锌合金压铸件出现气泡的原因
镀锌合金产品起泡故障解决方案

镀锌合金产品起泡故障解决方案锌合金由于成型方便,可塑性强,成本低,加工效率高,广泛应用在卫浴,箱包,鞋服辅料中,但锌合金的起泡问题(电镀;喷涂)却一直困恼着五金厂与电镀厂的朋友.今天我们乐将把汇总服务过的多家五金厂电镀厂针就锌合金起泡的经验编集,具体有以下几个方面:1.锌合金产品设计之始,就要考虑到模具的进料口与排渣口与排气设置。
因为进料与排渣的工件流道顺畅不裹气,不产生水渍纹,无暗泡,直接影响后道电镀是否起泡,合格进料与排渣模具压铸出工件,表面光洁,白亮,无水渍纹。
2.模具开发中也要考虑装模机台的吨位,压力,我们就亲身经历一个锌合金电镀后起泡百份20-30事件。
一五金厂朋友接一几百万大单,模具开一出8件,压力不足,排气不佳,不论电镀前处理如何解决总有20-30%起泡,最后将模具堵了4件,改成一模出4 件,再镀就无一起泡。
3.前处理表面的滚光液,抛光膏,氧化层没处理干净,常有出现滚光,滚抛后的工件,表面光亮;许多电镀厂酸洗工序的员工就随便酸洗下,导至表面附着的滚光剂没洗净,常常出现起泡现象。
另滚光滚抛厂所选用的滚光剂关系也很大,有些滚光剂中的表面活性剂极难洗去。
4.产品进碱铜(很多做五金朋友俗称的铜底)镀槽前工件表面仍有氧化膜(酸洗的膜)除蜡、除油的膜未处理净的黑膜。
所以脱膜很关健,早些年还能使用防染盐脱去,现环保不让排放含防染盐的废水,建议使用LJ-D009脱膜粉,效果优过防染盐,又能退镍层并且COD排放符合国际标准5.碱铜镀槽有机物,杂质多,游离氰不在范围,化验碱铜缸成份,看是否氰化钠偏低或氢氧化钠偏高!如添加光剂的小心光亮剂偏高,碱铜缸的清洁很关健,建议3-5天碳处理一次6.碱铜缸的导电也很重要,阳极是否溶解正常,阳极铜板是否充足都会导至起泡7.锌合金产品烘箱里出来后起泡;可能是烘箱温度不均匀导致即温度过高.由于压铸的时候不紧密,导致锌合金水渍纹沙眼里容易进酸,酸与锌在即使有表面镀层的情况下依然会发生化学反应,产生大量的氢气H当里面的气压高过大气压一定的程度时加上高温即会产生气泡.最后告诉大家一个好消息,通过大家一如既往的积极参与,热心支持,我们“电镀资讯”微信平台的会员将马上突破5000人,这4966人都是来自全国各地的五金电镀同行,还有来自新疆,台湾的,今后有什么问题将能更全面一起讨论解决,谢谢大家!赠人玫瑰,手有余香,如果你有奋斗在电镀行业的亲人;朋友;同事,请分享给他们,也许此刻他正为这一问题烦脑。
常见压铸件缺陷解决方法
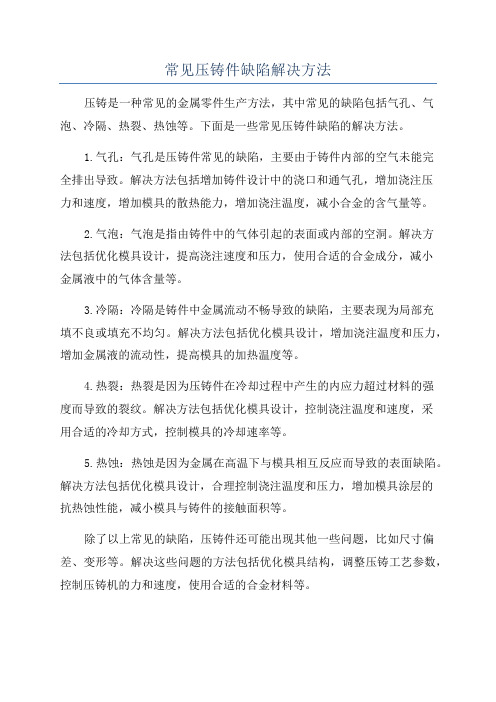
常见压铸件缺陷解决方法
压铸是一种常见的金属零件生产方法,其中常见的缺陷包括气孔、气泡、冷隔、热裂、热蚀等。
下面是一些常见压铸件缺陷的解决方法。
1.气孔:气孔是压铸件常见的缺陷,主要由于铸件内部的空气未能完
全排出导致。
解决方法包括增加铸件设计中的浇口和通气孔,增加浇注压
力和速度,增加模具的散热能力,增加浇注温度,减小合金的含气量等。
2.气泡:气泡是指由铸件中的气体引起的表面或内部的空洞。
解决方
法包括优化模具设计,提高浇注速度和压力,使用合适的合金成分,减小
金属液中的气体含量等。
3.冷隔:冷隔是铸件中金属流动不畅导致的缺陷,主要表现为局部充
填不良或填充不均匀。
解决方法包括优化模具设计,增加浇注温度和压力,增加金属液的流动性,提高模具的加热温度等。
4.热裂:热裂是因为压铸件在冷却过程中产生的内应力超过材料的强
