废水蒸发方案
高盐废水蒸发工艺选择:单效多效MVR
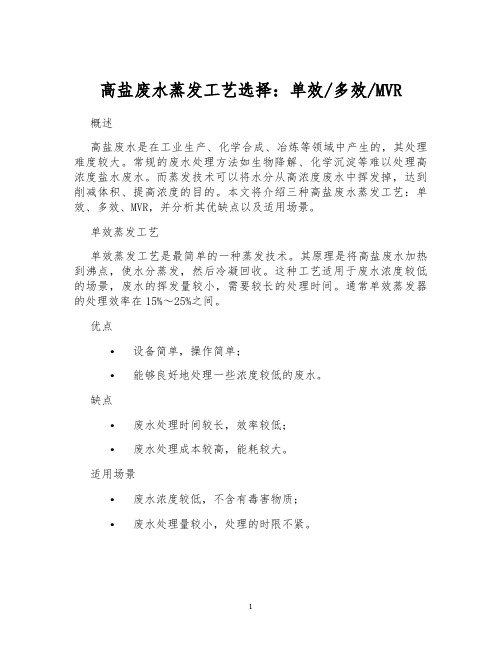
高盐废水蒸发工艺选择:单效/多效/MVR 概述高盐废水是在工业生产、化学合成、冶炼等领域中产生的,其处理难度较大。
常规的废水处理方法如生物降解、化学沉淀等难以处理高浓度盐水废水。
而蒸发技术可以将水分从高浓度废水中挥发掉,达到削减体积、提高浓度的目的。
本文将介绍三种高盐废水蒸发工艺:单效、多效、MVR,并分析其优缺点以及适用场景。
单效蒸发工艺单效蒸发工艺是最简单的一种蒸发技术。
其原理是将高盐废水加热到沸点,使水分蒸发,然后冷凝回收。
这种工艺适用于废水浓度较低的场景,废水的挥发量较小,需要较长的处理时间。
通常单效蒸发器的处理效率在15%~25%之间。
优点•设备简单,操作简单;•能够良好地处理一些浓度较低的废水。
缺点•废水处理时间较长,效率较低;•废水处理成本较高,能耗较大。
适用场景•废水浓度较低,不含有毒害物质;•废水处理量较小,处理的时限不紧。
多效蒸发工艺多效蒸发工艺是将单效蒸发器连接成多级,将蒸发失去的热量通过热量交换器传递给下一级蒸发器,达到节能的目的。
多效蒸发技术通常分为二效、三效、四效等,能够加添废水处理的效率,提高蒸发器的处理水平,将废水浓缩度提高至50%~70%。
优点•处理效率高,能够快速处理高浓度废水,节省处理时间;•设备占地面积小,能耗低。
缺点•设备多而杂,运行成本高,维护、保养难度较大;•对废水浓度变化较为敏感,需要搭配调整。
适用场景•废水浓度较高,需要快速处理;•废水处理量较大,需要较短的处理周期。
MVR蒸发工艺MVR(Mechanical Vapor Recompression )蒸发工艺是基于机械压缩对低级蒸汽进行加热,实现蒸发过程的再循环利用,使蒸汽压力渐渐上升来完成水的蒸发,并以小型离心压缩机为核心设备。
MVR蒸发与其他工艺相比,具有能耗低、设备体积小、处理效率高、操作易于自动化掌控等优点。
MVR 蒸发器处理效率相对于其他工艺高出很多,除了节省电力外也更环保。
同时MVR的出水质量高,最后的浓缩效率也特别高。
高盐废水蒸发结晶设计方案

高盐废水蒸发结晶设计方案1.设计条件:1.处理量:每小时处理量3000Kg/h。
2.湿盐产量:240Kg/h;湿盐含水量按8%计算3.设备蒸发水量:2800Kg/h。
4.蒸发出的水洁净程度能达到污水管网排放标准,可用于生产。
2.设备选型2.1 选择依据(1)溶液在蒸发过程中有结晶产生并分离出结晶。
(2)溶液从8%浓缩到饱和状态(27.3%)并结晶。
2.2 工艺及设备1.蒸发工艺:考虑到蒸发能耗大,因此选用采用并流三效蒸发工艺。
由于原料浓度较大,需要蒸发少量水份,到饱和时才能产生结晶.第二、三效采用强制外循环OSLO结晶蒸发器形式,物料经过三效蒸发,溶液在末效达到饱和并产生结晶,温度在70℃左右。
晶浆经过泵输送到结晶罐,在罐内冷却到40~45℃并进一步结晶,然后出料进入离心机进行固液分离,母液则返回蒸发器。
2.设备形式:外循环三效蒸发器,第二、三效采用强制外循环OSLO结晶蒸发器形式,出料采用泵送方式,晶浆送入结晶罐内降温结晶,然后经过离心机分离晶体和母液,母液则返回第三效蒸发器内蒸发。
3.流程:顺流(并流)方式,即原料由第一效进入,经过第二效再到第三效。
与加热蒸汽及二次蒸汽的流动方向相同。
4.预热:第三效二次蒸汽进入冷凝器之前先经过原料预热器,作为原料的第一级预热。
第一效加热蒸汽产生的冷凝水作为原料的第二级预热。
原料经过两次预热后,原料温度大约可以上升到72℃左右。
5.OSLO结晶蒸发器属于强制外循环蒸发结晶器。
操作时,料液自循环管下部加入,与离开结晶室底部的晶浆混合后,由泵送往加热室。
晶浆在加热室内升温(通常为2~3℃),但不发生蒸发。
OSLO是制盐行业中常用的一种典型的结晶器。
蒸发式OSLO结晶器是由外部加热器对循环料液加热进入真空闪蒸室蒸发达到过饱和,再通过垂直管道进入悬浮床使晶体得以成长,由OSLO结晶器的特殊结构,体积较大的颗粒首先接触过饱和的溶液优先生长,依次是体积较小的溶液;因此OSLO结晶器生产出的晶体具有体积大、颗粒均匀、生产能力大。
高盐废水蒸发结晶设计方案

高盐废水蒸发结晶设计方案1.设计条件:1.处理量:每小时处理量3000Kg/h。
2.湿盐产量:240Kg/h;湿盐含水量按8%计算3.设备蒸发水量:2800Kg/h。
4.蒸发出的水洁净程度能达到污水管网排放标准,可用于生产。
2.设备选型2.1 选择依据(1)溶液在蒸发过程中有结晶产生并分离出结晶。
(2)溶液从8%浓缩到饱和状态(27.3%)并结晶。
2.2 工艺及设备1.蒸发工艺:考虑到蒸发能耗大,因此选用采用并流三效蒸发工艺。
由于原料浓度较大,需要蒸发少量水份,到饱和时才能产生结晶.第二、三效采用强制外循环OSLO结晶蒸发器形式,物料经过三效蒸发,溶液在末效达到饱和并产生结晶,温度在70℃左右。
晶浆经过泵输送到结晶罐,在罐内冷却到40~45℃并进一步结晶,然后出料进入离心机进行固液分离,母液则返回蒸发器。
2.设备形式:外循环三效蒸发器,第二、三效采用强制外循环OSLO结晶蒸发器形式,出料采用泵送方式,晶浆送入结晶罐内降温结晶,然后经过离心机分离晶体和母液,母液则返回第三效蒸发器内蒸发。
3.流程:顺流(并流)方式,即原料由第一效进入,经过第二效再到第三效。
与加热蒸汽及二次蒸汽的流动方向相同。
4.预热:第三效二次蒸汽进入冷凝器之前先经过原料预热器,作为原料的第一级预热。
第一效加热蒸汽产生的冷凝水作为原料的第二级预热。
