过程能力指数案例分析
过程能力与过程能力指数

过程能力过程能力在管理状态的制程上,该过程具有达成品质的能力,称为过程能力。
正确地维持作业的条件或标准且在计数上、经济上良好且安定的制程上,量测产品的品质特性,通常以或有时仅以6 来表示。
过程能力指标(process capability indices ( 与 )):过程能力指标是一些简洁之数值,用来表示过程符合产品规格之能力。
指标之值可视为过程之潜在能力,亦即当过程平均值可调到规格中心或目标值时,过程符合规格之能力。
指标之值与指标类似,但将过程平均值纳入考虑。
过程能力分析(process capability analysis):在产品生产周期内统计技术可用来协助制造前之开发活动、过程变异性之数量化、过程变异性相对於产品规格之分析及协助降低过程内变异性。
这些工作一般称为过程能力分析(process capability analysis)。
过程能力的概念过程能力:所谓的过程能力,就是过程处于统计控制状态下,加工产品质量正常波动的经济幅度,通常同质量特性值分布的6倍标准偏差来表示,记为6σ.生产能力:指加工数量方面的能力。
过程能力决定于质量因素而与公差无关。
为什么要进行过程能力分析?之所以要进行过程能力分析,有两个主要原因:·我们需要知道过程度量所能够提供的基线在数量上的受控性;·由于我们的度量计划还相当“不成熟”,因此需要对过程度量基线进行评估,来决定是否对其进行改动以反映过程能力的改进情况。
根据过程能力的数量指标,我们可以相应地放宽或缩小基线的控制条件。
工序过程能力指该工序过程在5M1E正常的状态下,能稳定地生产合格品的实际加工能力。
过程能力取决于机器设备、材料、工艺、工艺装备的精度、工人的工作质量以及其他技术条件。
过程能力指数用Cp 、Cpk表示。
案例一:某公司某工序的关键指标?——拉力参数的控制图如下,我们进行如下过程能力的分析:Cpk= Min[ (USL- Mu)/3s, (Mu - LSL)/3s][1]过程能力的意义SPC的基准SPC的基准:就是统计控制状态或称稳态,过程能力即稳态下所能达到的最小变差。
过程能力指数计算例题
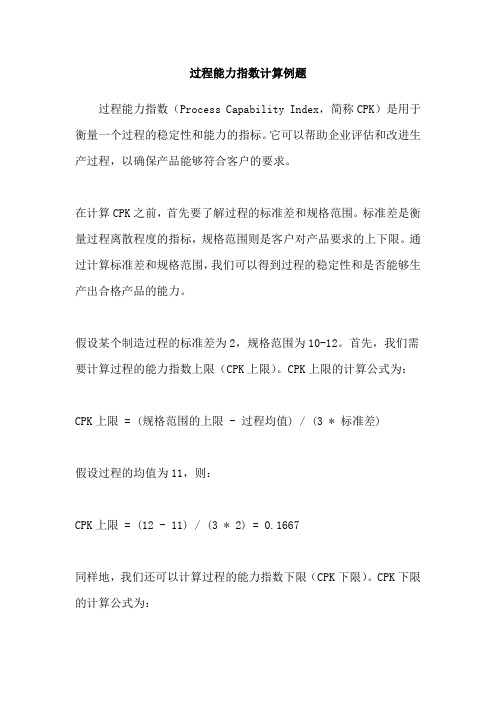
过程能力指数计算例题过程能力指数(Process Capability Index,简称CPK)是用于衡量一个过程的稳定性和能力的指标。
它可以帮助企业评估和改进生产过程,以确保产品能够符合客户的要求。
在计算CPK之前,首先要了解过程的标准差和规格范围。
标准差是衡量过程离散程度的指标,规格范围则是客户对产品要求的上下限。
通过计算标准差和规格范围,我们可以得到过程的稳定性和是否能够生产出合格产品的能力。
假设某个制造过程的标准差为2,规格范围为10-12。
首先,我们需要计算过程的能力指数上限(CPK上限)。
CPK上限的计算公式为:CPK上限 = (规格范围的上限 - 过程均值) / (3 * 标准差)假设过程的均值为11,则:CPK上限 = (12 - 11) / (3 * 2) = 0.1667同样地,我们还可以计算过程的能力指数下限(CPK下限)。
CPK下限的计算公式为:CPK下限 = (过程均值 - 规格范围的下限) / (3 * 标准差)假设过程的均值为11,则:CPK下限 = (11 - 10) / (3 * 2) = 0.1667通过比较CPK上限和CPK下限,我们可以判断过程的能力。
如果CPK 上限和CPK下限的值都大于等于1,说明该过程具有良好的能力,能够生产出合格的产品。
