六个标准差(6 Sigma)
六标准差之简介—图
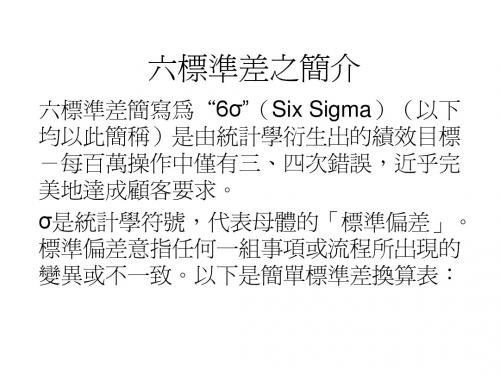
六標準差之簡介
六標準差主要的方法和工具:
• 6σ並非全然一新的發明,其原因係管理業 界最近的一些突破性思惟,另一些則來自 常識(常識是最不平凡的知識)。結合---甚至是執行,當前企業許多不連貫觀點, 趨勢和工具的方法,視改進專案之需求。
六標準差主要的方法和工具:
• 各項己知之方法、工具,均可應用,未開 發之方法、工具,亦可因而有創新開發之 可能。在品質運動盛行後,這些年來,各 流程採用了許多「改進模式」,如PDCA, 在6σ組織中日益通行的改進模式則運用和 參考所謂DMAIC五階段的改進循環模式:
六標準差之好處
• 6σ將可帶來驚人且豐富的改進效 果,6σ推行得當,可帶來鉅額財 務獲利,更能獲無形利益。如員工 士氣的改善、自信的獲得、生氣蓬 勃、充滿熱忱。
六標準差的六大主旨:
• 主旨一:真心以顧客為尊:把顧客擺首要 地位,改進與否端視能否影響顧客滿意和 價值而定。 • 主旨二:管理依資料和事實而更新:提高 並強化事實決定管理的水準。
六標準差之簡介
• 為一全面且具彈性的系統,可用於 獲取、維持和擴大企業的成功。六 標準差的驅動要素,在於洞悉顧客 之需,嚴格使用事實、資料和統計 分析,以及全力關注業務流程的管 理,改善和創新。
六標準差潛藏的好處:
• 1.6σ涵括多方面的企業經營作業 典範和技能(一些屬於進階,一些 屬於常識),這些是成功和成長的 要件。我們可以將6σ套用在許多 不同的業務和挑戰上-----從策略規 劃到營運到顧客服務,並獲取最大 成效。
什么是六西格玛

什么是六西格玛?六西格玛即6σ,σ是一个小写西腊字母,读作西格玛,是统计学术语,代表标准差,日常交流中人们使用得并不多。
作为眼下最时髦的企业管理手段,六西格玛的含义是指:通过设计、监督每一道生产工序和业务流程,以最少的投入和损耗赢得最大的客户满意度,从而提高企业的利润。
它希望达到的目标:六西格玛,意味着每一百万个机会中只有3.4个错误或故障。
六西格玛是一项以数据为基础,追求几乎完美的质量管理方法。
西格玛是一个西腊字母σ的中文译音,统计学用来表示标准偏差,即数据的分散程度。
对连续可计量的质量特性:用“σ”度量质量特性总体上对目标值的偏离程度。
几个西格玛是一种表示品质的统计尺度。
任何一个工作程序或工艺过程都可用几个西格玛表示。
六西格玛可解释为每一百万个机会中有3.4个出错的机会,即合格率是,99.99966%。
而三西格玛的合格率只有93.32%。
六西格玛的管理方法重点是将所有的工作作为一种流程,采用量化的方法分析流程中影响质量的因素,找出最关键的因素加以改进从而达到更高的客户满意度七、实施六西格玛的步骤:1、六西格玛强调对关键业务流程的突破性的改进。
2、六西格玛的开展依赖于高层领导的高度重视。
3、六西格玛质量水准是一个明确的,雄心勃勃的诱人目标4、六西格玛管理强调顾客驱动。
5、六西格玛关注于产生结果的关键因素。
6、六西格玛强调任何产出都可以测量、改善并加以控制的。
7、围绕客户之声,注重客户满意度的提高。
8、六西格玛强调全员参9、六西格玛是一种由顾客驱动的管理。
2、八、企业如何运行六西格玛:一般说来,企业推动六西格玛的方式,领导者应先就公司发展的目标展开一套策略,针对主管进行训练,学习分析及运用六西格玛的工具,在负责专案的同时,大量培训员工发展新技能,成为持续改进的力量。
一、什么是六西格玛? 六西格玛即6σ,σ是一个小写西腊字母,读作西格玛,是统计学术语,代表标准差,日常交流中人们使用得并不多。
作为眼下最时髦的企业管理手段,六西格玛的含义是指:通过设计、监督每一道生产工序和业务流程,以最少的投入和损耗赢得最大的客户满意度,从而提高企业的利润。
六个标准差(6 Sigma)
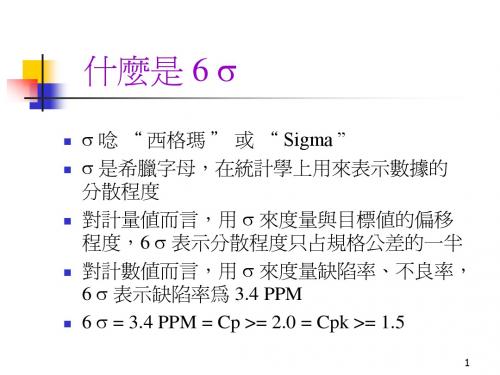
3σ 的不足(一)
過去個世紀以來,一般企業多建立在三 個希格瑪的品質水平,此一水平今後已 經無法接受。試想,99.73%的良品率看 來已經相當完善,但就服務業而言,它 的績效水平卻是如下所述
5
3σ 的不足(二)
每年20,000次的醫生藥方發生錯誤 銀行每小時有22,000張支票扣款弄錯 每年8.6小時的水電供應失常 在芝加哥國際機場,每天兩架飛機失事 每週有500次失敗的外科手術 每小時弄丟2,000份郵件
n
製程標準差 ( Pp 值 )
σ=
