制动管路布置技术规范
制动系统设计规范
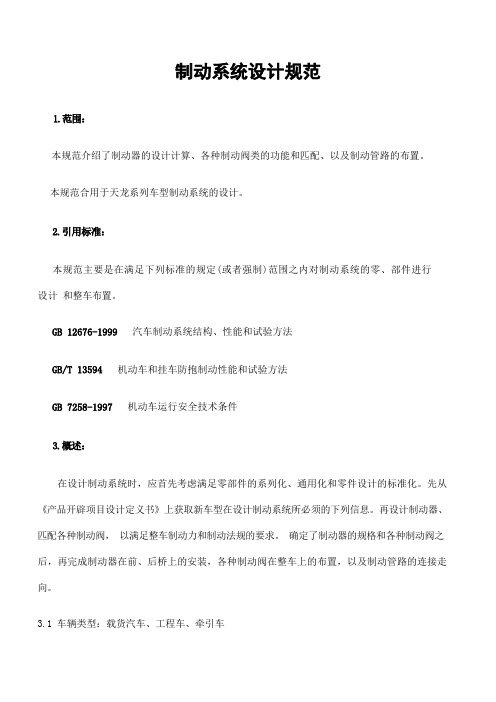
本规范介绍了制动器的设计计算、各种制动阀类的功能和匹配、以及制动管路的布置。
本规范合用于天龙系列车型制动系统的设计。
本规范主要是在满足下列标准的规定(或者强制)范围之内对制动系统的零、部件进行设计和整车布置。
汽车制动系统结构、性能和试验方法机动车和挂车防抱制动性能和试验方法机动车运行安全技术条件在设计制动系统时,应首先考虑满足零部件的系列化、通用化和零件设计的标准化。
先从《产品开辟项目设计定义书》上获取新车型在设计制动系统所必须的下列信息。
再设计制动器、匹配各种制动阀,以满足整车制动力和制动法规的要求。
确定了制动器的规格和各种制动阀之后,再完成制动器在前、后桥上的安装,各种制动阀在整车上的布置,以及制动管路的连接走向。
3.1 车辆类型:载货汽车、工程车、牵引车3.2 驱动形式:4×2、6×4、8×43.3 主要技术及性能参数:长×宽×高、轴距、空/满载整车重心高坐标、轮距、整备质量、额定载质量、总质量、前/后桥承载吨位、 (前/后)桥空载轴荷、 (前/后)桥满载轴荷、最高车速、最大爬坡度等。
3.4 制动系统的配置:双回路气/液压制动、弹簧制动、鼓/盘式制动器、防抱制动系统、手动/自动调整臂、无石棉磨擦衬片、感载阀调节后桥制动力、缓速器、排气制动。
本规范仅对鼓式制动器的各主要元件和设计计算加以阐述,盘式制动器的选型和计算将暂不列入本规范的讨论范围之内。
4.1 鼓式制动器主要元件:4.1.1 制动鼓:由于铸铁耐磨,易于加工,且单位体积的热容量大,所以,重型货车制动鼓的材料多用灰铸铁。
不少轻型货车和轿车的制动鼓为组合式,其圆柱部份用铸铁,腹板则用钢压制件。
制动鼓在工作载荷下将变形,使蹄、鼓间单位压力不均,带来少许踏板行程损失。
制动鼓变形后的不圆柱度过大,容易引起制动时的自锁或者踏板振动。
所以,在制动鼓上增加肋条,以提高刚度和散热性能。
中型以上货车,普通铸造的制动鼓壁厚为 13~18㎜。
底盘改装规范
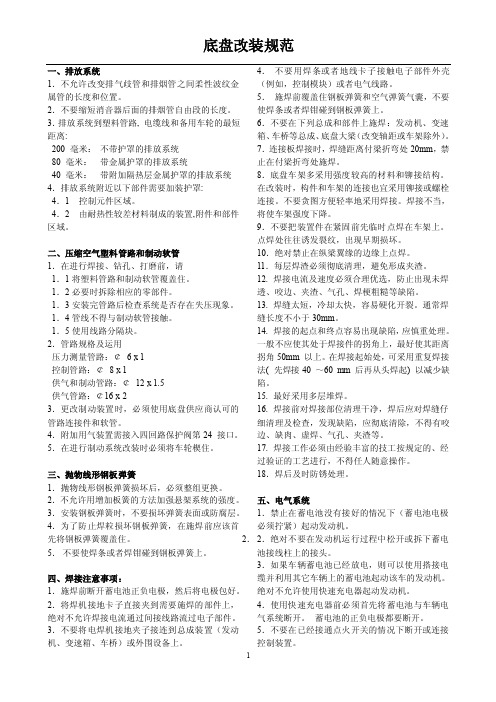
一、排放系统1.不允许改变排气歧管和排烟管之间柔性波纹金属管的长度和位置。
2.不要缩短消音器后面的排烟管自由段的长度。
3.排放系统到塑料管路, 电缆线和备用车轮的最短距离:200 毫米:不带护罩的排放系统80 毫米:带金属护罩的排放系统40 毫米:带附加隔热层金属护罩的排放系统4.排放系统附近以下部件需要加装护罩:4.1 控制元件区域。
4.2 由耐热性较差材料制成的装置,附件和部件区域。
二、压缩空气塑料管路和制动软管1.在进行焊接、钻孔、打磨前,请1.1将塑料管路和制动软管覆盖住。
1.2必要时拆除相应的零部件。
1.3安装完管路后检查系统是否存在失压现象。
1.4管线不得与制动软管接触。
1.5使用线路分隔块。
2.管路规格及运用压力测量管路:¢ 6 x 1控制管路:¢8 x 1供气和制动管路:¢12 x 1.5供气管路:¢16 x 23.更改制动装置时,必须使用底盘供应商认可的管路连接件和软管。
4.附加用气装置需接入四回路保护阀第24 接口。
5.在进行制动系统改装时必须将车轮楔住。
三、抛物线形钢板弹簧1.抛物线形钢板弹簧损坏后,必须整组更换。
2.不允许用增加板簧的方法加强悬架系统的强度。
3.安装钢板弹簧时,不要损坏弹簧表面或防腐层。
4.为了防止焊粒损坏钢板弹簧,在施焊前应该首先将钢板弹簧覆盖住。
5.不要使焊条或者焊钳碰到钢板弹簧上。
四、焊接注意事项:1.施焊前断开蓄电池正负电极,然后将电极包好。
2.将焊机接地卡子直接夹到需要施焊的部件上,绝对不允许焊接电流通过间接线路流过电子部件。
3.不要将电焊机接地夹子接连到总成装置(发动机、变速箱、车桥)或外围设备上。
4.不要用焊条或者地线卡子接触电子部件外壳(例如,控制模块)或者电气线路。
5.施焊前覆盖住钢板弹簧和空气弹簧气囊,不要使焊条或者焊钳碰到钢板弹簧上。
6.不要在下列总成和部件上施焊:发动机、变速箱、车桥等总成、底盘大梁(改变轴距或车架除外)。
7.连接板焊接时,焊缝距离付梁折弯处20mm,禁止在付梁折弯处施焊。
中华人民共和国机动车制动检验规范(试行)
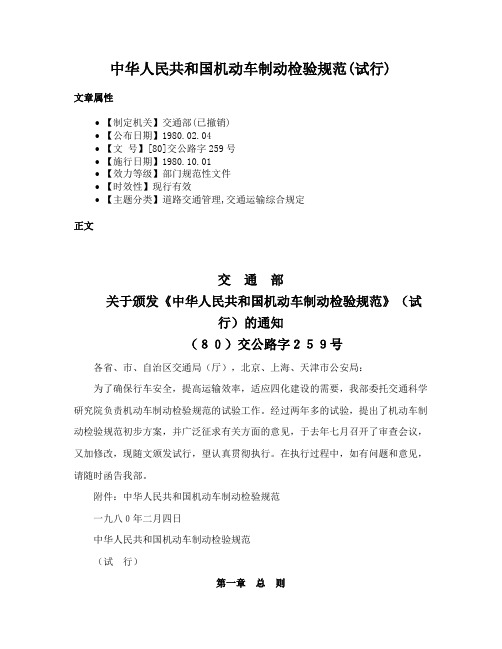
中华人民共和国机动车制动检验规范(试行)文章属性•【制定机关】交通部(已撤销)•【公布日期】1980.02.04•【文号】[80]交公路字259号•【施行日期】1980.10.01•【效力等级】部门规范性文件•【时效性】现行有效•【主题分类】道路交通管理,交通运输综合规定正文交通部关于颁发《中华人民共和国机动车制动检验规范》(试行)的通知(80)交公路字259号各省、市、自治区交通局(厅),北京、上海、天津市公安局:为了确保行车安全,提高运输效率,适应四化建设的需要,我部委托交通科学研究院负责机动车制动检验规范的试验工作。
经过两年多的试验,提出了机动车制动检验规范初步方案,并广泛征求有关方面的意见,于去年七月召开了审查会议,又加修改,现随文颁发试行,望认真贯彻执行。
在执行过程中,如有问题和意见,请随时函告我部。
附件:中华人民共和国机动车制动检验规范一九八0年二月四日中华人民共和国机动车制动检验规范(试行)第一章总则第一条为保障行车安全,提高运输效率,适应交通运输现代化的需要,特制订本规范。
第二条本规范适用于汽车(包括于汽车带挂车和半挂车)、无轨电车、特种汽车、二、三轮摩托车和方向盘式拖拉机带挂车等机动车辆,对手扶式拖拉机的制动装置也提出了适当要求。
第三条机动车的制动装置及制动性能,必须符合本规范的有关要求。
对于汽车、无轨电车和牵引车带半挂车的制动性能要求,根据其总重量按小、中、大三种车型分别规定(详见表一和表二)。
