喷涂工艺参数记录表
涂装工艺技术参数

涂装工艺技术参数一、施工环境条件1. 最佳施工环境条件为环境温度10-40℃,湿度30-70% 。
2. 空气湿度不得大于80%。
在湿度大于80%气候情况下,喷漆前需对工件进行烘烤,温度70-80℃(工件基体温度),保温时间30分钟。
3. 要求在配漆和施工环境中配置温度计和湿度计。
二、涂料调配(指加入固化剂后)1.按涂料技术参数进行调配。
2.涂料调配好后需进行过滤除去涂料中杂质,底漆用180目、中涂用180-240目、面漆用300-320目滤布过滤。
3.涂料调配后放置8-10分钟,使涂料熟化后再喷涂。
(此点需严格执行)4.涂料调配后应在4小时内使用完。
三、喷涂前准备工作1.工件在喷涂前应做到干净、干燥;施工场地保持清洁干净,喷漆室每天进行清扫,定期对喷漆室送风过滤棉清理干净。
2.采用空气喷涂时必须安装冷干机(或油水分离器),每天上午和下午各排放一次油、水,湿度大的季节,还需增加排放油、水次数,保证压缩空气无油和水份等杂质。
3.喷漆工和相关接触人员在工作中应做好劳动安全保护,穿戴防毒口罩、手套、工作服等劳保用品,防止吸入有毒溶剂、尘埃等。
四、底、面漆技术参数1. 大光黄底漆(1)稀释剂:茸康大光黄底漆稀释剂;(2)固化剂:进口固化剂;(3)配比:进口固化剂=4:1(重量比);(4)粘度:16-25秒;2. SPU70815P-Y黄色聚氨酯中涂(1) 稀释剂:RUT-085稀释剂(快干型,在15℃以下气温情况使用)或XPS90018溶剂(慢干型,15℃以上<含15℃>气温情况下使用);(2) 固化剂:GXH63417聚氨酯固化剂;(3) 配比: GXH63417聚氨酯固化剂=7:1(重量比);(4) 粘度:14-25秒;3. SPU70806T-Y聚氨酯面漆(或SPU70807T-GY聚氨酯面漆)(1) 稀释剂:RUT-085稀释剂(快干型,在15℃以下气温情况使用)或XPS90018溶剂(慢干型,15℃以上<含15℃>气温情况下使用);(2) 固化剂:GXH63417聚氨酯固化剂;(3) 配比: GXH63417聚氨酯固化剂=4:1(重量比);(4) 粘度:14-25秒;4.干燥:(1) 烘干温度需达到70-80℃(工件基体温度),保温时间30分钟;(2) 工件进烘干室前需流平8-10分钟;(3) 如常温自然干燥,干燥时间应大于24小时后才能开始涂刮腻子或喷涂面漆;5.漆膜厚度要求:(1) 底漆的干膜厚度应达到20- 35um;(2) 面漆的干膜厚度应达到40- 60um;(3) 涂膜总厚度:70μm≤磷化件≤100μm ,80μm≤抛丸喷砂件≤110μm;五、腻子刮磨1. 腻子桶打开后,观察腻子表面有无结皮,如有则去掉,然后将整桶腻子搅拌均匀;2. 严格按原子灰配比(一般为原子灰:固化剂=100:2-3)要求调配腻子,在气温高情况下,不能减少固化剂用量,而应适当减少每次原子灰调配量,并充分搅拌均匀颜色一致;3. 在刮涂腻子时应以工件表面为基准,刮平凹处,尽量使腻子薄而平整;4. 如存在较大凹坑,应分多次填刮,每次刮涂厚度不应超过1mm,且需在上道腻子干燥后进行;5. 腻子经干燥打磨后,整个表面应平整光滑,线角分明,腻子与涂层表面连接处不得有明显接痕,无漆粒等杂质附在工件表面上;6. 擦净:用压缩空气全面擦吹净后再用粘性纱布按一个方向擦净工件表面;。
喷粉工艺参数【范本模板】