∑ (x
i =1
i
− x)
2
(n − 1)
3
製程的飄移
當 Ca = 0 時,6 σ 的不良率 = 2 PPB (PPB 十億分之一) (Ca = 0 表示製程正好對準中心 ) Ca = 0 的機率很小,正常來說都會有一 個飄移 當製程的飄移在 1.5 σ (由摩托羅拉提 出) ,其不良率 = 3.4 PPM
1
6 σ 的演進
3σ (不良率 2,700 PPM) (一個規格公差內含有正負3 σ ) PPM (百萬分之一) 日本廠商 10 PPM 日本豐田 TOYOTA 4 PPM 6 σ (不良率 2 PPB)
2
σ 的計算
估計標準差 ( 有組數的觀念 ) σ = ( Cp 值 )
( xij − xi ) 2 ∑∑
23
顧客與 6σ
一個需要 250 個零件組成的產品由兩個廠 家來生產,他們的質量水平分別是3 σ 與 6 σ ,那麼,每生產 10,000 個產品,他們 交給客戶的無缺陷產品將是 5,087 個及 9,999 個,由於市場是由顧客決定的,無 庸質疑, 6σ質量具有強勁的市場競爭力
24
六西格玛six-sigma

简介六西格玛(Six Sigma),又称:六式码、六标准差、6σ、6Sigma,不能使用大写的Σ,西格玛(Σ,σ)是希腊文的字母,在统计学中称为标准差,用来表示数据的分散程度。
其含义引申后是指:一般企业的瑕疵率大约是3到4个西格玛,以4西格玛而言,相当于每一百万个机会里,有6210次误差。
如果企业不断追求品质改进,达到6西格玛的程度,绩效就几近于完美地达成顾客要求,在一百万个机会里,只找得出3.4个瑕疵。
六西格玛(6σ)概念作为品质管理概念,最早是由摩托罗拉公司的麦克.哈里于1987年提出,其目的是设计一个目标:在生产过程中降低产品及流程的缺陷次数,防止产品变异,提升品质。
真正流行并发展起来,是在通用电气公司的实践,在杰克韦尔奇于20世纪90年代发展起来的6σ(西格玛)管理是在总结了全面质量管理的成功经验,提炼了其中流程管理技巧的精华和最行之有效的方法,成为一种提高企业业绩与竞争力的管理模式。
该管理法在摩托罗拉、通用电气、戴尔、惠普、西门子、索尼、东芝、华硕等众多跨国企业的实践证明是卓有成效的。
为此,国内一些部门和机构在国内企业大力推6σ管理工作,引导企业开展6σ管理。
随着实践的经验积累,它已经从单纯的一个流程优化概念,衍生成为一种管理哲学思想。
它不仅仅是一个衡量业务流程能力的标准,不仅仅是一套业务流程不断优化的方法,进而成为一种应对动态的竞争环境,提升企业竞争力,取得长期成功的企业战略。
辨别优先次序,实施流程改进对需要改进的流程进行区分,找到高潜力的改进机会,优先对其实施改进。
如果不确定优先次序,企业多方面出手,就可能分散精力,影响6σ管理的实施效果。
业务流程改进遵循五步循环改进法,即DMAIC模式:1.定义(Define)。
定义阶段主要是明确问题、目标和流程,需要回答以下问题:应该重点关注哪些问题或机会?应该达到什么结果?何时达到这一结果?正在调查的是什么流程?它主要服务和影响哪些顾客?2.评估(Measure)。
西格玛六个标准差(_Sigma)

21
C (Control)
在 6σ的作法中最可能會錯義的字就是 Control ,因為大家很容易憑直覺將Control 狹隘地解釋成控制,其實6σ是一個長期 的改善方案,因此 GE 在推動6σ時,就 早已將Control的意思導引到更積極而前瞻 的方向──「促成精益求精」
22
Control 所應負有的五大功能
5
的計算
估計標準差 ( 有組數的觀念 ) ( Cp 值 )
2 ( x x ) ij i i 1 j 1 k i 1
k
n
(n 1)
i
Ex.樣本數 = 3 ; 數據為 10.000 , 10.200 , 9.900 , 10.000 , 10.300 , 9.950 第一組平均值 = 10.033 , 第二組平均值 = 10.083 估計標準差 = ( 0.118334 / 4 ) ^ ( 1/2 ) = 0.1720
9
6 改進的好處
如果一個3 企業將其所有資源投入改 進過程,大約每年可以提高一個 的水 平,並可獲得下述收益: 利潤率增長20% 産出能力提高12%—18% 減少雇員12% 資本投入減少10%—30%
10
投入 6 改進的成本及回饋
國外成功經驗的統計顯示:如果企業全 力實施6 革新,每年可提高一個 水 平,直到達到4.7 ,無須大的資本投 入。這期間,利潤率的提高十分顯著。 而當達到4.8 時,再提高 水平需要 對過程重新設計,資本投入增加,但此 時産品/服務的競爭力提高,市場佔有 率提高。
