数控车削不锈钢螺纹的加工方法
数控车如何加工螺纹【共18张PPT】
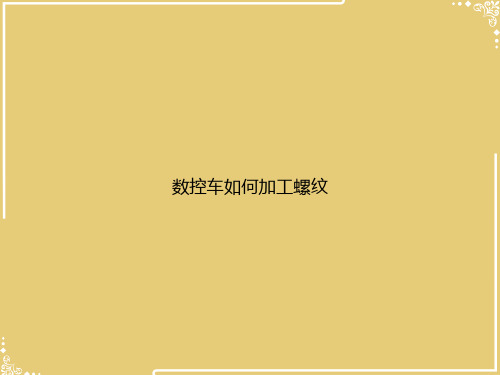
30
1 .5 O
70
3 Z
程序如下: O0308; N020 G00 U-62.0;
N021 G32 W-74.5 F4.0 ;
N022 G00 U62.0;
N023 W74.5; N024 U-64.0;
N025 G32 W-74.5; N026 G00 U64.0; N027 W74.5;
例:如下图所示圆锥螺纹,螺纹导程为1.5 mm。δ1=2 mm , δ2=1mm。 试编写螺纹加工程序
0.6
0.6
0.6
0.6
0.6
用G32加工螺纹时,由于机床伺服系统本身具有滞后特性,会在起始段和停止段发生螺纹的螺距不规则现象,故应考虑刀具的引入长度和超越长度,整个被加工螺纹的长度应该是引入长度、超越长度和
量 4 次 螺纹长度之和。
G32 W.
0.16
0.4
0.4
0.4
0.6
0.6
及 5 次 该指令的循环路线与前述的G90指令基本相同,只是F后面的进给量改为螺纹导程即可。
δ1=2 mm , δ2=1mm。
0.1
0.4
0.4
0.4
0.4
三、等螺距螺纹切削指令G32
四、简单螺纹切切削循6环指次令G92
0.15
0.4
0.4
0.4
削 7 次 D为第一次循环时的切削深度;
三、等螺距螺纹切削指令G32
N026 G00 U64.
次8次
0.2
0.2
0.4
0.15
0.3
数9次
0.2
例:如图所示是圆柱螺纹加工实例,螺距为4 mm,第一次 和第二次单边切削量均为1 mm,引入长度 为3 mm,超越长度为1.5 mm。
数控车床螺纹加工编程指令的应用

数控车床螺纹加工编程指令的应用济宁职业技术学院(山东)张玉香在目前的FANUC 和广州数控系统的车床上,加工螺纹一般可采用3 种方法:G32 直进式切削方法、G92直进式固定循环切削方法和G76 斜进式复合固定循环切削方法。
由于它们的切削方式和编程方法不同,造成的加工误差也不同,在操作使用时需仔细分析,以便加工出高精度的零件。
1.编程方法(1)G32 直进式螺纹切削方法指令格式:图1G32直进式螺纹切削方法指令格式:G32 X(U )_ Z(W )_ F_ ;该指令用于车削圆柱螺纹、圆锥螺纹、端面螺纹。
其编程方法与G01 相似,如图1所示。
使用说明:①式中(X ,Z )和(U ,W )为螺纹的终点坐标,即图1 中B 点的坐标值;F 后的数值为导程(单线时为螺距)。
②当α=0°时,作直螺纹加工,编程格式为G32 Z_F_或G32 W_F_ ;当α<45°时加工锥螺纹,螺距以Z轴方向的值指定;当α>45°时螺距以X 轴方向的值指定;当α=90°时,加工端面螺纹,编程格式为G32 X_ F_或G32 U_ F_ 。
③螺纹切削中进给速度倍率开关无效,进给速度被限制在100% ;螺纹切削中不能停止进给,一旦停止进给切深便急剧增加,非常危险。
因此,进给暂停在螺纹加工中无效。
④在螺纹切削程序段后的第一个非螺纹切削程序段期间,按进给暂停键时刀具在非螺纹切削程序段停止。
⑤主轴功能的确定。
在编写螺纹加工程序时,只能使用主轴恒转速控制功能(程序中编入G97 ),由于进给速度的最大值和最小值系统参数已设定,在加工螺纹时为了避免进给速度超出系统设定范围,所以主轴转速不宜太高,一般用如下公式计算:(取)且从粗加工到精加工,主轴转速必须保持恒定。
否则,螺距将发生变化,会出现乱牙。
⑥螺纹起点和终点轴向尺寸的确定。
螺纹加工时应注意在有效螺纹长度的两端留出足够的升速段和降速段,以剔除两端因进给伺服电动机变速而产生的不符合要求的螺纹段,通常:δ=(2~3 )螺距δ=(1~2 )螺距⑦螺纹起点和终点径向尺寸的确定。
不锈钢螺纹的车削加工方法总结

不锈钢螺纹的车削加工方法全世界因锈蚀而消耗的金属制品约占金属产量的10%,因此提高金属抗蚀性和耐蚀性具有非常重要的意义。
不锈钢能够达到相对较好的抗蚀要求,由起初的军用拓展到工业及民用各领域。
因此,对各种复杂曲面的不锈钢工件要求量较大。
但由于材质的特殊性,加工工艺成为制作产品的难题。
不锈钢材质本身的特殊性:不同种类的不锈钢由于机械性能和化学成分的不同其数控切削的难度也不相同。
有的不锈钢在切削加工时,很难达到满意的加工表面粗糙度;而有的不锈钢,虽容易达到要求的加工表面粗糙度,但在切削加工过程中刀具却特别容易磨损。
经总结,各类不锈钢很难切削的主要原因有以下几个方面:热强度高、韧性大对数控高速切削不适应奥氏体类不锈钢与马氏体类不锈钢其硬度和抗拉强度不高,只相当于40号钢,但延伸率、断面收缩率和冲击值却比较高。
如1Cr18Ni9Ti延伸率为40号钢的210%,这样在数控高速切削过程中就不容易被切断,切削变形时所消耗的功相当大。
相对来说,不锈钢在高温下的强度降低较少,如45号钢在500°时其持久强度为7kg/mM2,而1Cr18Ni9Ti在550°时其持久强度仍保持在19~24kg /mM2。
实践证明,在相同切削温度的作用下,不锈钢切削比普通碳素钢难加工,其热强度高是一个极其重要的因素;加工硬化趋势强对数控车削不利在数控高速车削的过程中,由于刀尖对工件材料挤压的结果使切削区的金属产生变形,晶内发生滑移,晶格畸变,组织致密,机械性能也随着发生变化,一般切削硬度也能增加2~3倍。