喷粉工艺参数(一)、前处理工序1、脱脂:温度40-60℃,时间:约5分钟(必要时开搅拌泵)游离酸度:3-6点。
如可用TL-30脱脂剂及TLJ-10脱脂粉;或碱脱脂游离碱度在30~40Pt,温度30~40℃,处理时间5~10min,再用冷水清洗用流动水清洗,控制水的PH值为7~8。
2、水洗:温度:常温时间:1-2分钟,PH=8-93、酸洗:温度:40-50℃(必要时)浓度:18%时间:(相对应工件的锈蚀程度而定) ,如可用CLJ-333除锈剂;或者控制除锈液中的Fe2+含量<120g/l,酸含量控制在20~30g/l,温度30~40℃,处理时间5~10min4、水洗:温度:常温,时间:2-3分钟PH=8-95、表调:温度:常温,时间:0。
5—1分钟,PH=8-9,如可用采用BLJ-66表面调整剂;或者控制表面调整液的酸度为16~20Pt,PH 值为8.5~9,处理时间为1~2min。
6、磷化:(锌 ):温度:40-55℃,时间:2-3分钟。
FA=0。
6-1。
3点,TA=18-25点,促进值:1.5-3。
5点,如可用LLJ -828补给剂及JLJ-82加速剂;或者控制磷化液的总酸度为30~35Pt,游离酸度2~3Pt,酸比>10,促进剂点数3~4Pt,磷化温度30~40℃,处理时间5~10min;磷化膜重1.5~2.0g/m2;耐蚀性:硫酸铜溶液点滴试验>5min,3%NaCl溶液浸泡>12h.然后用热水清洗控制热水温度80~90℃,PH值为7~8。
7、水洗:温度:常温或加垫60—70℃,时间:1—2分钟8、纯水洗:温度:常温,时间:待工件全部被洗到,并没有残留物为OK.(二)、脱水烘干1、方式:烘干炉烘烤。
2、温度:120-150℃。
3、时间:相对应工件定时间(必需实干)。
一般:5-10分钟(三)、上件工序:(四)、喷粉工序1、操作方式:人工(手动)喷粉2、技术工艺参数:●静电电压:70-80KV,电压过高容易造成粉末反弹和边缘麻点;电压过低上粉率低●压缩空气压力:6-7KG/cm2●静电高压60—90kV。
喷涂打样记录表

产品名称: 1、油漆参数
线别:
制程类型:
日期:
油漆类型
油漆名称
厂商 颜色 比重 稀释济名称 现场调配比例 粘度 滤网目数 备注
底漆
中漆
面漆
全光 消光
2、喷涂工艺参数
项目 类型
喷涂 时间
线速
自转 频率
设定 炉温
实测 炉温
雾化 压力
泵压
流平 时间
环境 干燥 等级 时间 (0.5
um)
UV累
枪数
UV时 间
计照 射能
UV炉温
UV灯 功率
量
底漆
中漆
面漆
3、喷涂产品特性
项目 时间 (标准要求)
:
:
:
:
:
:
酒精测试
百格测试
硬度测试
耐磨测试
底漆
膜厚 中漆
面漆
L
色差 a b
△E 4、制程总结
5、备注
填表:
审核:
喷粉工艺参数(精)

喷粉工艺参数(一)、前处理工序1、脱脂:温度40-60℃,时间:约5分钟(必要时开搅拌泵)游离酸度:3-6点。
如可用TL-30脱脂剂及TLJ-10脱脂粉;或碱脱脂游离碱度在30~40Pt,温度30~40℃,处理时间5~10min,再用冷水清洗用流动水清洗,控制水的PH值为7~8。
