煤矿自动装车
煤矿机械工程中自动化与精益生产的协同优化策略

煤矿机械工程中自动化与精益生产的协同优化策略摘要:我国作为煤炭大国,煤矿产业在国民经济中占据举足轻重的地位。
然而,传统的煤矿生产方式往往存在生产效率低、能耗大、安全隐患严重等问题。
近年来,随着科技的飞速发展,特别是人工智能、物联网、大数据等技术的不断成熟,为煤矿机械工程自动化生产提供了有力支持。
新形势下,煤矿机械工程中自动化生产的措施成为了产业转型升级的必然选择。
关键词:煤矿工程;自动化;科学开采引言在经济与科技持续进步的背景下,机械自动化技术不断发展,这就在一定程度上有效推动了煤矿生产机械化水平,纵观实际情况可以发现,以往的煤矿生产大多以人力为主,这就使得工作人员压力较重,同时安全隐患较多,容易出现事故问题,而在新时代背景下,先进自动化技术衍生并发展,将其应用在煤矿机械工程中可以更好地提高煤矿工程效率,促使精益生产目标的实现,为我国煤矿领域的发展提供助益。
1、煤矿机械工程中自动化生产重要性1.1提高生产效率自动化生产能够在很大程度上提高煤矿生产效率,降低人力成本。
通过引入智能化的生产设备,实现矿井生产过程中的快速、准确、高效,从而提高整体生产效益。
并且自动化生产技术能有效减少能源消耗和环境污染。
相较于传统生产方式,自动化设备能够在运行过程中实现能源的高效利用,降低能源消耗,减少废弃物排放,有利于实现绿色矿山的目标。
1.2安全生产自动化生产具有较高的安全性能,能有效降低事故风险。
通过智能化监测和控制系统,实时监控矿井生产环境,发现安全隐患及时预警,确保矿井生产安全。
同时应用自动化生产设备可以减少对劳动力的依赖,降低人力成本。
通过引入自动化设备,实现矿井生产过程中的智能化、自动化,降低了对熟练工人的需求,有利于缓解矿井用工难题[1]。
1.3促进产业升级煤矿机械工程自动化生产的实施有助于推动煤炭产业转型升级。
自动化生产技术的应用,将促使煤炭企业加大技术创新力度,提高产业整体竞争力,为我国煤炭产业可持续发展奠定基础。
煤炭装车自动化技术研究与开发

示 、 机 交互 操 作 , 时读 写 设备 运 行 数据 , 人 实 直观 地 控 制设 备 的定 位 运 行 , 体 设 备 数 字 精 确 单 定位 , 系统设 备 集 中控制运 行 。 高 了装车 系统 的生 产效 率和 设备 运行 的可 靠性 。操 作 系统 具 提
壁、 治理 片帮 , 施工 工 序 简单 , 大缩 短 了施 工时 间 。 大
少的, 主要 由放 仓设 备 、 输设 备 、 皮 调 度 绞 车等 运 车
组 成 。各个 环 节之 间的 运 作要 求 协 调有 序 、 准确 无
误, 单体 设 备 自身 的运作 需 要 进行 精 确 定 位 。 当前
维普资讯
20 0 6年第 4期
No 4 . 2o o6
煤
炭
科
技
3
C OAL S I C ENC & T CHN 0GY E E 0L MAG AZ NE I
文 章 编 号 :0 83 3 (0 6 0 -0 30 10 -7 12 0 )400 -3
理, 即得 出牵 引钩 头走 行 的距 离 . 并在 图示 操作 终端
1 原煤装车 系统概况
煤 由电 液推 杆 控 制 的平 板 闸 门 给人 带 式 输 送
上 显示 出 当前 所处 的 位置 。绞 车运行 定位 点可 由触 摸 屏设定 给人 .亦 可 沿装 车线对 运行 区 间进行 数字
( )在 对 煤 壁 进行 加 固后 , 架 的初 撑力 得 到 1 支 了提高 , 工作 状态 也 比较 正常 . 较好 地控 制 了工作 面 片帮 、 冒顶 事 故 , 果 明显 。 效 ()采 取 该 种煤 壁 加 固措施 后 , 2 不但 保 证 了矿
露天煤矿开采基本知识
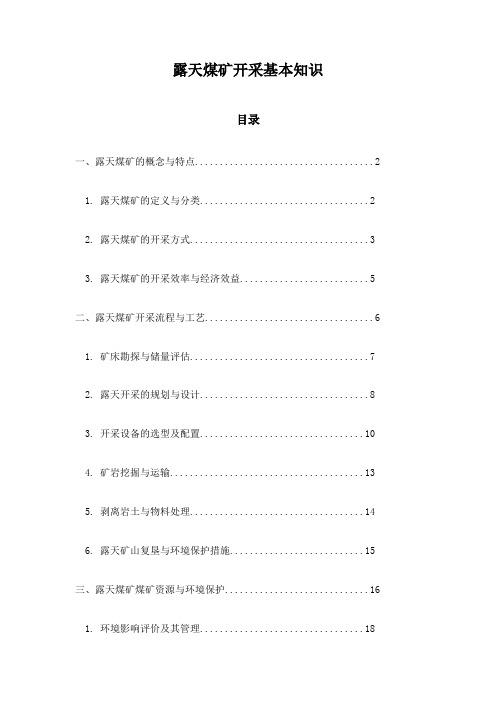
露天煤矿开采基本知识目录一、露天煤矿的概念与特点 (2)1. 露天煤矿的定义与分类 (2)2. 露天煤矿的开采方式 (3)3. 露天煤矿的开采效率与经济效益 (5)二、露天煤矿开采流程与工艺 (6)1. 矿床勘探与储量评估 (7)2. 露天开采的规划与设计 (8)3. 开采设备的选型及配置 (10)4. 矿岩挖掘与运输 (13)5. 剥离岩土与物料处理 (14)6. 露天矿山复垦与环境保护措施 (15)三、露天煤矿煤矿资源与环境保护 (16)1. 环境影响评价及其管理 (18)2. 有效控制水土流失和粉尘污染 (19)3. 减少对原生生态系统的破坏 (20)4. 节能减排与可持续发展 (22)四、露天煤矿的技术进步与管理创新 (23)1. 自动化与数字化矿山建设 (24)2. 智能化矿山信息系统 (26)3. 新技术在露天煤矿中的应用 (27)4. 煤矿工程项目管理与质量控制 (28)五、露天煤矿安全生产与员工培训 (29)1. 安全生产法规和标准制定 (31)2. 危险源识别与事故预防 (32)3. 员工职业健康与安全培训 (33)4. 应急救援体系建设与发展 (34)六、露天煤矿的持续性发展与未来趋势 (35)1. 新技术在露天煤矿的应用趋势 (37)2. 经济效益与环境效益平衡的策略 (38)3. 国际露天煤矿发展趋势与经验借鉴 (39)一、露天煤矿的概念与特点露天煤矿是指开采深度小于150米、易于直接采掘、并且地表结构有利于开采的煤炭矿床。
相对地下煤矿,露天煤矿开采方式简单,施工设备规模略大, production 能量高,也更易于实现机械化和自动化。
开采深度浅:主要开采地表附近的煤层,最大开采深度一般不超过150米,有时甚至更浅。
地面剥离:需要移除地表 overlying strata,包括岩石、土壤等,暴露煤炭层。
采矿方式较为集中:采用各种露天开采方法,如开挖、堆推、炸断等,对地域范围相对集中。
煤矿的自动装车系统

