连续重整PS-VI催化剂硫中毒分析及对策
重整装置催化剂异常运转的分析与处理措施

重整装置催化剂异常运转的分析与处理措施摘要:催化剂在重整装置中起着至关重要的作用,然而,由于操作不当、催化剂老化或污染等原因,催化剂可能会发生异常运转。
所以,必须要对重整装置催化剂异常运转的情况进行总结和分析。
基于这样的背景,本文旨在分析重整装置催化剂异常运转的原因,并提出相应的处理措施,以保证装置的正常运行和催化剂的稳定性,希望可以为相关工作者提供合理的建议。
关键词:重整装置;催化剂;异常运转;分析;处理引言重整反应通过使用催化剂将低辛烷值的烃类分子重新排列和重构,形成高辛烷值的环烷烃和芳烃化合物。
重整装置是炼油工业中重要的加工装置之一,催化剂作为其核心组成部分,直接影响装置的效能和产品质量。
催化剂异常运转将导致装置性能下降,产品质量下降,甚至催化剂失效。
因此,及时发现和解决催化剂异常运转问题,对于保障装置的正常运行至关重要。
一、重置装置催化剂异常运转的原因分析(一)操作不当重整装置催化剂是重整工艺的核心组成部分,在炼油和化工行业中具有重要的应用价值。
它能够提高汽油品质,满足清洁能源需求,并对环境保护和能源可持续发展做出贡献。
然而,在使用的过程中,如果操作人员对于重整装置的不熟悉或者操作不当,也常常会导致重整装置催化剂的异常运转。
例如,设置温度、压力、流速等参数不当,会使催化剂受到过高或过低的工艺条件影响,导致其活性降低或选择性下降,从而引起异常运转。
操作不当还包括未按照规定的程序进行操作、操作时忽视设备状态监测等情况,这些操作不当可能会导致过程中的温度变化不稳定、过高的流速、不恰当的催化剂再生等问题,最终导致催化剂异常运转。
(二)催化剂老化催化剂老化是导致重整装置催化剂异常运转的常见原因之一,随着时间的推移,催化剂的活性逐渐降低,从而影响其催化性能。
催化剂老化主要是由于长期使用、暴露在高温、高压、腐蚀性气体中等工作环境下引起的,随着催化剂老化,其表面发生物理和化学变化,包括孔结构的破坏、催化剂颗粒的磨损、活性组分的流失和结构的改变等。
国产重整催化剂PS-Ⅵ硫中毒分析与对策

国产重整催化剂PS-Ⅵ硫中毒分析与对策随着我国工业化进程的不断推进,对能源的需求日益增加,而石油是目前世界上最主要的能源之一,对石油的加工和利用成为了一个重要的领域。
在炼油过程中,重整催化剂被广泛应用于重整装置,用来将汽油中的芳烃和烯烃转化为高辛烷值的烃类产品。
重整装置中的重整催化剂在运行过程中容易受到硫的中毒影响,影响其催化活性和选择性,从而降低了产品的收率和质量。
本文将就国产重整催化剂PS-Ⅵ硫中毒问题进行分析,并提出对策,以期更好地解决这一问题。
一、国产重整催化剂PS-Ⅵ的特点国产重整催化剂PS-Ⅵ是一种活性高、稳定性好的重整催化剂。
它具有良好的耐硫性能,能够在高硫含量的条件下保持良好的催化活性和选择性。
PS-Ⅵ主要由负载型钼镍硫化物组成,具有较高的比表面积和孔容量,具有良好的抗毒性和热稳定性。
PS-Ⅵ在重整过程中还具有较高的抗结焦性能,不易被焦炭和杂质物质堵塞,从而延长了其使用寿命。
二、国产重整催化剂PS-Ⅵ的硫中毒问题分析虽然国产重整催化剂PS-Ⅵ具有较好的耐硫性能,但在实际运行中,仍然存在硫中毒问题。