数控切削后加工硬化层深度可以从几十微米到几百微米不等,因此前一次走刀所产生的加工硬化现象又妨碍了下一次走刀时的切削,并且加工硬化层的高硬度导致刀具特别容易磨损;切屑的粘附性强、导热差对数控切削有影响在数控切削过程中,切削碎屑很容易牢固地粘附或熔着在刀尖和刀刃上,形成积屑瘤,造成工件加工表面的表面粗糙度恶化,同时增加切削过程中的振动,加速刀具磨损。
不锈钢螺纹加工技巧
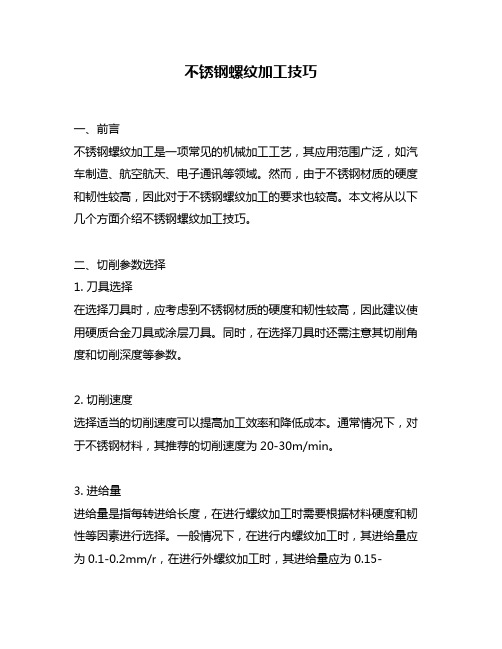
不锈钢螺纹加工技巧一、前言不锈钢螺纹加工是一项常见的机械加工工艺,其应用范围广泛,如汽车制造、航空航天、电子通讯等领域。
然而,由于不锈钢材质的硬度和韧性较高,因此对于不锈钢螺纹加工的要求也较高。
本文将从以下几个方面介绍不锈钢螺纹加工技巧。
二、切削参数选择1. 刀具选择在选择刀具时,应考虑到不锈钢材质的硬度和韧性较高,因此建议使用硬质合金刀具或涂层刀具。
同时,在选择刀具时还需注意其切削角度和切削深度等参数。
2. 切削速度选择适当的切削速度可以提高加工效率和降低成本。
通常情况下,对于不锈钢材料,其推荐的切削速度为20-30m/min。
3. 进给量进给量是指每转进给长度,在进行螺纹加工时需要根据材料硬度和韧性等因素进行选择。
一般情况下,在进行内螺纹加工时,其进给量应为0.1-0.2mm/r,在进行外螺纹加工时,其进给量应为0.15-0.3mm/r。
4. 切削深度切削深度是指每次切削的深度,其选择需要考虑到材料硬度和韧性等因素。
一般情况下,在进行内螺纹加工时,其切削深度应为1-2mm,在进行外螺纹加工时,其切削深度应为1.5-3mm。
三、螺纹加工方法1. 内螺纹加工内螺纹加工通常采用攻丝的方式进行。
在进行攻丝前需要先在孔口处预钻孔,并选择适当的攻丝刀具和攻丝规格。
在进行攻丝时,需注意控制进给量和转速等参数,并及时清理孔口处的铁屑和油渣等杂质。
2. 外螺纹加工外螺纹加工通常采用车床或数控机床进行。
在进行外螺纹加工前需要先确定好刀具的位置和角度,并选择适当的车刀或铣刀。
在进行外螺纹加工时,需注意控制进给量和转速等参数,并及时清理切屑和油渣等杂质。
四、加工注意事项1. 切削液的选择切削液可以起到冷却、润滑和清洗等作用,因此在进行不锈钢螺纹加工时需要选择适当的切削液。
一般情况下,建议使用硫化极压切削油或硫化碱性切削油。
2. 清洗和保养在进行不锈钢螺纹加工后,需要及时对机床和刀具进行清洗和保养。
特别是对于硬质合金刀具或涂层刀具,需要定期进行磨损检查和更换。
不锈钢管的螺纹加工工艺

不锈钢管的螺纹加工工艺
不锈钢管的螺纹加工工艺主要包括以下几个步骤:
1. 准备工作:选择合适的不锈钢材料,根据要求确定螺纹的尺寸和规格。
准备好螺纹刀具和加工设备。
2. 定位与固定:将需要加工的不锈钢管固定在加工设备上,确保不锈钢管的位置稳定。
3. 预切割:使用锯床或其他设备对不锈钢管的螺纹部分进行预先切割,以确保切割留出足够的余量。
4. 粗整:使用螺纹车床或其他车床设备将切割好的不锈钢管螺纹部分进行粗整,去除多余材料,使表面平整。
5. 精整:使用螺纹车床或其他车床设备对粗整后的不锈钢管螺纹进行精整,使其符合规定的螺纹标准和尺寸。
6. 整体表面处理:对加工完毕的不锈钢管进行整体的表面处理,例如抛光、打磨等,以提高外观质量和表面光洁度。
7. 检验与质量控制:对加工后的不锈钢管螺纹进行检验,包括尺寸、形状、表
面质量等方面的检查,确保符合要求。
以上是不锈钢管的螺纹加工工艺的基本步骤,具体的加工方法和设备选择可能会因应用领域的不同而有所区别。
加工操作时应注意安全,遵守相关规范和操作要求。
不锈钢螺纹车削
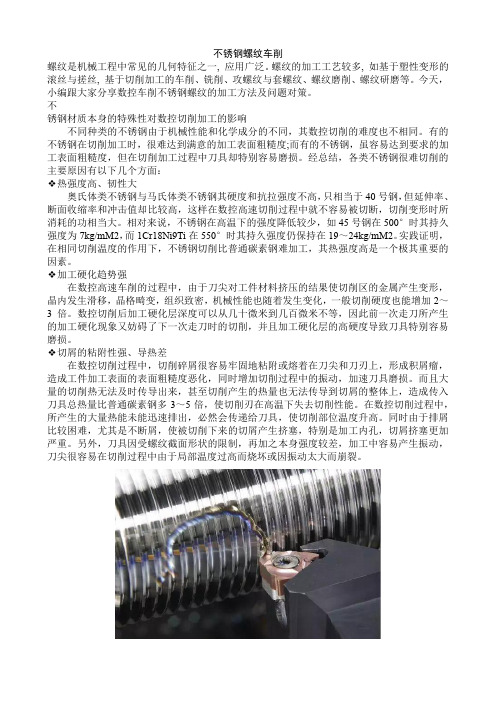
不锈钢螺纹车削螺纹是机械工程中常见的几何特征之一, 应用广泛。
螺纹的加工工艺较多, 如基于塑性变形的滚丝与搓丝, 基于切削加工的车削、铣削、攻螺纹与套螺纹、螺纹磨削、螺纹研磨等。
今天,小编跟大家分享数控车削不锈钢螺纹的加工方法及问题对策。
不锈钢材质本身的特殊性对数控切削加工的影响不同种类的不锈钢由于机械性能和化学成分的不同,其数控切削的难度也不相同。
有的不锈钢在切削加工时,很难达到满意的加工表面粗糙度;而有的不锈钢,虽容易达到要求的加工表面粗糙度,但在切削加工过程中刀具却特别容易磨损。
经总结,各类不锈钢很难切削的主要原因有以下几个方面:❖热强度高、韧性大奥氏体类不锈钢与马氏体类不锈钢其硬度和抗拉强度不高,只相当于40号钢,但延伸率、断面收缩率和冲击值却比较高,这样在数控高速切削过程中就不容易被切断,切削变形时所消耗的功相当大。
相对来说,不锈钢在高温下的强度降低较少,如45号钢在500°时其持久强度为7kg/mM2,而1Cr18Ni9Ti在550°时其持久强度仍保持在19~24kg/mM2。
实践证明,在相同切削温度的作用下,不锈钢切削比普通碳素钢难加工,其热强度高是一个极其重要的因素。
❖加工硬化趋势强在数控高速车削的过程中,由于刀尖对工件材料挤压的结果使切削区的金属产生变形,晶内发生滑移,晶格畸变,组织致密,机械性能也随着发生变化,一般切削硬度也能增加2~3倍。