煤矿自动装车系统0 引言铁路快速装车系统是一种将散装物料按规定的质量快速连续的称量并装入列车车厢的系统,具有一次称量、一次装载、速度快、精度高等特点。
当前在大型煤矿、非煤矿山等企业使用已经非常广泛,但由于受铁路技术水平及检测技术的影响,我国现有装车系统至今没有一家实现全自动控制。
某些环节仍然停留在手动、半自动装车的水平。
我国煤矿的重车称量是与装车同步进行,一种方式是轨道衡置于跨线煤仓仓口或胶带输送机卸料口下方,边装车边称量,通过称量控制装车;另一种方式是跨线多煤口装车线,轨道衡置于跨线煤仓出口,人工预装车后称量,多退少补,往返儿次才能达到准确装车。
随着电了称重业的发展,日前国外己采用大型定量仓快速装车系统,预先在定量仓中按车皮标重自动预装仓,待列车车厢行进经过定量仓仓口时,自动按车厢标重装车,实现快速、准确装车。
快速定量装车系统主要由输煤系统、定量装车机械设备、三级自动取样系统设备、液压控制系统、电脑监控系统等组成。
1 快速定量装车系统功能设计快速定量装车系统通过计算机采集主上煤带式给料机、主上煤带式输送机及各种现场设备的信号,处理接收操作指令后发出正确的控制指令,实现自动连续调节给料、定量自动装车、二级取样、清单打印、动态图面显示等功能。
1.1 装车操作者选定与机车(或调车绞车)的速度、车型相适应的给料量后,被选择的给料机给料,给料量随时由输送带秤(核了秤)反映出来,在计算机内部与设定的给料量比较,从而调节给料机给料量,两者协调一致,确保了装车的连续和稳定值,保证了连续自动调节给料。
当列车到装车塔下时,由系统控制放下装车溜槽,此时缓冲仓料位己到合适的位置。
操作者按下称重循环按钮后,缓冲仓下的4个配料液压平板闸门自动地向定量仓中卸料,同时称重传感器准确地称重、控制完成定量配料。
其后,由闸门控制向车厢中放料,料量放足后由称重传感器控制排料平板闸门关闭。
而后车辆行驶车厢之间的空档距离,这期间缓冲仓又向定量仓继续配料,为下一车厢装车作准备,从而实现连续定量自动装车。
PLC控制的自动装车系统设计

PLC控制的自动装车系统设计【摘要】根据现有煤矿装车系统的特点,提出自动化改造方案。
采用S7-200系列PLC和PC机实现对整个装车过程的自动控制。
通过PC机与PLC、PC机与工控以及PC机与现场仪表的通信实现PC对PLC装车系统的实时控制。
通过对整个装车流程的分析,用梯形图程序编写了通信模块、数据转换、加煤过程、状态代码传送过程以及装车精度控制等程序。
实验室的仿真结果证明了此装车系统的设计可以达到提出的技术指标要求,能够可靠、准确地实时监测和记录装车过程中的运行状况,并具有记录、查询等功能,解决了放料、传输、装载等环节的问题。
实践证明:装车过程的效率和自动化程度都达到了提高,成功实现了对装车系统的自动控制。
自动化控制领域的飞速发展给煤碳、电力、通信等行业带来了很大的经济效益。
【关键词】PLC;装车系统;S7-200According:to the characteristics of the existing coal loading systems,automation proposed reform program. With S7-200 series PLC and PC,to achieve automatic control of the entire loading process. Through the PC,and PLC,PC and PC-machine and industrial communication with field instrumentation to achieve PC loading system on the PLC real-time control. Through the analysis of the entire loading process,with the Ladder written communication module,data conversion,adding coal,a status code of the transmission process and the loading accuracy control procedures. Labs Simulation results show that loading system of the design can meet the technical index requirements,can be as accurate as real-time tests and accuracy of loadingsystem. The Function and have accuracy,searching so,solve the discharge,transmission,load and other aspects of the problem. Practice has proved that:loading process efficiency and automation have reached the higher loading was achieved on Automatic Control. The rapid development of the field of automatic control for coal,electricity,telecommunications and other industries has brought great economic benefits.Keywords:PLC;Loadingsystem;S7-2001.背景的提出1.1 课题的来源老式的煤矿装车系统多为手动操作,操作人员根据目测轨道的读数进行对装煤车的控制。
自动配煤系统简介-II

