汽车冲压新技术..
汽车生产中的冲压工艺
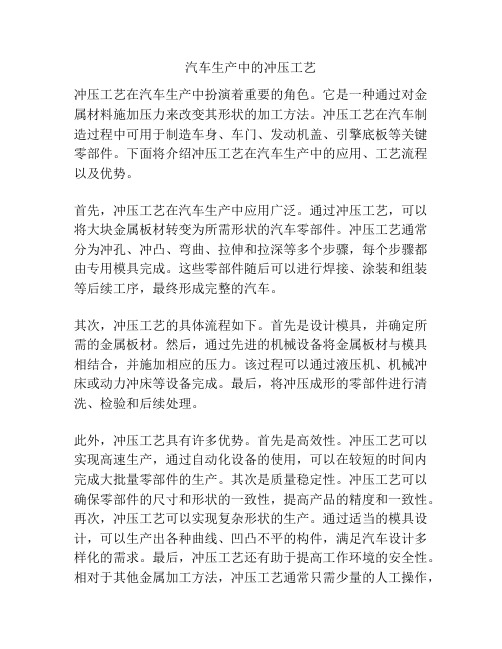
汽车生产中的冲压工艺冲压工艺在汽车生产中扮演着重要的角色。
它是一种通过对金属材料施加压力来改变其形状的加工方法。
冲压工艺在汽车制造过程中可用于制造车身、车门、发动机盖、引擎底板等关键零部件。
下面将介绍冲压工艺在汽车生产中的应用、工艺流程以及优势。
首先,冲压工艺在汽车生产中应用广泛。
通过冲压工艺,可以将大块金属板材转变为所需形状的汽车零部件。
冲压工艺通常分为冲孔、冲凸、弯曲、拉伸和拉深等多个步骤,每个步骤都由专用模具完成。
这些零部件随后可以进行焊接、涂装和组装等后续工序,最终形成完整的汽车。
其次,冲压工艺的具体流程如下。
首先是设计模具,并确定所需的金属板材。
然后,通过先进的机械设备将金属板材与模具相结合,并施加相应的压力。
该过程可以通过液压机、机械冲床或动力冲床等设备完成。
最后,将冲压成形的零部件进行清洗、检验和后续处理。
此外,冲压工艺具有许多优势。
首先是高效性。
冲压工艺可以实现高速生产,通过自动化设备的使用,可以在较短的时间内完成大批量零部件的生产。
其次是质量稳定性。
冲压工艺可以确保零部件的尺寸和形状的一致性,提高产品的精度和一致性。
再次,冲压工艺可以实现复杂形状的生产。
通过适当的模具设计,可以生产出各种曲线、凹凸不平的构件,满足汽车设计多样化的需求。
最后,冲压工艺还有助于提高工作环境的安全性。
相对于其他金属加工方法,冲压工艺通常只需少量的人工操作,减少了人员接触有害物质的机会和操作失误的风险。
总之,冲压工艺在汽车生产中发挥着重要作用。
它能够高效、精确地生产各种复杂形状的零部件,为汽车制造提供了强大的支持。
随着科技的进步,冲压工艺将继续发展,为汽车行业的发展做出更大的贡献。
冲压工艺在汽车生产中的应用非常广泛,几乎涵盖了整个汽车的制造过程。
它不仅可以制造车身、车门、发动机盖等零部件,还可以用于制造座椅、方向盘、悬挂系统等汽车内部的各种零部件。
冲压工艺的应用不仅降低了生产成本,提高了生产效率,还提高了汽车的质量和可靠性。
汽车冲压零件的设计及制造

汽车冲压零件的设计及制造摘要:在冲压塑料加工模具领域,通常都会使用一个产品的技术质量水平来直接衡量整个冲击冲压加工模具行业的技术发展创新水平。
冲压加工模具的结构设计的合理与否以及产品加工精细与否直接的会影响着整个冲压加工部件的生产质量。
关键词:冲压加工;冲压模具;冲压部件1 汽车冲压模具的设计分析在立体模型设计图纸的加工设计绘制过程中,应对设计技术上的切入点以及实际应用需求情况做出全面的分析考量,以此对立体模具的制造工艺设计排样和立体模具成型进行十分合理的加工设计。
以上几个步骤直接就会影响着最终产品批量生产最终设计得到的立体冲压成型模具产品质量。
1.1设定目标尺寸在最初确定最终设计一款产品冲头模具成型外形尺寸图纸的整个操作过程中,第一步就首先需要在对一款成型产品冲头模具外形图的各种外形尺寸公差设计量值分析的基本认识上和基础之上,对最终确定能够设计得到一款成型产品的模具外形尺寸设计量值公差进行正确性的设定。
具体一点说来在最终确定一款产品模具外形尺寸公差后的尺寸量值允许的测量精度要求范围之内,以一款产品模具冲头、凹模的美观外形以及磨损尺寸变化速度趋向等的情况来作为主要测量依据,决定最终的能够得到一款产品冲头凹模模具外形尺寸的一款产品设计量值。
1.2排样图设计以及力学计算产品力学测量计算与应用冲压工具模型最终产品能否安全完成批量生产,在最终客户自行使用产品生产工艺过程中产品主体压力能否完全正确承受力与使用冲压机械机的内部压力之间应该有着直接的密切相互联系,因此最终产品冲压力学模型测量综合计算的技术重要性和应用意义不言而喻。
1.3模具总装图绘制模具设备总装图的总体绘制设计过程一般应当以格式排样的绘图形式作为设计基准,在此基础之上不再进行总体设计绘制工作。
除此之外,需要详细结合各种冲压送料设备的需要合模高度、设备的需要安装模具尺寸以及各种送料加工装置的合模高度,最终可以绘制设计出各种冲压设备模具的详细总体结构。
汽车冲压新技术范文
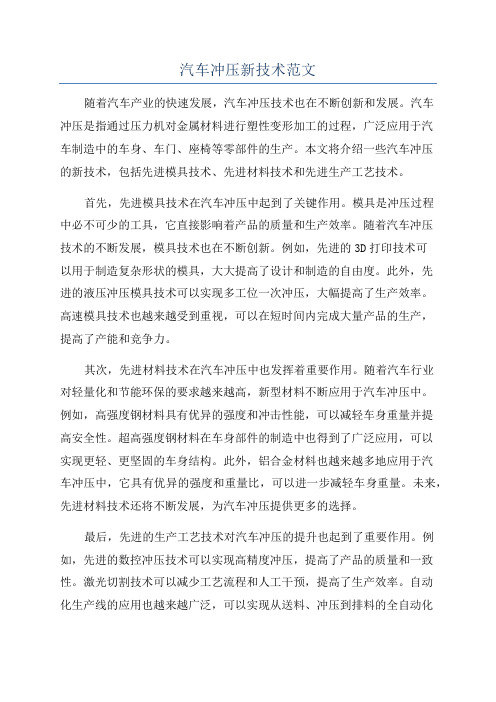
汽车冲压新技术范文随着汽车产业的快速发展,汽车冲压技术也在不断创新和发展。
汽车冲压是指通过压力机对金属材料进行塑性变形加工的过程,广泛应用于汽车制造中的车身、车门、座椅等零部件的生产。
