刃口尺寸计算.
凸、凹模刃口尺寸的计算
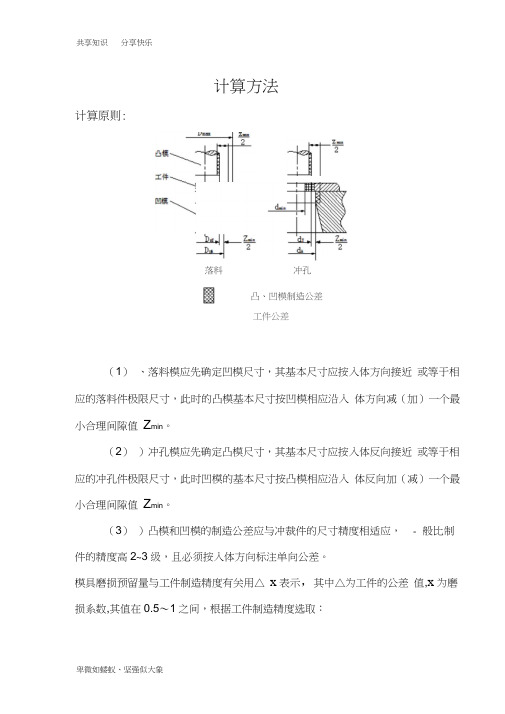
工件公差(1) 、落料模应先确定凹模尺寸,其基本尺寸应按入体方向接近 或等于相应的落料件极限尺寸,此时的凸模基本尺寸按凹模相应沿入 体方向减(加)一个最小合理间隙值 Z min 。
(2) )冲孔模应先确定凸模尺寸,其基本尺寸应按入体反向接近 或等于相应的冲孔件极限尺寸,此时凹模的基本尺寸按凸模相应沿入 体反向加(减)一个最小合理间隙值 Z min 。
(3) )凸模和凹模的制造公差应与冲裁件的尺寸精度相适应, - 般比制件的精度高2~3级,且必须按入体方向标注单向公差。
模具磨损预留量与工件制造精度有关用△ x 表示,其中△为工件的公差 值,x 为磨损系数,其值在0.5〜1之间,根据工件制造精度选取:计算原则:计算方法落料 冲孔凸、凹模制造公差工件精度IT10级以上X =1.0工件精度IT11〜13X =0.75工件精度IT14X =0.5规则形状冲裁模凸模、凹模制造偏差51、分别加工法§凸+ §凹W Z max- Z min落料D凹=(D max - X △0D凸=(D凹-Z min )二凸=(D max - X △Z min )」凸冲孔d凸=(d min + X △) 1凸d凹=(d凸+ Z min ) 0 = ( d min + X△Z min ) 0孔心距孔心距属于磨损后基本不变的尺寸,在同一工步中,在工件上冲出的孔距为L±2/2两个孔时,其凹模型孔心距L d可按下式确定。
L d =L+ —■-8:凸、「•凹一一凸、凹模制造公差,可按IT6〜IT7级来选取,或取、•凸W0.4 ( Z max- Z min ) , '•凹W0.6 ( Z max" Z min )2、单配加工法单配加工法是用凸模和凹模相互单配的方法来保证合理间隙的一种方法。
此方法只需计算基准件(冲孔时为凸模,落料时为凹模)基本尺寸及公差,另一件不需标注尺寸,仅注明“相应尺寸按凸模(或凹模)配做,保证双面间隙在Z max〜Z min之间”即可。
凸凹模刃口尺寸的计算
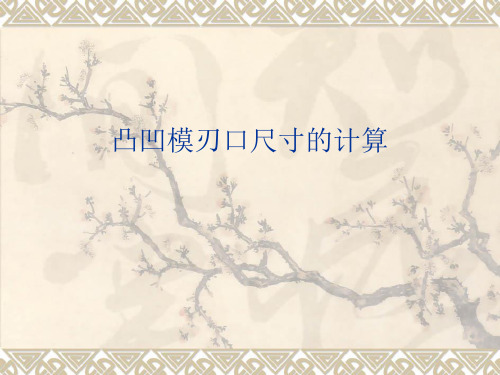
尺寸计算方法
2)落料
尺寸计算方法
dp、dd——别为冲孔凸模和凹模尺寸
Dp、Dd——分别喂落料凸模和凹模尺寸
——共建的迟早公差 D、d——分别为落料件和孔的基本尺寸 Zmin——最小合理间隙(双边) X——磨损系数,与制造精度有关
⊿
尺寸计算方法
凸模与凹模配合加工 适用于形状复杂或薄板料的冲裁件 根据冲裁件结构尺寸的不同类型,分别加以 对待。具体方法如下:
凸凹模刃口尺寸的计算
尺寸计算准则
凸模和凹模刃口尺寸直接决定工件的尺寸和
பைடு நூலகம்
模具间隙的大小,是模具上最重要的尺寸。 1、刃口尺寸计算的基本原则: 1)由于冲孔落料件都是测量其光亮带部分的 尺寸,而冲孔的光亮带是凸模挤入而形成。 落料的光亮带是落料件挤入凹模型孔形成。 故冲孔时孔的尺寸由凸模决定,落料时的外 形尺寸由凹模决定。
尺寸计算方法
第三类:凸模磨损后没有变化的尺寸,分三种 情况: (1)孔尺寸的标注为C+ ⊿时: Cp=(C+0.5 ⊿ )±&p (2)孔尺寸的标注为C+ ⊿时: Cp=(C-0.5 ⊿ )±&p (3)孔尺寸的标注为C ±⊿’时: Cp =C ±&p
2.