第四条本规范由交通监理部门和公安交通管理部门负责监督、贯彻执行。
第二章制动装置第五条通行城镇街道和公路的机动车以及出厂的新车,必须装有行车和停车制动装置。
挂车和半挂车(包括新出厂的)必须装有行车制动装置。
两轴挂车至少在后轴两轮上装有行车制动装置。
手扶拖拉机拖带的挂车也必须装有可靠的制动装置。
制动装置应保持技术状况良好,操纵轻便,完整可靠。
第六条停车制动装置的安装位置要适当,其手柄行程必须有一定的贮备。
浅谈重卡制动管路快插接头装配过程的配置

浅谈重卡制动管路快插接头装配过程的配置发布时间:2021-03-16T11:31:54.220Z 来源:《中国科技信息》2021年1月作者:黄虹连高祥超孔海龙苏远岗陈莉[导读] 不同的制动管路,需要采用不同的装配策略。
因此在进行快插接头装配时,需要严格按照装配工艺进行装配,避免强力装配,相对应的零部件应该做好匹配,避免零部件自身存在问题。
山东济宁中国重型汽车集团有限公司1 山东济宁山推工程机械股份有限公司2 黄虹连高祥超孔海龙苏远岗陈莉272000 摘要:不同的制动管路,需要采用不同的装配策略。
因此在进行快插接头装配时,需要严格按照装配工艺进行装配,避免强力装配,相对应的零部件应该做好匹配,避免零部件自身存在问题。
关键词:重卡;制动管路;快插接头;装配一、重卡快插接头装配过程1.1快插接头的组成在进行安装重卡快插接头时,首先要了解快插接头的部件组成,如图1所示。
从图1可以看出,快插接头主要有5部分组成,阴接头、密封垫、卡子、空心螺栓、o形圈以及阳接头。
各组件之前的配合关系,其中密封垫和卡子位于阴接头体内,O形密封圈在空心螺栓根部,并与阴接头体连接一起共同组成阴接头,两个O形密封圈套在阳接头体上一起构成密封阳接头。
1.2 快插接头的工作原理在阴接头和阳接头位置都有竹节结构,利用软管与阳接头竹节结构位置相配合,阴接头或者阀体通过卡子和阳接头连接,连接完成后,拔脱力要符合相关标准的要求,满足使用需求。
在快插结构中,密封功能主要依靠O形圈实现,阳接头的两道O形圈和阴接头内的密封垫保证阴接头和阳接头的连接的密封性。
空心螺栓和阴接头利用0密封圈实现与阀体之间的密封效果。
密封效果要保证能在-40℃~100℃范围内使用。
1.3常见的制动管路结构重卡中常用的制动管路接头有不同的几种形式,分别是卡套式气制动管路、刹车管路、自锁卡套接头,如图2所示。
从图2中可以看出,不同的结构形式,其装配方式以及结构均是不同的,因此在进行安装时,一定要充分考虑其结构特点,制定符合实际的安装工艺。
汽车改装技术标准
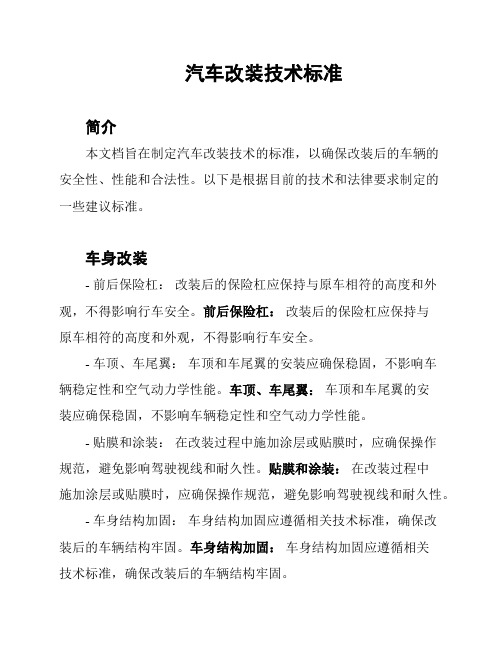
汽车改装技术标准简介本文档旨在制定汽车改装技术的标准,以确保改装后的车辆的安全性、性能和合法性。
以下是根据目前的技术和法律要求制定的一些建议标准。
车身改装- 前后保险杠:改装后的保险杠应保持与原车相符的高度和外观,不得影响行车安全。
前后保险杠:改装后的保险杠应保持与原车相符的高度和外观,不得影响行车安全。
- 车顶、车尾翼:车顶和车尾翼的安装应确保稳固,不影响车辆稳定性和空气动力学性能。
车顶、车尾翼:车顶和车尾翼的安装应确保稳固,不影响车辆稳定性和空气动力学性能。
- 贴膜和涂装:在改装过程中施加涂层或贴膜时,应确保操作规范,避免影响驾驶视线和耐久性。
贴膜和涂装:在改装过程中施加涂层或贴膜时,应确保操作规范,避免影响驾驶视线和耐久性。
- 车身结构加固:车身结构加固应遵循相关技术标准,确保改装后的车辆结构牢固。
车身结构加固:车身结构加固应遵循相关技术标准,确保改装后的车辆结构牢固。
引擎及动力系统改装- 底盘加固:底盘加固应符合相关标准,以确保引擎改装后的动力能够得到充分承载。
底盘加固:底盘加固应符合相关标准,以确保引擎改装后的动力能够得到充分承载。
- 排气系统:更换排气系统时,应选择符合排放标准的合法产品,避免超出噪音限制。
排气系统:更换排气系统时,应选择符合排放标准的合法产品,避免超出噪音限制。
- 进气系统:进气系统改装应确保供氧充足,同时遵守排放限制。
进气系统:进气系统改装应确保供氧充足,同时遵守排放限制。
- 动力系统管理:车辆动力系统的管理软件修改应符合法律要求,不得超出排放和性能范围。
动力系统管理:车辆动力系统的管理软件修改应符合法律要求,不得超出排放和性能范围。
制动系统改装- 制动片和制动盘:更换制动片和制动盘时,应选择符合相关标准的产品,确保制动性能不受影响。
制动片和制动盘:更换制动片和制动盘时,应选择符合相关标准的产品,确保制动性能不受影响。
- 刹车管路:刹车管路的改装应符合标准,保证刹车系统正常工作并避免系统泄漏。
公交制动布置方案

公交制动布置方案引言公交车是城市交通中重要的一部分,而制动系统是公交车安全运行的关键因素之一。
制动布置方案的设计合理与否直接关系到公交车的制动性能以及乘客的安全。
本文将介绍一种公交制动布置方案,旨在提高公交车的制动效果,并确保乘客的安全。
概述公交制动系统主要包括制动器、制动液、制动管路以及制动踏板等组成部分。
制动布置方案的核心是设计合理的制动管路,以便实现良好的制动效果。
下面将详细介绍公交制动布置方案的设计原则和实施步骤。
设计原则1. 制动平衡公交车是一种大型车辆,制动系统需要保证车辆在制动过程中的稳定性和平衡性。
因此,在制动布置方案中,需要合理安排前、后轮制动器的布置位置,使得制动力能够均匀地分配到各个轮胎上,以确保车辆的稳定制动。
2. 刹车响应时间短公交车的刹车响应时间直接关系到乘客的乘坐舒适度和安全性。
在制动布置方案中,需将制动液管路优化,缩短刹车指令的传递时间,确保刹车能够及时响应,提高制动的灵敏度。
3. 刹车力度可调公交车行驶过程中,不同的路况和载荷都会对制动性能产生影响。
因此,在制动布置方案中,应该考虑安装可调节刹车力度的装置,以便根据实际需求和情况对刹车力度进行调整。