如果CPK上限和CPK下限的值都小于1,说明该过程的能力较差,需要进行改进和调整。
除了CPK指数之外,还有其他一些指标可以用来评估过程的能力,如过程能力指数(CPL和CPU)、过程潜在能力指数(CPM)等。
这些指标可以帮助企业全面了解和分析生产过程,并采取相应的措施来提高产品质量和生产效率。
总之,过程能力指数是评估一个过程的稳定性和能力的重要指标。
通过计算CPK指数,企业可以了解生产过程的能力,并采取相应的措施来改善和提高产品质量。
统计过程控制(SPC)案例分析(2004-03-24).

【案例1】 R X -控制图示例某手表厂为了提高手表的质量,应用排列图分析造成手表不合格品的各种原因,发现“停摆”占第一位。
为了解决停摆问题,再次应用排列图分析造成停摆事实的原因,结果发现主要是由于螺栓松动引发的螺栓脱落成的。
为此厂方决定应用控制图对装配作业中的螺栓扭矩进行过程控制。
分解:螺栓扭矩是一计量特性值,故可选用基于正态分布的计量控制图。
又由于本例是大量生产,不难取得数据,故决定选用灵敏度高的R X -图。
解:我们按照下列步骤建立R X -图步骤1:取预备数据,然后将数据合理分成25个子组,参见表1。
步骤2:计算各组样本的平均数i X 。
例如,第一组样本的平均值为:0.16451621661641741541=++++=X其余参见表1中第(7)栏。
步骤3:计算各组样本的极差i R 。
例如,第一组样本的极差为:{}{}20154174min max 111=-=-=j j X X R其余参见表1中第(8)栏。
表1: 【案例1】的数据与R X -图计算表i故:272.163=X ,280.14=R 。
步骤5:计算R 图的参数。
先计算R 图的参数。
从D 3、D 4系数表可知,当子组大小n =5,D 4=2.114,D 3=0,代入R 图的公式,得到: 188.30280.14114.24=⨯==R D UCL R280.14==R CL R ==R D LCL R 3—极差控制图:均值控制图:图1 【案例1】 的第一次R X -图参见图1。
可见现在R 图判稳。
故接着再建立X 图。
由于n =5,从系数A 2表知A 2=0.577,再将272.163=X ,280.14=R 代入X 图的公式,得到X 图:512.171280.14577.0272.1632≈⨯+=+=R A X UCL X 272.163==X CL X032.155280.14577.0272.1632≈⨯-=-=R A X LCL X因为第13组X 值为155.00小于X LCL ,故过程的均值失控。
《过程能力指数分析》PPT课件

0.833
精选PPT
19
过程能力指数和不合格率的关系
▪ (1)无偏移时Cp和不合格率p的关系
设Pu=PL分别为超出规范上、下界限的不合 格率 ,于是总的不合格率:
PP UPL2PL
P L P (X T L ) P (X T L ) P ( Z 3 C p ) ( 3 C p )
▪ 称为过程性能指数,过程实绩指数或 者长期过程能力指数。
▪ 它反映的是生产系统当前实际状况的 过程能力,而不是在稳态的条件下。
精选PPT
27
Pp与Ppk的比较
PpK m in ( PpU , PPL )
PpK (1 K ) Pp
PPK
ˆ S T ˆ L T
C pK
精选PPT
28
精选PPT
2
二、 过程能力和过程能力指数
▪ 过程能力
定义:过程在一定时间,处于控制状态(稳定状 态)下的实际加工能力(固有能力/质量保证能 力),也就是加工质量满足技术标准的能力。
量化:可用过程质量特性值的波动范围来衡量。
