金属基烧结摩擦片制造工艺的制作方法
某公司摩擦片工艺流程
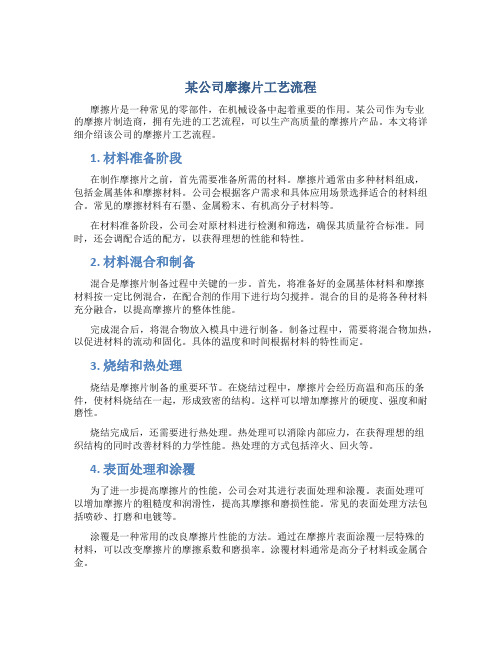
某公司摩擦片工艺流程摩擦片是一种常见的零部件,在机械设备中起着重要的作用。
某公司作为专业的摩擦片制造商,拥有先进的工艺流程,可以生产高质量的摩擦片产品。
本文将详细介绍该公司的摩擦片工艺流程。
1. 材料准备阶段在制作摩擦片之前,首先需要准备所需的材料。
摩擦片通常由多种材料组成,包括金属基体和摩擦材料。
公司会根据客户需求和具体应用场景选择适合的材料组合。
常见的摩擦材料有石墨、金属粉末、有机高分子材料等。
在材料准备阶段,公司会对原材料进行检测和筛选,确保其质量符合标准。
同时,还会调配合适的配方,以获得理想的性能和特性。
2. 材料混合和制备混合是摩擦片制备过程中关键的一步。
首先,将准备好的金属基体材料和摩擦材料按一定比例混合,在配合剂的作用下进行均匀搅拌。
混合的目的是将各种材料充分融合,以提高摩擦片的整体性能。
完成混合后,将混合物放入模具中进行制备。
制备过程中,需要将混合物加热,以促进材料的流动和固化。
具体的温度和时间根据材料的特性而定。
3. 烧结和热处理烧结是摩擦片制备的重要环节。
在烧结过程中,摩擦片会经历高温和高压的条件,使材料烧结在一起,形成致密的结构。
这样可以增加摩擦片的硬度、强度和耐磨性。
烧结完成后,还需要进行热处理。
热处理可以消除内部应力,在获得理想的组织结构的同时改善材料的力学性能。
热处理的方式包括淬火、回火等。
4. 表面处理和涂覆为了进一步提高摩擦片的性能,公司会对其进行表面处理和涂覆。
表面处理可以增加摩擦片的粗糙度和润滑性,提高其摩擦和磨损性能。
常见的表面处理方法包括喷砂、打磨和电镀等。
涂覆是一种常用的改良摩擦片性能的方法。
通过在摩擦片表面涂覆一层特殊的材料,可以改变摩擦片的摩擦系数和磨损率。
涂覆材料通常是高分子材料或金属合金。
5. 检测和质量控制在摩擦片制备完成后,公司会进行严格的检测和质量控制,以确保产品的质量符合要求。
常见的检测方法包括尺寸测量、硬度测试、摩擦性能测试等。
质量控制是整个制备过程中不可或缺的一环,通过各种控制措施,如工艺参数控制、设备状态监测和操作规范等,确保产品的稳定性和一致性。
汽车摩擦片的加工工艺
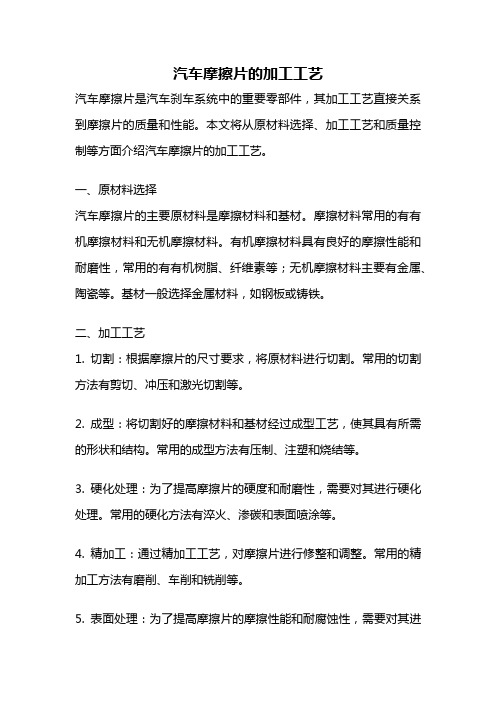
汽车摩擦片的加工工艺汽车摩擦片是汽车刹车系统中的重要零部件,其加工工艺直接关系到摩擦片的质量和性能。
本文将从原材料选择、加工工艺和质量控制等方面介绍汽车摩擦片的加工工艺。
一、原材料选择汽车摩擦片的主要原材料是摩擦材料和基材。
摩擦材料常用的有有机摩擦材料和无机摩擦材料。
有机摩擦材料具有良好的摩擦性能和耐磨性,常用的有有机树脂、纤维素等;无机摩擦材料主要有金属、陶瓷等。
基材一般选择金属材料,如钢板或铸铁。
二、加工工艺1. 切割:根据摩擦片的尺寸要求,将原材料进行切割。
常用的切割方法有剪切、冲压和激光切割等。
2. 成型:将切割好的摩擦材料和基材经过成型工艺,使其具有所需的形状和结构。
