1000万吨常减压装置标定报告常减压装置标定核算报告
1000万吨年常减压装置节能成效分析与对策
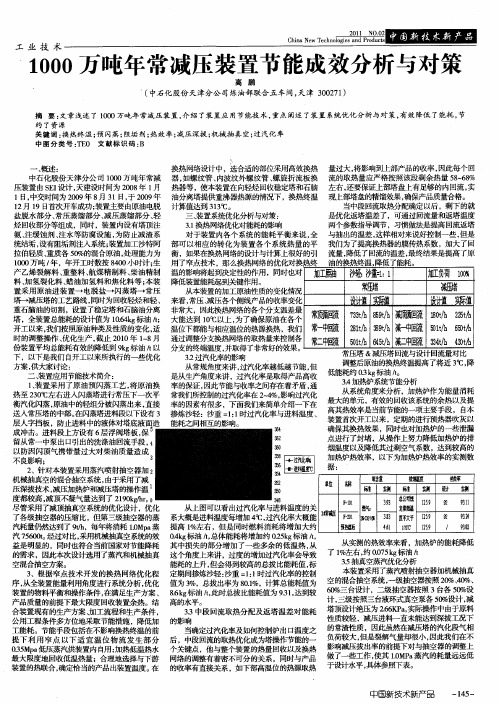
约 了资源 关 键词 : 热 终 温 ; 闪蒸 ; 换 预 阻垢 剂 ; 热效 率 ; 压深 拔 ; 械抽 真 空 ; 汽化 率 减 机 过
g- q -  ̄
2 2
点进行 了封堵 , 从操 作上努力降低加热 炉 的排 烟温度 以及 降低其过剩空气 系数 ,达到较高 的 加热炉热效率 ,以下为加热炉热效率的实测数 据
名: l { 营 撞
3 总 可 l9 9 3 公擐 2 S
单 位
揪车 设 计
蛇 蛇 91 3 1 92 3 隼
工 业技 术
Cae eoinrc 嵋 瞄瞄 -■ h hosdo t 啊 ■■■ _ i w c一 ds n TngaPu圈圆团圜圈阉 N l e ●
10 0 0万吨年常减压装置节能成效 分析 与对策
高 鹏
( 中石化 股份 天津分公 司炼 油部联合五车 间, 津 3 0 7 ) 天 0 2 1
摘 要 : 文作 者通 过 对 电力 系统 中的干 扰 来 源进 行 了分析 , 本 同时 结合 多年 的 工作 实践 主要 就 电力 系统 中继 电保 护 装置 可采 取 的 抗
干扰措 施 和 实施 方法进 行 了探 讨 。
关键 词 : 电保护 ; 置 ; 干扰 ; 施 继 装 抗 措
中 图分 类号 :M7 文献 标 识码 : T B
1 电力系统 中的干扰来源及分类 . 干扰 的分类有 多种方 法, 有以下几种: 主要
干扰
(j频率范围划允 干扰可以分为低频干扰 1安 1
常减压装置大负荷标定数据分析

常减压装置大负荷标定数据分析吴晓江;周超;曹阳【摘要】通过对四川石化公司的常减压装置迸行标定,考察了物料平衡、加热炉及主要设备的运行情况.发现了设计值和实际值之间的差距及高负荷下影响装置运行的瓶颈.常顶油收率和总拔出率可分别达到19.37%和76.04%,达到了设计要求.常压炉和减压炉的热效率分别达到93.75%和93.59%,优于设计值,同时综合能耗达到了337.70 MJ/t,远低于设计值,表明装置操作满足了设计要求.【期刊名称】《炼油与化工》【年(卷),期】2017(028)002【总页数】4页(P19-22)【关键词】物料平衡;标定;瓶颈;高负荷;生产优化【作者】吴晓江;周超;曹阳【作者单位】四川大学化学工程学院,四川成都 610065;中国石油四川石化有限责任公司生产一部,四川成都 611930;中国石油四川石化有限责任公司生产一部,四川成都 611930【正文语种】中文【中图分类】TE624.3四川石化公司的常减压装置设计加工能力为1 000×104t/a,设计操作弹性为60%~110%,设计开工时数为8 400 h/a。
装置主要由换热网络、电脱盐、闪蒸塔、常压炉、常压塔系统、减压炉、减压塔系统等部分组成[1]。
装置采用高速电脱盐技术,窄点技术优化换热网络,充分利用装置余热,加热炉设空气预热系统,降低排烟温度,提高加热炉效率,减压抽真空系统采用三级抽真空技术,其中第三级采用液环式真空泵。
装置控制系统采用横河CS3000集散控制系统(DCS),并设置紧急停车和安全连锁保护系统(SIS)、先进控制系统(APC)及气体报警系统(GDS)。
装置标定的时间为2015年10月28日09:00~10月31日09:00,共72 h。
标定目的是掌握装置高负荷生产的实际运行状况,各项指标能否达到设计要求,主要包括6项内容。
(1)考察装置加工量在1 190.5 t/h加工负荷时加热炉的实际运行能力和效果。
常减压装置HAZOP分析报告1.27

常减压装置HAZOP分析报告1.27自查报告。
报告标题,常减压装置HAZOP分析报告1.27。
报告日期,2023年5月15日。
报告对象,公司管理部门。
报告内容:
根据公司安全管理要求,我们对常减压装置进行了HAZOP分析,并现将分析结果报告如下:
1. 设备名称,常减压装置。
2. 分析日期,2023年5月10日。
3. 分析人员,工艺工程师、设备操作人员、安全主管等。
4. 分析内容:
a. 设备操作过程中可能出现的危险情况,压力过高、温度过高、阀门失灵等。
b. 可能导致危险情况的原因,设备老化、操作不当、设备故障等。
c. 针对每种危险情况的应对措施,定期检查设备、加强操作培训、设备维护保养等。
5. 结论,经过HAZOP分析,我们发现常减压装置存在一些潜在的危险情况,但通过加强管理和维护,可以有效降低这些风险,确保设备安全稳定运行。
6. 建议,建议公司加强对常减压装置的管理和维护,定期进行设备检查和操作培训,确保设备安全运行。
以上是我们对常减压装置进行HAZOP分析的报告,希望能够得到公司的重视和支持,共同确保设备安全运行。
报告人,XXX(签名)。
报告单位,XXX 公司(盖章)。
报告日期,2023年5月15日。
1000万吨常减压蒸馏装置腐蚀及防腐
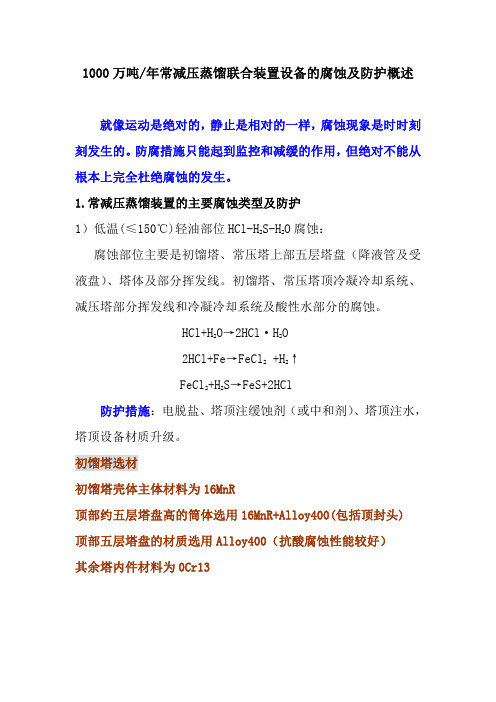
1000万吨/年常减压蒸馏联合装置设备的腐蚀及防护概述就像运动是绝对的,静止是相对的一样,腐蚀现象是时时刻刻发生的。
防腐措施只能起到监控和减缓的作用,但绝对不能从根本上完全杜绝腐蚀的发生。
1.常减压蒸馏装置的主要腐蚀类型及防护1)低温(≤150℃)轻油部位HCl-H2S-H2O腐蚀:腐蚀部位主要是初馏塔、常压塔上部五层塔盘(降液管及受液盘)、塔体及部分挥发线。
初馏塔、常压塔顶冷凝冷却系统、减压塔部分挥发线和冷凝冷却系统及酸性水部分的腐蚀。
HCl+H2O→2HCl·H2O2HCl+Fe→FeCl2 +H2↑FeCl2+H2S→FeS+2HCl防护措施:电脱盐、塔顶注缓蚀剂(或中和剂)、塔顶注水,塔顶设备材质升级。