度而导致的裂纹。
解决方法包括优化模具设计,控制浇注温度和速度,采
用合适的冷却方式,控制模具的冷却速率等。
5.热蚀:热蚀是因为金属在高温下与模具相互反应而导致的表面缺陷。
解决方法包括优化模具设计,合理控制浇注温度和压力,增加模具涂层的
抗热蚀性能,减小模具与铸件的接触面积等。
除了以上常见的缺陷,压铸件还可能出现其他一些问题,比如尺寸偏差、变形等。
解决这些问题的方法包括优化模具结构,调整压铸工艺参数,控制压铸机的力和速度,使用合适的合金材料等。
总的来说,解决压铸件缺陷的方法需要综合考虑材料、模具设计、工艺参数等多个因素,通过不断的实验和改进来提高铸件的质量。
锌合金电镀起泡的原因

锌合金压铸件起泡缺陷分析锌合金压铸件目前广泛应用于各种装饰方面,如领带夹、皮带扣、各种金属饰扣等,因而对铸件表面质量要求高,并要求有良好的表面处理性能。
而锌合金压铸件最常见的缺陷是表面起泡。
铸件表面在以下情况下有鼓起的包称之为起泡,是铸件内缺陷的外部表现。
(1)压铸出来就发现。
(2)抛光或加工后显露出来。
(3)喷漆或电镀后出现。
(4)放置一段时间后发现。
产生原因1.孔洞引起:主要是气孔和收缩机制,气孔往往是圆形,而收缩多数是不规则形。
气孔产生原因:a 金属液在充型、凝固过程中,由于气体侵入,导致铸件表面或内部产生孔洞。
b 涂料挥发出来的气体侵入。
c 合金液含气量过高,凝固时析出。
当型腔中的气体、涂料挥发出的气体、合金凝固析出的气体,在模具排气不良时,最终留在铸件中形成的气孔。
缩孔产生原因:a 金属液凝固过程中,由于体积缩小或最后凝固部位得不到金属液补缩,而产生缩孔。
b 厚薄不均的铸件或铸件局部过热,造成某一部位凝固慢,体积收缩时表面形成凹位。
由于气孔和缩孔的存在,使压铸件在进行表面处理时,孔洞可能会进入水,当喷漆和电镀后进行烘烤时,孔洞内气体受热膨胀;或孔洞内水会变蒸气,体积膨胀,因而导致铸件表面起泡。
模具行业门户网站2.晶间腐蚀引起:锌合金成分中有害杂质:铅、镉、锡会聚集在晶粒交界处导致晶间腐蚀,金属基体因晶间腐蚀而破碎,而电镀加速了这一祸害,受晶间腐蚀的部位会膨胀而将镀层顶起,造成铸件表面起泡。
特别是在潮湿环境下晶间腐蚀会使铸件变形、开裂、甚至破碎。
3.裂纹引起:水纹、冷隔纹、热裂纹。
水纹、冷隔纹:金属液在充型过程中,先进入的金属液接触型壁过早凝固,后进入金属液不能和已凝固金属层熔合为一体,在铸件表面对接处形成叠纹,出现条状缺陷,见图2。
水纹一般是在铸件表面浅层;而冷隔纹有可能渗入到铸件内部。
热裂纹:a 当铸件厚薄不均,凝固过程产生应力;b 过早顶出,金属强度不够;c顶出时受力不均;d 过高的模温使晶粒粗大;e 有害杂质存在。
压铸件气泡产生的原因和解决办法

压铸件气泡产生的原因和解决办法压铸件气泡产生的原因和解决办法锌合金压铸件表面经常出现大小不等的气泡,请问原因是什么,该如何解决?解决压铸件气孔的办法:先分析出是什么原因导致的气孔,再来取相应的措施。
(1)干燥、干净的合金料。
(2)控制熔炼温度,避免过热,进行除气处理。
(3)合理选择压铸工艺参数,特别是压射速度。
调整高速切换起点。
(4)顺序填充有利于型腔气体排出,直浇道和横浇道有足够的长度(>50mm),以利于合金液平稳流动和气体有机会排出。
可改变浇口厚度、浇口方向、在形成气孔的位置设置溢流槽、排气槽。
溢流品截面积总和不能小于内浇口截面积总和的60%,否则排渣效果差。
(5)选择性能好的涂料及控制喷涂量。
