铸轧
铸轧发展现状调研报告

铸轧发展现状调研报告铸轧发展现状调研报告一、引言铸轧是指将熔融金属液体倾倒到铸模中进行铸造,然后经过热轧加工或冷轧加工,最终得到所需产品的加工过程。
铸轧技术在现代工业中起到了重要的作用,广泛应用于钢铁、有色金属、铝型材等行业。
本调研报告旨在对铸轧发展现状进行调查研究,了解其发展趋势和面临的挑战,提出相应对策与建议。
二、调研内容与方法本次调研以国内铸轧生产企业为对象,采用问卷调查、访谈等方法获取数据和信息。
主要调查内容包括铸轧生产规模、技术水平、人才培养等方面。
三、铸轧生产规模与市场需求根据调查数据显示,目前国内铸轧生产企业数量众多,其中大部分为中小型企业。
铸轧生产规模不一,但整体生产能力较低。
市场需求方面,行业整体需求稳定增长,尤其是在工业领域需求较为旺盛。
四、铸轧技术水平与创新能力铸轧技术在国内已具备一定的发展基础,但与国外先进水平相比仍有差距。
调查发现,一些企业在技术装备升级方面存在困难,导致技术水平提升不够迅速。
创新能力方面,国内企业在材料配方、工艺流程等方面积极探索,但在核心技术创新方面还存在挑战。
五、人才培养与团队建设铸轧行业对高级技术人员的需求较大,但目前人才培养体系相对薄弱。
调研发现,企业在人才引进、培训等方面投入不足,导致技术团队整体素质有待提高。
建议加强高校与企业合作,加大对相关专业的培养力度,提高铸轧人才队伍素质。
六、面临的挑战与对策在调研过程中,我们也发现了一些铸轧行业所面临的挑战,主要包括市场竞争激烈、资源约束、环境压力等。
针对这些挑战,我们建议企业加强与供应商和客户的合作关系,提高资源利用效率;加强环境保护工作,推进绿色发展;积极开拓市场,增加产品附加值。
七、结论与建议通过对铸轧发展现状的调查研究,我们认为虽然国内铸轧行业还存在一些问题和挑战,但整体上发展态势稳定向好。
建议企业加强技术创新和人才培养,提高技术水平;加强与客户、供应商的合作,提高资源利用效率;积极开拓市场,开拓新的产品和应用领域。
铝合金铸轧工艺
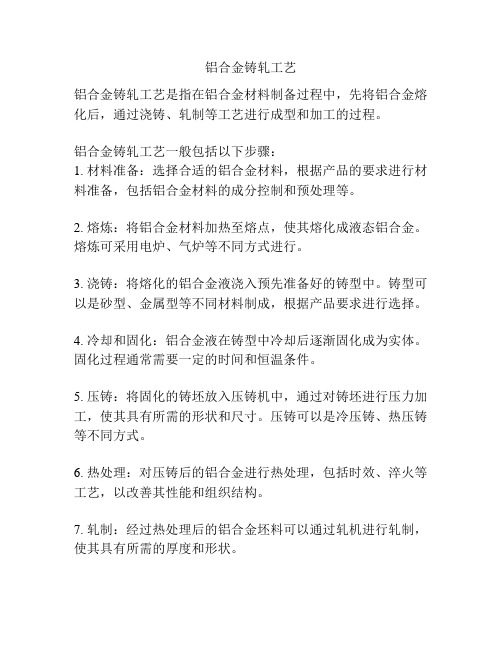
铝合金铸轧工艺
铝合金铸轧工艺是指在铝合金材料制备过程中,先将铝合金熔化后,通过浇铸、轧制等工艺进行成型和加工的过程。
铝合金铸轧工艺一般包括以下步骤:
1. 材料准备:选择合适的铝合金材料,根据产品的要求进行材料准备,包括铝合金材料的成分控制和预处理等。
2. 熔炼:将铝合金材料加热至熔点,使其熔化成液态铝合金。
熔炼可采用电炉、气炉等不同方式进行。
3. 浇铸:将熔化的铝合金液浇入预先准备好的铸型中。
铸型可以是砂型、金属型等不同材料制成,根据产品要求进行选择。
4. 冷却和固化:铝合金液在铸型中冷却后逐渐固化成为实体。
固化过程通常需要一定的时间和恒温条件。
5. 压铸:将固化的铸坯放入压铸机中,通过对铸坯进行压力加工,使其具有所需的形状和尺寸。
压铸可以是冷压铸、热压铸等不同方式。
6. 热处理:对压铸后的铝合金进行热处理,包括时效、淬火等工艺,以改善其性能和组织结构。
7. 轧制:经过热处理后的铝合金坯料可以通过轧机进行轧制,使其具有所需的厚度和形状。
8. 退火处理:通过对轧制后的铝合金进行退火处理,消除残余应力,改善其机械性能。
9. 表面处理:对轧制后的铝合金进行酸洗、氧化等表面处理,以提高其表面质量和耐腐蚀性能。
10. 检验和包装:对成品进行检验,包括外观检查、尺寸测量、性能测试等,然后进行包装和贮存。
铝合金铸轧工艺可以根据具体产品的要求进行调整和改进,在不同的铝合金材料、铸型和轧制设备等条件下,工艺参数和工艺流程也会有所差异。
浅谈铝业公司铸轧工作的流程和技术
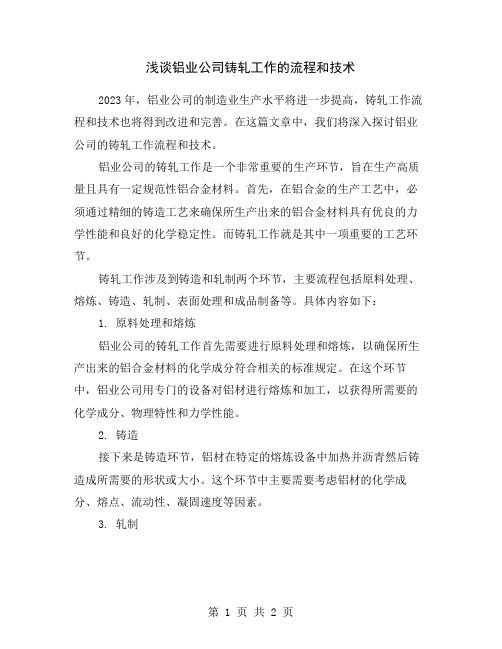
浅谈铝业公司铸轧工作的流程和技术2023年,铝业公司的制造业生产水平将进一步提高,铸轧工作流程和技术也将得到改进和完善。
在这篇文章中,我们将深入探讨铝业公司的铸轧工作流程和技术。
铝业公司的铸轧工作是一个非常重要的生产环节,旨在生产高质量且具有一定规范性铝合金材料。
首先,在铝合金的生产工艺中,必须通过精细的铸造工艺来确保所生产出来的铝合金材料具有优良的力学性能和良好的化学稳定性。
而铸轧工作就是其中一项重要的工艺环节。
铸轧工作涉及到铸造和轧制两个环节,主要流程包括原料处理、熔炼、铸造、轧制、表面处理和成品制备等。
具体内容如下:1. 原料处理和熔炼铝业公司的铸轧工作首先需要进行原料处理和熔炼,以确保所生产出来的铝合金材料的化学成分符合相关的标准规定。
在这个环节中,铝业公司用专门的设备对铝材进行熔炼和加工,以获得所需要的化学成分、物理特性和力学性能。
2. 铸造接下来是铸造环节,铝材在特定的熔炼设备中加热并沥青然后铸造成所需要的形状或大小。
这个环节中主要需要考虑铝材的化学成分、熔点、流动性、凝固速度等因素。
3. 轧制然后是轧制环节。
顾名思义,铝材需要通过轧辊等设备进行轧制,以获得所需要的产品规格和外观要求。
轧制环节中较为关键的是轧制温度和轧制速度,这两个因素将影响铝材的外观和性能特点。
4. 表面处理在铝材被轧制成所需的形状和尺寸之后,需要进行表面处理,主要包括酸洗、氧化、喷雾油、切割等。
这个环节中的表面处理措施的主要目的是增加铝材的抗腐蚀性和美观度,以提高铝材的整体质量。
5. 成品制备最后是成品制备环节,也是铸轧工作的最后一个环节。
在这个环节中,铝材被切割成所需的大小和尺寸。
这个过程不仅需要考虑产品规格和外观,还要考虑整体质量和成本。
综上所述,铝业公司的铸轧工作流程和技术相当复杂和精细,需要用先进设备和管理方法来保证产品质量。