本文将介绍一些汽车冲压的新技术,包括先进模具技术、先进材料技术和先进生产工艺技术。
首先,先进模具技术在汽车冲压中起到了关键作用。
模具是冲压过程中必不可少的工具,它直接影响着产品的质量和生产效率。
随着汽车冲压技术的不断发展,模具技术也在不断创新。
例如,先进的3D打印技术可以用于制造复杂形状的模具,大大提高了设计和制造的自由度。
此外,先进的液压冲压模具技术可以实现多工位一次冲压,大幅提高了生产效率。
高速模具技术也越来越受到重视,可以在短时间内完成大量产品的生产,提高了产能和竞争力。
其次,先进材料技术在汽车冲压中也发挥着重要作用。
随着汽车行业对轻量化和节能环保的要求越来越高,新型材料不断应用于汽车冲压中。
例如,高强度钢材料具有优异的强度和冲击性能,可以减轻车身重量并提高安全性。
超高强度钢材料在车身部件的制造中也得到了广泛应用,可以实现更轻、更坚固的车身结构。
此外,铝合金材料也越来越多地应用于汽车冲压中,它具有优异的强度和重量比,可以进一步减轻车身重量。
未来,先进材料技术还将不断发展,为汽车冲压提供更多的选择。
最后,先进的生产工艺技术对汽车冲压的提升也起到了重要作用。
例如,先进的数控冲压技术可以实现高精度冲压,提高了产品的质量和一致性。
激光切割技术可以减少工艺流程和人工干预,提高了生产效率。
自动化生产线的应用也越来越广泛,可以实现从送料、冲压到排料的全自动化生产,减少了人工操作和劳动强度。
智能化的生产管理系统可以优化生产调度和物流配送,实现生产效率的最大化。
综上所述,汽车冲压的新技术涵盖了先进模具技术、先进材料技术和先进生产工艺技术。
这些技术的不断创新和应用,不仅提高了汽车冲压的精度、效率和质量,也推动了整个汽车行业的发展。
汽车覆盖件冲压工艺及模具设计技术研究
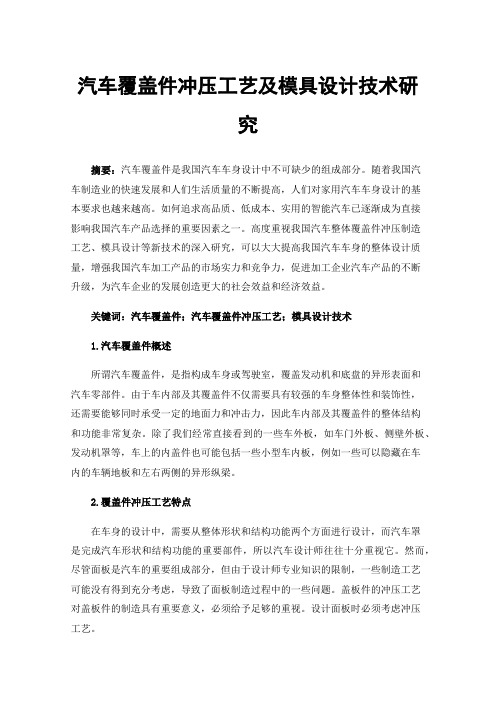
汽车覆盖件冲压工艺及模具设计技术研究摘要:汽车覆盖件是我国汽车车身设计中不可缺少的组成部分。
随着我国汽车制造业的快速发展和人们生活质量的不断提高,人们对家用汽车车身设计的基本要求也越来越高。
如何追求高品质、低成本、实用的智能汽车已逐渐成为直接影响我国汽车产品选择的重要因素之一。
高度重视我国汽车整体覆盖件冲压制造工艺、模具设计等新技术的深入研究,可以大大提高我国汽车车身的整体设计质量,增强我国汽车加工产品的市场实力和竞争力,促进加工企业汽车产品的不断升级,为汽车企业的发展创造更大的社会效益和经济效益。
关键词:汽车覆盖件;汽车覆盖件冲压工艺;模具设计技术1.汽车覆盖件概述所谓汽车覆盖件,是指构成车身或驾驶室,覆盖发动机和底盘的异形表面和汽车零部件。
由于车内部及其覆盖件不仅需要具有较强的车身整体性和装饰性,还需要能够同时承受一定的地面力和冲击力,因此车内部及其覆盖件的整体结构和功能非常复杂。
除了我们经常直接看到的一些车外板,如车门外板、侧壁外板、发动机罩等,车上的内盖件也可能包括一些小型车内板,例如一些可以隐藏在车内的车辆地板和左右两侧的异形纵梁。
2.覆盖件冲压工艺特点在车身的设计中,需要从整体形状和结构功能两个方面进行设计,而汽车罩是完成汽车形状和结构功能的重要部件,所以汽车设计师往往十分重视它。
然而,尽管面板是汽车的重要组成部分,但由于设计师专业知识的限制,一些制造工艺可能没有得到充分考虑,导致了面板制造过程中的一些问题。
盖板件的冲压工艺对盖板件的制造具有重要意义,必须给予足够的重视。
设计面板时必须考虑冲压工艺。
3汽车覆盖件冲压工艺与设计方案本文主要以某汽车生产公司的一辆小型货车的后门为分析对象。
后门内板尺寸大,形状多样,是典型的汽车覆盖件。
3.1汽车覆盖件冲压工艺分析汽车后门内板分为后窗内板和后门外板。
后车门的内板和外板通过内板的焊接边缘和冲压工艺相互连接,形成汽车的后车门,后车门直接安装在汽车的行李箱上。
汽车冲压模具的技术发展思路
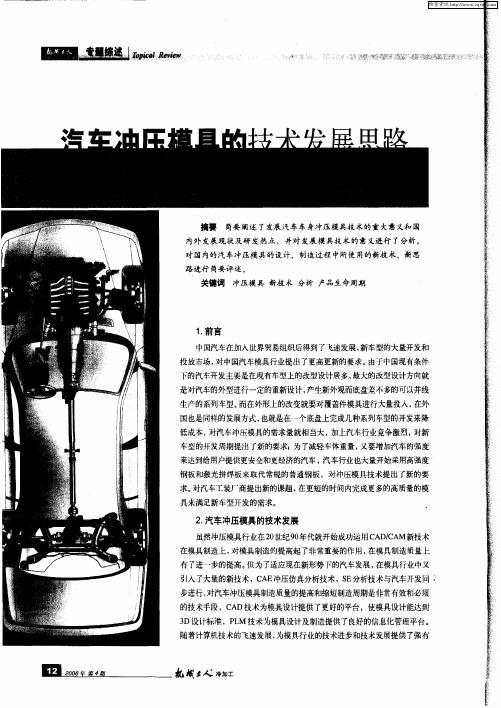
功能模块对模具的曲面进行数控加工 N C程序的计算和
() 2 车身覆盖件的 s E分析及工装同步开发 由于 汽车新车型的开发周期越来越短, 对模具1装的要求也 = =
是时间紧张 , 为了节约开发时间和开发中零件的工艺性 问题, 现在大部分主车厂在进行新品开发时都会提 对 新车型进行车身覆盖件的S I艺分析, E 在进行零件工艺
1 前言 .