常用的成型方法有压制、注塑和烧结等。
3. 硬化处理:为了提高摩擦片的硬度和耐磨性,需要对其进行硬化处理。
常用的硬化方法有淬火、渗碳和表面喷涂等。
4. 精加工:通过精加工工艺,对摩擦片进行修整和调整。
常用的精加工方法有磨削、车削和铣削等。
5. 表面处理:为了提高摩擦片的摩擦性能和耐腐蚀性,需要对其进行表面处理。
常用的表面处理方法有镀铬、镀锌和喷漆等。
三、质量控制汽车摩擦片的质量直接关系到汽车的行驶安全性,因此在加工过程中需要进行严格的质量控制。
主要包括以下几个方面:1. 原材料检验:对摩擦材料和基材进行化学成分和物理性能的检验,确保其符合相关标准要求。
2. 加工过程控制:在每个加工环节都需要进行严格的控制,包括尺寸、形状和表面质量等。
3. 硬度检测:对摩擦片进行硬度测试,确保其硬度达到要求,以保证刹车性能。
4. 摩擦系数测试:通过摩擦系数测试,评估摩擦片的摩擦性能,确保其符合相关标准要求。
5. 耐磨性测试:通过模拟实际使用条件下的磨损测试,评估摩擦片的耐磨性能。
6. 相关性能测试:对摩擦片的其他性能指标,如抗拉强度、冲击韧性等进行测试,确保其满足设计要求。
通过以上的加工工艺和质量控制,可以保证汽车摩擦片的质量和性能。
同时,加工过程中需要严格遵守相关的安全操作规程,确保加工过程的安全和环保。
一种铜基粉末冶金摩擦材料及其制备方法

一种铜基粉末冶金摩擦材料及其制备方法
铜基粉末冶金摩擦材料是一种具有优异摩擦性能的材料,广泛应用于摩擦副的
制造和磨损部件的修复。
这种材料的制备方法简单,成本相对较低。
制备铜基粉末冶金摩擦材料的方法包括以下几个步骤:
1. 材料准备:选择高纯度的铜粉末作为基础材料。
铜的纯度直接关系到最终制
备材料的性能,因此需选择高纯度的铜粉末。
2. 添加合金元素:在铜粉末中添加一定比例的合金元素,如锡、铅、锌等。
合
金元素的添加可以改善材料的硬度、磨损性能和耐蚀性。
3. 混合和球磨:将铜粉末和合金元素混合均匀后,置于球磨机中进行球磨。
球
磨的目的是使粉末颗粒更加细小,并增加合金元素的分散度。
4. 烧结:将球磨后的混合粉末置于加热炉中进行烧结。
烧结的温度和时间取决
于材料的成分和预期的性能。
通过以上步骤制备的铜基粉末冶金摩擦材料具有以下优势:
1. 优异的摩擦性能:铜基材料具有良好的摩擦性能,可以在高温和高压下保持
较低的摩擦系数和磨损率。
2. 耐磨性强:铜基材料的制备方法使得其颗粒密度高且均匀分布,从而提高了
材料的硬度和耐磨性。
3. 容易修复和再利用:铜基材料的制备方法可以根据需要对材料进行修复和再
利用,降低了材料的浪费和成本。
总之,铜基粉末冶金摩擦材料以其优异的摩擦性能和制备方法的简单性成为了
摩擦材料领域的热门选择。
在未来的发展中,我们可以进一步研究和改进制备方法,以满足不同领域对于摩擦材料的需求。
摩擦片生产工艺流程
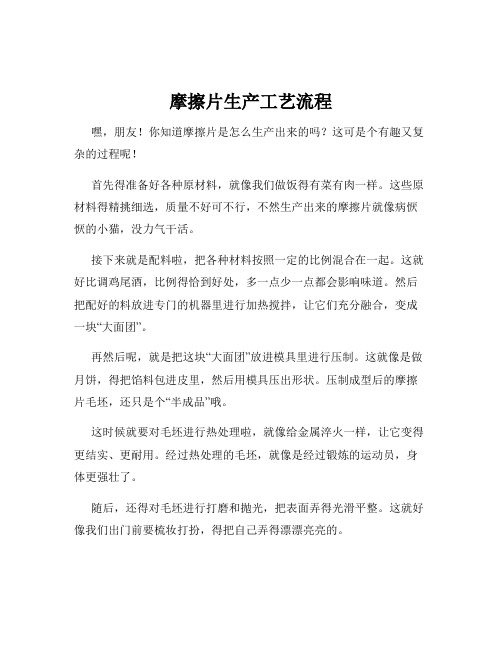
摩擦片生产工艺流程
嘿,朋友!你知道摩擦片是怎么生产出来的吗?这可是个有趣又复杂的过程呢!