数控切削后加工硬化层深度可以从几十微米到几百微米不等,因此前一次走刀所产生的加工硬化现象又妨碍了下一次走刀时的切削,并且加工硬化层的高硬度导致刀具特别容易磨损。
❖切屑的粘附性强、导热差在数控切削过程中,切削碎屑很容易牢固地粘附或熔着在刀尖和刀刃上,形成积屑瘤,造成工件加工表面的表面粗糙度恶化,同时增加切削过程中的振动,加速刀具磨损。
而且大量的切削热无法及时传导出来,甚至切削产生的热量也无法传导到切屑的整体上,造成传入刀具总热量比普通碳素钢多3~5倍,使切削刃在高温下失去切削性能。
UG NX8.5数控车床车削加工编程教程 螺纹加工

车削加工某轴类零件的模型及二维图如图1所示,对其轮廓进行加工。
图1一、创建车削加工几何体1.进入车削加工环境打开零件模型,选择“开始”|“加工”命令或使用快捷键[Ctrl+Alt+M]进入加工模块。
系统弹出如图2所示的“加工环境”对话框,在“要创建的CAM设置”列表框中选择“turning”模板,单击按钮,完成加工环境的初始化。
图22、创建加工坐标系在资源栏中显示“工序导航器”,将光标置于“工序导航器”空白部分右键单击弹出级联菜单。
级联菜单中有“程序顺序视图”、“机床视图”、“几何视图”、“加工方法视图”等,如图3所示。
在级联菜单中可以切换视图,单击“几何视图”切换到几何视图。
依次单击前的“+”符号,将WORKPIECE及TURNING_WORKPIECE 展开。
如图4所示图3 图4双击“MCS_SPINDLE”结点,系统弹出如图5所示的“MCS主轴”对话框,选择左端面的圆心以指定MCS,如图6所示。
车床工作面指定ZM-XM平面,则ZM轴被定义为主轴中心,加工坐标原点被定义为编程零点。
单击按钮,完成设置。
图5 图63、定义工件在“工序导航器—几何”视图中双击“WORKPIECE”结点,弹出如图7所示的“工件”对话框,完成几何体的指定。
其中,图7单击“指定部件”按钮,弹出“部件几何体”对话框,选择零件轴,如图8所示。
单击按钮,完成设置。
图8单击“指定毛坯”按钮,弹出“毛坯几何体”对话框,选择“包容圆柱体”类型,轴方向选择“+ZM”,按如图9所示设置参数,则可以指定一个长110mm,直径102mm的圆柱体作为毛坯。
单击按钮,完成对零件轴毛坯的指定。
图94、创建部件边界在“工序导航器—几何”视图中双击“TURNING_WORKPIECE”结点,弹出如图10所示的“车削工件”对话框。
图10在“部件旋转轮廓”类型中选择“无”,单击“指定部件边界”的按钮,弹出如图11所示的“部件边界”对话框,过滤类型默认为“曲线边界”。
螺纹数控车削加工几种不同进刀方式

螺纹是机械工程中比较常见的几何特征之一, 应用非常的广泛。
在各种螺纹加工工艺中,数控车削加工是生产单件或小批量螺纹工件的常用方法之一。
但是螺纹的数控车削也存在一定的难度,如加工参与的切削刃较长,容易出现啃刀和扎刀的现象,一般需要多刀切削才能完成;为了保证螺距准确,必须要选择合适的切入和切出长度;再有,螺纹加工的牙型及牙型角基本由刀具形状保证,因此,刀具的形状与正确安装直接影响螺纹牙型的质量;螺纹加工时的进给量与主轴转速必须保持严格的传动比,因此加工时禁止使用恒线速度控制;最后,螺纹切削加工的切削速度一般不高,否则容易出现积屑瘤或造成刀具塑性损坏。
螺纹数控车削的进刀方式:螺纹数控车削必须是多刀切削,其常用的进刀方式有径向进刀、侧向进刀、改进式侧向进刀、左右侧交替进刀以及分层切削式进刀这几种。
径向进刀是一种最基础的进给方式,其优点是编程比较简单,对左、右切削刃后刀面的磨损也比较均匀,牙型与刀头的吻合度高;但缺点是切屑不容易控制,可能会产生振动,刀尖处存在较大的切削力负荷,并且温度也较高。
径向进刀适合用在小螺距螺纹的加工以及螺纹的精加工中。
侧向进刀也是一种较为基础的进刀方式,这种方式有专用的复合固定循环指令编程,可以减小切削力, 便于控制切屑的排出;但这种切削方式使用的是纯单侧刃,因此刀具左、右切削刃的磨损不均匀,一般右侧后刀面磨损较大。
侧向进刀适合用在稍大螺距螺纹的粗加工中。
改进式侧向进刀,只是在侧向进刀的基础上,使进刀方向略微发生变化,这样就可以使右侧切削刃也参与到切削中来,从而抑制了右侧后刀面的磨损,减小了切削热的产生,在一定程度上改善了侧向进刀的不足。
左右侧交替进刀的最大特点是左、右切削刃磨损均匀,对于延长刀具寿命是非常有益的,而且也方便控制切屑的排出;单这种切削方式的不足之处在于编程比其他方式稍微复杂一些。
在编程能力允许的情况下,左右侧交替进刀适合对大牙型、大螺距的螺纹进行加工,甚至可加工梯形螺纹。
数控车床大螺距螺纹加工方法【技巧】

螺纹的车削工艺分析加工螺纹的加工有很多种:直进法、斜进法、左右切削法、车直槽法、分层法等等[1]。
由于螺纹较之三角螺纹,其螺距和牙型都大,而且精度高,牙型两侧面表面粗糙度值较小,致使螺纹车削时,吃刀深,走刀快,切削余量大,切削抗力大。
再[1]加工许多学校的数控车床刚性较差,这就导致了螺纹的车削加工难度较大,在数控车工技能培训中难于掌握,容易产生“扎刀”和“爆刀”现象,进而对此产生紧张和畏惧的心理。
在多年的数车工实习教学中,通过不断的摸索、总结、完善,对于螺纹的车削也有了一定的认知,我认为利用宏程序进行分层切削,可以很好地解决出现的问题。
“分层法”车削螺纹实际上是直进法和左右切削法的综合应用。