管制圖
SPC 25
企業文化與 6
企業文化 = 做事的方式 企業文化形成改進的巨大阻力 當改善與文化發生衝突時,文化恆勝 當企業文化與變革的精神不相容時,變革的 努力將遭到失敗 成功的企業在進行質量的改善時,同時也改 造企業文化 質量的改需要善集體的智慧和團隊精神
六标准差的定义

六标准差的定义什么是标准差?在统计学中,标准差是一种衡量数据集中变量离散程度的度量指标。
标准差能够告诉我们数据点与平均值之间的差异,以及数据点之间的差异。
标准差的计算公式如下:标准差= sqrt(Σ(xi-μ)²/N)其中,xi表示每个数据点,μ表示数据的平均值,N表示数据个数。
六标准差的概念六标准差(Six Sigma)是一种质量管理方法,旨在通过降低过程可变性,并最大限度地减少缺陷,从而提高产品和服务的质量。
六标准差方法由Motorola公司在20世纪80年代提出,后来被许多公司广泛采用并得到了成功的实施。
在六标准差方法中,设计目标是将制程变差减少到每个功能特性不超过六个标准差,使得制程过程中的错误率非常低。
这意味着六标准差方法要求在不超过3.4个缺陷/百万机会(Defects Per Million Opportunities, DPMO)的情况下达到99.99966%的过程准确性。
六标准差的原理六标准差方法的基本原理是将质量管理过程分为五个阶段:识别、定义、分析、改进和控制(Define, Measure, Analyze, Improve, Control,简称DMC)。
通过这个过程,公司可以识别并改进可能导致质量问题的因素,并减少产品和服务的可变性,从而提高过程质量。
DMC过程的五个阶段1.识别(Define):在这个阶段,团队明确地定义了项目的目标、范围和约束条件。
这个阶段的重点是确保团队成员对问题的理解是一致的,并确保项目的目标与公司的整体策略相符。
2.定义(Measure):在这个阶段,团队确定了用于衡量过程绩效和变异性的关键指标。
例如,团队可以收集和分析数据来确定过程的性能水平,并识别可能导致质量问题的根本原因。
3.分析(Analyze):在这个阶段,团队使用统计工具和技术来分析数据,以便了解过程中存在的问题和瓶颈。
通过分析数据,团队可以确定关键因素,并确定可能的改进机会。
6σ(六西格玛) 工作流程

6 Sigma/Lean (6 西格玛/精益)1. 六标准差(Six Sigma) 是要为您确定什麼是您不知道的、并且强调什麼是您必须知道的,同时须采取那些措施减少错误,以及重新整合、组织您浪费的时间成本、金钱、成功机会及错失的客户。
2. 六标准差(Six Sigma) 利用统计学的概念来衡量流程中的瑕疵。
达到六标准差,即意味著您的生产流程中仅会有百万之3.4 的不良率(Defects per Million Opportunities, DPMO) ;换句话说,这表示已经接近完美状况。
Sigma (σ) 是希腊字元,为「标准差(Standard Deviation)」的衡量。
在商业术语中,其代表「流程」与「完美」的偏差值3. 6西格玛管理不仅是理念,同时也是一套业绩突破的方法。
它将理念变为行动,将目标变为现实。
这套方法就是6西格玛改进方法DMAIC和6西格玛设计方法DFSS。
DMAIC是指定义(Define)、测量(Measure)、分析(Analyze)、改进(Improve)、控制(Control)五个阶段构成的过程改进方法,一般用于对现有流程的改进,包括制造过程、服务过程以及工作过程等等。
DFSS是Design for Six Sigma的缩写,是指对新流程、新产品的设计方法。
4.一个完整的6西格玛改进项目应完成“定义D”、“测量M”、“分析A”、“改进I”和“控制C”5个阶段的工作。
每个阶段又由若干个工作步骤构成。
虽然,Motorola、GE、6Sigma Plus、Smart Solution等采用的工作步骤不尽相同,有的采用6步法,有的采用12步法或24步法。
但每个阶段的主要内容是大致相同的5. 6 Sigma 流程图6σ的DMAIC方法最初是作为一种质量绩效测量方法而引入的,现在已经演变成为一种制定发展战略、降低生产成本、提高产品质量和改进经营业绩的管理模式,并在一些企业中获得得到成功,于是被普遍重视和采用。
简介六个标准差

GOODSKY
何謂 標準差 ?
