影响片剂质量的主要原因及解决方法
影响片剂质量的主要原因及解决方法
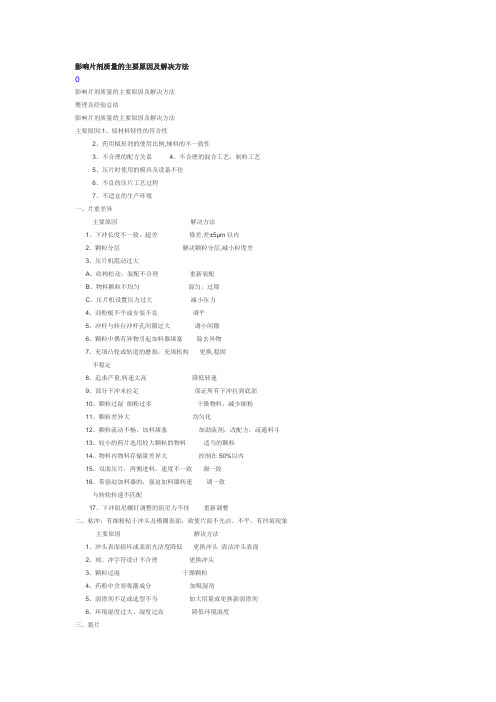
影响片剂质量的主要原因及解决方法影响片剂质量的主要原因及解决方法整理及经验总结影响片剂质量的主要原因及解决方法主要原因:1、原材料特性的符合性2、药用赋形剂的使用比例,辅料的不一致性3、不合理的配方关系4、不合理的混合工艺,制粒工艺5、压片时使用的模具及设备不佳6、不良的压片工艺过程7、不适宜的生产环境一、片重差异主要原因解决方法1、下冲长度不一致,超差修差,差±5μm以内2、颗粒分层解决颗粒分层,减小粒度差3、压片机震动过大A、结构松动,装配不合理重新装配B、物料颗粒不均匀混匀,过筛C、压片机设置压力过大减小压力4、刮粉板不平或安装不良调平5、冲杆与转台冲杆孔间隙过大调小间隙6、颗粒中偶有异物引起加料器堵塞除去异物7、充填凸轮或轨道的磨损,充填机构更换,稳固不稳定8、追求产量,转速太高降低转速9、部分下冲未拉足保证所有下冲拉到底部10、颗粒过湿细粉过多干燥物料,减少细粉11、颗粒差异大均匀化12、颗粒流动不畅,加料堵塞加助流剂,改配方,疏通料斗13、较小的药片选用较大颗粒的物料适当的颗粒14、物料内物料存储量差异大控制在50%以内15、双面压片,两侧进料,速度不一致调一致16、带强迫加料器的,强迫加料器转速调一致与转轮转速不匹配17、下冲阻尼螺钉调整的阻尼力不佳重新调整二、粘冲:有细粉粘于冲头及模圈表面,致使片面不光洁、不平、有凹痕现象主要原因解决方法1、冲头表面损坏或表面光洁度降低更换冲头清洁冲头表面2、刻、冲字符设计不合理更换冲头3、颗粒过湿干燥颗粒4、药粉中含易吸潮成分加吸湿剂5、润滑剂不足或选型不当加大用量或更换新润滑剂6、环境湿度过大、湿度过高降低环境湿度三、裂片主要原因解决方法1、压片时有空气存在于药片当中调整压力、减慢车速、增加预压时间或用有预压的工艺2、冲模磨损严重更换冲模3、黏结剂选型不当或不足更换黏结剂或加量4、颗粒含水量过低增加含水量5、颗粒过细或过粗调整颗粒粒度6、颗粒中油类成分较多加吸油剂7、模具间隙太小、不能顺利排气更换模具四、松片主要原因解决方法1、压力不够增加压力2、受压时间太少、转速快延长受压时间、增加预压、减低转速3、冲头长短不齐调整冲头4、活络冲冲头发生松动进行紧固5、下冲杆掉冲紧固6、黏结剂选型不当或太少更换黏合剂或加量7、颗粒中润滑剂比例不当调节比例8、颗粒太干燥增加颗粒水分9、物料粉碎粒度不够、纤维性或高弹性粉碎粒度过100目筛、加强黏合剂、药物或油类成分多,混合不均吸油剂10、药片压制后,置空气中过久,受潮缩短放置时间五、变色及斑点主要原因解决方法1、颗粒受油脂或其他杂质污染杜绝油脂及杂质污染2、颗粒过硬或含糖品种及有色降低颗粒硬度、有色片剂用片剂颗粒易出现乙醇为润滑剂制粒3、颗粒过大或过小颗粒适宜4、冲模型面出现锈斑清除锈斑5、加料器与转台表面摩擦有金属细粉调节加料器高度随颗粒进入模孔6、冲头与模圈内壁发生摩擦调节模圈致有色金属粉末进入颗粒六、崩解迟缓主要原因解决方法1、黏结剂粘性太强或用量过多,更换黏结剂或降低用量颗粒过硬过粗2、崩解剂选型不当、用量不足更换崩解剂或加量疏水性润滑剂太多降低疏水性润滑剂3、压力过大、片子过硬减低压力七、刻字或线条不清晰主要原因解决方法1、冲模的字符设计、布置不合理更换字符2、冲模型面磨损或破坏更换冲模3、冲模尺寸过大或不够更换冲模4、预压力过大降低预压力粉末直接压片粉末直接压片的应用方法及其注意事项由于粉末直接压片具有较明显的优点,如工艺过程比较简单,不必制粒、干燥,产品崩解或溶出快,成品质量稳定,在国外约有40%的片剂品种已采用这种工艺生产。
论述片剂压片中常见的问题及原因

论述片剂压片中常见的问题及原因《片剂压片中常见问题及原因》随着科技的进步,片剂作为一种常见的制剂形式,在医药领域中占有重要地位。
然而,片剂压片过程中常会遇到一些问题,这些问题可能会影响片剂的质量和稳定性。
本文将讨论片剂压片中常见问题及其原因。
首先,常见的问题之一是片厚度和硬度不均匀。
这意味着片剂在质量和形状上存在差异,可能会导致剂量的浮动或药效不一致。
造成这一问题的原因可能是压片机的不均匀力量分布,或者药物混合时没有均匀分散。
其次,片剂可能会在压片过程中出现断裂现象。
这一问题可能与原料的物理性质、药物与辅料之间的不良相互作用或制剂工艺有关。
例如,药物本身可能具有脆弱性,容易在压片过程中发生断裂。
另外,制剂工艺中的温度、压力和湿度等因素也可以影响片剂的断裂性质。
此外,片剂中可能存在空洞、裂纹或劣化现象。
这可能是由于原料粉末颗粒粒径分布不均,或者压片时药物与辅料之间发生了化学反应。
药物颗粒的大小和形状不一致可能导致空洞或裂纹的产生,而化学反应则可能导致药物劣化,降低药效。
最后,片剂在贮存过程中可能会出现退化现象。
片剂的退化可能是由于空气、光线、湿度等外界因素与片剂中的药物相互作用所致。
药物在暴露于不适宜的环境条件下容易发生物理和化学变化,从而导致片剂质量下降或发生降解。
综上所述,片剂压片中常见的问题包括片厚度和硬度不均匀、片剂断裂、空洞和裂纹以及片剂的退化现象。
这些问题的产生原因可能是压片机的力量分布不均、原料的物理性质不一致、药物与辅料之间的相互作用或环境因素的影响。
为了解决这些问题,制药厂商需要密切关注片剂制备过程中的每个环节,并采取相应的措施来提高片剂的质量和稳定性。
片剂制备常见问题及解决方法

片剂制备常见问题及解决方法二.片剂随着中国几千年历史的发展,尤其是近年来中药及其制剂的广泛使用中药已成为独具特色的治病良药。
但是,中药片剂在生产中也存在着不少问题,现对这些问题及其解决方法作一综述。
1 生产工艺糖衣片的常规打光方法是在闷锅结束后,打蜡粉加入片子中(每万片用量3~5g),开动糖衣锅打光,一般需15min完成。
但生产时,常因一些因素掌握不好而导致打光困难,甚至被迫停止。
报道可改用“布袋-糖衣锅”法打光,该法只需5~10min,且应用广泛。