落料时应以凹模为基准件来配做凸模,并按
凹模磨损后尺寸变大、变小、不变的规律分 三种类型进行计算。 第一类:当凹模磨损后变大的尺寸 Ad=(A-x⊿) +&d
第二类:当凹模磨损后变小的尺寸,
Bd=(B+x ⊿ )-&d
尺寸计算方法
第三类:当凹模磨损后没有变化的尺寸
(1)冲裁件尺寸标注为C+ ⊿时: Cd=(C+0.5 ⊿ )±&d (2)冲裁件尺寸标注为C+ ⊿时: Cd=(C-0.5 ⊿ )±&d (3)冲裁件尺寸标注为C ±⊿’时: Cd=C ±&d
凹凸模刃口尺寸计算方法

凹凸模刃口尺寸计算方法咱先说说凹模刃口尺寸的计算呢。
一般来说啊,凹模刃口尺寸是按照落料件来确定的。
为啥呢?因为落料件的尺寸是由凹模刃口决定的呀。
在计算的时候呢,要考虑到冲裁件的最大极限尺寸。
就好比给这个落料件的尺寸画个最大的圈儿,凹模刃口尺寸就得按照这个最大圈儿来定,还得把磨损量考虑进去哦。
这就像是给这个凹模刃口预留一点长胖的空间,毕竟它在工作的时候会有磨损嘛。
而且啊,这个制造公差得取负偏差,这就像是给它一个小小的范围,不能让它太任性地变大啦。
再聊聊凸模刃口尺寸。
凸模刃口尺寸是根据冲孔件来确定哒。
冲孔嘛,就是在材料上弄出个洞洞来。
那这个凸模刃口尺寸就得按照冲孔的最小极限尺寸来定咯。
为啥是最小极限尺寸呢?因为凸模要是太大了,那冲出来的孔可就不符合要求啦。
这里也要考虑磨损量哦,不过和凹模不太一样的是,凸模的制造公差要取正偏差。
这就像是给凸模规定了一个只能往大了长一点点的规则呢。
宝子们可能会问,那这个磨损量到底咋确定呀?这就和很多因素有关咯,像冲裁的材料呀,冲裁的次数呀之类的。
如果冲裁的材料比较硬,那磨损量可能就会大一些,就像硬东西更容易把刃口磨坏嘛。
要是冲裁次数很多,那磨损量也得考虑多留一点,毕竟用得多了,刃口就会越来越不锋利啦。
还有哦,在实际计算的时候,有时候会用到一些经验公式。
这些经验公式就像是前辈们总结出来的小秘籍一样。
但是呢,也不能完全依赖这些公式,还得根据具体的情况,像是冲裁件的精度要求呀,模具的结构特点呀来调整。
总之呢,凹凸模刃口尺寸计算虽然有点小复杂,但只要咱搞清楚落料和冲孔的区别,把磨损量、制造公差这些因素都考虑进去,再结合实际情况,就能够比较准确地计算出来啦。
宝子们要是在这个过程中遇到啥问题,可别自己一个人挠头哦,咱们可以一起讨论讨论呀。
凸凹模刃口尺寸的计算[整理]
![凸凹模刃口尺寸的计算[整理]](https://img.taocdn.com/s3/m/fb84b21278563c1ec5da50e2524de518964bd306.png)
凸凹模刃口尺寸的计算1. 计算分析(1) 模具的合理间隙值由模具刃口尺寸及其公差保证 (2) 间隙使材料和孔都带有锥度1) 落料件大端尺寸等于凹模刃口尺寸 2) 冲孔件小端尺寸等于凸模刃口尺寸(3) 在测量与使用中,落料件是以大端尺寸为基准,冲孔孔径是以小端尺寸为基准。
(4) 冲裁时,凸模越磨越小,凹模越磨越大,使间隙越来越大。
2. 计算原则(1) 设计落料模时,以凹模为基准,间隙取在凸模上设计冲孔模时,以凸模为基准,间隙取在凹模上(2) 由于冲裁中凸凹模的磨损,设计落料模时,凹模公称尺寸应取工件尺寸公差范围内的较小尺寸;设计冲孔模时,凸模公称尺寸应取工件尺寸公差范围内的较大尺寸(3) 冲模刃口制造公差的确定1) 零件精度与模具制造精度的关系 2) 零件没有标注公差时:a① 对于非圆形件,按国标“非配合尺寸的公差数值”IT14级精度来处理,冲模则按IT11精度制造② 对于圆形件,一般可按IT6—7级精度制造模具3. 计算方法(1) 凸模凹模分开加工时尺寸与公差的确定:1) 要求①分别标注凸模和凹模刃口尺寸与制造公差 (凸模p δ凹模d δ)②为了保证间隙值,必须满足下列条件p δ+d δ≤max Z -minZ式中:max Z ,min Z ——凸凹模之间最大,最小双面间隙。
或取p δ=0.4(max Z -min Z )d δ=0.6(max Z -min Z )2) 方法:① 先确定基准件刃口的尺寸 ② 根据间隙确定另一刃口尺寸③ 落料时所取凹模刃口尺寸应靠近落料件公差范围的最小尺寸④ 冲孔时所取凸模刃口尺寸应靠近孔的公差范围的最大尺寸⑤ 不论是落料还是冲孔,冲模间隙均应采用合理间隙范围内的最小值。