首先得准备好各种原材料,就像我们做饭得有菜有肉一样。
这些原材料得精挑细选,质量不好可不行,不然生产出来的摩擦片就像病恹恹的小猫,没力气干活。
接下来就是配料啦,把各种材料按照一定的比例混合在一起。
这就好比调鸡尾酒,比例得恰到好处,多一点少一点都会影响味道。
然后把配好的料放进专门的机器里进行加热搅拌,让它们充分融合,变成一块“大面团”。
再然后呢,就是把这块“大面团”放进模具里进行压制。
这就像是做月饼,得把馅料包进皮里,然后用模具压出形状。
压制成型后的摩擦片毛坯,还只是个“半成品”哦。
这时候就要对毛坯进行热处理啦,就像给金属淬火一样,让它变得更结实、更耐用。
经过热处理的毛坯,就像是经过锻炼的运动员,身体更强壮了。
随后,还得对毛坯进行打磨和抛光,把表面弄得光滑平整。
这就好像我们出门前要梳妆打扮,得把自己弄得漂漂亮亮的。
最后就是检查和测试啦,要看看这摩擦片是不是符合标准。
这就像老师批改作业,一个小错误都不能放过。
你想想,如果生产摩擦片的时候马马虎虎,那装在车上的摩擦片不得“闹脾气”?刹车不灵可就危险啦!所以啊,每一个步骤都得认认真真,不能有丝毫马虎。
总之,摩擦片的生产工艺流程就像是一场精心编排的舞蹈,每一个动作都要准确无误,才能跳出精彩的舞步,生产出高质量的摩擦片。
摩擦片生产工艺
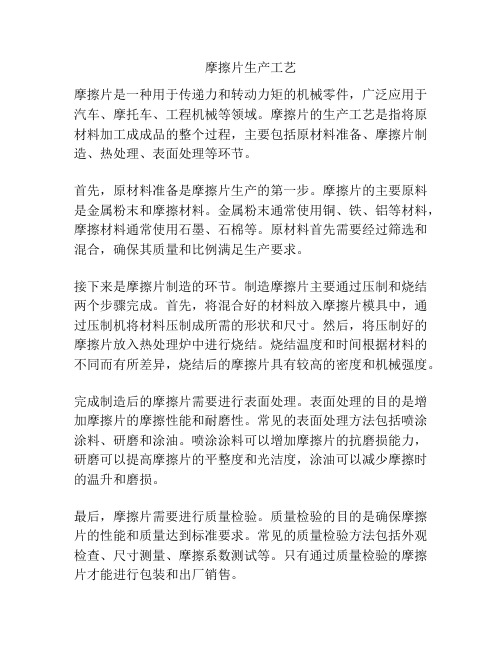
摩擦片生产工艺
摩擦片是一种用于传递力和转动力矩的机械零件,广泛应用于汽车、摩托车、工程机械等领域。
摩擦片的生产工艺是指将原材料加工成成品的整个过程,主要包括原材料准备、摩擦片制造、热处理、表面处理等环节。
首先,原材料准备是摩擦片生产的第一步。
摩擦片的主要原料是金属粉末和摩擦材料。
金属粉末通常使用铜、铁、铝等材料,摩擦材料通常使用石墨、石棉等。
原材料首先需要经过筛选和混合,确保其质量和比例满足生产要求。
接下来是摩擦片制造的环节。
制造摩擦片主要通过压制和烧结两个步骤完成。
首先,将混合好的材料放入摩擦片模具中,通过压制机将材料压制成所需的形状和尺寸。
然后,将压制好的摩擦片放入热处理炉中进行烧结。
烧结温度和时间根据材料的不同而有所差异,烧结后的摩擦片具有较高的密度和机械强度。
完成制造后的摩擦片需要进行表面处理。
表面处理的目的是增加摩擦片的摩擦性能和耐磨性。
常见的表面处理方法包括喷涂涂料、研磨和涂油。
喷涂涂料可以增加摩擦片的抗磨损能力,研磨可以提高摩擦片的平整度和光洁度,涂油可以减少摩擦时的温升和磨损。
最后,摩擦片需要进行质量检验。
质量检验的目的是确保摩擦片的性能和质量达到标准要求。
常见的质量检验方法包括外观检查、尺寸测量、摩擦系数测试等。
只有通过质量检验的摩擦片才能进行包装和出厂销售。
综上所述,摩擦片的生产工艺包括原材料准备、摩擦片制造、热处理、表面处理和质量检验等环节。
各个环节都很重要,只有在保证每个环节的质量和工艺稳定的情况下,才能生产出满足要求的摩擦片产品。
烧结生产工艺流程

烧结生产工艺流程烧结是一种常用的金属材料加工工艺,它通过高温加热金属粉末使其颗粒之间发生熔结,从而形成一体化的金属坯料。
烧结工艺流程主要包括原料准备、配料、混合、成型、烧结和后处理。
下面将详细介绍烧结生产工艺流程。
首先是原料准备和配料阶段。
原料主要包括金属粉末、添加剂和润滑剂。
金属粉末是烧结的主要原材料,而添加剂的选择是为了改善烧结工艺中的某些性能。
润滑剂的作用是降低粉末颗粒之间的摩擦力,便于后续工艺中的成型和去除氧化层。
配料时需要进行粉末的筛分和加入正确比例的各种原料。
其次是混合阶段。