生产复方冬凌草含片,老工艺是将冬凌草提取液经减压浓缩到稠膏状后,直接与其他浸膏混合置烘箱中高温烘干,新工艺将提取液经减压浓缩至稠膏状后,溶解在乙醇中,制粒前喷入干粉中,制粒后在鼓风机中低温烘干。
通过对比发现,采用新工艺制得的含片中冬凌草甲素含量比老工艺制得者高,临床疗效更显著。
2 崩解片剂崩解迟缓是影响片剂质量的主要因素之一。
据报道片剂崩解迟缓主要是受主药!赋形剂和生产过程的影响[3]"最佳解决办法是:加入崩解作用较强的崩解剂,如2%~5%羟甲基淀粉钠;在保证片剂成品质量的前提下,可按一定比例与崩解良好的颗粒混合均匀压片;先加入一定量的崩解剂,然后再与崩解良好的颗粒混合"另外,改进制粒方法也可改善片剂的崩解性能,如紫花杜鹃片(浸膏在颗粒中占80%)分别用混合机与喷雾制粒,两种片剂的崩解时限分别为60,20~30min;感冒清片(浸膏在颗粒中占40%)用上述两方法制粒,两种片剂的崩解时限分别为55,23min。
结果表明,改用喷雾制粒压片,崩解时限明显缩短,产品质量提高。
3 包衣在气温较高的条件下,片芯易失水,且由于受热膨胀,导致片子的爆裂。
一般认为,糖衣片所发生的龟裂砚象主要是包衣层中搪层和有色搪层水份挥发引起的,然面过份干燥还会析出糖的结晶,而形成龟裂,所以当羞片水份在30%-50%时,包衣温度在50℃以下干操,不会导致片芯的膨胀,低温放置也不会龟裂。
西药片剂生产过程中常见质量问题和解决方法
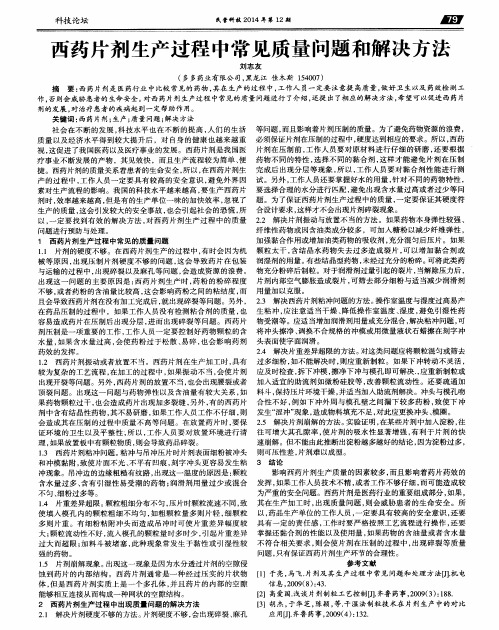
而且影 响着 片剂压制 的质量 。为了避免药物 资源 的浪费 , 社会 在不断 的发展 , 科技水 平也在 不断 的提高 , 人 们 的生 活 等 问题 , 必须保证片剂在压制的过程中 , 硬度达到相应 的要求 。所 以, 西药 质量 以及经济 水平得 到较大提 升后 ,对 自身 的健康也 越来越 重 工 作人员要 对原材 料进行仔 细的研磨 , 还要根 据 视, 这促进 了我 国医药 以及 医疗 事业 的发展 。西药片剂是 我 国医 片剂 在压制前 , 药 物不 同的特性 , 选择不 同的黏合 剂 , 这样才 能避免 片剂在压 制 疗事业不 断发 展的产物 ,其见效快 ,而且生产 流程 较为简单 、 便 完 成后 出现 分层等现象 , 所以 , 工作人 员要对 黏合剂性 能进行 测 捷 。西药片剂的质量 关系着 患者的生命安全 , 所以 , 在西药片剂生 试 。另外 , 工作人员还要 掌握好水的用量 , 针对不 同的药物特性 , 产 的过程 中 , 工 作人员一 定要具有 较高 的安全意识 , 避免外 界 因 要选择合 理的水分进行匹配 , 避免 出现含 水量过高或者 过少等问 素对生产 流程的影响 。我 国的科技水 平越来越 高 , 要 生产西药 片 一定要保证 其硬度符 剂时, 效率越来越 高 , 但是有 的生 产单 位一 味的加快效率 , 忽视 了 题 。为了保 证西药片剂生产过程 中的质量 , 合设计要求 , 这样才不会 出现片剂 碎裂 现象 。 生产 的质量 , 这会 引发较大的安全事故 , 也会 引起社会 的恐慌 , 所 2 . 2 解决 片剂 振动 与放 置不 当的方法 。如果药物本身 弹性较 强、 以, 一 定要找 到有效 的解 决方 法 , 对 西药 片剂生产过 程 中的质量
片剂及其生产过程中常见问题和处理方法

片剂及其生产过程中常见问题和处理方法片剂是一种常见的药物制剂形式,其以固体形式存在,适合口服给药。
然而,在片剂的生产过程中常会遇到一些问题,需要及时处理以保证片剂的质量和稳定性。
首先,常见的问题之一是片剂的压制不良。
这可能是由于颗粒的大小和形状不均匀,或者是由于药物成分没有充分混合导致的。
为了解决这个问题,可以通过优化颗粒的制备过程,确保颗粒的均匀性。
此外,在混合药物成分时,可以使用合适的混合设备,并控制好混合的时间和速度,以确保药物成分的均匀分布。
其次,片剂可能会出现分层现象,即药物成分在片剂中分布不均匀。
这可能是由于药物成分的溶解度不同,或者是由于片剂中的粘结剂不够均匀导致的。
为了解决这个问题,可以选择适当的粘结剂,并确保在制备过程中充分混合。
此外,可以考虑使用涂膜技术,将药物成分包裹在薄膜中,以避免分层现象的发生。
另外,片剂的溶解性也是一个需要注意的问题。
某些药物在水中的溶解性较差,可能会导致片剂在口腔中不能充分溶解,从而影响其吸收。
为了解决这个问题,可以选择适当的溶解助剂,并进行预溶解处理,以增加药物在水中的溶解度。
此外,片剂的稳定性也是一个需要关注的问题。
某些药物在制剂过程中可能会发生化学变化或降解,导致片剂的药效降低。
为了解决这个问题,可以选择合适的辅料,如抗氧化剂或稳定剂,来保护药物的稳定性。
此外,可以对片剂进行包衣处理,以增加其稳定性。
总之,片剂的生产过程中常见的问题包括压制不良、分层现象、溶解性较差和稳定性问题。
通过优化制剂工艺、选择合适的辅料和采取适当的措施,可以有效解决这些问题,确保片剂的质量和稳定性。
片剂生产中的问题和解决办法

片剂生产中的问题和解决办法研究和探讨压片过程中可能发生的问题,对于保证药品质量、提高生产工艺水平,革新操作技术具有重要意义。
本文根据压片学的理论结合实际中的体会,试丛生产要素诸方面(如颗粒的物理性状、压片机的机械条件及空气湿度等),对压片中易出现的问题做一综述。
1 颗粒的物理性状颗粒的物理性状与其所含药物原料的性状、所含水分、所用的赋形剂等有关。
而这些因素加上颗粒制成后的粒度比例分布,均可对压片工艺造成影响。
1.1药物原料的性状凡属立方系的晶体一般可直接压片。
而鳞片状、针状及球形晶体不易直接压片,应粉碎过80~100目筛后用。
否则压片中易产生裂片、松片、表面不光等现象。
当药物为有色物时,尤其要粉碎过筛后制粒,以免片剂表面产生斑点,致外观不合要求。
1.2颗粒中的水分适量的水分能增加脆碎粒子的塑性变形,减小弹性,有利于压片,硬度亦较好。
实践证明,维生素C片颗粒水分控制在1.5%~2%之间,则易压片,而水分减至1%以下时,易出现裂片、松片现象。