3)计算公式落料:设工件尺寸为0ΔD -d D =(max D -∆X )dδ÷0p D =(d D -min Z )0p δ-=(max D -∆X -min Z )0pδ-冲孔:设工件孔的尺寸为∆+0dp d =(min d +∆X )0p δ-d d =(p d +min Z )d δ÷0=(min d +∆X +min Z )dδ÷0式中:p d,d d ——冲孔时凸凹模直径p D,d D——落料时凸凹模尺寸min d ——工件最小的孔径max D——工件最大的外径例:图示垫圈,材料为3A 钢,料厚t=2毫米,凸凹模分别制造,试确定冲孔模和落料模的直径,垫圈的孔径是24.005.12+φ外圆直径为034.035-φ系数x解:(1)由表3-5查得min Z =0.24 max Z =0.36max Z -min Z =0.36-0.24=0.12(2) 由上表查得落料时d δ=0.03 p δ=0.02d δ+p δ=0.03+0.02=0.05<max Z -min Z =0.12冲孔时p δ=d δ=0.02d δ+p δ=0.04<max Z -min Z =0.12(3)由上表查得X 落=X 冲孔=0.5(4)落料时,凸凹刃口尺寸d D =(max D -∆X )d δ÷0=(35-0.5×0.34)03.00÷=34.8303.00÷p D =(d D -min Z )0pδ-=(34.83-0.24)002.0-=34.59002.0-(5)冲孔时刃口尺寸p d =(min d +∆X )0pδ-=(12.5+0.5×0.24)002.0-=12.62002.0-d d =(p d +min Z )d δ÷0=(12.62+0.24)02.00÷=12.8602.00÷。
冲模刃口尺寸计算

落料凸模的基本尺寸与凹模相同,分别是79.79mm,
39.75mm,34.75mm,22.07mm,14.94mm,不必标注公差,但
要在技术条件中注明:凸模刃口尺寸与落料凹模实际刃口尺寸配 制,保证最小双面合理间隙值
Z min 0 . 10 mm
落料凹模、凸模的尺寸如图。
d p ( d m in x ) (6 0 .7 5 0 .1 2 ) 0 .0 0 8 m m 6 .0 9 0 .0 0 8 m m
0 0 0
p
36 0 . 62 mm
0
d d ( d p Z min ) 0
d
( 6 . 09 0 . 04 ) 0
d
落料: D d ( D max x ) 0
( 36 0 . 5 0 . 62 ) 0
D p ( D d 2 c min ) p
0
0 . 025
mm 35 . 69 0
0 . 025
mm
( 35 . 69 0 . 04 ) 0 . 06 mm 35 . 65 0 . 016 mm
第二章 冲裁工艺与冲裁模设计
3.凸模与凹模配合加工刃口尺寸计算 (1)根据磨损后轮廓变化情况,正确判断出模具刃口尺寸类型:
即磨损后尺寸是变大,变小还是不变。
(2)根据尺寸类型,采用不同计算公式。 磨损后变大的尺寸,采用分开加工时的落料凹模尺寸计算公式。 磨损后变小的尺寸,采用分开加工时的冲孔凸模尺寸计算公式。 磨损后不变的尺寸,采用分开加工时的孔心距尺寸计算公式。 (3)刃口制造偏差可按工件相应部位公差值的1/4来选取。对于 刃口尺寸磨损后无变化的制造偏差值可取工件相应部位公差值的
冲裁凸、凹模刃口尺寸计算

2.7.3 冲裁凸、凹模刃口尺寸计算
[例2-1] 用分开制造计算图2-72所示零件的凸凹模 刃口尺寸。
图2-72 零件图
解:1、确定基本工序 内形:冲孔。外形:落料 2、画磨损曲线
2.7.3 冲裁凸、凹模刃口尺寸计算
① 冲孔 画凸模刃口的磨损曲线如图2-73
② 落料 画凹模刃口的磨损曲线。如图2-74
按上(1)、(2)之法可得出: 冲孔磨后变大的公式
δ 凹 a凸 (a max x)0
(2-28) (2-29)
a凹 (a凸 Z min)0 δ 凸
落料磨后变小的公式
δ 凹 B凸 (B凹 Z min)0
(2-30) (2-31)
B凹 (Bmin x)0 δ 凸
0 0.52
2.7.3 冲裁凸、凹模刃口尺寸计算
尺寸Ⅳ、Ⅴ:25( )为落料磨后变大. Δ=0.52→IT14→X=0.5 A凹1 =(A1max-xΔ) =(25-0.5×0.52) =24.74 A凸1=( A凹1- Zmin) =(24.74-0.24) =24.5 尺寸Ⅵ: 7为落料单边磨后变大, Δ=0.2→IT13→X=0.75 A凹2=(A2max-xΔ) =(7-0.750.2)=6.85 A凸2=( A凸2 - )=(6.85-)=(6.85-0.12) =6.73
0.2 0
2.7.3 冲裁凸、凹模刃口尺寸计算
尺寸Ⅳ、Ⅴ:25( )为落料磨后变大. Δ=0.52→IT14→X=0.5 A凹1 =(A1max-xΔ) =(25-0.5×0.52) =24.74 A凸1=( A凹1- Zmin) =(24.74-0.24) =24.5 尺寸Ⅵ: 7为落料单边磨后变大, Δ=0.2→IT13→X=0.75 A凹2=(A2max-xΔ) =(7-0.750.2)=6.85 A凸2=( A凸2 - )=(6.85-)=(6.85-0.12) =6.73