中国汽车在加入世界贸易组织后得到了飞速发展, 新车型的大量开发和 投放市场, 对中国汽车模具行业提出了更高更新的要求。 由于中国现有条件 下的汽车开发主要是在现有车型上的改型设计居多, 最大的改型设计方向就 是对汽车的外型进行一定的重新设计, 产生新外观而底盘差不多的可以并线
生产的系列车型。 而在外形上的改变就要对覆盖件模具进行大量投入, 在外
供 了技 术保障 。
同时也可以对零件工艺性提出很好的改进意见,为车身 工程化设计提供支持的同时, 也节约了车身冲压件模具 的设计时间。同样还会减少因分析结果不好造成_艺性 r :
差, 在后期增加大量 的设 计变 更 , j 1 中的设计 变 增)¥造 n1
3 汽车冲压模具设计制造中的新技术 .
决定 了模具 的设 计制 造水 平 ,目前 国内模具制造水平 同
国际先进水平的最大差距就体现在冲压工艺水平的差距
性分析的同时也就可以进行模具 的工艺设计与成彤分析 ,
编制,来满足数控机床加工复杂模具曲面的 N C加工程
序要求。 由于数控机床的精度提高, 刀具技术的发展, 数 控控制系统能力的提高,对于高质量外覆盖件模具的加 工已不是问题,高速加工技术和五轴加工技术都被广泛 地运用于汽车冲压模具制造中,也为制造高质量模具提
覆盖件和结构件 的数控加 工, 以引进 l 所 『 国外通 用的3 D
汽车钣金冲压工艺图文详解

冲压基础工艺培训
1.冷冲压:是指在常温下,利用安装在压力机上的冲模对材料施加压力, 使其产生分离或塑性变形,从而获得所需要零件的一种压力加工方 法
2.冷冲压的特点: 产品尺寸稳定,精度高,重量轻,刚度好,互换性好,高效低耗,
操作简单,易于实现自动化
冲压设备
冲压零件
模具
工艺条件
冲压零件影响因素
冲压基本工序分类
落料
BL
斜楔翻边/冲 CFL/CPI/CT
孔/修边
R
基本模具结构图 G
P
F
C M
E J
B
B
A
A
N
D
HLeabharlann DHNA
双
B
A
动B M
C
K
F
J
E
L
P G
H
J
K
U V
B
N
修翻
R M
Q
L
T
X
P
L
E
C S
G 边边 W 冲整
孔形
E
F
Y
D
A K
H
L
K
单 动
拉延方向的选择 合理的拉延方向应符合以下原则:
1.保证凸模能将工件需拉深的部位在一次拉深中完成,不应有凸 模接触不到的死区(即“倒勾”形)。 2.拉延开始时,凸模与毛坯的接触状态应良好;接触面积应尽 量大而靠近中心;凸模表面同时接触毛坯的点要多而分散,并 尽可能分布均匀,防止毛坯窜动。 3.尽可能减小拉延深度,并使各部位拉延深度趋于均匀。
压料面
B
A
A
B
A
分模线
分模线
B A
修边线
汽车车身制造工艺及新技术
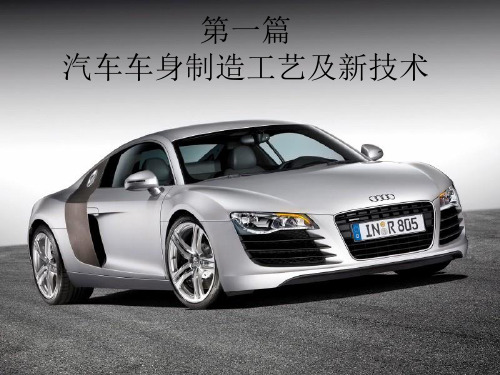
图1-3 间隙大小对冲裁件质量的影响 1-断裂带 光亮带 圆角带 断裂带;2-光亮带 圆角带; 断裂带 光亮带;3-圆角带
3) 冲裁间隙的确定原则:
保证冲裁件质量和尺寸精度的前提下,使模具寿命最高。 保证冲裁件质量和尺寸精度的前提下 , 使模具寿命最高 。 新模具采用最小合理 间隙Zmin。(见表 1-4) 间隙 。 )
3. 车身覆盖件的拉延工艺分析
选定拉延方向,就是确定工件在模具中的三向坐标(x,y,z) 位置。拉伸方向的合理性是拉延工艺合理性的前提。 其应符合以下原则: 其应符合以下原则: (1)保证凸模能够进入凹模不产生负角。 )保证凸模能够进入凹模不产生负角。 (2)工艺补充面 ) 在拉延本体外,另增添的必要材料称为工艺补充面,它 直接影响到抗延成形,及拉延后修边、整形、翻边等工序。 确定工艺补充部分考虑的问题 上:凸模不能进入凹模 下: 凸模能进入凹模 拉深深度尽可能浅 图1-19 覆盖件的凹形 尽量采用垂直修边 决定拉深方向 工艺补充部分尽量小 (3) 压边面 压边面指板料在凹模圆角以外的法兰部分, 由工件本体部分或工艺补充部分组成,其应是平 面或曲率较小的曲面,不允许有大的起伏或拐点。 ( 在拉伸成形的过程中,压边面的材料被逐渐 (a) (c) b) 拉入凹模腔内,转化为覆盖件形状。 压边面与凸模形状保持一定几何关系,保证在 拉伸过程中板料处于张紧状态,并能平稳地包拢 凸模,防止起皱破裂。
2. 冲裁间隙对冲裁件质量影响及间隙选择
1) 冲裁间隙:是指凹模凸模刃口工作部分尺寸之差。 2) 冲裁间隙大小的影响: 冲裁件的断面质量、尺寸精度、冲裁力大小、模具寿命 冲裁件的断面质量、尺寸精度、冲裁力大小、
因此,选择合适的间 隙同时保证间隙的匀, 是保证制件质量的重 要因素。 见图 1-3。