实施步骤1. 制动器位置选择在制动器位置选择时,应考虑到车辆的布局和空间限制。
一般来说,前轮制动器安装在车辆前部,后轮制动器安装在车辆后部,以保证制动力的平衡。
同时,还应考虑到制动器与其他部件(如悬挂系统)的衔接和配合,确保制动器的安装牢固可靠。
2. 制动管路布置制动管路的布置要求紧凑、合理,并且尽量减小刹车液的压力损失。
在设计制动管路时,应考虑到管路的长度、直径、连接方式等因素。
另外,为了提高制动效果,可以采用分段布置管路的方式,即将管路分成不同的段落,以减小制动液的压力损失和传递时间。
3. 制动踏板设计制动踏板的设计也是制动布置方案中的重要环节。
制动踏板的设计应该符合人体工程学原理,并且具有良好的力传递特性。
保证乘客可以轻松踩下制动踏板,并且制动力能够准确地传递到制动器上。
制动硬管技术要求及试验性能

制动硬管技术要求及试验性能发布实施发布目录前言 (1)1 范围 (2)2 规范性引用文件 (2)3 结构型式及尺寸 (2)4 技术要求 (5)5 试验方法 (8)6检验规则 (10)7包装,运输,贮存 (10)前言本标准按照GB/T 1.1—2020给出的规则起草。
本标准由提出。
本标准由归口。
本标准起草部门:本标准主要起草人:本标准为首次发布。
制动硬管技术条件及试验性能1 范围本标准规定了汽车制动硬管技术要求、试验内容。
本标准适用于汽车的制动硬管。
2 规范性引用文件下列文件对于本文件的应用是必不可少的。
凡是注日期的引用文件,仅注日期的版本适用于本文件。
凡是不注日期的引用文件,其最新版本(包括所有的修改单)适用于本文件。
SAE J463-2002 锻铜和铜合金SAE J527-2000 铜焊双层壁低碳钢管SAE J533-1999 管的扩口SAE J1290-2002 汽车液压制动系统——公制管联接件YB/T 4164-2007 双层铜焊钢管3 结构型式及尺寸3.1 A 型制动硬管总成的型式按图 11—双层扩口式硬管 2—管接头3.1.1双层扩口式硬管形状及尺寸按图 2 所示图2双层扩口式硬管形状及尺寸3.1.2管接头尺寸按图 3 所示图3管接头尺寸型式3.2 B 型制动硬管总成的型式按图 4图4 B 型制动硬管总成的型式前锥鼓式硬管尺寸按图 5 所示。
图5 前锥鼓式硬管尺寸3.2.1管接头尺寸及尺寸按图 6 所示图6 管接头尺寸型式及尺寸3.3 锥面密封的管路螺纹孔/内螺纹尺寸锥面密封的管路螺纹孔的形式及尺寸应符合图7的规定。
图7锥面密封的管路螺纹孔的形式及尺寸4 技术要求4.1 一般要求4.1.1 制动硬管总成应符合本标准规定,并按照经规定程序批准的技术图样及文件制造。
制动硬管总成商标标记执行公司标准,产品标记方法执行公司标准。
4.1.2 制动硬管总成的坐标尺寸应符合图样要求。
4.1.3 制动硬管内外表面应清洁、光滑,并不得有对使用有害的缺陷。
管线路布置设计规范
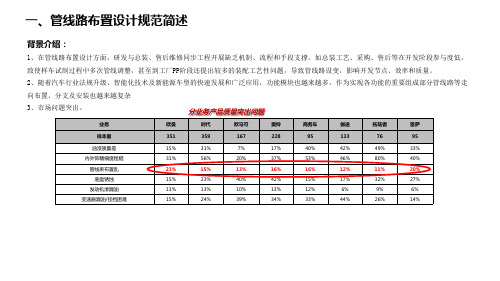
图51 管线集中固定,且合理分层图向图示-错误
图50 中后桥处布置图示-错误
四、整车管线路布置规范
6.1.7 燃油管路布置要求
➢ 燃油管路排列和走向应整齐一致,层次分明、便于安装。尽量采用水平或垂直布管,平行或交插的管系之间,应走向一致,间隙均匀。见图12。
图12 燃油管路布置图示
图13/14 水管固定及成型布置图示
四、整车管线路布置规范
6.1.9 管线支架及管夹布置要求 ➢ 管夹布置时要综合考虑整车管线走向,尽量同一部位共用支架、集中固定。 ➢ 在发动机悬置、变速箱托架等管线易干涉部位必须增加专用支架进行管线防护;防止管线路在装配和使用过程中被周围边界零部件磨碰。
➢ 门本身是运动机构,车门线束铰链部位在布置时需考虑最大/小运动极限,做好线束的防护固定,防止车门线束的疲劳断裂;同时车门线束铰链 部位是暴露的,需考虑橡胶件的密封和孔的相对位置,门的过孔一般低于车身的过孔,见图10。
➢ 转向轮气室、制动传感器处的相对运动由管路保证,此处线束随管路一起固定,线束尽可能在管路下面不暴露,不允许线束和管路相互缠绕交叉。
指外露的经过金属冲裁或切削形成的锐边,以及普通铸造、锻造形成的金属表面。如:螺栓的螺纹、车架纵梁与横梁翼缘、车架上各种 孔边缘以及冲压件的锐边。 2.6 固定点:
指管线路通过管夹、支架、卡扣、扎带等实现安装固定的点位。
二、整车管线路布置原则
5. 整车管线布置主要遵循如下原则:
➢ 基本功能: 管线应满足管线路制造工艺要求和管线路的基本功能要求;
•支架设计遵循如下原则: •支架形状要能尽可能引导管线走向 •支架设计要根据管线特点起到必要的防 护作用 •支架设计时,若用在管线较多部位尽可 能设计成复合型支架
液压制动管路技术协议
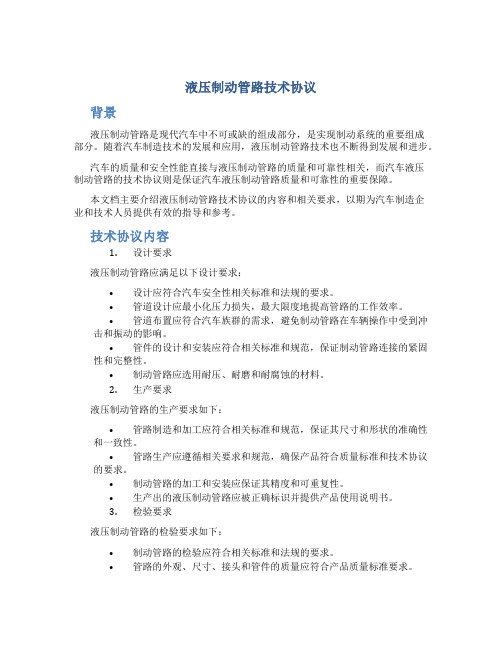
液压制动管路技术协议背景液压制动管路是现代汽车中不可或缺的组成部分,是实现制动系统的重要组成部分。
随着汽车制造技术的发展和应用,液压制动管路技术也不断得到发展和进步。
汽车的质量和安全性能直接与液压制动管路的质量和可靠性相关,而汽车液压制动管路的技术协议则是保证汽车液压制动管路质量和可靠性的重要保障。
本文档主要介绍液压制动管路技术协议的内容和相关要求,以期为汽车制造企业和技术人员提供有效的指导和参考。
技术协议内容1.设计要求液压制动管路应满足以下设计要求:•设计应符合汽车安全性相关标准和法规的要求。
•管道设计应最小化压力损失,最大限度地提高管路的工作效率。
•管道布置应符合汽车族群的需求,避免制动管路在车辆操作中受到冲击和振动的影响。
•管件的设计和安装应符合相关标准和规范,保证制动管路连接的紧固性和完整性。
•制动管路应选用耐压、耐磨和耐腐蚀的材料。
2.生产要求液压制动管路的生产要求如下:•管路制造和加工应符合相关标准和规范,保证其尺寸和形状的准确性和一致性。