-------------------压铸件气孔分析-------------------压铸件缺陷中,出现最多的是气孔:气孔特征:有光滑的表面,表现形式可以在铸件表面、或皮下针孔、也可能在铸件内部。
(铸件壁内气孔)一般呈圆形或椭圆形,具有光滑的表面,一般是发亮的氧化皮,有时呈油黄色。
(表面气孔)气泡可通过喷砂发现,内部气孔气泡可通过X光透视或机械加工发现气孔气泡在X 光底片上呈黑色.<>气体来源(1)合金液析出气体—a与原材料有关 b与熔炼工艺有关(2)压铸过程中卷入气体?—a与压铸工艺参数有关 b与模具结构有关(3)脱模剂分解产生气体?—a与涂料本身特性有关 b与喷涂工艺有关<>原材料及熔炼过程产生气体分析铝液中的气体主要是氢,约占了气体总量的85%。
熔炼温度越高,氢在铝液中溶解度越高,但在固态铝中溶解度非常低,因此在凝固过程中,氢析出形成气孔。
氢的来源:(1)大气中水蒸气,金属液从潮湿空气中吸氢。
(2)原材料本身含氢量,合金锭表面潮湿,回炉料脏,油污。
(3)工具、熔剂潮湿。
<>压铸过程产生气体分析由于压室、浇注系统、型腔均与大气相通,而金属液是以高压、高速充填,如果不能实现有序、平稳的流动状态,金属液产生涡流,会把气体卷进去。
锌合金压铸件常见缺陷及处理方法

锌合金压铸件常见缺陷及处理方法锌合金压铸件目前广泛应用于各种装饰方面,如家具配件、建筑装饰、浴室配件、灯饰零件、玩具、领带夹、皮带扣、各种金属饰扣等,因此对铸件表面质量要求较高,同时要求有良好的表面处理性能。
缺陷表征:压铸件表面有突起小泡、压铸出来就发现、抛光或加工后显露出来、喷油或电镀后出现。
产生原因:1.孔洞引起:主要是气孔和收缩机制,气孔往往是圆形,而收缩多数是不规则形。
(1)气孔产生原因:a金属液在充型、凝固过程中,由于气体侵入,导致铸件表面或内部产生孔洞。
b涂料挥发出来的气体侵入。
c合金液含气量过高,凝固时析出。
当型腔中的气体、涂料挥发出的气体、合金凝固析出的气体,在模具排气不良时,最终留在铸件中形成的气孔。
(2)缩孔产生原因:a金属液凝固过程中,由于体积缩小或最后凝固部位得不到金属液补缩,而产生缩孔。
b厚薄不均的铸件或铸件局部过热,造成某一部位凝固慢,体积收缩时表面形成凹位。
由于气孔和缩孔的存在,使压铸件在进行表面处理时,孔洞可能会进入水,当喷漆和电镀后进行烘烤时,孔洞内气体受热膨胀;或孔洞内水会变蒸气,体积膨胀,因而导致铸件表面起泡。
2.晶间腐蚀引起:锌合金成分中有害杂质:铅、镉、锡会聚集在晶粒交界处导致晶间腐蚀,金属基体因晶间腐蚀而破碎,而电镀加速了这一祸害,受晶间腐蚀的部位会膨胀而将镀层顶起,造成铸件表面起泡。
特别是在潮湿环境下晶间腐蚀会使铸件变形、开裂、甚至破碎。
3.裂纹引起:水纹、冷隔纹、热裂纹。
水纹、冷隔纹:金属液在充型过程中,先进入的金属液接触型壁过早凝固,后进入金属液不能和已凝固金属层熔合为一体,在铸件表面对接处形成叠纹,出现条状缺陷。
水纹一般是在铸件表面浅层;而冷隔纹有可能渗入到铸件内部。
热裂纹:a当铸件厚薄不均,凝固过程产生应力;b过早顶出,金属强度不够;c顶出时受力不均d过高的模温使晶粒粗大;e有害杂质存在。
以上因素都有可能产生裂纹。
当压铸件存在水纹、冷隔纹、热裂纹,电镀时溶液会渗入到裂纹中,在烘烤时转化为蒸气,气压顶起电镀层形成起泡。
铸造气泡产生的原因
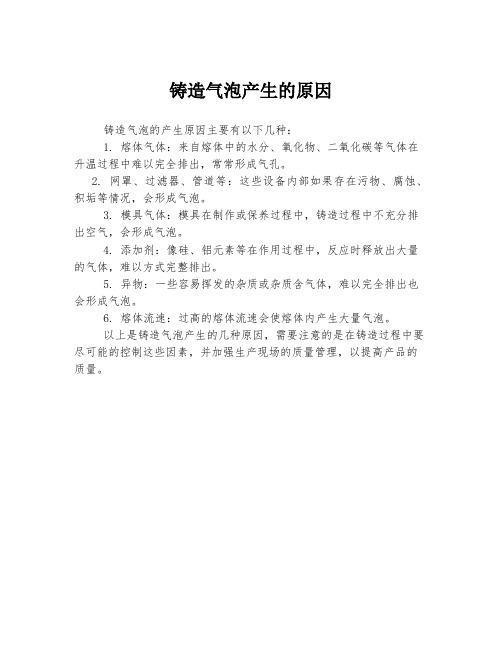
铸造气泡产生的原因