将各种原料放入搅拌罐中进行搅拌混合。
混合的目的是将金属粉末与添加剂和润滑剂充分混合,保证原料的均匀性和稳定性。
搅拌时间和速度要根据具体原料的特性进行合理的控制。
然后是成型阶段。
混合好的原料需要通过成型设备进行成型,常见的成型方法有压制成型和注射成型两种。
压制成型是将混合好的原料放入模具中,通过压力使原料形成所需形状。
注射成型是将混合好的原料注入注射机中,通过高压使原料进入模具形成所需形状。
成型后的坯体需要经过脱模处理。
接下来是烧结阶段。
烧结是将成型的坯体置于高温炉中进行加热处理。
烧结温度要根据具体材料的特性进行合理的设定,一般在金属材料的熔点以下进行烧结。
烧结过程中,金属粉末颗粒之间会发生熔结,粘接成为一体化的坯体。
烧结后的坯体需要经过冷却和退火处理。
最后是后处理阶段。
烧结后的坯体需要进行后处理来改善其性能。
常见的后处理方法有热处理、表面处理和机械加工等。
热处理可以使金属材料的组织结构得到优化和改善;表面处理可以提高材料的耐蚀性和耐磨性;机械加工可以对烧结坯体进行切削、打磨等操作,使其达到所需的尺寸和形状。
总的来说,烧结生产工艺流程包括原料准备、配料、混合、成型、烧结和后处理等几个主要步骤。
每个步骤的操作都需要严格控制和合理调控,以确保最终产品的质量和性能。
烧结工艺的应用广泛,适用于制造各种金属制品,如零件、工具和机械等。
铜基摩擦片生产流程
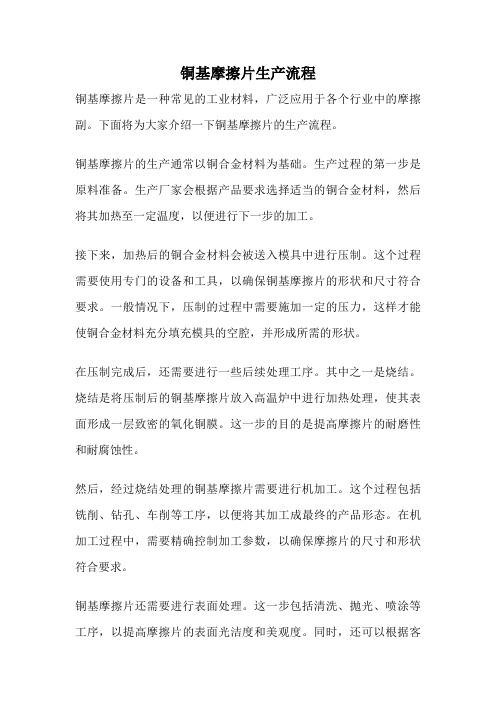
铜基摩擦片生产流程铜基摩擦片是一种常见的工业材料,广泛应用于各个行业中的摩擦副。
下面将为大家介绍一下铜基摩擦片的生产流程。
铜基摩擦片的生产通常以铜合金材料为基础。
生产过程的第一步是原料准备。
生产厂家会根据产品要求选择适当的铜合金材料,然后将其加热至一定温度,以便进行下一步的加工。
接下来,加热后的铜合金材料会被送入模具中进行压制。
这个过程需要使用专门的设备和工具,以确保铜基摩擦片的形状和尺寸符合要求。
一般情况下,压制的过程中需要施加一定的压力,这样才能使铜合金材料充分填充模具的空腔,并形成所需的形状。
在压制完成后,还需要进行一些后续处理工序。
其中之一是烧结。
烧结是将压制后的铜基摩擦片放入高温炉中进行加热处理,使其表面形成一层致密的氧化铜膜。
这一步的目的是提高摩擦片的耐磨性和耐腐蚀性。
然后,经过烧结处理的铜基摩擦片需要进行机加工。
这个过程包括铣削、钻孔、车削等工序,以便将其加工成最终的产品形态。
在机加工过程中,需要精确控制加工参数,以确保摩擦片的尺寸和形状符合要求。
铜基摩擦片还需要进行表面处理。
这一步包括清洗、抛光、喷涂等工序,以提高摩擦片的表面光洁度和美观度。
同时,还可以根据客户需求进行特殊涂层的处理,以改善摩擦片的摩擦性能和耐磨性。
经过以上的一系列工序,铜基摩擦片的生产流程基本完成。
生产出的摩擦片经过质量检验合格后,即可投入市场使用。
总的来说,铜基摩擦片的生产流程包括原料准备、压制、烧结、机加工和表面处理等多个环节。
每个环节都需要精确控制参数,以确保最终产品的质量和性能符合要求。
铜基摩擦片在工业中的应用广泛,它能够提供良好的耐磨性和耐腐蚀性,为各个行业的机械设备提供可靠的摩擦副。
烧结金属膜
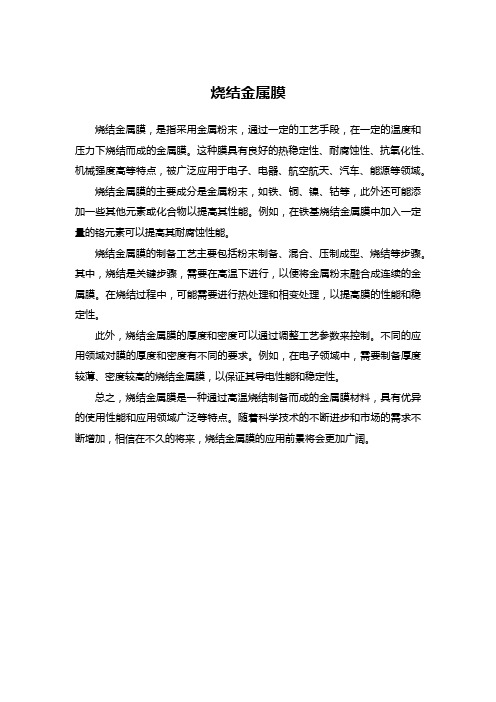
烧结网和烧结毡的区别1、烧结网烧结网是将同种或不同的多个单层不锈钢丝编织网叠放在一起,经过烧结、加压、轧制等工艺,采用真空烧结至1100℃后扩散固溶制作而成的,具有较高的机械强度和整体刚性的新型过滤材料。
最广泛使用的烧结网是五层烧结网,如图1所示。
