磁粉探伤检验规范
磁粉检测的操作规程和注意事项
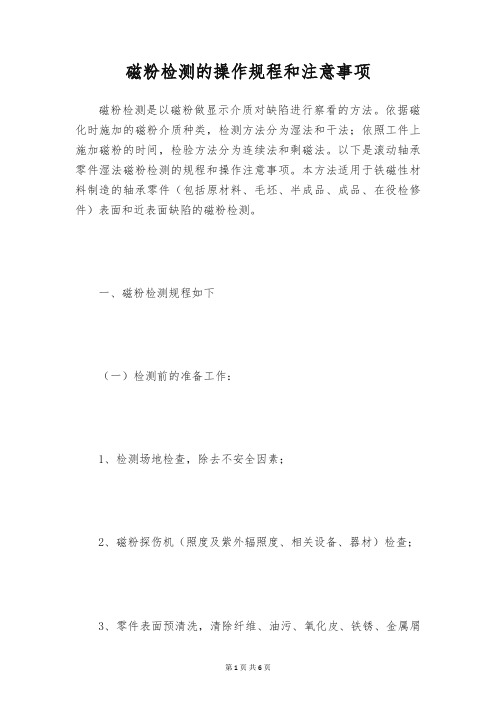
磁粉检测的操作规程和注意事项磁粉检测是以磁粉做显示介质对缺陷进行察看的方法。
依据磁化时施加的磁粉介质种类,检测方法分为湿法和干法;依照工件上施加磁粉的时间,检验方法分为连续法和剩磁法。
以下是滚动轴承零件湿法磁粉检测的规程和操作注意事项。
本方法适用于铁磁性材料制造的轴承零件(包括原材料、毛坯、半成品、成品、在役检修件)表面和近表面缺陷的磁粉检测。
一、磁粉检测规程如下(一)检测前的准备工作:1、检测场地检查,除去不安全因素;2、磁粉探伤机(照度及紫外辐照度、相关设备、器材)检查;3、零件表面预清洗,清除纤维、油污、氧化皮、铁锈、金属屑等杂物;4、磁悬液体积分数及污染物检测;5、水断试验(仅限水基磁悬液);6、系统灵敏度测试;7、零件内部存在有可能影响探伤效果的残磁时,检验前应对零件进行退磁。
(二)选择并确定磁化规范。
(三)按以下两种方法进行充磁及施加磁悬液:1、连续法:施加磁悬液,同时充磁,充磁时间为1s~3s,停止施加磁悬液后再连续充磁1次~2次,每次0.5s~1s;2、剩磁法:充磁后,接受浸泡法施加磁悬液,浸泡时间不少于30s。
(四)察看、评定及缺陷记录:对零件上形成的磁痕应适时察看,并评定是否为缺陷磁痕。
接受照相法、透亮胶带粘印法、书面描述等方法对缺陷进行记录。
(五)对合格零件和不合格零件进行区分标识。
(六)退磁。
1、检测合格的零件应进行退磁。
检测后尚有加热至700℃以上的热处理工序的零件可不退磁;2、多个零件同时退磁时,应将零件之间留有确定的间隔,摆放于非金属的料盘或料筐中进行退磁;3、退磁时所使用的电流值不应小于磁化时所使用的电流值。
一般情况下,交流电磁化用交流电退磁,直流电磁化用直流电退磁;4、零件退磁后,应进行残磁测定,其要求及方法应符合JB/T6641—2023的规定;5、已退磁的零件,应阔别磁化设备及退磁设备1.5m以外。
(七)如有疑问可重复(二)~(六)。
(八)检测后的合格零件应适时清洗,如有需要进行防锈处理。
轮轴、轮对、车轴磁粉探伤技术规范

轮轴、轮对、车轴磁粉探伤技术规范(总22页)-CAL-FENGHAI.-(YICAI)-Company One1-CAL-本页仅作为文档封面,使用请直接删除6 轮轴、轮对、车轴磁粉探伤6.1 磁粉探伤机6.1.1 磁粉探伤机应具备以下功能:6.1.1.1 轮轴、轮对和车轴磁粉探伤机,应具有手动和自动两种操作方式,具备周向磁化、纵向磁化、复合磁化三种磁化功能和自动退磁功能。
6.1.1.2 微机控制系统还应具备以下功能:6.1.1.2.1 能有效地对探伤设备的工作电压、周向磁化电流、纵向磁化电流、紫外线辐照度等主要技术参数进行实时监控和自动记录,并设置有紧急停机按钮。
6.1.1.2.2 具有磁悬液的高低液位、过载、欠流报警功能。
6.1.1.2.3 能对探伤性能校验和探伤记录进行打印、存储、查询。
6.1.1.2.4 具有探伤设备主要故障的自诊断功能和远程技术支持功能。
6.1.1.2.5 具有 HMIS 及 USB 接口。
6.1.2 磁粉探伤机应符合以下技术指标:6.1.2.1 周向磁化电流 0 ~ 3 000 A 应连续可调纵向磁化电流 0 ~ 2 400 A 应连续可调。
6.1.2.2 通电磁化时间应为 1s ~ 3 s ,停止喷淋磁悬液后应再磁化 2 次~ 3 次,每次 0.5 s ~ 1.0 s 。
6.1.2.3 探测面的白光强度应不大于 20lx ,紫外线辐照度应不小于 800 μ W/cm2 紫外线波长范围应在 320 nm ~ 400 nm 内,中心波长为 365 nm 。
6.1.2.4 整机绝缘电阻≥ 2M Ω。
6.1.2.5 退磁效果≤ 0.3 mT ( 3 Gs )。
6.2 工艺装备6.2.1 轮轴、轮对、车轴磁粉探伤应配置除锈机。
6.2.2 车轴探伤时,应配置起重吊运设备。
6.2.3 探伤工作间和探伤作业场地应配有必备的办公用品和工具,探伤人员还应配置紫外线防护眼镜。
6.2.4 应配置天平、长颈或梨形沉淀管、磁强计、白光照度计、紫外辐照度计、裂纹深度测试仪、铜网筛( 320 目)、磁悬浮测定玻璃管、磁吸附仪、配比磁悬液所用的量杯、量桶等。
磁粉探伤检验要求规范

磁粉探伤检验规范1、适用范围本规范叙述的是湿磁粉对铁磁性材料表面及近表面裂纹及其它不连续的一种检测。
适用于钻井工具表面和连接螺纹的磁粉检测。
2、引用标准、规范ASME 709 磁粉检测的标准推荐操作方法GB11522 标准对数视力表JB/T4730.1 承压设备无损检测第1部分:通用部分JB/T4730.4 承压设备无损检测第4部分:磁粉检测JB/T6063 磁粉探伤用磁粉技术条件JB/T6065 无损检测磁粉检测用试片JB/T8290 磁粉探伤机ASNT-TC-1A 无损检测人员的资格鉴定3、磁粉检测人员3.1 从业人员应按ASNT-TC-1A和《特种设备无损检查人员考核与监督管理规定》的要求,取得相应无损检测资格。
3.2 无损检测人员资格的分级为:Ⅲ(高)级、Ⅱ(中)级、Ⅰ(初)级。
取得不同无损检测方法和资格级别人员,只能从事于该方法和资格级别相应的工作,并负责相应的叫声责任。
3.3 磁粉检测人员未经矫正会经矫正的近(距)视力或远(距)视力应不低于5.0(小数记录值为1.0)。
测试方法应符合GB11533的规定。
3.4 无损检测人员应根据ASNT-TC-1A的规定,每年进行一次视力检查,不得有色盲。
4、检测设备、器材和材料4.1 磁粉探伤机磁粉探伤机,在有效适用期内应良好的保养。
交流电磁轭应有45N的提升力,直流电磁轭至少应有177N的提升力。
检测周期为6个月一次。
4.2 磁悬液磁悬液浓度应根据磁粉种类、力度、施加方法和被检工件表面状况等因素来确定。
用于完全润湿工件表面的油机介质,如出现不完全润湿,要从新进行清洗或添加更多磁粉或添加更多润湿剂。
4.3 退磁装置退磁装置应能保证退磁后,表面剩磁不大于0.3mT(240A/m)。
4.4 辅助设备磁场强度计标准试片A1(或CX)磁场指示器磁悬液浓度测试仪(管)2~10倍放大镜。
5、被检工件表面清洁被检工件表面,不得有油脂、铁锈、氧化皮或其他粘附磁粉的物质。
螺栓磁粉探伤机检测规程

螺栓磁粉探伤机检测规程概述:螺栓磁粉探伤仪器,是专用于螺栓及各类轴棒类零件的磁粉无损检测设备。
检测螺栓的磁粉探伤仪器有两种规格,一种是小型便携式磁粉探伤仪,一种是固定床式磁粉探伤机。
固定床式磁粉探伤机又有检测线与非检测线之分。
正常按非检测线的固定床式来做检测规程:引用标准:中华人民共和国磁粉探伤机《GB3721-83》标准,机械工业部行业磁粉探伤机《JB/T8290-2011》标准,行业《HB/Z72-98》标准。