•管路生产应遵循相关要求和规范,确保产品符合质量标准和技术协议的要求。
•制动管路的加工和安装应保证其精度和可重复性。
•生产出的液压制动管路应被正确标识并提供产品使用说明书。
3.检验要求液压制动管路的检验要求如下:•制动管路的检验应符合相关标准和法规的要求。
•管路的外观、尺寸、接头和管件的质量应符合产品质量标准要求。
•各项测试(如压力测试、扭矩测试等)应符合规定要求,确保有良好的流通性、密封性和耐久性。
•检验应被正确地记录和保留。
4.保养要求液压制动管路的保养要求如下:•制动管路的使用前应进行检查,并进行必要的维护和保养。
•制动管路应避免过度负荷和不当的使用,严禁超速行驶和频繁紧急制动。
•制动管路在使用中应被适当检查,发现问题及时进行修复或更换。
•制动管路的更换应在保养要求中规定的期限到期时进行。
液压制动管路技术协议的制定有助于规范液压制动管路的设计、生产、检验和保养等方面,并能有效提高汽车制动系统的质量和可靠性,确保行车安全。
罐车系列通用技术要求

1.目的规范公司半挂车的生产工艺要求,保证公司罐车产品质量。
2.适用范围公司所有罐车产品。
3.内容3.1 通用要求3.1.1 自制件一律按图纸要求,图纸中未注公差均按±1mm。
3.1.2 所有自备件均需去飞溅、飞边,无割渣。
3.1.3 所有焊缝均牢固可靠,焊缝均匀美观,去溅焊渣,无焊瘤、夹渣、虚焊、裂纹等焊接质量缺陷。
3.1.4 所有相贴或成形后不易喷涂油漆的部件(如相接合的平面、距离较近的二个面与箱形件等),焊接前应涂防锈底漆。
3.1.5 车辆成形后,各部件表面不得有锤击、引弧等印迹。
3.1.3 所有紧固件均要拧紧,无特殊要求的以弹垫压平为准。
有扭矩要求的按规定值进行拧紧。
3.2 车架纵梁3.2.1 车架纵梁长度公差为±5mm,水平直线度在任意1000mm长度内为2mm,在全长范围内不大于10mm,且向上拱10-20mm。
3.2.2纵梁腹板应处于上下翼面的中间,偏差不大于3mm,上下翼面对腹板的垂直度公差不大于1.5mm。
3.3 车架3.3.1 两车架纵梁相对平行且垂直于车架中心轴所在的平面,焊装后每根纵梁在纵向直线度大于10mm。
3.3.2 车架总长度极限偏差为±5mm,宽度极限偏差在任意点测量为±4mm。
3.3.3 车架边梁在水平直线度在任意1000mm长度内为2mm,在全长范围内不大于10mm,且只允许向上拱起。
腹面垂直于水平面,其垂直度不大于1.5mm。
3.3.4 车架横梁应垂直于车架中心纵向平面,其垂直度在全长范围内不大于3mm;左右应在同一水平面内,左右高差不大于3mm。
3.3.5 车架纵梁上加强板应于下翼面贴合紧密。
3.3.6 牵引销装焊在车架中心上,其左右偏差不大于1mm。
牵引销支承板平面平整,平面度不小于2mm,且表面无尖锐等杂物。
3.3.7 板簧支架定位准确,左右中线应与车架重合,偏差不大于1mm;左右支架拉杆销中心与牵引销中心的对角线偏差不大于3mm,各支架的拉杆销中心的对角线偏差不大于3mm,支架的前后距离偏差不大于3mm。
GB72582004、GB167372004、GB167352004标准宣贯ppt69(1)
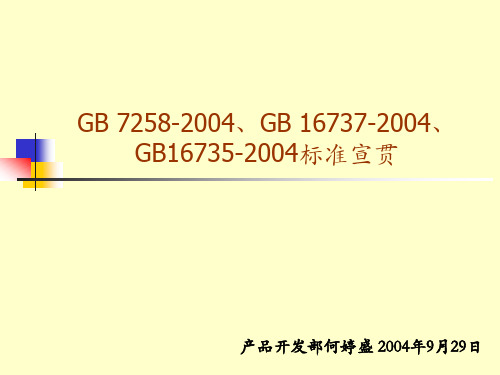
照明、信号装置及其他电器设备 增加灯具(除转向信号灯及消防车、救护车、 工程救险车和警车安装使用的标志灯具外) 不允许闪烁的要求 与GB 4785、GB 18100协调
照明、信号装置及其他电器设备
对称/同功能灯具光色/亮度不应明显差异 提高车速≥70km/h前照灯远光发光强度要求 前照灯远近光布置(近光位于外侧、上侧) 调整汽车前照灯照射位置要求
车发展研究中心、天津摩托车技术中心、天津市公安交通管理 局车辆管理所等8家
4
GB 7258修订情况简介
修订情况
经过八个月的工作,历经五稿修改完善 2004年5月、6月,形成标准报批稿上报 国家质检总局、国家标准化管理委员会正式
批准发布《机动车运行安全技术条件》 标准性质:强制性国家标准 发布日期:2004年7月12日 实施日期:2004年10月1日
修订情况
国家标准委《2003年制修订国家标准项目计划》 公安部科技局公科质[2003]52号文件 组长:公安部交通管理科学研究所/交通部公路科学研究所 技术归口:公安部道路交通管理标准化技术委员会 2003年9月,成立标准修订工作小组 参加起草单位 : 中国汽车技术研究中心、机械工业农用运输
2
GB 7258修订情况简介
GB 7258标准的提出和适用 为公安车管人员提供技术依据 适合新生产车、在用车 用于车辆注册、年检、事故鉴定、报 废 核准车辆技术特性及功能的指南 常用车辆检验项目的方法 约束车辆的运输和驾驶行为 对车辆的设计、生产产生影响
3
GB 7258修订情况简介
27
GB 7258主要内容
安全防护装置
增加乘用车、客车、货车的安全带安装要求 增加乘用车第3排可折叠座椅及第3排以后
制动系统作业指导书

13
1.3.4 制动踏板 制动踏板是在满足制动性能的前提下,根据人机工程学原理,按相应的的连
接结构进行设计和开发的。采用柱销形式与真空助力泵相连。
CHB021
CHB011
目前随着碰撞法规的要求提高,碰撞后制动踏板对人体腿部的倾入伤害也提 出要求。因此制动踏板还需考虑防倾入设计。如下图所示为 CRV 防侵入式制动踏 板:
