—阶段称为 保压。
塑料成型工艺 与模具设计
塑料成型工艺 与模具设计
二、相关知识
(二) 压缩成型
1.压缩成型原理
将塑料原料直接放在经过加热的模具型 腔(加料室)内,凸模向下工作,在热和 压力的作用下,塑料呈熔融状态并充满型 腔,然后再固化成型。 压缩模多用于热固性塑料制件的成型,但 该方法成型周期较长、生产效率低。
图2-6 压缩成型 1—上模座 2—上凸模 3—凹模 4—下凸模 5—下模板 6—下模座
② 预压
(2)压缩成型过程
(3)压后处理 退火处理。
主要作用是消除应力,提高稳定性,减少塑件的变形与开 裂,进一步交联固化,可以提高塑件电性能和力学性能。
塑料成型工艺 与模具设计
二、相关知识
(三) 压注成型 1.压注成型原理
将压注模的加料室与型腔是通过浇注系统连接起来的,通过压柱或柱 塞将加料室内受热塑化熔融的热固性塑料经浇注系统压入被加热的闭合 型腔,最后固化定型。压注模主要用于热固性塑料制件的成型。
常用的脱模剂有三种:硬脂酸锌(除PA),一般塑料均可用;液体石蜡(白油);硅油。手工喷涂
塑料成型工艺 与模具设计
二、相关知识
(一) 注射成型
2.注射成型工艺过程
(2).注射过程
包括:加料、塑化、充模、保压、倒流、冷却和脱模等步骤。 1)加料 将粒状或粉状塑料加入到注射机的料斗中。 2)塑化 对料筒中塑料进行加热,使其由固体颗粒转变成熔融状态并
塑料成型工艺 与模具设计
二、相关知识
(一) 注射成型
3.制品的后处理
⑴目的:减少内应力,稳定了尺寸 ⑵方法
① 退火处理的方法是把制品放在一定温度的烘箱中或液体介质(如热水、热矿 物油、甘油、乙二醇和液体石蜡等)中一段时间,然后缓慢冷却。温度高于使用温度 10 ~20°C,低于热变形温度10~20°C。
退火处理的结果,消除了塑料制品的内应力,稳定了尺寸。对于结晶型塑料还 能提高结晶度,稳定结晶结构,从而提高其弹性模量和硬度,但却降低了断裂伸长 率。
② 调湿处理主要是用于聚酰胺类塑料的制品。将刚脱模的这类塑料制品放在 热水中处理,不仅隔绝空气,防止氧化,消除内应力,而且还可以加速达到吸湿平 衡,稳定其尺寸,故称为调湿处理。
二、相关知识
(三) 压注成型 3.压注成型特点及应用
(1)成型周期短、生产效率高 (2)塑件的尺寸精度高、表面质量好\ (3)可以成型带有较细小嵌件、较深的侧孔及较复杂的塑件 (4)消耗原材料较多
(5)压注成型收缩率比压缩成型大 (6)压注模的结构比压缩模复杂,工艺条件要求严格压注成型适用于形状 复杂、带有较多嵌件的热固性塑料制件的成型。
第1阶段是固态塑料的塑化。 第2阶段是成型。 第3阶段是定型。
塑料成型工艺 与模具设计
二、相关知识
(五)气动挤出成型 气动成型是借助压缩空气或抽真空的方法来成型塑料
瓶、罐、盒、箱类塑件,主要包括中空吹塑成型、真空 成型及压缩空气成型。
图2-12 中空成型 1—吹塑模具 2、3—产品 4—瓶坯
图2-8 压注成型原理 1—压注柱塞 2—加料腔 3—上模座 4—凹模 5—凸模 6—凸模固定板
7—下模座 8—浇注系统凝料 9—制件
塑料成型工艺 与模具设计
二、相关知识
(三) 压注成型 2.压注成型工艺过程
包括压注成型前的准备、压缩成型和压后处理 。
图2-8 压注成型工艺过程
塑料成型工艺 与模具设计
塑料成型工艺 与模具设计
二、相关知识
(四) 挤出成型
挤出成型是利用挤出机 料筒内的螺杆旋转加压的方 式,连续地将塑化好的呈熔 融状态的物料从料筒中挤出, 通过特定截面形状的机头口 模成型,并借助于牵引装置 将挤出的塑料制件均匀拉出, 同时冷却定型而获得截面形 状一致的连续型材。
挤出成型工艺过程一般分为3个阶段