过程能力B=6σ。由于P(x∈μ±3σ)=99.73%, 故6σ近似于过程质量特性值的全部波动范围。 显然,B越小,过程能力就越强。
故
p2pL2 (3C p)
精选PPT
20
(2)有偏移过程能力指数Cpk、偏 移度K和不合格率p之间的关系
▪
当分布中心向规范上限TU 偏移时
PU
P[X
TU]
P[
X
TU ]
P[Z
TU
(T 2
)
]
T
T (1k)
P[Z 2 ]P[Z 2
]P[Z 3Cp(1K)]
SPC过程能力分析

控制图的构造要素
控制图通常包括中心线(CL)、上控制限(UCL) 和下控制限(LCL),通过这三个要素在图表上的 展示,来判断过程是否稳定。
控制图的分析与解读
判稳准则
控制图的分析首先关注过程是否 稳定,通常通过点是否超出控制 限、连续点的排列是否随机等方
面进行判断。
判异准则
当点超出控制限、连续7点位于 中心线同一侧等情况出现时,通
无法解决所有质量问题
SPC过程能力分析主要关注过程的稳定性和能力 ,但无法解决所有质量问题,如设备故障、原材 料缺陷等。
未来发展方向与趋势探讨
智能化分析
随着人工智能和机器学习技术的发展,未来SPC过程能力分析有望 实现智能化分析,自动识别生产过程中的异常和波动。
集成化管理
企业质量管理涉及的部门和流程众多,未来SPC过程能力分析有望 与其他质量管理方法集成,形成一体化的质量管理体系。
提升操作人员技能水平
加强操作人员技能培训和考核,确保操作人员熟练掌握生产技能和 操作规程,减小人为因素对生产过程的影响。
04
过程控制图分析与应用
Chapter
控制图的基本原理与构造
统计过程控制基础
控制图是统计过程控制(SPC)的核心工具,基于 数理统计原理,通过图形化展示过程中的波动,以 区分自然波动与异常波动。
解决方案
通过SPC分析发现,服务过程中存在员工服务态 度和技能水平不够稳定的问题。通过培训和考核 ,提高员工的服务意识和技能水平,最终实现服 务质量的提升和客户满意度的提高。
分析步骤
确定服务过程中的关键质量特性,收集数据并进 行统计分析,应用控制图和服务蓝图等工具进行 过程分析和改进。
经验教训
服务行业也可以应用SPC过程能力分析来提高服 务质量和效率,关键在于确定适当的关键质量特 性,并采取有针对性的改进措施。
「cpk」过程能力指数附案例分析和改善措施

「cpk」过程能力指数附案例分析和改善措施第一篇:「cpk」过程能力指数附案例分析和改善措施「CPK」过程能力指数,附案例分析和改善措施过程能力指数(Process capability index,CP或CPK),也译为工序能力指数、工艺能力指数、制程能力指数一、什么是过程能力指数过程能力指数也称工序能力指数,是指工序在一定时间里,处于控制状态(稳定状态)下的实际加工能力。
它是工序固有的能力,或者说它是工序保证质量的能力。
这里所指的工序,是指操作者、机器、原材料、工艺方法和生产环境等五个基本质量因素综合作用的过程,也就是产品质量的生产过程。
产品质量就是工序中的各个质量因素所起作用的综合表现。
对于任何生产过程,产品质量总是分散地存在着。
若工序能力越高,则产品质量特性值的分散就会越小;若工序能力越低,则产品质量特性值的分散就会越大。
那么,应当用一个什么样的量,来描述生产过程所造成的总分散呢?通常,都用6σ(即μ+3σ)来表示工序能力:工序能力是表示生产过程客观存在着分散的一个参数。
但是这个参数能否满足产品的技术要求,仅从它本身还难以看出。
因此,还需要另一个参数来反映工序能力满足产品技术要求(公差、规格等质量标准)的程度。
这个参数就叫做工序能力指数。