在车削较大螺距的螺纹时,“分层法”通常不是一次性就把槽切削出来,而是把牙槽分成若干层,每层深度根据实际情况而定。
转化成若干个较浅的槽来进行切削,可以降低车削难度。
每一层的切削都采用左右交替车削的方法,背吃刀量很小,刀具只需沿左右牙型线切削,螺纹车刀始终只有一个侧刃参加切削(如图2),从而使排屑比较顺利,刀尖的受力和受热情况有所改善,因此能加工出较高质量的螺纹,且容易掌握,程序简短,容易操作。
图2 分层切削法3 宏程序分层加工大螺距螺纹 3.2 程序以Fanuc 0i mateTC系统为例,图1所示螺纹的加工程序如下: O0001;T0101 M03 S300;换螺纹刀,主轴转速300r/min G00 X38 Z5;快速走到起刀点 M08;开冷却#101=36;螺纹公称直径 #102=0;右边借刀量初始值#103=-1.876;左边借刀量初始值(tg15*3.5*2或0.938*2) #104=0.2;每次吃刀深度,初始值N1 IF [#101 LT 29] GOTO2;加工到小径尺寸循环结束 G0 Z[5+#102] ;快速走到右边加工起刀点 G 92 X[#101] Z-30 F6;右边加工一刀 G0 Z[5+#103] ;快速走到左边加工起刀点 G92 X[#101] Z-30 F 6;左边加工一刀 #101=#101-#104;改变螺纹加工直径#102=#102-0.134*#104;计算因改变切深后右边借刀量(tg15/2=0.134) #103=#103+0.134*#104;计算因改变切深后左边借刀量(tg15/2=0.134) IF[#101 LT 34] THEN #104=0.15;小于34时每次吃刀深度为0.15 IF[#101 LT 32] THEN #104=0.1;小于32时每次吃刀深度为0.10 IF[#101 LT 30] THEN #104=0. 05;小于30时每次吃刀深度为0.05 GOTO 1;N2 G92 X29 Z-30 F6;在底径处精加工两刀 G92 X29 Z-30 F6;G00 X100 Z100 M09;刀架快速退回,关闭冷却 M05;主轴停M30;程序结束。
螺纹及锥面配合件的数控车削加工工艺及编程
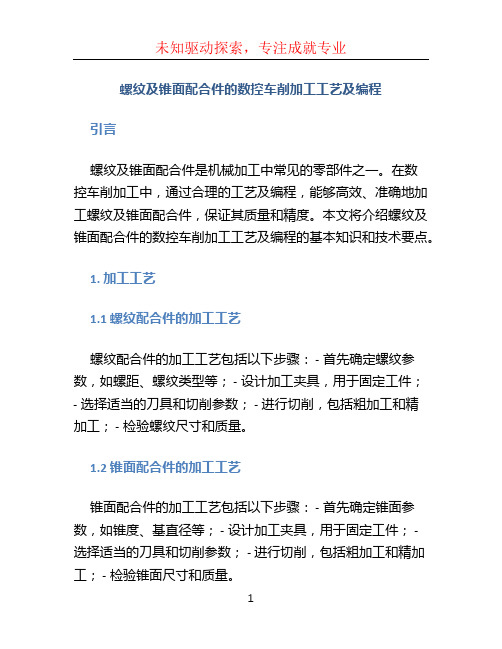
螺纹及锥面配合件的数控车削加工工艺及编程引言螺纹及锥面配合件是机械加工中常见的零部件之一。
在数控车削加工中,通过合理的工艺及编程,能够高效、准确地加工螺纹及锥面配合件,保证其质量和精度。
本文将介绍螺纹及锥面配合件的数控车削加工工艺及编程的基本知识和技术要点。
1. 加工工艺1.1 螺纹配合件的加工工艺螺纹配合件的加工工艺包括以下步骤: - 首先确定螺纹参数,如螺距、螺纹类型等; - 设计加工夹具,用于固定工件;- 选择适当的刀具和切削参数; - 进行切削,包括粗加工和精加工; - 检验螺纹尺寸和质量。
1.2 锥面配合件的加工工艺锥面配合件的加工工艺包括以下步骤: - 首先确定锥面参数,如锥度、基直径等; - 设计加工夹具,用于固定工件; - 选择适当的刀具和切削参数; - 进行切削,包括粗加工和精加工; - 检验锥面尺寸和质量。
2. 编程要点2.1 螺纹编程要点在数控车削加工中,编程螺纹配合件需要注意以下要点: - 使用适当的螺纹相关指令,如G76等; - 根据螺距设置进给速度; - 控制主轴速度; - 考虑螺纹的方向和公称直径等因素;- 进行刀具补偿。
2.2 锥面编程要点在数控车削加工中,编程锥面配合件需要注意以下要点: - 使用适当的锥度相关指令,如G02、G03等; - 根据锥度计算进给速度; - 控制主轴速度; - 考虑锥面的方向和基直径等因素; - 进行刀具补偿。
3. 示例程序程序示例:N10 G90 G54 G92 S1000 M03N20 T01 M06N30 G43 H01 Z1.0 M08N40 G00 X50. Y0.N50 G01 Z-10. F100.N60 G01 X10.N70 G01 G02 X0. Y0. R5.N80 G01 X-50. Y50.N90 G01 G02 X-50. Y-50. R50.N100 G01 X10.N110 G01 G02 X0. Y0. R5.N120 G01 X50. Y0.N130 G00 Z10.N140 M09 M05 M304. 总结螺纹及锥面配合件的数控车削加工是机械加工过程中的重要环节。
数控车削编程螺纹加工(“螺纹”文档)共45张

项
程序如表5.5所示。
目
表5.5复合螺纹切削循环指令编程
五
程序
…
螺
M03S800
纹
T0404
的
G00X32Z2
加
G76P010160Q50R0.5
工
G76X27.4Z-27.5P1300Q450F2
…
相关知识
例:试用复合螺纹切削循环指令G76编写图5.9所示的梯形螺纹加工程序。
项 目 五
螺
纹
的
加
图5.10 梯形螺纹编程
数控车削编程与加工
工程五 螺纹的加工
项 目 五
螺 纹 的 加 工
工程义务
粗精加工如图5.1所示螺纹套零件,零件资料为45钢。
项 目 五 螺 纹 的 加 工
图5.1螺纹套
相关知识
一、螺纹的根本要素和加工工艺
项 目
1.普通螺纹的根本要素
〔1〕牙型
沿螺纹轴线剖切时,螺纹牙齿轮廓的剖面外形称为牙型。螺纹的牙型
纹