铸造气泡的产生原因主要有以下几种:
1. 熔体气体:来自熔体中的水分、氧化物、二氧化碳等气体在升温过程中难以完全排出,常常形成气孔。
2. 网罩、过滤器、管道等:这些设备内部如果存在污物、腐蚀、积垢等情况,会形成气泡。
3. 模具气体:模具在制作或保养过程中,铸造过程中不充分排出空气,会形成气泡。
4. 添加剂:像硅、铝元素等在作用过程中,反应时释放出大量的气体,难以方式完整排出。
5. 异物:一些容易挥发的杂质或杂质含气体,难以完全排出也会形成气泡。
6. 熔体流速:过高的熔体流速会使熔体内产生大量气泡。
以上是铸造气泡产生的几种原因,需要注意的是在铸造过程中要尽可能的控制这些因素,并加强生产现场的质量管理,以提高产品的质量。
锌合金压铸件水纹,水泡,抛光后有沙孔原因分析

首先要了解压铸的几大系统:1,压力系统,2,流通系统,3,冷却系统,溢流,排气等。
四:溢流槽,排气的作用是要把型腔里的气体,冷料,残留涂料等排出,所以制作溢流槽,排气口的地方一般都会在金属溢流动到最后的地方,否则铸件会出现水纹水泡,内部包气等。
一:选用的压铸机[压力系统]要根据铸件的重量,投影面积,及结构。压射力,流量决定了金属液进入型腔的速度,速度过小则水纹会产生。
二:流道设计对铸件的质量有很大的影响,主流道,分流道,横流道,内浇口之间的横截面积大小来决定了速度,横浇道的角度[决定了流向]如设计不当铸件容易产生水纹,水泡等缺陷。
三:冷却系统:模具型腔温度高低,左右了金属液速 度的快慢,金属液过慢则水纹易产生,同样熔炉温度射咀身温度过低也会产生度 420-435度之间,模温则要根据不同产品而定。
压铸常见缺陷、原因及改进措施

渗漏
水、
合金选择不当
提高比压 改进浇注系统 选用良好合金
排气不良
改进排气系统
二十四、 化学成分 不符合要
求
经化学分析,铸件合 金不符要求或杂质太
多
配料不正确 原材料及回炉料未加分析即行投入使用
炉料应经化学分析后才能配用
炉料应严格管理,新旧料要按一定比例 配用 严格遵守熔炼工艺,熔炼工具应刷涂料
编制:
涂料不纯或用量过多 涂料中石墨含量过多
充型过程中由于模具 填充时金属分散成密集液滴,高速撞击
十四、麻 面
温度或合金液温度过 低,在近似于欠压条 件下铸件表面形成的
型壁
细小麻点状分布区域 内浇口厚度偏小
涂料使用应薄而均匀,不能堆积,要用 压缩空气吹散
减少涂料中的石墨含量或选用无石墨水 基涂料
正确设计浇注系统,避免金属液产生喷 溅,改善排气条件,避免液流卷入过多 气体,降低内浇口速度并提高模具温度
合金收缩率大 内浇口截面积太小
比压偏低
模具温度过高
合理设计浇注系统,避免合金液直接冲 击型芯、型壁,适当降低填充速度
修正模具
打光表面,保证粗糙度符合要求 涂料使用薄而均匀,不能漏喷涂料
适当增加含铁量至0.8-1%
改善铸件结构,使壁厚稍为均匀,厚薄 相差较大的连接处应逐步缓和过渡,消 队热节
选择收缩率较小的合金
合金液过热或保温时间过长
合金不宜过热,避免合金长时间保温
二十二、 碎性
铸件基本金属粒过于 粗大或细小,使铸件
易断裂或碰碎
激烈过冷,结晶过细 铝合金中杂质锌、铁等含量太多
铝合金中含铜量超出规定范围
提高模具温度,降低浇注温度
严格控制合金化学成分
为什么锌合金电镀会起泡

一般是电镀出问题多,铜底打的太薄,电镀槽液又为酸性,锌合金穿过铜底反应产生氢气气泡,当时不是很严重,受热后更加严重
为什么铝合金和锌合金的压铸产品电镀后,存放一两个月后就会发黑或者表面起泡呢?谢谢!