2、水洗:温度:常温时间:1-2分钟,PH=8-93、酸洗:温度:40-50℃(必要时)浓度:18%时间:(相对应工件的锈蚀程度而定),如可用CLJ-333除锈剂;或者控制除锈液中的Fe2+含量<120g/l,酸含量控制在20~30g/l,温度30~40℃,处理时间5~10min4、水洗:温度:常温,时间:2-3分钟PH=8-95、表调:温度:常温,时间:0.5-1分钟,PH=8-9,如可用采用BLJ-66表面调整剂;或者控制表面调整液的酸度为16~20Pt,PH值为8.5~9,处理时间为1~2min。
6、磷化:(锌):温度:40-55℃,时间:2-3分钟。
FA=0.6-1.3点,TA=18-25点,促进值:1.5-3.5点,如可用LLJ-828补给剂及JLJ-82加速剂;或者控制磷化液的总酸度为30~35Pt,游离酸度2~3Pt,酸比>10,促进剂点数3~4Pt,磷化温度30~40℃,处理时间5~10min;磷化膜重1.5~2.0g/m2;耐蚀性:硫酸铜溶液点滴试验>5min,3%NaCl溶液浸泡>12h。
然后用热水清洗控制热水温度80~90℃,PH值为7~8。
7、水洗:温度:常温或加垫60-70℃,时间:1-2分钟8、纯水洗:温度:常温,时间:待工件全部被洗到,并没有残留物为OK。
(二)、脱水烘干1、方式:烘干炉烘烤。
2、温度:120-150℃。
3、时间:相对应工件定时间(必需实干)。
一般:5-10分钟(三)、上件工序:(四)、喷粉工序1、操作方式:人工(手动)喷粉2、技术工艺参数:●静电电压:70-80KV,电压过高容易造成粉末反弹和边缘麻点;电压过低上粉率低●压缩空气压力:6-7KG/cm2●静电高压60-90kV。
6工艺检查记录

6工艺检查记录工艺点检记录表 DY-JL-ZK-06 A/1注:该记录此版本(A/1)从2013年8月1日起执行,之前的版本同时作废。
工艺点检记录表 DY-JL-ZK-06 A/1注:该记录此版本(A/1)从2013年8月1日起执行,之前的版本同时作废。
工艺点检记录表 DY-JL-ZK-06 A/1注:该记录此版本(A/1)从2013年8月1日起执行,之前的版本同时作废。
工艺点检记录表 DY-JL-ZK-06 A/1注:该记录此版本(A/1)从2013年8月1日起执行,之前的版本同时作废。
工艺点检记录表 DY-JL-ZK-06 A/1注:该记录此版本(A/1)从2013年8月1日起执行,之前的版本同时作废。
工艺点检记录表 DY-JL-ZK-06 A/1注:该记录此版本(A/1)从2013年8月1日起执行,之前的版本同时作废。
工艺点检记录表 DY-JL-ZK-06 A/1注:该记录此版本(A/1)从2013年8月1日起执行,之前的版本同时作废。
工艺点检记录表 DY-JL-ZK-06 A/1注:该记录此版本(A/1)从2013年8月1日起执行,之前的版本同时作废。
工艺点检记录表 DY-JL-ZK-06 A/1注:该记录此版本(A/1)从2013年8月1日起执行,之前的版本同时作废。
工艺点检记录表 DY-JL-ZK-06 A/1注:该记录此版本(A/1)从2013年8月1日起执行,之前的版本同时作废。
工艺点检记录表 DY-JL-ZK-06 A/1注:该记录此版本(A/1)从2013年8月1日起执行,之前的版本同时作废。
工艺点检记录表 DY-JL-ZK-06 A/1注:该记录此版本(A/1)从2013年8月1日起执行,之前的版本同时作废。
工艺点检记录表 DY-JL-ZK-06 A/1注:该记录此版本(A/1)从2013年8月1日起执行,之前的版本同时作废。
