《精益生产基础》PPT课件
合集下载
精益生产基础知识(PPT30页)
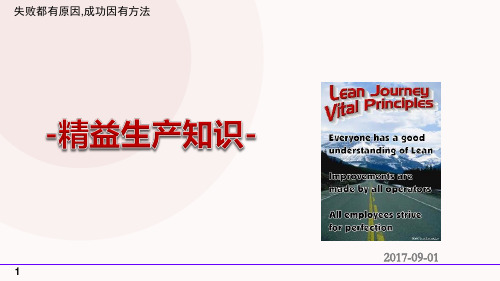
24
失败都有原因,成功因有方法
手工生产
大规模生产
同步生产
• 按照客户规 • 零件可互换-
格制造
惠特尼
• 单件生产 .. • 实现劳动分工 独特的产品 -泰勒
• 消除浪费 • 不断改进 • 员工参与
• 质量变异 • 大批量少品种
• 少量的存货 • 工序式生产
• 高的成本.. • 设备大难组合
只为富人提
精益生产使用的是拉动式作业流程.
20
失败都有原因,成功因有方法
Error Proofing (Poka Yoke) 防错技术
定 ---- “POKA-YOKE”又称愚巧法\防呆法.意即在过程失误发生之前即加以防止.是一种在 义 作业过程中采用自动作用\报警\标识\分类等 手段,使作业人员不特别注意也不会失误的
因经营效率极限化被美国学者赞誉为“精益生产”。继而在80年代中期 被欧美企业来纷纷采用。随着微利时代的来临,精益生产模式成为企业竞争 的有力武器,并对人类的生产革命产生了长远影响。
精益生产: 是一种快速缩短交期,有效降低库存成本、消除各种浪费的柔 性敏捷化生产方式。
9
失败都有原因,成功因有方法
J I T ust n ime
一组数据:丰田汽车销量变化趋势
2015年918W辆 2005年726W辆
4
2015年平均售价: 185000元 2005年平均售价: 210000元
失败都有原因,成功因有方法
一组数据:丰田汽车营业数据变化趋势
2015年
净利润率: 1400/17000≈8.2%
净利润率: 996/15264≈6.5%
适品 ·适量 ·适时
10
失败都有原因,成功因有方法
失败都有原因,成功因有方法
手工生产
大规模生产
同步生产
• 按照客户规 • 零件可互换-
格制造
惠特尼
• 单件生产 .. • 实现劳动分工 独特的产品 -泰勒
• 消除浪费 • 不断改进 • 员工参与
• 质量变异 • 大批量少品种
• 少量的存货 • 工序式生产
• 高的成本.. • 设备大难组合
只为富人提
精益生产使用的是拉动式作业流程.
20
失败都有原因,成功因有方法
Error Proofing (Poka Yoke) 防错技术
定 ---- “POKA-YOKE”又称愚巧法\防呆法.意即在过程失误发生之前即加以防止.是一种在 义 作业过程中采用自动作用\报警\标识\分类等 手段,使作业人员不特别注意也不会失误的
因经营效率极限化被美国学者赞誉为“精益生产”。继而在80年代中期 被欧美企业来纷纷采用。随着微利时代的来临,精益生产模式成为企业竞争 的有力武器,并对人类的生产革命产生了长远影响。
精益生产: 是一种快速缩短交期,有效降低库存成本、消除各种浪费的柔 性敏捷化生产方式。
9
失败都有原因,成功因有方法
J I T ust n ime
一组数据:丰田汽车销量变化趋势
2015年918W辆 2005年726W辆
4
2015年平均售价: 185000元 2005年平均售价: 210000元
失败都有原因,成功因有方法
一组数据:丰田汽车营业数据变化趋势
2015年
净利润率: 1400/17000≈8.2%
净利润率: 996/15264≈6.5%
适品 ·适量 ·适时
10
失败都有原因,成功因有方法
精益生产基础培训课件
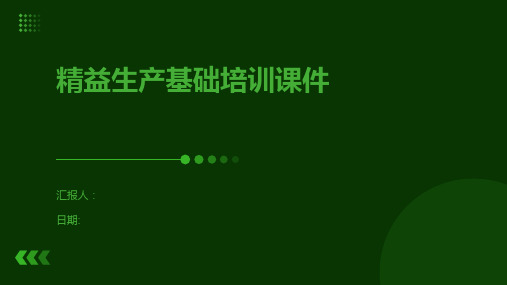
持续改进研讨会
持
续
定期组织研讨会,分享
改
改进成果和经验,推动
进
持续改进。
研
讨
会
分
深入剖析成功案例与失
享 改
败案例,总结经验教训
进
。
案
例
分
析
成
成立跨部门、跨职能的
功
改进小组,推动持续改
与
进的实施。
失
败
原
因
制
让员工分享自己所在部
定 改
门或团队的改进成果和
进
经验。
计
划
建
立
根据分析结果,制定针
改
对性的改进计划。
确保设备处于良好状态,减少换 模过程中的故障。
单元化生产
设计高效的生产单元
根据产品特性和工艺要求,合 理划分生产单元。
强化员工技能培训
让员工熟悉多岗位操作,提高 工作效率。
单元化生产
将生产线划分为独立的单元, 以提料在单元之间顺畅流动 ,减少运输时间和成本。
建立快速反馈机制
起源
精益生产起源于日本丰田汽车公司的生产方式,旨在消除浪费、提高效率和效 益。
发展
随着全球化和市场竞争的加剧,精益生产逐渐成为一种广泛应用的制造管理方 式,被众多企业采纳和实践。同时,精益生产也在不断发展和完善,以适应不 断变化的市场需求和技术创新。
02
精益生产的核心原则
价值流分析
总结词
价值流分析是识别和优化产品或服务从原材料到最终客户全过程中所有活动的关 键工具。
总结词
持续改进文化建立,推动企业不断发展和创新
详细描述
某物流企业为了推动不断发展和创新,建立了持续改进的文化。通过鼓励员工提 出改进意见和建议,企业不断优化流程和提高运营效率。同时,企业还加强了与 客户的沟通和合作,实现了整体服务水平的提升和客户满意度的提高。