图1 五层烧结网2、烧结毡不锈钢烧结毡又称金属无纺布,是采用极其精细的不同丝经的金属纤维(直径精确到微米)经无纺铺制、叠配、高温至1100℃烧结而成的一种新型过滤材料,如图2所示。
图2 不锈钢烧结毡3、区别3.1烧结工艺烧结网的烧结工艺是把几层不锈钢金属丝网按照不同的结构叠放在一起烧结,由图1可以看出烧结网的结构是有序的。
烧结毡的烧结工艺是无纺铺制,是把金属纤维杂乱无章的放在一起烧结的,如图3所示。
图3 若干金属纤维3.2 特性由于烧结网与烧结毡的制作工艺不一样,所以也具有不同的过滤特性。
A、纳污量由于烧结毡是由不同孔径的金属纤维经过无纺铺制烧结而成的,烧结过程中便会形成具有不同的孔径层的空梯度,所以烧结毡比烧结网具有更大的纳污量。
B、清洗周期由于烧结毡具有比烧结网更大的纳污量,所以其清洗的周期要长于烧结网。
C、盲孔率由于烧结网是把不锈钢丝网按照特殊结构一层一层的叠放在一起进行烧结的,其整体结构是整齐有序的,所以,相对于无纺铺制的烧结毡,烧结网的盲孔率几乎等于0,而烧结毡有一定的盲孔率。
D、过滤精度由于烧结毡具有一定的盲孔率,其过滤精度范围只有5—60um,而烧结网的过滤精度范围有1—200um,所以,烧结网的过滤精度要大于烧结毡的过滤精度。
综上所述,烧结网具有较大的过滤范围;烧结毡具有较大的纳污量,用户可根据自身的实际需求选取过滤材料。
湖南省双金属烧结的工艺流程和注意事项
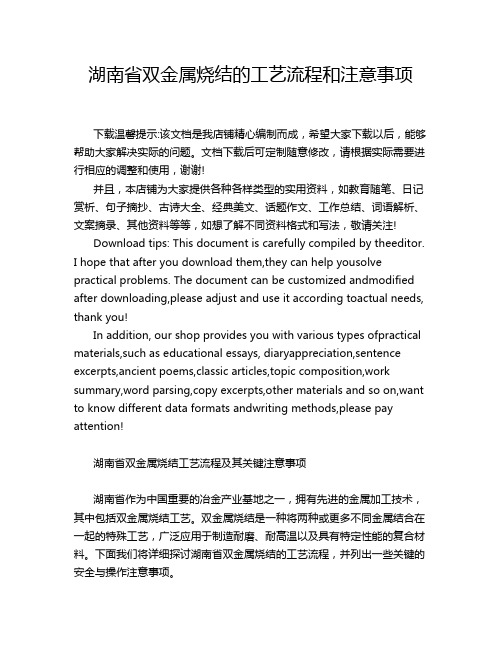
湖南省双金属烧结的工艺流程和注意事项下载温馨提示:该文档是我店铺精心编制而成,希望大家下载以后,能够帮助大家解决实际的问题。
文档下载后可定制随意修改,请根据实际需要进行相应的调整和使用,谢谢!并且,本店铺为大家提供各种各样类型的实用资料,如教育随笔、日记赏析、句子摘抄、古诗大全、经典美文、话题作文、工作总结、词语解析、文案摘录、其他资料等等,如想了解不同资料格式和写法,敬请关注!Download tips: This document is carefully compiled by theeditor.I hope that after you download them,they can help yousolve practical problems. The document can be customized andmodified after downloading,please adjust and use it according toactual needs, thank you!In addition, our shop provides you with various types ofpractical materials,such as educational essays, diaryappreciation,sentence excerpts,ancient poems,classic articles,topic composition,work summary,word parsing,copy excerpts,other materials and so on,want to know different data formats andwriting methods,please pay attention!湖南省双金属烧结工艺流程及其关键注意事项湖南省作为中国重要的冶金产业基地之一,拥有先进的金属加工技术,其中包括双金属烧结工艺。
- 1、下载文档前请自行甄别文档内容的完整性,平台不提供额外的编辑、内容补充、找答案等附加服务。
