催化剂中毒
催化剂中毒

催化剂中毒可逆中毒和不可逆中毒既然中毒是由于毒物和催化剂活性组分之间发生了某种相互作用,那么可以根据这种相互作用的性质和强弱程度,将其分为可逆的(可以再生,暂时的)和不可逆的(不可以再生)3.1金属催化剂的中毒用作催化剂的金属用吸附可利用的d轨道,这无论对它的毒性或它对毒物的敏感性都是关键。
金属催化剂的毒物有如下三类:第一类是Ⅴ族和Ⅵ族元素的具有未共享电子队的非金属化合物(N、P、As、Sb、和O、S、Se、Te的化合物),毒性的程度取决于空的价轨或未共享电子的可利用性。
一些非金属元素化合物,当它有未共享的电子对时,呈毒性;当元素的外层电子结构达到了稳定的八电子偶,而且不存在孤对电子时,则无毒。
第二类是金属离子,这些离子具有已占用的d轨道,并且d轨道上有与金属催化剂的空轨键合的电子。
当金属离子没有d轨道,或者d轨道全空着,或者d轨道伟达到半充满以前,它对铂是无毒的;金属离子的d轨道从半充满到全充满者,它对铂是有毒的。
第三类是不饱和化合物,由于它分子中的不饱和键能提供电子与金属催化剂的d 轨成键,使催化剂中毒。
下表列出了一些金属催化剂的不饱和化合物毒物序号反应催化剂毒物1环己烯加氢Ni、Pt苯,氰化物2乙烯加氢Ni C2H2、CO3合成氨Fe CO4氨氧化Pt C2H2由于不饱和化合物的毒性逾期不饱和度有关,若是其不饱和度减小,就可使毒性减弱或者消除。
例如在合成氨生产中,利用甲烷化催化剂除去原料气中的CO就是基于这一点。
3.2毒物的结构和性质对其毒性的影响毒物分子的毒性大小一般与两个因素有关:一是被毒物分子覆盖的催化剂活性位的数目,此为覆盖因子;二是毒物分子在催化剂表面的平均停留时间,此为吸附寿命因子。
如下表列出几种硫化物对用于丁二烯酸加氢的铂黑催化剂的毒性系数序号毒物分子量α×10-5相对毒性1、硫化氢343.4 12、二硫化碳766.41.93、噻吩8414.84.44、半胱氨酸12116.74.9从表中可以看出,毒物的分子量愈大,毒性系数愈大。
转化催化剂硫中毒的原因和处理

转化催化剂硫中毒的原因和处理肖春来(辽宁葫芦岛锦西石化分公司,辽宁葫芦岛125001) 2007-11-14 制氢转化过程中,硫对转化催化剂具有明显的毒害作用,因硫中毒导致转化催化剂失活甚至报废的情况时有发生,给炼厂造成巨大的经济损失。
为保证装置安全生产,保证转化催化剂长周期运行,需要高度重视硫对催化剂的危害。
1 硫的来源硫是转化催化剂最主要的毒物之一,制氢原料中均含有不同量的硫。
随着焦化干气制氢技术的普及,原料含硫量也在进一步增加。
脱硫单元效果变差,是使硫进入转化系统的最直接来源,大多数时候是由于加氢条件异常使原料中的有机硫氢解不完全,导致脱硫剂出现硫穿透现象;也可能由于原料中的硫含量在短时间内大幅度上升致使加氢脱硫能力不足引起硫穿透。
此外,汽包给水也有可能带入一定量的硫酸根。