未来,铝业公司的铸轧工作将继续发展和完善,将会更加多样化,并将继续保持其技术和管理领先地位,为行业市场的需求提供优质的铝合金材料。
铝业公司员工铸轧个人总结
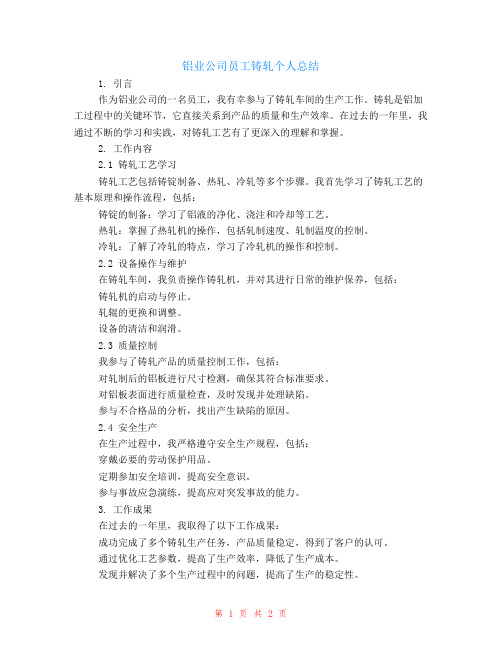
铝业公司员工铸轧个人总结1. 引言作为铝业公司的一名员工,我有幸参与了铸轧车间的生产工作。
铸轧是铝加工过程中的关键环节,它直接关系到产品的质量和生产效率。
在过去的一年里,我通过不断的学习和实践,对铸轧工艺有了更深入的理解和掌握。
2. 工作内容2.1 铸轧工艺学习铸轧工艺包括铸锭制备、热轧、冷轧等多个步骤。
我首先学习了铸轧工艺的基本原理和操作流程,包括:铸锭的制备:学习了铝液的净化、浇注和冷却等工艺。
热轧:掌握了热轧机的操作,包括轧制速度、轧制温度的控制。
冷轧:了解了冷轧的特点,学习了冷轧机的操作和控制。
2.2 设备操作与维护在铸轧车间,我负责操作铸轧机,并对其进行日常的维护保养,包括:铸轧机的启动与停止。
轧辊的更换和调整。
设备的清洁和润滑。
2.3 质量控制我参与了铸轧产品的质量控制工作,包括:对轧制后的铝板进行尺寸检测,确保其符合标准要求。
对铝板表面进行质量检查,及时发现并处理缺陷。
参与不合格品的分析,找出产生缺陷的原因。
2.4 安全生产在生产过程中,我严格遵守安全生产规程,包括:穿戴必要的劳动保护用品。
定期参加安全培训,提高安全意识。
参与事故应急演练,提高应对突发事故的能力。
3. 工作成果在过去的一年里,我取得了以下工作成果:成功完成了多个铸轧生产任务,产品质量稳定,得到了客户的认可。
通过优化工艺参数,提高了生产效率,降低了生产成本。
发现并解决了多个生产过程中的问题,提高了生产的稳定性。
4. 存在问题与改进措施在工作过程中,我也发现了一些问题,并提出了相应的改进措施:4.1 工艺优化问题:部分铸轧工艺参数设置不够合理,影响了产品质量。
改进措施:通过实验和数据分析,优化工艺参数,提高产品质量。
4.2 设备维护问题:部分设备老化,故障率较高,影响了生产效率。
改进措施:加强设备的维护保养,及时更换老化的部件。
4.3 员工培训问题:部分新员工对铸轧工艺掌握不够全面,影响了生产质量。
改进措施:加强新员工的培训,提高其对铸轧工艺的理解和操作技能。
薄带铸轧工艺技术规范
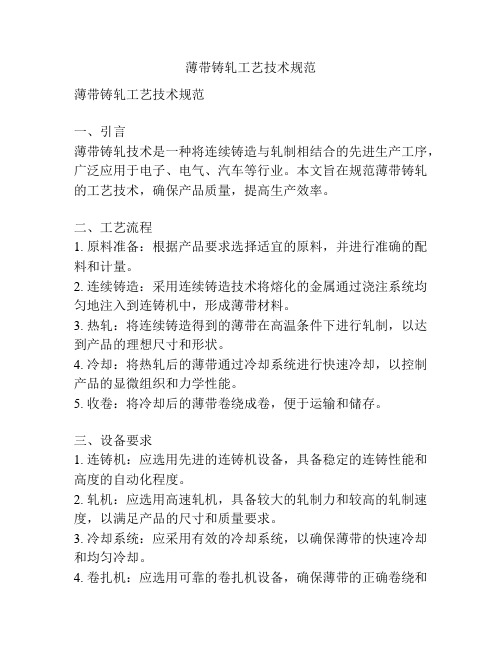
薄带铸轧工艺技术规范薄带铸轧工艺技术规范一、引言薄带铸轧技术是一种将连续铸造与轧制相结合的先进生产工序,广泛应用于电子、电气、汽车等行业。
本文旨在规范薄带铸轧的工艺技术,确保产品质量,提高生产效率。
二、工艺流程1. 原料准备:根据产品要求选择适宜的原料,并进行准确的配料和计量。
2. 连续铸造:采用连续铸造技术将熔化的金属通过浇注系统均匀地注入到连铸机中,形成薄带材料。
3. 热轧:将连续铸造得到的薄带在高温条件下进行轧制,以达到产品的理想尺寸和形状。
4. 冷却:将热轧后的薄带通过冷却系统进行快速冷却,以控制产品的显微组织和力学性能。
5. 收卷:将冷却后的薄带卷绕成卷,便于运输和储存。
三、设备要求1. 连铸机:应选用先进的连铸机设备,具备稳定的连铸性能和高度的自动化程度。
2. 轧机:应选用高速轧机,具备较大的轧制力和较高的轧制速度,以满足产品的尺寸和质量要求。
3. 冷却系统:应采用有效的冷却系统,以确保薄带的快速冷却和均匀冷却。
4. 卷扎机:应选用可靠的卷扎机设备,确保薄带的正确卷绕和稳定性。
四、工艺参数1. 连铸工艺参数:包括浇注温度、冷却方式、浇注速度等,应根据具体材料和产品要求进行合理的设定。
2. 轧制工艺参数:包括轧制温度、轧制力、轧制速度等,应根据材料的热变形特性和产品的尺寸要求进行合理的设定。
3. 冷却工艺参数:包括冷却速度、冷却介质等,应根据材料的热处理要求和产品的显微组织控制要求进行合理的设定。
五、质量控制1. 原料检验:对原材料进行化学成分、物理性能等方面的检验,确保原材料符合产品要求。
2. 在线检测:对连续铸造、热轧、冷却等过程进行在线检测,及时发现并纠正问题,确保产品质量。
3. 产品检验:对成品薄带进行外观质量、尺寸精度、机械性能、化学成分等方面的检验,确保产品达到标准要求。
六、安全环保1. 设备安全:保证设备的安全运行,提供必要的防护设施和安全培训。
2. 废水处理:配备有效的废水处理设施,确保废水符合环保要求。
铝板铸轧工艺
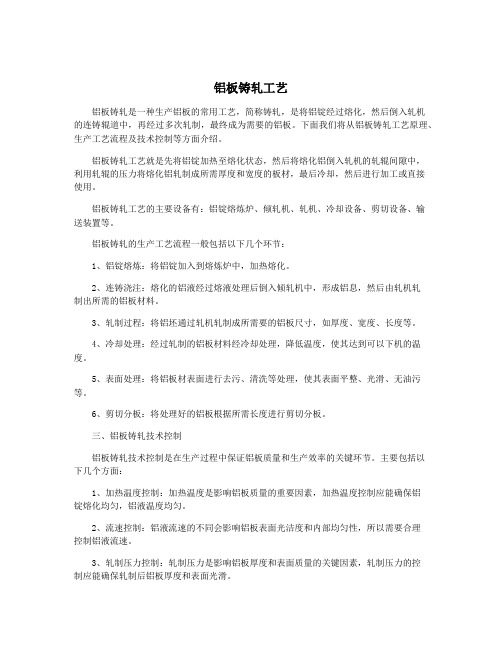
铝板铸轧工艺铝板铸轧是一种生产铝板的常用工艺,简称铸轧,是将铝锭经过熔化,然后倒入轧机的连铸辊道中,再经过多次轧制,最终成为需要的铝板。
下面我们将从铝板铸轧工艺原理、生产工艺流程及技术控制等方面介绍。
铝板铸轧工艺就是先将铝锭加热至熔化状态,然后将熔化铝倒入轧机的轧辊间隙中,利用轧辊的压力将熔化铝轧制成所需厚度和宽度的板材,最后冷却,然后进行加工或直接使用。
铝板铸轧工艺的主要设备有:铝锭熔炼炉、倾轧机、轧机、冷却设备、剪切设备、输送装置等。
铝板铸轧的生产工艺流程一般包括以下几个环节:1、铝锭熔炼:将铝锭加入到熔炼炉中,加热熔化。
2、连铸浇注:熔化的铝液经过熔液处理后倒入倾轧机中,形成铝息,然后由轧机轧制出所需的铝板材料。
3、轧制过程:将铝坯通过轧机轧制成所需要的铝板尺寸,如厚度、宽度、长度等。
4、冷却处理:经过轧制的铝板材料经冷却处理,降低温度,使其达到可以下机的温度。
5、表面处理:将铝板材表面进行去污、清洗等处理,使其表面平整、光滑、无油污等。
6、剪切分板:将处理好的铝板根据所需长度进行剪切分板。
三、铝板铸轧技术控制铝板铸轧技术控制是在生产过程中保证铝板质量和生产效率的关键环节。