技术要求:1、磁粉探伤对螺栓表面的要求1.1螺栓表面粗糙度Ra值为3.2µm。
1.2螺栓表面不应有油脂、锈斑、氧化皮及其它能粘附磁粉的物质。
1.3螺栓应在表面处理前进行磁粉探伤。
若必须在表面处理后进行,则覆盖层不应影响探伤效果。
2、探伤设备2.1探伤设备应具备对螺栓单周向、单纵向、周纵向复合磁化、喷洒磁悬液、紫外灯日光灯等观察设施及退磁等功能。
2.2设备配有磁悬液储液箱,需是非导磁材料制作,箱内要安装搅拌器,以使磁粉在油或水中均匀分布。
2.3使用荧光磁粉探伤时,其紫外线照射装置,荧光灯峰值波长为365nm,距灯380mm,照度不小于1000W/cm2。
2.4退磁效果应使螺栓剩磁减少到≤2Gs。
3、对磁粉和磁悬液的要求3.1探伤所用的磁粉建议采用荧光磁粉。
3.2磁粉的粒度在400目以内。
3.3探伤所用的磁悬液是由磁粉和液体介质配制而成。
4、荧光磁粉水磁悬液配方:乳化剂5克,亚硝酸钠15g,消泡剂0.5至1克,水1升,荧光磁粉1-3克配制时,将乳化剂和消泡剂搅拌均匀,并按比例加足水,成为水分散剂。
用少量水载液与磁粉和匀,再加人余量的水载液,最后加亚硝酸钠。
2g/L荧光磁粉,搅拌均匀,并根据使用情况定期添加或更换。
5、荧光磁粉油磁悬液配方:变压器油和无味煤油按1:5配制1升荧光磁粉1至5克磁粉在使用时需提前20分钟充分搅拌,定期每天或每周用磁悬液测淀管测量其浓度,按情况添加磁粉,或更换。
无损检测工艺规程(磁粉检验)
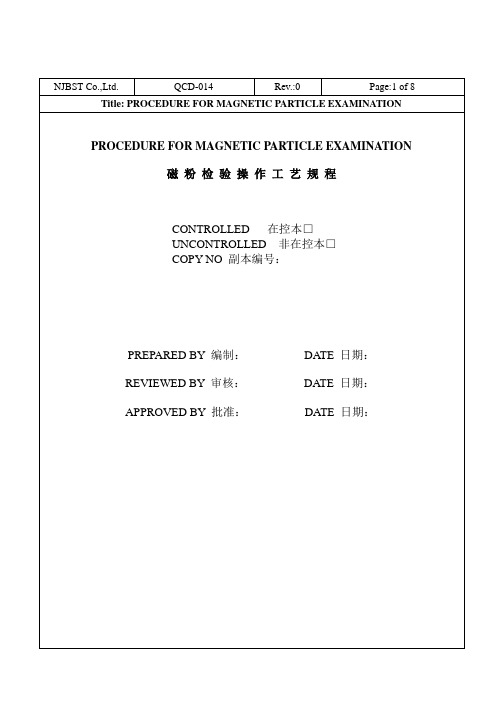
1. General
1.1 This procedure is applied to the magnetic particle examination of ferromagnetic materials and welds for ASME Code items.
1.2 The magnetic particle examination method is suitable for detecting cracks and other discontinuities on or near the surface in ferromagneticபைடு நூலகம்materials.
1.4 This procedure shall be demonstrated to the satisfaction of the AI prior to implementation.
2. Personnel
2.1 The NDE personnel who engage in magnetic particle examination shall be qualified and certified according to NJBST Co.,Ltd.’s “Written Practice for NDE Personnel Training, Examination, Qualification & Certification”(No.:QCD-011).
施工管理-磁粉探伤作业规程

磁粉检测作业规程目录一主题内容与适用范围 (3)二编制依据及相关标准规范 (3)三检测人员 (3)3.1视力要求 (3)3.2检测人员资格 (3)四磁粉检测程序 (3)五磁粉检测设备 (4)5.1设备 (4)5.2提升力 (4)5.3断电相位控制器 (4)5.4黑光辐照度及波长 (4)5.5退磁装置 (4)5.6辅助器材 (4)六磁粉、载体及磁悬液 (5)6.1磁粉 (5)七标准试件 (5)7.1标准试片 (5)7.2磁场指示器 (6)7.3中心导体磁化方法标准试块 (7)八磁化电流类型及其选用 (7)8.1电流类型 (7)8.2电流值 (7)九磁化方向 (7)9.1纵向磁化 (7)9.2周向磁化 (7)9.3复合磁化 (8)9.4焊缝的典型磁化方法 (8)十磁化规范 (8)10.1磁场强度 (8)10.2轴向通电法和中心导体法 (9)10.3偏置芯棒法 (9)10.4触头法 (9)10.5磁轭法 (10)10.6线圈法 (10)十一质量控制和安全防护 (11)11.1综合性能试验 (12)11.2磁悬液浓度测定 (12)11.3磁悬液污染判定 (12)11.4磁悬液润湿性能检验 (12)11.5电流表精度校验 (12)11.6电磁轭提升力校验 (12)11.7辅助仪表校验 (12)十二被检工件表面的准备 (13)12.1工件表面 (13)12.2安装接触垫 (13)12.3封堵 (13)12.4反差增强剂 (13)十三检测时机 (13)十四检测方法 (13)14.1检测方法分类 (13)14.2干法 (14)14.3湿法 (14)14.4连续法 (14)14.5剩磁法 (14)14.6交叉磁轭法 (14)十五磁痕显示的分类和记录 (14)15.1磁痕的分类 (14)15.2缺陷磁痕的观察 (15)15.3磁痕显示记录 (15)十六复验 (15)十七退磁 (16)17.1退磁一般要求 (16)17.2退磁方法 (16)17.3剩磁测定 (16)十八在用承压设备的磁粉检测 (16)十九磁粉检测质量分级 (17)19.1下列缺陷不允许存在 (17)19.2材料和焊接接头的磁粉检测质量分级 (17)19.3受压加工部件的磁粉检测质量分级 (17)19.4综合评级 (17)二十磁粉检测报告和资料保管 (17)附录A 各种磁化电流的波形、电流表指示及换算关系 (18)附录B焊缝的典型磁化方法 (19)一主题内容与适用范围本规程规定了压力管道安装及锅炉维修的磁粉检测方法及质量分级要求。
磁粉探伤检验规范

磁粉探伤检验规范1、适用范围本规范叙述的是湿磁粉对铁磁性材料表面及近表面裂纹及其它不连续的一种检测。
适用于钻井工具表面和连接螺纹的磁粉检测。
2、引用标准、规范ASME 709 磁粉检测的标准推荐操作方法GB11522 标准对数视力表JB/T4730.1 承压设备无损检测第1部分:通用部分JB/T4730.4 承压设备无损检测第4部分:磁粉检测JB/T6063 磁粉探伤用磁粉技术条件JB/T6065 无损检测磁粉检测用试片JB/T8290 磁粉探伤机ASNT-TC-1A 无损检测人员的资格鉴定3、磁粉检测人员3.1 从业人员应按ASNT-TC-1A和《特种设备无损检查人员考核与监督管理规定》的要求,取得相应无损检测资格。
3.2 无损检测人员资格的分级为:Ⅲ(高)级、Ⅱ(中)级、Ⅰ(初)级。
取得不同无损检测方法和资格级别人员,只能从事于该方法和资格级别相应的工作,并负责相应的叫声责任。