硫中毒是指在重整过程中,催化剂表面的活性位点被硫化物所占据,导致催化活性和选择性降低的现象。
硫中毒对PS-Ⅵ的影响主要体现在以下几个方面:1. 催化活性下降:硫化物的存在会占据PS-Ⅵ的活性位点,阻碍了相关反应的进行,导致了催化活性的下降。
2. 选择性降低:硫化物的存在还会改变反应的路径和产物的选择性,导致了产品的收率和质量的降低。
3. 促进剂失效:硫化物还会与催化剂中的一些促进剂发生作用,导致这些促进剂的失效,从而降低了催化剂的效果。
三、国产重整催化剂PS-Ⅵ的硫中毒对策针对国产重整催化剂PS-Ⅵ的硫中毒问题,我们可以采取以下对策来加以解决:1. 优化工艺条件:适当降低重整装置中的硫化氢含量,可以减少硫中毒的程度,延长PS-Ⅵ的使用寿命。
2. 加强预处理:在重整装置投运前,进行严格的预处理工作,将硫化物和其他有毒物质尽可能地去除,减少其对PS-Ⅵ的影响。
国产重整催化剂PS-Ⅵ硫中毒分析与对策
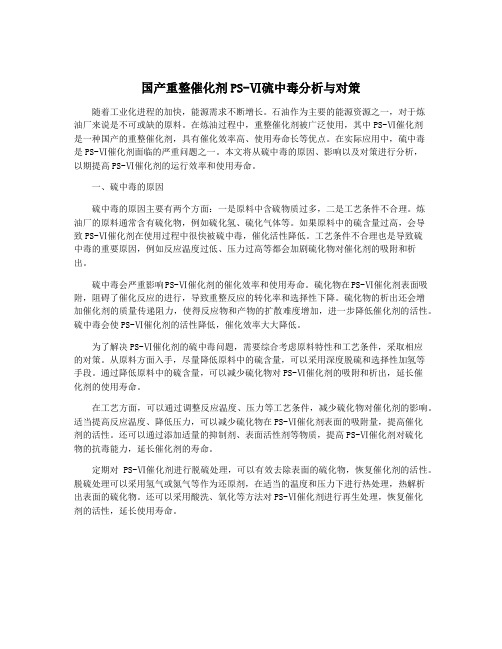
国产重整催化剂PS-Ⅵ硫中毒分析与对策随着工业化进程的加快,能源需求不断增长。
石油作为主要的能源资源之一,对于炼油厂来说是不可或缺的原料。
在炼油过程中,重整催化剂被广泛使用,其中PS-Ⅵ催化剂是一种国产的重整催化剂,具有催化效率高、使用寿命长等优点。
在实际应用中,硫中毒是PS-Ⅵ催化剂面临的严重问题之一。
本文将从硫中毒的原因、影响以及对策进行分析,以期提高PS-Ⅵ催化剂的运行效率和使用寿命。
一、硫中毒的原因硫中毒的原因主要有两个方面:一是原料中含硫物质过多,二是工艺条件不合理。
炼油厂的原料通常含有硫化物,例如硫化氢、硫化气体等。
如果原料中的硫含量过高,会导致PS-Ⅵ催化剂在使用过程中很快被硫中毒,催化活性降低。
工艺条件不合理也是导致硫中毒的重要原因,例如反应温度过低、压力过高等都会加剧硫化物对催化剂的吸附和析出。
硫中毒会严重影响PS-Ⅵ催化剂的催化效率和使用寿命。
硫化物在PS-Ⅵ催化剂表面吸附,阻碍了催化反应的进行,导致重整反应的转化率和选择性下降。
硫化物的析出还会增加催化剂的质量传递阻力,使得反应物和产物的扩散难度增加,进一步降低催化剂的活性。
硫中毒会使PS-Ⅵ催化剂的活性降低,催化效率大大降低。
为了解决PS-Ⅵ催化剂的硫中毒问题,需要综合考虑原料特性和工艺条件,采取相应的对策。
从原料方面入手,尽量降低原料中的硫含量,可以采用深度脱硫和选择性加氢等手段。
通过降低原料中的硫含量,可以减少硫化物对PS-Ⅵ催化剂的吸附和析出,延长催化剂的使用寿命。
在工艺方面,可以通过调整反应温度、压力等工艺条件,减少硫化物对催化剂的影响。
适当提高反应温度、降低压力,可以减少硫化物在PS-Ⅵ催化剂表面的吸附量,提高催化剂的活性。
还可以通过添加适量的抑制剂、表面活性剂等物质,提高PS-Ⅵ催化剂对硫化物的抗毒能力,延长催化剂的寿命。
定期对PS-Ⅵ催化剂进行脱硫处理,可以有效去除表面的硫化物,恢复催化剂的活性。
脱硫处理可以采用氢气或氮气等作为还原剂,在适当的温度和压力下进行热处理,热解析出表面的硫化物。
国产重整催化剂PS-Ⅵ硫中毒分析与对策