煤矿用自动装车配煤控制系统简介由于煤矿矿井煤质构造比较复杂,影响煤质的因素较多,造成矿井煤质不稳定,波动性较大,难以符合不同用户的不同需要。
把不同质量的煤相互掺合,从而得到所需要的目标煤质,称为配煤。
对于采用两种煤质的配煤,就是将矸石以一定的比例混入原煤中,使混合后的煤的热值符合用户的要求。
本系统适合两种煤质的配煤,是利用灰分测试仪在线测试混合后煤的灰分,然后动态调节矸石的流量,使混合后的煤符合用户的要求。
对多种煤质的配煤,需重新设计,但原理一样。
一、基本原理在煤的掺合过程中,煤的质和量有以下数学模型A1*Q1+A2*Q2=A3*Q3 -------------①式中各变量的定义:A1-----原煤的产品灰分Q1-----原煤的产品流量A2-----矸石的产品灰分Q2-----矸石的产品流量第 1 页共7 页A3-----配完以后的目标灰分Q3-----配完以后的目标流量,Q3=Q1+Q2由①式可得出:A3=( A1*Q1+A2*Q2)/(Q1+Q2)由于灰分是表示煤中所含杂质的比例,故必须存在A2≥A3≥A1的条件,配煤才有实际意义,只要满足此条件,无论A1、Q1、A2具体的值是多少,都可以通过增加和减少Q2来达到希望的A3,见图1-1。
图1-1第 2 页共7 页第 3 页 共 7 页当A3被指定后,通过指定值和检测值的比较,适时调节矸石流入量,从而达到A3在一个允许的小误差范围内波动,实现配煤自动化。
由此我们可以设计出如图1-2所示的基本系统:图1-2二、系统框图第 4 页共7 页二、系统各单元介绍1.储煤仓储煤仓用来储存待配比的原煤和矸石,本系统最少需要两个储煤仓,分别储存原煤和矸石,如有多个储煤仓轮流使用,效果最好。
2.流量自动调节装置流量自动调节装置是位于储煤仓底部,用来关闭储煤仓和自动调节从煤仓流到传送皮带的煤的流量,由自动控制箱、液压站、液压闸板、位置传感器组成,可受中心站计算机集中控制,能够预置或根据需要自动调节液压闸门的开启位置,由此开启位置中心站计算机可以估算出煤的流量。
液压自动装车控制系统的设计及应用
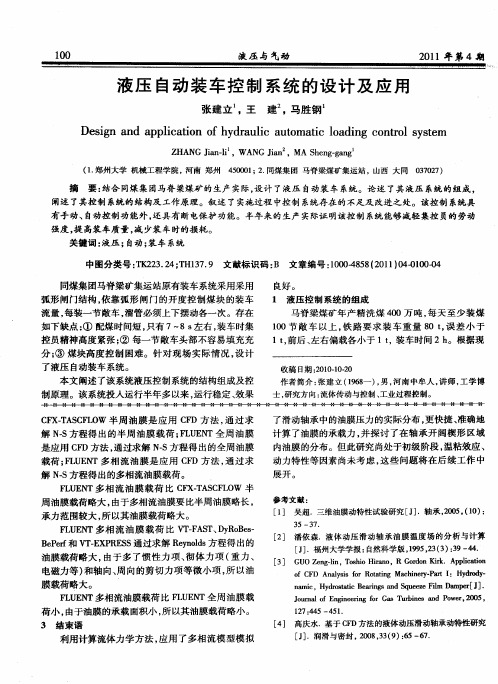
阐述 了其控 制 系统的结 构及 工作原 理 。叙 述 了实施过 程 中控 制 系统存 在的 不足及 改进之 处 。该控制 系统具
有 手动 、 自动控 制 功能 外 , 还具 有 断 电保护 功 能。半年 来 的生产 实 际证 明该控 制 系统能 够减轻 集控 员的 劳动 强度 , 高装 车质 量 , 少装 车 时的损 耗 。 提 减
本 文 阐述 了该 系统 液压 控制 系统 的结 构组 成及 控 制原理 。该 系统投 入运行 半 年多 以来 , 行稳 定 、 果 运 效
C X—A C L W 半 周 油 膜 是 应 用 C D 方 法 , 过 求 F T S FO F 通 解 N S方 程得 出 的半 周 油膜 载荷 ; L E T全 周 油 膜 . FU N
良好 。
1 液压控 制 系统 的组 成
弧形闸门结构 , 依靠弧形 闸门的开度控制煤块 的装车 流量 , 每装一 节 敞车 , 管必 须上下 摆动各 一 次 。存 在 溜 如下缺点 : 配煤时间短 , ① 只有 7~ 左右 , 88 装车时集 控员精神高度紧张 ; 每一节敞车头部不容易填充充 ② 分 ; 煤块高度控制 困难。针对现场实际情况, 计 ③ 设 了液压 自动 8 ) 男 , 16 一 , 河南 中牟人 , 师 , 学博 讲 工 士, 研究方 向: 流体传 动与控制 、 工业过程控制 。
了滑动轴 承 中的油膜 压力 的实 际分布 , 更快捷 、 准确 地 计算 了油膜 的承载力 , 探 讨 了在轴 承 开 阔 楔形 区域 并 内油膜 的分 布 。但此 研究 尚处 于初级 阶段 , 温粘效 应 、 动 力特性 等 因素 尚未 考 虑 , 些 问题 将 在 后 续 工作 中 这
马脊梁 煤矿 年 产精 洗 煤 4 0万 吨 , 0 每天 至 少 装煤 10节 敞 车 以 上 , 路 要 求 装 车 重 量 8 , 差 小 于 0 铁 0 t误 1t前后 、 , 左右 偏载各 小 于 1t ,装车 时间 2h 。根据 现
煤矿综合自动化在观音山煤矿的实际应用宋进

煤矿综合自动化在观音山煤矿的实际应用宋进发布时间:2021-09-17T06:30:37.585Z 来源:《现代电信科技》2021年第9期作者:宋进[导读] 煤矿综合自动化系统采用3层网络体系结构:浏览器、应用逻辑服务器、数据库服务器,煤矿综合自动化系统的开发平台为微软公司,监控软件基于网络平台运行,以网络操作系统Windows2003Server为运行环境,以关系数据库为数据库支撑。
(昭通市能源局 657000)摘要:本文探讨了煤矿综合自动化技术平台基本构架,并叙述了观音山煤矿在实际生产中的实施。
关键词:煤矿综合自动化、观音山煤矿;应用;减少人力;节能增效1煤矿综合自动化技术平台基本构架1.1硬件平台数据传输网采用光缆冗余环形工业以太网,实现集成传输功能,可提高系统可靠性。
地面信息管理中心采取双机互备的方式设置各子系统工作站、数据库服务器、管控服务器等,分别接入工业以太网核心交换机。
网络中的所有设备均支持SNMP网管。
整个控制网络为独立的监控信息传输网络,只通过硬件防火墙与管理信息网联接,保证系统的安全。
在管理信息网内配置Web服务器,用于提供Web应用发布,使管理信息网内的客户端能够浏览到综合自动化系的相关信息数据。
1.2软件平台煤矿综合自动化系统采用3层网络体系结构:浏览器、应用逻辑服务器、数据库服务器,煤矿综合自动化系统的开发平台为微软公司,监控软件基于网络平台运行,以网络操作系统Windows2003Server为运行环境,以关系数据库为数据库支撑。
与各子系统的软件接口主要采用OPC接口,对于不具备OPC接口的子系统,也采用DDE、TDCOM、ODBC或FTP接口方式。
软件功能:对各子系统进行信息协议交换、综合分析、分类处理,Web浏览,数据分级管理,事件记录,报表打印,安全认证。
1.3各接入子系统1.3.1井下胶带集控系统该系统的各胶带就地控制机通过RS485接口就近接入井下工业以太环网交换机,设在地面的管控服务器通过OPC软件接口与各就地控制机进行数据交换,获取现场各个点的信息并存储至实时数据库中,设在地面信息管理中心的胶带操控工作站与管控服务器进行数据交互并可发布控制命令,从而实现对多条胶带的集中控制和监测,以及顺、逆煤流程序控制和胶带运输系统的优化控制。
煤矿定量装车系统