汽车冲压制造技术
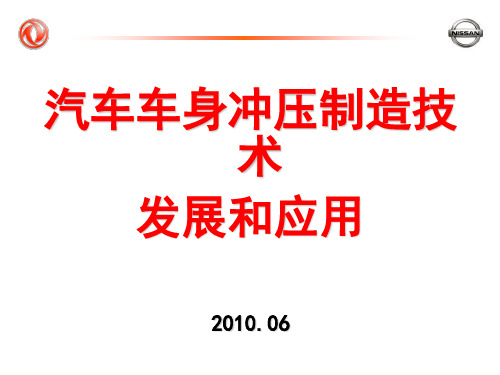
2010.06
汽车车身冲压技术的发展
趋势:随着整车要求更安全,更环保,更低能耗,需要车身
轻量化而更坚固,车身冲压在安全、环保、高品质、高效率、
低成本、数字化制造不断发展
材料:高强度钢板及激光拼焊板的应用
工艺:热冲压成形和液压成型技术的应用
设备:高速冲压自动线和伺服压力机的发展 模具:模具技术和有限元分析CAE技术在冲压 成形中快速发展和应用 2010年冲压规划工作介绍
冲压材料的发展
高强度及超高强度钢板的定义 随着整车轻量化和安全法规的碰撞安全性要求提高,冲压材料向着高强 度方向发展。高强度钢板在汽车应用上发展很快,目前在欧洲轻量化概念化车的用 材中,高强度钢板约占用80%左右。强度在270—780MPa应用的最多。
按抗拉强度划分: 高强钢:TS≥340MPa(冷轧) 70 TS≥370MPa(热轧及酸洗) 60 超高强钢:TS>590MPa 按屈服强度划分: 高强钢:YS≥210MPa
自动化成本/万 元 2100*2 1200*3
压力机/万 元 6000*2 6000*3
土建/万元 1800*2 1800*3
废料输送+天车/ 万元 80*2+(110+70) *2
合计/万 元 20320 27780
80*3+(110+70) *3
表2,运行投资对比 冲压线类别 机械手系统 机器人系统 班制 自动化 线/条 2 3 年人工成本/万 元 160*2 160*3 水电气/万元 12.5*2 12.5*3 备件费用 40*2 40*3 合计/万元 425.6 637.5
冲压设备的发展
冲压设备的发展
人工冲压线
汽车零部件冲压和压铸的工艺差别

汽车零部件冲压和压铸是两种常见的金属加工工艺,它们在汽车制造中扮演着重要的角色。
本文将就汽车零部件冲压和压铸的工艺差别展开详细讨论,以帮助读者更好地理解这两种工艺的特点和适用范围。
1. 背景介绍汽车零部件的生产通常采用冲压和压铸工艺。
冲压是指将金属板料通过冲模、模具等工具进行压力加工,在压力的作用下,使金属板料发生塑性变形,最终得到所需形状的零部件。
而压铸则是将金属加热到液态后,通过高压注入模具中,冷却后得到所需零部件的工艺。
2. 工艺原理2.1 冲压工艺原理冲压工艺是通过模具对金属板料施加压力,使之产生塑性变形,最终得到所需形状的零部件。
在冲压过程中,金属板料会受到拉伸、挤压、弯曲等力的作用,从而改变其形状和尺寸。
冲压工艺具有高效、精度高、成本低等优点,适用于大批量生产。
2.2 压铸工艺原理压铸工艺是将金属加热至液态后,借助高压将其注入模具中,经过冷却后得到所需零部件的工艺。
在压铸过程中,金属液体充填模腔并在一定压力下凝固,形成零部件的完整形状。
压铸工艺具有生产周期短、精度高、成型率高等优点,适用于复杂形状、精密要求较高的零部件。
3. 工艺特点比较3.1 精度要求在精度要求方面,冲压工艺通常适用于对形状尺寸精度要求不高的零部件,而压铸工艺适用于对形状尺寸精度要求较高的零部件。
3.2 适用范围冲压工艺适用于生产大批量、简单形状、尺寸较大的零部件,而压铸工艺适用于生产小批量、复杂形状、精度要求较高的零部件。
3.3 成本比较在成本方面,冲压工艺的模具成本低、生产效率高,适用于大规模生产;而压铸工艺的模具成本较高,适用于小规模生产。
3.4 工艺难度冲压工艺相对简单,操作技术要求较低;压铸工艺技术要求较高,对操作人员的技能和经验有较高的要求。
4. 产业发展趋势随着汽车制造技术的不断进步,冲压和压铸工艺都在不断完善和发展。
未来,随着汽车零部件对精度、强度、轻量化等性能要求的提高,冲压和压铸工艺都将面临新的挑战和机遇。
冲压新工艺(3篇)

第1篇随着我国制造业的快速发展,冲压工艺在汽车、家电、电子等行业中的应用越来越广泛。
传统的冲压工艺在满足产品性能和品质要求的同时,也存在一定的局限性,如能耗高、生产效率低、产品精度不足等。
为了推动制造业高质量发展,提升我国制造业的竞争力,冲压新工艺应运而生。
本文将从冲压新工艺的背景、关键技术、应用领域及发展趋势等方面进行探讨。
一、冲压新工艺的背景1. 传统冲压工艺的局限性传统冲压工艺主要依靠人力操作,设备较为简单,生产效率低,能耗高,且产品精度和一致性难以保证。
随着市场竞争的加剧,传统冲压工艺已无法满足现代制造业的需求。
2. 制造业高质量发展的需求为了提升我国制造业的竞争力,实现高质量发展,迫切需要提高生产效率、降低能耗、提高产品精度和一致性。