它是技术要求和工序能力的比值,即当分布中心与公差中心重合时,工序能力指数记为Cp。
当分布中心与公差中心有偏离时,工序能力指数记为Cpk。
运用工序能力指数,可以帮助我们掌握生产过程的质量水平。
二、过程能力指数的意义制程能力是过程性能的允许最大变化范围与过程的正常偏差的比值。
制程能力研究在於确认这些特性符合规格的程度,以保证制程成品不符规格的不良率在要求的水准之上,作为制程持续改善的依据。
当我们的产品通过了GageR&R的测试之后,我们即可开始Cpk值的测试。
CPK值越大表示品质越佳。
CPK=min ((X-LSL/3s),(USL-X/3s))三、过程能力指数的计算公式CPK= Min[(USL-Mu)/3s,(Mu|Ca|)Cpk是Ca及Cp两者的中和反应,Ca反应的是位置关系(集中趋势),Cp反应的是散布关系(离散趋势)八、过程能力指数的应用1 当选择制程站别Cpk来作管控时,应以成本做考量的首要因素,还有是其品质特性对后制程的影响度。
六西格玛计算公式案例解析

六西格玛计算公式案例解析六西格玛是一种统计学方法,旨在通过分析数据和过程以减少变异性,提高生产质量。
六西格玛计算公式是用于测量过程的性能和稳定性的数学工具。
本文将通过一个实际案例来解析六西格玛的计算公式和使用方法。
假设电子产品制造公司在生产过程中发现有关键组件的不良率过高,导致了不少产品需重新修复或者报废。
为了改进生产过程,公司决定使用六西格玛方法来分析并改善该过程的稳定性和质量。
首先,公司将收集实际数据,包括每个生产周期内所生产的产品数量以及其中不良品的数量。
假设公司连续进行了500个周期的生产,每个周期生产1000个产品。
在这500个周期内,共生产了500,000个产品。
第一步,我们需要计算不良品的比例。
假设在这500,000个产品中,有5,000个是不良品。
因此,不良率可以用下面的公式计算:不良率=不良品数量/总产量不良率=5,000/500,000不良率=0.01得到不良率为0.01,即每100个产品中有1个是不良品。
第二步,我们需要计算过程性能指数Cp。
过程性能指数是用于衡量生产过程是否符合规格要求的一个指标。
计算公式如下:Cp=(上限规格-下限规格)/(6*标准差)这里假设产品的规格要求范围为定为0.95到1.05、为了计算标准差,我们首先需要计算平均数。
平均数=总产量/总周期数平均数=500,000/500平均数=1,000然后,标准差可以通过以下公式计算:标准差 = sqrt((每个周期的不良品数量 - 平均数的平方) / (总周期数 - 1))在这个案例中,每个周期的不良品数量是10。
标准差的计算公式如下:标准差 = sqrt((10 - 1,000)^2 / (500 - 1))标准差=194.44最后,我们可以计算过程性能指数Cp:Cp=(1.05-0.95)/(6*194.44)Cp的值小于1,说明该生产过程的性能不达标。
第三步,我们需要计算过程能力指数 Cpk。
过程能力指数是用于衡量生产过程能否产生处于规格界限内的产品。
过程能力指数(Cpk)在质量管理中的应用与评估
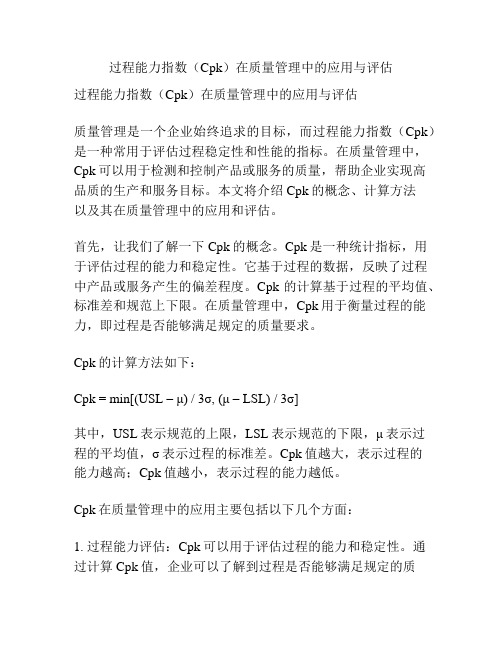
过程能力指数(Cpk)在质量管理中的应用与评估过程能力指数(Cpk)在质量管理中的应用与评估质量管理是一个企业始终追求的目标,而过程能力指数(Cpk)是一种常用于评估过程稳定性和性能的指标。
在质量管理中,Cpk可以用于检测和控制产品或服务的质量,帮助企业实现高品质的生产和服务目标。
本文将介绍Cpk的概念、计算方法以及其在质量管理中的应用和评估。
首先,让我们了解一下Cpk的概念。