即使片剂成形,通过数片分装时,药片的30%会出现毛角、麻面、松散等现象。
相反,水分超过3%时,又易产生粘冲现象。
一般解决水分过量颗粒的办法是采用去湿机,必要时重新干燥。
对完全干燥或水分不足的颗粒可根据药物本身的性质,采取自然吸湿或酌喷适宜浓度的乙醇,静置或密闭吸湿5h左右过筛后压片。
如对含结晶水的药物颗粒,结晶水失去过多时出现的裂片、松片、崩解迟缓等情况,可采用此法解决。
但黄连素颗粒,由于其药物粘性大,喷洒吸潮则易黏结成块状,坚硬不易均匀,会造成片重不稳及压片机受损等问题。
遇此情况,以自然吸湿或重新颗粒为好。
1.3颗粒所用的赋形剂压片过程中出现裂片、松片、边角毛缺等现象,多因黏合剂选用不当或用量不足所致。
当药物为疏松性或纤维性时更为明显。
对压出的片子出现崩解迟缓的情况时,除了其他因素外,要考虑黏合剂的浓度、用量是否过大。
临时解决措施为增加崩解剂的用量和减少压片机的压力。
片剂强度不合格的主要原因和解决方法

片剂强度不合格的主要原因和解决方法片剂是一种常见的药品剂型,但是有时候会出现片剂强度不合格的情况,主要原因有以下几点:
1. 原材料质量不过关。
片剂制备过程中,需要使用多种原材料,如药品原料、填充剂、分散剂等。
如果这些原材料的质量不过关,可能会导致片剂的强度不足。
2. 制备过程控制不当。
片剂制备需要控制压片力、压片时间、压片速度等多个参数,如果这些参数控制不当,可能会导致片剂强度不合格。
3. 设备故障或磨损。
片剂制备设备需要定期维护和检修,如果设备出现故障或者磨损,可能会导致片剂强度不合格。
为了解决片剂强度不合格的问题,可以采取以下措施:
1. 选用优质原材料。
片剂制备需要使用多种原材料,为了确保片剂质量,应该选择优质的原材料。
2. 加强制备过程控制。
片剂制备需要控制多个参数,为了确保片剂强度合格,应该加强制备过程的控制,严格按照规定的参数进行操作。
3. 定期维护和检修设备。
片剂制备设备需要定期维护和检修,以确保设备正常运转,不影响片剂质量。
综上所述,片剂强度不合格的原因主要包括原材料质量、制备过程控制和设备故障等多个方面,针对这些问题,需要采取相应的措施解决,确保片剂质量符合要求。
片剂的崩解时限不合格的主要原因和解决方法

片剂的崩解时限不合格的主要原因和解决方法下载提示:该文档是本店铺精心编制而成的,希望大家下载后,能够帮助大家解决实际问题。
文档下载后可定制修改,请根据实际需要进行调整和使用,谢谢!本店铺为大家提供各种类型的实用资料,如教育随笔、日记赏析、句子摘抄、古诗大全、经典美文、话题作文、工作总结、词语解析、文案摘录、其他资料等等,想了解不同资料格式和写法,敬请关注!Download tips: This document is carefully compiled by this editor. I hope that after you download it, it can help you solve practical problems. The document can be customized and modified after downloading, please adjust and use it according to actual needs, thank you! In addition, this shop provides you with various types of practical materials, such as educational essays, diary appreciation, sentence excerpts, ancient poems, classic articles, topic composition, work summary, word parsing, copy excerpts, other materials and so on, want to know different data formats and writing methods, please pay attention!一、主要原因1. 药品成分选择不当。
西药片剂生产过程中常见质量问题和解决方法

二、 结束语
据药物 自身的特 性来选择适合的黏合剂, 同时 , 还需要针对黏合剂的具体使 用量进行研究, 之后 , 对药物片剂压制过程 中所应当采取 的适合含水量状态 进行匹配, 确保 含水量的适宜性。只有通过 以上方式, 才 能够使得西药片剂 不至于在生产的过程 中便 出现碎裂的现象 。 2当药片片剂在受到一定程度 的振动或者是放置方法不 当,其片剂从 中间直接 断裂或者 是从项部裂开, 前一种被称之为腰裂 , 而后一种被称之为 顶裂。具体导致这一现象出现的原因和解决方案有以下几个方面: ( 1 ) 药物 本身弹性较 强、 纤维性药物或因含油类成分较多。 可加入糖粉 以减少纤维弹 性, 加 强黏合作用或增加油类 药物 的吸收剂, 充分混匀后压片。 ( 2 ) 黏合剂或
( 1 ) 原辅料的可压性, 可压 性强的原辅料被压缩 时易发 生塑性 变形, 片 剂的孔隙率及孔 隙径R皆较小,因而水分透入的数量和距离L 都 比较小, 片 剂的崩解较慢 。 实验证明, 在某些片剂中加 入淀粉 , 往往可增 大其孔隙率, 使 片剂的吸水性显著增强, 有利于片剂 的快速崩解。 但不能 由此推 断出淀粉越 多越好 的结论, 因为淀粉过多, 则可压性差 , 片剂难以成型。 ( 2 ) 颗粒 的硬 度, 颗粒 ( 或物料) 的硬度较小时, 易因受压而破碎, 所 以压成 的片剂孔 隙和 孔隙径R皆较小, 因而水分透入的数量 和距离L 也都 比较小, 片剂崩解亦慢 , 反之剐崩解较快。
片剂生产过程中常见质量问题和解决方法

工 程 技 术2008 NO.18Science and Technology Innovation Herald1 溶出超限片剂在规定的时间内未能溶出规定的药物,即为溶出超限或称为溶出度不合格。