表21制动法规基本要求序号试验路面应具有附着系数约为08的高附着系数路面和附着系数小于等于03的低附着系数路面gb72582004gb216702008载重空载满载f65500n双手不离开方向盘踏板行程应不大于踏板全行程的五分应急制动部分管路失效168md244msf65500n双手不离开方向盘gb216702008助力器失效驻车制动操纵手柄力400n停驻角度2012v30kmh附着利用系数曲线1在车辆所有载荷状态下当制动强度z处于01508之间时后轴附着利用系数曲线不应位于前轴上方2当附着系数在0208之间时制动强度z010702即0208之间时前轴后轴利用附着系数曲线应在z00407曲线之下3作为生产一致性检查的替代要求当制动强度在01508之间时后轴曲线应位于曲线z09以下即位于z09曲线以下详见制动系统计算报告2424根据上述两项最基本的前提条件再加上市场的确定使用条件竞争性及主机厂生产实际情况来确定设计方向
11
12
1.3.2.2.2 中心阀串联式双腔制动主缸原理图
中心阀式制动主缸特点: 由于 ABS 系统中液压泵的作用,使制动系统的制动液压发生波动,正是这种
作用使制动主缸内的液压产生波动,且活塞同时发生相对移动,其液压的变化频 率可达每秒 15 次左右,液压可达 20Mpa 高压,对于补偿孔式主缸,当活塞相对 缸体移动时,由于高压的作用,在补偿孔和回油孔处就会发生密封皮碗的过度摩 损或切削现象,这样就会造成制动主缸失效,从而造成制动失效,所以,在 ABS 系统中应采用中心阀式制动主缸,克服了以上不足,从而提高制动系统的安全可 靠性,所以在 ABS 及 ESP 系统中必须采用中心阀式制动主缸。
《道路车辆液压制动系统第1部分双喇叭口金属管螺纹孔》编制说明

道路车辆 液压制动系统第1部分:双喇叭口金属管、螺纹孔、螺纹管接头及管座编制说明1 任务来源工业和信息化部2009年12月15日印发的关于“2009年第二批工业行业标准制修订计划”文,计划号为2009-2434T-QC。
2 主要起草单位和工作组成员主要起草单位:东风汽车股份有限公司商品研发院、北汽福田汽车股份有限公司、浙江亚太机电股份有限公司。
工作组成员:张耀举、龚洪、王万顺、黄国兴、黎明。
3标准制定的目的和意义随着汽车行业不断发展,技术引进不断加快,工艺与材料技术水平也有了较大进步,汽车液压制动系统用金属管、接头和相关部件的品种出现了较大的新陈代谢,技术要求也有较大提高。
为了适应行业发展的需要,全国汽车标准化技术委员会于2009年提出了制定“道路车辆 液压制动系统 第1部分:双喇叭口金属管 螺纹孔 螺纹管接头及管座 ”标准要求。
该标准的制定,可进一步完善液压制动系统管路系统用金属管、接口及相关部件,提供双喇叭口金属管产品生产的一致性和互换性,为后续维修检测等带来方便。
4标准制定的基本原则尽量等同采用国际或国外先进标准,其技术水平应达到国际先进,评价指标的确定应充分考虑我国现有产品的技术水平,同时应能促进我国产品质量和水平的提高。
起草小组通过对目前液压制动金属管、螺纹孔、螺纹接头及管座国内外标准进行分析,最后确定以ISO13486-1(1999发布)标准为基础,结合我国的实际情况,适当给予补充,并对部分要求进行修改。
标准的编排格式按GB/T 1.1-2009要求编制。
5国内外相关标准情况在国际上,针对道路汽车用液压制动系统双喇叭口金属管,螺纹孔主要是国际标准ISO13486-1,美国采用SAEJ514/J533标准与ISO13486及国内通常管径使用规格有较大差别;日本JASO标准F402对管材力学性能没有直接规定。
目前国内只有单喇叭口标准,没有双喇叭口标准,部分企业制定了双喇叭口标准,但管径规格不是系列化,国内没有统一液压制动金属管方面双喇叭口金属管口、螺纹孔、螺纹接头及管座等行业和国家标准,目前我国颁布道路车辆,液压制动系统,第1部分 双喇叭口金属管、螺纹孔标准及管座标准,可提高液压制动密封性及可靠性。
汽车管线布置规范

汽车管线布置规范篇一:整车管线分离布置要求2.整车管线分离布臵要求2.1底盘管线路分离布臵要求2.1.1底盘线束和管路分开单独进行布臵,自制底盘管路布臵时,要预留线束的过线通道,当线束和管路都要经过同一位臵时,线束管路应上下分层布臵或并排进行布臵,管路布臵在底盘下方,线束布臵在底盘管路上方(如槽钢大梁结构,管路布臵在槽钢内侧,线束布臵在槽钢上侧);当因底盘骨架结构导致线束不能布臵在管路上方时,线束避免布臵在所有油管路接头下方(如中客及大客变速箱处的助力油管路);当管线束不能避免交叉时,交叉点应选择在避开油管接头处进行交叉,线束严禁在管路接头处的下方进行交叉。
2.1.2底盘线束不要依附燃油管路、助力油管路、离合油管路、档线等进行绑扎,底盘线束、暖风管路的固定位臵应不影响其它部件的安装、拆卸及检修,选择单独的过线通道进行布臵。
当线束为油管的一部分或油管在同一位臵受限时,用双头扎带进行紧固,如燃油加热器线束、ABS轮速传感器、蹄片磨损线束、气压传感器线束等。
2.1.3发动机周圈的管、线束进行布臵时,必须用合适的线束固定钢卡进行固定,扎带只进行辅助绑扎,所有钢卡、扎带绑扎到位,严禁出现线束与钢卡及扎带之间相互摩擦现象。
绑扎间距不大于300,线束悬空距离不大于350。
2.1.4底盘线束布臵时要距离打气泵管路、涡轮增压管、中冷器进气管等热源点距离在100以上,线束距传动轴、飞轮、皮带等运动件最近距离在20以上;当因车辆结构因素而无法保证时,线束用阻燃隔热材料管、陶瓷纤维带或隔热垫等隔热材料进行可靠防护后,最小距离控制在50以上。
2.1.5底盘管路、线束应布臵平顺,严禁出现管线之间交错缠绕,管、线路应呈现横平竖直的走向,拐角处过渡要平顺,当有多种线束或管路在同一处进行绑扎时,整理平顺绑扎成束后再依附物体进行绑扎。
2.1.6管、线路应避免过棱角位臵,如不能避免,必须加龙骨胶条、过线胶圈或密封胶进行防护。
2.1.7当管、线束在相对运动的两个物体上进行布臵时,管、线路应在振动频率不一样的物体之间进行可靠的固定,并留有适当的长度余量。
汽车气制动管束标准
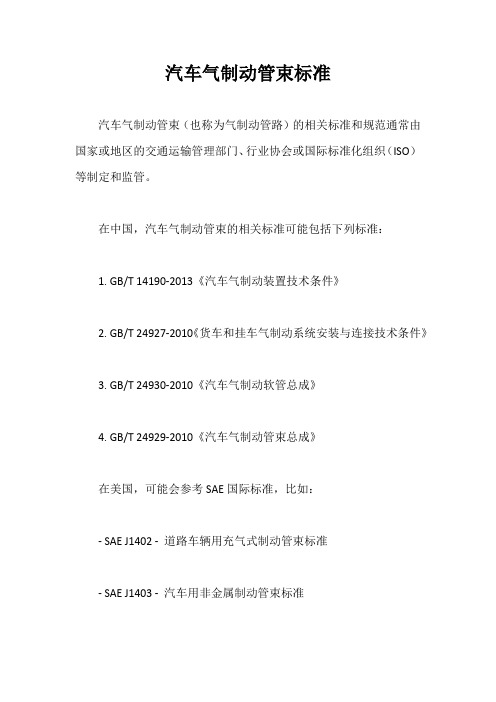
汽车气制动管束标准