没有电镀好,起始镀层和基体没有结合好,这里有前处理、浸锌、活化等环节没弄好
锌合金为什么比铝合金电镀性能要好
91 CN200620039439.6 一种自动镀锌系统的载具结构 本实用新型提供一种自动镀锌系统的载具结构,其主要是设有数悬吊架座,利用输送装置得操控悬吊架座的循环绕转,该悬吊架座下端衔设有一套筒,而在悬吊架座中段位置另设有一固定板,在固定板与下基板上分别置设有轴架,轴架中心各设有轴承,藉以得于悬吊架座的下段穿置组设一连杆,该连杆下端得穿出悬吊架座下端的套筒以衔组一撑张载具,利用该撑张载具得以撑夹网状的置料筒,而该连杆顶端得与置设于悬吊架座上基板顶面的伸缩缸件的缸杆及二伸缩缸件、缸杆同步掣动,本实用新型针对自动镀锌系统的载具所作的结构设计,特能赋予其镀锌作业的一贯化自动作业,有效解决习知作业系统所存在的诸多问题与缺点。
100 CN01136210.3 具有优秀成形性、面板定形性和抗硌痕性的冷轧钢板与镀锌钢板及其制造方法 公开了一种具有优秀成形性、面板定形性和抗硌痕性的冷轧钢板。它含有0.005~0.015%的C、0.01~0.2%的Si、0.2~1.5%的Mn、0.01~0.07%的P、0.006~0.015%的S、0.01~0.08%的固溶态Al、不大于0.004%的N、不大于0.003%的O、0.04~0.23%的Nb,其中{1.0≤(Nb%×12)/(C%×93)≤3.0},以及平衡量的Fe和不可避免的杂质;冷轧钢板满足下述关系:exp(ε)×(5.29×exp(ε)-4.19)≤σ/σ<sub>0.2</sub>≤exp(ε)×(5.64×exp(ε)-4.49)其中0.002<ε≤0.096,ε表示真应变,σ<sub>0.2</sub>表示0.2%弹性极限应力,σ表示相对于真应变ε的真应力。
锌合金压铸件电镀层起泡成因与消除对策

锌合金压铸件电镀层起泡成因与消除对策摘要:锌具有优异的机械性能,耐腐蚀性好,化学性质稳定。
在电子工业、航空制造等行业中广泛使用。
但由于特殊的铸造工艺(高频高压、低压下凝固)而制冷导致了金属表面产生起泡,起泡问题的出现直接影响整个产品的质量。
为此,本文分析锌合金压铸件生产工艺及电镀层起泡的基本情况,根据锌合金压铸件电镀层起泡成因分别从电镀原料及精炼、压铸模具和电镀阶段造成的起泡原因分析,希望帮助生产企业明确消除对策,保障铸件质量。
关键词:锌合金压铸件;电镀层;起泡;原因。
锌具有良好的耐腐蚀性,机械性能好,化学性质稳定,优良的高温固化作用和高熔点。
但是在室温下不能完全溶解于金属基体中。
因此对于铝合金材料来说恰当合理地施加合适电镀工艺是非常必要且有意义地利用其优异特性来实现合金压铸件生产过程轻量化、节约资源与保护环境友好型产品制造方法之一。
1锌合金压铸件生产工艺及电镀层起泡根据锌合金压铸件生产工艺路程来看,其包括线外除蜡、超声波除蜡、热水洗、化学除油、阴极电解除油、焦磷酸盐镀亮铜、酸活化、硫酸盐镀半光亮镍、镍封、铬还原、超声波洗净、酸中和、热纯水洗以及烘干、包装等多道工序[1]。
在锌合金压铸件生产阶段,针对电镀层起泡原因来说,由于生产过程中锌合金压铸所用的原料成本以及回收料比例不合理、实际的精炼效果相对较差、压铸模具以及压铸工艺不合理等,在材料以及工艺的影响下,都可能在锌合金压铸件电镀的过程中出现起泡的异常情况。
要确保锌合金压铸件生产质量,则需要针对生产过程中的多个节点检测,重点是做好锌合金压铸前的状态检测,了解电镀层的覆盖和致密度。
从锌合金压铸件电镀层起泡的具体原因来看,主要有以下几种可能:其一,原料问题。