主要包括以下几个方面:1、加热温度控制:加热温度是影响铝板质量的重要因素,加热温度控制应能确保铝锭熔化均匀,铝液温度均匀。
2、流速控制:铝液流速的不同会影响铝板表面光洁度和内部均匀性,所以需要合理控制铝液流速。
3、轧制压力控制:轧制压力是影响铝板厚度和表面质量的关键因素,轧制压力的控制应能确保轧制后铝板厚度和表面光滑。
4、冷却水温度和速度控制:冷却是保证铝板质量的关键环节,冷却水温度和速度的不同会影响铝板的冷却效果,所以需要合理控制冷却水温度和速度。
5、表面质量控制:铝板的表面质量是影响其用途的重要因素,应注意表面处理,减少表面缺陷,确保铝板表面质量。
总之,铝板铸轧工艺是一种常用的铝板生产工艺,对铝板的质量和生产效率有重要影响。
铸轧生产工艺

铸轧生产工艺
根据合金牌号及制品用途要求,控制主成分及杂质含量,进行所需液体料与各种固体料配料计算,配料后加入25t圆形天然气熔铝炉中进行熔化后,经扒渣、搅拌,取样分析铝液的化学成分,并根据分析结果对铝熔体的化学成份进行调整;成份合格、温度符合工艺要求的铝熔体,转入20t电阻保温炉精炼,铝熔体连续不断地流入在线处理装置,加入晶粒细化剂、除气、过滤、铸轧、切头、卷取,当卷重达到要求时,剪切机切断带材,由卸卷小车快速卸卷,捆缚称重,铸轧带材经检查合格后送往冷轧车间。
铸轧生产工艺流程见图
电解铝液
废料中间合金
配料、装炉
熔化
扒渣、搅拌、快速分析
调整成分
转炉
精炼、调温、静置
铝—钛—硼线杆
熔体处理
铸轧
卷取
剪断
卸卷、捆缚、称重
检查
成品铸轧带材
铸轧生产工艺流程图。
铝业企业工人铸轧工作总结
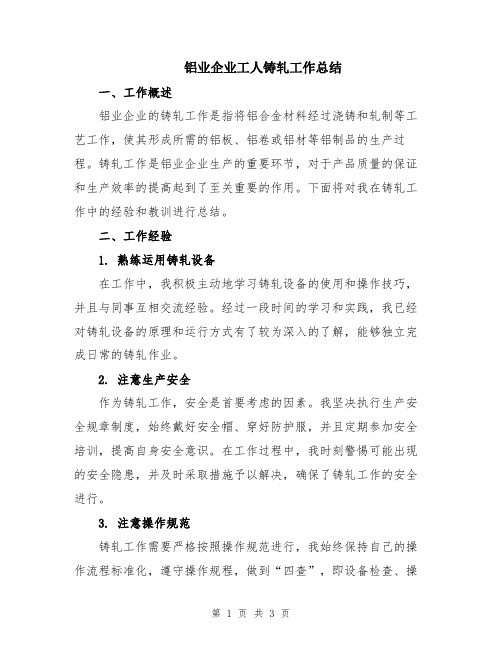
铝业企业工人铸轧工作总结一、工作概述铝业企业的铸轧工作是指将铝合金材料经过浇铸和轧制等工艺工作,使其形成所需的铝板、铝卷或铝材等铝制品的生产过程。
铸轧工作是铝业企业生产的重要环节,对于产品质量的保证和生产效率的提高起到了至关重要的作用。
下面将对我在铸轧工作中的经验和教训进行总结。
二、工作经验1. 熟练运用铸轧设备在工作中,我积极主动地学习铸轧设备的使用和操作技巧,并且与同事互相交流经验。
经过一段时间的学习和实践,我已经对铸轧设备的原理和运行方式有了较为深入的了解,能够独立完成日常的铸轧作业。
2. 注意生产安全作为铸轧工作,安全是首要考虑的因素。
我坚决执行生产安全规章制度,始终戴好安全帽、穿好防护服,并且定期参加安全培训,提高自身安全意识。
在工作过程中,我时刻警惕可能出现的安全隐患,并及时采取措施予以解决,确保了铸轧工作的安全进行。
3. 注意操作规范铸轧工作需要严格按照操作规范进行,我始终保持自己的操作流程标准化,遵守操作规程,做到“四查”,即设备检查、操作规程检查、环境检查和防火检查。
同时,我也积极参与审核工作流程,完善操作规范,提高铸轧工作的效率和质量。
4. 加强团队协作在铸轧工作中,我认识到一个人的力量是有限的,只有通过团队的协作才能更好地完成工作任务。
我与同事充分沟通合作,相互帮助,减少工作中的失误和漏洞。
通过团队协作,我们不仅提高了工作效率,还改进了工作方法,不断提升了铸轧工作的质量。
三、存在问题与教训1. 缺乏细致耐心在铸轧工作中,我有时候会因为工作繁忙或者其他原因,导致粗心大意,忽略了一些细节问题。
这给工作带来了一些隐患和问题。
教训是要时刻保持细致耐心,细心观察每一个细节,不允许任何疏忽和马虎。
2. 不善于沟通在团队协作中,我有时候表达不够清晰,导致同事可能会理解不准确,从而影响工作进展。
教训是要学会善于沟通,清晰地表达自己的意思,避免产生误解,保持团队的良好氛围。
3. 缺乏创新意识铸轧工作虽然有一定的规范和标准操作流程,但也需要我们具备一定的创新意识,及时发现问题和改进工作方法。
铸轧铝卷的种类
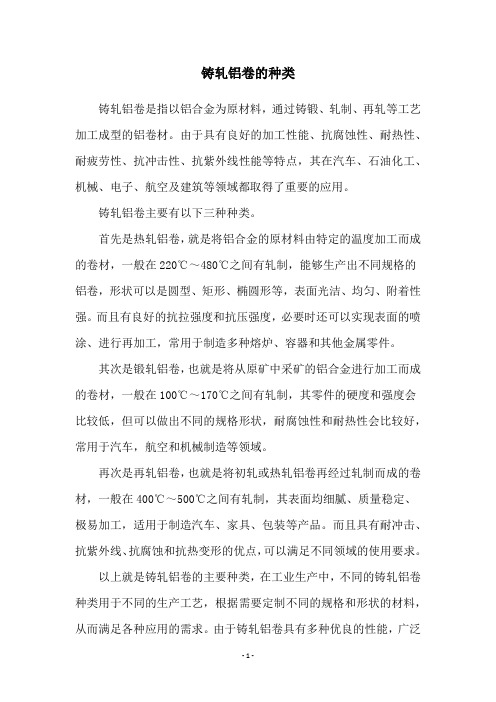
铸轧铝卷的种类
铸轧铝卷是指以铝合金为原材料,通过铸锻、轧制、再轧等工艺加工成型的铝卷材。
由于具有良好的加工性能、抗腐蚀性、耐热性、耐疲劳性、抗冲击性、抗紫外线性能等特点,其在汽车、石油化工、机械、电子、航空及建筑等领域都取得了重要的应用。
铸轧铝卷主要有以下三种种类。
首先是热轧铝卷,就是将铝合金的原材料由特定的温度加工而成的卷材,一般在220℃~480℃之间有轧制,能够生产出不同规格的铝卷,形状可以是圆型、矩形、椭圆形等,表面光洁、均匀、附着性强。
而且有良好的抗拉强度和抗压强度,必要时还可以实现表面的喷涂、进行再加工,常用于制造多种熔炉、容器和其他金属零件。
其次是锻轧铝卷,也就是将从原矿中采矿的铝合金进行加工而成的卷材,一般在100℃~170℃之间有轧制,其零件的硬度和强度会比较低,但可以做出不同的规格形状,耐腐蚀性和耐热性会比较好,常用于汽车,航空和机械制造等领域。
再次是再轧铝卷,也就是将初轧或热轧铝卷再经过轧制而成的卷材,一般在400℃~500℃之间有轧制,其表面均细腻、质量稳定、极易加工,适用于制造汽车、家具、包装等产品。
而且具有耐冲击、抗紫外线、抗腐蚀和抗热变形的优点,可以满足不同领域的使用要求。
以上就是铸轧铝卷的主要种类,在工业生产中,不同的铸轧铝卷种类用于不同的生产工艺,根据需要定制不同的规格和形状的材料,从而满足各种应用的需求。
由于铸轧铝卷具有多种优良的性能,广泛
应用于各行各业,在汽车、航空、机械、石油化工等行业均受到认可和青睐。
铸轧工艺操作规程