精益生产培训课件(PPT 72页)
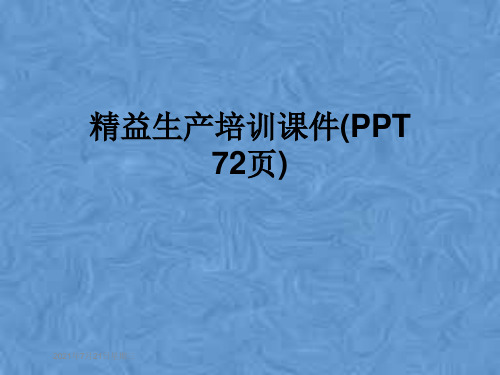
视5S工作。
素养
• 定义:人人依规矩行事,工作的每 分钟、每个环节都具备良好的思维 方式。
• 目的:提升人的品质,使每个人都 成为对任何工作都持认真态度 的 优秀管理者和员工。
5S活动开展原则
• 1、自我管理 • 2、持之以恒 • 3、小处着眼
• 实例
返回
推行精益重在坚持
维持
改 善
改善和维持 循环
整顿
• 定义:要的东 西依规矩定位, 摆放整齐,并 明确表明。
• 目的:不浪费 时间寻找需要 的物品
整顿
是对整理后的东西的整顿。
• 定位摆放
物各有位,物在其位
• 定量摆放
过目知数,控制库
• 目视管理
标识清晰,一目了然
• 取用方便
提高效率,保证质量
整顿推行要点
• 1、将整理后的货架、场所空间进行重新规 划使用。
库存的浪费
• 后果: 1、过多的库存,使资金都积压在原材料, 企业的利润有相当一部分被货款利息吃掉了。 2、库存过多,会产生锈蚀变质, 3、增加人去清点、整理
库存的浪费
后果
增加利息负担 占用场地厂房 管理人员增加 入出库的搬运 处锈等工作浪费 长时间失效的浪费
最大的问题: 完全掩盖了工 厂里的问题。
• 精益生产的基本思想 • 2.1 一大目标:低成本、高效率、高
质量地进行生产,消除生产中的一切浪 費 • 2.2两大支柱:准时化、自働化 • 2.3一大基础:改善活動
精益的5项原则
• 1 价值观(Value) 2 价值流(Value Stream) 3 流动(Flow) 4 拉动(Pull) 5 尽善尽美(Perfection)
动作的浪费
• 根源:
素养
• 定义:人人依规矩行事,工作的每 分钟、每个环节都具备良好的思维 方式。
• 目的:提升人的品质,使每个人都 成为对任何工作都持认真态度 的 优秀管理者和员工。
5S活动开展原则
• 1、自我管理 • 2、持之以恒 • 3、小处着眼
• 实例
返回
推行精益重在坚持
维持
改 善
改善和维持 循环
整顿
• 定义:要的东 西依规矩定位, 摆放整齐,并 明确表明。
• 目的:不浪费 时间寻找需要 的物品
整顿
是对整理后的东西的整顿。
• 定位摆放
物各有位,物在其位
• 定量摆放
过目知数,控制库
• 目视管理
标识清晰,一目了然
• 取用方便
提高效率,保证质量
整顿推行要点
• 1、将整理后的货架、场所空间进行重新规 划使用。
库存的浪费
• 后果: 1、过多的库存,使资金都积压在原材料, 企业的利润有相当一部分被货款利息吃掉了。 2、库存过多,会产生锈蚀变质, 3、增加人去清点、整理
库存的浪费
后果
增加利息负担 占用场地厂房 管理人员增加 入出库的搬运 处锈等工作浪费 长时间失效的浪费
最大的问题: 完全掩盖了工 厂里的问题。
• 精益生产的基本思想 • 2.1 一大目标:低成本、高效率、高
质量地进行生产,消除生产中的一切浪 費 • 2.2两大支柱:准时化、自働化 • 2.3一大基础:改善活動
精益的5项原则
• 1 价值观(Value) 2 价值流(Value Stream) 3 流动(Flow) 4 拉动(Pull) 5 尽善尽美(Perfection)
动作的浪费
• 根源:
《精益生产基础原》课件

流动制造
01
02
03
流动制造
通过采用拉动系统、单件 流等生产方式,实现生产 过程中的物料需求指令,实现按需 生产和减少在制品库存。
单件流
追求生产过程中的单件流 动,减少等待和搬运浪费 ,提高生产效率。
完美流程
完美流程
追求生产流程的完美化, 通过不断改进和优化,消 除浪费和降低成本。
解决方案
针对这些挑战,企业可以采取一系列的解决方案,如加强培训和宣传、优化资源 配置、引进先进技术等。这些解决方案有助于克服实施精益生产过程中的障碍, 确保企业能够顺利实现精益生产的目标。
对未来精益生产的展望
未来趋势
随着科技的不断进步和市场环境的变化,精 益生产将会继续发展并呈现出新的趋势。例 如,数字化和智能化技术的应用将进一步提 高生产效率和灵活性;可持续发展将成为企 业追求的重要目标;供应链协同和全球化的 趋势将要求企业更加注重跨组织的协作和共 赢。
整理
将工作场所内的物品进行分类, 保留需要的物品,移除不需要的 物品,使工作场所变得整洁有序 。
素养
培养员工良好的工作习惯和职业 素养,提高工作效率和品质意识 。
快速换模
快速换模是一种减少换模时间 、提高生产效率的精益工具。
通过减少换模时间,可以降低 生产成本、提高设备利用率和 灵活性,满足多品种、小批量 的生产需求。
总结词
快速换模技术应用,提高生产效率和灵活性
详细描述
某电子制造企业通过引入快速换模技术,缩短换模时间,提高生产效率。同时 ,采用标准作业和作业研究,优化生产流程,减少生产浪费。这种灵活性使得 企业能够快速应对市场变化和客户需求。
案例三:某机械制造企业的价值流图应用
总结词
精益生产培训课件(PPT 91页)