Cpk是一种统计指标,用于评估过程的能力和稳定性。
它基于过程的数据,反映了过程中产品或服务产生的偏差程度。
Cpk的计算基于过程的平均值、标准差和规范上下限。
在质量管理中,Cpk用于衡量过程的能力,即过程是否能够满足规定的质量要求。
Cpk的计算方法如下:Cpk = min[(USL –μ) / 3σ, (μ –LSL) / 3σ]其中,USL表示规范的上限,LSL表示规范的下限,μ表示过程的平均值,σ表示过程的标准差。
Cpk值越大,表示过程的能力越高;Cpk值越小,表示过程的能力越低。
Cpk在质量管理中的应用主要包括以下几个方面:1. 过程能力评估:Cpk可以用于评估过程的能力和稳定性。
通过计算Cpk值,企业可以了解到过程是否能够满足规定的质量要求。
如果Cpk值较低,说明过程存在偏差较大的情况,需要进行改进和控制;如果Cpk值较高,说明过程的能力较强,可以继续保持稳定状态。
2. 品质控制:Cpk可以用于控制产品或服务的质量。
通过设定Cpk值的目标或下限,企业可以监测产品或服务的质量水平。
当Cpk值低于目标或下限时,说明产品或服务存在质量问题,需要及时采取措施进行改进和控制。
3. 过程改进:Cpk可以用于指导过程改进。
通过持续监测和分析Cpk值,企业可以找出过程中存在的问题,并采取相应的改进措施。
比如,当Cpk值较低时,可能是因为过程中存在一些不稳定的因素,需要进行变量的控制和调整;或者是因为过程中存在一些特殊因素,需要进行剔除或调整。
- 1、下载文档前请自行甄别文档内容的完整性,平台不提供额外的编辑、内容补充、找答案等附加服务。
- 2、"仅部分预览"的文档,不可在线预览部分如存在完整性等问题,可反馈申请退款(可完整预览的文档不适用该条件!)。
- 3、如文档侵犯您的权益,请联系客服反馈,我们会尽快为您处理(人工客服工作时间:9:00-18:30)。
过程能力指数案例分析
过程能力判断
过程能力指数的值越大,表明产品的离散程度相对于技术标准的公差范围越小,因而过程能力就越高;过程能力指数的值越小,表明产品的离散程度相对公差范围越大,因而过程能力就越低。
因此,可以从过程能力指数的数值大小来判断能力的高低。
从经济和质量两方面的要求来看,过程能力指数值并非越大越好,而应在一个适当的范围内取值。
过程能力指数案例分析
服务是一种无形的产品,对其如何进行质量控制呢?在工业质量管理的方法里,有一种指标叫做过程能力指标C pk,表示生产的部件与设计界限规定的范围的吻合程度,我们发现,把它应用在服务业上,也是一种很好的控制方法。
下面就以某银行为例子,来说明它的应用。
某银行在营业高峰期时,顾客的等待时间最少是4分钟,银行承诺最多11分钟要办理完其全部业务,这是银行对过去的业务经验的总结,同时认为,一般的平均等待时间是8分钟,这反映了其职员处理业务的平均速度和平均熟练程度。
在某个高峰时段银行办理了50位客户业务,每位客户的等待时间如下(为了便于计算0.5表示半分钟):
9.5,6.0,8.0,8.5,10.5,8.5,10.0,9.0,6.0,9.5,8.0,8.5,7.5
9.0,8.5,10.0,7.5,9.0,6.5,9.5,8.0,8.5,10.0,7.0,7.0,9.5,8.5,9.0,8.0,8.0,11.0,7.5,8.5,6.5,10.5,8.0,7.0,9.0,8.5
9.0,8.0,8.0,6.5,7.5,8.5,8.5,7.0,7.5,9.0,9.0
从这些数据可以看出银行实现了对顾客的承诺,每位顾客的等待时间都不超过11分钟,是否可以说该银行的服务质量达到了标准?部门经理应该如何评价本银行的的业务处理能力呢?