铸轧工艺操作规程1、根据实际板厚调整好辊缝,并将轧辊转动用纤维粘将辊面清理干净,新辊需用棉纱粘四氯化碳将轧辊油渍清理干净,并用液压气喷涂枪携带压缩空气将轧辊辊面温度烘烤到50-60℃,并根据实际板宽清理边部积炭;2、磨耳子:用120目的纱纸贴严轧辊,将软耳子弧度磨成与两辊完全吻合,磨好后将轧辊辊面清理干净;3、检查设备正常后开始安装铸咀:4. 软质铸咀的组装:4.1从保温炉内,将成型的咀扇和垫块取出。
4.2在安装铸咀前先检查铸咀实际尺寸是否符合生产规格尺寸;4.3、检查铸咀是否损坏,如有损坏需更换咀扇;4.4按铸轧宽度要求,将供料咀放在小车支撑上,对中供料咀小车,咀子后部与咀子小车金属支撑平齐;4.5保证上下咀扇平齐,凸出金属支撑尺寸一致,咀子端部与轧辊中心线平行。
4.6稍稍拧紧压紧螺丝,从两边至中间对称逐个拧紧,每个螺丝拧紧程度要均匀,保证供料咀牢固、不变形。
4.7 调整4.7.1 将供料咀小车缓慢推入两辊间,在侧面观察咀端与铸轧辊是否对中,要求上、下咀唇应同时接触上、下辊面。
4.7.2沿咀子宽度数点测量咀端与轧辊中心线的距离,两边间距要求一致。
4.7.3 将进给小车退回,固定好咀子,并保持辊缝。
4.7.4 启动轧机,使轧辊快速倒转。
4.7.5 将进给小车推入, 使咀子与辊面接触,向前推进3mm左右磨咀子。
4.7.6 将咀子退出检查,要求上、下咀唇磨削对称,沿整个宽度均匀一致。
4.7.7重新推入, 每次推进3mm左右磨咀子,直至获得要求的铸轧区及咀辊间隙(上:0.5mm,下0.8mm)为止,停止轧辊转动。
4.7.8 测量铸轧区,当达到要求的数值时,标记好进给小车的位置,退出咀子,并吹扫干净。
4.7.9重新把小车推入到原来位置,并退后2~3mm。
4.8 固定边部耳子4.8.1 在咀子两侧插入磨好的软耳子,推到与上下轧辊吻合为止。
4.8.2 装好硬质副耳子,硬质耳子不能与上下辊接触,拧紧边部紧固螺丝。
铸轧工艺流程

铸轧工艺流程铸轧工艺流程指的是将铸造件经过一系列的热处理和机械加工过程,最终得到所需形状和性能的金属产品的工艺流程。
下面将以铸轧钢板的工艺流程为例,详细介绍铸轧工艺流程。
首先,铸轧工艺的第一步是选择合适的原材料。
原材料应具有良好的冶金性能和可锻性,一般选用的是高品质的钢坯。
这些钢坯需要经过化学成分分析和物理性能检验,确保其质量符合要求。
接下来是钢坯的预热处理。
在预热炉中,将钢坯加热至适当的温度,主要目的是消除材料中的内部应力,使钢坯具有更好的可锻性。
然后是铸轧。
铸轧是将预热后的钢坯倒入连续铸造机中,经过连铸机的铸造过程,将其变成连续的铸坯。
在连铸机中,钢坯被连续地浇注成带有一定截面尺寸的铸坯。
接下来是加热处理。
铸坯经过冷却后,会存在着各种缺陷和内应力。
因此,需要将铸坯再次进行加热处理,将其加热至适当的温度,使其内部结构重新组织,并消除缺陷和应力。
然后是轧制。
将加热后的铸坯送入轧机进行轧制。
轧制过程中,铸坯会不断变形,经过多次轧制,逐渐减小截面尺寸,并达到所需的材料性能。
接下来是冷却。
轧制后的铸坯需要进行冷却处理,以使其内部结构得到进一步调整和稳定。
冷却处理通常包括空冷和水冷两个阶段。
空冷是将铸轧件暴露在室温环境中进行自然冷却;水冷是将铸轧件浸入冷却水中进行快速冷却。
然后是去皮和去毛刺。
经过轧制和冷却处理后,铸轧件的表面通常会出现一些不平整和毛刺。
为了提高铸轧件的表面质量,需要对其进行去皮和去毛刺的处理,使其表面光滑。
最后是尺寸修整。
完成以上工序后,铸轧件的外形尺寸可能还需要进行修整。
这通常通过切割、修磨等加工方法来实现。
总结起来,铸轧工艺流程包括原材料选择、预热处理、铸轧、加热处理、轧制、冷却、去皮和去毛刺以及尺寸修整等步骤。
每个步骤都有其特定的要求和目的,通过合理的工艺流程,可以得到满足要求的铸轧产品。
铝板的铸轧工艺

铝板的铸轧工艺
铝板的铸轧工艺是指将铝合金熔化后,通过铸造和轧制工艺制成不同尺寸和形状的铝板,以满足不同领域的使用需求。
铝板的铸造工艺包括连铸和直铸两种,其中连铸工艺是通过将熔化的铝合金倒入连续铸造机中进行连续铸造,制成厚度较薄的板材;而直铸工艺则是通过将熔化的铝合金倒入铸模中进行单次铸造,制成厚度较厚的板材。
铝板的轧制工艺包括热轧和冷轧两种,其中热轧工艺是将连铸或直铸的铝板在高温下进行轧制,以减小板材厚度并提高其力学性能;而冷轧工艺则是将热轧后的铝板在常温下进行轧制,以提高其表面质量和精度。
此外,还可以采用涂层、拉伸等工艺对铝板进行进一步加工,以满足特定的使用需求。
总的来说,铝板的铸轧工艺是一个复杂的过程,需要精密的设备和技术,并需要根据不同的需求和使用环境选择适合的工艺和材料。
铝板的应用范围广泛,包括航空航天、汽车制造、建筑装饰、电子产品等多个领域。
- 1 -。
铸轧产品质量标准
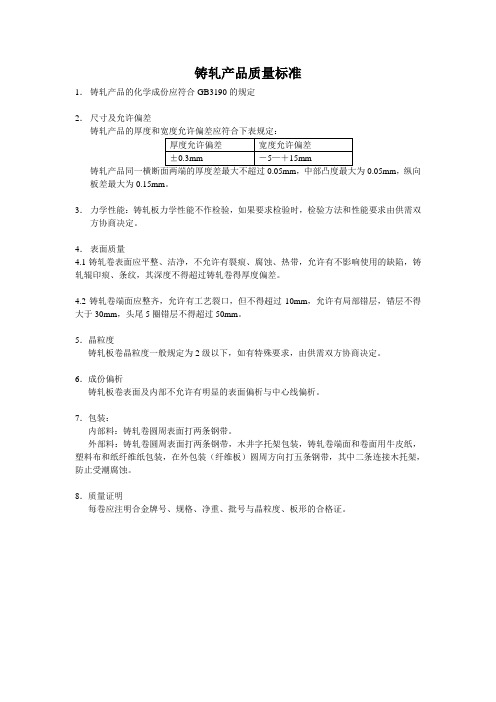
铸轧产品质量标准
1.铸轧产品的化学成份应符合GB3190的规定
2.尺寸及允许偏差
铸轧产品的厚度和宽度允许偏差应符合下表规定:
厚度允许偏差宽度允许偏差
±0.3mm-5—+15mm
铸轧产品同一横断面两端的厚度差最大不超过0.05mm,中部凸度最大为0.05mm,纵向板差最大为0.15mm。
3.力学性能:铸轧板力学性能不作检验,如果要求检验时,检验方法和性能要求由供需双方协商决定。
4.表面质量
4.1铸轧卷表面应平整、洁净,不允许有裂痕、腐蚀、热带,允许有不影响使用的缺陷,铸轧辊印痕、条纹,其深度不得超过铸轧卷得厚度偏差。
4.2铸轧卷端面应整齐,允许有工艺裂口,但不得超过10mm,允许有局部错层,错层不得大于30mm,头尾5圈错层不得超过50mm。
5.晶粒度
铸轧板卷晶粒度一般规定为2级以下,如有特殊要求,由供需双方协商决定。
6.成份偏析