片剂口服后,经过崩解、溶出、吸收产生药效,其中任何一个环节发生问题都将影响药的实际疗效。
未崩解的完整片剂的表面积很小,所以溶出速度慢。
崩解后所形成的小颗粒很多,表面积大幅度增加,溶出过程也随之增至最大,药物的溶出速度也最快,所以,能够使崩解加快的因素,一般也能加快溶出。
但是,也有不少药物的片剂虽可迅速崩解,而药物溶出却很慢,因此崩度合格并不一定能保证药物快速而完全的溶出,也就不能保证具有可靠的疗效。
对于许多难溶性药物来说,这种溶出加快的幅度不会很大,尚需采取一些其他的方法来改善溶出。
原因分析及解决方法。
1.1 研磨混合物疏水性药物单独粉碎时,随着粒径的减小,表面自由能增大,粒子易发生重新聚集的现象,粉碎的实际效率不高。
与此同时,这种疏水性的药物粒径减小、比表面积增大,会使片剂的疏水性增强,不利于片剂的崩解和溶出。
如果将这种疏水性的药与大量的水溶性辅料共同研磨粉碎制成混合物,则药物与辅料的粒径都可以降低到很小。
又由于辅料的量多,所以在细小的药物粒子周围吸附着大量水溶性辅料的粒子,这样就可以防止细小药物粒子的相互聚集,使其稳定地存在于混合物中。
当水溶性辅料溶解时,细小的药物粒子便直接暴露于溶出介质中,所以溶解(出)速度大大加快。
例如,将疏水性的地高辛、氢化可的松等药物与20倍的乳糖球磨混合后干法制粒压片,溶出度大大加快。
1.2 制成固体分散物将难溶性药物制成固体分散物是改善溶出速度的有效方法,例如,用1∶9的吲哚美辛与PEG6000制成的固体分散物粉碎后,加入适宜辅料压片,其溶出度呆得到很大的改善。
1.3 载体吸附将难溶性药物溶于能与小混溶的无毒溶剂(如PEG400)中,然后用硅胶一类多孔性的载体将其吸附,最后制成片剂。
影响片剂质量的主要原因及解决方法
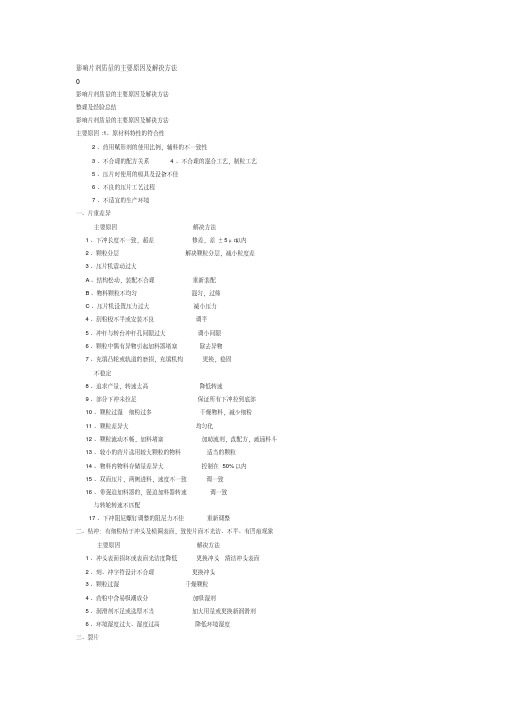
影响片剂质量的主要原因及解决方法影响片剂质量的主要原因及解决方法整理及经验总结影响片剂质量的主要原因及解决方法主要原因:1、原材料特性的符合性2、药用赋形剂的使用比例,辅料的不一致性3、不合理的配方关系4、不合理的混合工艺,制粒工艺5、压片时使用的模具及设备不佳6、不良的压片工艺过程7、不适宜的生产环境一、片重差异主要原因解决方法1、下冲长度不一致,超差修差,差±5μm以内2、颗粒分层解决颗粒分层,减小粒度差3、压片机震动过大A、结构松动,装配不合理重新装配B、物料颗粒不均匀混匀,过筛C、压片机设置压力过大减小压力4、刮粉板不平或安装不良调平5、冲杆与转台冲杆孔间隙过大调小间隙6、颗粒中偶有异物引起加料器堵塞除去异物7、充填凸轮或轨道的磨损,充填机构更换,稳固不稳定8、追求产量,转速太高降低转速9、部分下冲未拉足保证所有下冲拉到底部10、颗粒过湿细粉过多干燥物料,减少细粉11、颗粒差异大均匀化12、颗粒流动不畅,加料堵塞加助流剂,改配方,疏通料斗13、较小的药片选用较大颗粒的物料适当的颗粒14、物料内物料存储量差异大控制在50%以内15、双面压片,两侧进料,速度不一致调一致16、带强迫加料器的,强迫加料器转速调一致与转轮转速不匹配17、下冲阻尼螺钉调整的阻尼力不佳重新调整二、粘冲:有细粉粘于冲头及模圈表面,致使片面不光洁、不平、有凹痕现象主要原因解决方法1、冲头表面损坏或表面光洁度降低更换冲头清洁冲头表面2、刻、冲字符设计不合理更换冲头3、颗粒过湿干燥颗粒4、药粉中含易吸潮成分加吸湿剂5、润滑剂不足或选型不当加大用量或更换新润滑剂6、环境湿度过大、湿度过高降低环境湿度三、裂片主要原因解决方法1、压片时有空气存在于药片当中调整压力、减慢车速、增加预压时间或用有预压的工艺2、冲模磨损严重更换冲模3、黏结剂选型不当或不足更换黏结剂或加量4、颗粒含水量过低增加含水量5、颗粒过细或过粗调整颗粒粒度6、颗粒中油类成分较多加吸油剂7、模具间隙太小、不能顺利排气更换模具四、松片主要原因解决方法1、压力不够增加压力2、受压时间太少、转速快延长受压时间、增加预压、减低转速3、冲头长短不齐调整冲头4、活络冲冲头发生松动进行紧固5、下冲杆掉冲紧固6、黏结剂选型不当或太少更换黏合剂或加量7、颗粒中润滑剂比例不当调节比例8、颗粒太干燥增加颗粒水分9、物料粉碎粒度不够、纤维性或高弹性粉碎粒度过100目筛、加强黏合剂、药物或油类成分多,混合不均吸油剂10、药片压制后,置空气中过久,受潮缩短放置时间五、变色及斑点主要原因解决方法1、颗粒受油脂或其他杂质污染杜绝油脂及杂质污染2、颗粒过硬或含糖品种及有色降低颗粒硬度、有色片剂用片剂颗粒易出现乙醇为润滑剂制粒3、颗粒过大或过小颗粒适宜4、冲模型面出现锈斑清除锈斑5、加料器与转台表面摩擦有金属细粉调节加料器高度随颗粒进入模孔6、冲头与模圈内壁发生摩擦调节模圈致有色金属粉末进入颗粒六、崩解迟缓主要原因解决方法1、黏结剂粘性太强或用量过多,更换黏结剂或降低用量颗粒过硬过粗2、崩解剂选型不当、用量不足更换崩解剂或加量疏水性润滑剂太多降低疏水性润滑剂3、压力过大、片子过硬减低压力七、刻字或线条不清晰主要原因解决方法1、冲模的字符设计、布置不合理更换字符2、冲模型面磨损或破坏更换冲模3、冲模尺寸过大或不够更换冲模4、预压力过大降低预压力粉末直接压片粉末直接压片的应用方法及其注意事项由于粉末直接压片具有较明显的优点,如工艺过程比较简单,不必制粒、干燥,产品崩解或溶出快,成品质量稳定,在国外约有40%的片剂品种已采用这种工艺生产。
影响片剂质量的主要原因及解决方法

影响片剂质量的主要原因及解决方法前言制药行业重要的生产方式之一是片剂制造。
好的片剂质量为患者提供了更好的治疗体验,而劣质片剂的产生则会导致严重后果。
因此,理解影响片剂质量的原因,研究解决方法非常重要。
本文将介绍影响片剂质量的主要原因及解决方法。
影响片剂质量的主要原因原料质量制药过程中,原料的质量直接影响着片剂的质量。
原料应该来自可靠供应商,有严格的质量控制体系,并符合药典标准。
生产设备生产设备的操作和维护非常重要。
如果设备不干净或磨损过多,易产生异物或者粉尘,严重影响片剂的质量。
工艺控制片剂制造过程中的工艺控制也很重要。