刃口尺寸计算

冲裁模具工作零件设计试题 11
刃口尺寸计算 采用分开加工,计算凸凹模尺寸: 凸、凹模的间隙值为: Z min =0.132mm Z max =0.240mm Z max -Z min =0.24-0.132=0.108mm 由查表可知:δD 凹=+0.03mm δD 凸=-0.02 mm X =0.5 δd 凹=+0.02mm δd 凸=-0.02 mm X =0.5 因为∣δD 凹∣+∣δD 凸∣=0.05mm ≤Z max -Z min , 同样∣δd 凹∣+∣δd 凸∣=0.04mm ≤Z max -Z min.故能满足分开加工的要求. 落料:D 凹=﹙D -X △﹚凹δ+0=﹙35-0.5×0.62﹚03.00+=34.6903.00+mm D 凸=﹙D -Z min ﹚0凸δ-=﹙34.69-0.132﹚002.0-=34.558002.0-mm 冲孔:d 凸=﹙d +X △﹚0凸δ-=﹙5+0.5×0.3﹚002.0-=5.15002.0-mm d 凹=﹙d +Z min ﹚凹δ+0=﹙5.15+0.132﹚02.00+=5.28202.00+mm 凸模型孔中心距: L =L ±△/8=18±0.05375mm 校名称 株洲职业技术学院 姓名 王荣贵 准考证号
垫片冲模凹模设计:
如图
1、厚度H
查表得K=0.42mm
H=Kb=35×0.42=14.7mm≈15mm
长度和宽度相等。
查表得W=24mm
L=D+2W=35+2×24=83mm
为保证凹模强度,将尺寸放大到90mm后,凹模外形尺寸为:L×L×H=90mm×90mm×28mm
以下为凸凹模的三维立体图与工程图。
凸、凹模刃口尺寸计算
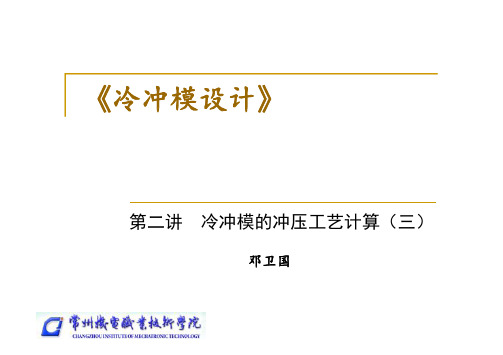
《冷冲模设计》第二讲冷冲模的冲压工艺计算(三)邓卫国第二讲冷冲模的冲压工艺计算(三)第三部分凸、凹模刃口尺寸的确定凹模与凸模的刃口尺寸计算定义:什么叫刃口尺寸:刃口尺寸指在凹模和凸模零件图上分别标注尺寸及公差值,这个值与冲压产品尺寸精度有关。
⏹学习目标☐掌握凸、凹模刃口计算作用☐掌握凸、凹模刃口尺寸计算的依据和原则☐掌握凸、凹模刃口尺寸计算的方法二、冲裁模凸、凹模刃口尺寸的确定1、冲裁模凸、凹模刃口计算的作用冲裁件的尺寸精度主要取决于凸、凹模的刃口部分尺寸。
并且合理的冲裁间隙也靠凸、凹模刃口尺寸保证。
凸模刃口尺寸示意图所以冲裁模刃口设计是冲裁模设计的重点。
凹模刃口尺寸示意图二、冲裁模凸、凹模刃口的确定2、凸、凹模刃口尺寸计算的依据在生产实践中发现:a.由于凸凹模之间存在间隙,冲裁件断面都带有锥度。
依据:①光亮带是冲压件测量和使用部位;②落料件的光亮带,是因凹模刃口挤切材料产生的;③冲孔件的光亮带,是因凸模刃口挤切材料产生的;④落料件的大端(光亮带)尺寸等于凹模尺寸;⑤冲孔件的小端(光亮带)尺寸等于凸模尺寸。
b.凸模轮廓越磨越小,凹模轮廓越磨越大,结果使间隙越用越大。
结论:在计算冲裁模刃口尺寸时,应按落料、冲孔两种情况分别进行计算。
二、冲裁模凸、凹模刃口尺寸确定3、冲裁模凸、凹模刃口计算的原则(一)(1)设计落料模先确定凹模刃口尺寸以凹模为基准,间隙取在凸模上,即冲裁间隙通过减小凸模刃口尺寸来取得;设计冲孔模先确定凸模刃口尺寸以凸模为基准,间隙取在凹模上,冲裁间隙通过增大凹模刃口尺寸来取得。
二、冲裁模凸、凹模刃口尺寸的确定4、冲裁模凸、凹模刃口计算的原则(二)(2)根据冲模在使用过程中的磨损规律:设计落料模时:凹模基本尺寸应取接近或等于零件的最小极限尺寸;设计冲孔模时:凸模基本尺寸则取接近或等于冲件孔的最大极限尺寸。
理由:凸、凹模在磨损到一定程度时,仍能冲出合格的零件。
二、冲裁模凸、凹模刃口尺寸确定5、冲裁模凸、凹模刃口计算的原则(三)(3)凹模和凸模制造公差主要与冲裁件的精度有关①一般冲模精度较零件精度高3~4级;②形状简单的圆形、方形刃口,其制造偏差值可按IT6~IT7级来选取,或查表;③形状复杂的刃口制造偏差可按零件相应部位公差值的1/4来选取;④刃口尺寸磨损后无变化的制造偏差值可取冲件相应部位公差值的l/8并冠(±);⑤若零件没有标注公差,则可按IT14级取值。
冲裁间隙及凸凹模刃口尺寸计算
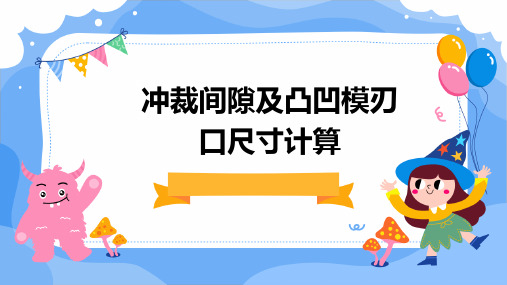
凹模刃口尺寸计算
根据凸模刃口尺寸和冲裁间隙,计算凹模刃口的基本尺寸 。