首先,我们要对这些数据作分析处理,如上图。
从图中我们可以得到,直方图表示数据的频度,数据的分布大体上是服从正态分布的,且曲线中值偏向右侧。
USL和LSL分别表示的是服务要求范围的上限和下限,在本案例中就是11分钟和4分钟,即落在这个界限内的顾客等待时间都是合适的。
一般对于USL和LSL的获得,可以有两种方法。
一是固有的标准,例如,某钢板厚度控制在6.4到5.6毫米为合格品,这就是标准;另外一个是以往的经验的总结,例如根据某种经验,处理某些业务,根据正常的程序,一般要3到8天等等。
使用统计软件可以计算出样本数据的平均值和标准差分别是8.36和1.165,我们用与S来表示,在数学上它们分别是与a的无偏估计值。
接下来让我们看一下它们的现实意义。
平均值=8.36分,反映了曲线的位置,是位置参数。
这个数字对于顾客来说,它反映了在该银行办理业务的平均等待时间;对该银行来说,他反映了该部门的平均效率;而对于其职员来说,它反映了职员办理业务的平均熟练程度。
而标准差S反映了顾客等待时间,即银行服务速度的波动性,波动造成差异,这是服务质量变异的属性。
差异的扩大会造成失控,在失控状态下,可能会造成业务的阻碍和客户的不满与抱怨。
因此,对于S当然是越小越好,因为它越小表示数据越集中,越靠近平均值,也就是时间长度的差异不大;如果S越大,就表示变化范围越大,也就是差异很大,很可能会造成服务质量变异。
顾客等待的标准差S=1.165分,它的意义就是:在平均值的正负三个S的分钟里,即从4.5分钟到12分钟,大约有99.73%顾客等待的时间在这个界限范围内。
有了这些数据,我们可以用过程能力指数C pk进行评价。
过程能力指数C pk原来指企业生产合格品能力的大小,在本案例中C pk指银行对顾客履行承诺的能力大小。
通常将C pk分为五个等级,以便针对不同的情况采取不同的措施来改进质量。
特级:C pk > 1.67,这时服务能力过高,企业可以考虑放宽质量要求;一级:1.33 < C pk < 1.67,那就是服务能很好地满足标准,是一种理想的状态;二级:1.00 < C pk < 1.33,可以认为服务质量是正常的,企业应该加强服务质量的控制和提高,以达到理想的状态;三级:0.67 < C pk< 1.00,服务质量较差,企业应该采取措施,加强对服务提供质量的控制与管理;四级:C pk< 0.67,企业服务质量严重不足,需要改进,如果C pk越小,那么服务很可能已经严重失控。
C pk的计算公式如下:
带入本案例数据计算出C pk为0.76,该企业服务质量处于第三级,从管理层面来讲,表示服
务质量不足,应立即采取措施改善。
如果遇到这种情况,我们应该如何解决呢?管理者可以把曲线尽量向规定的中心位置移动。
本案例中,一般顾客的平均等待时间是8分钟,可以说这是根据以往经验得到的平均效率,是正常的程序运作可以达到的,而顾客实际上平均的等待时间是8.36分,偏离了0.36。
因而质量曲线表现出向右偏移的现象,这样就会导致偏移出规定的范围。
所以,我们应该尽量把平均时间向中心位置(8分)靠近,即缩短顾客等待时间。
产生顾客等待现象的根本原因是服务现场的抵达者数量超过系统的处理能力,因此,减少等待时间的最好方案是消除根本原因,这通常需要对现有的生产和人力资源策略进行重新考察。