铸轧板卷表面及内部不允许有明显的表面偏析与中心线偏析。
7.包装:
内部料:铸轧卷圆周表面打两条钢带。
外部料:铸轧卷圆周表面打两条钢带,木井字托架包装,铸轧卷端面和卷面用牛皮纸,塑料布和纸纤维纸包装,在外包装(纤维板)圆周方向打五条钢带,其中二条连接木托架,防止受潮腐蚀。
8.质量证明
每卷应注明合金牌号、规格、净重、批号与晶粒度、板形的合格证。
铸轧工艺操作规程

铸轧工艺操作规程铸轧工艺操作规程一、目的和范围铸轧工艺是一种重要的金属加工方式,用于生产各种不同类型、规格和形状的金属产品。
为了确保铸轧工艺的操作过程安全、高效,制定了以下操作规程。
二、操作准备1. 设备检查:在使用铸轧设备之前,应进行设备检查,确保设备正常运转,没有故障和损坏。
2. 操作台准备:清理操作台面,确保没有杂物和障碍物。
准备好所需的工具和物料。
3. 个人准备:佩戴个人防护装备,包括安全帽、护目镜、防护手套等。
三、操作流程1. 准备原材料:对于铸轧工艺,需要准备合适的原材料,包括金属块或铸锭等。
2. 车间准备:将原材料搬运到车间,并放置在适当的位置上,方便操作。
3. 加热原材料:根据需要,将原材料进行加热,以使其达到适合铸轧工艺的温度。
4. 开始铸轧:根据工艺要求,安装合适的模具和辊子,将加热后的原材料进行铸轧。
5. 控制温度:在铸轧过程中,要控制原材料的温度,以确保产品质量。
6. 冷却处理:在铸轧完成后,将产品进行冷却处理,使其达到所需的硬度和强度。
7. 修整和检查:对于铸轧成品,需要进行修整和检查,确保其外观和尺寸符合要求。
8. 成品入库:对于合格的成品,将其安全地存放在指定位置,待分发或发运。
四、安全注意事项1. 严禁在操作过程中穿戴过长的衣物,以防被夹紧;2. 操作时要保持专注,避免分心造成操作失误;3. 在操作台附近严禁乱堆放物品,以免造成绊倒事故;4. 使用金属切割和磨削工具时,必须佩戴防护手套和护目镜;5. 严禁在设备运行时使用带有金属制品的手表、项链等饰品。
五、操作记录1. 在操作过程中,应对每个操作步骤进行记录,包括操作时间、操作人员、设备状态等。
2. 如果发现任何设备故障或操作失误,应立即记录并进行报告。
六、操作完成操作完成后,应按要求完成下列工作:1. 清理操作台和设备;2. 将未使用的物料归还到指定区域;3. 关闭设备,并断开电源;4. 将记录保存到相应的文件中。
铸轧工作规范

铸轧工作规范一、装炉1、连续铸轧的原料为:铝水、铝锭、待回炉废料、中间合金、易挥发合金。
2、熔炼炉装炉顺序为:小片料---板片料----难熔难挥发合金---铝水---易挥发合金。
3、各种炉料应均匀平坦分布在炉子中央或稍靠近烟道,同时不可堵住喷嘴。
4、使用电解铝水时必须配入30%~35%的废料。
5、装炉炉料应干净,无油污、无杂质、无水分等。
6、按要求进行配料和装炉。
加料要迅速,以尽量减少炉内热量损失。
7、当炉料化平后,应向炉内均匀撒入一层覆盖剂,用量为2kg/t.Al.二、熔炼炉精炼、扒渣、提气1、炉料添加完毕后进行升温熔炼,熔炼温度控制到750℃~760℃,炉料完全融化后进行搅拌。
2、搅拌要充分,要到边到沿,搅拌操作要平稳,尽可能不破坏熔体表面氧化膜。
3、进行炉前取样,试样要在不同位置共取两个,取样时样勺距炉底约100mm。
4、通过喷粉精炼装置利用氮气将除渣剂均匀的吹入炉内,用量为1.5~2.5kg/T.Al,同时氮气流量不宜过大,以防止铝液剧烈翻腾。
5、精炼时间应不低于10分钟,精炼完静止5~15分钟后及时将表面的浮渣捞出扒净,扒渣时尽可能将铝水控净,以减少铝损失。
6、根据样品分析结果进行配料,配料完成后进行二次取样分析。
7、成份合格后(最终化学分析试样应在流槽内取样),准备进行倒炉,倒炉时熔炼炉内铝水温度合金应控制在740℃~750℃,纯铝应控制在730℃~740℃,倒炉时倒炉时间应不大于30分钟。
三、静止炉精炼扒渣1、倒炉前,静止炉炉膛温度不低于所铸造合金的铸造温度(740℃)。
2、精炼温度应高于所铸造温度上限5℃~10℃。
3、精炼剂用量表:4、精炼时间应在30分钟左右。
5、精炼完静止15~20分钟后,必须将表面浮渣扒干净,然后洒上一层覆盖剂用量为4kg/炉。
四、钛硼丝速度控制根据铸轧机速度进行调节(26.2cm/min~43cm/min)五、在线精炼装置1、准备好符合要求的氮气,纯度99.997% 压力:0.4~0.6Mpa2、氮气入口压力调至0.4~0.6Mpa 空气压力:0.2~0.5Mpa3、氮气流量:4、氮气流量不得超过5m3/h,以避免流量计浮子将流量计打坏。
双辊铸轧技术
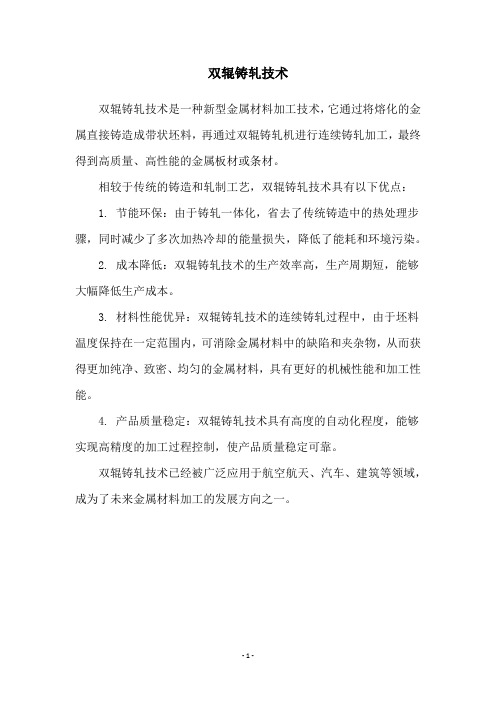
双辊铸轧技术
双辊铸轧技术是一种新型金属材料加工技术,它通过将熔化的金属直接铸造成带状坯料,再通过双辊铸轧机进行连续铸轧加工,最终得到高质量、高性能的金属板材或条材。
相较于传统的铸造和轧制工艺,双辊铸轧技术具有以下优点:
1. 节能环保:由于铸轧一体化,省去了传统铸造中的热处理步骤,同时减少了多次加热冷却的能量损失,降低了能耗和环境污染。
2. 成本降低:双辊铸轧技术的生产效率高,生产周期短,能够大幅降低生产成本。
3. 材料性能优异:双辊铸轧技术的连续铸轧过程中,由于坯料温度保持在一定范围内,可消除金属材料中的缺陷和夹杂物,从而获得更加纯净、致密、均匀的金属材料,具有更好的机械性能和加工性能。
4. 产品质量稳定:双辊铸轧技术具有高度的自动化程度,能够实现高精度的加工过程控制,使产品质量稳定可靠。
双辊铸轧技术已经被广泛应用于航空航天、汽车、建筑等领域,成为了未来金属材料加工的发展方向之一。
- 1 -。
铸轧工艺流程