工艺点检记录表 DY-JL-ZK-06 A/1注:该记录此版本(A/1)从2013年8月1日起执行,之前的版本同时作废。
静电喷涂工艺参数
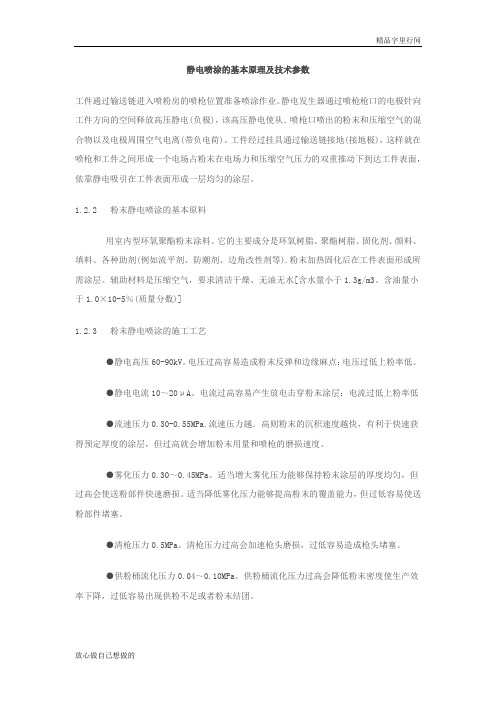
静电喷涂的基本原理及技术参数工件通过输送链进入喷粉房的喷枪位置准备喷涂作业。
静电发生器通过喷枪枪口的电极针向工件方向的空间释放高压静电(负极),该高压静电使从.喷枪口喷出的粉末和压缩空气的混合物以及电极周围空气电离(带负电荷)。
工件经过挂具通过输送链接地(接地极),这样就在喷枪和工件之间形成一个电场占粉末在电场力和压缩空气压力的双重推动下到达工件表面,依靠静电吸引在工件表面形成一层均匀的涂层。
1.2.2 粉末静电喷涂的基本原料用室内型环氧聚酯粉末涂料。
它的主要成分是环氧树脂、聚酯树脂、固化剂、颜料、填料、各种助剂(例如流平剂、防潮剂、边角改性剂等).粉末加热固化后在工件表面形成所需涂层。
辅助材料是压缩空气,要求清洁干燥、无油无水[含水量小于1.3g/m3、含油量小于1.0×10-5%(质量分数)]1.2.3 粉末静电喷涂的施工工艺●静电高压60-90kV。
电压过高容易造成粉末反弹和边缘麻点;电压过低上粉率低。
●静电电流10~20μA。
电流过高容易产生放电击穿粉末涂层;电流过低上粉率低●流速压力0.30-0.55MPa.流速压力越.高则粉末的沉积速度越快,有利于快速获得预定厚度的涂层,但过高就会增加粉末用量和喷枪的磨损速度。
●雾化压力0.30~0.45MPa。
适当增大雾化压力能够保持粉末涂层的厚度均匀,但过高会使送粉部件快速磨损。
适当降低雾化压力能够提高粉末的覆盖能力,但过低容易使送粉部件堵塞。
●清枪压力0.5MPa。
清枪压力过高会加速枪头磨损,过低容易造成枪头堵塞。
●供粉桶流化压力0.04~0.10MPa。
供粉桶流化压力过高会降低粉末密度使生产效率下降,过低容易出现供粉不足或者粉末结团。
●喷枪口至工件的距离150~300mm。
喷枪口至工件的距离过近容易产生放电击穿粉末涂层,过远会增加粉末用量和降低生产效率。
●输送链速度4.5~5.5m/min。
输送链速度过快会引起粉末涂层厚度不够,过慢则降低生产效率。
喷涂工艺卡片
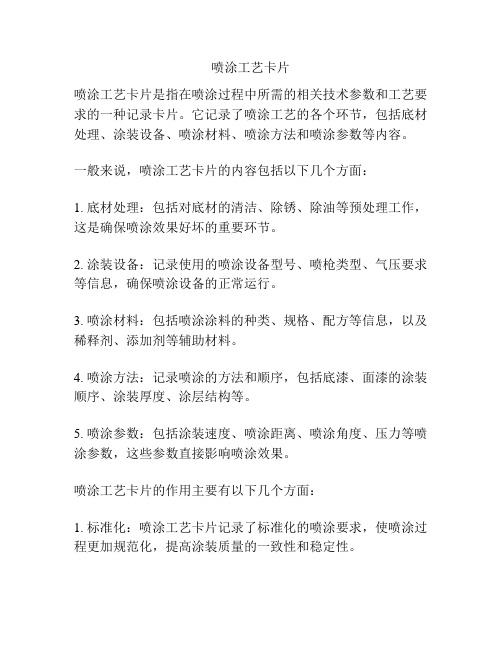
喷涂工艺卡片
喷涂工艺卡片是指在喷涂过程中所需的相关技术参数和工艺要求的一种记录卡片。
它记录了喷涂工艺的各个环节,包括底材处理、涂装设备、喷涂材料、喷涂方法和喷涂参数等内容。
一般来说,喷涂工艺卡片的内容包括以下几个方面:
1. 底材处理:包括对底材的清洁、除锈、除油等预处理工作,这是确保喷涂效果好坏的重要环节。
2. 涂装设备:记录使用的喷涂设备型号、喷枪类型、气压要求等信息,确保喷涂设备的正常运行。
3. 喷涂材料:包括喷涂涂料的种类、规格、配方等信息,以及稀释剂、添加剂等辅助材料。
4. 喷涂方法:记录喷涂的方法和顺序,包括底漆、面漆的涂装顺序、涂装厚度、涂层结构等。
5. 喷涂参数:包括涂装速度、喷涂距离、喷涂角度、压力等喷涂参数,这些参数直接影响喷涂效果。
喷涂工艺卡片的作用主要有以下几个方面:
1. 标准化:喷涂工艺卡片记录了标准化的喷涂要求,使喷涂过程更加规范化,提高涂装质量的一致性和稳定性。