考虑凹模的磨损和刃磨修正等因素,对刃口尺寸进行修正 。
03
冲裁间隙计算
理论计算方法
弹性变形
考虑材料在冲裁过程中的弹性变 形,通过弹性力学理论计算间隙
值。
塑性变形
基于塑性力学理论,分析材料在冲 裁过程中的流动和应力分布,以确 定合理的间隙值。
冲裁间隙及凸凹模刃 口尺寸计算
目录
• 引言 • 冲裁间隙概述 • 冲裁间隙概述 • 冲裁间隙计算 • 凸凹模刃口尺寸计算 • 实际应用案例 • 结论与展望
01
引言
目的和背景
目的
冲裁间隙及凸凹模刃口尺寸计算 是冲压工艺中的重要环节,其目 的是确保冲裁件的质量和模具的 寿命。
背景
随着制造业的发展,对冲压工艺 的要求越来越高,合理的冲裁间 隙及凸凹模刃口尺寸是实现高效 、高质量冲压的关键。
报告结构
01
本报告将详细介绍冲裁间隙及凸 凹模刃口尺寸的计算方法。
02
报告将分为以下几个部分:冲裁 间隙的概念和作用、凸凹模刃口 尺寸的计算、实际应用案例分析 以及结论。
02
冲裁间隙概述
凸料厚度,计算凸模刃口的基本尺 寸。
考虑凸模的磨损和热处理变形等因素,对刃口尺寸进行修正 。
凹模刃口尺寸计算公式
根据冲裁件的尺寸和公差要求,结合凹模的结构 形式,采用相应的计算公式来确定凹模的刃口尺 寸。
考虑因素
凹模刃口尺寸计算时需考虑冲裁件的形状、尺寸 精度、材料厚度、模具结构等因素。
3
精度要求
凹模刃口尺寸的精度要求较高,一般要求达到 ±0.01mm以内。
刃口尺寸修正
修正原因
刀刃刃口尺寸计算公式
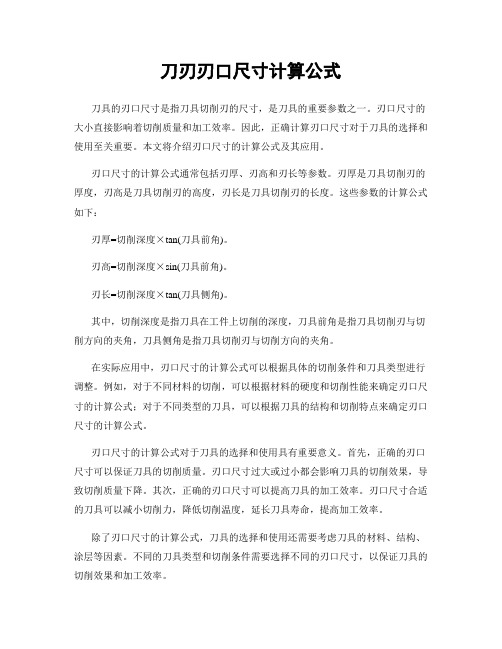
刀刃刃口尺寸计算公式刀具的刃口尺寸是指刀具切削刃的尺寸,是刀具的重要参数之一。
刃口尺寸的大小直接影响着切削质量和加工效率。
因此,正确计算刃口尺寸对于刀具的选择和使用至关重要。
本文将介绍刃口尺寸的计算公式及其应用。
刃口尺寸的计算公式通常包括刃厚、刃高和刃长等参数。
刃厚是刀具切削刃的厚度,刃高是刀具切削刃的高度,刃长是刀具切削刃的长度。
这些参数的计算公式如下:刃厚=切削深度×tan(刀具前角)。
刃高=切削深度×sin(刀具前角)。
刃长=切削深度×tan(刀具侧角)。
其中,切削深度是指刀具在工件上切削的深度,刀具前角是指刀具切削刃与切削方向的夹角,刀具侧角是指刀具切削刃与切削方向的夹角。
在实际应用中,刃口尺寸的计算公式可以根据具体的切削条件和刀具类型进行调整。
例如,对于不同材料的切削,可以根据材料的硬度和切削性能来确定刃口尺寸的计算公式;对于不同类型的刀具,可以根据刀具的结构和切削特点来确定刃口尺寸的计算公式。
刃口尺寸的计算公式对于刀具的选择和使用具有重要意义。
首先,正确的刃口尺寸可以保证刀具的切削质量。
刃口尺寸过大或过小都会影响刀具的切削效果,导致切削质量下降。
其次,正确的刃口尺寸可以提高刀具的加工效率。
刃口尺寸合适的刀具可以减小切削力,降低切削温度,延长刀具寿命,提高加工效率。
除了刃口尺寸的计算公式,刀具的选择和使用还需要考虑刀具的材料、结构、涂层等因素。
不同的刀具类型和切削条件需要选择不同的刃口尺寸,以保证刀具的切削效果和加工效率。
在实际应用中,刃口尺寸的计算可以通过刀具厂家提供的刀具参数表来进行,也可以通过切削力模型和切削仿真软件来进行。
通过这些手段,可以更加准确地确定刃口尺寸,提高刀具的切削效果和加工效率。
总之,刃口尺寸的计算公式是刀具选择和使用的重要参考依据。
正确的刃口尺寸可以保证刀具的切削质量和加工效率,提高加工质量和效率。
因此,刃口尺寸的计算应该引起我们的重视,加强研究和应用。
冲压模具刃口尺寸设计公式
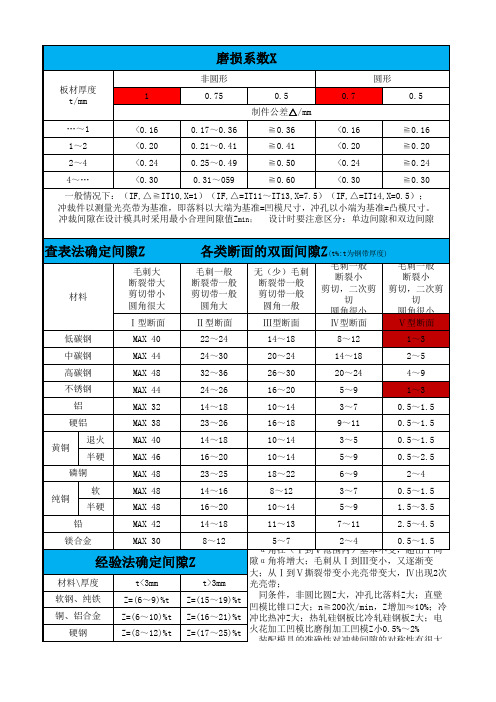
dp=(dmix+x△) -δp d
凹模配做:外向 Zmin/2上差+δd δ
Ld=(Lmin+0.5△)±0.125△即中间值 L
上述为配做法:以凸模尺寸配做凹模尺寸
规则形状凸凹模刃口尺寸偏差
基本尺寸 ≦18 >18~30 >30~80 >80~120 >120~180 >180~260 >260~360 >360~500 >500 -0.025 -0.03 -0.035 -0.04 -0.05 -0.02 凸模偏差δp δ 凹模偏差δd δ +0.02 +0.025 +0.030 +0.035 +0.040 +0.045 +0.050 +0.060 +0.070
材料
磷铜 纯铜
经验法确定间隙Z 经验法确定间隙Z
材料\厚度 软钢、纯铁 铜、铝合金 硬钢 t<3mm Z=(6~9)%t Z=(6~10)%t Z=(8~12)%t