煤矿定量装车系统
近年来,为响应生态文明建设,煤矿企业的发展更加注重绿色化和信息化,煤矿用定
量装车系统便是数字化矿山系统建设的一个重要组成部分。
江苏呈祥基于多年的实践经验,研发的煤矿用定量装车系统,具有功能全,效率高的
特点,不仅满足了定量装车的基本功能要求,同时考虑到各方面细节流程及安全防范的要素,使客户装运效率、精度、安全管理得到全方位提升。
系统组成: (1) 汽车衡称重系统 (2) 定量控制系统
(3) 系统软件 1、汽车衡称重系统
车辆到达地磅前,按照先后顺序,上磅称重。
系统采集信息汇总到集团,自动进行打印,仪表输出信号到定量控制系统
2、定量控制系统
定量控制系统由称重电控单元和电脑组成,在电脑系统内设置定量吨数,称重电控单
元在车辆装料到了荷载的吨位之后,系统自动断电,关闭下料口。
保存数据,车辆下磅,
完成一次自动装车。
3、系统软件
系统软件由软件以及服务器组成,企业工作人员通过控制软件定量设置吨数,该软件
简洁容易操作,用户容易上手。
如果您有实际的采购需求,欢迎致电联系江苏呈祥智能科技有限公司。
我们可以结合
您的实际需求来进行定制开发。
江苏呈祥智能科技有限公司,是一家以科技创造未来,智能定义世界为宗旨,面向钢铁行业、建材行业、电力行业、矿山、垃圾环保、公路治超、海关港口、
物流领域、大宗物资、智慧工地等行业的称重智能化和信息化的解决方案提供商,以及称重集中管控平台的系统集成商。
感谢您的阅读,祝您生活愉快。
ZCY60R煤矿用侧卸式装岩机使用说明书

ZCY60R煤矿用侧卸式装岩机使用说明书一、设备用途及工作环境该设备主要用于全岩巷道及半煤岩巷道短距离装载作业,用于岩石、煤及其它物料的装运。
二、主要组成部分该设备以电机为动力,液压马达驱动履带行走、液压油缸操作翻斗的全液压侧卸式装载设备。
1 工作机构、2 液压系统、3 机架体、4 履带行走部分、5 冷却系统、6 电气系统等部分组成,见图 1。
1、工作机构:工作机构由翻斗、翻斗座、翻斗臂、翻斗油缸、升降油缸、侧翻油缸等组成(见图 2)当翻斗油缸活塞杆收缩、翻斗翻转后与翻斗臂、支架间形成平行机构,此时升降,翻斗不会前倾或后仰。
操作侧翻油缸可使翻斗向一侧倾斜,达到卸载的目的。
翻斗通过销轴与翻斗座铰接,翻斗座与翻斗臂靠销轴连接。
翻斗臂上部与机架铰接。
翻斗前部铲板为耐磨钢板,可用于装载磨蚀性很高的物料,如硬砂岩等。
通过调换翻斗与侧翻油缸销轴的位置及翻斗挡板和料口的相互位置,可实现左右方向侧翻的调换。
2、液压系统:液压系统由电动机、三联泵、左右履带行走马达、液压油缸、操纵阀、主副油箱及其附件等组成开式系统。
左右履带行走马达各自由三联泵中的两联定量齿轮泵单独供油,压力约为16MPa。
工作机构的液压油缸由三联泵中余下的一联定量齿轮泵单独供油,压力约为16MPa。
履带行走马达回路中,高压油经泵、换向阀、分别到达左、右履带行走马达,驱动设备前进或后退。
回油经换向阀、滤油器回到油箱,左右马达泄油口直接通主油箱。
工作机构液压回路中,高压油经换向阀分别到达翻斗油缸、升降油缸和侧翻油缸,回油经换向阀、滤油器回副油箱。
主副油箱之间由软管相连,系统的压力由换向阀上的进油口一侧的安全溢流阀调节螺钉调定,出厂时已经调定,用户一般无需再调。
工作机构换向阀的中位可以临时封油,即操纵手柄在中位时,油缸可暂时相对固定不动。
但在任何时候都不得利用中位临时封油的特点作为安全固定斗臂的措施。
如果需要在翻斗工作机构下部检修时,必须首先用枕木将翻斗和翻斗臂垫实。
煤炭自动装车控制系统设计分析-系统设计论文-设计论文