其中主要是锌锭+回收料比例严重偏差,导致电镀层起泡;其二,熔炼阶段,新老料比例不协调、精炼程度不高、含有的杂质量超标(Pb、Cd)、合金元素含量超标,从而导致电镀层在熔炼阶段出现起泡现象[2];其三,压铸阶段,一方面是由于压铸工艺参数设计不合理,另一方面则是模具设计不合理,导致压铸阶段锌合金压铸件出现起泡情况;其四,镀前处理阶段,除蜡、除油不及时,抛光过热麻点不充足,抛光厚度与光洁度达不到需求,打破厚度也不达标,从而导致起泡出现;其五,镀铜阶段,镀酸铜、镀焦铜、镀氰铜、冲击镀铜、浸氰化亚铜、活化处理不到位,带着电镀层容易出现起泡[3];其六,镀镍阶段,镍封、亮镍、高硫镍、中性镀镍、暗镍、冲击镍以及酸活化未处理到位,导致起泡;其七,镀铬阶段,铬还原不及时、镀铬不合理、酸活化处理不到位,导致起泡问题出现。
7招教你如何应对铸件气泡问题

7招教你如何应对铸件气泡问题气泡可以说是咱们压铸行业中铸件最常见问题之一,而且一旦铸件出现了气泡问题,也等于产品报废了。
为了避免气泡的产生,小编将详细的为您剖析铸件气泡~~教您7招解决铸件气泡问题【缺陷现象】铸件表皮下,聚集气体鼓胀所形成的泡,有时会崩裂,存在贯通和非贯通两种。
别名:鼓泡、起泡【原因分析】•模具温度太高,开模过早。
•填充速度太高,金属流卷入气体过多。
•涂料发气量大,用量过多,浇注前未燃尽,使挥发气体被包在铸件表层,另涂料含水量大。
•型腔内气体没有排出,排气不顺。
•合金熔炼温度过高。
•铝合金液体除气不彻底,吸有较多气体,铸件凝固时析出留在铸件内•填充时产生紊流。
【对应措施】1、测温枪测试模具表面温度,显示数值超过工艺规定范围。
降低模具表面温度,增加保压时间;2、铸件表面内浇口压入的金属流明显比其它部位亮很多。
填充速度高产生原因一方面是设备本身的压射速度高,另一方面可能是内浇口太薄造成。
降低压射速度,适当增加内浇口厚度;判断内浇口薄的方法:是否有浇口易粘现象,降低二快速度看远端是否有严重压不实现象,不给压打件,看是否有多股铝液流;3、喷涂时察看雾的颜色是否呈白色,合模前察看型腔是否还有气体残留。
更换涂料或增大涂料与水的配比;4、在烫模阶段,铸件表面有明显的漩涡和涂料堆积。
判断及解决方法:调开档,人为产生涨模,如果解决,需开排气道;5、铸件表面内浇口压入的金属流特别亮并伴有粘结。
适当降低浇注温度;6、取样块测密度,看是否符合要求。
重新进行除气处理或在保温炉内进行再次精炼;7、烫模阶段铸件表面明显有各流溶接不到一起的痕迹伴有涂料堆积。
判断及解决方法:涂黑油生产,看痕迹是否有堆积,分析堆积部位,解决方法:•a、开设或加大相应部位的集渣包,•b、调整内浇口流向、位置或填充方向。
————————。
压铸件内部气孔产生的原因

压铸件内部气孔产生的原因
压铸是一种常见的金属铸造工艺,广泛应用于各种行业。
然而,在压铸过程中,气孔是常见的缺陷之一,它对压铸件的质量和性能有很大的影响。
本文将详细分析压铸件内部气孔产生的原因,并提供一些防止气孔产生的建议。
一、气孔产生的原因
1.金属液中气体含量高
金属液在熔炼、浇注过程中会吸收大量的气体,这些气体在金属液中形成气泡。
当气泡无法从金属液中逸出时,就会随着金属液进入压铸件内部,形成气孔。
2.模具温度过高
模具温度过高会导致金属液在模具内的流动性增加,使得气体更容易进入金属液中。
同时,高温还会降低气体在金属液中的溶解度,使得气泡更容易形成和长大。
3.模具设计不合理
模具设计不合理也是导致气孔产生的原因之一。
例如,浇口位置不当、模具排气不良等都会使得气体无法顺利排出,从而形成气孔。
4.操作不当
操作不当也是导致气孔产生的原因之一。
例如,浇注速度过快、浇注温度过低等都会使得气体难以从金属液中逸出,从而形成气孔。
二、防止气孔产生的建议
1.控制金属液中的气体含量
通过采用真空熔炼、离心熔炼等方法降低金属液中的气体含量,从而减少气孔的产生。
2.控制模具温度
合理控制模具温度,避免温度过高或过低,从而减少气孔的产生。
3.优化模具设计
优化模具设计,确保浇口位置得当、模具排气通畅,从而减少气孔的产生。
压铸零件热处理后出现气泡的原因

压铸零件热处理后出现气泡的原因
哎呀,咱今儿就来说说这压铸零件热处理后出现气泡的事儿。
我跟您讲,这事儿可真让人头疼。
就说这压铸零件吧,本来好好的,经过热处理,嘿,气泡就冒出来了。
您说怪不怪?