在每一个生产过程都必须有恰当的温度、湿度和压力,否则会影响片剂的质量。
人为失误工人的手动操作和检查技能是制造质量不可或缺的部分。
但如果工人们对工作重视不够,或者操作不当,会导致产生不符合标准的片剂。
解决方法一流的供应商选择公司应该寻求一流的原料供应商,并建立紧密的业务合作关系。
同时应该有严格的供应商评估流程,以保证原料符合质量和性能要求,并定期进行重要原料的检测。
设备保养与清洁在生产设备上,保持设备干净整洁并进行定期保养,是维护生产设备的重要手段。
同时,应设定一套维护计划和清洁方案。
可以考虑使用压缩空气和真空吸尘器等设备,对重要设备进行清洁。
工艺流程优化片剂制造过程中的细节和规范应被加强,以完善工艺流程。
同时,可以使用一些先进的技术和设备来优化工艺流程,如:粉碎设备、混合器、等离子喷雾干燥机等,从而达到优化和改进片剂质量的效果。
培训及管理管理人员和员工应该经过必要的培训和技能认证,以确保在制造过程中正确地执行工艺规范和操作标准。
同时,经常性地开展生产流程的管理,跟踪控制质量风险。
维持片剂质量是制药公司的最高任务。
为了确保产生合格的片剂,从原料质量、生产设备、工艺控制、技能认证和管理等多个方面着手,以最大程度地保证产品的重要性能参数和特性水平达标。
固体片剂“黑点”产生的原因分析及预防措施

固体片剂“黑点”产生的原因分析及预防措施固体片剂在生产过程中出现“黑点”是一个常见的问题,可能会影响产品质量和市场形象。
因此,对于这个问题的分析和预防措施是非常重要的。
首先,我们来分析“黑点”产生的原因。
主要原因如下:1.原材料问题:固体片剂生产过程中使用的原材料可能会受到污染或质量问题,例如颗粒物、杂质或化学物质。
这些污染物或质量问题可能会导致“黑点”的产生。
2.混合不均匀:固体片剂的生产过程中需要将各种原材料混合均匀。
如果混合过程不够均匀或时间不足,可能会导致部分原材料没有完全溶解或分散,形成“黑点”。
3.热处理问题:在片剂生产的过程中,热处理是一个必要的步骤。
如果温度不适宜或时间不足,可能会导致一些成分或原材料氧化或分解,产生“黑点”。
4.机械设备问题:生产过程中使用的设备,例如混合机、造粒机、压片机等,如果设备本身存在问题,例如表面腐蚀、粉尘积聚等,可能会导致“黑点”的产生。
针对这些原因,我们可以采取以下预防措施:1.优化原材料质量:严格控制原材料的采购渠道和质量标准,确保原材料没有污染和质量问题。
2.加强质量控制:建立严格的质量控制标准和流程,例如进行原材料的质量检验、加强混合过程的监控和调整等。
3.优化热处理条件:通过实验和工艺优化,确定最佳的热处理温度和时间,避免原材料的氧化和分解。
4.定期维护和检修设备:确保设备表面没有腐蚀和粉尘积聚,减少机械设备对产品质量的影响。
5.完善清洁制度:加强生产场所的清洁工作,减少杂质和颗粒物的污染。
另外,对于已经出现“黑点”的固体片剂,可以采取以下处理方法:1.分析原因:通过化学分析和检测,确定“黑点”产生的具体原因,找出问题所在。
2.改善工艺:根据问题的原因进行工艺调整和优化,避免类似问题再次发生。
3.控制质量:加强对“黑点”产品的质量控制,剔除不合格产品,确保优质产品出厂。
总之,固体片剂“黑点”的产生是一个影响产品质量和市场形象的重要问题。
通过分析产生原因并采取预防措施,可以减少“黑点”的发生,同时对已经出现的问题进行分析和处理,以提高产品质量和企业形象。
片剂质量控制要点
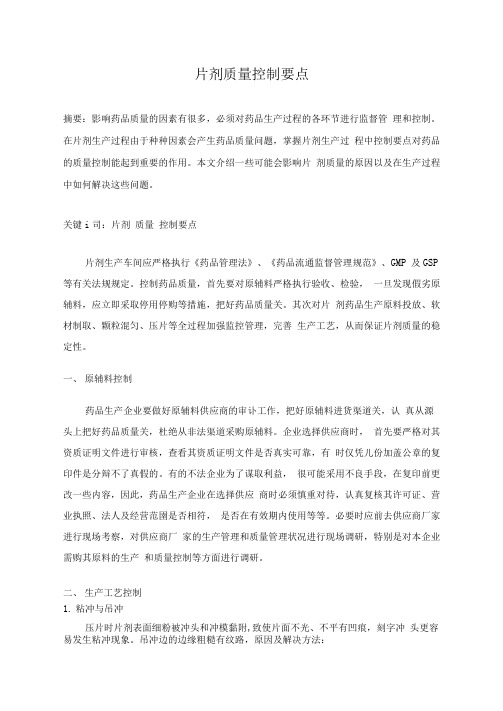
片剂质量控制要点摘要:影响药品质量的因素有很多,必须对药品生产过程的各环节进行监督管理和控制。
在片剂生产过程由于种种因素会产生药品质量问题,掌握片剂生产过程中控制要点对药品的质量控制能起到重要的作用。
本文介绍一些可能会影响片剂质量的原因以及在生产过程中如何解决这些问题。
关键i司:片剂质量控制要点片剂生产车间应严格执行《药品管理法》、《药品流通监督管理规范》、GMP 及GSP 等有关法规规定。
控制药品质量,首先要对原辅料严格执行验收、检验,一旦发现假劣原辅料,应立即采取停用停购等措施,把好药品质量关。
其次对片剂药品生产原料投放、软材制取、颗粒混匀、压片等全过程加强监控管理,完善生产工艺,从而保证片剂质量的稳定性。
一、原辅料控制药品生产企业要做好原辅料供应商的审讣工作,把好原辅料进货渠道关,认真从源头上把好药品质量关,杜绝从非法渠道采购原辅料。
企业选择供应商时,首先要严格对其资质证明文件进行审核,查看其资质证明文件是否真实可靠,有时仅凭儿份加盖公章的复印件是分辩不了真假的。
有的不法企业为了谋取利益,很可能采用不良手段,在复印前更改一些内容,因此,药品生产企业在选择供应商时必须慎重对待,认真复核其许可证、营业执照、法人及经营范圉是否相符,是否在有效期内使用等等。
必要时应前去供应商厂家进行现场考察,对供应商厂家的生产管理和质量管理状况进行现场调研,特别是对本企业需购其原料的生产和质量控制等方面进行调研。
二、生产工艺控制1.粘冲与吊冲压片时片剂表面细粉被冲头和冲模黏附,致使片面不光、不平有凹痕,刻字冲头更容易发生粘冲现象。
吊冲边的边缘粗糙有纹路,原因及解决方法:(1)颗粒含水量过多、含有引湿性易受潮的药物、操作室温度与湿度过高易产生粘冲。
应注意适当干燥、降低操作室温度、湿度,避免引湿性药物受潮等。
(2)润滑剂用量过少或混合不匀、细粉过多。
应适当增加润滑剂用量或充分混合,解决粘冲问题。
(3)冲头表面不干净,有防锈油或润滑油、新冲模表面粗糙或刻字太深有棱角。
松片、裂片、崩解延缓等质量问题的解决办法

生产过程中常见问题和处理方法一、质量问题制剂生产过程由于种种原因造成制剂的质量不合格,尤其是在片剂生产中,造成片剂质量问题的因素更多。
现仅对片剂、胶囊剂及注射剂生产中可能产生质量问题的原因及解决方法作介绍。
(一)片剂生产过程中可能发生问题的分析及解决方法1. 松片片剂压成后,硬度不够,表面有麻孔,用手指轻轻加压即碎裂,原因分析及解决方法:①药物粉碎细度不够、纤维性或富有弹性药物或油类成分含量较多而混合不均匀。