α角在(Ⅰ到Ⅴ范围内)基本不变,超出Ⅰ间 隙α角将增大;毛刺从Ⅰ到Ⅲ变小,又逐渐变 大;从Ⅰ到Ⅴ撕裂带变小光亮带变大,Ⅳ出现2次 t>3mm 光亮带; Z=(15~19)%t 同条件,非圆比圆Z大,冲孔比落料Z大;直壁 凹模比锥口Z大;n≧200次/min,Z增加≈10%;冷 Z=(16~21)%t 冲比热冲Z大;热轧硅钢板比冷轧硅钢板Z大;电 Z=(17~25)%t 火花加工凹模比磨削加工凹模Z小0.5%~2% 装配模具的准确性对冲裁间隙的对称性有很大
各类断面的双面间隙Z 各类断面的双面间隙Z(t%:t为钢带厚度)
毛刺一般 断裂带一般 剪切带一般 圆角大 Ⅱ型断面 22~24 24~30 32~36 24~26 14~18 23~26 14~18 16~20 23~25 14~16 16~20 14~18 8~12 无(少)毛刺 断裂带一般 剪切带一般 圆角一般 Ⅲ型断面 14~18 20~24 26~30 16~20 10~14 16~18 10~14 10~14 18~22 8~12 10~14 11~13 5~7 毛刺一般 断裂小 剪切,二次剪 切 圆角很小 Ⅳ型断面 8~12 14~18 20~24 5~9 3~7 9~11 3~5 5~9 6~9 3~7 5~9 7~11 2~4 毛刺一般 断裂小 剪切,二次剪 切 圆角很小 Ⅴ型断面 1~3 2~5 4~9 1~3 0.5~1.5 0.5~1.5 0.5~1.5 0.5~2.5 2~4 0.5~1.5 1.5~3.5 2.5~4.5 0.5~1.5
刃口尺寸计算范文
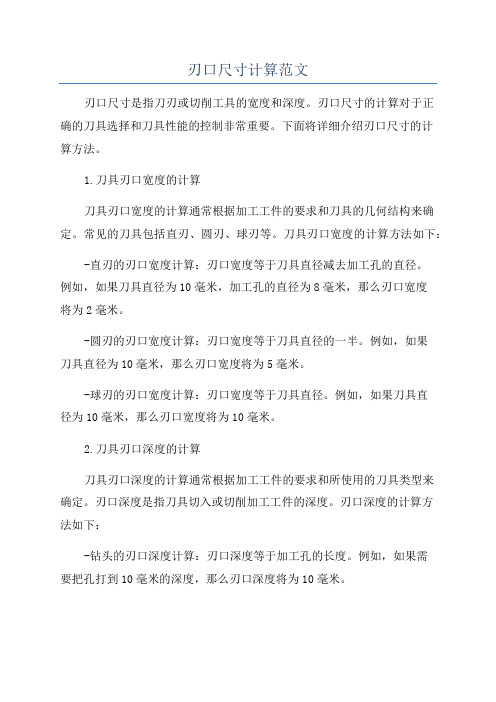
刃口尺寸计算范文刃口尺寸是指刀刃或切削工具的宽度和深度。
刃口尺寸的计算对于正确的刀具选择和刀具性能的控制非常重要。
下面将详细介绍刃口尺寸的计算方法。
1.刀具刃口宽度的计算刀具刃口宽度的计算通常根据加工工件的要求和刀具的几何结构来确定。
常见的刀具包括直刃、圆刃、球刃等。
刀具刃口宽度的计算方法如下:-直刃的刃口宽度计算:刃口宽度等于刀具直径减去加工孔的直径。
例如,如果刀具直径为10毫米,加工孔的直径为8毫米,那么刃口宽度将为2毫米。
-圆刃的刃口宽度计算:刃口宽度等于刀具直径的一半。
例如,如果刀具直径为10毫米,那么刃口宽度将为5毫米。
-球刃的刃口宽度计算:刃口宽度等于刀具直径。
例如,如果刀具直径为10毫米,那么刃口宽度将为10毫米。
2.刀具刃口深度的计算刀具刃口深度的计算通常根据加工工件的要求和所使用的刀具类型来确定。
刃口深度是指刀具切入或切削加工工件的深度。
刃口深度的计算方法如下:-钻头的刃口深度计算:刃口深度等于加工孔的长度。
例如,如果需要把孔打到10毫米的深度,那么刃口深度将为10毫米。
-铣刀的刃口深度计算:刃口深度等于刀具有效切削长度的一半。
有效切削长度是指刀具的刀尖到刀片支撑的部分的长度。
例如,如果刀具的有效切削长度为20毫米,那么刃口深度将为10毫米。
3.刀具磨损对刃口尺寸的影响刀具磨损会使刃口尺寸变大或变小,这可能影响刀具的切削性能和加工结果。
因此,在使用刀具之前和之后,应该对刀具进行检查和测量,以确保刃口尺寸符合要求。
4.提高刃口尺寸的方法有时,需要提高刃口尺寸以满足特定的加工要求。
-使用较大直径的刀具或刀片。
-使用带有刃口扩大器的刀具。
刃口扩大器是一种附件,可以将刀具的刃口尺寸扩大到所需的尺寸。
-进行粗加工后再进行细加工。
通过先使用较大刀具进行粗加工,然后再使用较小刀具进行细加工,可以达到所需的刃口尺寸。
综上所述,刃口尺寸的计算对于正确的刀具选择和刀具性能的控制非常重要。
通过准确计算刃口宽度和深度,可以确保刀具能够满足加工要求,并获得良好的加工效果。
第2章冲裁模设计-2(凸凹模刃口尺寸计算)
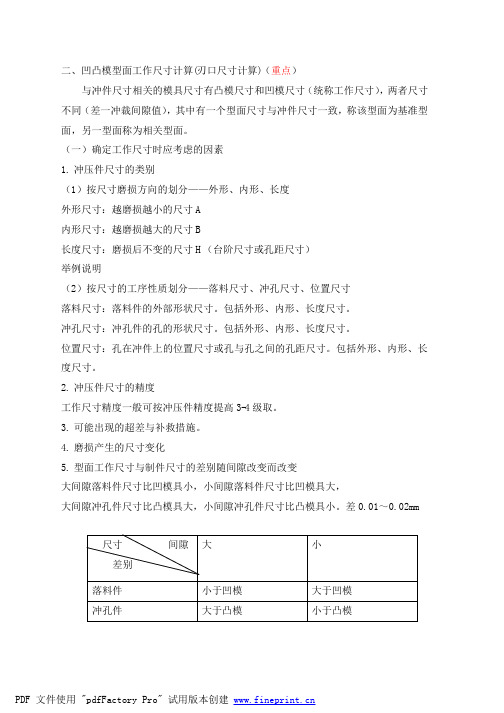
+0.02 (1)凹模尺寸 19.95 0 0 0 (2)凸模尺寸 a ' = (a − 2C min ) 0 −δ = (19.95 − 2 × 0.06) − 0.02 = 19.83 − 0.02 0 0 [ a ' = (a − C min ) 0 −δ = (19.95 − 0.06) − 0.02 = 19.89 − 0.02 ]
B0+ ∆ (内形尺寸) ∆ H ± (长度尺寸) 2 2. 基准型面尺寸计算 说明: (1) 计算结果符合标准形式
刃口尺寸的计算
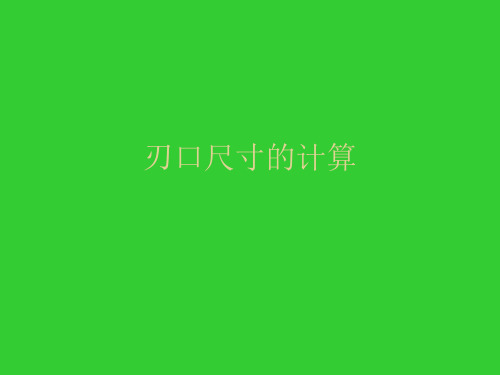
二、凸、凹模刃口尺寸的计算方法(续)
1.按凸模与凹模图样分别加工法(续)
为了保证可能的初始间隙不超过Zmax,即
T A
+Zmin≤Zmax,选取必须满足以下条件: T A ≤ Z max Z min
