原料中硫的控制问题与催化剂硫中毒事故
硫对镍催化剂

硫对镍催化剂
硫对镍催化剂的影响是显著的。
在加氢处理过程中,原料中的硫、氮化合物容易吸附在催化剂活性中心上,导致催化剂中毒。
特别地,硫中毒是一个普遍且重要的问
题。
原料油或气中的硫主要以H2S形式存在,在加氢过程中与催化剂的活性金属镍
发生反应,生成高熔点的硫化镍,沉积在催化剂颗粒表面,覆盖催化剂的活性中心,导致催化剂活性下降甚至完全丧失。
此外,硫还会与催化剂中的其他金属如钴、钼等发生反应,影响催化剂的整体性能和稳定性。
而且,硫中毒是永久性的,含硫化合物一旦吸附在催化剂活性中心上就很难脱附,即便在高氢压、高温下也很难被还原。
为了减轻硫对镍催化剂的毒害,可以采取一些措施,如降低原料中的硫含量、优化操作条件、选择合适的催化剂载体和助剂等。
然而,这些措施的实施可能会受到技术、经济和环境等方面的限制。
因此,在实际应用中,需要根据具体情况综合考虑各种因素,以找到最佳的解决方案。
同时,也需要不断研究和开发新的催化剂和工艺技术,以提高加氢处理的效率和降低硫对催化剂的毒害。
转化催化剂硫中毒的原因和处理

转化催化剂硫中毒的原因和处理肖春来(辽宁葫芦岛锦西石化分公司,辽宁葫芦岛125001) 2007-11-14 制氢转化过程中,硫对转化催化剂具有明显的毒害作用,因硫中毒导致转化催化剂失活甚至报废的情况时有发生,给炼厂造成巨大的经济损失。
为保证装置安全生产,保证转化催化剂长周期运行,需要高度重视硫对催化剂的危害。
1 硫的来源硫是转化催化剂最主要的毒物之一,制氢原料中均含有不同量的硫。
随着焦化干气制氢技术的普及,原料含硫量也在进一步增加。
脱硫单元效果变差,是使硫进入转化系统的最直接来源,大多数时候是由于加氢条件异常使原料中的有机硫氢解不完全,导致脱硫剂出现硫穿透现象;也可能由于原料中的硫含量在短时间内大幅度上升致使加氢脱硫能力不足引起硫穿透。
此外,汽包给水也有可能带入一定量的硫酸根。
2 硫对转化催化剂的危害硫是转化催化剂最常见、也是难以彻底清除的毒物。
不同的制氢原料含有不同量的硫,硫存在的形态十分复杂,大致可分为有机硫和无机硫。
常用的干法脱硫流程是先用加氢催化剂将有机硫氢解成无机硫H2S,然后用脱硫剂将无机硫脱除。
现有工业装置的脱硫精度一般能达到小于0.5×10-6或小于0.2×10-6的水平,残余的微量硫进入转化系统。
转化催化剂具有一定的抗硫性能,就目前常用的转化催化剂而言,脱硫气中硫含量小于0.5×10-6时,能够保证转化催化剂正常发挥活性,可以保证转化催化剂长期使用。
但是,如果进入转化催化剂的硫含量超标,将会引起转化催化剂中毒。
转化催化剂中毒是可逆的。
一般情况下,硫主要引起转化炉上部催化剂中毒,而不易引起整个床层中毒,硫严重超标时也会导致整个系统被污染。
硫中毒后的转化催化剂可以通过蒸汽再生而恢复活性。
转化催化剂严重硫中毒将使转化催化剂严重失活甚至报废。
3 硫中毒的机理转化催化剂中毒一般认为是硫化氢与催化剂的活性组分镍发生了反应:硫化氢使活性镍变成非活性的Ni3S2,因而使转化催化剂活性下降甚至失活。
国产重整催化剂PS-Ⅵ硫中毒分析与对策

国产重整催化剂PS-Ⅵ硫中毒分析与对策随着我国工业化进程的不断推进,对能源的需求日益增加,而石油是目前世界上最主要的能源之一,对石油的加工和利用成为了一个重要的领域。