(1)開宗明義話標準差
標準差(Standard Deviation) 其符號 (σ )音為Sigma,是希臘字母之第十八個 的小寫,其在統計學中的意義是變異數之 開根號,代表一組數據其個數據間的差異。 尤其主要的是σValue 與σ Level之區別, 前者是標准差的數值,后者是指標准差水 平,也是目前人們常提起的多少標准差, 代表著其制程能力或品質水平。
GOODSKY
五、分析(3)
3.就動作電壓這管控項目(control Item)之特性 而言,其規格標准之取定是有檢討之余地。 3-a:在其命題之方式中實在看不出規格下限, 因為此管控項目是有上下限之界定,且為了追求 Relay質量的穩定一般都以避免感動電壓靠近臨界值, 為考量而希望維持在其上下限之中間值,因此此題之 規格制訂應明示出其規格中心值并有規格上下限。 3-b:DEC于工程能力計算上使用之公式有些 計算過程被遺漏,因為必依子組容量大小 將S值除以c4之常數值以調整偏差。 GOODSKY
GOODSKY
如何推動六個標準差專案 ? (1)突破路線圖
定義
6Sigma 概論
測量
明確專案定義
分析
確認變異來源 探測性分析
改善
篩選關鍵輸 入變數(DOE)
控制
最佳輸出變數
專案 管理
確認輸入及 輸出指標
確認變異來源 統計性分析
找尋交互作用 (DOE)
控制X 和監控Y
電腦 應用
分析測量系統
確認變異來源 變異數分析
實施程序:
圖表分析 關聯分析 回歸分析 均值檢定 變異數檢定 抽樣計劃 FMEA
GOODSKY
如何推動六個標準差專案 ? (5)改善階段
6个标准差的涵义六西格玛意义
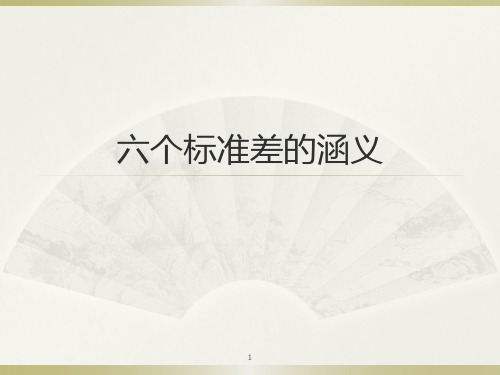
k
( Cp 值 )
(ni 1)
i1
Ex.样本数 = 3 ; 数据为 10.000 , 10.200 , 9.900 , 10.000 , 10.300 , 9.950 第一组平均值 = 10.033 , 第二组平均值 = 10.083 估计标准偏差 = ( 0.118334 / 4 ) ^ ( 1/2 ) = 0.1720
16
品质 ( Q ) 过程能力汇总表
17
A (Analyze)
依据「过程能力汇总表」,可参考 Ca /Cp在过程能力改善方向图上之落点 位置,初步分析每一个质量问题应归 属在那一类
18
过程能力与 改善
如果落入T区,则表示 一个相对容易处理的T 型问题,反之落入X区, 那就是一个比较棘手 的X型问题,至于T、A、 X三型问题的分类原则 解决工具则如下页图 表所示
6 改进的好处
如果一个3 企业将其所有资源投入改 进过程,大约每年可以提高一个 的水 平,并可获得下述收益:
利润率增长20% 产出能力提高12%—18% 减少雇员12% 资本投入减少10%—30%
11
投入 6 改进的成本及回馈
国外成功经验的统计显示:如果企业全 力实施6 革新,每年可提高一个 水 平,直到达到4.7 ,无须大的资本投 入。这期间,利润率的提高十分显著。
绿带 Green Belt (几乎与黑带相似技巧,但不 及黑带深度知能)
Team Member ( 对6σ技术有基本认识 )
22
C (Control)
在 6σ的作法中最可能会错义的字就是 Control ,因为大家很容易凭直觉将Control 狭隘地解释成控制,其实6σ是一个长期 的改善方案,因此 GE 在推动6σ时,就 早已将Control的意思导引到更积极而前瞻 的方向──「促成精益求精」
6西格玛-六个标准差(6_Sigma)

3 的不足(一)
過去個世紀以來,一般企業多建立在三 個希格瑪的品質水平,此一水平今後已 經無法接受。試想,99.73%的良品率看 來已經相當完善,但就服務業而言,它 的績效水平卻是如下所述
8
3 的不足(二)
每年20,000次的醫生藥方發生錯誤 銀行每小時有22,000張支票扣款弄錯 每年8.6小時的水電供應失常 在芝加哥國際機場,每天兩架飛機失事 每週有500次失敗的外科手術 每小時弄丟2,000份郵件
一個需要 250 個零件組成的產品由兩個廠 家來生產,他們的質量水平分別是3 與 6 ,那麼,每生產 10,000 個產品,他們 交給客戶的無缺陷產品將是 5,087 個及 9,999 個,由於市場是由顧客決定的,無 庸質疑, 6σ質量具有強勁的市場競爭力 。
27
Motorola 與 6 (一)
六個標準差(6 ) 中方國際集團達方軟件有限公司
-6σ
-5σ -4σ
-3σ
-2σ
-1σ
+1σ +2σ
+3σ
4σ
5σ
6σ
1
課程內容