冲压新工艺的出现,为制造业提供了新的解决方案。
二、冲压新工艺的关键技术1. 智能化控制系统智能化控制系统是冲压新工艺的核心技术之一,通过引入PLC、工控机等智能设备,实现冲压过程的自动化、智能化。
智能化控制系统具有以下特点:(1)实时监控:对冲压过程中的各项参数进行实时监控,确保生产过程的稳定性和安全性。
(2)故障诊断:对设备故障进行实时诊断,提高设备运行效率。
(3)工艺优化:根据实际生产情况,优化工艺参数,提高产品精度和一致性。
2. 高精度模具技术高精度模具是冲压新工艺的关键,通过采用CNC加工、电火花加工等先进加工技术,实现模具的高精度制造。
高精度模具具有以下特点:(1)精度高:满足产品尺寸精度和形状精度要求。
(2)耐磨性:延长模具使用寿命。
(3)一致性:提高产品的一致性。
3. 精密检测技术精密检测技术在冲压新工艺中扮演着重要角色,通过引入高精度测量设备,如三坐标测量机、光学投影仪等,对产品进行全方位检测,确保产品质量。
精密检测技术具有以下特点:(1)高精度:满足产品精度要求。
(2)高效:提高检测效率。
(3)自动化:实现检测过程的自动化。
4. 绿色环保技术绿色环保技术是冲压新工艺的重要组成部分,通过优化工艺流程、降低能耗、减少废弃物排放,实现生产过程的绿色环保。
钢板热冲压新技术介绍

钢板热冲压新技术介绍一、本文概述随着汽车工业的快速发展,对汽车零部件的性能要求日益提高,特别是在安全性、轻量化和节能减排方面。
钢板热冲压技术作为一种先进的金属成形工艺,以其独特的优势在这些领域发挥着重要作用。
本文旨在全面介绍钢板热冲压新技术,包括其基本原理、工艺流程、设备配置、材料选择以及应用领域等方面的内容。
通过深入了解钢板热冲压新技术,可以为汽车工业及其他相关领域的技术进步和创新发展提供有益的参考和借鉴。
二、传统钢板热冲压技术概述传统钢板热冲压技术,也被称为热成形或热压成形,是一种广泛应用于汽车制造业的金属成形工艺。
该技术主要利用高温下金属材料的良好塑性,通过在红热状态下对钢板进行冲压,以实现复杂形状和高强度构件的制造。
在传统的钢板热冲压过程中,钢板首先被加热到奥氏体相变温度以上,使其具备足够的塑性。
随后,在高温条件下,钢板被迅速转移到冲压模具中,利用模具的压力和形状,使钢板发生塑性变形,从而得到所需的形状和尺寸。
完成冲压后,零件通过淬火和回火等热处理工艺,获得高强度和高硬度的马氏体组织。
传统钢板热冲压技术的优点在于能够制造出高强度、高刚度的复杂形状零件,这些零件在汽车工业中广泛应用于车身结构、底盘部件以及安全系统等关键部位。
该技术还能够实现零件的轻量化,降低整车的能耗和排放。
然而,传统钢板热冲压技术也存在一些局限性。
高温操作对设备和模具的材料要求较高,增加了制造成本。
热冲压过程中需要精确控制加热温度、冲压速度和冷却速率等参数,以确保零件的质量和性能。
由于热冲压过程中金属材料的流动性和成形性受温度影响较大,因此对于一些形状复杂或尺寸精度要求较高的零件,制造难度较大。
随着科技的不断进步和汽车工业的发展,传统钢板热冲压技术也在不断创新和完善。
目前,研究人员正致力于探索新型加热方式、优化冲压工艺参数以及开发高性能的模具材料等方面的工作,以期进一步提高热冲压技术的成形精度、生产效率和经济效益。
三、钢板热冲压新技术介绍随着现代工业的快速发展,钢板热冲压技术作为一种先进的金属成型工艺,正日益受到业界的广泛关注和应用。
中国汽车冲压行业的技术发展趋势
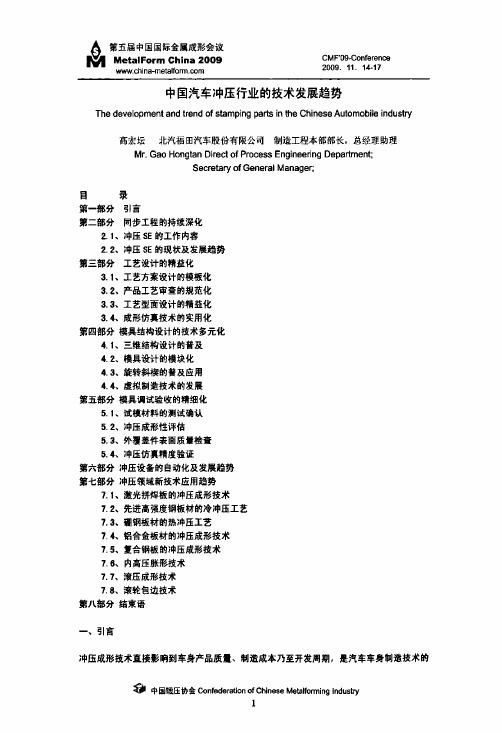
》
几何修正法是将馥^壹面各处沿着相应的回弹偏差方向傲匣向修正,通过反复试 错直至收敛。谆方法收敛逮度快但产品的截面线长在试错循环过程中不断地变化。
I旦翌!!堡堕查塑三堡鎏堡】
l
l∞培&EI序#∞目抖攥赧 l
l
月_弹&tn何&HnⅢz月#m”目抖补*
J
tf"#i∞&互I序#生成*的-^_B l _ad{f拉Ⅱ戚g柏日-曩报
7
7.5、复合钢板的冲压成形技术
7
7.7、滚压成形技术
7
第八部分结束语 一、引言
冲压成形技术直接影响到车身产品质量、制造成本乃至开发周期,是汽车车身制造技术的
翱中国锻压协会confederaIionofChin∞eMetalfo帅ilgIndustry
1
6第五届中国国际金属成形会议 ●翻MetalForm∞№2009
冲压行业既充满发展的机遇,又面临以高新技术进一步变革传统技术的严峻挑战。