凸、凹模的制造公差,可按IT6~IT7级来选取,也可 查表2.4.1选取,但需校核。或取
刃口尺寸的计算
一、凸、凹模刃口尺寸计算原则
1.设计落料模先确定凹模刃口尺寸。以凹 模为基准,间隙取在凸模上,即冲裁间隙 通过减小凸模刃口尺寸来取得。 设计冲孔模先确定凸模刃口尺寸。以凸 模为基准,间隙取在凹模上,冲裁间隙通 过增大凹模刃口尺寸来取得。
凸、凹模刃口尺寸计算原则
2.根据冲模在使用过程中的磨损规律,设 计落料模时,凹模基本尺寸应取接近或等 于工件的最小极限尺寸; 设计冲孔模时,凸模基本尺寸则取接近 或等于工件孔的最大极限尺寸。 模具磨损预留量与工件制造精度有关。
A
0 0
DT D A Z min T Dmax x Z min T
(2)冲孔 0 d T d min x T
d A dT Z min 0
1 8
ห้องสมุดไป่ตู้A
d min x Z min 0
A
(3)孔心距
凸、凹模刃口尺寸计算原则
3.冲裁(设计)间隙一般选用最小合理间 隙值(Zmin)。
4.选择模具刃口制造公差时,要考虑工件 精度与模具精度的关系,即要保证工件的 精度要求,又要保证有合理的间隙值。 5.工件尺寸公差与冲模刃口尺寸的制造偏 差原则上都应按“入体”原则标注为单向 公差。但对于磨损后无变化的尺寸,一般 标注双向偏差。
刀刃刃口尺寸计算公式
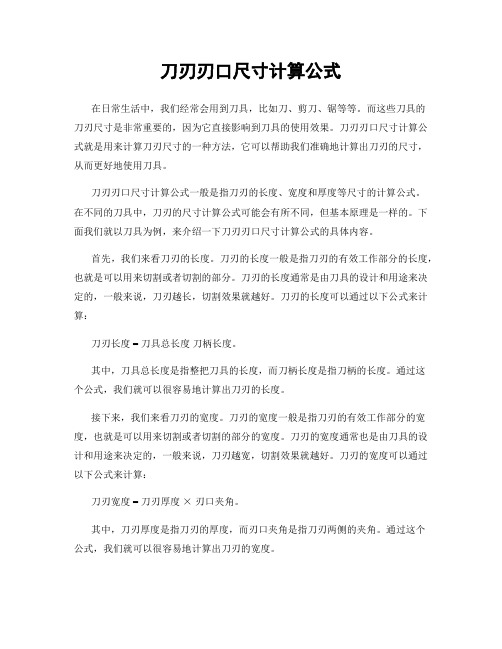
刀刃刃口尺寸计算公式在日常生活中,我们经常会用到刀具,比如刀、剪刀、锯等等。
而这些刀具的刀刃尺寸是非常重要的,因为它直接影响到刀具的使用效果。
刀刃刃口尺寸计算公式就是用来计算刀刃尺寸的一种方法,它可以帮助我们准确地计算出刀刃的尺寸,从而更好地使用刀具。
刀刃刃口尺寸计算公式一般是指刀刃的长度、宽度和厚度等尺寸的计算公式。
在不同的刀具中,刀刃的尺寸计算公式可能会有所不同,但基本原理是一样的。
下面我们就以刀具为例,来介绍一下刀刃刃口尺寸计算公式的具体内容。
首先,我们来看刀刃的长度。
刀刃的长度一般是指刀刃的有效工作部分的长度,也就是可以用来切割或者切割的部分。
刀刃的长度通常是由刀具的设计和用途来决定的,一般来说,刀刃越长,切割效果就越好。
刀刃的长度可以通过以下公式来计算:刀刃长度 = 刀具总长度刀柄长度。
其中,刀具总长度是指整把刀具的长度,而刀柄长度是指刀柄的长度。
通过这个公式,我们就可以很容易地计算出刀刃的长度。
接下来,我们来看刀刃的宽度。
刀刃的宽度一般是指刀刃的有效工作部分的宽度,也就是可以用来切割或者切割的部分的宽度。
刀刃的宽度通常也是由刀具的设计和用途来决定的,一般来说,刀刃越宽,切割效果就越好。
刀刃的宽度可以通过以下公式来计算:刀刃宽度 = 刀刃厚度×刃口夹角。
其中,刀刃厚度是指刀刃的厚度,而刃口夹角是指刀刃两侧的夹角。
通过这个公式,我们就可以很容易地计算出刀刃的宽度。
最后,我们来看刀刃的厚度。
刀刃的厚度一般是指刀刃的有效工作部分的厚度,也就是可以用来切割或者切割的部分的厚度。
刀刃的厚度通常也是由刀具的设计和用途来决定的,一般来说,刀刃越厚,切割效果就越好。
刀刃的厚度可以通过以下公式来计算:刀刃厚度 = 刀刃宽度÷刃口夹角。
通过以上的介绍,我们可以看到,刀刃刃口尺寸计算公式是非常重要的,它可以帮助我们准确地计算出刀刃的尺寸,从而更好地使用刀具。
当我们需要购买刀具或者使用刀具时,可以根据这些计算公式来选择合适的刀具,从而更好地满足我们的需要。
- 1、下载文档前请自行甄别文档内容的完整性,平台不提供额外的编辑、内容补充、找答案等附加服务。
- 2、"仅部分预览"的文档,不可在线预览部分如存在完整性等问题,可反馈申请退款(可完整预览的文档不适用该条件!)。
- 3、如文档侵犯您的权益,请联系客服反馈,我们会尽快为您处理(人工客服工作时间:9:00-18:30)。
2.4 凸模与凹模刃口尺寸的确定
一、凸、凹模刃口尺寸计算原则
生产实践发现的规律: 1.冲裁件断面都带有锥度。 由于凸、凹模之间存在着间隙,所以冲裁件断面都带有锥 度。但在冲裁件尺寸的测量和使用中: 落料件以大端尺寸为测量基准,冲孔件以小端尺寸为基 准;且落料件的大端(光面)尺寸等于凹模尺寸,冲孔件的小 端(光面)尺寸等于凸模尺寸。 2.凸模轮廓越磨越小,凹模轮廓越磨越大,结果使间隙越用越大
第二章 冲裁工艺
二、 凸、凹模刃口尺寸的计算方法
1. 凸模与凹模分别加工时(分别标注凸模、凹模尺寸和公差) 冲模的制造公差与冲裁间隙之间应满足: d p Zmax Zmin 注:凸、凹模的制造公差,可按IT6~IT7级来选取,也可 查课本P63表2-10选取,但需校核。