3.3 磁粉检测人员未经矫正会经矫正的近(距)视力或远(距)视力应不低于5.0(小数记录值为1.0)。
测试方法应符合GB11533的规定。
3.4 无损检测人员应根据ASNT-TC-1A的规定,每年进行一次视力检查,不得有色盲。
4、检测设备、器材和材料4.1 磁粉探伤机磁粉探伤机,在有效适用期内应良好的保养。
交流电磁轭应有45N的提升力,直流电磁轭至少应有177N的提升力。
检测周期为6个月一次。
4.2 磁悬液磁悬液浓度应根据磁粉种类、力度、施加方法和被检工件表面状况等因素来确定。
用于完全润湿工件表面的油机介质,如出现不完全润湿,要从新进行清洗或添加更多磁粉或添加更多润湿剂。
4.3 退磁装置退磁装置应能保证退磁后,表面剩磁不大于0.3mT(240A/m)。
4.4 辅助设备磁场强度计标准试片A1(或CX)磁场指示器磁悬液浓度测试仪(管)2~10倍放大镜。
5、被检工件表面清洁被检工件表面,不得有油脂、铁锈、氧化皮或其他粘附磁粉的物质。
焊缝磁粉检测
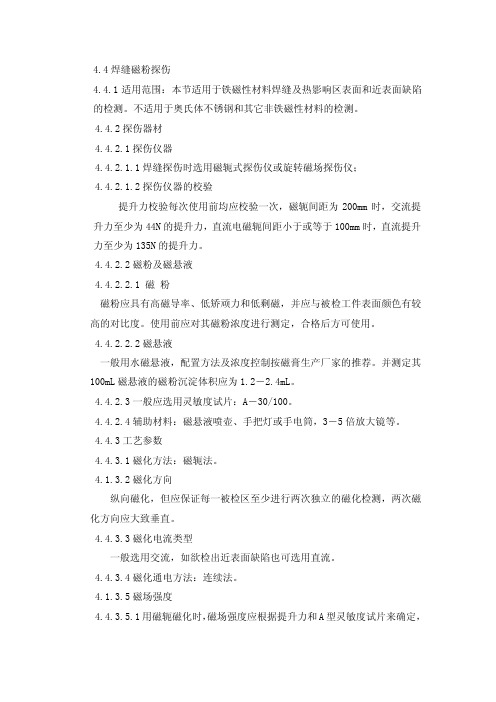
4.4焊缝磁粉探伤4.4.1适用范围:本节适用于铁磁性材料焊缝及热影响区表面和近表面缺陷的检测。
不适用于奥氏体不锈钢和其它非铁磁性材料的检测。
4.4.2探伤器材4.4.2.1探伤仪器4.4.2.1.1焊缝探伤时选用磁轭式探伤仪或旋转磁场探伤仪;4.4.2.1.2探伤仪器的校验提升力校验每次使用前均应校验一次,磁轭间距为200mm时,交流提升力至少为44N的提升力,直流电磁轭间距小于或等于100mm时,直流提升力至少为135N的提升力。
4.4.2.2磁粉及磁悬液4.4.2.2.1 磁粉磁粉应具有高磁导率、低矫顽力和低剩磁,并应与被检工件表面颜色有较高的对比度。
使用前应对其磁粉浓度进行测定,合格后方可使用。
4.4.2.2.2磁悬液一般用水磁悬液,配置方法及浓度控制按磁膏生产厂家的推荐。
并测定其100mL磁悬液的磁粉沉淀体积应为1.2-2.4mL。
4.4.2.3一般应选用灵敏度试片:A-30/100。
4.4.2.4辅助材料:磁悬液喷壶、手把灯或手电筒,3-5倍放大镜等。
4.4.3工艺参数4.4.3.1磁化方法:磁轭法。
4.1.3.2磁化方向纵向磁化,但应保证每一被检区至少进行两次独立的磁化检测,两次磁化方向应大致垂直。
4.4.3.3磁化电流类型一般选用交流,如欲检出近表面缺陷也可选用直流。
4.4.3.4磁化通电方法:连续法。
4.1.3.5磁场强度4.4.3.5.1用磁轭磁化时,磁场强度应根据提升力和A型灵敏度试片来确定,当提升力符合要求、灵敏度试片显示清晰时,即认为磁场强度是适宜的。
4.4.4验收标准除非设计文件另有规定,应按JB4730.4标准评定验收。
4.4.5系统灵敏度的校验用透明胶布将A-30/100试片贴在工件被检范围的一端,刻槽的一面朝向工件。
用与工件探伤相同的磁化规范进行磁化,当试片人工刻槽磁痕清晰显示时,则认为系统灵敏度合格。
4.4.6工件探伤4.4.6.1焊缝磁化4.4.6.1.1每条焊缝应至少放置一片灵敏度试片。
磁粉探伤检验规范

编号:SHZ—056版次:第一版磁粉探伤检验规范共 4 页(连封面)编制:审核:批准:2020-12-27发布 2020-12-28 实施磁粉探伤检验规范1.零件名称:2.零件图号:3.检测设备:磁轭4.检测方法:连续法5.磁化速度:移动速度应不大于2m/min.6.磁粉:湿黄色磁粉7.磁粉浓度:3-5g/L8.检测规范:JB/T6061-19929.仪器型号:Y-7AC/DC10.验收标准:JB/T6061-1992 I级11.适用范围:焊缝表面及近表面质量的检验和评定.12.磁痕的观察:非荧光磁粉的磁痕应当在白光照射下进行观察,白光强度不小于1000lx.荧光磁粉的磁痕应当在白光强度不大于20lx的阴暗环境下用紫外线灯进行观察,紫外线灯的发光亮度不低于1500uW/cm.13.检测要求:对焊缝表面及近表面缺陷的检验,评定,记录.14.检验人员资格:a.检验人员应按GB 9445的规定取证,经过有关部门考试合格方可从事操作,签发检验报告者必须持有磁粉检验二级以上资格证书.b.检验人员应了解产品焊接中常出现的缺陷类型,部位,方向,并掌握可使重要缺陷不漏检的试验方法.c. 检验人员的校正视力应不低于1.0,并且没有色盲.15.检验方法及要求:a.每班工作前需进行磁悬液度检测及用A试片验证系统灵敏度.b.磁轭的磁极间距在75-200mm,此磁化区域每次应有不少于15mm的重叠.c.对不合格区域用彩色记号笔做出明显的标记.d.在检测角向焊缝时需调节相应的角度.16.操作步骤:a.预处理:检查工作表面.b.磁化:工件(试片).c.施加磁悬液:在磁化过程中用喷嘴喷淋磁悬液(水+磁粉).d.检测:按规定的顺序进行检测并记录.e.缺陷评定:不允许存在任何裂纹和夹渣及所有的线性缺陷.f.统记缺陷.17.磁轭提升的力校定:每半年对磁轭进行提升力校定,交流电磁轭≥44N,直流电磁轭≥117N.18.质量评定和返修后的检验:a.焊缝磁粉检验的质量评定原则上根据缺陷磁痕的类型,长度,间距以及缺陷性质分为四个等级,I级质量最高,IV级质量最低.b.出现在同一条焊缝上不同类型或者不同性质的缺陷,可以选用相同的等级进行评定.c.评定为不合格的缺陷,在不违背焊接工艺规定的情况下,允许进行返修.返修后的检验和质量评定与返修前相同.19.检验报告:检验报告应至少包括下列内容:a.委托单位,报告编号.b.焊接件名称及编号.c.技术蓝图和被检部位.d.焊接件状况(材料,热处理情况,尺寸).e.焊缝情况(焊接方法,焊缝长度,焊缝所在部位).f.检验设备(型号,名称).g.磁粉种类和施加方法.h.磁方法,磁化电流值或磁场强度值.i.人工试片或试块.j.质量评定结果.k.检验日期和报告日期.l.检验者和审核者签名.缺陷磁痕分级表磁粉探伤操作流程1、3-4工作日对磁轭进行提升力检测。
ASTM A 275(A 275M-96 锻钢件磁粉检验检验规范
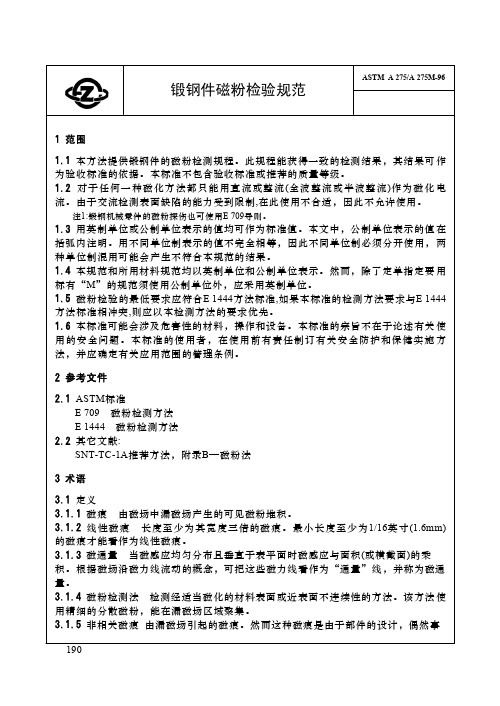
范围1.1本方法提供锻钢件的磁粉检测规程。
此规程能获得一致的检测结果,其结果可为验收标准的依据。
本标准不包含验收标准或推荐的质量等级。
ASTM A 275/A 275M - 96191故或与要探测的有害缺陷无关的其他特性造成的。
此术语的含义表明该磁痕与可能构成缺陷的不连续性无关。
4 应用依据4.1如按询价、合同,订单或规范的要求需对锻件进行磁粉检测时,则制造厂与用户应 就下列各项取得一致意见:4.1.1锻件上需进行磁粉检测的部位 ;4.1.2认为是缺陷磁痕的类型、尺寸、数量、部位和取向,4.1.3 施加磁粉的方法、退磁要求及磁场强度。