铸轧工艺流程铸轧工艺是一种将铸造和轧制工艺结合在一起的金属加工工艺,主要用于生产各种形状和尺寸的金属材料。
这种工艺可以通过铸造将金属熔化成特定形状的毛坯,然后通过轧制将毛坯加工成所需的尺寸和形状。
铸轧工艺在金属材料的生产中起着至关重要的作用,本文将详细介绍铸轧工艺的流程和各个环节的工艺特点。
1. 铸造铸造是铸轧工艺的第一步,通过将金属加热至熔化状态,然后倒入预先设计好的模具中,使其冷却凝固成为特定形状的毛坯。
铸造过程中需要控制金属的温度、流动性和凝固速度,以确保最终的毛坯具有良好的内部结构和表面质量。
铸造过程中还需要考虑模具的设计和制造,以确保毛坯的形状和尺寸符合要求。
2. 热轧热轧是铸轧工艺中的关键步骤,通过将铸造好的毛坯加热至一定温度,然后通过轧机进行轧制,将毛坯加工成所需的形状和尺寸。
热轧过程中,毛坯的温度、轧制力和轧制速度都是非常重要的参数,它们直接影响着最终产品的内部结构和力学性能。
热轧还可以通过多道次的轧制和不同方向的变形,改善毛坯的晶粒结构和机械性能。
3. 冷轧冷轧是铸轧工艺中的另一个重要步骤,通过将热轧好的毛坯加工成更细的尺寸和更高的表面质量。
冷轧过程中,毛坯的温度要控制在室温或低于室温,以确保产品的表面质量和尺寸精度。
冷轧还可以通过控制轧制力和轧制速度,调整产品的硬度、强度和塑性,以满足不同的使用要求。
4. 热处理热处理是铸轧工艺中的最后一道工序,通过对产品进行加热和冷却处理,改善产品的内部结构和力学性能。
热处理可以通过调整加热温度和保温时间,改变产品的组织和性能,如提高产品的硬度、强度和耐磨性。
热处理还可以通过控制冷却速度和冷却介质,调整产品的组织和性能,如提高产品的韧性、塑性和冲击性能。
总结铸轧工艺是一种将铸造和轧制工艺结合在一起的金属加工工艺,通过铸造将金属熔化成特定形状的毛坯,然后通过热轧、冷轧和热处理将毛坯加工成所需的尺寸和形状。
铸轧工艺在金属材料的生产中起着至关重要的作用,通过控制各个环节的工艺参数,可以生产出具有良好内部结构和优良力学性能的金属产品。
铸轧机原理
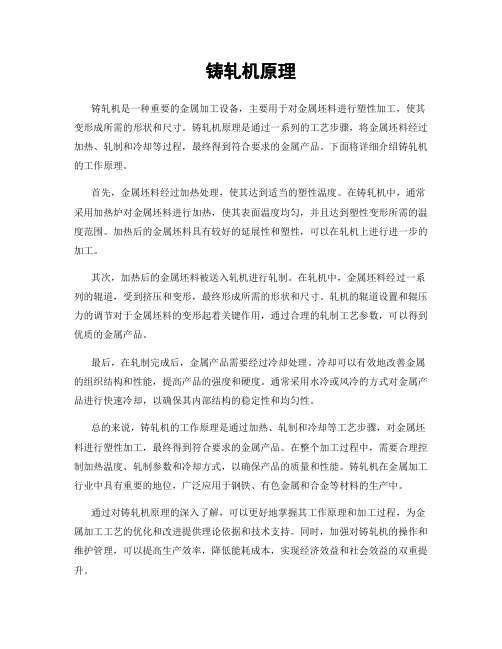
铸轧机原理铸轧机是一种重要的金属加工设备,主要用于对金属坯料进行塑性加工,使其变形成所需的形状和尺寸。
铸轧机原理是通过一系列的工艺步骤,将金属坯料经过加热、轧制和冷却等过程,最终得到符合要求的金属产品。
下面将详细介绍铸轧机的工作原理。
首先,金属坯料经过加热处理,使其达到适当的塑性温度。
在铸轧机中,通常采用加热炉对金属坯料进行加热,使其表面温度均匀,并且达到塑性变形所需的温度范围。
加热后的金属坯料具有较好的延展性和塑性,可以在轧机上进行进一步的加工。
其次,加热后的金属坯料被送入轧机进行轧制。
在轧机中,金属坯料经过一系列的辊道,受到挤压和变形,最终形成所需的形状和尺寸。
轧机的辊道设置和辊压力的调节对于金属坯料的变形起着关键作用,通过合理的轧制工艺参数,可以得到优质的金属产品。
最后,在轧制完成后,金属产品需要经过冷却处理。
冷却可以有效地改善金属的组织结构和性能,提高产品的强度和硬度。
通常采用水冷或风冷的方式对金属产品进行快速冷却,以确保其内部结构的稳定性和均匀性。
总的来说,铸轧机的工作原理是通过加热、轧制和冷却等工艺步骤,对金属坯料进行塑性加工,最终得到符合要求的金属产品。
在整个加工过程中,需要合理控制加热温度、轧制参数和冷却方式,以确保产品的质量和性能。
铸轧机在金属加工行业中具有重要的地位,广泛应用于钢铁、有色金属和合金等材料的生产中。
通过对铸轧机原理的深入了解,可以更好地掌握其工作原理和加工过程,为金属加工工艺的优化和改进提供理论依据和技术支持。
同时,加强对铸轧机的操作和维护管理,可以提高生产效率,降低能耗成本,实现经济效益和社会效益的双重提升。
铸轧机原理的研究和应用将为金属加工行业的发展和进步注入新的动力,推动行业向高质量、高效率、低能耗的方向迈进,为实现可持续发展作出积极贡献。
希望本文所介绍的铸轧机原理内容能够对相关领域的专业人士和学习者有所帮助,促进铸轧机技术的进步和创新。
一种计算铸轧区长度的方法

一种计算铸轧区长度的方法随着工业化进程的不断推进,铸轧技术越来越受到人们的关注。
铸轧是一种将铸造与轧制相结合的技术,通过铸造得到铸坯,再通过轧制加工成所需形状和尺寸的金属材料。
在铸轧过程中,铸轧区长度是一个非常重要的参数,它直接影响到金属材料的质量和加工效率。
本文将介绍一种计算铸轧区长度的方法,以帮助铸轧工程师们更好地控制铸轧过程。
一、铸轧区长度的定义铸轧区长度是指铸坯在轧机入口处到达其最终尺寸之前所经过的长度。
它是由铸坯的形状、尺寸、轧制工艺和轧机参数等因素决定的。
铸轧区长度的大小直接影响到轧制工艺的稳定性和金属材料的质量,因此在铸轧过程中,必须对铸轧区长度进行严密的控制。
二、传统的计算铸轧区长度的方法目前,传统的计算铸轧区长度的方法主要有两种:一种是基于经验公式的计算方法,另一种是基于数值模拟的计算方法。
基于经验公式的计算方法是通过对铸轧过程中的经验数据进行统计和分析,得出一个适用于大多数情况的计算公式。
这种方法简单易行,但是由于其基于经验数据,所以计算结果的精度较低,不够准确。
基于数值模拟的计算方法是通过建立数学模型,利用计算机进行模拟计算,得出铸轧过程中各个参数的变化规律和铸轧区长度的大小。
这种方法精度较高,但是需要较高的计算能力和较长的计算时间,不够实用。
三、一种新的计算铸轧区长度的方法针对传统的计算铸轧区长度方法存在的问题,我们提出了一种新的计算方法。
这种方法基于机器学习算法,通过对铸轧过程中的数据进行训练,得出一个适用于各种情况的计算模型。