- 2、"仅部分预览"的文档,不可在线预览部分如存在完整性等问题,可反馈申请退款(可完整预览的文档不适用该条件!)。
- 3、如文档侵犯您的权益,请联系客服反馈,我们会尽快为您处理(人工客服工作时间:9:00-18:30)。
金属基烧结摩擦片制造工艺的制作方法专利名称:金属基烧结摩擦片制造工艺的制作方法技术领域本发明属于摩擦材料制造技术领域,特别涉及烧结摩擦片制造工艺。
背景技术金属基烧结摩擦材料由于具有强度高、耐磨损、导热性好,并具有较高的摩擦系数、摩擦系数稳定等特点而成为制造离合器、制动器的关键材料,广泛用于汽车、摩托车、列车、飞机等运输工具及石油钻井、风力发电等机械中。
在列车车辆制造领域,用于制造制动闸瓦和制动闸片。
这类材料以金属为基体,含有均匀分布的硬质粒子和润滑粒子。
金属基体的含量对材料的强度和韧性起主导作用,硬质粒子和润滑粒子均为脆性材料,其含量控制着制品的摩擦系数和磨损量。
提高脆性材料的含量,有利于增加摩擦系数、降低磨损量,同时,降低制品的强度和韧性。
随着制动负荷的增加,如列车速度的提高,载重量增加,对摩擦制动材料性能提出了越来越高的要求,这就要求材料在保证基体强度的同时,进一步提高摩擦系数和降低磨损量。
这对摩擦材料的制造工艺提出了更高的要求。
目前国内外传统的制造工艺为原材料混合、冷压制成型、压力烧结成型。
压力烧结成型是将冷压制成型的毛坯叠放在一起,放入加压烧结炉中,在保护性气氛下加压烧结。
由于炉温分段固定加热,温区均匀性不足,造成制品质量难于均匀,同时,烧结压力调节范围有限,一般为1-5MPa 这个范围,难于进一步提高制品的密度和使制品有较复杂的形状。
另外,电阻加热炉升温、降温均需要较长时间,这使得每炉的烧结时间约为8-10小时,因此,压力烧结成型工序生产效率低、能耗大。
为提高制品的密度和使制品具有较复杂的形状,满足高速列车对高能量制动闸片的制造要求,国际专利WO97/43560采用的制造高速列车制动闸片的工艺为原材料混合、冷压制成型、第一次烧结、热锻成型、第二次烧结。
这种工艺可以提高制品密度,允许制品形状较复杂和尺寸精度好,然而,由于工艺中采用了3次加热工序,因此,制造时间长,制造成本显著提高。
发明内容本发明的目的是提出一种金属基烧结摩擦片制造工艺,工艺简单,制造效率高、成本低、产品性能优良,尺寸精度高。
本发明为实现上述目的所采用的技术方案是一种金属基烧结磨擦片制造工艺第一步混合原料粉末混合均匀;第二步冷压制成型将模具内表面涂润滑脂,将混合好的粉料及护套或护环置入模具中,在常温及100-600MPa压力下,压制出所需的毛坯;第三步电流直加热模压烧结成型将冷压制成型毛坯置入高强石墨或钢质模具中,将模具连同毛坯置入炉中,炉内通入氢气和氮气,或启动真空系统,真空度达70mmHg,然后,对毛坯施加电压3-15V、大电流10-200A,同时,对毛坯施加压力5-100MPa,烧结温度750-1500℃,保温时间为1-30分钟,随炉冷却至100℃出炉。
所述第一步混合将各组份材料按比例加入混合器中进行混合,首先混合密度较大的金属粉,如铜粉、锡粉、铁粉和铝粉等,再加入硬质粒子如Al2O3、SiO2、硬质合金等,最后加入石墨。
所述各种粉末粒子的尺寸小于800μm。
在混合时,可混入混合物重量的0.2-1%的轻质油或易挥发性溶剂。
所述第三步电流直加热模压烧结成型对毛坯施加压力,压力随毛坯温度升高而逐渐增加。
所述第三步电流直加热模压烧结成型对于铜基烧结材料,烧结温度为750-1000℃,保温时间为1-20分钟;对于铁基烧结材料,烧结温度为900-1500℃,保温时间为2-30分钟,随炉冷却至100℃出炉。