煤炭自动装车控制系统设计分析-系统设计论文-设计论文——文章均为WORD文档,下载后可直接编辑使用亦可打印——[摘要]针对目前煤炭人工控制装车,自动化水平较低且易造成装载量不合理的现状,设计一套以PLC为控制核心的煤炭自动装车控制系统,并利用工控机作为上层监控核心设备。
系统可实现无人干预下的自动装煤,且可实现装载量恒定,有效解决目前装车中超载以及亏载的问题。
应用测试表明,系统具有自动化控制、可靠性高、安全经济的优势,可为企业增加可观的经济效益。
[关键词]煤矿;装车;控制系统;自动化;PLC引言煤炭作为我国的基础能源,在我国能源结构中占有举足轻重的位置[1-2]。
我国的煤炭资源分布并不均匀,煤炭需要由原产地煤场运输到全国各地加以利用。
因此,煤炭的装载运输就成为较为重要的一环[3]。
但是,目前煤矿煤场装车主要是人工干预下的半自动化控制,时常造成装载量超载或者亏载的现象,造成很大的人力物力的浪费,给企业带来了很大的经济损失。
本文针对这种现状,提出开发一种基于PLC控制并利用上位机进行监控的煤炭自动化装车控制系统。
该系统可实现自动控制装车,根据实际情况调整控制装煤流量以及装煤量,有效实现准确装煤,减少工人工作量,同时保障装车工作安全,提升自动化水平,切实为企业增加经济效益。
1总体方案简介目前煤矿煤炭装车多采用人工控制的半自动化方式,利用称重系统边称重,边人工调整,装车人员依靠经验,时常造成装载量不准确且效率低,因此,自动化定量装煤控制系统成为迫切需求[4]。
本文所设计的煤炭自动装车控制系统主要由传感器检测模块、网络通讯模块、控制模块、执行模块以及上位机监控模块组成。
该系统简要工作过程为:当运煤车进入煤仓下方稳定后,系统通过重量、位移等传感器模块采集检测车辆信息,反馈给程序控制器,在确认车辆后,启动给煤设备以及输送设备,变频器可根据给煤总量调整给煤机给煤速率,并通过皮带秤对给煤量称重后进入运煤车,检测设备实时监测装煤量以及车厢质量直至达到设定量,系统停止给煤机输送机,实现自动化定量装煤控制。
泰安煤机公司研制成功新型汽车、火车两用煤炭装车系统

各县 市上报 的2 0 0 9年度 重点领域 首台( 技术装备项 目进行 了审核认 定, 将符合重点 领域首 台( ) 套) 并 套 条件 的技 术装备及
企 业 名 单 予 以公 布 , 省 上榜 的技 术 装 备 及 企 业 共 9 全 5家 , 莱芜 煤 机 公 司是 莱 芜 市唯 一 的一 家 。 X z 3 O 20 U 型 厢 式 隔膜 压 滤 机 是 莱 芜煤 机 公 司 自行设 计 制 造 的 一 种 新 型 、 自动 控 制 、 效 、 产 能 压 滤 机 , M G 4 / 0 0一 全 高 高 综 合 吸 收 国 内外 先 进 技 术 , 用 国家 相 关 标 准 设 计 制 造 , 用 多 油缸 压 紧 、 端 入 料 、 膜 压 榨 、 齿 链 分 段 开 框 、 成 叠加 式 采 采 双 隔 销 集
液压 系统 、L P C可编程序控制及 触敏屏等 多项技 术 , 实现压 滤机 的全 自动 闭路循环 , 具有 效率 高、 能耗 少、 滤饼 水分低 的特
点 。主 要 规 格 有 6 4 5 适 用 于煤 炭 、 工 、 0~ 2 m , 化 冶金 、 纸 、 金 属 矿 及 食 品 、 造 非 医药 等 行 业 的 固液 分 离 , 别适 用 于 浮选 精 煤 、 特
X MZG3 0 2 0 4 / O 0一U 型 厢 式 隔膜 压 滤 机 被 评 为
20 0 9年度 “ 山东 省 重 点领 域 首 台 ( ) 术 装 备 " 套 技
近 日, 东省 经 济 和 信 息 化 委 员会 、 东省 财 政 厅 联 合 公 布 了 20 山 山 09年 度 山 东 省 重 点 领 域 首 台 ( ) 术 装 备 及 企 业 名 套 技
求 面梁设计 为标准 的热轧 H型钢 , 在 将 在保证 强度 满足 的基 础上 , 充分考虑 了
装车站操作规程

装车站操作流程山东煤矿泰安机械厂装车站操作流程第一步:开计算机第二步:开油泵,冷却泵、风冷却器可在画面中打到自动位置第三步:操作台选择方式选择在“自动”第四步:选择所需要的缓冲仓配料闸板(缓冲仓的闸板可以停止使用一部分,以保证减少缓冲仓落煤时对称重传感器的冲击。
),选择1#或3#闸板的中位以保证闸板在自动配料时可精确配重。
第五步:点击主画面中的‘装车输入’按钮,进入装车输入画面,先点击‘新车次’,后点击‘保存当前车次’,再点击‘信息检查’进入车辆信息显示画面,最后返回至主画面。
第六步:在计算机桌面双击打开“装车站报表系统”,菜单栏选择“手动装车”,然后单击“新建”,“增加车厢”至列车的实际车厢总数,然后单击“开始装车”直至出现“等待火车到达”信息(此时“开始装车”变为“装车完成”,等待火车装完以后,点击“装车完成”按钮,手动输入“车厢编号”“车厢型号”“车厢流向”“车次”“流向”“请完时间”“对位时间”“装车时间”“装完时间”等)。
第七步:火车通过装车站控制室后,调节操作台上的“溜槽”按钮,使装车溜槽下降到适当的位置。
第八步:在电脑画面上点击称重方式选择,选择自动称重或仪表称重。
自动称重时,提前输入下一节车厢的额定重量输入,输入数量后点击回车确认。
仪表称重时,可在仪表上输入三个门槛的重量。
第九步:将操作台“启/停”旋转开关打到“启”的位置,缓冲仓闸板打开,系统自动向定量仓装煤,当达到仪表设定门槛1时,系统关闭1、2、3、4号闸板的左闸板,当达到仪表设定门槛2时,系统关闭2、4号闸板的右闸板,且关闭4号右闸板或4号左闸板的一半,当达到仪表设定门槛3时,系统全部关闭4号左闸板或4号右闸板。
配煤完毕。
(仪表设定值可根据用户的要求来进行选择,如装60T的列车时,可将门槛1设定为50T,门槛2设定为55T,门槛3设定为60T)故障处理:如发现定量仓闸板没关闭,用操作台“装车闸门关”关闭闸门。
(如夹煤,定量仓闸板没关闭,系统不自动配煤,用操作台“装车循环”关闭闸门,系统会自动配煤)。
潘二煤矿装火车自动采样机系统偏倚原因分析及解决方案