2. 信息共享:将喷涂工艺的相关信息记录下来,方便工艺人员、操作人员共同参考和使用。
3. 效率提升:喷涂工艺卡片可以提供喷涂工艺的参考依据,使工艺操作更加高效,减少浪费和返工。
总而言之,喷涂工艺卡片是一种记录和传递喷涂工艺要求的工具,它对于提高喷涂质量和工艺效率起到了重要的作用。
喷粉工艺参数
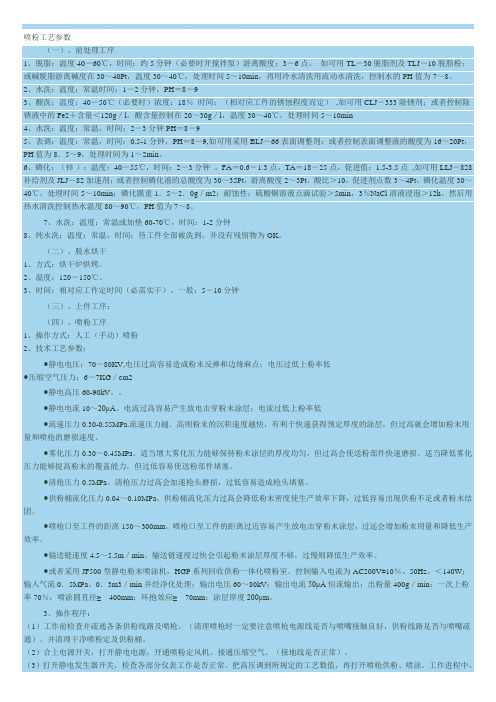
喷粉工艺参数(一)、前处理工序1、脱脂:温度40-60℃,时间:约5分钟(必要时开搅拌泵)游离酸度:3-6点。
如可用TL-30脱脂剂及TLJ-10脱脂粉;或碱脱脂游离碱度在30~40Pt,温度30~40℃,处理时间5~10min,再用冷水清洗用流动水清洗,控制水的PH值为7~8。
2、水洗:温度:常温时间:1-2分钟,PH=8-93、酸洗:温度:40-50℃(必要时)浓度:18%时间:(相对应工件的锈蚀程度而定),如可用CLJ-333除锈剂;或者控制除锈液中的Fe2+含量<120g/l,酸含量控制在20~30g/l,温度30~40℃,处理时间5~10min4、水洗:温度:常温,时间:2-3分钟PH=8-95、表调:温度:常温,时间:0.5-1分钟,PH=8-9,如可用采用BLJ-66表面调整剂;或者控制表面调整液的酸度为16~20Pt,PH值为8.5~9,处理时间为1~2min。
6、磷化:(锌):温度:40-55℃,时间:2-3分钟。
FA=0.6-1.3点,TA=18-25点,促进值:1.5-3.5点,如可用LLJ-828补给剂及JLJ-82加速剂;或者控制磷化液的总酸度为30~35Pt,游离酸度2~3Pt,酸比>10,促进剂点数3~4Pt,磷化温度30~40℃,处理时间5~10min;磷化膜重1.5~2.0g/m2;耐蚀性:硫酸铜溶液点滴试验>5min,3%NaCl溶液浸泡>12h。
然后用热水清洗控制热水温度80~90℃,PH值为7~8。
7、水洗:温度:常温或加垫60-70℃,时间:1-2分钟8、纯水洗:温度:常温,时间:待工件全部被洗到,并没有残留物为OK。
(二)、脱水烘干1、方式:烘干炉烘烤。
2、温度:120-150℃。
3、时间:相对应工件定时间(必需实干)。
一般:5-10分钟(三)、上件工序:(四)、喷粉工序1、操作方式:人工(手动)喷粉2、技术工艺参数:●静电电压:70-80KV,电压过高容易造成粉末反弹和边缘麻点;电压过低上粉率低●压缩空气压力:6-7KG/cm2●静电高压60-90kV。
水性涂料涂装工艺参数标准
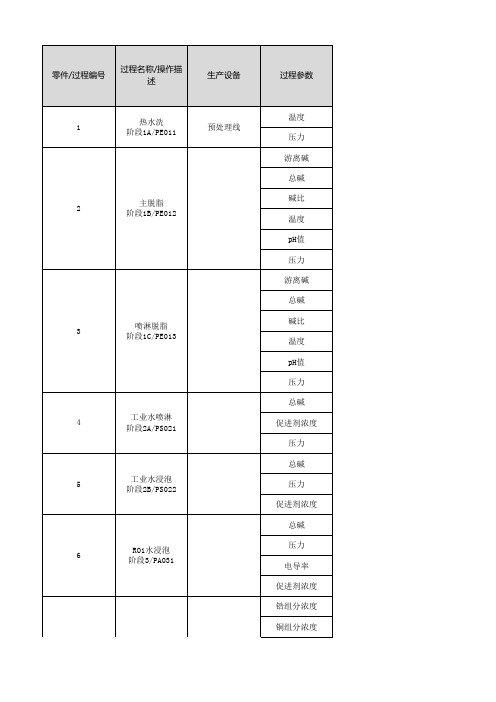
10min
流量计 压力表 压力表 pH计 电导率仪 细菌棒 pH计 电导率仪 压力表 流量计 分析天平,烘箱 细菌棒 压力表 pH计 分析天平,烘箱 压力表 细菌棒 分析天平,烘箱 细菌棒 压力表 电导率仪 pH计 压力表 电导率仪 pH计 压力表
目视 炉温跟踪仪 炉温跟踪仪
100%
100%
100%
30000~65000/min 50~550L/min
(2.3:1)~(2:1.2) 0.4~0.6m/s 21~28℃ 55%~75%RH 5~6.5bar
100~200mL/min (2.3:1)~(2:1.2)
见烘烤数据 20~55μm
制造商数据表
制造商数据表
>80/20°
测定仪 系统压力表 系统压力表 系统压力表 系统压力表 系统压力表