具体步骤如下: 1. 数据采集:我们在铸轧过程中,采集了大量的数据,包括铸坯的形状、尺寸、轧制工艺和轧机参数等因素。
这些数据将作为训练数据,用于训练机器学习算法。
2. 特征提取:我们对采集的数据进行特征提取,将其转化为机器学习算法可以处理的形式。
这一步是非常关键的,它直接影响到机器学习算法的准确性和性能。
3. 训练模型:我们使用机器学习算法对提取的数据进行训练,得出一个适用于各种情况的计算模型。
- 1、下载文档前请自行甄别文档内容的完整性,平台不提供额外的编辑、内容补充、找答案等附加服务。
- 2、"仅部分预览"的文档,不可在线预览部分如存在完整性等问题,可反馈申请退款(可完整预览的文档不适用该条件!)。
- 3、如文档侵犯您的权益,请联系客服反馈,我们会尽快为您处理(人工客服工作时间:9:00-18:30)。
铝及铝合金基本知识介绍1.1铝的性质(1)密度小:密度范围在2.63-2.85g/cm3之间,一般计算时取2.7g/cm3;(2)导电性和导热性好;(3)化学性比较活泼:主要由于铝的晶体结构为面心立方结构;(4)塑性和延伸性好,具有良好的加工性能。
1.2铝合金的分类铝合金分为以下几种:1.3变形铝合金牌号表示方法采用国际四位数表示方法:第一位数:表示合金系;第二位数:在纯铝中表示受控杂质的个数;在铝合金中表示对原合金改进的次数;第三、四位数:在1×××中表示Al 含量百分小数点后的最低含量;在其他系列中无特殊意义,只是为了相互区别。
例如:1100合金其中“00”表示铝的含量为99.00%,1235合金其中“35”表示铝的含量为99.35%。
熔炼部分熔炼目的:获得化学成分,温度符合要求,纯洁度高的熔体。
1.1 熔炼的设备熔炼的设备分为熔炼炉和保温炉(或称静置炉),蓄热式烧嘴熔炼炉如下图:我公司的熔炼炉采用是燃油火焰反射炉(0#轻柴油),现有铸轧炉组是“黑格慕林”提供的双通道热交换(雾化空气)反射炉。
炉组容量为:熔炼炉25吨,静置炉30吨。
1.2 熔炼炉内气氛熔炼炉内气氛:指熔炼炉内的气体组成。
熔炼时炉内气氛包括空气、燃烧物及燃烧产物。
炉内气氛随熔炼炉型及结构所用燃料的不同而含有不比例的H 2、Q 2、H 2O 、CO 2、CO 、N 2、SO 2、及碳氢化合物。
熔炼炉示意图燃油反射炉内气体:氧、二氧化碳、一氧化碳、氢水蒸气,溶解在铝合金熔体中最主要的气体是氢,铝合金在熔炼过程中易吸气(超温更为严重)和氧化,从而使铝熔体中含有大量的夹杂物。
造成炉气不稳定和燃烧状态不同,炉内有大量的H2O,主要来源:炉料燃料中吸附水分(空气,燃油),此外炉气中水蒸汽含量还与环境的湿度有关,湿度越大,炉气中水蒸汽含量越多。
根据铸轧实际生产情况:氢的溶解是在铝液中最易溶解的气体,其含量在所溶解的气体占90%。
氢是造成铸轧及下道工序产生气孔,疏松板带,起皮的重要原因(铝合金在熔炼过程中易吸氢和氧化从而使铝熔体中含有大量的夹杂物)。
减少氢含量的措施:(1)减少炉料含水量。
(2)控制炉气性质(不超温,炉前准备)。
(3)采用覆盖剂覆盖。
(4)彻底精炼除气。
常用有覆盖剂、精炼剂、清炉剂、打渣剂。
覆盖剂是碱土金属氯化物。
作用:(表面张力小,润湿性好)覆盖隔离铝液,减少铝液吸气和烧损。
精炼剂(氟化物)作用:吸附溶解的AL2O3等夹渣,便于渣铝分离,增大净化效果(精炼,过滤)。
1.3熔炼工艺流程熔炼工艺流程如下:熔炼炉的准备(烘炉、洗炉、清炉)—备料—投料—熔化(点火-停火)—(搅拌)—预分析—配料—搅拌—精炼—扒渣—转炉(1)熔炼炉准备烘炉:新、中、大修后,炉子都要按烘炉制度进行烘炉,以驱赶潮气;清炉:将炉内残留渣彻底清出炉外以保证炉膛清洁。
洗炉:将残留在熔池里的不合格成分金属和炉渣清除干净以免污染其它合金。
清炉:将炉内残留渣彻底清出炉外以保证炉膛清洁。
在熔炼过程中出现炉渣,经过扒渣后,还会吸附在炉底和炉壁上。
日积月累后占据了炉子大量地方,导致投料量的减少,大量的炉渣污染Al熔体,提高了柴油烧损能力(最不可取),加大各种有害气体存在的可能,所以必须清炉。
清炉分为冷清炉和热清炉两种。
(2)备料根据工艺要求,将纯铝锭、废料、再生锭等(或电解铝水)准备在料斗(或真空包)中。
废料根据其厚度、形状、污染程度分为一级废料、二级废料、三级废料。
一级废料为立板废卷、放流块板样、废卷1.2mm以上冷轧废料,2.0mm以上冷轧切头、切尾料。
适用加入高要求产品内(如BP等产品),而且按工艺要求的比例加入。
废料越薄,其烧损(即损失量的百分比)越大,造渣越厉害,对产品质量不利。
我公司废料标色:红色为(1235、1050合金);绿色为(1100、8011合金);黑色为(3003合金);黄色为(3105合金);蓝色为(5052、5005合金)备料时的数量必须估算准确,防止炉料太多使铝液溢出。
(3)投料即将备好的料投入熔炼炉中。
为减少烧损,装炉时先装小块料,后装薄板废料、大块料,最后装铝锭。
(4)熔化(点火-停火)点火时间需保证铸轧过程的连续性,同时保证铝水在熔炼炉停留时间尽可能短。
停火时间主要控制熔体的熔炼温度。
铝的熔点为660℃,理论上铝合金的熔炼温度应在液湘线上方50~100℃,在700~750℃左右,实际上根据产品质量的要求进行具体确定熔炼温度。
(5)预分析、配料预分析:即在熔炼炉两个炉门附近取样去化验。
配料:根据预分析结果和产品规定的化学成分要求,进行配料计算,确定添加剂、中间合金的添加量,往熔体加添加剂、中间合金,调整熔体化学成分,以符合产品化学成分要求。
铸轧所使用的添加剂一般有铁剂、铜剂、锰剂、钛剂,合金含量为75%左右。
即重量2Kg的添加剂,其所含铁、铜、锰、钛只为2*0.75=1.5Kg。