2 硫对转化催化剂的危害硫是转化催化剂最常见、也是难以彻底清除的毒物。
不同的制氢原料含有不同量的硫,硫存在的形态十分复杂,大致可分为有机硫和无机硫。
常用的干法脱硫流程是先用加氢催化剂将有机硫氢解成无机硫H2S,然后用脱硫剂将无机硫脱除。
现有工业装置的脱硫精度一般能达到小于0.5×10-6或小于0.2×10-6的水平,残余的微量硫进入转化系统。
转化催化剂具有一定的抗硫性能,就目前常用的转化催化剂而言,脱硫气中硫含量小于0.5×10-6时,能够保证转化催化剂正常发挥活性,可以保证转化催化剂长期使用。
但是,如果进入转化催化剂的硫含量超标,将会引起转化催化剂中毒。
转化催化剂中毒是可逆的。
一般情况下,硫主要引起转化炉上部催化剂中毒,而不易引起整个床层中毒,硫严重超标时也会导致整个系统被污染。
硫中毒后的转化催化剂可以通过蒸汽再生而恢复活性。
转化催化剂严重硫中毒将使转化催化剂严重失活甚至报废。
3 硫中毒的机理转化催化剂中毒一般认为是硫化氢与催化剂的活性组分镍发生了反应:硫化氢使活性镍变成非活性的Ni3S2,因而使转化催化剂活性下降甚至失活。
催化剂中毒的原因
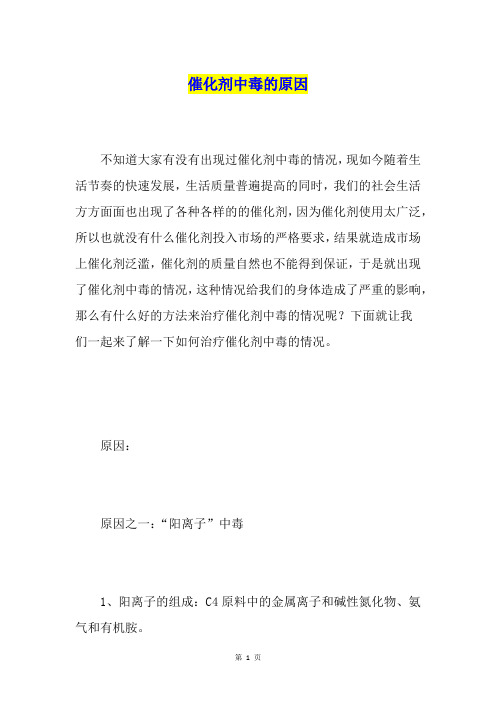
催化剂中毒的原因不知道大家有没有出现过催化剂中毒的情况,现如今随着生活节奏的快速发展,生活质量普遍提高的同时,我们的社会生活方方面面也出现了各种各样的的催化剂,因为催化剂使用太广泛,所以也就没有什么催化剂投入市场的严格要求,结果就造成市场上催化剂泛滥,催化剂的质量自然也不能得到保证,于是就出现了催化剂中毒的情况,这种情况给我们的身体造成了严重的影响,那么有什么好的方法来治疗催化剂中毒的情况呢?下面就让我们一起来了解一下如何治疗催化剂中毒的情况。
原因:原因之一:“阳离子”中毒1、阳离子的组成:C4原料中的金属离子和碱性氮化物、氨气和有机胺。
2、阳离子的来源:①上游原料水洗不彻底而带来的钠离子、钙离子;②设备管道或阀门所产生的可溶性的铁离子、铬离子;③FCC分子筛中的微量铝离子和硅离子;④C4中的氨、甲胺等碱性化合物也属于阳离子的范畴。
3、中毒原理和形式:这些阳离子和催化剂中的SO3OH产生离子交换而使催化剂“中毒”。
反应式如下:SO3OH+M+(Na+、Ca2+、Fe3+、Cr4+、Al4+、NH4+、CH3NH2+……)中毒形式:“一层一层”地中毒,即:先接触物料的先中毒,后接触物料暂不中毒。
原因之二:可水解的腈类和酰胺类物质中毒①在催化裂化中,C4、C5原料通常含有乙腈、丙腈。
②蒸气裂解C4料原中,偶尔会带有上游的丁二烯之抽提用的DMF.原因之三:新型水处理药剂催化剂孔道堵塞,使催化剂失活。
原因之四:催化基团脱落,使催化剂失活。
新型水处理药剂催化剂最高耐温120℃,但长时间在此温度下运行,催化剂的磺化基团会从结构骨架上脱落下来,而流入液相中,从而造成催化剂失活。