国产重整催化剂PS-Ⅵ硫中毒分析与对策催化剂是化学过程中的重要辅助剂,广泛应用于炼油、化工、石化等工业领域。
催化剂使反应速率大幅提高,提高产品质量,降低生产成本。
长期的使用会导致催化剂中毒现象,影响催化剂的活性和稳定性。
本文将阐述国产重整催化剂PS-Ⅵ硫中毒的分析与对策。
我们需要了解催化剂硫中毒的原因。
PS-Ⅵ是一种贵重金属成分较高的催化剂,经过长时间使用后,底物中的硫含量逐渐积累在催化剂表面,导致催化剂活性降低。
硫中毒的主要原因是硫与催化剂金属表面反应生成金属硫酸盐,阻塞反应物分子进入活性中心和产物分子的扩散。
针对PS-Ⅵ催化剂硫中毒问题,我们可以采取以下几种对策。
首先是加强原料气体的净化处理。
通过使用高效脱硫装置,降低底物中的硫含量,减少硫污染对催化剂的影响。
其次是优化操作条件。
合理控制反应温度、压力和催化剂的空速,提高反应物在催化剂表面的接触时间,降低硫中毒速度。
还可以采用周期逆流反应装置,定期逆流清洗催化剂表面的硫酸盐,恢复催化剂的活性。
在硫中毒发生后,我们可以采取一些方法重新活化PS-Ⅵ催化剂,恢复其活性。
首先是热解法。
将硫中毒的催化剂加热至一定温度,使催化剂表面的硫酸盐分解为硫化物和气体,去除硫污染。
其次是化学法。
使用硫化氢或氢气等可还原物质与硫酸盐反应,还原成非活性硫化物,恢复催化剂活性。
还可以考虑采用物理法,如超声波清洗、高压水汽冲刷等。
研发新的催化剂也是解决硫中毒问题的重要方向。
通过控制催化剂表面结构,改善催化剂的抗硫性能。
可以探索添加非贵金属助剂,提高催化剂的抗硫能力。
也可以研究催化剂的再生技术,实现长周期使用。
针对国产重整催化剂PS-Ⅵ的硫中毒问题,需要加强原料气体的净化处理,优化操作条件,采用周期逆流反应装置清洗催化剂,采用热解法、化学法或物理法重新活化催化剂,以及研发新的催化剂技术。
这些措施将有助于提高催化剂的抗硫性能,延长催化剂的使用寿命,提高生产效益。
连续重整PS_催化剂硫中毒分析及对策_刘宏鑫
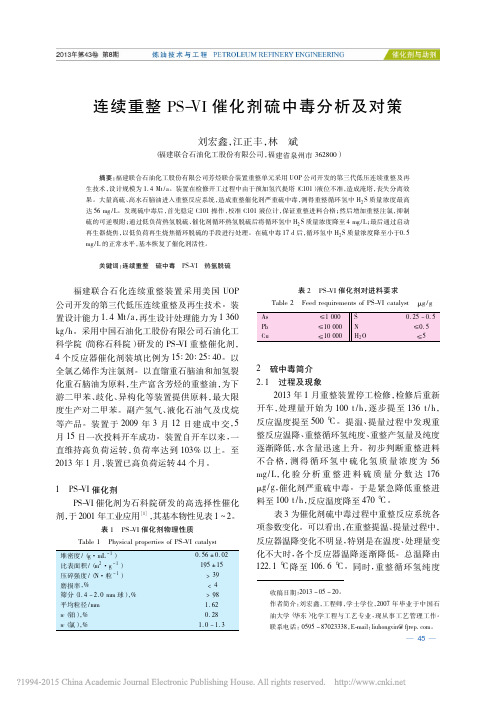
少,极大地左右了催化剂脱硫的处理方式,本次硫 中毒前,积炭维持在一个较低的水平,为之后的处 理提供了充足的时间和灵活性。
( 3) 在催化剂积炭不高时,提高重整进料注氯 和重整反应温度,加大产氢量,能加快脱硫效果。
( 4) PS-VI 催化剂具有较高的稳定性,在高负 荷运转 44 个月之后发生硫中毒时,仍能较好地恢
炭 4. 00 4. 20 3. 96 3. 29 4. 07 3. 91 3. 58 4. 08
氯 0. 89 0. 87 0. 89 0. 90 1. 10 1. 11 1. 19 1. 19
项目 ρ( H2 S) / ( mg·L - 1 ) ρ( HCl) / ( mg·L - 1 ) 注氯量 / ( μg·g - 1 ) 加权平均床层温度/ ℃
3 硫中毒处理 在发现重整催化剂硫中毒后,为防止重整进
料中带硫,污染催化剂,故停止重整注硫,并确认 C101 液位,修改仪表参数至正常值。预加氢反应 温度由 280 ℃ 提至 285 ℃ 。增加重整进料化验分 析频率,在确保进料合格的同时,采取以下措施恢 复催化剂活性。 3. 1 维持再生停车状态 低负荷热氢脱硫