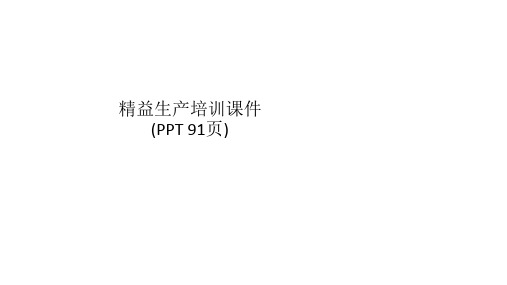
Value Added
Non Value Added
Distance
Time
360 Ft. 12 min.
工作场所布置
物料固定场所
工具,物料放在小臂范围内
工作场所布置
工作场所布置
物料依左右手拿的顺序去摆放
13 4 2
重量堕送
工作场所布置
工作场所布置
保持良好的姿势
工作台的设计:工作 台高度应在肘下一至 三寸
工具设备 设计
一.尽量使用工装或足踏工具,以解除手的“持住”动作。 二.可能时应将两种以上工具合并。 三.对手指的工作负荷应依其本能予以分配。 四.手柄之设计应可能使其与手之接触面积增大。 五.机器设备之操作杆、开关、手柄之位置应在工作者正常作业范围内,以尽量
级别 1 2 3 4 5
运动驱轴
指节 手腕
肘 肩 身躯
人体运动部位
手指 手指及手掌 手指,手掌及前臂 手指,手掌,前臂及上臂 手指,手掌,前臂,上臂及肩
在满足动作需要的情况下,人体的动作应尽量应用最低等级。
2.工作场所 布置
原则:
工具、物料应放置在固定的场所. 工具、物料及装置应放置在小臂的工作范围内. 工具、物料应依工作顺序放置排列以利使用. 零件物料之供给,应利用其重量堕送. 工作台及椅之式样使工作者保持良好的姿势
05
02
过量生产浪费
06
03
搬运浪费
07
04
动作浪费
08
等待浪费 库存浪费 过度加工浪费 管理浪费
良纠正 浪费
定义:由于工厂内出现不良品,需要进行处置的时间、人力、物 力上的浪费,以及由此造成的相关损失。
•额外的时间和人工进行检查, 返工等工作 •由此而引起的无法准时交货 •企业的运作是补救式的,而非 预防式的(救火方式的运作)
精益生产基础知识PPT课件

23
第二十三页,共48页。
Waste of Overproduction 过量生产
Producing More Than Needed
Producing Faster Than Needed
生产多于所需 快于所需
24
第二十四页,共48页。
Waste of Inspection/Correction/Rework 检验/校正 / 返工
Seiri Seiton Seiso Shitsuke Seiketsu
+ Safety
+ Save
整理 Sort
整顿 Straighten 清掃 Shine 清洁/展开 / 規範 Standardize
素養/保持/自律 Sustain
+ 安全
+ 节约
8
第八页,共48页。
Workplace Organization - 5S 现场组织管理- 5·S
第一步: Seiri 整理
• 确认什么是需要的 • 使用的频率有多高 • 给不需要的贴上标签 • 处理贴上标签的物品
9
第九页,共48页。
Workplace Organization - 5S 现场组织管理- 5S
5S 小组清查:
把生产不必、物料ID: 3、物料数量: 4、物料价值:
而在80年代中期被欧美企业纷纷采用。随着微利时代的 来临,精益生产模式成为企业竞争的有力武器。
3
第三页,共48页。
世界500强的制造业公司中
实施精益生产的占95%以上
4
第四页,共48页。
精益生产“五個原则”
①价值
— 站在客户的立场上;
②价值流 — 从接单到发货过程的一切活动;
第二十三页,共48页。
Waste of Overproduction 过量生产
Producing More Than Needed
Producing Faster Than Needed
生产多于所需 快于所需
24
第二十四页,共48页。
Waste of Inspection/Correction/Rework 检验/校正 / 返工
Seiri Seiton Seiso Shitsuke Seiketsu
+ Safety
+ Save
整理 Sort
整顿 Straighten 清掃 Shine 清洁/展开 / 規範 Standardize
素養/保持/自律 Sustain
+ 安全
+ 节约
8
第八页,共48页。
Workplace Organization - 5S 现场组织管理- 5·S
第一步: Seiri 整理
• 确认什么是需要的 • 使用的频率有多高 • 给不需要的贴上标签 • 处理贴上标签的物品
9
第九页,共48页。
Workplace Organization - 5S 现场组织管理- 5S
5S 小组清查:
把生产不必、物料ID: 3、物料数量: 4、物料价值:
而在80年代中期被欧美企业纷纷采用。随着微利时代的 来临,精益生产模式成为企业竞争的有力武器。
3
第三页,共48页。
世界500强的制造业公司中
实施精益生产的占95%以上
4
第四页,共48页。
精益生产“五個原则”
①价值
— 站在客户的立场上;
②价值流 — 从接单到发货过程的一切活动;
精益生产基础知识培训课件ppt
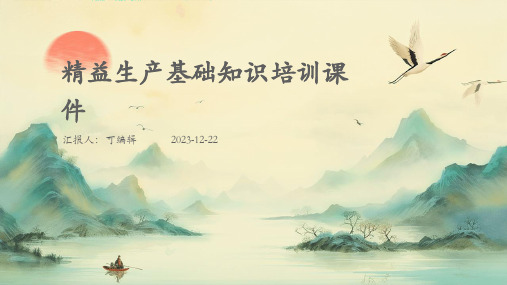
服务成本降低
资源优化
合理配置人力、物力和财力资源,避免浪费。
成本控制
通过精细化管理,降低服务过程中的成本支出。
价值创新
通过创新服务模式和手段,提高服务附加值,实现成本与效益的平衡。
服务效率提高
时间管理
合理安排服务时间,提高服务效率。
团队协作
加强团队之间的沟通与协作,提高工作效率 。
技术应用
利用先进的技术手段,如数字化、智能化等 ,提高服务效率和质量。
价值流分析
定义
价值流分析是一种识别、 测量和分析产品从原材料 到最终客户整个过程中的 所有活动的方法。
目的
通过价值流分析,企业可 以找出过程中的瓶颈和浪 费,并采取措施消除或减 少这些瓶颈和浪费。
步骤
价值流分析包括绘制当前 状态图、绘制未来状态图 、制定实施计划等步骤。
5S管理
定义
步骤
5S管理是一种以整理、整顿、清洁、 清洁检查和素养为主要内容的现场管 理方法。
精益生产的核心思想
01
02
03
04
以客户需求为导向