在炼油过程中,重整催化剂被广泛应用于重整装置,用来将汽油中的芳烃和烯烃转化为高辛烷值的烃类产品。
重整装置中的重整催化剂在运行过程中容易受到硫的中毒影响,影响其催化活性和选择性,从而降低了产品的收率和质量。
本文将就国产重整催化剂PS-Ⅵ硫中毒问题进行分析,并提出对策,以期更好地解决这一问题。
一、国产重整催化剂PS-Ⅵ的特点国产重整催化剂PS-Ⅵ是一种活性高、稳定性好的重整催化剂。
它具有良好的耐硫性能,能够在高硫含量的条件下保持良好的催化活性和选择性。
PS-Ⅵ主要由负载型钼镍硫化物组成,具有较高的比表面积和孔容量,具有良好的抗毒性和热稳定性。
PS-Ⅵ在重整过程中还具有较高的抗结焦性能,不易被焦炭和杂质物质堵塞,从而延长了其使用寿命。
二、国产重整催化剂PS-Ⅵ的硫中毒问题分析虽然国产重整催化剂PS-Ⅵ具有较好的耐硫性能,但在实际运行中,仍然存在硫中毒问题。
硫中毒是指在重整过程中,催化剂表面的活性位点被硫化物所占据,导致催化活性和选择性降低的现象。
硫中毒对PS-Ⅵ的影响主要体现在以下几个方面:1. 催化活性下降:硫化物的存在会占据PS-Ⅵ的活性位点,阻碍了相关反应的进行,导致了催化活性的下降。
2. 选择性降低:硫化物的存在还会改变反应的路径和产物的选择性,导致了产品的收率和质量的降低。
3. 促进剂失效:硫化物还会与催化剂中的一些促进剂发生作用,导致这些促进剂的失效,从而降低了催化剂的效果。
三、国产重整催化剂PS-Ⅵ的硫中毒对策针对国产重整催化剂PS-Ⅵ的硫中毒问题,我们可以采取以下对策来加以解决:1. 优化工艺条件:适当降低重整装置中的硫化氢含量,可以减少硫中毒的程度,延长PS-Ⅵ的使用寿命。
2. 加强预处理:在重整装置投运前,进行严格的预处理工作,将硫化物和其他有毒物质尽可能地去除,减少其对PS-Ⅵ的影响。
炼油厂事故案例分析

炼油车间事故案例分析目录1 同类装置事故汇编 11.1 重整催化剂水中毒事故 11.2 重整催化剂硫中毒事故 11.3 重整反应器结焦事故 11.4 催化剂跑损事故 21.5 催化剂提升管弯头破裂事故 31.6 重整第一反应器堵塞事故 31.7 容器严重憋压事故 41.8 锅炉干锅事故 41.9 装置进水事故 51.10 塔内瓦斯外泄事故 51.11 压控阀冻结设备超压事故 51.12 预分馏塔超压事故 61.13 重整临氢换热器出口管线弯头破裂事故 6 1.14 重整高压分离罐出口线堵塞事故 61.15 盲目进罐油气中毒事故71.16 盲板管理混乱造成紧急停工事故71.17 瓦斯罐超压险些爆炸事故71.18 重整反应器出口法兰焊口断裂事故81.19 氢压机出口补氮气阀阀芯碎裂事故81.20 某厂重整车间炉管堵塞事故81.21 氮气窒息事故之一81.22 氮气窒息事故之二91.23 氮气窒息事故之三91.24 氢气压缩机缸套冻裂101.25 氢气装瓶机抱轴事故101.26 预加氢压缩机玻璃看窗破裂事故101.27 往复式压缩机缸盖紧固螺栓断裂事故11 1.28 氢压机机身及进出口管线震动大事故11 1.29 加氢进料泵机械密封泄漏事故111.30 判断失误严重损坏氢压机事故121.31 重整压缩机曲轴箱爆炸事故121.32 九江石化铂重整装置F101闪爆事故之一13 1.33 九江石化铂重整装置F101闪爆事故之二13 1.34 九江石化铂重整装置F101闪爆事故之三14 1.35 九江石化铂重整装置F101闪爆事故之四14 1.36 