潘二煤矿装火车自动采样机系统偏倚原因分析及解决方案摘要:针对潘二煤矿装火车自动采样机存在系统偏倚,文章从煤炭储装运环节入手,分析了煤炭在储装运过程中产生粒度离析,对采制样精准度造成影响,形成系统偏倚。
通过试验调整自动采样机控制程序及参数设置,彻底消除了装火车自动采样系统的偏倚问题。
关键词:粒度离析;自动采样机;系统偏倚;数据分析潘二煤矿商品煤外运铁路运输装车方式为双股道(一道、二道)同时经过皮带装车。
矿井生产的原煤直接通过火车或汽车外运至其它地点洗选精煤,煤炭采样经过两套采样机进行采制样,一套为原煤皮带中部采样机,一套为装火车皮带中部自动采样机,自装火车采样机使用之后,我们通过数据统计发现,装火车采样月度累计灰分与原煤采样月度累计灰分存在正向偏差。
经过系统分析和试验得出结论为原煤在进入装火车储煤仓时存在粒度离析不均,造成两架装车皮带煤炭灰分存在正向偏差,而装火车皮带中部采样机在两架皮带采样参数设置存在系统偏倚,使火车采样灰分统计高于原煤采样灰分。
1 矿井生产煤炭粒度筛分浮沉试验筛分前煤样总重:854.4 kg,原煤筛分试验结果见表1,浮沉试验结果见表2。
由表1可知,潘二矿原煤灰分随着粒度的减小逐渐降低,粒度分布不均,6 mm 以上粒级产率为60.52%;由表2可知,密度大于1.8 g/cm3的灰分85.39%,产率46.61%,说明此次试验用煤矸石含量较高,且多分布于粒度大于6 mm粒级上,符合潘二煤矿复杂地质条件下回采上来的原煤特点。
由表2可知,煤泥产率1.54%,灰分为47.49%;总计产率100.00%,灰分52.71%。
2 煤炭进仓粒度离析情况2.1 胶带输送机运输过程发生粒度离析现象煤炭入仓采用拉上山胶带输送机运输和水平电滚筒皮带转载进仓,胶带输送机在机头驱动滚筒带动下,胶带在支架和众多托辊上运动以完成物料的运输。
由于托辊是按一定间隔架设的,且倾斜安装,煤炭随着胶带上下震动,在震动过程中煤炭产生一定的离析现象。
井下物料、设备装车的规定

井下物料、设备装车的规定引言:井下物料和设备的装车对于矿山生产起着至关重要的作用。
正确的装车流程和规定,不仅能保障井下作业安全,还能提高矿山生产效率和质量。
本文将针对井下物料和设备装车的规定进行详细阐述,介绍井下装车的流程、安全措施和注意事项,以提供参考。
一、装车前的准备工作1.装车计划编制在进行装车操作之前,需要制定详细的装车计划。
这包括装车时间、装车位置、装车数量以及装车顺序等信息。
装车计划应根据实际情况合理安排,确保装车作业的顺利进行。
2.装车现场准备装车现场的准备工作主要包括清理、清扫和检查。
装车前需要清理装车位置和周围环境,确保无障碍物和杂物。
同时,需要对装车设备进行检查,确保其正常运转,以避免在装车过程中出现故障。
二、装车操作流程1.物料和设备准备装车前需要将所需的物料和设备准备齐全,包括但不限于矿石、煤炭、矿泉水、电缆、防爆灯等。
物料和设备在装车前应做好分类和标记,以便于装车时的取用和管理。
2.装车顺序规定根据装车计划,确定装车的顺序。
一般情况下,应按照装车的优先级进行操作,确保优先装车的物料和设备能够及时投入生产和使用。
3.装车操作要求(1)严格按照装车计划进行装车,不得擅自更改装车顺序。
(2)装车时需要检查物料和设备的质量和数量,确保符合要求。
(3)装车操作过程中要关注安全事项,遵循矿山安全规定。
(4)装车完成后,需核对装车数量,并进行记录和报告。
三、井下装车的安全措施井下装车作业是一项高风险的作业,需要采取一系列的安全措施,保障工作人员的安全。
1.人员安全(1)装车人员需经过专业培训,具备装车操作技能和相关知识。
(2)装车人员应穿戴符合要求的工作服和安全装备,如安全帽、防护眼镜、防护服等。
(3)装车人员需遵守井下作业规定,确保自身的安全。
(4)装车现场需设置标志和警示牌,提醒他人注意装车操作。
2.设备安全(1)装车设备应定期检修和维护,确保其正常运转。
(2)装车设备的操作人员应经过相关培训,具备操作技能和安全意识。
煤矿专用线火车装车系统的改造优化

煤矿专用线火车装车系统的改造优化摘要:煤矿专用线火车装车系统是一种将散装物料按照规定的质量快速且连续的称量并将其装入到列车车厢系统,具有一次称量装载,和速度快、精度高的特点。
目前被很多煤矿企业广泛应用。
但是由于受到铁路技术水平以及检测技术的影响,我国现有的煤矿火车装车系统依旧没有得到很好地改造。
但是随着我国建设进程的加快以及科学技术水平的提高,传统的煤矿专用线火车装车系统已经无法满足现代化煤矿企业对装车系统的要求,这也就需要相关的工作人员考虑煤矿专用线火车系统的特殊性,并考虑工作环境和噪音的影响,然后对煤矿专用先火车装车系统进行改造,以帮助火车完成煤矿运输任务,并改善煤矿火车的工作环境,提高装车效率。
关键词:煤矿专用线;火车;装车系统;改造优化随着近些年来我国工业化和煤矿现代化程度的提高,煤炭的生产得到了很大的发展的同时,煤矿专用线火车的装车系统的工作任务量也在一定程度上增加了许多。
过去的时间里,煤矿专用线火车大多采用皮带机或者人工方式装车,这样的装车方法不仅效率低,而且误差也大,无法满足现代化的社会发展要求。
所以,对煤矿专用先火车装车系统进行改造优化是非常有必要的。
1、原煤矿专用线火车装车系统的分析为了更好地改造和优化煤矿专用线火车的装车系统,达到快速装车的目的,这也就需要对原煤矿专用线火车装车系统进行分析,以便于找到原煤矿专用线火车装车系统存在的不足之处。
1.1火车装车系统的溜槽口设计存在不足之处原火车煤矿专用线火车的装车系统溜槽口有梯形设计口,以为达到更好的装车效果和装车效率。
另外,梯形设计口两旁各有一个观察口,便于在装到车辆最末端时观察溜槽下煤量。
虽然这种设计在前期充分考虑了装车的多种因素,但是在实际的装车过车中,原煤矿专用线火车装车的溜槽口不仅会导致火车列车车厢内留下较大的梯形空隙,同时堆煤现象还会使煤矿质量发生非常频繁的煤质变化,严重影响装车效率[1]。
1.2缺少平煤作业平台根据上文可知,原煤矿专用线火车不仅存在堆煤现象,而且火车列车车厢也留存非常大的空隙等问题。
全自动汽车装车系统的设计与开发