将客户的需求作为生产的核心 ,确保产品和服务满足客户需
求。
消除浪费
通过消除生产过程中的浪费, 提高生产效率和降低成本。
持续改进
不断寻求改进的机会,持续优 化生产过程和流程。
团队合作
强调团队成员之间的协作和沟 通,共同实现生产目标。
02
精益生产工具与方法
特点
注重客户需求,强调持续改进, 追求卓越品质,降低成本并提高 生产效益。
精益生产的发展历程
01
02
03
起源
起源于日本丰田汽车公司 ,以减少浪费、提高生产 效率为目标。
《精益生产基础培训》ppt课件pptx
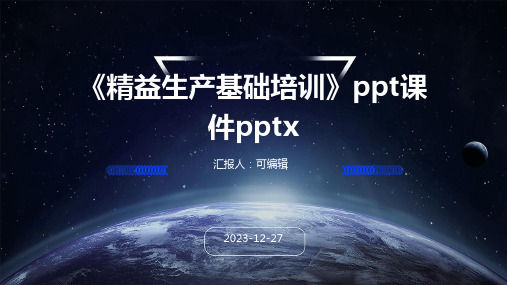
单元化生产
单元化生产是将生产线或设备按照产品族或工艺特点进行模块化设计,以提高生产 效率和灵活性的一种生产方式。
通过单元化生产,可以实现小批量、多品种的生产,满足市场需求的快速变化。同 时还可以提高设备的利用率和员工的技能水平。
单元化生产的实施需要提前进行生产线或设备的规划和设计,并注重员工培训和跨 部门协作。
竞争中获得优势。
促进可持续发展
精益生产注重环保和资源节约 ,有助于企业实现可持续发展
。
精益生产的历史与发展
起源
未来趋势
精益生产起源于日本丰田汽车公司的 生产方式,旨在消除浪费、提高效率 和效益。
随着科技的不断进步和应用,精益生 产将进一步与数字化、智能化相结合 ,实现更高水平的自动化和智能化。
发展历程
Straighten)、清扫(Shine)、清洁 (Standardize)、素养(Sustain)五
个方面。
通过实施5S管理,可以提高生产现场 的整洁度和效率,减少浪费,提高生产 质量、定期 检查和持续改进,确保管理效果的持久
性和有效性。
明确改进措施、时间表、责任人及所需资源。
风险评估与应对
预测潜在风险,制定应对措施,确保改进计划的顺利实施。
实施改进措施
1 2
培训与沟通
对相关人员进行培训,确保他们理解并掌握改进 措施。
资源配置
确保所需的人员、设备、材料和技术得到有效配 置。
3
实施改进措施
按照计划逐步实施改进措施,确保改进过程顺利 进行。
随着丰田生产方式的成功,精益生产 逐渐被全球范围内的企业所采纳和推 广。
02
精益生产的核心原则
价值导向
价值导向
强调从客户需求出发,识别并确 定客户认为有价值的流程和功能 ,消除非增值的环节和活动,实
《精益生产基础培训》ppt课件pptx
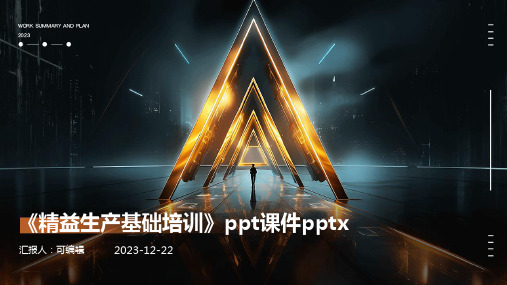
价值流图绘制与改进
绘制价值流图
根据价值流分析结果,绘制企业价值 流图,直观展示各环节之间的关系和 现状。
改进策略制定
针对价值流图中的瓶颈和浪费环节, 制定相应的改进措施和方案。
5S管理实施与标准化
5S管理推行
在企业内部推行5S管理,即整理、整顿、清扫、清洁和素养,提高现场管理水 平和效率。
标准化实施
精益生产的核心思想
01
02
03
04
价值流分析
识别并消除生产过程中的浪费 ,确保产品从供应商到客户的
过程是增值的。
流动与平衡
优化生产流程,确保产品在生 产过程中快速、顺畅地流动, 同时保持生产过程的平衡。
拉动系统
根据客户需求进行生产,采用 拉动系统实现准时化生产。
持续改进
不断寻求改进机会,通过不断 优化生产过程来提高效率、降
TPM有助于提高产品质量和生 产稳定性,降低生产成本。
TPM的实施需要制定详细的维 护计划和培训员工掌握维护技 能。
03
精益生产实施步骤
目标设定与价值流分析
目标设定
明确企业实施精益生产的目标,包括降低成本、提高效率、 优化流程等。
价值流分析
对企业业务流程进行全面分析,识别价值流中的瓶颈和浪费 环节。
02
精益生产工具与技术
价值流图
价值流图是一种可视化工具,用于描 绘产品从原材料到最终客户手中的整 个过程。
价值流图有助于企业了解客户需求, 制定出更符合客户期望的生产计划。
通过价值流图,企业可以识别出过程 中的瓶颈、浪费和不必要的环节,从 而优化流程,提高效率。
价值流图的应用范围广泛,适用于不 同规模和行业的企业。
01
《精益生产》PPT课件
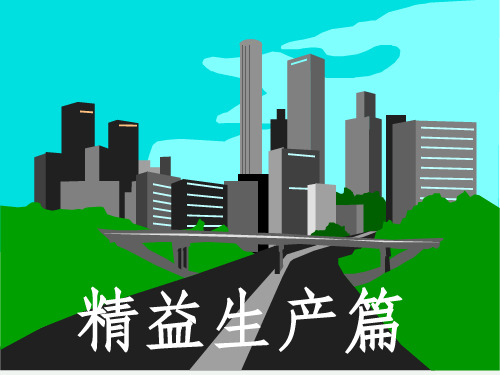
设备现场管理应用
在精益生产方式中,设备故障被视为无效劳动和浪费, 提出设备故障要向零进军,这就要求设备运行过程尽量 不发生故障,少发生故障。
实行全员维修和保养; 实行针对性预防检修; 实行改善性维修;
精益生产系统的五项原则
质量是 制造出来的
标准化
精益的 制造系统
持续改进
员工参与
短的制造周期
拉动式方法的特点:
坚持一切以后道工序需求出发,宁肯中断生产,也不搞超前超
1 量生产。拉动式生产的核心就是准时化,就是要求在需要的事
后,生产需要的产品和需要的数量,所以又把它称为准时化生 产(Just In Time)。
生产指令不仅仅是生产作业计划,而且还用看板进行为调节。
2 看板成为实施拉动式生产的重要手段。
看板来源于大野耐一从美国超级市场的启示。
拉动式方法 在生产制造过程中的具体运用
1 以市场需求拉动企业生产。
在企业内部,以后道工序拉动前道工序生产,以总装配拉动总
2 成装配,以总成装配拉动零件加工,以零件拉毛坯生产,用以
大幅度压缩在制品储备,消除无效劳动。
U型平面布置的“一个流”生产线; 多工序管理和多机床操作 成批轮番作业的生产线 快速换模技术,实现小批量多批次生产
jit以小批量生产为准则换模工作必须尽快完成消除浪费的方设计流程连接操作平衡工作站能力减小批量规减少安装换模时间2tqm全面质量管理尊重员工qcc小组合理化建议3稳定计划均衡计划不超过生产能力建立冻结区间指计划固定不弯一个时间区段4看板控制由后向前传送指令5与供应商紧密合作缩短提前期增加供货频率交货要及时保证质量可靠性6减少额外存货寻找其他区采用传送带运输机7改进产品设计产品标准化零件标准化及零件数减少改进过程设计产品质量期望jit七个前提条件61传统生产管理中的生产指令生产计划实际生产数量生产顺序表库存工序a工序b工序c库存完成生产指令计划生产数量与实际生产数量不同生产指令生产指令62jit生产计划实际生产数量生产顺序表看板工序a工序b工序c看板完成生产指令计划生产数量与实际生产数量相同63确定看板数量每个容器内数量64防止过量生产生产没有看板不能生产也不能运送目视管理看板必须附在实物上按照取下看板的顺序进行生产改善工具不能把不良品送往下一工序看板机能生产及运送的工作指令65生产系统