加热炉回火伤人事故之一151.37 加热炉回火伤人事故之二151.38 加热炉回火伤人事故之三151.39 加热炉回火事故之四161.40 加热炉回火伤人事故之五161.41 重整炉出口法兰着火事故161.42 处理堵塞管线引起人烧伤事故171.43 预加氢催化剂自燃事故171.44 炉膛气体未分析点火爆炸伤人事故171.45 加热炉炉膛爆炸事故171.46 扫线动火互不联系造成爆塔事故181.47 违章操作造成氢气爆炸着火烧伤人员事故181.48 装置吹扫中着火致使2人被烧死事故181.49 高温汽油烫伤人事故191.50 1993年金陵石化铂重整车间氢贮瓶爆炸事故报告192 镇海炼化公司部分事故汇编212.1 1980年11月6日炼油厂成品油码头冒罐跑油事故212.2 1981年3月7日炼油厂热电站重大停电事故212.3 1981年4月7日炼油厂热电站锅炉严重缺水造成炉管胀接口泄漏事故212.4 1982年7月23日炼油厂油品车间油罐爆炸事故222.5 1982年8月14日炼油厂催化车间跑润滑油事故222.6 1983年9月17日化肥厂合成车间2#渣油贮罐冒罐事故232.7 1984年6月18日炼油厂油品车间油罐抽瘪事故232.8 1985年1月11日化肥厂火炬倾斜事故232.9 1987年6月30日化肥厂4118-K1T烧瓦事故242.10 1988年1月30日炼油厂油品车间碱液严重烧伤事故242.11 1988年11月5日化肥厂仪表工误操作造成全厂停车事故24 2.12 1989年9月5日炼油厂排水车间重伤事故252.13 1990年1月5日化肥厂合成车间现场着火伤人事故252.14 1990年5月22日炼油厂油品车间氢氟酸灼伤事故252.15 1991年1月21日机修厂铆焊车间检修工硫化氢中毒事故26 2.16 1991年4月25日化肥厂合成车间现场着火伤人事故262.17 1992年10月16日化肥厂常明火炬管线水击落架事故262.18 1993年7月16日炼油厂丙烷压缩机开关带负荷合闸事故27 2.19 1994年4月1日炼油厂一套常减压串跑油事故272.20 1994年10月6日炼油厂催化车间着火烧伤检修工事故272.21 1995年3月31日炼油厂Ⅰ套常减压着火事故282.22 1995年5月28日化肥厂合成车间误操作引起停车事故282.23 1995年6月22日仓储公司贮运车间串油事故282.24 1995年9月10日化肥厂0101-V1-3渣油罐憋压损坏事故29 2.25 1995年9月19日炼油厂焦化行车工违章作业致人重伤事故29 2.26 1996年1月23日炼油厂加氢装置润滑油泵轴瓦损坏事故30 2.27 1997年1月10日化肥厂合成车间1#气化炉闪爆伤人事故30 2.28 1997年3月13日炼油厂聚丙烯车间三名职工违章抽烟引起闪燃事故302.29 1997年6月22日仓储公司贮运车间跑油事故312.30 1997年7月10日炼油厂加氢裂化F-304爆炸事故312.31 1998年1月22日炼油厂焦化车间火灾伤人事故312.32 1998年2月13日炼油厂一车间着火伤人事故322.33 1999年1月29日仓储公司贮运车间串油事故322.34 1999年3月21日炼油厂油品车间泵房火灾事故332.35 1999年11月22日炼油厂重油催化检修现场跑油事故332.36 1999年11月26日炼油厂油品车间丙烯栈台火灾事故332.37 