4.2如用户拟在锻件上加工出大凹槽,则制造厂发货前有权当设计允许时在粗加工锻 ()件上加工出切口或凹槽,以便检测内部情况。
4.3验收标准。
5 人员要求5.1使用本标准从事检测的人员,应按 SNT −推荐方法规定的书面程序或供需双方TC-1A 认可的其它国家标准进行资格鉴定和取证。
6 检测时期6.1除非用户另有规定,验收检测应在最终机械加工表面状态和最后热处理状态或离最 终机械加工还有英寸()余量的表面状态的锻件上进行。
0.030.8mm 6.2 当磁粉检测采用半波整流电流、直流电流和直接磁化时,验收检测可在最终机加工 表面状态加上英寸以内余量范围的锻件上进行。
0.03(0.8mm)7 磁化装置7.1可采用整流全波或半波或直流做磁化电源见第章。
如果电流通过工件本体,则()(9)磁化装置应包括具有足够表面积和夹持力的触头或夹持器,使之流过所需电流的被检部件不受损伤烧伤。
()7.2只要能证明检测裂纹类缺陷的灵敏度不低于直接磁化法,也可在直流模式下使用携 带式电磁轭交—直流作为磁化装置。
()8 磁粉8.1检测介质应由良好分散性的铁磁粉组成,它可悬浮在适当的液体介质中或以干粉的 形式使用。
8.2磁粉的尺寸、形状及其磁性,不论对单个还是就总体而言都是重要的见第章。
(10)9 表面清理9.1磁粉检测的灵敏度在很大程度上取决于被检表面的状况。
磁粉探伤规程

磁粉探伤规程1 适用范围1.1 本规程按ASNTTC—1A或ASNT所承认的同等标准要求编制。
1.2 本规程规定了磁粉检测方法及质量分级要求。
1.3 本规程适用于铁磁性材料制原材料、零部件和焊接接头表面、近表面缺陷的检测,不适用于奥氏体不锈钢和其他非铁磁性材料的检测。
2参考标准下列文件中的条款通过本规程的引用而成为本规程的条款。
凡是注日期的引用文件,其随后所有的修改单(不包括勘误的内容)或修订版均不适用于本部分,凡是不注日期的引用文件,其最新版本适用于本规程。
a) ASTM E 709 《磁粉检验的标准推荐操作方法》b) API规范4F、7K、8C、11Ec) ASNTTC-1A 《美国无损检测人员资格评定及认证推荐方法》d) ISO9712 《无损检测人员的资格鉴定和认证》e) JB/T6061—2007《焊缝无损检测》f) JB/T 4730 -2005 《承压设备无损检测》g) AWS D1.1/D1.1M:2010《钢结构焊接规范》h) ASME V《无损检测》3 人员3.1 Ⅰ级磁粉无损检测人员1)可在Ⅱ、Ⅲ级人员指导下进行无损检测操作;2)按照检测规程的要求,正确记录检测数据,整理检测记录。
3.2 Ⅱ级磁粉无损检测人员1)可编制一般的无损检测程序;2)按照无损检测工艺规程独立进行检测操作,评定检测结果,签发检测报告。
3.3 Ⅲ级磁粉无损检测人员负责验证和批准无损检测规程。
3.4 无损检测人员应按规定定期进行资格换证。
4 磁粉检测原理铁磁性材料和工件被磁化后,由于不连续性的存在,使工件表面和近表面的磁力线发生局部畸变而产生漏磁场,吸附施加在工件表面的磁粉,形成在合适光照下目视可见的磁痕,从而显示出不连续性的位置、形状和大小。
5 磁化设备校验5.1 MT设备采用CDX-Ⅲ型磁轭探伤仪。
5.2 设备校验5.2.1 校验周期:磁粉检测设备,至少每年校验一次;设备进行过重要电源修理,周期大修或损坏时,必须得到校验。
(完整)焊接磁粉检验规程

焊接磁粉检验规程1.适用范围1)本规程按ISO23278和ISO17638编制完成;2)本规程规定了磁粉检测方法及质量分级要求;3)本规程适用于铁磁性原材料、零部件和焊接接头表面、近表面缺欠的检测,不适用于不锈钢和其他非铁磁性材料的检测.2.参考标准1)ISO17638《焊接无损检测-磁粉检测》2) ISO23278《焊接无损检测-磁粉检测-可接受等级》3) ISO9712《无损检测人员的资格鉴定及认证推荐方法》3.人员1)Ⅰ级磁粉无损检测人员a)可在Ⅱ、Ⅲ级人员指导下进行无损检测操作;b)按照检测规程的要求,正确记录检测数据,整理检测记录.2)Ⅱ级磁粉无损检测人员a)可编制一般的无损检测程序b)按照无损检测工艺规程独立进行检测操作,评定检测结果,签发检测报告.3)Ⅲ级磁粉无损检测人员负责验证和批准无损检测规程、报告。
4)无损检测人员应按规定定期进行资格换证。
4.磁粉检测原理铁磁性材料和工件被磁化后,由于不连续性的存在,使工件表面和近表面的磁力线发生局部畸变而产生漏磁场,吸附施加在工件表面的磁性,形成在合适光照下目视可见的磁痕,从而显示出不连续的位置、形状和大小。
5.磁化设备校验1)校验周期磁粉检测设备至少每年校验一次;设备进行过重要电源修理,周期大修或损坏时,必须得到校验.如果设备已一年或一年以上未使用,则在第一次使用之前必须校验。
2)磁轭提升力的校验当使用磁轭最大间距时,交流电磁轭至少应有45N的提升力;直流电磁轭至少应有177N 的提升力;交叉磁轭至少应有118N的提升力。
6.磁粉、载体和磁悬液1)磁粉磁粉应具有高导磁率、低矫顽力和低剩磁,并应与被检工件表面颜色有较高的对比度。
2)载体本规程采用湿法,湿法采用水作为分散媒介。
3)磁悬液a)磁悬液浓度应按制造厂推荐,对循环使用的磁悬液,每天开始工作前,应进行磁悬液浓度测定;b)除制造厂另有规定外,非荧光磁粉磁悬液配制浓度应为10~25g/L,荧光磁粉应为0.5~3.0g/L。
磁粉探伤仪校验规程

磁粉探伤仪校验规程1.0目的规范磁轭式磁粉探伤机的校准操作,确保其有效性和准确性。
2.0范围本规程适用于本公司新购置和使用中的磁轭式磁粉探伤机的自校工作。
3.0校验用标准器具提升力试块、兆欧表。
4.0环境条件室温5.0校验及评定内容5.1外观及相互作用:目力观察、试验。
5.2 电磁轭提升力校验5.2.1 电磁轭的提升力至少半年校验一次。
在磁轭损伤修复后应重新校验。
5.2.2 准备45N、177N的试块各一块,试块须经检定合格,并在有效检定期内。
5.2.3 连接电源,打开仪器,将输出电流调节为交流状态。
磁轭探头置于45N 试块上,在通电磁化的同时提起探头,在探头能吸起试块的前提下,继续用砝码重力之和即为交流提升力。
5.2.4 连接电源,打开仪器,将输出电流调节为直流状态。
磁轭探头置于177N 试块上,在通电磁化的同时提起探头,在探头能吸起试块的前提下,继续用砝码重力之和即为直流提升力。
5.3绝缘电阻的测定将磁粉探伤机处于非工作状态,开关置于接通位置,用直流兆欧表在电源进线与机壳之间施加500V试验电压,稳定5s后测量绝缘电阻值。
5.4校验结果评定5.4.1 磁粉探伤机校验结果同是符合下列规定时为合格:A)交流提升力≥45N,直流提升力≥177N。
B)整机对地绝缘电阻大于5MΩ。