以上内容为我们介绍了如何治疗催化剂中毒的情况,我们应该都认真学习一下介绍的方法,无论是我们在今后的生活中出现类似的问题,就可以运用以上介绍的方法及时有效的对我们自身进行治疗,从而更快更好的恢复身体健康。
催化剂中毒原理

中毒原理1、co和co2进入合成塔会在催化剂的作用下与氢发生以下反应CO+3H2=CH4+H2OCO2+4H2=CH4+2H2O2、生成的水蒸汽又会和催化剂--aFe发生以下反应H2O+Fe=Feo+h23H2O+2Fe=Fe2O3+3H2这样催化剂中具有活性的a-Fe被氧化成氧化亚铁和三氧化二铁。
催化剂的活性降低。
现象;1、合成塔的温度是靠3H2+N2=NH3 这一放热反应的反应热维持的,催化剂活性下降,反应热减少,合成塔温度就会下降。
2、合成是一个回路,补充进来的气体靠生成氨后排放出去,催化剂活性下降,氨的合成率下降,补充进来的气体就会在回路里大量累积,合成压力上升。
3、中毒反应也是一个放热反应,所以合成中毒时第1、2点的温度会有一个短暂的温升过程,随着催化剂活性的下降,整个合成塔的温度会急剧下降。
也就是说前面两点温度上升,后面的温度下降。
我们俗称为打交叉。
当然,前面几点的温升时间不会很长,如果中毒深的话,整个合成塔的温度都会垮下来。
外理;1关补充气阀,停止补充不合格气体,直到合成温度正常,且气体合格。
(重新补入合格气体时要对补充气管线进行置换)2关死冷副线、减少循环量,防止温度进一步下降。
3打开塔后放空阀,控制好合成压力,防止超压。
4必要时启用电炉,靠电炉提供的热量提温。
5如果中毒较深,则要将系统内的不合格气体全部放空,并用合格气体顺流程进行置换。
不能犹豫!合成的中毒反应也是一个可逆反应,只要中毒不深,发现及时,处理迅速得当。
合成温度是完全可以保住的。
只是中毒会缩短催化剂的使用寿命,所以要严禁不合格气体进入合成塔。
催化剂经长期使用后,内因接触毒物,活性会逐渐下降。
原因:①催化剂长期处于高温之下,因受热的影响,催化剂的细小晶粒逐渐长大,表面积减小,活性下降;②催化剂层温度波动频繁、温差过大,使催化剂过热或熔融,活性下降;③气流的不断冲击,破坏了催化剂的结构,活性下降;④原料气中少量引起催化剂暂时中毒的毒物,使催化剂表面不停地反复进行氧化、还原反应,活性下降等。
有机催化反应工程-催化剂中毒
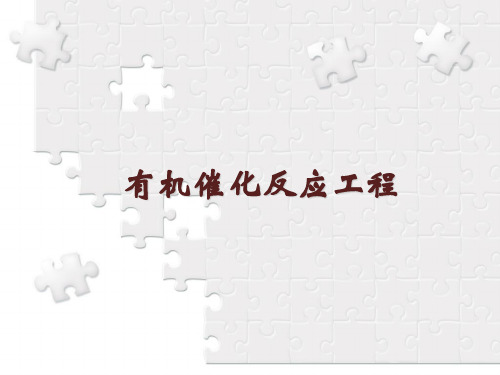
kW 是以催化剂颗粒质量为基准的反应速率常数
kP P kW
均匀中毒
主反应很慢(扩散快>主反应慢)
Effect of poisoning 中毒效应
1( 0.4)
rB kCA (1 ) rB随的增加而线性下降
A k B
比活性F
中毒时的反应速率 未中毒时的反应速率
rA ' rA
' (1 )
以毒物P沉积为基准 的壳层中毒(一)
CPl饱和时固体中毒物浓度(催化剂完全失活)
CP
,
C