1999年12月15日炼油厂重油催化检修现场瓦斯外泄事故33 2.38 2000年3月30日炼油厂一车间火灾事故342.39 2000年4月20日炼油厂二电站CFB锅炉设备损坏的事故35 2.40 2000年9月29日炼油厂油品车间重伤事故352.41 2001年3月15日一车间“3.15”火灾事故352.42 2001年3月31日重一F-501闪爆362.43 2001年7月24日炼油厂化验职工李一平死亡事故363 重整装置长期稳定运转中常见问题与相关事故383.1 重整装置预处理单元腐蚀问题及相关事故383.2 重整装置的积碳问题与相关事故413.3 重整催化剂氮中毒问题443.4 重整原料油的切割与保护问题453.5 原料中硫的控制问题与催化剂硫中毒事故463.6 重整反应系统水环境控制问题与相关事故473.7 催化剂氯失调问题与相关事故483.8 对突发事故的处理原则和方法501 同类装置事故汇编1.1 重整催化剂水中毒事故1.1.1 原料带水现象91年12月14日下午,九江石化铂重整装置预分馏塔操作出现异常,塔顶回流罐液面上升,拔头油量增大,随后出现重整产氢量逐渐下降,由4500Nm3/h下降到2000Nm3/h,循环氢纯度由83%上升到96%。
化工企业变换催化剂中毒原因分析

化工企业变换催化剂中毒原因分析摘要:针对某化工企业先后出现的耐硫宽温变换催化剂快速中毒失活现象,通过对失活催化剂进行检测分析认为是氯含量高引起。
经过排查,推断为原料煤中有机注浆材料中的有机氯导致催化剂中毒,并建议通过减少有机注浆材料用量、加强原料煤筛选、加强工艺水检测、加强管理等手段进行应对。
关键词:变换催化剂;中毒;氯1分析原因问题出现后,该企业多次更换部分催化剂并试用了不同厂家的同类催化剂,均出现了催化剂快速中毒的现象。
在排除了催化剂本身的质量因素后,该企业对中毒催化剂进行了分析化验。
化验结果表明,中毒催化剂中的氯含量为1.56%,远远超出了正常值(10×10-6),其他组分含量正常。
氯有未成键孤对电子,并有很大的电子亲和力,易与金属离子反应,造成催化剂活性组分流失、孔道阻塞或结构破坏,导致催化剂中毒。
氯还具有很高的迁移性,常随工艺气向下游迁移,造成催化剂全床层性中毒。
在实际生产中,氯引起的“累积效应”常造成各种催化剂中毒据此推断,该公司的变换催化剂失活是由于系统中的氯含量过高。
2排查来源为明确中毒原因,查明中毒来源,该企业变换催化剂中毒的氯的来源开展排查。
原料气中氯的来源主要有原料煤、工艺水和空气这3个途径。
2.1排查原料煤原料煤中氯元素以无机和有机两种形式存在,无机氯在造气过程中会随炉渣或造气循环水排出系统,不会进入变换工段,理论上不会导致变换催化剂中毒。
有机氯在造气炉干馏段(300℃)内由固态变成气态,由于有机物不溶于水,不能被造气冷却水洗涤脱除,就随粗煤气进入到了变换工段。
变换工段温度、压力升高,在H2氛围和金属氧化物存在的条件下,有机氯与H2发生取代反应,将有机氯化物转化成无机氯,主要是氯化氢。
氯化氢与催化剂中的金属离子反应,导致催化剂中毒失效。
2.1.1煤质我国煤中氯含量一般较低,通常都在0.101%~0.120%,晋城矿区的煤属于特低氯煤。
此次事件中该企业使用的原料煤主要是来自B、C、D、E4个矿井。
国产重整催化剂PS-Ⅵ硫中毒分析与对策