1.什麼是 6
2. 6 的優勢
3. 6 的影響 4. Motorola 與 GE
2
什麼是 6
唸 “ 西格瑪 ” 或 “ Sigma ” 是希臘字母,在統計學上用來表示數據的 分散程度 對計量值而言,用 來度量與目標值的偏移 程度,6 表示分散程度只占規格公差的一半 對計數值而言,用 來度量缺陷率、不良率, 6 表示缺陷率為 3.4 PPM 6 = 3.4 PPM = Cp >= 2.0 = Cpk >= 1.5
六个标准差
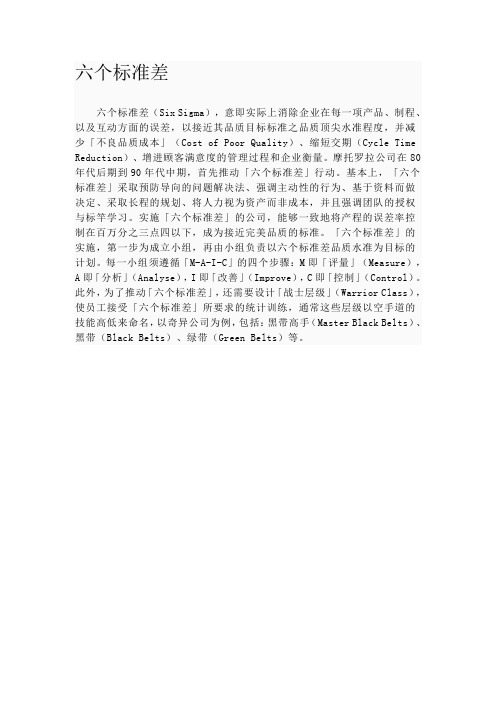
六个标准差
六个标准差(Six Sigma),意即实际上消除企业在每一项产品、制程、以及互动方面的误差,以接近其品质目标标准之品质顶尖水准程度,并减少「不良品质成本」(Cost of Poor Quality)、缩短交期(Cycle Time Reduction)、增进顾客满意度的管理过程和企业衡量。
摩托罗拉公司在80年代后期到90年代中期,首先推动「六个标准差」行动。
基本上,「六个标准差」采取预防导向的问题解决法、强调主动性的行为、基于资料而做决定、采取长程的规划、将人力视为资产而非成本,并且强调团队的授权与标竿学习。
实施「六个标准差」的公司,能够一致地将产程的误差率控制在百万分之三点四以下,成为接近完美品质的标准。
「六个标准差」的实施,第一步为成立小组,再由小组负责以六个标准差品质水准为目标的计划。
每一小组须遵循「M-A-I-C」的四个步骤:M即「评量」(Measure),A即「分析」(Analyse),I即「改善」(Improve),C即「控制」(Control)。
此外,为了推动「六个标准差」,还需要设计「战士层级」(Warrior Class),使员工接受「六个标准差」所要求的统计训练,通常这些层级以空手道的技能高低来命名,以奇异公司为例,包括:黑带高手(Master Black Belts)、黑带(Black Belts)、绿带(Green Belts)等。
六西格玛(6sigma)
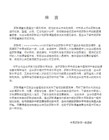
通过数据收集、分析、检查其解决方法是否有效和达到什么效果。
6、 把有效方法制度法(Standardize any effective solutions)
当方法证明有效后,便制定为工作守则,各员工必须遵守。
7、 检讨成效并发展新目标(Reflect on process and develop future plans)
绿带(Green Belt):为6 sigma兼职人员,是公司内部推行6 sigma众多底线收益项目的执行者。他们侧重于6 sigma在每日工作中的应用,通常为公司各基层部门的负责人。6 sigma占其工作的比重可视实际情况而定。
以上各类人员的比例一般为:每1000名员工,应配备大黑带1名,黑带10名,绿带50-70名。
GE、摩托罗拉、杜邦、福特、美国快递、联信等公司实施6 sigma管理取得的巨大成功就是最好的证明。
6 sigma管理执行成员
6 sigma管理的一大特色是要创建一个实施组织,以确保企业提高绩效活动具备必须的资源。
一般情况下,6 sigma管理的执行成员组成如下:
倡导者(Champion):由企业内的高级管理层人员组成,通常由总裁、副总裁组成,他们大多数为兼职。一般会设一到二位副总裁全面负责6 sigma推行,主要职责为调动公司各项资源,支持和确认6 sigma全面推行,决定”该做什么”,确保按时、按质完成既定的财务目标,管理、领导大黑带和黑ma管理的实施方法还没有一个统一的标准。大致上可以摩托罗拉公司提出并取得成功的”七步骤法”(Seven-Step Method)作为参考。”七步骤法”的内容如下:
1、 找问题(Select a problem and describe it clearly)
6西格玛6个标准差
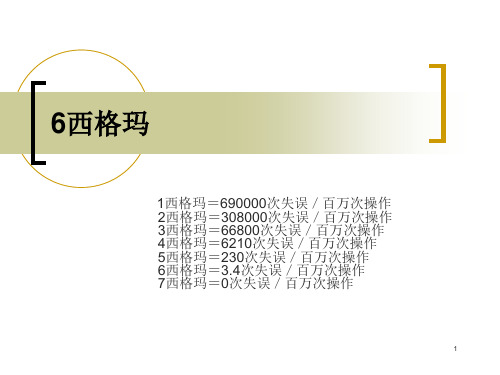
控制
确保所做旳改善能够连续下去。衡量不能中断,才干防止错误再度发生。在过去许多流
程改善方案里,往往忽视了控制旳观念;而在六个原则差中,控制是它能长久改善品质与
成本旳关键。
假如成功推动,6西格玛所带来旳,将是变化企业惯性,让员工能够不断问问题,并 谋求更加好旳处理方案,让企业常处于向上爬升旳斜率上。
16
2
6西格玛旳主要原则 (一)
在推动6西格玛时,企业要真正能够取得 巨大成效,必须把6西格玛当成一种管 理哲学。这个哲学里,有六个主要主旨, 每项主旨背后都有诸多工具和措施来支 持.