原料经过两次预热后,原料温度大约可以上升到72℃左右。
5.OSLO结晶蒸发器属于强制外循环蒸发结晶器。
操作时,料液自循环管下部加入,与离开结晶室底部的晶浆混合后,由泵送往加热室。
晶浆在加热室内升温(通常为2~3℃),但不发生蒸发。
OSLO是制盐行业中常用的一种典型的结晶器。
蒸发式OSLO结晶器是由外部加热器对循环料液加热进入真空闪蒸室蒸发达到过饱和,再通过垂直管道进入悬浮床使晶体得以成长,由OSLO结晶器的特殊结构,体积较大的颗粒首先接触过饱和的溶液优先生长,依次是体积较小的溶液;因此OSLO结晶器生产出的晶体具有体积大、颗粒均匀、生产能力大。
废水蒸发方案范文
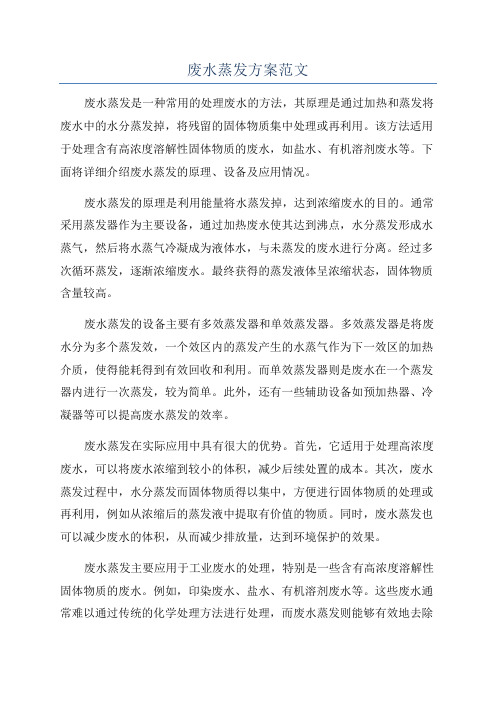
废水蒸发方案范文废水蒸发是一种常用的处理废水的方法,其原理是通过加热和蒸发将废水中的水分蒸发掉,将残留的固体物质集中处理或再利用。
该方法适用于处理含有高浓度溶解性固体物质的废水,如盐水、有机溶剂废水等。
下面将详细介绍废水蒸发的原理、设备及应用情况。
废水蒸发的原理是利用能量将水蒸发掉,达到浓缩废水的目的。
通常采用蒸发器作为主要设备,通过加热废水使其达到沸点,水分蒸发形成水蒸气,然后将水蒸气冷凝成为液体水,与未蒸发的废水进行分离。
经过多次循环蒸发,逐渐浓缩废水。
最终获得的蒸发液体呈浓缩状态,固体物质含量较高。
废水蒸发的设备主要有多效蒸发器和单效蒸发器。
多效蒸发器是将废水分为多个蒸发效,一个效区内的蒸发产生的水蒸气作为下一效区的加热介质,使得能耗得到有效回收和利用。
而单效蒸发器则是废水在一个蒸发器内进行一次蒸发,较为简单。
此外,还有一些辅助设备如预加热器、冷凝器等可以提高废水蒸发的效率。
废水蒸发在实际应用中具有很大的优势。
首先,它适用于处理高浓度废水,可以将废水浓缩到较小的体积,减少后续处置的成本。
其次,废水蒸发过程中,水分蒸发而固体物质得以集中,方便进行固体物质的处理或再利用,例如从浓缩后的蒸发液中提取有价值的物质。
同时,废水蒸发也可以减少废水的体积,从而减少排放量,达到环境保护的效果。
废水蒸发主要应用于工业废水的处理,特别是一些含有高浓度溶解性固体物质的废水。
例如,印染废水、盐水、有机溶剂废水等。
这些废水通常难以通过传统的化学处理方法进行处理,而废水蒸发则能够有效地去除废水中的水分,将固体物质集中处理。
此外,废水蒸发还可以用于一些特殊场合的处理,如舰船的废水处理等。
尽管废水蒸发具有很多优势,但也存在一些局限性。
首先,废水蒸发需要大量的能源供应,特别是在一些大规模蒸发的情况下,能耗较高。
其次,废水蒸发可能会产生一定数量的废热和废气,需要采取相应的措施进行处理或利用。
此外,废水蒸发过程中,废水中的一些挥发性有机物可能会排放到大气中,对环境造成一定的污染。
废水蒸发方案
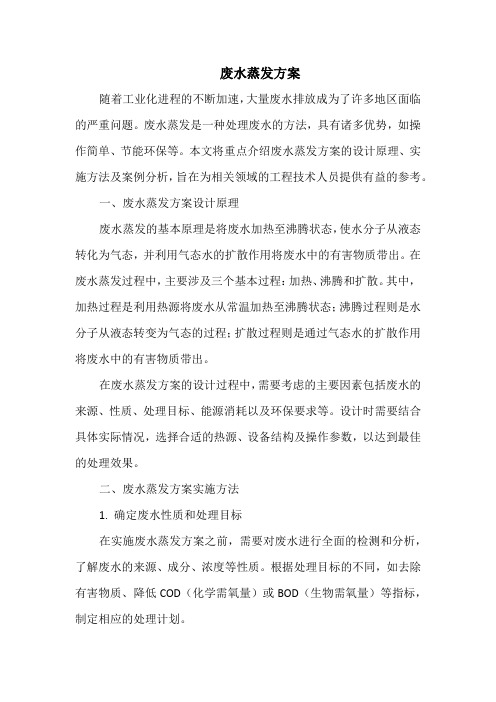
废水蒸发方案随着工业化进程的不断加速,大量废水排放成为了许多地区面临的严重问题。
废水蒸发是一种处理废水的方法,具有诸多优势,如操作简单、节能环保等。
本文将重点介绍废水蒸发方案的设计原理、实施方法及案例分析,旨在为相关领域的工程技术人员提供有益的参考。
一、废水蒸发方案设计原理废水蒸发的基本原理是将废水加热至沸腾状态,使水分子从液态转化为气态,并利用气态水的扩散作用将废水中的有害物质带出。
在废水蒸发过程中,主要涉及三个基本过程:加热、沸腾和扩散。
其中,加热过程是利用热源将废水从常温加热至沸腾状态;沸腾过程则是水分子从液态转变为气态的过程;扩散过程则是通过气态水的扩散作用将废水中的有害物质带出。
在废水蒸发方案的设计过程中,需要考虑的主要因素包括废水的来源、性质、处理目标、能源消耗以及环保要求等。
设计时需要结合具体实际情况,选择合适的热源、设备结构及操作参数,以达到最佳的处理效果。
二、废水蒸发方案实施方法1. 确定废水性质和处理目标在实施废水蒸发方案之前,需要对废水进行全面的检测和分析,了解废水的来源、成分、浓度等性质。
根据处理目标的不同,如去除有害物质、降低COD(化学需氧量)或BOD(生物需氧量)等指标,制定相应的处理计划。
2. 选择合适的热源热源是废水蒸发过程中的重要因素,其选择应根据废水的处理量、性质以及能源消耗等因素进行综合考虑。
常见的热源包括蒸汽、燃气、导热油等,根据实际情况进行选择。
3. 设计设备结构设备结构的设计应充分考虑废水的处理量、水质以及操作便利性等因素。
根据实际需要,可采用不同的设备结构形式,如列管式、盘管式、浸没式等蒸发器结构。
同时,设备材质的选择也非常重要,应选择耐腐蚀、耐高温的优质材料。
4. 确定操作参数操作参数的确定包括温度、压力、蒸发量等。
温度和压力应根据废水的性质和处理目标进行设定;蒸发量应根据废水的处理量和设备的蒸发能力进行确定。
在操作过程中,应定期检测和调整各项参数,以保证处理效果和设备的正常运行。
含盐废水蒸发工艺流程
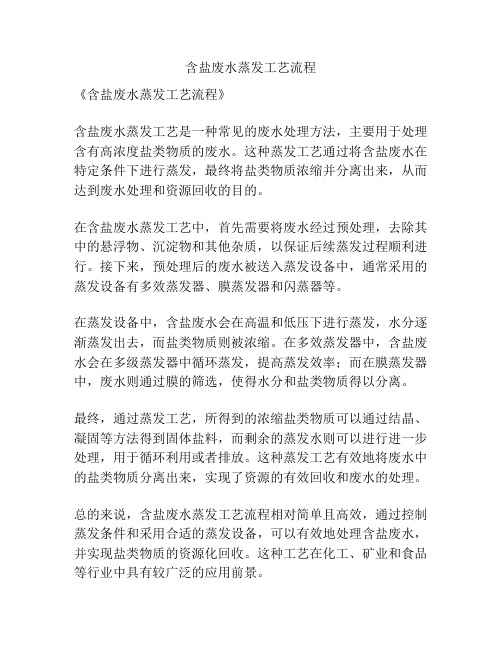
含盐废水蒸发工艺流程
《含盐废水蒸发工艺流程》
含盐废水蒸发工艺是一种常见的废水处理方法,主要用于处理含有高浓度盐类物质的废水。
这种蒸发工艺通过将含盐废水在特定条件下进行蒸发,最终将盐类物质浓缩并分离出来,从而达到废水处理和资源回收的目的。
在含盐废水蒸发工艺中,首先需要将废水经过预处理,去除其中的悬浮物、沉淀物和其他杂质,以保证后续蒸发过程顺利进行。
接下来,预处理后的废水被送入蒸发设备中,通常采用的蒸发设备有多效蒸发器、膜蒸发器和闪蒸器等。