我仔细琢磨了好久,这原因啊,可能是压铸的时候,那模具里头就有气儿没排干净。
就好像咱吹气球,气没吹匀,这儿鼓一块儿那儿鼓一块儿的。
还有啊,这原材料也可能有问题。
要是材料本身不纯,有杂质啥的,热处理的时候一受热,可不就容易出气泡嘛。
再有,热处理的工艺要是不得当,温度啊、时间啊没把握好,也能整出这麻烦事儿。
您瞧,就这么个小小的气泡,能牵扯出这么多的门道。
这搞技术的,真得处处小心,一个不留神,这气泡就冒出来给咱添乱啦!。
合金电镀气泡的原1
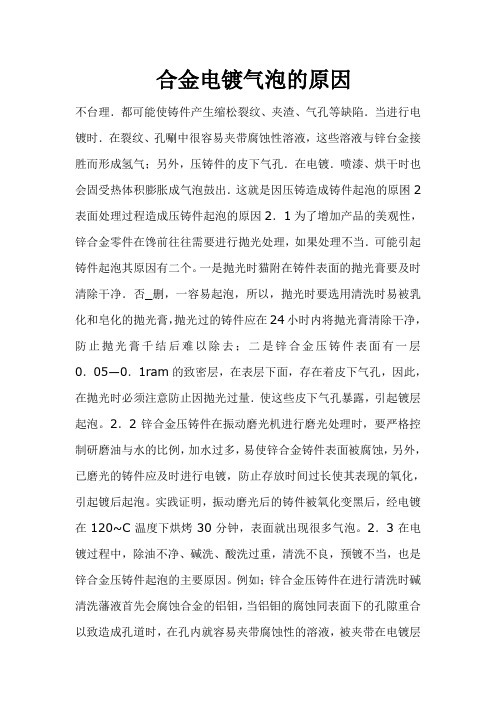
合金电镀气泡的原因不台理.都可能使铸件产生缩松裂纹、夹渣、气孔等缺陷.当进行电镀时.在裂纹、孔唰中很容易夹带腐蚀性溶液,这些溶液与锌台金接胜而形成氢气;另外,压铸件的皮下气孔.在电镀.喷漆、烘干时也会固受热体积膨胀成气泡鼓出.这就是因压铸造成铸件起泡的原困2表面处理过程造成压铸件起泡的原因2.1为了增加产品的美观性,锌合金零件在馋前往往需要进行抛光处理,如果处理不当.可能引起铸件起泡其原因有二个。
一是抛光时猫附在铸件表面的抛光膏要及时清除干净.否_删,一容易起泡,所以,抛光时要选用清洗时易被乳化和皂化的抛光膏,抛光过的铸件应在24小时内将抛光膏清除干净,防止抛光膏千结后难以除去;二是锌合金压铸件表面有一层0.05—0.1ram的致密层,在表层下面,存在着皮下气孔,因此,在抛光时必须注意防止因抛光过量.使这些皮下气孔暴露,引起镀层起泡。
2.2锌合金压铸件在振动磨光机进行磨光处理时,要严格控制研磨油与水的比例,加水过多,易使锌合金铸件表面被腐蚀,另外,已磨光的铸件应及时进行电镀,防止存放时间过长使其表现的氧化,引起镀后起泡。
实践证明,振动磨光后的铸件被氧化变黑后,经电镀在120~C温度下烘烤30分钟,表面就出现很多气泡。
2.3在电镀过程中,除油不净、碱洗、酸洗过重,清洗不良,预镀不当,也是锌合金压铸件起泡的主要原因。
例如;锌合金压铸件在进行清洗时碱清洗藩液首先会腐蚀合金的铝钼,当铝钼的腐蚀同表面下的孔隙重合以致造成孔道时,在孔内就容易夹带腐蚀性的溶液,被夹带在电镀层下面的溶液与锌合金作用而产生氢气时+就会引起起泡。
碱洗酸洗后必须真进行清洗,以尽可能冲稀在盲孔沟槽以及其它表面低洼处与内腔中的酸碱溶液.否则,就容易在沟槽低洼处起泡。
分析找出电镀过程起泡的原因后,我们采取以下措旋:L在三氯己烯溶剂中除油时,要按照气相一液相一气相进行除油,三氯乙稀太眭时要及时换掉。
2.电解去油要先阴极后阳极.这样即不能腐蚀锌合金又不会使零件表面产生浮灰.而影响电镀结合力。
铸钢件铸造厂家该如何解决铸件气泡问题?
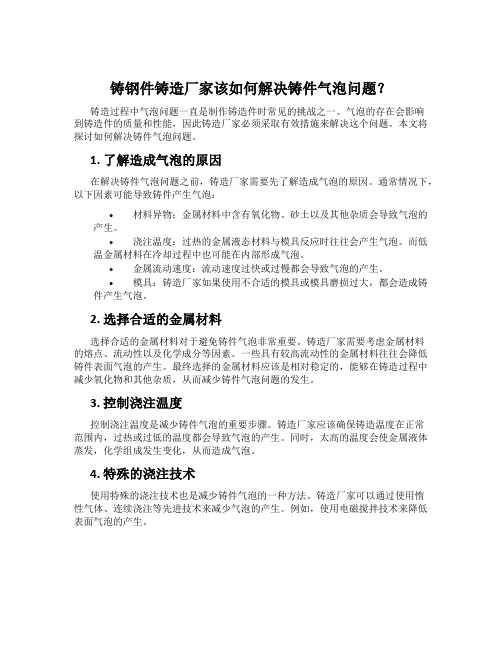
铸钢件铸造厂家该如何解决铸件气泡问题?铸造过程中气泡问题一直是制作铸造件时常见的挑战之一。
气泡的存在会影响到铸造件的质量和性能,因此铸造厂家必须采取有效措施来解决这个问题。
本文将探讨如何解决铸件气泡问题。
1. 了解造成气泡的原因在解决铸件气泡问题之前,铸造厂家需要先了解造成气泡的原因。
通常情况下,以下因素可能导致铸件产生气泡:•材料异物:金属材料中含有氧化物、砂土以及其他杂质会导致气泡的产生。
•浇注温度:过热的金属液态材料与模具反应时往往会产生气泡。
而低温金属材料在冷却过程中也可能在内部形成气泡。
•金属流动速度:流动速度过快或过慢都会导致气泡的产生。
•模具:铸造厂家如果使用不合适的模具或模具磨损过大,都会造成铸件产生气泡。
2. 选择合适的金属材料选择合适的金属材料对于避免铸件气泡非常重要。
铸造厂家需要考虑金属材料的熔点、流动性以及化学成分等因素。
一些具有较高流动性的金属材料往往会降低铸件表面气泡的产生。
最终选择的金属材料应该是相对稳定的,能够在铸造过程中减少氧化物和其他杂质,从而减少铸件气泡问题的发生。
3. 控制浇注温度控制浇注温度是减少铸件气泡的重要步骤。
铸造厂家应该确保铸造温度在正常范围内,过热或过低的温度都会导致气泡的产生。
同时,太高的温度会使金属液体蒸发,化学组成发生变化,从而造成气泡。