汽车气制动管束(也称为气制动管路)的相关标准和规范通常由国家或地区的交通运输管理部门、行业协会或国际标准化组织(ISO)等制定和监管。
在中国,汽车气制动管束的相关标准可能包括下列标准:
1. GB/T 14190-2013《汽车气制动装置技术条件》
2. GB/T 24927-2010《货车和挂车气制动系统安装与连接技术条件》
3. GB/T 24930-2010《汽车气制动软管总成》
4. GB/T 24929-2010《汽车气制动管束总成》
在美国,可能会参考SAE国际标准,比如:
- SAE J1402 -道路车辆用充气式制动管束标准
- SAE J1403 -汽车用非金属制动管束标准
这些标准通常包括气制动管束的技术要求、规格、安全性能、安装要求等,以确保气制动系统的正常运行和安全性。
具体的标准和规范需要根据您所在地区的法律法规和行业要求来确定,在实际应用中,建议您遵循当地的相关法规和标准进行操作,并在必要时咨询专业人士。
制动系统设计规范精选全文完整版

可编辑修改精选全文完整版一、国标要求1、GB 12676-1999《汽车制动系统结构、性能和试验方法》2、GB 13594-2003《机动车和挂车防抱制动性能和试验方法》3、GB 7258-1997《机动车运行安全技术条件》二、整车基本参数及样车制动系统主要参数整车基本参数样车制动系统主要参数三、计算1. 前、后制动器制动力分配1.1 地面对前、后车轮的法向反作用力 公式:gz h dt du mGb L F +=1 ………………………………(1) gz h dt du mGa L F -=2 (2)参数:1z F ——地面对前轮的法向反作用力,N ;2z F ——地面对后轮的法向反作用力,N ;G ——汽车重力,N ;b ——汽车质心至后轴中心线的水平距离,m ;a ——汽车质心至前轴中心线的距离,m 。
m ——汽车质量,kg ;gh ——汽车质心高度,m ;L ——轴距,m ;dt du——汽车减速度,m/s 2四、制动器的结构方案分析制动器有摩擦式、液力式和电磁式等几种。
电磁式制动器虽有作用滞后小、易于连接且接头可靠等优点,但因成本高而只在一部分重型汽车上用来做车轮制动器或缓速器。
液力式制动器只用作缓速器。
目前广泛使用的仍为摩擦式制动器。
摩擦式制动器按摩擦副结构形式不同,分为鼓式、盘式和带式三种。
带式只用作中央制动器。
一、鼓式制动器鼓式制动器分为领从蹄式、双领蹄式、双向双领蹄式、双从蹄式、单向增力式、双向增力式等几种,见图la ~f 。
不同形式鼓式制动器的主要区别有:①蹄片固定支点的数量和位置不同。
②张开装置的形式与数量不同。
③制动时两块蹄片之间有无相互作用。
因蹄片的固定支点和张开力位置不同,使不同形式鼓式制动器的领、从蹄数量有差别,并使制动效能不同。
制动器在单位输入压力或力的作用下所输出的力或力矩,称为制动器效能。
在评比不同形式制动器的效能时,常用一种称为制动器效能因数的无因次指标。
制动器效能因数的定义为,在制动鼓或制动盘的作用半径R 上所得到的摩擦力(RM μ)与输入力0F 之比,即RF M K 0μ=式中,K 为制动器效能因数;μM 为制动器输出的制动力矩。
制动化工程施工规范

制动化工程施工规范第一条为了正确、安全、高效地实施制动化工程,保障工程质量,减少事故发生,特制定本规范。
第二条施工单位应具备相应的资格、技术、人员和设备,并应在规定的时间内完成工程建设任务。
第三条施工单位应根据工程的实际情况,合理制定施工方案,并提交给相关主管部门进行审核。
第四条在施工前,须对工程现场进行认真勘察,确定施工范围、施工时间、施工方法等。
第五条施工单位应保证施工现场的环境卫生,并安排专人负责施工现场的管理工作。
第六条在施工前,应对施工人员进行必要的培训,包括施工安全、施工规范等方面的知识。
第七条在施工中,严格执行国家相关的法律法规,不得违法违规施工。
第八条施工单位应认真执行有关的标准和规范,确保施工质量。
第九条在施工中,必须配备必要的安全设备和防护措施,确保施工人员的生命安全。
第十条施工单位应按照工程进度安排施工人员,保证工程按时完成。
第十一条在施工过程中,应及时处理施工中发现的问题,保证工程质量。
第十二条在施工结束后,应对工程进行验收,确保工程质量符合相关标准。
第十三条在施工中,应保证与周边环境的协调,避免对周边环境造成影响。
第十四条在施工期间,应根据实际情况进行调整和改进施工方案,以保证工程质量和安全。
第十五条在施工中,应加强与监理单位的沟通和协调,及时解决施工中的问题。
第十六条在施工中,应保证工程文件的完整、准确,确保施工过程的记录和整理。
第十七条在施工中,应加强对施工人员的监督和检查,确保施工质量。
第十八条在施工结束后,应建立相关档案,包括施工过程、施工人员、施工材料等相关信息。
第十九条对于施工单位和相关人员的不良行为,应依法进行处罚和处理。
第二十条本规范由XX行业协会负责解释。
以上就是制动化工程施工规范的内容,希望广大施工单位能认真遵守,保证工程质量和施工安全。
nw12汽车管路标准

nw12汽车管路标准(原创实用版)目录1.NW12 汽车管路标准的概述2.NW12 汽车管路标准的具体内容3.NW12 汽车管路标准的应用4.NW12 汽车管路标准的重要性正文一、NW12 汽车管路标准的概述W12 汽车管路标准是我国汽车行业在管路设计、制造和使用方面的一项重要技术标准。
NW12 代表着一种特定的管路规格,其中“N”表示管路的类型,而“W12”则表示管路的尺寸。
这一标准规定了汽车管路的尺寸、形状、材料、制造工艺和质量要求等方面的内容,旨在确保汽车管路的安全、可靠和互换性。
二、NW12 汽车管路标准的具体内容1.尺寸:NW12 汽车管路的尺寸主要包括外径、壁厚和长度等参数,这些参数对于保证管路的流量、压力和稳定性等方面至关重要。
2.形状:NW12 汽车管路标准规定了管路的截面形状,如圆形、矩形等,以满足不同系统对管路的特殊需求。