精益生产基础培训课件

价值流图的应用
价值流图广泛应用于企业生产管理 、供应链优化等领域,有助于提高 生产效率、降低成本、改进质量。
流程图
流程图定义
流程图是一种用图形符号表示 工作流程或业务流程的方法, 可帮助人们更好地了解和改进
流程。
流程图的绘制
通过绘制流程图,将复杂的工 作流程或业务流程进行可视化 ,清晰地展示出各环节之间的
精益生产方式强调将顾客需求和期望置于首位,通过不断满 足顾客需求来推动企业的发展。
提高顾客满意度
精益生产方式致力于提高产品质量、缩短交货期、降低成本 ,从而提升顾客满意度。
消除浪费
七大浪费
精益生产将浪费分为七大类,包括过量生产、库存、运输、等待、加工、不 良品和人力资源浪费。
消除浪费的途径
通过优化流程、减少浪费环节、提高生产效率等措施,实现资源的有效利用 。
它关注客户需求,以最小成本 和最高质量来满足客户需求,
并不断追求卓越。
精益生产的核心是消除浪费, 包括减少不必要的库存、降低 制造成本、提高产品质量和缩
短交货周期。
精益生产的发展历程
精益生产的起源可以追溯到20世纪50年代的日本,当时日本汽车制造商丰田汽车 公司的工程师们开始研究如何提高生产效率和质量。
案例分析
通过学习精益生产理论,某公 司成功提高了生产效率
通过应用精益工具,某公司减 少了浪费并降低了成本
某公司通过数据分析,发现生 产瓶颈并采取措施加以改进
06
精益生产成功实施的关键因素
领导者的支持和员工的参与
领导者应积极参与精益生产培训,了解精益思想及价值观, 并推动精益改善项目的实施。
员工需要充分认识到精益生产对他们工作及职业发展的影响 ,并积极参与精益生产的实践。
价值流图广泛应用于企业生产管理 、供应链优化等领域,有助于提高 生产效率、降低成本、改进质量。
流程图
流程图定义
流程图是一种用图形符号表示 工作流程或业务流程的方法, 可帮助人们更好地了解和改进
流程。
流程图的绘制
通过绘制流程图,将复杂的工 作流程或业务流程进行可视化 ,清晰地展示出各环节之间的
精益生产方式强调将顾客需求和期望置于首位,通过不断满 足顾客需求来推动企业的发展。
提高顾客满意度
精益生产方式致力于提高产品质量、缩短交货期、降低成本 ,从而提升顾客满意度。
消除浪费
七大浪费
精益生产将浪费分为七大类,包括过量生产、库存、运输、等待、加工、不 良品和人力资源浪费。
消除浪费的途径
通过优化流程、减少浪费环节、提高生产效率等措施,实现资源的有效利用 。
它关注客户需求,以最小成本 和最高质量来满足客户需求,
并不断追求卓越。
精益生产的核心是消除浪费, 包括减少不必要的库存、降低 制造成本、提高产品质量和缩
短交货周期。
精益生产的发展历程
精益生产的起源可以追溯到20世纪50年代的日本,当时日本汽车制造商丰田汽车 公司的工程师们开始研究如何提高生产效率和质量。
案例分析
通过学习精益生产理论,某公 司成功提高了生产效率
通过应用精益工具,某公司减 少了浪费并降低了成本
某公司通过数据分析,发现生 产瓶颈并采取措施加以改进
06
精益生产成功实施的关键因素
领导者的支持和员工的参与
领导者应积极参与精益生产培训,了解精益思想及价值观, 并推动精益改善项目的实施。
员工需要充分认识到精益生产对他们工作及职业发展的影响 ,并积极参与精益生产的实践。
精益生产基础PPT课件

10.0
Ap Ma Jun Jul Au Se Oc No De Jan Fe Ma
ry
g pt t v c
br
Actual
Plan
第24页/共85页
定货执行表
100% 80% 60% 40% 20% 0%
ON TIME DELIVERY
$55,000 $53,000 $51,000 $49,000 $47,000 $45,000 $43,000 $41,000 $39,000 $37,000 $35,000
第30页/共85页
TURNS
$60,000
3.00
$50,000
2.50
$40,000
2.00
$30,000
1.50
$20,000
1.00
$10,000
0.50
$0
0.00
Raw
FG
WIP
Inv. Turns
Goal
第25页/共85页
生产周期时间 (MCT)
原料
操作 1
操作 2
操作 3
操作 4
成品
MCT
从原料输入各个操作单位开始到成品制成止 的时间
2.50% 2.30% 2.10% 1.90% 1.70% 1.50%
$250,000 $230,000 $210,000 $190,000 $170,000 $150,000
% of sales Goal
$ Warranty Expenses
Shipable Backlog
% Of All Backlog
3.1
Q3
Q4
Q3
Q4
5.2%
7.3%
3.1
精益生产(完美版)ppt课件
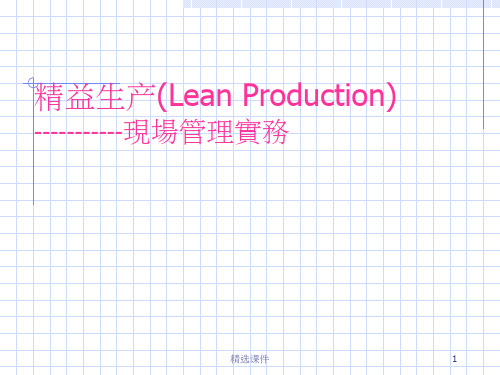
标准作业
生产安定化
标准作业
非标准作业
线上操作者负责 线外“水蜘蛛”负责
对“水蜘蛛”来说 是标准作业
全体标准作业
精选课件
41
(2)产距时间 ——生产的指挥棒
考虑信息流动—— 生产指示明确
流畅
便于信息传递
☆ 后补式/前后式生产指示 ☆ 生产实绩显现化 ☆ 便于批量区分
④.少人化生产—— 人多人少都能生产
☆ 警示灯及线体控制
☆ U形布置方式
☆ 逆时针摆放 ☆ 设备间无阻隔 ☆人与设备分工:
少人 化
人—装料、卸料
设备—加工
☆启动按钮安装方式适当
精选课件
32