5.5校验周期磁粉探伤机根据使用的具体情况确定检定周期,一般最长不超过一年(其中电磁轭的提升力至少半年校验一次),必要时随时校验。
5.0参考文件JB/T 4730-2005《承压设备无损检测》JB/T 7411-94《电磁轭探伤仪技术条件》JJG(机械)100—92《磁粉探伤机检定规程》JJF1071国家计量校准规范编写规则JJF1001通用计量术语及定义GBT/T8170数值修约规则与极限数值的表示和判定7.0记录表格磁粉探伤仪校验记录磁粉探伤仪校验记录仪器型号仪器编号出厂日期生产厂家校验周期校验日期检定内容要求检查情况保养情况整机完整性及清洁保养完整清洁电压,电流表指示精度测量符合 1.5级精度开关及按钮性能检验接触性能良好开机运转情况检查正常运转磁场强度校验见注AC: >45N提升力校验DC:>177N通电触棒接触头检查无明显损伤内部短路检查无短路现象照明电路检查工作正常绝缘性能>5MΩ/500V注: 磁场强度检验法:20mm厚度钢板,触头间距150--200mm,磁化电流4--5A/mm,用磁场指示器,显示清晰可见.备注:校验结论:校验人:审核人:。
磁粉探伤检验要求要求规范
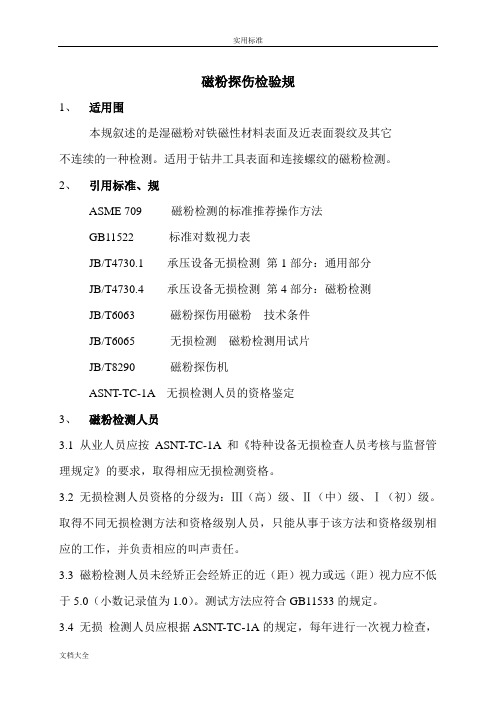
磁粉探伤检验规1、适用围本规叙述的是湿磁粉对铁磁性材料表面及近表面裂纹及其它不连续的一种检测。
适用于钻井工具表面和连接螺纹的磁粉检测。
2、引用标准、规ASME 709 磁粉检测的标准推荐操作方法GB11522 标准对数视力表JB/T4730.1 承压设备无损检测第1部分:通用部分JB/T4730.4 承压设备无损检测第4部分:磁粉检测JB/T6063 磁粉探伤用磁粉技术条件JB/T6065 无损检测磁粉检测用试片JB/T8290 磁粉探伤机ASNT-TC-1A 无损检测人员的资格鉴定3、磁粉检测人员3.1 从业人员应按ASNT-TC-1A和《特种设备无损检查人员考核与监督管理规定》的要求,取得相应无损检测资格。
3.2 无损检测人员资格的分级为:Ⅲ(高)级、Ⅱ(中)级、Ⅰ(初)级。
取得不同无损检测方法和资格级别人员,只能从事于该方法和资格级别相应的工作,并负责相应的叫声责任。
3.3 磁粉检测人员未经矫正会经矫正的近(距)视力或远(距)视力应不低于5.0(小数记录值为1.0)。
测试方法应符合GB11533的规定。
3.4 无损检测人员应根据ASNT-TC-1A的规定,每年进行一次视力检查,不得有色盲。
4、检测设备、器材和材料4.1 磁粉探伤机磁粉探伤机,在有效适用期应良好的保养。
交流电磁轭应有45N的提升力,直流电磁轭至少应有177N的提升力。
检测周期为6个月一次。
4.2 磁悬液磁悬液浓度应根据磁粉种类、力度、施加方法和被检工件表面状况等因素来确定。
用于完全润湿工件表面的油机介质,如出现不完全润湿,要从新进行清洗或添加更多磁粉或添加更多润湿剂。
4.3 退磁装置退磁装置应能保证退磁后,表面剩磁不大于0.3mT(240A/m)。
4.4 辅助设备磁场强度计标准试片A1(或CX)磁场指示器磁悬液浓度测试仪(管)2~10倍放大镜。
5、被检工件表面清洁被检工件表面,不得有油脂、铁锈、氧化皮或其他粘附磁粉的物质。
被检工件表面不规则状态,不得影响检测结果的正确性和完整性。
磁粉检测通用工艺规程

1. 范围适用于铁磁性材料制承压设备的原材料、零部件和焊接接头表面近表面缺陷的检测。
2.引用标准法规GB/T16673-1996 无损检测用黑光源辐射的测量JB/T4730-2005 承压设备无损检测JB/T6063-1992 磁粉探伤用磁粉JB/T6065-2004 无损检测磁粉检测用试片JB/T8290-1998 磁粉探伤机3. 检测人员3.1、磁粉检测人员上岗前, 应按照《特种设备无损检测人员考核与监督管理规则》的要求, 取得磁粉检测资格, 且只能从事相应资格的检测工作。
3.2、磁粉检测人员的矫正视力应不低于5.0, 并每年检查一次, 不得有色盲。
4. 检测设备、器材和材料4.1.设备磁粉检测设备应符合JB/T8290的规定。
4.1.1.当磁轭间距最大时, 交流电磁轭的提升力≮44N, 直流电磁轭的提升力≮177N.4.1.2、剩磁法检测时, 交流探伤机必配备断电相位控制器。
4.1.3、荧光磁粉检测时, 黑光灯在工作表面的照度≥1000μw/ , 黑光的波长λ=320nm~400nm,中心波长λ≈365nm。
黑光源应符合GB/T16673的规定。
4.1.4.退磁装置应保证退磁后表面剩磁≤0.3mT4.2.辅助器材一般包括下列器材:a)A1型、C型、D型和M1型试片, 磁场指示器;b)磁场强度计及毫特斯拉计;c)磁悬液浓度沉淀管;d)2~10倍放大镜;d)白光照度计;f)黑光灯;g)黑光辐照计。
4.3.磁粉、载液、磁悬液4.3.1、磁粉应具有高磁导率、低矫顽力和低剩磁, 并与工件表面的颜色对比度要较高。
其他要求应符合GB/T6063的规定。
4.3.2、载液为水时, 应加入防锈剂、表面活性剂及清洗剂。
载液为油时, 其运动粘度在38℃时应小于或等于3.0 /s, 使用温度小于或等于5.0 /s, 闪点不低于94℃, 且无荧光和异味。
4.3.3.磁悬液浓度范围应符合表1的规定。
测定前应充分搅匀。
表1 磁悬液浓度4.4.标准试块4.4.1、一般应选用A1-30/100, 检测狭小部位可选用C-15/50。
磁粉检测技术规范
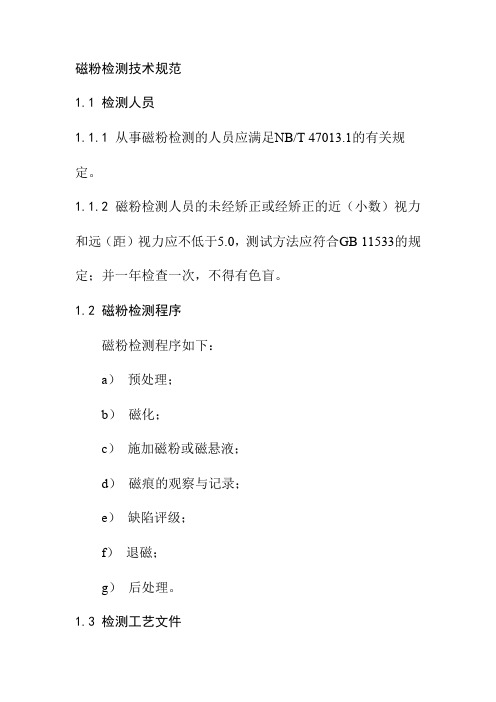
磁粉检测技术规范1.1 检测人员1.1.1 从事磁粉检测的人员应满足NB/T 47013.1的有关规定。
1.1.2磁粉检测人员的未经矫正或经矫正的近(小数)视力和远(距)视力应不低于5.0,测试方法应符合GB 11533的规定;并一年检查一次,不得有色盲。
1.2 磁粉检测程序磁粉检测程序如下:a)预处理;b)磁化;c)施加磁粉或磁悬液;d)磁痕的观察与记录;e)缺陷评级;f)退磁;g)后处理。
1.3 检测工艺文件1.3.1 检测工艺文件包括工艺规程和操作指导书。
1.3.2工艺规程除满足NB/T 47013.1的要求外,还应规定下列相关因素的具体范围或要求;当相关因素的一项或几项发生变化并超出规定时,应重新编制或修订工艺规程。
a) 被检测对象(形状、尺寸、材质等);b) 磁化方法;c) 检测用仪器设备;d) 磁化电流类型及其参数;e) 表面状态;f) 磁粉(类型、颜色、供应商);g) 磁粉施加方法;h) 最低光照度;i) 非导电表面反差增强剂(使用时);j) 黑光福照度(使用时)。