P ≤ 0.4Z max Z min
适用于:异形或复杂刃口。 设计时:基准件的刃口尺寸及制造公差应详细标注,非基准 件上只标注公称尺寸,但在图样上注明:“凸(凹)模刃口按凹
(凸)模实际刃口尺寸配作,保证最小双面合理间隙值Zmin”。
第二章 冲裁工艺
3.凸模与凹模配合加工刃口尺寸计算 (1)根据磨损后轮廓变化情况,正确判断出模具刃口尺寸类型:
d 落料: Dd ( Dmax x) 0 0.025 0.025 (36 0.5 0.62) 0 m m 35.690 mm
D p ( Dd 2c min ) 0 p
0 (35.69 0.04) 0 m m 35 . 65 0.06 0.016 m m
第二章 冲裁工艺
计算原则: 观察冲压件,寻找计算的依据,
根据观察的结果确定刃口尺寸计算和选择公差的原则:
1、先确定基准件
落料:以凹模为基准,间隙取在凸模上; 冲孔: 以凸模为基准,间隙取在凹模上。
2、考虑冲模的磨损规律
落料模:凹模基本尺寸应取接近于或等于工件的最小极限尺寸;
冲孔模:凸模基本尺寸应取接近于或等于工件的最大极限尺寸。
Zmax Zmin (0.06 0.04)mm 0.02mm
由公式表查得: 2 60.12 mm 为IT12级,取x = 0.75; 0
360 为IT14级,取x = 0.5; 0.62 mm
设凸、凹模分别按IT6和IT7级加工制造(公差也可直接查书),
冲孔:
0 0 d p (dmin x)0 (6 0.75 0.12) mm 6.09 p 0.008 0.008 mm
校核:
0.06 0.025 0.04 0.02
不满足间隙要求
第二章 冲裁工艺
由此可知,只有缩小
p , d
,提高制造精度,才能保证间隙
在合理范围内,此时可取
p 0.4 0.02 0.008mm, d 0.6 0.02 0.012mm
故
0.012 Dd 35 .69 0 mm
d 0.012 0.012 d d (d p Z min ) 0 (6.09 0.04) 0 m m 6.130 mm
第二章 冲裁工艺
校核: p d Z max Z min 0.008 0.012 0.06 0.04 孔距尺寸:
Ld =18±0.125×2×0.09 = (18±0.023)mm
1/8并冠以(±)。
简单的原则:磨损后不变的尺寸取平均值,磨 损后变大的尺寸取较小值,磨损后变小的 尺寸取较大值。
例2.4.2
第二章 冲裁工艺
练习题13: 计算如图所示零件,材料Q235,
t=0.5mm,冲裁凸、凹模刃口尺寸及公差。 解:由图知,该零件属于一般的冲孔落料件.
查表得 Z min 0.04mm , Zmax 0.06mm
(2)冲孔:设工件孔的尺寸为 d 0
0 凸模刃口尺寸: d p (d min x) p
凹模刃口尺寸: d d (d p Z min ) 0
d
(3)孔心距
Ld L / 8
其中: 为工件制造公差,d D 为工件公称尺寸,x 为磨 min max
损系数。
即磨损后尺寸是变大,变小还是不变。
(2)根据尺寸类型,采用不同计算公式。 磨损后变大的尺寸,采用分开加工时的落料凹模尺寸计算公式。 磨损后变小的尺寸,采用分开加工时的冲孔凸模尺寸计算公式。 磨损后不变的尺寸,采用分开加工时的孔心距尺寸计算公式。 (3)刃口制造偏差可按工件相应部位公差值的1/4来选取。对于 刃口尺寸磨损后无变化的制造偏差值可取工件相应部位公差值的
例2.4.1
第二章 冲裁工艺
2、凸模与凹模配合加工:不需要校合 d p Zmax Zmin
是先按尺寸和公差制造出凹模或凸模其中一个(基准件), 然后依此为基准再按最小合理间隙配做另一件。
优点:容易保证凸、凹模间隙很小,而且制造还可以放大基准
件的制造公差,使制造容易。
缺点:凸模、凹模不能互换
d ≤ 0.6Z max Z min
当无现成资料时可取
适用于:圆形或简单刃口。
优点:具有互换性、制造周期短,但Zmin不易保证,需提高
加工精度,增加制造难度。
第二章 冲裁工艺
0 (1) 落料:设工件尺寸为 D
: D ( D Z )0 ( D x Z )0 p d min p max min p
第二章 冲裁工艺
3、冲裁(设计)间隙一般选用最小合理间隙值(Zmin)。
4、 凸、凹模刃口制造公差应合理
形状简单的刃口制造偏差:按IT6~IT7级或查表; 形状复杂的刃口制造偏差:取冲裁件相应部位公差的1/4; 对刃口尺寸磨损后无变化的制造偏差:取冲裁件相应部位公 差的1/8并冠以(±); 5、工件和模具刃口尺寸偏差应按“入体”原则标注单向公差。 落料件标注单项负公差;冲孔件标注单项正公差。 提问:凸模、凹模应该如何标注公差