3.材料:NW12 汽车管路标准对管路材料的选择和质量要求进行了详细规定,以确保管路的强度、耐腐蚀性和耐磨性等方面的性能。
4.制造工艺:标准中还详细描述了管路的制造工艺,包括冷拔、热轧、焊接等方法,并对工艺过程中的各项参数和质量要求进行了明确规定。
5.质量要求:NW12 汽车管路标准对管路的质量要求进行了严格规定,包括表面光洁度、尺寸公差、弯曲度、泄漏试验等方面。
三、NW12 汽车管路标准的应用W12 汽车管路标准广泛应用于各类汽车的燃油、润滑、冷却、制动等系统中,确保汽车管路的设计、制造和使用满足安全、可靠和互换性的要求。
四、NW12 汽车管路标准的重要性W12 汽车管路标准的实施对于我国汽车行业的健康发展具有重要意义。
首先,标准为汽车管路的设计、制造和使用提供了统一的技术依据,有助于提高产品质量和安全性能。
其次,标准促进了汽车管路行业的规范化、规模化发展,提高了生产效率和经济效益。
第1页共1页。
管路间隙
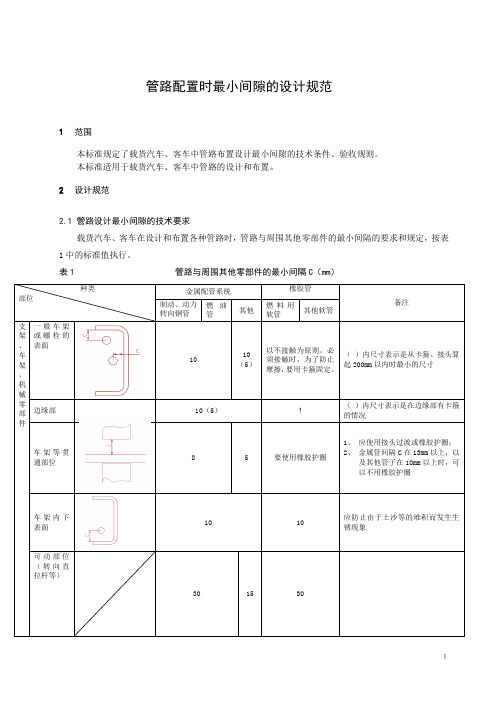
部位
金属配管系统
橡胶管
备注
制动、动力转向钢管
燃油管
其他
燃料用软管
其他软管
支架
、
车架
、
机械零部件
一般车架或螺栓的表面
10
10
(5)
以不接触为原则。必须接触时,为了防止摩擦,要用卡箍固定。
()内尺寸表示是从卡箍、接头算起200mm以内时最小的尺寸
边缘部
10(5)
↑
()内尺寸表示是在边缘部有卡箍的情况
3、当液压制动软管的最小间隔C在400mm以下时,软管的温度不得高于70℃。
与左边所示零件的平行超过200mm以上
同上
180
必须有隔热板
180
必须有隔热板
300
接头
螺母部位
20
1、左侧表格内规定的是一般尺寸,特殊情况下,可根据配管附近的状态进行适当修正;
2、燃油管的接头部位不能设置在发热体的上部
车架等贯通部位
8
5
要使用橡胶护圈
1、应使用接头过渡或橡胶护圈;
2、金属管间隔C在13mm以上,以及其他管子在10mm以上时,可以不用橡胶护圈
车架内下表面
10
10
应防止由于土沙等的堆积而发生生锈现象
可动部位(转向直拉杆等)
30
15
30
种类
部位
金属配管系统
橡胶管
备注
制动、动力转向钢管
燃油管
其他
燃料用软管
其பைடு நூலகம்软管
管子之间
平行部位(直)
10
20
平行部分超过500mm,管子之间的间隔在20mm以下时,应使用一个卡箍固定两根管子
- 1、下载文档前请自行甄别文档内容的完整性,平台不提供额外的编辑、内容补充、找答案等附加服务。
- 2、"仅部分预览"的文档,不可在线预览部分如存在完整性等问题,可反馈申请退款(可完整预览的文档不适用该条件!)。
- 3、如文档侵犯您的权益,请联系客服反馈,我们会尽快为您处理(人工客服工作时间:9:00-18:30)。
制动管路布置规范1.范围本标准规定了制动管路布置规范。
本标准适用于商用车气制动系统开发。
2.规范性引用文件下列文件对于本文件的应用是必不可少的。
凡是注日期的引用文件,仅注日期的版本适用于本文件。
凡是不注日期的引用文件,其最新版本(包括所有的修改单)适用于本文件。
GB/T 34020.2-2017双层卷焊钢管第2部分:汽车管路系统用管GB/T 3639精密管GB/T 18033无缝铜水管和铜气管GB 16879制动软管的结构、性能要求及试验方法QC/T 80道路车辆-气制动系统尼龙(聚酰胺)管3.术语和定义3.1 供能管路连接空压机和干燥器之间的制动管路;通常包括:高温软管、钢管或铜管、管接头及紧固部件。
3.2 制动软管连接干燥器、储气筒、各制动阀(制动总泵、继动阀、差动继动阀、快放阀、ABS电磁阀)之间的管路;通常包括:尼龙管、橡胶制动软管、管接头及紧固部件。
连接气室的制动软管需3C认证。
4.布置要求4.1 零部件布置的优先原则制动管路布置,优先考虑空压机、干燥器、储气筒及各制动阀的位置。
各零部件布置要方便后续管路布置。
管路走向平顺,不能打折、不能和周边件干涉。
在进行制动管路布置时,由于受到诸多因素的影响,因此要充分考虑各系统、各部件的关系。
各零部件模块化布置,方便车型拓展,各零部件布置后需检修方便。
4.1.1 空压机、干燥器布置要求a)空压机一般布置于车辆后部,安装位置要求通风良好(或安装在散热风扇附近)、远离热源(距离热源小于70mm需加装隔热板),并能防止雨水喷溅在机器上,加油、放油方便;有利于观察油镜和压力表。
b)干燥器布置于空压机附近,位置方便钢管连接空压机。
干燥器上方至少应有35mm以上空间,以便更换干燥罐。
干燥器下方不布置零部件,以免干燥器卸荷时排出油水污染零部件。
4.1.2 储气筒布置要求a)储气筒布置要求方便接管路,接头安装拆卸方便。
b)储气筒布置在车辆底部时,最低点应高于该位置最底部骨架,避免车辆运行中磕碰。
c)储气筒不能布置于乘客区及风道内,避免储气筒爆裂发生意外;不能布置在前后保险杠位置,避免发生碰撞后影响制动性能。
4.1.3 各制动阀布置要求a)制动总泵根据人机工程布置在驾驶员座椅前部地板上。
b)ABS电磁阀布置在气室附近车身骨架上,一般在前、后悬骨架上。
d)快放阀、继动阀布置在ABS电磁阀附近骨架上。
d)放水阀直接布置在储气筒上或车辆裙边,方便驾驶员维护的位置;也选用自动放水阀和智能排水系统。
4.2 制动管路布置要求在制动管路中有高温软管、钢管(铜管)、尼龙管、橡胶软管四种管路和各种接头。
4.2.1 钢管(铜管)a)电动空压机排出的温度高达100℃,所以从空压机到干燥器的管路一般采用钢管,钢管一般采用精密管和双层卷焊管。
空压机输出压缩空气温度较高,且含有油、水及尘埃等物质,管材内外径需要做防腐处理。
b)为避免管路锈蚀及获得良好散热,连接空压机出气口制动管路选用紫铜管。