在蒸发设备中,含盐废水会在高温和低压下进行蒸发,水分逐渐蒸发出去,而盐类物质则被浓缩。
在多效蒸发器中,含盐废水会在多级蒸发器中循环蒸发,提高蒸发效率;而在膜蒸发器中,废水则通过膜的筛选,使得水分和盐类物质得以分离。
最终,通过蒸发工艺,所得到的浓缩盐类物质可以通过结晶、凝固等方法得到固体盐料,而剩余的蒸发水则可以进行进一步处理,用于循环利用或者排放。
这种蒸发工艺有效地将废水中的盐类物质分离出来,实现了资源的有效回收和废水的处理。
总的来说,含盐废水蒸发工艺流程相对简单且高效,通过控制蒸发条件和采用合适的蒸发设备,可以有效地处理含盐废水,并实现盐类物质的资源化回收。
这种工艺在化工、矿业和食品等行业中具有较广泛的应用前景。
废水浓缩蒸发方案对比
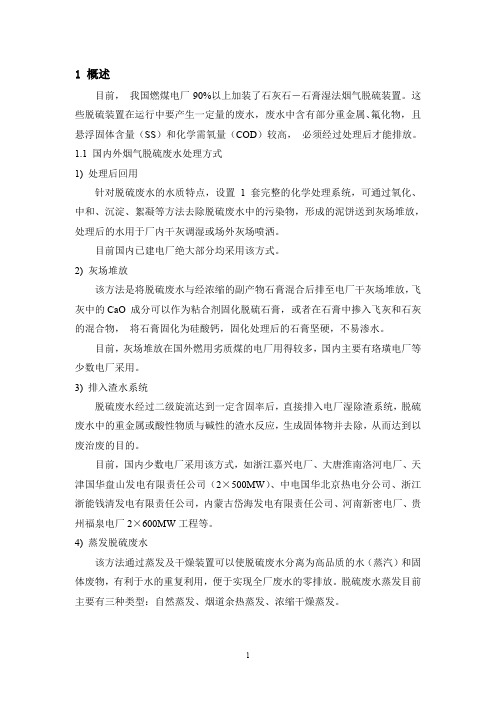
1 概述目前,我国燃煤电厂90%以上加装了石灰石-石膏湿法烟气脱硫装置。
这些脱硫装置在运行中要产生一定量的废水,废水中含有部分重金属、氟化物,且悬浮固体含量(SS)和化学需氧量(COD)较高,必须经过处理后才能排放。
1.1 国内外烟气脱硫废水处理方式1) 处理后回用针对脱硫废水的水质特点,设置 1 套完整的化学处理系统,可通过氧化、中和、沉淀、絮凝等方法去除脱硫废水中的污染物,形成的泥饼送到灰场堆放,处理后的水用于厂内干灰调湿或场外灰场喷洒。
目前国内已建电厂绝大部分均采用该方式。
2) 灰场堆放该方法是将脱硫废水与经浓缩的副产物石膏混合后排至电厂干灰场堆放,飞灰中的CaO 成分可以作为粘合剂固化脱硫石膏,或者在石膏中掺入飞灰和石灰的混合物,将石膏固化为硅酸钙,固化处理后的石膏坚硬,不易渗水。
目前,灰场堆放在国外燃用劣质煤的电厂用得较多,国内主要有珞璜电厂等少数电厂采用。
3) 排入渣水系统脱硫废水经过二级旋流达到一定含固率后,直接排入电厂湿除渣系统,脱硫废水中的重金属或酸性物质与碱性的渣水反应,生成固体物并去除,从而达到以废治废的目的。
目前,国内少数电厂采用该方式,如浙江嘉兴电厂、大唐淮南洛河电厂、天津国华盘山发电有限责任公司(2×500MW)、中电国华北京热电分公司、浙江浙能钱清发电有限责任公司,内蒙古岱海发电有限责任公司、河南新密电厂、贵州福泉电厂2×600MW工程等。
4) 蒸发脱硫废水该方法通过蒸发及干燥装置可以使脱硫废水分离为高品质的水(蒸汽)和固体废物,有利于水的重复利用,便于实现全厂废水的零排放。
脱硫废水蒸发目前主要有三种类型:自然蒸发、烟道余热蒸发、浓缩干燥蒸发。
自然蒸发主要利用大面积废水池,依靠自然干燥气候使水蒸发,该方式由于具有占地极大、效果差,而且受气象条件等诸多因素制约而很少采用;烟道余热蒸发是利用电除尘器(ESP)和空气预热器之间的烟道间隙来加热脱硫废水,使废水完全蒸发,所含的固体物与飞灰一起收集处置。
废水蒸发方案

废水蒸发方案废水处理一直是环境保护领域的重要课题之一。
废水中的有害物质如果不得到适当的处理和处置,将对生态环境产生严重的影响。
废水蒸发方案是一种常用的废水处理技术,它通过将废水转化为蒸汽, 进而实现废水的处理和净化。
本文将为您介绍废水蒸发方案的原理、应用场景以及优势。
一、废水蒸发方案的原理废水蒸发方案的原理是利用蒸发的方式将废水中的水分转化为水蒸气,以达到净化废水的目的。
在废水蒸发过程中,废水被加热,水中的有机物、无机物和悬浮固体等污染物质随着蒸汽一同升腾,经过适当的处理,废水中的无害成分被分离出来,而有害物质则集中处理或进一步处理。
二、废水蒸发方案的应用场景废水蒸发方案的应用场景广泛,包括但不限于以下几个方面:1. 工业废水处理:工业生产中产生的大量废水,常常含有高浓度的有机物和无机物。
通过废水蒸发方案,可以将废水中的有害物质转化为水蒸气,从而实现废水的净化和资源化利用。
2. 污水处理厂余热利用:在城市污水处理厂中,一部分废水蒸发方案采用了余热回收技术。
通过利用燃烧产生的余热,加热废水,提高蒸发效率,减少能源消耗。
3. 盐水处理:一些地区的水资源短缺,但又存在大量的咸水资源。
废水蒸发方案可以将咸水中的水分转化为水蒸气,从而实现盐水的淡化和资源回收。
4. 化工废液处理:在化工行业生产过程中,会产生大量的废液。
废水蒸发方案可以将废液中的水分蒸发掉,使得废液中的有害物质浓缩,便于后续的处理和排放。
三、废水蒸发方案的优势1. 高效净化:废水蒸发方案可以将废水中的水分转化为水蒸气,从而实现废水的蒸发和净化。
相比传统的化学处理方法,废水蒸发方案具有更高的净化效率。
2. 资源回收:在废水蒸发过程中,水分变成了水蒸气,而有机物、无机物和悬浮固体等污染物质则集中处理或进一步处理。
这使得废水中的有害成分被分离出来,废水的处理和净化更加彻底。
3. 余热利用:在一些废水蒸发方案中,采用了余热回收技术。
通过利用废热加热废水,不仅减少了能源的消耗,还实现了能源的回收利用。
电镀废水蒸发处理方案
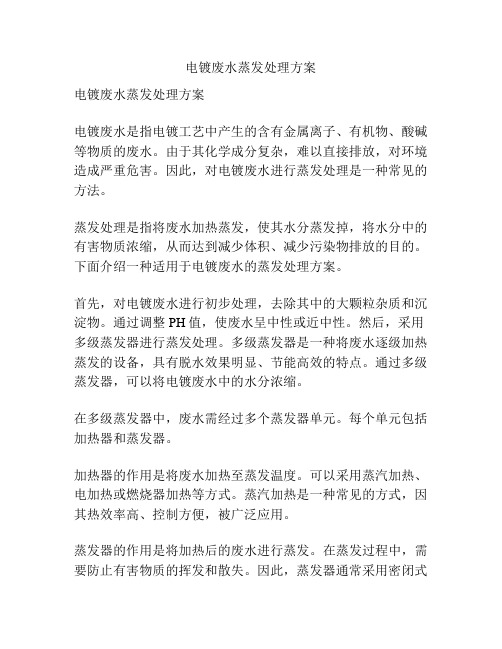
电镀废水蒸发处理方案电镀废水蒸发处理方案电镀废水是指电镀工艺中产生的含有金属离子、有机物、酸碱等物质的废水。
由于其化学成分复杂,难以直接排放,对环境造成严重危害。
因此,对电镀废水进行蒸发处理是一种常见的方法。
蒸发处理是指将废水加热蒸发,使其水分蒸发掉,将水分中的有害物质浓缩,从而达到减少体积、减少污染物排放的目的。
下面介绍一种适用于电镀废水的蒸发处理方案。
首先,对电镀废水进行初步处理,去除其中的大颗粒杂质和沉淀物。
通过调整PH值,使废水呈中性或近中性。
然后,采用多级蒸发器进行蒸发处理。