全自动汽车装车系统的设计与开发
徐明;徐孝飞;赵九州;李健
【期刊名称】《中国机械》
【年(卷),期】2014(000)006
【摘要】为了提高当前国内汽车装车系统的自动化水平,解决人工操作速度慢、容易超偏载等常见缺陷,着重从煤矿运输环节入手,重点研究实现全自动汽车装车的关键问题,如远程数据终端(RDT)、RFID识别器、溜槽自动升降等,通过引入现代电子技术、检测技术和计算机信息处理技术,制定相应的解决方案。
仿真试验和现场应用表明,系统具有较强的适用性,无论对于旧装车系统的改造还是新装车系统的开发,实现全自动装车系统均是可行的。
【总页数】1页(P66-66)
【作者】徐明;徐孝飞;赵九州;李健
【作者单位】山东泰安煤矿机械有限公司;山东泰安煤矿机械有限公司;山东泰安煤矿机械有限公司;山东泰安煤矿机械有限公司
【正文语种】中文
【相关文献】
1.全自动矿山铁路装车系统的设计与开发
2.吕临选煤厂全自动装车计量系统的设计与应用
3.连续式装车机全自动电气控制系统设计
4.全自动货运列车车号识别与自动称重数据记录系统的研发设计及在神东锦界装车站的应用
5.全自动移动式平料装车机控制系统设计
因版权原因,仅展示原文概要,查看原文内容请购买。
- 1、下载文档前请自行甄别文档内容的完整性,平台不提供额外的编辑、内容补充、找答案等附加服务。
- 2、"仅部分预览"的文档,不可在线预览部分如存在完整性等问题,可反馈申请退款(可完整预览的文档不适用该条件!)。
- 3、如文档侵犯您的权益,请联系客服反馈,我们会尽快为您处理(人工客服工作时间:9:00-18:30)。
煤矿自动装车系统
0 引言
铁路快速装车系统是一种将散装物料按规定的质量快速连续的称量并装入列车车厢的系统,具有一次称量、一次装载、速度快、精度高等特点。
当前在大型煤矿、非煤矿山等企业使用已经非常广泛,但由于受铁路技术水平及检测技术的影响,我国现有装车系统至今没有一家实现全自动控制。
某些环节仍然停留在手动、半自动装车的水平。
我国煤矿的重车称量是与装车同步进行,一种方式是轨道衡置于跨线煤仓仓口或胶带输送机卸料口下方,边装车边称量,通过称量控制装车;另一种方式是跨线多煤口装车线,轨道衡置于跨线煤仓出口,人工预装车后称量,多退少补,往返儿次才能达到准确装车。
随着电了称重业的发展,日前国外己采用大型定量仓快速装车系统,预先在定量仓中按车皮标重自动预装仓,待列车车厢行进经过定量仓仓口时,自动按车厢标重装车,实现快速、准确装车。
快速定量装车系统主要由输煤系统、定量装车机械设备、三级自动取样系统设备、液压控制系统、电脑监控系统等组成。
1 快速定量装车系统功能设计
快速定量装车系统通过计算机采集主上煤带式给料机、主上煤带式输送机及各种现场设备的信号,处理接收操作指令后发出正确的控制指令,实现自动连续调节给料、定量自动装车、二级取样、清单打印、动态图面显示等功能。
1.1 装车
操作者选定与机车(或调车绞车)的速度、车型相适应的给料量后,被选择的给料机给料,给料量随时由输送带秤(核了秤)反映出来,在计算机内部与设定的给料量比较,从而调节给料机给料量,两者协调一致,确保了装车的连续和稳定值,保证了连续自动调节给料。
当列车到装车塔下时,由系统控制放下装车溜槽,此时缓冲仓料位己到合适的位置。
操作者按下称重循环按钮后,缓冲仓下的4个配料液压平板闸门自动地向定量仓中卸料,同时称重传感器准确地称重、控制完成定量配料。
其后,由闸门控制向车厢中放料,料量放足后由称重传感器控制排料平板闸门关闭。
而后车辆行驶车厢之间的空档距离,这期间缓冲仓又向定量仓继续配料,为下一车厢装车作准备,从而实现连续定量自动装车。
1. 2取样
系统的二级取样与快速定量装车系统协调工作,在装车的同时实现煤炭的采样、缩分、破碎、再缩分与装罐工序(图1)。
第一级取样机全截面比例截取主上煤输送带上的物料作为样品,通过一级给料机将样品送至第一级取样机进行取样,通过一级给料机送入样品破碎机,将样品破碎至预定尺寸,再送至第二级取样机获取最终样品装入样品容器。
一级、二级所取样品的余量通过相应溜槽返回到缓冲仓。
二级取样的样品余量,每隔1个车厢或2个车厢,经过相应溜槽、螺旋输送机及回料液压平板闸门回到定量仓1次。
1. 3打印
装车前先把车皮号、标号和车皮质量输入计算机。
当某个车厢装料完成后,计算机立即给出该车厢的车号、净质量、皮质量、毛质量、累计质量、装车时间等一系列数据,并把需要的装车清单打印出来。
直到最后一节车厢,计算机才让装车程序停止,并自动打出整列车
的总料质量。
1. 4监控
装车时,计算机将显示所有设备的运行状态,如给料机的起停、带式输送机运行状态、缓冲仓煤位变化、各闸门开关状态、二级取样系统各设备的运行状况、定量仓煤量变化等,便于监控整个装车过程。
2.快速定量装车系统的应用
2.1 在太原选煤厂的应用
太原选煤厂经过设备选型,通过考察论证,选用快速定量装车系统取代了原有手动装车系统,控制系统采用的是美国Rockwell公司Contra Logix系统系列的PLC对设备进行控制,并于2005年对该装车系统进行了改造。
快速定量装车系统采用一个定量仓和几个运输系统组成。
运输系统(8, 10道)通过轮叶给煤机向下输送精煤,然后经过皮带运输机417, 418或者419,421, 418到达快速定量仓内,该装置称重采用4个传感器支撑,该系统采用ZIP快速定量装车控制系统,