可将药物粉碎过100目筛、选用黏性较强的黏合剂、适当增加压片机的压力、增加油类药物吸收剂充分混匀等方法加以克服。
②黏合剂或润湿剂用量不足或选择不当,使颗粒质地疏松或颗粒粗细分布不匀,粗粒与细粒分层。
可选用适当黏合剂或增加用量、改进制粒工艺、多搅拌软材、混均颗粒等方法加以克服。
③颗粒含水量太少,过分干燥的颗粒具有较大的弹性、含有结晶水的药物在颗粒干燥过程中失去较多的结晶水,使颗粒松脆,容易松裂片。
故在制粒时,按不同品种应控制颗粒的含水量。
如制成的颗粒太干时,可喷入适量稀乙醇(50%—60%),混匀后压片。
④药物本身的性质。
密度大压出的片剂虽有一定的硬度,但经不起碰撞和震摇。
如次硝酸铋片、苏打片等往往易产生松片现象;密度小,流动性差,可压性差,重新制粒。
⑤颗粒的流动性差,填入模孔的颗粒不均匀。
⑥有较大块或颗粒、碎片堵塞刮粒器及下料口,影响填充量。
⑦压片机械的因素。
压力过小,多冲压片机冲头长短不齐,车速过快或加料斗中颗粒时多时少。
可调节压力、检查冲模是否配套完整、调整车速、勤加颗粒使料斗内保持一定的存量等方法克服。
2.裂片片剂受到震动或经放置时,有从腰间裂开的称为腰裂;从顶部裂开的称为顶裂,腰裂和顶裂总称为裂片,原因分析及解决方法:①药物本身弹性较强、纤维性药物或因含油类成分较多。
可加入糖粉以减少纤维弹性,加强黏合作用或增加油类药物的吸收剂,充分混匀后压片。
②黏合剂或润湿剂不当或用量不够,颗粒在压片时粘着力差。
片剂制备中可能发生的问题及原因

片剂制备中可能发生的问题及原因在片剂制备过程中,可能会遇到以下问题:
1.片剂断裂或碎裂:这可能是由于制备过程中压力不足、配方中活性成分含量过高或过低、填充物选择不当等原因引起的。
解决方法可能包括增加制备时的压力、调整配方中的成分含量或更换合适的填充物。
2.片剂重量变化:片剂的重量可能会因为填充物的不均匀分布、设备问题或操作错误而发生变化。
这可能需要检查设备设置、操作技术以及填充物的质量控制,确保充填过程均匀且准确。
3.片剂不容易分散或释放:片剂在服用后应该能够迅速分散或释放活性成分,但如果发现片剂难以分散或释放,可能是由于配方中的粘结剂或包衣材料不适合、颗粒大小分布不均匀等原因。
需要重新评估配方和制备工艺,选择适当的粘结剂和包衣材料,确保片剂的性能符合预期。
4.片剂稳定性问题:片剂在制备过程中或储存过程中可能会遇到稳定性问题,如溶解度降低、色素变化、氧化等。
这可能是由于原材料质量不稳定、制备过程中的温度、湿度或光照条件不当等原因引起的。
需要仔细评估原材料的质量,并采取适当的储存条件和制备工艺来确保片剂的稳定性。
5.制备工艺不一致:片剂的制备过程可能会受到温度、湿度、压力等因素的影响,如果这些因素没有得到有效控制,可能会导致不一致的制备结果。
为了解决这个问题,需要确保在制备过程中对环境条件进行严格控制,并进行工艺优化和验证。
1/ 1。
片剂强度不合格的主要原因和解决方法
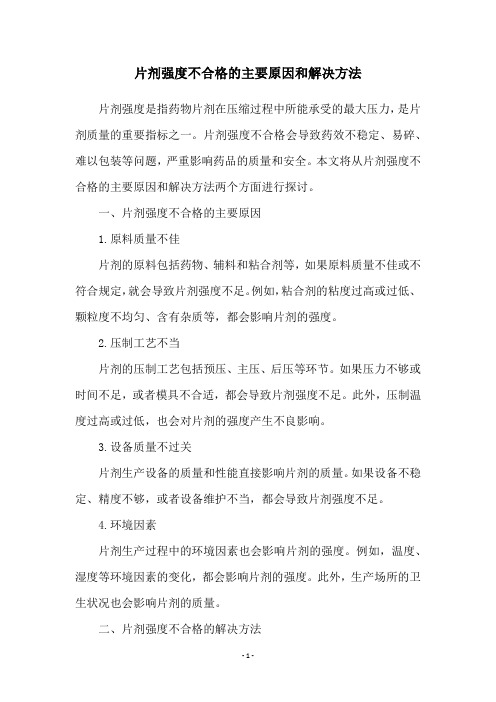
片剂强度不合格的主要原因和解决方法片剂强度是指药物片剂在压缩过程中所能承受的最大压力,是片剂质量的重要指标之一。
片剂强度不合格会导致药效不稳定、易碎、难以包装等问题,严重影响药品的质量和安全。
本文将从片剂强度不合格的主要原因和解决方法两个方面进行探讨。
一、片剂强度不合格的主要原因1.原料质量不佳片剂的原料包括药物、辅料和粘合剂等,如果原料质量不佳或不符合规定,就会导致片剂强度不足。
例如,粘合剂的粘度过高或过低、颗粒度不均匀、含有杂质等,都会影响片剂的强度。
2.压制工艺不当片剂的压制工艺包括预压、主压、后压等环节。
如果压力不够或时间不足,或者模具不合适,都会导致片剂强度不足。
此外,压制温度过高或过低,也会对片剂的强度产生不良影响。
3.设备质量不过关片剂生产设备的质量和性能直接影响片剂的质量。
如果设备不稳定、精度不够,或者设备维护不当,都会导致片剂强度不足。
4.环境因素片剂生产过程中的环境因素也会影响片剂的强度。
例如,温度、湿度等环境因素的变化,都会影响片剂的强度。
此外,生产场所的卫生状况也会影响片剂的质量。
二、片剂强度不合格的解决方法1.优化原料质量优化原料质量是解决片剂强度不合格的关键。
在选择原料时,应注重原料的质量和来源,并进行严格的检验和质量控制。
此外,应加强对原料的储存和保管,避免原料受潮、受污染等情况。
2.优化压制工艺优化压制工艺也是解决片剂强度不合格的重要手段。
在压制过程中,应根据原料的性质和特点,选择合适的压制模具和参数,并加强对压制过程的监控和调整,确保片剂的强度符合要求。
3.升级设备质量升级设备质量是解决片剂强度不合格的另一重要手段。
在选择设备时,应注重设备的质量和性能,并进行充分的测试和验证。
此外,应加强设备的维护和保养,保证设备的正常运转和性能稳定。
4.改善生产环境改善生产环境也是解决片剂强度不合格的重要手段。
在生产场所中,应加强卫生管理,保证生产环境的清洁和卫生。
此外,应控制生产场所的温度、湿度等环境因素,确保生产环境的稳定和适宜。
压片过程中片剂重量差异不合格的原因

压片过程中片剂重量差异不合格的原因引言片剂作为一种常见的药物剂型,被广泛应用于医疗领域。
在片剂制备过程中,片剂重量的合格性是一个重要的指标。
然而,我们常常会遇到压片过程中出现片剂重量差异不合格的情况。
本文将从多个角度分析压片过程中片剂重量差异不合格的原因,并提出相应的解决方案。
原因一:原料配比不准确片剂的重量差异不合格的一个常见原因是原料配比不准确。
在制备片剂时,原料的配比是十分关键的,每种原料的用量都需要精确控制。
如果原料配比不准确,不同批次的片剂重量就会存在差异。
为了解决这个问题,制药厂家应该加强原料配比的控制。
在配料过程中,使用精确的称量设备,确保原料的用量准确无误。
同时,应该建立严格的质量控制系统,对原料的配比进行严格监测和记录,及时发现并纠正配比偏差。