d)管路一般采用锥型管节式和扩口式,管路外径一般大于等于15mm。
d)空压机到干燥器管路长度应为4~6m,以保证干燥器进气口温度降至约65℃。
e)管路应连续下行,干燥器进气口一般为管路最低点。
f)管路内应清洁,安装应固定牢靠,不与其它管线束困在一起。
4.2.2 高温软管电动空压机振动较大,钢管(铜管)与空压机直接连接,接口易振裂或松动而漏气,一般在空压机与钢管(铜管)之间连接高温软管。
高温软管走向应平顺,不能扭曲打折,不能与周边件干涉。
4.2.3 尼龙管a)尼龙管为主要制动管路,材料采用PA11。
尼龙管柔性好,可适合较大变形弯曲,一般不用定型就能直接装配,减少设计人员大量工作;尼龙管耐腐蚀,使用寿命长,耐油性能好。
b)尼龙管走向应避开尖锐和高温零部件,不允许与酸、碱或其它腐蚀性溶液接触,并按要求装配尼龙管保护套。
c)尼龙管应固定可靠,不能与其它零部件有相对运动。
每隔300mm,尼龙管应按图纸要求用适宜的管夹固定一次。
固定时不应扭曲或压扁尼龙管。
d)为保证尼龙管不打折,尼龙管装配时最小弯曲半径不小于表1的规定。
表1 尼龙管最小弯曲半径e表2 尼龙管联管螺母的紧固要求f管路两端粘贴相同色标,具体要求按表3。
表3 尼龙管色标要求4.2.4a)由于不同载荷气室相对车架状态不一,转向时气室随转向轮转动及车辆运行中车轮跳动,所以连接气室管路一般采用带钢丝护套的橡胶制动软管。
b)安装连接转向桥气室橡胶管时,调整安装接头方向;要求转向极限位置时,橡胶管不得打折,不得与周边件干涉。
c)橡胶制动软管不得与周边件存在运动干涉。
4.2.5 接头a)螺纹管接头的紧固要求应符合表4要求,普通螺纹接头的紧固要求应符合表5要求。
表4 螺纹管接头的紧固要求b表5 普通螺纹接头体的紧固要求图1、图2为常见制动原理图,制动管路各接口需按图连接,不允许接错。
图1 制动原理图图2 带ASR制动原理图附录A(规范性附录)制动管路技术要求A.1 钢管技术要求A.1.1钢管材料为:精密管20-16x1.5-Y-GB 3639;A.1.2 管材内外表面与接头处做防腐处理,镀锌钝化Fe/EpZn8-QC/T 625;A.1.3 总成100%在1.4MPa压力下进行气密性试验,无任何渗漏现象;A.1.4 管路两端配装内螺纹为M22x1.5的卡套螺母及相应卡套;A.1.5 管路两端进行防尘处理。
A.2 铜管技术要求A.2.1钢管材料为:紫铜,规格φ16x2;A.2.2 铜管外表面不允许有裂纹、碰伤等有害缺陷;A.2.3 总成100%在1.4MPa压力下进行气密性试验,无任何渗漏现象;A.2.4 管路两端配装内螺纹为M22x1.5的卡套螺母及相应卡套;A.2.5 钢管总成应满足GB/T 18033的规定;A.2.6 管路两端进行防尘处理。
A.3 高温软管技术要求A.3.1管材及技术要求符合GB 16897的规定;A.3.2 软管耐高温220℃;A.3.3 总成100%在1.4MPa压力下进行气密性试验,无任何渗漏现象;A.3.4 总成两端接头处镀锌钝化Fe/EpZn8-QC/T 625,两端配装内螺纹为M22x1.5的卡套螺母及相应卡套;A.3.5 两端接头材质为35-GB/T 699,技术条件按GB/T3765;A.3.6 管路总成应加认证标识和认证号,要求应符合GB 16897。
A.3.7 管路两端进行防尘处理。
A.4 尼龙管管技术要求A.4.1尼龙管材料为:PA11;A.4.2 尼龙管两端平整、无毛刺,管路上缠护套,两端管口应进行防尘处理;A.4.3 装配尼龙管总成时应轴向压紧,并保证不松脱,压紧后各零件不得有外形变化;A.4.4 管路两端粘贴相应色标;A.4.5 快插接头需满足DIN 73377要求;A.4.6 尼龙管总成满足QC/T 80的要求;A.4.7 管路两端进行防尘处理。
A.5 制动软管技术要求A.5.1胶管材料内层为丁晴橡胶,外层为氯丁橡胶;A.5.2 总成100%在1.4MPa压力下进行气密性试验,无任何渗漏现象;A.5.3 胶管总成两端接口形式为卡套式,配装内螺纹为M18x1.5的卡套螺母及相应卡套;A.5.4 总成爆破压力≥5.52MPa;A.5.5 胶管规格φ17x10;A.5.6 橡胶管外加钢丝护套;A.5.7 胶管其余技术性能应符合GB16897规定;A.5.8 管路两端进行防尘处理。
附录B(规范性附录)气压制动的特殊要求B.1 最不利制动气室响应时间(A)采用气压制动的汽车,按照GB12676 规定的方法进行测试时,从踩下制动踏板到最不利的制动气室响应时间(A)应小于等于0.6s;A 的数值(取值到0.01s,精确到0.05s)应在产品标牌(或车辆易见部位上设置的其他能永久保持的标识)上清晰标示。
采用气压制动的汽车,在设计和制造上每个储气筒(有压力表等压力显示装置的除外)和制动气室都应具有可用于测试制动管路压力的连接器。
B.2 气密性要求采用气压制动的机动车,在气压升至750kPa(或能达到的最大行车制动管路压力,两者取小的值)且不使用制动的情况下,停止空气压缩机工作3min 后,其气压的降低值应小于等于10kPa。
在气压为750kPa(或能达到的最大行车制动管路压力,两者取小的值)的情况下,停止空气压缩机工作,将制动踏板踩到底,待气压稳定后观察3min,气压降低值对汽车应小于等于20kPa。
B.3 储气筒额定工作气压车长大于9m 的客车,采用气压制动时,储气筒的额定工作气压应大于等于850kPa,且装备有空气悬架或盘式制动器时还应大于等于1000kPa。
采用气压制动的汽车,应在产品标牌(或车辆易见部位上设置的其他能永久保持的标识)上清晰标示储气筒额定工作气压的数值。
B.4 制动协调时间要求汽车的制动协调时间,对气压制动的汽车应小于等于0.60s;铰接客车、铰接式无轨电车的制动协调时间应小于等于0.80s。
注:附录B气压制动的特殊要求按GB7258相关规定执行。