2.1.1快速定量装车系统综述
Contro Logix是一种被称为混合控制系统的新概念控制器,为DCS系统提供了解决方案,网络组态软件RS NebvorX允许对ControNet网上的任一模块或框架或控制站进行组态,对模块的组态达到点级。
2.2.2快速定量装车系统的组成
ZIP快速定量装车控制系统由以下部分组成: PLC柜,MCC柜、操作台、现场操作箱、
上位机及打印机现场仪表。
称量仓的煤量是由拉姆齐M T2000静态重量指示仪来测量并通过通讯接口发给PLC控制系统,由PLC来控制缓冲仓的4个闸板。
操作员在控制室通过微机可了解列车的装车情况并进行相关的操作,也可通过操作台对列车进行加煤。
现场操作箱主要是用户检修时可在现场操作设备。
2.2 潞宁煤业公司的自动装车系统
为了解决车辆装载过程中的超载、欠载问题,潞宁煤业公司与山西联通电子信息有限公司共同开发出了一套高效、准确实用的筒仓自动装车网络系统。
2.2.1系统构成及原理
自动装车系统主要由输送机、测量单元(含测速和测重单元)、控制仪表、电气装置、刷卡系统、网络系统(光纤、光端机、交换机等)、大屏幕显示器、计算机等构成。
装煤车辆进厂时通过磅房发卡给车主,同时系统将与该卡对应的相关信息(如合同号、限载值,车号、单位等)存储于和自动装车系统联网的服务器,此后车辆称皮重,并保存与之对应的数据至服务器,当该车到达指定装车位置时刷卡,装车计算机系统根据卡号从服务器读取相关信息,并计算出装车量,通过网络传送给智能仪表,同时将相关信息(如合同号、限载值,车号、单位等)显示到大屏慕显示器,工作人员开启定量给料设备开始装车。
在装车过程中测量单元把采集到的流量信号实时反馈给控制仪表,当实际下料量达到车辆额定载荷时,控制仪表输出自动停车信号,系统自动停车,避免了人工装车过程中可能出现的超载或欠载,从而达到了自动定量装车的日的。
系统配备装车数据修正功能,当装车量与过磅量出现误差时,授权工作人员可根据误差量输入校正值,无需经常进行停车调零和标定,大大提高工作效率。
为保证装车的可靠性,系统设计双重控制方案,如计算机系统出现故障时,该系统可从智能仪表手动输入装车量,同样可以达到定量装车的效果。
对于定量给料控制系统,控制器通过实际测量值与日标量进行比较,达到日标量时,输出控制信号至相应的控制设备,从而停止设备,同时进入下一个循环等待状态。
图3:系统组成
2.3煤科总院北京高新技术开发中心研究的不同装车系统中的装车过程自动化2.
3.1 采用煤矿装车增补技术实现跨线多煤口装车线装车过程自动化
系统工作原理:联挂列车由调车绞车牵引,通过大型储煤仓按体积预装车,装车量控制在额定装载的95%,列车后的车厢依次经过电了轨道衡,自动称得重量后,由微机系统自动
去皮得到实际装车量和欠装量,同时将欠装量信号传给位于电了轨道衡上方的煤量自载增补系统;在重车继续行进通过增补系统时,微机控制增补系统定量仓卸料闸门自动开启,以向该车厢按实际欠装量补煤,补煤后装车准确度优于0. 5 % ,符合铁路运输要求,整车称量精度优于GB/ T17167《企业能源计量器具配备和竹理导则》规定的0. 3%的要求;最后自动打印输出单节车厢报表和整列车的实际装车量。
图4:装车工艺流程示意图
2.3.2采用煤矿用微机电子轨道衡实现单点装车系统装车过程自动化
系统原理:联挂列车车厢依次进入煤仓下,当计算机判别到第1节车厢到位时,发出控制信号,启动给定煤仓下带式输送机和给料机,通过胶带秤检测煤流流量,自动控制列车调车绞车运行速度,保证列车通过卸料口时,能按确定输煤量准确装车。
胶带机输送的煤经双向溜槽后日进入车厢,通过车厢轨轮上轨道衡台面位置的逻辑判别,达到预定要求后,自动改换双向溜槽到前溜槽口装车。
当本车厢第4个轨轮上轨道衡台面后,定重控制双向溜槽向后一节车厢卸煤(第2节车厢),使列车顺利通过车节,同时自动称重计量,记录该车毛重。
依此类推。
当装最后一节车厢时,按预设时间提前关闭给料机,待最后一节车厢第4轮上台面后,定重或定时关闭带式输送机,并收回溜煤槽,等待下一次装车。
最后,通过统计报表软件将称量结果按序打印,并累积。
图5:煤矿单点装车自动装载与计量管理系统结构示意图
2.3.3 采用大型定量仓快速装车系统实现快速准确装车
系统原理:大型定量仓快速装车系统是基于大型定量料斗秤的工作原理。
首先,通过给料机和带式输送机经缓冲仓向定量仓按车厢标重预装煤,当达到车厢标重后,关闭缓冲仓闸门;等待行进车厢到位后,打开定量仓闸门进行煤炭定量装车,通过卸料溜槽控制装车速度,使装载过程不受行车速度影响。
卸空后,关闭定量仓闸门,按下节车厢标重重新预装载。
整套系统由可编程序控制器控制输煤系统预装载、定量控制和向车皮中卸载。
图6:煤矿大型定量仓快速定重装车系统结构示意图
2.3.4 自动化装配煤系统在高庄煤矿的研究与应用
系统原理:如图7所示,该系统共有8个精煤仓,由8台给煤机给煤,分别为由1~8号电机控制;另外有4个原煤仓,由4台给煤机给煤,分别为由9~13号电机控制。
煤通过给煤皮带运输到缓冲仓经卸料口进行装车,皮带有1台电机带动,即13号电机。
由15~17号电机控制卸料口的翻转,以及由14号电机控制铁牛牵引的运作。
图7:装车系统图
控制室中的“全自动定量装煤控制系统”主要采用Windows XP以上操作系统,由西门了视窗控制中心SIMATIC WinCC和STEP7编程软件实现远程监控。
图8:装车的控制系统结构图。