系统仪表 目视
系统压力表 见附着力测试规范/批
次样板 测定仪 系统压力表 系统压力表 系统仪表 系统仪表 系统仪表 系统仪表
目视 系统压力表 见附着力测试规范/批
次样板 测定仪 系统压力表 系统压力表 系统压力表
目视 见附着力测试规范/批
机器人
烘房窗口 压缩空气
温度 湿度 向下风速 向下风速 温度 湿度 油漆流量 电流 旋杯转速 成型空气
烘烤温度
脱水率
湿度 向下风速
温度 湿度 油漆流量 旋杯转速
30
自动喷涂内表面色 漆
机器人
成型空气
向下风速
喷房
温度
31
自动喷涂外表面色 漆
机器人
湿度 油漆流量
电流 旋杯转速
成型空气
向下风速
喷房
温度
32
主要工序工艺参数表

主要⼯序⼯艺参数表主要⼯序⼯艺参数表表⼀、喷粉:其它要求:⼯件表⾯温度<47度、粉房最佳温度15-25度、湿度<75%、粉房空⽓含尘量<1.5mg/m3、粉房附近横向风速≤0.3m/s、照明≥300克勒斯,压缩空⽓含⽔量<1PPM、含油量<0.1PPM、压⼒4.0-7.0kgf/cm2。
表⼆、主要⼯序常见问题及解决⽅法表对基材进⾏检验按《铝型材检验规程》检验,发现问题及时反馈到上道⼯序。
2.上排绑挂4.1按⽣产计划备料,看每筐料的随⾏卡⽚并认真核对型号数量,做好上料记录。
4.2根据型材种类选择合适的吊架,将型材主要装饰⾯向上⽤铝丝固定在吊架上,要求固定牢固稳定、型材与型材之间留有⾜够的空隙。
尽量将型材平⾯向下以防⽌⽓泡发⽣。
4.3上排绑挂过程中注意复查型材外观有⽆缺陷。
例如油斑、⽔锈、胶迹。
4.4将外观有缺陷的型材进⾏返修,变形⽤钳⼦矫正、胶迹⽤信那⽔擦除、其它⽤180-600#砂纸打磨。
返修后合格的允许上排绑挂。
5. 脱脂5.1型材进⼊脱脂槽前要注意观察其表⾯状态,灰尘和铝屑较多时先⽔洗再脱脂,根据油渍和斑点情况合理调整脱脂⼯艺参数。
5.2正常情况按表⼀中脱脂⼯艺参数操作。
5.3根据化验分析结果、⽣产量和型材脱脂效果及时补加药剂,加药时应缓慢均匀地添加到槽⾯各处,⽤吊架上下搅拌均匀后使⽤。
5.4槽液使⽤⼀段时间后效果差时应及时倒槽,清除槽底铝粉和沉淀。
5.5脱脂完毕从脱脂槽吊起后应使型材倾斜并保持1-2分钟,⾄型材表⾯槽液基本滴⼲为⽌,以节省药剂和利于后续清洗。
注意观察脱脂效果,发现问题及时处理。
5.6常见问题参照表⼆中规定的⽅法处理,仍不能处理时及时通知技术⼈员解决。
6. ⽔洗6.1进⼊⽔洗槽先使型材上下摆动2-3次,再浸泡1-2分钟。
6.2型材从⽔洗槽吊起后应注意观察其表⾯除油状况(⽔膜是否连续、有⽆斑点残留、背⾯有⽆泡沫残留),发现异常及时处理。
6.3⽣产时应保证⽔洗槽的溢流,发现⽔质浑浊时及时清槽换⽔。
喷漆工作检测记录表

喷漆工作检测记录表
1. 检测项目
1.1 检测日期
记录检测的日期,以便追溯和记录。
1.2 检测人员
填写进行喷漆工作检测的人员姓名,确保检测的准确性和可靠性。
1.3 检测设备
记录使用的检测设备的型号和编号,保证设备的正确性和标准化。
1.4 检测地点
填写进行喷漆工作检测的具体地点,方便追溯和记录。
1.5 检测标准
列出用于喷漆工作检测的标准和规范,确保检测的一致性和准确性。
2. 检测结果
2.1 喷漆工作信息
记录进行喷漆工作的相关信息,包括喷漆颜色、喷漆区域、喷漆材料等。
2.2 喷漆质量检测