1.3.3应根据工艺规程的内容和被检工件的检测要求编制操作指导书,其内容除满足NB/T 47013.1的要求外,至少还应包括:a) 检测区域和表面质量要求;b) 检测环境要求;c) 检测技术要求:灵敏度试片显示,磁化方法,磁化规范,磁化时间等;d) 磁粉或磁悬液的施加方法;e) 磁痕观察条件;f) 退磁要求。
1.3.4操作指导书在首次应用前应采用标准试件进行工艺验证,以确定是否能达到标准规定的要求。
1.4 安全要求1.1.1电流短路引起的电击或在所用相对较低电压下的大电流引起的灼伤。
1.1.2使用荧光磁粉检测时,黑光灯激发的黑光对眼睛和皮肤产生的有害影响。
1.1.3使用或去除多余磁粉时,尤其是干磁粉,其悬浮的颗粒物等被吸入或进入眼睛、耳朵导致的伤害。
1.1.4使用不符合要求的有毒磁粉等材料引起的有害影响。
1.1.5易燃易爆的场合使用通电法和触头法引发的火灾。
磁粉探伤检验要求规范标准
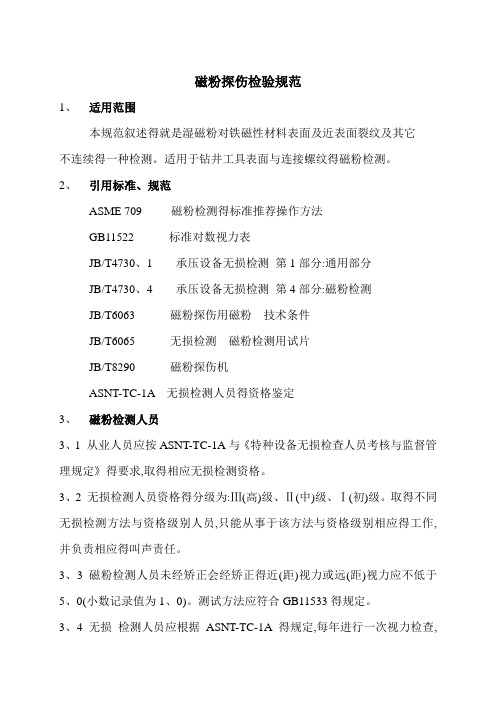
磁粉探伤检验规范1、适用范围本规范叙述得就是湿磁粉对铁磁性材料表面及近表面裂纹及其它不连续得一种检测。
适用于钻井工具表面与连接螺纹得磁粉检测。
2、引用标准、规范ASME 709 磁粉检测得标准推荐操作方法GB11522 标准对数视力表JB/T4730、1 承压设备无损检测第1部分:通用部分JB/T4730、4 承压设备无损检测第4部分:磁粉检测JB/T6063 磁粉探伤用磁粉技术条件JB/T6065 无损检测磁粉检测用试片JB/T8290 磁粉探伤机ASNT-TC-1A 无损检测人员得资格鉴定3、磁粉检测人员3、1 从业人员应按ASNT-TC-1A与《特种设备无损检查人员考核与监督管理规定》得要求,取得相应无损检测资格。
3、2 无损检测人员资格得分级为:Ⅲ(高)级、Ⅱ(中)级、Ⅰ(初)级。
取得不同无损检测方法与资格级别人员,只能从事于该方法与资格级别相应得工作,并负责相应得叫声责任。
3、3 磁粉检测人员未经矫正会经矫正得近(距)视力或远(距)视力应不低于5、0(小数记录值为1、0)。
测试方法应符合GB11533得规定。
3、4 无损检测人员应根据ASNT-TC-1A得规定,每年进行一次视力检查,不得有色盲。
4、检测设备、器材与材料4、1 磁粉探伤机磁粉探伤机,在有效适用期内应良好得保养。
交流电磁轭应有45N得提升力,直流电磁轭至少应有177N得提升力。
检测周期为6个月一次。
4、2 磁悬液磁悬液浓度应根据磁粉种类、力度、施加方法与被检工件表面状况等因素来确定。
用于完全润湿工件表面得油机介质,如出现不完全润湿,要从新进行清洗或添加更多磁粉或添加更多润湿剂。
4、3 退磁装置退磁装置应能保证退磁后,表面剩磁不大于0、3mT(240A/m)。
4、4 辅助设备磁场强度计标准试片A1(或CX)磁场指示器磁悬液浓度测试仪(管)2~10倍放大镜。
5、被检工件表面清洁被检工件表面,不得有油脂、铁锈、氧化皮或其她粘附磁粉得物质。
新版起重机械吊钩探伤检测(吊钩应半年进行一次磁粉探伤)
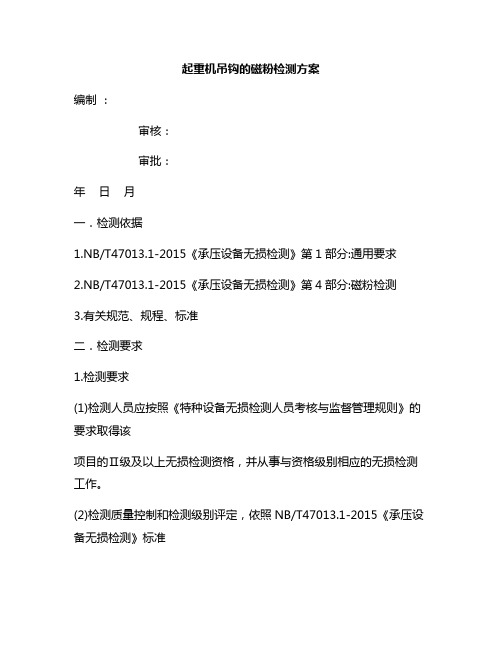
起重机吊钩的磁粉检测方案编制:审核:审批:年日月一.检测依据1.NB/T47013.1-2015《承压设备无损检测》第1部分:通用要求2.NB/T47013.1-2015《承压设备无损检测》第4部分:磁粉检测3.有关规范、规程、标准二.检测要求1.检测要求(1)检测人员应按照《特种设备无损检测人员考核与监督管理规则》的要求取得该项目的Ⅱ级及以上无损检测资格,并从事与资格级别相应的无损检测工作。
(2)检测质量控制和检测级别评定,依照NB/T47013.1-2015《承压设备无损检测》标准进行。
检测部位和比例,应符合有关规程、规范和本院有关检验规范的要求。
三 .检测准备1. 检测人员详细了解被检吊钩的设计、制造、使用、检验情况。
2.仪器、设备、材料。
所使用的仪器设备和材料应是鉴定和检验合格的产品,性能指标应符合NB/T47013.1-2015标准。
磁轭式检测仪应定期校验提升力,当使用磁轭最大间距时,交流电磁轭至少应有45N的提升力。
3. 磁悬液配制非荧光磁悬液浓度为:10-25g/L。
4.吊钩被检测表面的制备(1) 若吊钩被检测表面凹凸不平,以至可能遮盖缺陷显示时,应通过打磨来制备。
被检测工件的表面粗糙度Ra应不大于25μm。
(2) 工件表面应保证无锈、无油、无污、无涂层。
清理可采用砂纸、钢丝刷、砂轮、棉纱等。
(3) 工件表面色泽应保证能与磁粉颜色形成较大反差。
采用非荧光磁粉时,可使用反差增强剂。
四.检测方法和检测区域1.磁化方法采用连续磁化方法,先用磁悬液润湿工件受检表面,在通电磁化的同时施加磁悬液,持续磁化时间为1~3s。
为保证磁化效果至少反复磁化二次,停施磁悬液至少1s后才可以停止磁化。
2.磁化方向和检测区域(1) 使用电磁轭磁粉探伤仪时,被检工件的每一被检区域至少应进行两次独立的检测,两次检测的磁力线方向应大致相互垂直。
(2) 磁轭的磁极间距应控制在75-200mm的范围内,检测的有效区域为两极连线两侧各50mm的范围内,磁化区域每次应有不少于15mm的重叠。
磁粉探伤一级二级三级标准

磁粉探伤一级二级三级标准一、保证项目1、焊接材料应符合设计要求和有关标准的规定,应检查质量证明书及烘焙记录。
2、焊工必须经考试合格,检查焊工相应施焊条件的合格证及考核日期。
3、Ⅰ、Ⅱ级焊缝必须经探伤检验,并应符合设计要求和施工及验收规范的规定,检查焊缝探伤报告。
4、焊缝表面Ⅰ、Ⅱ级焊缝不得有裂纹、焊瘤、烧穿、弧坑等缺陷。
Ⅱ级焊缝不得有表面气孔、夹渣、弧坑、裂纹、电弧擦伤等缺陷,且Ⅰ级焊缝不得有咬边、未焊满等缺陷。
二、基本项目1、焊缝外观:焊缝外形均匀,焊道与焊道、焊道与基本金属之间过渡平滑,焊渣和飞溅物清除干净。
2、表面气孔:Ⅰ、Ⅱ级焊缝不允许;Ⅲ级焊缝每50mm长度焊缝内允许直径≤0.4t;且≤3mm气孔2个;气孔间距≤6倍孔径。
3、咬边:Ⅰ级焊缝不允许。
Ⅱ级焊缝:咬边深度≤0.05t,且≤0.5mm,连续长度≤100mm,且两侧咬边总长≤10%焊缝长度。
Ⅲ级焊缝:咬边深度≤0.lt,且≤lmm。
注:t为连接处较薄的板厚。
4、允许偏差项目,见表5-1。
三、成品保护1、焊后不准撞砸接头,不准往刚焊完的钢材上浇水。
低温下应采取缓冷措施。
2、不准随意在焊缝外母材上引弧。
3、各种构件校正好之后方可施焊,并不得随意移动垫铁和卡具,以防造成构件尺寸偏差。
隐蔽部位的焊缝必须办理完隐蔽验收手续后,方可进行下道隐蔽工序。
4、低温焊接不准立即清渣,应等焊缝降温后进行。
四、应注意的质量问题1、尺寸超出允许偏差:对焊缝长宽、宽度、厚度不足,中心线偏移,弯折等偏差,应严格控制焊接部位的相对位置尺寸,合格后方准焊接,焊接时精心操作。