初馏塔选材初馏塔壳体主体材料为16MnR顶部约五层塔盘高的筒体选用16MnR+Alloy400(包括顶封头)顶部五层塔盘的材质选用Alloy400(抗酸腐蚀性能较好)其余塔内件材料为0Cr13常压塔选材壳体材料根据介质在不同的温度下的不同的腐蚀机理和腐蚀速率分别选用16MnR+0Cr13A1、16MnR+304L、16MnR+316L,塔内件材料亦分别选用0Cr13、304L(304不锈钢成分为0Cr18Ni9 C <0.1 Cr 18% Ni9%)、316L(316的不锈钢成分为0Cr17Ni12Mo2 C <0.1 Cr 17% Ni12% Mo2%) 2) 高温硫化物、环烷酸腐蚀及冲腐腐蚀部位主要是240~400℃与原油、馏分油接触的设备与管道。
Fe+S→FeSFe+2RCOOH→Fe(RCOO)2+ H2↑Fe+ H2S→FeS+H2↑FeS+2RCOOH→Fe(RCOO)2+H2S环烷酸腐蚀的特点:(1)220℃时,环烷酸腐蚀已开始,随着温度的升高腐蚀加剧;(2)270~280℃时环烷酸腐蚀较剧烈,以后随温度的上升而逐渐减弱;(3)280~380℃时环烷酸腐蚀急剧增加。
1000万吨年常减压工艺管道施工组织设计

A2施工组织设计(方案)报审表审批表中国石油广西石化1000万吨/年炼油工程常减压蒸馏装置工艺管道施工方案中国石油一建广西项目经理部目录1. 编制说明 (1)1.1工程说明 (1)1.2编制依据 (1)2. 工程概况 (1)2.1施工内容和施工范围 (1)2.2计划开、竣工日期 (1)2.3工程实物量 (2)2.4工程设计参数及工艺特点 (2)3. 施工进度计划 (4)4. 主要施工方法 (5)4.1施工原则、工序 (5)4.2 施工方法及步骤 (6)4.3管线焊接 (9)4.4焊接工艺 (13)4.5焊接检验 (15)4.6 管道安装 (17)4.7伴热管安装 (21)4.8管道试压 (22)4.9 管道吹扫、清洗 (22)4.10 管道的防腐与保温 (22)5. 质量保证措施 (22)5.1质量目标 (22)5.2施工质量措施 (23)6. 安全技术措施 (24)6.1安全目标 (24)6.2施工安全措施 (24)7. 劳动力需求计划 (24)8. 主要施工机具和设备配置计划 (25)9. 施工手段用料 (26)附件:现场平面布置图。
(28)1. 编制说明1.1工程说明·中国石油广西石化1000万吨/年炼油工程的常减压蒸馏装置属于新建工程,该项目位于广西壮族自治区钦州市钦州港经济开发区,占地面积为23940平方米。
装置原油来源于苏丹油,采用海上运输。
装置由换热、电脱盐、闪蒸塔、常压炉、常压塔系统、减压炉、减压塔系统、气体压缩、一脱三注等部分组成。
·本工程由中国石油天然气华东勘察设计院设计,抚顺诚信石化工程建设监理有限公司监理,中国石油天然气第一建设公司负责施工。
1.2编制依据·国家和石油部颁发现行施工验收规范及质量验评标准。
·公司质量、HSE管理手册及程序文件。
·广西石化公司的有关规章制度。
·《工业金属管道施工及验收规范》GB50235-97。
1000万吨常减压静设备方案
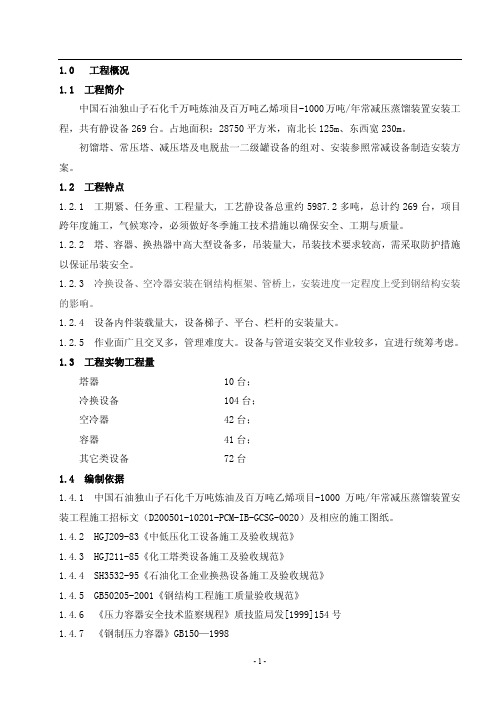
1.0 工程概况1.1 工程简介中国石油独山子石化千万吨炼油及百万吨乙烯项目-1000万吨/年常减压蒸馏装置安装工程,共有静设备269台。
占地面积:28750平方米,南北长125m、东西宽230m。
初馏塔、常压塔、减压塔及电脱盐一二级罐设备的组对、安装参照常减设备制造安装方案。
1.2 工程特点1.2.1 工期紧、任务重、工程量大, 工艺静设备总重约5987.2多吨,总计约269台,项目跨年度施工,气候寒冷,必须做好冬季施工技术措施以确保安全、工期与质量。
1.2.2 塔、容器、换热器中高大型设备多,吊装量大,吊装技术要求较高,需采取防护措施以保证吊装安全。
1.2.3 冷换设备、空冷器安装在钢结构框架、管桥上,安装进度一定程度上受到钢结构安装的影响。
1.2.4 设备内件装载量大,设备梯子、平台、栏杆的安装量大。
1.2.5 作业面广且交叉多,管理难度大。
设备与管道安装交叉作业较多,宜进行统筹考虑。
1.3 工程实物工程量塔器 10台;冷换设备 104台;空冷器 42台;容器 41台;其它类设备 72台1.4 编制依据1.4.1 中国石油独山子石化千万吨炼油及百万吨乙烯项目-1000万吨/年常减压蒸馏装置安装工程施工招标文(D200501-10201-PCM-IB-GCSG-0020)及相应的施工图纸。
1.4.2 HGJ209-83《中低压化工设备施工及验收规范》1.4.3 HGJ211-85《化工塔类设备施工及验收规范》1.4.4 SH3532-95《石油化工企业换热设备施工及验收规范》1.4.5 GB50205-2001《钢结构工程施工质量验收规范》1.4.6 《压力容器安全技术监察规程》质技监局发[1999]154号1.4.7 《钢制压力容器》GB150—19981.4.8 《空冷式换热器》GB/T15386—941.4.9 《钢制塔式容器》JB4710-922.0施工程序2.0 施工程序2.1 整体到货立式设备/塔器安装程序整体到货的小型设备可以使用50吨吊车进行吊装,超过20m高的设备和超过25t的设备采用100吨履带吊进行整体吊装。
我国第一套千万吨级常减压蒸馏装置的设计与运行
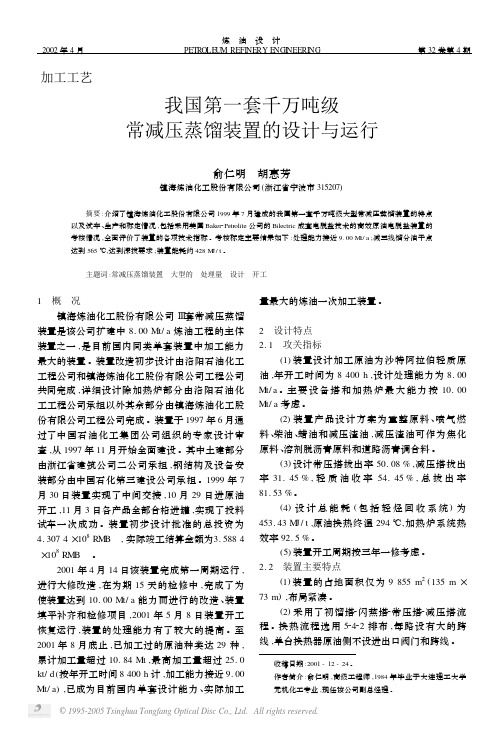
—3 —
燃料 、柴油 、加氢裂化原料 (或催化裂化原料) 以及 盐装置进行了一次考核标定 。从标定的结果以及