49. 8
20∶ 00 128 488. 0
40. 1 36. 9 26. 4 18. 1 121. 5 73. 0
70. 0
22∶ 00 128 488. 0
35. 1 30. 1 23. 9 17. 5 106. 6 69. 4
86. 2
24∶ 00 136 500. 0
42. 3 35. 7 28. 8 19. 4 126. 0 67. 4
01 - 22 13 15
重整进料硫含量超标分析

重整进料硫含量超标分析摘要:对连续重整装置出现的重整进料硫含量超标的异常情况进行了分析,认为预加氢反应进料、出料换热器内漏、重整进料注硫过量、罐区来精制石脑油中溶解氧与硫化氢反应生成不易汽提脱除的硫化物等是硫含量超标的原因,通过采取相应的措施,问题得以解决。
关键词:重整进料;硫含量超标;溶解氧0引言含硫化合物对重整催化剂是一种典型的毒物,可以导致催化剂失活。
在一定的重整反应条件下,含硫化合物很容易生成硫化氢,它可以吸附在金属表面上导致催化剂活性降低。
装置在运行过程中,曾出现过两次硫含量超标的情况。
本文主要对硫含量超标的异常情况进行介绍,并进行原因分析,提出采取的措施。
1硫含量超标的情况2017年9月22日起,重整进料(SN261)中硫含量开始出现超标现象(最高达到1.1ppm,要求<0.5ppm),出现这一现象后,装置区及时进行对全馏分石脑油及加氢裂化石脑油进行了加样分析,结果为加氢裂化石脑油硫含量最高达到2.4ppm,于是装置区立即联系调度协调调整,9月27日,重整进料硫含量开始恢复正常(<0.5ppm),期间装置区除参照重整循环氢中H2S含量外,又使用H2S 检测管多次测量了循环氢中硫化氢含量,结果都显示<1ppm,除此之外,一反温降变化并不明显,总温降也变化不大。
从此之后至12月,陆陆续续出现了多次进料硫含量超标的现象,装置区也及时进行了加样分析,除重石硫含量高,直馏石脑油硫含量偶尔超标外,也不排除分析误差原因,因为从数据表中可以看出,循环氢中H2S含量最大没有超过3ppm,经过自己检测也没有超过这个数值,但多次出现分析数据超标,包括一些未查明原因的超标,为防止预加氢催化剂性能下降导致脱硫效果不佳,虽从分析结果上看,预加氢反应系统高分罐生成油中硫含量并不是很高(基本稳定在100ppm以下),但装置区还是决定提高预加氢反应温度由276℃提高至279℃,并持续关注。
12月开始至2月初,重整进料硫含量超标现象仍时有出现,且有一定增加趋势(具体详见分析及运行数据表),循环氢中H2S含量也时有上升趋势,且一反温降时有下降趋势,装置区始终加样跟踪,也时有重石和全馏分石脑油超标现象,虽及时多次与调度和厂协调,但还是没有根本杜绝S含量超标的问题。
重整催化剂PS-VI在连续重整装置的应用和使用情况分析
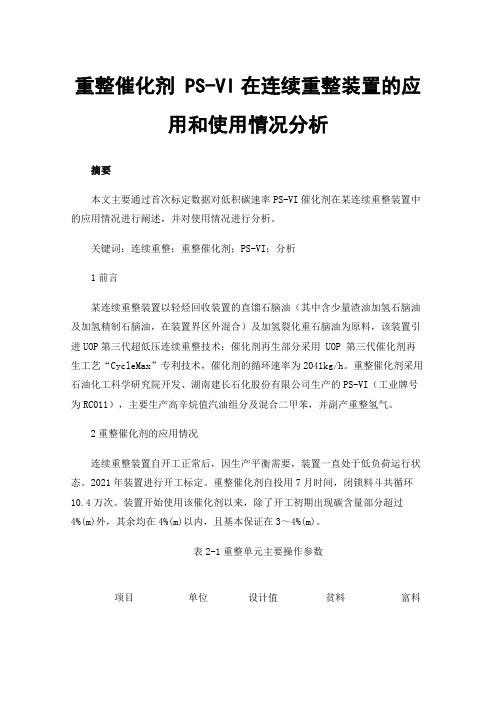
重整催化剂 PS-VI在连续重整装置的应用和使用情况分析摘要本文主要通过首次标定数据对低积碳速率PS-VI催化剂在某连续重整装置中的应用情况进行阐述,并对使用情况进行分析。