2、焊缝裂纹:为防止裂纹产生,应选择适合的焊接工艺参数和施焊程序,避免用大电流,不要突然熄火,焊缝接头应搭10~15mm,焊接中木允许搬动、敲击焊件。
3、表面气孔:焊条按规定的温度和时间进行烘焙,焊接区域必须清理干净,焊接过程中选择适当的焊接电流,降低焊接速度,使熔池中的气体完全逸出。
4、焊缝夹渣:多层施焊应层层将焊渣清除干净,操作中应运条正确,弧长适当。
磁粉检测规程
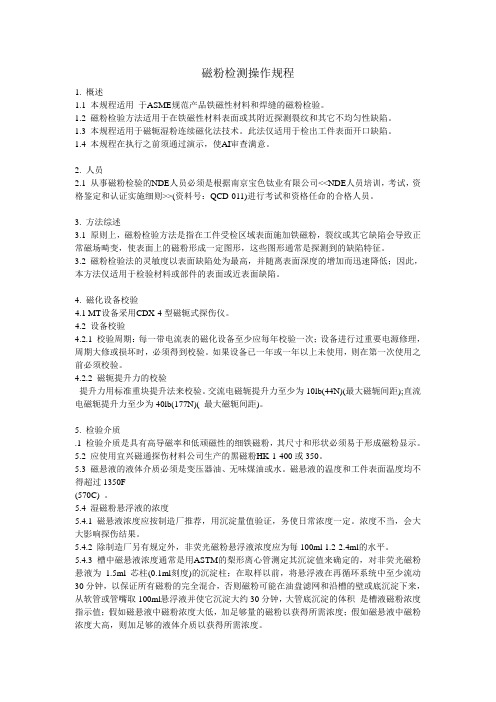
磁粉检测操作规程1. 概述1.1 本规程适用于ASME规范产品铁磁性材料和焊缝的磁粉检验。
1.2 磁粉检验方法适用于在铁磁性材料表面或其附近探测裂纹和其它不均匀性缺陷。
1.3 本规程适用于磁轭湿粉连续磁化法技术。
此法仅适用于检出工件表面开口缺陷。
1.4 本规程在执行之前须通过演示,使AI审查满意。
2. 人员2.1 从事磁粉检验的NDE人员必须是根据南京宝色钛业有限公司<<NDE人员培训,考试,资格鉴定和认证实施细则>>(资料号:QCD-011)进行考试和资格任命的合格人员。
3. 方法综述3.1 原则上,磁粉检验方法是指在工件受检区域表面施加铁磁粉,裂纹或其它缺陷会导致正常磁场畸变,使表面上的磁粉形成一定图形,这些图形通常是探测到的缺陷特征。
3.2 磁粉检验法的灵敏度以表面缺陷处为最高,并随离表面深度的增加而迅速降低;因此,本方法仅适用于检验材料或部件的表面或近表面缺陷。
4. 磁化设备校验4.1 MT设备采用CDX-4型磁轭式探伤仪。
4.2 设备校验4.2.1 校验周期:每一带电流表的磁化设备至少应每年校验一次;设备进行过重要电源修理,周期大修或损坏时,必须得到校验。
如果设备已一年或一年以上未使用,则在第一次使用之前必须校验。
4.2.2 磁轭提升力的校验提升力用标准重块提升法来校验。
交流电磁轭提升力至少为10lb(44N)(最大磁轭间距);直流电磁轭提升力至少为40lb(177N)( 最大磁轭间距)。
5. 检验介质.1 检验介质是具有高导磁率和低顽磁性的细铁磁粉,其尺寸和形状必须易于形成磁粉显示。
5.2 应使用宜兴磁通探伤材料公司生产的黑磁粉HK-1-400或350。
5.3 磁悬液的液体介质必须是变压器油、无味煤油或水。
磁悬液的温度和工件表面温度均不得超过1350F(570C) 。
5.4 湿磁粉悬浮液的浓度5.4.1 磁悬液浓度应按制造厂推荐,用沉淀量值验证,务使日常浓度一定。
- 1、下载文档前请自行甄别文档内容的完整性,平台不提供额外的编辑、内容补充、找答案等附加服务。
- 2、"仅部分预览"的文档,不可在线预览部分如存在完整性等问题,可反馈申请退款(可完整预览的文档不适用该条件!)。
- 3、如文档侵犯您的权益,请联系客服反馈,我们会尽快为您处理(人工客服工作时间:9:00-18:30)。
磁粉探伤检验规范1、适用范围本规范叙述的是湿磁粉对铁磁性材料表面及近表面裂纹及其它不连续的一种检测。
适用于钻井工具表面和连接螺纹的磁粉检测。
2、引用标准、规范ASME 709 磁粉检测的标准推荐操作方法GB11522 标准对数视力表JB/T4730.1 承压设备无损检测第1部分:通用部分JB/T4730.4 承压设备无损检测第4部分:磁粉检测JB/T6063 磁粉探伤用磁粉技术条件JB/T6065 无损检测磁粉检测用试片JB/T8290 磁粉探伤机ASNT-TC-1A 无损检测人员的资格鉴定3、磁粉检测人员3.1 从业人员应按ASNT-TC-1A和《特种设备无损检查人员考核与监督管理规定》的要求,取得相应无损检测资格。
3.2 无损检测人员资格的分级为:Ⅲ(高)级、Ⅱ(中)级、Ⅰ(初)级。
取得不同无损检测方法和资格级别人员,只能从事于该方法和资格级别相应的工作,并负责相应的叫声责任。
3.3 磁粉检测人员未经矫正会经矫正的近(距)视力或远(距)视力应不低于5.0(小数记录值为1.0)。
测试方法应符合GB11533的规定。
3.4 无损检测人员应根据ASNT-TC-1A的规定,每年进行一次视力检查,不得有色盲。
4、检测设备、器材和材料4.1 磁粉探伤机磁粉探伤机,在有效适用期内应良好的保养。
交流电磁轭应有45N的提升力,直流电磁轭至少应有177N的提升力。
检测周期为6个月一次。
4.2 磁悬液磁悬液浓度应根据磁粉种类、力度、施加方法和被检工件表面状况等因素来确定。
用于完全润湿工件表面的油机介质,如出现不完全润湿,要从新进行清洗或添加更多磁粉或添加更多润湿剂。
4.3 退磁装置退磁装置应能保证退磁后,表面剩磁不大于0.3mT(240A/m)。
4.4 辅助设备磁场强度计标准试片A1(或CX)磁场指示器磁悬液浓度测试仪(管)2~10倍放大镜。
5、被检工件表面清洁被检工件表面,不得有油脂、铁锈、氧化皮或其他粘附磁粉的物质。
被检工件表面不规则状态,不得影响检测结果的正确性和完整性。
6、检测操作规程及工艺6.1 用磁悬液浓度沉淀管或浓度测试仪测量磁粉浓度,浓度范围见表1。
表1磁悬液浓度6.2 检测工件表面:非荧光磁粉检测时,缺陷磁痕的评定应在可见光下进行,其检测表面可见光照度不小于1000lx,当采用便携式检测仪时,可见光照度不小于500lx。
荧光磁粉检测时,所用黑光灯在工件表面的辐照度大于或等于1000μW/cm2。
另外要保持检测场所没有其他干扰作用的杂物。
6.3 用磁场强度计测量磁场强度的大小在30~60c范围内。
6.4 用标准试片检验检测设备、磁粉和磁悬液的综合性能。
6.4.1 选用A1型标准试片,试片表面有锈蚀、皱折或磁特性发生改变时不得继续使用。
6.4.2 将试片人工缺陷的面朝下,将其平整的粘贴在被检面上。
6.4.3 用连续磁化的方法检验磁粉检测设备、磁粉和磁悬液的综合性能,保证试片表面显示能代表伤深度30%的清晰的磁粉痕迹。
6.5施加磁粉磁化6.5.1 磁悬液每次施加前应充分搅匀。
6.5.2 采用自动喷涂施加、连续检测的方法进行,及被检工件的磁化、施加磁悬液以及观察磁痕显示都应在通电磁化时间内完成,通电时间1s-3s,停止施加磁悬液至少1s后,方可停止磁化。
6.5.3 喷涂磁悬液时,不应使检测表面上的磁悬液流速过快,避免影响磁粉附着效果。
6.5.4 为保证磁化效果,同一检测面同一方向上至少反复磁化两次。
6.5.5 同一检测面至少两个方向磁化,两次磁化,两极连线夹角尽量保持90°,使在检测面所有方向上能显示缺陷的痕迹。
6.5.6 检测应有足够的覆盖,保证被检面100%检验。
6.5.7 将磁场检测计放到检测面的范围内,磁化的同时,核实磁场的强度和方向。
6.6 磁痕的观察与记录6.6.1 缺陷磁化的观察应在磁痕形成后立即进行。
6.6.2 除能确认磁痕是由于工件材料局部磁性不均或操作不当照成的外,其他磁痕显示应作为缺陷处理。