多级蒸发器是一种将废水逐级加热蒸发的设备,具有脱水效果明显、节能高效的特点。
通过多级蒸发器,可以将电镀废水中的水分浓缩。
在多级蒸发器中,废水需经过多个蒸发器单元。
每个单元包括加热器和蒸发器。
加热器的作用是将废水加热至蒸发温度。
可以采用蒸汽加热、电加热或燃烧器加热等方式。
蒸汽加热是一种常见的方式,因其热效率高、控制方便,被广泛应用。
蒸发器的作用是将加热后的废水进行蒸发。
在蒸发过程中,需要防止有害物质的挥发和散失。
因此,蒸发器通常采用密闭式设计,以防止有害物质的挥发。
蒸发器的内部壁面通常采用特殊材料涂覆,以增强耐腐蚀性能。
通过多级蒸发器的多次蒸发处理,废水中的有害物质被浓缩,水分减少。
蒸发后的浓缩废水可以进一步进行其他处理,如固化、焚烧等方式,以减少污染物排放。
总的来说,电镀废水蒸发处理方案通过多级蒸发器的多次蒸发处理,将废水中的水分浓缩,达到减少体积、减少污染物排放的目的。
同时,多级蒸发器具有脱水效果明显、节能高效的特点,可以提高处理效果,减少能源消耗。
然而,蒸发处理方案对设备投资和运行维护成本较高,需要综合考虑经济可行性和环保效益。
含氯化钙废水单效蒸发方案
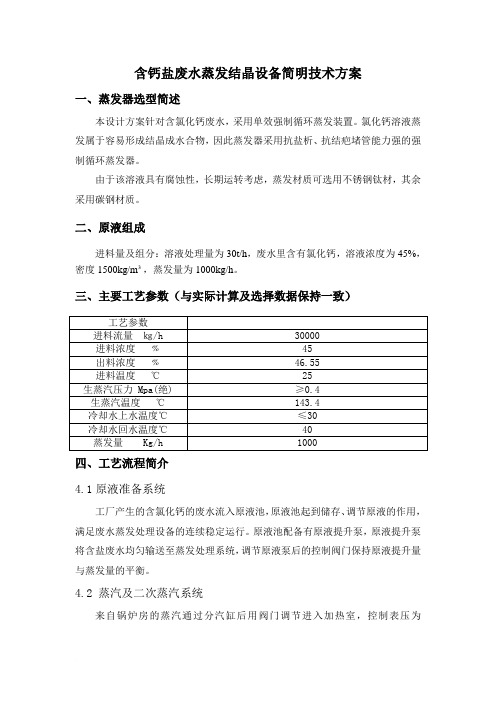
含钙盐废水蒸发结晶设备简明技术方案一、蒸发器选型简述本设计方案针对含氯化钙废水,采用单效强制循环蒸发装置。
氯化钙溶液蒸发属于容易形成结晶成水合物,因此蒸发器采用抗盐析、抗结疤堵管能力强的强制循环蒸发器。
由于该溶液具有腐蚀性,长期运转考虑,蒸发材质可选用不锈钢钛材,其余采用碳钢材质。
二、原液组成进料量及组分:溶液处理量为30t/h,废水里含有氯化钙,溶液浓度为45%,密度1500kg/m³,蒸发量为1000kg/h。
三、主要工艺参数(与实际计算及选择数据保持一致)四、工艺流程简介4.1原液准备系统工厂产生的含氯化钙的废水流入原液池,原液池起到储存、调节原液的作用,满足废水蒸发处理设备的连续稳定运行。
原液池配备有原液提升泵,原液提升泵将含盐废水均匀输送至蒸发处理系统,调节原液泵后的控制阀门保持原液提升量与蒸发量的平衡。
4.2 蒸汽及二次蒸汽系统来自锅炉房的蒸汽通过分汽缸后用阀门调节进入加热室,控制表压为3.0Kgf/cm2。
生蒸汽管路上设置有安全阀,超压后自动排泄报警,确保蒸发系统的安全。
蒸发室蒸发后的二次蒸汽经蒸汽到冷凝器进口,冷凝水经阀门调节进入冷凝水平衡缸。
加热室的冷凝水排回锅炉房。
4.3 盐浆系统本工艺采用转效排盐,集中排母液的方式进行生产。
集盐角的盐浆由盐浆泵抽入漩涡盐分离器进行分离进入沉盐器,沉盐器收集满后将盐排入离心机离心分离,离心母液回蒸发室再次蒸发结晶,离心机离心分离出来的盐分可以直接出售,如果要求更低的含水率,也可以再进入干燥系统进一步脱离水处理。
4.4 二次蒸汽循环冷凝系统蒸发室产生的二次蒸汽进入冷凝器,冷凝器采用循环冷却水进行换热降温。
根据该蒸发设备的处理量,该循环水的循环量一般应控制在80m3/h,最佳温度控制在30℃以下。
4.5 事故及洗罐系统工作出现事故及运转过程中洗罐时,首先停止进料,将蒸发设备中的母液排净。
洗罐水用冷凝水储池的水,洗罐完毕后,将洗罐水排掉,初次洗罐水排入原液池,排空蒸发罐后,首先将部分母液通过原液泵进入蒸发罐,然后通过原液泵补充加入原液,使蒸发罐中的液位满足工艺要求。
氯化钠废水蒸发结晶方案

氯化钠废水蒸发结晶方案清晨的阳光透过窗帘,洒在我的笔记本上,我开始构思这个氯化钠废水蒸发结晶方案。
得承认这事儿听起来有点儿高大上,但其实原理并不复杂,就是让废水中的氯化钠通过蒸发结晶的方式分离出来。
就让我们一起走进这个方案的详细步骤吧。
一、方案背景咱们先聊聊这废水的来源。
氯化钠废水主要来自化工、医药、食品等行业,这些行业在生产过程中会产生大量含有氯化钠的废水。
如果不进行处理,这些废水会对环境造成很大的危害。
所以,我们得想法子把它们处理掉。
二、方案目标1.将氯化钠废水中的氯化钠结晶分离出来,实现资源化利用。
2.降低废水中的氯化钠含量,减少对环境的污染。
3.提高废水处理效率,降低处理成本。
三、方案步骤1.预处理阶段(1)废水收集:将含有氯化钠的废水统一收集起来,确保废水来源的稳定。
(2)水质检测:对废水进行水质检测,了解氯化钠的含量以及其他杂质的情况。
(3)水质调节:根据检测结果,对废水进行水质调节,使其满足蒸发结晶的要求。
2.蒸发结晶阶段蒸发结晶是核心环节,具体步骤如下:(1)蒸发:将预处理后的废水送入蒸发器,通过加热使水分蒸发,留下氯化钠。
(2)结晶:在蒸发过程中,氯化钠逐渐结晶,形成固态。
(3)分离:将结晶后的氯化钠与母液分离,得到纯净的氯化钠。
3.后处理阶段后处理阶段主要是对母液和氯化钠进行进一步处理,具体步骤如下:(1)母液处理:将母液进行处理,回收其中的有用成分,降低处理成本。
(2)氯化钠干燥:将分离出的氯化钠进行干燥,得到干燥的氯化钠产品。
四、关键技术1.蒸发器选型:选择合适的蒸发器是关键,需要考虑蒸发效率、能耗等因素。
2.结晶控制:结晶过程中,需要控制好结晶速度和结晶质量,确保氯化钠产品的纯度。
3.母液处理:母液处理技术需要综合考虑回收利用和环保要求。
五、实施方案1.建立项目组:成立一个专门的项目组,负责整个方案的实施。
2.制定实施计划:根据方案步骤,制定详细的实施计划,明确各阶段的工作内容和时间节点。
废水蒸发方案

随着环保要求的逐步提高, 同时含有氯化钠氯化钾的废水处理要 求也就越来越严格, 为了实现收益最大化, 能够将溶液中的两种盐分 离提纯无疑是极好的。
本文以处理量 5t/h,含氯化钠,含氯化钾的混 盐溶液为例,给出了其中一种蒸汽耗量较低的多效蒸发分离方案。