液化石油气 、轻石脑油等产品或中间产品 。装置 生产情况来看 ,电脱盐装置达到了考核指标 ,脱后
能耗降低到 449. 24 MJ / t ,达到了设计指标 ,成为国 原油盐浓度降至 0. 5 mg/ L (混合样) ,水分在 0. 2 %
现在装置能适应 14. 0~25. 0 kt/ d 的加工负 荷 ,灵活性较大 。能生产重整原料 (石脑油) 、喷气
© 1995-2005 Tsinghua Tongfang Optical Disc Co., Ltd. All rights reserved.
第 4 期 俞仁明等. 我国第一套千万吨级常减压蒸馏装置的设计与运行
(3) 大型装置所选用的机泵设备等均较大 , 6 000 V的高压电动机较多 ,这些机泵设备的扬程 、 排量和运转时的噪声均较大 ,这就要求在设计选 择机泵时应该多方面考虑 ,从装置设计的负荷范 围到机泵排量 、扬程的匹配 ,从机泵基础到出入口 管道 、阀门的设置 ,从机泵的封油 、冷却和预热设 施到后续管路 、冷换设备 、调节机构的选型以及电 动机的匹配和适当的降噪声设施等方面均要比小 型装置设计考虑周全 。从装置试车与生产的角度 来看 ,机泵试运行 、水冲洗 、水联运时特别要注意 不得使电动机超负荷操作 , 必 要 时 可 关 小 泵 出 口阀 。
主题词 :常减压蒸馏装置 大型的 处理量 设计 开工
1 概 况 镇海炼油化工股份有限公司 Ⅲ套常减压蒸馏
装置是该公司扩建中 8. 00 Mt/ a 炼油工程的主体 装置之一 ,是目前国内同类单套装置中加工能力 最大的装置 。装置改造初步设计由洛阳石油化工 工程公司和镇海炼油化工股份有限公司工程公司 共同完成 ,详细设计除加热炉部分由洛阳石油化 工工程公司承担以外其余部分由镇海炼油化工股 份有限公司工程公司完成 。装置于 1997 年 6 月通 过了中 国 石 油 化 工 集 团 公 司 组 织 的 专 家 设 计 审 查 ,从 1997 年 11 月开始全面建设 。其中土建部分 由浙江省建筑公司二公司承担 ,钢结构及设备安 装部分由中国石化第三建设公司承担 。1999 年 7 月 30 日装置实现了中间交接 ,10 月 29 日进原油 开工 ,11 月 3 日各产品全部合格进罐 ,实现了投料 试车一次成功 。装置初步设计批准的总投资为 4. 307 4 ×108 RMB , 实际竣工结算金额为3. 588 4 ×108 RMB 。
年处理1000万吨原油常减压、配套装置及公用工程项目可行性研究报告

年处理1000万吨原油常减压、配套装置及公用工程项目可行性研究报告编制单位:北京大唐汇泽投资顾问有限公司目录第一章项目总论 (7)1.1项目概况 (7)1.1.1项目名称 (7)1.1.2项目承建单位 (7)1.1.3拟建设地点 (7)1.1.4建设内容与规模 (7)1.1.5项目性质 (8)1.1.6项目总投资及资金筹措 (9)1.1.7建设期 (9)1.2编制依据和原则 (10)1.2.1编制依据 (10)1.2.2编制原则 (10)1.3项目投资单位介绍 (11)1.4主要技术经济指标 (11)1.5可行性研究结论 (12)第二章项目背景及必要性分析 (13)2.1项目建设背景 (13)2.1.1 项目发展背景介绍 (13)2.1.2行业发展前景 (31)2.2项目必要性 (32)2.2.1工程的建设是XX市城市发展的需要。
(32)2.2.2 本工程的建设是发挥靖江资源优势发展外向型经济的需要。
(33)2.2.3本项目的建设是促进液体化工、燃料油销售市场多元化发展、补充国家能源储备的需要 (33)2.2.4项目是加快发展战略性新兴产业的政策需要 (34)2.2.5 项目是当地人民脱贫致富和增加就业的需要 (34)第三章项目市场分析与预测 (36)3.1炼油能力需求 (36)3.2未来市场预测 (40)3.2.1 2010年炼油能力需求 (40)3.2.2 2020年炼油能力需求 (41)3.2.2 炼油规划需求 (42)第四章建设规模与产品方案 (44)4.1建设规模 (44)4.2产品方案 (46)4.3产量及产值预测 (54)第五章项目选址及建设条件 (55)5.1项目选址 (55)5.1.1项目建设地点 (55)5.1.2项目用地性质及面积 (55)5.1.3土地现状 (56)5.1.4项目选址意见 (56)5.2建设条件分析 (56)5.2.1交通、能源供应条件 (56)5.2.2政策及用工条件 (57)5.3.3投资单位产业背景条件 (57)5.2.4施工条件 (57)5.2.5公用设施条件 (57)第六章原辅材料及燃料、动力供应 (59)6.1原辅材料供应 (59)6.2燃动力供应 (59)6.3物料流动 (59)第七章技术与设备方案 (60)7.1技术方案 (60)7.1.1技术方案选择的基本原则 (60)7.1.2技术来源 (60)7.1.3原油加工生产工艺流程 (60)7.2设备方案 (65)7.2.1 主要设备选型的原则 (65)7.2.2 设备配置方案 (66)7.3设备招标采购方式 (66)7.3.1基本原则 (66)7.3.2招标程序 (67)7.3.3对招标单位的要求 (68)第八章工程方案与总图运输 (69)8.1工程方案 (69)8.1.1工程设计原则 (69)8.1.2建筑设计 (75)8.1.3结构选型 (76)8.1.4主要建、构筑物工程方案 (76)8.1.5建筑功能布局 (81)8.1.6建筑结构 (82)8.2公用辅助工程 (83)8.2.1总平面布置原则 (83)8.2.2总平面布置 (83)8.2.3给排水系统 (85)8.2.4供电系统 (86)8.2.5空调采暖 (87)8.2.6通风采光系统 (88)8.2.7总图运输 (88)第九章节能评估分析与节能措施 (90)9.1用能标准和节能规范 (90)9.1.1原则和标准 (90)9.1.2规范和依据 (91)9.2能耗状况和能耗指标分析 (91)9.3节能措施和节能效果分析 (92)9.3.1建筑节能 (92)8.3.2道路照明节能 (94)8.3.3电气节能 (95)8.3.4暖通、动力节能 (95)第十章生态与环境影响分析 (98)10.1项目自然环境 (98)10.1.1项目地理位置 (98)10.1.2气候特点 (98)10.1.3地形地貌 (99)10.1.4自然资源 (99)10.2社会环境现状 (101)10.2.1行政划区 (101)10.2.2 经济建设 (105)10.2.3 交通建设 (107)10.3项目主要污染物及污染源分析 (108)10.3.1施工期 (108)10.3.2使用期 (112)10.4拟采取的环境保护标准 (113)10.4.1国家环保法律法规 (113)10.4.2地方环保法律法规 (114)10.4.3技术规范 (115)10.5环境保护措施 (115)10.5.1施工期环保措施 (115)10.5.2使用期环保措施 (119)10.5.3其它污染控制和环境管理措施 (120)10.6环境影响结论 (120)第十一章劳动安全卫生及消防 (121)11.1劳动保护与安全卫生 (121)11.1.1安全防护 (121)11.1.2劳动保护 (122)11.1.3安全卫生 (123)11.2消防 (124)11.2.1建筑防火设计依据 (124)11.2.2消防给水及灭火设备 (124)11.2.4消防电气 (124)第十二章组织机构与人力资源配置 (126)12.1组织机构 (126)12.1.1组织机构设置因素分析 (126)12.1.2项目组织管理模式 (126)12.1.3组织机构图 (126)12.2人员配置 (127)12.2.1人力资源配置因素分析 (127)12.2.2生产班制 (128)12.2.3劳动定员 (128)表11-1 劳动定员一览表 (128)12.2.4职工工资及福利成本分析 (129)表11-1 工资及福利估算表 (129)12.3人员来源与培训 (130)12.3.1人员来源 (130)12.3.2职工培训 (130)第十三章项目实施进度方案 (132)13.1项目工程总进度 (132)13.2用款计划 (132)13.3项目实施进度分期 (132)第十四章投资估算与资金筹措 (135)14.1投资估算依据 (135)14.2项目总投资估算 (135)表14-1 项目总投资估算表单位:亿元 (135)14.3建设投资估算 (136)表14-2 建设投资估算表单位:亿元 (138)14.4设备投资估算 (139)表14-3 设备总投资估算单位:亿元 (139)14.5流动资金估算 (139)表14-4 计算期内流动资金估算表单位:亿元 (141)14.6资金筹措 (142)14.7资产形成 (142)第十五章财务分析 (143)15.1基础数据与参数选取 (143)15.2营业收入、经营税金及附加估算 (143)表15-1 营业收入、营业税金及附加估算表单位:亿元 (145)15.3总成本费用估算 (146)表15-2 总成本费用估算表单位:亿元 (147)15.4利润、利润分配及纳税总额预测 (148)表15-3 利润、利润分配及纳税总额估算表单位:亿元 (149)15.5现金流量预测 (150)表15-4 现金流量表单位:亿元 (151)15.6赢利能力分析 (153)15.6.1动态盈利能力分析 (153)15.6.2静态盈利能力分析 (153)15.7盈亏平衡分析 (153)15.8财务评价 (154)表15-5 财务指标汇总表 (154)第十六章风险分析 (156)16.1风险影响因素 (156)16.1.1可能面临的风险因素 (156)16.1.2主要风险因素识别 (156)16.2风险影响程度及规避措施 (157)16.2.1风险影响程度评价 (157)16.2.2风险规避措施 (157)第十七章结论与建议 (159)17.1结论 (159)17.2建议 (159)。
500万吨常减压车间全面标定报告

室温 2.5 0.16 室温 2.5 0.17
0.13 <-30 0.18 <-30
减顶 10:00 840.1 226 15 油 16:00 839.7 227
256.5 273.5 287.5 302.0 325.0 336 349.5 全/99.0 256.5 265.5 276.5 293.0 319.0 334 349.5 全/99.0
16.87 16.1
204 1.5 0.23 0.36 0.22 +37
201 1.5 0.24
0.21 +37
减三 10:00 882.9 343 396 416 432 443 449 457 473 484 495 99 0.1 18 线 16:00 881.6 346 392 416 428 439 446 452 466 477 486 94 0.1
上 280/下 350
上 255/下 338
操作 0.08 0.08
0.08 绝压 45mmHg
绝压 45mmHg
绝压 45mmHg
2.2 常压炉性能表
工艺编号
F-101
制造厂家
设备名称
常压炉
制造日期
2003.4
总重(Kg)
启用日期
2003.7
规格型号
介质
初底油、过热蒸汽
固定资产号
技术数据
炉管部位
光 16/2 翅 60/8
Φ219x10 Φ273x12
Φ168x8
Φ325x12
18000
11460(有效)
580