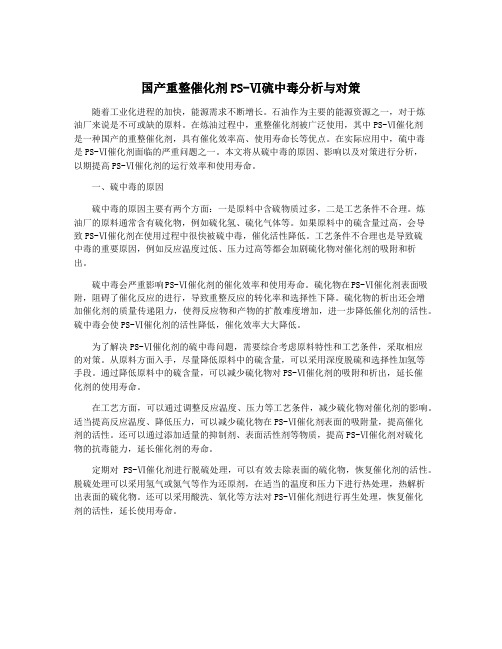
国产重整催化剂PS-Ⅵ硫中毒分析与对策随着工业化进程的加快,能源需求不断增长。
石油作为主要的能源资源之一,对于炼油厂来说是不可或缺的原料。
在炼油过程中,重整催化剂被广泛使用,其中PS-Ⅵ催化剂是一种国产的重整催化剂,具有催化效率高、使用寿命长等优点。
在实际应用中,硫中毒是PS-Ⅵ催化剂面临的严重问题之一。
本文将从硫中毒的原因、影响以及对策进行分析,以期提高PS-Ⅵ催化剂的运行效率和使用寿命。
一、硫中毒的原因硫中毒的原因主要有两个方面:一是原料中含硫物质过多,二是工艺条件不合理。
炼油厂的原料通常含有硫化物,例如硫化氢、硫化气体等。
如果原料中的硫含量过高,会导致PS-Ⅵ催化剂在使用过程中很快被硫中毒,催化活性降低。
工艺条件不合理也是导致硫中毒的重要原因,例如反应温度过低、压力过高等都会加剧硫化物对催化剂的吸附和析出。
硫中毒会严重影响PS-Ⅵ催化剂的催化效率和使用寿命。
硫化物在PS-Ⅵ催化剂表面吸附,阻碍了催化反应的进行,导致重整反应的转化率和选择性下降。
硫化物的析出还会增加催化剂的质量传递阻力,使得反应物和产物的扩散难度增加,进一步降低催化剂的活性。
硫中毒会使PS-Ⅵ催化剂的活性降低,催化效率大大降低。
为了解决PS-Ⅵ催化剂的硫中毒问题,需要综合考虑原料特性和工艺条件,采取相应的对策。
从原料方面入手,尽量降低原料中的硫含量,可以采用深度脱硫和选择性加氢等手段。
通过降低原料中的硫含量,可以减少硫化物对PS-Ⅵ催化剂的吸附和析出,延长催化剂的使用寿命。
在工艺方面,可以通过调整反应温度、压力等工艺条件,减少硫化物对催化剂的影响。
适当提高反应温度、降低压力,可以减少硫化物在PS-Ⅵ催化剂表面的吸附量,提高催化剂的活性。
还可以通过添加适量的抑制剂、表面活性剂等物质,提高PS-Ⅵ催化剂对硫化物的抗毒能力,延长催化剂的寿命。
定期对PS-Ⅵ催化剂进行脱硫处理,可以有效去除表面的硫化物,恢复催化剂的活性。
脱硫处理可以采用氢气或氮气等作为还原剂,在适当的温度和压力下进行热处理,热解析出表面的硫化物。
国产重整催化剂PS-Ⅵ硫中毒分析与对策

国产重整催化剂PS-Ⅵ硫中毒分析与对策催化剂是化学过程中的重要辅助剂,广泛应用于炼油、化工、石化等工业领域。
催化剂使反应速率大幅提高,提高产品质量,降低生产成本。
长期的使用会导致催化剂中毒现象,影响催化剂的活性和稳定性。
本文将阐述国产重整催化剂PS-Ⅵ硫中毒的分析与对策。
我们需要了解催化剂硫中毒的原因。
PS-Ⅵ是一种贵重金属成分较高的催化剂,经过长时间使用后,底物中的硫含量逐渐积累在催化剂表面,导致催化剂活性降低。
硫中毒的主要原因是硫与催化剂金属表面反应生成金属硫酸盐,阻塞反应物分子进入活性中心和产物分子的扩散。
针对PS-Ⅵ催化剂硫中毒问题,我们可以采取以下几种对策。
首先是加强原料气体的净化处理。
通过使用高效脱硫装置,降低底物中的硫含量,减少硫污染对催化剂的影响。
其次是优化操作条件。
合理控制反应温度、压力和催化剂的空速,提高反应物在催化剂表面的接触时间,降低硫中毒速度。
还可以采用周期逆流反应装置,定期逆流清洗催化剂表面的硫酸盐,恢复催化剂的活性。
在硫中毒发生后,我们可以采取一些方法重新活化PS-Ⅵ催化剂,恢复其活性。
首先是热解法。
将硫中毒的催化剂加热至一定温度,使催化剂表面的硫酸盐分解为硫化物和气体,去除硫污染。