⑤. 质量
精选课件
8
(3)消除浪费——管理的重要目的之一
Management
创造性的管理活动 提高产品和服务的附加价值
+1 增加价值
0
-1
消除浪费
最大限度地减少不增值劳动 封闭性的管理活动
精选课件
9
精益思维(Lean Thinking)的5个基本原则
No.1 从顾客的角度而不是从某个公司、部门或机构 的角度确定价值;
37
Step3 将长屋型改为大通铺式
大 通 铺 式 布 置
Hale Waihona Puke 精选课件38Step4 整体上呈一笔画布置
一 笔 画 布 置
精选课件
39
STEP2 安定化生产
人员安定化管理
安定化 生产
设备安定化管理 质量安定化管理 切换安定化管理
现场安定化管理
精选课件
40
1、人员安定化管理
(1)标准作业与非标准作业
精选课件
27
生产安定化
标准作业
非标准作业
线上操作者负责 线外“水蜘蛛”负责
对“水蜘蛛”来说 是标准作业
全体标准作业
精选课件
41
(2)产距时间 ——生产的指挥棒
考虑信息流动—— 生产指示明确
流畅
便于信息传递
☆ 后补式/前后式生产指示 ☆ 生产实绩显现化 ☆ 便于批量区分
④.少人化生产—— 人多人少都能生产
☆ 警示灯及线体控制
☆ U形布置方式
☆ 逆时针摆放 ☆ 设备间无阻隔 ☆人与设备分工:
少人 化
人—装料、卸料
设备—加工
☆启动按钮安装方式适当
精选课件
32
⑤. 质量
精选课件
8
(3)消除浪费——管理的重要目的之一
Management
创造性的管理活动 提高产品和服务的附加价值
+1 增加价值
0
-1
消除浪费
最大限度地减少不增值劳动 封闭性的管理活动
精选课件
9
精益思维(Lean Thinking)的5个基本原则
No.1 从顾客的角度而不是从某个公司、部门或机构 的角度确定价值;
37
Step3 将长屋型改为大通铺式
大 通 铺 式 布 置
Hale Waihona Puke 精选课件38Step4 整体上呈一笔画布置
一 笔 画 布 置
精选课件
39
STEP2 安定化生产
人员安定化管理
安定化 生产
设备安定化管理 质量安定化管理 切换安定化管理
现场安定化管理
精选课件
40
1、人员安定化管理
(1)标准作业与非标准作业
精选课件
27
精益生产基础知识培训课件(PPT 56页)

•范围 •改善指引给出了公司内的改善活动所需的改善指导. •需要收集那些数据,做什么改善 •如何展现自己的成绩
New Challenge
Page 2
二、培训目标
• 为改善活动提供指引 • 为怎样填写改善表格提供指引 • 从事情的不同角度来做改善,然后达到目标 • 查看不同的改善例子 • 持续执行改善,时刻牢记改善的重要性
➢标准化(实施系统控制) 1. 列出系统,程序,规格中所不能预防此问题发生与流出的所有文件 (作业流程,程序文件,图纸,规格书,控制计划等); 2. 依照新的作业方法及时更新、受控并发放相关的文件; 3. 水平展开,扩大改善范围; 4. 同时更新培训资料,组织培训。
➢对策的内容要详细,具体,语言要简练,通俗易懂;
➢要层次清晰,有先后,主次之分。
改善KAIZEN
New Challenge
Page 24
改善KAIZEN
6: 对策实施
➢依对策的先后与主次 1. 列出定下的措施并定出开始执行时间与计划完成时间; 2. 安排所需的资源(团队组长协调,公司高层支持); 3. 分派责任:有负责人 4. 监督执行:要有确认人
1.对生产部日常活动进行 管理 2.对员工进行指导和培训 (作业方法,操作技巧, 品质与安全意识等) 3.模具/机器设备的日常 点检与维护 4.统计生产过程的不良数 据并分析原因,进行改善 5.执行改善小组所要求的 其它工作内容
1.制作BOM,工艺文件 ,优化生产工艺及参数
2.制作工装夹具,模具制 作/维修/保养(含计划) 3.生产设备的定期保养与 维护
加强客户关注
D Guarantee
Delivery保证交期
Q
Improved
Logistics 改进物流
New Challenge
Page 2
二、培训目标
• 为改善活动提供指引 • 为怎样填写改善表格提供指引 • 从事情的不同角度来做改善,然后达到目标 • 查看不同的改善例子 • 持续执行改善,时刻牢记改善的重要性
➢标准化(实施系统控制) 1. 列出系统,程序,规格中所不能预防此问题发生与流出的所有文件 (作业流程,程序文件,图纸,规格书,控制计划等); 2. 依照新的作业方法及时更新、受控并发放相关的文件; 3. 水平展开,扩大改善范围; 4. 同时更新培训资料,组织培训。
➢对策的内容要详细,具体,语言要简练,通俗易懂;
➢要层次清晰,有先后,主次之分。
改善KAIZEN
New Challenge
Page 24
改善KAIZEN
6: 对策实施
➢依对策的先后与主次 1. 列出定下的措施并定出开始执行时间与计划完成时间; 2. 安排所需的资源(团队组长协调,公司高层支持); 3. 分派责任:有负责人 4. 监督执行:要有确认人
1.对生产部日常活动进行 管理 2.对员工进行指导和培训 (作业方法,操作技巧, 品质与安全意识等) 3.模具/机器设备的日常 点检与维护 4.统计生产过程的不良数 据并分析原因,进行改善 5.执行改善小组所要求的 其它工作内容
1.制作BOM,工艺文件 ,优化生产工艺及参数
2.制作工装夹具,模具制 作/维修/保养(含计划) 3.生产设备的定期保养与 维护
加强客户关注
D Guarantee
Delivery保证交期
Q
Improved
Logistics 改进物流
《精益生产完整》课件

人工智能可以通过机器学习和深度学习等技术,对大量数据进行处理和 分析,预测未来的市场需求和生产趋势,为生产计划和决策提供依据。
人工智能还可以通过智能控制和优化算法等技术,对生产过程进行实时 监控和调整,提高生产过程的稳定性和效率。
绿色精益生产