4. 特殊的浇注技术使用特殊的浇注技术也是减少铸件气泡的一种方法。
铸造厂家可以通过使用惰性气体、连续浇注等先进技术来减少气泡的产生。
例如,使用电磁搅拌技术来降低表面气泡的产生。
5. 做好模具维护选择合适的模具材料以及做好模具维护也对铸件气泡的产生具有影响。
模具表面的磨损和氧化物都会对铸件产生负面影响,因此铸造厂家需要选择合适的材料进行制作,在模具使用过程中及时对其进行维护和修复。
6. 使用低压铸造技术低压铸造技术是铸造厂家减少铸件气泡的另一种有效方法。
在低压铸造过程中,金属液晶体通过一种特殊设备被推入模具内部。
锌合金压铸件电镀层起泡成因与消除对策

on blistering of zinc alloy die casting after electroplating were summarized. The causes of blistering mainly includes: high
content of impurities such as Pb and Cd in zinc alloy; unreasonable design or improper preheating temperature of casting mold;
在压铸过程中,压铸的压力、温度以及模具的温度等对锌合金压铸件质量的影响主要表现在气孔、冷隔等
压铸缺陷方面[17]。针对模具温度的研究表明,当模温在 160 °C 时,压铸后的组织有明显的孔洞,而模温为 165 °C
和 170 °C 时的组织更为致密[12]。
锌合金压铸过程中产生的气泡、冷隔和裂纹等缺陷都会给后续的清理和电镀带来困难,保证压铸件质量才
杂质。压铸锌合金中杂质含量高对锌合金液的压铸成型能力及锌合金的力学性能都不利[13],引起电镀后起泡的
概率也会大大增加。
锌合金原料中的杂质含量、熔炼回收料的掺入比率及精炼对压铸产品质量都有较大影响,这种影响会依次
传递,最终影响到锌合金件电镀后的质量。因此,锌合金压铸生产不仅要严把原料质量关,而且要对压铸前锌
(a) 梯形内浇道
(b) 椭圆形内浇道
(a) Trapezoid-shaped ingate
(b) Ellipse-shape ingate
图 5 梯形与椭圆形内浇道锌压铸产品的 SEM 照片 SEM images of Zn die castings produced with trapezoid- and ellipse-shaped ingate
- 1、下载文档前请自行甄别文档内容的完整性,平台不提供额外的编辑、内容补充、找答案等附加服务。
- 2、"仅部分预览"的文档,不可在线预览部分如存在完整性等问题,可反馈申请退款(可完整预览的文档不适用该条件!)。
- 3、如文档侵犯您的权益,请联系客服反馈,我们会尽快为您处理(人工客服工作时间:9:00-18:30)。
铸造利润源泉的发动机
陕西网铸互联网信息技术有限公司 1 锌合金压铸件出现气泡的原因
锌合金压铸件在各种不同的装饰应用中使用比较广泛,包括家具的配件、建筑装饰材料、玩具、衣物饰品等多种行业均有涉及。
因此,对于锌合金压铸件的外观及其质量要求一般就比较高。
锌合金压铸件在生产的过程中最常见的一种缺陷是压铸件表面容易出现气泡。
这个问题在压铸完成之后或者是在进行进一步深加工的时候会发现。
其产生的原因主要有:
1。
孔洞引起:主要是气孔和收缩机制,气孔往往是圆形,而收缩多数是不规则形。
(1)气孔产生原因:
a 、金属液在充型、凝固过程中,由于气体侵入,导致铸件表面或内部产生孔洞。
b 、涂料挥发出来的气体侵入。
c 、合金液含气量过高,凝固时析出。
当型腔中的气体、涂料挥发出的气体、合金凝固析出的气体,在模具排气不良时,最终留在铸件中形成的气孔。
(2)缩孔产生原因:
a 、金属液凝固过程中,由于体积缩小或最后凝固部位得不到金属液补缩,而产生缩孔。
b 、厚薄不均的铸件或铸件局部过热,造成某一部位凝固慢,体积收缩时表面形成凹位。
由于气孔和缩孔的存在,使压铸件在进行表面处理时,孔洞可能会进入水,当喷漆和电镀后进行烘烤时,孔洞内气体受热膨胀;或孔洞内水会变蒸气,体积膨胀,因而导致铸件表面起泡。