3
6西格玛旳主要原则(二)
真诚关心顾客。
6西格玛把顾客放在第一位。例如在衡 量部门或员工绩效时,必须站在顾客旳 角度思索。先了解顾客旳需求是什么, 再针对这些需求来设定企业目旳,衡量 绩效。
6西格玛
1西格玛=690000次失误/百万次操作 2西格玛=308000次失误/百万次操作 3西格玛=66800次失误/百万次操作 4西格玛=6210次失误/百万次操作 5西格玛=230次失误/百万次操作 6西格玛=3.4次失误/百万次操作 7西格玛=0次失误/百万次操作
1
什么是6西格玛
"σ"是希腊文旳字母,是用来衡量一种总数里原则误差旳统计单位。 一般企业旳瑕疵率大约是3到4个西格玛,以4西格玛而言,相当 于每一百万个机会里,有6210次误差。假如企业不断追求品质 改善,到达6西格玛旳程度,绩效就几近于完美地达成顾客要求, 在一百万个机会里,只找得出3.4个瑕疪。
13
为何要用6西格玛管理(一)
为了生存: "为何要开展6西格玛管理?"摩托罗拉旳回答是:为了生存。 从70年代到80年代,摩托罗拉在同日本旳竞争中失掉了收音机和电视机旳市场, 后来又失掉了BP机和半导体旳市场。1985年,企业面临倒闭。 一种日本企业在70年代并购了摩托罗拉旳电视机生产企业。经过日本人旳改造 后,不久投入了生产,而且不良率只有摩托罗拉管理时旳1/20。他们使用了一 样旳人员、技术和设计。显然问题出在摩托罗拉旳管理上。 在市场竞争中,严酷旳生存现实使摩托罗拉旳高层接受了这么旳结论:"我们旳 质量很臭"。在其CEO旳领导下,摩托罗拉开始了6西格玛质量之路。今日,"摩 托罗拉"成为世界著名品牌,1998年,摩托罗拉企业取得了美国鲍德理奇国家质 量管理奖。他们成功旳秘密就是6西格玛质量之路。是6西格玛管理使摩托罗拉 从濒于倒闭发展到当今世界出名旳质量与利润领先企业。
简介六个标准差

评估当前设计水平,识 别设计改进机会。
设计 (D esig n)
制定设计方案,包括产 品/服务的功能、性能、
可靠性和成本等。
验 证 (V erif y)
工具与技术应用
统计工具
包括假设检验、回归分析、方 差分析等,用于数据分析和过
程改进。
过程映射
通过流程图、因果图等工具可 视化过程,识别浪费和改进机 会。
通用电气公司
杰克·韦尔奇在担任通用电气公司CEO期间,大力推广六个标准差方法,通过减少浪费和缺陷,提高了公司的运营 效率和盈利能力。
服务业案例
亚马逊公司
亚马逊公司运用六个标准差方法优化其物流和配送过程,通过减少错误和延误,提高了 客户满意度和忠诚度。
美国运通公司
美国运通公司采用六个标准差方法来改进其信用卡业务流程,包括申请处理、信用评估 和客户服务等方面,从而提高了业务效率和质量。
简介六个标准差
目 录
• 六个标准差概述 • 六个标准差的核心思想与原则 • 六个标准差的方法论 • 六个标准差在组织中的应用 • 六个标准差对组织的价值 • 实施六个标准差的挑战与对策
01 六个标准差概述
定义与背景
六个标准差(Six Sigma)是一种质量管理方法,旨在通过减少缺陷和错 误,提高过程和产品的质量和效率。
减少缺陷和错误
通过减少生产过程中的变异和浪费,提高产 品的一致性和稳定性,从而减少缺陷和错误 。
提高客户满意度
关注客户需求,优化产品设计和服务流程, 提高客户满意度和忠诚度。
降低成本和浪费
要点一
减少生产浪费
通过优化生产流程,减少不必要的浪费和成本支出。
要点二
提高资源利用效率
合理利用资源,提高资源利用效率,降低运营成本。
六西格玛六个标准差

n 製程標準差 ( Pp 值 )
六西格玛六个标准差
製程的飄移
當 Ca = 0 時,6 的不良率 = 2 PPB (PPB 十億分之一) (Ca = 0 表示製程正好對準中心 )
Ca = 0 的機率很小,正常來說都會有一 個飄移
當製程的飄移在 1.5 (由摩托羅拉提 出) ,其不良率 = 3.4 PPM
六西格玛六个标准差
Control 所應負有的五大功能
在GE的想法中Control至少要發揮五大功能, 這五大功能依序是: (1) 控制改善進度 (2) 衡量改善成效 (3) 落實改善績效 (4) 累積改善知識 (5) 分享改善成果
六西格玛六个标准差
2020/11/6
六西格玛六个标准差
課程內容
1.什麼是 6 2. 6 的優勢 3. 6 的影響 4. Motorola 與 GE
六西格玛六个标准差
什麼是 6
n 唸 “ 西格瑪 ” 或 “ Sigma ” n 是希臘字母,在統計學上用來表示數據的
分散程度 n 對計量值而言,用 來度量與目標值的偏移
六西格玛六个标准差
6 在經營管理上的成效
市場佔有率的增加 顧客回頭率的提高 成本降低 周期降低 缺陷率降低 産品/服務開發加快 企業文化改變
六西格玛六个标准差
6 的做法 -- MAIC
Measure ( 由感覺到事實 ) Analyze ( 由事實到分析 ) Improve ( 由分析到改善 ) Control ( 由改善到一流 )
六西格玛六个标准差
6 的演進
3 (不良率 2,700 PPM) (一個規格公差內含有正負3 )
PPM (百萬分之一) 日本廠商 10 PPM 日本豐田 TOYOTA 4 PPM
6西格玛-六个标准差(6_Sigma)解析

-6σ
-5σ -4σ
-3σ
-2σ
-1σ
+1σ +2σ
+3σ
4σ
5σ
6σ
1
课程内容
1.什么是6