其次是化学法。
使用硫化氢或氢气等可还原物质与硫酸盐反应,还原成非活性硫化物,恢复催化剂活性。
还可以考虑采用物理法,如超声波清洗、高压水汽冲刷等。
研发新的催化剂也是解决硫中毒问题的重要方向。
通过控制催化剂表面结构,改善催化剂的抗硫性能。
可以探索添加非贵金属助剂,提高催化剂的抗硫能力。
也可以研究催化剂的再生技术,实现长周期使用。
针对国产重整催化剂PS-Ⅵ的硫中毒问题,需要加强原料气体的净化处理,优化操作条件,采用周期逆流反应装置清洗催化剂,采用热解法、化学法或物理法重新活化催化剂,以及研发新的催化剂技术。
这些措施将有助于提高催化剂的抗硫性能,延长催化剂的使用寿命,提高生产效益。
连续重整PS_催化剂硫中毒分析及对策_刘宏鑫
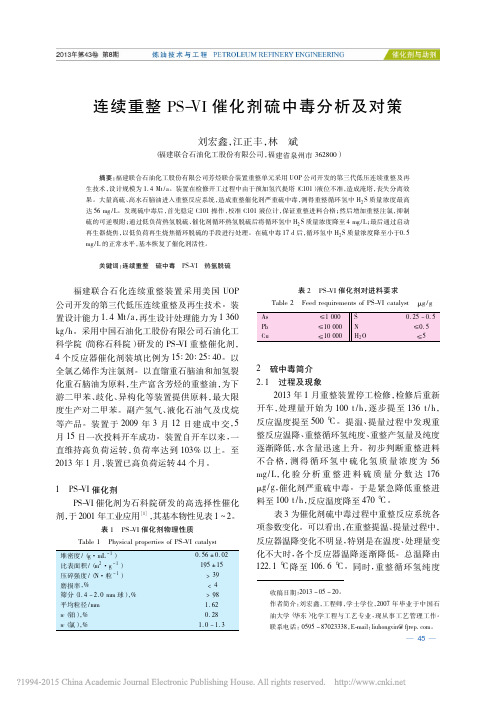
少,极大地左右了催化剂脱硫的处理方式,本次硫 中毒前,积炭维持在一个较低的水平,为之后的处 理提供了充足的时间和灵活性。
( 3) 在催化剂积炭不高时,提高重整进料注氯 和重整反应温度,加大产氢量,能加快脱硫效果。
( 4) PS-VI 催化剂具有较高的稳定性,在高负 荷运转 44 个月之后发生硫中毒时,仍能较好地恢
炭 4. 00 4. 20 3. 96 3. 29 4. 07 3. 91 3. 58 4. 08
氯 0. 89 0. 87 0. 89 0. 90 1. 10 1. 11 1. 19 1. 19
项目 ρ( H2 S) / ( mg·L - 1 ) ρ( HCl) / ( mg·L - 1 ) 注氯量 / ( μg·g - 1 ) 加权平均床层温度/ ℃
3 硫中毒处理 在发现重整催化剂硫中毒后,为防止重整进
料中带硫,污染催化剂,故停止重整注硫,并确认 C101 液位,修改仪表参数至正常值。预加氢反应 温度由 280 ℃ 提至 285 ℃ 。增加重整进料化验分 析频率,在确保进料合格的同时,采取以下措施恢 复催化剂活性。 3. 1 维持再生停车状态 低负荷热氢脱硫
49. 8
20∶ 00 128 488. 0
40. 1 36. 9 26. 4 18. 1 121. 5 73. 0
70. 0
22∶ 00 128 488. 0
35. 1 30. 1 23. 9 17. 5 106. 6 69. 4
86. 2
24∶ 00 136 500. 0
42. 3 35. 7 28. 8 19. 4 126. 0 67. 4
01 - 22 13 15
- 1、下载文档前请自行甄别文档内容的完整性,平台不提供额外的编辑、内容补充、找答案等附加服务。
- 2、"仅部分预览"的文档,不可在线预览部分如存在完整性等问题,可反馈申请退款(可完整预览的文档不适用该条件!)。
- 3、如文档侵犯您的权益,请联系客服反馈,我们会尽快为您处理(人工客服工作时间:9:00-18:30)。
原料中硫的控制问题与催化剂硫中毒事故
问题的提出
众所周知,硫是含Pt重整催化剂的主要毒物之一,硫的问题在实际工作中给我们带来不少问题和困扰。
但必须看到,在某种程度上,它又是重整催化剂中不可缺少的一个组元。
《催化重整通讯》(1986(2),1–18)报导,硫在催化剂上以可逆吸附硫和不可逆吸附硫两种类型存在,不可逆吸附硫主要吸附在金属表面及部分强酸中心上,吸附量与硫化时气流中的H
2
S分压无关,只与活性金属组分有关。