二、同步工程的持续深化
近年来,同步工程(踮工程)的理念已莲步被我国主机厂接纳并渫八推广。制造工艺的同 步工程赫是将工艺设计与产品设计并行开发.在产品搬横珠结之前挖掘产品和工艺存在的 问置井殛时整改,吼黛少后期由于设计变更而造成的成本浪费。
5)横具型面在冲压过程中的运动关系和参数设定;
6)压边力和成形吨位的预测方法; 7)板料形状尺寸的优化方法。
3 4
3仿真结果评价的专业化
9中目锻&协eco…fed rati㈣ofChi
6
eMetaffe…i
gIndu“w
6第五届中国国际金属成形会议
嘲M㈣etaⅢlFna_morm☆C№hina∞m20”
我国主机厂对同步工程的开晨通常经历“项目外叠合作”、“内部消化暇收”和“项目独自 承担。三个阶段。 榀田公司通过B璜目和韩国DPECO公司、∞项目与意大利柯马公司合作已初步建立开
2023年汽车冲压模具行业市场分析现状

2023年汽车冲压模具行业市场分析现状汽车冲压模具行业是指制造汽车冲压件所使用的模具制造行业。
随着汽车工业的不断发展,大量的汽车冲压件被应用于汽车生产中,汽车冲压模具行业也得到了快速发展。
以下是对汽车冲压模具行业市场分析现状的1500字阐述:一、市场规模和发展态势1. 市场规模:汽车冲压模具行业的市场规模庞大,与汽车工业密切相关。
根据行业数据显示,全球冲压模具市场规模年销售额超过3000亿美元,其中汽车冲压模具占比约30%。
2. 发展态势:随着汽车工业的快速发展,汽车冲压模具行业也呈现出良好的发展态势。
特别是近年来,随着新能源汽车的兴起和环保要求的提高,对汽车冲压件的需求也在不断增长,推动了汽车冲压模具行业的进一步发展。
二、需求分析1. 增量需求:随着汽车保有量的增加和市场竞争的不断加剧,汽车生产商需要不断进行新车型的开发和上市,这就对汽车冲压模具的需求提出了新的要求。
同时,新能源汽车的不断普及也带动了对新型冲压件和相应模具的需求增长。
2. 更新需求:随着汽车工业的不断进步和技术更新,汽车冲压模具也需要不断更新和改良。
新材料、新工艺的应用以及设计与制造技术的不断提升,对模具行业带来了巨大的挑战和机遇。
3. 换代需求:随着汽车产业的不断发展和市场需求的不断变化,一些老旧汽车冲压模具将面临淘汰和更新。
这将给一些模具制造企业带来机会,可以进行冲压模具更新服务,以满足市场需求。
三、市场竞争分析1. 龙头企业:汽车冲压模具行业中存在一些规模较大的龙头企业,它们的技术实力和市场份额占有优势,比如广汽集团、东风汽车等。
这些企业拥有较强的研发能力和生产能力,具备较高的市场竞争力。
2. 中小企业:汽车冲压模具行业中还存在大量的中小型企业,它们主要承担着部分冲压件的生产任务。
这些企业通常通过专业化、差异化的产品和服务来进行市场竞争,但在技术研发和市场拓展等方面存在一定的困难。
3. 国外竞争:汽车冲压模具行业具有一定的国际竞争性,国外的一些模具企业也在中国市场开展业务。
- 1、下载文档前请自行甄别文档内容的完整性,平台不提供额外的编辑、内容补充、找答案等附加服务。
- 2、"仅部分预览"的文档,不可在线预览部分如存在完整性等问题,可反馈申请退款(可完整预览的文档不适用该条件!)。
- 3、如文档侵犯您的权益,请联系客服反馈,我们会尽快为您处理(人工客服工作时间:9:00-18:30)。
主要用途:汽车发动机中,如气门、气 门座、气门弹簧、摇臂、连杆、离合器 板以及其它如转向齿轮、车轮、紧固件 必须耐腐蚀、耐损伤的车底覆盖件、侧 视镜架等也可以用钛合金制作。 应用现状:由于钛的价格极贵,一般汽 车上使用较少,主要用于赛车上。
特高强度钢的主要应用为卡车底盘、 各种专用车、移动式起重机和建筑工程 机械。特高强度钢的应用主要是为了减 轻重量和提高有效负载能力,同时由于 良好的冷成形性使产品的生产成本降低。
超高强钢焊接抗扭结构,主臂Hale Waihona Puke 侧向 刚度更好轻金属材料--铝
铝及铝合金的密度大致约为钢的1/3。 铝合金具有重量轻、加工性能良好、抗 腐蚀性好、吸振性强等优点,应用于汽 车制造对汽车轻量化有十分显著的效果。
最近,开发出690MPa级卡车大梁用钢, 它利用了在由热带轧机直接轧出的贝氏 体钢中所有的强化机理。
DP钢板
主要组织:铁素体和马氏体,其中马氏 体的含量在5%~20%。 强度:500~1200MPa。 特征:DP钢具有低屈强比、高的加工硬 化指数、高烘烤硬化性能、没有屈服延 伸和室温时效等特点.