关键词:连续重整;重整催化剂;PS-VI;分析1前言某连续重整装置以轻烃回收装置的直馏石脑油(其中含少量渣油加氢石脑油及加氢精制石脑油,在装置界区外混合)及加氢裂化重石脑油为原料,该装置引进UOP第三代超低压连续重整技术;催化剂再生部分采用 UOP 第三代催化剂再生工艺“CycleMax”专利技术,催化剂的循环速率为2041kg/h。
重整催化剂采用石油化工科学研究院开发、湖南建长石化股份有限公司生产的PS-VI(工业牌号为RC011),主要生产高辛烷值汽油组分及混合二甲苯,并副产重整氢气。
2重整催化剂的应用情况连续重整装置自开工正常后,因生产平衡需要,装置一直处于低负荷运行状态。
2021年装置进行开工标定。
重整催化剂自投用7月时间,闭锁料斗共循环10.4万次。
装置开始使用该催化剂以来,除了开工初期出现碳含量部分超过4%(m)外,其余均在4%(m)以内,且基本保证在3~4%(m)。
表2-1重整单元主要操作参数项目单位设计值贫料富料总温降℃306303.9241.9 WAIT℃-519.5519.1 WABT℃-484.3490.82反应空速(体积)贫料/富料h-12.7/2.751.66 1.66反应压力MPa0.240.2520.249氢油比(贫料/富料)mol2/1.7 3.28 4.41 3重整催化剂使用情况分析3.1催化剂物理性质装置刚运行期间该催化剂比表面积为190m2/g,运行3个月后,该剂比表面积为180m2/g。
从该数据可知,目前该剂仍处于新鲜剂状态。
从表3.1-2可知,再生部分在60%(即1.225t/h)催化剂循环速率时,富料工况待生催化剂碳含量3.4%(wt),再生催化剂碳含量为0.055%(wt),氯含量为1.16%(wt);贫料工况待生催化剂碳含量为3.24%(wt),再生催化剂碳含量为0.045%(wt),氯含量为1.13%(wt)。
国产重整催化剂PS-Ⅵ硫中毒分析与对策
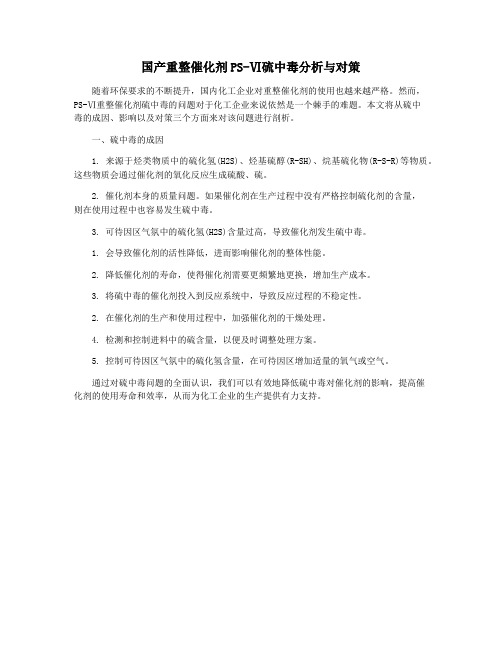
国产重整催化剂PS-Ⅵ硫中毒分析与对策
随着环保要求的不断提升,国内化工企业对重整催化剂的使用也越来越严格。
然而,PS-Ⅵ重整催化剂硫中毒的问题对于化工企业来说依然是一个棘手的难题。
本文将从硫中
毒的成因、影响以及对策三个方面来对该问题进行剖析。
一、硫中毒的成因
1. 来源于烃类物质中的硫化氢(H2S)、烃基硫醇(R-SH)、烷基硫化物(R-S-R)等物质。
这些物质会通过催化剂的氧化反应生成硫酸、硫。
2. 催化剂本身的质量问题。
如果催化剂在生产过程中没有严格控制硫化剂的含量,
则在使用过程中也容易发生硫中毒。
3. 可待因区气氛中的硫化氢(H2S)含量过高,导致催化剂发生硫中毒。
1. 会导致催化剂的活性降低,进而影响催化剂的整体性能。
2. 降低催化剂的寿命,使得催化剂需要更频繁地更换,增加生产成本。
3. 将硫中毒的催化剂投入到反应系统中,导致反应过程的不稳定性。
2. 在催化剂的生产和使用过程中,加强催化剂的干燥处理。
4. 检测和控制进料中的硫含量,以便及时调整处理方案。
5. 控制可待因区气氛中的硫化氢含量,在可待因区增加适量的氧气或空气。
通过对硫中毒问题的全面认识,我们可以有效地降低硫中毒对催化剂的影响,提高催
化剂的使用寿命和效率,从而为化工企业的生产提供有力支持。