确后,方可加工,防止出现不测事故。
的
加
4.螺纹切入切出量确实定
工
为保证螺纹加工质量,螺纹切削时在两端设置足够的切入切出量。因此,
实践螺纹的加工长度为:W=L(螺纹实际长度)+δ1+δ2
相关知识
式中:δ1——切入量,普通取2-5;
项
δ2——切出量,普通取0.5δ1左右;
目
五பைடு நூலகம்
螺 纹 的 加 工
图5.2螺纹的切入切出量
单一螺纹切削循环 …
G92X42.2Z-41R-14.5
X41.6
X41.2
注释 …
ap =0.8
螺纹的车削方法

螺纹的车削方法螺纹是机械制造中常见的一种零部件,它具有优良的螺旋连接效果,在机械制造中应用广泛。
螺纹是具有一定螺旋角度的圆柱体表面形状,它可以通过车削加工得到。
下面将介绍几种螺纹的车削方法。
一、普通车床车削普通车床常常用于对螺纹进行车削加工。
具体车削过程如下:1、将工件固定在车床上,调整好位置和夹紧力,并选择合适的车刀和进给速度。
2、加工螺纹前,需要先进行车削前的准备工作,如找中心、测量螺距和安装切断刀等。
3、先进行螺旋沟的车削,包括切断刀的切槽、切断刀的切槽、冷镇银器的冷却、螺旋沟的整理以及螺纹的整形。
4、进行螺纹的车削。
在车削时,要控制车刀与工件的角度、刀具前刀角、转速和进给速度等,保证车削尺寸和表面质量。
5、切断刀的切割要齐,避免过度挤压而损坏螺纹。
车削完毕后,需要对加工的螺纹进行检验,如螺距和径向跳动等。
螺纹车床是专门用于车削螺纹的机床,它可以实现自动车削和精密加工。
在进行螺纹车削时,需要注意以下几点:2、在车床上安装好螺纹导板和读数仪后,将车刀调整到导板的切线上,通过读数仪进行精确定位和加工。
3、在车削螺纹的同时,需要同时进行螺旋沟的车削,实现连续的车削作业。
三、立式轴向数控车床车削立式轴向数控车床是一种新型的数控机床,它具有高度集成的控制系统和优质的结构设计。
在进行螺纹车削时,需要注意以下几点:1、在准备车削前,需要进行数控程序的编写和导入,并进行参数的设置,如转速、进给速度、切削速率等。
总之,螺纹的车削方法有普通车床车削、螺纹车床车削和立式轴向数控车床车削等,选用不同的方法和工艺路线,能够实现高效的螺纹加工。
不锈钢螺丝生产工艺

不锈钢螺丝生产工艺
不锈钢螺丝生产工艺主要包括以下几个步骤:材料准备、冲压、车削、螺纹加工、表面处理和质检。
下面将详细介绍每个步骤的工艺流程。
首先是材料准备。
不锈钢螺丝的主要原材料为不锈钢钢坯,通常采用304不锈钢或316不锈钢。
钢坯先进行切割,然后经热处理,将其硬度控制在一定范围内,以便于后续加工。
接下来是冲压。
将经过热处理的钢坯放入冲压机中,通过冲压模具将钢坯冲压成预定形状的螺丝头部。
冲压过程中需要控制好压力和速度,以确保螺丝头部的质量和尺寸符合要求。
然后是车削。
经过冲压后的螺丝头部需要进行车削,以使其具有一定的形状和尺寸精度。
车削过程中,需要控制好车刀的进给速度和切削深度,以确保螺丝头部的精度和光洁度。
接着是螺纹加工。
将经过车削的螺丝头部放入螺纹加工机中,通过螺纹刀具将螺纹加工成标准的内螺纹或外螺纹。
螺纹加工过程中要控制好螺距和螺纹深度,以确保螺纹的质量符合要求。
然后是表面处理。
经过螺纹加工后的螺丝需要进行表面处理,以提高其抗腐蚀性能和美观度。
常见的表面处理方法有镀铬、镀锌和电镀等,选择合适的表面处理方法根据不同的需求。
最后是质检。
经过表面处理后的螺丝需要进行质量检验,以确保其质量符合要求。
质检主要包括外观检查、尺寸检测和功能
性检测等。
只有合格的螺丝才能被包装和出厂销售。
以上就是不锈钢螺丝的生产工艺的主要步骤。
通过科学的工艺流程和严格的质量控制,可以生产出质量优良的不锈钢螺丝,满足各种不同需求的使用要求。
华中系统数控车车削螺纹的方法分析

华中系统数控车车削螺纹的方法分析作者:周国平来源:《南北桥》2019年第24期【摘要】加工螺纹需要保证加工进给与主轴旋转同步,伺服电机带动滚珠丝杠的旋转,从而使刀具移动进行切削加工。
在华中数控系统中,G32、G82、G76能实现不同要求下的螺纹车削。
【关键词】螺纹车削原理加工常识华中数控车削方法中图分类号:G4 文献标识码:A DOI:10.3969/j.issn.1672-0407.2019.24.173一、数控车削螺纹加工原理数控机床车削螺纹时,走的是丝杆路线,数控车床车削螺纹不乱牙主要靠主轴上安装的编码器实现,当转速一定,在退刀時,主轴的转动方向与进刀时同步但相反,这就保证刀具进刀时都是在同一点上,使得车削时不会乱牙。
了解了数控机床加工螺纹的原理,才能充分发挥数控机床的功效,数控机床加工螺纹需要保证加工螺纹的进给与主轴旋转同步,其控制主要依靠数控机床的四个部件来实现。
①主轴编码器。
②运算器。
③伺服电机。
④滚珠丝杠。
二、螺纹加工工艺常识了解螺纹相关知识对于车削螺纹加工的编程数据尤为重要。
常见三角形螺纹,牙型角为60度,有粗牙和细牙之分,粗牙普通螺纹螺距是标准螺距,其代号用字母“M”及公称直径表示。
细牙普通螺纹代号用字母“M”及公称直径◇螺距表示,如M24◇1.5等。
普通螺纹又有左旋(加注“LH”)和右旋之分,如M20◇1.5LH等,未注明的是右旋螺纹。
①车削螺纹前工件大径的确定,车削三角螺纹时,应考虑螺纹的公差要求和螺纹切削过程中对大径的挤压作用,编程过程中的实际大径应比其公称直径略小,按经验公式取值约0.13P。