本发明工艺简单粉末原料混合、冷压制成型、电流直加热模压烧结成型。
这种工艺具有如下优点1.基体金属材料可以是铜基,也可以是铁基;2.制品在模具内成型,成型压力调节范围大,使制品密度高、尺寸精度好、允许形状复杂,可实现摩擦材料与护套、护环完整结合;3.将低电压、大电流直接施加在坯料上进行加热,烧结时间短、效率高、节能效果显著;4.烧结压力和烧结温度可灵活匹配,调节范围大,可实现半凝固状态下的压力烧结,这允许进一步提高脆性粒子的含量,使材料的摩擦磨损性能实现在更大范围内的调节。
本发明尤其适用于制造铁路车辆制动闸片和风力发电设备制动闸片。
制造的闸片在高温高速制动条件下,具有高的摩擦系数,良好的耐磨性,更适于时速200公里以上的高速列车和大功率风力发电机使用。
附图说明图1是闸片制动块的制造工序。
图2是定速摩擦试验机转速为200r/Min时制动块的摩擦系数。
图3是定速摩擦试验机转速为500r/Min时制动块的摩擦系数。
图4是定速摩擦试验机转速为2000r/Min时制动块的摩擦系数。
图5是定速摩擦试验机转速为3000r/Min时制动块的摩擦系数。
图6是1∶1制动试验台测试的最高速度为300km/H时制动闸片的瞬时摩擦系数。
具体实施方式结合附图对本发明进行详细叙述实施例1各组份重量百分比如下铜粉54%,锡粉6%,铝粉3%,铁粉12%,Al2O36%,SiO29%,石墨10%。
首先将金属粉进行混合3-5min,再加入Al2O3和SiO2混合3-5min,最后加入石墨和混合粉重量的0.5%煤油,混合5-10min。
将适合重量的混合粉放入模具中,在500MPa的压力下压制5-10秒,取出后成为冷压制毛坯。
将冷压制毛坯置入热模压模具3中,启动真空系统,当真空度达70mmHg 时,通过上下凸模4、5对毛坯施加3MPa压力,同时,启动加热电流6,加热时间在2-3min左右,毛坯温度达到800℃,对毛坯施加50MPa压力,保温2min,随炉冷却至100℃出炉,制成制动块。
制得的材料的硬度HB70,密度为5.6g/Cm3。
在GF150D型定速摩擦试验机上,比压为0.6MPa,摩擦转速为200,500,2000,3000r/Min,测得的摩擦系数为0.49(图2),0.45(图3),0.42(图4),0.36(图5),磨损量为0.41cm3/MJ。
同样条件下,采用传统工艺制造制动块,将冷压制毛坯置入钟罩式加压烧结炉中,烧结气氛为氢气,压力为3.5MPa,经2-3h加热,温度达到800℃,保温时间为1小时,随炉冷却4-6h至100℃出炉,制成制动块。
制得的材料的硬度HB60,密度为5.0g/Mm3。
在GF150D型定速摩擦试验机上,比压为0.6Mpa,摩擦转速为200,500,2000,3000r/Min,测得的摩擦系数为0.44,0.45,0.39,0.35,磨损量为0.65cm3//MJ。
两种工艺比较可知,本发明工艺的烧结成型时间远小于传统工艺,而制品的密度高于传统工艺,由于制品的密度高,使耐磨性能明显提高。
采用本发明制造出了符合国际铁路联盟标准的高速列车铜基烧结制动闸片,将制动闸片在1∶1制动试验台上进行了最高速度达300km/H测试,测试结果表明,瞬时摩擦系数完全处于国际铁路联盟标准的控制范围内(图6),磨损量为0.38cm3/MJ。
实施例2各组份重量百分比如下铁粉60%,铜粉10%,锡粉5%,铝粉5%,Al2O35%,SiO25%,石墨10%。
首先将金属粉进行混合3-5min,再加入Al2O3和SiO2混合3-5min,最后加入石墨和混合粉重量的0.5%煤油,混合5-10min。