绿色精益生产是指将环保理念融入生产 过程中,通过改进和优化生产过程,减 少对环境的负面影响。
精益生产的重要性
01
提高生产效率和产 品质量
通过消除浪费和优化流程,精益 生产能够显著提高生产效率和产 品质量。
降低成本
02
03
增强企业竞争力
通过减少浪费和优化库存,精益 生产能够降低生产成本和运营成 本。
精益生产能够帮助企业提高效率 和效益,从而在激烈的市场竞争 中获得竞争优势。
精益生产的历史与发展
总结词:精细管理
详细描述:某物流企业通过精益化运营实践,实现了对运输、仓储和配送等环节的精细化管理。通过 消除浪费、提高运输效率、优化仓储布局和配送路线,该企业成功降低了运营成本,提高了客户满意 度。同时,精益化运营还促进了企业内部的沟通与协作,增强了团队凝聚力。
THANK YOU
01
人才缺乏
中国在精益生产方面的专业人才相对较 少,这可能会影响精益生产的推广和应 用。
02
03
制度环境
中国的制度环境可能对精益生产的推 广和应用产生影响,例如法律法规、 政策等。
05
精益生产的未来发展
数字化精益生产
01
数字化精益生产是指利用数字化技术对生产过程进行优化和改进,以提高生产 效率和产品质量。
素养
培养员工遵守规章制度、注重 细节、积极主动的良好习惯, 提高整体素质。
快速换模
人工智能还可以通过智能控制和优化算法等技术,对生产过程进行实时 监控和调整,提高生产过程的稳定性和效率。
绿色精益生产
绿色精益生产是指将环保理念融入生产 过程中,通过改进和优化生产过程,减 少对环境的负面影响。
精益生产的重要性
01
提高生产效率和产 品质量
通过消除浪费和优化流程,精益 生产能够显著提高生产效率和产 品质量。
降低成本
02
03
增强企业竞争力
通过减少浪费和优化库存,精益 生产能够降低生产成本和运营成 本。
精益生产能够帮助企业提高效率 和效益,从而在激烈的市场竞争 中获得竞争优势。
精益生产的历史与发展
总结词:精细管理
详细描述:某物流企业通过精益化运营实践,实现了对运输、仓储和配送等环节的精细化管理。通过 消除浪费、提高运输效率、优化仓储布局和配送路线,该企业成功降低了运营成本,提高了客户满意 度。同时,精益化运营还促进了企业内部的沟通与协作,增强了团队凝聚力。
THANK YOU
01
人才缺乏
中国在精益生产方面的专业人才相对较 少,这可能会影响精益生产的推广和应 用。
02
03
制度环境
中国的制度环境可能对精益生产的推 广和应用产生影响,例如法律法规、 政策等。
05
精益生产的未来发展
数字化精益生产
01
数字化精益生产是指利用数字化技术对生产过程进行优化和改进,以提高生产 效率和产品质量。
素养
培养员工遵守规章制度、注重 细节、积极主动的良好习惯, 提高整体素质。
快速换模
- 1、下载文档前请自行甄别文档内容的完整性,平台不提供额外的编辑、内容补充、找答案等附加服务。
- 2、"仅部分预览"的文档,不可在线预览部分如存在完整性等问题,可反馈申请退款(可完整预览的文档不适用该条件!)。
- 3、如文档侵犯您的权益,请联系客服反馈,我们会尽快为您处理(人工客服工作时间:9:00-18:30)。
SCREEN PRINT
BARCODE APPLY
FUJI CP-IV TOPSIDE PLACE
FUJI IP-II TOPSIDE
PLCC
REFLOW OVEN
TOPSIDE PLACEMENT CELL
AXIAL
FUJI GLV EPOXY PLACE
FUJI CP4-II BOTTOM
SMD
TREATMENT
AREA
CLEAN
OP 70
4
OP 125
8
OP 165
11
OP 260
16
OP 320
20
OP 370
23
OP 430
26
OP 460
29
INSP AREA
OP 80
5
OP 130
9
OP 220
14
OP 270
17
OP 330
21
OP 380
24
OP 440
27
OP 520
31
1559M30 G06/G10 Front Case
1958 - Shoichiro Toyoda 计划在 Motomachi 建立一个新的工厂及生产 线,时间上正好是在亨利 福特的 River Rouge 工厂之后,它后来被政府 命名为-丰田城。 丰田向美国出口第一辆汽车 Corona。
精益生产模式年表
1980 – 丰田汽车在美国与通用汽车 NUMMI工厂 合资,并将丰田生产方式 植入这个原本绩效颇差的工厂,经过整改,使得这个工厂一举打破了所有 通用汽车工厂成本、交货及质量的历史记录。
Deburr
Finish Mill OD
5 Axis
42
Finish Mill OD
5 Axis
42
42
5 Axis
Finish Mill OD
42
5 Axis
Finish Mill OD
工厂布局图 – 之前
工厂布局图 – 之后
B1B 飞机维修 (润滑 & 维修) 流程
群策群力行动之前
Action Workout Results
润滑剂 工具库
群策群力行动之后
如何实现的: * 缩减准备时间 * 重组工作场所 (重新将工具等部署于方便 易取的地方) * 流程标准化 (重新排序来优化流程)
轻便工具和设备
润滑油 小车
Action Workout Results
轻便小车
工具间
New Lube & Service
Yellow = ADG/IDG Flush Red = Strut Servicing Green = Crew Entry Ladder & Flap/Salt Servicing
对分析阶段进行评估 - 咨询师意见 - 与团队成员沟通所有信息 培训团队成员六西格玛工具 团队成员精益生产培训 回顾旧流程图 创建新流程图 更新项目管理检查单 筛选潜在原因 X’s 识别产生变异的根本原因 建立过程容差 编制改进行动计划 - 应用精益生产工具 进行风险评估 风险控制计划 为改进计划赢得支持 改进计划实施 群策群力改善行动 - 实施单元设计布局 - 建立绩效测量基准 - 建立目视管理工作场所 - 流水线硬件设施确认 收集和分析数据以确认改进活动 的有效性 沟通改进后所取得的成绩,编制 项目汇报报告(ppt 文件) - 与咨询师评估,设计汇报报告 - 将汇报报告提交领导层