96/363
336
304
349500
349500
两炉烟气预热空气
2014年常减压装置改造标定报告资料

中国化工集团油气公司昌邑石化分公司500万吨/年常减压蒸馏装置标定报告中国化工油气昌邑分公司生产技术部中国化工油气昌邑分公司运行一部2014年10月目录1. 概述 (1)1.1 装置概况 (1)1.2主要改造工作说明 (1)1.2.1初馏塔系统 (1)1.2.2常压塔系统 (2)1.2.3加热炉系统 (2)1.3本次改造核算 (2)1.4本装置主要组成 (2)2.工艺流程简述 (2)3 .装置开工运转与标定 (7)3.1 标定期间数据与分析 (7)3.2标定结果 (12)3.2.1 原油加工量 (12)3.2.2 轻收及总拔 (12)3.2.3 产品质量 (13)3.2.4 装置能耗 (14)3.2.5 塔系统 (14)3.2.6 换热网络 (15)3.2.7 机泵 (15)3.2.8 加热炉 (15)3.2.9装置防腐 (16)3.2.10 环境保护 (16)4.存在的问题及建议 (16)5.结论 (17)1. 概述1.1 装置概况山东昌邑石化有限公司500×104t/a 常减压蒸馏装置,系公司重交沥青装置能量系统优化改造项目核心装置,总投资7.6亿元,装置投资5.4亿元,占地15000m2。
由西安长庆科技工程有限责任公司设计,山东环海石化工程建设公司和山东宏扬石化工程公司等公司承建,于2008年5月开工建设,于2009年5月建成投产运行。
装置原设计加工混合重质含硫原料油,处理量为500万吨/年,设计年开工时间为8000小时,为燃料型装置。
但随着企业的持续性发展, 加工规模的继续扩大, 以及原油品种的日益多样化, 装置难以适应加工轻质原油的变化情况。
装置于2010年08月,在原装置的基础上,进行了第一次挖潜改造,充分利用已有设备和成熟的工艺,最大限度地减少改造工程量及投资,使其轻油加工能力提升至450万吨/年,尽可能降低生产成本,确保装置安全运行。
改造后的装置增加了初馏塔系统,旧闪蒸塔T1001改造成初馏塔,装填8.8m高的规整填料及气液分布器等塔内件;增加一台初馏塔回流罐V1026;新增初顶回流泵P1032AB 二台,初侧泵P1033AB二台;新增初顶油气后冷却器E1033一台。
常减压装置年产350万吨计算
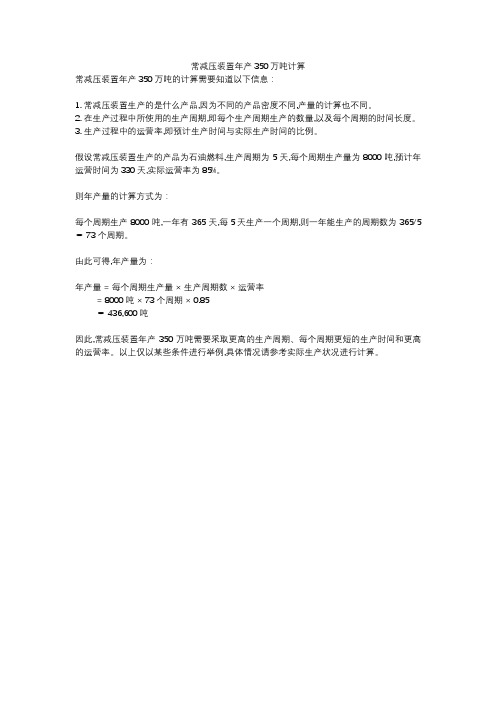
常减压装置年产350万吨计算
常减压装置年产350万吨的计算需要知道以下信息:
1. 常减压装置生产的是什么产品,因为不同的产品密度不同,产量的计算也不同。
2. 在生产过程中所使用的生产周期,即每个生产周期生产的数量,以及每个周期的时间长度。
3. 生产过程中的运营率,即预计生产时间与实际生产时间的比例。
假设常减压装置生产的产品为石油燃料,生产周期为5天,每个周期生产量为8000吨,预计年运营时间为330天,实际运营率为85%。
则年产量的计算方式为:
每个周期生产 8000 吨,一年有 365 天,每5天生产一个周期,则一年能生产的周期数为 365/5 ≈ 73 个周期。
由此可得,年产量为:
年产量 = 每个周期生产量× 生产周期数× 运营率
= 8000 吨× 73 个周期× 0.85
≈ 436,600 吨
因此,常减压装置年产 350 万吨需要采取更高的生产周期、每个周期更短的生产时间和更高的运营率。
以上仅以某些条件进行举例,具体情况请参考实际生产状况进行计算。
01常减压装置
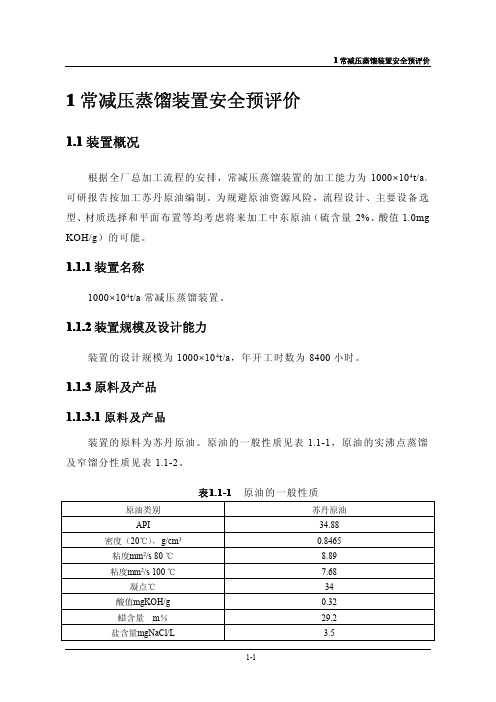
原油的一般性质
苏丹原油 34.88 0.8465 8.89 7.68 34 0.32 29.2 3.5
1 常减压蒸馏装置安全预评价
残炭 m% 胶质 m% 沥青质 m% 硫 氮 m% m% 铁ppm 镍ppm 铅ppm 钒ppm K
3.57 9.7 0.2 0.05 0.09 4.8 6.2 <0.1 0.3 >12.6
序号物料名称数值备注wtkgh104ta一常压部分1原料11苏丹混合原油1000011904761000002产品21常顶气损失0202381200去加热炉22石脑油783932177830去轻烃回收装置23常一线油827984588270去罐区24常二线油9221097839222其中4099104ta柴油加氢精制其余去罐区25常三线油711846437110去柴油加氢精制26常四线油306364053058去蜡油加氢裂化27常压渣油643176559064310其中210104ta进催化合计100001190476100000二减压部分1原料11常压渣油10000515590433102产品21减顶气012595050去加热炉22减顶油0201031087去蜡油加氢裂化23减一线油52126881225824减二线油25771328471115925减三线油177291356767426减压渣油509926287922082140104ta去重油催化裂化其余作为燃料油至罐区合计10000515589433091111常减压蒸馏装置安全预评价16212工艺流程设备1121工艺流程11211工艺流程概述原油经闪蒸塔闪底油由泵抽出经换热后进入常压炉加热后进入常压塔
515590
433.10
0.50 0.87 22.58 111.59 76.74 220.82 433.09
1000万吨年常减压工艺管道施工组织设计