6.6.3 辨认细小磁痕采用2—10倍放大镜进行观察。
6.6.4 磁痕显示记录照相或草图示的方式记录,并在工件上标示。
6.7 磁痕的分类6.7.1 磁痕显示分为相关显示、非相关显示和伪显示。
6.7.2 长度和宽度之比大于3的缺陷磁痕,按条状磁痕处理,长度与宽度之比小于3的缺陷磁痕,按圆形磁痕处理。
6.7.3 缺陷磁痕长轴方向与工件(轴类或管类)轴线的夹角大于或等于30°时,按横向缺陷处理,其他按纵向缺陷处理。
6.7.4 两条或两条以上磁痕在同一直线上且其间距不大于2mm时,按一条缺陷处理,其长度为各磁痕长度加间隙长度之和。
6.7.5 长度小于0.5mm的磁痕可以不计。
6.8 工件的退磁工件可使用交流磁轭进行局部退磁或采用缠绕线圈分段或连续退磁。
工件已退磁效果可用磁场强度计测定,不大于0.3mT(240A/m)。
7、复验当出现下列情况之一时需复验:1)检测结束时,用标准试片验证检测灵敏度不符合要求时;2)发现检测过程中,操作失误过或技术条件改变时;3)合同各方有争议或认为有必要时;8、检测效果评定和质量分类8.1 不允许存在任何裂纹和白点。
8.2 紧固件和轴类零件不允许任何横向缺陷。
8.3 质量分级见下表2。
表3。
表2 焊接接头磁粉检测质量分级表3 受压加工部件和材料磁粉检测质量分级8.4 综合评级圆形缺陷评定区内,同时存在多种缺陷时,应进行综合评级。
对各类缺陷进行分别评级,区质量级别最低级别为综合评定级别;当各类质量评定级别相同时,则降低一级为综合评定级别。
9、磁粉检测报告9.1 磁粉检测报告应客观、准确、完整、清晰和及时。
9.2 报告的内容应至少包括以下内容:1)委托单位;2)被检工件:名称、规格、材质、编号、焊接方式、热处理状况;3)检测设备:名称、型号;4)检测规范:磁化方法及磁化规范,磁粉种类及磁悬液浓度和施加方法,检测灵敏度校验及标准试片、标准试块;5)磁痕记录及工件草图(或示意图);6)检测结果及质量分级、检测标准名称及验收等级;7)检测人员和责任人员签字及技术等级;8)检测日期。
10、后处理10.1 检测工作结束以后,应及时处理工件及由检测过程产生的废弃物,各种设施及仪器、仪表恢复到初始状态。
10.2 评定发现超标的磁痕时,应在工件相关位置上,标识出清晰的标记,并记录,以便实施打磨等补修措施及另行处理。
附录A 磁粉检测设备验证周期磁粉检测用设备及辅助设备应进行定期检测,验证其适宜性,并符合表A的要求。
表A 验证周期西安长庆石油工具制造有限责任公司文件编号:CQGJ磁粉探伤检验规范,编制:审核:批准:2008-12-20 2008-12-20实施西安长庆石油工具制造有限责任公司发布摩擦焊接钻杆焊缝区磁粉检测作用指导书1检测范围本指导书适用于对摩擦焊接钻杆焊缝区的磁粉检测。
2检测目的采用荧光磁粉法,检测出摩擦焊接钻杆焊缝区表面及近表面的缺陷。
3引用标准、规范见《磁粉探伤检验规范》2。
4检测人员要求见《磁粉探伤检验规范》3。
5检测设备5.1设备:磁粉检测设备为CJW20000E,其对工件的磁化采用复合磁化方法,即周向磁轭磁化法和纵向线圈磁化法。
5.2荧光磁悬液:本方案用水作为分散剂,并加入适量防锈剂、表面活性剂和消泡剂。
其配方见附表B1。
5.3标准试片:使用符合JB/T6056规定的A1-15/50型试片。
5.4磁场指示器:用于指示磁场方向和有效检测区。
是粗略的方法。
5.5辅助器材应包括以下器材a)磁场强度计;b)磁悬液浓度沉淀管;c)2-10倍放大镜;d)黑光辐照计;e)黑光灯。
6工件被检区域焊颈外表面。
7检测流程7.1接收流转单或检测委托单:熟悉和掌握相关技术要求。
7.2待检测工件表面检查:被检表面不得有油脂、铁锈、氧化皮或其他粘附磁粉的物质。
表面的不规则不能影响检测的正确性和完整性,否则应继续修理。
如打磨,则其表面粗糙度应R a≤25μm。
7.3设备启动和灵敏度测试7.3.1检查并调整电路、气路、水(磁悬液)路正确、安全、可靠,依次启动电、气、水(磁悬液)系统。
7.3.2黑光度检测。
7.3.3磁粉浓度及污染物检测。
见附录B2。
7.3.4水断(润湿)试验。
完全覆盖检测范围,无反润湿现象。
7.3.5灵敏度测试:将人工缺陷的面朝下紧附与被检表面,试片表面显示清晰的磁粉痕迹。
7.4将工件输送到检测工位,磁化、施加磁悬液(磁粉)、观察磁痕显示。
停施磁悬液至少1s后,方可停止磁化。
为保证磁化效果应至少反复磁化两次。
注意,磁悬液流速不宜过快。
7.5检测范围:焊颈外径。
7.6工件退出工位。
7.7不合格品检出,放置到指定区域。
7.8记录检测结果,填写流转单或委托单。
8 磁痕的观察与记录8.1 缺陷磁化的观察应在磁痕形成后立即进行。
8.2 除能确认磁痕是由于工件材料局部磁性不均或操作不当照成的外,其他磁痕显示应作为缺陷处理。
8.3 辨认细小磁痕采用2—10倍放大镜进行观察。
8.4 磁痕显示记录用草图示的方式记录,并在工件上标示。
9、复验当出现下列情况之一时需复验:1)检测结束时,用标准试片验证检测灵敏度不符合要求时;2)发现检测过程中,操作失误过或技术条件改变时;3)合同各方有争议或认为有必要时;10、检测效果评定和质量分类10.1 不允许存在任何裂纹和白点。
10.2 质量分级见下表1。
表2。
表1 磁粉检测质量分级10.3 本方案采用Ⅰ级。
11 综合评级圆形缺陷评定区内,同时存在多种缺陷时,应进行综合评级。
对各类缺陷进行分别评级,区质量级别最低级别为综合评定级别;当各类质量评定级别相同时,则降低一级为综合评定级别。
12、磁粉检测报告12.1 磁粉检测报告应客观、准确、完整、清晰和及时。
12.2 报告的内容应至少包括以下内容:1)委托单位;2)被检工件:名称、规格、材质、编号、焊接方式、热处理状况;3)检测设备:名称、型号;4)检测规范:磁化方法及磁化规范,磁粉种类及磁悬液浓度和施加方法,检测灵敏度校验及标准试片;5)磁痕记录及工件草图(或示意图);6)检测结果及质量分级、检测标准名称及验收等级;7)检测人员和责任人员签字及技术等级;8)检测日期。
13、后处理13.1 检测工作结束以后,应及时处理工件及由检测过程产生的废弃物,各种设施及仪器、仪表恢复到初始状态。
13.2 评定发现超标的磁痕时,应在工件相关位置上,标识出清晰的标记,并记录,以便实施打磨等补修措施及另行处理。
附录B 荧光磁悬液B1 荧光磁悬液(水载液)配方:YC2磁粉:0.5-2g/L(≥400目)防锈剂:1-2g/L分散剂:1-2g/L消泡剂:1-2g/L配制方法:首先将乳化剂与消泡剂加入水中搅拌均匀,并按比例加足水,成为水载液。
用水载液与磁粉搅匀,然后加入亚硝酸钠。