利用氯化钠和氯化钾在不同温度的溶解度不同原理,根据 NaCL-KCL-H20 四元体系相图的基本原理,在高温浓缩结晶析出 氯化钠,在低温浓缩结晶析出氯化钾,温度范围为 30~120℃。
Nacl (%)21.5 20.7 21 19.6 19.1 18.6 18 17.75 17.55 17.15 16 16.3 16Kcl (%)8.9 10.4 11.85 13.25 14.7 16.15 17.6 18.35 19.05 20.4 21.7 24.9 27.7温度℃10 20 30 40 50 60 70 75 80 90 100 125 150序 号 1 2 3 4 5 6 7 8 9 10 11 12 13备注302520151050 10 20 30 40 50 60 70 80 90 100 125 150将几个蒸发器串联运行的蒸发操作,使蒸汽热能得到多次利用,从而提高热能的利用率,多用于水溶液的处理。
在多效蒸发操作的流程 (见图) 中,第一个蒸发器 (称为第一效) 以生蒸汽作为加热蒸汽,其余称为第二效、第三效,均以其前一效的二次蒸汽作为加热蒸汽,从而可大幅度减少生蒸汽的用量。
每一效的二次蒸汽温度总是低于其加热蒸汽,故多效蒸发时各效的操作压力及溶液沸腾温度沿蒸汽流动方向挨次降低。
依据二次蒸汽和溶液的流向,多效蒸发的流程可分为:①并流流程。
溶液和二次蒸汽同向挨次通过各效。
由于前效压力高于后效,料液可借压差流动。
但末效溶液浓度高而温度低,溶液粘度大,因此传热系数低。
②逆流流程。
溶液与二次蒸汽流动方向相反。
需用泵将溶液送至压力较高的前一效,各效溶液的浓度和温度对粘度的影响大致抵消,各效传热条件基本相同。
含盐废水蒸发结晶处理方案模板
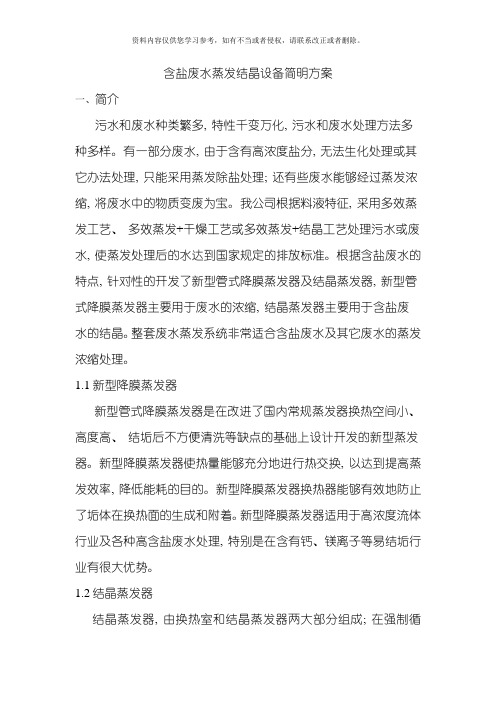
含盐废水蒸发结晶设备简明方案一、简介污水和废水种类繁多, 特性千变万化, 污水和废水处理方法多种多样。
有一部分废水, 由于含有高浓度盐分, 无法生化处理或其它办法处理, 只能采用蒸发除盐处理; 还有些废水能够经过蒸发浓缩, 将废水中的物质变废为宝。
我公司根据料液特征, 采用多效蒸发工艺、多效蒸发+干燥工艺或多效蒸发+结晶工艺处理污水或废水, 使蒸发处理后的水达到国家规定的排放标准。
根据含盐废水的特点, 针对性的开发了新型管式降膜蒸发器及结晶蒸发器, 新型管式降膜蒸发器主要用于废水的浓缩, 结晶蒸发器主要用于含盐废水的结晶。
整套废水蒸发系统非常适合含盐废水及其它废水的蒸发浓缩处理。
1.1新型降膜蒸发器新型管式降膜蒸发器是在改进了国内常规蒸发器换热空间小、高度高、结垢后不方便清洗等缺点的基础上设计开发的新型蒸发器。
新型降膜蒸发器使热量能够充分地进行热交换, 以达到提高蒸发效率, 降低能耗的目的。
新型降膜蒸发器换热器能够有效地防止了垢体在换热面的生成和附着。
新型降膜蒸发器适用于高浓度流体行业及各种高含盐废水处理, 特别是在含有钙、镁离子等易结垢行业有很大优势。
1.2结晶蒸发器结晶蒸发器, 由换热室和结晶蒸发器两大部分组成; 在强制循环泵的作用下,液体在列管中高速循环加热, 饱和液体在结晶器内会不断的蒸发并将盐不断的析出来。
盐和水会在各级盐水分离器内实现盐水有效分离。
强制循环结晶蒸发器特点: 操作周期长——沸腾/蒸发过程不在加热表面而是在结晶器中进行。
因此, 在换热列管中由结壳和沉淀产生的结垢现象被降到最低限度; 优化的换热表面——管内流速由循环泵决定。
二、项目水质特点及参数2.1 系统处理水量:废水处理量: 3.0 m3/h2.2 项目水质参数:进水TDS≤45675.16mg/L出水TDS≤60.0mg/L2.3 理论蒸气消耗量:理论蒸汽消耗量: 330kg生蒸汽/吨水三、废水蒸发器处理流程针对废水含盐量高的特点, 整套蒸发系统由三组强制循环结晶蒸发器组成。
废水蒸发方案

废水蒸发方案随着工业的快速发展和城市化进程的加快,废水的排放量越来越大,给环境和生态系统带来了严重的影响。
为了减少废水对环境的影响,废水处理成为了必不可少的环节。
其中,蒸发作为一种高效的废水处理技术,被广泛应用于各种废水处理场景。
本文将介绍废水蒸发方案的设计、应用和优势。
一、废水蒸发方案的设计废水蒸发方案的设计主要包括废水预处理、蒸发系统和冷凝系统三个部分。
1. 废水预处理废水预处理的目的是去除废水中的悬浮物、油脂、重金属等杂质,以便更好地进行蒸发处理。
预处理的方法包括过滤、沉淀、除油、化学沉淀等。
根据废水的特性和处理要求,可以选择不同的预处理方法。
2. 蒸发系统蒸发系统是废水蒸发方案的核心部分,其目的是通过加热使废水中的水分蒸发,而盐分等杂质则留在了蒸发器中。
根据废水的水质、处理规模和处理要求,可以选择不同的蒸发器类型,如多效蒸发器、机械搅拌蒸发器、自然通风蒸发器等。
3. 冷凝系统冷凝系统的作用是将蒸发器中产生的蒸汽冷凝成水,以便回收利用或排放。
根据实际需要,可以选择不同的冷凝方式,如水冷、风冷等。
回收的淡水可以用于工业冷却、锅炉补给水等用途,从而实现水资源的循环利用。
二、废水蒸发方案的应用废水蒸发方案广泛应用于各种废水处理场景,如化工、制药、食品加工、造纸等行业。
在这些行业中,废水中含有大量的盐分、有机物、重金属等杂质,通过废水蒸发方案的处理,可以有效地去除这些杂质,达到排放标准或回收利用的要求。
以化工行业为例,该行业产生的废水中含有大量的盐分、有机物等杂质,直接排放会对环境造成严重的影响。
通过废水蒸发方案的处理,可以将废水中的盐分和其他杂质去除,使废水达到排放标准。