②螺纹总切深的确定,螺纹总切深与螺纹牙型高度及螺纹中径的公差带有关,在编制螺纹加工程序时,总切深量h’=2h+T,T为螺纹中径公差带的中值。
③螺纹加工的多刀切削,在数控车床上多刀车削螺纹的常用方法有直进法和斜进法两种,在螺纹总切深确定后,如果螺纹的牙型较深,可以多次进给,每次进给的背吃刀量依递减规律分配。
数控车床螺纹的加工方法

数控车床螺纹的加工方法摘要:螺纹加工是车床操作工必备技能。
在目前的数控车床中,螺纹切削一般有G32直进式切削方法、G76斜进式切削方法,结合我院实践教学融入质量控制技术,争取加工出高精度的零件及高的合格率。
关键词:数控加工螺纹切削加工方法一、数控加工中螺纹的主要加工方法在目前的数控加工中,螺纹切削一般有两种方法:G32直进式切削方法和G76斜进式切削方法,由于切削方法不同,编程的方法不同,加工误差也不同。
我们在操作使用中要仔细分析。
其中指令G32用于加工单行程螺纹,编程任务重,程序复杂;指令G76克服了指令G32的缺点,可以将工件从坯料到成品螺纹一次性加工完成,且程序简捷,可节省编程时间。
1.G32直进式切削方法,由于两侧刃同时工作,切削力较大,而且排削困难,因此在切削时,两切削刃容易磨损。
在切削螺距较大的螺纹时,由于切削深度较大,刀刃磨损较快,造成螺纹中径产生误差;但是其加工的牙形精度较高,因此一般多用于小螺距螺纹加工。
由于其刀具移动切削均靠编程来完成,因此加工程序较长;由于刀刃容易磨损,因此加工中要做到勤测量。
2.螺纹加工完成后可以通过观察螺纹牙型判断螺纹质量及时采取措施,当螺纹牙顶未尖时,增加刀的切入量会使螺纹大径增大,增大量视材料塑性而定;当牙顶已被削尖时,增加刀的切入量,则大径成比例减小。
要根据这一特点正确对待螺纹的切入量,防止报废。
二、车削螺纹应注意的问题1.确定车螺纹切削深度的起始位置,将中滑板刻度调到零位,开车,使刀尖轻微接触工件表面,然后迅速将中滑板刻度调至零位,以便于进刀记数。
2.试切第一条螺旋线并检查螺距。
将床鞍摇至离工件端面8―10牙处,横向进刀0.05左右。
开车,合上开合螺母,在工件表面车出一条螺旋线,至螺纹终止线处退出车刀,开反车把车刀退到工件右端;停车,用钢尺检查螺距是否正确。
3.用刻度盘调整背吃刀量,开车切削。
螺纹的总背吃刀量ap与螺距的关系按经验公式ap≈0.65P,每次的背吃刀量约0.1。
数控车床螺纹加工调节实用方法

数控车床螺纹加工调节实用方法我折腾了好久数控车床螺纹加工调节这事儿,总算找到点门道。
说实话,刚开始的时候我也是瞎摸索。
我就知道要加工出合格的螺纹,肯定有不少参数得搞对。
就好像炒菜,盐放多放少,火候大小,都能把菜的味道变得完全不同,数控车床螺纹加工里那些参数也同理。
我一开始最常犯的错就是切削深度设的不合适。
有一回,我把切削深度设得太大了,就想着能快点加工好螺纹呢,结果螺纹完全都变形了。
这个就好比你要盖房子,一下挖太深的地基,旁边的土都塌了,房子还能好好盖吗?那肯定不行啊。
所以啊,切削深度一定得慢慢试,找准合适的值。
后来我就每次只增加一点点切削深度,这样虽然加工得慢一些,但是成功率高多了。
还有转速这东西,也是很有讲究的。
我试过设置得很高,那时候心里想着转速高肯定加工得快又好。
可没想到,高速下加工出来的螺纹表面特别粗糙。
我就琢磨,这就像开车太快,路上小石头就更容易把车给崩坏一样,刀具在高速下也不好控制,就把螺纹给搞花啦。
所以转速得适中,不同的材料和刀具,合适的转速都不一样,得多试试才能知道。
螺距这个参数我也折腾了好久。
有时候图纸上标的螺距,我设置到车床里去,加工出来的螺纹就有点不对。
后来才发现,不能只看图纸上的,还得考虑车床本身的一些误差因素。
我专门找了一些废料来试,一块废料上反复加工不同螺距的螺纹,一点点去校准车床里设置的螺距数值,直到加工在废料上的螺纹和标准件能完全匹配。
对了,刀具也特别关键。
我刚开始用一些便宜的刀具,总觉得应该都差不多吧。
结果发现便宜的刀具磨损特别快,用不了多久加工出来的螺纹就不合格了。
这就跟你写字一样,好的笔能一直写出漂亮的字,差的笔写一会儿就不好使了。
所以啊,在数控车床螺纹加工调节里,万万不能为了省点小钱就忽视刀具的质量。
那些复杂的数控计算公式我看着就头大。
我就自己手动去试切,一点点去找到最好的参数。
这种手动试切就像是摸黑走路一样,虽然慢,但每一步你都能清楚知道是不是走对了。
不锈钢数控车削加工工艺
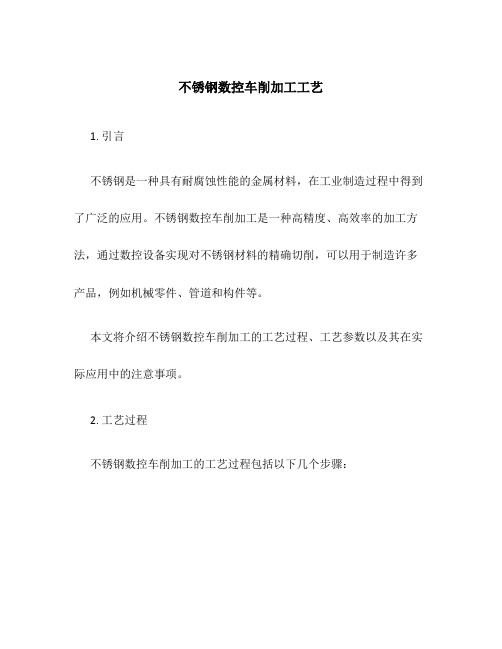
不锈钢数控车削加工工艺1. 引言不锈钢是一种具有耐腐蚀性能的金属材料,在工业制造过程中得到了广泛的应用。
不锈钢数控车削加工是一种高精度、高效率的加工方法,通过数控设备实现对不锈钢材料的精确切削,可以用于制造许多产品,例如机械零件、管道和构件等。
本文将介绍不锈钢数控车削加工的工艺过程、工艺参数以及其在实际应用中的注意事项。
2. 工艺过程不锈钢数控车削加工的工艺过程包括以下几个步骤:2.1 零件准备在进行车削加工之前,首先需要准备好要加工的不锈钢零件。
清洁表面,并确保其表面没有明显的凹陷和磨损。
2.2 工艺规划在进行数控车削加工之前,需要进行工艺规划。
工艺规划包括确定零件的加工顺序、选择合适的刀具和切削参数等。