其余0.5Kg为助溶剂、粘结剂等。
铸轧所使用的中间合金有铝硅锭、镁锭。
由于添加剂、中间合金等在使用过程中存在损失现象,故存在实收率概念。
实收率的计算公式为:X=(熔体重量×熔体中所增加金属元素的质量百分数/添加剂中的纯金属质量)×100%例如:熔炼炉内铝液重量20500kg,预分析成份:Fe0.11%,Si0.08%,为提高铁含量,加入Fe75添加剂20kg,再次分析成分Fe0.18%,试计算铁添加剂的实收率。
X=[(20500+20) ×(0.18%-0.11%)/20×75%]×100%配料计算公式为:熔体重量×熔体中所增加金属元素的质量百分数熔炼炉内20吨3003合金,预分析成份Mn0.90%,要求将锰含量提高到1.05%,应加入多少锰75。
X=20000×(1.05%-0.90%)/75%(6)搅拌为了获取均匀的化学成分及加快熔化过程。
现在新上熔炼炉一般利用电磁搅拌设备进行搅拌操作。
(7)精炼、扒渣精炼时在熔炼炉内的精炼温度应控制在熔炼温度上限,利用惰性气体作为载体,将精炼剂通入熔体的过程。
目的:除去熔体中的各种夹渣物、氢气。
要求:精炼均匀、无死角。
(8)转炉将熔炼炉中的铝熔体引入保温炉(或称静置炉)的过程。
要求:转炉过程必须潜流(即铝水在氧化膜底部流动,不与空气接触的过程),在保证潜流的情况下,为了减少再次造渣、吸气,尽量缩短转炉时间。
铸轧部分1立板操作(1)立板前准备工作A、将静置炉内的铝液温度调整至750℃±10℃(冬季取上限,夏季取下限);B、检查流槽系统是否结合紧密,将各种立板工具放在合适位置;C、根据板宽调整石墨喷涂限位,装配好前箱热电偶;D、启动机列检查设备各部位系统是否正常(冷却水)。
(2)铸嘴位置调整A、把经烧烤的铸咀组合件吊到铸轧机上,在铸嘴平台上对好位置紧固好B、将铸嘴水平位置调至适当值C、将铸嘴缓慢地移向辊缝,调整垂直和水平位置使之达到预定的铸轧区长度范围,并观察铸嘴与上下辊之间的间隙最佳状态(3)放流:A、当立板准备工作完成后,操作人员按分工进入各岗位;B、打开保温炉流眼,用铝液预热流槽及前箱,预热用的铝液通过放流槽流入渣箱;C、当前箱温度达700℃时搅拌流口箱及过滤箱,清理沉积在底部的铝渣。
(4)立板(跑渣型立板)(直接立固体板):A、立板前辊表面线速度设定(1200~1800)mm/min(根据规格厚度而定);B、当前箱温度达720~730℃时,拔出前箱流口堵头,让铝液流入铸嘴;C、观察铝液在辊缝中分布和结晶情况,调整液面高度和铸轧速度。
直至出现完整的固体板,并让铸轧带通过导向辊剪切机刀口,直至卷取机;D、用干净的棉布和砂布擦去轧辊污染痕迹;E、启动石墨喷涂系统调整喷涂行程和喷涂量;F、随着前箱温度的降低逐渐提高铸轧速度至设定值,稳定后取板型样测量厚度宽度,两边厚差,中凸度等,确定测量值合格后,开始卷取成品;G、打开除气装量,并根据不同产品添加细化钛杆;H、正常铸轧过程中,必须做好各参数记录。
(5)立板注意事项总结:保温炉的温度750℃是否达到;Al液质量是否大于等于12T;过滤片是否放置正确,加温正确;除气炉的保温温度是否达到,各段的流槽的保温是否到位;工具的完备情况;渣箱,放流箱是否准备好,各流口是否已处理好;劳保的穿戴情况;各操作手与配合人员的劳保是否穿戴整齐,工作的精神可好;检查设备的运行情况,运行是否良好。
每一次立板的成功,凭个人的努力是不行的,操作手与配合人员紧密合作是很重要的一环。
2铸轧工艺参数的调整1.1铸轧机型铸轧机型国内常见的为水平式和倾斜式,水平式即牌坊架垂直于水平方向,倾斜式即牌坊架与垂直方向成15度。
为什么铸轧机要倾斜?原因:(1)更好控制前箱液位;(2)上下辊热传导更为均匀;(3)铸咀结构简单,不像水平式上下面长短不一致;1.2铸轧主要工艺参数铸轧主要的工艺参数有:铸轧区长度,铸轧速度,浇注温度,冷却强度和凝固瞬间的铝熔体供给所需的静压力。
各工艺参数处于一个动态的平衡中。
(1)铸轧区即铸嘴位置到上下轧辊中心线的距离。
铸轧整个过程就在铸轧区中完成。
铸轧区分为三个区:Z1是铝熔体冷却到结晶温度的冷却区域,Z2是铝熔体完成铸造过程的铸造区,Z3是两辊对铸坯进行轧制的变形区。
如图所示:A、决定铸轧区长度的主要因素:(a)铸轧辊直径铸嘴开口一定时,铸轧辊直径越大,铸轧区长度也越大。
(b)冷却条件及加工变形率铸轧区越长,需要传递的热量也越多。
由于辊内的冷却水流量只能达到一定值,影响辊套的热交换量。
因此,铸轧区长度受到限制。
B、铸轧区长度计算:(a)理论计算:L≈(R*△h)1/2其中△h=(H-h)H为铸嘴总开口+嘴辊缝隙(一般为2mm);h为辊缝值;例如:上、下轧辊辊径分别为781、783mm,WS、DS侧辊缝为6.231mm、6.225mm,铸嘴总开口为11.1mm,则铸轧区L≈(R*△h)1/2={(781+783)/2*[(11.1+2)-(6.231+6.225)/2]}1/2 ≈52mm例题:假设铸轧辊直径为1000mm,铸嘴内开口为7mm,铸嘴唇口厚度为2.7mm,辊缝设定6.4mm,请推导铸轧区公式并计算铸轧区长度为多少?解:H=铸嘴内开口+2*铸嘴唇厚度+嘴辊间隙h=辊缝=6.4mm△h=H-h=14.4-6.4=8mmZ2=R2-(R-1/2△h)2Z=63.2mm(b)实际测量:铸轧区L=测量长度-上下轧辊半径的平均值R,测量方法如下图所示:C、铸轧区长度的调整:通过调节铸嘴平台的水平位置(电机的转动)进行调整,调整时注意控制铸嘴板与辊面之间的间隙,防止间隙过大,造成漏铝。
(2)铸轧速度指轧辊的速度。
在生产中,指铸轧带坯速度(通过导出辊处的编码器测定)。