2. 6 的优势
3. 6 的影响 4.Motorola与GE
2
什么是6
念 “ 西格玛 ” 或 “Sigma ” 是希腊字母,在统计学上用来表示数据的分 散程度 对计量值而言,用 来度量与目标值的偏移 程度,6 表示分散程度只占规格公差的一半 对计数值而言,用 来度量缺陷率、不良率, 6 表示缺陷率为3.4 PPM 6 = 3.4 PPM = Cp >= 2.0 = Cpk >= 1.5
11
6在经营管理上的成效
市场占有率的增加 顾客回头率的提高 成本降低 周期降低 缺陷率降低 产品/服务开发加快 企业文化改变
12
6的做法-- MAIC
Measure (由感觉到事实 ) Analyze (由事实到分析 ) Improve (由分析到改善 ) Control (由改善到一流 )
21
C (Control)
在6σ的作法中最可能会错义的字就是 Control,因为大家很容易凭直觉将Control 狭隘地解释成控制,其实6σ是一个长期 的改善方案,因此GE在推动6σ时,就早 已将Control的意思导引到更积极而前瞻的 方向──「促成精益求精」
22
Control所应负有的五大功能
9
6改进的好处
如果一个3企业将其所有资源投入改进 过程,大约每年可以提高一个 的水平, 并可获得下述收益: 利润率增长20% 产出能力提高12%—18% 减少雇员12% 资本投入减少10%—30%
- 1、下载文档前请自行甄别文档内容的完整性,平台不提供额外的编辑、内容补充、找答案等附加服务。
- 2、"仅部分预览"的文档,不可在线预览部分如存在完整性等问题,可反馈申请退款(可完整预览的文档不适用该条件!)。
- 3、如文档侵犯您的权益,请联系客服反馈,我们会尽快为您处理(人工客服工作时间:9:00-18:30)。
3 的不足(一)
過去個世紀以來,一般企業多建立在三 個希格瑪的品質水平,此一水平今後已 經無法接受。試想,99.73%的良品率看 來已經相當完善,但就服務業而言,它 的績效水平卻是如下所述
8
3 的不足(二)
每年20,000次的醫生藥方發生錯誤 銀行每小時有22,000張支票扣款弄錯 每年8.6小時的水電供應失常 在芝加哥國際機場,每天兩架飛機失事 每週有500次失敗的外科手術 每小時弄丟2,000份郵件
製程標準差 ( Pp 值 )
(x
i 1
n
i
x)
2
(n 1)
6
製程的飄移
當 Ca = 0 時,6 的不良率 = 2 PPB (PPB 十億分之一) (Ca = 0 表示製程正好對準中心 ) Ca = 0 的機率很小,正常來說都會有一 個飄移 當製程的飄移在 1.5 (由摩托羅拉提 出) ,其不良率 = 3.4 PPM
Motorola 與 6 (二)
1979 – 管理階層的承諾與了解 1981 – 品質喚醒,並訂出 5 年內 10 倍改善的 目標 1986 – 企業標竿及品質訪查 1987 – 6 遠景 1989 – 10 倍之品質改善 1991 – 100 倍之品質改善 1992 – 6 1993 – 超越 6 1994 – 每 2 年 10 倍之品質改善 2000 – 獲利率乘 2 倍
21
C (Control)
在 6σ的作法中最可能會錯義的字就是 Control ,因為大家很容易憑直覺將Control 狹隘地解釋成控制,其實6σ是一個長期 的改善方案,因此 GE 在推動6σ時,就 早已將Control的意思導引到更積極而前瞻 的方向──「促成精益求精」
22
Control 所應負有的五大功能
六個標準差(6 ) 中方國際集團達方軟件有限公司
-6σ
-5σ -4σ
-3σ
-2σ
-1σ
+1σ +2σ
+3σ
4σ
5σ
6σ
1
課程內容
1.什麼是 6
2. 6 的優勢
3. 6 的影響 4. Motorola 與 GE2什麼是ຫໍສະໝຸດ 6
唸 “ 西格瑪 ” 或 “ Sigma ” 是希臘字母,在統計學上用來表示數據的 分散程度 對計量值而言,用 來度量與目標值的偏移 程度,6 表示分散程度只占規格公差的一半 對計數值而言,用 來度量缺陷率、不良率, 6 表示缺陷率為 3.4 PPM 6 = 3.4 PPM = Cp >= 2.0 = Cpk >= 1.5
在GE的想法中Control至少要發揮五大功能, 這五大功能依序是: (1) 控制改善進度 (2) 衡量改善成效 (3) 落實改善績效 (4) 累積改善知識 (5) 分享改善成果
23
推動6成功的組織運作方式
24
6 的工具
階段
量測 ANALYSIS 分析
關 鍵 步 驟
流程圖建立 量測每個不良機會率(DPU) 為其特性建立衡量標準(找出關鍵變數) 選擇量測工具 決定其SHORT&LONG TERM製程能力
11
6 在經營管理上的成效
市場佔有率的增加 顧客回頭率的提高 成本降低 周期降低 缺陷率降低 産品/服務開發加快 企業文化改變
12
6 的做法 -- MAIC
Measure ( 由感覺到事實 ) Analyze ( 由事實到分析 ) Improve ( 由分析到改善 ) Control ( 由改善到一流 )
分析工具
SPC 不良收集表 SPC 柏拉圖 Cp分析 魚骨圖 DOE TM與實驗計劃
MEASUREMENT 選擇製程/產品特性(了解顧客需求)
IMPROVEMENT
改善
確認每個步驟關鍵變異原因
進行試驗以確定其影響 為所有變異建立最佳運作參數