不是让人
随着东西运动。这就是我们最基本的观
念,流水线的传送带仅仅是众多的手段之一。”
- 亨利 福特 : “ 今天和明天”
精益生产模式年表
1937 – 以丰田自动纺织机公司的自动化部为雏形,建立了丰田汽车有限 公司并设立了工厂,由于生产流动过程的不平衡,引发他们开始在生产线 上悬挂使用标志进行生产指挥,称为“ 准时制生产”
工具间
Old Lube & Service
Yellow = ADG/IDG Flush Red = Strut Servicing Green = Crew Entry Ladder & Flap/Salt Servicing
全部距离 (行走距离×人) = 17,017 feet 生产周期 = 19 hours
1
WCI
OP 280
18
MAZAK
OP 40/50
3
OP 400/410
25
MILLING
19 CENTER
MAKINO
DIX I
OP 30
2
OP 40/100
10
OP 230/240
15
OP 340/350
22
TURING
CENTER
OP 110
7
OP 190
13
图中描述出当前流程非常混乱
SURFACE
• 分析
– 观察表 Observation Sheets – 过程产能分析 Process Capacity Table – 标准作业表 Standard Work Sheet – 标准作业结合表 Standard Work Combination – 交叉培训计划矩阵 Cross Training Matrix – 周期 / 节拍时间图 Cycle Time / TAKT Time Bar Chart
5 Axis
35
Simi Finish
5 Axis
35
Clean
Finish Turn
V/L
9
RM
WC
6
4 Axis
Mill Split face Mill Keyway
18
V/L
Rough Turn
35
5 Axis
2.5
Tumble
Simi Finish
Tumble Deburr
Parts would be assembled before going to Deburr and tumblin进行评估 - 咨询师意见 - 与团队成员沟通所有信息 培训团队成员六西格玛工具 团队成员精益生产培训 创建行动计划清单 发布改进活动更新的流程控制文 件 更新项目管理检查单 再次验证原因效果分析来确认 X’ s 与 Y’s 的对应关系 确定过程能力 实施控制系统 建立后续行动计划和人员责任机 制 识别系统可进行标准化的机会 汇总项目的经验和教训 确认绩效测量基准 将流程交接给相应实际流程负责 人 编制项目汇报报告(ppt 文件) - 与咨询师评估,设计汇报报告 - 将汇报报告提交领导层 监控流程绩效趋势 完成行动计划清单 员工后续培训 编制下一次精益生产行动计划
全部距离 生产周期
(行走距离×人) = 3.85 hours
=
1,381
f98e20e%%t
提高 提高
测量
生产过程中的浪费
观察说明书
• 1. 详细列出完成操作所需的所有步骤 • 2. 观测,并对整个过程进行时间测量 • 3. 确认每一个步骤是手动操作还是自动操作
手动 – 装载/卸载部件,调整量具及部件,填写报表等 自动 – 机器从被按动开始按钮起,到完成加工过程之间的周期
介绍
群策群力工具:
• 改进 - ( 群策群力行动 )
– “ 四幅” 关键图表 – 目视 – 其他可以从前面阶段应用的工具
• 控制
– 行动计划
六西格玛精益生产计分卡/检查单
1
2
3
测量
分析
改进
前期工作 - 与公司领导层沟通精益生产实施计 划 - 获得领导层支持 - 项目范围及涉及企业流程确认 - 为流程设定负责人 - 确定项目组核心团队成员 - 项目所需资源确认 培训团队成员六西格玛工具 团队成员精益生产培训 创建产品结构图 确定客户需求 - 应用QFD工具分析客户需求 - 确定其他所需数据 - 计算和确定节拍时间 创建流程图 创建混合型号图 创建流程关系图 对所有流程完成观察表 确定绩效标准 - 数据收集,柏拉图分析 - 历史数据分析 测量系统分析 - 重复性&再现性分析 (Gage R&R) 创建周期时间/节拍时间柱状图 计算产品当前过程能力 - 计算 Zst 和 Zlt 编制项目汇报报告(ppt 文件) - 与咨询师评估,设计汇报报告 - 将汇报报告提交领导层
1990 - Womack 和 Jones 出版了“ 改变世界的机器” 一书,唤醒了美 国商业、投资及学术界对“精益思维” 重视。现在,包括GE在内的众多美 国公司纷纷采用丰田公司的“精益模式思维” ,并且已经实施了很长的 时间了。
奋斗还在继续………
介绍
群策群力工具:
• 测量
– 节拍时间 TAKT Time – 混合型号图 Mix Model Map – 流程关系图 Spaghetti Chart – 观察表 Observation Sheets – 周期 / 节拍时间图 Cycle Time / TAKT Time Bar Chart
改善后
R/M
Stock
Front
Ship
Case
节拍时间 = 11.45 Hrs. 库存周转率 = 14 生产周期= 7 Days
Tack Weld 2
Inspection
CMM
Rough Turn
V/L
18
Special Processes
Grit Blast
Spray Coating
FPI
Simi Finish
COATING
FINAL ASSEMBLY
FINAL TEST
LABEL ATTACH
PACK Q.C. AUDIT
SHIP
测量 平衡生产
•节拍时间 (TAKT Time) - 第二个成品下线与第一个成品下线之间的周