原因二:压片机性能问题另一个导致片剂重量差异的原因是压片机性能问题。
压片机是制备片剂过程中的核心设备,若其性能存在问题,就会直接影响片剂的质量,包括重量的一致性。
压片机性能问题可能包括以下几个方面:1.压片机良好的调整和维护压片机在使用之前需要进行良好的调整和维护,确保其各项参数的准确性和稳定性。
若参数调整不当或者设备运行不稳定,就会导致片剂重量的不一致。
为解决这个问题,制药厂家应根据良好的操作规程,对压片机进行适当的调整和维护。
同时,定期进行设备的检查和维修,确保设备运行的稳定性和可靠性。
2.压片机压力控制压片机的压力是影响片剂重量的关键因素之一。
若压力控制不准确,就会导致不同片剂的压实程度不一致,从而造成重量差异。
为解决这个问题,制药厂家应充分了解所使用的压片机的性能特点,并确保压力控制系统的可靠性和准确性。
在片剂制备过程中,应根据不同药物的特性和配方要求,合理选择和调整压力参数,达到一致的压实效果。
原因三:制造过程操作不当除了原料配比和压片机性能问题外,制造过程中的操作不当也是导致片剂重量差异的原因之一。
操作不当可能包括以下几个方面:1.混合均匀性不足在片剂制备过程中,应将各种原料充分混合均匀,以确保药物成分的均一性和稳定性。
- 1、下载文档前请自行甄别文档内容的完整性,平台不提供额外的编辑、内容补充、找答案等附加服务。
- 2、"仅部分预览"的文档,不可在线预览部分如存在完整性等问题,可反馈申请退款(可完整预览的文档不适用该条件!)。
- 3、如文档侵犯您的权益,请联系客服反馈,我们会尽快为您处理(人工客服工作时间:9:00-18:30)。
影响片剂质量的主要原因及解决方法影响片剂质量的主要原因及解决方法整理及经验总结影响片剂质量的主要原因及解决方法主要原因:1、原材料特性的符合性2、药用赋形剂的使用比例,辅料的不一致性3、不合理的配方关系4、不合理的混合工艺,制粒工艺5、压片时使用的模具及设备不佳6、不良的压片工艺过程7、不适宜的生产环境一、片重差异主要原因解决方法1、下冲长度不一致,超差修差,差±5μm以内2、颗粒分层解决颗粒分层,减小粒度差3、压片机震动过大A、结构松动,装配不合理重新装配B、物料颗粒不均匀混匀,过筛C、压片机设置压力过大减小压力4、刮粉板不平或安装不良调平5、冲杆与转台冲杆孔间隙过大调小间隙6、颗粒中偶有异物引起加料器堵塞除去异物7、充填凸轮或轨道的磨损,充填机构更换,稳固不稳定8、追求产量,转速太高降低转速9、部分下冲未拉足保证所有下冲拉到底部10、颗粒过湿细粉过多干燥物料,减少细粉11、颗粒差异大均匀化12、颗粒流动不畅,加料堵塞加助流剂,改配方,疏通料斗13、较小的药片选用较大颗粒的物料适当的颗粒14、物料内物料存储量差异大控制在50%以内15、双面压片,两侧进料,速度不一致调一致16、带强迫加料器的,强迫加料器转速调一致与转轮转速不匹配17、下冲阻尼螺钉调整的阻尼力不佳重新调整二、粘冲:有细粉粘于冲头及模圈表面,致使片面不光洁、不平、有凹痕现象主要原因解决方法1、冲头表面损坏或表面光洁度降低更换冲头清洁冲头表面2、刻、冲字符设计不合理更换冲头3、颗粒过湿干燥颗粒4、药粉中含易吸潮成分加吸湿剂5、润滑剂不足或选型不当加大用量或更换新润滑剂6、环境湿度过大、湿度过高降低环境湿度三、裂片主要原因解决方法1、压片时有空气存在于药片当中调整压力、减慢车速、增加预压时间或用有预压的工艺2、冲模磨损严重更换冲模3、黏结剂选型不当或不足更换黏结剂或加量4、颗粒含水量过低增加含水量5、颗粒过细或过粗调整颗粒粒度6、颗粒中油类成分较多加吸油剂7、模具间隙太小、不能顺利排气更换模具四、松片主要原因解决方法1、压力不够增加压力2、受压时间太少、转速快延长受压时间、增加预压、减低转速3、冲头长短不齐调整冲头4、活络冲冲头发生松动进行紧固5、下冲杆掉冲紧固6、黏结剂选型不当或太少更换黏合剂或加量7、颗粒中润滑剂比例不当调节比例8、颗粒太干燥增加颗粒水分9、物料粉碎粒度不够、纤维性或高弹性粉碎粒度过100目筛、加强黏合剂、药物或油类成分多,混合不均吸油剂10、药片压制后,置空气中过久,受潮缩短放置时间五、变色及斑点主要原因解决方法1、颗粒受油脂或其他杂质污染杜绝油脂及杂质污染2、颗粒过硬或含糖品种及有色降低颗粒硬度、有色片剂用片剂颗粒易出现乙醇为润滑剂制粒3、颗粒过大或过小颗粒适宜4、冲模型面出现锈斑清除锈斑5、加料器与转台表面摩擦有金属细粉调节加料器高度随颗粒进入模孔6、冲头与模圈内壁发生摩擦调节模圈致有色金属粉末进入颗粒六、崩解迟缓主要原因解决方法1、黏结剂粘性太强或用量过多,更换黏结剂或降低用量颗粒过硬过粗2、崩解剂选型不当、用量不足更换崩解剂或加量疏水性润滑剂太多降低疏水性润滑剂3、压力过大、片子过硬减低压力七、刻字或线条不清晰主要原因解决方法1、冲模的字符设计、布置不合理更换字符2、冲模型面磨损或破坏更换冲模3、冲模尺寸过大或不够更换冲模4、预压力过大降低预压力粉末直接压片粉末直接压片的应用方法及其注意事项由于粉末直接压片具有较明显的优点,如工艺过程比较简单,不必制粒、干燥,产品崩解或溶出快,成品质量稳定,在国外约有40%的片剂品种已采用这种工艺生产。
一、应用1、用于遇湿、热易变色、分解的药物许多药物对湿、热不稳定,如头孢克肟遇湿、热易发生变色,效价降低;维生素C具有还原性,易被空气氧化,以致颜色变黄、含量下降,特别是受水分、温度、金属离子等影响时,更易造成药品变质;氨茶碱遇湿、热均易分解、变色,放出强烈氨臭;利福平对湿、热也不稳定,含量下降,溶出度不合格;维生素B1、B2、B6等对湿、热、金属离子均不稳定。
这些药物若采用常规湿法制粒,因在生产过程中,药物与黏合剂中的溶剂接触,并经高温干燥,必会对产品质量有影响。
而采用粉末直接压片工艺,所制得的片剂片面光滑,无裂片和粘冲,片重差异小,崩解时限短,经加速实验、留样观察,片剂各项质量指标均无变化。
2、用于酯类、酰胺类等易水解药物因盐酸甲氯芬酯极易水解,采用常规的湿法制粒工艺,因生产过程中加入黏合剂,含有水分,在干燥的高温条件下,药物分解加快,从而影响药品的质量,不仅降低了药物的含量,而且增加了降解产物,使疗效降低,副作用增加。