A2施工组织设计(方案)报审表审批表中国石油广西石化1000万吨/年炼油工程常减压蒸馏装置工艺管道施工方案中国石油一建广西项目经理部目录1. 编制说明 (1)1.1工程说明 (1)1.2编制依据 (1)2. 工程概况 (1)2.1施工内容和施工范围 (1)2.2计划开、竣工日期 (1)2.3工程实物量 (2)2.4工程设计参数及工艺特点 (2)3. 施工进度计划 (4)4. 主要施工方法 (5)4.1施工原则、工序 (5)4.2 施工方法及步骤 (6)4.3管线焊接 (9)4.4焊接工艺 (13)4.5焊接检验 (15)4.6 管道安装 (17)4.7伴热管安装 (21)4.8管道试压 (22)4.9 管道吹扫、清洗 (22)4.10 管道的防腐与保温 (22)5. 质量保证措施 (22)5.1质量目标 (22)5.2施工质量措施 (23)6. 安全技术措施 (24)6.1安全目标 (24)6.2施工安全措施 (24)7. 劳动力需求计划 (24)8. 主要施工机具和设备配置计划 (25)9. 施工手段用料 (26)附件:现场平面布置图。
(28)1. 编制说明1.1工程说明²中国石油广西石化1000万吨/年炼油工程的常减压蒸馏装置属于新建工程,该项目位于广西壮族自治区钦州市钦州港经济开发区,占地面积为23940平方米。
装置原油来源于苏丹油,采用海上运输。
装置由换热、电脱盐、闪蒸塔、常压炉、常压塔系统、减压炉、减压塔系统、气体压缩、一脱三注等部分组成。
²本工程由中国石油天然气华东勘察设计院设计,抚顺诚信石化工程建设监理有限公司监理,中国石油天然气第一建设公司负责施工。
1.2编制依据²国家和石油部颁发现行施工验收规范及质量验评标准。
²公司质量、HSE管理手册及程序文件。
²广西石化公司的有关规章制度。
²《工业金属管道施工及验收规范》GB50235-97。
1000万吨常减压装置钢结构施工方案解析
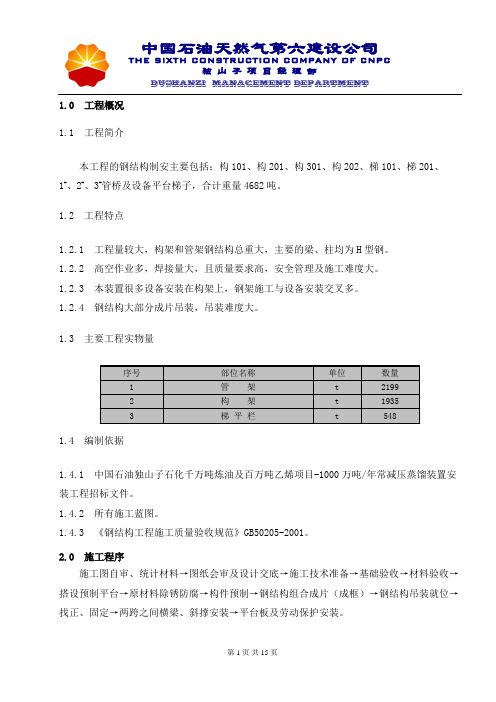
DUSHANZI MANAGEMENT DEPARTMENT1.0 工程概况1.1 工程简介本工程的钢结构制安主要包括:构101、构201、构301、构202、梯101、梯201、1#、2#、3#管桥及设备平台梯子,合计重量4682吨。
1.2 工程特点1.2.1 工程量较大,构架和管架钢结构总重大,主要的梁、柱均为H型钢。
1.2.2 高空作业多,焊接量大,且质量要求高,安全管理及施工难度大。
1.2.3 本装置很多设备安装在构架上,钢架施工与设备安装交叉多。
1.2.4 钢结构大部分成片吊装,吊装难度大。
1.3 主要工程实物量1.4 编制依据1.4.1 中国石油独山子石化千万吨炼油及百万吨乙烯项目-1000万吨/年常减压蒸馏装置安装工程招标文件。
1.4.2 所有施工蓝图。
1.4.3 《钢结构工程施工质量验收规范》GB50205-2001。
2.0 施工程序施工图自审、统计材料→图纸会审及设计交底→施工技术准备→基础验收→材料验收→搭设预制平台→原材料除锈防腐→构件预制→钢结构组合成片(成框)→钢结构吊装就位→找正、固定→两跨之间横梁、斜撑安装→平台板及劳动保护安装。
DUSHANZI MANAGEMENT DEPARTMENT3.0 主要施工方法3.1 钢结构框架及管架采用分片组焊、分片吊装。
以构101为例,施工过程示意图如下:钢结构分片示意图DUSHANZI MANAGEMENT DEPARTMENT框架分片组合成型示意图框架分片吊装及横梁安装示意图3.2 钢梯间先组合成片,再组合成框,然后整体吊装。
施工过程示意如下:DUSHANZI MANAGEMENT DEPARTMENT钢梯间分片示意图钢梯间组合成片示意图钢梯间安装成型示意图DUSHANZI MANAGEMENT DEPARTMENT3.3 设备平台、梯子、栏杆等在预制场集中预制,现场吊装、组焊。
DUSHANZI MANAGEMENT DEPARTMENT4.0 施工步骤4.1 施工技术准备4.1.1 组织施工班组人员熟识图纸及附属设计文件或相关资料,对施工班组进行技术交底,使其明确安装程序及安装质量控制点及要求和安全教育,切实做到质量第一、文明施工。
1000万吨/年常减压装置工程施工项目管理案例分析与研究

1000万吨/年常减压装置工程施工项目管理案例分析与研究摘要:本文通过选取石油化工行业千万吨炼油项目龙头装置--1000万吨/年常减压工程施工的项目管理实施案例,从项目管理策划、准备、项目管理过程控制、项目管理风险控制等方面,分析、总结了项目管理过程中好的措施、经验,论述了石油化工施工企业应如何加强大型炼油化工装置工程施工的项目管理,从而确保工程施工项目管理目标实现。
关键词:石油化工施工企业项目管理常减压工程一、工程概况中国石油独山子石化公司1000万吨/年常减压蒸馏装置(以下简称常减压工程)位于新疆克拉玛依市独山子区,占地22000平方米,是国内同类装置中最大的常减压装置。
该工程主要包括:一脱四注、常压、减压、脱硫、轻烃回收等五个部分。
安装范围如下:地下管网(包括给排水、消防水等安装、土方、井子等)和安装工程(钢结构、工艺设备、工艺及公用管道、电气、电信、自控仪表、消防、防腐、化验分析等安装工程)。
该工程于2006年8月25日开工建设,2009年4月24日顺利实现安全、优质中交,并一次投产成功,生产出优良产品。
该工程荣获中国石油优质工程金奖、全国优秀焊接工程一等奖、全国工程建设优秀项目管理成果一等奖、新中国成立60周年100项经典暨精品工程等多项荣誉。
二、项目管理实施1.抓实项目管理过程控制重点抓实以下六个方面的管理过程控制:1.1抓实物资采购管理控制项目部制定了1000万吨/年常减压蒸馏装置物资管理办法、设备材料进货产品验收及检验计划、进货产品标识策划、1000万吨常减压项目部测量过程台帐。
细化物资部门、岗位职责;积极推行使用公司MIS物资管理系统,同时利用信息管理系统,建立工程物资到货动态信息管理台帐,确保随时能提供准确的材料信息,为施工生产和人员进场提供决策依据。