可逆吸附主要吸附在载体上,其吸附量与载体表面积上的铝离子(Al+3)数量有关,氯离子的存在会抑制这部分硫的吸附。
不可逆吸附硫可抑制催化剂的氢解活性,起到改善催化剂选择性的作用。
催化剂上吸附硫以后必然会影响其反应性能,Apesteguia的研究结果认为,硫化后Pt—Re催化剂活性下降程度比单Pt或Pt—Ir催化剂要大得多,且对不同类型的反应,硫对催化剂活性的影响也不一样。
还有资料报导,微量硫对重整催化剂的敏感度的次序为单Pt:Pt一非贵金属:Pt—Re催化剂为1:3:5。
CHEVRON公司曾介绍说,进料含硫1.0ppm 比0.5ppm的运转周期缩短25%,生成油液收减少1%。
有资料报导,对Pt—Re
重整催化剂,进料硫含量应<0.5ppm,即循环气中H
2
S<lppm。
某厂进料硫含量从lppm上升到4—5ppm(缓和操作苛刻度下),结果氢产率
和氢纯度(<80%)均下降,重整生成油收率也下降3—5%,CH
4一C
4
H
10
气体增加
了3—5%。
资料还介绍,有中试数据说明,原料油中硫含量由lppm增加列3ppm,催化剂寿命下降20—30%。
硫中毒事故
国内重整工业装置曾多次出现硫超标造成催化剂硫中毒的事件。
如某厂催化剂硫中毒后,温降、液收、氢纯度和芳含先突降,然后有一段缓慢下降后,芳含又一次突降,芳含从开始的52.2W%下降到40.9W%;液收从89.2W%下降到81.2W%;氢纯度从88.2V%下降到79.0V%。
因装置无手段改变进料质量,提供不了合格精制油(S<0.5ppm),只能被迫停工。
采取措施
催化剂硫中毒以后,只要切断硫源,提供合格的进料,中毒的硫会逐渐解除,催化剂性能能得到恢复。
引起重整进料硫含量增高的原因及相应的对策
正常生产中,造成进料硫含量增高的原因一般有以下四种可能:
(1)、蒸发脱水塔操作失调
这种硫是未吹脱的H
2
S。
重整系统可适当降温,投入分子筛,把硫的影响减小到最低程度,待蒸发脱水塔操作恢复正常后即可恢复。
(2)、预加氢精制进料硫含量变化
预加氢进料硫含量变大,预加氢条件已不适应,这通常是原油含硫高或二次加工油比例改变所致,适当调整预加氢的条件即可解决。
(3)、预加氢部分出了问题
预加氢催化剂活性下降,满足不了加氢要求,可以提高预加氢反应温度。
一般说预加氢催化剂活性不会突然下降。
预加氢反应器是冷壁的,还有可能出现反应器内衬龟裂,造成物流短路而使精制油硫增高(有机硫),如不严重,有硫保护器的装置,可以维持运转。
如严重则需停工处理。
(4)、换热器内漏
换热器内漏,造成精制油硫超标的事在工业装置上时有发生。
常见的是预加氢进料/精制油换热器内漏。
也曾发生预加氢生成油/预分馏进料换热器内漏造成硫不合格。
这里令人费解的是低压往高压漏,因此也常为人所忽视。
换热器可在一天内抢修完,重整可降温降量吃精制油罐贮存的精制油维持运转。
换热器检修试压后,投入使用前务必将器内及管线中残存水处理净,否则会将残存水带入重整系统,造成高水冲击,
为了及时发现原料硫超标,一定要坚持每天分析进料含硫。
这里也存在由于微量硫分析方法精度、采样、分析人员操作素质,一时难以发现硫高,造成延误。
补救的办法是通过分析循环气体和稳定塔顶气中H
2
S含量对比值作旁证参考。
循
环气中H
2S浓度约为重整进料的2—3倍。
稳定塔顶气中H
2
S含量约为进料硫的
10倍。
气中H
2
S分析方便快速,车间亦可自己直接用检测管测定。