2.3 加工装夹将不锈钢零件安装在数控车床上,进行加工装夹。
确保零件固定牢固且位置准确。
使用合适的夹具和固定装置,以避免零件在加工过程中发生移动或变形。
2.4 加工参数设置根据零件的要求和刀具的特性,设置合适的加工参数。
包括切削速度、进给速度和切削深度等。
合理的加工参数可以提高加工效率和加工质量。
2.5 车削加工根据工艺规划和加工参数,使用数控设备进行车削加工。
通过控制刀具的运动轨迹和加工参数,将不锈钢材料逐渐切削,得到所需形状和尺寸的零件。
2.6 质量检验在完成车削加工后,进行质量检验。
检查零件的尺寸、表面质量和精度等。
确保加工的零件符合要求。
3. 工艺参数不锈钢数控车削加工的工艺参数对加工质量和效率有着重要影响。
以下是一些常用的工艺参数:•切削速度:通常以米/分钟为单位。
根据不锈钢材料的硬度和刀具的材质来确定合适的切削速度。
•进给速度:刀具在单位时间内在工件上的移动速度。
根据不同的切削工况和加工精度要求,选择合适的进给速度。
•切削深度:刀具每次切削所去除的材料层厚度。
根据零件的要求和刀具的稳定性,选择合适的切削深度。
•刀具半径补偿:在车削过程中,考虑到刀具的几何特性和零件的轮廓,需要进行刀补。
不锈钢数控车削加工工艺

数
零 件
使工件均匀受力,减小变形。
的
控
装
车
夹
削
工
也可以改变夹紧力的作
件
用点,采用轴向夹紧的方式。
的
装 夹
第三节 数控车削加工工艺
常用对刀方式
数
控 车
直接用刀具试切对刀 自动对刀
削
机外对刀仪对刀
的
对
刀
对刀是确定工件在机床上的位置, 也即是确定工件坐标系与机床坐 标系的相互位置关系。对刀过程 一般是从各坐标方向分别进行, 它可理解为通过找正刀具与一个 在工件坐标系中有确定位置的点 (即对刀点)来实现。
最多的加工方法之一,由于数控车床
数 具有精度高、能做直线和圆弧插补以
控 车 床
及在加工过程中能自动变速的特点, 其工艺范围较普通机床宽得多。数控
的 主
车床适合于车削具有以下要求和特点
要 的回转类零件。
加
工
对
象
第三节 数控车削加工工艺
● 精度要求高的回转体零件
数
控
车
床
的
主
要
加
工 对
高精度的机床主轴
象
找正:找正装夹时必
须将工件的加工表面回
数 转轴线(同时也是工件
控 坐标系Z轴)找正到与车
车 床主轴回转中心重合。
削 工 件
一般为打表找正。通过 调整卡爪,使工件坐标
的 系Z轴与车床主轴的回转
装 中心重合。
夹
采用找正的方法
第三节 数控车削加工工艺
薄壁零件容易变形,普
薄 通三爪卡盘受力点少,采用
壁 开缝套筒或扇形软卡爪,可
象
采用车铣加工中心
- 1、下载文档前请自行甄别文档内容的完整性,平台不提供额外的编辑、内容补充、找答案等附加服务。
- 2、"仅部分预览"的文档,不可在线预览部分如存在完整性等问题,可反馈申请退款(可完整预览的文档不适用该条件!)。
- 3、如文档侵犯您的权益,请联系客服反馈,我们会尽快为您处理(人工客服工作时间:9:00-18:30)。
数控车削不锈钢螺纹的加工方法
newmaker
全世界因锈蚀而消耗的金属制品约占金属产量的10%,因此提高金属抗蚀性和耐蚀性具有非常重要的意义。
不锈钢能够达到相对较好的抗蚀要求,由起初的军用拓展到工业及民用各领域。
因此,对各种复杂曲面的不锈钢工件要求量较大。
但由于材质的特殊性,加工工艺成为制作产品的难题。
不锈钢材质本身的特殊性
对数控切削加工的影响
不同种类的不锈钢由于机械性能和化学成分的不同其数控切削的难度也不相同。
有的不锈钢在切削加工时,很难达到满意的加工表面粗糙度;而有的不锈钢,虽容易达到要求的加工表面粗糙度,但在切削加工过程中刀具却特别容易磨损。
经总结,各类不锈钢很难切削的主要原因有以下几个方面:
热强度高、韧性大对数控高速切削不适应奥氏体类不锈钢与马氏体类不锈钢其硬度和抗拉强度不高,只相当于40号钢,但延伸率、断面收缩率和冲击值却比较高。
如,1Cr18Ni9Ti延伸率为40号钢的210%,这样在数控高速切削过程中就不容易被切断,切削变形时所消耗的功相当大。
相对来说,不锈钢在高温下的强度降低较少,如45号钢在500°时其持久强度为7kg/mM2,而1Cr18Ni9Ti在550°时其持久强度仍保持在19~24kg/mM2。
实践证明,在相同切削温度的作用下,不锈钢切削比普通碳素钢难加工,其热强度高是一个极其重要的因素。
加工硬化趋势强对数控车削不利在数控高速车削的过程中,由于刀尖对工件材料挤压的结果使切削区的金属产生变形,晶内发生滑移,晶格畸变,组织致密,机械性能也随着发生变化,一般切削硬度也能增加2~3倍。
数控切削后加工硬化层深度可以从几十微米到几百微米不等,因此前一次走刀所产生的加工硬化现象又妨碍了下一次走刀时的切削,并且加工硬化层的高硬度导致刀具特别容易磨损。
切屑的粘附性强、导热差对数控切削有影响在数控切削过程中,切削碎屑很容易牢固地粘附或熔着在刀尖和刀刃上,形成积屑瘤,造成工件加工表面的表面粗糙度恶化,同时增加切削过程中的振动,加速刀具磨损。
而且大量的切削热无法及时传导出
来,甚至切削产生的热量也无法传导到切屑的整体上,造成传入刀具总热量比普通碳素钢多3~5倍,使切削刃在高温下失去切削性能。
在数控切削过程中,所产生的大量热能未能迅速排出,必然会传递给刀具,使切削部位温度升高。