同时,回收的淡水可以用于工厂的冷却、锅炉补给水等用途,实现水资源的循环利用。
三、废水蒸发方案的优点相比于其他废水处理技术,废水蒸发方案具有以下优点:1. 处理效率高:废水蒸发方案的效率高,能够快速地去除废水中的杂质,达到排放标准或回收利用的要求。
废水浓缩蒸发方案对比

废水浓缩蒸发方案对比目前,常见的废水浓缩蒸发方案包括多级蒸发、气浮浓缩、微蒸发、热压缩蒸发等。
首先,多级蒸发是一种不断蒸发和冷凝的过程,通过多个蒸发器级联进行操作。
废水在第一级蒸发器中被蒸发,产生的蒸汽经二级或多级冷凝器冷凝,形成浓缩液。
多级蒸发具有能耗低和浓缩效果好的优点,但其设备体积较大且操作复杂。
其次,气浮浓缩是通过注入气泡的方式将废水中的水分与浮力一起带到液面上,再通过电压调节器将上升到一定高度的液面从液相分离。
气浮浓缩技术具有设备结构简单、处理效果好的特点,但对气泡的控制较为困难,需要经常进行维护和清洗。
此外,微蒸发是通过利用微孔薄膜的毛细作用和压力差,将废水中的水分分子从膜表面蒸发至膜背面,并通过蒸发器底部的真空抽气系统将蒸发的水分从蒸发器中除去。
微蒸发具有处理量大、效率高的特点,但设备成本较高。
最后,热压缩蒸发是通过加热压缩气体来加热废水,使废水中的水蒸发变成水蒸汽,并经冷凝器冷凝成水。
热压缩蒸发技术能够达到极高的浓缩效果,废水处理效果好,但其能耗较高,需要大量热能的支持。
在对比这几种废水浓缩蒸发方案时,需要综合考虑以下因素:1.处理效率:不同方案的处理效率不同,需要根据废水的特性选择最适合的方案。
例如,对于含有大量悬浮物的废水,气浮浓缩可能是更合适的选择。
2.能耗:不同方案的能耗不同,需要综合考虑处理效果和能源消耗之间的平衡。
一般来说,多级蒸发和热压缩蒸发的能耗较高,微蒸发和气浮浓缩的能耗较低。
3.处理容量:不同方案的处理容量也存在差异,需要根据实际废水产生量选择相应的方案。
一般来说,多级蒸发和热压缩蒸发适用于大量废水的处理,微蒸发和气浮浓缩适用于小型废水处理。
4.设备成本和维护成本:不同方案的设备成本和维护成本也不同,需要综合考虑初期投资和后期维护费用。
综上所述,不同的废水浓缩蒸发方案各有优劣,需要根据实际情况选择最合适的方案。
在实际应用中,也可以将多种方案进行组合使用,以达到更好的处理效果和经济效益。
电镀废水MVR蒸发方案
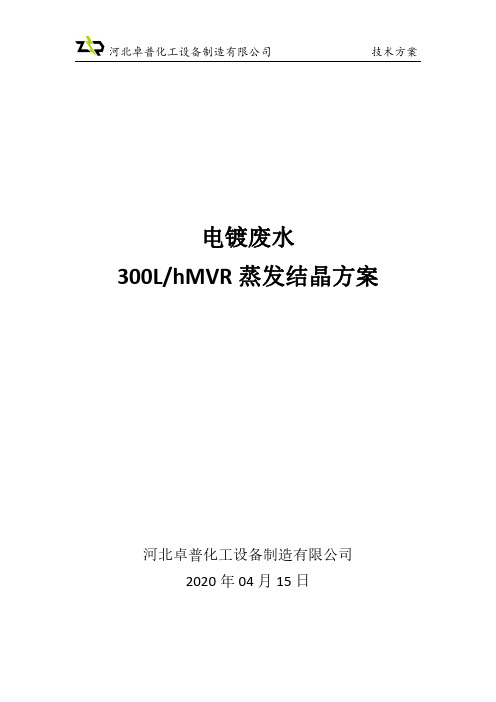
河北卓普化工设备制造有限公司
技术方案
节+ MVR 的处理工艺,最大程度的降低能耗和使整个系统运行稳定。
2.2MVR 原理介绍
MVR 强制循环蒸发器由加热器、分离器和强制循环泵等组成。物料在换热器
的换热管内被换热管外的蒸汽加热温度升高,在循环泵作用下物料上升到分离器
中。蒸发产生二次蒸汽从物料中溢出,物料被浓缩产生过饱和而使结晶生长,解
考虑到硫酸镍沸点较高,采用高温升的 MVR 蒸发浓缩后,然后进入真空闪蒸 结晶出硫酸镍结晶盐,然后进入离心机进行离心处理,离心出母液返回 MVR 蒸发 器,考虑到有机物等杂质的富集对于 MVR 蒸发的影响,工作段时间后需定期外排 较少溶液。
综合考虑,考虑到系统设计余量,项目设计处理水量为 300L/h,通过 PH 调
河北卓普化工设备制造有限公司
技术方案
电镀废水 300L/hMVR 蒸发结晶方案
河北卓普化工设备制造有限公司 2020 年 04 月 15 日
河北卓普化工设备制造有限公司
一、原水水质参数
技术方案
1.1 项目要求
项目主要为含镍电镀废水处理。
1.2 原水水质
原水水质
镍
COD
全盐 氨氮
PH
氯离子
单位 mg/L
12. 真空泵
电机功率:1.45kw;
台
1
FRPP
带节水器;
13. 离心机
处理量:80kg/h; 电机功率:7.5kw;
台
1
316L
吸流量:250kg/h;
进口温度:86-88℃;
温升:18℃; 14. 罗茨蒸汽压缩机 电机功率:18.5kw;
电压:380V;
台
日处理100吨废水蒸发脱盐处理设计方案

日处理100吨含盐废水蒸发脱盐方案选型计算书一、公司简介:我公司主要产品为蒸发、干燥、结晶、过滤等化工单元设备及非标设备,产品已广泛应用于化工、医药、饲料、化肥、染料、食品等行业,顾客遍布全国。
主要产品为多效降膜蒸发器、多效升膜蒸发器、强制循环蒸发器、刮板薄膜蒸发器、OSLO结晶机、旋转闪蒸干燥机、双桨叶干燥机、振动流化床、圆盘干燥机、非标设备等。
多效蒸发器产品已成功应用于氨基酸行业、味精行业、淀粉行业、硫酸铵、硫化碱、氯化钠、氯化钾、硫酸钠、硝酸钠、亚硝酸钠、氯化钡、硫氢化钠等行业。
二、设计条件:1、小试蒸发情况:加入废水500ml,加热蒸发,约3小时剩余晶浆54ml,已基本蒸干。
固体颗粒直径约0.2mm,较容易分离。
从蒸发过程来看,结疤情况不严重,后期溶液沸点升高约5度,并且溶液饱和后的粘度也不大,适宜用自然循环蒸发器。
2、根据要求,蒸发器的蒸发能力设计为4吨/小时。
盐分为384kg/h。
通过废水蒸发器的浓缩,将其中的盐份结晶出来。
含盐的晶浆定期排出进料量为至沉降槽,母液返回到稀溶液池继续蒸发,盐由人工定期清理。
蒸发出的冷凝水可以生产使用也可以处理后排放。
三、设计方案:1、为降低蒸汽消耗选择三效蒸发器,蒸发每吨水消耗蒸汽约400公斤。
即蒸发4.2吨/小时需要消耗0.5MPa锅炉蒸汽1.68吨/小时;需要冷却水循环量约55m3/h;2、设备功率:循环水泵11kw、凉水塔风扇2.2kw、上料泵4kw、真空泵11kw,共28.2kw。
电价按0.7元/度,蒸汽价格按200元/吨核算,蒸发每吨水的能耗费用为0.4×200+22.8×0.7=96元。