s Ps
,
C
c 本体流体、固体表面、核边界处的毒
Ps
物浓度
k
外表面传质系数
gP
k
壳核表面的毒物反应速度常数
sP
DeP毒物的有效扩散系数
吸附
P
分配
系数
CPl催化剂粒子平均毒物浓度
毒物P沉积为基准的壳层中毒(二)
均匀中毒
颗粒内有内扩散影响
F rB ' ' (1 ) rB
1
1
tanh 3
1
1
3
1
1
1
tanh 3 3
均匀中毒
内扩散影响严重时
3.0时
1
1
F ' (1 )
1
'
(1
)
1
均匀中毒 Uniform poisoning
1
F
0
α
内扩散影响严重时
F 1-
内扩散影响小时
1
F 1
内扩散影响的催化剂失活
Sh' =0.5 P
pl
pl
<C >/C
脱硝催化剂中毒的原因与中毒处理

脱硝催化剂中毒的原因与中毒处理目录前言催化剂中毒是指催化剂的活性因接触少量的杂质而使活性显著下降,使催化剂丧失催化作用的物质,称为催化剂的毒物。
烟气中的成分,特别是粉尘中的碱金属、碱土金属和P2O5和烟气中的AS2O3蒸汽等都会使得催化剂活性下降。
下面来了解下脱硝催化剂中毒的原因及处理方法。
1.脱硝催化剂中毒的原因脱硝催化剂中毒简单来说就是指其反应活性位点,被其他离子占据或表面物质阻碍氧化剂还原剂无法接触,导致的脱硝效率、活性等性能下降的现象。
主要包括:神(AS)中毒、S03中毒、碱金属(Na、K)中毒、碱土金属(Ca)中毒。
1.1.神(AS)中毒在燃煤电厂的实际运行当中,神中毒是引起脱硝催化剂活性下降的主要原因之一,如果煤中碎的质量分数超过3X10・6,SCR脱硝催化剂的寿命将降低30%左右。
脱硝催化剂的活性下降将会对脱硝系统及下游设备的运行造成不良影响,甚至会导致NOX超标排放。
1.2.S()3中毒大量的脱硝催化剂都显示了良好的低温脱硝性能,然而,低温下Sθ2引起的脱硝催化剂的中毒,是一个世界性的难题,是目前困扰低温脱硝脱硝催化剂应用的关键。
即使在经过脱硫装置后,烟气中残留的少量sOz,一方面与还原剂氨气发生反应,生成硫酸核盐,堵塞脱硝催化剂的孔洞并覆盖脱硝催化剂的活性位,降低脱硝催化剂的活性。
1.3.碱金属中毒(Na、K)碱金属可直接与催化剂活性组分反应,使催化剂表面酸性下降,降低活性组分的可还原性,致使催化剂失去活性。
1.4.碱土金属中毒(Ca)我国的煤中CaO含量相对较高,尤其在当前电厂广泛使用的神府煤和东胜煤中CaO含量很高,煤中灰含量为9%~24%,而灰中CaO含量为13%~30%,因此CaO对我国SCR催化剂的影响尤为严重。
当煤粉锅炉产生的飞灰中含有碱性、带腐蚀性的氧化钙时,催化剂的中毒会更加明显,这主要是因为CaO的存在除了导致催化剂的物理中毒外,还会导致化学中毒:CaO的碱性使得催化剂酸性下降,另外其生成的CaS(‰也会使活性下降。
催化剂中毒的原因,现象及处理方法?

催化剂中毒的原因,现象及处理方法?