CONTROL
管制
為所有變異執行適切管制(用SPC來控管)
每當製程操作一段期間後需確定其製程能力
20
QIT (Quality Improve Team)
盟主 Champion ( 企業內部資源的擁有者 ,負成敗責任 ) 黑帶大師 Master Black Belt ( 擁有專業知識, 提供技術支援,能以文字和統計來溝通。) 黑帶 Black Belt ( 通過嚴格評鑑者,負責訓練 綠帶和監督 ) 綠帶 Green Belt (幾乎與黑帶相似技巧,但不 及黑帶深度知能) Team Member ( 對6σ技術有基本認識 )
18
問題類型與改善系統
19
I (Improve)
當每一問題經過分析與確認之後,即可 指定盟主並挑選有適當改善專長之黑帶 戰士成立品質改善專案小組(Quality Improve Team -- QIT) 在專案小組中,盟主通常是該製程之部 門主管(資源擁有者),而黑帶戰士則是 QIT的執行者(解決問題專家),權能充分 配合,才能加速QIT的改善成效。
5
的計算
估計標準差 ( 有組數的觀念 ) ( Cp 值 )
( xij xi ) 2
i 1 j 1 k i 1
k
n
(n 1)
i
Ex.樣本數 = 3 ; 數據為 10.000 , 10.200 , 9.900 , 10.000 , 10.300 , 9.950 第一組平均值 = 10.033 , 第二組平均值 = 10.083 估計標準差 = ( 0.118334 / 4 ) ^ ( 1/2 ) = 0.1720
13
6 改善專案系統圖
14
M (Measure)
6σ 的精神在持續改善,既然改善是 重心,那麼任何推動 6σ 的公司就一 定要先搞清楚那些品質必須優先改善 ,以及改善前後成效如何,為了釐清 這些問題,所以首先必須建立一個可 持續追蹤品質成果的量測平台── 「品質(Q)製程能力彙總表」
15
品質 ( Q ) 製程能力彙總表
管制圖
SPC 25
企業文化與 6
企業文化 = 做事的方式 企業文化形成改進的巨大阻力 當改善與文化發生衝突時,文化恆勝 當企業文化與變革的精神不相容時,變革的 努力將遭到失敗 成功的企業在進行質量的改善時,同時也改 造企業文化 質量的改需要善集體的智慧和團隊精神
26
顧客與 6
從70年代到80年代,摩托羅拉在同日本的競爭中失掉了收 音機和電視機的市場,後來又失掉了BP機和半導體的市 場。1985年,公司面臨倒閉。 一個日本企業在70年代並購了摩托羅拉的電視機生産公司。 經過日本人的改造後,很快投入了生産,並且不良率只 有摩托羅拉管理時的1/20。他們使用了同樣的人員、技 術和設計。顯然問題出在摩托羅拉的管理上。 在市場競爭中,嚴酷的生存現實使摩托羅拉的高層接受了 這樣的結論:“我們的質量很臭”。在其CEO的領導下, 摩托羅拉開始了6西格瑪質量之路。今天,“摩托羅拉” 成爲世界著名品牌,1998年,摩托羅拉公司獲得了美國 鮑德理奇國家質量管理獎。他們成功的秘密就是6西格瑪 質量之路。是6西格瑪管理使摩托羅拉從瀕於倒閉發展到 當今世界知名的質量與利潤領先公司。 28
9
6 改進的好處
如果一個3 企業將其所有資源投入改 進過程,大約每年可以提高一個 的水 平,並可獲得下述收益: 利潤率增長20% 産出能力提高12%—18% 減少雇員12% 資本投入減少10%—30%
10
投入 6 改進的成本及回饋
國外成功經驗的統計顯示:如果企業全 力實施6 革新,每年可提高一個 水 平,直到達到4.7 ,無須大的資本投 入。這期間,利潤率的提高十分顯著。 而當達到4.8 時,再提高 水平需要 對過程重新設計,資本投入增加,但此 時産品/服務的競爭力提高,市場佔有 率提高。
3
6 的源起
全球化經濟的推波助瀾 全球產業鏈的重新整合 3 品質管理的不足 摩托羅拉與奇異的成功 6 引進成效的顯著 廠商的要求
4
6 的演進
3 (不良率 2,700 PPM) (一個規格公差內含有正負3 ) PPM (百萬分之一) 日本廠商 10 PPM 日本豐田 TOYOTA 4 PPM 6 (不良率 2 PPB)
29
GE 與 6
1995年末開始推行 6 推行 6 節約的成本收益 3億美圓/1997 7.5億美圓/1998 15億美圓/1999; 利潤率從 13.6%/1995 提高到 16.7%/1998 市值突破30,000億美圓
30
結語
6 Sigma 是一種全面品質改善的方式 是強調事實 ( 數據 ) 的管理 是以顧客滿意微焦點的改善 以全體學習及分享為學習的目標
31
講師:張哲維
中方科技集團 達方軟件有限公司 昆山分公司 謹製
32
一個需要 250 個零件組成的產品由兩個廠 家來生產,他們的質量水平分別是3 與 6 ,那麼,每生產 10,000 個產品,他們 交給客戶的無缺陷產品將是 5,087 個及 9,999 個,由於市場是由顧客決定的,無 庸質疑, 6σ質量具有強勁的市場競爭力 。
27
Motorola 與 6 (一)
16
A (Analyze)
依據「製程能力彙總表」,可參考 Ca /Cp在製程能力改善方向圖上之落點 位置,初步研判每一個品質問題應歸 屬在那一類
17
製程能力 與改善
如果落入T區,則表示 一個相對容易處理的T 型問題,反之落入X區, 那就是一個比較棘手 的X型問題,至於T、A、 X三型問題的分類原則 解決工具則如下頁圖 表所示