3、通过蒸发器的浓缩将废水中的盐分结晶分离出来,第三效加热室出来的高温冷凝水约2.6吨/小时温度约为80℃。
第三效蒸发出的冷凝水约1.3吨/小时温度约为50℃。
4、由于氯化钠的沸点升高较大,为提高各效传热温差,第三效采用副压蒸发。
5、设备材质选择碳钢。
- 1、下载文档前请自行甄别文档内容的完整性,平台不提供额外的编辑、内容补充、找答案等附加服务。
- 2、"仅部分预览"的文档,不可在线预览部分如存在完整性等问题,可反馈申请退款(可完整预览的文档不适用该条件!)。
- 3、如文档侵犯您的权益,请联系客服反馈,我们会尽快为您处理(人工客服工作时间:9:00-18:30)。
废水蒸发结晶方案随着环保要求的逐步提高,同时含有氯化钠氯化钾的废水处理要求也就越来越严格,为了实现收益最大化,能够将溶液中的两种盐分离提纯无疑是极好的。
本文以处理量5t/h,含氯化钠,含氯化钾的混盐溶液为例,给出了其中一种蒸汽耗量较低的多效蒸发分离方案。
一.工艺原理利用氯化钠和氯化钾在不同温度的溶解度不同原理,根据NaCL-KCL-H20四元体系相图的基本原理,在高温浓缩结晶析出氯化钠,在低温浓缩结晶析出氯化钾,温度范围为30~120℃。
111001621.71212516.324.9131501627.7二.多效蒸发将几个蒸发器串联运行的蒸发操作,使蒸汽热能得到多次利用,从而提高热能的利用率,多用于水溶液的处理。
在多效蒸发操作的流程(见图)中,第一个蒸发器(称为第一效)以生蒸汽作为加热蒸汽,其余称为第二效、第三效,均以其前一效的二次蒸汽作为加热蒸汽,从而可大幅度减少生蒸汽的用量。
每一效的二次蒸汽温度总是低于其加热蒸汽,故多效蒸发时各效的操作压力及溶液沸腾温度沿蒸汽流动方向依次降低。
依据二次蒸汽和溶液的流向,多效蒸发的流程可分为:①并流流程。
溶液和二次蒸汽同向依次通过各效。
由于前效压力高于后效,料液可借压差流动。
但末效溶液浓度高而温度低,溶液粘度大,因此传热系数低。
②逆流流程。
溶液与二次蒸汽流动方向相反。
需用泵将溶液送至压力较高的前一效,各效溶液的浓度和温度对粘度的影响大致抵消,各效传热条件基本相同。
③错流流程。
二次蒸汽依次通过各效,但料液则每效单独进出,这种流程适用于有晶体析出的料液。
在生蒸汽温度与末效冷凝器温度相同(即总温度差相同)条件下,将单效蒸发改为多效蒸发时,蒸发器效数增加,生蒸汽用量减少,但总蒸发量不仅不增加,反而因温度差损失增加而有所下降。
多效蒸发节省能耗,但降低设备的生产强度,因而增加设备投资。
在实际生产中,应综合考虑能耗和设备投资,选定最佳的效数。
烧碱等电解质溶液的蒸发,因其温度差损失大,通常只采用2~3效(见彩图);食糖等非电解质溶液,温度差损失小,可用到4~6效;海水淡化所蒸发的水量大,在采取了各种减少温度差损失的措施后,可采用20~30效三、物料的特性及蒸发形式选型原始物料说明:根据溶液内主要含有氯化钾,氯化钠,要求出料结晶。
晶体析出要过饱和蒸发,使晶体长大。
含有晶体的溶液在蒸发系统运行,流量小了会造成堵管现象,为此我们必须采用强制循环的方式让晶体混合溶液在蒸发系统流动。
多效强制循环蒸发系统是最佳的选择。
废水的沸点升高为9°,为此每效温差不能小于15°才能有效持续蒸发。
我们采用四效在真空状态下工作。
每效的真空度不同,沸点不同,每效的蒸发温度不同。
这样达到了节约能源的效果,利用前一效二次蒸汽加热物料,在真空状态下持续蒸发,一个生蒸汽的进量,使用四次,完全吸收蒸汽的热焓值。
因为目前国内做的蒸汽在压缩离心风机的额定蒸发量最小的为2.5t/h,我们的量达不到最小额定值,为此蒸发结晶首选的是多效。
蒸发形式选型:根据氯化钾,氯化纳结晶特性,采用四效蒸发高温出氯化钠,饱和氯化钾卤水冷却析钾工艺,达到分离钾、钠,得到合格氯化钾和氯化钠产品。
材质选择依据:SUS304 成份0Cr18Ni9SUS316L 成份00Cr17Ni14Mo22205双相钢成份00Cr22Ni5Mo3N(国标)Ta2钛合金材质使用范围SUS304中性或弱碱性Cl 和F 均小于1×102ppmSUS316L弱酸性:Cl 和F 均小于1×103ppm中性:Cl 和F 无要求弱碱性:Cl 和F 无要求2205双相钢弱酸性:Cl 和F 均小于2×103ppm中性:Cl 和F 无要求弱碱性:Cl 和F 无要求Ta2钛合金强酸性:Cl 和F 均小于5×103ppm弱酸性:Cl 和F 无要求中性:Cl 和F 无要求弱碱性:Cl 和F 无要求强碱性:Cl 和F 无要求根据表格数据,过料部分采用2205,其他采用SUS316L材质比较合适。
但考虑到高氯根对设备的腐蚀及强制循环冲刷,加热器高温特点,一效列管用T10,二、三、四效列管用T2.四、强制循环蒸发器流程说明1、物料流程:物料经进料泵由原料罐进入板式预热器和冷凝水热交换器后进入四效强制循环蒸发加热室,循环加热,再通过切线喷入分离器,进行蒸发、汽液分离。
水份蒸发后的二次蒸汽作为热源对二效进行加热,物料则通轴流泵送至三效强制循环加热室。
同样的方式在三效完成蒸发后,物料连续送入第二效强制循环系统,在第二效再次蒸发后,进入一效蒸发、结晶系统,氯化钠晶体由出料泵打出,然后进入离心机上方旋液分离器。
送至离心机脱水,母液回到一效强制循环系统。
一效结晶器饱和上清液溢流至五效闪发降温结晶器经降温析出KCl,由出料泵打出,然后进入离心机上方旋液分离器。
送至离心机脱水,母液回到五效强制循环系统。
五效析钾上清液回流至四效。