将适合重量的混合粉放入模具中,在600MPa的压力下压制5-10秒,取出后成为冷压制毛坯。
将冷压制毛坯置入热模压模具3中,启动真空系统,当真空度达70mmHg 时,通过上下凸模4、5对毛坯施加5MPa压力,同时,启动加热电流6,加热时间在2-3min左右,毛坯温度达到1000℃,对毛坯施加60MPa压力,保温2min,随炉冷却至100℃出炉,制成制动块。
制得的材料的硬度HB210,密度为4.8g/Cm3。
在GF150D型定速摩擦试验机上,比压为0.6MPa,摩擦转速为200,500,2000,3000r/Min,测得的摩擦系数为0.39,0.35,0.32,0.29,磨损量为0.39cm3/MJ。
同样条件下,采用传统工艺制造制动块,将冷压制毛坯置入钟罩式加压烧结炉中,烧结气氛为氢气,压力为3.5MPa,经3-4h加热,温度达到1000℃,保温时间为1.5小时,随炉冷却4-6h至100℃出炉,制成制动块。
制得的材料的硬度HB150,密度为4.6g/Mm3。
在GF150D型定速摩擦试验机上,比压为0.6Mpa,摩擦转速为200,500,2000,3000r/Min,测得的摩擦系数为0.34,0.35,0.29,0.28,磨损量为0.45cm3//MJ。
权利要求1.一种金属基烧结磨擦片制造工艺,其特征是第一步混合原料粉末混合均匀;第二步冷压制成型将模具内表面涂润滑脂,将混合好的粉料及护套或护环置入模具中,在常温及100-600MPa压力下,压制出所需的毛坯;第三步电流直加热模压烧结成型将冷压制成型毛坯置入高强石墨或钢质模具中,将模具连同毛坯置入炉中,炉内通入氢气和氮气,或启动真空系统,真空度达70mmHg,然后,对毛坯施加电压3-15V、大电流10-200A,同时,对毛坯施加压力5-100MPa,烧结温度750-1500℃,保温时间为1-30分钟,随炉冷却至100℃出炉。
2.根据权利要求1所述的一种金属基烧结磨擦片制造工艺,其特征是第一步混合将各组份材料按比例加入混合器中进行混合,首先混合密度较大的金属粉,如铜粉、锡粉、铁粉和铝粉等,再加入硬质粒子如A12O3、SiO2、硬质合金等,最后加入石墨。
3.根据权利要求1所述的一种金属基烧结磨擦片制造工艺,其特征是各种原料粉末粒子的尺寸小于800μm。
4.根据权利要求1所述的一种金属基烧结磨擦片制造工艺,其特征是第一步混合可混入混合物重量的0.2-1%的轻质油或易挥发性溶剂。
5.根据权利要求1所述的一种金属基烧结磨擦片制造工艺,其特征是第三步电流直加热模压烧结成型对毛坯施加压力,压力随毛坯温度升高而逐渐增加。
6.根据权利要求1所述的一种金属基烧结磨擦片制造工艺,其特征是第三步电流直加热模压烧结成型对于铜基烧结材料,烧结温度为750-1000℃,保温时间为1-20分钟。
7.根据权利要求1所述的一种金属基烧结磨擦片制造工艺,其特征是对于铁基烧结材料,烧结温度为900-1500℃,保温时间为2-30分钟,随炉冷却至100℃出炉。
8.根据权利要求1-7任一所述的一种金属基烧结磨擦片制造工艺,其特征是热压模具材料为高密度石墨、钢或石墨与钢的复合模。
专利摘要本发明涉及属于摩擦材料制造技术领域,一种金属基烧结摩擦片制造工艺,金属基烧结摩擦片由铜、铁等金属材料为基体,含有硬质粒子、石墨粒子等摩擦性能调节组分,通过粉末原料混合、冷压制成型、电流直加热模压烧结成型工序制成摩擦块。
由于工艺中采用了电流直加热模压烧结成型工序,使制品密度显著提高,这允许材料中的脆性粒子变化范围增加,有利于调节制品的摩擦性能和降低磨损量。