而采用粉末直接压片工艺生产,避免了与水的接触,同时可选用引湿性小的辅料,进一步保证药物在贮藏期间的稳定性。
3、用于溶解度较小或疏水性的药物溶解度小的药物的溶出度受其比表面积和药物成品表面性质的影响较大,通过药剂学方法,选用亲水性辅料,经粉末直接压片后,药品崩解后药物直接从粉末中释放出来,分散度增大,溶出加快,相对生物利用度提高。
4、用于低熔点及产生共熔的复方药物环扁桃酯的熔点为50℃~62℃,常规湿法制粒可造成药物熔化而影响质量;盐酸麻黄素和盐酸苯海拉明的复方制剂,湿法制粒干燥时两者可产生共熔,不易烘干。
而采用粉末直接压片工艺,可有效解决以上问题。
二、注意事项1、药物与辅料的性质要相近进行粉末直接压片时,药物与辅料的堆密度、粒度及粒度分布等物理性质要相近,以利于混合均匀,尤其是规格较小、需测定含量均匀度的药物,必须慎重选择各种辅料。
2、不溶性润滑剂须最后加入用于粉末直接压片的不溶性润滑剂一定要最后加入,即先将原料与其它辅料混合均匀后,再加入不溶性润滑剂,并且要控制好混合时间,否则会严重影响崩解或溶出。
另外,以预胶化淀粉、微晶纤维素等为辅料时,硬脂酸镁的用量如果较多且混合时间较长,片剂有软化现象,所以一般用量应在0.75%以下,而且要对混合时间、转速及强度进行验证。
3、混合后要进行含量测定与常规湿法制粒的生产工艺一样,进行粉末直接压片的各原辅料混合后要进行含量测定,以确保中间产品和成品的质量符合规定标准。
4、小试后须进行充分的试验放大一般情况下,用粉末直接压片工艺压制的不合格片剂不宜返工。
因为返工须将片剂重新粉碎,粉碎后物料的可压性会显着降低,以致不适于进行直接压片。
所以,从小试至大生产,必须进行中试,并经过充分的验证,且中试应采用与以后大生产相同类型的设备,以使确定的参数对大生产有指导作用。
5、微晶纤维素的使用片剂硬度和脆碎度不合格时,可以加入微晶纤维素,其用量可高达65%;还可以采用先压成大片,然后破碎成颗粒,再行压片的方法,可得到满意的结果。
6、及时处理压片中的异常情况在压片过程中,应按标准操作程序及时取样,观察片剂的外观及测定片重差异、硬度、脆碎度、崩解时间、片厚等质量指标,并观察设备运行情况,出现异常情况应及时报告并采取应急措施,详细记录异常现象和处理结果,进行详细的分析,以确保产品质量。
随着国外新型药用辅料的引入,国内药用辅料新品种的不断开发、上市,压片设备的不断更新、改进、完善,粉末直接压片法在国内的应用必将逐渐增加。
片剂制备中常用辅料介绍从总体上看,片剂是由两大类物质构成的,一类是发挥治疗作用的药物(即主药),另一类是没有生理活性的一些物质,它们所起的作用主要包括:填充作用、粘合作用、崩解作用和润滑作用,有时,还起到着色作用、矫味作用以及美观作用等,在药剂学中,通常将这些物质总称为辅料(Excipients 或Adjuvants)。
根据它们所起作用的不同,常将辅料分成四大类。
(一)稀释剂(Diluents)稀释剂(或称为填充剂,Fil1ers)的主要作用是用来填充片剂的重量或体积,从而便于压片;常用的填充剂有淀粉类、糖类、纤维素类和无机盐类等;由压片工艺、制剂设备等因素所决定,片剂的直径一般不能小于6mm、片重多在100mg以上,如果片剂中的主药只有几毫克或几十毫克时,不加入适当的填充剂,将无法制成片剂,因此,稀释剂在这里起到了较为重要的、增加体积助其成型的作用。
1.淀粉比较常用的是玉米淀粉,它的性质非常稳定,与大多数药物不起作用,价格也比较便宜,吸湿性小、外观色泽好,在实际生产中,常与可压性较好的糖粉、糊精混合使用,这是因为淀粉的可压性较差,若单独使用,会使压出的药片过于松散。
2.糖粉糖粉系指结晶性蔗糖经低温干燥粉碎后而成的白色粉末,其优点在于粘合力强,可用来增加片剂的硬度,并使片剂的表面光滑美观,其缺点在于吸湿性较强,长期贮存,会使片剂的硬度过大,崩解或溶出困难,除口含片或可溶性片剂外,一般不单独使用,常与糊精、淀粉配合使用。
3.糊精糊精是淀粉水解中间产物的总称,其化学式为(C6H10O5)n•XH2O,其水溶物约为80%,在冷水中溶解较慢,较易溶于热水,不溶于乙醇。
习惯上亦称其为为高糊(高粘度糊精),即具有较强的粘结性,使用不当会使片面出现麻点、水印或造成片剂崩解或溶出迟缓;同理,在含量测定时如果不充分粉碎提取,将会影响测定结果的准确性和重现性,所以,很少单独大量使用糊精作为填充剂,常与糖粉、淀粉配合使用。
4.乳糖乳糖是一种优良的片剂填充剂,由牛乳清中提取制得,在国外应用非常广泛,但因价格较贵,在国内应用的不多。
常用含有一分子水的结晶乳糖(即α-含水乳糖),无吸湿性,可压性好,性质稳定,与大多数药物不起化学反应,压成的药片光洁美观;由喷雾干燥法制得的乳糖为非结晶乳糖,其流动性、可压性良好,可供粉末直接压片使用。
5.可压性淀粉亦称为预胶化淀粉(Pregelatinized starch),是新型的药用辅料,英、美、日及中国药典皆已收载,我国于1988年研制成功,现已大量供应市场。
国产可压性淀粉是部分预胶化的产品(全预胶化淀粉又称为α-淀粉),与国外Colorcon公司的Starch RX1500相当。
本品是多功能辅料,可作填充剂,具有良好的流动性、可压性、自身润滑性和干粘合性,并有较好的崩解作用。
若用于粉末直接压片时,硬脂酸镁的用量不可超过0.5%,以免产生软化效应。
6.微晶纤维素微晶纤维素(Microcrystalline cellulose,MCC)是纤维素部分水解而制得的聚合度较小的结晶性纤维素,具有良好的可压性,有较强的结合力,压成的片剂有较大有硬度,可作为粉末直接压片的"干粘合剂"使用。
国外产品的商品名为Avicel,并根据粒径约不同有若干规格。
国产微晶纤维素已在国内得到广泛应用,但其质量有待于进一步提高,产品种类也有待于丰富。
另外,片剂中含20%微晶纤维素时崩解较好。
7.无机盐类主要是一些无机钙盐,如硫酸钙、磷酸氢钙及药用碳酸钙(由沉降法制得,又称为沉降碳酸钙)等。