2、蒸汽流程:蒸汽首先进入一效强制循环加热室,和物料热交换,加热后的物料进入一效气液分离器,产生二次蒸汽进入二效强制循环加热室,同样方式进入三效强制循环加热室,三效气液分离器产生的二次蒸汽进入四效,四效气液分离器产生的二次蒸汽进入冷凝器。
最后由真空泵排除系统。
五效产生的二次蒸汽进入冷凝器。
最后由真空泵排除系统3、冷凝水流程:一效至板式预热器和原料热交换后。
送回锅炉回用。
、二效、三效、四效加热室产生的冷凝水汇集到冷凝水罐,用冷凝水泵送至洗料回用。
4、不凝性气体流程:各个加热室效体上下侧端都开有不凝性气体出口,蒸发中产生的不凝性气体经真空泵抽走并排出.(详见工艺流程图)五、设备的技术参数技术方案内的参数为参考数据。
以合同协议参数为准六、产品配置清单:七、设备制造标准非标设备1)GB151-1999《管壳式换热器》2)JB/T4710-2005《钢制塔式容器》3)JB/T4735-1997《钢制焊接常压容器》4)JB/T4731-2005《钢制卧式容器》5)HG20580-1998《钢制化工容器设计基础规定》6)HG20581-1998《钢制化工容器材料选用规定》7)HG20582-1998《钢制化工容器强度计算规定》8)HG20583-1998《钢制化工容器结构设计规定》9)HG20584-1998《钢制化工容器制造技术要求》10)HG205920~20635-97《钢制管法兰、垫片、紧固件》11)JB/T4736-2002《补强圈》12)JB/T4712、4713、4724、4725-1992《容器支座》13)JB/T4718~4720-92《管壳式换热器用垫片》14)GB/T983-1995《不锈钢焊条》15)GB/T5117-1995《碳钢焊条》16)GB/T5118-1995《低合金钢焊条》17)HG/T21514~21535-2005《钢制人孔和手孔》18)HG21537.7~8-1995《搅拌传动装置》19)HG21505-1992《组合式视镜》20)HG/T21619~620-1986《视镜》、《带颈视镜》21)HG20652-1998《塔器设计技术规定》22)HG/T21618-1998《丝网除沫器》23)HG/T21639-1980《塔顶吊柱》24)HG/T21574-94《设备吊耳》25)JB/T1205-2001《塔盘技术条件》26)HG/T21512-95《梁型气体喷射式填料支承板》27)GB/T13148-1991《不锈钢复合钢板焊接技术条件》28)HG/T20678-2000《衬里钢壳设计技术规定》29)GB/T12459-2005《钢制对焊无缝管件》30)GB50316-2000《工业金属管道设计规范》31)GB50264-97《工业设备及管道绝热工程设计规范》机泵1)API610《石油、化工和天然气工业用离心泵》2)API682《离心泵和旋转泵的轴密封系统》3)GB3215《炼油厂、化工及石油化工流程用离心泵通用技术条件》4)GB3216《离心泵、混流泵、轴流泵和旋涡泵试验方法》5)GB/T5656《离心泵技术条件》6)GB/T5659《多级离心泵技术条件》7)HG20592B《钢制管法兰、垫片、紧固件》8)GB/T3214《水泵流量的测定方法》9)GB13006《离心泵、混流泵和轴流泵汽蚀余量》10)GB13007《离心泵效率》11)GB9239《刚性转子平衡品质许用不平衡的确定》12)JB/T8097《泵的振动测量与评价方法》13)JB/T8098《泵的噪声测量与评价方法》14)JB/T4297 《泵产品涂漆技术条件》15)JB/T6879《离心泵铸件过流部位尺寸公差》16)GB2100《不锈耐酸钢铸件技术条件》管道、管件阀门与法兰1)GB/T8163-1999《输送流体用无缝钢管》2)GB/T14976-2002《流体输送用不锈钢无缝钢管》3)JB/T81-88《法兰、垫片、紧固件》4)JB/T2769-2008《阀门零部件螺纹法兰》5)HG20553-1993《化工配管用无缝及焊接钢管尺寸选用系(公制II系列)》电动机及电气设备1)GB755-2000《旋转电机基本技术要求》2)GB50054-1995《低压配电设计规范》3)GB50058-1992《爆炸和火灾危险环境电力装置设计规范》仪表1)GB50093-2002《工业自动化仪表工程施工及验收规范》2)HG/T20505-2000《过程测量和控制仪表的功能标志及图形符号》3)HG/T20507-2000《自动化仪表选型设计规定》4)HG/T20511-2000《信号报警,安全连锁系统设计规定》5)HG/T20512-2000《仪表配管配线设计规定》6)HG/T20513-2000《仪表系统接地设计规定》7)HG/T21581-95《自控安装图册》8)SH 3005-1999《石油化工自动化仪表选型设计规范》9)SH/T 3018-2003《石油化工安全仪表系统设计规范》10)SHJ19-90《石油化工企业仪表配管配线设计规范》11)SHJ521-91《石油化工企业仪表工程施工技术规程》保温《GB50264-97工业设备及管道绝热工程设计规范》八、蒸发器安装、调试、培训现场安装严格按照安装图纸进行施工,记录了施工过程的实施人、检查人,无论哪个环节出现问题,都可追溯责任者的责任。
组织优秀的施工人员参加施工,选派技术素质好从事工程施工多年的工人参加施工。
严把材料质量关:现场采购或汽运到现场的框架材料,必须具有合格证、质保书。
总之,施工中不得使用任何不合格材料。
严格遵守公司的安全制度,确保安全文明施工。
试车调试在工程安装完工后,对设备进行详细检查后,其后进行单机试车,然后以水代料试运转,正常后正式投料试车,进行72小时验收调试。