根据喷漆工作的标准和规范,对喷漆质量进行检测,包括涂层厚度、颜色均匀性、涂层附着力等。
2.3 检测结果记录
记录喷漆工作的检测结果,包括合格或不合格,并填写具体的检测数值或问题描述。
3. 处理措施
3.1 不合格处理
对于出现不合格的喷漆工作,记录具体问题,并提出相应的处理措施,以确保喷漆质量达到标准要求。
3.2 处理结果
记录对不合格喷漆工作进行处理后的结果,包括重新检测的结果和喷漆质量是否符合标准要求。
4. 备注
在此部分填写任何额外的备注信息,如特殊情况、检测过程中的注意事项等。
喷粉工艺参数

喷粉工艺参数(一)、前处理工序1、脱脂:温度40-60℃,时间:约5分钟(必要时开搅拌泵)游离酸度:3-6点。
如可用TL-30脱脂剂及TLJ-10脱脂粉;或碱脱脂游离碱度在30~40Pt,温度30~40℃,处理时间5~10min,再用冷水清洗用流动水清洗,控制水的PH值为7~8。
2、水洗:温度:常温时间:1-2分钟,PH=8-93、酸洗:温度:40-50℃(必要时)浓度:18%时间:(相对应工件的锈蚀程度而定),如可用CLJ-333除锈剂;或者控制除锈液中的Fe2+含量<120g/l,酸含量控制在20~30g/l,温度30~40℃,处理时间5~10min4、水洗:温度:常温,时间:2-3分钟PH=8-95、表调:温度:常温,时间:0.5-1分钟,PH=8-9,如可用采用BLJ-66表面调整剂;或者控制表面调整液的酸度为16~20Pt,PH值为8.5~9,处理时间为1~2min。
6、磷化:(锌):温度:40-55℃,时间:2-3分钟。
FA=0.6-1.3点,TA=18-25点,促进值:1.5-3.5点,如可用LLJ-828补给剂及JLJ-82加速剂;或者控制磷化液的总酸度为30~35Pt,游离酸度2~3Pt,酸比>10,促进剂点数3~4Pt,磷化温度30~40℃,处理时间5~10min;磷化膜重1.5~2.0g/m2;耐蚀性:硫酸铜溶液点滴试验>5min,3%NaCl溶液浸泡>12h。
然后用热水清洗控制热水温度80~90℃,PH值为7~8。
7、水洗:温度:常温或加垫60-70℃,时间:1-2分钟8、纯水洗:温度:常温,时间:待工件全部被洗到,并没有残留物为OK。
(二)、脱水烘干1、方式:烘干炉烘烤。
2、温度:120-150℃。
3、时间:相对应工件定时间(必需实干)。
一般:5-10分钟(三)、上件工序:(四)、喷粉工序1、操作方式:人工(手动)喷粉2、技术工艺参数:●静电电压:70-80KV,电压过高容易造成粉末反弹和边缘麻点;电压过低上粉率低●压缩空气压力:6-7KG/cm2●静电高压60-90kV。
冷喷涂工艺流程
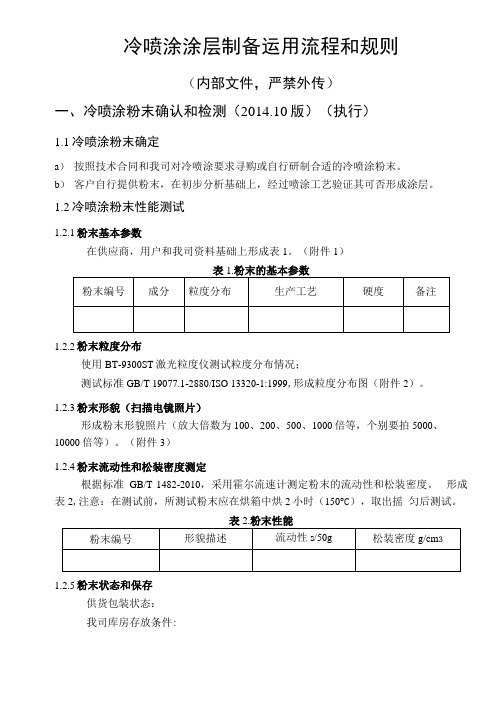
冷喷涂涂层制备运用流程和规则(内部文件,严禁外传)一、冷喷涂粉末确认和检测(2014.10版)(执行)1.1冷喷涂粉末确定a)按照技术合同和我司对冷喷涂要求寻购或自行研制合适的冷喷涂粉末。
b)客户自行提供粉末,在初步分析基础上,经过喷涂工艺验证其可否形成涂层。
1.2冷喷涂粉末性能测试1.2.1粉末基本参数在供应商,用户和我司资料基础上形成表1。
(附件1)表1.粉末的基本参数1.2.2粉末粒度分布使用BT-9300ST激光粒度仪测试粒度分布情况;测试标准GB/T 19077.1-2880/ISO 13320-1:1999,形成粒度分布图(附件2)。