由于这样的改变可能需要花钱,所以商业银行管理人员必须高度重视服务质量和顾客满意度,把费用与提供给顾客更快服务的竞争优势联系起来。
鉴于此,我们拟将对减少顾客等待时间的策略浅述如下
(一)加强员工培训,规范工作程序
管理者可以通过加强对员工的培训与监督,特别是效绩较差的员工,来改进服务质量,同时管理者应该建立一套规范的工作程序,使服务过程标准化,并且制定遇到特殊情况时的处理方式,以免顾客流失。
此外,银行可向顾客提供“如何减少等待时间”宣传手册,提醒顾客高峰期的时间,并鼓励他们在不拥挤的非高峰时间寻求服务,那个时候服务会更快、更舒适。
(二)切实推行随机动态服务系统,实现服务时间的最优配置
一般情形下,商业银行提高服务水平自然就会降低顾客等待费用,但却常常增加了服务机构的成本。
为解决这个问题,有必要切实推行随机动态服务系统,最大限度缩短顾客等待时间,使商业银行的服务时间达到最优配置。
其中要重点考虑和解决以下两个方面的内容:(1)性态问题。
指各种顾客排队系统的概率规律性,研究队伍长度分布、等待时间分布和高峰期顾客分布等;(2)服务系统的统计推算。
即判断一个给定的排队系统符合哪种模型,服从于哪种统计分布规律。
(三)改进窗口设置方式和采取叫号方法
银行营业厅需要改进服务窗口设置方式,即不应全部设置为综合窗口和让顾客不加区别地排队,而是应根据顾客类别(如根据顾客办理业务种类不同分为现金业务、非现金业务、理财业务等,根据顾客办理业务额大小分为大额业务和小额业务等)分设不同服务窗口和让不同顾客分别排在不同价置。
其次,采取号码排队结构,即顾客到达银行营业厅后,通过号票打印机获得号码,当叫到自己所持号码时即到服务台接受服务。
此种排队结构有效地减少了顾客的体力成本和精神成本,能够保证“先到先服务”,顾客隐私和安全得到最大程度保障,从而受到顾客极大欢迎。
(四)创新服务手段,提高服务效率
信息技术的飞速发展使银行逐渐改变了以柜面服务为主的营业方式,而侧重于服务体系的建设,以低成木高效率的“机构+鼠标”的方式发展,以实体银行的信誉、信用和基本功能为平台,延伸虚拟网点,从而收到“1+1>2”的效果。
例如扩展自助设备功能,方便服务一般客户。
自助设备相对于柜面服务来说,操作简单快捷,是服务一般客户口常存取款、代缴费等业务的主要手段,并且能有效减轻柜面的人流压力,使需要办理复杂业务的客户能更快地得到服务。
利用互联网技术开通网上银行服务,不仅降低了的运营成本,还克服了时间和空间上的障碍,使顾客金融交易和服务可在任何时间、任何地点进行。
管理者结合上述手段,通过具体的措施实现改进,缩短顾客的等待时间,提高服务效率。
当部门可以稳定达到指标时,管理者可以调节LSL与USL的值或中心值,例如,管理者可以把
USL的值调到10分钟,计算得C pk为0.47,显然降低,管理者需要进一步加强措施来提高效率。
通过这样不断的调节,可以使服务标准得到不断改进与提高,并且在实际操作上加以配合,才可以达到顾客所意想不到的高效率与满意度。
同时这是一种以数据和现实分析驱动的管理方法,它可以应用到很多地方,例如,餐饮、物流、零售等服务业,帮助我们改进和提高服务质量。