同时由于排屑比较困难,尤其是不断屑,使被切削下来的切屑产生挤塞,特别是加工内孔,切屑挤塞更加严重。
另外,刀具因受螺纹截面形状的限制,再加之本身强度较差,加工中容易产生振动,刀尖很容易在切削过程中由于局部温度过高而烧坏或因振动太大而崩裂。
数控切削不锈钢刀具的问题及解决对策
数控切削后螺纹表面粗糙度太差鱼鳞斑状波纹及啃刀现象是不锈钢螺纹车削中最常遇到的现象,产生这些现象的原因有:(1)螺纹车刀两侧刃后角太小,两侧刃与后面的螺纹表面相摩擦使加工表面恶化,加工时必须考虑螺纹旋转角对两侧刃实际后角的影响。
(2)螺纹车刀的前角太小,刃口不够锋利,切屑不能顺利地被切断,而是部分地被挤压或撕裂下来,必定造成螺纹表面非常粗糙。
当前角太大时,刀刃强度削弱且容易磨损、崩裂、扎刀,更容易引起振动而使螺纹表面产生波纹。
因此,应根据不锈钢的不同材质选择适当的前角。
车削耐浓硫酸用不锈钢螺纹时,应比车削2Cr13不锈钢螺纹采用较小的前角,车刀两侧
切削刃上应带有很窄的刃带以避免刃口迅速被磨损。
切削
2Cr13、1Cr17、4Cr13时,切削刃应尽可能锋利,否则就不容易达到所需的良好的表面粗糙度。
(3)螺纹刀刀片磨钝,实际上的前角、后角由大变小,切屑在形成过程中挤压严重,使切削过程中切削力增加振动加剧,加工表面恶化严重。
因此,车削不锈钢螺纹时,必须随时保持刀刃的锋利,及时更换刀头。
(4)螺纹车刀固定不牢、刀头伸出过长、刀杆刚性不够,或者是机床精度差、主轴松动、刀架部分松动等因素都会引起振动,使螺纹表面产生波纹。
因此,在操作时必须注意操作机床、刀具及工件,使系统有足够的刚性。
安装车刀时,除了保证安装牢固、不能有任何松动以外,车刀刀尖应略高于工件中心0.2~0.5mm,绝不能低于中心,以免扎刀。
(5)车削螺纹时应避免采用直进法,由于左右两侧的切屑接触长度长,容易产生振动,使刀尖承受的负荷加大,引起振动和增加排屑时的阻力,把加工表面划伤。
因此,对于不锈钢螺纹的加工最好选用交叉式车削螺纹的方法。
这种方法采用交替侧向进给,尤其对于大螺距螺纹、粘性材料的切削,是解决振动问题的最有效措施。
由于左右交叉使用切削刃,故磨损均匀,还能延长刀具的使用寿命。
(6)数控切削螺纹的过程中切削用量的匹配程度直接影响加工的效率。
切削量过小将会使刀具加剧磨损,过大则将使刀具产生崩碎,因此进刀数和每刀进给量会对车削螺纹产生决定性的影响。
为了获得最佳刀具寿命,工件直径不应大于螺纹大径0.14mm,应当避免
少于0.05mm的每刀进给量。
加工的总切削量应设定在0.1mm左右,第一次的切深应是刀尖半径(R)的150~200%,最大不能超过0.5mm,对于奥氏体不锈钢应避免少于0.08mm的每刀进给量,内螺纹用刀尖半径小的普通刃刀片,随着刀深的缩小切削次数可能相应地增加。
数控切削后螺纹尺寸不稳定螺纹加工后,用螺纹环规测量外螺纹“通端”进不去或者出现前后松紧不一致以及“止端”部分通过等现象。
产生这些弊病的原因:(1)螺纹牙形不对。
即使螺纹中径已经达到规定尺寸,螺纹环规、塞规仍可能拧不动。
(2)螺纹倒牙。
用螺纹量规测量时,往往会出现受方向性限制的现象,也就是从一端拧过较紧,而从另一端拧过较松,甚至出现“通端”通不过而“止端”反而通过的现象。
(3)内螺纹底径车的太小,或外螺纹底径过大,也会使得螺纹规拧不进去,这是由于车刀磨损变钝,切削过程中有挤压现象,使螺纹的外径或内径挤压出毛刺的结果。
(4)车削直径较小的内螺纹时因车刀刀杆受尺寸的限制刚性较差,车削过程中容易产生“让刀”,以至四部尺寸较大造成局部超差。
(5)车削细长螺杆时,由于工件的刚性较差,车削过程中产生变形,造成螺纹上的尺寸误差。
(6)车削薄壁工件的内、外螺纹时,工件因受力和切削温度的影响,产生局部变形,也会产生螺纹的局部超差。
因此,要解决“螺纹量规进不去”的问题,必须针对上述原因采取相应的措
施,主要是从正确安装及工件装卡合适等方面着手。
冷却润滑液在数控切削螺纹中的微妙作用
合理地使用润滑液能改善切削条件达到事半功倍的效果。
在数控切削不锈钢螺纹时应注意:
要了解冷却润滑液的特殊要求(1)由于不锈钢的韧性大、切削不易被分离,故要求冷却液要有较高的冷却性能,以带走大量的热量。
(2)由于粘性大、熔着性大,在切削螺纹过程中容易产生积屑瘤,故应使冷却液具有较高的润滑性能。
(3)要求冷却液有较好的渗透性,可在切削中渗入到金属区的微细隙线中,使切屑容易断离。
(4)还要有一定的洗涤功能。
取用几种合适的冷却液(1)硫化油具有较好的冷却性能和润滑
机能,按照配制方法的不同可分为直接和间接两种。
直接流化油的配方为:矿物油98%,硫2%。
间接硫化油配方为:矿物油78%~80%,黑机油、植物油18%~20%,硫1.7%。
(2)F43号机油适合于作不锈钢切削的冷却润滑液,对车不锈钢螺纹效果最佳。
其配方为:5号高速机油83.5%,石油磺酸钙4%,石油磷酸钡4%,氧化石油脂钡皂4%,二烷硫代磷酸锌4%,二硫化0.5%。
(3)植物油如豆油,在车削螺纹时有利于得到较好的螺纹表面粗糙
度和延长刀具的使用寿命。
综上所述,无论是马氏体类不锈钢、铁素体类不锈钢还是奥氏体类不锈钢,甚至奥氏体+铁素体类不锈钢,都应根据不同的金相组织制定相应的加工方法,以达到理想的加工效果,创造更多的经济效益和社会效益。
(end)。