1.2.3粉末形貌(扫描电镜照片)形成粉末形貌照片(放大倍数为100、200、500、1000倍等,个别要拍5000、10000倍等)。
(附件3)1.2.4粉末流动性和松装密度测定根据标准GB/T 1482-2010,采用霍尔流速计测定粉末的流动性和松装密度。
形成表2,注意:在测试前,所测试粉末应在烘箱中烘2小时(150°C),取出摇匀后测试。
表2.粉末性能1.2.5粉末状态和保存供货包装状态:我司库房存放条件:1.3自制(自混粉末)1.3.1混粉工艺根据技术要求制粉,具体工艺参数见表3。
3.1.3.2粉末性能检测粉末性能检测参见“1.2冷喷涂粉末性能测试”。
二、冷喷涂基体2.1基体性能了解基体试样的材质、成分、热处理状态、硬度、数量、喷涂位置。
2.2基体测试一般情况下,中、低硬更HB300,高硬ffi>HRC30。
用布洛维硬度计和显微硬度计(硬质相和基体相明显分布时)测试基体的硬度,并形成报告表4。
(附件4)表4基体试样状态2.3基体处理2.3.1热处理(选作)用加热炉和真空气氛电阻炉对基体进行退火等热处理(保护气体为N2或Ar 气)。
2.3.2编号按试验情况对基体试样进行编号2.3.3喷砂处理采用20#棕刚玉砂或者45目细砂或指定材料对基体进行喷砂处理。
静电喷涂工艺参数
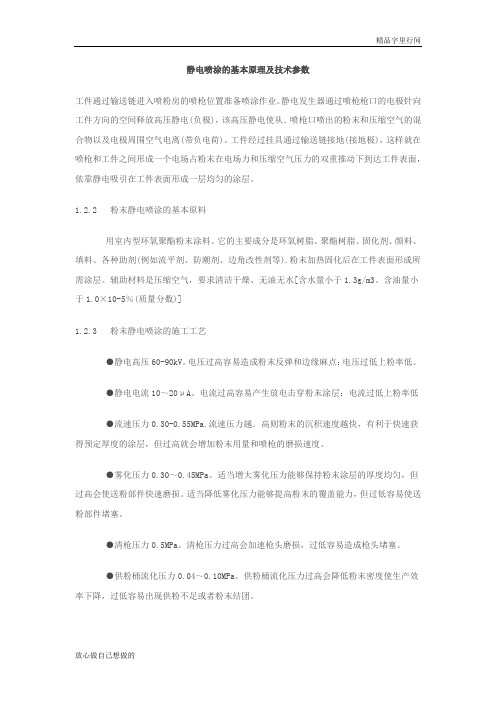
静电喷涂的基本原理及技术参数工件通过输送链进入喷粉房的喷枪位置准备喷涂作业。
静电发生器通过喷枪枪口的电极针向工件方向的空间释放高压静电(负极),该高压静电使从.喷枪口喷出的粉末和压缩空气的混合物以及电极周围空气电离(带负电荷)。
工件经过挂具通过输送链接地(接地极),这样就在喷枪和工件之间形成一个电场占粉末在电场力和压缩空气压力的双重推动下到达工件表面,依靠静电吸引在工件表面形成一层均匀的涂层。
1.2.2 粉末静电喷涂的基本原料用室内型环氧聚酯粉末涂料。
它的主要成分是环氧树脂、聚酯树脂、固化剂、颜料、填料、各种助剂(例如流平剂、防潮剂、边角改性剂等).粉末加热固化后在工件表面形成所需涂层。
辅助材料是压缩空气,要求清洁干燥、无油无水[含水量小于1.3g/m3、含油量小于1.0×10-5%(质量分数)]1.2.3 粉末静电喷涂的施工工艺●静电高压60-90kV。
电压过高容易造成粉末反弹和边缘麻点;电压过低上粉率低。
●静电电流10~20μA。
电流过高容易产生放电击穿粉末涂层;电流过低上粉率低●流速压力0.30-0.55MPa.流速压力越.高则粉末的沉积速度越快,有利于快速获得预定厚度的涂层,但过高就会增加粉末用量和喷枪的磨损速度。
●雾化压力0.30~0.45MPa。
适当增大雾化压力能够保持粉末涂层的厚度均匀,但过高会使送粉部件快速磨损。
适当降低雾化压力能够提高粉末的覆盖能力,但过低容易使送粉部件堵塞。
●清枪压力0.5MPa。
清枪压力过高会加速枪头磨损,过低容易造成枪头堵塞。
●供粉桶流化压力0.04~0.10MPa。
供粉桶流化压力过高会降低粉末密度使生产效率下降,过低容易出现供粉不足或者粉末结团。
●喷枪口至工件的距离150~300mm。
喷枪口至工件的距离过近容易产生放电击穿粉末涂层,过远会增加粉末用量和降低生产效率。
●输送链速度4.5~5.5m/min。
输送链速度过快会引起粉末涂层厚度不够,过慢则降低生产效率。