日本某公司实际测定该钢的特征值如表 2所示。该钢板可保持良好的韧性,冲 击韧度达到800 J/cm2,低温脆性也较 好。焊接性能较好。采用此种钢板生产 的汽车零件可以使同等强度、刚度的零 件减重50%以上。
涂层板
在耐腐蚀钢板中,镀覆金属层的钢板属 于一种涂层板。因为传统的镀锡板、镀 锌板等已不能适应汽车工业、电器工业、 农用机械及建筑工业的需要,因此新品 种的镀层钢板不断被开发出来。
Octavia明锐全车大量采用了激光拼焊
尽管拼焊材料在使用初期以提高材料利 用率为目的,仅用于小型部件上,但最 近已将拼焊材料扩大应用于车身侧板和 车箱底板等大型部件。 拼焊板主要采用400~590MPa级高强度钢 板,也有使用780MPa级和980MPa级高强 度钢板的情况。
3. 高强度钢板在汽车底盘上的应用
用材已从传统的440MPa级热轧板发展到 780MPa,最大减重达30%。近年来,高强 度钢板在底盘上的使用比例正在急剧增 加。今后,高强度钢板的使用比例及更 高强度钢板的应用有望进一步提高。
采用高强钢制造的汽车底盘
举例:同升专用汽车公司
为了从根本上摆脱对底盘厂商的过度依 附,最终达到底盘厂商对自己的依附, 依托有限公司,将铁路货车新材料、新 工艺等专有技术平移到专用汽车产品上, 努力走自主创新的道路。
高强度钢板的高强度涵义
a. 屈服强度、抗拉强度高,在2703l0MPa范围之内。用于汽车零件的高强 度钢板,其抗拉强度可以达到600800MPa,而相应的普通冷轧软钢板的抗 拉强度只有300MPa; b.高强度钢板的应用,能减轻冲压件 的重量,节省能源和降低冲压产品成本。
在日本,抗拉强度不小于490MPa的热 轧带钢和抗拉强度不小于340MPa的冷轧 钢带被称为高强度钢。
高强度钢板可以减轻零件质量,提高 整车碰撞的安全性,提高零件的外观质 量和抗凹性,因此近年来在车身生产中 得到了越来越多的应用。
1.高强度钢在汽车面板上的应用
车顶、车门、等部件要求具有变形刚度 和抗凹陷性,主要使用抗拉强度为340~ 390MPa的烘烤硬化钢板(BH钢板)。 BH钢板的屈服强度在烘烤涂漆时升高, 可在不损失成形性的前提下,提高抗凹 陷性,减薄钢板。现在,有的车型已使 用440MPa级BH型高强度钢板。
汽车冲压新技术
报告内容
第一节 冲压原材料研究的最新进 展(高强度钢和超高强度钢板以及轻 质金属材料等的使用)
第二节 冲压技术发展的新动向(内 高压成形技术与热冲压成形等)
第三节 模具的发展新动向(产品专业 化、制造数字化与模具设计的专门化) 第四节 冲压设备的发展新动向(大型 多工位压力机与柔性生产化)
5. 展望
目前只有少数国际先进钢铁企业能生产 的960兆帕特高强度热轧工程机械用钢 在宝钢研制成功,填补了国内空白。
中国宝钢集团亦开发了热冲压用硼钢板。 其硬度为450~500HV,强度达到1300~ 1500 MPa,无镀层。 德国蒂森克虏伯开发了锰硼合金钢, 其热冲压淬火后最高强度可达1600MPa。
一般用于需高强度、高抗碰撞吸收能且 也有一定成形要求的汽车零件,如车轮、 保险杠、悬挂系统及其加强件等。
DP钢板优点
①屈服点低,抗拉强度高,屈强比低; ②无屈服点伸长或是屈服伸长,应力应 变曲线平滑; ③伸长率高; ④初始加工硬化率高,加工强化性能好; ⑤抗疲劳性能好。所以DP钢特别适合冲 压翻边性能良好的部件,一直被汽车界 所关注,有可能成为汽车首选的冷轧高 强度钢板。
南车眉山车辆有限公司同升专用汽车
08年,在继具备自主知识产权的“轻量 化半挂车”推向市场后,再度推出高强 度钢“轻量化散装水泥罐车”。“5.12” 灾后重建,四川水泥需求量陡增至3.7亿 吨,需新增车辆约4000台(每台1年运能 2.5万吨,3年运完),针对这一市场需 求,专汽公司在经过充分的市场论证后, 提出了散装水泥罐车研发思路,得到有 限公司的大力支持。
文献综述
汽车车身冲压成形技术是汽车制造技术的 重要组成部分,以致有些国际同行认为汽 车技术的竞争实质上是冲压成形技术及其 相应的焊装技术的竞争。虽然上述观点不 一定准确,但说明冲压成形技术在汽车制 造中的重要地位。
众所周知,汽车车身的金属件几乎 100%为冲压件,而且汽车车身的更新 换代远比底盘和发动机的更新换代快。 这就决定了冲压成形技术在汽车产品 的开发中不仅影响制造周期,还直接 影响成本和产品品质,因而影响产品 的综合竞争力。