1.2抓实人力资源管理控制一是抓劳动力投入。
在工程主体安装阶段最高时投入人力1300多人,在试压吹扫保运、防腐保温阶段,最高时投入人力达到808人,劳动力投入人员工时累计4,108,364工时;二是抓人员能力评价。
- 1、下载文档前请自行甄别文档内容的完整性,平台不提供额外的编辑、内容补充、找答案等附加服务。
- 2、"仅部分预览"的文档,不可在线预览部分如存在完整性等问题,可反馈申请退款(可完整预览的文档不适用该条件!)。
- 3、如文档侵犯您的权益,请联系客服反馈,我们会尽快为您处理(人工客服工作时间:9:00-18:30)。
1总论中国石油集团工程设计有限责任公司某分公司(以下简称某分公司)受某石化公司委托,对某石化公司1000万吨/年蒸馏装置进行标定核算。
1.1编制依据1.1.1某石化公司1000万吨/年蒸馏装置标定设计核算委托书。
1.1.2某石化公司1000万吨/年蒸馏装置标定操作数据。
1.1.3某石化公司1000万吨/年蒸馏装置标定原始设计文件。
1.2装置简介根据某石化分公司加工进口含硫原油技术改造工程总流程的规定,2005年将某石化分公司原有的三蒸馏装置简易地改造为加工进口含硫原油的1000万吨/年常减压蒸馏联合装置。
改造后的三蒸馏装置由1000万吨/年常减压蒸馏、380万吨/年石脑油加氢、420万吨/年轻烃回收、1#变电所和溴化锂制冷站五部分组成。
在装置的改扩建中,常减压蒸馏、石脑油加氢和轻烃回收由Shell Global Solutions International 公司提供工艺设计包,采用了国外先进、可靠的工艺技术设备,使装置改造后的总体水平达到国际先进的水平,装置设备、管道等级材质符合加工含硫原油的要求。
本装置由中国石化集团洛阳石油化工工程设计,于2005年11月建成,2006年3月一次开气成功,投产至今。
投产后生产和标准表明,生产能力、油品收率、产品质量、能耗和加热炉效率等绝大部分指标均已达到或超过设计要求,只有极少数指标距设计期望值略有差距,但已处于同类装置的最好水平。
由于本装置还处于过度期,轻烃回收单元处于低负荷运行,胺洗系统尚未投入使用,故与设计值存在较大的差别;同时石脑油加氢装置尚在建设中,因此本次标定只考察了常减压蒸馏装置、轻烃回收装置。
1.3主要标定结果2006年7月份,按最大加工量进行了正式标定,由于调整仓促,不可能全部调优,但已经可以看出装置生产情况和质量、能耗水平。
标定及核算结果汇总如下:表1-1常减压蒸馏单元2装置采用的主要技术及特点2.1常减压蒸馏单元1初馏塔提压操作,采用无压缩机回收液化气。
2抑制原油及初底油在换热器中汽化。
为保证单元的长周期远行,减轻油品在换热器中的结垢,在原油进初馏塔前设置了调节阀以抑制原油出现汽化。
3原油进初馏塔前设置蒸汽加热器为稳定原油进初馏塔的温度,进行稳定初馏塔的操作,在原油进初馏塔前设置蒸汽加热器,以补偿换热网络的温度变化,并可缩短单元开工时原油升温的时间。
4原油进初馏塔温度较低,塔底吹入一定量的汽提蒸汽。
原油进初馏塔的设计温度为190℃。
为保证塔顶石脑油的质量及收率,塔底吹入17 t/h汽提蒸汽。
5常压塔不设置冷回流常压塔设置常顶循、常一中和常二中三个取热段,塔顶不设置冷回流。
为提高换热效果,中段回流采用小温差、大流量的方式。
6常二线油设置减压真空干燥常二线油设置减压真空干燥,控制柴油的含水量不大于80ppm(wt),以满足柴油加氢装置对原料中含水量的要求。
7常压塔强化汽提效果常压塔底采用内缩径,以强化塔底汽提效果。
8换热网络对常减压和轻烃回收一起进行热整合,优化换热网络。
9换热器设置旁路控制为稳定换热网络,增加换热网络的弹性,对重沸器、原油加热器、中段回流换热器以及部分原油换热器的热流侧设置控制旁路。
10先进的HSE设置SGSI对重要的工艺参数均设置链锁保护系统、事故报警及紧急停车链锁系统,大大提高了单元安全运转的可靠性。
2.3主要设备说明2.3.1塔类1初馏塔1)进料温度211℃/206℃,塔顶操作压力为0.33MPa,初馏塔不设进料加热器,塔底不吹气。
2)初馏塔进料段以上直径为3.4M,设20层塔盘;进料段以下直径为5.7M,设5层塔盘,总塔盘25层。
塔盘采用高性能塔盘。
3)初馏塔采用热回流,回流温度为96℃。
4)壳体第五层塔盘以上材质采用16MnR+alloy400,其余为16MnR;顶部5层塔盘材质采用alloy 400,其余为0Cr13。
2常压塔1)常压塔进料温度367℃/356℃;塔顶操作压力为0.06MPa。
常压塔设顶循、一中和二中三个取热中段。
常压塔塔顶不设冷回流。
2)常压塔塔径分3段,常顶循段(1至4层塔盘)直径为6.1M,其余进料段以上塔径均为8M,共45层塔盘。
塔底汽提段设8层塔盘,采用内缩径,直径为4.25M。
3)常压塔设4个部分抽出塔盘,分别是3个中段回流抽出和1个常二线抽出。
设2个全抽出塔盘,分别是常一线和常三线抽出。
4)塔盘采用高性能塔盘。
5)壳体在300℃以上材质采用16MnR+316L,其余为16MnR+405和16MnR+304L。
塔盘材质根据不同温度,分别采用0Cr13、304L和316L。
4减压塔1)减压塔进料温度为384℃(设计工况)/383℃(灵活工况);塔顶操作压力为16mbar。
减压塔的设计压力为0.15MPa。
2)减压塔设计四个侧线,减一,减二,减三混合作为蜡油,减四线为洗涤油,返回至减压炉入口循环。
3)减压塔塔径分为三段,减一中塔径为7.8M,减二中段塔径为11.8M,其余段塔径为13.8M。
4)减压塔塔内采用SGSI设计结构。
各中段回流取热段采用空塔喷淋取热技术。