原因:
主要原因是催化剂中附着了Fe、Ni、Cu、VS四种重金属,催化剂在使用过程中,由于这些物质吸附在它的表面而使它的活性和选择性大大下降。
现象:
催化剂的选择性降低,使产品的分布变坏,使汽油和液化气产量降低,干气和焦碳产率上升,最明显的是富气和干气中氢含量增加,气压机超负荷,反应压力上升。
处理:
降低处理量;改变原料性质。
置换催化剂,提高活性。
加入钝化剂,助燃剂。
减少游浆回炼量或不回炼,油浆适当外甩。
提高烧焦效果,预提升介质由原来蒸汽改为干气。
催化剂中毒

催化剂中毒可逆中毒和不可逆中毒既然中毒是由于毒物和催化剂活性组分之间发生了某种相互作用,那么可以根据这种相互作用的性质和强弱程度,将其分为可逆的(可以再生,暂时的)和不可逆的(不可以再生)3.1金属催化剂的中毒用作催化剂的金属用吸附可利用的d轨道,这无论对它的毒性或它对毒物的敏感性都是关键。
金属催化剂的毒物有如下三类:第一类是Ⅴ族和Ⅵ族元素的具有未共享电子队的非金属化合物(N、P、As、Sb、和O、S、Se、Te的化合物),毒性的程度取决于空的价轨或未共享电子的可利用性。
一些非金属元素化合物,当它有未共享的电子对时,呈毒性;当元素的外层电子结构达到了稳定的八电子偶,而且不存在孤对电子时,则无毒。
第二类是金属离子,这些离子具有已占用的d轨道,并且d轨道上有与金属催化剂的空轨键合的电子。
当金属离子没有d轨道,或者d轨道全空着,或者d轨道伟达到半充满以前,它对铂是无毒的;金属离子的d轨道从半充满到全充满者,它对铂是有毒的。
第三类是不饱和化合物,由于它分子中的不饱和键能提供电子与金属催化剂的d 轨成键,使催化剂中毒。
下表列出了一些金属催化剂的不饱和化合物毒物序号反应催化剂毒物1环己烯加氢Ni、Pt苯,氰化物2乙烯加氢Ni C2H2、CO3合成氨Fe CO4氨氧化Pt C2H2由于不饱和化合物的毒性逾期不饱和度有关,若是其不饱和度减小,就可使毒性减弱或者消除。
例如在合成氨生产中,利用甲烷化催化剂除去原料气中的CO就是基于这一点。
3.2毒物的结构和性质对其毒性的影响毒物分子的毒性大小一般与两个因素有关:一是被毒物分子覆盖的催化剂活性位的数目,此为覆盖因子;二是毒物分子在催化剂表面的平均停留时间,此为吸附寿命因子。
如下表列出几种硫化物对用于丁二烯酸加氢的铂黑催化剂的毒性系数序号毒物分子量α×10-5相对毒性1、硫化氢343.4 12、二硫化碳766.41.93、噻吩8414.84.44、半胱氨酸12116.74.9从表中可以看出,毒物的分子量愈大,毒性系数愈大。
- 1、下载文档前请自行甄别文档内容的完整性,平台不提供额外的编辑、内容补充、找答案等附加服务。
- 2、"仅部分预览"的文档,不可在线预览部分如存在完整性等问题,可反馈申请退款(可完整预览的文档不适用该条件!)。
- 3、如文档侵犯您的权益,请联系客服反馈,我们会尽快为您处理(人工客服工作时间:9:00-18:30)。
催化剂中毒catalyst poisoning
反应原料中含有的微量杂质使催化剂的活性、选择性明显下降或丧失的现象。
中毒现象的本质是微量杂质和催化剂活性中心的某种化学作用,形成没有活性的物种。
在气固多相催化反应中形成的是吸附络合物。
一类是如果毒物与活性组分作用较弱,可用简单方法使活性恢复,称为可逆中毒或暂时中毒。
另一类为不可逆中毒,不可能用简单方法恢复活性。
为了降低副反应的活性,有时需要使催化剂选择中毒。
催化剂在使用中会因各种因素而失去活性,其中重要的一个因素就是中毒.催化剂中毒的原因有几种可能,原科中所含的少量杂质,或是强吸附(多为化学吸附)在活性中心上,或是与活性中心起化学作用,变为别的物质,都能使活性中心中毒.另外,反应产物中也可能有这样的毒物;在催化剂的制备过程中,载体内所含的杂质与活性组分相互作用,也可能毒化活性中心。
一些催化剂在一些反应中的毒物,其中有些是暂时性毒物,有些是永久性毒物.例如合成氨中用的铁系催化剂,水和氧是毒物,当这种中毒现象发生时,可以用还原或加热的方法,使催化剂重新活化,这种中毒是暂时性中毒,或称可逆中毒;而硫或磷的化合物对于这个催化剂和这个反应也是毒物,当由它们引起中毒时,催化剂就很难重新活化,这是永久性中毒,或称不可逆中毒.后面一种中毒,是可以预防的。
中毒不仅影响催化剂的活性,造成催化剂的活性下降,也影响催化剂的选择性.中毒是在化工生产中使用催化剂时经常遇到的实际问题,但我们了解得还不十分清楚.至于怎样防止中毒和解毒,要通过实践来加以解决.。