TRIP钢
包括热轧、冷轧、电镀和热镀锌产品。 主要组织:铁素体、贝氏体和残余奥氏 体,其中残余奥氏体的含量在5%~15%, 强度:600~800MPa。 主要成分:C、Si和Mn,其中Si的主要作 用是抑制贝氏体转变时渗碳体的析出, 但对于钢板表面质量不利。
在日本,TRIP钢板已被用在概念车底盘 的约80种零件上,同传统钢板相比,用 这种钢板制造的零件重量减轻约12%。 TRIP钢具有高延伸率,同DP钢相比,起 始加工硬化指数小于DP钢,加工硬化指 数在很长的应变范围内仍保持较高,特 别适合胀形成形。
第一节 冲压原材料研究的最新进展
新型冲压用板材包括: 高强度钢板; 耐腐蚀钢板; 双相钢板; 涂层板及复合板材。
高强度钢板
定义:指对普通钢板加以强化处理而得 到的钢板。 强化原理:固溶强化、析出强化、细 晶强化、组织强化(相变强化及复合组 织强化)、时效强化及加工强化等。其 中,前5种是通过添加合金成分和热处 理工艺来控制板材性质的。
有些厂家甚至采用将390MPa、440MPa级 高强度钢板冲压成形后,对强化部分进 行高频加热和淬火,以使部件局部抗拉 强度达到1200MPa,并在冲压加热钢板的 同时进行冷却,以使部件整体抗拉强度 达到1470MPa的方法。
欧洲流行的高强钢U形车厢结构
此外,还有采用激光拼焊方法,将不同 厚度、不同材质钢板拼合起来,使材料 配置适用于所要求材质和使用部位。
车用镁制件应用:仪表板衬底和横梁、 座椅架、方向盘柱、发动机缸盖、变速 器壳体、进气歧管等。
镁合金方向盘
镁合金汽车车轮,质量轻,性能好
轻金属材料--钛
钛的密度为4.5g/cm-3,质轻、强度高、 耐腐蚀性能非常好,但钛价格很贵。钛 应用于汽车,可起到减重、节能、减震、 降噪、减污、延寿、提高汽车安全性和 舒适度的综合作用。
发动机用铝合金支架
铝合金轮毂
轻金属材料--镁
镁合金的主要优点是比强度和比刚度高。 镁的密度仅为铝的2/3,采用镁制造汽车 零件的轻量化效果更胜于铝。不仅如此, 由于镁熔点低,回收再利用的耗能也更 少。镁合金零件的尺寸稳定性好,对振 动的阻尼性能优于铝和钢。
在20世纪50年代至60年代,由于镁合金 的价格不高,德国大众公司的甲壳虫汽 车大量使用镁合金作为结构零件。近年 来,开发出了高纯度耐腐蚀镁合金AZ91D、 AZ91E和高延展性镁合金AM20、AM50等, 性价比有了很大提高。
新马自达2的车身结构中使用了440, 590,780和980Mpa级别的高强度钢板 和超高强度
2. 高强度钢板在车体框架上的应用
随着正面撞击、侧面撞击的撞击安全性标 准的提高,结构件、加强件等主要使用 590MPa级高强度钢板,也有厂家使用 780MPa级、980MPa级高强度钢板。
前防撞梁外板
特高强度钢-瑞典钢板公司生产
特高强度Domex特高强度冷成形钢是在用 计算机严格控制的现代化工厂中生产。 在低碳和一定锰含量的条件下,加入微量 合金元素如铌、钛等细化晶粒,以及超纯 净钢水提供的良好冶金条件,决定了钢的 最终性能。
与普通高强度热轧冷成形钢比,Domex高 强度钢具有更高的铌,钛及钒等微合金 化元素。另外,通过精确控制的加热、 轧制、冷却等步骤组成的热机械轧制工 艺过程是获得高性能的关键因素。 Domex系列冷成形钢具有在高强度条件 下良好的可成形性,可焊性和高冲击强 度。
目前,在汽车上使用的铝质零件除传统 的车轮盖、空调系统、保险杠、座椅、 换热器、油管外,高强度铝合金还广泛 应用于汽车的连杆、摇臂、凸轮座等零 件。由于铝及其合金的原材料价格比钢 高得多,制约了其在汽车上更大范围内 的应用。
轻质铝板可用于车身和底盘的许多零部 件,关键是改进工艺、降低制造成本。 日本于1985年开始采用铝合金板材生产 汽车覆盖件,应用的零件主要是发动机 罩(内板和外板)、前挡泥板及顶蓬窗盖 板等,并且对车身整体进行轻量化设计, 大量采用不等厚的拼焊高强度钢板和深 冲钢板,结合激光焊接装配技术,使车身 重量减轻25%以上。
在涂层板中,各种涂覆有机膜层的板 材具有更好的防腐蚀、防表面损伤的性 能,因此正被大量用作各类结构件。
彩色涂层板具有优异的装饰性、成形 性、抗腐蚀性
复合板材
涂覆塑料的钢板是一种复合板;不同金 属板叠合在一起(如冷轧叠合等)也是 一种复合板,或叫叠合复合板。这类复 合板材破裂时的变形比单体材料破裂时 的变形要大,其基本材料特性值(比如n 值)变大。