减压塔内主要有两段填料,分别为柴油分离段和洗涤段。
5)减压塔上部简体材料为20R,中部简体以及过度段材料为20R+304L,下部简体材料为20R+316L,减压塔填料采用316L材料。
2.3.2加热炉(1)设计负荷常压加热炉的设计热负荷,工况一(阿拉伯轻油)为104654KW;工况二(俄罗斯轻油)为103924KW。
减压加热炉的设计热负荷,设计工况(阿拉伯轻油,VG0 T95=555℃)为80641KW;灵活工况(阿拉伯轻油,VG0 T95=575℃)为74488KW,加热炉设计弹性为操作工况的50%~110%。
(2)加热炉炉型两台加热炉炉型均为三辐射室十二辐射单元立管式炉,每个辐射单元设置一台低氧化氮燃烧器,共用一个对流室。
油品介质分十二程从对流段上部进炉,经对流加热后进入辐射段,从辐射顶出炉。
2.3.3机泵由于原油泵、初底泵、常一中泵、常二中泵、减二线及减二中泵、减三泵及减三中泵等扬程较高或流量过大,对以上机泵采用2开1备的运行方式,以节省投资。
对于大流量机泵采用效率较高、NPSH较低的双吸两端支撑式化工流程泵,高电压电机采用隔爆型电机。
2.4设计主要指标2.4.1加工量及操作弹性CDU3规模为1000万吨/年,设计弹性为50%~100%。
HVU3规模为630万吨/年,设计弹性为50%~100%。
石脑油加氢单元规模为380万吨/年,设计弹性为50%~100%。
2.4.2装置能耗常减压单元能耗不大于13.8Kg标油/t原油。
石脑油加氢单元能耗不大于6.71Kg标油/t原油。
3标定情况及说明3.1原油及标定方案(1)加工原油为卡宾达原油,本标定及核算是根据2006年7月14日标定数据整理核算的,日炼油量为25752吨。
(2)标定生产方案初、常顶石脑油重整原料常一线3#航空煤油常二、三线;减一线0#柴油减二、三线混合蜡油,按减压深拔工况操作95%点不大于575℃减压塔底渣油催化裂化原料3.2检测说明(1)物料平衡均以装置油表计量为准,参考罐区检尺计量,并根据实际的温度进行密度校正。
(2)对装置所有计量一次指示在标定前进行了回零校正。
(3)初馏塔、常压塔、常压汽提塔的注汽量均以各自孔板计量为准。
(4)各冷却器水分支流采用脉冲流量测量仪测定。
(5)冷去系统中,冷热流无热偶处的温度值是由水银温度计测得。
(6)冷换系统及辅助系统无压力变送指示均采用就地指示弹簧管式压力计测得,并在测量前经过校验。
3.3标定目的(1)考察装置的运行情况及装置的技术经济指标是否达到设计要求,为装置考核验收提供依据。
(2)考察产品质量情况。
(3)考察减压系统抽真空专利设备水环真空泵和蒸汽喷射泵实际抽真空的能力。
(4)考察减压塔喷头喷淋效果,检验减压空塔喷淋技术,进而考察减压深拔技术的实际运行效果。
(5)考察装置塔内构件的水力学性能,并验证其适用性。
(6)考察加热炉专利火嘴的运行能力。
(7)考察装置物料平衡、热平衡情况。
(8)考察装置换热网络实际运行情况。
(9)考察装置各换热器换热效率。
(10)考察装置加热炉运行情况及效率。
(11)考察电脱盐运行情况。
(12)考察装置能耗水平及技术指标,确定本装置在国内、国际上所处地位。
(13)摸清目前装置存在影响正常生产、处理能力、物耗、能耗、产品收率及产品质量的不利因素,为进一步调整优化操作及今后整改指明方向。
(14)考察各单位单体设备处理能力和效果。
(15)考察装置各计量表的精度、DCS控制系统的准确性和稳定性。
3.4标定时间2006年7月13日9:30至2006年7月14日9:30时共计24小时。
4原油及产品分析数据4.1原油性质本次标定的原油为卡宾达原油,其主要性质见下表4.2产品分析数据4.2.1蒸顶、常顶、减顶不凝气表4-3塔顶干气分析化验成绩由于胺洗系统未投用,轻烃干气未经精制,导致干气中硫化氢含量严重超标。
4.2.3初顶、常顶、石脑油分离塔轻重石脑油:表4-5塔顶石脑油分析化验成绩标定期间初、常顶石脑油质量完全符合工艺指标要求的数值,并且标定期间各馏出点温度也比较稳定,这说明常压塔采用常顶循环回流来控制塔顶温度是可行的。
但重石脑油的初馏点比设计值低30℃,与设计值有较大的偏差,这主要是石脑油分离塔塔底重沸器热量不够造成的,在以后生产中需要调整操作参数。
4.2.4常一线:标定期间常一线航煤质量完全符合工艺卡片的指标要求。
同时,常顶KK平均值与常一线HK平均值之差为14℃,满足常压产品煤油与石脑油脱空度大于5℃的分离要求。
4.2.5常二线/常三线/减一线:表4-7柴油产品化验分析成绩标定期间常二线产品质量完全符合0#柴油的质量要求,且产品质量稳定;尽管常三线初馏点较低,但与常二线、减一线混合后完全满足0#柴油的质量要求。
常三线初馏点低的主要原因是常三线抽出层塔盘为全抽出塔盘,且汽提塔无汽提蒸汽。
标定期间减一线产品质量完全符合柴油指标要求,可见,该减压塔在只有两段填料的前提下,减一线产柴油是完全可行的。
常二线HK平均值与常一线KK平均值之差为1℃,不满足常压产品煤油与石脑油脱空度>5℃的分离要求,在生产中需优化操作条件以满足产品质量的要求。
4.2.6混合蜡油不大于555℃)要求。
标定期间减压蜡油的氮含量满足设计要求,低于1500ppm;残碳平均为0.19%,远低于设计值0.9%。
1)塔顶真空度还未达到设计值12~16mbar,即99kpa以上,主要是因为水环真空泵未投用。
2)由于减压系统部分流量部分孔板不指示值,造成减压系统操作未达到设计值。
3)加压系统符合略低,部分操作条件与设计值相差较大。
4.2.7常压渣油:常压渣油中小于350℃馏分含量大于5%,尚未达到设计指标,其主要原因常压塔进料温度低于设计值5℃左右,小于350℃馏分蒸发不完全所致。